压铸模具设计规范
压铸模技术要求规笵
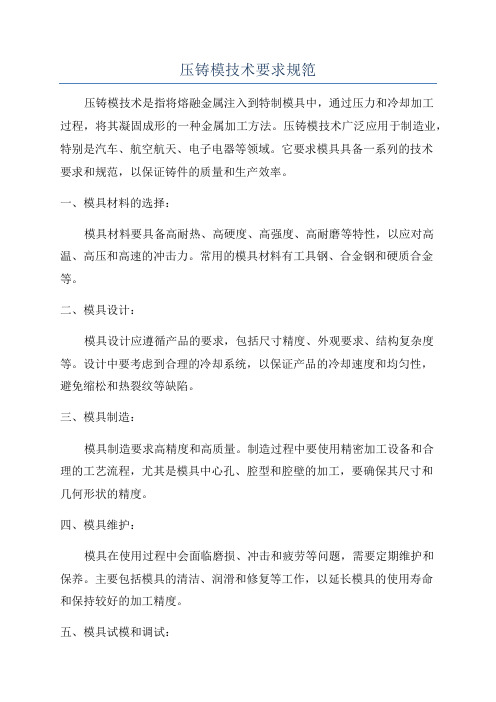
压铸模技术要求规笵压铸模技术是指将熔融金属注入到特制模具中,通过压力和冷却加工过程,将其凝固成形的一种金属加工方法。
压铸模技术广泛应用于制造业,特别是汽车、航空航天、电子电器等领域。
它要求模具具备一系列的技术要求和规范,以保证铸件的质量和生产效率。
一、模具材料的选择:模具材料要具备高耐热、高硬度、高强度、高耐磨等特性,以应对高温、高压和高速的冲击力。
常用的模具材料有工具钢、合金钢和硬质合金等。
二、模具设计:模具设计应遵循产品的要求,包括尺寸精度、外观要求、结构复杂度等。
设计中要考虑到合理的冷却系统,以保证产品的冷却速度和均匀性,避免缩松和热裂纹等缺陷。
三、模具制造:模具制造要求高精度和高质量。
制造过程中要使用精密加工设备和合理的工艺流程,尤其是模具中心孔、腔型和腔壁的加工,要确保其尺寸和几何形状的精度。
四、模具维护:模具在使用过程中会面临磨损、冲击和疲劳等问题,需要定期维护和保养。
主要包括模具的清洁、润滑和修复等工作,以延长模具的使用寿命和保持较好的加工精度。
五、模具试模和调试:模具制造完成后,需要进行试模和调试工作。
通过试模可以检验模具的结构和尺寸是否满足要求,是否有漏料、开裂等问题。
调试过程中需根据试模结果进行调整,以确保铸件的质量和尺寸精度。
六、模具应用:模具在使用中要对材料性能、温度、压力等参数进行合理控制,以避免过渡应力、热裂纹和变形等问题。
模具应用过程中,操作人员需要按照操作规程进行操作,并保持模具的清洁和正常维护。
七、模具质量管理:模具的质量管理是整个生产过程的重要环节。
要建立相应的质量管理体系,制定操作规程和质量标准,监控和控制每一个生产环节,确保产品的质量和生产效率。
总之,压铸模技术要求规范的模具材料选择、合理的模具设计、高精度的模具制造、定期的模具维护、严格的模具试模和调试工作、合理的模具应用和质量管理。
只有严格按照这些要求进行操作和管理,才能保证压铸模技术的高质量和高效率。
压铸件设计规范
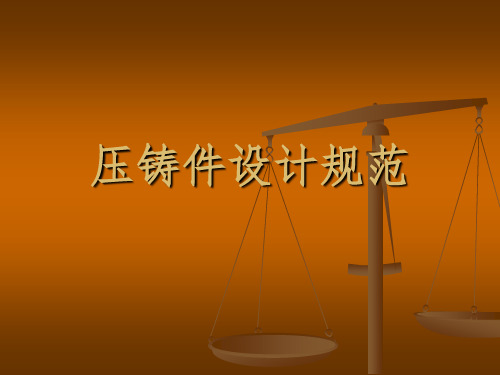
2.0
+1 -0.4
表9 推荐铰孔加工余量(mm)
公称孔径D
≤6
铰孔余量
0.05
>6~10 0.1
> 10 ~18 >18 ~30 >30 ~50 >50 ~60
0.15
0.2
0.25
0.3
我司现采用的机加工余量一般取0.3~0.5mm。
②、计算后的最小圆角应符合表2的要求。
2) 脱模斜度
设计压铸件时,就应在结构上 留有结构斜度,无结构斜度时,在需要 之处,必须有脱模的工艺斜度。斜度的 方向,必须与铸件的脱模方向一致。推 荐的脱模斜度见表4。
表4 脱模斜度
合金
锌合金 铝、镁合金
铜合金
配合面的最小脱模 斜度
外表面α 内表面β
0°10′ 0°15′ 0°30′
推荐采用的机加工余量及其偏差值见表8。铰孔余 量见表9。
表8 推荐机加工余量及其偏差(mm)
基本尺寸 每面余量
≤100
0.5
+0.4 -0.1
>100~250
0.75
+0.5 -0.2
> 250 ~400
1.0
+0.5 -0.3
> 400 ~630
1.5
+0.6 -0.4
> 630 ~1000
>500
0.5
1.5
0.8
2.0
0.8
2.0
0.8
1.5
1.0
1.8
1.22.51来自22.51.5
2.0
1.5
2.2
1.8
3.0
1.8
3.0
2.0
2.5
2.0
2.5
压铸模具设计规范
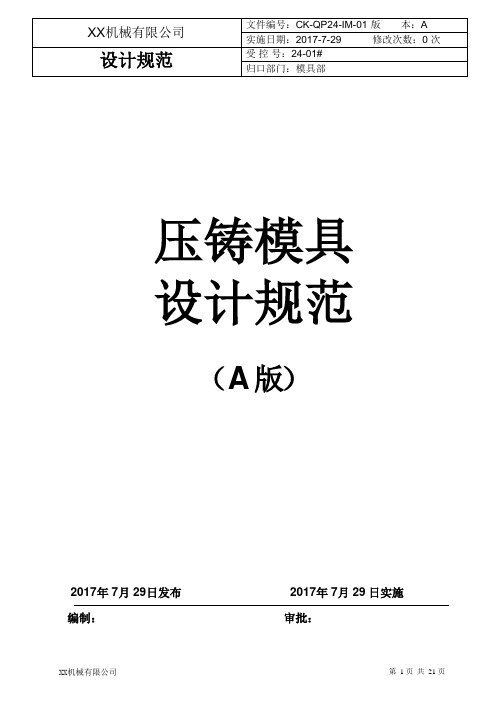
压铸模具设计规范(A 版)2017 年 7 月 29 日发布2017 年 7 月 29 日实施编制:审批:01. 目录一:模芯1.1模芯尺寸1.1.1模芯边距尺寸机型(T)160T 280T400T 500T-630T800T 1250T1600T三面(mm)55 60 70 80 100 120 140料筒面(mm)60 65 80 90 110 130 160 1.1.2模芯底面厚度尺寸机型(T)160T 280T400T500T-630T800T 1250T 1600T定模芯(mm)50 55 60 65 70 80 85动模芯(mm) 55 60 70 80 85 100 105敞开式滑块(mm)55 60 70 80 85 100 105 1.2模芯定位设计1.2.1模芯四角精定位斜度:动定模配合处单边 5°,与模框干涉处也要做斜度,单边 1.5°。
侧面转角圆角在 R8 以上。
定位的平面要避空 0.1mm,所有 R 角都要避空。
总高度最少 8mm。
1.2.2模芯周围一圈定位的斜度也做成 5°,平面不避空。
插入附件1.3,模芯冷却系统设计1.3.1:冷却水应设于流道附近、水管之间距保持 40mm-60mm,单独的孤岛处(凸起的)、大面积凹坑的侧边,产品最后凝固的厚壁处;1.3.2:环形冷却水的螺纹接口为 ZG1/4,冷却水管ø8-ø10mm,距离侧壁为 15mm 左右,距离顶面为 20~30mm,距离顶杆孔或销子孔至少 5mm;1.3.3:环形冷却水管经过的地方有高出平面的凸台或圆柱时应当采用隔水片的方式进行冷却,每一个环形最多允许有 6 个隔水片,隔水片孔与成型部位的距离参照点冷却;1.3.4:点冷却的水管直径为ø15.3mm-23mm 螺纹接口一般为 ZG3/8,距离侧壁为 15mm 左右,产品特殊厚壁可做到 6mm 左右,距离顶面为 15~25mm。
压铸模具技术规范

1目的:规范公司模具设计、制造的技术、质量标准,在顾客没有特殊要求的情况下,作为公司模具制造、验收的准则。
2适用范围:适用于公司制造的铝、镁、锌压铸模具的设计、制造、验收、运输过程3引用标准:GB/T8844-2003压铸模具技术要求GB/T1804-2000 —般公差未注公差的线性和角度公差GB/T1184-1996形状公差和位置公差未注公差值GB/T197-1981 普通螺纹公差与配合4技术要求4.1压铸模材料、热处理技术要求压铸模零件选用的材料、热处理技术要求:应符合表1。
表1:压铸模零件常用材料及热处理要求4.2压铸模几何尺寸技术要求4.2.1成型部位未注公差的极限偏差:应符合表2要求表2 :成型部位未注公差mm4.2.2成型部位转接圆弧未注公差的极限偏差:应符合表3要求表3:成型部位圆弧未注公差mm423成型部位未注角度和锥度公差:应符合表4要求(注:锥度公差按锥体母线长度决定, 角度公差按角度短边长度决定)表4:成型部位未注角度和锥度公差4.2.4非成型部位未注公差的极限偏差:应符合表5要求表5:非成型部位未注公差mm425螺钉安装孔、推杆孔、复位杆孔等未注孔距公差的极限偏差:应符合表6要求表6:螺钉安装孔、推杆孔、复位杆孔等未注孔距公差mm426模具零件图中螺纹的基本尺寸:应符合表7要求表7:螺纹的基本尺寸mm427压铸模模具零件的配合类别和精度等级:应符合表8、表9要求表8:模具零件的配合类别和精度等级表9:极限公差表ym4.3压铸模脱模斜度技术要求4.3.1成型部位未注脱模斜度时,形成铸件内侧壁的脱模斜度:应不大于表10的规定值(外侧壁的脱模斜度不大于表5规定值的1/2)表10:成型部位未注脱模斜度432圆模芯的脱模斜度:应不大于表11的规定值表11:圆模芯脱模斜度433文字符号的脱模斜度:10° -15 °。
4.4压铸模形位公差技术要求4.4.1模具结构零件和有配合关系结构的形位公差:应符合表12、表13、表14的要求表12:模具结构零件的形位公差表13:模具有配合关系结构的形位公差表14:形位公差数值表442模具零件图中未注形位公差:应符合表15要求表15:未注形位公差卩m4.5压铸模表面粗糙度技术要求压铸模零件表面粗糙度:应符合表16的要求表16:压铸模零件工作部位表面粗糙度4.6压铸模其他技术要求4.6.1成型部位未注明圆角:R0.5,非工作部位棱边应倒角,型面与分型面或与型芯、推杆等相配合的交接边缘不允许倒角或倒圆。
压铸件设计规范详解

压铸件设计规范详解压铸件是指利用压铸工艺将熔融金属注入模具中,经过凝固和冷却后得到的零件。
由于该工艺具有生产效率高、成本低、制造精度高等优点,被广泛应用于汽车、航空航天、电子等领域。
为了保证压铸件质量和安全性,需要遵循一系列的设计规范。
下面将详细介绍压铸件设计规范。
一、材料选择1.铝合金:常用的有A380、A383、A360等。
根据使用条件和要求,选择合适的铝合金材料,确保压铸件具有良好的强度和塑性。
2.压铸型腔材料:常用的有铜合金、热处理工具钢等。
要选择适当的材料,以耐高温和磨损。
二、模具设计1.模具设计必须满足压铸件的要求,保证铸件的尺寸精度和表面质量。
2.模腔设计要考虑到铸件收缩率、冷却速度等因素,以避免产生缺陷和变形。
3.合理安排模具冷却系统,保证压铸件内部和表面的冷却均匀。
三、尺寸设计1.压铸件的尺寸设计应符合产品技术要求和工艺要求,确保功能和安装的需要。
2.避免设计尺寸太小或太薄,以免产生破裂和变形。
3.设计保证良好的表面质量,避免设计中出现接触不良、挤压不足等问题。
四、壁厚设计1.壁厚不应过薄,以免影响产品的强度和刚性。
2.避免壁厚过大,以减少成本和缩短冷却时间。
3.边缘和角部应注意壁厚过渡,避免产生应力集中。
五、设计角度和半径1.设计时应根据铝合金的流动性选择合适的角度和半径。
2.避免设计尖锐角度和太小的半径,以免产生气孔和挤压不足。
3.设计角度和半径应保持一定的一致性,避免因设计不当导致铸件变形和收缩不均匀。
六、设计放射状构件1.当压铸件具有放射状构件时,要合理设计放射状梁的位置和数量,以充分利用材料,并减少成本。
2.注意放射状构件的设计不应影响整体结构的强度。
七、设计排气系统1.设计时要考虑到铸件内部的气孔、气泡等气体排出问题。
2.合理安排和设计排气道,以保证良好的注模效果和铸件质量。
八、设计孔和螺纹1.设计孔和螺纹时应遵循标准规范,确保质量和安装的可靠性。
2.孔和螺纹的位置和尺寸应符合产品要求,保证压铸件的功能和使用要求。
压铸模具标准
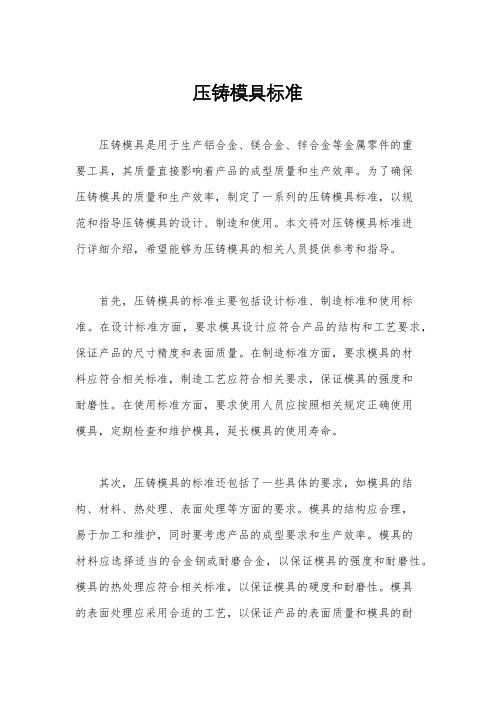
压铸模具标准压铸模具是用于生产铝合金、镁合金、锌合金等金属零件的重要工具,其质量直接影响着产品的成型质量和生产效率。
为了确保压铸模具的质量和生产效率,制定了一系列的压铸模具标准,以规范和指导压铸模具的设计、制造和使用。
本文将对压铸模具标准进行详细介绍,希望能够为压铸模具的相关人员提供参考和指导。
首先,压铸模具的标准主要包括设计标准、制造标准和使用标准。
在设计标准方面,要求模具设计应符合产品的结构和工艺要求,保证产品的尺寸精度和表面质量。
在制造标准方面,要求模具的材料应符合相关标准,制造工艺应符合相关要求,保证模具的强度和耐磨性。
在使用标准方面,要求使用人员应按照相关规定正确使用模具,定期检查和维护模具,延长模具的使用寿命。
其次,压铸模具的标准还包括了一些具体的要求,如模具的结构、材料、热处理、表面处理等方面的要求。
模具的结构应合理,易于加工和维护,同时要考虑产品的成型要求和生产效率。
模具的材料应选择适当的合金钢或耐磨合金,以保证模具的强度和耐磨性。
模具的热处理应符合相关标准,以保证模具的硬度和耐磨性。
模具的表面处理应采用合适的工艺,以保证产品的表面质量和模具的耐蚀性。
最后,压铸模具的标准还包括了一些检验和测试的要求,如模具的出厂检验、使用前检验、定期检验等。
模具的出厂检验应包括模具的尺寸检验、材料检验、热处理检验等,以保证模具的质量。
使用前检验应包括模具的装配检验、润滑检验、保养检验等,以保证模具的正常使用。
定期检验应包括模具的尺寸检验、磨损检验、裂纹检验等,以保证模具的使用寿命。
总之,压铸模具标准是保证压铸模具质量和生产效率的重要依据,对压铸模具的设计、制造和使用都有着重要的指导作用。
压铸模具的相关人员应严格按照相关标准执行,以保证产品质量和生产效率,推动压铸模具行业的健康发展。
希望本文所介绍的压铸模具标准能够为相关人员提供参考和指导,推动我国压铸模具行业的发展。
压铸工艺流程中的模具设计要点
压铸工艺流程中的模具设计要点压铸是一种常用的金属加工工艺,通过将熔融金属注入模具中,并在固化后取出成型件。
模具设计是整个压铸工艺中的关键环节,决定了成型件的质量和生产效率。
本文将从模具结构设计、材料选择和加工工艺三个方面讨论压铸工艺流程中的模具设计要点。
一、模具结构设计要点1. 合理选择模具结构模具结构的设计应根据产品的形状、尺寸和压铸工艺要求进行合理选择。
一般常见的模具结构包括单腔、多腔、合模和分模等。
对于形状复杂的产品,可以采用多腔结构来提高生产效率。
对于尺寸较大的产品,可以考虑采用合模结构来减少模具成本。
2. 考虑产品的冷却和顶针装置在模具设计中,需要考虑产品的冷却和顶针装置。
冷却系统的设计应能够有效地排除熔融金属的热量,以确保成型件的质量。
顶针装置的设计应满足产品的要求,并保证顶针在压铸过程中的精确位置。
3. 设计合理的浇口和溢流槽浇口和溢流槽是模具设计中的重要组成部分。
设计浇口时应考虑熔融金属的流动性和冷却速度,并确保浇口与产品的结合处处于合适的位置。
溢流槽的设计应考虑金属液体的顺利流动,以避免产生气体和杂质。
二、材料选择要点1. 选择耐磨耐热的材料模具在压铸过程中需要承受高温和高压的作用,因此材料的选择至关重要。
一般采用耐磨耐热的工具钢或合金钢作为模具材料,以保证模具的使用寿命和成型件的质量。
此外,还应考虑材料的加工性能和可靠性。
2. 考虑材料的强度和刚性模具的结构设计需要兼顾材料的强度和刚性。
材料的强度直接影响到模具的承载能力,而刚性则影响到模具的稳定性和精度。
因此,在模具设计中应根据产品的要求选择合适的材料,并进行合理的加工和热处理,以提高模具的性能。
三、加工工艺要点1. 精确计算和控制成型参数在压铸工艺中,成型参数的精确计算和控制是保证成型件质量和加工效率的关键。
成型参数包括注射速度、压力、温度和冷却时间等。
合理选择和控制这些参数,可以避免产生缺陷和变形,提高成型件的精度和表面质量。
压铸模具的技术要求文档
压铸模具的技术要求文档压铸模具是现代工业生产中常用的一种模具,用于制造各种金属制品。
压铸模具的技术要求非常高,对模具的设计、制造、使用等方面都有相应的要求。
本文将从几个方面详细介绍压铸模具的技术要求。
一、设计要求1.模具结构设计要合理,要考虑到产品的结构特点、工艺要求等因素,并保证在模具使用中有较高的稳定性和精度。
2.模腔的设计要充分考虑充型性、冷却性、顶出性等要素,确保产品成型质量稳定。
3.模具的开口方式、进料方式等设计要符合产品要求,并能保证模具的安全操作。
二、材料要求1.模具材料应具有良好的刚性、韧性和耐磨性,能够承受较大的冲击负荷和高温环境,如工具钢、合金钢等。
2.模具的热处理要求良好,能够使模具硬度均匀、稳定,延长使用寿命。
三、制造要求1.模具加工要求高精度、高质量,要保证模具的尺寸精度和表面质量。
2.维修和保养要定期进行,及时处理模具的磨损、损伤等问题,确保模具的正常使用和寿命。
四、使用要求1.模具的操作人员要具备一定的技能和经验,严格按照操作规程进行操作,保证操作的安全和准确性。
2.模具的使用环境要保持清洁、干燥,避免灰尘、水汽等对模具的损坏。
3.模具的顶出装置、冷却装置等要保持良好的工作状态,及时进行维修和更换。
五、质量控制要求1.模具的尺寸精度、表面质量等要进行严格的检测和控制,保证产品的准确性和一致性。
2.定期对模具进行检测和维修,及时发现并解决模具的问题,防止因模具问题引起的产品质量问题。
总结:压铸模具的技术要求非常高,对模具的设计、制造、使用等方面都有严格要求。
只有合理的设计,良好的材料和制造工艺,正确的使用和维护,才能保证模具的高质量和长寿命,从而保证产品的质量和生产效率。
因此,在实际应用中,需要充分重视压铸模具的技术要求,综合考虑各方面因素,确保模具的高效稳定运行。
压铸用模具技术规范
谢谢观看
压铸用模具技术规范
2019年08月25日实施的行业标准
01 起草人
03 适用范围
目录
02 起草单位 04 主要内容
基本信息
《压铸用模具技术规范》是 2019年08月25日实施的一项行业标准。
起草人
起草人
孙公益、王卓明、侯小华、李向、方宏机、牟雄、李永能、钟永佳、李丰、钱永锋、阳向阳、周冠华、周永 强、周彬、陈汝杰、苏丽洁。
起草单位
起草单位
佛山市南海区模具协会、佛山市南海区合亿金属制品有限公司、广东文灿模具有限公司、广东银迪压铸有限 公司、佛山市启新模具有限公司、佛山市南海蕾特汽车配件有限公司、佛山市智星铝合金制品实业有限公司、广 东汇策标准化服务有限公司、佛山市成阳正大模具五金塑料有限公司、佛山市南海区凯力五金制品有限公司、佛 山群志光电有限公司、佛山市南海新力金属制品有限公司、广东北重特钢有限公司。
适用范围
适用范围
本标准规定了压铸模的要求、检验方法、验收、标志、包装、运输。本标准适用于佛山市南海区模具协会内 的生产压铸模具的相关企业。
主要内容
2、零件要求 提出了设计模具所选用零件的材料性能、热处理技术、成型部位公
差和脱模斜度等要求。 3、装配要求 提出主了要内定容 模座板、动模座板、合模位置、平衡度公差,垂直度公差 等要求。 4、检验方法 提出了检验方法的要求。
压铸模设计制造规范
压铸模设计制造规范压铸模设计制造规范这些标准在于给压铸模具设计者和制造者在模具设计和制造的过程中提供满足压铸标准的要求而必须控制的项目,有利于减少设计失误、提高模具制造的质量和效率。
在设计和制造的过程中任何有与本标准不符的项目必须得到技术主管或制造主管的同意。
本标准应随技术的不断改进、制造工艺的提高定期更新。
并注明版本号。
常规模具报价以此为基础,特殊情况另外注明。
一、总体要求:如采用H13电渣重熔钢材料必须按认可的上钢五厂的牌号供应,如采用其他的厂商或品牌,需得到的书面许可。
进口模芯材料需专营商供应。
按的压机尺寸设计外形,防止干涉。
(125T~1600T)(压机尺寸表正在编写过程中)或另见表单中。
吊装孔至少为M30深60的,顶部至少2个,大型模具动定模架上要各2个,需设于模具的重心上(每半模),以利于吊装时的安全。
动定模上方距分型线8 mm处设计宽15 mm深5 mm的脱模剂残液排出槽一直延伸到模架边缘。
(除非额外允许)如图所示:模具压夹槽,最小30 mm×30 mm(400T以下),40 mm×40 mm(400T以上),到型板高最小25 mm(400T以下),40 mm(400T以上)。
跨距大于150 mm时都应考虑加支撑柱。
支撑柱直径(或宽)不小于75 mm,尽可能靠近压射变形位。
减小变形,动模架支撑模芯的厚度至少为悬空位宽度的三分之一(大于50mm)。
安装防止飞水挡水板,一般设于前、后、上三侧。
分流锥和浇口套按的标准设计,400T以下为标准化浇口套,400T以上为整体压室。
下图为400T以下压铸机标准化浇口套:下图为500T以上压铸机标准化整体压室:二、压铸模设计制造流程:产品分析:对客户提供的产品图纸或样品进行分析,确认如下项目:精度等级、加工装配基准。
加工余量、分型位置、顶出位置、浇口位置等客户是否认可。
模具设计:2D模具结构设计和3D造型分模同时进行。
模具制造:按的模具制造标准实施。
- 1、下载文档前请自行甄别文档内容的完整性,平台不提供额外的编辑、内容补充、找答案等附加服务。
- 2、"仅部分预览"的文档,不可在线预览部分如存在完整性等问题,可反馈申请退款(可完整预览的文档不适用该条件!)。
- 3、如文档侵犯您的权益,请联系客服反馈,我们会尽快为您处理(人工客服工作时间:9:00-18:30)。
压铸模具设计规范1.目的:为了规范和不断提高公司的模具设计水平,特制订本规范;《压铸模具设计规范》是设计课在进行模具设计时所参照的主要依据及基本要求.2.范围:适用于本公司所有压铸模具设计.3.权责:由设计课负责所有需由本公司自己做模的模具设计工作.4.定义:5.作业内容:5.1.模具设计资料提供5.1.1.在进行模具设计时有以下资料需客户/技术部确认:5.1.1.1.2D、3D成品图(需有出模角);5.1.1.2.成品出模分型线;5.1.1.3.模腔数量;5.1.1.4.入水位置及形式;5.1.1.5.顶针分布位置;5.1.1.6.模芯镶接印确认;5.1.1.7.模芯用料及标准件要求;5.1.1.8.外观及标记(如: 蚀纹, 刻字, 日期唛, 环保及循环使用符号等);5.1.1.9.成品用料﹑材料成份及性能表;5.1.1.10.成品加工及装配要求;5.1.1.11.客户有无其它特殊要求;5.1.1.12.如需要,客户啤机的资料;5.1.1.13.如需要,定位﹑行程及安全要求(如: 定位锁, 行程锁, 先复位机构等);5.1.1.15.如需要,行位要求等.5.1.2.检查所得资料(如:铸件壁厚是否均匀、出模角是否足够、是否R角过渡、模芯是否有薄弱胶位等), 如有疑问,可提出改良意见,经客户确认后再进行后续工作.5.1.3.如果因时间关系要先行设计, 来不及确认的资料设计课要继续主动跟进.5.2.模具设计方案5.2.1.为提高工作效率, 减少修改量, 设计人员可将设计意图及关键结构的构思绘出草图方案,经讨论确定方案后,再进行后续绘图工作.5.2.2.如客人有要求要确定方案的,要经客人确定后,再进行后续设计.5.3.材料订购5.3.1.设计草图方案确定完成后,先根据草图的设计尺寸,订购模芯钢材,模胚及其它模具配件,再进行后续的设计.5.3.2.模胚的订购参考发斯特标准备品模胚图,非备品模胚尽可能采用标准模胚(如:震坚模胚﹑龙记模胚),需要加工的位置(如:精框﹑开滑块槽﹑真空阀槽等)要注明加工要求及公差配合要求,确保模胚购回后可直接进行装配.5.3.3.结构复杂的模具,在订购模胚时,无法准确把握滑块槽的配合要求,可以在模胚制造厂开粗后,单边留1-2mm,购回后再精锣.5.3.4.模具外购标准件,尽量做到常用的统一标准,以便互换,如:油缸、顶针.5.4.工程图纸5.4.1.工程图纸绘图要求5.4.1.1.工程图纸(包括模具装配图、模具散件图、成品图)的图框﹑标签, 统一用公司规定图框﹑标签,除非客户有特别指定.(见附件《图纸标签》及《图框》)5.4.1.2.模具装配图的图面通常包括以下这些内容:5.4.1.2.1.后模的俯视图; 前模的底视图; 平行于X轴的全模剖视图; 平行于Y轴的全模剖视图; 这四个主要视图在装配图中的投影摆放方位如图所示:5.4.1.2.2.若装配图中表达不清,要增加入水口放大图、溢流口放大图等.5.4.1.2.3.若成品分型复杂或难以在装配图中表达清楚, 则把3D成品斜视图放在装配图中,用箭头将分型线指示清楚.5.4.1.2.4.没有表达出来的模具关键结构部分, 需要增加部分剖视图来表达; 一些结构太细小, 看不清楚和不方便标数的, 需要增加一些放大图来表达;(或者参考3D模图).5.4.1.2.5.散件图跟装配图一起发放,顶针尺寸图需要单独出图;5.4.1.2.6.有拉杆结构及行程控制开关的模具, 要把它们的装配尺寸表达在模具装配图上;5.4.1.2.7.要在模具装配图上表达清楚运水的IN 1…、OUT 1… 的位置.(制作时要在模胚上标识清楚).5.4.2.成品缩水的计算.5.4.2.1.选择以下方法计算成品的缩水率: 模具尺寸=产品尺寸x(1+缩水率)5.4.2.2.在3D软件系统中, 以上计算方法是现成的选项.5.4.3.材料表.名称5.4.3.1.模具材料在模具零件表中体现.零件图中也有注明,包括热处理5.4.3.2.采购现成的标准件, 按照供货商的规格及订购编号填写材料表, 如上表装配图材料表中的第1行.5.4.3.3.本公司加工的模具零件(包括部分标准件), 填写材料表如上表装配图中的第2行.5.4.3.4.材料(如模钢, 针类等等)的填写尺寸用图纸上的最大尺寸. 如图所示.5.4.4.技朮说明5.4.4.1.模具装配图的技术说明一般包括.A.模具编号采用CNC加工在两个模腿上.B.非分型面的所有模边均需倒角 1.5X45 .C.如果模具装配图上找不到所需的尺寸, 请参考成品图和3D拆模图D.客户的模具要求. 比如:a镶件与b镶件能够替换、前模的蚀纹要求、后模的拋光要求等等.E.胶位的技术说明参照成品图.F.非胶位的技术说明公司规定如下:1.未注明的尺寸及公差参考产品图.2.未注明圆角按R0.5,倒角按C0. 5.G.撑头比方铁高0.25 mm.H.模具零件加工的通用公差要求:TOLERANCE: UNLESS OTHERWISE SPECIFIED. UNIT: mmX. ±0.10 SCREWS &WATER LOC ±0.20X.X ±0.05 FRAC ±0.20X.XX ±0.02 ANG ±30’X.XXX ±0.0055.5.模具工程图的确认5.5.1.模具装配图的审查,应确保《模具装配图审查表》的每一项审查内容都审查过(如果有的话), 并在审查表的项目框框内打勾或打交叉, 没有的项目划斜线, 以确保图纸是彻底审查过.5.5.2.合格受控后的图纸,如果有问题需要修改的地方, 审查者必须将怎样修改及修改的尺寸清楚无误地画在图纸上(或另附修改指示图纸). 口述问题或欠绘图表示具体尺寸, 常造成漏改和重复改及其它误会.5.5.3.图纸如已经更改,则新图纸发放的同时收回/废除旧图纸,确保新图纸的版本号是正确的.5.5.4.确认后的图纸应有主管/经理人员的签字(或盖章), 并交由专人进行发放与备案.5.6.模具工程图的存盘管理.5.6.1.模具工程图纸(包括产品2D图﹑3D图,模具装配图)完成并确认后(或修改后), 除了发放外,计算机档案应交给专人,在共享区用计算机分类进行存盘备份.5.6.2.为方便查阅,对图纸的文件名命名规定如下:A. 模具命名:□□(客户代码)□□(编号)□(“A”代表原模,“B”代表复制模)-□(产品型号)例: LX01A-SMART, “LX”代表联想客户代码;“01”代表第一个项目;“A”代表原模;“SMART”代表产品型号。
注:1.多个产品可以选其中一个命名,另外用文本额外特别备注.5.6.3. 公司对档案目录名取法规定如下:A.档案所在目录:模具部服务器/模具图5.6.4.模具图纸有更新,要及时换版更新存盘,以便查阅。
5.7.模芯5.7.1.模芯的方位.5.7.1.1.尽量避免模芯的长与宽的尺寸相等.5.7.1.2.正方形或近似正方形的模芯, 要在模芯与模胚之间有对准符号.如图:5.7.1.3.模芯的宽度一般小于或等于顶针板的宽度.5.7.1.4.模芯偏离模具中心距离尽量≦30mm.5.7.1.5.成品胶位距离模芯边最少的距离是20mm.5.7.1.6.模芯的四个角做R圆角, 以配合A.B板的模腔.5.7.1.7.藏模芯的A.B板模腔尽量用凹腔,不用通腔.5.7.2.模芯的定位及紧固.5.7.2.1.锁模时不平整的分模面令所受的锁模力不平衡的, 要设置模芯止口锁进行调节.5.7.2.2.将模芯收紧在模胚上的螺丝, 分布尽量对称平衡.5.8.模胚及组件(一般外购标准件)5.8.1.模胚.5.8.1.1. 公司一般选指定供方的模胚(如震坚、龙洲模胚),客户指定用其它供货商的模胚标准时,向指定的供方订货(如龙记)订做.5.8.1.2.模板的钢料用S50C或者45#钢(黄牌钢).5.8.1.3.要保证模胚的强度,形状复杂的(如铲鸡需要高出的),要订做模胚.5.8.1.4.模胚的模板要平整, 平行,确保垂直度, 公差在±0.01mm之内.5.8.1.5.模胚的A.B板在模具装配时有0.2-0.3mm空隙, 以保证模芯的锁模.5.8.1.6.模仁及模架由设计提单采购,标准备品模架及模仁预留2套备料。
5.8.2.导柱5.8.2.1.柱长度控制到最长比铸件最高面高50mm即可,需要特别注明5.8.3.撑头.5.8.3.1.用45#黄牌钢做撑头, 最小∅45, 最大∅120, 用M12 螺丝固定.5.8.3.2.顶针板小于150 mm一般不需放撑头.5.8.3.3.撑头尽量往中间放, 并且尽量均衡对称.5.8.3.4.如底板开通,撑头要做带台阶的,以便承受压力5.8.4.顶棍孔(K.O).5.8.4.1.一般的顶棍孔排布要均匀对称.5.8.4.2.顶针板导边的长宽尺寸囊括的范围是顶棍孔的排布范围, 这个范围能排下多少个标准尺寸的顶棍孔,根据具体情况选者数量,一般选4个.5.8.4.3.如果模具要先复位机构,要在顶棍孔所对位置的底针板上做拉杆螺钉孔.5.8.5.码模位, 码模槽.5.8.5.1.按标准码模槽大小位置开设,在情况允许下,吊模螺钉位置尽量不要开码模槽.5.8.5.2.大的模具考虑四周都设置码模位.5.8.6.吊模螺丝孔, 吊铃和吊模铁.5.8.6.1.吊模螺丝孔一般按标准制作,最小用M10, 常用M12, M16, M20, M24, M28, M32. …5.8.6.2.一个吊模螺丝孔的螺纹能至少能承受一边模具(前模或后模)的重量.5.8.6.3.如果一块模板的重量在30~40kg之间, 至少要有一个吊模孔.5.8.6.4.如果一块模板重于400kg, 则四周各至少要有一吊模孔, 共四个.5.8.6.5.在前后模之间设置吊模铁或模扣, 预防在吊装时前后模分开或吊装不平衡5.9.流道.5.9.1.浇口套.5.9.1.1.浇口套的钢料一般用H13钢, 浇口套一定要与模胚及分流锥配合良好, 法兰盘配合位置一般要有3X45 的倒角,以便装模.5.9.1.2.浇口套需做好冷却水。
5.9.1.3.如果浇口套上有开设流道入口,需要做定位防转.5.9.1.4.用热流道的模具(一般用于锌合金):A.客户是否需要确认热唧咀的供货商?B.要注意定位﹑隔热和避空的地方, 防止热流失.C.热唧咀的电线要有电线坑并固定好, 电线的插座凹入模胚的藏位, 防碰撞.5.9.2.分流锥.5.9.2.1.分流锥的钢料一般用H13、SKD61钢, 分流锥一定要与模胚及浇口套配合良好, 分流锥后部可以适当避空.5.9.2.2.分流锥需做好喷泉式冷却水(定点冷却).5.9.2.3.分流锥设置流道要注意保证侧边强度.5.9.3.流道.5.9.3.1.流道过渡要圆滑,便于金属流动,除特殊情况外, 其它一般都开在后模.5.9.3.2.一模出多个成品的时候, 流道的大小长短要均衡.5.9.3.3.设计流道的大小要合适,同时要控制好比例关系。