熔体静电纺丝的特点与产业化
静电纺丝前景
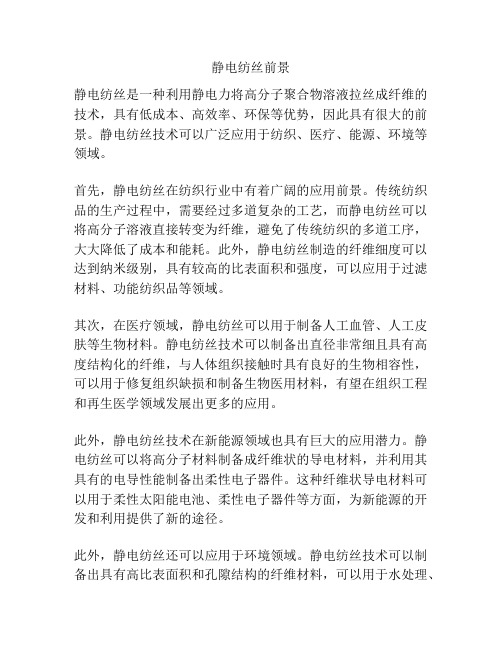
静电纺丝前景静电纺丝是一种利用静电力将高分子聚合物溶液拉丝成纤维的技术,具有低成本、高效率、环保等优势,因此具有很大的前景。
静电纺丝技术可以广泛应用于纺织、医疗、能源、环境等领域。
首先,静电纺丝在纺织行业中有着广阔的应用前景。
传统纺织品的生产过程中,需要经过多道复杂的工艺,而静电纺丝可以将高分子溶液直接转变为纤维,避免了传统纺织的多道工序,大大降低了成本和能耗。
此外,静电纺丝制造的纤维细度可以达到纳米级别,具有较高的比表面积和强度,可以应用于过滤材料、功能纺织品等领域。
其次,在医疗领域,静电纺丝可以用于制备人工血管、人工皮肤等生物材料。
静电纺丝技术可以制备出直径非常细且具有高度结构化的纤维,与人体组织接触时具有良好的生物相容性,可以用于修复组织缺损和制备生物医用材料,有望在组织工程和再生医学领域发展出更多的应用。
此外,静电纺丝技术在新能源领域也具有巨大的应用潜力。
静电纺丝可以将高分子材料制备成纤维状的导电材料,并利用其具有的电导性能制备出柔性电子器件。
这种纤维状导电材料可以用于柔性太阳能电池、柔性电子器件等方面,为新能源的开发和利用提供了新的途径。
此外,静电纺丝还可以应用于环境领域。
静电纺丝技术可以制备出具有高比表面积和孔隙结构的纤维材料,可以用于水处理、空气过滤等领域。
此外,静电纺丝还可以制备出具有光催化性能的纤维材料,用于光催化降解有机污染物,对环境的治理起到积极的作用。
综上所述,静电纺丝技术具有广泛的应用前景。
它在纺织、医疗、能源、环境等领域都有很大的应用潜力,可以为这些领域的发展带来许多新的机遇和挑战。
随着静电纺丝技术的不断创新和改进,相信它将在未来发展出更多的应用,对人们的生活和社会的进步做出更大的贡献。
静电纺丝技术的原理及应用前景

静电纺丝技术的原理及应用前景随着时代的发展,科技的不断进步,纺织工业也不断得到新的提升,其中静电纺丝技术是近年来突破性的技术之一。
静电纺丝是一种新型的材料制备方法,这种方法可以制备出极细的纤维,具有应用前景广阔。
一、静电纺丝技术的原理静电纺丝是指通过高压电场将高分子材料纤维化的一种方法,其原理是利用电场的力量将聚合物液滴从尖端拉伸,喷到距离高压电极的距离处,同时在喷雾丝所在的电场下强制拉伸成纤维形状。
这种方法可以制备出直径从几纳米到几微米的纳米级纤维。
在静电纺丝技术中,原料物质首先通过溶液的形式送入静电纺丝装置中。
将溶液注入静电喷射电极中,当喷出的溶液滴遇到高压静电场时,液滴表面产生了电荷,由于同性相斥,液滴表面会产生一种电势差,从而导致溶液滴的形成变成了锥状,直至其顶端形成了一个纤维化的喷嘴。
当荷电的液滴通过电场的作用被拉伸时,产生了“喷点”对应的“收点”,在喷点到收点之间产生了电张力,从而拉伸液滴,形成如丝质般的超细纤维。
二、静电纺丝技术的应用前景1. 医疗卫生领域静电纺丝技术在医疗卫生领域的广泛应用。
由于其制备的纤维可模拟自然生物纤维的结构,因而制得产品具有很好的生物有效性,可以用作人工血管、人工血小板、人工心脏瓣膜、骨结构支架等等。
也可以制备用于防疫物资、医疗包装、医用敷贴等等。
2. 纺织领域静电纺丝技术在纺织领域是一种绿色技术。
传统的纺织产品采用有机溶剂、洗涤液等,会产生大量的有害气体和废液,造成严重的环境问题,而静电纺丝可以在无需溶剂的情况下将纤维化,不会污染环境,符合绿色可持续发展的理念。
由于其优秀的性能,静电纺丝技术的应用在穿戴、防守装备、运动装备等方面具有广阔的前景。
3. 能源领域静电纺丝技术可以制备高性能的锂离子电池、超级电容器等能源材料。
新型锂电池具有高比能量、长循环寿命、快速充放电等特点,已经成为电动汽车、移动设备等新型电源的首选。
静电纺丝技术可以制备纳米级、微米级的无序三维材料结构,极大提高了锂离子电池和超级电容器电极的电荷传递速率。
静电纺丝技术

静电纺丝技术静电纺丝技术是利用高压静电作用使聚合物溶液或熔体带电并发生形变,在喷头末端处形成悬垂的锥状液滴,当液滴表面静电斥力大于其表面张力时,液滴表面就会喷射出高速飞行的射流,并在较短的时间内经电场力拉伸、溶剂挥发、聚合物固化形成纤维。
所获得的静电纺纤维直径小、比表面积大,同时纤维膜还具有孔径小、孔隙率高、孔道连通性好等优势,在过滤、传感、医疗卫生以及自清洁等领域具有广泛的应用。
1静电纺丝的起源与发展静电纺丝起源于200多年前人们对静电雾化过程的研究。
1745年,Bose通过对毛细管末端的水表面施加高电势,发现其表面将会有微细射流喷出,从而形成高度分散的气溶胶,并得出该现象是由液体表面的机械压力与电场力失衡所引起的。
1882年,Rayleigh指出当带电液滴表面的电荷斥力超过其表面张力时,就会在其表面形成微小的射流,并对该现象进行理论分析总结,得到射流形成的临界条件。
1902年,Cooley与Morton申请了第一个利用电荷对不同挥发性液体进行分散的专利。
随后Zeleny研究了毛细管端口处液体在高压静电作用下的分裂现象,通过观察总结出几种不同的射流形成模型,认为当液滴内压力与外界施加压力相等时,液滴将处于不稳定状态。
基于上述的基础研究,1929年,Hagiwara公开了一种以人造蚕丝胶体溶液为原料,通过高压静电制备人造蚕丝的专利。
1934年,Formhals设计了一种利用静电斥力来生产聚合物纤维的装置并申请了专利,该专利首次详细介绍了聚合物在高压电场作用下形成射流的原因,这被认为是静电纺丝技术制备纤维的开端。
从此,静电纺丝技术成为了一种制备超细纤维的有效可行方法。
1966年,Simons发明了一种生产静电纺纤维的装置,获得了具有不同堆积形态的纤维膜。
20世纪60年代,Taylor在研究电场力诱导液滴分裂的过程中发现,随着电压升高,带电液体会在毛细管末端逐渐形成一个半球形状的悬垂液滴,当液滴表面电荷斥力与聚合物溶液表面张力达到平衡时,带电液滴会变成圆锥形;当电荷斥力超过表面张力时,就会从圆锥形聚合物液滴表面喷射出液体射流。
静电纺丝资料

1.静电纺丝的定义静电纺丝又称“电纺”, 是一种使带电荷的聚合物溶液或熔体在静电场中射流来制备聚合物超细纤维的加工方法。
在电纺丝过程中,喷射装置中装满了充电的聚合物溶液或熔融液。
在外加电场作用下,受表面张力作用而保持在喷嘴处的高分子液滴,在电场诱导下表面聚集电荷, 受到一个与表面张力方向相反的电场力。
当电场逐渐增强时,喷嘴处的液滴由球状被拉长为锥状,形成所谓的“泰勒锥”,而当电场强度增加至一个临界值时,电场力就会克服液体的表面张力,从“泰勒锥”中喷出。
在高速震荡中,喷射流被迅速拉细,溶剂也迅速挥发,最终形成直径在纳米级的纤维,并以随机的方式散落在收集装置上,形成无纺布。
2.静电纺丝的生物材料领域应用可行性由电纺丝纤维制得的无纺布具有孔隙率高、比表面积大、纤维精细程度与均一性高、长径比大等优点, 这些优点使其具备了现实的和潜在的众多应用价值。
由电纺法制备出的无纺布具有良好的生物相容性和结构相容性,可以在生物医学材料中广泛应用。
通过对材料加工过程的调控,可以实现电纺丝材料在结构、形貌、组分和功能上满足生物医用材料的要求。
3.用于组织工程支架制备的纺丝工艺①溶液浇铸成孔剂滤出法。
该法所用的成孔剂含量低,由于采用溶液浇铸于器皿中,从而导致成孔剂下沉,孔隙分布不均匀以及上下表面形态出现诧异。
②三维层化法。
通过制备多孔膜,然后再通过溶剂把各层粘接起来,从而形成三维的支架。
该法工艺复杂,而且在粘接过程中,粘接部分孔被封闭,从而形成界面,使材料内部形态不均匀。
③熔融加工法。
该法在聚合物的熔点以上,把成孔剂与聚合物共混挤人模具。
冷却得到预定形状的多孔支架。
该法的缺点是在挤出机里,由于熔体与成孔剂的密度相差较大,因而混合难以均匀。
而且部分聚合物,尤其是生物可降解的聚合物在熔融加工时,容易热降解。
④相分离法。
该法采用溶液混合物冷却到溶剂的熔点以下,从而产生相分离。
再通过真空干燥,从而得到多孔支架。
该法的缺点是所得的孔径一般在10μm 以下,而且控制较为困难。
静电纺丝的原理及应用

静电纺丝的原理及应用静电纺丝就是高分子流体静电雾化的特殊形式,此时雾化分裂出的物质不是微小液滴,而是聚合物微小射流,可以运行相当长的距离,最终固化成纤维。
静电纺丝是一种特殊的纤维制造工艺,聚合物溶液或熔体在强电场中进行喷射纺丝。
在电场作用下,针头处的液滴会由球形变为圆锥形(即“泰勒锥”),并从圆锥尖端延展得到纤维细丝。
这种方式可以生产出纳米级直径的聚合物细丝。
原理将聚合物溶液或熔体带上几千至上万伏高压静电,带电的聚合物液滴在电场力的作用下在毛细管的Taylor锥顶点被加速。
当电场力足够大时,聚合物液滴克服表面张力形成喷射细流。
在细流喷射过程中溶剂蒸发或固化,最终落在接收装置上,形成类似非织造布状的纤维毡。
装置静电纺丝的装置主要由推进泵、注射器、高压电源以及接收装置组成。
其中,高压电源的正极与负极分别与注射器针头和接收装置相连,而接收装置的形式也是多样化的,可以是静止的平面、高速转动的滚筒或者圆盘。
纺丝的参数设置、环境条件等对纺丝过程的影响至关重要。
影响因素静电纺丝法制备纳米纤维的影响因素很多,这些因素可分为溶液性质,如黏度、弹性、电导率和表面张力;控制变量,如毛细管中的静电压、毛细管口的电势和毛细管口与收集器之间的距离;环境参数,如溶液温度、纺丝环境中的空气湿度和温度、气流速度等。
溶液黏度对纤维性能的影响同轴静电纺丝同轴静电纺是在静电纺的基础上改造而来,其基本原理是在两个内径不同但同轴的毛细管中分别注入芯质和壳质溶液,二者在喷头末端汇合,在电场力的作用下固化成为复合纳米纤维。
同轴静电纺丝解决了纺丝时纺丝液必须是均一体系的缺陷,所制备的同轴纤维在均匀性、连续性上都优于其它方法得到的纤维。
采用同轴静电纺丝的方法可以制得中空纤维和纳米复合纤维等。
应用静电纺丝技术制备的纳米纤维,具有比表面积大、孔隙率高、尺寸容易控制、表面易功能化(如表面涂覆、表面改性)等特点,在许多领域都有重要的应用价值。
静电纺丝技术在构筑一维纳米结构材料领域已发挥了非常重要的作用,应用静电纺丝技术已经成功的制备出了结构多样的纳米纤维材料。
静电纺丝纳米纤维的工艺原理、现状及应用前景
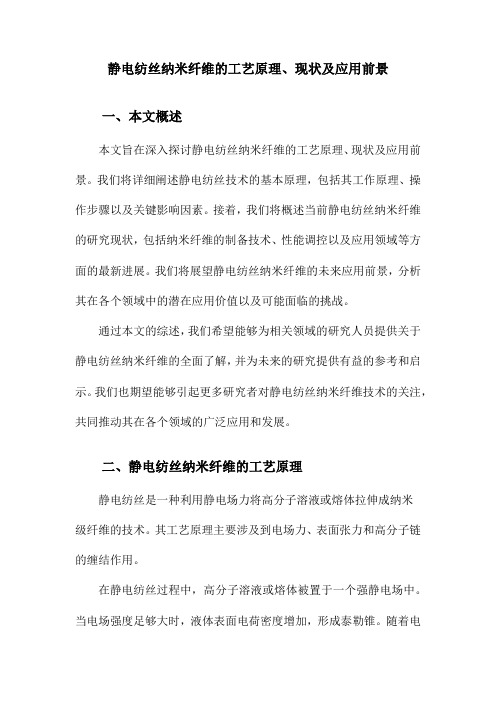
静电纺丝纳米纤维的工艺原理、现状及应用前景一、本文概述本文旨在深入探讨静电纺丝纳米纤维的工艺原理、现状及应用前景。
我们将详细阐述静电纺丝技术的基本原理,包括其工作原理、操作步骤以及关键影响因素。
接着,我们将概述当前静电纺丝纳米纤维的研究现状,包括纳米纤维的制备技术、性能调控以及应用领域等方面的最新进展。
我们将展望静电纺丝纳米纤维的未来应用前景,分析其在各个领域中的潜在应用价值以及可能面临的挑战。
通过本文的综述,我们希望能够为相关领域的研究人员提供关于静电纺丝纳米纤维的全面了解,并为未来的研究提供有益的参考和启示。
我们也期望能够引起更多研究者对静电纺丝纳米纤维技术的关注,共同推动其在各个领域的广泛应用和发展。
二、静电纺丝纳米纤维的工艺原理静电纺丝是一种利用静电场力将高分子溶液或熔体拉伸成纳米级纤维的技术。
其工艺原理主要涉及到电场力、表面张力和高分子链的缠结作用。
在静电纺丝过程中,高分子溶液或熔体被置于一个强静电场中。
当电场强度足够大时,液体表面电荷密度增加,形成泰勒锥。
随着电荷的不断积累,电场力克服表面张力,使得泰勒锥的尖端形成射流。
射流在电场力的作用下被迅速拉伸,同时溶剂挥发或熔体冷却固化,最终形成纳米级纤维。
在这个过程中,高分子链的缠结作用也起到了关键作用。
高分子链之间的缠结使得纤维在拉伸过程中保持一定的结构稳定性,防止纤维断裂。
缠结作用还有助于纤维在接收装置上的沉积和收集。
静电纺丝技术具有操作简便、纤维直径可控、可制备多种材料等优点,因此在纳米材料制备、生物医用、环境保护等领域具有广泛的应用前景。
通过深入研究静电纺丝纳米纤维的工艺原理,可以进一步优化纺丝过程,提高纤维的性能和产量,为相关领域的科技进步做出贡献。
三、静电纺丝纳米纤维的现状静电纺丝技术自其诞生以来,在纳米纤维制备领域已经取得了显著的进展,并逐渐发展成为一种高效、可控的纳米纤维生产方法。
目前,静电纺丝纳米纤维的研究与应用已经涉及到了众多领域,如环境保护、生物医疗、能源科技、纺织工程等。
静电纺丝技术在纺织产业中的应用
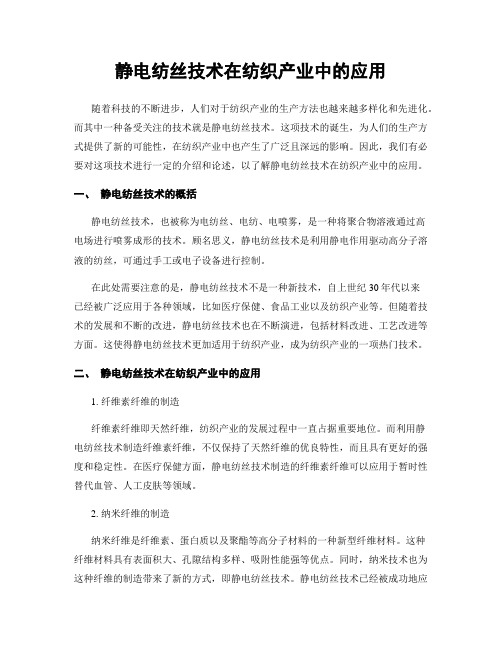
静电纺丝技术在纺织产业中的应用随着科技的不断进步,人们对于纺织产业的生产方法也越来越多样化和先进化。
而其中一种备受关注的技术就是静电纺丝技术。
这项技术的诞生,为人们的生产方式提供了新的可能性,在纺织产业中也产生了广泛且深远的影响。
因此,我们有必要对这项技术进行一定的介绍和论述,以了解静电纺丝技术在纺织产业中的应用。
一、静电纺丝技术的概括静电纺丝技术,也被称为电纺丝、电纺、电喷雾,是一种将聚合物溶液通过高电场进行喷雾成形的技术。
顾名思义,静电纺丝技术是利用静电作用驱动高分子溶液的纺丝,可通过手工或电子设备进行控制。
在此处需要注意的是,静电纺丝技术不是一种新技术,自上世纪30年代以来已经被广泛应用于各种领域,比如医疗保健、食品工业以及纺织产业等。
但随着技术的发展和不断的改进,静电纺丝技术也在不断演进,包括材料改进、工艺改进等方面。
这使得静电纺丝技术更加适用于纺织产业,成为纺织产业的一项热门技术。
二、静电纺丝技术在纺织产业中的应用1. 纤维素纤维的制造纤维素纤维即天然纤维,纺织产业的发展过程中一直占据重要地位。
而利用静电纺丝技术制造纤维素纤维,不仅保持了天然纤维的优良特性,而且具有更好的强度和稳定性。
在医疗保健方面,静电纺丝技术制造的纤维素纤维可以应用于暂时性替代血管、人工皮肤等领域。
2. 纳米纤维的制造纳米纤维是纤维素、蛋白质以及聚酯等高分子材料的一种新型纤维材料。
这种纤维材料具有表面积大、孔隙结构多样、吸附性能强等优点。
同时,纳米技术也为这种纤维的制造带来了新的方式,即静电纺丝技术。
静电纺丝技术已经被成功地应用于制造纳米纤维口罩、过滤材料以及无菌医疗器具等,并且在该领域中已经取得了重要进展。
3. 复合纤维的制造静电纺丝技术还可以用于制造不同种类的纤维复合材料,比如碳纤维、玻璃纤维等。
这种材料相比于传统材料具有更好的力学性能和耐热性能。
正因为如此,在航天、汽车和建筑等领域中得到了广泛应用。
4. 纤维袋的制造纤维袋是指用纤维材料制成的袋子,具有良好的透气性、吸湿性以及防湿性。
静电纺丝的原理及应用

静电纺丝的原理及应用静电纺丝就是高分子流体静电雾化的特殊形式,此时雾化分裂出的物质不是微小液滴,而是聚合物微小射流,可以运行相当长的距离,最终固化成纤维。
静电纺丝是一种特殊的纤维制造工艺,聚合物溶液或熔体在强电场中进行喷射纺丝。
在电场作用下,针头处的液滴会由球形变为圆锥形(即“泰勒锥”),并从圆锥尖端延展得到纤维细丝。
这种方式可以生产出纳米级直径的聚合物细丝。
原理将聚合物溶液或熔体带上几千至上万伏高压静电,带电的聚合物液滴在电场力的作用下在毛细管的Taylor锥顶点被加速。
当电场力足够大时,聚合物液滴克服表面张力形成喷射细流。
在细流喷射过程中溶剂蒸发或固化,最终落在接收装置上,形成类似非织造布状的纤维毡。
装置静电纺丝的装置主要由推进泵、注射器、高压电源以及接收装置组成。
其中,高压电源的正极与负极分别与注射器针头和接收装置相连,而接收装置的形式也是多样化的,可以是静止的平面、高速转动的滚筒或者圆盘。
纺丝的参数设置、环境条件等对纺丝过程的影响至关重要。
影响因素静电纺丝法制备纳米纤维的影响因素很多,这些因素可分为溶液性质,如黏度、弹性、电导率和表面张力;控制变量,如毛细管中的静电压、毛细管口的电势和毛细管口与收集器之间的距离;环境参数,如溶液温度、纺丝环境中的空气湿度和温度、气流速度等。
溶液黏度对纤维性能的影响同轴静电纺丝同轴静电纺是在静电纺的基础上改造而来,其基本原理是在两个内径不同但同轴的毛细管中分别注入芯质和壳质溶液,二者在喷头末端汇合,在电场力的作用下固化成为复合纳米纤维。
同轴静电纺丝解决了纺丝时纺丝液必须是均一体系的缺陷,所制备的同轴纤维在均匀性、连续性上都优于其它方法得到的纤维。
采用同轴静电纺丝的方法可以制得中空纤维和纳米复合纤维等。
应用静电纺丝技术制备的纳米纤维,具有比表面积大、孔隙率高、尺寸容易控制、表面易功能化(如表面涂覆、表面改性)等特点,在许多领域都有重要的应用价值。
静电纺丝技术在构筑一维纳米结构材料领域已发挥了非常重要的作用,应用静电纺丝技术已经成功的制备出了结构多样的纳米纤维材料。
- 1、下载文档前请自行甄别文档内容的完整性,平台不提供额外的编辑、内容补充、找答案等附加服务。
- 2、"仅部分预览"的文档,不可在线预览部分如存在完整性等问题,可反馈申请退款(可完整预览的文档不适用该条件!)。
- 3、如文档侵犯您的权益,请联系客服反馈,我们会尽快为您处理(人工客服工作时间:9:00-18:30)。
编者按——静电纺丝技术主要分为溶液静电纺和熔体静电纺。
近年来溶液静电纺发展迅速,可制备得到纳米纤维,但是目前存在生产效率较低,溶剂回收或排放污染等问题。
相比而言,熔体静电纺技术在某种上可弥补溶液静电纺的不足,因此熔体静电纺也成为新热点。
本专栏邀请了北京化工大学的博士生导师,也是国内近年来研究熔体静电纺丝较成功的研究者之一、并且已取得一定研究成果的刘勇老师,对熔体静电纺丝的特点以及发展状况进行介绍。
同时,我们也希望做到各位老师与学者的桥梁,让大家都能够对静电纺丝领域的发展有更全面、直观的了解,方便研究与探讨。
熔体静电纺丝的特点与工业化刘勇1,杨卫民1,胡平21北京化工大学机电工程学院,北京,1000292清华大学化工系高分子所,北京,100084静电纺丝(简称电纺)分为溶液电纺和熔体电纺两类。
其中溶液电纺因为设备简单、溶液配制容易、方便添加多种成分、室温下即可纺丝等众多优点而受到广泛关注。
目前大多数的电纺研究都是利用溶液电纺进行的。
熔体电纺诞生较晚,关注和使用该法的人也相对较少,这主要是因为1.熔体电纺设备包含加热及控制装置,比溶液电纺设备复杂;2.熔体粘度比溶液的大很多,实现电纺所要求的电压要高很多,容易产生空气放电(击穿)现象;3.熔体电纺所要求的温度不仅高于聚合物的熔点,而且一般比普通加工温度还要高,容易使高分子原料产生热降解;4.熔体电纺所得纳米纤维的直径一般比溶液电纺的要高一个数量级。
但熔体电纺不需要溶剂,比溶液电纺环境友好、成本低、效率高,越来越受到国际科学界的重视,国内也有越来越多的科学家开始关注和研究熔体电纺。
虽然溶液电纺和熔体电纺这两种纺丝方式的基本原理是一样的,但下落过程中纤维的形成有明显区别:溶液电纺纤维是靠大量溶剂蒸发,剩下的溶质固化形成的;熔体电纺纤维是靠热量散失,高分子逐渐冷凝固化形成的。
因此这两种纺丝过程中纤维超分子结构(又称聚集态结构,是指大分子在空间的位置和排列的规整性,比如结晶和取向)的变化规律、环境因素对纤维运动规律的影响、纤维中高分子链的运动规律等都应该有明显不同。
熔体电纺与已经工业化的熔喷纺丝从原理上说也有些相似。
熔喷纺丝是采用高速热空气流对模头喷丝孔挤出的聚合物熔体细流进行牵伸,由此形成超细纤维的一种纺丝工艺,如图1所示。
熔体电纺与熔喷纺丝都是对高分子熔体进行拉伸,直接形成纤维,不需要使用有机溶剂。
二者的区别首先是牵伸力的不同,一个是电场力,一个是热空气的拉力;其次是纤维直径的不同,熔喷纤维的直径一般在几十微米以上,少数纤维的直径在10微米以下,熔体电纺纤维的直径多在10微米以下,少数能达一二百纳米;还有纤维的长度不同,熔喷纤维受热空气波动的影响一般比较短,而电纺纤维则是连续的,理论上是无限长;另外纤维直径分布也不同,熔喷纤维的直径分布很宽,而电纺纤维的则比较窄;生产过程的能耗也差别明显,熔喷纺丝由于需要使用高温高压空气,且不是循环利用,导致生产过程耗能巨大,而熔体电纺虽然使用高达万伏的电压,但生产过程电流非常小,整套生产过程非常节能。
目前溶液电纺国外已有工业化生产设备在销售,但销量很小,原因在于溶液电纺过程中大量有机溶剂的挥发很容易产生环境污染,而当前对挥发后的有机溶剂进行回收的技术尚不成熟;另外这种生产方式的成本因昂贵溶剂的使用而太高,严重阻碍了其大规模应用。
熔喷纺丝在我国已有大大小小上百家的生产厂家,生产线有近千条,2009年生产超细纤维3万多吨,但现在的熔喷技术发展到了瓶颈时期,一方面是因为该技术的原理决定了它不太可能生产出纳米级纤维,另一方面是大量高压热空气的使用很难使成本再降低了。
熔体电纺的工业化因为研究基础薄弱而进展缓慢,尚未见到国内外有正式工业化生产的报道。
目前作者所在研究组进行了多方面的工业化尝试,不仅成功设计制作了大型纺丝组件(64个伞形喷头),在螺杆直径45mm,长径比25:1的双螺杆挤出机上成功进行了熔体静电纺丝工业化初步实验,还利用专利技术一种一字架型纺丝喷头制作了幅宽300mm长1200mm的纤维毡。
[1]刘勇;郝明凤;丁玉梅;杨卫民;王德禧.一种新型一字架静电纺丝喷头[P].中国专利:CN101871130A,2010-10-27.[2]刘勇;王欣;丁玉梅;杨卫民.一种喇叭状高效静电纺丝喷头[P].中国专利:CN101985777A,2011-03-16.[3]刘勇;王建强;丁玉梅.一种静电纺丝的环境温度控制装置[P].中国专利:CN102268746A,2011-12-07.[4]刘勇;邓荣坚;杨卫民;丁玉梅.一种熔体静电纺丝生产复合纤维的装置[P].中国专利:CN101812734A,2010-08-25.[5]Yong Liu,Xin Wang,Hua Yan,Changfeng Guan,Weimin Yang,Dissipative Particle Dynamics Simulation on the Fiber Dropping Process of Melt Electrospinning,J Mater Sci(2011) 46(24):7877–7882[6]Yong Liu,Rongjian Deng,Mingfeng Hao,Hua Yan,Weimin Yang,Orthogonal design study on factors effecting on fibers diameter of melt electrospinning,Polymer Engineering and Science,2010,50 (10),2074-2078.[7]Fengwen Zhao,Yong Liu,Huilin Yuan,Weimin Yang,Orthogonal design study on factors affecting the degradation of polylactic acid fibers of melt electrospinning,Journal of Applied Polymer Science,Vol.125,2652–2658(2012).作者:刘勇,博士,北京化工大学副研究员,博士生导师。
关于溶液静电纺丝和熔融静电纺丝被引频次较多的文章1.Huang,Z.M.;Zhang,Y.Z.;Kotaki,M.;Ramakrishna,S.,A review on polymer nanofibers by electrospinning and their applications in posites Science and Technology2003, 63(15),2223-2253.2.Reneker,D.H.;Chun,I.,Nanometre diameter fibres of polymer,produced by electrospinning. Nanotechnology1996,7(3),216-223.3.Doshi,J.;Reneker,D.H.,Electrospinning Process And Applications Of Electrospun Fibers.Journal of Electrostatics1995,35(2-3),151-160.4.Reneker,D.H.;Yarin,A.L.;Fong,H.;Koombhongse,S.,Bending instability of electrically charged liquid jets of polymer solutions in electrospinning.Journal of Applied Physics2000,87(9),4531-4547.5.Deitzel,J.M.;Kleinmeyer,J.;Harris,D.;Tan,N.C.B.,The effect of processing variables on the morphology of electrospun nanofibers and textiles.Polymer2001,42(1),261-272.6.Lyons,J.;Li,C.;Ko,F.,Melt-electrospinning part I:processing parameters and geometric properties.Polymer2004,45(22),7597-7603.7.Zhou,H.;Green,T.B.;Joo,Y.L.,The thermal effects on electrospinning of polylactic acid melts.Polymer2006,47(21),7497-7505.8.McCann,J.T.;Marquez,M.;Xia,Y.,Melt coaxial electrospinning:A versatile method for the encapsulation of solid materials and fabrication of phase change nanofibers.Nano Lett.2006,6(12), 2868-2872.9.Lee,S.;Obendorf,S.K.,Developing protective textile materials as barriers to liquid penetration using melt-electrospinning.J.Appl.Polym.Sci.2006,102(4),3430-3437.10.Ogata,N.;Yamaguchi,S.;Shimada,N.;Lu,G.;Iwata,T.;Nakane,K.;Ogihara,T.,Poly(lactide) nanofibers produced by a melt-electrospinning system with a laser melting device.J.Appl.Polym.Sci. 2007,104(3),1640-1645.来源:静电纺丝行业期刊。