陶瓷摩擦材料摩擦性能影响因素探讨
纤维增强陶瓷摩擦材料研究现状

1 纤维增强陶瓷摩擦材料 的性能
陶 瓷是一种 无 机非 金 属材料 ,陶瓷 材料 一般具 有较 高 的摩擦 系数I 4 J 。陶瓷及 其复合 材料所具 有 的高 熔 点 、 硬度 、 高 良好 的化 学稳 定 性 、 温 机 械性 能 等 高
在长纤维 增 强 陶瓷复 合材 料 的制造 中 ,浆料浸
透法是最合适 的方法。把增强纤维柬或织物等成型
体在 陶瓷浆 料 中浸 渍后 , 行 干 燥 , 进 然后 , 空 气 中 在 烧结 或 进行 热 压 等 处理 , 增 强 纤维 与 基 体进 行 复 使
合化 际应用 , 作为高温
耐磨 结 构 件 具 有 比金 属 基 材 料更 加 广 阔 的 应 用 前 景 。其 中陶瓷纤维 更 是 以其 良好 的抗老化性 能 、 强度
摘 要 纤维 增 强陶 瓷材 料具 有较 高 的摩擦 系数 、 滑动磨 损 性 、 蚀 性 , 高 的抗 抗 抗 较 压 强度 和 较低 的热 膨胀 系数 , 因此在摩 擦 材 料领 域 弓 起 了越 来 越 多 的关 注 和研 究 。 I 本 文对 纤维 增 强陶瓷 摩擦 材料 的研 究进 展进行 了简要 的综述 。
擦材 料行业 的广泛 注 意 。将 陶瓷 材料用 于制 造阻摩 器件 , 利用 其强度 高 、 温性能 好 、 可 高 耐磨损 等优 良性 能 。另外 , 陶瓷 材料 的密 度较 低 , 如果将 陶瓷 材料 制 造 的制动器在 高速列 车上 成功应 用, 可使每个 转 向架
是制动过程中所产生 的磨屑颗粒 ,有很强的致癌作 用 。因此 从 7 O年代 起 , 多 国家 开始 禁止 生产 和使 许 用 石棉纤维 制 品 。之 后 , 金属 摩擦 材料 、 金属 摩擦 半
陶瓷摩擦片单位面积所能承受的压力

陶瓷摩擦片单位面积所能承受的压力陶瓷摩擦片,这玩意儿说起来也许大家不太熟悉,但一提到刹车、摩擦、甚至汽车,这些词大家肯定都听过吧?陶瓷摩擦片呢,说白了就是刹车系统中的一种重要部件。
你知道刹车片吗?它们是摩擦片的一种,作用就是通过摩擦力来减少车速、停车。
可陶瓷摩擦片跟普通的刹车片比,有些不一样。
它的主要优势就是抗压、耐高温、摩擦力稳定,而且用得时间久了,磨损也慢。
说到这里,你可能会有个问题:陶瓷摩擦片到底能承受多大的压力呢?它的“硬核”到底在哪儿?好啦,先从简单的开始吧。
陶瓷摩擦片的工作原理,顾名思义,就是通过摩擦产生阻力来降低速度。
摩擦力跟压力、温度等因素都有关系。
而压力呢,就是指单位面积上所承受的力。
其实你想想,陶瓷摩擦片就是“在狭小空间里承受巨大的压力”,这种压力可不是一般的“大”,如果它不能承受这些压力,那刹车就没用了,车就不能停了!不过,陶瓷摩擦片的材质特性就是能承受非常大的压力,承受的范围一般能达到200 MPa左右,有时候高达300 MPa!如果用简单点的方式理解,这意味着陶瓷摩擦片的每一平方厘米,都能承受大约200到300公斤的压力,相当于你跟我站在一起,也能给这个小小的摩擦片“施加”这么多的重量,简直是牛得不要不要的!说实话,陶瓷摩擦片这么能承受压力,不仅仅是它的“硬”,更是因为它的材料特性。
陶瓷材料本身就有很高的密度和强度,所以在面对来自刹车盘的巨大压力时,它能够稳定地保持自己的形态,而不容易变形或碎裂。
这就好比你平时穿的牛仔裤,不管怎么折腾都不会撕裂,因为它的材质就在那里,经得起折腾。
你要是把陶瓷摩擦片比作“超人”,那么它就是那个能够在高速行驶中,凭一己之力“死死扛住”车速压力的家伙。
不过,压力虽然大,但陶瓷摩擦片也有它的极限。
别觉得陶瓷摩擦片是无敌的哦!它毕竟是摩擦材料,不是钢铁侠。
陶瓷摩擦片能承受的压力并不是无限大的,如果压力超过了它的极限,它就会发生变形、磨损加速,甚至出现裂痕,影响刹车效果。
热处理工艺对金属陶瓷材料的摩擦磨损性能和抗磨损性的调控
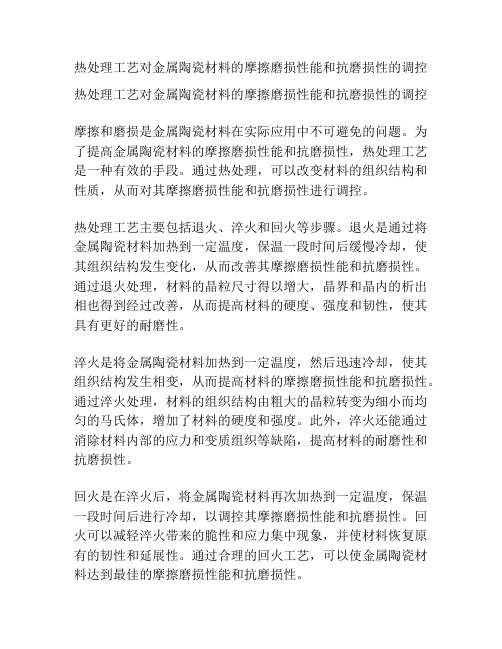
热处理工艺对金属陶瓷材料的摩擦磨损性能和抗磨损性的调控热处理工艺对金属陶瓷材料的摩擦磨损性能和抗磨损性的调控摩擦和磨损是金属陶瓷材料在实际应用中不可避免的问题。
为了提高金属陶瓷材料的摩擦磨损性能和抗磨损性,热处理工艺是一种有效的手段。
通过热处理,可以改变材料的组织结构和性质,从而对其摩擦磨损性能和抗磨损性进行调控。
热处理工艺主要包括退火、淬火和回火等步骤。
退火是通过将金属陶瓷材料加热到一定温度,保温一段时间后缓慢冷却,使其组织结构发生变化,从而改善其摩擦磨损性能和抗磨损性。
通过退火处理,材料的晶粒尺寸得以增大,晶界和晶内的析出相也得到经过改善,从而提高材料的硬度、强度和韧性,使其具有更好的耐磨性。
淬火是将金属陶瓷材料加热到一定温度,然后迅速冷却,使其组织结构发生相变,从而提高材料的摩擦磨损性能和抗磨损性。
通过淬火处理,材料的组织结构由粗大的晶粒转变为细小而均匀的马氏体,增加了材料的硬度和强度。
此外,淬火还能通过消除材料内部的应力和变质组织等缺陷,提高材料的耐磨性和抗磨损性。
回火是在淬火后,将金属陶瓷材料再次加热到一定温度,保温一段时间后进行冷却,以调控其摩擦磨损性能和抗磨损性。
回火可以减轻淬火带来的脆性和应力集中现象,并使材料恢复原有的韧性和延展性。
通过合理的回火工艺,可以使金属陶瓷材料达到最佳的摩擦磨损性能和抗磨损性。
需要注意的是,热处理工艺对金属陶瓷材料的调控需要综合考虑材料的组成、制备工艺和使用环境等因素。
不同的金属陶瓷材料具有不同的组织结构和性质,对热处理工艺的响应也有差异。
因此,在进行热处理之前,需要对材料进行详细的分析和测试,制定相应的热处理工艺。
总之,热处理工艺是调控金属陶瓷材料摩擦磨损性能和抗磨损性的重要手段。
通过退火、淬火、回火等工艺的组合应用,可以调整金属陶瓷材料的组织结构和性质,从而实现对其摩擦磨损性能和抗磨损性的精确调控。
在实际应用中,需要根据具体情况选择合适的热处理工艺,以获得最佳的摩擦磨损性能和抗磨损性。
材料表面涂层对摩擦和磨损的影响机理研究

材料表面涂层对摩擦和磨损的影响机理研究摩擦和磨损是各种机械系统中普遍存在的问题,对材料和设备的性能产生负面影响。
为了解决这一问题,研究人员发现通过在材料表面涂层来改善其摩擦和磨损性能是一种有效的方法。
这种表面涂层技术在工业领域已经被广泛应用,本文将重点探讨材料表面涂层对摩擦和磨损的影响机理。
涂层是通过在材料表面上形成一层覆盖物来提高摩擦和磨损性能的技术。
涂层可以通过物理气相沉积(PVD)、化学气相沉积(CVD)、电沉积、溅射等方法进行制备。
涂层材料的选择主要依据于材料的使用环境和要求,如金属、陶瓷、聚合物等。
首先,涂层可以改变材料表面的摩擦特性。
涂层可以利用其固有的滑动特性,降低材料表面与其他物体之间的接触力,从而减小了摩擦系数。
此外,一些涂层材料还具有自润滑的特性,能够在摩擦过程中释放润滑剂,降低了摩擦系数,并减少了摩擦产生的热量。
其次,涂层可增加材料的硬度和耐磨性。
在表面涂层的过程中,涂层材料与基材之间发生化学反应,使涂层与基材形成牢固的结合。
这样,在摩擦和磨损过程中,由于涂层的硬度高于基材,涂层能够承受更大的载荷,减少了材料表面的磨损。
同时,涂层还能够有效减少摩擦表面的接触面积,从而降低了摩擦表面的磨损。
涂层还可以增加材料的抗腐蚀性能。
在某些工作环境中,材料容易受到氧化、腐蚀等侵蚀。
通过在材料表面形成涂层,可以有效隔绝外界环境对材料的侵蚀,提高材料的抗腐蚀性能。
涂层的抗腐蚀性能主要取决于涂层材料的化学稳定性和结构稳定性。
涂层的厚度和结构对摩擦和磨损性能也有重要影响。
较厚的涂层可以提供更好的保护层,延长材料的使用寿命。
然而,过厚的涂层可能导致表面粗糙度增加,反而影响材料的摩擦和磨损性能。
此外,涂层结构的致密性和均匀性也对摩擦和磨损性能起着关键作用。
较致密的涂层结构可以有效减少材料表面的微孔和缺陷,提高摩擦和磨损性能。
此外,涂层的制备工艺和材料的选择也对摩擦和磨损性能有直接影响。
不同的制备工艺会影响涂层的致密性、晶体结构和表面形貌,从而影响材料的摩擦和磨损性能。
陶瓷材料的结构与性能关系研究

陶瓷材料的结构与性能关系研究1. 引言陶瓷材料是一类重要的结构材料,因其良好的耐热、耐腐蚀性以及高硬度等特性,在各个领域都有广泛的应用。
想要进一步提升陶瓷材料的性能,就需要深入研究其结构与性能之间的关系。
2. 表面形貌与力学性能陶瓷材料的表面形貌对其力学性能有着重要的影响。
通常,表面越光滑,材料的强度和韧性就越高。
光滑的表面能减少材料内部的裂纹和孔洞的存在,从而提高其强度。
同时,表面形貌也会影响材料的磨损和摩擦性能。
研究发现,通过调节陶瓷材料的表面形貌,可以有效地提高其力学性能。
3. 晶体结构与热性能陶瓷材料的晶体结构对其热性能有着重要的影响。
各种陶瓷材料的晶体结构不同,其热膨胀系数和导热系数也会不同。
例如,氧化铝的热膨胀系数较低,具有良好的热稳定性,适用于高温环境。
而氮化硅的导热系数很高,可以作为热散射材料使用。
因此,通过研究陶瓷材料的晶体结构,可以为其在不同温度和热环境下的应用提供参考。
4. 缺陷与导电性能陶瓷材料中的缺陷对其导电性能有着重要的影响。
通常,导电性能较好的陶瓷材料往往具有更多的缺陷,如空位、杂质等。
这些缺陷能够提供导电路径,从而增强材料的导电性能。
例如,氧化锌陶瓷中的氧空位可以提供电子迁移的通道,因此氧化锌陶瓷具有良好的导电性能。
研究陶瓷材料中缺陷与导电性能的关系,可以为设计和制备具有特定导电性能的陶瓷材料提供指导。
5. 成分与光学性能陶瓷材料的成分对其光学性能有着决定性的影响。
不同元素的添加和摩尔比例变化,会对陶瓷材料的吸收、透射和散射等光学性质产生显著影响。
例如,掺杂不同元素的陶瓷材料可以实现对特定波长的光的吸收和发射。
这一特性使得陶瓷材料在光学器件中有广泛应用,如激光器、光纤等。
因此,深入研究陶瓷材料的成分与光学性能的关系,可以为其在光学领域的应用提供理论基础。
6. 结论陶瓷材料的结构与性能之间存在着密切的关系。
不同的结构特点会导致陶瓷材料具有不同的力学性能、热性能、导电性能和光学性能等特性。
TiC/NiCr金属陶瓷复合材料摩擦磨损性能

TiC/NiCr金属陶瓷复合材料摩擦磨损性能本文主要研究TiC/NiCr金属陶瓷复合材料的摩擦磨损性能。
首先介绍了该复合材料的成分及制备方法,并探讨了该材料的物理、力学性能。
然后,通过摩擦试验及磨损测试,对其摩擦磨损性能进行了研究与分析。
一、TiC/NiCr金属陶瓷复合材料的制备方法该复合材料是在NiCr合金基体上通过等离子烧结技术制备而成的。
制备过程分为两个步骤:首先,将TiC陶瓷粉末与NiCr金属粉混合,并通过球磨机混合均匀;其次,将混合物压制成形,并在真空条件下等离子烧结。
最终得到的复合材料具有较高的密度和强度,且陶瓷颗粒分布均匀。
二、TiC/NiCr金属陶瓷复合材料的物理、力学性能该复合材料具有优异的耐磨性、高温抗氧化性、较高的硬度和强度等物理、力学性能。
其中,通过硬度测试可知,该复合材料的硬度约为1900HV,远高于NiCr合金和传统的钢铁材料。
因此,该材料可以应用于高耐磨及高温环境下的机械零件制作。
三、TiC/NiCr金属陶瓷复合材料的摩擦磨损性能本实验采用了环形槽摩擦实验机对该复合材料进行了摩擦试验。
实验结果表明,与NiCr合金相比,该复合材料具有较低的摩擦系数。
在高温状况下,该复合材料的抗磨损性能出现了明显的提高,表现出了良好的耐磨损性。
此外,我们还进一步进行了磨损测试,研究了该复合材料的磨损机理。
实验结果表明,摩擦过程中,在TiC颗粒的作用下,合金基体表面形成了一层坚硬的氧化物保护层,从而减缓了磨损速率。
综合以上实验结果,可以得出结论:TiC/NiCr金属陶瓷复合材料具有较好的耐磨损性,并表现出了优异的高温抗氧化性。
这种复合材料的开发有望解决许多行业在高温及高磨损环境下所遇到的问题,具有广阔的应用前景。
此外,我们还通过扫描电镜(SEM)观察了该复合材料的微观结构。
观察结果表明,陶瓷颗粒与金属基体间形成了良好的结合,陶瓷颗粒分布均匀且呈现出网状结构。
这种结构可以提高材料的耐磨性和热稳定性,减少短时间内的塑性变形。
《2024年Ti3SiC2替代石墨对铜基摩擦材料性能的影响》范文

《Ti3SiC2替代石墨对铜基摩擦材料性能的影响》篇一一、引言随着现代工业的快速发展,铜基摩擦材料在机械、汽车、航空航天等领域的应用越来越广泛。
为了提高铜基摩擦材料的性能,研究者们不断探索新的材料替代品。
其中,Ti3SiC2作为一种新型的陶瓷材料,因其优异的物理和化学性能,被视为石墨的潜在替代品。
本文旨在研究Ti3SiC2替代石墨对铜基摩擦材料性能的影响。
二、Ti3SiC2材料概述Ti3SiC2是一种具有层状结构的陶瓷材料,具有高硬度、高导电性、高热稳定性和良好的化学稳定性等优点。
其独特的物理和化学性质使其在高温、高负载、高速度等恶劣环境下表现出良好的性能。
因此,Ti3SiC2被认为是一种具有潜力的新型材料,可以用于替代传统的石墨材料。
三、实验方法本实验采用Ti3SiC2替代部分石墨,制备铜基摩擦材料。
通过改变Ti3SiC2的含量,制备出一系列不同配比的铜基摩擦材料样品。
然后,对样品进行性能测试,包括硬度、耐磨性、摩擦系数等指标。
最后,对实验结果进行统计分析,以评估Ti3SiC2对铜基摩擦材料性能的影响。
四、实验结果与分析1. 硬度实验结果显示,随着Ti3SiC2含量的增加,铜基摩擦材料的硬度逐渐提高。
这是因为Ti3SiC2具有较高的硬度,其加入使得材料的整体硬度得到提升。
2. 耐磨性Ti3SiC2的加入显著提高了铜基摩擦材料的耐磨性。
与纯石墨铜基摩擦材料相比,添加了一定比例的Ti3SiC2后,材料的耐磨性得到了显著提高。
这主要归因于Ti3SiC2的高硬度和良好的化学稳定性。
3. 摩擦系数在摩擦过程中,Ti3SiC2的加入对铜基摩擦材料的摩擦系数产生了一定影响。
随着Ti3SiC2含量的增加,摩擦系数呈现先降低后升高的趋势。
这可能与材料的表面形貌、接触面积以及润滑性能等因素有关。
五、结论本文通过实验研究了Ti3SiC2替代石墨对铜基摩擦材料性能的影响。
实验结果表明,Ti3SiC2的加入显著提高了铜基摩擦材料的硬度、耐磨性和摩擦性能。
摩擦材料的制备与性能研究

摩擦材料的制备与性能研究摩擦材料是一种特殊的材料,其研制目的是为了在摩擦运动中发挥优异的性能。
因此,摩擦材料的制备和性能研究是摩擦学领域中的重要研究课题。
本文将为大家介绍摩擦材料的制备方法和性能研究进展。
一、摩擦材料的制备方法1.化学制备法化学制备法是一种常见的摩擦材料制备方法。
该方法的核心原理是根据材料成分和性能要求,在溶液中加入一定的化学试剂,通过反应生成特定的化学物质,制备摩擦材料。
例如,针对特定的炭素纤维聚酰亚胺复合材料,化学制备法可以通过调节反应物浓度、反应温度、反应时间等参数,控制反应过程中复合材料表面的化学成分,从而改善材料的摩擦和磨损性能。
2.物理制备法物理制备法是一种常用的摩擦材料制备方法。
该方法的主要原理是利用各种物理手段,如机械磨削、沉积、薄膜制备等技术,来改变摩擦材料的物理特性和形态结构,从而改善材料的摩擦和磨损性能。
例如,利用黑磷纳米片的高比表面积和较低垂直间隙厚度,可通过机械磨削、热处理等物理制备手段,制备出具有优异摩擦特性的黑磷基摩擦材料。
3.纳米材料制备法纳米材料制备法是一种以纳米技术为基础的摩擦材料制备方法。
该方法是利用纳米材料的高比表面积、尺寸效应等特性,来改变材料的的物理、化学、电学等性能,从而提高其摩擦和磨损性能。
例如,将纳米氧化铝粉末加入到聚乙烯树脂中,用溶液制备成复合材料,可制备出优异的摩擦和磨损性能的摩擦材料。
二、摩擦材料的性能研究进展1.摩擦学性能指标研究摩擦学性能指标是指用来评估摩擦材料性能的一组指标。
在实践应用中,摩擦学性能指标是非常重要的,因为它们直接关系到摩擦材料的使用寿命和效率。
目前,研究人员已经发现了一些新的摩擦学性能指标,比如摩擦轨迹形状、摩擦力矩振荡平衡点、摩擦因数稳定性等,这些指标将对摩擦材料的性能研究产生积极意义。
2.摩擦材料表面改性研究摩擦材料表面改性研究是一种常见的摩擦性能研究方法。
与传统的摩擦材料表面改性方法不同,目前研究人员正在开发使用一些新型的表面改性技术,如等离子体改性技术、激光改性技术等,来改善材料的摩擦性能。
- 1、下载文档前请自行甄别文档内容的完整性,平台不提供额外的编辑、内容补充、找答案等附加服务。
- 2、"仅部分预览"的文档,不可在线预览部分如存在完整性等问题,可反馈申请退款(可完整预览的文档不适用该条件!)。
- 3、如文档侵犯您的权益,请联系客服反馈,我们会尽快为您处理(人工客服工作时间:9:00-18:30)。
陶瓷摩擦材料摩擦性能影响因素探讨
摘要:本文探讨了外部因素和纤维对结构陶瓷摩擦磨损的影响,旨在促进在
特定工况下正确使用相应的陶瓷材料作为摩擦学部件。
关键词:陶瓷 摩擦材料 摩擦性能
陶瓷是一种无机非金属材料,陶瓷材料一般具有较高的摩擦系数。陶瓷及其
复合材料所具有的高熔点、高硬度、良好的化学稳定性、高温机械性能等特点,
使其在众多领域中得到了实际应用,作为高温耐磨结构件具有比金属基材料更加
广阔的应用前景。其中陶瓷纤维更是以其良好的抗老化性能、强度和在各种工作
温度下保持稳定的摩擦能力而引起摩擦材料行业的广泛注意。将陶瓷材料用于制
造阻摩器件,可利用其强度高、高温性能好、耐磨损等优良性能。另外,陶瓷材
料的密度较低,如果将陶瓷材料制造的制动器在高速列车上成功应用,可使每个
转向架上制动盘的总重量由1560kg下降到750kg。
1 外部因素对工程陶瓷摩擦学特性的影响
外部因素是指一个完整的摩擦学系统中除了摩擦材料自身特性以外的因素,
主要包括法向载荷、滑动速度、滑行距离、滑行时间、界面介质、环境气氛、温
度、对摩材料、摩擦方式等。
1.1法向载荷的影响
研究者们普遍发现摩擦因数、磨损量随载荷增加而增加,但变化规律不是简
单的线性递增关系,而是在某个载荷下摩擦因数有一明显跃变,磨损率也呈量级
增加,国外的研究者们将之称作磨损突变(Wear Transition)。磨损率的突变对应着
磨损机制的变化,即由塑性变形、犁耕、微切削和微断裂磨损转变为断裂磨损。
研究表明在干摩擦条件下Y-TZP陶瓷材料在法向载荷大于142N时,轻微磨损突
变为严重磨损,磨损机制由塑性变形转变为脆性断裂。同时,滑行速度对磨损行
为有较大影响,在高速(≥1.26m/s)条件下发生了磨损突变。磨损由塑性变形转为
断裂发生。在石蜡油润滑条件下A1203陶瓷在50N(10min)、ZTA复合陶瓷在
320N(150min)时,磨损率发生突变。Kong等采用环一块式摩擦副,研究了自相
配莫来石陶瓷在不同的介质和载荷下的摩擦磨损特性,实验结果表明:莫来石陶
瓷以水为介质时在20N、以机油为介质时在1000N附近存在磨损突变。磨损突
变前主要的磨损机理为塑性变形和犁耕:磨损突变后断裂磨损成为主要的磨损机
理。机油为介质时,磨损率与载荷基本呈线性关系。
1.2滑动速度的影响
有关滑动速度对陶瓷摩擦磨损的影响,已经有不少学者作了这方面的研究。
Esposito等研究表明在低滑行速度时氧化铝含量在79.0%-95.3%范围内的氧化铝
陶瓷的磨损率随着氧化铝含量的降低而升高,但在高滑行速度时,此影响非常小。
磨损率随滑行速度的增加也存在磨损突变的现象。但这种突变与载荷所致磨损突
变有着本质的区别,后者是载荷所致应力超过某一临界值导致陶瓷表面产生裂纹
进而发生断裂引起的,前者是滑行速度过快导致摩擦表面温度过高所致。当速度
达到某一临界值时,会使陶瓷表面产生剧烈的摩擦,因陶瓷的导热性能较差,造
成试件表面温度过高,而导致磨损突变现象。
1.3滑行距离的影响
陶瓷材料的磨损率随滑动距离的变化一般为线性的。不同的材料和不同的操
作参数,这种线性关系的斜率一般不同,在相同的操作参数下,氧化锆陶瓷与氧
化铝陶瓷的磨损率随滑行距离变化的斜率相差较大。有的研究发现在某一滑动距
离后磨损率会突然大幅增大,认为是摩擦过程中缺陷的积累而导致裂纹的生成,
产生断裂磨损的结果。如Farhat等研究表明纳米多晶氧化铝陶瓷材料的磨损体积
随晶粒尺寸的增大和滑行距离的延长而增加,不同晶粒尺寸的陶瓷材料都在滑行
20m后发生了磨损突变,
1.4界面介质
界面介质主要包括有无润滑介质,润滑介质包括无反应润滑介质和有反应润
滑介质两个方面。一般而言,干摩擦比有润滑摩擦有更高的摩擦因数和较高的磨
损率。无反应润滑介质是一些特殊的润滑油,能明显降低系统的摩擦因数和磨损
率。有反应润滑介质是指与对磨材料发生化学反应的润滑介质,研究较多的是水。
由于ZrO2陶瓷在许多应用场合都不可避免要与水或水溶液接触,研究其在水中
的摩擦磨损特性是十分重要的。
2 纤维增强陶瓷摩擦材料的性能
陶瓷是一种无机非金属材料,陶瓷材料一般具有较高的摩擦系数。陶瓷及其
复合材料所具有的高熔点、高硬度、良好的化学稳定性、高温机械性能等特点,
使其在众多领域中得到了实际应用,作为高温耐磨结构件具有比金属基材料更加
广阔的应用前景。其中陶瓷纤维更是以其良好的抗老化性能、强度和在各种工作
温度下保持稳定的摩擦能力而引起摩擦材料行业的广泛注意。将陶瓷材料用于制
造阻摩器件,可利用其强度高、高温性能好、耐磨损等优良性能。另外,陶瓷材
料的密度较低,如果将陶瓷材料制造的制动器在高速列车上成功应用,可使每个
转向架上制动盘的总重量由1560kg下降到750kg。
陶瓷材料早在上世纪60年代开始开发,但是作为结构材料存在容易脆裂的
严重缺点,因而作为结构功能材料的用途有限。纤维增强陶瓷是陶瓷基复合材料
中最有发展前景的。陶瓷基体经纤维或晶须增强后,不仅强度提高,而且韧度增
加,韧性大大上升。如短纤维增强氧化铝和氮化硅的弯曲强度和断裂韧性比来增
强的成倍提高。用长纤维增强陶瓷可大大提高其韧性。扩大其作为耐高温结构材
料的用途。陶瓷复合材料作为耐高温(1200-1600%)的结构材料有巨大的潜在应
用,其相对密度低(仅为钛合金的1/2,镍基超合金的1/31,除了航空航天和
军事工业中的耐高温用途外,还可能在陆地运输、能源和环保等领域获得广泛应
用。
3 总结
往往受到多种因素的同时或交替作用,而各种因素之间又可能是相互转化和
相互制约的,这就更增加了研究工作的难度。因此,只有系统地研究不同的工况
对陶瓷材料摩擦磨损性能的影响。深入地研究陶瓷材料的微观结构对其摩擦磨损
性能的影响,才能正确和经济地选择与设计可在某一相对固定的摩擦磨损环境下
使用的陶瓷材料。