油漆工艺规范文件
涂装通用工艺规范(精编文档).doc
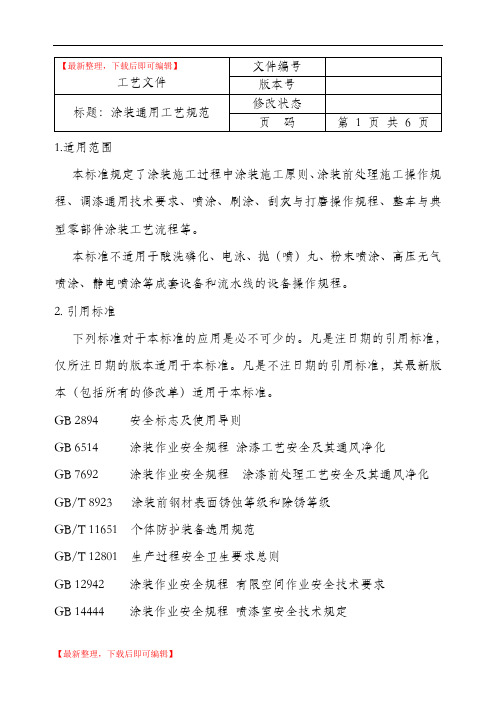
1.适用范围本标准规定了涂装施工过程中涂装施工原则、涂装前处理施工操作规程、调漆通用技术要求、喷涂、刷涂、刮灰与打磨操作规程、整车与典型零部件涂装工艺流程等。
本标准不适用于酸洗磷化、电泳、抛(喷)丸、粉末喷涂、高压无气喷涂、静电喷涂等成套设备和流水线的设备操作规程。
2. 引用标准下列标准对于本标准的应用是必不可少的。
凡是注日期的引用标准,仅所注日期的版本适用于本标准。
凡是不注日期的引用标准,其最新版本(包括所有的修改单)适用于本标准。
GB 2894 安全标志及使用导则GB 6514 涂装作业安全规程涂漆工艺安全及其通风净化GB 7692 涂装作业安全规程涂漆前处理工艺安全及其通风净化GB/T 8923 涂装前钢材表面锈蚀等级和除锈等级GB/T 11651 个体防护装备选用规范GB/T 12801 生产过程安全卫生要求总则GB 12942 涂装作业安全规程有限空间作业安全技术要求GB 14444 涂装作业安全规程喷漆室安全技术规定3 涂装施工原则3.1 涂装施工人员应经基础知识和专业培训并考核合格方能上岗操作。
3.2 涂装作业应满足GB 6514、GB 7692和GB/T 12801要求;施工环境、原材料、工具设备及操作工的劳动保护没达到要求不得施工。
3.3 前处理及上道工序不合格不得进行涂装施工,底漆不合格的零件不得打密封胶或刮灰处理。
3.4 零部件在涂装施工过程中不得交叉污染,离地高度应大于500mm。
4 涂装前处理施工操作规程4.1 薄板件涂装前处理4.1.1所有薄板件后续要求加工且未预处理的零件表面经除油、打磨、除锈、去氧化皮处理后喷涂预处理车间可焊型防锈底漆,漆膜厚度为20~25 m。
4.1.2 对于油污或锈蚀较为严重的零件,应在零件进入抛(喷)丸前进行人工除油或打磨处理,除油剂首选水溶性清洗剂,也可选用200#溶剂汽油;除锈用80目砂纸或0#砂布。
4.1.3漆烘干后,应用120~180目砂纸仔细打磨一遍,缝隙处应挤涂焊缝密封胶保护(碰焊件可预先打好碰焊胶);有缺陷的地方,可填补原子灰刮平。
GB6514-2008涂装作业安全规程-涂漆工艺安全及其通风净化
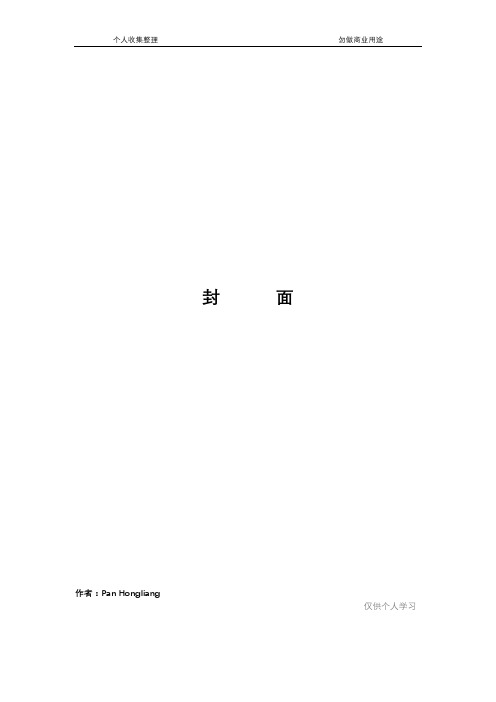
封面作者:Pan Hongliang仅供个人学习中华人民共和国国家标准涂装作业安全规程涂漆工艺安全及其通风净化GB 6514—2008代替GB 6514—1995 2008—12-11发布2009—10—01实施中华人民共和国质量监督检验检疫总局中国国家标准化管理委员会前言本标准除第1章、第2章、第3章为推荐性外,其余为强制性。
《涂装作业安全规程》系列国家标准已制订的共有12项:——GB 6514—2008《涂装作业安全规程涂漆工艺安全及其通风净化》;——GB 7691—2003《涂装作业安全规程安全管理通则》;——GB 7692—1999《涂装作业安全规程涂漆前处理工艺安全及其通风净化》;——GB 12367—2006《涂装作业安全规程静电喷漆工艺安全》;——GB 12942—2006《涂装作业安全规程有限空间作业安全技术要求》;——GB/T 1444 1—2008《涂装作业安全规程术语》;——GB 14443—2007《涂装作业安全规程涂层烘干室安全技术规定》;——GB 14444—2006《涂装作业安全规程喷漆室安全技术规定》;——GB 14773—2007《涂装作业安全规程静电喷枪及其辅助装置安全技术条件》;——GB 15607—2008《涂装作业安全规程粉末静电喷涂工艺安全》;——GB 17750—1999《涂装作业安全规程浸涂工艺安全》;——GB 20101—2006《涂装作业安全规程有机废气净化装置安全技术规定》。
本标准为《涂装作业安全规程》系列标准之一。
本标准对应于美国防火协会标准NFPA 33《易燃和可燃材料喷涂作业标准》(2007版),与NFPA 33:2007版一致性程度为非等效。
本标准修订并代替GB 6514—1995《涂装作业安全规程涂漆工艺安全及其通风净化》。
本标准与GB 6514—1995((涂装作业安全规程涂漆工艺安全及其通风净化》相比,主要差异如下:——增加、更新了引用的国家标准。
GB涂装作业安全规程涂漆工艺安全及其通风净化

中华人民共和国国家标准涂装作业安全规程涂漆工艺安全及其通风净化GB 6514—2008代替GB 6514—1995 2008—12-11发布2009—10—01实施中华人民共和国质量监督检验检疫总局中国国家标准化管理委员会前言本标准除第1章、第2章、第3章为推荐性外,其余为强制性。
《涂装作业安全规程》系列国家标准已制订的共有12项:——GB 6514—2008《涂装作业安全规程涂漆工艺安全及其通风净化》;——GB 7691—2003《涂装作业安全规程安全管理通则》;——GB 7692—1999《涂装作业安全规程涂漆前处理工艺安全及其通风净化》;——GB 12367—2006《涂装作业安全规程静电喷漆工艺安全》;——GB 12942—2006《涂装作业安全规程有限空间作业安全技术要求》;——GB/T 1444 1—2008《涂装作业安全规程术语》;——GB 14443—2007《涂装作业安全规程涂层烘干室安全技术规定》;——GB 14444—2006《涂装作业安全规程喷漆室安全技术规定》;——GB 14773—2007《涂装作业安全规程静电喷枪及其辅助装置安全技术条件》;——GB 15607—2008《涂装作业安全规程粉末静电喷涂工艺安全》;——GB 17750—1999《涂装作业安全规程浸涂工艺安全》;——GB 20101—2006《涂装作业安全规程有机废气净化装置安全技术规定》。
本标准为《涂装作业安全规程》系列标准之一。
本标准对应于美国防火协会标准NFPA 33《易燃和可燃材料喷涂作业标准》(2007版),与NFPA 33:2007版一致性程度为非等效。
本标准修订并代替GB 6514—1995《涂装作业安全规程涂漆工艺安全及其通风净化》。
本标准与GB 6514—1995((涂装作业安全规程涂漆工艺安全及其通风净化》相比,主要差异如下:——增加、更新了引用的国家标准。
——引用GB 50016—2006中有关条文和表作为涂漆作业场所火灾危险性分类的依据。
喷漆工艺规范

喷漆工艺规范篇一:喷漆技术规范※※目錄※※编制:审核:审批:1.范围:1.1 本规范规定了我司在金属零件或其组合件上进行喷漆的工艺要求及其质量要求。
1.2 本规范适用于工艺鉴定和批生产质量检验。
1.3本规范适用于所有金属基结构件。
2.引用标准:下列标准包含的条文,通过在本标准中引用而构成本标准的条文。
在标准出版时,所示版本均为有效。
所有标准都会被修订,使用本标准的各方应探讨,使用下列标准最新版本的可能性。
ISO 2409 涂料和清漆—交叉切割试验GB 6682-92分析实验室用水规格和试验方法GB 9271-88色漆和清漆标准试板GB 9274-88色漆和清漆耐液体介质的测定GB 9754-88色漆和清漆不含金属颜料的色漆漆膜之20°60°和85°镜面光泽的测定GB 11186.2-89 涂膜颜色的测量方法论每二部分测量GB/T 1732-93 漆腊耐冲击测定法GB/T 6739-1996涂膜硬度铅笔测定法GB/T 13452.2-92 色漆和清漆漆膜厚度的测定3.定义:批:指同一天在相同工艺条件下应用同种油漆的、材料和形状相似的零件的总和。
4.工艺鉴定要求: 4.1 总则:生产者的工艺设备、工艺流程、质量保证措施应在其主要的工艺文件中加以说明。
生产者的工艺、设备、质量必须满足第4节的要求。
4.2 设计要求:生产者应保持并遵守经华为技术有限公司正式批准的设备、工艺和检验文件。
4.3 喷漆间设施要求4.3.1 喷漆间应保持环境清洁,避免灰尘、油污等污染;4.3.2 喷漆间的温、湿度应能控制在以下范围:温度15-35℃相对湿度30-80%4.3.3 喷漆间最好有单独的零件进、出通道,尤其是要控制进入喷漆间的零件不会受到污染;4.3.4 所有设备应保持清洁、良好的状态;4.3.5 压缩空气应无油无水(操作者可用压缩空气对着干净的镜子吹2-3min,检查镜子上应无油、无水痕迹);4.3.6 烘房内温度应保持均匀,有效烘烤区的温差应能控制在+-5℃以内;温度控制、显示仪表的精度不低于1级。
2023修正版油漆喷涂工艺质量控制标准[1]
![2023修正版油漆喷涂工艺质量控制标准[1]](https://img.taocdn.com/s3/m/7ce5e79e294ac850ad02de80d4d8d15abe230033.png)
油漆喷涂工艺质量控制标准油漆喷涂工艺质量控制标准引言油漆喷涂是一种常见的表面处理方法,广泛应用于家具、汽车、建筑等各个领域。
为了确保油漆喷涂工艺的质量,需要制定标准来进行质量控制。
本文将介绍油漆喷涂工艺的质量控制标准,包括表面准备、涂装工艺、涂料选择和质量检验等方面。
1. 表面准备为了确保油漆的附着力和涂层的质量,对表面的准备十分重要。
以下是表面准备的标准:- 清洁度:表面应干净、无灰尘、油脂等污染物。
- 平整度:表面应平整,无凹凸不平的地方。
- 粗糙度:表面粗糙度应符合涂料厂家规定的要求。
2. 涂装工艺油漆喷涂工艺包括底涂、中涂和面涂等步骤。
以下是涂装工艺的标准:- 喷涂设备:喷枪、喷嘴等喷涂设备应符合要求,喷涂设备的调试和维护应定期进行。
- 喷涂厚度:涂装厚度应符合设计要求,需定期进行涂层厚度的测量。
- 喷涂均匀性:涂层应均匀、无滴流、鱼鳞状等缺陷。
- 喷涂速度:喷涂速度应适中,避免过快或过慢导致涂料流挂、鱼眼等问题。
3. 涂料选择涂料的选择对于油漆喷涂工艺的质量控制至关重要。
以下是涂料选择的标准:- 质量标准:涂料应符合国家相关质量标准或行业标准。
- 适用性:涂料应符合工件表面状态、环境要求等特殊要求。
- 技术指标:涂料的干燥时间、附着力、硬度等技术指标应达到要求。
4. 质量检验质量检验是确保油漆喷涂工艺质量的重要环节。
以下是质量检验的标准:- 外观检验:检查涂层是否均匀、有无鱼眼、流挂、刷破等问题。
- 膜厚检测:使用测膜仪等工具对涂层厚度进行检测。
- 附着力检验:采用划格法、胶带法等方法对涂层的附着力进行检验。
- 总检验:对喷涂工艺的各个环节进行全面的检查和评估,确保质量符合标准。
结论油漆喷涂工艺质量控制标准的制定对于确保产品的质量、延长使用寿命具有重要意义。
通过表面准备、涂装工艺、涂料选择和质量检验等方面的标准,可以实现油漆喷涂工艺的规范化和标准化管理,提高产品的质量和市场竞争力。
GB6514_2008涂装作业安全规程_涂漆工艺设计安全和通风净化
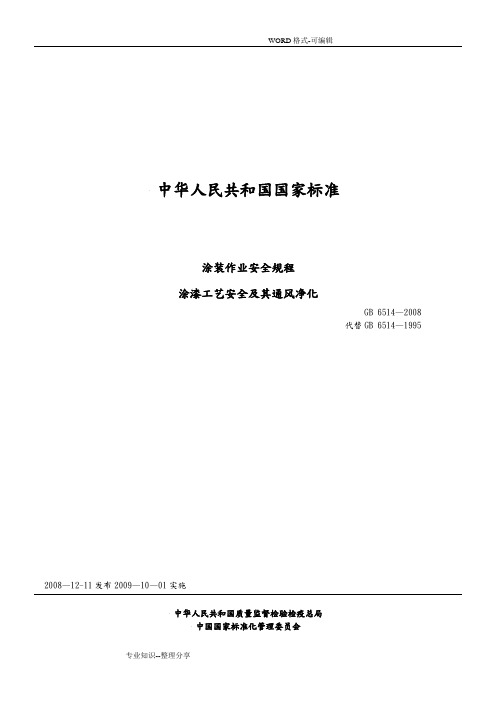
中华人民共和国国家标准涂装作业安全规程涂漆工艺安全及其通风净化GB 6514—2008代替GB 6514—19952008—12-11发布2009—10—01实施中华人民共和国质量监督检验检疫总局中国国家标准化管理委员会前言本标准除第1章、第2章、第3章为推荐性外,其余为强制性。
《涂装作业安全规程》系列国家标准已制订的共有12项:——GB 6514—2008《涂装作业安全规程涂漆工艺安全及其通风净化》;——GB 7691—2003《涂装作业安全规程安全管理通则》;——GB 7692—1999《涂装作业安全规程涂漆前处理工艺安全及其通风净化》;——GB 12367—2006《涂装作业安全规程静电喷漆工艺安全》;——GB 12942—2006《涂装作业安全规程有限空间作业安全技术要求》;——GB/T 1444 1—2008《涂装作业安全规程术语》;——GB 14443—2007《涂装作业安全规程涂层烘干室安全技术规定》;——GB 14444—2006《涂装作业安全规程喷漆室安全技术规定》;——GB 14773—2007《涂装作业安全规程静电喷枪及其辅助装置安全技术条件》;——GB 15607—2008《涂装作业安全规程粉末静电喷涂工艺安全》;——GB 17750—1999《涂装作业安全规程浸涂工艺安全》;——GB 20101—2006《涂装作业安全规程有机废气净化装置安全技术规定》。
本标准为《涂装作业安全规程》系列标准之一。
本标准对应于美国防火协会标准NFPA 33《易燃和可燃材料喷涂作业标准》(2007版),与NFPA 33:2007版一致性程度为非等效。
本标准修订并代替GB 6514—1995《涂装作业安全规程涂漆工艺安全及其通风净化》。
本标准与GB 6514—1995((涂装作业安全规程涂漆工艺安全及其通风净化》相比,主要差异如下:——增加、更新了引用的国家标准。
——引用GB 50016—2006中有关条文和表作为涂漆作业场所火灾危险性分类的依据。
油漆通用标准工艺

油漆通用工艺
1)一般涂漆通用工艺
2)阴极电泳涂装通用工艺
编制:
审核:
批准:
五月十四日
一般涂漆通用工艺
1 范畴
本守则规定了一般涂漆加工旳工艺规则,合用于我司旳一般涂漆加工。
2 除锈
2.1 对工件表面旳型沙、毛刺、焊渣、飞溅物、油污、灰尘等物用砂皮及钢丝刷等除锈工具刮,铲清除干净,使其达到平整、清洁,提高涂层旳附着力。
2.2 锈蚀级别见表
2.3 除锈级别见表
零件非焊接部位应按St2彻底除锈,零件焊接部位应按St3非常彻底除锈。
3 底漆
3.1 底漆重要是起锈和增长附着力作用,在除锈完旳表面施工。
3.2 底漆可以用喷、刷措施进行。
3.3 施工时底漆粘度调到喷为18-22秒、刷为30-50秒。
3.4 零件焊接接头前不涂底漆,待焊后补涂。
3.5 底漆涂1-2遍。
4 调漆
4.1 调漆前旳准备工作涉及对旳选择涂料、稀释剂、辅助材料和所需旳工具。
4.2 核对材料旳名称、生产厂家、批号、日期和重量。
4.3 油漆旳配色,一般按色卡、样板来进行,先试小样,再对照样板,按一定旳重量比例,。
油漆调配工艺操作规范

油漆调配工艺操作规范1 范围本标准规定了江联重工股份有限公司表面涂装油漆调配技术要求。
本标准适用于包装车间油漆调配技术要求和注意事项。
2目的为了更好提高包装车间产品表面漆膜质量和成本控制,制订油漆调配操作规范.3 调漆人员要求3.1 设定专人调配油漆和保管油漆日常工作。
3。
2对油漆的调配方法、注意事项和安全有足够的认识和理解。
3.3 对油漆的品种相互之间配套可行性的了解,避免造成不必要的浪费。
3.4 控制好每次调配油漆用量,保证涂装工在有效时间内用完,未用完的油漆妥善保管好,能再次利用的油漆尽量在最短的时间内使用完。
3。
5 调漆人员对每次调好的油漆做好记录,方便以后数据统计、分析和质量跟踪。
4 油漆调配方法4。
1 准备好要调配油漆的电子秤或量具、清洁的油漆空桶和搅拌油漆棍等工具。
4。
2核对所要调配油漆的品种、型号、配套性、有效期、规格是否符合技术条件要求的规定,质量不合格、变质、过期的油漆不能使用。
4。
3 调漆前用搅拌棒将原漆桶的油漆搅拌直至均匀。
4。
4 根据所需喷涂的面积和时间,来调配油漆的用量.4.5 双组份油漆调配依次倒入油漆、固化剂、稀释剂;调配比例按照油漆厂家提供的参数,调和的油漆使用前根据实际情况用80-120目的滤网进行过滤;并放置5—15分钟熟化后方可使用,调配好的双组份油漆在规定的可使用期限2—4小时内用完,油漆变稠后不能再使用。
4。
6单组份油漆调和后根据实际情况用80—120目的滤网进行过滤,稀释剂比例按照油漆厂家提供的参数比例调配。
4.7调配油漆参数见:表一表一5 注意事项5。
1、调配油漆不能用带有颜色和不清洁的空桶,避免引起色差.5。
2、油漆开桶后未用完的要及时封闭好,避免油漆表面长时间接触空气造成结皮、稀释剂不封闭好易挥发造成浪费和存在安全隐患.5.3、油漆、稀释剂都是易燃易爆物品,现场、调配区尽量保证当天用量。
5。
4、涂料在调配过程当中发现有过期的要及时通知检验、工艺相关人员确认合格后方可使用.5。
- 1、下载文档前请自行甄别文档内容的完整性,平台不提供额外的编辑、内容补充、找答案等附加服务。
- 2、"仅部分预览"的文档,不可在线预览部分如存在完整性等问题,可反馈申请退款(可完整预览的文档不适用该条件!)。
- 3、如文档侵犯您的权益,请联系客服反馈,我们会尽快为您处理(人工客服工作时间:9:00-18:30)。
5 油漆喷涂工艺流程
5.1油漆喷涂工艺流程路线
1脱脂→2水洗→3中和→4清洗→5烘干→6打磨a→7刮灰a→8打磨b→9底漆→10风干→11刮灰b→12打磨检查c→13喷面漆→14风干
5.2油漆喷涂工艺要求
6、5.2.1脱脂(去油除锈):
4.2.2油漆作业的环境湿度应保持在85%以下;
4.2.3进行涂装前必须检查所需的照明、排风、喷枪、烘箱等设备是否完备可靠;
4.2.4施工场所应有良好的通风条件;
4.2.5电线必须按防爆等级进行安装,电动机的启动装置和配电设备应是防爆式的;
4.2.6照明灯应用安全灯并要加玻璃罩保护.为避免静电聚集,喷漆室及喷枪应有接地装置;
4.2.7超出不符合以上规定条件需要作业的必须采取相应的措施,以达到规定条件方可进行作业。
4.3操作人员应具备资格和防护措施
4.3.1操作人员需经过培训,考核合格后方可进行油漆作业;
4.3.2操作人员在作业时需保持良好的身体条件,避免带情绪上岗作业;
4.3.3操作人员在使用手工或风动工具打磨时,为了避免眼睛受伤和吸入灰尘,应戴防护眼镜和防尘口罩;
5.2.12.2需仔细比对面漆颜色规格与油漆作业图上是否一致;
5.2.12.3将零件放入工作台中进行油漆喷涂;
5.2.12.4需控制喷台四周的粉尘,防止喷漆后产生颗粒;
5.2.12.5喷漆不得有桔皮、流挂、颗粒、花斑、变色等缺陷,由操作人员进行自检。
5.2.13风干
5.2.13.1将喷完面漆的零件放入风干区域,均匀摆放;
非标机械零件表面油漆喷涂作业规
1 目的
为保证公司非标机械零件经油漆喷涂后,其表面美观大器,提升产品外在质量,特制定本作业规。
2 作业围
适用于本公司自有品牌产品的所有非标机械零件、对外加工的零件。
3 责任单位
3.1 采购部负责提供优质的油漆喷涂材料,前期处理合格的外协零件(焊接、毛边前期处理)。
3.2 制造部负责提供前期处理合格的外协零件(焊接、毛边前期处理)。
4.1.2涂料调配过程中要不断搅拌沉淀物。催干剂、稀释剂、固化剂等 辅助材料加入数量应该严格按照施工作业指导书及产品使用说明书中有关规定使用。
4.1.3调配的涂料应粘度适中,颜色符合标准样板及色差围,色泽 均匀一致。
4.2油漆喷涂作业具备的环境条件和设备条件
4.2.1油漆作业的环境温度应保持在5℃——30℃;
4.3.4操作人员为了防止油漆溅在皮肤上或眼睛,作业时必须穿戴工作服、手套、防护眼镜、防毒口罩;
4.3.5操作人员如有头晕、头痛、恶心、呕吐不适感觉,应立即到有新鲜空气的地方,直至原工作处的通风条件得改善后才可继续进行涂装.如因吸入过量的溶剂气体或漆雾而昏厥者,则应立即将其移至空气新鲜的地方,使其渐渐复原,但不要进行强迫运动;
5.2.1.1脱脂所需液体为水,盐酸,除油剂;其中盐酸的PH值应控制在2-3之间;
5.2.1.2水,盐酸,除油剂按4:1:1的比例倒入脱脂池中进行去油除锈;
5.2.1.3时间根据零件的含油脂量及表面锈蚀情况而定;
5.2.1.4从脱脂池中取出,表面需保证不得有锈斑和油渍;
5.2.1.5对于锈蚀不严重或者局部有锈斑的可不放入脱脂池中整体处理,而可进行局部的脱脂(去油除锈)处理。
5.2.2水洗
5.2.2.1将柜体及零件放在清水中浸泡,清水的PH值应该控制在6-7之间;
5.2.2.2清洗的时间控制在1-3分钟之间。
5.2.3中和
5.2.3.1将清水洗好的柜体或零件放入中和池中;
5.2.3.2中和池中强碱粉(NaOH氢氧化纳PH值为12)跟水的比率请控制在3%——10%之间;
5.2.3.3中和处理的时间需控制在1-3分钟之间。
5.2.6.1选用合适的砂轮机(角磨机)打磨零件表面;
5.2.6.2零件表面四周棱角处都需打磨平整。
5.2.7刮灰a
5.2.7.Байду номын сангаас固化剂与原子灰比例依据既定标准进行调和;
5.2.7.2将零件表面不平整的部位、焊接凹陷、表面划痕等部位用原子灰补平。
5.2.8打磨b
5.2.8.1选用合适的砂纸打磨零件表面;
3.3 品质部负责焊接、毛边等前期处理的质量管控,油漆喷涂前、中、后的质量监督。
3.4 仓库负责入库、出库焊接、毛边等前期处理合格的非标机械零件。
3.5 油漆组负责按《非标零件表面油漆喷泉涂作业标准》执行油漆喷涂作业。
4 作业前油漆喷涂材料的准备
4.1 油漆涂料及辅助材料的准备
4.1.1按照订单指定的型号、颜色及调配的涂料和辅助材料使用,严禁施工人员使用超过质量保质期的涂料及辅助材料。
5.2.13.2风干时间依据实际室温控制;以保证漆面的牢固、光滑、饱满。
5.3油漆作业过程中防护
5.3.1底漆前需用美纹纸将外螺纹、轴承位、油封位、外配合面等缠裹严住;
5.3.2对部分表面处理的零件,对该零件表面没有油漆喷涂时,底漆前需用美纹纸(或其他纸)将已作表面的部分缠裹严住。
5.2.10.3原子灰的调制比例同上。
5.2.11打磨检查c
5.2.11.1先用180#砂纸粗打机柜或零件表面;
5.2.11.2需将全部表面都打磨到位;
5.2.11.3后用240#砂纸细打零件表面;
5.2.11.4检查零件表面是否留有气孔,划痕,凹陷等缺陷。
5.2.12喷面漆
5.2.12.1油漆作业人员需再次检查二次打磨的零件是否达到喷面漆的标准;
5.2.4清洗
5.2.4.1请将磷化好的机柜或零件用循环水(活水)冲洗;
5.2.4.2冲洗时间规定为1分钟左右。
5.2.5烘干
5.2.5.1将零件放入烘箱烘干,烘箱温度控制在60℃-70℃度之间;
5.2.5.2烘干时间需控制在15-20分钟之间;
5.2.5.3零件也可作吹干处理,或者晒干处理。
5.2.6打磨a
5.2.8.2零件表面四周棱角处都需打磨平整。
5.2.9底漆
5.2.9.1将零件摆放在油漆作业区域上;
5.2.9.2将调制好的油漆喷于零件的外表面上;
5.2.9.3零件表面不得有流漆、漏喷现象;
5.2.9.4由操作人员进行自检。
5.2.10刮灰b
5.2.10.1将零件进行二次刮灰;
5.2.10.2零件表面未刮好的凹坑、划痕、气孔等用原子灰刮平;