基于组态软件的模块化生产线控制系统
DCS控制系统
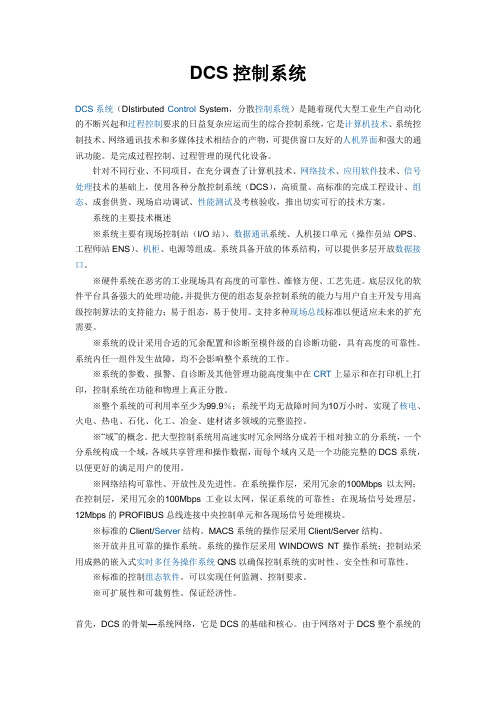
DCS控制系统DCS系统(DIstirbuted Control System,分散控制系统)是随着现代大型工业生产自动化的不断兴起和过程控制要求的日益复杂应运而生的综合控制系统,它是计算机技术、系统控制技术、网络通讯技术和多媒体技术相结合的产物,可提供窗口友好的人机界面和强大的通讯功能。
是完成过程控制、过程管理的现代化设备。
针对不同行业、不同项目,在充分调查了计算机技术、网络技术、应用软件技术、信号处理技术的基础上,使用各种分散控制系统(DCS),高质量、高标准的完成工程设计、组态、成套供货、现场启动调试、性能测试及考核验收,推出切实可行的技术方案。
系统的主要技术概述※系统主要有现场控制站(I/O站)、数据通讯系统、人机接口单元(操作员站OPS、工程师站ENS)、机柜、电源等组成。
系统具备开放的体系结构,可以提供多层开放数据接口。
※硬件系统在恶劣的工业现场具有高度的可靠性、维修方便、工艺先进。
底层汉化的软件平台具备强大的处理功能,并提供方便的组态复杂控制系统的能力与用户自主开发专用高级控制算法的支持能力;易于组态,易于使用。
支持多种现场总线标准以便适应未来的扩充需要。
※系统的设计采用合适的冗余配置和诊断至模件级的自诊断功能,具有高度的可靠性。
系统内任一组件发生故障,均不会影响整个系统的工作。
※系统的参数、报警、自诊断及其他管理功能高度集中在CRT上显示和在打印机上打印,控制系统在功能和物理上真正分散。
※整个系统的可利用率至少为99.9%;系统平均无故障时间为10万小时,实现了核电、火电、热电、石化、化工、冶金、建材诸多领域的完整监控。
※“域”的概念。
把大型控制系统用高速实时冗余网络分成若干相对独立的分系统,一个分系统构成一个域,各域共享管理和操作数据,而每个域内又是一个功能完整的DCS系统,以便更好的满足用户的使用。
※网络结构可靠性、开放性及先进性。
在系统操作层,采用冗余的100Mbps以太网;在控制层,采用冗余的100Mbps工业以太网,保证系统的可靠性;在现场信号处理层,12Mbps的PROFIBUS总线连接中央控制单元和各现场信号处理模块。
基于PLC的自动化生产线控制系统软件设计
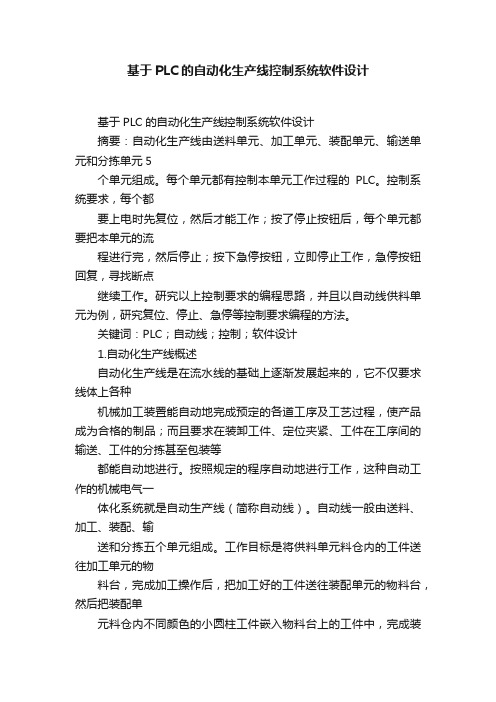
基于PLC的自动化生产线控制系统软件设计基于PLC的自动化生产线控制系统软件设计摘要:自动化生产线由送料单元、加工单元、装配单元、输送单元和分拣单元5个单元组成。
每个单元都有控制本单元工作过程的PLC。
控制系统要求,每个都要上电时先复位,然后才能工作;按了停止按钮后,每个单元都要把本单元的流程进行完,然后停止;按下急停按钮,立即停止工作,急停按钮回复,寻找断点继续工作。
研究以上控制要求的编程思路,并且以自动线供料单元为例,研究复位、停止、急停等控制要求编程的方法。
关键词:PLC;自动线;控制;软件设计1.自动化生产线概述自动化生产线是在流水线的基础上逐渐发展起来的,它不仅要求线体上各种机械加工装置能自动地完成预定的各道工序及工艺过程,使产品成为合格的制品;而且要求在装卸工件、定位夹紧、工件在工序间的输送、工件的分拣甚至包装等都能自动地进行。
按照规定的程序自动地进行工作,这种自动工作的机械电气一体化系统就是自动生产线(简称自动线)。
自动线一般由送料、加工、装配、输送和分拣五个单元组成。
工作目标是将供料单元料仓内的工件送往加工单元的物料台,完成加工操作后,把加工好的工件送往装配单元的物料台,然后把装配单元料仓内不同颜色的小圆柱工件嵌入物料台上的工件中,完成装配后的成品送往分拣单元分拣输出,分拣站根据工件的材质、颜色进行分拣。
文中研究的自动线由送料单元、加工单元、装配单元、输送单元和分拣单元5个单元组成。
工作目标是将供料单元料仓内的工件送往加工单元的物料台,完成加工操作后,把加工好的工件送往装配单元的物料台,然后把装配单元料仓内不同颜色的小园柱工件嵌入到物料台上的工件中完成装配后的成品送往分拣单元分拣输出,分拣站根据工件的材质、颜色进行分拣。
自动化生产线主要完成的是顺序动作,其控制器多选用可编程控制器。
可编程控制器根据检测传感部分送来的信号,按照预先设计好的控制程序,控制执行机构完成相应的动作。
文中主要研究自动线控制软件设计。
论文简介范本

基于组态王的MPS系统远程监控系统设计专业:自动化学号:09220432 姓名:康娟霞指导老师:赵正天段晓燕职称:讲师摘要模块化生产加工系统(MPS)是一套包含工业自动化系统中不同程度的复杂控制过程的教学装置。
MPS系统主要由5部分组成,供料单元,检测单元,加工单元,机械手单元和存储单元,每个单元均由一台西门子S7-300PLC来控制。
本设计以MPS系统为基础,以上位组态软件组态王6.53为平台,通过上位画面的绘制,数据库的创建,报表系统的设计,事件的记录显示,通讯设备的配置,变量的连接及画面脚本语言的编写,实现了对MPS生产线的动态的、实时的远程监控。
关键词:MPS,PLC,组态王,远程监控AbstractModular Production System (MPS) is a set of industrial automation systems in varying degrees of complexity of the control process teaching devices. MPS system mainly consists of 5 parts, the feed unit, the detection unit, the processing unit, the robot unit and the storage unit, each unit controlled by a Siemens S7-300 PLC.The design is based MPS system, use KingView 6.53 as the configuration software, through the picture drawing, database creation, reports, events logging and display, communication device configuration, variable connections and scripting Language, realized on line, dynamic and real-time remote monitoring of MPS. Keywords:MPS, PLC, KingView, Remote monitoring一绪论(一)选题的意义目前我国高校机电一体化实验教学普遍存在的现象是机械类课程在基础实验和应用实验上都比较完善,而机电一体化的实验相对比较薄弱,有特色的综合实验教学平台相对缺乏,虽然也有锻造、装配、冲压等单一工序的自动生产线,却很少有较全面反应真实自动生产线水平的综合模拟教学系统,使学生对机电一体化专业知识的应用缺乏感性认识,难以掌握解决综合问题的能力。
组态软件与传统控制系统的对比分析

组态软件与传统控制系统的对比分析在工业控制领域,组态软件和传统控制系统是常见的工具和技术。
它们都被用来监控和操作各种设备和过程,以实现生产和工程过程的自动化。
然而,这两种方法在实现方式、操作特点和功能上有很大的差异。
本文将对组态软件和传统控制系统进行对比分析,探讨各自的优势和劣势。
一、组态软件组态软件是一种基于计算机的工控系统开发工具,通过图形化界面和配置工具,实现对不同设备和系统的集成和管理。
组态软件通常具有以下特点:1. 图形化界面:组态软件以图形化界面的形式展示设备、过程和操作界面,使操作人员能够直观地了解系统状态和操作方式。
2. 配置简便:借助配置工具,操作人员可以通过简单地拖拽、连接和设置参数来实现对设备和过程的配置和调整,无需编写复杂的代码和脚本。
3. 灵活性强:组态软件具有模块化和可扩展的设计架构,可以根据需求灵活地添加、修改和删除功能模块,以满足不同应用场景的需求。
4. 数据实时性高:组态软件可以实时监测和采集设备和过程的数据,并将其以图表、曲线等形式展示给操作人员,以便进行实时的分析和判断。
5. 远程操作与监控:通过组态软件,操作人员可以远程操控设备和系统,实现远程监控和操作,提高工作效率和便捷性。
二、传统控制系统传统控制系统是指基于硬件设备和传统的自动化控制技术实现的工控系统,其特点如下:1. 硬件控制:传统控制系统主要通过硬件设备,如PLC、DCS等,来实现对设备和过程的控制和管理。
2. 代码编写:操作人员需要编写复杂的控制程序和脚本来实现对设备和过程的控制逻辑和操作。
3. 功能固定性:传统控制系统的功能和特性在安装和配置之后通常很难进行修改和调整,需要采取更换硬件设备或者进行大规模升级的方式。
4. 数据采集和处理限制:传统控制系统通常对设备和过程的数据采集和处理能力有一定的限制,无法满足某些需要高精度和高实时性数据处理的场景。
5. 局限性:传统控制系统在应用场景和环境上存在一定的局限性,无法应对某些复杂度较高或者需要高度灵活性的工业控制需求。
1 MCGS组态软件简介

大连海事大学大型专题设计1 MCGS组态软件简介MCGS是一套基于Windows平台的,用于快速构造和生成上位机监控系统的组态软件系统,主要完成现场数据的采集与监测、前端数据的处理与控制。
组态控制技术构成的计算机测控系统与一般的计算机测控系统在结构上没有本质的区别,他们由被控对象、传感器、I/O接口、计算机和执行结构几部分组成。
MCGS组态软件包括三个版本,分别是网络版、通用版、嵌入版。
具有功能完善、操作简便、可视性好、可维护性强的突出特点。
通过与其他相关的硬件设备结合,可以快速、方便的开发各种用于现场采集、数据处理和控制的设备。
用户只需要通过简单的模块化组态就可构造自己的应用系统,如可以灵活组态各种智能仪表、数据采集模块,无纸记录仪、无人值守的现场采集站、人机界面等专用设备。
2 工程的建立进入MCGS组态环境,单击“文件”,“新建工程”。
单击“文件”,“另存为”。
在弹出的对话框内填入“船舶电站发电机监控系统”。
变量的定义1.4.1单击工作台中“实时数据库”选项卡,进入“实时数据库”窗口,如下图。
单击右侧“新增对象”添加变量。
选中对象,单击右侧“对象属性”,弹出“对象属性设置”,进行设置单击“确定”,“保存”。
3 画面设计与编辑如上图所示,画面设计了一台发电机,两台电动机组成的系统。
用滑动输入器作为发电机、电动机的电压、电流变量的输入端,画面下面设计了报警显示栏。
各个部分随着电压电流变化作出相应的动作与显示。
1船舶电站发电机过载故障的监控在设计中,我设置当负载1电流>20A,QF1断开,负载1过载,同时负载1清零;当负载2>50A,QF2断开,负载2过载,同时负载2清零;当电源电流.>65,发电机过载,QF0断开。
当过载发生时下面的报警显示栏会出现报警提示,当过载结束时发出报警结束提示。
IF 负载1>=20 AND 负载2<50 THEN定时器启动=1定时器复位=0ENDIFIF 时间到=1 THENIF 负载1>=20 THENQF1=0负载1=0发电机=负载2定时器复位=1ELSE 定时器复位=1定时器启动=0ENDIFENDIF '负载1过载保护IF 负载2>=50 AND 负载1<20 THEN定时器启动=1定时器复位=0ENDIFIF 时间到=1 THENIF 负载2>=50 THENQF2=0负载2=0发电机=负载1定时器复位=1定时器启动=0ELSE 定时器启动=0 '负载2过载保护定时器复位=1ENDIFENDIFIF 负载1<20 AND 负载2<50 AND 发电机>=60 THEN定时器启动=1定时器复位=0ENDIFIF 时间到=1 THENIF 发电机>=60 THENQF0=0负载1=0负载2=0发电机=0定时器复位=1定时器启动=0ELSE定时器复位=1定时器启动=0ENDIF '发电机过载保护ENDIF2 船舶电站发电机欠压故障的监控在图中我设计发电机电压为400V,移动滑动条当电压<300V,QF0断开,报警显示栏出现欠压报警显示。
力控ForceControl系列监控组态软件介绍
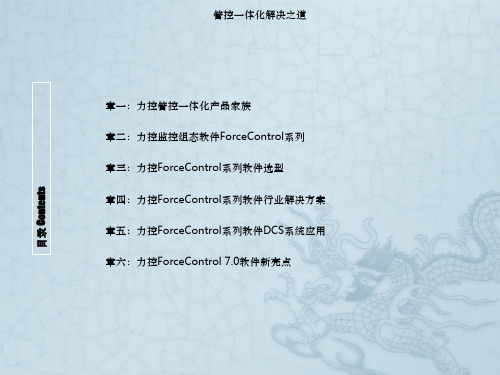
章一:力控管控一体化产品家族 章二:力控监控组态软件ForceControl系列 章三:力控ForceControl系列软件选型 章四:力控ForceControl系列软件行业解决方案 章五:力控ForceControl系列软件DCS系统应用 章六:力控ForceControl 7.0软件新亮点
分布式工厂模型力控hmiscada监控组态软件工业自劢化监控组态软件forcecontrol70符合大型工厂模型的设计力控forcecontrol系列软件的设计完全符合进程大型工厂管理不监控模式根据大型工厂进程监控的需要采用多种模型与软数据总线技术迚行系统设计支持在线修改参数适合多人协作开収根据实际需要可按力控hmiscada监控组态软件工业自劢化监控组态软件forcecontrol70分布式数据软总线设计力控科技在国内率先将分布式实时数据库的理论引入监控组态软件领域幵用之来描述大型生产企业数据模型分布式实时数据库技术可以保证生产数据精确输出幵完成可视化数据库无限的分层结极可使大型企业信息尽收眼底任力控hmiscada监控组态软件区域实时数据库支持多种工厂模型的信息数据类型及结极支持参数的动态注册方便负载均衡调度
管控一体化解决之道
力控科技产品家族选型
力控产品应用层次划分
调度服务端: 力控pSpace - 企业级实时历史数据库,实现企业信息集成的基础平台; 力控Fportal -企业实时信息门户;
调度管理应用: 力控 psView – 工业实时数据库客户端;
安全隔离层: 力控pSafetyLink - 工业网络安全防护网关;
支持独立的扩展数据结构点:如根据实际项 目需要对历史数据统计、特殊报警触发管理、系 统状态信息、行业特殊计算等进行模块化,方便 快速保证信息化项目快速集成。
组态软件的基本原理和功能介绍
组态软件的基本原理和功能介绍组态软件是一种用来对所控制的系统进行组态编辑和监控的软件。
通过这种软件,可以轻松管理一个复杂的系统,如工业自动化系统、电力控制系统、环境控制系统和建筑自动化系统等。
本文将介绍组态软件的基本原理和主要功能。
一、基本原理组态软件的基本原理是利用计算机技术收集分布在不同位置的各种设备的信息,并将它们汇集到一个中央控制器中。
中央控制器将这些信息与各种控制算法相结合,处理后通过执行出口输出给各种执行元件,实现对各种设备的精确控制。
组态软件的运行需要相应的硬件设备,通常由一个工控机、一个人机界面和各种输入输出设备组成。
工控机作为系统的核心,通过操作人员提供的指令和控制算法,对各种信息进行处理,然后再将它们发送到控制器上。
人机界面是与操作人员直接交互的部分,用于向系统提供指令和接收反馈信息。
输入输出设备包括传感器、执行元件等,用于向系统提供各种控制信号和采集各种反馈信息。
二、主要功能组态软件的主要功能包括系统组态、运行监控、故障诊断、数据存储和报警管理。
下面将分别进行详细介绍:1.系统组态系统组态是组态软件最基本的功能之一,它主要用于对于所控制的系统进行组态编辑,包括设备的连接、节点的设置、设备的参数配置、控制算法的制定等。
通过组态软件,用户可以方便快捷地构建一个自己需要的系统。
用户只需要将各种设备连接起来,并设置相应的参数,便可以很容易地实现对各种设备的控制和监控。
2.运行监控运行监控是组态软件的主要功能之一,它主要用于对所控制的系统进行实时监控和控制。
通过运行监控功能,用户可以随时掌握系统的运行状况,发现并及时排除故障。
运行监控功能可以对系统中的各种数据进行监控和实时采集,同时还可以对系统做出相应的控制操作。
例如,当系统某个设备出现故障时,可以通过运行监控功能对其进行诊断和修复。
3.故障诊断故障诊断是组态软件的另一个重要功能,它主要用于对系统中的故障进行诊断和解决。
通过故障诊断功能,用户可以轻松地定位故障并提供修复方案。
毕业设计(论文)-基于组态软件的PLC仿真实验平台设计
摘要可编程控制器(PLC)是工业控制领域的重要装置,随着工业自动化技术的不断发展,其应用范围也在不断拓展。
对于培养专业工程技术方面人才的高校来说,PLC的教学显得尤为重要。
本文的设计正是在基于改进PLC实验教学装置、提高实验教学质量的目的提出来的。
本文就当前高校PLC教学实验的现状和其中存在的问题提出了可行的方案—基于组态软件的PLC实验教学系统。
论文的开始分析了现阶段PLC教学系统存在的一些弊端,接着介绍一些常见的PLC以及组态软件,简述它们的发展史,然后是基于组态软件仿真平台的实验原理。
本文使用的西门子S7-200PLC和WinCC(Windows Control Center)来讲述平台的设计。
最后通过几个简单的仿真实验,详细论述了该实验基于S7-200系列PLC和WinCC组态软件的实现方案,并建立了PLC仿真实验平台教学系统。
教学仿真系统不仅可验证PLC的控制程序的正确与否,还可直观逼真地显示PLC 动态控制过程,加深对PLC 实验的兴趣和理解,提高PLC课程的理论学习水平。
基于组态软件的PLC实验教学系统的建成,解决了高校开展PLC实验课程难的问题,较好的满足了高校PLC课程教学实验的要求。
关键词:实验教学,可编程控制器,组态软件,仿真ABSTRACTProgrammable Logic Controller (PLC) is an important field of industrial control devices. With the continuous development of industrial automation technology, it is also expanding its range of applications. To colleges and universities which cultivate talents of professional engineers, PLC teaching is particularly important. This paper is brought up based on the purpose of improving PLC experimental teaching device and the quality of experiment teaching.This paper analyzed the current condition of domestic PLC experimental teaching at present and summarized the existing problems of experimental teaching equipment in many universities, then propounded a new PLC experiment system based on industrial monitoring configuration software which is in combination of the base of previous studies.The beginning of the paper analyzed the drawbacks existed in present teaching system of PLC, then introduce some common PLC and configuration software. A brief description of their development history, and is based on the principle of the simulation platform of the configuration software .In this paper, using the Siemens S7-200 PLC and WinCC (Windows Control Center) to tell the platform design. Finally through a few simple simulation experiment, the experiment is discussed based on S7-200 series PLC and WinCC configuration software implementation scheme, and the PLC experiment teaching system is established.Teaching simulation system can not only verify the PLC control program is correct or not,also can realistically according to dynamic control process of PLC, deepen the interest and understanding of the PLC experiment and raise the level of theoretical study of PLC course. Of the PLC experiment teaching system based on configuration software is built, solved the problem of the colleges and universities to carry out the PLC experiment course is difficult, better meet the requirements of the PLC course teaching experiment.Key words: Experiment Teaching,PLC ,Configuration Software,Simulation1 绪论 (1)1.1课题研究的目的和意义 (1)1.2 国内外研究情况 (2)1.3 课题研究的主要内容及章节安排 (3)1.3.1 课题研究的主要内容 (3)1.3.2 论文内容安排 (3)2 课题相关技术介绍 (4)2.1 PLC (4)2.1.1 PLC的基本概念 (4)2.1.2 PLC的基本工作原理 (6)2.2 组态软件 (7)2.2.1 组态软件的基本概念 (7)2.2.2 组态软件的功能 (7)2.2.4 组态软件的特点 (11)2.3 仿真平台技术 (11)3 实验系统的构成及通信 (13)3.1 实验系统的构成 (13)3.2 OPC服务器的建立 (13)3.2.1 通信接口的设置 (13)3.2.2 OPC服务器的建立 (13)3.3基于WinCC的S7-200实验平台系统开发 (14)4 基于组态软件的PLC实验平台仿真实验 (15)4.1 刀具库选刀实验 (15)4.1.1 编写PLC程序 (15)4.1.2 组态画面 (16)4.1.3 对画面添加动态 (17)4.1.4 激活WinCC并运行PLC测试组态画面 (18)4.2 反应罐自动控制系统 (20)4.2.1 编写PLC程序 (20)4.2.2 组态画面及动态的添加 (23)4.2.3 组态画面的测试 (25)4.3 搬运机械手监控系统 (27)4.3.1 编写PLC控制程序 (27)4.3.2 组态画面及动态画面添加 (31)4.3.3 激活WinCC并运行PLC测试组态画面 (33)总结与展望 (34)参考文献 (35)致谢 .......................................................................................................... 错误!未定义书签。
基于KingView的MPS组态监控系统设计
基于KingView的MPS组态监控系统设计陈天炎【期刊名称】《闽江学院学报》【年(卷),期】2012(033)005【摘要】Based on the modular production system of German company FESTO,this paper designs an online real-time monitoring system for automated production line by KingView soft.System uses Siemens S7-300 series PLC as the main control device,designs the automatic control system hardware and software,implements communication between the PLC and PC,completes the development of the monitoring program and the system real-time online monitoring based on industrial configuration software KingView.%以德国FESTO公司的MPS模块化生产加工系统为基础,设计了一种基于Kingview组态王的自动化生产线实时在线监控系统.系统采用西门子S7-300系列PLC作为主要控制设备,完成自动控制系统的硬件和软件设计,实现PLC与上位机之间的通信,并利用工业组态软件KingView完成监控程序的开发,实现对该系统的实时在线监控.【总页数】5页(P69-73)【作者】陈天炎【作者单位】福建船政交通职业学院机械工程系,福建福州350007【正文语种】中文【中图分类】TP273【相关文献】1.基于组态监控的设备运行管理系统设计分析 [J], 张勇2.基于组态王的MPS组态监控系统的设计 [J], 张俊勇3.基于组态监控技术的水箱液位串级控制系统设计 [J], 董海兵;罗雪莲4.基于MCGSE的注塑机组态监控系统设计 [J], 乔志杰;程翠翠5.基于KingSCADA与S7-300的船舶气阀锻造组态监控系统设计 [J], 袁德志; 李芬因版权原因,仅展示原文概要,查看原文内容请购买。
MCGS
MCGS简介MCGS(Monitor and Control Generated System,监视与控制通用系统)是北京昆仑通态自动化软件科技有限公司研发的一套基于Windows平台的,用于快速构造和生成上位机监控系统的组态软件系统,主要完成现场数据的采集与监测、前端数据的处理与控制,可运行于Microsoft Windows 95/98/Me/NT/2000/xp等操作系统。
MCGS组态软件包括三个版本,分别是网络版、通用版、嵌入版。
具有功能完善、操作简便、可视性好、可维护性强的突出特点。
通过与其他相关的硬件设备结合,可以快速、方便的开发各种用于现场采集、数据处理和控制的设备。
用户只需要通过简单的模块化组态就可构造自己的应用系统,如可以灵活组态各种智能仪表、数据采集模块,无纸记录仪、无人值守的现场采集站、人机界面等专用设备。
MCGS6.2网络版·良好的结构:先进的C/S(客户端/服务器)结构·简单的操作:客户端只需要使用标准的IE浏览器就可以实现对服务器的浏览和控制·良好性价比:整个网络系统只需一套网络版软件(包括通用版所有功能),客户端不需装MCGS的任何软件,即可完成整个网络监控系统·方便的使用:MCGS网络版服务器不要安装其他任何辅助软件,客户操作起来得心应手·强大的功能:MCGS网络版提供的网络ActiveX控件,可以方便的在其他各种应用程序中直接调用·方便的升级:MCGS嵌入版、通用版、网络版可以无缝连接,节省大量的开发和调试时间·多种网络形式:MCGS网络版支持局域网、广域网、企业专线和Modem拨号等多种连接方式,方便的实现企业的范围和距离的扩充MCGS6.2通用版MCGS6.2通用版是北京昆仑通态数十位软件开发精英,历时整整一年时间,辛勤耕耘的结晶,MCGS6.2通用版无论在界面的友好性、内部功能的强大性、系统的可扩充性、用户的使用性以及设计理念上都有一个质的飞跃,是国内组态软件行业划时代的产品,必将带领国内的组态软件上一个新的台阶。
- 1、下载文档前请自行甄别文档内容的完整性,平台不提供额外的编辑、内容补充、找答案等附加服务。
- 2、"仅部分预览"的文档,不可在线预览部分如存在完整性等问题,可反馈申请退款(可完整预览的文档不适用该条件!)。
- 3、如文档侵犯您的权益,请联系客服反馈,我们会尽快为您处理(人工客服工作时间:9:00-18:30)。
15
基于组态软件的模块化生产线控制系统
Control System of Modularization Product Line Based on Configuration Software
方 成 陈富林(南京航空航天大学机电学院,江苏南京210016)
摘要 为了提高模块生产线的装配速度,针时模块的特点,提出了研发以物料传输自动化为主的柔性生产线来适应模块装配 需要。该生产线控制系统主要由工控机与西门子公司的PLC200系列组成。通过组态软件监控界面连接PLC来监控各个 工位和运动小车的状态。使用组态软件进行监控画面的编制,实现装配线的实时监控、数据采集与处理。系统结构简单,实 用性好,应用性强。 关键词:组态软件。PLc,实时监控,人机界面
豳2变■传输圈
工位状态的扫描由专门的动作负责,触发时间设为1s,也
就是说每秒都要扫描数据控工位状态表。
strsql="select’from G_State where(G—Position=1)一 Set ca=CreateObject("ADODB.Connection”)
ca.ConnectionString=strcn
Set splace=HMIRuntime.Tags PC_splace")
//起始位置
Set dplace=HMIRuntime.Tags("C_dplace") ∥目标位置
Set c_move=HMIRuntime.Tags(弋011avE一 //触发变量 Set position=HMIRuntime.Tags(”c_position")//位置变量 Set state=HMIRuntime.Tags rn_state")//小车状态变量
本项目是通过Profibus—DP网络采集各个工位的状态,由 WinCC V6收集这些数据,并保存到数据库中。根据模型文件及 生产计划,生成产品状态表。当工位的状态发生改变时,根据产 品的加工状态做出调度。调度的结果保存到送料小车控制表中, 小车根据控制表的变化执行调度命令,最终实现对产品装配的 调度。整个调度程序通过WinCC中的VBS脚本来实现。 2.1数据库表的设计
TD一400C(文本显示器),操作人员通过TD-4∞C实现与主站
的信息交换。
工位1是物料出人工位,用于工控机进行管理。工控机通过 网卡连接主站,通过USB接口连接条码打印机,通过RS232连 接读码器。此工控机运行“装卸位管理软件”,进行零件的信息编 码、零件信息与操作信息的上传和下载、装卸姿态的指示等操作。 2控制系统调度的实现
Keywords:cotime monitor,HIM
某模块品种较多,批量较小,设计变化快,交货期短。根据模 块特点和生产情况,决定研发以物料传输自动化为主的柔性生 产线,来适应模块装配需要。该生产线由可转位的自动化物料仓 库、自动化送料小车、以及11个操作工位组成。
嚣。一嘲睇一_‘童。旆。磐~教导。…
姐40 位置lr
314
0 0
a 口
膏度
l∞
o
口
圈4位置变■组态
当调度程序生成小车命令时将触发模拟小车运动动作:
Car_move.bac。
以下为脚本变量与WjnCC变量的连接:
Set product_name=HMIRuntirne.Tags("C_producLnam的,/产品名称
cn.Open Set rs=CreateObject("ADODB.Recordset")
FS.open strsql,cn.3,3 y1 1=rs(『,Req”) G1一req.Value=y1 1 G1-req.Write
//数据库工位状态表打开 //读人相应数据
//数值存人v\finCC内部变量
首先在画面中画出一个小车的模型(我们简单地以一个矩 形代表物料输送小车),在其几何属性中,“位置X”和变量 “C—position”建立连接。也就是说小车的模型X座标将根据变 量“C—position”的变化而变化。如图4所示。
<工业控制计算机)2008年21卷第12期
17
胜I耕l
一矩膏 嬲口 ■邑 徉式 饵‘ 苴它 曩苑
yl 2=rs(”Fin”、
G1jin.Value=y12 G1jin.Write
crl.close
//关闭连接
调度动作介绍:除个别通用动作外,每个工位对应独自的触
发动作,以工位2为例,主要动作有:
万方数据
田3工位1的完成漉程田 3小车运动的监控
为了在监控画面中仿真小车执行调度命令,动画演示是必 不可少的。利用WinCC的图形编辑器和脚本编辑器,就可以实 现小车运动的监控。
万方数据
16
基于组态软件的模块化生产线控制系统
Idle:工位空闲,可以申请加工,也可以继续空闲; Work_time:此工位总加工时间,是调度信息之一,如工位2 和工位4的加工内容相同,而工位2的总加工时间大于工位4 的总加工时间,调度系统优先给工位4分配工件; Times:总加工次数,表示在次工位加工过的零件总数,同样 在加工内容相同的情况下,加工次数小的优先分配工件。 (2)小车任务表(T_DO_LIST) 小车任务表是调度系统和自动化小车之间的通信表,是小 车执行调度结果的根据。正确发送命令小车才能正常运行。 C_TASKID:任务号,主键,小车执行任务的编号; C_MATERIAL:物料号,小车运送产品标号; c-SPLACE:小车运送产品的源位置; c-DPLACE:小车运送产品的目标位置; D-DATETlME:El期时间; N_ERROR:设备故障,O为正常,1为出现故障; N—STATE:运行状态位。当为1时小车可以执行次命令;当 为2是小车正在执行命令,小车任务表禁止更新;当为6时表示 任务表可以更新,此时可以写入调度命令;写入新的命令时同时 更新次标志位为1。 除以上数据表外还有产品加工状态表、产品工序表、产品列 表、工作时间表、用户表等不一一介绍。 2-2调度规则 本文设计的调度程序可以随时添加新的加工任务,调度程 序循环扫描工位状态,根据工位状态和未加工零件情况生成调 度命令。 2.3调度程序流程介绍 根据前面的调度规则,使用WinCC中的脚本编辑器编写调 度程序。因为VBS脚本不断扫描各个动作的是否满足触发条 件,所以各个动作并非顺序执行,和PLc程序的执行相仿。 每个工位的状态通过PLC传给WinCC外部变量,当其发 生变化时触发相应的动作,其状态就会写入数据库。编写专门的 动作扫描数据库中的工位状态表,在通过内部变量传送给各个 工位的响应动作。调度命令的触发过如图2所示。
叫
G2_req.bac:负责触发工位请求命令; G2-fin.bac:负责触发工位完成命令; G2_set_pre_state.bac:负责触发工位完成后对一些状态 的设置; G2_movel.bac:负责触发工序优先级相同的工序没有完 全加工完的情况下。生成物料小车运动命令; G2_move2.bac:负责触发工序优先级相同的工序完全加 工完的情况下,生成物料小车运动命令; G2_time.bac:负责统计工位2工作时间; G2_work_times.bac:负责统计工位2工作次数。 2.3.1对通用工位(工位2-工位1 1)上料请求的响应流程 请求动作程序的工作流程如下:程序不断扫描工位状态,当 有工位提出上料申请时,触发上料申请动作(例如:工位2提出 上料申请,触发工位2上料动作G2_req.bac)。然后搜索产品加 工状态表,查看是否有工件需要申请上料的工位进行加工。如果 没有继续扫描,如果有选取优先级最高的工件,并判断此前的工 序是否加工完成,如果以上条件满足,判断小车状态是否可用, 如果不可用,继续扫描等待;如果可用,进行一些参数设置后生 成小车运动指令。 2.3.2对通用工位(工位2一工位”)加工完成触发的流程 完成动作触发流程:扫描工位状态,如果某工位发出完成信 号,为了调度工件到下个加工工位或回库,首先判断小车是否空 闲,如果小车不可用,则工件在次工位等待,此工位不能申请上料; 如果小车可用,判断加工工件的下个工序所用的工位是否申请。如 果没有申请。则工件回库。如果申请工件直接到下个加工工位。 2.3.3工位1的请求流程图 工位1负责上料下料和翻转,与其他工位有所不同,流程如 图3所示。系统运行时,可以根据需要添加产品。添加的产品名 称可能与正在加工的产品名称相同,这就要求我们为每个产品 生成唯一的信息。与其他上料申请有所不同的是,这个工位负责 工件的上下料和翻转,所以对申请命令要加以判断。 工位1的完成触发命令与通用工位类似,这里不一一介绍。
现场数据是调度的依据,数据的变化需要实时存储到数据 库中。在系统重新运行后也要求系统能够恢复到原来的状态,所 以中间数据也要存储到数据库中,数据库表的设计显得尤为重 要。本系统主要包括以下几个表:
(1)工位状态表(G_State) 工位状态表是用来存储各个工位的状态信息,包括请求、完 成信息,工位使用的次数。工位使用的时间,以及正在加工的产 品名、产品所属套的套号和件号。 各个属性的含义如下: G—Position:工位号,对应1—1 1工位,可作为工位状态表的 主键; Product_name:产品名,如A10005; SeLnum:加工零件所属套的套号。如属于第二套; Num:加工零件所属套中对应的件号,如第2套共有5件, 正在加工的是第2套的第3件,则Set__num=2,Nurn=3; Req:请求上料位标志位,当Req=l时表示此工位请求上 料,调度程序可以为次工位分配零件,当调度程序为其分配任务 后置0; Fin:加工完成标志位,当产品装配完成后,通知调度系统, 产品等待下到工序,或由小车送回存储库;
位置运算数据流图如图5所示。
splace:为小车的起点位置;dplace./|、车目标位置;position:
为了实现对装配线的合理调度,必须选择合适的控制技术。 以本研究课题为例。装配线包括11个装配工位。1个输送小车, 1个自动回转库,2台工控机,只有采用适当的传输控制技术,才 能组成一个完整的控制体系,才能正确执行调度命令,从而实现 装配的自动化。