金麒麟摩擦材料发展历程及陶瓷摩擦材料性能 介绍
陶瓷制动摩擦材料的分析及性能探究

陶瓷制动摩擦材料的分析及性能探究汽车产业快速发展,对汽车的制动系统要求越来越高,作为汽车刹车片的摩擦材料要具有良好的热传递性和耐磨损性,同时摩擦系数要适度,而且还要具备优良的隔热性能,本文对摩擦材料的组成和性能进行了分析和探究,得出陶瓷制动摩擦材料热稳定性和热传导率的性能优异,并且还具有良好的硬度大、污染少、安全性、耐磨性、使用寿命长、轻量化等优点。
前言目前,汽车产业、汽车制造环境的快速发展,使汽车制造过程向高速化、安全化、稳定和可靠的方向发展,同时对汽车的制动系统要求越来越高。
由于汽车刹车过程都是靠摩擦产生的,而且都需要一种耐磨的材料铸成的摩擦片,与汽车的旋转部分紧密贴合,致使摩擦力快速增大,让旋转部位快速停止转动,车辆就停止下来,在此过程中伴随着温度的变化和能量的传递,会使局部温度急剧升高,从而影响摩擦性能。
因此,作为汽车刹车片的摩擦材料要具有良好的热传递性和耐磨损性,同时摩擦系数要适度,不能过大或过小,而且还要具备优良的隔热性能[1]。
传统刹车片制动时起主要作用的材料是金属,而陶瓷刹车片起主要作用的是陶瓷,因此具备噪声小的优点。
与此同时,陶瓷刹车片摩擦材料热稳定性和热传导率的性能优异,并且还具有良好的硬度大、污染少、安全性、耐磨性、使用寿命长、轻量化等优点[2]。
一、摩擦材料的组成刹车片作为汽车制动体系中最重要的部位,性能优异的刹车片的,是通过多种摩擦材料的混合压制而成的,每种摩擦材料的含量对刹车片摩擦性能有很大的影响,所以我们应该控制每种摩擦材料的含量,使其刹车性能达到最优化。
其中,长纤维、粘合剂、填料和摩擦改性剂对刹车片的性能影响最大。
刹车片的摩擦材料一般包括三部分,粘合剂、纤维增强材料和填料,每一种材料所起的作用都不同,通过对这三种材料和其他材料的混合、热处理等工艺,在经过一系制作工艺生产出的成品。
1.粘合剂作为刹车片材料中的粘合剂,不只是树脂和橡胶,现在已经展到使用在高温下具有特殊性能的金属粉末或金属硫化物,是为了减少摩擦材料中树脂的含量,填补高温条件下树脂和橡胶的不足,从而改善高温条件下摩擦材料的不足之处,使在性能上更加优化。
摩擦材料的历史以及研究发展方向2

我国摩擦材料的发展方向1、纤维增强材料纤维作为摩擦材料的骨架材料,不但对摩擦片的强度起着至关重要的作用,同时也对摩擦片的性能有着重要的影响。
目前在欧美等发达国家和地区又开始对纤维的结构和理化性能提出了更为严格的要求,而木质纤维、无机晶须(硫酸钡晶须;碳酸钙晶须;钛酸钾晶须等)、矿物纤维、陶瓷纤维、碳纤维、各种有机合成纤维等给我们提供了大量的选择余地,但从成本等综合因素上来看晶体结构和水溶性纤维材料等将是我们未来摩擦材料中的首选纤维。
2、粘合剂粘合剂是我们生产摩擦材料必不可少的材料,人们从最早利用纯酚醛树脂(固态和液态),到后来采用各种橡胶通过多种工艺对酚醛树脂进行改性,发展到今天使用多种无机物或有机物对树脂进行改性。
目前已经不再是单纯的追求摩擦系数和磨损性能的稳定和提高,而是从摩擦片与刹车盘表面的相互作用去分析摩擦材料的工作原理。
所以作为摩擦材料的粘合剂材料,不再仅限于树脂与橡胶,而是已经拓展到了利用金属粉末或金属硫化物在高温下所具有的特殊性能,来减少树脂在摩擦材料中的使用比例,弥补树脂及橡胶在高温条件下的不足,改善高温时在刹车片与刹车盘之间形成的转移膜的结构与性能,进而提高摩擦片的摩擦性能以及其与刹车盘的磨损性能,从而达到提高制动的安全性能、舒适性能和环保性能。
因此说,我们在采用高性能的树脂来提高摩擦材料性能的同时,应更多地关注和利用一些金属粉末或金属硫化物以改善摩擦过程中形成的转移膜的形状与结构,使静态摩擦系数与动态摩擦系数达到相对的平衡,确保刹车片与刹车盘具有良好的磨损性能的同时,达到提高摩擦材料的速度与压力敏感性、消除高温衰退、减少噪音、减少落灰的目的。
3、摩擦性能调节剂摩擦性能调节剂在改善摩擦材料综合性能过程中起着非常关键的作用,过去我们的摩擦材料技术工作者在材料品种的选择上做了大量的研究,并且对其形状和结构也做了相应的探讨,但与世界先进的水平相比还有很大的差距,今后的研究工作不但要在选材上不断扩大应用范围,而且要对每种材料的粒度分布做出明确的规定,并且对其理化性能提出详细的技术参数,同时在配方的研究过程中,对于同一种材料的应用,要根据其形状与粒度的进行多种型号的搭配使用,以确保其优点在摩擦材料中得到充分的发挥。
摩擦材料的历史以及研究发展方向1

摩擦材料的历史以及研究发展方向汽车摩擦材料是汽车制动器、离合器和摩擦传动装置中的关键材料, 它的作用是将汽车运动的动能转化为热能和其他形式的能量, 从而使汽车制动, 它的性能好坏直接关系到汽车系统运行的可靠性和稳定性。
作为汽车零配件之一的摩擦材料, 其发展与汽车工业的发展是紧密相关并且是同步发展的。
1 国外汽车摩擦材料的发展历史从上个世纪70 年代至今的30 多年来, 随着科学技术的发展, 汽车的功率、速度和载荷日益提高,其运行工况条件日益严峻, 同时, 伴随着世界能源危机与人类环境保护意识的增强, 对汽车和汽车零配件提出更高的要求, 促进了包括摩擦材料在内的汽车零配件的快速发展。
对于摩擦材料而言, 要求有足够而稳定的摩擦系数, 动静摩擦系数之差小; 有良好的导热性和一定的高温机械强度; 有良好的耐摩性和抗粘着性, 不易擦伤对偶件, 无噪声; 低成本, 对环境无污染等。
汽车摩擦材料的发展大致经历了以下3 个阶段:①20 世纪70 年代中期以前为第一时期, 在这个时期汽车制动系统多为四轮鼓式, 摩擦材料几乎全为石棉摩擦材料。
由于石棉摩擦材料具有成本低、比重小、不易损伤对偶材料等独特优点, 故获得极为广泛的应用。
②20 世纪70 年代中期至80 年代中期为第二时期, 世界性的能源危机、汽车速度的提高均促使制动系统向盘式制动转化, 这些均要求提高摩擦材料的高温摩擦性能和制动效率, 要求克服因尺寸小而带来的噪声增强和振颤增强等问题, 石棉摩擦材料的性能已逐渐不能适应这些要求, 加上1972 年石棉被国际肿瘤学讨论会确认属于影响人体健康的致癌物质, 石棉摩擦材料更是被各国纷纷排除使用, 从而促使各国研究开发高性能的适应汽车和社会发展要求的摩擦材料, 此后便出现了半金属摩擦材料、烧结摩擦材料、代用纤维增强或聚合物粘结摩擦材料、混杂纤维摩擦材料等无石棉材料, 这些材料以增加金属成分来提高摩擦稳定性和抗粘性、降低制动噪声和振颤现象。
摩擦材料的演变过程
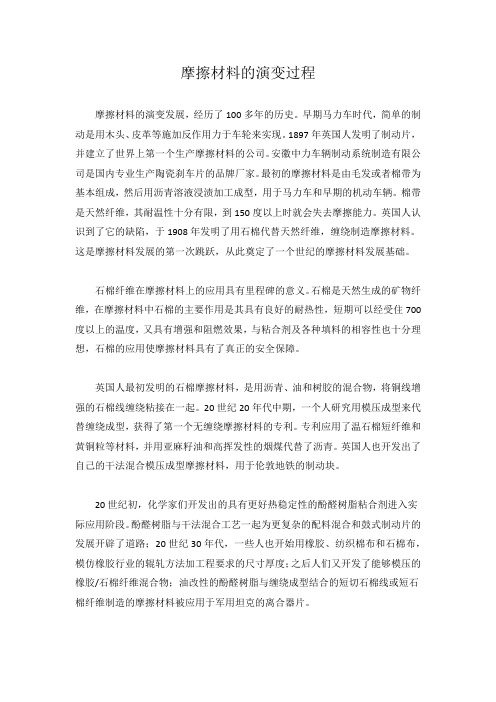
摩擦材料的演变过程摩擦材料的演变发展,经历了100多年的历史。
早期马力车时代,简单的制动是用木头、皮革等施加反作用力于车轮来实现。
1897年英国人发明了制动片,并建立了世界上第一个生产摩擦材料的公司。
安徽中力车辆制动系统制造有限公司是国内专业生产陶瓷刹车片的品牌厂家。
最初的摩擦材料是由毛发或者棉带为基本组成,然后用沥青溶液浸渍加工成型,用于马力车和早期的机动车辆。
棉带是天然纤维,其耐温性十分有限,到150度以上时就会失去摩擦能力。
英国人认识到了它的缺陷,于1908年发明了用石棉代替天然纤维,缠绕制造摩擦材料。
这是摩擦材料发展的第一次跳跃,从此奠定了一个世纪的摩擦材料发展基础。
石棉纤维在摩擦材料上的应用具有里程碑的意义。
石棉是天然生成的矿物纤维,在摩擦材料中石棉的主要作用是其具有良好的耐热性,短期可以经受住700度以上的温度,又具有增强和阻燃效果,与粘合剂及各种填料的相容性也十分理想,石棉的应用使摩擦材料具有了真正的安全保障。
英国人最初发明的石棉摩擦材料,是用沥青、油和树胶的混合物,将铜线增强的石棉线缠绕粘接在一起。
20世纪20年代中期,一个人研究用模压成型来代替缠绕成型,获得了第一个无缠绕摩擦材料的专利。
专利应用了温石棉短纤维和黄铜粒等材料,并用亚麻籽油和高挥发性的烟煤代替了沥青。
英国人也开发出了自己的干法混合模压成型摩擦材料,用于伦敦地铁的制动块。
20世纪初,化学家们开发出的具有更好热稳定性的酚醛树脂粘合剂进入实际应用阶段。
酚醛树脂与干法混合工艺一起为更复杂的配料混合和鼓式制动片的发展开辟了道路;20世纪30年代,一些人也开始用橡胶、纺织棉布和石棉布,模仿橡胶行业的辊轧方法加工程要求的尺寸厚度;之后人们又开发了能够模压的橡胶/石棉纤维混合物;油改性的酚醛树脂与缠绕成型结合的短切石棉线或短石棉纤维制造的摩擦材料被应用于军用坦克的离合器片。
1932年前苏联开始建立石棉制品公司,生产石棉纤维增强的摩擦材料。
刹车片摩擦材料的研究现状与发展趋势

刹车片摩擦材料的研究现状与发展趋势发布时间:2021-07-28T10:37:25.767Z 来源:《基层建设》2021年第13期作者:刘倩[导读] 摘要:作为车辆和机械离合器总成及制动器中的关键性安全部件,高性能刹车片摩擦材料的研究广泛受到各科研机构和主机厂的关注。
山东金麒麟股份有限公司山东省德州市 253600摘要:作为车辆和机械离合器总成及制动器中的关键性安全部件,高性能刹车片摩擦材料的研究广泛受到各科研机构和主机厂的关注。
本文介绍了刹车片摩擦材料的可压缩性、内剪切强度、热膨胀量等主要性能,同时从粘结剂、增强纤维、填料和摩擦性能调节剂等方面概述了主要影响刹车片摩擦材料性能的研究现状,并归纳了正交试验设计与模糊综合评价法、黄金分割法与灰色相关度分析、人工神经网络等摩擦材料配方设计及优化方法的应用情况,进一步探索了刹车片摩擦材料的未来发展趋势,指出摩擦材料各组分之间的耦合机理及对性能影响的研究是未来的热点,多种优化方法的融合将有利于新型刹车片摩擦材料的开发应用.关键词:刹车片;摩擦;研究引言随着汽车技术应用向环保、高速及重载方向的发展,对汽车制动系统的稳定性和可靠性提出了更高要求,而刹车片摩擦材料的综合性能将直接影响到汽车行驶过程中的安全和舒适。
汽车制动的实质是把汽车的大部分的动能通过刹车片和制动盘(或鼓)之间的摩擦转化为热能,大部分的热能又被制动器吸收引起温度升高的过程[1]。
重型汽车由于载重吨位较大和车速的提高,比一般中小型汽车制动时的惯性大、制动距离长。
重型汽车摩擦材料的耐高温性能要好,摩擦系数不宜太高,否则会使制动器温度急剧上升,在刹车片表面产生粘滑的碳化层,导致摩擦系数产生衰退,达不到制动效果,造成车辆打滑、翻转,对行车安全构成严重威胁。
因此,重型汽车的摩擦材料除了具有良好的机械强度、较小的对偶面磨损、无公害、无毒之外,更应有良好的热稳定性,使刹车片在高温下摩擦系数变化小,热磨损小,减小对环境的噪音污染。
山东名牌产品综述

山东金麒麟集团有限公司是我国汽车刹车片制造行业规模最大、出口量最多的外向型、民营、国家级高新技术企业。
2001年,集团正式成立后,在各级政府的正确领导下、在有关部门的大力支持下,集团步入快速发展的轨道,特别是在深入贯彻落实党中央、国务院开展“促进加工贸易转型升级”战略部署以来,刹车片的年产量由50万套增长到3000万套,销量连续十年保持30%以上的增长速度,产品出口到世界80多个国家和地区,在全球同类产品市场占有率达到10%,在国内市场占有率达到30%以上,已成为中国汽车刹车片行业龙头企业,被授予“国家汽车零部件出口基地企业”称号。
2007-2009年,金麒麟集团主导产品产销均同比增长30%以上,是当地第一纳税大户,发展势头良好。
在金融危机时期、后危机时代,金麒麟集团对外贸易均实现逆势而上、增速不减,主要得益于集团紧紧抓住加工贸易转型升级的发展契机,未雨绸缪,打了一场漂亮的转型升级仗。
主要做法是:一、注重品牌培育,发挥名牌效应。
市场的竞争是品牌和企业知名度的竞争。
金麒麟集团尤为注重自主品牌的培育,多年来坚持走自主品牌道路,在各级商务部门的大力支持下,集团上下齐心协力,强化质量管理,提高产品质量,加大宣传力度,“LPB”商标先后荣获“中国名牌产品”、“中国驰名商标”、“山东省重点培育和发展的出口名牌”等一系列荣誉称号。
为进一步提高品牌知名度,集团还在美国、欧盟等28个国家及地区注册了“LPB”商标。
凭借“LPB”品牌,现集团产品已远销到欧洲、美洲、亚洲、非洲等80多个国家和地区,出口量占中国摩擦材料全行业的70%以上,以出口销量和出口创汇第一稳居中国刹车片行业龙头老大的地位。
二、坚持多措并举,拓展国际市场。
不断拓展营销渠道是企业运行之本。
多年来,金麒麟集团坚持不懈地大力开拓境内外市场。
通过新闻、媒体、网络等方式,大力宣传企业,提高产品知名度;参加美国拉斯维加斯、法国巴黎、德国法兰克福、北京、上海、广州等国际和国内大型汽车展览会和汽车零部件展览会,广泛结识客商,积极推介企业产品;积极开展电子商务,充分利用第三方贸易平台--环球资源、阿里巴巴等网站,开拓市场,扩大营销;在境外设立营销网络,开展全球化经营。
半金属与陶瓷对比报告
陶瓷摩擦片与半金属摩擦片性能对比报告半金属摩擦材料是20世纪70年代发展起来的一种新型汽车制动材料。
其配方中通常含有20%~45%左右的铁质金属组分,通过加入这些组分的材料热稳定性好、导热性好、克服了石棉摩擦材料在高温下热衰退严重、摩擦表面易开裂等缺点,目前国内应用最广泛的依然是半金属摩擦材料,但是对于国外还是国内而言,半金属摩擦材料仍然存在着很多缺点,例如,钢纤维易生锈,锈蚀后易粘着对偶并且对其有较大的损伤,使摩擦材料强度降低、磨损加剧,同时钢纤维的硬度高,与对偶的硬度差过大,易损伤对偶,加速对偶磨损。
这种种问题就像“顽疾”一般困扰着诸多厂家,一直得不到有效解决。
为解决半金属摩擦材料的诸多问题,陶瓷刹车片作为新型的配方呈现在人们眼前。
陶瓷刹车片是从金属陶瓷而非非金属陶瓷的原理出发,刹车片由于高速大力制动时,在摩擦表面产生高温。
在此高温下,制动片表面会发生金属陶瓷烧结类似反应,使刹车片在此温度下有良好的稳定性。
而半金属刹车片在此温度下不会产生烧结反应,由于表面温度急剧升高会使表面物质熔化甚至产生气垫,这就有造成连续刹车后刹车性能急剧降低或者刹车全失的情况。
因为钢纤维会锈蚀,产生噪音和粉尘,因此不能满足陶瓷型配方的要求,因此,陶瓷刹车片是由陶瓷纤维、不含铁的填料物质、胶粘剂和少量的金属组成的,包括矿物纤维、芳纶纤维和陶瓷纤维,比其他的刹车片相比,陶瓷型刹车片更清洁安静,并且在提供卓越刹车性能的同时,不磨耗对偶件。
陶瓷刹车片相比其他类型的刹车片有如下的优点:1)陶瓷刹车片与半金属刹车片最大差别是没有金属。
半金属刹车片中金属是主要产生摩擦力的材料,制动力大,但是磨损大,而且易出现噪音。
安装陶瓷刹车片后,在正常行驶中,不会产生异常尖叫。
因为陶瓷刹车片中不含金属成份,所以就避免了类似半金属刹车片与对偶件(即刹车片与刹车盘)相互磨擦的金属尖叫声。
2)稳定的摩擦系数。
摩擦系数是任何摩擦材料最重要的性能指标,关系刹车片制动能力的好坏。
刹车片基本知识汇总
刹车片基本知识刹车片也叫刹车皮。
在汽车的刹车系统中,刹车片是最关键的安全零件,所有刹车效果的好坏都是刹车片起决定性作用,所以说好的刹车片是人和汽车的保护神。
刹车片是指固定在与车轮旋转的制动鼓或制动盘上的摩擦材料,其中的摩擦衬片及摩擦衬块承受外来压力,产生摩擦作用从而达到车辆减速的目的。
组成结构刹车片一般由钢板、粘接隔热层和摩擦块构成,钢板要经过涂装来防锈,涂装过程用SMT-4炉温跟踪仪来检测涂装过程的温度分布来保证质量。
其中隔热层是由不传热的材料组成,目的是隔热。
摩擦块由摩擦材料、粘合剂组成,刹车时被挤压在刹车盘或刹车鼓上产生摩擦,从而达到车辆减速刹车的目的。
由于摩擦作用,摩擦块会逐渐被磨损,一般来讲成本越低的刹车片磨损得越快。
摩擦材料使用完后要及时更换刹车片,否则钢板与刹车盘就会直接接触,最终会丧失刹车效果并损坏刹车盘。
传统制造工艺中,在刹车片上使用的摩擦材料是由多种粘合剂或添加剂组成的混合物,并在其中添入纤维以提高其强度,起加固作用。
刹车片生产厂家在关于使用材料的公布上特别是新配方上往往是守口如瓶的,当然,一些成分配料如:云母、硅石、橡胶碎片等是公开的。
而刹车片制动的最终效果、抗磨损能力、抗温能力及其它性能将取决于不同成分间的相对比例。
刹车片原材料的组成一般分为粘结剂、增强纤维、摩擦性能调节剂、填料四大部份:粘结剂是摩擦材料中的一个最重要的组元,它可以影响材料的热衰退性能、恢复性能、磨损性能和机械性能。
一般有热固性、热塑性、橡胶类、复合型类几种,汽车摩擦材料中一般采用的是热固化型粘结剂,具体应用的有酚醛树脂、三聚氰胺树脂、环氧树脂、硅树脂、聚酰胺树脂等。
应用最广泛的是酚醛树脂及其改性树脂。
改性的目的是改善树脂的高温性能。
为了更大的提高粘结剂的高温性能,现在先进的汽车摩擦材料已经有些采用聚酰亚胺树脂,但目前这种树脂成本太高,普及不容易。
增强纤维是摩擦材料也是主要的摩擦组元起增强基的作用,传统材料用的是石棉等矿物纤维,半金属汽车摩擦材料中使用的是钢纤维,同时加入少量铜纤维及其少量矿物纤维。
陶瓷摩擦材料摩擦性能影响因素探讨
陶瓷摩擦材料摩擦性能影响因素探讨摘要:本文探讨了外部因素和纤维对结构陶瓷摩擦磨损的影响,旨在促进在特定工况下正确使用相应的陶瓷材料作为摩擦学部件。
关键词:陶瓷摩擦材料摩擦性能陶瓷是一种无机非金属材料,陶瓷材料一般具有较高的摩擦系数。
陶瓷及其复合材料所具有的高熔点、高硬度、良好的化学稳定性、高温机械性能等特点,使其在众多领域中得到了实际应用,作为高温耐磨结构件具有比金属基材料更加广阔的应用前景。
其中陶瓷纤维更是以其良好的抗老化性能、强度和在各种工作温度下保持稳定的摩擦能力而引起摩擦材料行业的广泛注意。
将陶瓷材料用于制造阻摩器件,可利用其强度高、高温性能好、耐磨损等优良性能。
另外,陶瓷材料的密度较低,如果将陶瓷材料制造的制动器在高速列车上成功应用,可使每个转向架上制动盘的总重量由1560kg下降到750kg。
1外部因素对工程陶瓷摩擦学特性的影响外部因素是指一个完整的摩擦学系统中除了摩擦材料自身特性以外的因素,主要包括法向载荷、滑动速度、滑行距离、滑行时间、界面介质、环境气氛、温度、对摩材料、摩擦方式等。
1.1法向载荷的影响研究者们普遍发现摩擦因数、磨损量随载荷增加而增加,但变化规律不是简单的线性递增关系,而是在某个载荷下摩擦因数有一明显跃变,磨损率也呈量级增加,国外的研究者们将之称作磨损突变(Wear Transition)。
磨损率的突变对应着磨损机制的变化,即由塑性变形、犁耕、微切削和微断裂磨损转变为断裂磨损。
研究表明在干摩擦条件下Y-TZP陶瓷材料在法向载荷大于142N时,轻微磨损突变为严重磨损,磨损机制由塑性变形转变为脆性断裂。
同时,滑行速度对磨损行为有较大影响,在高速(≥1.26m/s)条件下发生了磨损突变。
磨损由塑性变形转为断裂发生。
在石蜡油润滑条件下A1203陶瓷在50N(10min)、ZTA复合陶瓷在320N(150min)时,磨损率发生突变。
Kong等采用环一块式摩擦副,研究了自相配莫来石陶瓷在不同的介质和载荷下的摩擦磨损特性,实验结果表明:莫来石陶瓷以水为介质时在20N、以机油为介质时在1000N附近存在磨损突变。
刹车片培训资料
• 磨耗:指刹车片在使用过程中的磨损情况。一般汽车前刹车片更换周期在3-5 万公里,后刹车片在8-12万公里;
不伤盘——刹车盘磨损
• 在制动过程中,优质的刹车片会在刹车盘表面形成一层保护膜,能够减少刹 车盘得磨损,从而有效的延长刹车盘的使用寿命;而劣质的刹车片含有大量 的硬点和杂质,会在刹车盘表面拉出许多沟槽,加速刹车片和刹车盘的磨损; 刹车盘的更换周期一般为8-12万公里!
类型 -制动盘损伤 : 因刹车片完全磨损导致 钢背与制动盘磨擦,超 出使用界限 。
措施 -超出更换周期; -不可退货。
制动盘损伤(2)
类型 -制动盘损伤 : 安装前制动盘状态不良
措施 -更换前制动盘加工及 更换。
7. 制动力不足
类型 -制动力达不到 : 1.制动盘和刹车片初期磨合状 态不佳; 2.卡钳异常,导致滑动不畅;
A 少金属摩擦材料
B 陶瓷型摩擦材料
C 混合纤维摩擦材料
D
时间:20世纪90年代末 NAO(少金属)摩擦材料首次出现在欧洲便成为 了一个新的发展趋势,用来取代半金属摩擦材料。
应用:从广义上是指非石棉-非钢纤维型摩擦材 料,偶尔也含有少量的钢纤维,有助于克服半金 属型摩擦材料固有的高比重、易生锈、易产生制 动噪音、伤对偶(盘、鼓)及导热系数过大等缺 陷。。
优点: 1、有陶瓷纤维片的低返工率与舒适性 2、有金属片稳定的制动性能
4、影响刹车片性能的因素
我用的是“软”片,用 起来脚感舒适、制动灵 敏、噪音低。不像你用 的“硬”片噪音大,而
且容易伤盘。
我用的是“硬”片 ,很耐用,不像你 用的“软”片使用 时间还不到我的一 半,太不划算了。
4、影响刹车片性能的因素
- 1、下载文档前请自行甄别文档内容的完整性,平台不提供额外的编辑、内容补充、找答案等附加服务。
- 2、"仅部分预览"的文档,不可在线预览部分如存在完整性等问题,可反馈申请退款(可完整预览的文档不适用该条件!)。
- 3、如文档侵犯您的权益,请联系客服反馈,我们会尽快为您处理(人工客服工作时间:9:00-18:30)。
陶瓷型摩擦材料性能
27
陶瓷型摩擦材料性能
28
噪音试验性能 配方:OEM 车型:荣威前片
29
噪音试验性能 配方:OEM 车型:荣威前片
30
噪音试验性能 配方:TTD-58TTD-58D 车型:荣威前片
32
33
34
35
36
37
总结:
半金属 低金属 陶瓷型
39
2008年 公司增加了重型台架试验机一台 惯量为:3000Kg·m2
40
2009年 公司又引进了美国格林双头试验 可以前后轮同时测试,模拟各类 环境,是目前国内最先进的试验机
41
我们虽然取得了以上这些成果,但要 做到世界最好,还有一定的差距。金麒人 本着一种谦虚、务实的态度,继续努力, 以赶超世界先进为目标。
摩擦系数 0.30~0.40 0.35~0.45 0.45~0.55
寿命
>5万km >3万km >10万km
制动距离 100km/h
<78m
<70m
<60m
热衰退
<40%
<30%
<20%
高温稳定性 <20%
<15%
<10%
噪音指数
9.6
——
9.9
灰尘
良
优
良
38
2005年 公司引进了一台美国LINK3000型 台架试验机,可运行欧洲、美国、 日本标准的试验检验。
23
陶瓷材料刹车片性能特点:
1. 摩擦系数较高,GG级 0.45~0.55 2. 制动距离短,100km/h <60m 3. 耐热性能极好,热衰退率<20% 4. 高速稳定性 <10% 5. 寿命可达10万km以上 6. 几乎无噪音 LACT试验噪音指数为9.9
24
陶瓷型摩擦材料性能
25
陶瓷型摩擦材料性能
21
2003年 购进了第二台克劳斯台架试验机
22
2003年 随着汽车对摩擦材料的要求不 断提 升,高温、 高速、耐磨性、制动力 、刹车感、噪音等这些性能要求更加 严格,我们又在原来半金属和低金属 配方的基础上,自主研发出了代表着 当今世界最先进技术的陶瓷材料。 已于2004年投放市场,并获得认可。
6
半金属型摩擦材料性能
7
半金属型摩擦材料性能
8
半金属型摩擦材料性能
9
半金属型摩擦材料性能
10
半金属型摩擦材料性能
11
1995年 购进了第一台克劳斯台架试验机
12
2001年 公司为更快的拓展欧洲市场,自主研发低金 属刹车片的工艺配方,制造出了公司低金属 材料的刹车片。
13
低金属刹车片性能特点:
1. 摩擦系数较半金属提高到FF级(0.35~0.45之间) 2. 耐热性能好,热衰退率低 <30% 3. 高速性能好,高速稳定性<15% 4. 制动距离短,车速100km/h时,制动距离<70m 5. 寿命3万km以上 6. 噪音低
14
SAEJ2521 其他制造商 帕萨特B5
15
SAEJ2521 其他制造商 帕萨特B5
各位来宾
上午好!
1
山东金麒麟集团有限公司
摩擦材料发展历程和研发成果
2
1991年 山东金麒麟集团有限公司成立,公司决 定从加拿大引进 完整的工艺配 方技术——半金属配方
3
实践证明,这个决策是正确的,它 成就了金麒麟的辉煌大业。当时,也有 很多条路可走,国内也有很多业内的专 家、学者愿意参与金麒麟的建设,但当 时在国内还没有半金属刹车片成熟的工 艺。半金属刹车片代表着当时最先进的 生产工艺。
42
43
4
半金属刹车片性能特点:
1. 制动平稳,摩擦系数稳定(FE级)(0.30~0.40) 2. 寿命长,可达5万km以上 3. 耐热性能好,热衰退率低 <40% 4. 制定距离短,车速100km/h时,制动距离78m 5. 噪音低,LACT试验,噪音指数为9.6 6. 高速稳定性<20%
5
半金属型摩擦材料性能
16
SAEJ2521 其他制造商 帕萨特B5
17
SAEJ2521 LPB M09 帕萨特 B5
18
SAEJ2521 LPB M09 帕萨特 B5
19
SAEJ2521 LPB M09 帕萨特 B5
20
低金属配方的开发,很好的拓展了欧洲 市场,并有约700个型号通过了E-Mark认 证,这使得欧洲市场的份额得到了快速 提升。