熔体静电纺丝发展及应用
熔体静电纺丝技术

熔体静电纺丝技术
熔体静电纺丝技术是一种新型的纳米材料制备技术,它通过将高分子
材料或金属材料加热至熔化状态,然后通过高压电场使其在空气中形
成纳米级的纤维。
这种技术具有制备纳米级材料的高效性、低成本和
易于控制等优点,因此在材料科学、生物医学、纺织工业等领域得到
了广泛的应用。
熔体静电纺丝技术的原理是利用高压电场将熔化的高分子材料或金属
材料从喷嘴中喷出,然后在空气中形成纳米级的纤维。
这种技术的关
键在于高压电场的控制,它可以调节纤维的直径、形态和排列方式等
参数,从而得到不同性质的纳米材料。
熔体静电纺丝技术的应用非常广泛,其中最重要的是在材料科学领域。
通过这种技术制备的纳米材料具有很高的比表面积和特殊的物理、化
学性质,可以用于制备高性能的传感器、催化剂、电池等材料。
此外,熔体静电纺丝技术还可以制备纳米级的药物载体,用于生物医学领域
的药物传递和组织工程等方面。
在纺织工业领域,熔体静电纺丝技术也有着广泛的应用。
通过这种技
术制备的纳米纤维可以用于制备高性能的纺织品,如防护服、过滤材料、医用敷料等。
此外,熔体静电纺丝技术还可以制备具有特殊功能
的纺织品,如防辐射、防静电、防紫外线等。
总的来说,熔体静电纺丝技术是一种非常有前途的纳米材料制备技术,它具有高效、低成本、易于控制等优点,可以用于制备各种高性能的
材料。
随着技术的不断发展,相信熔体静电纺丝技术将会在更多的领
域得到应用。
静电纺丝技术

静电纺丝技术静电纺丝技术是利用高压静电作用使聚合物溶液或熔体带电并发生形变,在喷头末端处形成悬垂的锥状液滴,当液滴表面静电斥力大于其表面张力时,液滴表面就会喷射出高速飞行的射流,并在较短的时间内经电场力拉伸、溶剂挥发、聚合物固化形成纤维。
所获得的静电纺纤维直径小、比表面积大,同时纤维膜还具有孔径小、孔隙率高、孔道连通性好等优势,在过滤、传感、医疗卫生以及自清洁等领域具有广泛的应用。
1静电纺丝的起源与发展静电纺丝起源于200多年前人们对静电雾化过程的研究。
1745年,Bose通过对毛细管末端的水表面施加高电势,发现其表面将会有微细射流喷出,从而形成高度分散的气溶胶,并得出该现象是由液体表面的机械压力与电场力失衡所引起的。
1882年,Rayleigh指出当带电液滴表面的电荷斥力超过其表面张力时,就会在其表面形成微小的射流,并对该现象进行理论分析总结,得到射流形成的临界条件。
1902年,Cooley与Morton申请了第一个利用电荷对不同挥发性液体进行分散的专利。
随后Zeleny研究了毛细管端口处液体在高压静电作用下的分裂现象,通过观察总结出几种不同的射流形成模型,认为当液滴内压力与外界施加压力相等时,液滴将处于不稳定状态。
基于上述的基础研究,1929年,Hagiwara公开了一种以人造蚕丝胶体溶液为原料,通过高压静电制备人造蚕丝的专利。
1934年,Formhals设计了一种利用静电斥力来生产聚合物纤维的装置并申请了专利,该专利首次详细介绍了聚合物在高压电场作用下形成射流的原因,这被认为是静电纺丝技术制备纤维的开端。
从此,静电纺丝技术成为了一种制备超细纤维的有效可行方法。
1966年,Simons发明了一种生产静电纺纤维的装置,获得了具有不同堆积形态的纤维膜。
20世纪60年代,Taylor在研究电场力诱导液滴分裂的过程中发现,随着电压升高,带电液体会在毛细管末端逐渐形成一个半球形状的悬垂液滴,当液滴表面电荷斥力与聚合物溶液表面张力达到平衡时,带电液滴会变成圆锥形;当电荷斥力超过表面张力时,就会从圆锥形聚合物液滴表面喷射出液体射流。
静电纺丝技术及其应用前景

静电纺丝技术及其应用前景静电纺丝技术是一种快速、简单和低成本的纺织工艺,在纺织、医疗、能源、环境等领域有着广阔的应用前景。
它利用高压电场作用于高分子溶液或熔体,使其成线状或膜状,并在收集器上固化,从而制备出纳米、亚微米级别的纳米纤维或纳米膜。
本文将从静电纺丝技术的原理、优势、应用等方面进行论述,阐明其应用前景。
静电纺丝技术的原理静电纺丝技术是一种利用高压电场将高分子聚合物或其它材料成线状或膜状的制备技术,其主要原理是在高压电场作用下,高分子溶液或熔体中的电荷在电场作用下向电场强度方向移动,引起流体分子的动态变化,形成电荷密集层,并在电场强度足够大的情况下形成喷雾,最终固化在收集器上。
静电纺丝技术的优势静电纺丝技术具有一系列显著的优点:①制备简单、成本低,纺织过程几乎不需要化学剂及其它附加助剂,避免了传统纺织过程中可能存在的有害物质;②可制备纳米级纤维和纳米膜,表面积大,比表面积高,活性和反应性大,应用前景广阔;③可以制备无纺布、药物缓释材料、3D 及仿生材料等多种功能性材料;④制备过程快速、高效,操作简便快速,纺丝过程可以在常温下完成,不需要耗费过高能量。
静电纺丝技术的应用前景静电纺丝技术在新材料领域的应用前景十分广阔,下面列举几个典型应用场景:1. 纳米纤维材料静电纺丝技术制备的纳米纤维材料具有独特的微观结构和物理化学性质,具有非常广泛的应用前景。
如生物医药领域中使用纳米纤维制备的药物缓释材料、伤口敷料、封膜材料、组织工程支架材料等;在环境污染治理方面使用纳米纤维材料制备的过滤材料、防护材料等等。
2. 功能性膜材料静电纺丝技术的另一个典型应用是制备膜材料。
静电纺丝技术可以制备出超滤、气体分离、催化反应、压电、光学等多种性能的功能膜材料,应用广泛。
3. 纳米复合材料利用静电纺丝技术可以将不同材料的纳米粒子制备成复合材料,增强材料的力学性能,例如制备的纳米复合材料可以用于高性能增强材料、透明导电膜、光电材料以及石墨烯增强材料等领域。
静电纺丝纳米材料的制备与应用研究

静电纺丝纳米材料的制备与应用研究静电纺丝技术是一种简单、有效的制备纳米材料的方法,对于制备催化剂、传感器、纳米纤维等材料具有广泛的应用前景。
本文将从静电纺丝纳米材料的制备原理、结构特征和应用研究三个方面进行介绍。
一、制备原理静电纺丝技术的原理是利用高电压电场将高分子溶液或熔体喷射出来,使其在空气中快速成纤维状,然后在收集器上自行沉积成膜。
熔体静电纺丝与溶液静电纺丝相比,熔体速度更快,材料结晶程度高,适合制备颗粒尺寸更小的纳米材料。
而溶液静电纺丝则可以选择不同的溶剂和不同的高分子材料来制备纳米纤维,制备颗粒尺寸也更加灵活。
二、结构特征静电纺丝制备的材料具有很高的比表面积和特殊的纳米结构,因此在催化剂、分离膜、传感器等领域具有广泛的应用前景。
静电纺丝纳米材料的纤维尺寸从几纳米到几微米不等,表面可以加上各种功能组团,如金属纳米颗粒、分子印迹、寡聚体等。
因此,静电纺丝制备的材料可以具备更优异的催化性能、选择性、稳定性和灵敏度。
此外,纳米材料的静电纺丝制备过程是在常温环境下进行,避免了高温条件下材料结晶、生长不均匀的问题。
三、应用研究静电纺丝制备的纳米材料应用领域广泛。
在催化领域,静电纺丝制备的纳米催化剂具有极高的比表面积、可调控性以及可控制催化活性和选择性等优异性能,适用于制备氧化剂、还原剂、过氧化物分解催化剂等等。
例如,通过控制静电纺丝溶液的pH值和静电纺丝参数,制备出核壳结构的纳米催化剂,在催化还原二氧化碳制备甲烷中表现出较高的产甲烷率和稳定性。
在传感器领域,基于静电纺丝制备的纳米纤维磁性材料、荧光材料和结构化合陶瓷材料等都有广泛探索。
例如,应用静电纺丝技术制备的纳米剪切流传感器,可以实现对于单细胞排列、细胞膜的二维分类,为了解生物芯片研究中面对的甚至是生命科学探索中的难点问题提供了新的技术思路。
在纺织领域,静电纺丝制备的材料可以应用于制备高强度、高效能的纳米纤维布,也可以用于生物医用维生素E。
此外,静电纺丝技术还被用于电子元件制备和生物医学领域。
静电纺丝技术在医疗材料中的应用现状
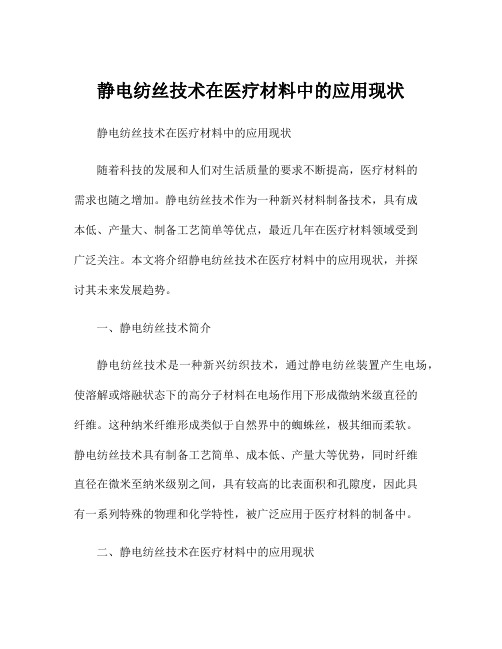
静电纺丝技术在医疗材料中的应用现状静电纺丝技术在医疗材料中的应用现状随着科技的发展和人们对生活质量的要求不断提高,医疗材料的需求也随之增加。
静电纺丝技术作为一种新兴材料制备技术,具有成本低、产量大、制备工艺简单等优点,最近几年在医疗材料领域受到广泛关注。
本文将介绍静电纺丝技术在医疗材料中的应用现状,并探讨其未来发展趋势。
一、静电纺丝技术简介静电纺丝技术是一种新兴纺织技术,通过静电纺丝装置产生电场,使溶解或熔融状态下的高分子材料在电场作用下形成微纳米级直径的纤维。
这种纳米纤维形成类似于自然界中的蜘蛛丝,极其细而柔软。
静电纺丝技术具有制备工艺简单、成本低、产量大等优势,同时纤维直径在微米至纳米级别之间,具有较高的比表面积和孔隙度,因此具有一系列特殊的物理和化学特性,被广泛应用于医疗材料的制备中。
二、静电纺丝技术在医疗材料中的应用现状1、纳米纤维支架的制备静电纺丝技术制备的纳米纤维支架具有高孔隙度,表面积大,软、柔性好等优点,因此被广泛应用于组织工程,如血管、心脏、神经等的修复和再生。
同时,纳米纤维支架具有超强吸附性和生物相容性,可以增强组织修复过程中的细胞黏附和迁移,促进组织修复。
2、药物释放材料的制备静电纺丝技术制备的纳米纤维具有极高的比表面积和孔隙度,可以加速药物在纳米纤维内的扩散和释放。
同时,纳米纤维具有良好的生物相容性和可控性,可以控制药物释放速率和药物储存时间,逐渐释放药物,实现长期治疗效果。
因此,静电纺丝技术制备的药物释放材料被广泛应用于外科手术、植入物领域等生物医学领域。
3、口腔医疗材料的制备静电纺丝技术制备的纳米纤维具有极细的直径和良好的生物相容性,可以保持口腔的清洁和舒适,具有良好的吸附性,可以吸附口腔中的细菌、食物残渣等杂质。
静电纺丝技术制备的口腔医疗材料涉及口腔用纱布、漱口水等产品,已经成为口腔医学领域中的重要研究课题之一。
三、静电纺丝技术在医疗材料领域的未来发展趋势静电纺丝技术作为一种新兴的医疗材料制备技术,具有广阔的发展前景。
静电纺丝的原理及应用

静电纺丝的原理及应用静电纺丝就是高分子流体静电雾化的特殊形式,此时雾化分裂出的物质不是微小液滴,而是聚合物微小射流,可以运行相当长的距离,最终固化成纤维。
静电纺丝是一种特殊的纤维制造工艺,聚合物溶液或熔体在强电场中进行喷射纺丝。
在电场作用下,针头处的液滴会由球形变为圆锥形(即“泰勒锥”),并从圆锥尖端延展得到纤维细丝。
这种方式可以生产出纳米级直径的聚合物细丝。
原理将聚合物溶液或熔体带上几千至上万伏高压静电,带电的聚合物液滴在电场力的作用下在毛细管的Taylor锥顶点被加速。
当电场力足够大时,聚合物液滴克服表面张力形成喷射细流。
在细流喷射过程中溶剂蒸发或固化,最终落在接收装置上,形成类似非织造布状的纤维毡。
装置静电纺丝的装置主要由推进泵、注射器、高压电源以及接收装置组成。
其中,高压电源的正极与负极分别与注射器针头和接收装置相连,而接收装置的形式也是多样化的,可以是静止的平面、高速转动的滚筒或者圆盘。
纺丝的参数设置、环境条件等对纺丝过程的影响至关重要。
影响因素静电纺丝法制备纳米纤维的影响因素很多,这些因素可分为溶液性质,如黏度、弹性、电导率和表面张力;控制变量,如毛细管中的静电压、毛细管口的电势和毛细管口与收集器之间的距离;环境参数,如溶液温度、纺丝环境中的空气湿度和温度、气流速度等。
溶液黏度对纤维性能的影响同轴静电纺丝同轴静电纺是在静电纺的基础上改造而来,其基本原理是在两个内径不同但同轴的毛细管中分别注入芯质和壳质溶液,二者在喷头末端汇合,在电场力的作用下固化成为复合纳米纤维。
同轴静电纺丝解决了纺丝时纺丝液必须是均一体系的缺陷,所制备的同轴纤维在均匀性、连续性上都优于其它方法得到的纤维。
采用同轴静电纺丝的方法可以制得中空纤维和纳米复合纤维等。
应用静电纺丝技术制备的纳米纤维,具有比表面积大、孔隙率高、尺寸容易控制、表面易功能化(如表面涂覆、表面改性)等特点,在许多领域都有重要的应用价值。
静电纺丝技术在构筑一维纳米结构材料领域已发挥了非常重要的作用,应用静电纺丝技术已经成功的制备出了结构多样的纳米纤维材料。
静电纺丝的发展及应用
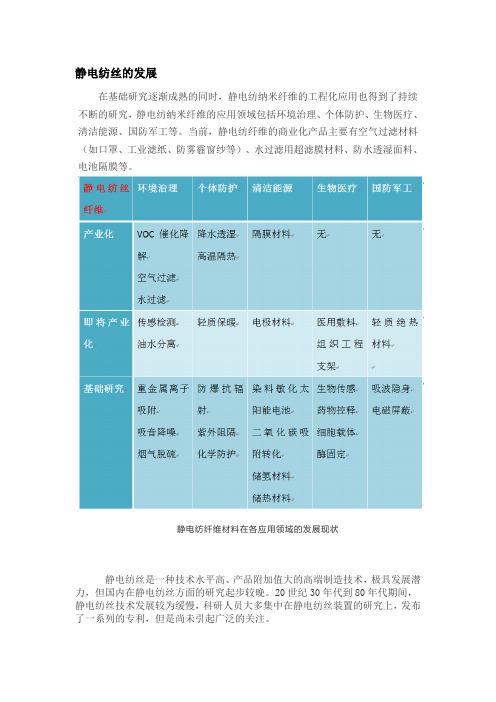
静电纺丝的发展在基础研究逐渐成熟的同时,静电纺纳米纤维的工程化应用也得到了持续不断的研究,静电纺纳米纤维的应用领域包括环境治理、个体防护、生物医疗、清洁能源、国防军工等。
当前,静电纺纤维的商业化产品主要有空气过滤材料(如口罩、工业滤纸、防雾霾窗纱等)、水过滤用超滤膜材料、防水透湿面料、电池隔膜等。
静电纺纤维材料在各应用领域的发展现状静电纺丝是一种技术水平高、产品附加值大的高端制造技术,极具发展潜力,但国内在静电纺丝方面的研究起步较晚。
20世纪30年代到80年代期间,静电纺丝技术发展较为缓慢,科研人员大多集中在静电纺丝装置的研究上,发布了一系列的专利,但是尚未引起广泛的关注。
进入90年代,美国阿克隆大学Reneker研究小组,对静电纺丝工艺和应用展开了深入和广泛的研究。
特别是近年来,随着纳米技术的发展,静电纺丝技术获得了快速发展,世界各国的科研界和工业界,都对此技术表现出了极大的兴趣。
此段时期,静电纺丝技术的发展大致经历了四个阶段:第一阶段主要研究不同聚合物的可纺性,和纺丝过程中工艺参数对纤维直径,及性能的影响以及工艺参数的优化等;第二阶段主要研究静电纺纳米纤维成分的多样化,及结构的精细调控;第三个阶段主要研究静电纺纤维在能源、环境、生物医学、光电等领域的应用;第四阶段主要研究静电纺纤维的批量化制造问题。
静电纺丝并以其制造装置简单、纺丝成本低廉、可纺物质种类繁多、工艺可控等优点,已成为有效制备纳米纤维材料的主要途径之一。
目前,与静电纺丝相关的科研院所及企业已覆盖全国32个省、市、区。
国外高技术企业如德国Freudenberg、美国Donaldson、日本Fuence等公司均拥有制备商业化静电纺纤维产品的核心技术。
而我国在静电纺纤维产品开发方面存在企业规模小、零散度大、自主研发能力弱等问题,导致相关产品主要依赖进口。
而聚纳达(青岛)科技有限公司则是一家以静电纺丝技术为主的中外合资企业,系英国皇家工程院院士西拉姆Seeram Ramakrishna与国内顶尖静电纺丝技术团队共同创办的高新技术企业。
静电纺丝技术的发展与应用
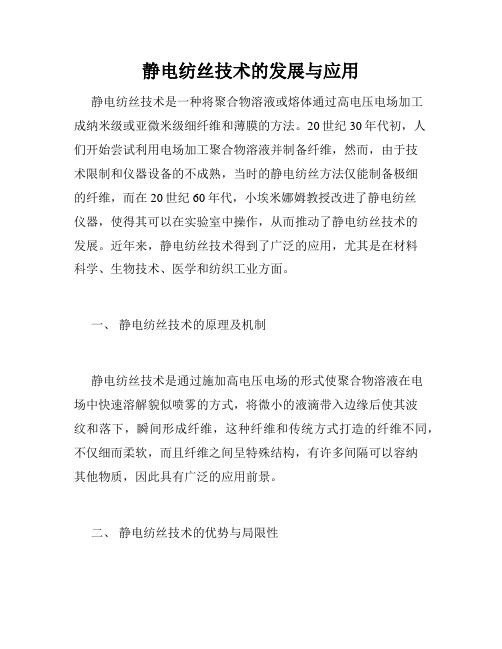
静电纺丝技术的发展与应用静电纺丝技术是一种将聚合物溶液或熔体通过高电压电场加工成纳米级或亚微米级细纤维和薄膜的方法。
20世纪30年代初,人们开始尝试利用电场加工聚合物溶液并制备纤维,然而,由于技术限制和仪器设备的不成熟,当时的静电纺丝方法仅能制备极细的纤维,而在20世纪60年代,小埃米娜姆教授改进了静电纺丝仪器,使得其可以在实验室中操作,从而推动了静电纺丝技术的发展。
近年来,静电纺丝技术得到了广泛的应用,尤其是在材料科学、生物技术、医学和纺织工业方面。
一、静电纺丝技术的原理及机制静电纺丝技术是通过施加高电压电场的形式使聚合物溶液在电场中快速溶解貌似喷雾的方式,将微小的液滴带入边缘后使其波纹和落下,瞬间形成纤维,这种纤维和传统方式打造的纤维不同,不仅细而柔软,而且纤维之间呈特殊结构,有许多间隔可以容纳其他物质,因此具有广泛的应用前景。
二、静电纺丝技术的优势与局限性相对于传统的制备方法,静电纺丝技术有着一系列的优势。
首先,静电纺丝能够制备出极细的细纤维,其尺寸可达到亚微米级,而一般化学合成方法难以制备细度小于几微米以下的材料。
其次,静电纺丝过程中,聚合物的分子结构和溶剂的化学性质均可以自由调控,从而可以设计出满足不同需求的纤维材料。
此外,静电纺丝还能够制备出独特的纤维结构和形态,如中空纤维、粗糙表面纤维、多孔纤维、核-壳结构纤维等。
然而,静电纺丝技术也存在一些局限性。
首先,纤维直径对静电纺丝过程的稳定性和产量有很大的影响。
当聚合物液滴的尺寸较小时,静电纺丝的稳定性会降低,且纤维产量也会减少。
其次,静电纺丝过程中,容易发生聚集和交联,造成纤维有缺陷或不能形成,降低产量和质量。
三、静电纺丝的应用(一)材料科学领域静电纺丝技术在材料科学领域中有广泛的应用。
可应用于制备纳米级材料,如纳米电子材料,纳米复合材料,纳米多孔陶瓷材料等。
在制备过程中可以自由控制各项制备条件,如聚合物的种类,溶剂质量分数,电场强度,注射速度等,在控制粒子尺寸、形貌、组分、晶形、表面性质等方面具有显著优势。
- 1、下载文档前请自行甄别文档内容的完整性,平台不提供额外的编辑、内容补充、找答案等附加服务。
- 2、"仅部分预览"的文档,不可在线预览部分如存在完整性等问题,可反馈申请退款(可完整预览的文档不适用该条件!)。
- 3、如文档侵犯您的权益,请联系客服反馈,我们会尽快为您处理(人工客服工作时间:9:00-18:30)。
熔体静电纺丝发展及应用徐阳,王肖娜,黄锋林,魏取福﹒江南大学生态纺织教育部重点实验室摘要:静电纺丝法是制备纳米纤维的一种有效方法,得到了广泛的关注和研究。
而作为其分支之一的熔体静电纺丝是近年来才逐渐有研究报道的。
虽然其装置较为复杂,纺丝过程不易调控,但其原料适用性广、无毒无污染及产品转化率高等特点,使其在过滤防护、生物医药等领域有着广阔的应用前景。
本文在总结熔体电纺典型装置、工艺及聚合物的基础上,分析了熔体射流的运动规律,探讨了熔体电纺纤维的应用,并对其发展方向进行了预测和展望。
关键词:熔体电纺;装置;聚合物;纤维物化性质;应用引言静电纺丝是指聚合物溶液或熔体在高压电场中拉伸成纤的过程。
自1902年Cooley在其申请的专利[1]中阐明溶液的静电纺丝技术以来,已经100多年了,其间备受关注,研究广泛。
而熔体电纺虽然在1936年Charles Norton等的专利中就已提出[2],但直到1981年才有相关的研究论文出现。
Larrondo和Manley发表的三篇系列论文中的第一篇以聚丙烯(PP)和聚乙烯(PE)为原料,探究了熔体电纺的可能性,对比了溶液电纺和熔体电纺的临界电压,并对射流成丝过程进行了摄像记录[3]。
此后对熔体电纺的研究依然是持续的空白。
21世纪初,才真正掀起了熔体电纺的研究高潮。
熔体电纺过程无毒无污染,克服了溶液电纺中溶剂残留和聚集的问题,可以弥补溶液电纺在某些对卫生、安全要求较高的领域如组织工程的应用缺陷。
可能是受近年来生物工程研究热潮的推动,国内外学者都对熔体电纺展开了逐渐深入的研究。
从2005年到2012年的研究论文达60余篇,并陆续有专利的申请。
熔体电纺装置熔体电纺的装置目前均由各个研究机构自行搭建,尚无公认的成熟设备。
其必要的组成部分是加热部件、给料部件、高压电源及接收部件。
熔体电纺装置采取的加热方式主要有激光加热、电加热、流体加热、热风加热。
电加热是最普遍的加热方式,笔者所在实验室搭建的熔体电纺装置采用的就是电加热的方式,如图1所示,使用电热圈加热,利用传感器和温控仪对熔体温度实现实时有效调控。
实验中分别采用滚筒、平板作为接收装置得到的聚丙烯纤维膜的形态及其SEM 图如图1所示。
对应不同的加热方式给料部件的结构有所不同。
激光电纺装置采用棒状或片状聚合物喂料;非激光加热的装置,大多采用单孔喷丝头,控制熔体流速的方法多样,但只有一部分是可以对给料速度进行定量控制的。
熔体电纺的接收装置也趋于多样化,除了最常见的滚筒和平板以外,还有转盘、镊子状接收器、细胞培养皿等等[4-7]。
值得注意的是,聚合物从熔融到形成射流并最终沉积到接收装置上的整个过程,都受到温度的重要影响。
如果可以通过控制射流路径上的温度进而控制射流的冷却速度,将会对纤维直径和形貌的调控产生至关重要的影响。
图2为笔者实验室在提高射流路径周围空间温度的情况下得到的聚乳酸(PLA)和聚己内酯(PCL)纤维,可以看到,纤维与纤维之间产生了粘结,说明射流在沉积到接收板上的时候还没有完全冷却,这些粘结对纤维膜的形状稳定性及强力都有益处[7-9]另外,熔体电纺中也出现了无针头的实验装置[10]及同轴熔体电纺装置[11-13]。
今后熔体电纺装置的发展趋势,除了进一步的集成化与多样化以外,也会更加注重对环境因素,如温湿度、空气流动的控制;为了提高产率,必将向多喷头或者无喷头方向发展。
纺丝聚合物及工艺过程理论上,只要分解温度大于熔点的聚合物均可进行熔体电纺。
目前通过熔体电纺实现纺丝的聚合物接近20种,尝试最多的是常规的熔体纺纤维如PP和聚酯(PET),因具有生物相容性和可降解性而有望应用于生物医学的PLA,用于同轴熔体电纺以实现封装的相变材料等。
同时,也有一部分研究者采用了共混聚合物或嵌段共聚物来探究混纺的特点。
聚合物性质和纺丝过程中的工艺参数共同决定了聚合物纤维的物化性质。
影响聚合物静电纺丝能力的两个最重要的性质是其粘弹性和电导性[14]。
一旦这两个性质受到影响,必然会影响到纤维的物化性质。
当熔体受力被拉伸时,必须有足够的粘度来与这个拉伸力相平衡才不会使射流断裂;但若粘度过大,则不利于熔体在电场中被牵伸变细。
熔体温度是调控粘度的一个重要参数;另一种有效的方法是在聚合物中混入可降低其粘度的添加剂[15-16],使实验在较低温度下顺利进行。
在增强聚合物导电性方面,Nayak等[17]在PP中加入油酸钠/氯化钠,测试证明聚合物的导电性增强,得到纤维的平均直径比纯PP纺丝的小,且直径分布变窄。
优化工艺参数是减小熔体电纺纤维直径的有效途径之一。
不同的装置和纺丝方法的主要工艺参数及其可调节范围存在着较大的差别。
首先,静电压的加压方式不同,临界电压及电压范围有很大区别:电压正极加在接收板上(反纺)的临界电压一般比电压正极加在喷丝头上(正纺)大很多。
目前正纺方式下加压范围为4~41kV,而反纺中这个范围为12~130kV。
电压在调控纤维直径方面的作用并不统一,在各自选定的电压范围内,大部分报道中纤维的直径随电压升高而减小,有的则没有明显变化[9-10],甚至有随电压升高纤维直径增大[18]或先减小再增大[19]的情况。
纺丝距离对纤维直径的影响同样具有不确定性。
喂料速度对纤维的质量、形貌和直径都有重要影响。
喂料速度越小,纤维直径越细,目前最小的是Dalton小组采用的5μL/h[20]。
图3为该研究小组在不同速率下纺丝得到纤维的扫描电镜图。
可以看到,当速率过低时,成丝不连续,有很多颗粒出现,而当速率过高时,熔体不能得到充分冷却和牵伸,出现了图(d)目前,还有一些研究者对对熔体电纺纤维膜进行某些形式的后处理,其中最常见的是退火处理,主要是为了改善纤维膜的热学和力学性能[17]。
射流运动规律与数学模型无论是溶液还是熔体,在静电纺丝过程中都要先形成液滴/熔滴,在电场作用下逐渐拉成锥状并最终形成射流,射流经过一段距离的空间运动后沉积在接收器上。
对于射流的空间运动,目前观察与记录到的较为普遍的一个规律是射流经历一定长度直线运动后在接近接收器时发生不规则鞭动。
图4是笔者采用PLA进行熔体电纺时拍摄下的射流运动图,从图中可以清晰的看到射流在空间运动的两个不同阶段。
笔者在实验中还发现,电压越大,射流下冲的速度越快,直线段运动所占的比例越大。
且熔体纺射流的直线段比溶液纺的要长,这与熔体粘度较大有关。
而采用相反的加压方式时,由于电场分布发生了很大的变化,越接近接收板电场越集中,抑制了射流的鞭动,使射流运动在整个过程中几乎呈直线状态,收集到的纤维膜成小丘状,如图5所示。
对于熔体射流在电场中的运动模型,Larrondo在1981年第一个开展熔体电纺实验后就进行了相关探索[22-23]:采用硅油为模拟流体,得到了射流某一点速度的数学计算公式。
Eduard等建立了非等温条件下熔体静电纺丝稳定射流段的数学模型[24];此后,又将上述模型与Ziabichi的FIC模型结合,得出了新的数学模型,借以推断纤维微观结构信息[25];Carroll等[26]建立的数学模型则是用来预测轴对称不稳定性出现的临界条件。
目前国内外研究大多是在探索各种单一或共混聚合物的成丝能力和特点,对成丝过程内在机理的研究还比较少。
熔体电纺最终的发展方向必然是要实现纤维物化性质的有效控制。
要达到这一目标不能只靠实验工艺研究,深入研究熔体在电场中的带电和运动机理,并最终得到一个可广泛适用的数学模型,是最根本的控制方法。
应用熔体电纺有许多潜在应用领域,但目前对其应用的研究主要集中在组织工程、过滤防护和储能封装这三大方面。
组织工程的支架材料,须满足诸多条件,如纤维直径需跟细胞外基质中的原纤维直径相当,具有一定大小的孔洞,表面的化学性能要做到对细胞很好的吸附并利于细胞的分裂增殖等。
熔体电纺在理论上是制造组织工程支架材料的绝佳方法。
Dalton等[4-5]进行了PEO-b-PCL&PCL的熔体电纺,成功进行了纤维母细胞的培养,并提出了一个新的概念——“试管静电纺”。
Karchin[27]和Kim[28]等研究小组也都利用熔体电纺纤维膜成功进行了细胞培养。
熔体电纺制得的超细纤维无溶剂残留,很适合用做过滤或防护材料。
Lee等[29]将熔体电纺纤维网进行了两种处理——层压或与非织造布复合,以解决防护服防护性与热湿舒适性之间的矛盾。
Zhou等[30]将熔体电纺PLA纤维(0.8μm)直接沉积到纤维素滤材上,大幅提升了滤材对亚微米大小的粉尘颗粒的过滤效应。
Cho等[31]以聚丙烯为原料,进行了高温下的溶液电纺(140℃~170℃)和熔体电纺,并等重量沉积在聚丙烯非织造布上,赋予其出色的阻隔功能,并有望应用于电池隔膜中。
近年来纺织服装的发展趋势之一就是智能化,其实现途径之一就是利用相变材料来实现能量的储藏和释放。
Jesse等[11]是最先采用熔体同轴电纺的方法来实现相变材料的封装的。
尽管其采用的是熔点很低的十八烷和二十烷,但这一将熔体和溶液结合起来进行静电纺丝的全新尝试为封装提供了一种新的途径。
封装不仅可以应用在储能材料上,也可应用于医药领域制作微胶囊以实现药物的传递与释放,化妆品中某些疏水性的化合物封装于亲水性外壳中增强吸收能力与作用效果[32]。
这些都有望于借助熔体同轴静电纺的方式得以实现。
结论熔体电纺作为一种制备超细纤维的重要方法,相对于溶液电纺有着独特的优势,在生物医药、过滤、封装等领域有着广阔的应用前景。
目前已有数十种聚合物或混合聚合物用于熔体纺丝实验,制得的纤维直径从数百纳米到几十微米不等。
多样性的熔体电纺装置使得各工艺参数对纤维物化性质的调控也具有多样性。
为了保证良好的重复性并最终实现工业化生产,熔体电纺装置需要向集成化、精细化和多喷头的方向发展。
对于纺丝过程内在机理的研究,目前尚未形成一定的理论体系,将是今后研究的重点之一。
另外,将熔体电纺与其他纺丝方法协同应用,共同构建具有一定功能性的材料体系,是拓宽熔体电纺纤维应用的重要途径之一。
参考文献[1]Cooley J P,692631.1902-02-04.[2]Norton C P,2048651.1936-07-21.[3]Larrondo L,Manley R ST J.J.Polym.Sci.Pt.B-Polym.Phys.,1981,19(6):909-920.[4]李莘,徐阳,魏取福,王爱民,王肖娜,杜远之.工程塑料应用.2012,40(12):41-45.[5]Dalton P D,Klinkhammer K,Salber J,Klee D,Moller M.Biomacromolecules,2006,7(3):686–690[6]Ogata N,Yamaguchi S,Shimada N,Lu G,Iwata T,Nakanr K,Ogihara T.J.Appl.Polym.Sci, 2007,104(3):1640-1645.[7]Dalton P D,Grafahrend D,Klinkhammer K,Klee D,Moller M.Polymer,2007,48(23):6823-6833.[8]Wang X N,Xu Y,Wei Q F,Cai Y B.Advanced Materials Research,2011,332-334,1550-1556.[9]Li X Y,Liu H C,Wang J N,Li C J.Polymer,2012,53(1):248-253.[10]Fang J,Zhang L,Sutton D,Wang X G,Lin T.J.Nanomater.,2012.[11]McCann J T,Marquez M,Xia Y N.Nano Lett.,2006,6(12):2868-2872.[12]Li F Y,Zhao Y,Wang S,Han D,Jiang L,Song Y L.J.Appl.Polym.Sci,2008,112(1):269-274.[13]Vando C,Nguyen T T T,Park J S.Sol.Energy Mater.Sol.Cells.,2012,104(9):131-139.[14]Hutmacher D W,Dalton P D.Chem-Asian J.,2011,6(1):44-56.[15]Wang X F,Huang Z M.Chin.J.Polym.Sci.,2010,28(1):45-53.[16]Malakhov S N,Khomenko A Y,Belousov S I,Prazdnichnyi A M,Chvalun S N,Shepelev A D, Budyka A K.Fibre Chem.,2009,41(6):355-359.[17]Nayak R,Kyratzis I L,Truong Y B,Padhye R,Arnold L.J.Mater.Sci.,2012,47(17):6387-6396.[18]Takasaki M,Fu H,Nakata K,Ohkoshi Y,Hirai T.SEN-I GAKKAISHI,2008,64(1):29-31.[19]Mitchell S B,Sanders J E.J.Biomed.Mater.Res.Part A,2006,78(1):110-120.[20]Dalton P D,Joergensen N T,Groll J,Moeller M.Biomed.Mater.,2008,3(3):1-11.[21]Dalton P D,Calvet J L,Mourran A,Klee D,Moller M.Biotech J.,2006,1(9):998-1006.[22]Larrondo L,Manley R ST J.J.Polym.Sci.Pt.B-Polym.Phys.,1981,19(6):921-932[23]Larrondo L,Manley R ST J.J.Polym.Sci.Pt.B-Polym.Phys.,1981,19(6):933-940.[24]Zhmayev E,Zhou H J,Joo Y L.J.Non-Newton.Fluid Mech.,2008,153(2/3):95-108.[25]Zhmayev E,Cho D,Joo Y L.Polymer,2010,51(6):274-290.[26]Carroll C P,Joo Y L.J.Non-Newton.Fluid Mech.,2008,153(2/3):130-148.[27]Karchin A,Simonovsky F I,Ratner B D,Sanders J E.Acta Biomater..2011,7(9):3277-3284.[28]Kim S J,Jang D H,Park D H,Min B M.Polymer,2010,51(6):1320-1327.[29]Lee S,Obendorf S K.J.Appl.Polym.Sci,2006,102(4):3430-3437.[30]Zhou H J,Green T B,Joo Y L.Polymer,2006,47(21):7497-7505.[31]Cho D,Zhou H J,Cho Y,Audus D,Joo Y L.Polymer,2010,51(25):6005-6012.[32]Díaz J E,Barrero A,Márquez M,Loscertales I G.Adv.Funct.Mater..2006,16(16):2110-211来源:静电纺丝进展期刊。