对辊压球机在转底炉工艺的应用
国内外转底炉的发展趋势及我国发展转底炉技术的建议

一、国内外转底炉技术的发展过程简介
1、转底炉直接还原工艺简介
转底炉炼铁工艺是非高炉炼铁工艺的一种,从1978年加拿大国际镍集团 (Inco,Ltd)建成第一座转底炉以来,已有近30年的历史,它从美国发源ห้องสมุดไป่ตู้先在日 本推广、后在中国得到发展。
转底炉法以其原料适应性强和操作工艺的灵活性等优点,引起冶金界的高度重视。 但由于原料加工方法条件和对产品质量要求的不同,转底炉直接还原炼铁分为 Inmetco法、DRYIRON法, FASTMET法和ITKM3等不同工艺路线。
国内外转底炉的发展趋势及 我国发展转底炉技术的建议
周渝生 齐渊洪 严定鎏 洪益成
钢铁研究总院先进钢铁流程及材料国家重点实验室 钢研晟华工程技术有限公司 20141106
目录
一、国内外转底炉技术的发展过程简介 二、国内外转底炉技术的发展趋势 三、我国发展转底炉技术的背景 四、对我国发展转底炉技术的建议
项目
单位
原料 铁精矿粉 还原煤 皂土 有机粘结剂 小计 能源 电 天然气 氮气 水 小计 其他 消耗品 维修与备件
kg kg kg kg
kwh m3(STP) m3(STP) t
美元 美元
消耗量 单位
1335 410 5 5
65 60 10 0.30
国内外转底炉的发展趋势及我国发展转底炉技术的建议 PPT课件

2020/3Βιβλιοθήκη 317一、国内外转底炉技术的发展过程简介
2、国内外转底炉直接还原工艺简介
2020/3/31
8
一、国内外转底炉技术的发展过程简介
2、国内外转底炉直接还原工艺简介
• Inmetco流程的最突出特点是使用冷固结含碳球团。可使用 矿粉或冶金废料作为含铁原料,焦粉或煤作为内配还原剂。 将原燃料混匀磨细,制作成冷固结球团,然后将冷固结球团 连续加入转体炉,在炉盘上均匀布上一层厚度约为球团矿直 径3倍的炉料。
2020/3/31
2
一、国内外转底炉技术的发展过程简介
1、转底炉直接还原工艺简介
转底炉炼铁工艺是非高炉炼铁工艺的一种,从1978年加拿大国际镍集团 (Inco,Ltd)建成第一座转底炉以来,已有近30年的历史,它从美国发源、先在日 本推广、后在中国得到发展。
转底炉法以其原料适应性强和操作工艺的灵活性等优点,引起冶金界的高度重视。 但由于原料加工方法条件和对产品质量要求的不同,转底炉直接还原炼铁分为 Inmetco法、DRYIRON法, FASTMET法和ITKM3等不同工艺路线。
属化球团经过冷却区后被排出炉外冷却,部分再氧化金属化率降低一些。煤气燃烧
及反应生成的烟气沿着与炉料转动相反的方向流动,最后流入废气净化处理及余热 回收系统。
装料 区
900~1100 ℃
预热区
烟气流动方向 1200~1400℃
还原区
1100~900℃
烧嘴
冷却区
排料区
转底炉炉底转动方向
2020/3/31
2020/3/31
9
一、国内外转底炉技术的发展过程简介
⑵. 干铁法
GLOBA公司(原MR&E公司)在1960年是米德兰-罗斯的快速加热工艺的技 术开发部门,1985年成为独立公司。曾经为美国Ameristeel公司的电炉粉 尘处理系统以及美国Rouge Steel公司综合钢铁厂的粉尘和污泥处理系统提 供DRYIRON法的相关设备,具备丰富的应用实绩。GLOBA公司开发的干铁法 有两项专利技术:用废糖浆作为粘结剂,利用氧化铁粉与碳粉混合物成型 的干压块方式对辊压球机压成球团后直接装入转底炉,取消了球团的烘干 程序;采用特殊的震动传送装置的炉料装入方法。可以得到金属化率大于 90%的DRI。 是一种较理想的煤基直接还原工艺。 该工艺过程中在转底炉 内的高温作用与短暂的停留时间(约10min),其操作具有巨大的灵活性, 而且设备的操作控制非常容易。考虑到上述炼铁厂粉尘和污泥处理以及还 原铁生产的需要,新日铁钢铁事业部于1999年从美国MR&E公司引进转底炉 DRYIRON法,并且争取到代理推销资格。 这是日本FASTMET法发展的基础。
转底炉处置含锌粉尘压球用粘结剂工业化应用研究

转底炉处置含锌粉尘压球用粘结剂工业化应用研究摘要:近些年来,随着钢铁工业的飞速发展,钢铁生产产生的粉尘对环境和人类的危害日益加重,这也对企业铁前生产造成危害。
钢铁企业一般将低锌含铁粉尘配入烧结使用,但中高锌粉尘配入烧结会降低烧结矿质量,并对高炉顺性和高炉寿命产生不良影响。
如何经济地实现含锌粉尘的高效利用成为难题。
关键词:转底炉;含锌粉尘;压球;粘结剂;工业化应用引言目前处理冶金尘泥的方式中,因转底炉工艺的适应性较好、可靠性高、易于操作和维护、且对环境污染相对较小,具有较大应用价值,更适合钢铁企业流程化生产。
转底炉生产线采用压球工艺对含锌粉尘进行成型及烘干含锌粉尘的脱锌处理,脱锌后的金属化物料返回炼铁炼钢工序得到循环利用,锌富集于烟尘进行收集后用于外售。
由于含锌粉尘种类多、性能差异大,必须使用粘结剂强化成球,以提高成球率及球团强度保证转底炉运转稳定及产品质量。
但是,目前大多使用淀粉类粘结剂,存在添加量大(3%~7%)、生产成本高、成品率较低及成品粉化率高(全流程返料量高达30%~60%),易导致转底炉底结块,影响排料等问题。
1转底炉发展概述转底炉工艺最初是一种煤基直接还原炼铁工艺,后来用于处理钢铁厂含锌粉尘,尤其在日本和中国得到快速发展。
20世纪50年代,美国Ross公司发明了转底炉直接还原法,取名为Fastmet工艺。
1974年,加拿大的国际镍集团公司用转底炉处理不锈钢的氧化物废料,并命名为Inmetco工艺。
日本神户钢铁厂与美国Miderx公司联合开发转底炉直接还原新工艺,在20世纪90年代中后期取得突破性进展,生产出了高纯度粒铁,该产品被命名为ITmk3。
新日铁于1998年从美国MaumeeR&E公司引进转底炉技术处理钢铁厂粉尘,技术改进后在日本Kimitsu、Hikari、Hirohata等企业建造了工业生产规模的转底炉。
北京科技大学是我国最早研究转底炉的科研院所,在1992、1996和2001年分别在河南舞钢、鞍山和山西冀城建成了不同规模的转底炉。
转底炉生产金属化球团工业性试验
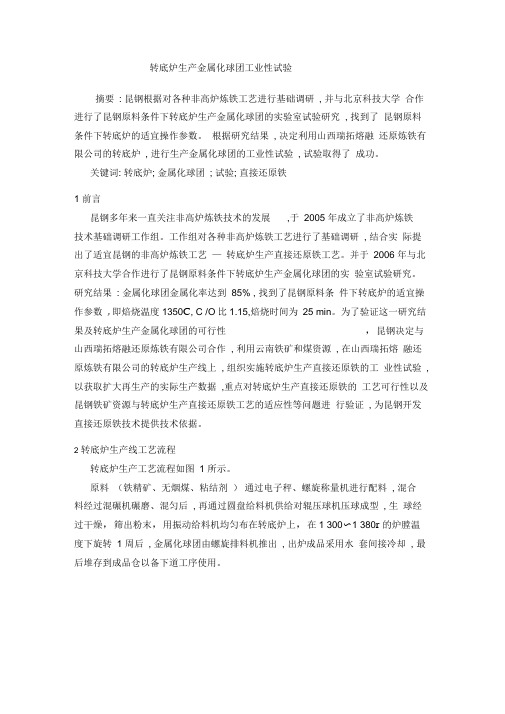
转底炉生产金属化球团工业性试验摘要: 昆钢根据对各种非高炉炼铁工艺进行基础调研, 并与北京科技大学合作进行了昆钢原料条件下转底炉生产金属化球团的实验室试验研究, 找到了昆钢原料条件下转底炉的适宜操作参数。
根据研究结果, 决定利用山西瑞拓熔融还原炼铁有限公司的转底炉, 进行生产金属化球团的工业性试验, 试验取得了成功。
关键词: 转底炉; 金属化球团; 试验; 直接还原铁1 前言昆钢多年来一直关注非高炉炼铁技术的发展,于2005 年成立了非高炉炼铁技术基础调研工作组。
工作组对各种非高炉炼铁工艺进行了基础调研, 结合实际提出了适宜昆钢的非高炉炼铁工艺—转底炉生产直接还原铁工艺。
并于2006 年与北京科技大学合作进行了昆钢原料条件下转底炉生产金属化球团的实验室试验研究。
研究结果: 金属化球团金属化率达到85% , 找到了昆钢原料条件下转底炉的适宜操作参数,即焙烧温度1350C, C /O比1.15,焙烧时间为25 min。
为了验证这一研究结果及转底炉生产金属化球团的可行性,昆钢决定与山西瑞拓熔融还原炼铁有限公司合作, 利用云南铁矿和煤资源, 在山西瑞拓熔融还原炼铁有限公司的转底炉生产线上, 组织实施转底炉生产直接还原铁的工业性试验, 以获取扩大再生产的实际生产数据,重点对转底炉生产直接还原铁的工艺可行性以及昆钢铁矿资源与转底炉生产直接还原铁工艺的适应性等问题进行验证, 为昆钢开发直接还原铁技术提供技术依据。
2 转底炉生产线工艺流程转底炉生产工艺流程如图 1 所示。
原料(铁精矿、无烟煤、粘结剂)通过电子秤、螺旋称量机进行配料, 混合料经过混碾机碾磨、混匀后, 再通过圆盘给料机供给对辊压球机压球成型, 生球经过干燥,筛出粉末,用振动给料机均匀布在转底炉上,在1 300〜1 380r 的炉膛温度下旋转 1 周后, 金属化球团由螺旋排料机推出, 出炉成品采用水套间接冷却, 最后堆存到成品仓以备下道工序使用。
T朗輯]]嵌辅如I [煤粉I哥I山茜刘底炉1.艺漬即示童用3原料准备试验原料为云南产的铁精矿、无烟煤,粘结剂由山西瑞拓公司提供。
650对辊式压球机

单位代码学号分类号1023密级0022设计(论文)650型对辊式压球机设计院(系)名称工学院机械系专业名称机械设计制造及其自动化学生姓名企业指导郑州博金机器制造有限公司网址2012年 5 月15日650式对辊式压球机摘要压球机是用于粉料成球的设备,目前主要用于冶金白灰筛下料,氧化铁皮以及各种物料的制球生产,本压球机是在原高压压球机基础上进行改进设计的,这次改进设计中能使压球机能够进行干压压球,设计中增大了予压机的挤压力矩同时也加大了供料量,并对油压系统做了重新设计,由于双传动占地面积大,这次改为单传方式,使压球机更加紧凑由于成型物料的种类不同,它所要求的压缩比相差很大为适应这一要求,予压电机采用滑差调速电机通过对予压螺旋转速的改变,实现改变加料量的目的,调速方式采用手控的,通过试验机的工业试验证明,成型单位压力与供料量有密切的关系,而与总压力的无明显的直接关系,所以不必用总压力的变化作调速的依据,可观察主电机工作电流的变化量作为调速的依据,主电机通过皮带轮得到两种速度,如须增加供料量可以取下螺旋衬套换上直径大的螺旋即可。
关键词:压球机,成型物料,挤压力The 650 type of roller compaction machineAbstractAuthor:Tutor: 650 Pressure ball machine is used for powder into a ball of equipment, which are mainly used in metallurgical lime sieve of material, iron oxide and of all kinds of material in the ball production, the ball is in the original machine pressure phi high pressure ball machine based on improving the design, the design improvement can pressure on dry pressing machine can ball pressure ball, design increases the pressure of extrusion machine to torque and increase the feed for, and the hydraulic system to do the design, because the double transmission covers an area of big, the way to request, makes the ball machine more compactDue to the different kinds of material molding, it required is great for adapting to the compression ratio this request, to pressure the motor control motor sliding through the pressure of the spiral speed to change, realize the purpose of the feed and change, the speed adjustment way by hand control, through the test enginery industrial experiments prove, forming units pressure and for shoes have close relations, and total pressure and has no obvious direct relation So don't have to use the total pressure of the variation of the speed, the basis of the main motor can observe the variation of working current speed as the basis, the main motor through two speed by pulley, such as must increase feed can take for spiral bushing change into large diameter spiral can.Key words: Pressure secret machine, Molding materials, extrusion pressure1.1压球机的重要性 (1)1.2 压球机的发展现状 (1)1.3压球机在工业中的作用 (2)1.4压球机设备构造及构造的具体分析 (2)1.4.1压球机的三大系统 (2)1.4.2 压球机的工作过程 (3)2基本参数的确定 (4)2.1电动机的选择 (4)2.1.1选择电动机的类型和结构形式 (4)2.1.2选择电动机的容量 (4)2.2传动比的计算及分配 (5)3 v带带轮设计 (5)3.1设计功率 (5)3.2选定带型 (5)3.3传动比 (5)3.4小带轮的基准直径 (5)3.5大带轮的基准直径 (6)3.6带速 (6)3.7初定轴间距 (6)3.8所需基准长度 (6)3.9实际轴间距 (6)3.10小带轮包角 (6)3.11单根v带传递的基本额定功率 (7)3.12传动比i≠1时的额定功率增量 (7)3.13v带的根数 (7)3.14单根v带的预紧力 (7)3.15作用在轴上的力 (7)3.16带轮的结构和尺寸 (7)4.1各轴的转速 (8)4.2各轴功率 (8)4.3各轴转矩 (8)5轴的设计计算 (9)5.1轴材料的选择 (9)5.2计算Ⅲ轴最小轴径 (9)5.2.1Ⅱ-Ⅲ段的直径确定 (10)5.2.2轴承 (10)5.2.3辊子部分的轴的设计 (10)5.2.4轴承端盖 (10)5.2.5齿厚的相关计算 (10)5.2.6确定轴上圆角和倒角尺寸 (11)5.2.7求轴上载荷 (11)5.2.8按弯扭合成应力校核轴的强度 (12)5.3Ⅳ轴的校核 (12)6齿轮的设计与计算 (13)6.1选定齿轮的类型,精度等级,材料,初定其模数及齿数 (13)6.2按齿根弯曲强度设计 (13)6.2.1确定公式内的各计算数值 (13)7减速器的选用 (15)7.1以下对几种减速器进行对比: (15)7.1.1圆柱齿轮减速器 (15)7.1.2圆锥齿轮减速器 (16)7.1.3蜗杆减速器 (16)7.1.4齿轮-蜗杆减速器 (16)7.2传统型减速器结构 (16)7.3新型减速器结构 (17)结论 (18)参考文献 (20)1绪论1.1压球机的重要性原煤不经过入洗而直接用于燃烧,不仅浪费能源,而且产生大量的煤烟和温室气体的排放发。
辊底炉的应用现状及关键工艺技术分析
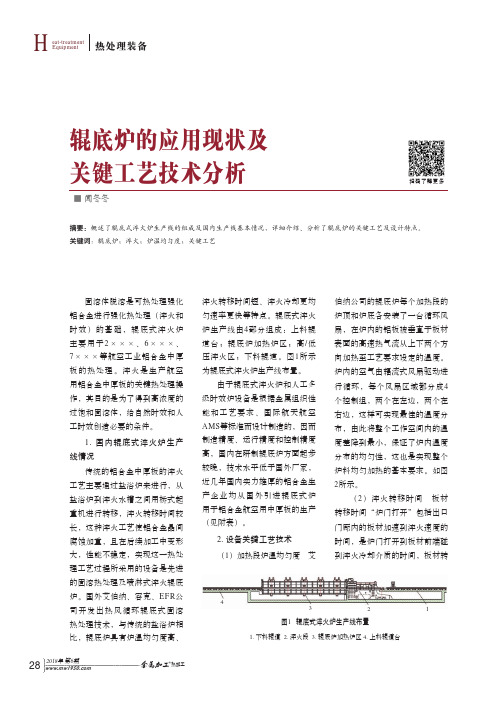
282018年 第6期 热加工H热处理装备eat-treatment Equipment辊底炉的应用现状及关键工艺技术分析■ 闻冬冬固溶体脱溶是可热处理强化铝合金进行强化热处理(淬火和时效)的基础,辊底式淬火炉主要用于2×××、6×××、7×××等航空工业铝合金中厚板的热处理。
淬火是生产航空用铝合金中厚板的关键热处理操作,其目的是为了得到高浓度的过饱和固溶体,给自然时效和人工时效创造必要的条件。
1. 国内辊底式淬火炉生产线情况传统的铝合金中厚板的淬火工艺主要通过盐浴炉来进行,从盐浴炉到淬火水槽之间用桥式起重机进行转移,淬火转移时间较长,这种淬火工艺使铝合金晶间腐蚀加重,且在后续加工中变形大,性能不稳定,实现这一热处理工艺过程所采用的设备是先进的固溶热处理及喷淋式淬火辊底炉。
国外艾伯纳、容克、EFR 公司开发出热风循环辊底式固溶热处理技术,与传统的盐浴炉相比,辊底炉具有炉温均匀度高、摘要:概述了辊底式淬火炉生产线的组成及国内生产线基本情况,详细介绍、分析了辊底炉的关键工艺及设计特点。
关键词:辊底炉;淬火;炉温均匀度;关键工艺扫码了解更多淬火转移时间短、淬火冷却更均匀速率更快等特点。
辊底式淬火炉生产线由4部分组成:上料辊道台;辊底炉加热炉区;高/低压淬火区;下料辊道。
图1所示为辊底式淬火炉生产线布置。
由于辊底式淬火炉和人工多级时效炉设备是根据金属组织性能和工艺要求、国际航天航空AMS 等标准而设计制造的,因而制造精度、运行精度和控制精度高,国内在研制辊底炉方面起步较晚,技术水平低于国外厂家,近几年国内实力雄厚的铝合金生产企业均从国外引进辊底式炉用于铝合金航空用中厚板的生产(见附表)。
2. 设备关键工艺技术(1)加热段炉温均匀度 艾伯纳公司的辊底炉每个加热段的炉顶和炉底各安装了一台循环风扇,在炉内的铝板被垂直于板材表面的高速热气流从上下两个方向加热至工艺要求设定的温度。
磷矿粉制备球团生产黄磷的技术综述-冶金工程论文-工程论文

磷矿粉制备球团生产黄磷的技术综述-冶金工程论文-工程论文——文章均为WORD文档,下载后可直接编辑使用亦可打印——摘要:简述了黄磷生产的必要性及磷矿粉制备球团的意义, 分析了黄磷生产对磷矿的要求和对磷矿粉制备球团的性能要求, 从圆盘造球机造球、磷矿粉压球和磷精矿成球3个方面对磷矿粉制备球团生产黄磷的技术现状进行了总结, 并对球团制备工艺的选择提出了建议。
关键词:磷矿粉; 造球工艺; 压球工艺;Abstract:This paper briefly describes the necessity of yellow phosphorus production and the significance of producing pellets from phosphate rock and analyses the requirements for yellow phosphate production and the performance requirements of pellets produced from phosphate rock powder.The technical status of producing yellow phosphorus from pellets made from phosphate rock powder is summarized by three directions of disk pelletizing, phosphate powder extruding ball and phosphate concentrate pelletizing and suggestions on pellet production are put forward.Keyword:phosphate rock powder; pelletizing process; extruding ball process;0、引言黄磷是一种重要的化工原料, 以其为原料生产的各种磷化物和磷酸盐品种繁多, 用途广泛[1]。
浅谈辊底式加热炉技术

浅谈辊底式加热炉技术浅谈辊底式加热炉技术【摘要】辊底式加热炉是薄板坯连铸连轧生产线上的一个重要设备。
本文阐述了辊底式加热炉的基本概念及作用,并重点介绍了辊底式加热炉的主要技术特点。
【关键词】步进式加热炉机械设备辊底式加热炉是薄板坯连铸连轧生产线上的一个重要设备,在功能上起着承上启下的作用,它一面将连铸出来的板坯加热至轧钢工艺所要求的出钢温度1150±10℃,这个温度精度要远高于一般步进炉所能够达到的±30℃的温差值,这样就为生产超薄热带产品奠定了基础,另一方面,辊底炉在整个工艺中还起着重要的缓冲作用。
一、辊底式加热炉概述辊底式加热炉用炉内辊道运送热处理材,沿炉子整个长度每隔一定距离安装一根辊子,物料在辊子上运行,在辊子上面和下面的炉膛都可布置烧嘴供热。
辊子有环辊(带有盘形辊环)和平辊二种,前者只能用于加热板材,后者可用于加热板材、型钢、管材和棒材。
辊子外层辊套的材质通常为耐热钢,有的也用碳化硅。
温度高的炉子(1000-1150℃)采用水冷轴并带绝热内衬的耐热钢炉辊,或全水冷的炉辊。
为了防止炉辊弯曲,在高温下工作的辊子必须不停地旋转;当炉子空烧或不出料时,也要用低速以每分钟0.5-1.5周的转速摆动或旋转。
辊底式炉因物料两面受热,加热较快、较均匀,广泛应用于常化、退火、淬火、回火等热处53工艺。
二、辊底式加热炉的作用将连铸机送来的薄板坯按工艺要求均匀地加热到轧制温度。
投产的生产线连铸坯入炉温度一般在850℃-1050℃之间,出炉温度(轧制温度)1100℃-1150℃,在炉内需提温50℃-300℃。
要求出炉板坯长度与宽度方向温差≤±10℃,板坯边部(约40ram范围内)温度比中部温度高40℃左右。
在单尺坯轧制时,炉子能储存若干块单尺坯,当轧机换辊或事故停轧时,连铸机送来的薄板坯可储存在加热炉内,保证连铸机正常生产,炉子起到了缓冲储存作用。
根据轧钢工艺要求,单尺坯生产时的缓冲时间应≥12min,确保轧机有充足的时间换辊和处理事故。
- 1、下载文档前请自行甄别文档内容的完整性,平台不提供额外的编辑、内容补充、找答案等附加服务。
- 2、"仅部分预览"的文档,不可在线预览部分如存在完整性等问题,可反馈申请退款(可完整预览的文档不适用该条件!)。
- 3、如文档侵犯您的权益,请联系客服反馈,我们会尽快为您处理(人工客服工作时间:9:00-18:30)。
对辊压球机在转底炉工艺的应用
0前言
在钢铁工业飞速发展的过程中,由于传统的高炉炼铁方式投资大、能耗高、流程长、污染严重等因素的影响,各种非高炉炼铁工艺成了世界各国研究的重点,其中的转底炉直接还原工艺在各国受到了极大的关注。
我国在二十世纪九十年代初期开始对转底炉技术进行研究,尤其在近几年一直备受青睐,陆续建设了多条转底炉工业化示范项目。
目前转底炉直接还原工艺基本可分为两类:一是以回收冶金废弃物为原料,如高转炉瓦斯灰、轧钢氧化铁皮、钒钛磁铁矿综合利用等;二是以铁精粉为原料,直接还原成珠铁,这种工艺方法已有多次的实验成果,虽然国外曾经报道过建设商业规模工厂,但在我国还没有工业示范项目;这种工艺方法属于正在发展中的先进技术。
目前我国建成并能连续运转的江苏沙钢集团30万吨转底炉、四川龙莽集团7万吨转底炉、四川攀枝花钢铁公司10万吨转底炉、马鞍山钢铁股份有限公司20万吨转底炉等工艺线是属于第一种类型,得到国内相关专家的鉴定及认可。
对辊压球机在这些工艺线上起到了重要作用,为整条线的顺利运转提供了有利条件。
1对辊压球机起源
对辊压球机是发展较早、应用最多的压团法设备。
在冶金行业造块方法可分为3类:烧结、球团和压团。
压团时一般需配入一定数量的黏结剂,其适用的粒度范围比较宽,且过程简单,其产品团块可直接使用或者经过热处理后再使用。
团块的冶金性能良好,但加工成本较高。
同时与需要造块的铁精矿或粉矿的巨大数量相比,压团设备的生产能力有限。
所以,铁矿石压团法未能在钢铁工业中得到发展。
然而在有色金属火法冶炼中,常采用烧结法和压团法。
在粉煤成型中,压团法仍是唯一的造块法。
冶金工业部于1992年3月批准了YB/T 019—1992对辊式高压粉矿压块机标准,这充分说明此种设备应用比较多而且很受关注,同时该标准的制定为设备的设计和选型提供了统一参考依据。
在转底炉工艺路线里,原料的成型设备有圆盘造球机、对辊压球机两种。
其中圆盘造球机在设备成本与生产技术上相对比较成熟,但是生产的球团含水量高,后续烘干工艺要消耗很大的能量,一般使用膨润土做粘结剂,直接还原后膨润土成分大部分留在直接还原球团中,降低产品品质;同时圆盘造球机使用原料范围窄,产量低。
对辊压球机的设备造价与维护成本稍高,但制球过程中可选用有机粘结剂,且有机粘结剂在燃烧过程中可以提供部分热量,燃烧产物少,不会影响到直接还原后产品品质。
近几年来国内各大钢铁企业先后兴建了转底炉直接还原铁项目,如马钢、沙钢、莱钢、
日钢、荣钢、攀钢、龙莽等,在这几个项目中,仅马钢的造球方法是采用圆盘造球机,其余各生产线上的成球方法都是采用对辊压球机,也称高压压球机。
对辊压球机在这里得到应用的原因之一是各个项目的产能都不高,正好能体现出自身的优势。
2对辊压球机的分类及原理
对辊压球机因其应用物料的特性、用途及压力大小不同,分为低压压球机、中压压球机、高压压球机。
至于三者的压力界定目前还没有统一的标准,一般都以线压力(成形压力通常以总压力除以辊皮宽度表示,称之为线压力[1])的大小进行区分。
目前在转底炉工艺上应用的均为高压压球机。
对辊压球机主要靠两个相向转动的辊轮,使流入两辊间隙的混合料受压成型[2](见图1)。
其中一个为定辊,另一个为可以前后水平移动的动辊,压力加在动辊两端的轴承座上。
高、中、低压压球机的不同,主要是加压方式和传动机构上的区别。
低压压球机一般采用弹簧加压,而中压和高压压球机则采用高压油缸加压。
两辊辊面上可开出型槽,型槽数目和大小根据需要设计,其产品可为卵型、枕型或椭圆型[2]。
图1 对辊压球机成型原理图
高压压球机主要由预压装置、压球机主体、油压支承系统形成一个机组,见图2。
图2 高压压球机示意图
1.传动装置
2.联轴器
3.压辊
4.预压装置
5.进料口
6.支承油缸
7.机架
预压装置由2部分组成,一是调速电机、联轴器、减速机等传动部分;二是单头或双头螺旋及加料嘴构成的预压装置。
其作用是将细粉状物料进行预压缩、脱气、保证供料压力,提高物料容重。
对于不同品种、粒度的粉料,所需的最佳供料容积(或转速)不相同,因此要求预压传动装置是可以调速的[1]
压球机主体由两个相对旋转的带有半槽的压辊、电动机、联轴器、减速机、双出轴联轴器、机架构成。
两个压辊一个是固定的,另一个是可移动的,目的是确保压球过程保持恒压,当有硬物进入时可起安全保护作用。
双出轴联轴器必须具有挠性,才能适应压辊移动的需求。
电动机最好选用变频调速电机,以便根据物料特性需要调整辊子的转速。
因转速过快会出现半球增多,降低成球率和成球质量。
油压支承系统主要由油箱、油泵、电动机、液压阀门和油缸组成。
影响成型机作业效率的关键部件是压球辊子,压球轧辊的毛坯分为:整体锻造和铸造的,铸造的密度小,结构粗糙,但是比较经济。
锻造而成的密度大,结构紧密,耐磨性号,寿命长,球槽加工工艺性好,合适物料种类多,而且运行可靠,大多用于中高压的大型成型机,但是成本高。
3、能力计算[1]
高压压球机一般计算压球机的通过量,若计算压球机的球坯产量,则将通过量乘以成球率φ。
压球机通过量计算见公式(1)、(2):
Q V=60iVn×10-6 (1)
Q w=60iVnγ×10-6 (2)
式中Q V—单位时间容积通过量,m3/h;
Q w—单位时间质量通过量,t/h;
i— 一个压辊上的槽数;
V— 每个球坯的容积,cm3;
n— 压辊每分钟转数,r/min;
γ— 单个球坯的容重,g/cm3。
成球率计算如下:
成球率φ=单位时间筛上合格球质量/单位时间总通过量×100%
3对辊压球机应用
因对辊压球机具有成球率高、消耗功率小、结构紧凑、便于检修调试等优点,近几年在转底炉工艺上成为了主要工序之一。
另外对辊压球机一直被用来压制煤粉、铁粉、焦煤、铝粉、铁屑、氧化铁皮、碳粉、矿渣、石膏、尾矿、污泥、高岭土、活性炭、焦末等各种粉末、粉料、废料、废渣,广泛应用于耐火材料、电厂、冶金、化工、能源、运输、供暖等行业。
经对辊压球机制作成型后的物料,节能环保,便于运输,提高了对废料的利用率,具有良好的经济效益和社会效益。
[参考文献]
[1]曹希成.钢铁企业机电设备设计安装与检修维护手册[M].北京:北京冶金出版社,2007.
[2]李健.现代烧结生产技术工艺流程、设备选型计算与烧结效率实用手册[M].北京:当代中国音像出版社,2005.。