100万吨焦化基础资料讲解
“100万吨年延迟焦化工程”PM设计
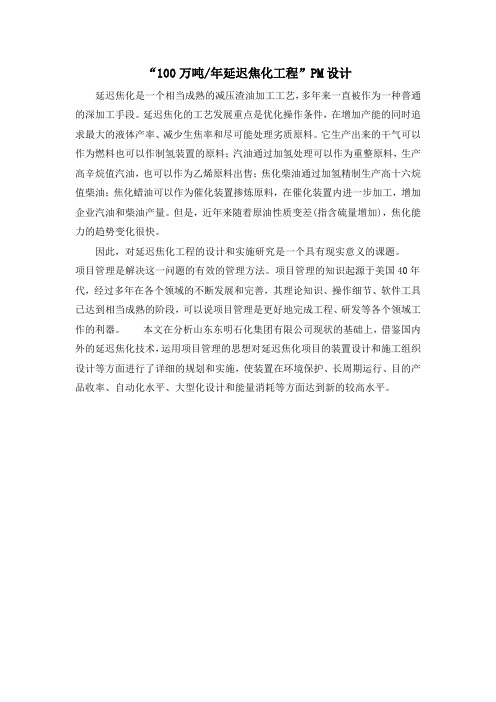
“100万吨/年延迟焦化工程”PM设计
延迟焦化是一个相当成熟的减压渣油加工工艺,多年来一直被作为一种普通的深加工手段。
延迟焦化的工艺发展重点是优化操作条件,在增加产能的同时追求最大的液体产率、减少生焦率和尽可能处理劣质原料。
它生产出来的干气可以作为燃料也可以作制氢装置的原料;汽油通过加氢处理可以作为重整原料,生产高辛烷值汽油,也可以作为乙烯原料出售;焦化柴油通过加氢精制生产高十六烷值柴油;焦化蜡油可以作为催化装置掺炼原料,在催化装置内进一步加工,增加企业汽油和柴油产量。
但是,近年来随着原油性质变差(指含硫量增加),焦化能力的趋势变化很快。
因此,对延迟焦化工程的设计和实施研究是一个具有现实意义的课题。
项目管理是解决这一问题的有效的管理方法。
项目管理的知识起源于美国40年代,经过多年在各个领域的不断发展和完善,其理论知识、操作细节、软件工具已达到相当成熟的阶段,可以说项目管理是更好地完成工程、研发等各个领域工作的利器。
本文在分析山东东明石化集团有限公司现状的基础上,借鉴国内外的延迟焦化技术,运用项目管理的思想对延迟焦化项目的装置设计和施工组织设计等方面进行了详细的规划和实施,使装置在环境保护、长周期运行、目的产品收率、自动化水平、大型化设计和能量消耗等方面达到新的较高水平。
100万吨焦化工程施工组织
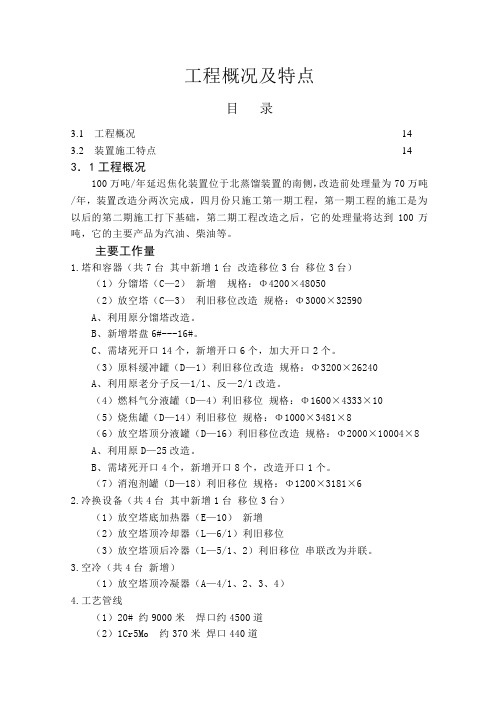
工程概况及特点目录3.1 工程概况14 3.2 装置施工特点14 3.1工程概况100万吨/年延迟焦化装置位于北蒸馏装置的南侧,改造前处理量为70万吨/年,装置改造分两次完成,四月份只施工第一期工程,第一期工程的施工是为以后的第二期施工打下基础,第二期工程改造之后,它的处理量将达到100万吨,它的主要产品为汽油、柴油等。
主要工作量1.塔和容器(共7台其中新增1台改造移位3台移位3台)(1)分馏塔(C—2)新增规格:Φ4200×48050(2)放空塔(C—3)利旧移位改造规格:Φ3000×32590A、利用原分馏塔改造。
B、新增塔盘6#---16#。
C、需堵死开口14个,新增开口6个,加大开口2个。
(3)原料缓冲罐(D—1)利旧移位改造规格:Φ3200×26240A、利用原老分子反—1/1、反—2/1改造。
(4)燃料气分液罐(D—4)利旧移位规格:Φ1600×4333×10(5)烧焦罐(D—14)利旧移位规格:Φ1000×3481×8(6)放空塔顶分液罐(D—16)利旧移位改造规格:Φ2000×10004×8A、利用原D—25改造。
B、需堵死开口4个,新增开口8个,改造开口1个。
(7)消泡剂罐(D—18)利旧移位规格:Φ1200×3181×62.冷换设备(共4台其中新增1台移位3台)(1)放空塔底加热器(E—10)新增(2)放空塔顶冷却器(L—6/1)利旧移位(3)放空塔顶后冷器(L—5/1、2)利旧移位串联改为并联。
3.空冷(共4台新增)(1)放空塔顶冷凝器(A—4/1、2、3、4)4.工艺管线(1)20# 约9000米焊口约4500道(2)1Cr5Mo 约370米焊口440道5.框架(1)框架—2A、共两层,地面12根立柱,其中8米平台为21200×11100,13米平台为14400×11100。
年产100万吨焦炭焦化厂硫铵工段初步设计
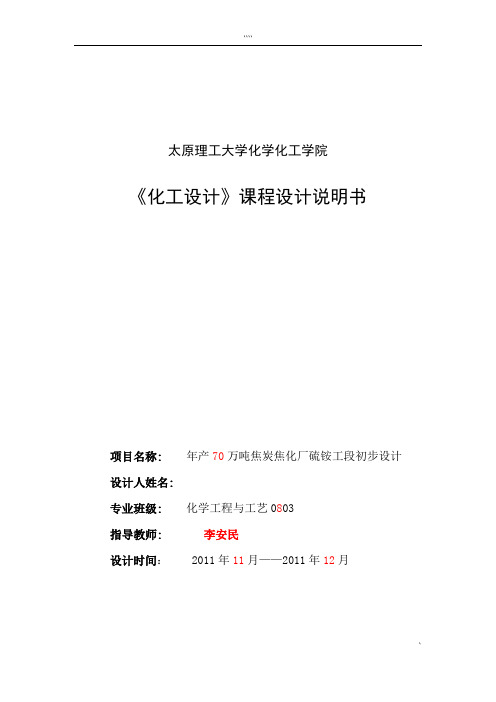
太原理工大学化学化工学院《化工设计》课程设计说明书项目名称: 年产70万吨焦炭焦化厂硫铵工段初步设计设计人姓名:专业班级: 化学工程与工艺0803****: ***设计时间: 2011年11月——2011年12月目录第一章概述1设计依据--------------------------------------------------------------------3 2硫铵生产方法的确定----------------------------------------------------------5 第二章饱和器法硫铵生产工艺1工艺流程图及流程叙述--------------------------------------------------------7 2硫铵工段的正常操作制度------------------------------------------------------8 3硫铵工段的工艺操作参数------------------------------------------------------9 4车间工艺布置---------------------------------------------------------------10 第三章化工计算1计算原始数据---------------------------------------------------------------12 2小时生产能力计算 ----------------------------------------------------------13 3氨平衡计算-----------------------------------------------------------------134 水平衡的计算---------------------------------------------------------------145 热平衡计算-----------------------------------------------------------------15 第四章设备选型1饱和器基本尺寸-------------------------------------------------------------20 2旋风式除酸器的基本尺寸-----------------------------------------------------22 第五章设备结构图叙述及附表1设备结构图叙述-------------------------------------------------------------23 2 工艺设备一览表-------------------------------------------------------------26 致谢-----------------------------------------------------------------------27参考文献--------------------------------------------------------------------28第一章、概 述1设计依据(1) 设计项目名称:年产70万吨焦炭焦化厂硫铵工段初步设计(2) 生产能力:年产干硫铵2.7万吨(3) 生产方法:饱和器法(外部除酸式),又称半直接法(4) 硫铵主要质量标准:硫铵的主要质量标准名称指标 一级品 二级品 三级品 颜色白色或微带颜色的结晶 氮含量(以干基计)≥21 ≥20.8 ≥20.6 水分%≤0.3 ≤1.0 ≤2.0 游离酸()% ≤0.05≤0.2 ≤0.3 粒度(60目筛余量)≥75 (5) 硫铵的物理化学性质:硫铵的分子式为,分子量为132.16。
100万吨焦炉基础工程施工组织设计方案

焦化甲醇项目焦炉基础施工方案焦炉基础施工方案目录1.项目简介2.施工技术准备3.施工部署4.施工顺序和施工网络计划5.主要施工方法和技术要求6.质量保证措施7.安全保证措施8.现场文明施工9.施工期间的保证措施10.冬季施工计划11.附图……附图……附图……附图一、项目概况1.1.1瑞祥焦化100万吨焦炉项目位于尼勒克县郊区。
该焦炉系统的基础主要包括焦炉基础、推焦车基础、阻力墙、主副烟道、端部平台和中间平台基础等。
焦炉基础为钢筋混凝土框架结构,混凝土强度等级为C30和C35,包括基础底、顶板和28 KJ-1、50 KJ-2、底板。
推焦车轨道基础为钢筋结构,上部采用预埋螺栓固定,阻力墙为现浇钢筋混凝土剪力墙结构,顶部标高为▽10.23,主、分烟道底板和墙体为C30混凝土,顶部为钢筋混凝土板,分烟道底板标高为▽-3.79 ▽-0.02。
1.1.2桥台基础为钢筋混凝土框架结构,基础为独立基础。
板底标高为▽-4.0。
1.1.3操作平台侧的基础为钢筋混凝土独立基础,基础标高为▽-4.85。
操作平台侧基础为钢筋混凝土挡土墙,操作平台侧基础为钢筋混凝土独立基础。
1.1.4推焦车轨道基础为钢筋混凝土框架结构,顶部标高为▽0.18,轨道安装标高为▽0.34。
熄焦轨道基础为钢筋混凝土条形基础,基础标高为-2.50,安装轨道标高为0.210。
1.1.5操作台为单层钢结构,机侧操作台顶标高为▽3.968,焦侧操作台顶标高为▽3.28,焦侧操作台尺寸为92.3×2.285,机侧操作台尺寸为92.3×2.335。
1.2工程特点1.2.1焦炉炉顶有2044×2燃气预埋管和1460×2清扫管。
它们的位置要求精确,正负误差为3毫米。
同时车顶和侧梁高度较高,不允许有正公差。
因此,在焦炉炉顶施工时,应精心组织施工,采取强有力的施工技术措施,确保焦炉炉顶的设计参数符合设计要求。
1.2.2挡土墙设计中预埋件和预埋螺栓较多,结构形式复杂。
100万吨焦炉基础施工方案
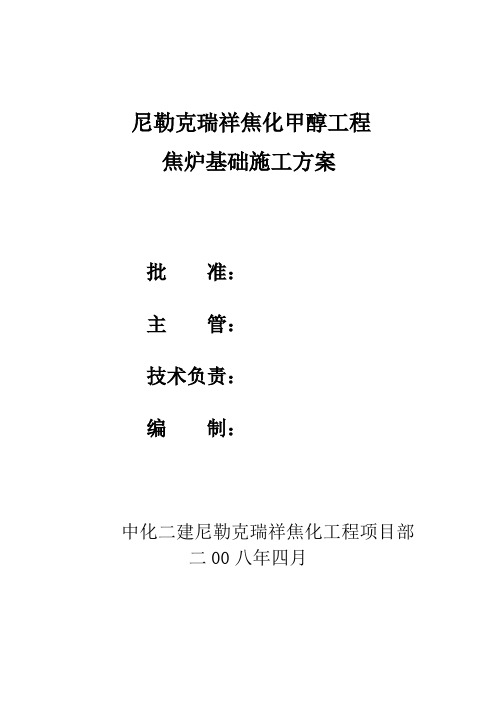
尼勒克瑞祥焦化甲醇工程焦炉基础施工方案批准:主管:技术负责:编制:中化二建尼勒克瑞祥焦化工程项目部二00八年四月焦炉基础施工方案目录1、工程概况 (4)2、施工技术准备 (5)3、施工部署 (8)4、施工顺序及施工网络计划 (9)5、主要施工方法及技术要求 (9)6、质量保证措施 (21)7、安全保证措施 (26)8、现场文明施工 (27)9、工期保证措施 (27)10、冬季施工方案 (30)11、附图表 (32)一、工程概况1.1.1 瑞祥焦化100万吨焦炉新建工程座落在尼勒克县郊,本焦炉系统基础主要包括焦炉基础、推焦机基础、抵抗墙、主、分烟道及端台、间台基础等,焦炉基础为钢筋砼框架结构,砼强度等级为C30、C35,包括基础底、顶板和28个KJ-1、50个KJ-2,底板平面尺寸为95×14.3米,板厚800mm,两端1200mm,基底标高为▽-3.20,两端为▽-3.60,顶板标高为▽0.874。
推焦机轨道基础为钢筋结构,上部预埋螺栓固定轨道,抵抗墙为现浇钢筋砼剪力墙结构,顶标高为▽10.23,主、分烟道底板及墙体为C30砼,顶板钢筋砼板,分烟道底板标高▽-3.79顶标高▽-0.02。
1.1.2 间台基础为钢筋砼框架结构,基础为独立基础,板底标高为▽-4.0。
1.1.3操作台端台焦侧基础为钢筋砼独立基础,基底标高为▽-4.85, 操作台端台机侧基础为钢筋砼挡土墙, 操作台间台焦侧基础为钢筋砼独立基础。
1.1.4推焦车轨道基础为钢筋砼框架结构,基顶标高为▽0.18,安装车轨的标高为▽0.34。
熄焦车轨道基础为钢筋砼条形基础,基底标高为▽-2.50,安装车轨标高为▽0.210。
1.1.5操作平台为单层钢结构,机侧操作平台顶标高为▽3.968,焦侧平台顶标高为▽3.28,焦侧平台尺寸92.3×2.285机侧平台尺寸为92.3×2.335。
1.2 工程特点1.2.1焦炉顶板上有2044×2根煤气预埋管,1460×2根清扫管,其位置要求相互准确,正负误差在3mm以内,同时顶板标高及边梁高要求很高,不允许出现正公差,因此在施工焦炉顶板时,顶部应精心组织,精心施工,采取强有力的施工技术措施,确保焦炉顶板设计参数达到设计要求。
100万-220万吨焦化工程解析

1、220万吨全焦(含干熄焦)及20万吨甲醇投资分析本工程资金总需求量为199227.39万元,其中固定资产投资为167311.08万元,建设期贷款利息9687.96万元,铺底流动资金为6668.50万元,详见投资分析表、总估算表。
5、120万t焦化厂(2011年项目)** 工程、水文地质条件和气象资料(本资料仅供参考,详细资料由承包方向当地气象部门索取)该项目位于六盘水市钟山区水城盆地东北边缘的群峰之间,东经104°53`。
北纬26°36`。
距市中心约4千米,海拔在1800~2000米之间。
水城地处云贵高原中部,海拔较高,纬度较低,冬无严寒,夏无酷暑,气候温和,属亚热带湿润季风气候。
年内雨日多、湿度大、日照少,并有冰雹、大风暴雨、雨淞、霜冻、雪凝等灾害性天气发生。
冬季采暖室外计算温度:-3.8℃夏季通风室外计算温度:23℃冬季通风室外计算温度:3.0℃夏季空气调节室外计算干球温度:27.8℃夏季空气调节室外计算日平均温度:24.8℃冬季空气调节室外计算相对湿度:75%夏季空气调节室外计算相对湿度:69%冬季室外平均风速:2.4m/s夏季室外平均风速:2.1m/s冬季大气压力:819hPa夏季大气压力:815.1hPa海拔:>1800m最大冻土深度为:0.1m2.2.1 工程地质工程所在区碳酸盐分布广泛,岩溶发育。
正地形以峰丛为主,负地形以洼地和谷地为主;洼地从分水岭向水城盆地变浅,由锥状变为蝶状,地貌类型从分水岭的丛峰洼地,峰丛谷地向水城盆地两侧的峰林洼地、峰林谷地或峰林台地过渡。
本工程所在地周围土壤为第四系粘土、亚粘土覆盖层。
本工程位于NWW—SEE 向构造的威水复式背斜与法子冲涡轮构造的结合部。
2.2.2 地震烈度、水文特征按国家地震局1976《中国地震烈度区划图》水城地区地震烈度为6度。
水文特征地面水主要有响水河、三岔河和窑上水库。
水城盆地地下水丰富,日最大开采量约15万m3。
100万吨焦炉基础施工方案

尼勒克瑞祥焦化甲醇工程焦炉基础施工方案批准:主管:技术负责:编制:中化二建尼勒克瑞祥焦化工程项目部二00八年四月焦炉基础施工方案目录1、工程概况 (4)2、施工技术准备 (5)3、施工部署 (8)4、施工顺序及施工网络计划 (9)5、主要施工方法及技术要求 (9)6、质量保证措施 (21)7、安全保证措施 (26)8、现场文明施工 (27)9、工期保证措施 (27)10、冬季施工方案 (30)11、附图表 (32)一、工程概况1.1.1 瑞祥焦化100万吨焦炉新建工程座落在尼勒克县郊,本焦炉系统基础主要包括焦炉基础、推焦机基础、抵抗墙、主、分烟道及端台、间台基础等,焦炉基础为钢筋砼框架结构,砼强度等级为C30、C35,包括基础底、顶板和28个KJ—1、50个KJ-2,底板平面尺寸为95×14.3米,板厚800mm,两端1200mm,基底标高为▽-3.20,两端为▽-3。
60,顶板标高为▽0。
874.推焦机轨道基础为钢筋结构,上部预埋螺栓固定轨道,抵抗墙为现浇钢筋砼剪力墙结构,顶标高为▽10。
23,主、分烟道底板及墙体为C30砼,顶板钢筋砼板,分烟道底板标高▽—3。
79顶标高▽-0.02。
1.1.2 间台基础为钢筋砼框架结构,基础为独立基础,板底标高为▽-4.0.1.1.3操作台端台焦侧基础为钢筋砼独立基础,基底标高为▽-4。
85, 操作台端台机侧基础为钢筋砼挡土墙,操作台间台焦侧基础为钢筋砼独立基础。
1.1.4推焦车轨道基础为钢筋砼框架结构,基顶标高为▽0.18,安装车轨的标高为▽0。
34.熄焦车轨道基础为钢筋砼条形基础,基底标高为▽-2。
50,安装车轨标高为▽0.210。
1.1.5操作平台为单层钢结构,机侧操作平台顶标高为▽3。
968,焦侧平台顶标高为▽3.28,焦侧平台尺寸92.3×2。
285机侧平台尺寸为92.3×2。
335。
1.2 工程特点1.2.1焦炉顶板上有2044×2根煤气预埋管,1460×2根清扫管,其位置要求相互准确,正负误差在3mm以内,同时顶板标高及边梁高要求很高,不允许出现正公差,因此在施工焦炉顶板时,顶部应精心组织,精心施工,采取强有力的施工技术措施,确保焦炉顶板设计参数达到设计要求。
焦化基础知识ppt课件
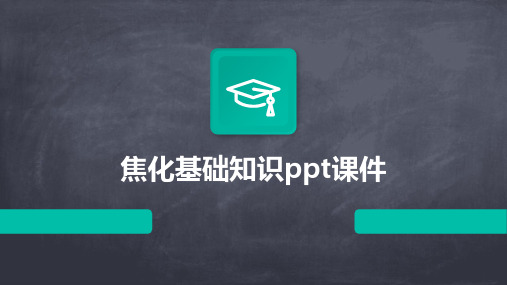
强化焦炭后处理
通过焦炭后处理技术,如熄焦 、筛分等,进一步提高焦炭质
量。
06
安全生产与环境保护
Chapter
焦化行业安全生产特点
高温高压
焦化生产过程中涉及高温高压环 境,易引发火灾、爆炸等事故。
有毒有害
生产过程中产生的废气、废水和固 废等污染物,对人体健康和环境造 成危害。
焦炭反应后强度(CSR)
表示焦炭在经历反应后的抗碎能力, 是评价焦炭质量的关残渣,对 焦炭质量和高炉冶炼有重要影响。
焦炭硫分
焦炭中含硫量,对高炉冶炼和环境保 护有重要意义。
焦炭质量影响因素分析
原料煤性质
原料煤的种类、成分、结 构和性质对焦炭质量有决 定性影响。
辅助材料种类及作用
辅助材料种类
主要包括溶剂、催化剂、添加剂 等。
作用
改善炼焦过程,提高焦炭质量; 降低炼焦成本,提高经济效益; 减少环境污染,保护环境。
03
炼焦工艺与设备
Chapter
炼焦炉结构类型及特点
炼焦炉结构类型
根据加热方式、煤气供入方式等 可分为多种类型,如直立式炼焦 炉、水平式炼焦炉等。
连续性生产
焦化生产为连续性作业,一旦发生 事故,可能导致整个生产线停产。
常见事故类型及预防措施
火灾事故
加强火源管理,严禁违章动火;定期 检查消防设施,确保其完好有效。
中毒窒息事故
加强通风换气,降低有毒有害气体浓 度;配备个人防护用品,定期进行体 检。
爆炸事故
严格控制可燃气体浓度,防止形成爆 炸性混合物;定期检测安全阀、压力 表等安全附件。
焦化基础知识ppt课件
目录
- 1、下载文档前请自行甄别文档内容的完整性,平台不提供额外的编辑、内容补充、找答案等附加服务。
- 2、"仅部分预览"的文档,不可在线预览部分如存在完整性等问题,可反馈申请退款(可完整预览的文档不适用该条件!)。
- 3、如文档侵犯您的权益,请联系客服反馈,我们会尽快为您处理(人工客服工作时间:9:00-18:30)。
100万吨/年延迟焦化基础资料镇海炼化股份有限公司炼油二部2004年7月目录第一章、总说明 (1)第二章、原料及产品性质 (3)第三章、主要技术规格 (10)第四章、生产方案及生产过程 (19)第五章、工艺技术路线及特点 (26)第六章、主要设备选择 (32)第七章、生产控制 (37)第八章、装置平面布置 (40)第九章、公用工程及辅助设施 (42)第十章、生产控制分析 (44)第十一章、主要技术经济指标 (45)第十二章、安全、环保、消防 (47)附工艺流程图第一章、总说明1、设计依据1.1 镇海炼油化工股份有限公司综合管理处2003年2月20日提供的“150万吨/年延迟焦化装置”设计委托单,委托编号2003S008。
1.2 中国石油化工科学研究院96年8月19日提供的沙轻减压渣油。
1.3 “镇海炼油化工股份有限公司150万吨/年延迟焦化装置可行性研究报告”,2003年3月。
1.4 镇海炼油化工股份有限公司综合管理处提供的“2003年公司重点项目设计进度对接会会议纪要”,2003技改纪040号,2003年5月7日。
1.5 镇海炼油化工股份有限公司综合管理处提供的“100万吨/年延迟焦化装置初步设计中间汇报审查会会议纪要”,2003技改纪048号,2003年5月23日。
2、装置概况2.1装置建设性质本装置为新建装置。
2.2装置组成装置由焦化部分、分馏部分、接触冷却部分、水力除焦部分、切焦水和冷焦水部分组成。
2.3装置规模焦化部分:设计规模为100×104t/a;分馏部分:设计规模为200×104t/a;装置设计年开工时数为:8000小时;循环比:0.25;生焦时间:24小时。
2.4装置定员按照中国石油化化工总公司《石油化工生产装置设计定员暂行规定(试行)》SHSG-051-98规定,新建100万吨/年延迟焦化装置定员见表1-1。
鉴于炼化公司目前采用五班三倒制的倒班方式,新建装置的定员也五班三倒的要求确定,管理人员、技术人员、辅助岗位操作人员(包括吊车、电梯、高压水泵、除焦岗位操作人员)和后勤服务人员由镇海炼化公司另外统一考虑。
表1-1 装置定员表第二章、原料及产品1、原料装置的原料为沙轻减压渣油和伊重减压渣油,由工厂罐区提供。
表2-1 沙轻减渣和伊重减渣的性质进装置温度:150℃进装置压力:0.5Mpa(g)进装置相态:液相进装置方式:管道输送进装置流量:125000kg/hr2、产品装置的产品包括:焦化富气、粗汽油、柴油、轻蜡油以及石油焦。
2.1 焦化富气产量:9883.1 kg /hr出装置温度:49℃出装置压力:1.0Mpa(g)出装置相态:气相出装置方式:管道输送至脱硫装置脱硫2.2粗汽油产量:21206 kg /hr出装置温度:40℃出装置压力:0.5Mpa(g)出装置相态:液相出装置方式:管道输送至加氢精制装置2.3柴油产量:29000kg /hr出装置温度:65℃出装置压力:0.5Mpa(g)出装置相态:液相出装置方式:管道输送至加氢精制装置2.4轻蜡油产量:23000kg /hr出装置温度:150℃出装置压力:0.5Mpa(g)出装置相态:液相出装置方式:管道输送至加氢精制装置或罐区2.5石油焦产量:36200kg /hr出装置相态:固相出装置方式:用汽车或皮带输送机转运至CFB锅炉作燃料3、产品性质3.1富气性质表2-23.3汽油性质表2-33.4柴油性质表2-43.5轻蜡油性质表2-53.6焦化重蜡油性质表2.63.7第三章、主要技术规格1、化学药品性质消泡剂名称:CDF-10A焦化消泡剂产品标准:Q/CP XJH024-2002消泡剂指标见表3-1。
2、物料平衡装置加工量为100×104t/a,循环比为0.25。
装置计算物料平衡时数8000小时。
装置物料平衡见表3-2。
物料平衡表3-23、辅助材料及公用工程消耗3.1辅助材料消耗见表3-3辅助材料消耗表3-33.2公用工程消耗3.2.1水用量(见表3-4)3.2.2电用量(见表3-5)3.2.3蒸汽用量(见表3-6)3.2.4压缩空气及氮气用量(见表3-7)3.2.5燃料用量(见表3-8)续表3-5续表3-53.2.3蒸汽用量表3-64 装置消耗指标及能耗4.1 装置能耗见表3-94.2 能耗分析本装置能耗为1137.974 MJ/t原料,与ZRCC现有焦化装置的能耗相比偏高,主要有以下原因:4.2.1本装置设计采用空冷凝汽式富气压缩机,而现有焦化装置采用背压式富气压缩机,其能耗相差约127.279 MJ/t原料。
4.2.2现有焦化装置低温热输出到ZRCC二电站,其能耗相差约163.285MJ/t原料。
4.2.3同类装置能耗比较:上海金山100万吨/年延迟焦化装置焦化部分设计能耗为:1282.07 MJ/t原料。
中石化系统19套焦化装置2001年综合能耗平均为:1256.88 MJ/t原料(该数据取自《2001年中国石化集团公司炼油生产装置基础数据汇编》)。
4.3节能措施4.3.1焦化加热炉采用热管式空气预热器,回收烟气中余热,提高了加热炉效率。
4.3.2选用高效率的机泵,合理匹配电机,降低电耗。
4.3.3充分利用分馏塔各侧线的逐级能量,优化换热流程,提高加热炉进料温度,降低加热炉负荷,减少燃料用量。
4.3.4根据各冷却器的运行工况,冷却水采用分级使用,部分冷却器采用二次用水,减少循环水用量。
4.3.5合理选用各保温管线的保温厚度,降低热损失。
4.3.6采用发生0.35 MPa(g)低压蒸汽的办法尽可能回收装置余热。
4.4节水措施4.4.1采用空冷凝汽式压缩机,大量节约冷却水。
4.4.2尽量采用空冷器代替水冷器,从而节省冷却水用量。
第四章、生产方法及生产过程1、生产方法延迟焦化是将渣油经深度热裂化转化为气体、轻、中质馏分油及焦炭的加工过程,是炼油厂提高轻质油收率和生产石油焦的主要手段。
渣油在通过加热炉时,采用高的流速和较高的加热强度,使油品在短时间内获得焦化反应所需的热量,并迅速离开加热炉管进入焦炭塔内进行裂化缩合反应,生成焦炭和高温油气,高温油气进一步分馏后得到粗汽油、柴油、蜡油、重蜡油、富气等产品。
2、主要生产过程自装置外来原料油(减压渣油)进入装置原料缓冲罐,经原料油泵升压后分别与柴油、轻蜡油、重蜡油换热后分二路进入分馏塔,一路与来自焦炭塔的高温油气(420℃左右)接触换热,高温油气中的循环油馏份被冷凝,原料油与冷凝的循环油一起进入分馏塔底,另一路直接进入分馏塔底,分馏塔底油经辐射进料泵升压后进入焦化加热炉,经对流室、辐射室加热至495~505℃左右离开加热炉,经过四通阀进入焦炭塔底部。
在焦炭塔内经过高温和长时间的停留,原料油和循环油发生了一系列的热裂解和缩合等反应,最后生成焦炭和高温油气。
生成的焦炭贮存在焦炭塔内,高温油气从焦炭塔顶出来后进入分馏塔下段换热区。
进入分馏塔下段换热区的高温油气与原料油直接接触换热,冷凝出的循环油流入分馏塔底,大量油气经过3块洗涤板后进入重蜡油集油箱以上分馏段,经过进一步分馏,从下往上分别分馏出重蜡油、蜡油、柴油、汽油和富气。
3、工艺流程说明原料渣油(包括催化油浆及常Ⅲ洗涤油等)从装置外来,进入原料缓冲罐(V1101),经原料油泵(P1101/1、2)抽出升压后,先于柴油换热至181℃(E1101/1、2),接着与中段油换热至227℃(E1102/1、2),最后与蜡油换热至289℃ (E1103/1~4)后分两股进入分馏塔,一股(约占总物料的四分之一)进入分馏塔(T1102) 下段换热区与来自焦炭塔(T1101/1、2)的高温油气接触换热,高温油气中的循环油馏分被冷凝,原料油与冷凝的循环油一起进入分馏塔底,另一股(约占总物料的四分之三)直接进入分馏塔底部。
分馏塔底部的原料油经加热炉辐射进料泵(P1102/1~2)升压后进入加热炉(炉1101),经对流室和辐射室加热至500℃后出加热炉经四通阀进入焦炭塔(T1101/1、2)底部。
在高温和长停留时间的条件下,高温原料油在焦炭塔内进行一系列复杂的热裂解、缩合等反应,最后生成焦炭和油气。
高温油气自焦炭塔顶逸出去分馏塔,焦炭在塔内沉积生焦,当焦炭塔生焦到一定高度后停止进料,切换到另一个焦炭塔内进行生焦。
切换后,老塔用蒸汽进行小吹汽,将塔内残留油气吹至分馏塔,然后再改为大吹汽、给水进行冷焦,焦炭塔大吹汽、给水冷焦时产生的大量高温蒸汽及少量油气进入接触冷却塔(T1103),接触冷却塔底的污油用接触冷却塔底泵(P1112/1、2)抽出,经水箱冷却器(WC1105)冷却后,部分打入T1103顶部做回流,部分送入本装置污油罐经脱水后做急冷油回炼。
塔顶蒸汽及轻质油气经塔顶空冷器、水冷器后入接触冷却塔顶油气分离器(V1106)分离,分离出的污油送入本装置污油罐,污水经接触冷却塔顶污水泵(P1113/1、2)升压后排入含油污水罐(V1403),不凝气进入低压瓦斯管网。
焦化回炼排水污泥是利用焦化换塔后停止生产的焦碳塔(俗称老塔)余热,将排水污泥注入塔底,进入塔内的排水污泥在塔底350℃以上的高温焦床中骤然汽化,其中的水、轻烃组份迅速汽化形成汽流,并携带污泥中300℃以上的重烃及灰份沿生焦孔上升。
在塔上部由于体积骤然膨胀,流速减缓,固体灰分及难汽化的重烃沉降或吸附在焦碳塔上部的泡沫层中,重烃则在高温下继续与泡沫层中自由基进一步反应,体积缩小形成新的泡沫层,轻烃及水汽组份随油气进入分馏。
焦炭塔在大吹汽结束后,将大吹汽切换成小吹汽,视10米排水污泥线阀前压力变化情况逐步开启焦-1、2底污泥进料阀,关排水污泥进焦-1、2顶作急冷油阀,内外操配合,根据塔顶温度、压力情况,逐渐开大污泥阀,直到全开。
当冷焦塔塔顶温度<350℃时,立即联系调度或排水调小污泥泵量,开排水污泥进焦-1、2顶作急冷油阀,关10米焦-1、2排水污泥线阀。
塔底污泥回炼时间约1小时。
塔底污泥回炼结束,进行小给水操作。
打开冷焦水去焦炭塔塔底的控制阀门,由冷焦水冷水泵(P1403/1、2)把冷焦水贮罐内(V1402)的冷焦水抽送至焦炭塔进行冷焦,根据焦炭塔顶压力,由控制阀调节给水量大小,直至大给水。
当冷焦塔塔顶温度低于150℃时,15米平台处开溢流阀关去接触冷却塔阀,同时停用接触冷却塔系统,冷焦进入溢流阶段。
溢流时冷焦水从塔顶溢出,在进入冷焦水罐前,采用水--水混合器注水冷却,把部分低温冷焦水注入到高温溢流水中,控制溢流水进罐温度在100℃以下,以降低冷焦水罐振动。
当焦炭塔顶温度降至90℃以下时,冷焦完毕,塔内存水放至冷焦水热水罐。
进入冷焦水罐内的冷焦水经冷焦水热水泵(P1402/1、2)抽出,送旋流除油器除油,最后进空冷进行第二次冷却,冷至50℃以下进入冷焦水贮水罐(V1402/1、2)循环使用。