破岩钻井方法及高压水射流破岩机理研究_王瑞和
取心中心在青海油田柴页1井长井段密闭取心再创新纪录

[ 3 4 ]李根生 , 宋 剑.双射流流 动特性 数值模 拟和 P I V实验 研究[ J ] .自然科学进展 , 2 0 0 4, 1 4 ( 1 2 ) : 1 4 4 —1 6 4 6 8 . [ 3 5 ]B u c k m a n W G .Me t h o d a n d a p p a r a t u s f o r j e t d r i l l i n g d r a i n h o l e s f r o m w e l l s [ P ] :美 国 ,U S 6 2 6 3 9 8 4 B 1 .2 0 0 1
石油钻采工艺 , 1 9 9 7 , 1 9 ( 2 ) : 7—1 1 .
※ ※ ※ ※ ※ ※ ※ ※ ※ ※ ※ ※ ※ ※ ※ ※ ※ ※ ※ ※ ※ ※ ※ ※ ※ ※ ※ ※ ※ ※ ※ ※ ※ ※ ※ ※ ※ ※ ※ ※ ※ ※ ※ ※ ※ ※
究进展 [ J ] .金 属矿 山 , 2 0 0 5 ( 7 ) : 6 l一 6 6 .
( 编辑 : 黄晓川)
[ 2 8 ]何 育荣 , 沈忠厚 , 王瑞 和. 锥形 旋转水 射流 的实验研 究
[ J ] . 石油大学学报 , 1 9 9 4 , 1 8 ( 1 ) : 3 0— 3 4 . [ 2 9 ]步玉环 , 王瑞 和 , 周卫东. 旋 转射流 流动规 律研究 [ J ] .
—
7 —2 4.
[ 3 6 ]吴 为, 李根生 , 牛继磊 , 等. 直旋 混合 射流破岩 钻孔参数 试验研究 [ J ] . 流体机械 , 2 0 0 9 , 3 7 ( 6 ) : 1 —6 . [ 3 7 ]李 瑞 营 , 杨智光, 李玉海, 等. 径 向水 平 井 高 压 喷 嘴 [ P ] . 中国专利 : Z L 2 0 0 8 2 0 0 9 0 4 5 5 . 7 , 2 0 0 9 . 4 . 8 .
海洋超高温高压油气钻井关键设备技术研究

石 油 机 械
CHINA PETROLEUM MACHINERY
2024 年 第 52 卷 第 1 期
◀海洋石油装备▶
海洋超高温高压油气钻井关键设备技术研究
王 蓉 王定亚 郝和伢 刘文霄 赵 海
( 中国海洋工程装备技术发展有限公司)
王蓉, 王定亚, 郝和伢, 等. 海洋超高温高压油气钻井关键设备技术研究 [ J] . 石油机械, 2024, 52 ( 1) :
品, 其中: Solar175 最高工作温度 175 ℃ , 最大压
2024 年 第 52 卷 第 1 期
华北荣盛公司于 2010 年成功研制出国内第一
套 28 ~ 140 MPa 防喷器组, 防喷器极限高温达到
力 155 MPa; Quasar Pulse 于 2013 年实现了产品技
132 ℃ , 并已成功应用 8 组, 完成 20 余口井的钻
最大工作压力 206 MPa; HEATWAVETM 最高工作
温度 200 ℃ , 最 大 工 作 压 力 206 MPa。 另 外 还 有
APS 公司、 TOLTEQ 公司也能够研制出最高工作温
度 175 ℃ 、 最大工作压力 172 MPa 的产品 [11] 。
摘要: 为了提升我国海洋超高温高压钻井设备的国产化水平, 对海洋超高温高压钻井主要设
备进行了简要介绍, 分析了海洋超高温高压钻井设备的国内外技术现状, 重点阐述了海洋超高温
高压钻井设备的关键技术及其研发思路。 分析结果表明: 钻井防喷器及控制系统、 井口装置、 泥
线悬挂装置及井下工具等为当前急需攻关突破的超高温高压钻井关键设备; 我国在这些关键设备
design, manufacturing and testing of these key equipment, mainly reflected in four key technologies: development
新型双级扩眼钻头研制及试验

新型双级扩眼钻头研制及试验发布时间:2022-10-10T05:24:51.295Z 来源:《科技新时代》2022年3月6期作者:刘明[导读] 目前国内在深井、大斜度井扩孔难题上一直没很好的解决办法刘明成都迪普金刚石钻头有限责任公司四川成都610500摘要:目前国内在深井、大斜度井扩孔难题上一直没很好的解决办法。
传统的方法:其一是采用钻后扩孔的方式,此种方法作业环节多不仅钻井周期较长而且需要承担二次风险,钻井成本高,经济效率低,经过在现场试验证明,随着井斜的增加,钻后扩孔难度也随之而增加,当井斜大于32°时扭矩过大,常出现憋停顶驱的现象,施工难以正常进行;其二采用单级扩眼钻头(普通双芯钻头)进行随钻扩眼,这种方式在进行增降斜时候表现出工具面不稳定,造斜率达不到要求,井径扩大率不能达标。
本文针对普通随钻扩孔钻头的弱点,进行了新型双级扩孔钻头的研制。
研制的新型双级扩眼钻头成功运用于塔河油田定向随钻扩孔井眼,实践应用证明,该型号钻头取得了不错的使用效果,解决了上述难题。
关键词:定向;随钻扩孔;领眼钻头;扩眼钻头;钻头设计;机械钻速随着钻井技术的不断进步, 扩眼作业已成为解决易缩井、易垮塌地层、改良套管程序、增大固井环空、提高固井质量以及降低钻井成本的重要手段。
目前,许多国家都有各种类型的钻井扩眼工具,也在进一步进行新型扩眼工具的研发。
近年来,中石化塔河油田老井采收率低,为了提高采收率、开发剩余油,降低钻井成本实行老三级井身结构井开窗侧钻,从石炭系巴楚组或奥陶系上部桑塔木组灰色泥岩段进行开窗侧钻,由于灰色泥岩在井内钻井液长时间浸泡下容易出现坍塌、掉块等现象,在钻井过程中容易出现卡钻的安全隐患。
由于受老井眼井身结构的约束,若采用常规钻头进行定向钻进会引起下一开井眼钻头尺寸很小所带来的井眼钻具和仪器配套选择,液力保障与钻压传递等一系列问题。
所以需要进行定向随钻扩孔钻进,若采用钻后扩孔的方式,当井斜大于30°以上扩孔难度大;若采用普通双芯钻头进行随钻扩孔,在使用过程中工具面不稳定,可控性差,井径扩大率低;针对塔河油田这种侧钻井扩眼钻头国外研究也比较少,国内之前是一个空白,我公司研制的新型双级扩眼钻头属首次。
岩屑分形特征对PDC_齿破岩性能影响规律研究

◀钻井技术与装备▶岩屑分形特征对PDC齿破岩性能影响规律研究∗赫文豪1ꎬ2㊀陈振良3㊀史怀忠3㊀黄中伟3㊀熊超3㊀李欣龙1ꎬ3㊀史明豪3(1 中国石油大学(北京)油气光学探测技术北京市重点实验室㊀2 中国石油大学(北京)理学院能源交叉学科基础研究中心㊀3 中国石油大学(北京)油气资源与探测国家重点实验室)赫文豪ꎬ陈振良ꎬ史怀忠ꎬ等.岩屑分形特征对PDC齿破岩性能影响规律研究[J].石油机械ꎬ2023ꎬ51(8):1-10.HeWenhaoꎬChenZhenliangꎬShiHuaizhongꎬetal.Influenceoffractalcharacteristicsofcuttingsontherockbreak ̄ingperformanceofPDCcutter[J].ChinaPetroleumMachineryꎬ2023ꎬ51(8):1-10.摘要:随着油气井钻井工程研究的不断深入ꎬ岩屑形貌特征已成为评测岩石可钻性级值与钻头破岩效率的关键考量因素之一ꎮ为探究岩屑形貌分形特征对钻头破岩效率的影响规律ꎬ结合理论建模和室内试验等研究方法ꎬ围绕岩屑粒径分形维数㊁岩屑最大粒径㊁地层岩性系数等关键岩屑形貌描述参数ꎬ建立了基于岩屑粒径分形特征的PDC齿破岩比功评估模型ꎬ并针对常规齿和锥形齿等PDC齿开展破碎硬质花岗岩试验研究ꎬ验证该模型评估PDC齿破岩性能的预测精度ꎮ利用该理论模型和试验规律ꎬ进一步揭示常规齿和锥形齿等类型PDC齿不同出刃高度㊁布齿角度等破岩工艺参数下岩屑形貌生成特征及破岩能耗变化规律ꎮ研究结果发现:切削深度对PDC齿破岩性能影响效果远大于切削角度ꎬ随着地层埋深的增大ꎬPDC齿吃入深度减小ꎬPDC齿生成岩屑分形维数逐渐增大ꎬ最大岩屑粒径显著减小ꎬ且锥形齿生成岩屑平均粒径大于常规齿ꎻ同等钻压或破岩能量条件下ꎬ锥形齿脆性破碎能力强于常规齿ꎬ生成岩屑分形维数和最大粒径均大于常规齿ꎮ研究结果可为深层硬岩钻进过程中岩屑录井形貌数据和PDC钻头混合布齿工艺提供理论依据ꎮ关键词:PDC齿ꎻ岩屑ꎻ分形维数ꎻ最大岩屑粒径ꎻ破岩比功中图分类号:TE21㊀文献标识码:A㊀DOI:10 16082/j cnki issn 1001-4578 2023 08 001InfluenceofFractalCharacteristicsofCuttingsontheRockBreakingPerformanceofPDCCutterHeWenhao1ꎬ2㊀ChenZhenliang3㊀ShiHuaizhong3㊀HuangZhongwei3XiongChao3㊀LiXinlong1ꎬ3㊀ShiMinghao3(1 BeijingKeyLaboratoryofOpticalDetectionTechnologyforOilandGasꎬChinaUniversityofPetroleum(Beijing)ꎻ2 BasicResearchCenterforEnergyInterdisciplinaryꎬCollegeofScienceꎬChinaUniversityofPetroleum(Beijing)ꎻ3 StateKeyLaboratoryofPetroleumResourcesandProspectingꎬChinaUniversityofPetroleum(Beijing))Abstract:Alongwiththedeepeningresearchonoilandgaswelldrillingengineeringꎬthemorphologyofcut ̄tingshasbecomeoneofthekeyconsiderationsforevaluatingthedrillabilitylevelofrocksandtherockbreakingef ̄ficiencyofbits.Inordertoexploretheimpactoffractalcharacteristicsofcuttingsmorphologyontherockbreaking1 ㊀2023年㊀第51卷㊀第8期石㊀油㊀机㊀械CHINAPETROLEUMMACHINERY㊀㊀㊀∗基金项目:国家重点研发计划项目 复杂油气智能钻井理论与方法 复杂地层智能化破岩机理与导向控制方法 (2019YFA0708302)ꎻ国家自然科学基金项目 三轴应力条件下奔驰形PDC齿压剪耦合破岩机理研究 (52004296)㊁ 轴扭耦合冲击辅助钻头破碎高温花岗岩机理研究 (52274016)ꎻ中国石油大学(北京)科研基金 能源交叉学科基础研究中心建设与发展规划 (2462022YXZZ007)㊁ 高温作用下深层硬岩力学特性与渗流机制演化机理研究 (2462022BJRC012)ꎻ油气资源与探测国家重点实验室定向课题 考虑摩擦功耗的PDC齿破岩比功评估模型研究 (PRP/DX-2206)ꎮefficiencyofthebitꎬcombinedwiththeoreticalmodelingandlaboratorytestsꎬcenteredonthekeycuttingsmor ̄phologydescriptionparameterssuchasfractaldimensionofcuttingsizeꎬmaximumcuttingsizeandformationlithol ̄ogycoefficientꎬarockbreakingspecificenergyevaluationmodelofPDCcutterbasedonthefractalcharacteristicsofcuttingsizewasbuiltꎬandexperimentalresearchonbreakinghardgranitebyconventionalandconicalPDCcut ̄terswascarriedouttoverifythepredictiveaccuracyofthemodelinevaluatingtherockbreakingperformanceofPDCcutter.ThetheoreticalmodelandexperimentalruleswereusedtofurtherrevealthegenerationcharacteristicsofcuttingsmorphologyandthevariationlawofrockbreakingenergyconsumptionunderdifferentrockbreakingprocessparameterssuchasexposureheightandcutterarrangementangleofconventionalandconicalPDCcutters.TheresultsshowthattheinfluenceofcuttingdepthonrockbreakingperformanceofPDCcutterisfargreaterthanthatofcuttingangleꎻastheburieddepthoftheformationincreasesꎬthepenetrationdepthofPDCcutterdecrea ̄sesꎬthefractaldimensionofcuttingsgeneratedbyPDCcuttergraduallyincreasesꎬthemaximumcuttingsizesig ̄nificantlydecreasesꎬandtheaverageparticlesizeofcuttingsgeneratedbyconicalcutterislargerthanthatbycon ̄ventionalcutterꎻunderthesameweightonbit(WOB)orrockbreakingenergyconditionsꎬthebrittlebreakingca ̄pacityofconicalcutterisstrongerthanthatofconventionalcutterꎬandthefractaldimensionandmaximumparticlesizeofgeneratedcuttingsarealllargerthanthoseofconventionalcutter.TheresearchresultsprovideatheoreticalbasisforthemorphologydataofsieveresiduelogandmixedcutterarrangementtechnologyofPDCbitinthecourseofdeephardrockdrilling.Keywords:PDCcutterꎻcuttingꎻfractaldimensionꎻmaximumcuttingsizeꎻrockbreakingspecificenergy0㊀引㊀言随着对油气井钻井工程研究的不断深入ꎬ岩屑粒径及其分布特征已成为评测岩石可钻性级值㊁钻头破岩效率㊁环空钻井液携岩性能㊁钻具冲蚀磨损和卡钻等井下复杂事故的关键考量因素[1-4]ꎮ研究数据表明ꎬ钻井岩屑颗粒粒径分布特征与地层岩性和破岩工具及破岩方法息息相关ꎬ钻进地层越深ꎬ岩屑粒径越小ꎬ且牙轮钻头生成岩屑粒径显著大于PDC钻头生成岩屑粒径[1ꎬ5-6]ꎮ通过对普光气田气体钻井工艺上返岩屑观察ꎬ岩屑粒径与形状和钻头选型密切相关ꎬ空气锤钻头生成岩屑平均粒径显著大于牙轮钻头生成岩屑粒径ꎬ且空气锤破岩形成的岩屑多呈片状椭圆形ꎬ而牙轮钻头破岩形成岩屑多呈纺锤形[6]ꎮ对于同一岩性地层ꎬ随着埋藏深度的增加ꎬ岩石上覆压力越大ꎬ岩石可钻性越差ꎬ钻速越慢ꎬ岩屑粒度越趋近于小尺寸细粒[3ꎬ7]ꎮ因此ꎬ利用钻井过程中生成岩屑的形貌特征可以有效表征钻遇地层可钻性及破岩能耗等关键评价参数ꎬ相关研究成果对于提高钻头破岩性能㊁缩短钻井周期和降低钻井成本具有重要意义ꎮ李士斌㊁李玮等[2-3ꎬ7-8]通过研究钻井过程中上返岩屑粒径分布发现ꎬ上返岩屑粒径符合分形分布特征ꎬ且钻进地层越深ꎬ钻速越慢ꎬ岩屑粒径分形维数逐渐减小ꎬ岩石可钻性级值与岩石硬度越大ꎬ并随着分形维数变化呈线性增大ꎮ根据松辽盆地火成岩地层钻井岩屑分形分布特征ꎬ苏鹏[4]提出了一种基于破碎比功表征的地层可钻性评价方法ꎬ可以有效反应钻头与地层的匹配性ꎮ张立刚等[9]通过引入分形方法ꎬ利用上返岩屑形貌特征建立了岩石可钻性实时预测模型ꎬ对指导大庆油田实时钻井参数优选提供了一种新思路ꎮ利用岩屑分形破碎特征和钻井工况特点ꎬ闫铁等[10]建立了基于岩屑分形破碎特征的钻井工程能效评价模型ꎬ发现岩屑粒度分形维数和最大岩屑尺寸及岩石特性常数是破碎能耗的主要影响因素ꎬ岩屑分形维数越大ꎬ生成岩屑最大粒径越小ꎬ岩石破碎剧烈程度越大ꎬ破碎能耗越高ꎮ文献调研数据显示ꎬ前人对岩屑粒径研究多集中于录井过程中岩屑形貌特征分析及其对岩石破碎效率影响规律研究ꎬ而对岩屑粒径控制机制研究相对较少ꎮ根据2015年全国油气资源动态评价ꎬ我国深层㊁超深层油气资源量671亿t油当量ꎬ占油气资源总量的34%ꎮ以塔里木盆地为例ꎬ仅埋深在6000~10000m的石油和天然气资源就分别占其总量的83 2%和63 9%ꎮ但随着钻井深度的增加ꎬ地层岩石强度与硬度显著增大ꎬ钻头磨损严重ꎬ机械钻速低ꎬ亟需高效勘探开发钻井工艺以缩短钻井周期和降低钻井成本[11-15]ꎮ为此ꎬ结合理论建模和室内试验等方法ꎬ从钻头破岩性能角度出发ꎬ建立基于岩屑粒径分形特征的PDC齿破岩比功理论2 ㊀㊀㊀石㊀油㊀机㊀械CHINAPETROLEUMMACHINERY㊀2023年㊀第51卷㊀第8期模型ꎬ揭示不同出刃高度㊁布齿角度等破岩工艺参数下ꎬ岩屑形貌生成特征及破岩能耗变化规律ꎬ以期为深层硬岩PDC钻头混合布齿工艺提供理论方法指导ꎮ1㊀岩屑体积与岩屑质量分布分形特征根据分形分布粒径特征ꎬPDC齿切削破碎生成岩屑粒径分布应满足[3ꎬ8ꎬ16]:N(l)=C1l-Dl(1)式中:Dl是岩屑粒径的分形维数ꎻN(l)是粒径大于l(单位为mm)的岩屑颗粒数量ꎻC1是与岩石粒径属性有关的常数ꎮ岩屑粒径越大ꎬ对应的岩屑颗粒数目越少ꎮ根据式(1)有lmin≪lmaxꎬ且由岩屑粒径密度分布函数f(l)和岩屑粒径分形维数可求得岩屑平均粒径l:f(l)=NlN(lmin)=Dll-Dl-1l-Dlmin(2)l=ʏlmaxlminlf(l)dl=DlDl-1lmin(3)式中:Nl为固定粒径长度为l的岩屑颗粒总数ꎮ由式(3)可知ꎬ岩屑平均粒径与岩屑分形维数呈正相关ꎬ岩屑分形维数越大ꎬ岩屑平均粒径也就越大ꎮ假定岩屑二维粒形是一个圆度较好的椭圆ꎬ根据几何学长径比的定义ꎬ由粒径长径比AR来描述粒形:AR=dmax/dmin(4)式中:dmax和dmin分别是椭圆长轴和短轴的长度ꎬmmꎬ且岩屑颗粒的长轴应为岩屑粒径ꎬ即dmax=lꎮ因此ꎬ当dmax=dmin时ꎬ岩屑粒形长径比有最小值ARmin=1ꎬ此时颗粒是一个正圆ꎮ假设岩屑颗粒长径比也应服从分形分布ꎬDs是岩屑长径比的分形维数ꎬC2是一个与岩石粒形属性有关的常系数ꎬ则类比公式(1)有ARmin≪ARmaxꎬ即ARmax≫1ꎮ若椭球是从二维椭圆绕长轴旋转而来ꎬ则根据椭球体积计算公式有椭球体积V0:V0=4π3dmax2æèçöø÷dmin2æèçöø÷dmin2æèçöø÷=π6d3maxAR2(5)㊀㊀对式(5)进行岩屑长径比和粒径积分可得岩屑总体积Vt:Vt=ʏARmaxARminʏllmin(V0NARd(AR))Nldl=πC1C2DlDs6(Ds+2)(3-Dl)l3-Dlmax=Cl3-Dlmax(6)式中:C为与岩石物性有关的比例常数ꎬ与岩屑尺寸㊁岩屑形状㊁岩性等属性相关ꎬ具体量值可由试验数据取得ꎮ由于岩石破碎体积为宏观表征ꎬ带入岩石孔隙度φꎬ可将式(6)转化为宏观表征体积VT:VT=Vt1-φ=C1-φl3-Dlmax(7)㊀㊀若岩石材料均质且密度均为ρꎬ则根据式(6)和式(7)ꎬ岩石岩屑尺寸小于l的累计质量ML和岩石岩屑总质量MT为:ML=ρVL=ρCl3-Dl(8)lnMLMT=(3-Dl)lnl-(3-Dl)ln(lmax)(9)式中:VL为岩石岩屑尺寸小于l的累计体积ꎮ由式(6)~式(9)可见ꎬ若破碎岩石生成岩屑粒径满足分形分布ꎬ则岩屑体积与岩屑质量也应满足分形分布特征ꎮ由于体积较难直接测量ꎬ可根据式(9)ꎬ利用不同粒径筛网求取特定PDC齿切削生成岩屑的粒径分形维数Dl和最大生成岩屑粒径lmaxꎮ2㊀基于岩屑粒径分形特征的PDC齿破岩比功评估模型㊀㊀破岩比功又称破岩比能或机械比功ꎬ通常是指破碎单位体积岩石需要消耗的能量ꎬ单位为MPaꎬ其值越大ꎬ表示破碎单位体积岩石要求的能量越多ꎬ能耗越大ꎮ若PDC齿匀速切削破碎岩石过程中受到钻压为FWOBꎬ则按照图1所示ꎬ分别以常规齿和锥形齿为研究对象ꎬ可以得到切削过程中沿水平方向PDC齿作用于破碎岩石的净切削力F(分别记作FC和FZ)为:F=Fh-f=FC=FWOBcosθ-μtanθ()㊀常规齿FZ=FWOB[cosα2-θæèçöø÷-㊀㊀μtanα2-θæèçöø÷]锥形齿ìîíïïïïïï(10)式中:Fh为钻压横向分量ꎬ用于克服摩擦力f和破碎岩石ꎬ单位均为Nꎻθ为PDC齿切削角度(对常规齿和锥形齿分别定义为后倾角和前倾角)ꎬ(ʎ)ꎻα为锥形齿顶角ꎬ(ʎ)ꎻμ为岩石对切削齿摩擦因数ꎮ则用于破碎岩石的净做功W为:W=FL(11)32023年㊀第51卷㊀第8期赫文豪ꎬ等:岩屑分形特征对PDC齿破岩性能影响规律研究㊀㊀㊀式中:L为沿切削方向切削距离ꎬmꎮ因此ꎬPDC齿破岩比功EMS可定义为:EMS=WVT=FL1-φ()Cl3-Dlmax=FWOBcosθ-f()1-φ()LCl3-Dlmax㊀㊀常规齿FWOBcosα2-θæèçöø÷-féëêêùûúú1-φ()LCl3-Dlmax㊀锥形齿ìîíïïïïïï(12)㊀㊀由式(12)可知ꎬPDC齿破岩比功与钻压㊁切削角度及锥形齿顶角㊁岩石孔隙度㊁生成岩屑最大粒径㊁岩屑粒径分形维数和地层岩性相关ꎮ图1㊀PDC齿匀速切削破岩力学物理模型Fig 1㊀MechanicsmodelofPDCcutterrock ̄breakingatconstantspeed3㊀PDC齿破岩比功评估模型验证为验证PDC齿切削生成岩屑形貌分形特征ꎬ利用自主研制的PDC齿单齿切削破岩试验装置开展相关室内试验ꎬ相关试验设备㊁测量方法和测量数据在文献[17-21]有详细叙述ꎮ试验采用的2种齿形分别为直径19mm常规齿和直径16mm锥形齿ꎮ其中常规齿总高度13mmꎬ包括金刚石层2mmꎻ锥形齿总高度21mmꎬ包括金刚石层8mmꎬ锥顶角为90ʎ且锥顶球面半径为2mmꎮ测试岩性为硬质花岗岩ꎬ其密度为2 62g/cm3ꎬ孔隙度为2 6%ꎬ单轴抗压强度约为150MPaꎮ试验过程中ꎬ通过改变PDC齿切削深度d㊁切削角度θ和切削速度v等破岩工艺参数可实时控制生成岩屑粒径大小ꎮ根据式(9)ꎬ通过收集并测量不同粒径下的岩屑质量与岩屑总质量占比ꎬ可作出lnMLMT~lnl的函数曲线ꎬ并由曲线斜率求取不同作业参数下的岩屑粒径分形维数和最大岩屑粒径ꎮ相关数据可见图2和表1ꎮ图2㊀PDC齿生成岩屑质量分数随粒径分布曲线Fig 2㊀DistributioncurveofmassfractionofcuttingsgeneratedbyPDCcutterwithitsparticlesize由图2和表1可知ꎬ在不同布齿工艺参数下PDC齿生成岩屑质量分数随粒径均呈现出显著的分形分布特征ꎬ除0 3mm切深条件下岩屑质量分数拟合优度为0 80外ꎬ其他布齿工艺参数下表现出的岩屑质量分数拟合优度均大于0 90ꎮ对于常规齿和锥形齿ꎬ岩屑粒径分形维数均随着PDC齿的切削深度增大而显著降低ꎬ类比于深层地层钻井过程ꎬ钻井深度增加ꎬ钻井切削深度降低ꎬ岩屑粒径分形维数增加ꎮ随着常规齿后倾角的增大或锥形齿前倾角的减小ꎬPDC齿生成岩屑粒径分形维数呈增加趋势ꎮ同时ꎬ根据表1中数据ꎬ切削速度对常规齿生成岩屑分形维数呈显著影响ꎮ为探究PDC齿破岩特性参数随作业参数变化关系ꎬ定义硬质PDC齿与岩石摩擦因数为0 4ꎬ利用混合逐步(CombinedStepwise)拟合方法ꎬ可求4 ㊀㊀㊀石㊀油㊀机㊀械2023年㊀第51卷㊀第8期得式(12)中相关参数随不同切削参数变化规律ꎬ如表2所示[22-23]ꎮ表1㊀PDC齿生成岩屑分形分布特征㊀㊀将表2中各关键参数拟合公式代入式(12)可求得PDC齿破碎硬质花岗岩破岩比功预测值ꎬ做图拟合PDC齿生成岩屑特征参数与破岩比功预测值和试验测量值ꎬ可得图3ꎮ设置拟合线截距为0ꎬ若拟合曲线斜率为1且拟合优度为1ꎬ则表明关键参数预测值与试验值拟合精度较高ꎮ常规齿生成岩屑分形维数㊁最大岩屑粒径㊁破岩横向切削力和破岩比功分别如图3a~图3d所示ꎻ锥形齿生成岩屑分形维数㊁最大岩屑粒径㊁破岩横向切削力和破岩比功分别如图3e~图3h所示ꎻ考虑常规齿和锥形齿的PDC齿破岩比功预测精度如图3i所示ꎮ由于图3所有曲线拟合斜率和拟合优度均接近1ꎬ表明模型预测精度高ꎬ可用于表征不同类型PDC齿在不同切削深度及布齿角度配合条件下PDC齿破岩性能ꎮ表2㊀PDC齿破岩比功理论模型关键参数拟合公式5 2023年㊀第51卷㊀第8期赫文豪ꎬ等:岩屑分形特征对PDC齿破岩性能影响规律研究㊀㊀㊀图3㊀PDC齿破岩比功理论模型精度评估Fig 3㊀EvaluationonaccuracyoftheoreticalmodelforrockbreakingspecificenergyofPDCcutter4㊀PDC齿破岩比功理论模型的应用针对不同类型PDC切削齿破岩性能ꎬ可将其破岩拟合规律与式(12)联立以求取不同类型PDC齿在不同切削参数下的破岩性能ꎮ如表2所示ꎬ本节内容主要针对常规齿和锥形齿探究PDC齿破岩性能ꎮ4 1㊀切削深度与切削角度对PDC齿生成岩屑分形特征影响规律㊀㊀定义切削角度为20ʎꎬ切削速度为5mm/sꎬ按表2中关键参数拟合规律ꎬ可得硬质花岗岩岩性在不同切削深度下PDC齿生成岩屑分形维数和最大岩屑粒径如图4a和图4b所示ꎮ在该讨论情况下ꎬ随着PDC齿切削深度的增加ꎬ锥形齿和常规齿生成岩屑的分形维数均显著降低ꎬ相较于锥形齿生成岩屑ꎬ平面齿生成岩屑的分形维数随PDC齿切削深度的增加呈线性降低ꎮ另外ꎬ随着PDC齿切削深度的增加ꎬ锥形齿和常规齿生成岩屑的最大粒径均呈线性增加ꎬ相较于常规齿ꎬ锥形齿生成岩屑最大粒径随切深变化较常规齿增幅显著ꎮ研究数据表明ꎬ同种岩性地层条件下ꎬ浅部地层硬度和岩石强度低ꎬPDC齿吃入深度大ꎬ生成岩屑分形维数小ꎬ最大岩屑粒径较大ꎻ但随着钻进深度的增加ꎬ地层硬度和岩石强度均显著增加ꎬPDC齿吃入深度小ꎬ生成岩屑分形维数大ꎬ岩屑最大粒径随着埋藏深度增加逐渐减小ꎮ相较于常规齿生成岩屑ꎬ相同岩性同等切深条件下锥形齿生成岩屑分形维数与最6 ㊀㊀㊀石㊀油㊀机㊀械2023年㊀第51卷㊀第8期大粒径均较大ꎮ由式(3)可证明锥形齿生成岩屑平均粒径大于平面齿生成岩屑平均粒径ꎬ间接说明了锥形齿脆性破碎能力强于常规齿ꎮ定义切削深度为1 5mmꎬ切削速度为5mm/sꎬ按表2中关键参数拟合规律ꎬ可得硬质花岗岩岩性在不同切削角度下PDC齿生成岩屑分形维数和最大岩屑粒径如图4c和图4d所示ꎮ在该讨论情况下ꎬ随着PDC齿切削角度的增加ꎬ锥形齿生成岩屑分形维数无显著变化ꎬ而常规齿生成岩屑的分形维数显著增大ꎬ但在讨论范围内仍低于锥形齿生成岩屑分形维数ꎮ另外ꎬ随着PDC齿切削深度的增加ꎬ常规齿生成岩屑最大粒径无显著变化ꎬ而锥形齿生成岩屑的最大粒径显著增大ꎬ且在讨论范围内普遍高于常规齿生成岩屑最大粒径ꎮ研究数据表明ꎬ同种岩性地层条件下ꎬ同等切削深度时ꎬ改变锥形齿布齿角度对于产生岩屑分形维数无显著影响ꎬ即岩屑生成平均粒径不变(或变化可以忽略不计)ꎬ但随着切削角度的增大ꎬ其最大岩屑粒径趋于增大ꎬ犁削效果显著ꎮ针对常规齿ꎬ同等切削深度下ꎬ改变常规齿布齿角度可以显著增大生成岩屑分形维数ꎬ即增大生成岩屑平均粒径ꎬ但却对生成岩屑最大粒径无明显效果ꎮ图4㊀PDC齿生成岩屑分形特征随切削深度和切削角度变化规律Fig 4㊀VariationoffractalcharacteristicsofcuttingsgeneratedbyPDCcutterwithcuttingdepthandcuttingangle4 2㊀岩屑分形特征对PDC齿单齿破岩钻压影响规律㊀㊀类比于4 1节试验数据ꎬ按表2中关键参数拟合规律可得硬质花岗岩岩性中PDC齿破岩钻压随不同切削参数下岩屑分形维数和岩屑最大粒径变化规律ꎬ如图5所示ꎮ在该讨论情况下ꎬ若固定PDC齿切削深度ꎬ则锥形齿生成岩屑分形维数与常规齿生成岩屑最大粒径均无显著变化ꎬ常规齿单齿破岩钻压在岩屑粒径分形维数大于2 4后ꎬ随岩屑分形维数呈逐渐升高趋势ꎬ而锥形齿单齿破岩钻压则随岩屑最大粒径增大而显著增加ꎮ若固定PDC齿切削角度ꎬ常规齿和锥形齿破岩单齿钻压均随着生成岩屑分形维数的增大而显著减小ꎬ且随着岩屑最大粒径的增大而显著增加ꎮ研究数据表明ꎬ同种岩性地层㊁同等钻压条件下ꎬ锥形齿生成岩屑分形维数和最大粒径均大于常规齿ꎬ这表明锥形齿更易形成大尺寸岩屑ꎬ其平均岩屑粒径和最大岩屑粒径显著大于常规齿ꎬ锥形齿脆性破碎能力较强ꎮ4 3㊀岩屑分形维数对PDC齿破岩比功影响规律类比于4 1节试验数据ꎬ按表2中关键参数拟合规律ꎬ可得硬质花岗岩岩性中PDC齿破岩比功随不同切削参数下岩屑分形维数和岩屑最大粒径变化规律ꎬ如图6所示ꎮ在该讨论情况下ꎬ若固定7 2023年㊀第51卷㊀第8期赫文豪ꎬ等:岩屑分形特征对PDC齿破岩性能影响规律研究㊀㊀㊀图5㊀PDC齿破岩单齿钻压随岩屑分形特征变化规律Fig 5㊀VariationofWOBofPDCcutterwithfractalcharacteristicsofcuttings图6㊀PDC齿破岩比功随岩屑分形特征变化规律Fig 6㊀VariationofrockbreakingspecificenergyofPDCcutterwithfractalcharacteristicsofcuttings8 ㊀㊀㊀石㊀油㊀机㊀械2023年㊀第51卷㊀第8期PDC齿切削深度ꎬ则锥形齿生成岩屑分形维数与常规齿生成岩屑最大粒径均无显著变化ꎬ常规齿单齿破岩比功随岩屑分形维数增大呈逐渐升高趋势ꎬ而锥形齿单齿破岩比功则随岩屑最大粒径先减小后增加ꎮ若固定PDC齿切削角度ꎬ常规齿和锥形齿单齿破岩比功均随着生成岩屑分形维数的增大而显著增大ꎬ且随着岩屑最大粒径的增大而趋于减小ꎮ研究数据表明ꎬ同种岩性地层同等破岩能量条件下ꎬ锥形齿生成岩屑分形维数和最大粒径均大于常规齿ꎬ表明锥形齿更易形成大尺寸岩屑ꎬ其平均岩屑粒径和最大岩屑粒径显著大于常规齿ꎬ脆性破碎能力较强ꎮ5㊀结㊀论(1)基于PDC齿切削破碎岩石过程中生成岩屑形貌特征ꎬ综合考虑PDC齿单齿钻压㊁岩屑粒径分形维数㊁岩屑最大粒径和地层岩性等因素ꎬ建立了基于岩屑粒径分形特征的PDC齿破岩比功评估模型ꎮ(2)针对性地开展了常规齿和锥形齿等PDC齿破碎硬质花岗岩破岩比功试验研究ꎬ岩屑分形维数㊁最大岩屑粒径㊁破岩横向切削力和破岩比功等试验测量值与模型预测值拟合效果好ꎬ模型预测精度高ꎮ(3)随着地层埋深的增大ꎬPDC齿吃入深度减小ꎬPDC齿预测生成岩屑分形维数逐渐增大ꎬ最大岩屑粒径显著减小ꎬ且锥形齿生成岩屑平均粒径大于常规齿ꎬ锥形齿脆性破碎能力强于常规齿ꎮ(4)切削角度对锥形齿生成岩屑分形维数和常规齿生成岩屑最大粒径无显著影响ꎬ但增大切削角度有助于增加锥形齿岩屑最大粒径和常规齿岩屑分形维数ꎮ(5)地层岩性相同时ꎬ同等钻压或破岩能量条件下ꎬ锥形齿生成岩屑分形维数和最大粒径均大于常规齿ꎬ更易形成大尺寸岩屑ꎬ也从另一个角度验证了锥形齿脆性破碎能力较强ꎮ参㊀考㊀文㊀献[1]㊀张杰ꎬ李荣鑫ꎬ李鑫ꎬ等.泡沫钻水平井岩屑颗粒的运移规律研究[J].钻采工艺ꎬ2022ꎬ45(1):53-58.ZHANGJꎬLIRXꎬLIXꎬetal.Migrationlawstudyoncuttingsparticlesforfoamdrillinginhorizontalwells[J].Drilling&ProductionTechnologyꎬ2022ꎬ45(1):53-58.[2]㊀李士斌ꎬ李玮.岩石可钻性分形法的可行性分析[J].大庆石油学院学报ꎬ2006ꎬ30(3):24-26ꎬ146.LISBꎬLIW.Feasibilityanalysisoffractalcharacteris ̄ticsofrockdrillability[J].JournalofDaqingPetrole ̄umInstituteꎬ2006ꎬ30(3):24-26ꎬ146. [3]㊀李玮ꎬ闫铁.岩石可钻性分形法的检验与评价[J].西部探矿工程ꎬ2013ꎬ25(1):52-54ꎬ58.LIWꎬYANT.Testingandevaluationoffractalmethodforrockdrillability[J].West ̄ChinaExplorationEngi ̄neeringꎬ2013ꎬ25(1):52-54ꎬ58. [4]㊀苏鹏.松辽盆地北部火成岩地层岩石可钻性与钻头选型研究[D].大庆:大庆石油学院ꎬ2010.SUP.Researchondrillabilityandbitselectionofigne ̄ousrocklayerinnorthofSongliaobasin[D].Daqing:DaqingPetroleumInstituteꎬ2010.[5]㊀易先中ꎬ王利成ꎬ魏慧明ꎬ等.钻井岩屑粒径分布规律的研究[J].石油机械ꎬ2007ꎬ35(12):1-4ꎬ94.YIXZꎬWANGLCꎬWEIHMꎬetal.Studyofthesizedistributionofdrillcuttings[J].ChinaPetroleumMachineryꎬ2007ꎬ35(12):1-4ꎬ94. [6]㊀黄小兵ꎬ陈次昌ꎬ董耀文.气体钻井的岩屑特征及粒度分布测试[J].天然气工业ꎬ2008ꎬ28(11):83-84.HUANGXBꎬCHENCCꎬDONGYW.Characteris ̄ticsofgasdrillingcuttingsandgrainsizedistributionde ̄termination[J].NaturalGasIndustryꎬ2008ꎬ28(11):83-84.[7]㊀李士斌ꎬ阎铁ꎬ李玮.钻井上返岩屑块度分形表示岩石可钻性方法[C]ʊ2006中国油气钻采新技术高级研讨会论文集.秦皇岛:中国石油学会ꎬ2006.LISBꎬYANTꎬLIW.Fractalrepresentationofrockdrillabilitybyusingdrillingupwardcuttings[C]ʊPro ̄ceedingsofthe2006ChinaAdvancedSymposiumonNewTechnologiesforOilandGasDrillingandProduc ̄tion.Qinhuangdao:ChinesePetroleumSocietyꎬ2006. [8]㊀李士斌ꎬ李玮ꎬ由洪利ꎬ等.基于分形理论的岩石可钻性分级方法[J].天然气工业ꎬ2007ꎬ27(10):63-66.LISBꎬLIWꎬYOUHLꎬetal.Classificationmeth ̄odsofrockdrillabilitybasedonthefractaltheory[J].NaturalGasIndustryꎬ2007ꎬ27(10):63-66. [9]㊀张立刚ꎬ吕华恩ꎬ李士斌ꎬ等.钻井参数实时优选方法的研究与应用[J].石油钻探技术ꎬ2009ꎬ37(4):35-38.ZHANGLGꎬLYUHEꎬLISBꎬetal.Researchandapplicationofdrillingparametersreal ̄timeoptimization92023年㊀第51卷㊀第8期赫文豪ꎬ等:岩屑分形特征对PDC齿破岩性能影响规律研究㊀㊀㊀[J].PetroleumDrillingTechniquesꎬ2009ꎬ37(4):35-38.[10]㊀闫铁ꎬ张杨ꎬ杜树明.基于岩屑分形破碎特征的钻井工程能效评价模型[J].岩石力学与工程学报ꎬ2014ꎬ33(增刊1):3157-3163.YANTꎬZHANGYꎬDUSM.Energyefficiencyeval ̄uationmodelindrillingbasedonfractalfragmentationcharacteristicsofrockcuttings[J].ChineseJournalofRockMechanicsandEngineeringꎬ2014ꎬ33(S1):3157-3163.[11]㊀陈小东.刮切 冲击复合破岩工具技术研究[D].成都:西南石油大学ꎬ2015.CHENXD.Researchonthetechnologyofscrapingimpactcompositerockbreakingtool[D].Chengdu:SouthwestPetroleumUniversityꎬ2015.[12]㊀陈子贺.松辽火山岩地层PDC钻头切削齿破岩机理研究[D].大庆:东北石油大学ꎬ2020.CHENZH.RockbreakingmechanismofPDCcutterappliedinSongliaovolcanicrockstratum[D].Daqing:NortheastPetroleumUniversityꎬ2020. [13]㊀李相勇ꎬ王春华ꎬ杨决算ꎬ等.深部难钻地层提速工具现状及发展趋势[J].西部探矿工程ꎬ2018ꎬ30(11):74ꎬ77.LIXYꎬWANGCHꎬYANGJSꎬetal.Currentsit ̄uationanddevelopmenttrendofspeedraisingtoolsfordeepdifficulttodrillstrata[J].West ̄ChinaExplora ̄tionEngineeringꎬ2018ꎬ30(11):74ꎬ77. [14]㊀汪海阁ꎬ黄洪春ꎬ毕文欣ꎬ等.深井超深井油气钻井技术进展与展望[J].天然气工业ꎬ2021ꎬ41(8):163-177.WANGHGꎬHUANGHCꎬBIWXꎬetal.Deepandultra ̄deepoil/gaswelldrillingtechnologies:pro ̄gressandprospect[J].NaturalGasIndustryꎬ2021ꎬ41(8):163-177.[15]㊀周立明ꎬ韩征ꎬ张道勇ꎬ等.中国新增石油和天然气探明地质储量特征[J].新疆石油地质ꎬ2022ꎬ43(1):115-121.ZHOULMꎬHANZꎬZHANGDYꎬetal.Charac ̄teristicsofincrementalprovenoilandnaturalgasgeo ̄logicalreservesinChina[J].XinjiangPetroleumGe ̄ologyꎬ2022ꎬ43(1):115-121.[16]㊀MANDELBROTBB.Thefractalgeometryofnature[M].SanFrancisco:W.H.Freemanꎬ1982. [17]㊀徐卫强ꎬ史怀忠ꎬ曹权ꎬ等.锥形PDC齿破碎砾岩特性试验研究[J].石油机械ꎬ2021ꎬ49(9):9-16.XUWQꎬSHIHZꎬCAOQꎬetal.Experimentalstudyonconglomeratebreakingcharacteristicsofconi ̄calPDCcutter[J].ChinaPetroleumMachineryꎬ2021ꎬ49(9):9-16.[18]㊀CHENGZꎬSHENGMꎬLIGSꎬetal.Imagingtheformationprocessofcuttings:characteristicsofcut ̄tingsandmechanicalspecificenergyinsinglePDCcut ̄tertests[J].JournalofPetroleumScienceandEngi ̄neeringꎬ2018ꎬ171:854-862.[19]㊀XIONGCꎬHUANGZWꎬYANGRYꎬetal.Com ̄parativeanalysiscuttingcharacteristicsofstingerPDCcutterandconventionalPDCcutter[J].JournalofPetroleumScienceandEngineeringꎬ2020ꎬ189:106792.[20]㊀XIONGCꎬHUANGZWꎬSHIHZꎬetal.Perform ̄ancesofastingerPDCcutterbreakinggranite:cuttingforceandmechanicalspecificenergyinsinglecuttertests[J].PetroleumScienceꎬ2023ꎬ20(2):1087-1103.[21]㊀CHENGZꎬLIGSꎬHUANGZWꎬetal.AnalyticalmodellingofrockcuttingforceandfailuresurfaceinlinearcuttingtestbysinglePDCcutter[J].JournalofPetroleumScienceandEngineeringꎬ2019ꎬ177:306-316.[22]㊀HEWHꎬCHENKYꎬHAYATDAVOUDIAꎬetal.Incorporatingtheeffectsofelementalconcentrationsonrocktensilefailure[J].InternationalJournalofRockMechanicsandMiningSciencesꎬ2019ꎬ123:104062.[23]㊀MONTGOMERYDCꎬRUNGERGCꎬHUBELENF.Engineeringstatistics[M].5thed.Hoboken:JohnWiley&Sonsꎬ2010.㊀㊀第一作者简介:赫文豪ꎬ副教授ꎬ生于1994年ꎬ2019年毕业于美国路易斯安纳大学系统工程专业ꎬ获博士学位ꎬ现从事油气井岩石破碎机理和油气资源与矿物材料的研究与教学工作ꎮ地址:(102249)北京市昌平区ꎮE ̄mail:hwh@cup edu cnꎮ通信作者:史怀忠ꎬE ̄mail:shz@cup edu cnꎮ㊀收稿日期:2023-02-18(本文编辑㊀刘㊀锋)01 ㊀㊀㊀石㊀油㊀机㊀械2023年㊀第51卷㊀第8期。
基于ABAQUS的PDC钻头切削齿破岩仿真及热分析

基于ABAQUS的PDC钻头切削齿破岩仿真及热分析张丽秀;申强;张珂;魏春雨【摘要】目的研究聚晶金刚石(PDC)钻头切削齿破岩过程中的温升及变形情况,确定在不同切削参数下PDC钻头单齿破岩时温升和变形的变化规律.方法利用非线性有限元仿真软件,建立了二维PDC钻头切削齿-岩石动态仿真模型,通过改变钻头切削齿破岩时的切削参数,得到了不同参数条件下切削齿温度和变形的变化规律,对切削齿破岩过程中的温升及热变形进行分析.结果切削温度在初始阶段上升较快,0.02s左右趋于平稳,同时切削深度对温度的影响最大;温度的升高以及切削力的变大,会使切削齿的变形增大.结论在PDC钻头单齿破岩的过程中,PDC切削齿的温度变化与其切削深度、切削速度以及齿前角密切相关.切削深度对其温度的影响较为明显.与所受的切削力相比温度对切削齿的变形影响较为明显.【期刊名称】《沈阳建筑大学学报(自然科学版)》【年(卷),期】2018(034)005【总页数】9页(P912-920)【关键词】PDC切削齿;破岩;温升;变形;有限元【作者】张丽秀;申强;张珂;魏春雨【作者单位】沈阳建筑大学机械工程学院,辽宁沈阳110168;沈阳建筑大学机械工程学院,辽宁沈阳110168;沈阳建筑大学机械工程学院,辽宁沈阳110168;沈阳建筑大学机械工程学院,辽宁沈阳110168【正文语种】中文【中图分类】TE921煤层气钻机在勘探钻井时,聚晶金刚石(PDC)钻头切削齿在破岩过程中,会产生明显的温升变化,如果钻头的温度过高,其产生的热应力不但会超过材料的最大许用强度从而造成钻头的失效,影响其使用寿命,同时温度的升高必然也会导致钻头切削齿的热变形从而影响其切削效率[1-2].MAMALIS A G等 [3]研究了在高速切削过程中塑性形变消耗的功率与热量的转化关系.VORONTSOV A L 等[4]研究了刀具前角对切削温度的影响关系.CAO L等[5]对切削过程进行了三维顺序耦合热应力分析,并将仿真所得到结果与其所做的实验结果进行对比分析,对有限元方法的可行性进行了验证.杨晓峰等[6]深入研究了钻头破岩的传热过程,从而建立了钻头切削破岩过程中温度场的微分方程组以及温度场的边界条件.阳启华[7]等人利用有限元分析软件,对切削过程中刀具的温度场进行了模拟分析,得出了刀具前角对切削温度的影响规律.龙巾帼等[8]模拟了热-结构耦合场下 PDC切削齿破岩过程,通过对比理论计算结果,确立了其方法的可行性.可见,大多研究是只对切削过程中的温度变化情况做了分析,并没有考虑到温升对切削齿变形的影响情况及其PDC 钻头切削齿破岩很强非线性的特征[9-10].基于此,笔者首先利用有限元方法对PDC钻头切削齿切削岩石过程中温升变化进行研究,建立了二维切削齿-岩石切削仿真模型,并采用岩石弹塑性D-P 模型[11-14]以及材料失效准则来模拟钻头切削齿动态破岩过程中的切屑与岩石的分离,模拟了钻头切削齿动态破岩过程,然后通过仿真所得的结果对切削齿的变形影响因素进行分析,确定在不同切削参数下PDC钻头单齿破岩时温升和变形的变化规律.1 PDC钻头破岩热理论分析1.1 破岩过程生热机理煤层气钻机工作时,PDC钻头钻削岩石的过程中,切削力所做的功很大一部分都被转化为热能,即切削热.由于瞬时切削所产生大量的热量在短时间内无法快速扩散,导致了在切削区域的温度大幅度升高.温度的急剧上升,会降低切削区域的岩石硬度和强度,有利于切削的进行,但是切削齿温度的升高,不仅加快了钻头切削齿的热磨损程度还会使整个钻头体产生相应的热变形,造成切削齿PCD表面层的损伤和破坏,从而影响其钻进效率,如果长时间处于高温状态就会使PDC钻头失效[15-17].钻头切削齿在破岩的过程中产生的热量主要来自于两个方面:一是切削岩石时使岩石发生弹性变形和塑性变形而产生的热量;二是在破岩时切削齿与岩石基体以及产生的岩屑相接触时,由于滑动摩擦而产生的大量摩擦热量.假设钻头进给时消耗的能量忽略不计,钻头切削过程中所产生的热量为Q=Fcv1.(1)式中:Q为切削热;Fc为主切削力;v1为切削速度.1.2 切削过程热传导分析钻头的破岩过程是一个极其复杂的热传导过程,无法利用公式准确地计算出钻头工作时的实际温度,同时摩擦热是钻头温升的主要来源.由于PDC 复合片的导热率要远远大于岩石的导热率,在破岩时岩石和岩屑的温度相比切削齿的温度会较高.在破岩过程中岩石与切削齿是面接触,所以岩屑表面层温度相对较高,而岩体则由于导热率偏低,沿岩石深度方向温度函数降低最快.1.2.1 导热微分方程想要准确描述切削齿的温度场的变化情况,就要全面考虑切削过程中的岩石、切屑以及周围环境等复杂的影响因素,通过傅里叶导热定律和能量守恒定律推导出导热微分方程.(2)式中:kx、ky、kz分别为沿着各方向的热传导系数;Q(x,y,z,t)为内部的热源强度;ρ为材料密度;cT为比热容.1.2.2 温度场边界条件在切削区接触面上通过摩擦所产生的热流密度与温度 T的关系可由傅里叶定律推导出:(3)假设在整个切削过程中,摩擦热全部是由摩擦力所做的功转化而来,会有:(4)式中:nx、ny、nz为边界处外法线的方向余弦;为边界上的热流密度;μ为摩擦系数;F为接触面正法向力;v2为滑动摩擦速度.2 PDC切削齿破岩有限元模型的建立设置岩石基体长度为120 mm,高度为30 mm,PDC切削齿直径为13.44 mm,厚度为5 mm,其中PDC复合片1 mm,碳化钨基体4 mm.装配时将切削齿的齿前角设置为10°,切削深度为2 mm.装配后的二维模型如图1所示.图1 PDC切削齿破岩有限元几何模型Fig.1 Finite element geometric model of PDC cutting tooth breaking rock考虑到存在于煤层附近的基本都是沉积岩,同时砂岩在沉积岩中是非常普遍的,并且在煤层附近分布很广,因此在建模时岩石的基本参数选择砂岩作为其主要参数,建模时所用到的主要材料参数如表1所示.表1 有限元分析物理热力学性能参数Table 1 Finite element analysis of physical thermodynamic performance parameters材料弹性模量/GPa密度/(kg·m-3)热导率/(J·(ms·℃)-1)比热容/(J·(kg·℃)-1)热膨胀系数/106 ℃泊松比PDC层8903 5505528002.70.07硬质合金58215 2001102605.40.22岩石392 6303.58406.00.25切削齿和岩石模型都采用四边形单元进行划分,单元类型选择四节点热耦合平面应变四边形减缩积分单元:CPE4RT.在载荷模块中设置边界条件,创建初始的边界条件使岩石的左下底面完全固定,在创建分析步中的边界条件为沿着X轴负方向切削速度为2 m/s,创建预定义初始温度为20 ℃,根据建模时岩石的长度以及切削速度设置分析步的时间为0.05 s.笔者在模拟切削齿动态切削岩石的过程中,运用了材料失效准则(剪切损伤)与失效单元删除相结合的方法,模拟出了切削过程中的切屑与岩石的分离效果.3 仿真结果分析3.1 切削齿温度分布分析图2为建模后的某一时刻的动态破岩过程已经成功地模拟了切削齿切削岩石时的切屑与岩石的分离,由于切削齿的网格划分较密,为观察切削齿的温度变化情况,在软件中创建显示组单独显示切削齿并将其进行局部放大.图2 切削齿动态切削岩石过程Fig.2 Dynamic cutting process of the cutting tooth图3为设置切削齿为显示组之后切削齿在切削过程中的温度变化及分布情况.可以发现最高温度出现在切削齿与切屑的接触区,这是由于在破岩过程中岩石受到弹塑性变形从而产生了大量的热能,使得在切削齿前齿面的接触区出现很高的温度.同时还可以看到切削齿的一些部位仍然处于初始温度,这是因为在切削岩石的过程中,接触区域摩擦表面的滑动速度很快,接触时间较短,由于摩擦瞬时产生的摩擦热来不及向内部扩散.所以,在切削过程中所产生的摩擦热量绝大部分集中在切削齿前齿面处的表面较薄的区间,使得切削齿外表面的温度很高,这会使岩石表层软化并降低岩石的强度、硬度,从而更有利于破岩的进行.图3 切削齿随时间变化的温度云图Fig.3 The temperature of the cutting tooth varies with time图4为在切削深度为1 mm、切削速度为2 m/s、齿前角为10°的情况下,选取切削齿前齿面上某一节点的温度变化情况.可以看出切削齿前齿面的温度在切削的初始阶段上升很快,大约在0.01 s内就完成了整个温度的上升阶段.在随后的时间里,温度处于较为稳定的状态,这是因为受到削齿前齿面与切屑间发生的强烈的摩擦热及切屑变形热的作用,而且切削温度是一个不断积累的过程,在切削区域塑性变形和摩擦产生的热都在不断的积累导致温度会随着时间的增加而上升,最后达到相对热平衡状态.热平衡状态下温度曲线呈现出在一定的范围内上下波动的状态,这也比较符合塑脆性材料在达到相对稳定状态时,其稳定值不会一直处于平稳不变的状态,而是会在一定的幅度内上下波动的基本特征.图4 切削齿前齿面一节点温度时间曲线Fig.4 The time curve for front tooth surface temperature of cutting tooth3.2 切削参数对切削温度的影响分析3.2.1 切削深度对切削齿温度的影响分析图5为切削速度为1.5 m/s,齿前角为10°时的不同切削深度下对应的温度曲线.可以看出,随着切削深度的增加切削齿的温度也在逐渐升高.这是由于在切削的初始阶段,切削深度较小时,切削过程主要产生的是挤压破碎粉屑,这时主要是热传导过程导致切削齿温度的上升,温度的最大值变化不太明显;而当切削深度增大时,岩石的剪切面增大,从而增大了岩石的剪切变形,相应随着剪切变形所做的功也增大,导致了摩擦产生的热量也在增加,因此在整个切削过程中,切削温度会逐渐上升.在实际工程应用中,由于地层周围复杂的地理环境和破岩工作状况的波动会对PDC切削齿造成一定的冲击,过多的进给量(切削深度)会使钻头切削齿承受过高的冲击载荷,从而对PDC 切削齿造成损坏.因此,在钻机实际钻井工作中需要控制在合理的进给量范围内来保证钻机钻进过程的顺利进行,而2 mm处于比较适中的深度,更具有代表性,因此选用2 mm作为进一步研究切削速度和齿前角对温度的影响的切削深度.图5 温度随切削深度的变化Fig.5 The temperature varies with the depth of the cutting3.2.2 切削速度对切削齿温度的影响图6为在切削深度为2 mm,齿前角为10°时,不同切削速度下的温度变化图.从图6(a)可看出,在切削初始阶段,切削齿温度上升很快,而后随着切削过程的进行,温度变化波动趋于平缓,最后达到了一个相对稳定状态.不同的切削速度进入稳态的时间也不同,切削速度越大,进入稳态的时间就越短,达到稳定状态时的温度值也就越高.随着切削速度的增大,达到热平衡的时间越短.经过分析得出,在钻头切削岩石的过程中,随着切削速度加快的同时,切削所产生的岩屑速率也在逐渐增加,这就导致切削产生的热量还没来得及传导到切削齿就被岩屑带走了,因此被岩屑带走的这部分热量也在增加,所以随着切削速度的增加温度上升的速率在逐渐变缓.由图6(b)所示可得,在相同的切削深度和齿前角的条件下,随着切削速度的增加,切削齿的平均温度也在逐渐升高.图6 温度随切削速度的变化Fig.6 The temperature varies with the cutting speed3.2.3 齿前角对温度的影响分析图7为在切削深度为2 mm,切削速度为2 m/s时,达到热平衡时的齿前角在0°,5°,10°,15°,20°时切削齿的温度-齿前角关系图.从图中可以看出当齿前角为0°和5°时,切削齿的温度较高并且当齿前角为5°时温度达到最大,当切削角从10°到20°时,温度逐渐降低.PDC钻头刀翼上的切削齿的齿前角都是负值[18],因为负齿前角可以提高钻头的破岩效率.但是负的齿前角会加大切削齿对岩屑的挤压变形,产生排屑较困难的情况,增加了岩屑与切削齿前齿面的接触面积和接触时间,使摩擦加剧,摩擦热量也会增加.在实际工程中切削深度一样的情况下,需要找出合适的齿前角角度,过大或过小的齿前角都有可能导致钻头扭矩和钻压增大,切削齿就越容易造成损伤,虽然根据仿真结果显示齿前角在20°时的温度最低,但是综合考虑到钻头所受的扭矩和钻压以及钻头工作时的实际齿前角角度,最佳齿前角为10°~15°.图7 温度随齿前角的变化Fig.7 The change of temperature with the tooth front angle3.3 切削齿的变形分析3.3.1 温度对切削齿的变形影响切削齿切削岩石的过程中,切削齿的温度最高可上升至将近100 ℃左右,但是在钻机实际工作过程中受到复杂的地理环境以及外界环境的影响,钻头的温度一般都会高于此温度.因此,在仿真过程中设置对切削齿的基本载荷温度为100 ℃,切削齿的最大变形量u在0.036 14 μm.图8为在切削深度为1 mm、切削速度为2 m/s、齿前角为10°的条件下温度和受力对切削齿的变形情况.在300 ℃时,最大变形量为0.108 4 μm.结果显示需要把变形缩放系数设置为一致.可以看出随着切削温度的升高切削齿的变形也在不断的增大.图8 温升引起的切削齿的变形图Fig.8 The deformation of the cutting tooth caused by the temperature rise3.3.2 切削力对切削齿变形的影响由于目前的切削力的计算只针对于刀具切削金属条件下,还没有切削岩石这方面的切削力的计算式.根据文献[19-20]的实验数据得出主切削力为200~900 N,图9为在切削深度为1 mm、切削速度为2 m/s、齿前角为10°的条件下温度和受力对切削齿的变形情况.可以看出随着切削力的增大,变形也在不断增大,并且产生的应变范围相对较广.图9 受力引起的切削齿的变形图Fig.9 The deformation of the cutting toothcaused by force3.3.3 温度和切削力对切削齿的变型影响将其所受的载荷温度及切削力同时加载到切削齿上,进行有限元仿真.图10为在切削深度为1 mm、切削速度为2 m/s、齿前角为10°的条件下温度和受力对切削齿的变形情况.从仿真结果可以看出,温度对切削齿变形的影响要明显大于切削力对切削齿变形的影响.因此,在只针对于切削齿变形的影响因素中,要优先考虑温度对其所带来的影响程度.图10 热力耦合引起的切削齿的变形Fig.10 The deformation of the cutting tooth caused by thermo-mechanical coupling4 结论(1)根据切削温升-时间变化曲线可得出破岩过程中切削齿上的温度分布情况,在切削的初始阶段切削齿的温度上升很快,在0.02 s左右温度上升速度趋于平缓,最终达到热平衡状态.(2)与切削速度、齿前角对切削温度的影响相比.切削深度对切削齿温度影响更大,在切削深度为3 mm时最高温度可达90 ℃左右.(3)切削齿的变形随着温度的升高以及切削力的增大而增大,在300 ℃时最大变形为0.108 4 μm,而在800 N的切削力时的变形为0.026 6 μm,由此可得温度对切削齿的变形影响更为明显.参考文献【相关文献】[1] BESTE U,JACOBSON S.A new view of the deterioration and wear of WC/Co cemented carbide rock drill buttons[J].Wear,2008,264(11):1129-1141.[2] 王红波,刘娇鹏,鲁鹏飞,等.PDC钻头发展与应用概况[J].金刚石与磨料磨具工程,2011,31(4):74-78.(WANG Hongbo,LIU Jiaopeng,LU Pengfei,et al.General situations of development and application of PDC bits[J].Diamond & abrasives engineering,2011,31(4):74-78.)[3] MAMALIS A G,HORVATH M,BRANIS A S,et al.Finite element simulation of chip formation in orthogonal metal cutting[J].Journal of materials processingtech,2009,110(1):19-27.[4] VORONTSOV A L,SULTAN-ZADE N M,ALBAGACHIEV A Y,et al.Development of a new theory of thermal cutting processes 3.Influence of cutter’s front angle on the cutting temperature and influence of preheating of the blank on the cutting force[J].Russian engineering research,2010,30(3):274-275.[5] CAO L,SHEN X J,LI R Y.Three-dimensional thermal analysis of spherical plain bearings with self-lubricating fabric liner[J].Advanced materials research,2010,97/101:3366-3370.[6] 杨晓峰,李晓红,卢义玉.岩石钻掘过程中的钻头温度分析[J].中南大学学报(自然科学版),2011,42(10):3164-3169.(YANG Xiaofeng,LI Xiaohong,LU Yiyu.Temperature analysis of drill bit in rockdrilling[J].Journal of central south university(natural science edition),2011,42(10):3164-3169.)[7] 阳启华,杜茂华,蒋志涛.基于ABAQUS的金属切削过程中刀具温度场模拟研究[J].工具技术,2008,42(11):31-33.(YANG Qihua,DU Maohua,JIANG Zhitao.Temperature field simulation of cutting tool in metal cutting process on ABAQUS[J].Tool technology,2008,42(11):31-33.)[8] 龙巾帼.PDC 钻头齿破岩热-结构耦合有限元仿真分析[D].成都:西南石油大学,2012. (LONG Jinguo.PDC drill bit tooth-rock thermal-structural coupling finite element simulation analysis[D].Chengdu:Southwest Petroleum University,2012.)[9] 路德春,杜修力.岩石材料的非线性强度与破坏准则研究[J].岩石力学与工程学报,2013,32(12):2394-2408.(LU Dechun,DU Xiuli.Research on nonlinear strength and failure criterion of rock materials[J].Chinese journal of rock mechanics and engineering,2013,32(12):2394-2408.)[10] STERPI D,GIODA G.Visco-plastic behavior around advancing tunnels in squeezing rock[J].Rock mechanics & rock engineering,2009,42(2):319-339.[11] ALEJANO L R,BOBET A.Drucker-prager criterion[J].Rock mechanics and rock engineering,2012,45(6):995-999.[12] QI Y,JIANG Q,WANG Z,et al.3D creep constitutive equation of modified nishihara model and its parameters identification[J].Chinese journal of rock mechanics &engineering,2012,31(2):347-355.[13] 丁祥,张广清,王芝银.关联Drucker-Prager条件下等效塑性应变系数[J].应用力学学报,2017,34(1):1-7.(DING Xiang,ZHANG Guangqing,WANG Zhiyin.Coefficient of effect plastic strain based on associated flow of Drucker-Prager criterion[J].Chinese journal of appliedmechanics,2017,34(1):1-7.)[14] 袁小平,刘红岩,王志乔.基于 Drucker-Prager 准则的岩石弹塑性损伤本构模型研究[J].岩土力学,2012,33(4):1103-1108.(YUAN Xiaoping,LIU Hongyan,WANG Zhiqiao.Study of elasticplastic damage constitutive model of rocks based on Drucker-Prager criterion[J].Rock and soilmechanics,2012,33(4):1103-1108.)[15] 张富晓.PDC钻头切削齿失效分析与耐磨抗冲击性能试验研究[D].成都:西南石油大学,2014. (ZHANG Fuxiao.The failure analysis of PDC drill bit and the experimental study of its wear and impact resistance[D].Chengdu:Southwest Petroleum University,2014.)[16] ZEREN M,KARAGOZ S.Sintering of polycrystalline diamond cut-ting tools[J].Materials & design,2007,28(3):1055-1058.[17] 吴金炎,王庆明.基于热力耦合模型的金属切削过程有限元分析[J].机械,2009,36(2):18-21. (WU Jinyan,WANG Qingming.Finite element analysis of metal orthogonal cutting process based on coupied thermo-mechanical model[J].Machinery,2009,36(2):18-21.)[18] 邹德永,曹继飞,袁军,等.硬地层PDC钻头切削齿尺寸及后倾角优化设计[J].石油钻探技术,2011,39(6):91-94.(ZOU Deyong,CAO Jifei,YUAN Jun,et al.Optimization design of the cutter size and back rake for PDC bit in hard formation[J].Petroleum drilling techniqus,2011,39(6):91-94.) [19] 张明,王菲,杨强.基于三轴压缩试验的岩石统计损伤本构模型[J].岩土工程学报,2013,35(11):1965-1971.(ZHANG Ming,WANG Fei,YANG Qiang.Statistical damage constitutive model for rocks based on triaxial compression test[J].Chinese journal of geotechnicalengineering,2013,35(11):1965-1971.)[20] 秦朝.三轴围压条件下岩石力学性质的实验研究[D].成都:西南石油大学,2014.(QIN Chao.Experimental study on mechanical properties of rock under three-axis confining pressure[D].Chengdu:Southwest Petroleum University,2014.)。
ú

【 参考文献 】
… 1 曹立 刚 , 郭海林, 顾 谦 隆. 煤 层 气 井排 采过 程 中 各排 采参
数 间 关 系的探 讨 卟 中国煤 田地 质 , 2 0 t 1 0 , 1 2 ( 1 ) : 3 1 — 3 5
【 2 J吕景昶 , 朱 礼斌 , 张涛. 煤 层 气 井排 采 工 艺技 术 U ] . 油 气 井
抽油杆上分段加装增 抽器或举液器 ,同时对煤粉浓度 大 、容易 堵 塞 泵 球 座 的 井 配 合 使 用弹 簧 球 座 从 而 达 到 多 级举 升 、提 升 泵 效 、防止煤粉或压裂砂卡泵的工艺。
4 结 论
为排 水段 、憋压段 、控压段 、高产稳产段 和衰竭段 ;三压为井
底 流 压 、解 吸 压 力 、地 层 压 力 );排 采 工 艺 上 做 了 相 应 的 创
2 1 / 1 4 年 刘 国伟 针 对 多分 支 水平 井 排 采特 征 ,将 其生 产过 程
采过程 中生产压差与储层渗透率 、煤粉运移量 、气体解吸时机
的 一个 综 合 关 系 ,既 可 以 指 导 煤 层 气 井有 效 排 采 ,又 可 以 降 低 煤粉 对 井筒 内设备 的磨 损 。
田地 质 与勘探 ,2 0 0 8 ,3 6 ( 2 ) : 2 0 — 2 7
酶液
阶段
捧水 产气
阶 段 瓣 段
艇产
黔 段
ห้องสมุดไป่ตู้
阶段
【 5 】 李金海, 苏现 波, 林 晓 英, 等. 煤 层 气井排 采速 率 与 产 能 的
关系 煤炭 学报 , 2 1 ) 0 9 , 3 4 ( 3 ) : 3 7 6 — 3 8 0
新 ,采 用 抽 油机 +管 式 泵 +电子 压 力 计 和 防 卡 泵 防气 锁 配 套 工
井喷
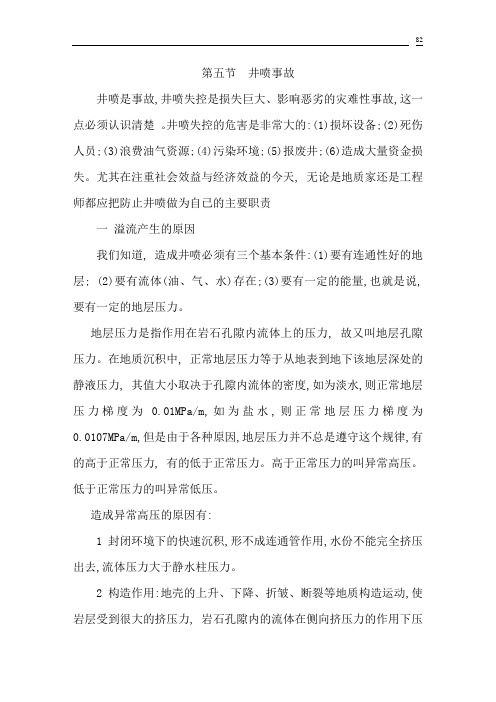
第五节井喷事故井喷是事故,井喷失控是损失巨大、影响恶劣的灾难性事故,这一点必须认识清楚。
井喷失控的危害是非常大的:(1)损坏设备;(2)死伤人员;(3)浪费油气资源;(4)污染环境;(5)报废井;(6)造成大量资金损失。
尤其在注重社会效益与经济效益的今天,•无论是地质家还是工程师都应把防止井喷做为自已的主要职责一溢流产生的原因我们知道,•造成井喷必须有三个基本条件:(1)要有连通性好的地层;•(2)要有流体(油、气、水)存在;(3)要有一定的能量,也就是说,要有一定的地层压力。
地层压力是指作用在岩石孔隙内流体上的压力,•故又叫地层孔隙压力。
在地质沉积中,•正常地层压力等于从地表到地下该地层深处的静液压力,•其值大小取决于孔隙内流体的密度,如为淡水,则正常地层压力梯度为0.01MPa/m,如为盐水,则正常地层压力梯度为0.0107MPa/m,但是由于各种原因,地层压力并不总是遵守这个规律,有的高于正常压力,•有的低于正常压力。
高于正常压力的叫异常高压。
低于正常压力的叫异常低压。
造成异常高压的原因有:1 封闭环境下的快速沉积,形不成连通管作用,水份不能完全挤压出去,流体压力大于静水柱压力。
2 构造作用:地壳的上升、下降、折皱、断裂等地质构造运动,使岩层受到很大的挤压力,•岩石孔隙内的流体在侧向挤压力的作用下压力升高。
3 热能增压作用;•如地层是一个封闭系统,随着沉积的加深,地温的升高,孔隙中的流体将随温度的升高而膨胀,形成高压。
4 地化作用:在沉积的封闭系统中,沉积物内的蒙脱石向伊泥石转化,石膏向硬石膏转化,都要脱出过量的水,增加了地层压力。
在钻井过程中,一方面岩层孔隙中的流体有着压力P p,我们叫地层压力,另一方面井眼中的钻井液也会产生液柱压力P m,我们叫井底压力,在正常情况下,•我们正是用井底压力P m来平衡地层压力P p的,因此,为了保持地层和井眼系统的压力平衡,应该建立和维持下列平衡关系P m=P p+P e……………………………………………………………………………………………………………………………(5 -1)只要在渗透性好的地层中有流体存在,不论其压力高低,•只要它的压力高于钻井液液柱压力就能产生溢流。
地应力与压裂力学----水力压裂
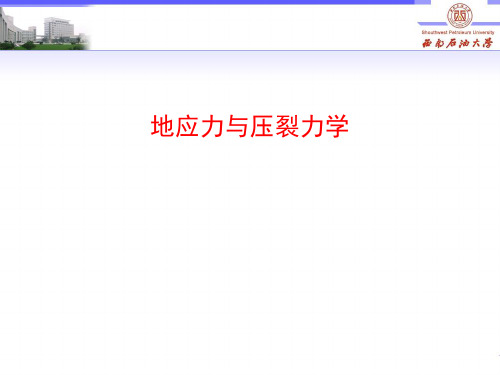
tectmin
Eh 1 1 21 2 r2 r1
-O h
构造主曲率与井所处 的位置有关。可以通过趋 势面分析法,利用构造图 上的各点x,y坐标及高程 数据,可建立正归方程来 求取。
性 中
Oh
dz d x2
T=1/2H
2
=
1
r
面
R2
R1
0
X
地应力来源
基本概念
重力应力、构造应力与热应力
重力应力(gravity stress ):指由于上覆岩层(overburden )的重量引 起的地应力分量,特别指由于上覆岩层的重量产生的水平应力(horizontal stress )大小。 构造应力(structural stresses ):由构造运动在岩体中引起的应力叫构 造应力。在地质力学中常把构造应力叫做地应力,是指导致构造运动、形成 各种构造形迹的那部分应力。
不完全闭合,因此即可在油气层中形成一条具有足够长度、宽度和高度的填砂 裂缝。此裂缝具有很高的渗滤能力,并且扩大了油气水的渗滤面积,故油气可
畅流入井,注入水可沿裂缝顺利进入地层,从而达到增产增注的目的。
压裂第一步就是造缝
一
地应力研究
1. 地应力概述 2. 地应力在水力压裂施工中的应用 3. 地应力大小的确定 4. 地应力方向的研究方法
地应力与压裂液的选择
主要表现在对压裂液的摩阻和压裂液的流变性要求上。
Pstp Pbhtp Pf Ppnwb Ph 3 h H ps t Pf Ppnwb Ph
Pstp Pbhtp Pf Ppnwb Ph
地面施工泵压恒定时,最小主应力越大,要求摩阻压力越小。 降低施工摩阻,一是降低施工排量,二是进一步降低压裂液的粘度。 施工摩阻的降低是有一定限度的:排量太低,增加脱砂风险;降低压
- 1、下载文档前请自行甄别文档内容的完整性,平台不提供额外的编辑、内容补充、找答案等附加服务。
- 2、"仅部分预览"的文档,不可在线预览部分如存在完整性等问题,可反馈申请退款(可完整预览的文档不适用该条件!)。
- 3、如文档侵犯您的权益,请联系客服反馈,我们会尽快为您处理(人工客服工作时间:9:00-18:30)。
第31卷第5期2003年10月 石 油 钻 探 技 术PETROLEUM DRILLING TECHNIQUES Vol.31,No.5Oct.,2003
收稿日期:2003-07-01作者简介:王瑞和(1957—),男,教授,博士生导师。联系电话:(0546)8394360
校庆专栏 破岩钻井方法及高压水射流破岩机理研究
王瑞和,倪红坚,周卫东(石油大学油气井工程学科,山东东营 257061)摘 要:简要分析回顾了破岩和钻井方法的发展,论述了激光钻井和高压水射流钻井的发展潜力,阐明了高压水射流钻井技术已具备工业应用的可行性。分析了高压水射流破岩机理研究中的关键问题及解决途径,介绍了利用数值模拟和试验相结合的方法研究高压水射流破岩机理所取得的一些突破性进展,提出了建立和完善高压水射流破岩理论体系、发展水射流钻井技术的研究方向。关键词:钻井;射流;岩石破碎;机理;数值模拟;模拟试验中图分类号:TE248 文献标识码:A
文章编号:1001-0890(2003)05-0007-04
随着人类社会进入21世纪,经济和社会的发展对油气资源的需求进一步增加,而油气生产却受到后备储量严重不足和开采难度不断增大的严峻挑战。油气钻井作为建立开采地下油气资源通道的唯一手段,一直在油气勘探、开发全过程中发挥着不可替代的重要作用。油气钻井技术的进步,推动了石油工业的发展,社会发展对油气的需求又促进了钻井新技术的产生。有利于发现和保护油气藏的欠平衡钻井技术和以MWD、LWD、SWD为核心的导向钻井技术等,就是为适应现代油气钻井面临的更深和更复杂的地质条件、复杂井眼轨迹和井身结构以及提高采收率的要求而产生并不断发展的。随着钻井深度的不断加大,传统破岩钻井方式中能量的有效利用率越来越低。随着井眼轨迹和井身结构的复杂程度不断增加,尤其在三维井眼大斜度井段钻井过程中,钻压的传递和施加非常困难,从而严重降低了传统钻井方法的破岩效率和机械钻速,导致油气钻井的质量、速度和效益下降。因此,研究新的破岩方法和机理,形成新的钻井技术,以提高钻井的效率和效益,已成为钻井工程领域面临的事关可持续发展的战略任务。1 破岩钻井方法的发展1.1 破岩机理和方式钻井过程中,只有及时破碎井底岩石才能使井眼不断延伸,最终形成开采地下油气藏的通道。不同的破岩机理和方式,具有不同的适用条件,也决定了钻井的方法和效率。目前破岩方式按岩石破碎的基本机理可分为热力破坏、熔融和汽化、化学溶解及机械破碎四种[1]。热力破坏是指快速作用于岩石表面的高热应力超过岩石强度时,岩石会发生热力剥落而破碎;当岩石被加热到足够高的温度时,则会被熔融或汽化,如火成岩熔化温度为1100~1600°C,石灰岩则在2600°C以上;化学溶解是采用能与岩石产生强烈化学反应的化学药剂溶解岩石,从而达到破碎消除岩石的目的;机械破碎是指通过冲击、剪切、磨蚀等机械方式进行岩石破碎。当岩石上机械作用产生了超过岩石强度的拉伸或剪切应力时,岩石就会产生塑性或脆性破碎。机械破碎是最典型、最常用的一种破碎形式,目前传统的钻井方式均采用该方法破岩。1.2 传统钻井方法的发展破岩钻井技术的发展经历了由简单到复杂、由原始到现代的过程。虽然破碎岩石的方法有多种,但要真正用于实际,必须具备安全、经济和可以实现的特点。最早真正意义上的破岩钻井技术起源于中国的盐井采掘,采用的是顿钻法。1041年,中国利用顿钻法在四川自贡市大安区钻成了世界上第一口超千米的盐井——海井,而西方直到1808年才开始使用顿钻法采盐。因此,该技术也被称为继造纸术、指南针、火药及印刷术之后的中国第五大发明[2]。
18世纪90年代初,美国得克萨斯州的水井钻井承包商首先利用了旋转钻井法打出了水井。1900年,石油钻井工作者借鉴旋转钻井法打水井的经验,首次将该方法应用于油井钻井[2]。由于旋转钻井法是通过
在钻头上施加一定的轴向压力(钻压),并利用转盘或井下动力钻具带动钻头旋转,使井底岩石在冲击、剪切及压碎等多种作用下发生破碎,破岩效率高,钻进速度快,不但能钻浅井,还可以钻深井,因此,从它问世以来,便得到了迅速的发展。到目前为止,旋转钻井法在油气钻井领域内占绝对的主导地位,世界范围内的绝大多数油气井都是采用该方法钻成的。1.3 破岩钻井新方法社会的进步,科学技术的发展,对石油、天然气等地下资源需求的不断增长,以及人类认识地球内部奥秘的迫切愿望,推动了钻井破岩技术的迅速发展。自20世纪60年代末开始,美国国家科学基金会发起了探寻高效破岩方法的庞大研究计划,研究了电子束、激光、水射流等25种破岩新方法。在中等强度的岩石上进行的切割实验,得出了高压水射流、激光、电子束、等离子体4种典型破岩方法所消耗的能量范围分别为:250~500、1000~2000、3000~6000、50000~100000J/cm2[1]。由此可以看出,最易于实现且效率高的方法当属高压水射流破岩法和激光破岩法。高压水射流破岩仍属于机械破碎,激光破岩则属于熔融和汽化方式。1.3.1 激光钻井20世纪70年代,在美国、法国和荷兰出现了激光钻井的研究文献和专利。但由于当时的激光技术限制,无法满足岩石破碎的高能量要求。1990年,美国天然气研究所(GRI)的研究中仍认为激光钻井难以实现,直到1999年,GRI完成的一项旨在彻底改变天然气井钻井和完井方法的研究中才肯定了激光钻井的可行性。试验结果表明,激光束可以137.2m/h(450ft/h)速度钻进砂页岩夹层,可使机械钻速达到目前转盘钻井的100倍以上,而且激光钻井形成的井眼井壁坚固、光滑,避免了井壁坍塌等复杂情况,甚至在钻井过程中不用下套管。虽然在针对实际钻井中遇到的各种岩石性质对激光钻井的影响规律以及破岩所需激光功率及控制等方面尚无完全定量的研究结果,但这一新的钻井方法的潜在优势已逐渐显现[3]。甚至有不少专家预言,不久的将来,激光钻井技术的实现,可能会使钻井技术产生类似于旋转钻井取代顿钻钻井那样的根本性变革。1.3.2 高压水射流钻井水射流技术最早应用于采矿业。早期利用水射流冲洗矿石中的泥土,借助水力运送并筛选矿石和直接用水射流冲刷煤层。由冲刷到破碎岩石实际上是水射流技术的一个质的飞跃。20世纪30年代开始采用压力10MPa以下的水射流冲采中硬以下的煤层,50年代俄罗斯采用压力105~210MPa的纯水射流在花岗岩地层进行了钻井试验,钻速达到了10m/h。60年代,海湾石油公司采用压力56~102MPa的磨料射流进行了硬岩钻进试验,结果表明磨料射流的钻速是常规钻进方法的2~3倍。70年代,壳牌以及埃克森石油公司分别进行了压力在70~105MPa范围内的射流辅助PDC钻头破岩的钻井试验,钻速比常规钻井方法提高了3倍左右。90年代,美国Flowdril公司采用柱塞式井底增压技术在井底将1/10的钻井液增压到200MPa左右进行了辅助钻头破岩钻进试验,钻速提高了1.5~2.5倍[4]。这些结果均表明,射流钻井技术
具有巨大潜力,但由于系统配套及运行成本等问题,使得该技术至今未能得到推广应用。美国Bechtel投资公司和Petrophysics有限公司,于20世纪80年代开展了高压水射流钻径向水平井的新技术研究[5],利用高压水射流破岩方法在直井的产层部位钻出多个辐射状水平井眼,以提高薄油层、低渗油层和气锥、水锥油层的开发效果,进一步提高油气采收率。该钻井技术不需要钻柱和钻头的旋转,不需要给钻头施加用以破岩的“钻压”,采用水射流全面破碎井底岩石,形成井眼,从而彻底解决了常规水平井钻井技术所遇到的钻压施加困难及钻柱旋转带来的一系列复杂问题,提高了钻井速度,减少了井下复杂事故的发生。同时该技术能在0.3m的井段内完成水平转向,定向准确,直接进入产层,简化了井眼轨迹控制过程。90年代初,石油大学全面启动了“径向水平钻井技术”研究计划,通过对高压射流结构特性、破岩规律、井下钻柱运动及变形过程等基础研究[6-10],结合大量的工程试验,基本解决了高压水射流钻进中的射流破岩、转向器系统和参数控制等核心技术。1997年,该技术在辽河油田锦45-04-19井首次井下试验即获成功,钻出了长15.86m、直径120~140mm的水平井眼,钻速达9~12m/h。该井产量提高了7倍以上,获得了良好的经济效益,填补了我国在该领域的技术空白[11]。到目前为止,该技术已经进行了近10次的井下
试验,大都取得了良好的试验效果。
2 高压水射流破岩机理研究高压水射流破岩是高压水射流技术应用的一个重要方面。高压水射流钻井技术的出现,促使水射流理论及水射流破岩理论的进一步发展和完善。加强对高压水射流破岩机理的研究,深刻认识和揭示其破岩机理和过程对促进高压水射流破岩钻井技术的发展具有
·8·石 油 钻 探 技 术 2003年10月极其重要的理论和应用价值。虽然在过去的几十年中,国内外学者已经进行了一些有关高压水射流破岩基本过程、高压水射流切割岩石的理论模型、水射流的冲击动载等方面的研究[12-14],但由于水射流破岩体系的复杂性,在理论分析和试验研究方面均有较大困难,现有理论模型对水射流破岩过程简化过多,且大多停留在假设阶段,没有涉及破碎过程的本质,许多研究要点因为存在较大难度而被忽略,许多关键问题尚未解决或引起重视,因此导致高压水射流破碎岩石的真实物理机制尚不清晰,从而制约了水射流破岩理论与技术的发展,因此必须深入系统地进行高压水射流破岩机理及过程的研究。2.1 当前高压水射流破岩机理研究的关键问题高压水射流破岩的实质是水射流与岩石相互作用,并由此引起岩石损伤破碎的过程,因此高压水射流破岩过程中的流固耦合作用机制、水射流作用下岩石的动态损伤破碎、水射流流场的演化机制对岩石破碎的影响等是高压水射流破岩机理研究中的几个重要方面。其中,在高压水射流作用下,岩石和流体的耦合作用机制以及岩石的动态损伤破碎过程的定量分析是开展高压水射流破岩机理研究中的两个关键问题。高压水射流破岩的实质决定了流体和固体之间的相互作用是揭示其破岩机理的关键。特别是高压水射流破岩这种非线性冲击动力学问题,具有瞬时强值动荷载、柔性撞击、大变形、高应变率等特点,更增加了问题分析的难度。但是随着计算机技术和计算方法的不断发展,已能够在一定程度上模拟研究穿甲、爆破、鸟撞[15]等高度非线性的冲击动力学。这些相似领域的研究成果、研究手段等为当前水射流破岩机理的研究提供了借鉴。在高压水射流作用下岩石损伤破碎过程的研究中,因为岩石的严重不均质性,岩石本构关系的研究一直是岩石力学中最不成熟的一个领域。尤其在动态下,岩石的本构关系研究难度更大。近几年,以细观物理背景为基础的损伤理论以及考虑细观机制的唯象的动态损伤破碎理论有了一定进展,另外随着非线性科学的发展,分形、逾渗、重正化群等理论被尝试用于岩石爆破等岩石动态破碎领域[16],并取得了初步的一些研究成果,因此这些相关领域的理论方法和研究手段,为研究高压水射流作用下岩石的动态破碎问题提供了一定依据。由于射流的尺寸较小,水射流破碎岩石表现出明显的局部效应,岩石孔隙、颗粒等性能的变化已不可忽略,因此高压水射流破岩机理的研究中,重点在于探索水射流冲击作用下岩石的动态破碎失效准则和岩石动态力学行为,并在此基础上,分析岩石非均质性对水射流破岩过程的影响规律。2.2 高压水射流破岩机理的研究进展近年来,石油大学(华东)利用数值模拟与试验相结合的方法对高压水射流破岩机理和过程进行了较为系统的研究,取得了突破性进展[8,17-22]。主要体现在