全钢子午胎成型基本缺陷及处理措施
全钢载重子午胎压延帘布常见缺陷原因分析及对策

全钢载重子午胎压延帘布常见缺陷原因分析及对策全钢载重子午胎压延帘布常见缺陷原因分析及对策子午线轮胎生产工艺复杂,半成品部件精度要求高,钢丝帘布是子午线轮胎重要的骨架材料.其尺寸精度与轮胎成本密切相关.由于笔者所在工厂全钢压延设备自动化程度较低,没有帘布厚度,胶片厚度检测以及自动调节装置.在很大程度上是靠操作人员手动测量及调整帘布厚度,胶片厚度.存在测量误差和调整误差,大大降低了操作精度,直接影响帘布品质.在生产过程中,帘布常见的缺陷有整幅钢丝稀线,局部稀线,边部稀线,整幅脱层,边部脱层,掉皮,帘布喷霜等,由于这些因素的存在直接影响帘布品质,导致压延,裁断耗损量及X光废品率的增加,降低了轮胎的高速,耐久性能,影响轮胎的使用寿命.本文针对压延生产过程中常出现的一些帘布缺陷进行分析,并针对不同缺陷制定相应的解决措施,重在提高帘布质量,降低耗损,提升轮胎品质.一,帘布整幅钢丝稀线帘布整幅钢丝出现排列不均,布面凹凸不平,帘布切面钢丝间距大于正常钢丝间距,稀开距离为1根钢丝.1.原因分析(1)压延机2,3辊速比不合理,2辊速度过快,导致上胶片擦人钢丝间的力过大,将相邻钢丝向两侧挤,造成钢丝间距大于正常钢丝间距:(2)压延辊温度与供胶温度偏低,胶料未充分渗透到钢丝帘线间,从而导致钢丝帘线压延密度不均: (3)单丝张力不均匀或锭子架掉压,钢丝进入辊隙被胶料挤开,造成帘布整幅稀线;(4)胶料门尼过高,致使胶料渗透性差,造成帘布整幅稀线:(5)整经辊,压力辊沟槽与钢丝帘线直径不匹配,压延时钢丝帘线跳动比较严重,造成钢丝帘线嗣赵金龙陆林压延密度不均:(6)压力辊与主机辊筒间隙过大,钢丝未能嵌入下胶片中,钢丝帘线被上胶片挤开,造成帘布整幅稀线:(7)整经辊,压力辊支架液压站掉压.钢丝进入辊隙被胶料挤开,造成帘布整幅稀线:(8)上胶片偏厚,下胶片偏薄,钢丝嵌人下胶片深度不够,上胶片余胶偏多,将钢丝帘线挤开,造成钢丝间距大于正常钢丝间距.2.解决措施(1)控制压延机2,3辊速比,不易过大,2,3辊速比设置为1.02—1.04:1:(2)严格控制压延辊温和供胶温度,可以根据不同季节制定标准,夏季为75-+5cI=,冬季为85+5℃, 供胶温度为90+5℃,保证压延时胶料具有良好的流动性,使胶料能够充分渗透到钢丝帘线间;(3)定期对单丝张力进行标定以及对锭子架风(4)严禁使用门尼粘度不合格的胶料,高门尼胶料与低门尼胶料搭配使用:(5)整经辊,压力辊标识要清楚,不同钢丝帘线要使用相应的整经辊,压力辊;规范整经辊,压力辊保养周期,磨损严重的不能投入使用:(6)定期校验压力辊跳动量.生产前检测压力辊与主机辊间隙.确定压力辊与主机辊间隙左右一致:(7)生产前检点整经辊,压力辊支架液压站压力,确定没有掉压及左右压力不一致情况:(8)压延时对上下胶片厚度进行检点,控制好上胶片余胶量,余胶量控制在0~3mm范围内. 二,局部稀线在帘布表面局部出现小面积稀线,位置不定,而且呈周期出现.1.原因分析(1)划气泡装置失灵,上下胶片与辊筒间的气泡将钢丝帘线局部挤开,造成钢丝帘线局部出现稀线:(2)辊筒表面温度不一致,局部温度偏低,会降低该位置胶料流动性,从而产生局部稀线;(3)辊筒表面有硬伤,凹进去的部分加大了此处胶料体积,在压延过程中多余的胶料会把钢丝帘线挤开,造成钢丝帘线局部稀线;(4)单根钢丝张力消失,压延时会产生局部稀线:(5)掉胶造成帘布局部稀线.(1)定期检查气泡刀刀片是否锋利,如果磨顿要及时更换新刀.压延时调整气泡刀风压,保证气泡刀划破胶片,排净上下胶片与辊筒间气体; (2)定期测量压延辊筒表面各位置温度,对于温度变差大的位置要及时排查;(3)保证金属探测设备的灵敏性,坚决不能让金属杂质进人辊隙,伤害辊筒表面精度.对有硬伤的压延辊筒,采取磨削的方式对辊筒表面进行研磨;(4)定期对单丝张力进行标定,对于损害的锭子架一定要作好标记,在压延过程中可将此根钢丝剪断或更换锭子位置等方法进行处理;(5)在上供胶皮带下面加托盘,防止运输带上面胶料落到钢丝帘线上.三,边部稀线片左右厚度一致:(2)每次开班前用塞尺测量辊筒间隙,保证辊筒左右间隙一致.在生产过程中单侧调整辊距时, 要注意帘布边部是否有稀线情况,并且测量帘布调整后厚度:(3)生产前检点整径辊,压力辊支架液压站压力.确定没有掉压及左右压力不一致情况.定期标定压力辊与主机辊间隙,如有异常立即调整.四,整幅脱层帘布表面大面积麻面,不平,起鼓,取帘布断面,胶料没有渗透到钢丝帘线缝隙中,钢丝帘线在帘布里面发生窜动.1.原因分析(1)上胶片偏薄,在辊隙间没有余胶,胶料渗透能力下降,导致帘布覆胶不实,而产生帘布大面积脱层:(2)主机辊筒间隙太大,上下胶片压力降低,胶料渗透能力下降,导致帘布覆胶不实,而产生帘布大面积脱层:(3)胶料中含有过量的水,油等物质,降低胶料与钢丝附着力,造成帘布大面积脱层.2.解决措施(1)压延时对上下胶片厚度进行检点,同时控制上胶片余胶量在0~3ram范围内;(2)压延时注意帘布表面,如果发生帘布脱层时,可以在保证帘布厚度的情况下,减小辊距,加大辊隙间胶料压力,使帘布覆胶更密实;(3)开班前认真检点胶料,严禁使用不合格胶压延帘布边部出现宽20~30mm范围内连续稀料. 线.1.原因分析(1)上胶片,下胶片左右厚度不一致,在辊筒间隙一定的情况下.胶片厚的一侧上胶片对边部钢丝帘线压力偏大,造成帘布边部稀线;(2)主机辊筒左右间隙不一致,间隙小的一侧压力偏大,把钢丝帘线挤开,造成帘布边稀线; (3)压力辊与主机辊左右间隙不一致,间隙大的一侧钢丝帘线未嵌入下胶片中,进入辊隙时被上胶片挤开.造成帘布边部稀线.2.解决对策(1)压延时对上下胶片厚度进行检点,保证胶五,边部脱层帘布单侧边部出现宽lOmm左右小面积脱层. 1.原因分析(1)上胶片,下胶片左右厚度不一致,在辊筒间隙一定的情况下,胶片薄的一侧上胶片对边部钢丝帘线压力偏小,造成帘布边部连续脱层;(2)主机辊筒左右间隙不一致,在上下胶片厚度一定的情况下,辊筒间隙大的一侧压力偏小,胶料渗透性能下降,造成帘布边部连续脱层;(3)辊筒快速打开液压站泄漏掉压,造成2,3辊辊隙周期变化,当打开的时候,辊距变大,造成帘布一侧胶料压力变小,胶料渗透性能下降,造成帘布边部周期性脱层.2.解决措施(1)压延时对上下胶片厚度进行检点,保证胶片左右厚度一致:(2)每次开班前用塞尺测量辊筒间隙,保证辊筒左右间隙一致.在生产过程中单侧调整辊距时, 要注意帘布边部是否有脱层情况.并且测量帘布调整后厚度:(3)定期检测快速打开液压站压力,如发现异常立即调整.六,掉皮帘布局部露钢丝,面积大小不等.1.原因分析(1)人工扎气泡时,破坏胶片面积偏大,造成帘布表面局部漏钢丝帘线且连续:(2)上下供胶出现断胶情况,降低辊筒上胶容量,造成帘布表面局部漏钢丝帘线且连续.2.解决措施(1)人工扎气泡工具头部作成锋利的刺头,在扎气泡过程中不要划胶片表面,用尖部均匀刺扎胶片气泡位置:(2)合理确定胶片宽度,保证辊筒上胶容量,出现断胶时,放慢生产速度,人工从开炼机取料,补充辊筒上胶容量.七,帘布喷霜帘布表面发暗或发白.帘布粘性下降或丧失粘性,导致成型贴合过程中粘合性不好,部件间有气泡产生.1.原因分析(1)胶料门尼偏高,混炼过程中不易压合,导致压合时间过长,致使胶料内部积聚大量的热量,使胶料中配合剂局部过量析出:(2)压延速度过快,致使帘布表面温度过高,导致胶料中配合剂局部过量析出:(3)压延帘布在现场停放时间超期;(4)压延温控系统故障,如水循环通道阻塞,使辊筒温度过高:(5)压延帘布时,热炼机,供胶机积胶过多,胶料停留时间过长.导致胶料喷霜;(6)压延帘布遇急冷产生喷霜;(7)帘布表面受摩擦,致使帘布粘性下降.2.解决措施(1)胶料的门尼粘度尽量控制在77+7之间,同时偏上公差胶料最好与偏下公差胶料搭配使用: (2)针对高门尼的胶料要控制压延速度,避免因为速度过快,温度过高,冷却不好导致喷霜; (3)成型严格按照压延帘布的先后顺序裁断,使用,做好计划调度,防止超期料的出现;(4)设备在停车检修期间,针对压延工序温控系统重点检修,保障各水循环通道畅通:(5)压延帘布时,热炼机,供胶机积胶不能过多,防止胶料混炼时间过长,温度过高导致喷霜; (6)第一个与帘布接触的冷却辊温度不能太低,由上到下要有一个温度梯度.即由高到低的一个冷却过程:(7)帘布在压延联动线上避免与非转动辊有硬接触.八,结论通过分析全钢载重子午线轮胎压延帘布常见的稀线,脱层,掉皮,帘布喷霜等缺陷的产生原因, 制定了合理的解决措施,有效提高了压延帘布品质,降低帘布耗损和成品轮胎稀线的发生机率,同时大大提升了成品轮胎的高速性能,耐久性能.为企业带来了经济效益和社会效益.口。
轮胎行业质量培训 子午胎质量缺陷及原因分析 轮胎缺陷分析

胎圈部位
★子口部位露线
1、缺陷描述: 轮胎子口部位一侧或两侧有胎体帘线露
出的现象。 2、缺陷原因及纠正办法: 1)缺胶缺料
—检查胎侧宽度和定位(可能非常窄 或定位出差错)
2)帘线伸张过大 —检查帘线压延张力 —检查机头宽度,必要时增加。 3)生胎在模型中定位出差错 —检查装胎器定中情况 4)硫化胶囊膨大 —检查硫化胶囊情况如必要加以更换
漏 —检查中心机构有无蒸汽泄漏 4)胎体帘布不正常 —检查帘布中胶料渗入帘线的情况,厚度
重量 —把帘布裁断时或压延时不正常部分剔出
报废 5)在二段时定型压力过大 —检查二段成型机的定型压力
13
胎里部位
★胶囊打折
1、缺陷描述: 因硫化胶囊打折(局部伸张不好)轮胎胎里出现下述
夹挤痕迹:1)橡胶;2)胶与胎体帘线。 2、缺陷原因及纠正办法: 1)胶囊规格出错 —检查硫化胶囊尺寸是否符合规定(可能硫化胶囊太
6
胎圈部位
★子口撕裂
1、缺陷描述: 轮胎子口部位在下列部位出
现撕裂现象: 1)橡胶部分; 2)橡胶和帘布 2、缺陷原因及纠正办法: 1)硫化机动作不正常 —检查卸胎顺序 —检查抽真空效果 2)修边时受到损伤 —检查修边工具及工艺过程
7
胎圈部位
★子口变形
1、缺陷描述: 轮胎子口部位出现径向及侧向周长
·一般必须提高前10个周期的预定型和 定型压力
5)生胎喷涂欠量 —送生胎去重新喷涂
24
胎里部位
★胎里肩部周向裂口
1、缺陷描述: 轮胎胎里肩部周向裂口 。 2、缺陷原因及纠正办法: 1)周向裂口 —检查成型机头 —压延帘线品种和性能
25ቤተ መጻሕፍቲ ባይዱ
胎侧部位
★胎侧缺胶
全钢载重子午胎生产车间常见质量问题及原因分析
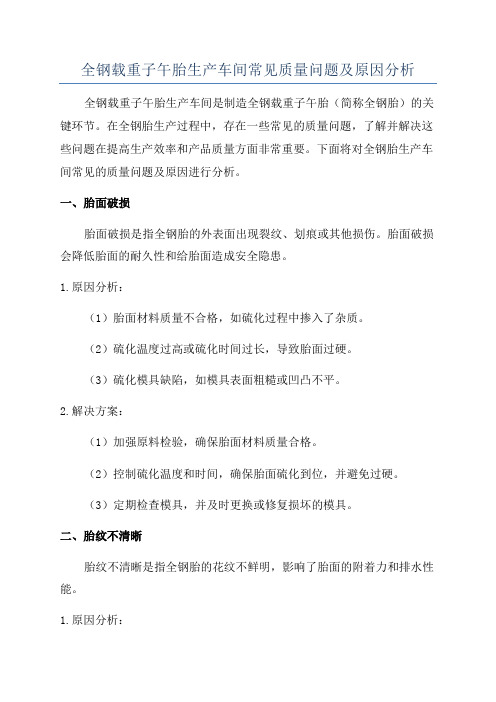
全钢载重子午胎生产车间常见质量问题及原因分析全钢载重子午胎生产车间是制造全钢载重子午胎(简称全钢胎)的关键环节。
在全钢胎生产过程中,存在一些常见的质量问题,了解并解决这些问题在提高生产效率和产品质量方面非常重要。
下面将对全钢胎生产车间常见的质量问题及原因进行分析。
一、胎面破损胎面破损是指全钢胎的外表面出现裂纹、划痕或其他损伤。
胎面破损会降低胎面的耐久性和给胎面造成安全隐患。
1.原因分析:(1)胎面材料质量不合格,如硫化过程中掺入了杂质。
(2)硫化温度过高或硫化时间过长,导致胎面过硬。
(3)硫化模具缺陷,如模具表面粗糙或凹凸不平。
2.解决方案:(1)加强原料检验,确保胎面材料质量合格。
(2)控制硫化温度和时间,确保胎面硫化到位,并避免过硬。
(3)定期检查模具,并及时更换或修复损坏的模具。
二、胎纹不清晰胎纹不清晰是指全钢胎的花纹不鲜明,影响了胎面的附着力和排水性能。
1.原因分析:(1)硫化时间不足,胎面未完全形成。
(2)硫化模具表面质量不良,导致花纹模糊不清。
2.解决方案:(1)加强硫化过程控制,确保胎面能够完全形成。
(2)定期检查模具表面质量,确保花纹能够清晰可见。
三、胎体开裂胎体开裂是指全钢胎胎体出现裂纹和断裂现象。
胎体开裂会导致胎压不稳定和胎面变形,进而影响行驶安全。
1.原因分析:(1)胎体成型时混入了空气或其他杂质。
(2)硫化温度和时间不足,导致胶料未完全熟化。
(3)硫化压力不够,无法将胶料牢固固定。
2.解决方案:(1)加强胎体成型过程监控,确保胎体无杂质混入。
(2)控制硫化温度和时间,确保胶料完全熟化。
(3)增加硫化压力,确保胶料能够牢固固定在胎体上。
四、轮胎不均衡轮胎不均衡是指全钢轮胎在使用过程中出现抖动或振动。
不均衡的轮胎会导致驾驶不舒适,并可能损坏车辆的其他部件。
1.原因分析:(1)施胶不均匀,导致轮胎重心偏移。
(2)胎体结构不均衡,如钢帘线紧张度不一致。
(3)胎面花纹设计不合理,导致轮胎不平衡。
子午胎缺陷原因及纠正方法
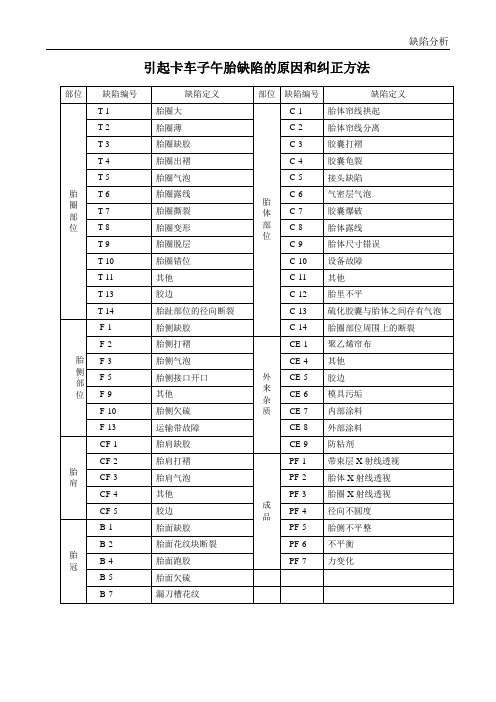
引起卡车子午胎缺陷的原因和纠正方法缺陷说明:轮胎的一个或两个胎圈过厚。
此缺陷表现为在相应的胎趾上有周向胶边,和/或胶与补强条,和缺陷T-2:胎圈薄缺陷T-3:胎圈缺胶缺陷T-6:胎圈露线缺陷T-7:胎圈撕裂缺陷说明:轮胎的一侧或两侧胎圈在下面部位出现破裂:a)只在胶料部位,b)橡胶和胎圈补强条部位,c)缺陷T-8:胎圈变形缺陷T-9:胎圈脱层缺陷说明:轮胎的一侧或两侧胎圈在下列部位脱层:a)胎体帘布和胎圈填充胶之间b)胎体帘布反包部位和缺陷T-10:胎圈错位缺陷说明:轮胎的一侧胎圈过厚,其表现为下列材料的周向跑边:a)胶料b)胶料和胎圈补强条c)胶料,胎缺陷T-11:其它缺陷T-13:胶边和/或毛刺缺陷T-14:胎趾部位径向裂口,在半硫化包边胶条接头不好缺陷说明:轮胎存在:a)起自胎趾部位的裂口,沿胎趾方向逐渐减少b)由于包边胶条接头的模具不好,从缺陷C-1:胎体帘布拱起缺陷C-2:胎体帘线劈缝缺陷说明:在轮胎内部,钢丝帘布上带接头或不带接头的钢丝分布不均,使得胎体帘布钢丝之间的间距太缺陷C-3:胶囊起褶缺陷说明:轮胎内表面出现:a)表面粗糙,尤其是在胎圈部位b)由于硫化胶囊老化过度,造成的胶线有裂缺陷C-5:接头缺陷缺陷说明:轮胎内表面出现:a)在相应的帘线接头处胶变薄和/或露线b)帘布接头张开c)帘布接头的接头过缺陷C-6:气密层有气泡缺陷说明:在胎内表面表现为:a)海绵现象b)在帘线之间的粘着胶片明显出现裂口c)完全裂开:由于硫化缺陷C-8:胎体露线缺陷C-9:半成品胎规格不对缺陷说明:由于在规格不对的模具中硫化,在轮胎内部表现为:a)断缺的不正常表面和/或重量超过规定b)缺陷C-10:设备故障缺陷C-11:其他缺陷C-12:胎里不平缺陷C-13:硫化胶囊与胎体之间有气泡缺陷C-14:胎圈部位内表面周向裂口缺陷F-1:胎侧缺胶缺陷说明:轮胎一侧或两侧在轮辋装配线与上防擦线中部,和/或与防擦线花纹沟,和/或与胎肩起始处之缺陷F-2:胎侧打褶缺陷说明:轮胎一边或两边胎侧在轮辋装配线与防擦线中部分,和/或防擦线花纹沟,和/或与胎肩起始处缺陷F-3:胎侧气泡缺陷说明:轮胎一边或两边有气泡:a)在胶料的胎体帘线间b)在表面和/或胶料中,在轮辋装配线和上防擦缺陷F-5:胎侧接头张开缺陷说明:由于在轮辋装配线与上防擦线中部和/或与防擦线花纹沟,和/或与胎肩起始处之间的部位内,缺陷F-9:其它—模具不正确缺陷说明:轮胎的一侧或两侧胎侧在轮辋装配线与上防擦线中部,和/或防擦线花纹沟和/或胎肩起始处之缺陷F-13:传送带缺陷缺陷说明:轮胎在一侧或两侧胎肩在防擦线花纹沟之间和/或防擦线中间与胎面花纹块的起始部位之间周缺陷CF-2:胎肩打褶缺陷说明:轮胎在一侧或两侧胎肩在防擦花纹沟之间和/或防擦线中间与胎面花纹块的起始部位之间周向打缺陷说明:轮胎在一侧或两侧胎肩在下列部位有气泡:a)胶料与胎体帘布之间b)防擦线花纹沟之间和/或防缺陷CF-4:其它缺陷CF-5:胶边缺陷B-2:胎面花纹块撕裂缺陷B-4:胎面上的胶边缺陷B-5:胎面欠硫缺陷B-7:漏刀槽花纹缺陷CE-4:其它缺陷CE-5:胶边缺陷CE-6:模具污垢缺陷CE-7:内部涂料缺陷CE-8:外涂料缺陷PF-1:带束层X射线的检测缺陷PF-2:胎体X射线的检测缺陷PF-3:胎圈X射线的检测缺陷PF-4:径向不圆度缺陷PF-5:胎侧不平缺陷PF-6:不平衡缺陷PF-7:力的变化缺陷说明:从轮胎断面看,由于结构和几何形状的变化,在加载转动时,发现轮胎的径向力和/或侧向力变。
全钢载重子午线轮胎胎里拱的原因分析及解决措施
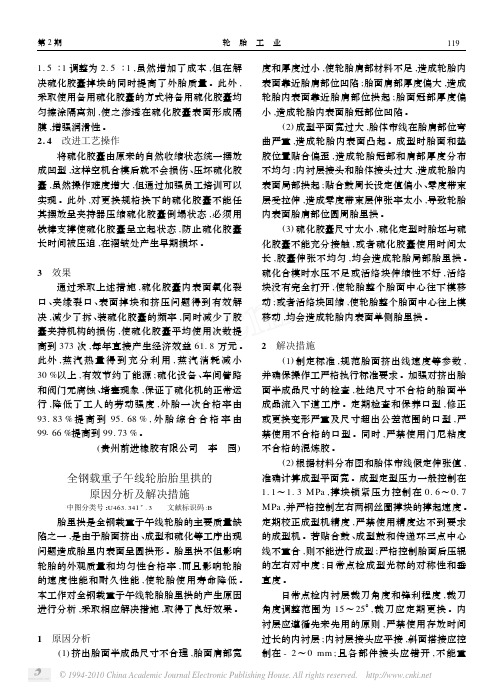
第2期1.5∶1调整为2.5∶1,虽然增加了成本,但在解决硫化胶囊掉块的同时提高了外胎质量。
此外,采取使用备用硫化胶囊的方式将备用硫化胶囊均匀擦涂隔离剂,使之渗透在硫化胶囊表面形成隔膜,增强润滑性。
2.4 改进工艺操作 将硫化胶囊由原来的自然收缩状态统一摆放成凹型,这样空机合模后就不会损伤、压坏硫化胶囊,虽然操作难度增大,但通过加强员工培训可以实现。
此外,对更换规格换下的硫化胶囊不能任其摆放呈夹持器压缩硫化胶囊倒塌状态,必须用铁棒支撑使硫化胶囊呈立起状态,防止硫化胶囊长时间被压迫,在褶皱处产生早期损坏。
3 效果 通过采取上述措施,硫化胶囊内表面氧化裂口、夹缘裂口、表面掉块和挤压问题得到有效解决,减少了拆、装硫化胶囊的频率,同时减少了胶囊夹持机构的损伤,使硫化胶囊平均使用次数提高到373次,每年直接产生经济效益61.8万元。
此外,蒸汽热量得到充分利用,蒸汽消耗减小30%以上,有效节约了能源;硫化设备、车间管路和阀门无腐蚀、堵塞现象,保证了硫化机的正常运行,降低了工人的劳动强度,外胎一次合格率由93.83%提高到95.68%,外胎综合合格率由99166%提高到99.73%。
(贵州前进橡胶有限公司 李 园)全钢载重子午线轮胎胎里拱的原因分析及解决措施中图分类号:U463.341+.3 文献标识码:B 胎里拱是全钢载重子午线轮胎的主要质量缺陷之一,是由于胎面挤出、成型和硫化等工序出现问题造成胎里内表面呈圆拱形。
胎里拱不但影响轮胎的外观质量和均匀性合格率,而且影响轮胎的速度性能和耐久性能,使轮胎使用寿命降低。
本工作对全钢载重子午线轮胎胎里拱的产生原因进行分析,采取相应解决措施,取得了良好效果。
1 原因分析 (1)挤出胎面半成品尺寸不合理,胎面肩部宽度和厚度过小,使轮胎肩部材料不足,造成轮胎内表面靠近胎肩部位凹陷;胎面肩部厚度偏大,造成轮胎内表面靠近胎肩部位拱起;胎面冠部厚度偏小,造成轮胎内表面胎冠部位凹陷。
全钢载重子午线轮胎几种外观质量缺陷的成因及解决措施
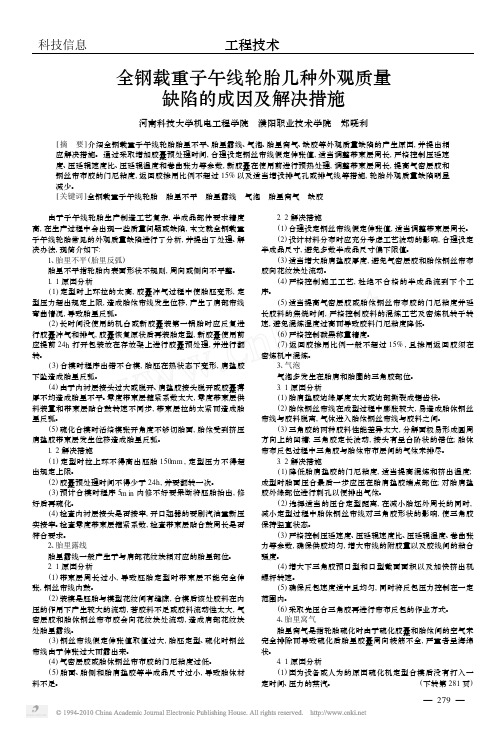
帘布反包过程中三角胶与胎体帘布层间的气体未排尽。
3. 2 解决措施
(1) 降低胎肩垫胶的门尼粘度, 适当提高混炼和挤出温度;
成型时胎面压合最后一步应压在胎肩垫胶端点部位; 对胎肩垫
胶外缘部位进行刺孔以便排出气体。
(2) 选择适当的压合定型距离, 在减小胎坯外周长的同时,
减小定型过程中胎体钢丝帘线对三角胶形状的影响, 使三角胶
来进行, 称为扩充响应曲线法。 其步骤如下:
4. 4 根据所求得的 Tm、Σ 和 Tm Σ 的值, 查下表即可求得控
4. 1 断开数字控制器, 使系统在手动状态下工作。当系统在 制器的 T、Kp、T I 和 TD 的值, 表中控制度的求法与扩充临界比
给定值处于平衡后, 给一阶跃输入。
例度法相同。
扩充响应曲线法整定参数表
(4) 气密层胶或胎体钢丝帘布胶的门尼粘度过低。 (5) 胎面、胎侧和胎肩垫胶等半成品尺寸过小, 导致胎体材 料不足。
2. 2 解决措施
(1) 合理设定钢丝帘线假定伸张值, 适当调整带束层周长。
(2) 设计材料分布时应充分考虑工艺波动的影响, 合理设定
半成品尺寸, 避免多数半成品尺寸偏下限值。
(3) 适当增大胎肩垫胶厚度, 避免气密层胶和胎体钢丝帘布
(4) 胶囊的存放要尽量保持原有的形状, 在装第一锅的时候 对胶囊进行多次的伸张动作。
5、缺胶 缺胶产生于轮胎的各部位。 5. 1 原因分析 (1) 胎坯周长过大。 (2) 定型压力过大。 (3) 定型过程中胎体钢丝帘线伸张过大。 (4) 材料分布不合理。 (5) 模具排气孔堵塞或排气孔、排气线分布不合理。
(8) 延长二次定型时间, 增大二次定型压力。 (9) 避免胎坯存放时间过长, 控制其在 2~ 72 h 。 (10) 减小胎圈包布或胎圈外护胶厚度, 避免胎侧下端点落 在胎踵处或胎圈底部及其稍高部位。
全钢子午胎轮胎外观病象图案分析
轮胎外观成型常见病象分析1、病象描述:胎里不平(内不平)、肩弯胎里不平是指轮胎内表面形状不规则,周向或横向不平。
1.1原因分析:1.1.1压延原因:(1)、胎面等半成品尺寸不合格1.1.2成型原因:(1)、内衬层接头过大或脱开,胎肩垫胶接头脱开,胶囊厚薄不均。
(2)、平面宽(扣圈位)不符合施工标准,过大,或者左右不对称(3)、胎肩垫胶上反或位置偏移。
(4)、辅鼓周长过小,造成带束层复合件带束层拉得太紧。
(5)、带束层偏(6)、扇形块其落不一致1.1.3硫化原因:(1)、定型时上环拉得太高,胶囊充放过程中胎胚变形。
(2)、定型压力超出规定上限,造成胎体帘线位移,产生弯曲。
(3)、程序出错不合模,胎胚在热状态下变形,胎肩垫胶下坠。
(4)、新胶囊使用前没进行预热处理。
(5)、硫化合模时活络模的张开角度不够致使切胎面,胎体受到挤压,胎肩垫胶、带束层发生位移。
1.2解决措施:(1)、确保所使用的半成品符合标准。
(2)、确保内衬层接头接牢,接头部位开口或翘起应及时刷汽油重新压实接牢。
(3)、确保平面宽(扣圈位)、辅鼓周长等在工艺要求的范围之内。
(4)、确保成型各种半成品上正压实。
(5)、确保硫化定型时一二次定性高度复合标准(6)、硫化确保定型压力在工艺要求的范围之内。
(7)、合模时设备出现问题且预计5min内修不好,应立即将胎胚吊出。
(8)、确保活络模水缸压力适中,不出现回缩等现象。
2、病象描述:胎里漏丝(内漏丝)胎里漏线是指轮胎内钢丝帘线漏出胎里表面。
胎里漏线多出现在胎肩或胎侧部位,表现为帘线漏出或“漏筋骨”现象,存在该种缺陷的轮胎在使用过程中胎里漏出的钢丝容易损坏内胎,使胎体鼓包甚至爆破。
2.1原因分析(1)、平面宽度与帘线伸张值选取不合理是主要原因。
平面宽过小(2)、半成品尺寸和质量不合理或不合格。
胎面、胎侧或胎肩垫胶、内衬层的厚度或长度不足、内轮廓帘线伸展过度,容易导致胎里漏线。
(3)、胎胚外周长选取不合理。
全钢子午胎成型基本缺陷及处理措施
全钢子午胎成型基本缺陷及处理措施4、胎里气泡和脱层胎里气泡和脱层是指内衬层与胎体之间存有空气、水、汽油或隔离剂,硫化后胎里产生气泡或脱层的现象。
4.1 原因分析(1)成型贴合时部件间因间隙超标存在空气或组合压辊各段压力和轨迹设置不当,以及超定型压力不足,造成胎肩垫胶、气密层等部件未压实,存有空气。
(2)部件层间夹有塑料垫布和胶带断头及纸片等杂质。
(3)硫化前、中期掉压时间超过6min,部件层间形成气孔。
(4)成型贴合时涂刷的汽油未挥发干即进行下一步操作,胎体气泡未刺破。
(5)胎肩垫胶定位偏歪,带束层与胎体帘布层间产生空隙。
(6)炼胶或半成品加工过程中温度偏高致使半成品焦烧时间短,胶料或半成品部件未按顺序使用,半成品过期后粘性差,喷霜后未经处理;汽油胶浆未干,成型过程中压辊不实,均会造成胎里脱层。
(7)内衬层复合时未压实,层间存有气体。
(8)胶囊排气线不通畅,内压作用下胶料中的气体进入气密层与胎体帘布层间。
4.2 解决措施(1)如有必要,重新设定成型机压力、各个压合辊轨迹参数以及各种定位参数,保证成型时各部件的贴合质量,使胎肩垫胶和气密层等部件接牢、压实。
(2)检查各半成品部件的灯光定位,防止定位灯光偏移。
(3)半成品部件按顺序使用,汽油挥发完后方可贴合下一个部件。
(4)成型时除净塑料及纸片等杂质。
(5)适当延长硫化定型时间、提高定型压力,使胶囊充分伸展,保证胶囊排气线畅通。
(6)确保硫化温度、压力曲线正常。
(7)气泡刺破。
5、胎里窝气胎里窝气是指轮胎硫化时由于硫化胶囊和胎体之间的空气未排干净而导致硫化后胎里周向呈现的胶囊棱筋不全或棱筋不清晰,严重者呈海绵状的现象。
5.1 原因分析(1)胶囊及其夹环排气线不畅通或胶囊隔离剂喷涂过多且未挥发干就装胎胚,造成胎里和胶囊之间有水分存在,或合模后未及时充内压。
(2)冬春季节节假日后,新换的胶囊没有充分预热,装胎时胶囊没有充分伸展;硫化机管路内的凉水未排干净,胎胚硫化前未预热,胶囊与胎胚轮廓吻合不好。
全钢工程胎常见质量缺陷、产生原因及解决措施
全钢工程胎常见质量缺陷、产生原因及解决措施全钢工程胎常见质量缺陷、产生原因及解决措施(草稿)一、常见内在质量缺陷(X光检验)1、带束层1.1、差级不均或齐边带束层差级不均或齐边,会使轮胎两侧肩部材料分布不均,造成轮胎行驶时受力不均,较厚的一侧生热大,易产生脱空;较薄的一侧易发生肩部裂开。
产生原因:①辅助鼓的定中心装置错误,灯光标尺偏离中心线。
②带束层部件喷霜、粘合性能差,滚压时造成移位。
③成型定型时压力及宽度不合格,使胎体与带束层定型时差合不上,滚压胎冠时造成带束层偏歪。
④带束层斜边长度不合格或带束层宽窄不一。
解决措施:①检查辅助鼓定中心装置,灯光标尺必须定位于中心,供料架不许偏歪。
②带束层部件喷霜及粘合性能差的,甩出不使用。
③检查成型定型压力及宽度,不符合施工标准的应及时调整。
④对于带束层斜边长度不合格或宽窄不一的部件要甩出不使用。
1.2散线带束层断线后用胶条包边,其主要目的:一是裁断后至成型前防止帘线端边受潮;二是避免钢帘布端头处松散和提高裁断后端部与其它部件的粘合性。
散线主要产生在第二、三层带束层,带束层散线的轮胎在行驶中易局部生热大,产生脱层。
产生原因:①成型后压辊定位偏高,低压设定不合理,滚压时高压使用过早。
②带束层粘性差,不能很好地与其它带束层成为一体,在滚压时产生移位。
③垫胶贴合偏移或左右贴反。
④垫胶过薄。
⑤胎冠肩部超厚。
解决措施:①成型操作前要检查平面宽度是否符合工艺要求,防止因扇形块风压不稳定而引起组合件移位。
②调整设定好定型风压,使其符合工艺要求。
③滚压胎冠时,检查后压辊的位置,使用低风压或高风压时要掌握好风压及滚压时间。
④贴合带束层时,第二、三层带束层接头后压实,并用胶片对两侧端点包边。
⑤校正供料架、灯标(贴合部件手工加以调整)。
贴合垫胶时要注意,梯形长斜面靠向外侧。
⑥过薄的垫胶停止使用。
⑦胎冠肩部超厚停止使用。
2、胎体2.1接头开接头开主要是指钢丝帘布接头拼接不牢,在成型充气膨胀和硫化内压的作用下,拼接不牢的部位断裂开缝,缺少钢丝。
全钢载重子午胎质量缺陷产生原因及解决措施
全钢载重子午胎质量缺陷产生原因及解决措施1胎里露线胎里露线是指轮胎里面钢丝骨架材料内表面覆胶不足,钢丝露出胎里表面。
胎里露线多在肩部或侧部出现。
经过里程实验,出现露线的外胎在耐久实验15小时左右即出现肩部鼓包或爆破,基本没有使用价值,由于影响因素较多,因此,胎里露线是废品率很高的一种缺陷,也是全钢胎制造过程中最容易出现、最难解决的问题。
1.1原因分析1.1.1胎里露线主要原因是机头平宽设计偏小或在成型过程中胎圈定位撑块出现漂移造成。
成型机头宽度窄,两胎圈之间的帘线长度短,当硫化给内压时,由于胎胚外直径小于设计尺寸,伸张变形大,这样帘线会抽出内衬层导致胎里露线。
1.1.2材料分布不足也会产生胎里露线,如果胎面或垫胶的厚度或长度不够标准,在成型时强行拉伸,导致局部材料缺失,肩部内轮廓帘线伸展过渡,易出现胎里露线现象。
1.1.3内衬层的厚度及各部位的尺寸低于设计尺寸,或成型时贴合偏移,造成局部材料分布不均,或密封层的塑性过大均会造成肩部漏钢丝的现象。
1.1.4硫化定型失控也是造成成品肩部漏钢丝的不可忽视的原因。
在硫化定型时,如果定型压力不能稳定在规定值,那么在合模过程中,胎胚外直径一直处于逐渐增大的状态,这样会有肩部部分胶料随着花纹块下移,造成上模花纹块处缺胶,成品胎里肩部露线。
1.1.5硫化机机械手定位高度过低,胎胚的中心线与胶囊中心线不吻合,定型时胎胚上部过度伸张,钢丝帘线析出内衬层表面,出现露线现象。
1.2 解决措施:1.2.1 结构设计是内在因素,工艺和操作是外部因素。
若存在着普遍的胎里露线现象,并且通过X光检测,发现胎体帘线成直线排列,则应重新考虑平宽的选取,一般增大2~4mm可解决。
严格控制挤出、压型半成品部件的的尺寸,不合格的半成品部件严禁使用。
1.2.2 严格控制成型操作,每班开产前必须对成型鼓的平宽、送料架的定位尺寸进行测量,不符合要求的应通知维修人员解决后方可生产。
同时要检查各种半成品部件是否符合施工条件,不合格的半成品严禁使用。
- 1、下载文档前请自行甄别文档内容的完整性,平台不提供额外的编辑、内容补充、找答案等附加服务。
- 2、"仅部分预览"的文档,不可在线预览部分如存在完整性等问题,可反馈申请退款(可完整预览的文档不适用该条件!)。
- 3、如文档侵犯您的权益,请联系客服反馈,我们会尽快为您处理(人工客服工作时间:9:00-18:30)。
4、胎里气泡和脱层
胎里气泡和脱层是指内衬层与胎体之间存有空气、水、汽油或隔离剂,硫化后胎里产生气泡或脱层的现象。
4.1 原因分析
(1)成型贴合时部件间因间隙超标存在空气或组合压辊各段压力和轨迹设置不当,以及超定型压力不足,造成胎肩垫胶、气密层等部件未压实,存有空气。
(2)部件层间夹有塑料垫布和胶带断头及纸片等杂质。
(3)硫化前、中期掉压时间超过6min,部件层间形成气孔。
(4)成型贴合时涂刷的汽油未挥发干即进行下一步操作,胎体气泡未刺破。
(5)胎肩垫胶定位偏歪,带束层与胎体帘布层间产生空隙。
(6)炼胶或半成品加工过程中温度偏高致使半成品焦烧时间短,胶料或半成品部件未按顺序使用,半成品过期后粘性差,喷霜后未经处理;汽油胶浆未干,成型过程中压辊不实,均会造成胎里脱层。
(7)内衬层复合时未压实,层间存有气体。
(8)胶囊排气线不通畅,内压作用下胶料中的气体进入气密层与胎体帘布层间。
4.2 解决措施
(1)如有必要,重新设定成型机压力、各个压合辊轨迹参数以及各种定位参数,保证成型时各部件的贴合质量,使胎肩垫胶和气密层等部件接牢、压实。
(2)检查各半成品部件的灯光定位,防止定位灯光偏移。
(3)半成品部件按顺序使用,汽油挥发完后方可贴合下一个部件。
(4)成型时除净塑料及纸片等杂质。
(5)适当延长硫化定型时间、提高定型压力,使胶囊充分伸展,保证胶囊排气线畅通。
(6)确保硫化温度、压力曲线正常。
(7)气泡刺破。
5、胎里窝气
胎里窝气是指轮胎硫化时由于硫化胶囊和胎体之间的空气未排干净而导致硫化后胎里周向呈现的胶囊棱筋不全或棱筋不清晰,严重者呈海绵状的现象。
5.1 原因分析
(1)胶囊及其夹环排气线不畅通或胶囊隔离剂喷涂过多且未挥发干就装胎胚,造成胎里和胶囊之间有水分存在,或合模后未及时充内压。
(2)冬春季节节假日后,新换的胶囊没有充分预热,装胎时胶囊没有充分伸展;硫化机管路内的凉水未排干净,胎胚硫化前未预热,胶囊与胎胚轮廓吻合不好。
(3)硫化机停机时间过长,胶囊在硫化模具内自然下坠变形。
(4)定型压力过小,囊壁与胎胚之间存在空气。
5.2 解决措施
(1)疏通胶囊排气线,待喷涂的胶囊隔离剂干后再装胎。
(2)温模时提前4h把胎胚放在硫化机前预热。
(3)冬季新换胶囊要温模预热1h以上。
(4)长时间停机后第一次硫化时硫化机管道中的热水要充分循环,胶囊要进行多次伸张,定型时要充分伸展,要延时硫化。
6、胎里不平(反弧及轴向棱子)
胎里不平是指轮胎内表面形状不规则,周向或横向不平。
6.1 原因分析
(1)定型时上环拉得太高,胶囊充放过程中胎胚变形。
(2)定型压力超出规定上限,造成胎体帘线位移,产生弯曲。
(3)程序出错不合模,胎胚在热状态下变形,胎肩垫胶下坠。
(4)新胶囊使用前没进行预热处理。
(5)硫化合模时活络模的张开角度不够致使切胎面,胎体受到挤压,胎肩垫胶、带束层发生位移。
(6)内衬层接头过大或脱开,胎肩垫胶接头脱开,胶囊厚薄不均。
(7)0度带束层箍紧因数太大(拉伸小于0.3%),0度带束层供料装置与B&T鼓转速不同步,带束层拉得太紧。
(8)胎肩垫胶上反或位置偏移。
6.2 解决措施
(1)确保定型时上环不高于胎胚150㎜。
(2)确保定型压力不高于规定上限。
(3)合模时设备出现问题且预计5min内修不好,应立即将胎胚吊出。
(4)确保活络模水缸压力适中。
(5)确保内衬层接头接牢,接头部位开口或翘起应及时刷汽油重新
压实接牢。
(6)确保0度带束层箍紧因数和B&T鼓周长适中。
7、胎里缺损
胎里缺损是指由于胶囊缺陷引起的胎里凹凸不平的现象。
7.1 原因分析
(1)胶囊有沙眼、漏水。
(2)胶囊未充分伸展,造成胎里产生胶棱或窝胶囊缺胶现象。
(3)胶囊老化裂口。
(4)胶囊隔离剂喷涂过多且未干就装胎。
(5)内衬层接头脱开。
7.2 解决措施
(1)仔细检查胶囊的使用情况,确保其无沙眼、漏水,及时更换老化胶囊,胶囊隔离剂喷涂均匀且待隔离剂完全干后方可装入胎胚。
(2)确保硫化定型过程中胶囊充分伸展。
(3)内衬层接头脱开,一定重新接好、压实。
8、下模窝胶囊
下模窝胶囊是指轮胎一侧胎圈部位或胎里被胶囊折叠挤压产生的缺陷。
8.1 原因分析
(1)装胎时胎胚没放正或机械手与中心机构不对中。
(2)定型胶囊未伸展开(胶囊老化)。
(3)定型压力偏小。
(4)未按规定喷涂隔离剂,胶囊润滑性能不好。
8.2 解决措施
(1)装胎时必须放正胎胚,若机械手晃动或与中心机构不对中应及时处理。
(2)确保胶囊伸展开,老化胶囊及时更换。
10.00R20规格以下的中小胶囊使用400次、11.00R20以上规格的胶囊使用450次应及时更换。
(3)确保定型压力适当。
(4)按规定喷涂隔离剂,保证胶囊的润滑性能良好。