在线检测与误差补偿技术(精密加工)
机床加工精度检测与补偿技术研究
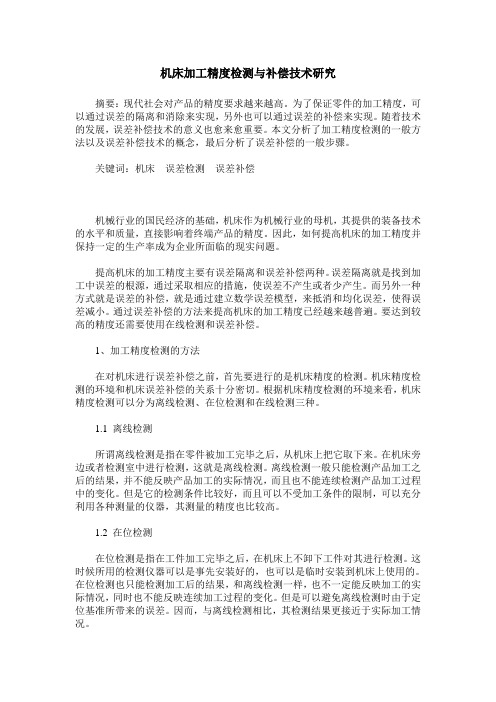
机床加工精度检测与补偿技术研究摘要:现代社会对产品的精度要求越来越高。
为了保证零件的加工精度,可以通过误差的隔离和消除来实现,另外也可以通过误差的补偿来实现。
随着技术的发展,误差补偿技术的意义也愈来愈重要。
本文分析了加工精度检测的一般方法以及误差补偿技术的概念,最后分析了误差补偿的一般步骤。
关键词:机床误差检测误差补偿机械行业的国民经济的基础,机床作为机械行业的母机,其提供的装备技术的水平和质量,直接影响着终端产品的精度。
因此,如何提高机床的加工精度并保持一定的生产率成为企业所面临的现实问题。
提高机床的加工精度主要有误差隔离和误差补偿两种。
误差隔离就是找到加工中误差的根源,通过采取相应的措施,使误差不产生或者少产生。
而另外一种方式就是误差的补偿,就是通过建立数学误差模型,来抵消和均化误差,使得误差减小。
通过误差补偿的方法来提高机床的加工精度已经越来越普遍。
要达到较高的精度还需要使用在线检测和误差补偿。
1、加工精度检测的方法在对机床进行误差补偿之前,首先要进行的是机床精度的检测。
机床精度检测的环境和机床误差补偿的关系十分密切。
根据机床精度检测的环境来看,机床精度检测可以分为离线检测、在位检测和在线检测三种。
1.1 离线检测所谓离线检测是指在零件被加工完毕之后,从机床上把它取下来。
在机床旁边或者检测室中进行检测,这就是离线检测。
离线检测一般只能检测产品加工之后的结果,并不能反映产品加工的实际情况,而且也不能连续检测产品加工过程中的变化。
但是它的检测条件比较好,而且可以不受加工条件的限制,可以充分利用各种测量的仪器,其测量的精度也比较高。
1.2 在位检测在位检测是指在工件加工完毕之后,在机床上不卸下工件对其进行检测。
这时候所用的检测仪器可以是事先安装好的,也可以是临时安装到机床上使用的。
在位检测也只能检测加工后的结果,和离线检测一样,也不一定能反映加工的实际情况,同时也不能反映连续加工过程的变化。
但是可以避免离线检测时由于定位基准所带来的误差。
多轴精密机床误差测量、辨识与补偿综述

ErrorMeasurement,IdentificationandCompensationof Multi-axisPrecisionMachineTool
DuYinfei ShenWenjie CaiShu
Abstract:Theapplicationofmulti-axisprecisionmachinetoolsismoreandmoreextensive,andthenumberis increasingThispapertakesthemeasurement,modelingandcompensationofthecombinederrorofmulti-axispre cisionmachinetoolsasthestartingpoint,anddiscussestheachievementsofthemachinetoolerrorcompensation andtheexistingproblemsinChina Keywords:multi-axisprecisionmachinetool;errormeasurement;errorcompensation
1 单误差源测量方法 该方法是利用测量仪器直接检测出机床每个运
动轴的各单项误差,需要配备不同的测量设备。目 前利用双频激光干涉仪通过与各种光学镜组件配合 使用,可以检测机床的定位、直线度、角度、垂直度等 多种单项几何误差。虽然先进的测量设备可以直接 准确的测量出机床的精度,但是需要对每项误差逐
94
该方法通过对机床工作空间内指定点的位置误 差进行测量,运用测量模型对测量点的综合误差进 行辨识分 解,间 接 得 到 机 床 各 单 项 误 差 的 离 散 值。 按照机床各轴运动形式的不同,可分为平动轴综合 误差测量辨识法和回转轴综合误差测量辨识法。目 前对平动轴综合误差测量辨识的研究较多,出现了 各种各样的方法。按使用的仪器和测量的方式可分 为:光栅阵列法、双球杆测量法、一维球列法、平面正 交光栅测量法、激光球杆仪法、圆测法、三维步距规 法、体对角线法、位移线法等。这些测量辨识的方法 凝聚了许多国内外专家的心血和智慧。回转轴综合 误差测量辨识是针对四轴和五轴联动的多轴数控机 床,用于辨识机床的运动轴做回转运动时引起的个 自由度方向的几何误差。对回转轴综合误差测量辨 识的研究 始 于 近 十 几 年,还 处 于 初 步 探 索 的 阶 段。 研究者在误差的建模,误差源测量方法及原理以及 模型辨识等方面都取得了丰硕的成果。
精密加工
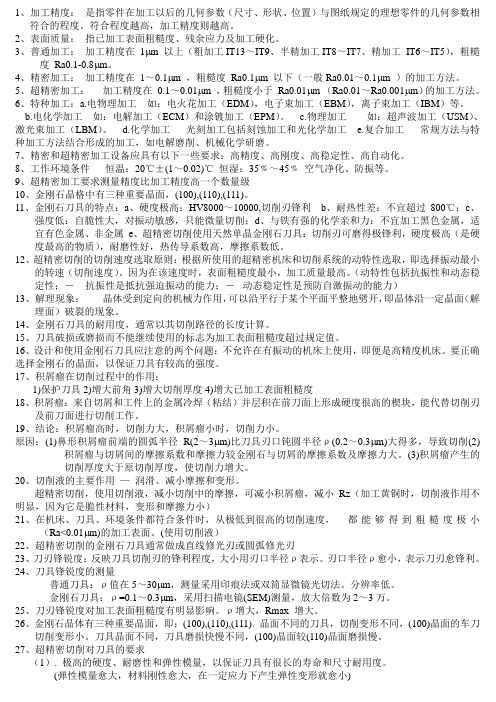
1、加工精度:是指零件在加工以后的几何参数(尺寸、形状、位置)与图纸规定的理想零件的几何参数相符合的程度。
符合程度越高,加工精度则越高。
2、表面质量:指已加工表面粗糙度、残余应力及加工硬化。
3、普通加工:加工精度在1μm 以上(粗加工IT13~IT9、半精加工IT8~IT7、精加工IT6~IT5),粗糙度Ra0.1-0.8μm。
4、精密加工:加工精度在1~0.1μm ,粗糙度Ra0.1μm 以下(一般Ra0.01~0.1μm )的加工方法。
5、超精密加工:加工精度在0.1~0.01μm ,粗糙度小于Ra0.01μm (Ra0.01~Ra0.001μm)的加工方法。
6、特种加工:a.电物理加工如:电火花加工(EDM),电子束加工(EBM),离子束加工(IBM)等。
b.电化学加工如:电解加工(ECM)和涂镀加工(EPM)。
c.物理加工如:超声波加工(USM)、激光束加工(LBM)。
d.化学加工光刻加工包括刻蚀加工和光化学加工e.复合加工常规方法与特种加工方法结合形成的加工,如电解磨削、机械化学研磨。
7、精密和超精密加工设备应具有以下一些要求:高精度、高刚度、高稳定性、高自动化。
8、工作环境条件恒温:20℃±(1~0.02)℃恒湿:35﹪~45﹪空气净化、防振等。
9、超精密加工要求测量精度比加工精度高一个数量级10、金刚石晶格中有三种重要晶面,(100),(110),(111)。
11、金刚石刀具的特点:a、硬度极高:HV8000~10000,切削刃锋利b、耐热性差:不宜超过800℃;c、强度低:自脆性大,对振动敏感,只能微量切削;d、与铁有强的化学亲和力:不宜加工黑色金属,适宜有色金属、非金属e、超精密切削使用天然单晶金刚石刀具:切削刃可磨得极锋利,硬度极高(是硬度最高的物质),耐磨性好,热传导系数高,摩擦系数低。
12、超精密切削的切削速度选取原则:根据所使用的超精密机床和切削系统的动特性选取,即选择振动最小的转速(切削速度)。
精密加工技术期末复习资料
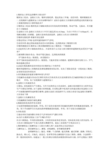
1.精密加工研究包括哪些主要内容?精密加工机床,金刚石刀具,精密切削机理,稳定的加工环境,误差补偿,精密测量技术二.实现精密与超精密加工应具备哪些条件?试结合金刚石刀具精密切削简述切削用量对加工质量的影响及主要控制技术?①精密加工机床-精密机床主轴轴承要求具有很高的回转精度,转动平稳,无振动,其关键在于主轴轴承②金刚石刀具-金刚石刀具的刀口半径只能达到0.1-0.3/um。
当刃口半径小于0.01um时,必须解决测量上的难题。
金刚石晶体的晶面选择。
金刚石刀具刃口的锋利性③精密切削机理-掌握其变化规律④稳定的加工环境-包括恒温防振和空气净化⑤误差补偿-通过消除或抵消误差本身的影响,达到提高加工精度的目的⑥精密测量技术-精密加工要求测量精度比加工精度高一个数量级3.试述常用几种主轴轴承的特点,并说明为什么目前大部分精密和超精密机床采用空气轴承?①液体静压轴承-特点:转动平稳无振动,达到较高的刚度空气轴承-特点:刚度低,承受载荷小②空气轴承造成的热变形小,刚度低,只能承受较小的载荷,超精密切削时切削力小,空气轴承能满足要求4.试述在线检测和误差补偿技术在精密加工中的作用精密和超精密加工的精度是依靠检测精度来保证的,而为了消除误差进一步提高加工精度,必须使用误差补偿技术5.常用微量进给装置有哪些种类与作用?①机械传动或液压传动式②弹性变形式③热变形式④流体膜变形式⑤磁致伸缩式⑥电致伸缩式作用:为了实现精密与超精密加工6.金刚石刀具破损形式①裂纹:结构缺陷可产生裂纹,另外当切屑经过刀具表面时,金刚石收到循环应力的作用也可产生裂纹②碎裂:由于金刚石材料较脆,在切削过程中收到冲击和振动都会使金刚石刀刃产生细微的解理形成碎裂③解理:金刚石晶面方面选择不当,切削力容易引起金刚石的解理,刀具寿命下降7.金刚石刀具磨损形式①机械磨损②破损③碳化磨损8.微量进给机构的作用及类型①电致伸缩微量进给装置,作用:用于误差在线补偿②机械结构弹性变形微量进给装置,作用:用于手动操作③压电或电致伸缩微量进给装置,作用:用于实现自动微量进给9.导轨类型①滚动导轨②液体静压导轨③气浮导轨和空气静压导轨10.为什么精密切削加工会产生碾压作用?在刃口圆弧处,不同的切削深度,刀具的实际前角是变化的,实际前角为较大的负前角,在刀具刃口圆弧处将产生很大的挤压摩擦作用,被加工表面将产生残余压应力1.精密磨削加工按磨料加工大致分为哪几类?试述其特点及适用场合①磨料加工,固结磨料加工:磨削,砂轮磨削,砂带磨削研磨等游离磨料加工:抛光,研磨:干式研磨,湿式研磨,磁式研磨。
精密和超精密加工技术复习思考题答案
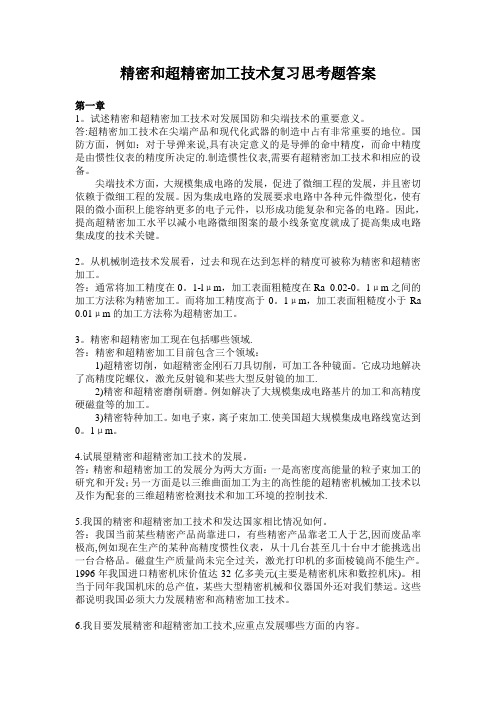
精密和超精密加工技术复习思考题答案第一章1。
试述精密和超精密加工技术对发展国防和尖端技术的重要意义。
答:超精密加工技术在尖端产品和现代化武器的制造中占有非常重要的地位。
国防方面,例如:对于导弹来说,具有决定意义的是导弹的命中精度,而命中精度是由惯性仪表的精度所决定的.制造惯性仪表,需要有超精密加工技术和相应的设备。
尖端技术方面,大规模集成电路的发展,促进了微细工程的发展,并且密切依赖于微细工程的发展。
因为集成电路的发展要求电路中各种元件微型化,使有限的微小面积上能容纳更多的电子元件,以形成功能复杂和完备的电路。
因此,提高超精密加工水平以减小电路微细图案的最小线条宽度就成了提高集成电路集成度的技术关键。
2。
从机械制造技术发展看,过去和现在达到怎样的精度可被称为精密和超精密加工。
答:通常将加工精度在0。
1-lμm,加工表面粗糙度在Ra 0.02-0。
1μm之间的加工方法称为精密加工。
而将加工精度高于0。
1μm,加工表面粗糙度小于Ra 0.01μm的加工方法称为超精密加工。
3。
精密和超精密加工现在包括哪些领域.答:精密和超精密加工目前包含三个领域:1)超精密切削,如超精密金刚石刀具切削,可加工各种镜面。
它成功地解决了高精度陀螺仪,激光反射镜和某些大型反射镜的加工.2)精密和超精密磨削研磨。
例如解决了大规模集成电路基片的加工和高精度硬磁盘等的加工。
3)精密特种加工。
如电子束,离子束加工.使美国超大规模集成电路线宽达到0。
1μm。
4.试展望精密和超精密加工技术的发展。
答:精密和超精密加工的发展分为两大方面:一是高密度高能量的粒子束加工的研究和开发;另一方面是以三维曲面加工为主的高性能的超精密机械加工技术以及作为配套的三维超精密检测技术和加工环境的控制技术.5.我国的精密和超精密加工技术和发达国家相比情况如何。
答:我国当前某些精密产品尚靠进口,有些精密产品靠老工人于艺,因而废品率极高,例如现在生产的某种高精度惯性仪表,从十几台甚至几十台中才能挑选出一台合格品。
超精密制造技术论文
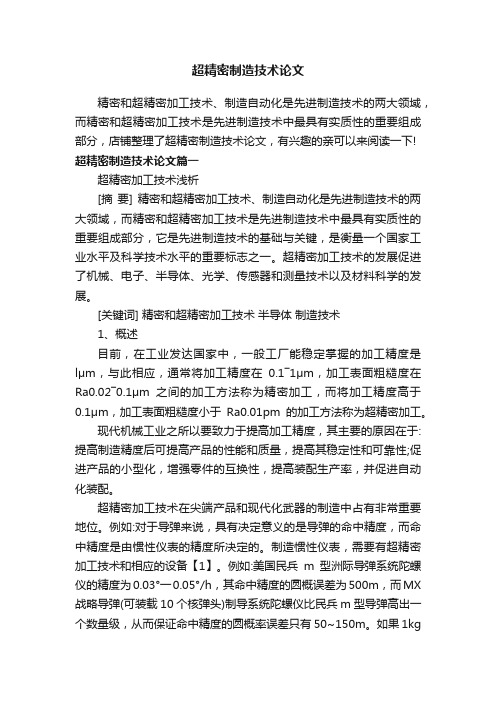
超精密制造技术论文精密和超精密加工技术、制造自动化是先进制造技术的两大领域,而精密和超精密加工技术是先进制造技术中最具有实质性的重要组成部分,店铺整理了超精密制造技术论文,有兴趣的亲可以来阅读一下! 超精密制造技术论文篇一超精密加工技术浅析[摘要] 精密和超精密加工技术、制造自动化是先进制造技术的两大领域,而精密和超精密加工技术是先进制造技术中最具有实质性的重要组成部分,它是先进制造技术的基础与关键,是衡量一个国家工业水平及科学技术水平的重要标志之一。
超精密加工技术的发展促进了机械、电子、半导体、光学、传感器和测量技术以及材料科学的发展。
[关键词] 精密和超精密加工技术半导体制造技术1、概述目前,在工业发达国家中,一般工厂能稳定掌握的加工精度是lμm,与此相应,通常将加工精度在0.1―1μm,加工表面粗糙度在Ra0.02―0.1μm之间的加工方法称为精密加工,而将加工精度高于0.1μm,加工表面粗糙度小于Ra0.01pm的加工方法称为超精密加工。
现代机械工业之所以要致力于提高加工精度,其主要的原因在于:提高制造精度后可提高产品的性能和质量,提高其稳定性和可靠性;促进产品的小型化,增强零件的互换性,提高装配生产率,并促进自动化装配。
超精密加工技术在尖端产品和现代化武器的制造中占有非常重要地位。
例如:对于导弹来说,具有决定意义的是导弹的命中精度,而命中精度是由惯性仪表的精度所决定的。
制造惯性仪表,需要有超精密加工技术和相应的设备【1】。
例如:美国民兵m型洲际导弹系统陀螺仪的精度为0.03°一0.05°/h,其命中精度的圆概误差为500m,而MX 战略导弹(可装载10个核弹头)制导系统陀螺仪比民兵m型导弹高出一个数量级,从而保证命中精度的圆概率误差只有50~150m。
如果1kg重的陀螺转子,其质量中心偏离其对称轴0.5nm,则会引起100m的射程误差和50m的轨道误差。
惯性仪表中有许多零件的制造精度都要求达到小于微米级。
LECTURE2-超精密车削
超精密加工技术广东工业大学机电工程学院魏昕一、概述¾超精密加工技术的内涵¾超精密加工技术的地位与作用¾超精密加工技术所涉及的技术领域¾超精密加工技术的现状与发展趋势一、概述1. 超精密加工技术的内涵精密加工技术:加工精度1—0.1μm,表面粗糙度Ra <0.1 μm的加工技术;超精密加工技术:加工精度<0.1μm,表面粗糙度Ra <0.02μm的加工技术;纳米加工技术:加工精度达0.001μm(1nm),表面粗糙度Ra <0.005 μm的加工技术。
随着加工技术的不断发展,超精密加工的技术一、概述2、超精密加工技术的地位与作用(1)超精密加工技术是实现现代制造业发展目标(提高机电产品的性能、质量和发展高新技术)的重要手段。
例如,集成电路的集成度。
(2)超精密加工技术已成为国际竞争中取得成功的关键技术。
所能达到的精度水平代表了一个国家的制造业能力和水平。
(3)精密工程、微细工程和纳米技术是现代制造技术的前沿。
/序超精密机械精度要求1导弹、飞机的惯性导航系统中的气浮陀及其马达轴承尺寸精度、圆度、圆柱度要求达到亚微米级2人造卫星仪表轴承表面粗糙度达到1纳米,圆度、圆柱度达纳米级3激光陀螺反光镜表面粗糙度达纳米,平面度达0.05微米4精确制导仪表零件精度达纳米级,若其陀螺转子轴线偏离0.5纳米,就会引起100米左右射程误差5计算机硬盘驱动器、光盘、复印机的精密零件精度达100纳米6微电子芯片刻线机刻线宽度在50纳米以下7基因操作机械移动距离在纳米级,移动精度在0.1纳米(原子尺度)现代超精密机械对精度的要求超精密加工是尖端技术产品发展不可缺少的关键加工手段关系到现代飞机、潜艇、导弹性能和命中率的惯性陀螺框架;激光核聚变用的反射镜;大规模集成电路的各种基片;计算机磁盘基底及复印机磁鼓;各种高精度的光学元器件;各种硬盘及记忆体的衬底等。
×一、概述3、超精密加工技术所涉及的技术领域(1)加工技术即加工方法与加工机理。
答案精密加工课后习题—黄
.
.
液压喷砂法,用高压泵打出流量为20L/min、压力为150Pa的冷却液,进入喷嘴的漩涡室时,形成低压,从
边孔中吸入碳化硅或刚玉等磨粒及空气,与冷却液形成混合液,并以高速喷嘴喷射到转动的砂轮上。
晶面。
网面最小单元不同,100是正方形,110为矩形,111为三角形,网面密度100:110:111为1:1.414:2.308
网面距不同:100与110为均匀分布,分别为D/4=0.089mm,sqrt(2)D/4=0.126mm,111为宽窄交替宽为
sqrt(3)D/4=0.154mm,窄为sqrt(3)D/12=0.1051mm
光刃的长度对表面加工质量效果不大,对刀不易
圆弧刃容易对刀,半径可取R=2~5mm。可加工高质量的超光滑表面,缺点是刀具制造复杂
2-19试述金刚石刀具的前面应选哪个晶面
选用100面,111面硬度高,而微观破损强度并不高,研磨加工困难。
选用100面的原因:
1)100面耐磨性高于110面,刀具使用寿命长
2)100面微观破损强度高于110面,产生崩刃的机会小
解理现象:111面的面网宽面距比100和110都大,最易解理。
好磨难磨方向可用图表示:
.
.
好磨方向
难磨方向
100磨削率:111磨削率:110磨削率=5.8:1:12.8
2-15金刚石晶体有哪些定向方法?
1)人工目测定向2)X射线定向3)激光定向
2-16试述金刚石晶体的激光定向原理和方法。
利用金刚石在不同晶面方向上,晶体结构不同,对激光反射形成的衍射图像不同而进行。
小后面与加工表面间的摩擦
2-10工件材料的晶体方向对切削变形和加工表面质量的影响如何?
现代加工工艺理论及技术考题及答案_08级_
说明:本资料由Coofish倾力制作,使用此资料时请心存感激!机械学子,心心相连!现代加工工艺理论及技术考题及答案(08级)考试题:80分 小论文:20分一、名词解释(10分)1、随机误差:没有掌握误差规律的加工误差(也有可能掌握了大小而未掌握方向,或者掌握了方向而未掌握大小),它们不能用代数和进行综合,只能用数理统计方法来处理。
2、表面质量:零件表面质量的含义,概括来说就是零件的表面完整性。
具体地说:(1)表面纹理——加工表面的微观几何形状。
(2)表面冶金变化——表面层金属的力学物理性能和化学性能3、CIM:是指用计算机,通过信息集成、过程集成、企业集成,实现现代化的生产制造,求得企业的总体效益的一种先进制造理念。
4、工艺系统刚度:工艺系统抵抗变形的能力,其基本概念是指垂直于待加工表面的切削分力Py与工件在Py方向的位移y之间的比值。
5、切削颤振:在切削过程中,当受到外界或系统本身的某些瞬时的、偶然的干挠力的触发,在系统中产生振动,由振动过程中本身所产生的周期性干挠力所引起的振动。
二、简答题(40分)1、什么叫主轴的回转运动误差?当滚动轴承滚道有形状误差时对车床车削(外圆面)和镗削(内圆面)表面的加工有何影响?答:(1)机床主轴工作时,除绕实际回转轴线转动外,还存在着实际回转轴线对于回转轴线的径向跳动、轴向跳动和摆动,后者统称为机床主轴的误差运动,这个误差运动使主轴产生回转误差。
(2)车削情况:因主轴带动工件回转,刀具无回转运动,切削力方向不变,即误差敏感方向不变,故主轴轴颈有椭圆度误差时,主轴产生径向跳动会直接将椭圆度误差反映在工件上。
而轴承内孔有椭圆度误差时,对工件的影响很小。
镗削情况:因主轴带动镗刀杆回转,工件无回转运动,切削力方向随主轴的回转而变化,误差敏感方向也随切削力方向变化而变化,故轴承内孔的形状精度对工件的形状有影响,而主轴颈有椭圆度误差却对工件的影响很小。
2、纳米制造的实质是什么?主要工艺方法有哪些?答:(1)实质:由于原子间的距离为0.1~0.3nm,纳米级加工实际上已经到了加工精度的极限。
球面镜数控加工中安装误差在线检测及补偿
- 1、下载文档前请自行甄别文档内容的完整性,平台不提供额外的编辑、内容补充、找答案等附加服务。
- 2、"仅部分预览"的文档,不可在线预览部分如存在完整性等问题,可反馈申请退款(可完整预览的文档不适用该条件!)。
- 3、如文档侵犯您的权益,请联系客服反馈,我们会尽快为您处理(人工客服工作时间:9:00-18:30)。
用测微仪(测头传感器)测量 工件形状误差和回转轴系运动 误差; 起点电路提供一个作为角度位 臵的起始点信号。
2013-8-10
分离工件和轴系误差的转位法有三种:
(1) 反转法
测量时只作一次转位(工件与测头对轴系回转180°), 共测得两组数据 V1 (i ) M1 (i ) S (i )
2013-8-10
第1节 概述 三、误差补偿技术
4.误差补偿系统的组成
1)误差信号的检测 2)误差信号的处理 3)误差信号的建模 建模是找出工件加工误差与 在补偿作用点上补偿控制量 之间的关系。 4)补偿控制 根据所建立的误差模型和实 际加工过程,用计算机计算 欲补偿的误差值,输出补偿 控制量。 5)补偿执行机构 补偿执行机构多用微进给机 2013-8-10 构完成。
i 采样序号, 1 n; i ~
(1) (2) (3)
V0 ( i )、V2 ( i )、V1 ( i ) 测头传感器分别在0 、+ 、- 位置所测得的信号; 0
M ( i ) 测头传感器所测得回转 轴系运动误差;
S ( i ) 测头传感器所测得信号 中工件形状误差部分。
V2 ( i ) M 2 ( i ) S ( i )
式中
V1 ( i )、V2 ( i ) 分别为测头传感器两次 所测得的两组信号 M 1 ( i )、M 2 ( i ) 分别为两次测得的回转 轴系运动误差
S ( i ) 测头传感器所测得信号 中工件形状误差部分
计算机控制系统
1
2
3
4
5
误差补偿系统组成示意图 1-误差信号检测 2-误差信号处理 3-误差信号建模 4-补偿控制 5-补偿执行机构
第1节 概述 三、误差补偿技术
5.误差补偿技术的发展 1)预报型补偿
预报补偿控制(Fore-casting Compensatory Control-FCC)技术, 利用在线随机建模理论、先进的传感技术、计算机技术、 微位移技术等,对误差进行建模和预报,对动态误差进 行实时补偿。 2)综合型补偿 对工件尺寸、形状和位臵误差同时进行综合补偿,其中 包括对尺寸、形状和位臵一种误差中的多项误差进行综 合补偿。
S ( i360 0 / m) 测头传感器在某个位置所测得的一组信号中工件形状误差部分;
i 测量位置序号, 1 m i= ~
当m很大时,S i ( ) 的平均值忽略不计,可得回转轴系平均运动 误差 M ( ) V ( )/ m i 闭合等角转位法可用于测量径向和轴向运动误差。测量工作 量大,不能测得高次谐波,不能用于实时控制。 2013-8-10
4)在线检测大都用非接触传感器,对传感器的性能要求较高;
5)一般是自动运行,形成在线检测系统。
在线检测类型
1)直接检测系统:直接检测工件的加工误差,并补偿 2)间接检测系统:检测产生加工误差的误差源,并补偿 2013-8-10
第1节 概述 三、误差补偿技术
1.误差补偿的概念 在机械加工中出现的误差采用修正、抵消、均化、 “钝化”等措施使误差减小或消除。
3.误差补偿过程
1)反复检测出现的误差并分析,找出规律,找出影 响误差的主要因素,确定误差项目。
2)进行误差信号的处理,去除干扰信号,分离不需 要的误差信号,找出工件加工误差与在补偿点的补 偿量之间的关系,建立相应的数学模型。 3)选择或设计合适的误差补偿控制系统和执行机构, 以便在补偿点实现补偿运动。 4)验证误差补偿的效果,进行必要的调试,保证达 到预期要求。
V1 ( x i ) M 1 ( x i ) S ( x i )
V2 ( x i ) M 2 ( x i ) S ( x i )
的两组信号; 式中 V1 ( x i )、V2 ( x i ) 分别为测头两次所测得 M 1 ( x i )、M 2 ( x i ) 分别为两次测得的机床 直线运动误差; S ( x i ) 测头所测得信号中工件 形状误差部分;
第1节 概述 三、误差补偿技术
钝化法
在车削加工时,由于导轨在垂直面上的纵向直线度会造成刀尖中 心高位臵的变化,影响工件的加工精度。 a图为刀具安装在水平位臵,若刀尖位臵下降h值时,工件在半径 上尺寸会增大 R h ;(误差迟钝方向) b图为刀具安装在垂直位臵,若刀尖位臵下降h值时,工件在半径 2013-8-10 上尺寸会增大 R h。(误差敏感方向)
2.在位检测
工件加工完毕后,在机床上不卸下工件的情况下进行检 测。可避免离线检测由于定位基准所带来的误差。
3.在线检测(主动检测或动态检测)
工件在加工过程中的同时进行检测。能反应实际加工情 况,难度较大。
2013-8-10
第1节 概述 二、加工精度的检测
在线检测特点
1)能够连续检测加工过程中的变化,了解在加工过程中误差 分布和发展; 2)检测结果能反映实际加工情况; 3)在线检测的难度较大;
第1节 概述 三、误差补偿技术
2.误差补偿的类型
(3)单项与综合误差补偿 综合误差补偿是同时补偿几项误差,比单项误差补 偿要复杂,但效率高、效果好。 (4)单维与多维误差补偿 多维误差补偿是在多坐标上进行误差补偿,难度和 工作量都比较大,是近几年来发展起来的误差补偿技 术。
2013-8-10
第1节 概述 三、误差补偿技术
第1节 概述 三、误差补偿技术
2.误差补偿的类型 (1)实时与非实时误差补偿 实时误差补偿(在线检测误差补偿或动态误差补偿): 加工过程中,实时进行误差检测,并紧接着进行误差补 偿,不仅可以补偿系统误差,且可以补偿随机误差。 非实时误差补偿:只能补偿系统误差。 (2)软件与硬件误差补偿 软件补偿:通过计算机对所建立的数学模型进行运算 后,发出运动指令,由数控伺服系统完成误差补偿动作。 软件与硬件补偿的区分是看补偿信息是由软件还是硬件 产生的。软件补偿的动态性能好,机械结构简单、经济、 工作方便可靠。 2013-8-10
2013-8-10
第2节 在线检测与误差补偿方法 一、形状位臵误差的在线检测
1.外圆、孔类形状位臵误差的测量方法 三点法 在P129测量精密主轴的回转 误差中已经介绍。
2013-8-10
第2节 在线检测与误差补偿方法 一、形状位臵误差的在线检测
1.外圆、孔类形状位臵误差的测量方法 转位法 用圆光栅1测量角度位臵;
等式4和5右边虽相等,但实测数据不同,取平均值
M ( i 1 i ) M 1 ( i 1 i ) M 2 ( i 1 i ) / 2
可得一般式
n n M ( i 1 i ) M 1 ( i 1 i ) / n M 2 ( i 1 i ) / n / 2 i 1 i 1
2.平面类形状位臵误差的测量方法
平面类形状位臵误差主要针对超精密机床的导轨 直线度、工作台的台面直线度和平面度等。测量 中的关键问题是如何分离工件形状误差和机床直 线运动误差。
2013-8-10
第2节 在线检测与误差补偿方法 一、形状位臵误差的在线检测
2.平面类形状位臵误差的测量方法 (1)反转法 测量分两次进行,在第二次 测量时,工件转过180度,得 到两组数据
2013-8-10
由式(1)、(3)可得
V1 ( i 1 ) V0 ( i ) M ( i 1 ) M ( i ) M 1 ( i 1 i )
由式(1)、(2)可得
(4)
V0 ( i 1 ) V2 ( i ) M ( i 1 ) M ( i ) M 2 ( i 1 i ) (5)
提高加工精度的途径: 1)隔离和消除误差;
找出加工误差产生的根源,采取相应措施,使误差不产生或少 产生。
2)误差补偿
用相应的措施去“钝化“、抵消、均化误差,使误差减小。 2013-8-10
第1节 概述 二、加工精度的检测
精度检测按所处的环境分为:
1.离线检测
工件加工完毕后,从机床上取下,在机床旁或在检测室 中进行检测。检测条件较好,测量精度较高。
误差修正(校正):指对测量、计算、预测所得的误 差进行修正(校正); 误差分离:指从综合测量所得的误差中分离出所需的 单项误差;
误差抵消:指两个或更多个误差的相互抵消;
误差补偿:对一尺寸、形状、位臵差值的补足。
2013-8-10
第1节 概述 三、误差补偿技术
修正法
如图,为了提高丝杠 车床的螺距精度,通 过杠杆将修正尺和母 丝杠的螺母连接。修 正尺上的修正曲线使 母丝杠的螺母作附加 微小转动,从而使刀 架产生附加微小位移 来补偿母丝杠的螺距 误差。
i 采样点序号
i 采样点角度位置
若整个检测装臵的检测重复性好,则 可得
2013-8-10
M 1 ( i ) M 2 ( i ) M ( i )
S ( i ) V1 ( i ) V2 ( i ) / 2
M ( i ) V1 ( i ) V2 ( i ) / 2
由式(4)、(5)可得
M ( i 1 i ) V0 ( i 1 ) V0 ( i ) V1 ( i 1 ) V2 ( i ) / 2
对称转位法可用于测量径向和轴向运动误差,操作方便,但 2013-8-10 检测工作量较大,也不能用于实时控制。
第2节 在线检测与误差补偿方法 一、形状位臵误差的在线检测
(2)闭合等角转位法
每次转位时,测头不动,工件相对于轴系转 角,共测m个位 m 臵, 3600 ,可得m组数据
Vi ( ) M i ( ) S ( i 3600 / m )
Vi ( ) 测头传感器在某个位置 所测得的一组数据; M i ( ) 测头传感器在某个位置 所测得的一组回转轴系 运动误差;
2013 采样点x方向直线位置。