HBZ346-2002 熔模铸造钢铸件补焊工艺及检验
GB标准汇总
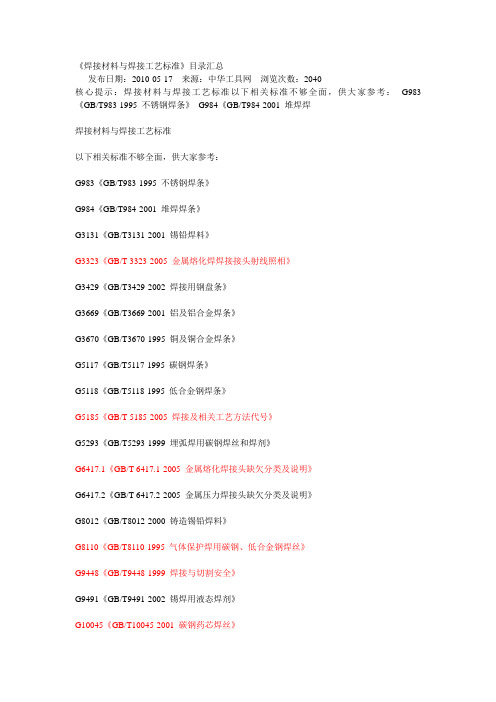
《焊接材料与焊接工艺标准》目录汇总发布日期:2010-05-17 来源:中华工具网浏览次数:2040核心提示:焊接材料与焊接工艺标准以下相关标准不够全面,供大家参考:G983《GB/T983-1995 不锈钢焊条》G984《GB/T984-2001 堆焊焊焊接材料与焊接工艺标准以下相关标准不够全面,供大家参考:G983《GB/T983-1995 不锈钢焊条》G984《GB/T984-2001 堆焊焊条》G3131《GB/T3131-2001 锡铅焊料》G3323《GB/T 3323-2005 金属熔化焊焊接接头射线照相》G3429《GB/T3429-2002 焊接用钢盘条》G3669《GB/T3669-2001 铝及铝合金焊条》G3670《GB/T3670-1995 铜及铜合金焊条》G5117《GB/T5117-1995 碳钢焊条》G5118《GB/T5118-1995 低合金钢焊条》G5185《GB/T 5185-2005 焊接及相关工艺方法代号》G5293《GB/T5293-1999 埋弧焊用碳钢焊丝和焊剂》G6417.1《GB/T 6417.1-2005 金属熔化焊接头缺欠分类及说明》G6417.2《GB/T 6417.2-2005 金属压力焊接头缺欠分类及说明》G8012《GB/T8012-2000 铸造锡铅焊料》G8110《GB/T8110-1995 气体保护焊用碳钢、低合金钢焊丝》G9448《GB/T9448-1999 焊接与切割安全》G9491《GB/T9491-2002 锡焊用液态焊剂》G10045《GB/T10045-2001 碳钢药芯焊丝》G10046《GB/T10046-2000 银钎料》[page]G12467《GB/T12467.1~4-1998 焊接质量要求金属材料的熔化焊》G12470《GB/T12470-2003 低合金埋弧焊用焊剂》G14693《GB/T14693-1993 焊缝无损检测符号》G15169《GB/T15169-2003 钢熔化焊手焊工资格考试方法》G15620《GB/T15620-1995 镍及镍合金焊丝》G15747《GB/T15747-1995 正面角焊缝接头拉伸试验方法》G15830《GB/T15830-1995 钢制管道对接环焊缝超声波探伤方法和检验》G16672《GB/T16672-1996 焊缝-工作位置-倾角和转角的定义》G17493《GB/T17493-1998 低合金钢药芯焊丝》G17853《GB/T17853-1999 不锈钢药芯焊丝》G17854《GB/T17854-1999 埋弧焊用不锈钢焊丝和焊剂》G18290.2《GB/T18290.2-2000 无焊连接:无焊压连连接一般要求》G18290.3《GB/T18290.3-2000 无焊连接:可接触无焊绝缘位移连接一般要求》G18290.4《GB/T18290.4-2000 无焊连接:不可接触无焊绝缘位移连接一般要求》G18290.5《GB/T18290.5-2000 无焊连接:无焊压入式连接一般要求》G18591《GB/T18591-2001 焊接预热温度、道间温度及预热维持温度的测量指南》G18762《GB/T18762-2002 贵金属及其合金钎料》G19418《GB/T19418-2003 钢的弧焊接头缺陷质量分级指南》G19419《GB/T19419-2003 焊接管理任务与职责》G19804《GB/T 19804-2005 焊接结构的一般尺寸公差和形位公差》G19805《GB/T 19805-2005 焊接操作工技能评定》G19866《GB/T 19866-2005 焊接工艺规程及评定的一般原则》G19867.1《GB/T 19867.1-2005 电弧焊焊接工艺规程》G19868.1《GB/T 19868.1-2005 基于试验焊接材料的工艺评定》G19868.2《GB/T 19868.2-2005 基于焊接经验的工艺评定》G19868.3《GB/T 19868.3-2005 基于标准焊接规程的工艺评定》G19868.4《GB/T 19868.4-2005 基于预生产焊接试验的工艺评定》G19869.1《GB/T 19869.1-2005 钢、镍及镍合金的焊接工艺评定试验》G19897.1《GB/T 19897.1-2005 自动抄表系统低层通信协议:直接本地数据交换》[page]G19897.3《GB/T 19897.3-2005 自动抄表系统低层通信协议:异步数据交换的物理层服务进程》图书中国机械工业标准汇编(第二版):金属无损检测与探伤卷(上)目录: —、通用与综合GB/T5616—1985常规无损探伤应用导则GB/T6417—1986金属熔化焊焊缝缺陷分类及说明GB/T9445—1999无损检测人员资格鉴定与认证GB/T12469—1990焊接质量保证钢熔化焊接头的要求和缺陷分级GB/T14693—1993焊缝无损检测符号JB4730—1994压力容器无损检测JB/T5000.14—1998重型机械通用技术条件铸钢件无损探伤JB/T5000.15—>998重型机械通用技术条件锻钢件无损探伤JB/T7406.2—1994试验机术语无损检测仪器JB/T9095—1999离心机、分离机锻焊件常规无损探伤技术规范二、表面方法GB/T5097—1985黑光源的间接评定方法GB/T9443—1988铸钢件渗透探伤及缺陷显示迹痕的评级方法GB/T9444—1988铸钢件磁粉探伤及质量评级方法GB/T10121—1988钢材塔形发纹磁粉检验方法GB/T12604.3—1990无损检测术语渗透检测GB/T12604.5—1990无损检测术语磁粉检测GB/T15147—1994核燃料组件零部件的渗透检验方法GB/T15822—1995磁粉探伤方法GB/T16673—1996无损检测用黑光源(UV—A)辐射的测量GB/T17455—1998无损检测表面检查的金相复制件技术GB/T18851—2002无损检测渗透检验标准试块JB/T5391—1991铁路机车车辆滚动轴承零件磁粉探伤规程JB/T5442—1991压缩机重要零件的磁粉探伤JB/T6061—1992焊缝磁粉检验方法和缺陷磁痕的分级JB/TGJ294A《GJB294A-2005 铝及铝合金熔焊技术条件》GJ607A《GJB607A-1998 金属材料及其焊件的爆炸试验规程》GJ724A《GJB/Z724A-1998 不锈钢电阻点焊和焊缝质量检验》GJ1138《GJB1138-1999 铝及铝合金焊丝规范》GJ1718A《GJB1718A-2005 电子束焊接》GJ3021《GJB 3021-1997 航空用结构钢焊丝规范》GJ3785《GJB3785-1999 航空用不锈钢焊丝规范》GJ5162《GJB5162-2003 镍-金基合金高温钎料规范》WJ2613《WJ 2613-2003 兵器铝合金焊接技术要求》QJ2844《QJ2844-1996 铝及铝合金硬钎焊技术条件》QJ2864《QJ2864-1997 铝及铝合金熔焊工艺规范》QJ2868《QJ2868-1997 二氧化碳气体保护半自动焊工艺规范》QJ2845《QJ 2845-1996 铝及铝合金硬钎焊工艺》QJ3040《QJ3040-1998 焊缝建档规定》QJ3071《QJ3071-1998 等离子弧焊技术条件》QJ3072《QJ3072-1998 铝合金铸件补焊工艺规范》QJ3090《QJ3090-1999 焊接材料复验规定》QJ3115《QJ3115-1999 导管熔焊接头角焊缝X射线照相检验方法》QJ3116《QJ3116-1999 金属熔焊内部缺陷X射线照相参考底片》H238《HB/Z238-1993 高温合金电阻点焊和缝焊工艺》H309《HB/Z309-1997 高温合金及不锈钢真空钎焊》H315《HB/Z315-1998 高温合金、不锈钢真空电子束焊接工艺》[page] H328《HB/Z328-1998 镁合金铸件补焊工艺及检验》H345《HB/Z345-2002 铝合金铸件补焊工艺及检验》H346《HB/Z346-2002 熔模铸造钢铸件补焊工艺及检验》H348《HB/Z348-2001 钛及钛合金铸件补焊工艺及检验》H459《HB 459-2004 航空用结构钢焊条规范》H5134《HB/Z 5134-2000 结构钢和不锈钢熔焊工艺》H5135《HB 5135-2000 结构钢和不锈钢熔焊接头质量检验》H5299《HB5299-1996 航空工业手工熔焊焊工技术考核》H5363《HB5363-1995 焊接工艺质量控制》H6771《HB 6771-1993 银基钎料》H6772《HB 6772-1993 镍基钎料》H7052《HB 7052-1994 铝基钎料》H7053《HB 7053-1994 铜基钎料》H7575《HB7575-1997 高温合金及不锈钢真空钎焊质量检验》H7608《HB7608-1998 高温合金、不锈钢真空电子束焊接质量检验》J3168《JB/T3168.1~3-1999 喷焊合金粉末》J3223《JB/T3223-1996 焊接材料质量管理规程》J4291《JB/T4291-1999 焊接接头裂纹张开位移(COD)试验方法》J6963《JB/T6963-1993 钢制熔化焊工艺评定》J6964《JB/T6964-1993 特细碳钢焊条》J6966《JB/T6966-1993 钎缝外观质量评定方法》J6967《JB/T6967-1993 电渣焊通用技术条件》J6975《JB/T6975-1993 自熔合金喷焊技术条件》J7520《JB/T7520.1~6-1994 磷铜钎料化学分析方法》J7524《JB/T7524-1994 建筑钢结构焊缝超声波探伤》J7716《JB/T7716-1995 焊接接头四点弯曲疲劳试验方法》J7717《JB/T7717-1995 焊接接头ECO试验方法》J7853《JB/T7853-1995 铬镍奥氏体不锈钢焊缝金属中铁素体数的测量》J7948《JB/T7948.1~12-1999 熔炼焊剂化学分析方法》J7949《JB/T7949-1999 钢结构焊缝外形尺寸》[page]J8423《JB/T8423-1996 电焊条焊接工艺性能评定方法》J8428《JB/T8428-1996 校正钢焊缝超声检测仪用标准试块》J8931《JB/T8931-1999 堆焊层超声波探伤方法》J9185《JB/T9185-1999 钨极惰性气体保护焊工艺方法》J9186《JB/T9186-1999 二氧化碳气体保护焊工艺方法》J9212《JB/T9212-1999 常压钢质油罐焊缝超声波探伤》J10045《JB/T10045.1~5-1999 热切割》J10375《JB/T10375-2002 焊接物件振动时效工艺参数选择及技术要求》J50076《JB/T50076-1999 气体保护电弧焊用碳钢,低合金钢焊丝产品质量分等》J50193《JB/T50193-1999 银钎料产品质量分等》J50194《JB/T50194-1999 锡铅焊料产品质量分等》J56050《JB/T56050-1999 铜基钎料产品质量分等》J56097《JB/T56097-1999 碳素钢埋弧焊用焊剂产品质量分等》J56098《JB/T56098-1999 铝及铝合金焊丝产品质量分等》J56099《JB/T56099-1999 铜及铜合金焊丝产品质量分等》J56100《JB/T56100-1999 堆焊焊条产品质量分等》J56101《JB/T56101-1999 铸铁焊条产品质量分等》J56102.1《JB/T56102.1-1999 碳钢焊条产品质量分等》J56102.2《JB/T56102.2-1999 低合金钢焊条产品质量分等》J56102.3《JB/T56102.3-1999 不锈钢焊条产品质量分等》TB2374《TB/T2374-1999 铁路机车车辆用耐钢焊条和焊丝》SH3520《SH/T3520-2004 石油化工工程铬钼耐热钢管道焊接技术规程》SH3525《SH/T3525-2004 石油化工低温钢焊接规程》SH3526《SH/T3526-2004 石油化工异种钢焊接规程》SH3527《SH3527-1999 石油化工不锈钢复合钢钢焊接规程》DL678《DL/T678-1999 电站钢结构焊接通用技术条件》DL754《DL/T754-2001 铝母线焊接技术规程》DL816《DL/T816-2003 电力工业焊接操作技能教师资格考核规则》DL819《DL/T819-2002 火力发电厂焊接热处理技术规程》[page]DL833《DL/T833-2003 民用核承压设备焊工资格考核规则》DL868《DL/T 868-2004 焊接工艺评定规程》DL869《DL/T 869-2004 火力发电厂焊接技术规程》JG11《JG11-1999 钢网架焊接球接点》JG3034.1《JG/T3034.1-1996 焊接球节点钢网架焊缝超声波探伤及质量分级法》JG3034.2《JG/T3034.2-1996 螺栓球节点钢网架焊缝超声波探伤及质量分级法》YB5092《YB/T5092-1996 焊接用不锈钢丝》YB9259《YB/T9259-1998 冶金工程建设焊工考试规程》YS458《YS/T458-2003 轨道车辆结构用铝合金挤压型材配用焊丝》SJ10534《SJ/T10534-1994 波峰焊接技术要求》SJ11168《SJ/T11168-1998 免清洗焊接用焊锡丝》SJ11186《SJ/T11186-1998 锡铅膏状焊料通用规范》SJ11216《SJ/T11216-1999 红外/热风再流焊接技术要求》SJ11273《SJ/T11273-2002 免清洗液态助焊剂》SH3520《SH/T3520-2004 石油化工工程铬钼耐热钢管道焊接技术规程》SH3523《SH/T 3523-1999 石油化工铬镍奥氏体钢、铁镍合金和镍合金管道焊接规程》SH3524《SH/T3524-1999 石油化工钢制塔式容器现场组焊施工工艺标准》SH3525《SH/T3525-2004 石油化工低温钢焊接规程》SH3526《SH/T3526-2004 石油化工异种钢焊接规程》SH3527《SH3527-1999 石油化工不锈钢复合钢钢焊接规程》SY0059《SY/T0059-1999 控制钢制设备焊缝硬度防止硫化物应力开裂》焊93《焊接标准汇编》(1993~1995)(96机械版)焊96《焊接标准汇编》(1996~1999)(2000机械版)焊39《焊接材料标准汇编》(1992~1999)(2001机械版)[page]本篇文章来源于中华工具网(/) 原文链接:/news/show-21785.html。
铸钢件焊补工艺守则
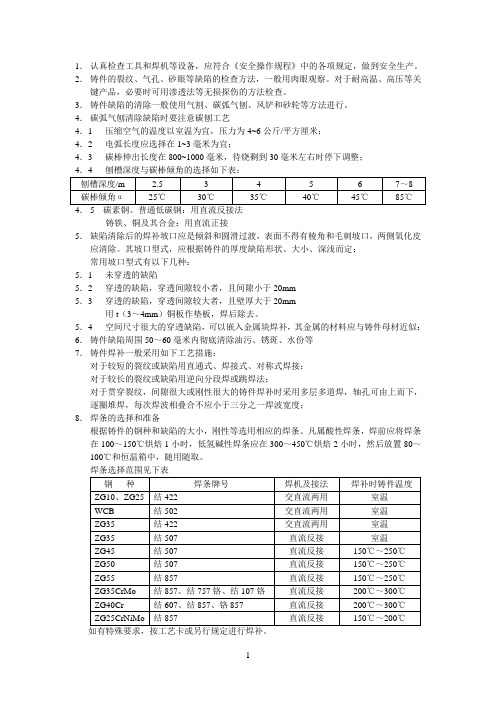
1.认真检查工具和焊机等设备,应符合《安全操作规程》中的各项规定,做到安全生产。
2.铸件的裂纹、气孔、砂眼等缺陷的检查方法,一般用肉眼观察。
对于耐高温、高压等关键产品,必要时可用渗透法等无损探伤的方法检查。
3.铸件缺陷的清除一般使用气割、碳弧气刨、风铲和砂轮等方法进行。
4.碳弧气刨清除缺陷时要注意碳刨工艺4.1压缩空气的温度以室温为宜,压力为4~6公斤/平方厘米;4.2电弧长度应选择在1~3毫米为宜;4.3碳棒伸出长度在800~1000毫米,待烧剩到30毫米左右时停下调整;4.4刨槽深度与碳棒倾角的选择如下表:刨槽深度/m 2.5 3 4 5 6 7~8碳棒倾角α25℃30℃35℃40℃45℃85℃4.5 碳素钢、普通低碳钢:用直流反接法铸铁、铜及其合金:用直流正接5.缺陷清除后的焊补坡口应是倾斜和圆滑过渡,表面不得有棱角和毛刺坡口,两侧氧化皮应清除。
其坡口型式,应根据铸件的厚度缺陷形状、大小、深浅而定;常用坡口型式有以下几种:5.1未穿透的缺陷5.2穿透的缺陷,穿透间隙较小者,且间隙小于20mm5.3穿透的缺陷,穿透间隙较大者,且壁厚大于20mm用t(3~4mm)铜板作垫板,焊后除去。
5.4空间尺寸很大的穿透缺陷,可以嵌入金属块焊补,其金属的材料应与铸件母材近似:6.铸件缺陷周围50~60毫米内彻底清除油污、锈斑、水份等7.铸件焊补一般采用如下工艺措施:对于较短的裂纹或缺陷用直通式、焊接式、对称式焊接;对于较长的裂纹或缺陷用逆向分段焊或跳焊法;对于贯穿裂纹,间隙很大或刚性很大的铸件焊补时采用多层多道焊,轴孔可由上而下,逐圈堆焊,每次焊波相叠合不应小于三分之一焊波宽度;8.焊条的选择和准备根据铸件的钢种和缺陷的大小,刚性等选用相应的焊条。
凡属酸性焊条,焊前应将焊条在100~150℃烘焙1小时,低氢碱性焊条应在300~450℃烘焙2小时,然后放置80~100℃和恒温箱中,随用随取。
焊条选择范围见下表钢种焊条牌号焊机及接法焊补时铸件温度ZG10、ZG25 结422 交直流两用室温WCB 结502 交直流两用室温ZG35 结422 交直流两用室温ZG35 结507 直流反接室温ZG45 结507 直流反接150℃~250℃ZG50 结507 直流反接150℃~250℃ZG55 结857 直流反接150℃~250℃ZG35CrMo 结857、结757铬、结107铬直流反接200℃~300℃ZG40Cr 结607、结857、铬857 直流反接200℃~300℃ZG25CrNiMo 结857 直流反接150℃~200℃如有特殊要求,按工艺卡或另行规定进行焊补。
铸钢件缺陷焊补规程

铸钢件缺陷焊补规程1.目的规范阀体零件的补焊工艺,使被焊零件的性能稳定,保证阀门整体性能符合要求。
2.范围本规程适用于本公司生产的阀门的铸钢件、阀体等的补焊。
3.职责3.1 技术科负责补焊工艺评定和编制补焊工艺;3.2 生产科负责组织补焊的实施;3.3 车间焊工负责阀门零件的补焊;3.4 质检科负责补焊件的PT检测和再次进行阀体压力试验;3.5 公司办负责补焊操作人员的培训和上岗资格认可工作。
4.工作程序4.1对焊工、设备、环境的要求4.1.1从事焊接工作的焊工按要求进行考试合格。
4.1.2 工作前必须检查电源线是否漏电、二次线及外壳接地是否良好。
一次与二次线路必须完整,焊钳必须绝缘良好。
4.1.3工作前必须穿戴好防护用品,操作时(包括清渣)所有工作人员必须戴好防护眼镜或面罩,扎紧袖口。
4.1.4工作现场应保持干燥,通风良好。
4.1.5焊接过程中应尽量避免多次引弧和电弧中断,在换焊条时,其接头一定要有很好的熔合后方可继续焊接。
4.1.6进行阀体补焊时,必须在消除体腔内压力后方可补焊,严禁带压补焊。
4.1.7 焊接设备应经常检修、擦拭。
工作前应先让焊机空载运行2min~3min后方可焊接,以保证焊接设备处于良好的工作状态。
4.1.8 工作完毕后应先关闭电焊机,然后切断电源,切不可逆向停机;回收未用完的焊材,整理设备,清理现场。
4.2 焊前准备4.2.1阀体压力试验:当质检员发现阀体不上压后,应将阀门渗漏部位做出明显标记并口头通知焊工进行补焊。
4.2.2检查所用设备(焊机、转胎等)运转情况是否正常,地线与工件连接是否紧固,避免因接触不良损伤焊接表面。
4.2.3检查焊条是否经过烘干处理。
经过烘干的焊条放入保温筒;在烘干箱外停留时间不应超过1小时,以免焊条受潮。
焊条尽量避免反复烘干。
4.2.4 认真清除焊道上的铁锈、油污、毛刺和水等。
4.3 补焊工艺4.3.1 承压件的补焊a.受压零件经水压试验后,在有缺陷位置打上标识。
铸件焊接修补实验报告
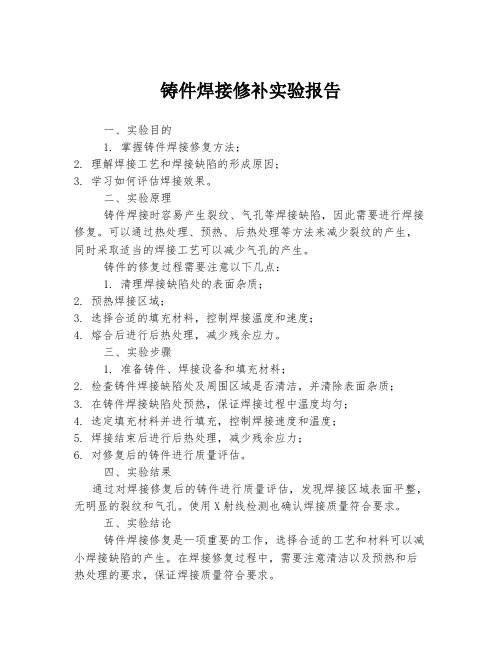
铸件焊接修补实验报告
一、实验目的
1. 掌握铸件焊接修复方法;
2. 理解焊接工艺和焊接缺陷的形成原因;
3. 学习如何评估焊接效果。
二、实验原理
铸件焊接时容易产生裂纹、气孔等焊接缺陷,因此需要进行焊接修复。
可以通过热处理、预热、后热处理等方法来减少裂纹的产生,同时采取适当的焊接工艺可以减少气孔的产生。
铸件的修复过程需要注意以下几点:
1. 清理焊接缺陷处的表面杂质;
2. 预热焊接区域;
3. 选择合适的填充材料,控制焊接温度和速度;
4. 熔合后进行后热处理,减少残余应力。
三、实验步骤
1. 准备铸件、焊接设备和填充材料;
2. 检查铸件焊接缺陷处及周围区域是否清洁,并清除表面杂质;
3. 在铸件焊接缺陷处预热,保证焊接过程中温度均匀;
4. 选定填充材料并进行填充,控制焊接速度和温度;
5. 焊接结束后进行后热处理,减少残余应力;
6. 对修复后的铸件进行质量评估。
四、实验结果
通过对焊接修复后的铸件进行质量评估,发现焊接区域表面平整,无明显的裂纹和气孔。
使用X射线检测也确认焊接质量符合要求。
五、实验结论
铸件焊接修复是一项重要的工作,选择合适的工艺和材料可以减小焊接缺陷的产生。
在焊接修复过程中,需要注意清洁以及预热和后热处理的要求,保证焊接质量符合要求。
铸钢件 焊补 标准
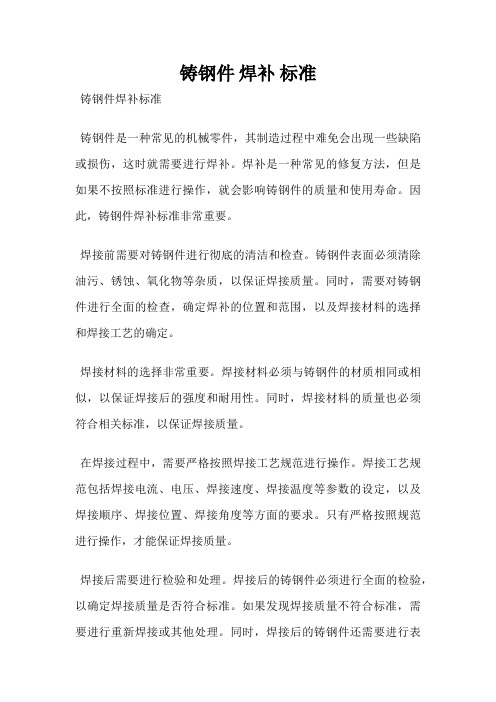
铸钢件焊补标准
铸钢件焊补标准
铸钢件是一种常见的机械零件,其制造过程中难免会出现一些缺陷或损伤,这时就需要进行焊补。
焊补是一种常见的修复方法,但是如果不按照标准进行操作,就会影响铸钢件的质量和使用寿命。
因此,铸钢件焊补标准非常重要。
焊接前需要对铸钢件进行彻底的清洁和检查。
铸钢件表面必须清除油污、锈蚀、氧化物等杂质,以保证焊接质量。
同时,需要对铸钢件进行全面的检查,确定焊补的位置和范围,以及焊接材料的选择和焊接工艺的确定。
焊接材料的选择非常重要。
焊接材料必须与铸钢件的材质相同或相似,以保证焊接后的强度和耐用性。
同时,焊接材料的质量也必须符合相关标准,以保证焊接质量。
在焊接过程中,需要严格按照焊接工艺规范进行操作。
焊接工艺规范包括焊接电流、电压、焊接速度、焊接温度等参数的设定,以及焊接顺序、焊接位置、焊接角度等方面的要求。
只有严格按照规范进行操作,才能保证焊接质量。
焊接后需要进行检验和处理。
焊接后的铸钢件必须进行全面的检验,以确定焊接质量是否符合标准。
如果发现焊接质量不符合标准,需要进行重新焊接或其他处理。
同时,焊接后的铸钢件还需要进行表
面处理,以保证外观和防腐性能。
铸钢件焊补标准是保证焊接质量和使用寿命的重要保障。
只有严格按照标准进行操作,才能保证焊接质量和使用效果。
因此,在进行铸钢件焊补时,必须认真遵守相关标准和规范,以保证焊接质量和安全性。
铸钢件焊补工艺规程

铸钢件焊补工艺规程1.范围本工艺规程规定了起重机采用的铸钢件进行焊补的技术要求。
2.焊前准备铸件焊前准备工作包括:缺陷的清理、焊接坡口的制备、焊前预热、焊接材料的选择,电流强度规范的调整等。
1)焊补前应由专职检查人员检查焊前准备的各道工序和工艺规定的质量要求符合要求后,方可允许进行焊补;2)铸钢件毛坯缺陷焊补前,必须经过退火或正火处理;3)根据焊件不同情况,可采用气割、电弧气刨、砂轮打磨、机械加工等方法清理铸件缺陷和焊接坡口的加工;4)在应力集中处在制备坡口前应先在两端钻孔,防止裂纹延伸,孔径选取φ8~15mm,钻孔深度超出裂纹深度3~4mm;5)焊接坡口加工后,在坡口周边15~30mm范围内用磨光机打磨,去除氧化物及渗碳层,露出原金属光泽;6)在同一平面内的两处缺陷之间的非缺陷部位,若长度小于40mm时,应将两缺陷相距沟通成焊槽。
为了改善应力状态和焊接方便,焊槽的几何形状不应有锐角形状,转角处应圆滑过渡;7)对穿透性裂纹和其它缺陷,需要采用垫板或镶板时,垫板允许用低碳钢代替,而镶板的钢号必须和母材一致;8)根据铸件壁厚和焊接条件确定焊接坡口形式;如表1所示9)一般情况下,按铸件抗拉强度等级选用相应强度等级焊条;10)铸件缺陷周围50mm范围内如有油、锈、粘砂等杂物,焊前要清理干净;11)焊条使用前要烘干。
碱性焊条的烘干温度在250~350℃,保温1~2h。
酸性焊条的烘干温度一般在150~200℃,保温1~2h。
严禁用火焰直接烘烤;12)铸件缺陷清理后,经检查确认缺陷清理质量合格后,方准许进行焊补。
表13.焊补工艺1)一般铸钢件焊补工艺(1)焊补缺陷处理范围按表2,如超出此范围需经总工程师核准后方可焊补;(2)铸件焊补必须在室内进行,并且不准在通风处,在进行焊补时周围温度应保持在5℃以上;(3)碱性焊条低氢型必须采用直流反接法(即工件为负极),焊缝与母材交界处,必须很好的熔合;(4)碱性焊条的焊接不易操作,焊缝容易出现气孔,引弧时应在工艺板上进行,电弧稳定后再进行缺陷的焊补;(5)碱性焊条在焊缝过程中灭弧时,电弧不能拉长,必须压弧后迅速灭弧,弧坑应尽量减小,避免弧坑出现气孔和裂纹。
铸钢件补焊通用工艺
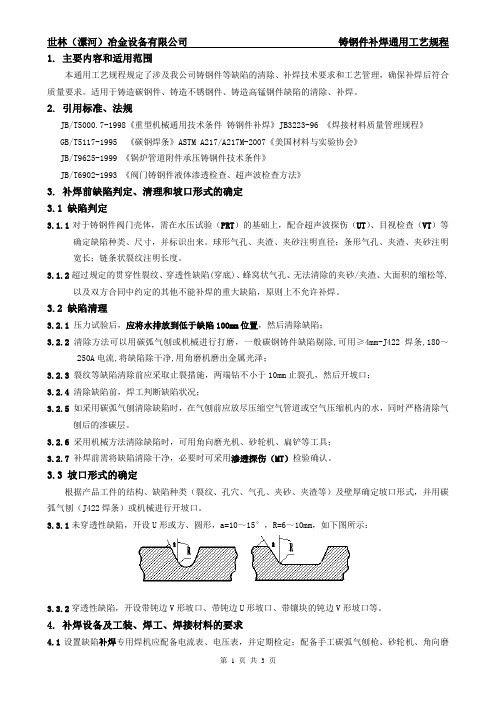
1. 主要内容和适用范围本通用工艺规程规定了涉及我公司铸钢件等缺陷的清除、补焊技术要求和工艺管理,确保补焊后符合质量要求。
适用于铸造碳钢件、铸造不锈钢件、铸造高锰钢件缺陷的清除、补焊。
2. 引用标准、法规JB/T5000.7-1998《重型机械通用技术条件铸钢件补焊》JB3223-96 《焊接材料质量管理规程》GB/T5117-1995 《碳钢焊条》ASTM A217/A217M-2007《美国材料与实验协会》JB/T9625-1999 《锅炉管道附件承压铸钢件技术条件》JB/T6902-1993 《阀门铸钢件液体渗透检查、超声波检查方法》3. 补焊前缺陷判定、清理和坡口形式的确定3.1 缺陷判定3.1.1对于铸钢件阀门壳体,需在水压试验(PRT)的基础上,配合超声波探伤(UT)、目视检查(VT)等确定缺陷种类、尺寸,并标识出来。
球形气孔、夹渣、夹砂注明直径;条形气孔、夹渣、夹砂注明宽长;链条状裂纹注明长度。
3.1.2超过规定的贯穿性裂纹、穿透性缺陷(穿底)、蜂窝状气孔、无法清除的夹砂/夹渣、大面积的缩松等,以及双方合同中约定的其他不能补焊的重大缺陷,原则上不允许补焊。
3.2 缺陷清理3.2.1 压力试验后,应将水排放到低于缺陷100mm位置,然后清除缺陷;3.2.2 清除方法可以用碳弧气刨或机械进行打磨,一般碳钢铸件缺陷剔除,可用≥4mm-J422焊条,180~250A电流,将缺陷除干净,用角磨机磨出金属光泽;3.2.3 裂纹等缺陷清除前应采取止裂措施,两端钻不小于10mm止裂孔,然后开坡口;3.2.4 清除缺陷前,焊工判断缺陷状况;3.2.5 如采用碳弧气刨清除缺陷时,在气刨前应放尽压缩空气管道或空气压缩机内的水,同时严格清除气刨后的渗碳层。
3.2.6 采用机械方法清除缺陷时,可用角向磨光机、砂轮机、扁铲等工具;3.2.7 补焊前需将缺陷清除干净,必要时可采用渗透探伤(MT)检验确认。
3.3 坡口形式的确定根据产品工件的结构、缺陷种类(裂纹、孔穴、气孔、夹砂、夹渣等)及壁厚确定坡口形式,并用碳弧气刨(J422焊条)或机械进行开坡口。
铸件常见缺陷修补及检验

铸件常见缺陷的鉴别、起因、修补及检验----------------------------------------------福联造型,呋喃树脂、酚醛树脂、覆膜砂专家1.缺陷的分类铸件常见缺陷分为孔眼、裂纹、表面缺陷、形状及尺寸和重量不合格、成份及组织和性能不合格五大类。
(注:主要介绍铸钢件容易造成裂纹的缺陷)1.1孔眼类缺陷孔眼类缺陷包括气孔、缩孔、缩松、渣眼、砂眼、铁豆。
1.1.1气孔:别名气眼,气泡、由气体原因造成的孔洞。
铸件气孔的特征是:一般是园形或不规则的孔眼,孔眼内表面光滑,颜色为白色或带一层旧暗色。
(如照片)气孔照片1产生的原因是:来源于气体,炉料潮湿或绣蚀、表面不干净、炉气中水蒸气等气体、炉体及浇包等修后未烘干、型腔内的气体、浇注系统不当,浇铸时卷入气体、铸型或泥芯透气性差等。
1.1.2缩孔缩孔别名缩眼,由收缩造成的孔洞。
缩孔的特征是:形状不规则,孔内粗糙不平、晶粒粗大。
产生的原因是:金属在液体及凝固期间产生收缩引起的,主要有以下几点:铸件结构设计不合理,浇铸系统不适当,冷铁的大小、数量、位置不符实际、铁水化学成份不符合要求,如含磷过高等。
浇注温度过高浇注速度过快等。
1.1.3缩松缩松别名疏松、针孔蜂窝、由收缩耐造成的小而多的孔洞。
缩松的特征是:微小而不连贯的孔,晶粒粗大、各晶粒间存在明显的网状孔眼,水压试验时渗水。
(如照片2)缩松照片2产生的原因同以上缩孔。
1.1.4渣眼渣眼别名夹渣、包渣、脏眼、铁水温度不高、浇注挡渣不当造成。
渣眼的特征是:孔眼形状不规则,不光滑、里面全部或局部充塞着渣。
(如照片3)渣眼照片3产生的原因是:铁水纯净度差、除渣不净、浇注时挡渣不好,浇注系统挡渣作用差、浇注时浇口未充满或断流。
1.1.5砂眼砂眼是夹着砂子的砂眼。
砂眼的特征是:孔眼不规则,孔眼内充塞着型砂或芯砂。
产生的原因是:合箱时型砂损坏脱落,型腔内的散砂或砂块未清除干净、型砂紧实度差、浇注时冲坏型芯、浇注系统设计不当、型芯表面涂料不好等。
- 1、下载文档前请自行甄别文档内容的完整性,平台不提供额外的编辑、内容补充、找答案等附加服务。
- 2、"仅部分预览"的文档,不可在线预览部分如存在完整性等问题,可反馈申请退款(可完整预览的文档不适用该条件!)。
- 3、如文档侵犯您的权益,请联系客服反馈,我们会尽快为您处理(人工客服工作时间:9:00-18:30)。
补焊后的典型 热 处理规范
16 ' ,h-2.h 0 6C l 5
水冷 或空冷
1 5 1 , 0 0v h-2. l 5 h
Z Cr8 9 GI l NiTi
铸态或 固溶
水 冷或空冷
HO l 9 Ni Cr9 A1 2, 3 HTB一2 3 A1 7,
Z C2 Ni0 GI r5 2
4. 陷 后 对 缺 区 重 进 检 直 确 缺 已 底 除 止 .2缺 排除 应 排除 陷 域 新 行 验,至 认 陷 彻 排 为 。 5
453 对于待补焊的部位, .. 缺陷排除后可用丙酮、 汽油等有机溶剂擦拭干净。对距坡口边缘不小于
1mm范 围内的表 面也应进行清理 , 0 除去氧化皮 、 油污及其它污物 。 45 4 铸件清 理后在保证 无污染的条件下 , .. 其存放时间应不超过 4 h 8. 46 补焊用焊 接材料的选择 . 铸件补焊推荐采用与铸件基体材料化学成分 相同或相 近的焊接材料 。在 补焊低合 金钢及 马氏体不
5 . 引弧后, .2 2 焊枪应稍停留一定时间以 预热焊件, 待坡口 熔化形成熔池后再填充焊丝。
52 3 补焊 时应 采用短 弧、 电流 、 速施 焊。焊枪与焊丝之 间的夹角约为 9 0 .. 小 快 0。补焊处厚度不均匀 时 , 焊接热源应偏向厚壁处 。 52 4 补焊过 程中, .. 不允许钨极端头与熔池或焊丝接触。 525 补焊结 束时应采用电流衰减收弧 , .. 填满弧坑 。 53 焊条 电弧焊 .
行。
471 整体预热适用于各类型的铸件。对于材料裂纹倾向 ... 2 性大 或拘束度大的 铸件, 推荐采用整体预
热 。预热保温 时间可根据铸件 壁厚、 大小等确定。 47 13 局部预热可用氧 一乙炔焰进行 , 用中性焰 , .. . 应采 火焰焰芯离铸件表面的距离应 不小于 l O mmo
471 当采用钨极氨弧焊方法补焊时, ... 4 除裂纹 倾向 性大的 材料或拘束度大的铸件需预热外, 般可不 一
HI 6 2 2 Ni1 Cr 八4 2, 0 A4 2 0 A4 7, 1 HGH3 3, (一1 11 HS; 2 0-2 0 0 5 Z C 1 NiW M o GI r 1 2 V HO 2 Ni4Mo Cr0 l 3
H l r 1 iW 2M o C 1N 2 V
10℃ h h 10 , -2 1 空冷
G 94 焊接与切割安全 B 8 4 H 50 结构钢熔模铸件技术标准 B 1 0
H 59 航空工业手工熔焊焊工技术考核 B 9 2
H 56 焊接工艺质量控制 B 3 3 H 53 不锈钢、 B 0 4 耐热钢 熔模铸件
S/ 17 3 惰性气体保 护电弧焊和等离子焊接、 J 04 T 切割用钨柿电极
424 其 它应符合 H156 .. 3 3的规定 。 3
43 材料 .
43 1 焊丝和焊条 .. 铸件补焊用 的焊丝 和焊条应符合相应焊接 材料技术条件 的要求。焊条 型号和牌号 的对照关 系见附 录 A, 焊条新 、 旧牌号对照关系见附录 B o 432 保护气体 ..
钨极氢弧 焊用氢气应符 ( / 44 的规 , 合 : T 2 定 纯度应不低于9.9 B 8 99%.
51 对于材料裂纹倾向睦 .. 4 大或拘束度大的 铸件, 补焊后 应采用石棉将其覆盖Байду номын сангаас放人炉中缓慢冷却。
5 15 对补焊用 的焊丝应清理 干净 。焊条使用前应按相应焊条技术条件规定的烘焙条件烘干 。烘千后 .. 的焊 条应 放在恒温箱或保温筒内 , 随取 。 随用 52 钨极氨弧焊 . 52 1 应采用直 流正接法施 焊。 ..
H日
中华 人 民共和国航 空行业标 准
F 97 L 5 0 HB/ 3 6一 2 0 Z 4 02
熔模铸造钢铸件补焊工艺及检验
Poe ad pc o o rpi w li rcs n iset n ea e n s n i f r d g fr e n csn s t l met t g o s e oi s n t v ai f e
433 钨电极 ..
钨极氢弧 焊用的钨电极可以采用饰钨丝或牡钨丝, 推荐采用饰钨丝 WC 0 e o钵钨丝应符合 ST 2 J /
173 04 的规定。
44 环境条件 .
补焊工作 场地的环境条件应符合H 56 的规定。 B 3 3
45 铸件缺 陷的清理 .
451 按铸件上标出的 .. 缺陷 位置及范围, 根据缺陷 部位的大小、 缺陷的 性质和铸件的 形状, 选择尺寸 合 适的 工具 , 采用机械加工方法排除 缺陷。
20 一1 一2 发布 02 1 0
20 一0 一0 实施 03 2 1
国防科学技术工业委员会 发 布
HB Z 4 / 3 6一2 0 02
前
言
本指导性技术文件根据航空工业 四十多年来的熔模铸造钢铸件 补焊经验 , 并参考美 国宇航 材料规范
A S 4 、 M 29A 法国T R O C 6 U B M A公司规范 C TL59加拿大 P WC公司规范 CW20 E C . 7、 C & P 9 及俄罗斯标 准 I 1 222 P .. 和M I41 1 1 6 . 7 等国外有关航空 . 3 铸件补焊的 技术资料编制而成。 本指导性技术文件的附录A和附录B为 资料性附录。 本指导性技术文件由中国 航空工业第一集团公司提出。
用 手工钨极氢弧焊和焊条电弧焊进行的补焊。 2 规范性 引用文件 下列文 件中的条款通过本指导性技术文件的引用 而成为本指导性技 术文件的条 款。凡是注 日 的 期 引用文件 , 其随后所有 的修改单 ( 不包括勘误的内容) 或修订版均不适用于本指导 性技术文件 , 然而 , 鼓励 根据本指导性技 术文件达成协议的各方 研究 是否可使用这 些文件的最新 版本 。凡是不注 日期的 引用文 件 , 最新版本适用于本指导性技术文件 。 其 G到 44 2 纯氢 1T 8
均匀化处理及 时效
重新 热处理 ( 均匀化处理可不 重 复进行 ) 不热处理
(HJ一3 ) B
淬火 +时效
HO C lNiMo S O r2 9 2 i
47 预 热 .
47 1 概述 ..
4711 铸件的补焊可视铸件材料、 ... 结构、 大小等具体情况在整体预热、 局部预热或不预热的条件下进
范围
本指导性技术文件规定 了对结构钢 、 钢及耐热钢熔模 铸造钢铸件 缺陷补焊的补 焊铸件确定 、 不锈 补 焊前准备 、 补焊 、 补焊后的清理 、 焊后 的热处理 、 补 补焊质量检验、 质量控制及技术安全。
本指导性技术文件适用于航空产品熔模铸造钢铸件铸造缺陷及其在机械加工过程中出现的缺陷采
42 设 备 .
42 1 氢弧焊设备应有自 .. 动引弧、 气体提前和延时供给、 流衰减等装置, 保护 电 能方便地调节焊接工艺
参 数。
t
HB Z 4 / 3 6一2 0 02
42 2 从氢气 瓶到焊枪的管路上应装有气体减压阀和气 体流量计 。 ..
423 补焊工作场地应备有焊条烘干箱、 .. 铸件预热及焊后保温装置。
本指导性技术文件 由中国航空综合技术研究所归 口。
本指导性技术文件由中国 南方航空动 力机械公司、 北京航空 材料研究院 负责起草。 本指导性技术文件主要 起草人: 吴家云、 郝俊明、 刘东升、 杨玲秀。
HB 7 3 6 2 0 /, 一 0 2 4
熔模铸造钢铸件补焊工艺及检验
33 铸件上允许的 . 补焊处数、 最大缺陷的尺寸和补焊区总面积应符合设计图样和铸件专用技术文件的 要求。当 设计图样和铸件专用技术文件未规定时, 铸件补焊部位的补焊区总面积对于不锈钢及耐热钢 铸 件应不大于 铸件表面积的 19, 06对于结构钢铸件应不大于铸件表面积的56 90
34 铸 件缺陷的补焊在机械加工和热处理前后均可进行 。 . 35 应 由检验人员在铸件上准确标 出需要补焊的部位及范围。 . 4 补焊前的准备 4 1 人员 . 从事航空产 品熔模铸造钢铸 件补焊的焊工应持有符合 H3 9 159 规定 的有效焊工技术合格证书 。 2
HB/ 34 Z 6一 2 2 00
表 1续 ) 《
铸件材料牌号
Z Cr9 lNb GO 1NiO Z Cr9 lNb GI lNi2 Z Cr8 9 GO l NiTi
焊前状 态
预热 温度
℃
焊接材料
HO 0NiO C2 lNb 八L A1 7 2, 3 3 HOC2 NiO r0 lTi HO 9 9 l Ni Cr A1 A1 7 2, 3 3 HOC2 NiO rO lTi
丰 焊 铸 件 的 确定 卜
31 应由 . 检验人员按 H 50,B 0 B 1H 53 或铸件专用技术文件的规定确 0 4 定可以补焊的 铸件。 32 铸件上凡不符合铸件相应 . 技术文件要求的缺陷, 除设计图 样和铸件技术文件规定不允许进行补 焊
的部 位外 , 其它便 于进行 补焊和检验 的部位均 允许进行补 焊。允许补焊 的缺陷有 : 缩孔 、 气孔 、 松、 疏 夹 渣、 夹杂 、 欠铸 、 、 冷隔 裂纹及机械损伤等。
531 应根据焊条类型正确选择焊接电源种类和 .. 极性, 碱性焊条推荐采用直流反接法施焊, 酸性焊条推
60 , h 8` 5-8 C h 空冷 重新 热处理
Z Cr3 G1 l
退火或 淬火 十回火
G2 2, 0 0 G2 7 HO lNiCu Nb Cr7 4 4 HO C l 9MoS O r2Ni 2 i
Z Cr6 4 Cu GO l NiNb 3 Z GOC l 5 2 u r4NiMo C
9 0 一 10 1 0℃ 0 0r
ZG2 2 Ni2W3 i Cr3 l S
0s 空冷 , .h
50C 5 - 6 8 ' , h h 空冷