晶圆激光划片切割应用范围【详解】
半导体封装领域的晶圆激光划片概述

洗。 冲洗 的作 用是 冷却 的 同时带走切 割 时生成 的粉 尘 , 自动砂轮 划 片工序 如 图 2I 全 | I 。
装 片 位 置 校 准 切 割
@ ⑦
图3 有 效 的 晶 粒 数 量 增 加
上
清沈 / 干燥
过 程 中应 用 。
关 键词 :半 导体 封装 ; 圆, 光划 片 晶 激
中图分 类 号 : N2 5 T 0
文 献标 识 码 : A
文章 编 号 : 0 44 0 (0 0 1—0 90 1 0 —5 72 1 )20 3 .5
La e a e c n n s m i o s r w f r di i g i e c ndu t r e c p ul t0 e d co n a s a i n f l i
半 导 体 元 器 件 的制 造 过 程 可 主 要 分 为 四 个 阶
段 : 料准 备 、 材 晶体 生 长 和 晶 圆准 备 、 圆制 造 、 晶 封
电测 完 毕 的 晶 圆片 在 贴 膜 后 ,通 过 切 割 的方
式 将 晶 圆 分 离 为 晶粒 , 以便进 行 封 装 工 序 。 常 的 通 做 法 是 在 晶 圆上 划 切 出沟 槽 ,然 后 进 行 裂 片 再 将 其 分 离 。 为 半 导 体 封装 的第 一 道 工 序 , 片 质 量 作 划 的好 坏 直 接 影 响 到 整 体 的封 装 质 量 。而 晶 圆 在 划 片过 程 中 容 易 发 生 崩 角 、 层 与 剥 离 等 缺 陷( 图 分 如 1 , 划 片 工 艺 带 来 了挑 战 , 使 划 片 工 艺不 断 向 )给 促 前发展 , 目前 , 片 的方 式 主 要 有 砂 轮划 片和 激 光 划
晶圆划片工艺分析
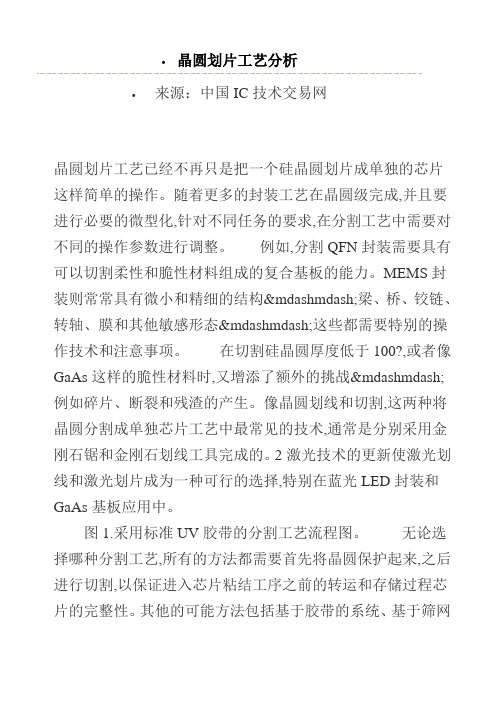
•晶圆划片工艺分析•来源:中国IC技术交易网晶圆划片工艺已经不再只是把一个硅晶圆划片成单独的芯片这样简单的操作。
随着更多的封装工艺在晶圆级完成,并且要进行必要的微型化,针对不同任务的要求,在分割工艺中需要对不同的操作参数进行调整。
例如,分割QFN封装需要具有可以切割柔性和脆性材料组成的复合基板的能力。
MEMS封装则常常具有微小和精细的结构&mdashmdash;梁、桥、铰链、转轴、膜和其他敏感形态&mdashmdash;这些都需要特别的操作技术和注意事项。
在切割硅晶圆厚度低于100?,或者像GaAs这样的脆性材料时,又增添了额外的挑战&mdashmdash;例如碎片、断裂和残渣的产生。
像晶圆划线和切割,这两种将晶圆分割成单独芯片工艺中最常见的技术,通常是分别采用金刚石锯和金刚石划线工具完成的。
2 激光技术的更新使激光划线和激光划片成为一种可行的选择,特别在蓝光LED封装和GaAs基板应用中。
图1.采用标准UV胶带的分割工艺流程图。
无论选择哪种分割工艺,所有的方法都需要首先将晶圆保护起来,之后进行切割,以保证进入芯片粘结工序之前的转运和存储过程芯片的完整性。
其他的可能方法包括基于胶带的系统、基于筛网的系统以及采用其他粘结剂的无胶带系统。
工艺标准的切割工艺中首先是将减薄的晶圆放置好,使其元件面朝下,放在固定于钢圈的释放胶带上。
这样的结构在切割过程中可以保证晶圆,并且将芯片和封装继续保持在对齐的位置,方便向后续工艺的转运。
工艺的局限来自于减薄晶圆的应用,在存储之后很难从胶带上取下晶圆,采用激光的话容易切到胶带,同时在切割过程中冷却水的冲击也会对芯片造成损伤。
基于胶带的分割图2.可处理200或300 mm晶圆的UV固化单元可以放置在桌子上,采用365 nm波长的激光每个小时可以处理50片晶圆。
采用基于胶带的系统时,需要重点考虑置放系统,以及所采用的条带类型是不是适合要切割的材料。
用热激光切割技术切割晶圆

用热激光切割技术切割 晶圆
前言 建立在众所周知的原理基础上的热激光切割技术 ( e a l e s a t n T S t r la r e ri , L )用于切割 h m s p ao 脆性材料。应用范围包括切割显示器玻璃 ( 包括层状玻璃 ) 、浮法玻璃生产线上的玻璃边缘、氧 化铝陶瓷等。 与其他的激光技术 比较, T S 用 L 取代机械法切割晶圆有诸多优点。 本文论述 了T S L 在切割半导体硅片领域的应用。 热激光切割是切割脆性材料 的简单技术,是利用热感应机械应力的切割工艺。工艺过程分 两步进行。开始时,需要有一个非常小的划痕 ( 缺陷) ,划痕可能是前一步的工艺过程造成的, 例如碾磨或线状锯切割; 在大 多数情况下,可以用工具如金刚石或造痕激光器来制造这个划痕 。 这个起始的划痕给 了切割过程一个明确的起始点。否则,切割可能从离缺陷最近的地方开始。 在切割过程中,被切割材料被带有能量子的激光加热,被加热 的材料膨胀并产生放射状的 压力,在受热带周围感应发生切 向拉伸应力 ( S ) T 。 I 激光聚焦处随之被冷却,材料因冷却而收缩。 在冷却区域感应产生额外的拉力 ( F ) 在 T Ⅱ。 两种应力的覆盖区——只有在这个区域一 材料开始裂开。从最初的划痕开始,至此完成了材 料的切割过程 。被切割晶圆具有质量优异的切割边缘 。 对于晶体材料 ( 例如硅片 )来说,分离是完全的。局部最大的拉伸应力位于受热焦点和冷 却点之间的轴上,因此力和强度的中心也可 自定位 。如果开裂速度比受热焦点和冷却点汇聚进 行得快 ,开裂 就会 向零压 力处 蔓延并 导致延 迟 。 尽 管 T S的进 行几 乎与切 割边 缘 的裂 纹前沿 晶面 的排列 无 关 ,但通 常 的机 械划 痕和切割 技 L 术也如此。更多的竖 向的裂纹前沿与晶面排列的关系更小且可得到最好的结果,而获得竖向的 裂纹前沿的关键是利用激光波长 ,激光可被吸收到裂纹深处。 工艺条件/ 特点 下面 对一 些影 响因素和 工艺 条件进 行讨论 。 T S工艺需要被切割的材料内部具有大的热膨胀梯度。由于热能的切割作用主要集中在晶 L 圆的表面,高能量的激光不可能补偿小的热值。基于这个事实,熔化硅片的切割在 以前是不可 能实现的。 该项技术是建立在材料内部产生热感应机械应力的基础上的。当晶圆的厚度很薄时,分别 进行的加热和冷却的部分非常小,难 以产生断裂力。到 目前为止,试验成功的切割晶圆的最薄 的厚度为 5 g 0 m,切割厚度的下 限尚需通过进一步的试验确定。 感应力和材料 内部的固有力相结合而发生切割过程。由于这个原因,切割多晶的 ( 光伏的) 晶圆更为困难,但存在切割的可能性 。对于较大面积的晶圆,切割线会与晶圆的边缘以小角度 汇合 ,这 时需要特 别措 旄来 稳定切 割过程 。 在激光的应用 中,吸收值和反射值通常是重要的指标 。为了达到硅材料的表面和内部的均 衡受热,激光的波长在近红外区为最优 ( 00 18n 。考虑由功能层,例如表面钝化层导致 13 ̄ 00m)
晶圆工艺的切割方法
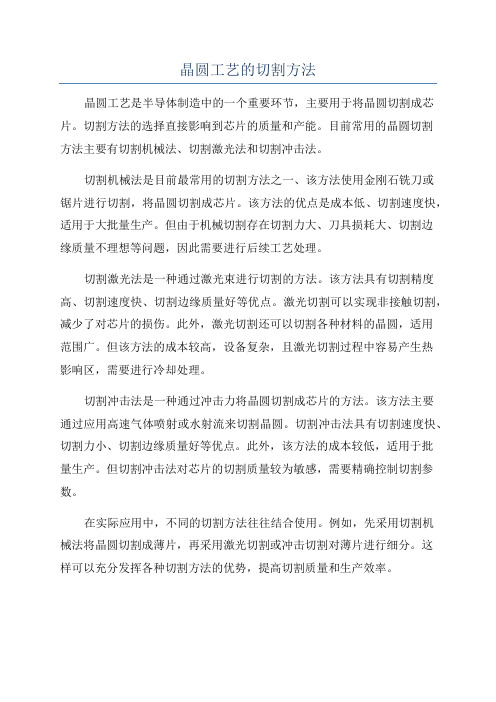
晶圆工艺的切割方法晶圆工艺是半导体制造中的一个重要环节,主要用于将晶圆切割成芯片。
切割方法的选择直接影响到芯片的质量和产能。
目前常用的晶圆切割方法主要有切割机械法、切割激光法和切割冲击法。
切割机械法是目前最常用的切割方法之一、该方法使用金刚石铣刀或锯片进行切割,将晶圆切割成芯片。
该方法的优点是成本低、切割速度快,适用于大批量生产。
但由于机械切割存在切割力大、刀具损耗大、切割边缘质量不理想等问题,因此需要进行后续工艺处理。
切割激光法是一种通过激光束进行切割的方法。
该方法具有切割精度高、切割速度快、切割边缘质量好等优点。
激光切割可以实现非接触切割,减少了对芯片的损伤。
此外,激光切割还可以切割各种材料的晶圆,适用范围广。
但该方法的成本较高,设备复杂,且激光切割过程中容易产生热影响区,需要进行冷却处理。
切割冲击法是一种通过冲击力将晶圆切割成芯片的方法。
该方法主要通过应用高速气体喷射或水射流来切割晶圆。
切割冲击法具有切割速度快、切割力小、切割边缘质量好等优点。
此外,该方法的成本较低,适用于批量生产。
但切割冲击法对芯片的切割质量较为敏感,需要精确控制切割参数。
在实际应用中,不同的切割方法往往结合使用。
例如,先采用切割机械法将晶圆切割成薄片,再采用激光切割或冲击切割对薄片进行细分。
这样可以充分发挥各种切割方法的优势,提高切割质量和生产效率。
总之,晶圆工艺的切割方法是半导体制造中的重要环节,不同的切割方法各有优劣。
通过合理选择切割方法,并结合其他工艺步骤,可以实现高质量和高产能的芯片生产。
晶圆划片刀分类

晶圆划片刀分类(原创实用版)目录一、晶圆划片刀简介二、晶圆划片刀的分类1.机械式晶圆划片刀2.气浮式晶圆划片刀3.液压式晶圆划片刀4.电磁式晶圆划片刀三、各类晶圆划片刀的特点及应用1.机械式晶圆划片刀的特点及应用2.气浮式晶圆划片刀的特点及应用3.液压式晶圆划片刀的特点及应用4.电磁式晶圆划片刀的特点及应用四、晶圆划片刀的发展趋势正文一、晶圆划片刀简介晶圆划片刀是一种用于切割晶圆的精密工具,广泛应用于半导体制造、光电子器件制造等领域。
晶圆划片刀的切割效果直接影响到后续工序的进行,因此其性能和精度至关重要。
二、晶圆划片刀的分类1.机械式晶圆划片刀机械式晶圆划片刀主要依靠机械传动来进行切割,其结构简单,操作方便,但切割精度相对较低,适用于对精度要求不高的场合。
2.气浮式晶圆划片刀气浮式晶圆划片刀在刀片与晶圆之间形成气浮层,以减少摩擦力,提高切割精度。
其切割精度较高,适用于对精度要求较高的场合。
3.液压式晶圆划片刀液压式晶圆划片刀通过液压传动来实现刀片的上下运动,切割力度大,切割速度快,适用于大规模生产线。
4.电磁式晶圆划片刀电磁式晶圆划片刀通过电磁力吸附和释放晶圆,实现切割。
其切割精度高,且具有高效率、节能等优点。
三、各类晶圆划片刀的特点及应用1.机械式晶圆划片刀的特点及应用机械式晶圆划片刀的特点是结构简单,操作方便,适用于对精度要求不高的场合,如实验室、中小型企业等。
2.气浮式晶圆划片刀的特点及应用气浮式晶圆划片刀的特点是切割精度高,适用于对精度要求较高的场合,如高端半导体制造、光电子器件制造等。
3.液压式晶圆划片刀的特点及应用液压式晶圆划片刀的特点是切割力度大,切割速度快,适用于大规模生产线,如半导体芯片制造、太阳能电池制造等。
4.电磁式晶圆划片刀的特点及应用电磁式晶圆划片刀的特点是切割精度高,具有高效率、节能等优点,适用于对切割精度和效率要求高的场合,如高端半导体制造、光电子器件制造等。
四、晶圆划片刀的发展趋势随着科技的不断发展,晶圆划片刀在精度、效率、智能化等方面将不断得到提升。
激光技术在半导体行业的应用

激光技术在半导体行业的应用一、激光技术在晶片/芯片加工领域的应用1、在划片方面的应用划片工艺隶属于晶圆加工的封装部分,它不仅仅是芯片封装的关键工艺之一,而是从圆片级的加工(即加工工艺针对整片晶圆,晶圆整片被同时加工)过渡为芯片级加工(即加工工艺针对单个芯片)的地标性工序。
从功能上来看,划片工艺通过切割圆片上预留的切割划道(street),将众多的芯片相互分离开,为后续正式的芯片封装做好道准备。
目前业界讨论最多的激光划片技术主要有几种,其主要特征都是由激光直接作用于晶圆切割道的表面,以激光的能量使被作用表面的物质脱离,到达去除和切割的目的。
但是这种工艺在工作过程中会产生巨大的能量,并导致对器件本身的热损伤,甚至会产生热崩边(Chipping),被剥离物的沉积(Deposition)等至今难以有效解决的问题。
与很多先行技术不同,传统旋转砂轮式划片机的东京精细公司和日本的激光器生产商滨松光学联合推出了突破传统理念的全新概念的激光划片机MAHOH。
其工作原理摒弃了传统的表面直接作用、直接去除的做法;而采取作用于硅基底内的硅晶体,破坏其单晶构造的技术,在硅基底内产生易分离的变形层,然后通过后续的崩片工艺使芯片间相互分离。
从而到达了无应力、无崩边、无热损伤、无污染、无水化的切割效果。
2、在晶片割圆方面的应用割圆工艺是晶体加工过程中的一个重要组成部分。
早期,该技术主要用于水平砷化镓晶片的整形,将水平砷化镓单晶片称为圆片。
随着晶体加工各个工序的逐步加工,在各工序将会出现各种类型的废片,将这些废片加工成小直径的晶片,然后再经过一些晶片加工工序的加工,使其变成抛光片。
传统的割圆加工方法有立刀割圆法、掏圆法、喷砂法等。
这些方法在加工过程中对晶片造成的损伤较大,出片量相对较少。
随着激光加工技术的发展,一些厂家对激光加工技术引入到割圆工序,再加上较为成熟的软件控制,可以在一个晶片上加工出更多的小直径晶片。
二、激光打标技术激光打标是一种非接触、无污染、无磨损的新标记工艺。
LED蓝宝石晶圆激光划片机
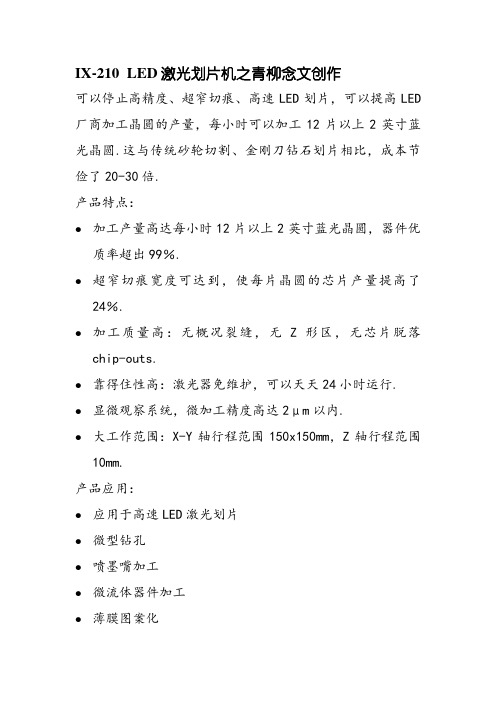
IX-210 LED激光划片机之青柳念文创作
可以停止高精度、超窄切痕、高速LED划片,可以提高LED 厂商加工晶圆的产量,每小时可以加工12片以上2英寸蓝光晶圆.这与传统砂轮切割、金刚刀钻石划片相比,成本节俭了20-30倍.
产品特点:
●加工产量高达每小时12片以上2英寸蓝光晶圆,器件优
质率超出99%.
●超窄切痕宽度可达到,使每片晶圆的芯片产量提高了
24%.
●加工质量高:无概况裂缝,无Z形区,无芯片脱落
chip-outs.
●靠得住性高:激光器免维护,可以天天24小时运行.
●显微观察系统,微加工精度高达2μm以内.
●大工作范围:X-Y轴行程范围150x150mm,Z轴行程范围
10mm.
产品应用:
●应用于高速LED激光划片
●微型钻孔
●喷墨嘴加工
●微流体器件加工
●薄膜图案化
MEMS微机械加工
IX-260 LED激光剥离机
采取紫外激光器,通过光剥离(Laser Liftoff)的工艺,对资料停止紧密加工.●采取JPSA专利技术,加工精度可达1~100μm●采取248nm或157nm紫外准分子激光器,输出平均矩形光斑●持续、高速重复的激光脉冲,适合于切削微小、可节制的资料量●应用于大尺寸、高亮度、高功率LED生产,可有效提高LED出光效率,也可用于其他高精度掩模加工。
晶圆激光切割工艺技术
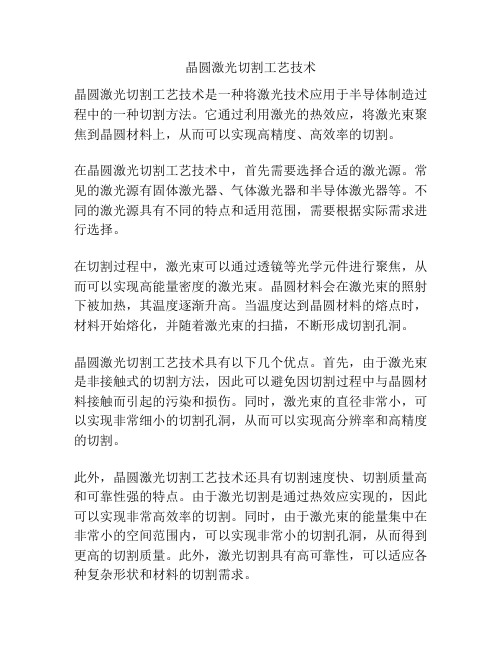
晶圆激光切割工艺技术晶圆激光切割工艺技术是一种将激光技术应用于半导体制造过程中的一种切割方法。
它通过利用激光的热效应,将激光束聚焦到晶圆材料上,从而可以实现高精度、高效率的切割。
在晶圆激光切割工艺技术中,首先需要选择合适的激光源。
常见的激光源有固体激光器、气体激光器和半导体激光器等。
不同的激光源具有不同的特点和适用范围,需要根据实际需求进行选择。
在切割过程中,激光束可以通过透镜等光学元件进行聚焦,从而可以实现高能量密度的激光束。
晶圆材料会在激光束的照射下被加热,其温度逐渐升高。
当温度达到晶圆材料的熔点时,材料开始熔化,并随着激光束的扫描,不断形成切割孔洞。
晶圆激光切割工艺技术具有以下几个优点。
首先,由于激光束是非接触式的切割方法,因此可以避免因切割过程中与晶圆材料接触而引起的污染和损伤。
同时,激光束的直径非常小,可以实现非常细小的切割孔洞,从而可以实现高分辨率和高精度的切割。
此外,晶圆激光切割工艺技术还具有切割速度快、切割质量高和可靠性强的特点。
由于激光切割是通过热效应实现的,因此可以实现非常高效率的切割。
同时,由于激光束的能量集中在非常小的空间范围内,可以实现非常小的切割孔洞,从而得到更高的切割质量。
此外,激光切割具有高可靠性,可以适应各种复杂形状和材料的切割需求。
然而,晶圆激光切割工艺技术也存在一些挑战和难点。
首先,由于激光切割需要对晶圆材料进行加热,因此可能会引起晶圆材料的热应力,从而影响材料的性能和可靠性。
此外,激光切割过程中会产生大量的热量和烟尘,需要进行有效的散热和烟尘处理。
同时,晶圆激光切割工艺技术的设备和操作都需要非常高的技术要求,对操作人员的技术水平和经验要求非常高。
总的来说,晶圆激光切割工艺技术是一种高效、高精度的切割方法,广泛应用于半导体制造领域。
随着激光技术的不断发展和创新,相信晶圆激光切割工艺技术将会越来越成熟和完善,为半导体制造业的发展提供强有力的支持。
- 1、下载文档前请自行甄别文档内容的完整性,平台不提供额外的编辑、内容补充、找答案等附加服务。
- 2、"仅部分预览"的文档,不可在线预览部分如存在完整性等问题,可反馈申请退款(可完整预览的文档不适用该条件!)。
- 3、如文档侵犯您的权益,请联系客服反馈,我们会尽快为您处理(人工客服工作时间:9:00-18:30)。
晶圆激光划片切割应用
内容来源网络,由“深圳机械展(11万㎡,1100多家展商,超10万观众)”收集整理!
更多cnc加工中心、车铣磨钻床、线切割、数控刀具工具、工业机器人、非标自动化、数字化无人工厂、精密测量、3D打印、激光切割、钣金冲压折弯、精密零件加工等展示,就在深圳机械展.
圆划片是半导体芯片制造工艺流程中的一道必不可少的工序,在晶圆制造中属后道工序。
将做好芯片的整片晶圆按芯片大小分割成单一的芯片(晶粒),称之为晶圆划片。
在晶圆划片行业,主要有两种切割工艺,一个是传统的刀片切割,另一个新型的现代工艺激光划片。
下面,将通过对比两种切割工艺,证明激光划片的优势。
刀片划片
最早的晶圆是用划片系统进行划片(切割)的,现在这种方法仍然占据了世界芯片切割市场的较大份额,特别是在非集成电路晶圆划片领域。
金刚石锯片(砂轮)划片方法是目前常见的晶圆划片方法。
原理:当工作物是属于硬、脆的材质,钻石颗粒会以撞击(Fracturing)的方式,将工作物敲碎,再利用刀口将粉末移除。
存在的问题
●刀片划片直接作用于晶圆表面,易产生裂纹,碎片和分层;
●划片线宽较大,宽切槽一般有50-100um,晶圆利用率低;
●刀具易磨损,需要频繁更换刀具,另外还需要大量去离子水,增加了切割成本;
●化学法,蚀刻速度慢,对环境污染大,切割后的硅粉水难处理。
激光划片
由于激光在聚焦上的优点, 聚焦点可小到亚微米数量级, 从而对晶圆的微处理更具优势, 可以进行小部件的加工。
即使在不高的脉冲能量水平下, 也能得到较高的能量密度, 有效地进行材料加工。
激光划片属于非接触式加工,可以避免出现芯片破碎和其它损坏现象。
加工优势
●激光划片窄切槽(10-30um),晶圆利用率高;
●激光是非接触加工,不会产生机械应力,适合薄晶圆作业,具有更好的兼容性和通用性;
●激光划片速度快,高达300mm/s;
●激光自动化程度高,可以切割一些较复杂的晶圆芯片;
●激光划片不需要去离子水,不存在刀具磨损问题,并可连续24小时作业。
下图所示为使用皮秒超精细激光切割后的状况示意图,由图中可以看出,相对于传统的机械切割方式,使用激光切割边缘几乎无任何崩边等问题,亦不存在任何残渣等影响产品后续效果的物质,由此产品的良品率得到大幅的提升,同时激光切割的速度可以达到300mm/s,相对传统的几十mm/s的速度,产品的产能得到大幅的提升,机器的购买数量减少,相应的厂房占地、人员管理等都相应大幅减少,为企业的生存及竞争力提供了强有力的保障。
由最下方图示可以看出,由于皮秒激光超精细微加工的切割缝宽做到了10微米级别的程度,单片晶圆的晶粒数得到了大幅的增长,为企业降低成本、提高产能、提高利润提供了非常强大的技术应用基础;
内容来源网络,由“深圳机械展(11万㎡,1100多家展商,超10万观众)”收集整理!
更多cnc加工中心、车铣磨钻床、线切割、数控刀具工具、工业机器人、非标自动化、数字化无人工厂、精密测量、3D打印、激光切割、钣金冲压折弯、精密零件加工等展示,就在深圳机械展.。