自动板形控制系统在热轧生产线的应用
热轧精轧机板形控制操作方法和经验浅谈
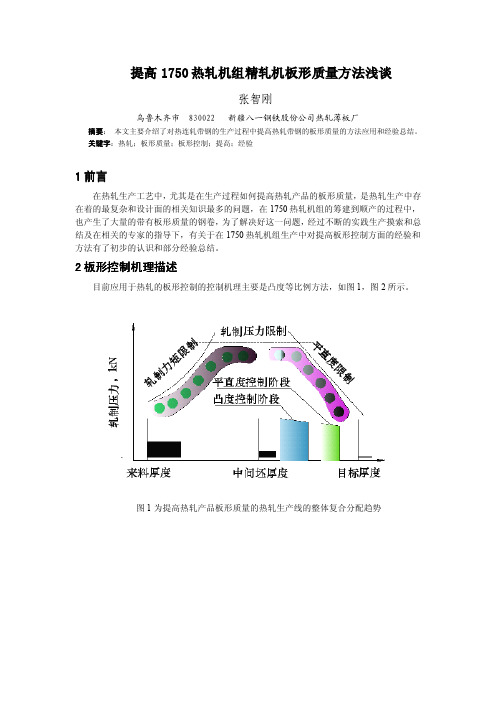
OS 机架水平 DS
OS≥DS OS≥DS OS≥DS OS≥DS
水平度最大范围
≤0.15mm/3m ≤0.15mm/3m ≤0.15mm/3m ≤0.15mm/3m
支持辊轧制 吨位
8 万吨 8 万吨 8 万吨 6 万吨
水平度要求
精轧 机的下支 撑辊水平度倾斜方 向必须一致,同时下 支撑辊的水平度应 该≤0.05mm/m
轧机传动侧和操作侧的 HGC 动作不同步、响应不同步、活套在工作时有机械干涉,及 轧机之间的侧导板和过渡板存在着不利于钢带自由通过的因素,这些都是影响板形提高的最 基本的因素。AGC、AFC 自动闭环和开环控制功能的影响因素,由于外方调试的这些自动 控制功能时处于技术保密顾虑不是太充分的给 1750 热轧职工培训,导致有可能在使用的方 法不正确导致增加了堆钢的次数。同时,VAI 制作的自动控制功能是否有自身的缺陷和尚未 调试优化,导致了功能在工作时发生堆钢和轧烂的事故,这些都是影响到堆钢和轧烂的软件 方面的因素。
是否均匀的主要因素。精轧机的入口擦拭器和出口切水板对工作辊轧制时的紧密配合是提高 板形控制的基础工作,轧制薄规格时必须要求切水板精密结合。另外还要扼制精轧区的冷却 水对带钢的不规则冷却和异常冷却对轧制的钢卷的断面的不规则带来的温度不均匀的影响。 3.4.4 操作工调整时的方法对板形控制和提高的影响:
粗轧中间坯操作侧和传动侧的厚度偏差对精轧板形控制有明显的影响因素:粗轧轧出的 中间坯在操作侧和传动侧的厚度偏差值小于±1mm 时,精轧机控制板形比较空难。 粗轧轧 出的中间坯在操作侧和传动侧的厚度偏差值小于±1mm 时,中间坯在不存在明显的镰刀弯 时,精轧的轧制稳定性较好。 3.3 中间坯的横截面温度差对板形控制的影响因素:
通过用这样的操作方法,操作员充分的把握好对轧机在整体单个轧制计划中的稳定状态 的控制的几个重要的阶段。在前一个阶段的快速的调整中要把带尾的形状也要仔细观察,同 时结合对侧导板的夹紧间隙控制,使轧制计划在轧制到薄规格的主题材前进入轧机的稳定状 态,为轧制主题材做好一定的良好基础。对于状态不好的轧机或着对于试验比较高的轧制带 钢就要使轧机的稳定状态要控制的更高和更充分,可以相应的就增加更多的易轧材帮助操作 工充分的调平轧机。
浅析智能控制技术在轧钢企业中的应用

浅析智能控制技术在轧钢企业中的应用作者:张卫东来源:《城市建设理论研究》2014年第11期摘要:随着现代钢铁工业的飞速发展,轧机的轧制速度不断提高,本文介绍了智能控制技术在轧制过程中的应用状况,并从冷轧与热轧两个方面介绍了我国智能控制技术的发展与可行性方案。
关键词:轧制;智能控制中图分类号:TH-39 文献标识码:A一、轧制工艺原理从炼钢厂出来的钢坯还仅仅是半成品,必须到轧钢厂去进行轧制以后,才能成为合格的产品。
从炼钢厂送过来的连铸坯,首先是进入加热炉,然后经过初轧机反复轧制之后,进入精轧机。
在热轧生产线上,轧坯加热变软,被辊道送入轧机,最后轧成用户要求的尺寸。
轧钢是连续的不间断的作业,钢带在辊道上运行速度快,设备自动化程度高,效率也高。
从平炉出来的钢锭也可以成为钢板,但首先要经过加热和初轧开坯才能送到热轧线上进行轧制,工序改用连铸坯就简单多了,一般连铸坯的厚度为150~250mm,先经过除磷到初轧,经辊道进入精轧轧机,精轧机由7架4辊式轧机组成,机前装有测速辊和飞剪,切除板面头部。
精轧机的速度可以达到23m/s。
热轧成品分为钢卷和锭式板两种,经过热轧后的钢轨厚度一般在几个毫米,如果用户要求钢板更薄的话,还要经过冷轧。
二、智能控制技术在轧钢过程中的应用在钢铁生产流程中,无论是以铁矿石为原料,还是以废钢为原料,炼钢、连铸、热轧都是不可缺少的三大关键工序。
这就要求将这三道工序视为一个整体,实现一体化管理。
一体化管理是指炼钢-连铸-热轧生产的一体化管理,统一计划,统一调度,以此指导炼钢-连铸-热轧的生产,使物流连续高效运作,也是钢铁企业近期生产组织追求的目标,其核心就是计算机生产过程的管理与调度系统。
炼钢、连铸、热轧一体化管理系统,以L4 系统为核心,在与整体产销作业一致的整合化原则下建立热轧D H CR 作业与管理的相关系统。
热轧D H CR 系统主要开发内容包含生产计划编制系统、生产跟踪、合同跟踪及动态调度系统、热轧D H CR 生产组织支持系统及三炼钢L3 系统升级改造。
热轧带钢生产中的板形控制

热轧带钢生产中的板形控制是指通过有效的生产工艺和控制措施,使得热轧带钢的板形达到设计要求,保证其质量和使用性能。
板形是指热轧带钢在轧制过程中产生的纵横向偏差,包括厚度不均匀、横向偏斜、波浪形状等。
合理的板形控制不仅能提高产品的表面质量、平坦度和尺寸精度,还能减少废品率和提高生产效率。
本文将从板形控制的重要性、主要影响因素和改善措施等方面进行分析和探讨。
一、板形控制的重要性热轧带钢的板形控制对产品质量和性能至关重要,具有以下重要性:1. 保证产品的平整度和尺寸精度。
合理的板形控制可以减少热轧带钢在轧制过程中产生的纵横向偏差,从而提高产品的平整度和尺寸精度,确保产品符合设计要求。
2. 改善产品的表面质量。
板形不均匀会导致带钢表面产生波浪、皱纹等缺陷,降低产品的表面质量。
通过有效的板形控制,可以减少这些缺陷的发生,提高产品的表面光洁度和平坦度。
3. 减少废品率和提高生产效率。
不合格的板形会导致产品剪切不良、卷取不良等问题,增加废品率。
通过优化板形控制,可以减少废品率,提高产品的一次成型合格率,提高生产效率。
二、主要影响因素热轧带钢的板形受到多个因素的影响,主要包括以下几个方面:1. 轧制工艺参数。
轧制工艺参数对板形的影响是最直接和关键的。
包括轧制温度、轧制速度、带材的展宽比、轧辊的形状等。
合理的调整和控制这些参数,可以有效地改善板形。
2. 带钢的翘曲性能。
带钢的翘曲性能取决于材料的力学性能和内应力状态。
当带钢的翘曲性能较差时,易出现板形不佳的现象。
3. 轧机设备的状态。
轧机设备的磨损程度、轧辊的偏差和挠度等都会对板形产生影响。
定期检查和维护轧机设备,保持其正常状态,对于控制板形至关重要。
4. 轧机辊系布置。
轧机辊系布置的合理性会对板形产生直接影响。
轧机辊系的过柱、过程和反曲等布置方式,可以通过对带材的实际形变过程进行控制,达到改善板形的效果。
三、改善措施为了控制热轧带钢的板形,可以采取以下措施:1. 合理调整和控制轧制工艺参数。
板形自动控制在热连轧中的应用

机 械 工 程 与 自 动 化
M ECHANI CAL ENGI NEERI NG & AUT( ) M ATI ( ) N
NO .5 Oc t .
文章 编 号 : 1 6 7 2 — 6 4 1 3 ( 2 0 1 3 ) 0 5 — 0 2 0 8 — 0 2
置 主要是 利用 传感 技 术来 实 现 对 带 钢 板 形 的检 测 , 板 形 检测 主要 分两种 : 测 量 带 材横 向 张力 分 布 的 隐 含板 形 和测量 带材 表 面波浪 度 的宏 观 波形 。热 轧过程 中使 用 的检测 装 置 以测 量宏 观 板 形 为 主 , 目前 钢 铁 公 司采 用 较 多的是 激光板 形仪 。 1 板 形控 制 系统构 成 带 钢热 连轧 板 形 质 量 控 制 的 区 域 主 要 是 在 精 轧 区, 在精 轧 区域 的出 口安装 凸度 仪 和平 坦 度 仪 是 保证 板 形控制 的关 键 。 目前 , 热 连轧 生 产 线 大 多 采 用 四辊 六 机架 连轧 机组 , 对 于每 个 机 架来 说 都 具 备 正 负 弯 辊 和窜 辊 的 功 能 。 系 统 设 定 弯 辊 力 的 最 大 调 节 值 达 4 0 0 0 k N, 机架 F 1 、 F 2 、 F 3的 最 大 窜 辊 量 为 1 5 0 mm, F 4 、 F 5 、 F 6的最 大 窜 辊 量 为 2 0 0 mm。弯 辊 控 制是 动 态 板形 调控 的重要 手段 , 凸度 控制 、 平坦 度控 制 为反馈 的辅助 手段 。 板 形控 制程序 根 据其 系统 结 构 图设 计 编 写 , 如 图 1 所示 。该 系 统 中 主要 包 含 板 形 设 定 、 弯辊 力 前 馈控 制、 弯辊 力正 弯与 负 弯控 制 、 凸度 仪 的反 馈 闭 环 控 制 、 平 坦度 的反馈 闭环 控 制 、 板 形 与板 厚 的解 耦 控 制 等 手 段 。其 中板 形设定 主要 是 由操 作 人员 根据 客户 的 生产 要求, 按 已设 计好 的数 学模 型计算 设定 , 以达 到工艺 要 求 。弯辊 力 前馈控 制 的 目的主要 是对 带钢 在轧 制生 产 中的轧 制力 波动进 行预 控制 。 凸度反馈 控 制 与平坦 度 闭环 反馈 控制 是 为了得 到理 想板 形 的一种 精 细控制 手
马钢热轧CSP生产线自动化控制系统的应用

马钢热轧CSP生产线自动化控制系统的应用
戚明星;李耀辉;兰宇;吴苓;郭德福
【期刊名称】《安徽工业大学学报(自然科学版)》
【年(卷),期】2011(028)003
【摘要】马钢CSP薄板坯热轧生产线自动化控制系统是采用西门子过程自动化系统和基础自动化系统,该系统具有设定精度高、对信号能快速响应、控制功能多且集中等优点.生产实绩证明,在生产薄规格冷轧基料及高强钢的过程中,轧机轧制稳定,成品带钢质量较高.
【总页数】4页(P228-231)
【作者】戚明星;李耀辉;兰宇;吴苓;郭德福
【作者单位】马鞍山钢铁公司第四钢轧总厂,安徽马鞍山,243000;马鞍山钢铁公司第一钢轧总厂,安徽马鞍山,243000;马鞍山钢铁公司第一钢轧总厂,安徽马鞍
山,243000;马钢培训中心,安徽马鞍山,243000;北京科技大学高效轧制国家工程研究中心,北京,100083
【正文语种】中文
【中图分类】TG334.9
【相关文献】
1.马钢CSP热轧带钢产品质量现状和发展趋势 [J], 李苹;王步更;曹燕
2.马钢CSP热轧、冷轧和镀锌板卷表面氧化铁皮压入和夹杂缺陷分类、原因和区别 [J], 马玉平;朱涛;陈友根;杨兴亮;焦兴利;董梅;吴文林;王小燕
3.马钢热轧CSP板形控制系统 [J], 邓槟杰;石俊龙
4.马钢CSP立辊半自动化控制系统的改造及应用 [J], 邓槟杰;吴军
5.提高马钢CSP热轧带钢卷取温度命中率 [J], 王宏军;赵海山;曹荐;李耀辉;史红林;张云锦;王鸿翔;贾龙杰;刘树伟
因版权原因,仅展示原文概要,查看原文内容请购买。
热轧带钢生产中的板形控制
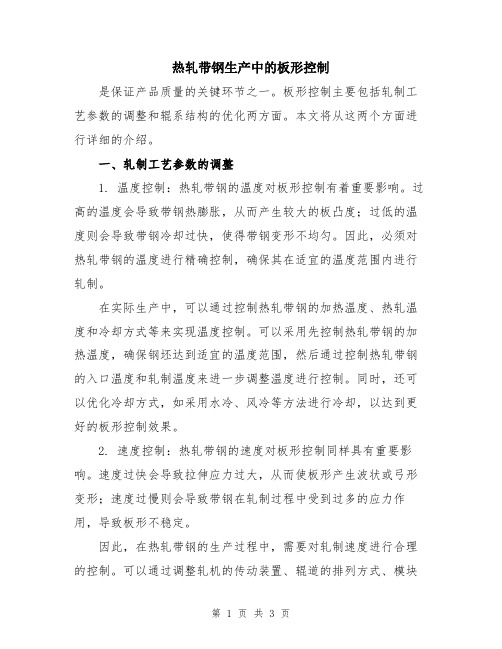
热轧带钢生产中的板形控制是保证产品质量的关键环节之一。
板形控制主要包括轧制工艺参数的调整和辊系结构的优化两方面。
本文将从这两个方面进行详细的介绍。
一、轧制工艺参数的调整1. 温度控制:热轧带钢的温度对板形控制有着重要影响。
过高的温度会导致带钢热膨胀,从而产生较大的板凸度;过低的温度则会导致带钢冷却过快,使得带钢变形不均匀。
因此,必须对热轧带钢的温度进行精确控制,确保其在适宜的温度范围内进行轧制。
在实际生产中,可以通过控制热轧带钢的加热温度、热轧温度和冷却方式等来实现温度控制。
可以采用先控制热轧带钢的加热温度,确保钢坯达到适宜的温度范围,然后通过控制热轧带钢的入口温度和轧制温度来进一步调整温度进行控制。
同时,还可以优化冷却方式,如采用水冷、风冷等方法进行冷却,以达到更好的板形控制效果。
2. 速度控制:热轧带钢的速度对板形控制同样具有重要影响。
速度过快会导致拉伸应力过大,从而使板形产生波状或弓形变形;速度过慢则会导致带钢在轧制过程中受到过多的应力作用,导致板形不稳定。
因此,在热轧带钢的生产过程中,需要对轧制速度进行合理的控制。
可以通过调整轧机的传动装置、辊道的排列方式、模块的配比等来实现速度控制。
同时,还可以通过控制轧机的压下量、变形度等工艺参数来进一步调整速度进行控制。
3. 张力控制:热轧带钢的张力对板形控制同样具有重要影响。
张力过大会导致带钢产生不均匀的塑性变形,从而使板形产生波状或弓形变形;张力过小则会导致带钢发生塑性回弹,导致板形不稳定。
因此,在热轧带钢的生产过程中,需要对张力进行精确的控制。
可以通过调整轧机的辊道间隙、调整轧机的压下量、调整轧机的传动装置等来实现张力控制。
同时,还可以采用张力控制系统进行实时的张力监测和调整,以确保带钢在轧制过程中保持适宜的张力。
二、辊系结构的优化1. 辊系选择:辊系的选择对板形控制具有重要影响。
辊系的结构参数、辊型和辊材质等都会对板形产生影响。
合适的辊系选择可以实现板形的稳定控制,提高产品的表面质量和机械性能。
热轧带钢生产中的板形控制

热轧带钢生产中的板形控制导言热轧带钢是广泛应用于各行各业的一种重要材料,其生产质量直接关系到各领域的使用效果。
在热轧带钢生产过程中,板形控制是保证带钢质量稳定的重要环节。
本文将介绍热轧带钢生产中的板形控制方法及其关键环节。
热轧带钢的板形控制方法热轧带钢的板形控制是通过控制轧制力、温度、轧制参数、板形机构和辊系质量等一系列环节来实现的。
下面将分别介绍各环节的作用和控制方法。
轧制力控制轧制力是热轧带钢生产中的重要参数之一,其大小直接影响着带钢的板形。
一般来说,轧制力越大,带钢的板形越难控制。
因此,正确控制轧制力是实现板形控制的重要手段之一。
控制轧制力的方法包括调整轧辊直径、倾斜角度和绕组角度等。
其中,减小轧辊直径可以减小轧制力;合理地调整倾斜角度和绕组角度可以使轧制力分布更加均匀,从而减少板形变形。
温度控制温度是热轧带钢生产中影响板形的另一个重要因素。
带钢的温度会影响其塑性变形,从而影响轧制力的大小和分布。
因此,正确控制带钢温度也是实现板形控制的重要手段之一。
控制带钢温度的方法包括合理设置加热炉的进出口和布置,对带钢进行预弯曲等。
其中,合理设置加热炉的进出口和布置可以控制带钢的温度分布,从而减少板形变形;预弯曲则可以在热轧压下后通过弹性复原抵消因轧辊形变引起的板形变形。
轧制参数控制轧制参数也是热轧带钢生产中影响板形的重要因素之一。
其中,轧制速度、轧制行程、辊系间距等参数都会影响带钢的板形。
因此,在热轧带钢生产中必须通过控制这些参数来实现板形控制。
正确控制轧制参数可以通过合理设置轧制参数和充分利用各项设备的功能来实现。
例如,通过预弯曲或者预拉伸来调整轧制参数,从而减小带钢的板形变形;通过调整辊系间距等参数,可以减少轧制力分布的不均匀性,进而减少带钢的板形变形。
板形机构控制板形机构是热轧带钢生产中起到非常重要作用的设备,其主要作用是通过改变辊系的几何形状来实现带钢的板形控制。
板形机构在生产中可以通过控制机构的布置、调整机构的形状等来实现板形控制。
1750热轧厂二级自动化系统控制简述

步运行 , 实现真 正意义 上 的容错 。 轧 线过程 服 务 器有 2 台冗 错 式 P 服 务器 , C 所
2 2 软 件 开 发 平 台 .
1 服务器 软件 系统 )
2 工程师 站软件 系统 )
有过程 自动化 的操作终 端将 通过 以太 网与 服务器进 行通讯 。设置 2台工 程 师站 用 于服 务 器进 行 编程 、
作者简介 : 马占福 , , 男 工程师 , 在读博 士 , 主要负责热轧板厂工艺技 术 、 过程控制 、 板形 控制方面 工作 , E—m i w e in@ ht a : m rag o l j ’
mal c n i. o
第 6期
ScunM t l g i a e l ry h au
开发 、 护 和监 控 。轧 线 过 程 服 务 器 与 L 维 3之 间是 通过 T P I C /P+D B的方 式 进 行通 讯 , 与加 热 炉过 程 自动化之 间通过 T P I C /P进行 通讯 , L 与 l之 间通过 T PI C /P进行通 讯 。
( . o Sr l o B y So k C m a y 2 X ’ nv r t o rht tr a d T c n lg ) 1 H t t p Mi f a i t o p n ; . i n U i s y f c i cuen e h o y i l c a e i A e o
[ src] L o pt s m cnrln b oe cn oigraz epemia aapoes Abtat 2cm ue s t ot l g,ym dl otln , let rl nr dt rcs— ry e oi rl e i h i y
i g o lb a d srp, tra r c i g, t smo e a c l t g,e h o o y p r mee n cme to ts n fsa n ti mae ilta k n ma d lc lu ai t c n lg a a t re a t n fma h n h mo li h o s fp o u i de n te c ureo r d cng,fnih d t o lci g,h o g e d t e ie mo g L1, 2, 3, i s a a c l tn t r u h t aa d l r a n e h vy L L MES
- 1、下载文档前请自行甄别文档内容的完整性,平台不提供额外的编辑、内容补充、找答案等附加服务。
- 2、"仅部分预览"的文档,不可在线预览部分如存在完整性等问题,可反馈申请退款(可完整预览的文档不适用该条件!)。
- 3、如文档侵犯您的权益,请联系客服反馈,我们会尽快为您处理(人工客服工作时间:9:00-18:30)。
自动板形控制系统在热轧生产线的应用
本文介绍自动板形控制系统(APFC)如何在热轧生产線进行板形自动控制的原理,研究自动板形控制系统的模型设定功能,动态控制功能等,并介绍这些功能如何提高热轧板形控制精度,提高热轧产品质量。
标签:模型设定动态控制功能轧辊磨损计算轧辊热凸度补偿计算
引言
随着社会发展和科学技术的进步,用户对高技术、高质量、高附加值的热轧带钢产品需求显著增加,对钢铁产品质量、品种、性能方面的要求也越来越高,自动板形控制系统(APFC)在热轧生产线的应用也显得也越来越重要。
自动板形控制系统(APFC)主要包括PC角初始设定,弯辊力初始设定,轧辊磨损计算,轧辊热凸度补偿计算功能和平直度反馈等功能。
一、自动板形控制系统(APFC)功能应用
1.模型设定功能
自动板形控制系统(APFC)主要是根据热轧二级粗轧和精轧的计算结果对PC角的初始设定和弯辊力的初始设定进行二次计算,通过精轧入口板坯凸度和粗轧实际轧制数据计算出热轧轧机的R2到F5的的弯辊力和F1、F2、F3的PC 角(0-1.5度),并根据轧制时间计算出轧辊的热凸度和磨损值用于模型修正计算。
自动板形控制系统(APFC)计算流程图
关于PC角初始设定和弯辊力初始设定在算法上可根据需求自动选择模型的计算重点,保证自动板形控制系统(APFC)有合理的计算结果。
APFC系统主要通过优化弯辊力和PC角计算方法来提高模型计算的精度和合理性,来满足板卷的凸度和平直度。
通过热轧二级计算设定数据计算出板坯的凸度偏差。
(1)
由板坯的凸度偏差计算出板坯凸度。
由板坯凸度的计算结果,再根据等比例凸度原理计算板坯平直度。
通過采集大量的生产数据,根据不同的钢种、厚度和宽度进行优质数据归纳总结,提取关键模型设定数据,再利用神经元算法和轧辊形变模型计算出符合生产实际的模型修正系数,定期反馈给自动板形控制系统(APFC),使其模型计算
结果与生产状况保持一致。
自动板形控制系统(APFC)还可以根据用户需求进行模型计算权重分配,当需要对某一项技术指标(对平直度需求或对凸度需求)进行侧重时,模型会自动提高该项的权重,从而调高该模型计算成功率来达到用户预期需求。
2.轧辊磨损计算功能
轧辊磨损计算功能主要是计算R2到F5每部轧机在轧制过程中的轧辊磨损消耗,通过模型计算出弯辊力补偿值来弥补轧制过程中的消耗轧辊偏差。
轧辊热凸度计算主要是计算R2到F5每部轧机在正常生产过程中轧辊的温度,轧制过程中许多因素影响轧辊的实际温度,比如空气的温度,冷却水的温度,轧制节奏,板坯温度,轧辊材质等。
通过计算得出外界因素对轧辊的影响。
头部弯辊力补偿功能主要是通过采集热轧二级模型设定数据和实际轧制生产数据,计算R2到F4轧机模型设定轧制力和实际轧制力偏差,通过偏差值修正F5咬钢设定弯辊力,从而在F5出口达到板卷目标凸度和目标平直度。
平直度反馈补偿功能主要是计算出平直度仪实际检测的平直度和目标平直度值的偏差,通过计算出的偏差值修正F5出口弯辊力从而达到目标平直度。
3.轧辊热凸度补偿功能
轧辊热凸度补偿功能主要包括两个功能,第一是通过轧辊温度偏差计算出弯辊力补偿值来弥补轧辊在轧制过程中温度的变化影响,第二是防止轧制过程中板坯甩尾功能。
轧辊热凸度补偿功能计算出每一块板坯轧制过中轧辊的温度变化和长周期轧制过程中轧辊的温度变化,把温度变化通过模型计算出弯辊力补偿值。
当温度上升时减小弯辊力,当温度下降时增大弯辊力,来弥补轧辊温度变化对轧制状态影响,当换辊时补偿值清零。
热凸度补偿功能还可以在板坯轧制到尾部时降低尾部弯辊力来防止板坯甩尾现象,当轧制规格厚度越小该功能越明显。
4.平直度反馈功能
当平直度仪检测到带钢头部平直度时,计算出带钢实际平直度与目标平直度的偏差,通过平直度的偏差值利用神经元算法和线性回归算法,计算出弯辊力偏差值,通过PI控制反馈到F5的弯辊力,从而修正F5的平直度,使带钢达到平直度目标值。
当F5弯辊力变化过大时,会影响带钢的稳定轧制,导致堆钢的恶性现象,所以平直度反馈功能对弯辊力偏差进行增益控制,使弯辊力变化逐渐发生,减少对带钢稳定性的影响,一般弯辊力偏差控制在300kN/Chock以内。
当带钢平直度控制在-5I-Unit到+5I-Unit时,平直度反馈功能就认为达到模型的控制精度以内,从而该功能被停用,等待超出控制范围时继续启用。
当平直度仪检测出单边浪时(即单侧浪形超过50I-Unit)平直度反馈功能也被停用。
这时,只能有操作人员进行调平工作,对带钢进行纠正,平直度反馈功能才能继续发挥总用。
二、结束
通过自动板形控制系统(APFC)的应用,热轧生产线带钢的稳定性得到有效的提升,带钢的平直度和凸度可以有效的控制,提高带钢的成品率来大幅度地提高板形质量,提高带钢热连轧生产的自动化水平,提高生产效率,改善产品质量,简化工艺过程,降低生产成本。