浅谈多头蜗杆的快速车削
浅谈多线蜗杆的车削方法
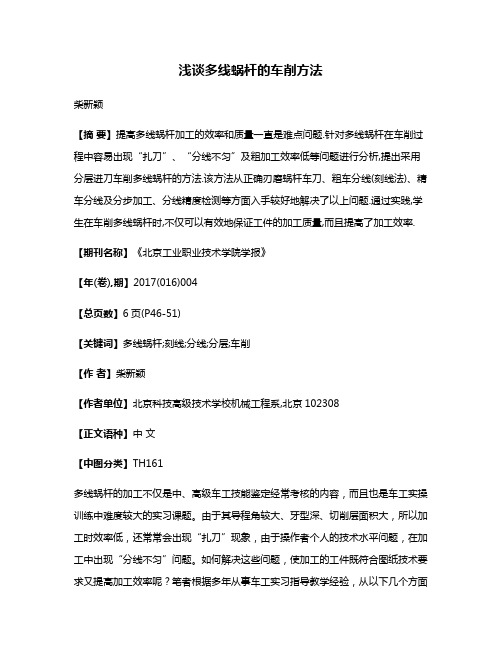
浅谈多线蜗杆的车削方法柴新颖【摘要】提高多线蜗杆加工的效率和质量一直是难点问题.针对多线蜗杆在车削过程中容易出现“扎刀”、“分线不匀”及粗加工效率低等问题进行分析,提出采用分层进刀车削多线蜗杆的方法.该方法从正确刃磨蜗杆车刀、粗车分线(刻线法)、精车分线及分步加工、分线精度检测等方面入手较好地解决了以上问题.通过实践,学生在车削多线蜗杆时,不仅可以有效地保证工件的加工质量,而且提高了加工效率.【期刊名称】《北京工业职业技术学院学报》【年(卷),期】2017(016)004【总页数】6页(P46-51)【关键词】多线蜗杆;刻线;分线;分层;车削【作者】柴新颖【作者单位】北京科技高级技术学校机械工程系,北京102308【正文语种】中文【中图分类】TH161多线蜗杆的加工不仅是中、高级车工技能鉴定经常考核的内容,而且也是车工实操训练中难度较大的实习课题。
由于其导程角较大、牙型深、切削层面积大,所以加工时效率低,还常常会出现“扎刀”现象,由于操作者个人的技术水平问题,在加工中出现“分线不匀”问题。
如何解决这些问题,使加工的工件既符合图纸技术要求又提高加工效率呢?笔者根据多年从事车工实习指导教学经验,从以下几个方面入手:正确刃磨车刀、采用分层法粗车、精车分线及步骤和正确的检测,较好地解决了车削中“扎刀”的问题,也提高了加工效率和分线精度。
车削蜗杆的方法主要有左右切削、切槽、分层切削3种方法[1]。
1.1 左右切削法在车削中为防止3个切削刃同时参加切削而引起扎刀,利用左右进给的进刀方式逐渐车至槽底的方法,称为左右车削法。
采用左右车削法车削时,背吃刀量不能太大,尤其是向右侧赶刀时,存在切削阻力大,排屑不顺畅,易产生“扎刀”现象,并且效率低。
1.2 切槽法切槽法是先用矩形螺纹车刀将螺旋直槽车至蜗杆齿根处,然后再粗车刀粗车成形的方法,称为直槽法。
利用直槽法车削比左右切削法效率提高了,但是学生需要刃磨切槽刀、蜗杆粗、精车刀,由于切槽刀的角度及刃磨是一大难点,不易掌握,当模数较大时,刀头太长,刀具强度低,易产生刀头折断现象。
高精度多头蜗杆的车削方法
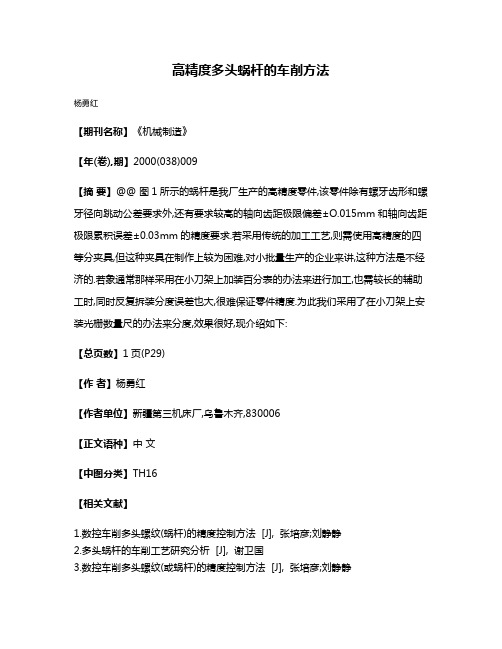
高精度多头蜗杆的车削方法
杨勇红
【期刊名称】《机械制造》
【年(卷),期】2000(038)009
【摘要】@@ 图1所示的蜗杆是我厂生产的高精度零件,该零件除有螺牙齿形和螺牙径向跳动公差要求外,还有要求较高的轴向齿距极限偏差±O.015mm和轴向齿距极限累积误差±0.03mm的精度要求.若采用传统的加工工艺,则需使用高精度的四等分夹具,但这种夹具在制作上较为困难,对小批量生产的企业来讲,这种方法是不经济的.若象通常那样采用在小刀架上加装百分表的办法来进行加工,也需较长的辅助工时,同时反复拆装分度误差也大,很难保证零件精度.为此我们采用了在小刀架上安装光栅数量尺的办法来分度,效果很好,现介绍如下:
【总页数】1页(P29)
【作者】杨勇红
【作者单位】新疆第三机床厂,乌鲁木齐,830006
【正文语种】中文
【中图分类】TH16
【相关文献】
1.数控车削多头螺纹(蜗杆)的精度控制方法 [J], 张培彦;刘静静
2.多头蜗杆的车削工艺研究分析 [J], 谢卫国
3.数控车削多头螺纹(或蜗杆)的精度控制方法 [J], 张培彦;刘静静
4.多头蜗杆的车削 [J], 张燕平
5.在多线螺纹和多头蜗杆车削教学中应注意的两个问题 [J], 李小强;王宏斌
因版权原因,仅展示原文概要,查看原文内容请购买。
单件生产中多头蜗杆的车削论文:单件生产中多头蜗杆的车削
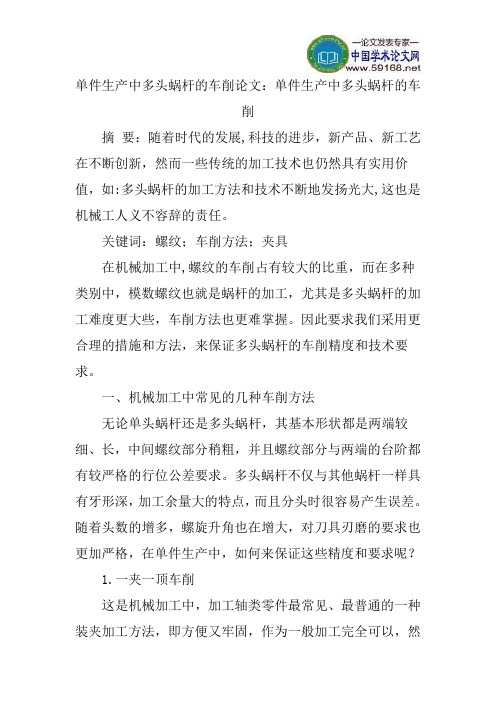
单件生产中多头蜗杆的车削论文:单件生产中多头蜗杆的车削摘要:随着时代的发展,科技的进步,新产品、新工艺在不断创新,然而一些传统的加工技术也仍然具有实用价值,如:多头蜗杆的加工方法和技术不断地发扬光大,这也是机械工人义不容辞的责任。
关键词:螺纹;车削方法;夹具在机械加工中,螺纹的车削占有较大的比重,而在多种类别中,模数螺纹也就是蜗杆的加工,尤其是多头蜗杆的加工难度更大些,车削方法也更难掌握。
因此要求我们采用更合理的措施和方法,来保证多头蜗杆的车削精度和技术要求。
一、机械加工中常见的几种车削方法无论单头蜗杆还是多头蜗杆,其基本形状都是两端较细、长,中间螺纹部分稍粗,并且螺纹部分与两端的台阶都有较严格的行位公差要求。
多头蜗杆不仅与其他蜗杆一样具有牙形深,加工余量大的特点,而且分头时很容易产生误差。
随着头数的增多,螺旋升角也在增大,对刀具刃磨的要求也更加严格,在单件生产中,如何来保证这些精度和要求呢?1.一夹一顶车削这是机械加工中,加工轴类零件最常见、最普通的一种装夹加工方法,即方便又牢固,作为一般加工完全可以,然而加工精度较高的工件时,要采用这种方法,必须用四爪盘找正,(以保证工件的精度)。
装卡要牢固,有的操作者怕夹伤工件,就用垫铜皮的方法加以预防,由于加工螺纹时,螺旋升角,对车削的阻力也大,所以装卡一定要牢固,牢固了就会卡伤工件(尽管垫铜皮了)夹的不牢固工件会产生旋转,也会产生位移,怎样才能既保证精度又不使工件夹伤呢?2.两顶尖车削这种加工方法是一种较方便的能保证工件有良好同轴度的加工方法,它是采用两顶尖支承工件,因此不会夹伤工件的现象发生。
可是它的强度呢?在一次技能竞赛中,加工的就是一个蜗杆,有位师傅就是采用两顶尖的方法进行车削,其结果是撅了一次,又一次,最终把工件撅废了,也没能完成以上两种车削方法虽然都可行。
但一个容易夹伤工件,一个容易撅废工件,人什么方法使其即装夹牢固又不夹伤工件,即保证精度而又不撅活呢?二、夹具的合理使用我这里所说的夹具,并不是制造特别复杂的那种,它只是一个带有开口的夹套。
浅谈多头蜗杆的车削及测量

浅谈多头蜗杆的车削及测量作者:于帅来源:《科技视界》2014年第10期【摘要】如何能严格按蜗杆的车削技术要求、蜗杆车削方法和步骤,以及蜗杆有关车削的计算方法,制定蜗杆加工工艺,准确的测量蜗杆尺寸等。
笔者通过实践中的积累,对上述问题进行分析,避免常见问题的发生,有效的提高蜗杆的加工质量和加工效率,合理解决了车削蜗杆过程中的难点。
【关键词】多头蜗杆车削;车刀刃磨及角度;测量方法0 引言实习教学是技工学校的基本课程,学生在毕业前应熟练地掌握一定的专业操作技能,成为合格的技术工人。
为了提高、巩固学生操作技能,针对学生对车削外圆、内孔、圆锥、成形面等切削部分则比较容易掌握,而对车螺纹特别是对多头蜗杆的车削,掌握起来较为困难,蜗杆的齿型和梯形螺纹很相似。
常用的蜗杆有米制蜗杆(模数),齿型角为20°(牙形角40°);英制蜗杆(径节)齿型角为14°30′,(牙形角29°)两种。
我国一般常用米制蜗杆。
齿型又分轴向直廓蜗杆和法向直廓蜗杆。
通常轴向直廓蜗杆应用较多,展成法是车蜗杆的最有效方法,但由于蜗杆的齿型较深,蜗杆的一般技术要求切削面积大,因此车削时比一般梯形螺纹更困难些。
沿两条或两条以上,在轴向等距分布的螺旋线所形成的蜗杆叫多头蜗杆。
多头蜗杆分为轴向直廓(阿基米德螺线)蜗杆和法向直廓蜗杆两种,前者的齿形在轴平面内为直线,在法平面内为曲线,后者的齿形与前者正好相反。
多头蜗杆有着特殊的技术要求,加工过程中必须限制蜗杆螺纹轴向齿距偏差、轴向齿距的累积误差、蜗杆齿形误差应在公差之内,否则将影响蜗轮副的传动精度。
蜗杆的螺纹齿面粗糙,将影响工作表面的耐磨性和使用寿命。
下面从加工方面加以说明,以保证蜗杆的生产加工质量。
1 蜗杆的一般技术要求1)蜗杆的齿距必须等于蜗轮的齿距。
2)轴向或法向齿厚必须符合要求。
3)蜗杆齿形两侧表面粗糙度值要小,齿形应符合图样要求。
4)蜗杆径向跳动应在允许范围内。
浅谈蜗杆的车削

浅谈蜗杆的车削作者:桑艳平来源:《现代企业文化·理论版》2008年第12期【摘要】蜗轮、蜗杆组成的运动副常用于减速传动机构中,蜗杆的齿形较大,在切削时很难把握。
通过革新刀具、合理使用刻度和选择切削用量,采用这种新的车削蜗杆的方法大大提高了生产质量和生产效率,是一种可以推行的蜗杆加工方法。
【关键词】蜗杆模数刃磨;刻度线;刀体;加工步骤蜗杆的车削加工具有很重要的位置。
蜗杆、蜗轮组成的运动副常用于减速传动机构中,以传递两轴在空间成900交错的运动。
蜗杆的齿形与梯形螺纹很相似,其轴向剖面图形状为梯形。
常用的蜗杆有米制(齿形角为400)和英制(齿形角为290)两种。
我国大多数采用米制蜗杆。
工业上最常用的是阿基米德蜗杆(即轴向直轮廓蜗杆),蜗杆的车削方法和梯形螺纹相似,但蜗杆的齿形比梯形螺纹的齿形大,车削时刀具和工件容易发生振动,使工件变形甚至会产生“扎刀”现象。
为解决这样的问题,这里介绍的车削蜗杆的方法主要是对刀具、刀体车削方法进行了改进,使粗车时能够进行强力切削,而且振动小,能保证顺利排屑,不产生“扎刀”现象。
当熟练地掌握了这种加工方法以后,生产效率比一般的车削方法有所提高。
下面就以教学中加工模数mx=6的单头的蜗杆为例,介绍此革新方法车削蜗杆的主要过程和加工特点,车削时采用工件材料为45钢。
一、改进一般的弹性刀为刚性刀1.刀块材料:高速钢(W18Cr4V),刀体材料:45钢(刀体需经热处理,HRC38—42)。
2.刀体可以转动。
在粗车时,如用一般的“死体刀”,由于工件螺旋角的关系,需把刀块一侧刃的后角刃磨得较大,使刀头强度减小,不能进行强力切削。
而采用可以旋转角度的刀体,在车削时,就能根据工件螺旋角的大小,把刀体转过这个角度。
这时刀块只要刃磨成和一般车刀相同的后角即可,不需要磨成大后角,保持了刀头强度,有利于强力切削。
3.刀体采用刚性强的刀体,一般的弹性刀体在较大的轴向切削力的影响下,会发生扭转变形使所车蜗杆的轴向齿形角发生变化和螺距产生变化和螺距产生误差,降低加工精度。
蜗杆加工方法

在数控车床上快速车削蜗杆的方法摘要:在数控车床上车削较大导程的蜗杆、梯形螺纹和锯齿螺纹,由于工件的齿形深,需要切除的毛坯余量多,一般是选择较低的切削速度和高速钢成形刀,使用G32和G76等指令车削,加工精度特别是表面粗糙度很难达到图纸要求,加工难度较大。
针对出现的加工精度低、生产效率低等特点,说明如何有效地发挥数控车床的高精度,高速度、定位精度高、生产效率高的优势。
我们以沈阳CAK3675v 华中数控系统的车床来论述快速车削蜗杆的方法。
如图1关键词:蜗杆数控车床成形刀硬质合金宏程序蜗杆和大导程螺纹车削的进刀方法有多种,如直进法、左右切削法、斜进法和切槽法等。
以前车削蜗杆等大导程零件的方法是:选用较低主轴转速(数控车床最低速为100转/分时转动无力)和高速钢成形车刀,车削蜗杆时的生产效率低。
为解决上述问题,我认为应从刀具材料、几何形状及角度和车削方法来谈谈快速车削蜗杆和大导程螺纹的方法。
一、突破传统选择刀具的习惯,合理选择车削蜗杆的刀具角度,使刀具的刀尖角小于齿形角车削蜗杆刀具的刀尖角如果等于蜗杆的齿形角。
这种刀具在车削时两侧刀刃与工件侧面容易发生摩擦,甚至三个刀刃同时参加切削,易产生较大的切削力而损坏刀具。
如果选择车刀的刀尖角35小于蜗杆的齿形角40,(如图2)这种车刀在车削时,可防止三个刀刃同时参加切削,减少了摩擦、切削力,能很好地避免“闷车”、“扎刀”和打刀的情况发生。
二、在数控车床上使用硬质合金车刀高转速车削蜗杆成为现实以前,车削加工蜗杆和大导程螺纹,只能用高速钢车刀低速车削加工,生产效率非常低。
如果将车刀的刀尖角磨小,使车刀的刀尖角35小于蜗杆的齿形角40,可避免三个刀刃同时参加切削,切削刀显剧下降,这时可使用较高的切削速度和硬质合金车刀对蜗杆进行车削。
当工件直径、导程越大时,可获得的线速度越高,加工出的工件表面质量越好,而且生产效率明显提高。
彻底解决在数控车床不能用硬质合金刀具车削蜗杆和大导程螺纹零件。
高效加工蜗杆的数控车削方法,超有用!

高效加工蜗杆的数控车削方法,超有用!随着当今时代电子信息技术的突飞猛进,现代机械设备不断向自动化、数控化方向发展。
数控机床是现代制造业的基础技术,是提高产品质量和劳动生产率必不可少的手段,数控技术的发展和应用水平也是一个国家综合国力的标志,普通车床的加工也逐步被数控车床所取代。
对于蜗杆的加工,因螺距大,牙型深,加工余量大,再因其牙型特点,车削时刀刃与工件接触面大,容易发生振动,加工途中极易因工件与刀具间切屑的挤压造成刃具损坏,产生“扎刀”现象,造成蜗杆报废,而且加工时间周期长。
本文结合具体的生产实际,从刀具、车削方法和切削参数等方面对现有的加工进行改进,改善了刀具受力情况、提高了加工质量和切削效率;因数控程序简单,操作性强,为此类零件的加工提供了一定的借鉴、参考。
一、蜗杆的特性及参数的计算1.蜗杆的特性常用的蜗杆有公制(齿形角为40o)和英制(齿形角为29o)两种。
我国大多数采用公制蜗杆。
而最常用的是阿基米德蜗杆(即轴向直轮廓蜗杆)它的齿面为阿基米德螺旋面,端面是阿基米德螺旋线,如图1所示。
轴向齿廓(A-A截面)是直线,而法面(N-N截面)的齿形则为曲线,如图2所示。
2.蜗杆的结构及参数根据生产的要求,所要加工的蜗杆为公制蜗杆,模数Mx=3,齿形角为40o,材料45号钢,具体参数如表1所示。
蜗杆的结构和尺寸要求如图3所示。
如图所示,该蜗杆的尺寸精度和形位公差要求高,加工难度大,为了保证其精度要求,应尽量采用高精度的设备。
另外,公司产品以多品种小批量为主,采用专用铣削机床投入成本高,如果使用普通车床加工,对人员的要求很高,而且加工成本很高,效率太低,产品质量难以保证。
因公司的机床设备多样化,数控加工机床占生产设备70%左右,所以本次加工蜗杆决定采用高精度的数控车床HARDINgE (Quest 8/51),该数控车床为斜床身,12位刀塔,定位精度0.00mm ,重复定位精度0.005mm,Fanuc series 21i-T操作系统,最高转速3 500r/min,最低加工转速50r/min,最大加工直径400mm。
如何进行高效的多线蜗杆车削加工
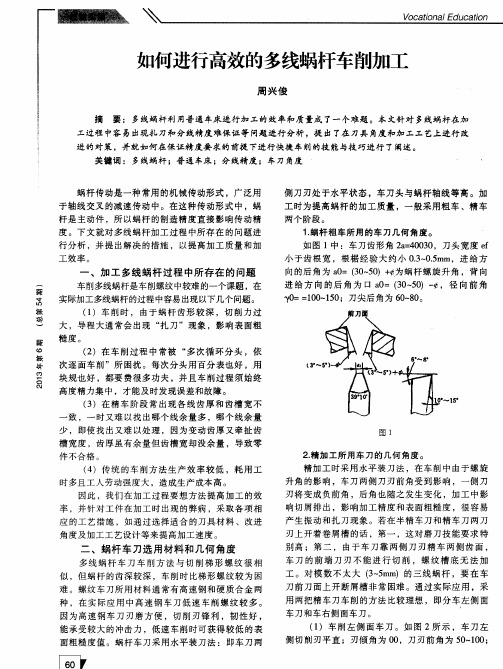
块规 也 好 ,都要 费很 多 功夫 ,并且 车 削 过程 须 始 终 高度 精力 集 中 ,才 能及 时发 现误 差 和故 障 。 ( 3 )在 精 车 阶 段 常 出现 各 线 齿 厚 和 齿 槽 宽 不
一
— 一l s .
向 的后 角 为 a O =( 3 0 - 5 0 )+ 为蜗 杆 螺 旋升 角 ,背 向
、
加 工 多线 蜗 杆 过 程 中所 存 在 的 问题
车削多线蜗杆是 车削螺纹 中较难 的一个 课题 ,在 实 际加工多线蜗杆 的过程 中容易 出现 以下 几个 问题 。 ( 1 )车 削 时 , 由于 蜗 杆齿 形 较 深 ,切 削 力 过
一 躁甘 躲 舶 一
躁 ∞躲 奸 L 0
蜗杆传动是一种常用的机械传动形式 ,广泛用 于轴线交叉的减速传动 中。在这种传动形式 中,蜗 杆 是 主动 件 ,所 以蜗 杆 的制 造精 度 直接 影 响 传 动 精 度 。下文 就对 多 线 蜗 杆加 工 过程 中所 存 在 的问 题 进 行 分 析 ,并 提 出解 决 的措 施 ,以提 高 加工 质 量 和 加 工 效率 。
别高 ;第二 ,由于车刀靠两侧刀刃精车两侧齿面 , 车 刀 的 前 端 刀 刃 不 能 进 行 切 削 ,螺 纹 槽 底 无 法 加 工 。对 模 数 不 太 大 ( 3 - 5 mm )的 三 线 蜗 杆 ,要 在 车
刀 前 刀 面上 开 断 屑槽 非 常 困难 。通 过 实 际应 用 ,采 用 两 把精 车 刀 车 削 的方法 比较 理想 , 即分车 左 侧 面
产 生 振动 和 扎 刀现 象 。若 在 半精 车 刀 和精 车 刀 两 刀 刃 上 开着 卷 屑槽 的话 ,第 一 ,这 对 磨 刀技 能 要 求 特
- 1、下载文档前请自行甄别文档内容的完整性,平台不提供额外的编辑、内容补充、找答案等附加服务。
- 2、"仅部分预览"的文档,不可在线预览部分如存在完整性等问题,可反馈申请退款(可完整预览的文档不适用该条件!)。
- 3、如文档侵犯您的权益,请联系客服反馈,我们会尽快为您处理(人工客服工作时间:9:00-18:30)。
浅谈多头蜗杆的快速车削
摘要:本文是作者通过自身多年的生产实践,积累了丰富的经验而撰写。
在实际生产过程中,经常会遇到多头蜗杆的车削工作。
多头蜗杆在工艺上属复杂零件加工。
在加工过程中,应对其结构进行工艺分析,并根据其加工特点和加工方法进行分析探讨。
经过生产实践,能够对多头蜗杆采取有效措施和进行技术革新,使其加工顺利进行,从而达到零件图纸要求和各项技术指标要求,这对保证产品的质量,提高生产效率具有重要意义。
关键词:多头蜗杆;加工方法;生产效率
引言:随着科技和生产的发展,常用于作减速运动的传动机构中出现的多头蜗杆零件越来越多。
多头蜗杆由于导程大、齿形深、切削面积大、导程角也大,故增加了切削难度,所以其生产效率往往受到了很大影响。
为此,应对多头蜗杆的加工工艺性进行有理有据的技术分析,选用合理和先进的工艺方法,为今后在加工多头蜗杆时奠定了坚实的基础,从而为保证产品的质量,提高企业的生产效率提供了实际性和创造性的理论依据。
正文:
一.多头蜗杆的工艺问题分析
1.蜗杆的分类
米制蜗杆的齿形角为20°,有轴向直廓蜗杆和法向直廓蜗杆两种。
轴向直廓蜗杆的齿形在轴平面内为直线,在法平面内为曲线,在端平面内为阿基米德螺旋线,又称为ZA蜗杆或阿基米德蜗杆。
法向直廓蜗杆的齿形在法平面内为直线,在轴平面内为曲线,又称为ZN蜗杆。
2.多头蜗杆的分头方法
沿两条或两条以上,在轴向等距分布的螺旋线所形成的蜗杆叫多头蜗杆。
车多头蜗杆,主要是解决分头方法,根据多头蜗杆形成原理分头方法有轴向分头法和圆周分头法两类。
3.多头蜗杆的加工方法分析
多头蜗杆惯用的加工方法伴有如下几个难题:第一在车削过程中常被“多次循环分头,依次逐面车削”所困扰。
每次用百分表也好,用块规也好,都要费很
多事,并且车削过程须始终高度精力集中及时发现误差和故障。
由于多数频繁的分头,频繁的记忆常使工人感到非常疲惫,而频繁误差机率越高。
第二,在精车阶段常出现各头齿厚和齿槽宽不一致相差较多,一时难以找出哪头余量多,哪头余量少,即使找出有又难以处理,因为动齿厚又牵扯齿槽宽度,齿厚虽有余量可是这里的齿槽宽却没了余量,导致零件不合格。
第三,传统的车削方法生产效率缓慢,耗用工时多,工人劳动强度大,造成生产成本高。
二.多头蜗杆课题的选择。
1.多头蜗杆课题的工艺要求
(1).轴向或法向齿厚,齿形必须符合图样要求。
(2).各头的齿厚、齿槽宽必须相应统一在规定的精度之内。
(3).蜗杆径向圆跳动应在允许范围内。
2.多头蜗杆的工艺分析
多头蜗杆的车削是车削出各头齿槽的过程,蜗杆分头有轴向和圆周向若干种分法。
下面以车削Z=3.Mx=6蜗杆为例.
车削方法:在粗车、半精车、精车分别车削每头齿槽宽的时候必须要记住背吃刀量值,中、小滑板刻度数并且相同。
左右切削法进给量相等,进刀次数必须相等,车削各齿侧面要通过频繁的循环分头来逐一完成,其目的是为了各头的齿距一致。
齿距一致的标志是各头齿厚,齿槽宽都要在图样给定的偏差之内。
而往往最终的齿厚、齿槽宽偏差由于各元误差的原因,仍不能确保。
最后还要用移动中小滑板修正车削才得以实现偏差要求。
多元因素产生误差,如车刀的磨损、车刀与工件的位移、中小滑板的间隙等,一般是无规律发生,而发生往往是在车过之后, 误差的控制只能依靠工人高技能的表现。
3.快速车削方法
循环分头逐槽、逐面依次车削,尤其对于多头较大模数蜗杆更具其优越性。
仍分粗车、半精车、精车步骤,但具体做法不同。
(1)粗车先按多头蜗杆的齿距分头划线。
可用三角螺纹车刀在工件外圆以背吃刀量0.05~0.01mm划出痕迹线1,再轴向用小滑板分别移动一个齿距px划线2、3,之后再轴向移动一个齿顶宽sax =0.843mx+0.6mm划线为第4头,再分
别轴向移动一个齿距划出第5、6头结束。
这时可要在划出的齿槽线内将各槽粗车出。
各槽车削只需摇动中小滑板进给量车出,或用切槽刀粗车,或用蜗杆粗车刀车削到线为止。
(2)半精车确定某齿厚有0.6mm(sx+0.6)余量,并将该齿左侧设为1,先半精车留0.15mm(sx +0.45) 余量。
表面粗糙度控制在Ra=3.2~6.3m以内。
用齿厚游标尺测检。
继而车削该槽侧面2,余量控制用单针测检掌握齿槽宽px-0.3mm ,再车侧面3留0.15mm余量,此时①齿齿厚余量是sx +0.3mm.,在测检时如果图样是轴向齿厚标注尺寸须换算成法向尺寸测检,还有螺旋角造成的测检误差,单针测检时也要加进一个修正值,这里不再详述有关计算。
以此方法推算下面各齿,并加将各头槽底直径车至图样尺寸可完成半精车,并可消除粗车是产生的齿距、齿厚和齿槽宽误差而达到余量均匀。
(3)精车确定某齿厚有0.3mm余量(sx +0.3mm),并将该齿左侧设为1精车成,该齿厚控制在(sx +0.15mm),以侧面为1为基准精车侧面2,控制分度圆直径完成槽1车削。
继而精车齿侧3。
控制齿①齿厚,这是精车成第一个头的齿厚。
其后各头齿厚及齿槽宽这样依次车下去就可以了,测检手段同半精车。
4.其他
(1)测量中径M值的确定:蜗杆径向X量针测检M值它有两种意义,其一是用相关公式直接控制分度圆直径值:其二是由图样给定的轴向齿厚偏差换算成径向量针测检偏差值间接控制厚偏差。
确切地说两者都是通过控制齿槽宽以达到控制齿厚的目的。
而对于多头较大模数蜗杆来讲,如果不加用其他量具而可测的只能是单头蜗杆,对于多头蜗杆由于量针直径和测量跨度的问题,只是理论上可行实际上非常困难。
因此可用单针测检加齿厚游标卡尺使用于半精车和精车过程:
(2)这种工艺之所以快速是因为次序简捷,省去了频繁循环分线,确定以1侧面为基准逐槽、逐齿分别车削,测检控制偏差的方法,很像车削单头蜗杆一样专车一齿一槽。
对于车削过程中误差影响因素都能及时发现,断定准确而及时处理。
车削过程中,中小滑板刻度值、背吃刀量、次数不必须频繁记录和一致,具体的背吃刀量由测检该处的结果给定。
(3)对性的冷却润滑液
在车削多头蜗杆时,冷却润滑液能起的作用较大。
冷却润滑液选用的正确,能减少切屑变形,降低切削力,同时能提高加工精度和刀具的耐用度。
结束语:
在生产实际加工过程中,生产时间=加工时间+辅助时间,通过这种加工方法很显然生产时间减少,在相同生产量的情况下,以这种多头蜗杆加工方法生产率会有很大的提高。
因此在蜗杆加工生产中合理的进行技术革新可以在一定程度
上,保证工件质量,降低成本,提高生产效率,减少消耗,为企业创造一定的经济效益。