弧线齿面齿轮齿面接触分析
轮齿弯曲疲劳强度和齿面接触疲劳强度-(机械设计齿轮传动章节课件2)-2020329

(10-8),同时引入载荷系数
KH(见下一页),可得:
=
4 −
3
(公式10-9)
1 ± 1
2
=
1
1 ± 1
1
齿轮传动的计算
上式中:
-接触疲劳强度计算的载荷系数, = ,即PPT一开始提到的4个载荷系数;
载荷分布系数Kβ。
= α
(公式10-2)
齿轮传动的计算
1,使用载荷系数KA
是考虑齿轮啮合时外部因素引起的附加载荷影响的系数。这种附加载荷取决
于原动机和从动机械的特性、联轴器类型以及运动状态等。KA的实用值应针
对设计对象,通过实践确定。
1),原动机包括:电动机、均匀运转的蒸汽机、燃气轮机;蒸汽机、燃气轮机液压装置;
当接触位置连续改变时,显然对于零件上任一点处的接触应力只能在材料许用接触应力的范围内改变,因此接触变应
力是一个脉动循环变应力。在做接触疲劳计算时,极限应力也应是一个脉动循环的极限接触应力。
接触应力也称为赫兹应力,是为了纪念首先解决接触应力计算问题的科学家赫兹(H.Hertz)。
齿轮传动的计算
+用于外啮合
多缸内燃机;单缸内燃机。
2),载荷状态分为:均匀平稳、轻微冲击、中等冲击、严重冲击。
工作状态外在因素越恶劣, KA的取值越大。
齿轮传动的计算
使用载荷系数KA
原动机
载荷状态
工作机器
电动机、均匀运转的
蒸汽机、燃气轮机
蒸汽机、燃气
轮机液压装置
多缸内燃机
单缸内燃机
均匀平稳
发动机、均匀传送的带式输送机或板式输送机、
弧齿锥齿轮接触与弯曲强度ISO与AGMA标准比较及有限元验证
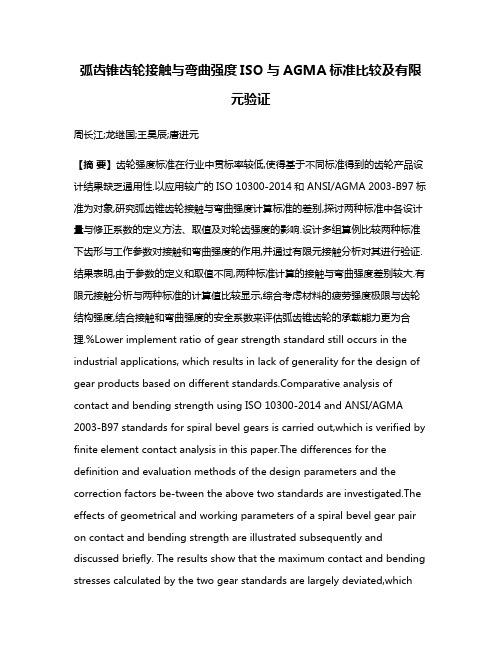
弧齿锥齿轮接触与弯曲强度ISO与AGMA标准比较及有限元验证周长江;龙继国;王昊辰;唐进元【摘要】齿轮强度标准在行业中贯标率较低,使得基于不同标准得到的齿轮产品设计结果缺乏通用性.以应用较广的ISO 10300-2014和 ANSI/AGMA 2003-B97标准为对象,研究弧齿锥齿轮接触与弯曲强度计算标准的差别,探讨两种标准中各设计量与修正系数的定义方法、取值及对轮齿强度的影响.设计多组算例比较两种标准下齿形与工作参数对接触和弯曲强度的作用,并通过有限元接触分析对其进行验证.结果表明,由于参数的定义和取值不同,两种标准计算的接触与弯曲强度差别较大.有限元接触分析与两种标准的计算值比较显示,综合考虑材料的疲劳强度极限与齿轮结构强度,结合接触和弯曲强度的安全系数来评估弧齿锥齿轮的承载能力更为合理.%Lower implement ratio of gear strength standard still occurs in the industrial applications, which results in lack of generality for the design of gear products based on different parative analysis of contact and bending strength using ISO 10300-2014 and ANSI/AGMA 2003-B97 standards for spiral bevel gears is carried out,which is verified by finite element contact analysis in this paper.The differences for the definition and evaluation methods of the design parameters and the correction factors be-tween the above two standards are investigated.The effects of geometrical and working parameters of a spiral bevel gear pair on contact and bending strength are illustrated subsequently and discussed briefly. The results show that the maximum contact and bending stresses calculated by the two gear standards are largely deviated,whichare closely relative to the definition and evaluation methods of the design parame-ters and correction factors.Furthermore,the comparative results of finite element contact analysis and the calculation results from the gear standards indicate that the fatigue strength limit of gear material and the gear strength are necessary to be included simultaneously.These results also show that a more reasonable determination of load capacity in spiral bevel gears is attained according to the safety factors of contact and bending strength.【期刊名称】《湖南大学学报(自然科学版)》【年(卷),期】2018(045)004【总页数】9页(P1-9)【关键词】弧齿锥齿轮;ISO与AGMA标准;接触强度;弯曲强度;有限元接触分析【作者】周长江;龙继国;王昊辰;唐进元【作者单位】湖南大学汽车车身先进设计制造国家重点实验室,湖南长沙 410082;湖南大学汽车车身先进设计制造国家重点实验室,湖南长沙 410082;湖南大学汽车车身先进设计制造国家重点实验室,湖南长沙 410082;中南大学高性能复杂制造国家重点实验室,湖南长沙 410083【正文语种】中文【中图分类】TH132弧齿锥齿轮是重要的基础传动件,主要应用于大型飞行器、重型车辆、能源与海洋装备等[1].齿轮强度计算是齿轮标准及产品设计的核心,国际上应用最为广泛的是ISO 10300-2014[2-4]和ANSI/AGMA 2003-B97[5]标准.ISO标准由国际标准技术委员会制订,适用于等高齿与渐缩齿锥齿轮的接触与弯曲强度计算;AGMA标准由美国齿轮制造协会制订,适用于直齿锥齿轮、零度锥齿轮、弧齿锥齿轮的疲劳点蚀和弯曲强度计算.我国现行的GB/T 10062-2003《锥齿轮承载能力计算方法》,根据ISO 10300-2001标准转化制订.标准是齿轮质量的重要保障,但由于标准化投入少且基础数据缺乏,使我国的自制齿轮标准适应性较差,贯标率较低[6].因此,现用的标准较难适应多样化的齿轮产品设计.ISO和AGMA齿轮标准及其适应性,一直受到学界与行业的关注.早在1984年,Dudley[7]对两种标准关于渐开线圆柱齿轮的计算方法进行了系统的比较研究;1990年,梅宏修[8]重点分析了两种标准中动载系数的定义与取值方法.Labath等[9-10]研究显示,根据ISO和AGMA标准计算出的齿轮强度与齿形、螺旋角、压力角等参数密切相关.周长江等[11]对两种标准中直齿圆柱齿轮的设计步骤、计算式及系数含义进行了分析,通过将两种标准计算的齿根应力与有限元仿真结果进行对比,指出两种标准的计算值均比较保守.Kawalec等[12]研究显示,有限元法计算的直齿与斜齿轮齿根应力比ISO标准的计算值小,但比AGMA标准的计算值大.近几年,吴昌林等[13]采用分类比较法,考虑两种标准中弯曲与接触疲劳强度极限差异,分析了修正系数与齿形参数对渐开线圆柱齿轮强度的影响.邹又名等[14]不计上述疲劳强度极限的差异,重点研究了ISO(2001)和AGMA标准中锥齿轮参数对轮齿强度的作用.ISO与AGMA两种齿轮标准关于齿轮接触与弯曲强度的解析计算式,分别基于Hertz接触理论和Lewis悬臂梁模型.近代数值方法与测试技术的发展,为传统的弧齿锥齿轮强度计算标准提供了较好的验证手段.1981年,Krenzer[15]对弧齿锥齿轮和准双曲面齿轮进行了加载分析,计算出齿面载荷分布及轮齿变形.ChenLiangyu等[16]采用加载接触分析(LTCA)和有限单元法计算出弧齿锥齿轮的齿根应力,并试验验证了计算结果的正确性.方宗德等[17-18]采用LTCA和有限元接触分析法,研究了弧齿锥齿轮齿面接触应力沿接触路径的优化方法与齿根弯曲应力的变化规律;Litvin等[19-20]则基于微分几何与啮合原理建立了精确的弧齿锥齿轮几何模型,对弯曲应力与接触应力进行了计算.Simon[21]采用有限单元法编程分析了弧齿锥齿轮的齿形参数与加载位置对齿根应力的影响,并通过回归分析与差补函数得到了不同啮合点的轮齿变形及齿根应力方程.Handschuh等[22]则利用有限元法和试验法研究了转速和转矩对弧齿锥齿轮弯曲应力的影响.Hotait等[23]采用类似的方法研究了含安装误差准双曲面齿轮的齿根应力分布规律.邓效忠等[24]通过LTCA分析和齿根动态应力测试,对所提出的高重合度弧齿锥齿轮的改进设计方法进行了验证.李源等[25]进行了齿轮连续动态啮合过程的仿真,研究了轮齿的动态啮合齿面接触和齿根弯曲疲劳性能.综上所述,文[7-13]关于ISO和AGMA两种标准的对比研究对象均为渐开线圆柱齿轮,对比结果显示两种标准的计算结果存在较大的差异.文[14]对ISO(2001)与AGMA锥齿轮强度标准进行了比较研究,但在采用两种标准计算齿轮强度时,取了相同的材料疲劳极限值,实际上两种标准关于相同材料的疲劳极限取值有较大差别.本文拟在考虑齿轮材料强度极限差异的同时,研究ISO(2014)和AGMA(2003)标准.新制订的ISO标准删减了旧标准中的节点区域系数,新增了准双曲面系数、当量圆柱齿轮垂直接触线相对曲率半径;旧标准的接触强度计算式中的螺旋角系数,在新标准的弯曲强度计算式中予以考虑且表达符号不同,新的接触强度计算式中不再含有该系数.通过对新版的两种齿轮标准进行比较研究和齿轮参数对轮齿强度的影响度分析,旨在探索面向同一齿轮产品设计中各标准得出不同结果的原因.另外,拟通过有限元接触分析法与上述两种标准的计算结果进行比较,探讨不同标准的设计余量与适应度.1 强度计算原理比较ISO和AGMA齿轮标准中接触与弯曲强度计算式,均分别基于Hertz接触理论与Lewis悬臂梁理论.两种齿轮标准中,强度分析时定义的计算基准不同,计算式的表达形式及引入的修正系数亦不一致.因此,面向同样的齿轮产品设计时,根据不同标准得到的计算结果和齿轮结构参数有时会存在较大的差别.关于弧齿锥齿轮的强度计算,ISO标准采用齿宽中点处当量圆柱齿轮参数为基准参数.接触强度计算是以齿面最大接触应力点作为判定齿面抗点蚀能力的依据;弯曲强度计算则是以齿根危险截面处最大拉应力作为名义齿根应力,引入修正系数后得出计算齿根应力.AGMA标准中以弧齿锥齿轮大端参数为基准参数,进行齿轮的强度计算.其中,以两啮合齿面间的赫兹接触应力作为分析接触强度的依据,考虑齿间载荷分配和加工误差引起的载荷集中对计算式进行修正;弯曲强度计算则是基于悬臂梁模型及“30°切线法”确定的齿根危险截面推导出最大弯曲拉应力,并在计算式中引入相关修正系数.2 强度计算式比较2.1 接触强度计算式比较ISO 10300-2014标准中,弧齿锥齿轮接触强度计算的基本表达式为σH≤σHP(1)(2)Fmt=2 000T1/dml(3)σHP=σHlimZNTZXZLZVZRZWZHyp(4)(5)ANSI/AGMA 2003—B97标准中,弧齿锥齿轮接触强度计算的基本表达式为:σH≤σHP(6)(7)(8)(9)为便于比较ISO与AGMA标准中的接触应力计算式,将式(2)改写为:(10)式(1)~(10)中,两种计算标准中设计参数及相关修正系数含义见表1与表2.表1 弧齿锥齿轮接触强度的设计参数比较Tab.1 Design parameters comparison of contactstrength for spiral bevel gearsISO参数含义AGMA参数含义σH/(N·mm-2)计算接触应力σH/(N·mm-2)计算接触应力σHP/(N·mm-2)许用接触应力σHP/(N·mm-2)许用接触应力σHlim/(N·mm-2)接触疲劳极限应力σHlim/(N·mm-2)接触疲劳极限应力Fmt/N锥齿轮名义切向力T1/(N·m)小齿轮工作转矩lbm/mm齿宽中点接触线长度b/mm齿宽dm1小齿轮齿宽中点分度圆直径de1/mm小齿轮大端节圆直径ρrel/mm当量圆柱齿轮垂直接触线的相对曲率半径Paz/(r·min-1)接触强度许用传动功率SH,min接触强度最小安全系数SH接触强度最小安全系数SH接触强度计算安全系数αn/(°)法向压力角βm1/(°)齿宽中点螺旋角弧齿锥齿轮接触强度计算式比较:两种标准采用的基准参数不一样,ISO标准接触应力计算式(10)中,Fmt、dm1和ρrel等为齿宽中点处当量圆柱齿轮的参数;AGMA标准接触应力计算式(7)中,de1为大端参数.两种标准的计算接触应力表达式均含有系数标准中采用KHβ和KHα两个修正系数分别考虑齿向载荷分布不均与齿间载荷分配不均对接触应力的影响;AGMA标准中则采用参数KHβ同时考虑齿向与齿间载荷分配不均的影响.ISO标准中其他修正系数不含开方运算;AGMA 标准中除了弹性系数ZE,其他系数均含有开方运算.部分修正系数表达式的差异,是两种标准中这些系数含义相同但取值不一样的重要原因.表2 弧齿锥齿轮接触强度的修正系数比较Tab.2 Correction factors comparison of contactstrength for spiral bevel gears影响因素ISOAGMA载荷系数使用系数KA动载系数KV齿向载荷分布系数KHβ齿间载荷分配系数KHα过载系数KA 动载系数KV载荷分布系数KHβ几何参数中间区域系数ZM-B载荷分担系数ZLS 锥齿轮系数ZK准双曲面系数ZHyp尺寸系数ZX几何系数ZI鼓形系数ZXC尺寸系数ZX弹性系数弹性系数ZE弹性系数ZE寿命系数寿命系数ZNT寿命系数ZNT 材料特性参数齿面硬化系数ZW润滑剂系数ZL粗糙度系数ZR速度系数ZV硬度比系数ZW温度系数Kθ安全系数最小安全系数SH,min可靠性系数ZZ安全系数SH许用接触应力计算式比较:ISO标准中许用接触应力式(4)考虑的影响因素较为全面,引入的修正系数较多,如寿命系数ZNT、尺寸系数ZX、润滑剂系数ZL、粗糙度系数ZR、速度系数ZV、工作齿面硬化系数ZW和准双曲面系数ZHyp;AGMA标准中许用接触应力式(8)考虑的影响因素相对较少,仅引入寿命系数ZNT、硬度比系数ZW、温度系数Kθ、可靠性系数ZZ和安全系数SH.AGMA标准的许用接触应力值与安全系数有关;ISO标准中许用接触应力值与安全系数无关.ISO标准中的参数SH与AGMA标准中的参数SH含义不同,前者为计算安全系数,后者为安全系数.AGMA标准中的安全系数考虑了设计分析、材料特性和加工质量等影响因素,系数取值需要考虑齿轮材料、结构与使用工况等因素.弧齿锥齿轮强度校核计算式比较:ISO标准中是通过比较计算安全系数与最小安全系数来评估轮齿的接触强度,等效于比较计算接触应力与许用接触应力值;AGMA标准中,通过比较计算接触应力与许用接触应力值来评估接触强度,没有计算安全系数这一评估指标.此外,AGMA标准中定义了许用接触功率,当输入功率小于许用接触功率时则满足强度条件.该判定方法与ISO标准的判定方法差别较大,可比性较弱.2.2 弯曲强度计算式比较ISO 10300-2014标准中,弧齿锥齿轮弯曲强度计算的基本表达式为:σF≤σFP(11)(12)(13)σFP=σFlimYSTYNTYδrelTYReTYX(14)(15)ANSI/AGMA 2003—B97标准中,弧齿锥齿轮弯曲强度计算的基本表达式为:σF≤σFP(16)(17)(18)(19)为便于比较ISO与AGMA标准中的弯曲应力计算式,将式(12)改写为(20)式(11)~(20)中,两种计算标准中设计参数及相关修正系数含义见表3及表4.表3 弧齿锥齿轮弯曲强度的设计参数比较Tab.3 Design parameters comparison of bendingstrength for spiral bevel gearsISO参数含义AGMA 参数含义σF/(N·mm-2)计算弯曲应力σF/(N·mm-2)计算弯曲应力σFP/(N·mm-2)许用弯曲应力σFP/(N·mm-2)许用弯曲应力σFlim/(N·mm-2)弯曲疲劳极限应力σFlim/(N·mm-2)弯曲疲劳极限应力Fvmt/N当量圆柱齿轮名义切向力met/mm 大端端面模数SF弯曲强度计算安全系数Pay/kW弯曲强度许用传动功率SH,min 接触强度最小安全系数SF弯曲强度计算安全系数bv/mm当量圆柱齿轮齿宽mmn/mm齿宽中点法向模数βv/(°)当量螺旋角表4 弧齿锥齿轮弯曲强度的修正系数比较Tab.4 Correction factors comparison of bendingstrength for spiral bevel gears影响因素ISOAGMA载荷系数使用系数KA动载系数KV齿向载荷分布系数KFβ齿间载荷分布系数KFα过载系数KA 动载系数KV载荷分布系数KHβ几何参数齿形系数YFa应力修正系数YSα重合度系数Yε载荷分担系数YLS螺旋角系数YBS尺寸系数YX几何系数YJ纵向曲率系数Yβ尺寸系数YX寿命系数寿命系数YNT寿命系数YNT材料特性参数相对齿根圆角敏感系数YδrelT相对齿面表面状况系数YRrelT温度系数Kθ其他试验齿轮应力修正系数YST安全系数SF可靠性系数YZ弧齿锥齿轮的弯曲强度计算式比较:两种标准采用的基准参数不一样,ISO标准弯曲应力计算式(20)中,mmn、dm1与bv等为齿宽中点当量圆柱齿轮的参数;AGMA标准弯曲应力计算式(17)中,met、de1等为大端参数.ISO标准中采用KFβ和KFα两个修正系数分别考虑齿向载荷分布不均与齿间载荷分配不均对弯曲应力的影响;AGMA标准中则采用参数KHβ同时考虑齿向与齿间载荷分配不均的影响.许用弯曲应力式比较:ISO标准中许用弯曲应力式(14)考虑的影响因素较为全面,引入的修正系数较多,如试验齿轮应力修正系数YST、寿命系数YNT、相对齿根圆角敏感系数YδrelT、相对齿面表面状况系数YRelT和齿根强度的尺寸系数YX;AGMA标准的许用弯曲应力式(18)考虑的影响因素较少,只引入寿命系数YNT、安全系数SF、温度系数Kθ和可靠性系数YZ.AGMA标准的许用弯曲应力值与安全系数有关,ISO标准中许用弯曲应力值与安全系数无关.ISO标准中的参数SF与AGMA标准中的参数SF含义不同,前者为计算安全系数,后者为最小安全系数.AGMA标准中的最小安全系数考虑了设计分析、材料特性和加工质量等影响因素,系数取值需要考虑齿轮材料、结构与使用工况等因素.弧齿锥齿轮的强度校核计算式比较:ISO标准是通过比较计算安全系数与最小安全系数来评估轮齿的弯曲强度,等效于比较计算弯曲应力与许用弯曲应力值;AGMA标准中,通过比较计算弯曲应力与许用弯曲应力值来评估弯曲强度,没有计算安全系数这一评估指标.此外,AGMA标准中定义了许用弯曲功率,当输入功率小于许用接触功率时则满足强度条件.该判定方法与ISO标准的判定方法差别较大,可比性较弱.3 修正系数比较3.1 接触强度修正系数比较由表2可知,ISO标准和AGMA标准引入的接触强度修正系数及其含义不完全相同.ISO标准考虑的影响因素较全面,引入的修正系数较多;AGMA标准考虑了温度和可靠性对齿轮强度的影响.具体比较如下:1)ISO标准中KA为使用系数,AGMA标准中KA为过载系数,均为描述因动力源、执行器及传动系统引起的过载程度.动载系数KV主要考虑了设计参数、加工精度、传动误差、动态响应和共振等对速度与载荷的影响.但两种标准动载系数计算式不同,ISO标准的动载系数KV计算式为:(21)AGMA标准的动载系数KV计算式为(22)式(21)中,A=50+56(1.0-X),X=0.25(C-4.0)0.667;式(22)中,A=50+56(1.0-B),B=0.25(12-QV)0.667.其中,C和QV分别表示ISO和AGMA标准中的齿轮精度等级.两种标准对精度等级的定义及取值均不同,因此动载系数KV取值差别较大.ISO标准引入了KHβ和KHα两个修正系数考虑载荷分布不均匀度,AGMA标准仅引入修正系数KHβ考虑载荷分布不均的影响.ISO标准中,齿向载荷分布系数KHβ表征了齿宽方向上载荷分布不均匀程度对轮齿强度的影响,计算式为:KHβ =1.5 KHβ-be(23)式中KHβ-be为装配系数,与齿轮副的安装方式有关.对于非鼓形齿,KHβ值适当增大.齿间载荷分配系数KHα查表可知.AGMA标准中KHβ取值与齿宽有关,鼓形齿载荷分布系数KHβ计算式为:KHβ=1.5Kmb+5.6×10-6b2(24)非鼓形齿载荷分布系数为鼓形齿的两倍.2)ISO标准中考虑的几何参数较全面,包括中间区域系数ZM-B、载荷分担系数ZLS、准双曲面系数ZHyp、锥齿轮系数ZK和尺寸系数ZX;AGMA标准中只考虑了几何系数ZI、鼓形系数ZXC和尺寸系数ZX.ISO标准中,ZX取1;AGMA 标准中ZX由齿宽决定,即根据式(25)求得:(25)3)ISO和AGMA标准中弹性系数ZE的计算方法相同,均是考虑齿轮材料特性和泊松比对齿面接触应力的影响.4)寿命系数ZNT的取值在ISO和AGMA标准中有所差别,主要原因是两种标准中试验齿轮材料以及试验条件不尽相同,其取值亦不一致.5)ISO和AGMA标准中的齿面硬化系数(硬度比系数)取决于大小齿轮材料的相对硬度,对于相同材料、相同硬度的齿轮两种标准中硬度比系数均取1.AGMA标准相比ISO标准多考虑了温度系数Kθ.即在0~120 ℃内,温度系数取1;当温度大于120 ℃时,材料特性发生变化,计算式为:(26)式中θT为齿轮本体温度.6)AGMA标准增加了可靠性系数,该系数由齿轮的失效概率确定.3.2 弯曲强度修正系数比较ISO标准和AGMA两个标准引入的弯曲强度修正系数如表4所示,系数的数量与含义不完全相同.具体比较如下:1)ISO与AGMA标准中,弯曲强度计算式中使用系数或过载系数KA与动载系数KV的取值与接触强度计算相同.ISO标准中弯曲强度计算式中齿间载荷分配系数KFα与接触强度计算的齿间载荷分配系数KHα取值相同;弯曲强度计算齿向载荷分布系数KFβ=KHβ/KF0,其中KF0为纵向曲率系数.AGMA标准中弯曲强度和接触强度计算载荷分布系数均用KHβ表达,且取值相同.2)ISO标准考虑的几何因素较多,包括齿形系数、应力修正系数、重合度系数、载荷分配系数、锥齿轮系数和尺寸系数.AGMA标准只考虑几何系数、纵向曲率系数和尺寸系数.尺寸系数YX在ISO标准中用于许用弯曲应力的计算,AGMA标准中则是用于计算弯曲应力,因此尺寸系数在两种标准中的计算表达式及取值也不尽相同.ISO标准中尺寸系数计算式见表5.表5 弯曲强度尺寸系数YXTab.5 Size factor, YX, for root strength材质mmn≤55<mmn≤25mmn>25结构钢、调质钢、球墨铸铁、珠光体可锻铸铁1YX=1.03-0.006mmn0.85渗碳淬火钢、渗氮钢、硝基渗碳钢1YX=1.05-0.01mmn0.8灰铸铁1YX=1.075-0.015mmn0.7AGMA标准中尺寸系数与大端端面模数有关,不考虑齿轮材料和热处理方式,计算式如下.(27)3)材料特性和表面状况系数,ISO标准引入相对齿根圆角敏感系数YδrelT和相对齿面表面状况系数YRrelT.AGMA标准引入了温度系数,取值与接触强度计算一样.4)ISO标准中重合度系数Yε为0.625,试验齿轮应力修正系数YST为2;AGMA标准中没有这两个系数.4 强度计算结果比较4.1 实例计算弧齿锥齿轮接触与弯曲强度校核时,ISO与AGMA齿轮强度标准中的表达式与修正系数不尽相同,配副材料的许用应力值亦有差别.参照ISO标准中接触与弯曲强度安全系数的定义方法,AGMA标准的接触和弯曲强度安全系数可分别定义为SH-AGMA=σHP/σH和SF-AGMA=σFP/σF,进而通过安全系数比较两种标准计算出的齿轮承载能力.为探讨传动比、端面模数、螺旋角、转速等参数对齿轮强度的影响,选取5组齿轮进行分析,参数设置见表6.表中5组齿轮精度等级为7级,材料均为45#钢,调质处理,硬度240 HBS;齿宽30 mm,输入功率20 kW,设计寿命107r,失效概率1%.根据表6中给出的参数,各组齿轮强度的评估值(即接触与弯曲强度安全系数)见表7.表6 齿轮参数组Tab.6 Gear parameters in five cases组别Z1Z2met/mmβ/(°)αn/(°)n/(r·min-1)14080335201000240100335201000340804352010004408032520100054************表7 各组齿轮强度评估值Tab.7 Estimation values of gear strength in five cases组别接触强度安全系数SH-ISOSH-AGMA弯曲强度安全系数SF-ISOSF-AGMA11.04911.35052.22551.046321.09841.42032.30201.092931.39901.79 123.55981.810940.97471.21592.03480.993551.26221.64153.22131.5459由表7可知,接触与弯曲强度安全系数随齿形参数和工况变化而改变.对于同样的齿形与工作参数,两种标准的计算结果不同,其中弯曲强度安全系数的差别较大.随着大齿轮齿数、小齿轮大端端面模数和转速的增加,两种标准计算得到的接触和弯曲强度安全系数均有不同程度的增加;安全系数的变化对端面模数与转速较为敏感.为了直观地分析不同参数对弧齿锥齿轮强度的影响,将表7中的计算结果绘制成折线图(见图1).图1 接触和弯曲强度安全系数Fig.1 Safety factors of contact and bending strength由表7及图1可知,AGMA标准中接触强度校核偏保守;而ISO标准中弯曲强度校核偏保守.造成上面差别的主要原因,与两种标准中接触与弯曲疲劳强度极限取值存在较大差异有关.其中,ISO标准中σHlim=582 MPa,σFlim=220.6 MPa;AGMA标准中σHlim=806.3 MPa,σFlim=120.4 MPa.即AGMA标准的接触疲劳强度极限比ISO高出38.5%,而弯曲疲劳强度极限则比ISO低45.4%.4.2 齿轮强度的有限元验证根据齿面展成与变性法加工原理得到弧齿锥齿轮的几何模型(图2);在Abaqus中建立其有限元接触分析模型(图3).几何模型分割后采用结构化网格,单元类型为C3D8R.考虑到计算效率、精度和重合度,选取4对啮合齿进行网格细分,在主动轮凹面与从动轮凸面间建立面-面接触对.由于弧齿锥齿轮强度标准在计算齿根弯曲应力和齿面接触应力时均未考虑齿面摩擦力,因此有限元模型接触属性中未定义摩擦系数.图2 弧齿锥齿轮装配图Fig.2 Assembling in spiral bevel gears图3 弧齿锥齿轮有限元接触模型Fig.3 Finite element contact model for spiral bevel gears齿形与工况参数取表6中的第1组参数.有限元实体单元没有转动自由度,可采用刚体参考点耦合约束模型.即分别在主、从动轮轴线上设定参考点,在参考点与相应齿轮内表面建立耦合约束,将边界条件施加在参考点上.为保证轮齿初始接触分析易收敛,在从动轮上建立多个分析步逐步施加转矩至381.96 N·m.主动轮参考点上施加全约束,从动轮参考点则约束其三个平动自由度和两个转动自由度(RX和RY),进行准静态分析.图4(a)与(b)分别为从动轮的最大齿面接触应力与最大齿根弯曲应力云图,最大接触应力值为522.423 MPa,最大弯曲应力值为213.161 MPa.(a) 最大齿面接触应力云图(b) 最大齿根弯曲应力云图图4 从动轮的最大齿面接触应力与齿根弯曲应力云图Fig.4 Contours of the maximum contact and bendingstresses for the driven gear将ISO和AGMA标准与有限单元法计算得到的弧齿锥齿轮齿面接触应力与齿根弯曲应力的最大值进行对比,见表8.表8 3种方法计算的齿面接触应力与齿根弯曲应力Tab.8 Contact and root stressed based on three methods应力有限元法ISOAGMAσH/MPa522.423554.735787.468556.908(修正)σF/MPa213.161204.198116.259162.828(修正)根据表8,有限单元法计算的齿根弯曲应力值比ISO与AGMA标准的值均大,这与Kawalec[12]的研究结论略有不同,可能与齿形不同有关.若以ISO标准的计算结果为参照基准,根据有限单元法计算得到的最大接触应力比之小5.8%,最大弯曲应力则比之高出4.4%.但根据AGMA标准计算得到的最大接触应力则比之高出42.0%,而最大弯曲应力则比之小43.1%.两种标准得到的值相差较大,主要与式中齿轮参数和修正系数的数目及其取值有关.如计算该算例的接触强度时,AGMA标准中多一个鼓形系数,非鼓形齿取值为2(开根号后为1.414);弯曲强度计算时,ISO标准中尺寸系数取1,AGMA标准中的取值为0.51(开根号后为0.714).若消。
HGT准双曲面齿轮传动的轮齿接触分析

HGT准双曲面齿轮传动的轮齿接触分析王星;方宗德;李声晋;高正国;宁程丰【摘要】In machining hypoid gear with the HGT method, the large gear is machined with generated method and the pinion is machined with "tilt" method. Based on the machining principle and method of Gleason hypoid gears machined by the HGT method and on the basis of traditional machine tools with cradle mechanism, the mathemati-cal model of machining was established and the theoretical tooth surface equations were derived;on this basis, the tooth contact analysis ( TCA) including tooth contact analysis and edge contact analysis was carried out. The above steps are programmed on the computer;using numerical simulation, we can display the different parameters, gear meshing process and performance with different misalignment, verifying that the mathematical model and theoretical derivation is correct;we believe that this may serve as the foundation for Loaded Tooth Contact Analysis ( LTCA) .%HGT准双曲面齿轮,大轮采用展成法加工,小轮采用刀倾法加工。
齿面接触强度计算
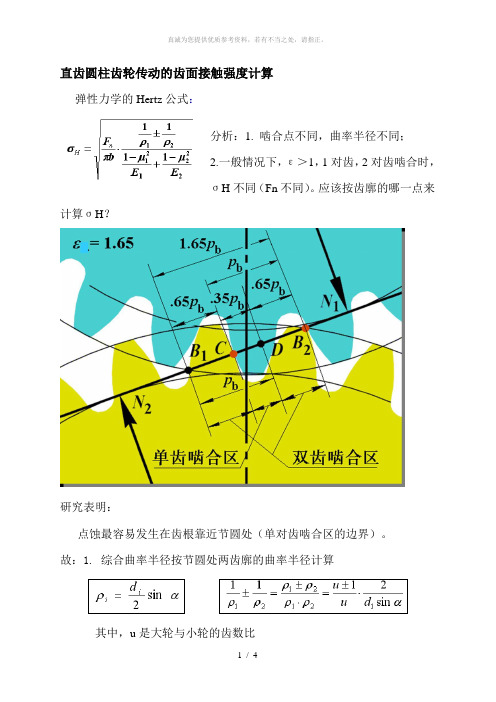
直齿圆柱齿轮传动的齿面接触强度计算
弹性力学的Hertz公式:
分析:1. 啮合点不同,曲率半径不同;
2.一般情况下,ε>1,1对齿,2对齿啮合时,
σH不同(Fn不同)。
应该按齿廓的哪一点来计算σH?
研究表明:
点蚀最容易发生在齿根靠近节圆处(单对齿啮合区的边界)。
故:1. 综合曲率半径按节圆处两齿廓的曲率半径计算
其中,u是大轮与小轮的齿数比
2. Fn按单对齿啮合计算
针对钢制齿轮,引入钢的泊松比μ1= μ2 =0.3,钢的弹性模量
E=2.06×105 MPa,载荷系数K,中心距a,得齿面接触强度的验算公式:令齿宽系数ψa =b/d1,代入上式得中心距:
分析:当一对齿轮的材料、传动比、齿宽系数一定时,接触应力σH 仅取决于分度圆直径d或中心矩a,与模数m无关。
即:两对分度圆直径对应相等的齿轮传动,具有相同的接触强度,与各自模数无关。
即:增大模数m(但d不改变),不能提高齿面接触强度。
关于齿宽系数ψa
理论上讲,ψa越大,a越小,结构越紧凑。
但实际上,ψa↑,可能降低结构的刚性,载荷分布越不均匀,轮齿更易折断。
许用接触应力按下式计算:
式中: σHlim为试验齿轮的接触疲劳强度
极限,按图11-7查得;
S H为齿面接触疲劳安全系数,查表11-4得到。
图11-7。
弧齿锥齿轮的齿面主动设计

理想 的齿轮传 动 是共轭 的,但完 全 共轭 的齿 轮
副没 有任 何 可调 性 ,制 造和 安 装误 差 、承 载变 形 都
会 造 成负荷 集 中而 使轮 齿破 坏 。点接 触 齿面 的准 共 轭特 性克 服 了 以上 不足 ,在 整个 啮合 过程 中的瞬 时 传动 比是 变 化 的,齿面 上 仅在 设计 参 考 点处 的瞬 时 传 动 比等 于 齿轮 副 的名 义传 动 比,其 余啮 合位 置 都
r =r , ) 2 2 (
刀 具面 和大 轮齿 面 的啮合 方程 , 得到 大 轮齿 面在
曹雪梅 方 宗德 张金 良 邓效忠 2
f .西北 工业 大学 机 电学 院 1 西安 707; 10 2
2 .河南 科技 大学 机 电工程 学 院
洛阳
4 13) 7 0 9
摘 要 :齿 面 印痕 和 传 动 误 差 对 齿 轮 传 动 的性 能 起 着 决 定 作 用 ,针 对 齿 面 印痕 和 传 动 误 差 ,提 出弧 齿 锥 齿 轮 点 啮合 齿 面 主 动 设 计 的 方 法 。该 方 法 突 破 了传 统 齿 轮 设 计 的 局 限 性 ,采 用 “ 部 共轭 原 理 ”和 “ 部 综 合 法 ” 局 局 ,并依 据 弧
点处 及其 附近 的啮 合性 能 ,无 法控 制远 离参 考 点 的
齿面性 质 ,可能 出现 接 触迹 线严 重 弯 曲,瞬 时 接触 椭 圆长轴 的长度变 化 剧烈 等现 象 ,以至 于 齿面 接触
区 域 出现 菱 形 、鱼 尾 形 、 扇 形 、三 角 形 或 梯 形 等
情形。
是 非共轭 的 ,均 存在 传 动误 差 。因此 ,定 义传 动 误 差 为 :当小 轮转 过 一角度 时,大轮 相 对 于理想 位 置
齿轮齿面接触疲劳特性与寿命预测
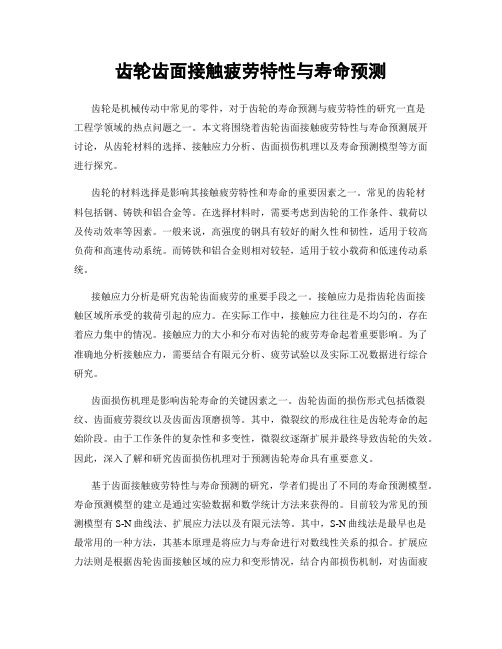
齿轮齿面接触疲劳特性与寿命预测齿轮是机械传动中常见的零件,对于齿轮的寿命预测与疲劳特性的研究一直是工程学领域的热点问题之一。
本文将围绕着齿轮齿面接触疲劳特性与寿命预测展开讨论,从齿轮材料的选择、接触应力分析、齿面损伤机理以及寿命预测模型等方面进行探究。
齿轮的材料选择是影响其接触疲劳特性和寿命的重要因素之一。
常见的齿轮材料包括钢、铸铁和铝合金等。
在选择材料时,需要考虑到齿轮的工作条件、载荷以及传动效率等因素。
一般来说,高强度的钢具有较好的耐久性和韧性,适用于较高负荷和高速传动系统。
而铸铁和铝合金则相对较轻,适用于较小载荷和低速传动系统。
接触应力分析是研究齿轮齿面疲劳的重要手段之一。
接触应力是指齿轮齿面接触区域所承受的载荷引起的应力。
在实际工作中,接触应力往往是不均匀的,存在着应力集中的情况。
接触应力的大小和分布对齿轮的疲劳寿命起着重要影响。
为了准确地分析接触应力,需要结合有限元分析、疲劳试验以及实际工况数据进行综合研究。
齿面损伤机理是影响齿轮寿命的关键因素之一。
齿轮齿面的损伤形式包括微裂纹、齿面疲劳裂纹以及齿面齿顶磨损等。
其中,微裂纹的形成往往是齿轮寿命的起始阶段。
由于工作条件的复杂性和多变性,微裂纹逐渐扩展并最终导致齿轮的失效。
因此,深入了解和研究齿面损伤机理对于预测齿轮寿命具有重要意义。
基于齿面接触疲劳特性与寿命预测的研究,学者们提出了不同的寿命预测模型。
寿命预测模型的建立是通过实验数据和数学统计方法来获得的。
目前较为常见的预测模型有S-N曲线法、扩展应力法以及有限元法等。
其中,S-N曲线法是最早也是最常用的一种方法,其基本原理是将应力与寿命进行对数线性关系的拟合。
扩展应力法则是根据齿轮齿面接触区域的应力和变形情况,结合内部损伤机制,对齿面疲劳寿命进行预测。
有限元法则通过建立齿轮的数值模型,对接触应力进行详细分析,从而得到齿面疲劳寿命的预测结果。
总之,齿轮齿面接触疲劳特性与寿命预测是机械工程领域中的重要研究方向。
ansys齿轮接触分析案例

加载与求解
01
施加约束
根据实际情况,对齿轮的轴孔、 端面等部位施加适当的约束,如 固定约束、旋转约束等。
02
03
施加接触力
求解设置
根据齿轮的工作状态,在齿面之 间施加接触力,模拟实际工作情 况。
设置合适的求解器、迭代次数、 收敛准则等,确保求解的准确性 和稳定性。
后处理
结果查看
查看齿轮接触分析的应力分布、应变分布、接触压力分布等 结果。
02
分析接触区域的大小、应力分布情况,评估齿轮的传动性能和
寿命。
根据分析结果,优化齿轮的设计和制造工艺,提高其传动性能
03
和寿命。
06
CATALOGUE
ansys齿轮接触分析案例四:蜗轮蜗杆
问题描述
蜗轮蜗杆传动是一种常见的减速传动 方式,具有传动比大、传动平稳、噪 音低等优点。但在实际应用中,蜗轮 蜗杆的接触问题常常成为影响其性能 和寿命的关键因素。
属性。
边界条件和载荷
01
约束蜗杆的轴向位移,固定蜗轮的底面。
02 在蜗杆的输入端施加扭矩,模拟实际工作状态。
03 考虑温度场的影响,在模型中设置初始温度和环 境温度,并考虑热传导和热对流。
求解和结果分析
进行静力分析和瞬态动力学分析,求解接触应力 分布、摩擦力变化以及温度场分布等。
对求解结果进行后处理,提取关键数据,进行可 视化展示。
通过齿轮接触分析,可以发现潜在的 应力集中区域和齿面磨损问题,提高 齿轮的可靠性和寿命。
齿轮接触分析的应用领域
汽车工业
用于研究汽车变速器、发动机和传动系统中的齿轮接触行为,优 化齿轮设计以提高燃油经济性和可靠性。
风电领域
用于研究风力发电机组中齿轮箱的齿轮接触行为,提高风力发电设 备的效率和可靠性。
齿轮齿面接触强度及齿根弯曲强度核算

齿面接触强度及齿根弯曲强度核算在设计产品过程中,经常会选用齿轮作为传动力及扭矩的原件。
在大部分成型产品改造或调整过程中,关于齿轮的强度校核这一步骤就可以用类比法代替,从而节省设计人员的精力,缩短了设计周期。
但得出的结果没有书面依据以及理论方面的支持。
所以当进行多次类比之后,所设计出来的齿轮与理论计算得出的齿轮偏差会较大。
其原理类似于累计偏差。
所以应该进行强度校核方面的计算。
齿轮强度校核计算,在实际应用中,主要是两方面的核算:1、齿面接触强度的核算。
2、齿根弯曲强度的核算。
1.齿面接触强度核算-分度圆直径计算参考文献:在初步设计齿轮时,根据齿面接触强度,可按照下列公式估算齿轮传动的尺寸。
(机械设计手册P14-133)a≥A a(μ±1)·√KT1ψaσHP23①d1≥A d·√KT1ψdσHP2·μ±1μ3②公式①为两齿轮中心距的计算;公式②为齿轮分度圆直径的计算。
由于本次计算的是齿轮齿条传动。
所以,中心距a= d1/2其中:d1为齿轮分度圆直径,只需要核算齿轮分度圆直径d1首先,要确定公式②中各个符号代表的含义及数值选取。
d1—齿轮分度圆直径;A d—常系数;K—载荷系数;μ—齿数比;σHP—许用接触应力;ψd—齿宽系数;T1—电机减速机输出扭矩;d1:齿轮分度圆直径,待求;A d:常系数值;A d值在表14-1-65中,通过螺旋角角度β的数值求得。
齿轮的螺旋角β=11.655°,则A d = 756。
载荷系数K,常用值K=1.2~2(机械设计手册P14-133),当载荷平稳,齿宽系数较小,轴承对称布置,轴的刚性较大,齿轮精度较高(6级以上),以及齿轮的螺旋角较大时取较小值;反之取较大值。
根据对比后的结果在K的常用范围内选取。
此次选择K=1.8(载荷平稳,齿宽系数较小,轴为非对称分布,轴的刚性不大,齿轮精度不高)u:传动比。
当齿轮之间为外啮合的时候,选取“+”;当齿轮之间为内啮合的时候,选取“-”,本次计算为齿轮齿条,不影响计算结果。