加热炉的温度控制
温度控制与调节的加热炉管理制度

温度控制与调节的加热炉管理制度一、引言加热炉是工业生产中常见的设备之一,主要用于加热各类材料和物体。
在加热炉的运行过程中,温度的控制与调节是至关重要的。
为了保证加热炉的正常运行和安全性,建立一个合理有效的温度控制与调节的加热炉管理制度是必不可少的。
二、管理目标1.保证工作人员的安全:确保工作人员在操作加热炉时不受伤害,并具备相关的操作技能和知识。
2.提高生产效率:通过合理的温度控制与调节,达到最佳的加热效果,提高生产效率。
3.延长设备寿命:通过严格的管理制度,降低加热炉的故障率,延长设备的使用寿命。
4.节约能源:合理控制温度,减少能源浪费,提高能源利用率。
三、管理措施1.设立管理责任部门:明确温度控制与调节的加热炉管理责任部门,并明确各个岗位的职责和权限。
2.制定管理制度:制定温度控制与调节的加热炉管理制度,明确操作规程和安全操作要求。
3.安全培训与技能考核:对从事加热炉操作的人员进行安全培训,确保其具备相关的操作技能和安全意识。
定期进行技能考核,对不合格人员进行补充培训。
4.设备维护与检修:定期进行加热炉设备的检修与维护,确保其良好的工作状态。
对设备故障及时处理,避免因故障引发的安全事故。
5.温度监测与控制:安装可靠的温度监测和控制设备,在加热炉运行过程中及时监测温度变化,并根据需要进行调节,确保温度在设定范围内稳定运行。
6.备份与记录:建立温度控制参数的备份与记录制度,定期进行数据备份,并保留至少一年的记录。
备份与记录可以为温度控制提供参考,并为后续的改进提供依据。
四、应急预案1.事故应急预案:制定加热炉事故应急预案,明确事故发生时的应急处理措施和责任人。
2.紧急停机:在发生温度控制异常或设备故障时,应立即停机,并及时通知相关人员进行处理。
五、管理评估与持续改进定期对温度控制与调节的加热炉管理制度进行评估,检查执行情况和效果。
基于评估结果,对管理制度进行调整和改进,以不断提高管理水平和工作效率。
炉内温度监测与控制的加热炉管理制度

炉内温度监测与控制的加热炉管理制度1. 引言2. 加热炉温度监测2.1 温度监测设备选择温度计热电阻红外线测温仪2.2 温度监测点选择加热炉内的温度监测点应覆盖加热区域、冷却区域和均热区域。
根据不同加热炉的结构和工艺要求,确定合理的温度监测点。
2.3 温度监测频率根据炉内温度的变化情况,设置合理的温度监测频率。
一般来说,加热炉炉内温度的监测频率应不低于30分钟。
3. 加热炉温度控制3.1 温度控制设备选择PID控制器温度控制模块3.2 温度控制参数设置根据加热炉的工艺要求和产品特性,设置合理的温度控制参数。
包括温度上下限设定、控制精度设定等。
3.3 温度控制策略根据加热炉的类型和工艺要求,确定合理的温度控制策略。
例如,采用开关控制、PID控制等方式实现温度控制。
4. 炉内温度监测与控制的规范要求4.1 设备保养与维护定期检查温度计、热电阻等温度监测设备的准确性和可靠性。
定期校准温度监测设备,确保测量结果的准确性。
及时修复和更换不正常工作的温度监测设备。
4.2 温度数据记录与分析定期记录炉内温度的监测数据。
对温度数据进行分析,及时发现和处理温度异常情况。
建立温度数据的历史记录,用于追溯和分析。
4.3 温度监测与控制的纪录与报告对炉内温度监测和控制的情况进行记录和报告。
建立温度监测与控制的档案,包括温度曲线、温度控制参数设置等信息。
5. 总结炉内温度监测与控制是加热炉管理中的重要环节。
通过合理的温度监测设备选择、温度监测频率设置以及温度控制参数设置和策略确定,可以确保加热炉的稳定运行和产品质量的稳定性。
同时,加热炉管理人员应严格遵守规范要求,对温度监测与控制的数据进行记录、分析和报告,以提高加热炉的管理水平和生产效率。
工业加热炉温度控制方法
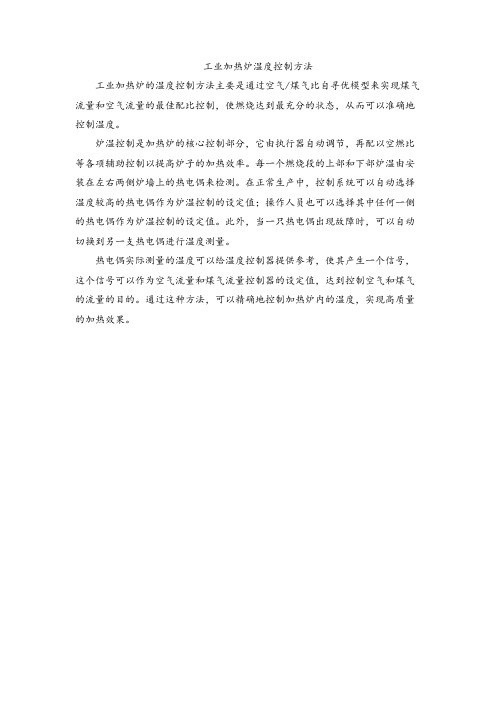
工业加热炉温度控制方法
工业加热炉的温度控制方法主要是通过空气/煤气比自寻优模型来实现煤气流量和空气流量的最佳配比控制,使燃烧达到最充分的状态,从而可以准确地控制温度。
炉温控制是加热炉的核心控制部分,它由执行器自动调节,再配以空燃比等各项辅助控制以提高炉子的加热效率。
每一个燃烧段的上部和下部炉温由安装在左右两侧炉墙上的热电偶来检测。
在正常生产中,控制系统可以自动选择温度较高的热电偶作为炉温控制的设定值;操作人员也可以选择其中任何一侧的热电偶作为炉温控制的设定值。
此外,当一只热电偶出现故障时,可以自动切换到另一支热电偶进行温度测量。
热电偶实际测量的温度可以给温度控制器提供参考,使其产生一个信号,这个信号可以作为空气流量和煤气流量控制器的设定值,达到控制空气和煤气的流量的目的。
通过这种方法,可以精确地控制加热炉内的温度,实现高质量的加热效果。
加热炉温度控制系统工作原理
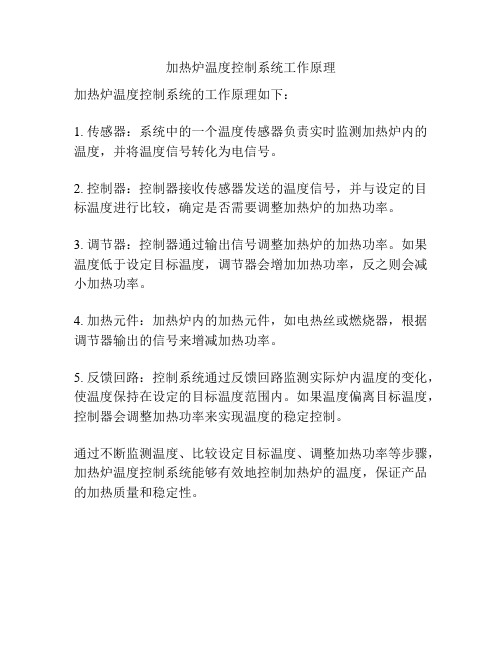
加热炉温度控制系统工作原理
加热炉温度控制系统的工作原理如下:
1. 传感器:系统中的一个温度传感器负责实时监测加热炉内的温度,并将温度信号转化为电信号。
2. 控制器:控制器接收传感器发送的温度信号,并与设定的目标温度进行比较,确定是否需要调整加热炉的加热功率。
3. 调节器:控制器通过输出信号调整加热炉的加热功率。
如果温度低于设定目标温度,调节器会增加加热功率,反之则会减小加热功率。
4. 加热元件:加热炉内的加热元件,如电热丝或燃烧器,根据调节器输出的信号来增减加热功率。
5. 反馈回路:控制系统通过反馈回路监测实际炉内温度的变化,使温度保持在设定的目标温度范围内。
如果温度偏离目标温度,控制器会调整加热功率来实现温度的稳定控制。
通过不断监测温度、比较设定目标温度、调整加热功率等步骤,加热炉温度控制系统能够有效地控制加热炉的温度,保证产品的加热质量和稳定性。
加热炉温度控制系统
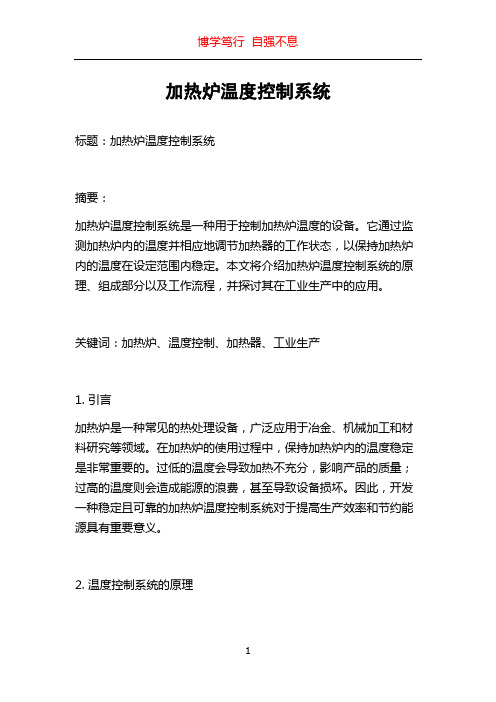
加热炉温度控制系统标题:加热炉温度控制系统摘要:加热炉温度控制系统是一种用于控制加热炉温度的设备。
它通过监测加热炉内的温度并相应地调节加热器的工作状态,以保持加热炉内的温度在设定范围内稳定。
本文将介绍加热炉温度控制系统的原理、组成部分以及工作流程,并探讨其在工业生产中的应用。
关键词:加热炉、温度控制、加热器、工业生产1. 引言加热炉是一种常见的热处理设备,广泛应用于冶金、机械加工和材料研究等领域。
在加热炉的使用过程中,保持加热炉内的温度稳定是非常重要的。
过低的温度会导致加热不充分,影响产品的质量;过高的温度则会造成能源的浪费,甚至导致设备损坏。
因此,开发一种稳定且可靠的加热炉温度控制系统对于提高生产效率和节约能源具有重要意义。
2. 温度控制系统的原理温度控制系统通常由温度传感器、控制器和执行器组成。
温度传感器用于实时监测加热炉内的温度变化,将温度信号传输给控制器。
控制器根据设定的温度范围和温度传感器反馈的实时温度,计算出相应的控制信号。
执行器根据控制信号调节加热器的工作状态,从而实现加热炉温度的稳定控制。
3. 温度控制系统的组成部分3.1 温度传感器温度传感器是温度控制系统中的重要组成部分。
常用的温度传感器有热电阻和热电偶两种。
热电阻传感器的工作原理是利用金属电阻随温度变化而发生的电阻变化,通过测量电阻的变化来确定温度。
热电偶传感器则是利用两种不同材料的接触产生的热电势随温差变化而变化,通过测量热电势的变化来确定温度。
3.2 控制器控制器是温度控制系统的核心部件,负责计算控制信号并将其传输给执行器。
控制器根据设定的温度范围和温度传感器反馈的实时温度,做出相应的控制决策。
常见的控制器包括PID控制器和模糊控制器。
PID控制器根据比例、积分和微分三个方面来调节控制信号;模糊控制器则利用模糊逻辑推断得出控制信号。
3.3 执行器执行器根据控制器传输的控制信号调节加热器的工作状态。
常见的执行器包括电动阀和可调电阻。
电阻加热炉温度控制系统设计
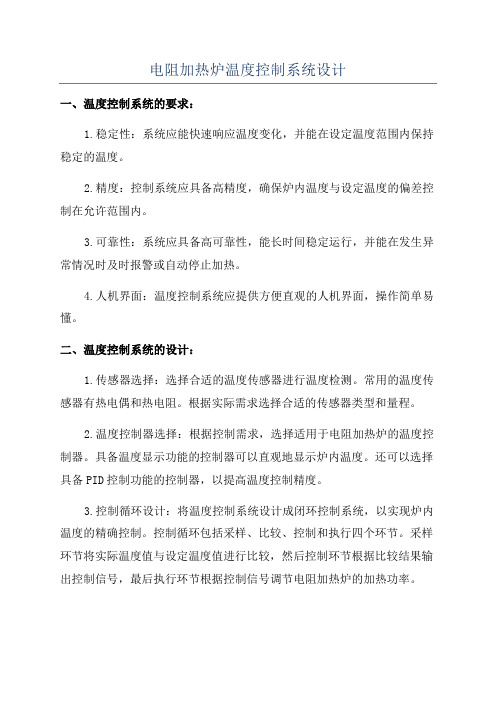
电阻加热炉温度控制系统设计一、温度控制系统的要求:1.稳定性:系统应能快速响应温度变化,并能在设定温度范围内保持稳定的温度。
2.精度:控制系统应具备高精度,确保炉内温度与设定温度的偏差控制在允许范围内。
3.可靠性:系统应具备高可靠性,能长时间稳定运行,并能在发生异常情况时及时报警或自动停止加热。
4.人机界面:温度控制系统应提供方便直观的人机界面,操作简单易懂。
二、温度控制系统的设计:1.传感器选择:选择合适的温度传感器进行温度检测。
常用的温度传感器有热电偶和热电阻。
根据实际需求选择合适的传感器类型和量程。
2.温度控制器选择:根据控制需求,选择适用于电阻加热炉的温度控制器。
具备温度显示功能的控制器可以直观地显示炉内温度。
还可以选择具备PID控制功能的控制器,以提高温度控制精度。
3.控制循环设计:将温度控制系统设计成闭环控制系统,以实现炉内温度的精确控制。
控制循环包括采样、比较、控制和执行四个环节。
采样环节将实际温度值与设定温度值进行比较,然后控制环节根据比较结果输出控制信号,最后执行环节根据控制信号调节电阻加热炉的加热功率。
4.温度传感器布置:将温度传感器布置在炉内合适位置,确保能够准确测量到炉内温度。
传感器的安装位置应避免热点和冷点,以避免温度不均匀。
5.控制参数调整:根据实际情况进行PID参数的调整。
通过实验或仿真等方法,逐步调整PID参数,使得系统能够快速响应温度变化、准确跟踪设定温度,并保持稳定的温度输出。
6.报警和保护设计:设计温度控制系统时,应考虑到电阻加热炉的过热或温度异常等情况,并设置相应的报警和保护功能。
当温度超过安全范围时,系统应及时报警,并自动停止加热。
7.人机界面设计:为了方便操作和监控,可以在温度控制系统上设置触摸屏或显示屏。
通过人机界面,操作人员可以方便地设定温度、监测炉内温度,并能够实时查看温度曲线和报警信息。
总之,电阻加热炉温度控制系统的设计需要考虑到温度控制精度、稳定性、可靠性和人机界面等方面的要求。
加热炉控温方法

加热炉是一种广泛应用于工业生产中的加热设备,其控温方法主要包括以下几种:
1. 手动控温:通过手动调节加热炉的加热功率或温度控制器的设定值来控制温度。
这种方法适用于简单的加热需求,但需要操作人员不断观察和调整温度,以确保加热效果和安全性。
2. 自动控温:使用温度控制器自动控制加热炉的温度。
温度控制器可以通过传感器感知加热炉内部的温度,并根据设定的温度值自动调整加热功率,以保持加热炉内部的温度稳定。
这种方法适用于需要精确控温的场合,可以提高加热效率和稳定性。
3. 比例积分微分(PID)控温:PID 控温是一种更为精确的自动控温方法,它可以根据加热炉内部的温度变化自动调整加热功率,以保持温度的稳定性。
PID 控温系统通常包括温度传感器、PID 控制器和执行器等组成部分,可以实现快速、准确的温度控制。
4. 分段控温:对于需要在不同温度范围内进行加热的场合,可以采用分段控温的方法。
将加热炉分成多个加热区域,并分别控制每个区域的温度,可以实现更精确的温度控制。
5. 远程控温:通过网络或其他通信方式实现远程控温。
操作人员可以在远程控制中心对加热炉的温度进行监测和控制,提高了加热炉的可操作性和管理效率。
电加热炉温度控制系统设计
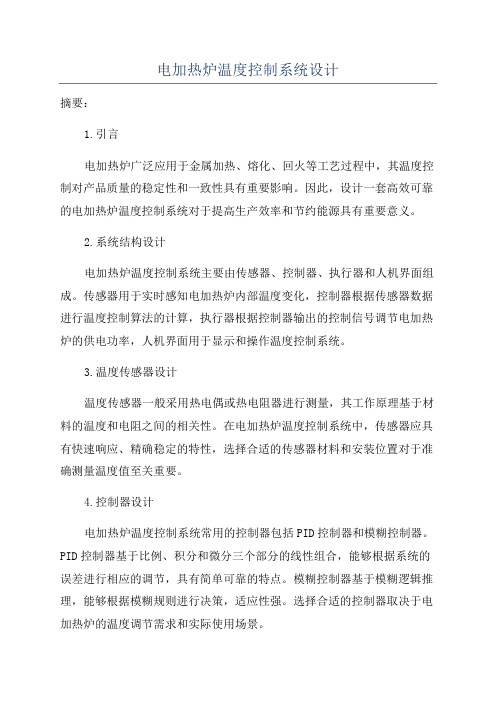
电加热炉温度控制系统设计摘要:1.引言电加热炉广泛应用于金属加热、熔化、回火等工艺过程中,其温度控制对产品质量的稳定性和一致性具有重要影响。
因此,设计一套高效可靠的电加热炉温度控制系统对于提高生产效率和节约能源具有重要意义。
2.系统结构设计电加热炉温度控制系统主要由传感器、控制器、执行器和人机界面组成。
传感器用于实时感知电加热炉内部温度变化,控制器根据传感器数据进行温度控制算法的计算,执行器根据控制器输出的控制信号调节电加热炉的供电功率,人机界面用于显示和操作温度控制系统。
3.温度传感器设计温度传感器一般采用热电偶或热电阻器进行测量,其工作原理基于材料的温度和电阻之间的相关性。
在电加热炉温度控制系统中,传感器应具有快速响应、精确稳定的特性,选择合适的传感器材料和安装位置对于准确测量温度值至关重要。
4.控制器设计电加热炉温度控制系统常用的控制器包括PID控制器和模糊控制器。
PID控制器基于比例、积分和微分三个部分的线性组合,能够根据系统的误差进行相应的调节,具有简单可靠的特点。
模糊控制器基于模糊逻辑推理,能够根据模糊规则进行决策,适应性强。
选择合适的控制器取决于电加热炉的温度调节需求和实际使用场景。
5.执行器设计电加热炉的供电功率调节通常通过调整炉内的电阻或使用可调电压/电流源实现。
执行器的设计应考虑到功率调节的精度和响应时间等因素,确保控制系统能够快速准确地调节电加热炉的供电功率,实现温度控制目标。
6.人机界面设计温度控制系统的人机界面一般包括温度显示、参数设置、报警显示和历史数据查询等功能。
界面设计应简洁明了,易于操作,提供必要的温度控制信息和报警提示,方便操作员进行实时监测和调节。
7.系统安全与优化温度控制系统应考虑到系统的安全性和优化性能。
安全性包括对系统故障的检测和处理,例如传感器异常、控制器故障等;优化性能包括对温度变化的快速响应和精确控制,例如减小温度波动、提高温度稳定性等。
8.结论本文基于电加热炉温度控制系统设计原理和方法进行了综合考虑,针对不同的温度控制要求给出了相应的解决方案。
- 1、下载文档前请自行甄别文档内容的完整性,平台不提供额外的编辑、内容补充、找答案等附加服务。
- 2、"仅部分预览"的文档,不可在线预览部分如存在完整性等问题,可反馈申请退款(可完整预览的文档不适用该条件!)。
- 3、如文档侵犯您的权益,请联系客服反馈,我们会尽快为您处理(人工客服工作时间:9:00-18:30)。
二、加热炉支路平衡控制
3、常压炉的工艺计算
3.2 常压炉出口温度偏差计算
3.2.1 该计算的目的:是得到常压炉Profit Controller的一个被控变量 。 3.2.2 该计算项目的原因:为最大限度的提高加 热炉的加热效率,抑制加热炉炉管内的结焦现象, 以保证加热炉长周期的稳定运行,需要实现加热 炉各支路出口温度偏差的最小化 。
二、加热炉支路平衡控制
3、常压炉的工艺计算
3.2 常压炉出口温度偏差计算
3.2.3 常压炉支路一、二路出口温度偏差(TPC0004)
计算公式如下: TPC 0004 .PV TI1156 A.PV TI1156 B.PV 其中: TPC0004.PV:常压炉支路一、二路出口温度偏差,单位 ℃。
二、加热炉支路平衡控制
3、常压炉的工艺计算
3.3 常压炉炉膛最高温度计算
3.3.3常压炉炉膛最高温度一(TZD0006A)
计算描述 :
TZD0006A.PV MAX (TI1712A.PV , TI1712 C.PV , TI1712E.PV )
计算输入 常压炉炉膛温度测量值一,TI1712A.PV,单位℃; 常压炉炉膛温度测量值三,TI1712C.PV,单位℃; 常压炉炉膛温度测量值五,TI1712E.PV,单位℃。 计算输出:常压炉炉膛最高温度一,TZD0006A.PV,单位℃。 备注:该计算项目在DCS中实现,运行周期为秒级。
一、加热炉常规温度控制
4、加热炉简单控制
加热炉的简单控制系统仅对出口温度控 制要求不十分严格;外来扰动缓慢而比较小, 且不频繁;炉膛容量较小,即滞后不大的加 热炉。最常见的加热炉简单是以出口温度为 被控变量、以燃料油(或气)为操纵变量组成 的简单控制系统。
一、加热炉常规温度控制
5、加热炉串级控制
其中:FPC0002.PV:常压炉一、二路与三、四路进料平均流量偏差, 单位t/h 。 该计算项目在DCS中实现,运行周期为秒级。
二、加热炉支路平衡控制
3、常压炉的工艺计算
3.1 常压炉进料流量偏差计算
3.1.5 常压炉三、四路进料流量偏差(FPC0003) 计算公式如下: FPC 0003 .PV FIC 1111C.SP FIC 1111 D.SP 计算输入 常压炉支路三流量控制回路的设定值,FIC1111C.SP,单位t/h; 常压炉支路四流量控制回路的设定值,FIC1111D.SP,单位t/h。 计算输出 常压炉三、四路进料偏差,FPC0003.PV ,单位t/h。 备注 该计算项目在DCS中实现,运行周期为秒级。
一、加热炉常规温度控制
3、加热炉扰动分析
加热炉最主要的控制指标是工艺介质的 出口温度。此温度是控制系统的被控变量, 而操纵变量是燃料油或燃料气的流量。对于 不少加热炉来说,温度控制指标要求相当严 格,如允许波动范围为±(1~2)℃。
一、加热炉常规温度控制
3、加热炉扰动分析
影响炉出口温度的扰动因素主要有: (1)进料方面:工艺介质的流量、温度、压力、 组分等; (2)燃料方面:燃料油(或燃料气)的流量、温度、 压力、成分(或热值)、燃料油的雾化情况等; (3)其他方面:空气质量情况(氧含量)、喷嘴 的阻力、烟囱抽力等。
一、加热炉常规温度控制
2、加热炉特点
2.1 传热过程复杂 加热炉是传热设备的一种,燃料的燃烧产生炽 热的火焰和高温的气流,热量主要通过辐射传给管 壁,然后由管壁传给工艺介质。工艺介质在辐射室 获得的热量约占热负荷的70%~80%,其余热量在 对流段获得。因此加热炉的传热过程比较复杂,想 从理论上获得其对象特性是困难的。
一、加热炉常规温度控制
3、加热炉扰动分析
在上述这些扰动因素中,有些是可控的, 有些是不可控的。为了保证炉出口温度稳定, 对扰动应采取必要的措施。如对可控干扰设 置控制回路,或与主要控制系统组成串级系 统;对可测干扰引入前馈补偿等。
一、加热炉常规温度控制
4、加热炉简单控制
加热炉的简单控制系统仅对出口温度控 制要求不十分严格;外来扰动缓慢而比较小, 且不频繁;炉膛容量较小,即滞后不大的加 热炉。
中国石化齐鲁分公司
加热炉的控制系统
胜利炼油厂仪表车间
吴 爱 泉
胜利炼油厂仪表车间
主 要 内 容
一、加热炉常规温度控制 二、加热炉的支路平衡控制
一、加热炉常规温度控制
一、加热炉常规温度控制
1、加热炉概述
在石油、化工生产过程中常见的加热炉主要是 管式加热炉。对于加热炉,工艺介质受热升温或同 时进行汽化,其温度的高低会直接影响后一工序的 操作工况和产品质量,同时当炉子温度过高时会使 物料在加热炉内分解,甚至造成结焦而烧坏炉管。 加热炉的平稳操作可以延长炉管的使用寿命,因此 必须严加控制加热炉出口温度。
二、加热炉支路平衡控制
3、常压炉的工艺计算
3.1 常压炉进料流量偏差计算
3.1.4 常压炉一、二路与三、四路进料平均流量偏差(FPC0002) 计算公式如下:
FPC0002 .PV ( FIC1111 A.SP FIC1111 B.SP) ( FIC1111 C.SP FIC1111 D.SP) 2
二、加热炉支路平衡控制
3、常压炉的工艺计算
3.1 常压炉进料流量偏差计算
3.1.3 常压炉一、二路进料流量偏差(FPC0001)
.PV FIC 1111 A.SP FIC 1111 B.SP 计算公式如下: FPC0001 其中: FPC0001.PV:常压炉一、二路进料偏差,单位t/h。 注:在进行计算前,应首先检验参与计算的变量状态是否 正确。(以下同样要求,不再重复)
二、加热炉支路平衡控制
3、常压炉的工艺计算
3.1 常压炉进料流量偏差计算 3.1.1 该计算的目的:是为常压炉的支路平衡控制提供一 个被控变量。 3.1.2 该计算项目的原因:在实现常压炉支路平衡控制方 案的过程中,应考虑到常压炉操作的合理性和安全性,其 中包括常压炉的各路分支流量偏差不要太大。实际操作中, 偏差的上限可由操作人员调整。常压炉有两个辐射室,每 个辐射室有两路进料。每个辐射室的进料偏差分别考虑, 同时也考虑两个辐射室进料的偏差。
加热炉的简单采用简单控制系统往往很难满足 工艺上对炉出口温度波动1~2℃的严格要求。因 为加热炉对象的传递滞后和测量滞后都较大,控制 不及时。为了改善控制品质,满足生产需要,石油 化工中的加热炉大多采用串级控制系统。由于扰动 作用及加热炉的型式不同,可以选择不同的副变量 组成不同的串级控制系统。
一、加热炉常规温度控制
二、加热炉支路平衡控制
4、常压炉系统Profit Controller设计
4.1 控制目标
4.1.1实现常压炉支路平衡控制。其中,常压炉支路平衡控 制包括: ★ 通过调整各支路的流量平衡加热强度 ★ 在调整各支路流量同时保持总流量恒定 ★ 实现各支路出口温度的平衡 4.1.2通过加热炉支路平衡控制,可以: ★ 改进加热炉热效率 ★ 降低加热炉炉管结焦的可能性 。
二、加热炉支路平衡控制
3、常压炉的工艺计算
3.2 常压炉出口温度偏差计算
3.2.4 常压炉支路三、四路出口温度偏差(TPC0005)
计算公式如下: 其中: TPC0005.PV:常压炉支路三、四路出口温度偏差,单位 ℃。
该计算项目在DCS中实现,运行周期为秒级。
TPC 0005 .PV TI1156 C.PV TI1156 D.PV
一、加热炉常规温度控制
2、加热炉特点
2.2 滞后 加热炉具有较大的时间常数和纯滞后时间。特别是炉 膛,它有很大的热容量,滞后更为显著。因此加热炉属于 一种多容量的被控对象,可以用一阶惯性环节加纯滞后来 近似加热炉的对象特性。其时间常数和纯滞后时间与炉膛 容量大小及工艺介质的停留时间有关,炉膛容量大,工艺 介质的停留时间,用一阶惯性环节加纯滞后来近似加热 炉的对象特性还是可行的。
二、加热炉支路平衡控制
3、常压炉的工艺计算
3.2 常压炉出口温度偏差计算 3.2.3 常压炉支路一、二路出口温度偏差(TPC0004) 计算公式如下: TPC 0004 .PV TI1156 A.PV TI1156 B.PV
计算输入 常压炉支路一出口温度,TI1156A.PV,单位℃; 常压炉支路二出口温度,TI1156B.PV,单位℃。 计算输出 常压炉支路一、二路出口温度偏差,TPC0004.PV ,单位℃。 该计算项目在DCS中实现,运行周期为秒级。
二、加热炉支路平衡控制
3、常压炉的工艺计算
3.1 常压炉进料流量偏差计算
3.1.3 常压炉一、二路进料流量偏差(FPC0001)
.PV FIC 1111 A.SP FIC 1111 B.SP 计算公式如下: FPC0001 计算输入 常压炉支路一流量控制回路的设定值,FIC1111A.SP,单位t/h; 常压炉支路二流量控制回路的设定值,FIC1111B.SP,单位t/h。 计算输出 常压炉一、二路进料偏差,FPC0001.PV ,单位t/h。 备注 该计算项目在DCS中实现,运行周期为秒级。
二、加热炉支路平衡控制
下面以炼油厂第三常减压装置为 例,简要介绍先进控制系统中有关 加热炉支路平衡控制的有关知识。
二、加热炉支路平衡控制
2、仪表位号的构建规则
X XX 0 0 XX .PV 仪表编号,起始编号为1,取值域为整数域; 数字“0”代表该位号将用于APC; 数字“0”尊重装置命名习惯,以“0”开始; 表征位号来历的字符,取值域如下: PJ:平均值; CZ:差值; BZ:比值; PC:偏差; JQ:加权平均; ZD:最大值; ZX:最小值; TC:推测值; JH:加和值。 表征位号类型的字符,取值域如下: F:流量; T:温度; P:压力; L:液位; Q:热量; A:产品性质或组成。
二、加热炉支路平衡控制
3、常压炉的工艺计算