转底炉工艺的发展与实践_朱荣
国内外转底炉的发展趋势及我国发展转底炉技术的建议

一、国内外转底炉技术的发展过程简介
1、转底炉直接还原工艺简介
转底炉炼铁工艺是非高炉炼铁工艺的一种,从1978年加拿大国际镍集团 (Inco,Ltd)建成第一座转底炉以来,已有近30年的历史,它从美国发源ห้องสมุดไป่ตู้先在日 本推广、后在中国得到发展。
转底炉法以其原料适应性强和操作工艺的灵活性等优点,引起冶金界的高度重视。 但由于原料加工方法条件和对产品质量要求的不同,转底炉直接还原炼铁分为 Inmetco法、DRYIRON法, FASTMET法和ITKM3等不同工艺路线。
国内外转底炉的发展趋势及 我国发展转底炉技术的建议
周渝生 齐渊洪 严定鎏 洪益成
钢铁研究总院先进钢铁流程及材料国家重点实验室 钢研晟华工程技术有限公司 20141106
目录
一、国内外转底炉技术的发展过程简介 二、国内外转底炉技术的发展趋势 三、我国发展转底炉技术的背景 四、对我国发展转底炉技术的建议
项目
单位
原料 铁精矿粉 还原煤 皂土 有机粘结剂 小计 能源 电 天然气 氮气 水 小计 其他 消耗品 维修与备件
kg kg kg kg
kwh m3(STP) m3(STP) t
美元 美元
消耗量 单位
1335 410 5 5
65 60 10 0.30
国内外转底炉技术发展及工业化应用情况

国内外转底炉技术发展及工业化应用情况文档下载说明Download tips: This document is carefully compiled by this editor. I hope that after you download it, it can help you solve practical problems. The document 国内外转底炉技术发展及工业化应用情况can be customized and modified after downloading, please adjust and use it according to actual needs, thank you! In addition, this shop provides you with various types of practical materials, such as educational essays, diary appreciation, sentence excerpts, ancient poems, classic articles, topic composition, work summary, word parsing, copy excerpts, other materials and so on, want to know different data formats and writing methods, please pay attention!转底炉技术是一种在冶金工业中用于炼钢和炼铁的重要工艺。
在国内外,随着技术的不断创新和发展,转底炉技术已经取得了长足的进步,并得到了广泛的工业化应用。
本文将就国内外转底炉技术的发展及工业化应用情况进行探讨。
国内转底炉技术发展及工业化应用情况。
中国作为世界上最大的钢铁生产国之一,在转底炉技术领域也有着长足的发展。
转底炉工艺技术存在的问题与发展建议

( 1 . T e c h n o l o g y Ce n t r e o f A n g a n g S t e e l C o . ,L t d .,An s h a n 1 1 4 0 1 1 ,L i a o n i n g ;2 . S c i e n c e a n d T e c h n o l o g y De p a  ̄-
提 出 了发 展 转 底 炉 工 艺 技术 的 几 点建 议 。 关键词 转底炉 ; 冶金尘泥 ; 直接 还 原 文献标识码 : A 文章编号 : 1 6 7 1 — 3 8 1 8 ( 2 0 1 3 ) 0 2— 0 0 4 2—0 3 .
中图 分 类 号 : T F 7 0 2 . 9
d e s c r i be d i n t h e p a p e r ,a n d s o me p r o b l e ms d u r i n g p r o d u c t i o n p r o c e s s a r e s y s t e ma t i c a l l y i n t r o d u c e d a n d
o b j e c t i v e l y a n a l y z e d .At t h e e n d,s o me a d v i c e s f o r d e v e l o p me n t o f Ro t a r y He a r t h F u r n a c e a r e p r o p o s e d .
me n t o f A n g a n g S t e e l G r o u p,An s h a n 1 1 4 0 1 1,L i a o n i n g )
Abs t r a c t Th e c u r r e n t s t a t u s o f Ro t a r y He a r t h F ur n a c e d i r e c t r e d u c t i o n pr o c e s s a t h o me a n d a b o a r d i s
国内外转底炉的发展趋势及我国发展转底炉技术的建议 PPT课件

2020/3Βιβλιοθήκη 317一、国内外转底炉技术的发展过程简介
2、国内外转底炉直接还原工艺简介
2020/3/31
8
一、国内外转底炉技术的发展过程简介
2、国内外转底炉直接还原工艺简介
• Inmetco流程的最突出特点是使用冷固结含碳球团。可使用 矿粉或冶金废料作为含铁原料,焦粉或煤作为内配还原剂。 将原燃料混匀磨细,制作成冷固结球团,然后将冷固结球团 连续加入转体炉,在炉盘上均匀布上一层厚度约为球团矿直 径3倍的炉料。
2020/3/31
2
一、国内外转底炉技术的发展过程简介
1、转底炉直接还原工艺简介
转底炉炼铁工艺是非高炉炼铁工艺的一种,从1978年加拿大国际镍集团 (Inco,Ltd)建成第一座转底炉以来,已有近30年的历史,它从美国发源、先在日 本推广、后在中国得到发展。
转底炉法以其原料适应性强和操作工艺的灵活性等优点,引起冶金界的高度重视。 但由于原料加工方法条件和对产品质量要求的不同,转底炉直接还原炼铁分为 Inmetco法、DRYIRON法, FASTMET法和ITKM3等不同工艺路线。
属化球团经过冷却区后被排出炉外冷却,部分再氧化金属化率降低一些。煤气燃烧
及反应生成的烟气沿着与炉料转动相反的方向流动,最后流入废气净化处理及余热 回收系统。
装料 区
900~1100 ℃
预热区
烟气流动方向 1200~1400℃
还原区
1100~900℃
烧嘴
冷却区
排料区
转底炉炉底转动方向
2020/3/31
2020/3/31
9
一、国内外转底炉技术的发展过程简介
⑵. 干铁法
GLOBA公司(原MR&E公司)在1960年是米德兰-罗斯的快速加热工艺的技 术开发部门,1985年成为独立公司。曾经为美国Ameristeel公司的电炉粉 尘处理系统以及美国Rouge Steel公司综合钢铁厂的粉尘和污泥处理系统提 供DRYIRON法的相关设备,具备丰富的应用实绩。GLOBA公司开发的干铁法 有两项专利技术:用废糖浆作为粘结剂,利用氧化铁粉与碳粉混合物成型 的干压块方式对辊压球机压成球团后直接装入转底炉,取消了球团的烘干 程序;采用特殊的震动传送装置的炉料装入方法。可以得到金属化率大于 90%的DRI。 是一种较理想的煤基直接还原工艺。 该工艺过程中在转底炉 内的高温作用与短暂的停留时间(约10min),其操作具有巨大的灵活性, 而且设备的操作控制非常容易。考虑到上述炼铁厂粉尘和污泥处理以及还 原铁生产的需要,新日铁钢铁事业部于1999年从美国MR&E公司引进转底炉 DRYIRON法,并且争取到代理推销资格。 这是日本FASTMET法发展的基础。
转底炉 (2)
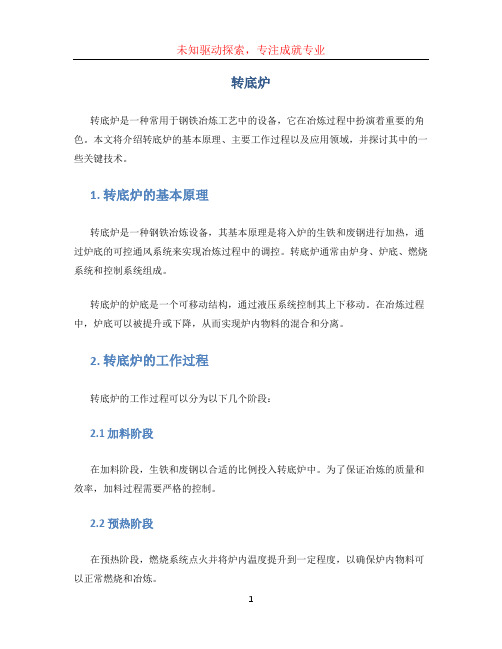
转底炉转底炉是一种常用于钢铁冶炼工艺中的设备,它在冶炼过程中扮演着重要的角色。
本文将介绍转底炉的基本原理、主要工作过程以及应用领域,并探讨其中的一些关键技术。
1. 转底炉的基本原理转底炉是一种钢铁冶炼设备,其基本原理是将入炉的生铁和废钢进行加热,通过炉底的可控通风系统来实现冶炼过程中的调控。
转底炉通常由炉身、炉底、燃烧系统和控制系统组成。
转底炉的炉底是一个可移动结构,通过液压系统控制其上下移动。
在冶炼过程中,炉底可以被提升或下降,从而实现炉内物料的混合和分离。
2. 转底炉的工作过程转底炉的工作过程可以分为以下几个阶段:2.1 加料阶段在加料阶段,生铁和废钢以合适的比例投入转底炉中。
为了保证冶炼的质量和效率,加料过程需要严格的控制。
2.2 预热阶段在预热阶段,燃烧系统点火并将炉内温度提升到一定程度,以确保炉内物料可以正常燃烧和冶炼。
2.3 冶炼阶段在冶炼阶段,炉底开始下降,炉内的物料在高温和高压的环境下进行冶炼反应。
冶炼过程中,炉内的废气通过翻转炉顶部的排气系统排出,同时新鲜空气通过炉底通风系统进入炉内维持燃烧所需的氧气供应。
2.4 炉底升起和排渣阶段在冶炼结束后,炉底开始升起,炉内产生的废渣通过炉底排渣装置排出。
同时,炉内残余渣和铁水经过冷却后也会从炉底排出。
3. 转底炉的应用领域转底炉主要应用于钢铁冶炼和废钢回收工艺中。
由于其灵活性和可控性,转底炉在这些工艺中被广泛使用。
转底炉可以适应不同种类和比例的原料,包括生铁、废钢、废铁等。
同时,转底炉还可以通过控制炉底的升降速度和炉内通风系统的调节来调整冶炼过程中的溶解度和升降速度。
4. 转底炉的关键技术转底炉作为一种复杂的冶炼设备,涉及到多种关键技术。
以下是其中的一些关键技术:4.1 燃烧系统转底炉的燃烧系统需要能够提供足够的热量来加热炉内物料,并确保燃烧的充分和稳定。
常用的燃料包括焦炭、天然气和重油等。
4.2 炉底控制系统转底炉的炉底控制系统需要能够准确地控制炉底的升降速度,以及炉内通风系统的调节。
转底炉的发展及其功能

转底炉的发展及其功能佘雪峰;孔令坛【摘要】Experiment or industrial practices on disposal of dust generated by iron and steel plant, production of sponge iron and comprehensive utilization of compound mineral were introduced briefly and the development of Rotary Hearth Furnace(RHF) was comprehensively discussed in domestic and overseas. American, Japan, China and Korea had disposed the dust and sludge generated by iron and steel plant. Hazardous elements were removed from the dust and the zinc was recycled for improving the environment. At the same time metallized pellets and hot briquette iron(HBI) were produced by RHF used as raw materials of BF. In addition, DRI produced by RHF was used as raw materials of steelmaking which can be simplified the steelmaking process. Many compound iron ore containing vanadium, titanium, boron, magnesium, rare earth were investigated in lab and industry.%在对国内外转底炉的发展进行综合论述的同时,简要介绍了转底炉在处理钢铁厂粉尘,生产海绵铁,以及复合矿综合利用方面的实验研究和工业生产实践。
国内外转底炉的发展趋势及我国发展转底炉技术的建议

• 含碳球团内,矿粉与还原剂具有良好的接触条件。在高温下 ,还原反应以高速进行。经过15~20min的还原,球团矿金 属化率即可达到88%~92%。还原好的球团经一个螺旋排料 机卸出转底炉,供电炉作炼钢原料。
属化球团经过冷却区后被排出炉外冷却,部分再氧化金属化率降低一些。煤气燃烧
及反应生成的烟气沿着与炉料转动相反的方向流动,最后流入废气净化处理及余热 回收系统。
装料 区
900~1100 ℃
预热区
烟气流动方向 1200~1400℃
还原区
1100~900℃
烧嘴
冷却区
排料区
转底炉炉底转动方向
一、国内外转底炉技术的发展过程简介
一、国内外转底炉技术的发展过程简介
DRYIRON工艺流程图
料仓
空气
换热器
烟气
混 压球机
布料器
螺旋排料
DRI料罐
布袋除尘器
一、国内外转底炉技术的发展过程简介
⑵. 干铁法
GLOBA公司(原MR&E公司)在1960年是米德兰-罗斯的快速加热工艺的技 术开发部门,1985年成为独立公司。曾经为美国Ameristeel公司的电炉粉 尘处理系统以及美国Rouge Steel公司综合钢铁厂的粉尘和污泥处理系统提 供DRYIRON法的相关设备,具备丰富的应用实绩。GLOBA公司开发的干铁法 有两项专利技术:用废糖浆作为粘结剂,利用氧化铁粉与碳粉混合物成型 的干压块方式对辊压球机压成球团后直接装入转底炉,取消了球团的烘干 程序;采用特殊的震动传送装置的炉料装入方法。可以得到金属化率大于 90%的DRI。 是一种较理想的煤基直接还原工艺。 该工艺过程中在转底炉 内的高温作用与短暂的停留时间(约10min),其操作具有巨大的灵活性, 而且设备的操作控制非常容易。考虑到上述炼铁厂粉尘和污泥处理以及还 原铁生产的需要,新日铁钢铁事业部于1999年从美国MR&E公司引进转底炉 DRYIRON法,并且争取到代理推销资格。 这是日本FASTMET法发展的基础。
我国转底炉工艺技术发展现状与前景浅析

供 少许 借鉴 与参 考 。 关键词 转底 炉 直接 还原
炼铁
1 转 底 炉 发 展 概 况 转 底 炉 ( o r er u ae 简 称 R t y H at F r c , a h n R F 工 艺 是 以一 种 煤 基 快 速 直 接 还 原 技 术 。 H ) 该 工 艺 思 想 最早 由 R s 公 司 ( de os Mir x公 司前
目前 , 国内 D I R 生产达 到工业 化规模 的 10万吨/ 0 年座 的转底 炉 , 各种直接 还原装置 直接还原技 术有转底 炉 、 回转 窑 和隧道 窑三 的生产能力 见表 2 。转底炉生产 的单 位能耗 种, 这三种工艺都 属煤基 直接还 原技 术。其 也小于 回转窑和隧道窑工艺 , 具备一定优势 。
另有多家钢铁企业规划设计上 马转底炉 ,转
转底 炉发展过程 中美 国、 国、 德 日本等 国家 都 底 炉工 艺逐 渐成 为直接还原铁领域 的一个建 相继投入力 量 开发研 究 , 先后建 立 起工 业 化 设热点 。 目前 ,国内工业规模转底 炉建设情 生产厂 。 目前该技术 已经逐渐趋 于成熟并 表 况如下 表 1 。
17 年在美 国 Elod市建 成第一 座具 有商 几年在消化吸收 国外转底 炉技术 发展 的基础 98 l o w
业意义的转底 炉 I ME C N T O工 艺起 到 现在 转 上 ,先 后有 多家企 业投 资建 设转 底炉 装置 ,
底 炉的发 展 已经 有 3 0多 年 的历 史 H 3。 在 -
第3 5卷
・
第 4期
攀枝 花科 技 与信息
( 总第 13期 ) 0
非 高炉 炼铁会 议专题 ・
我 国 转 底 炉 工 艺 技 术 发 展 现 状 与 前 景 浅 析
- 1、下载文档前请自行甄别文档内容的完整性,平台不提供额外的编辑、内容补充、找答案等附加服务。
- 2、"仅部分预览"的文档,不可在线预览部分如存在完整性等问题,可反馈申请退款(可完整预览的文档不适用该条件!)。
- 3、如文档侵犯您的权益,请联系客服反馈,我们会尽快为您处理(人工客服工作时间:9:00-18:30)。
第29卷 增刊1 北 京 科 技 大 学 学 报 Vol.29 Suppl.12007年 6月Journal of University of Science and Technology BeijingJun 2007收稿日期:2007−02−06 修回日期:2007−04−16 作者简介:朱荣(1962⎯),男,教授,博士生导师转底炉工艺的发展与实践朱 荣 任江涛 刘 纲 万天骥 徐 萌北京科技大学冶金与生态工程学院,北京 100083摘 要 论文介绍了转底炉炼铁工艺在国内外的发展概况,重点阐述北京科技大学研究和开发转底炉炼铁技术所取得的经验与成果.结合国情和政策,认为我国当前应把“转底炉预还原+熔融造气炉终还原”双联工艺作为发展转底炉技术的方向,主要应用于为电炉提供热装铁水、钢铁厂粉尘回收利用和特殊矿综合利用等方面. 关键词 转底炉工艺;含碳球团;直接还原;熔融还原 分类号 TF 748.2+06转底炉煤基直接还原是最近30年间发展起来的炼铁新工艺,主体设备源于轧钢用的环形加热炉,虽然最初的目的只是用于处理含铁废料,但很快就有美国、德国、日本等国将其转而开发应用于铁矿石的直接还原.由于这一工艺无需燃料的制备和原料的深加工,对合理利用自然资源、保护人类环境有积极的作用,因而受到了冶金界的普遍关注.在20世纪50年代,美国Midrex 公司的前身Ross 公司就发明了含碳球团的转底炉直接还原法方法,于1965~1966年在明尼苏达州的Cooley 进行了2 t ⋅h −1的小规模热固结法试验,获得了成功,后取名为Fastmet 工艺.1974年,加拿大的国际镍集团——Inmetco 公司开始研究把转底炉用于还原该公司生产不锈钢的氧化物粉尘废料,经转底炉预还原的金属化球团,直接热装入电炉生产,同时将其命名为Inmetco 工艺.之后,二者各自申请了专利,并开发和转让技术.当以Fastmet 和Inmetco 工艺为代表的两大转底炉工艺在不断进行转底炉工业化生产和推广的时候,产品硫含量过高的问题始终未得到很好解决,难以成为电炉的优质原料,因此相继出现了Fastmelt 、Redsmelt 等转底炉直接还原−埋弧式电炉熔分的双联工艺(RHF −SAF ).日本神户制钢与美国Midrex 公司联合开发转底炉直接还原新工艺,在20世纪90年代中后期取得了突破性进展,使金属化球团在转底炉中还原时熔化,生成铁块(Nuggets),同时脉石也熔化,形成渣铁分离.此法的成功,将解脱DRI 对原料品位的苛求,能用普通的高炉用铁矿为电炉提供优质铁料.因此意义重大,被命名为“第三代炼铁法”(Itmk3)[1-4].建于美国明尼苏达州北部,年产能为25000 t 的Itmk3转底炉示范厂,已于2003年5月24日投产出铁.预计Mesabi Nugget LLC 将于2006年在美国Minnesota 或者位于Indiana 的美国钢铁动力公司附近建成第一台50万t 转底炉,到2007年建成年产能150万t Iron Nugget 的生产厂.根据国内的铁矿资源和能源结构,开发具有投资少、操作简便、生产成本低等特点的转底炉工艺符合我国国情以及我国的产业政策.北京科技大学是国内第一家,也是迄今为止唯一一家转底炉工艺的研究单位.经过多年的基础研究和工艺开发,已经全面掌握了转底炉的工作原理、工艺和相关的设备设计、制造等配套技术.自主开发了转底炉−熔融造气炉双联炼铁工艺 [5]和煤基热风熔融还原炼铁工艺(Coal ,Hot-air ,Rotary Hearth Furnace Proc-ess ,简称CHARP ) [6].1 国内转底炉工业试验转底炉因具有环形炉膛和可转动的炉底而得名,其原料是铁矿粉和煤粉制成的含碳球团,经配料、混料、制球和干燥后加入转底炉中,炉膛温度可达1250~1350℃左右,含碳球团在这样的高温下,随着炉底旋转一周的过程中,铁矿被碳快速还原,生成金属化球团,最后由螺旋出料机推出炉外,经冷却后运往熔分炉作原料,或作为电炉炼钢的原料.长期以来,北京科技大学一直致力于含碳球团• 172 • 北京科技大学学报2007年增刊1还原的机理和实验研究,获得了大量的理论依据和实验数据,充分证明由含碳球团自还原作用生产金属铁是完全可以实现的.在此基础上,开始了大量的半工业、工业试验.1992年,北京科技大学和当时的舞阳钢铁公司合作,自行设计和建设了一座直径3 m,年生产能力3000 t的试验用转底炉,于1992年5月开始第一次半工业试验,同年12月至1993年2月进行了第二次半工业试验.这是在我国建设的第一座用于铁矿石直接还原的转底炉.由于设备原因和缺乏操作经验,产品的平均金属化率只达到76%~78%.1996年,北京科技大学和鞍山市科委合作,在鞍山汤岗子铁矿建成了一座转底炉试验装置,转底炉平均直径5.5 m,炉底有效宽度2.0 m,炉底面积30 m2,设计油烧嘴12个.1997年6月8日,开始热态试验,6月19日完成了第一次热试,这次试验是北京科技大学在舞阳钢铁公司的转底炉生产试验的继续.试验初步取得了良好的结果:产品的金属化率稳定,达80%~85%;操作容易,证明转底炉生产直接还原铁是可行的.北京科技大学冶金喷枪研究中心自1998年以来,一直致力于转底炉生产金属化球团——熔分炉熔分双联工艺的研究开发,并从2000年着手设计工业规模的转底炉.现在已经在山西和河南的两家钢铁公司建成了中径13.5 m, 炉底面积100 m2的转底炉2台,设计年生产能力为金属化球团矿7万t.2001年12月山西翼城的转底炉建成,举行了开炉仪式,并生产出一批合格的金属化球团矿.由于山西翼城明亮钢铁公司的高炉煤气不能持续稳定供应,转底炉炉温难以保持必要的水平,因此被迫停炉,解决煤气供应问题.河南巩义永通钢铁公司的转底炉于2003年11月试运转成功,但由于诸多因素的制约,一直处于停炉状态.2005年9月山西明亮钢铁公司、北京科技大学与山东瑞拓公司合作,对转底炉进行完善和改造,于2006年4月进行试生产,取得成功,生产出金属化球团,金属化率达到80%以上,各项经济指标达到预期的结果.2转底炉含碳球团炼铁关键技术2.1含碳球团成球技术冷固结含碳球团是实现转底炉直接还原工艺的关键因素,具有与一般氧化球团和块矿不同的还原方式,是靠内部碳进行自身直接还原,无需外部提供还原剂.还原产生的CO在球团周围形成自封闭作用,一定程度上隔绝了球团内部与环境气氛,因而使球团可在氧化性气氛下进行还原反应.含碳球团制造所采用的研磨、配料、混合设备必须保证球团的化学成分精确及矿煤的均匀混合,煤粉的粒度应在0.25 mm以下,矿粉粒度小于0.1 mm.还原剂用煤一般为无烟煤,要求固定碳>75%,挥发分<20%,低灰分,低硫.挥发分高,球团还原后强度差,不能满足熔分炉的要求.冷固结含碳球团应满足恰当的物理和力学性能,在输送、加热、还原的过程中粉化率最低.为达到这一要求,首先必须选用合适的特殊粘结剂配方,其次采用合理的造球技术.传统造球技术多采用圆盘滚球机,对原料粒度要求比较高,因此需要配备相应规格的磨料设备.目前所采用的对辊压球技术对原料粒度要求相对较低,生产率高,球团强度好.美国动力钢公司原来采用滚球技术,后来也改为压球技术.目前所生产的含碳球团的强度指标一般为:湿球0.5 m落下次数4~7次,湿球抗压6~7 kg/个;干球1 m落下次数10~15次,干球抗压75~95 kg /个.完全可以满足转底炉生产的要求.2.2转底炉喂料和出料设备转底炉内含碳球团升温、反应所需热量主要来源于炉壁、炉气的辐射传热,因此要求炉内球团薄层均匀布料.根据这一特点,研制出振动布料机,实现在转底炉炉底横向、径向都均匀布料,避免机械强度有限的球团破碎,避免原料堆积和料层不均.振动给料机兼有筛除球团粉末的作用.该装置易于维护,且允许在各种生产率下操作.螺旋出料机的功能是将还原后的金属化球团卸出炉外,因处理的金属化球团温度为1000℃左右,所以必须耐热耐磨,螺旋采用水冷,叶片上堆焊硬质合金,由北京科技大学冶金喷枪研究中心专门设计.该装置可使成品金属化球团从炉膛顺利排出且不产生大量粉末,螺旋本身也易于拆卸和维修.2.3金属化球团冷却设备不同于氧化球团,高温金属化球团在大气中易于氧化,因此,设计金属化球团冷却机时应考虑到防止再氧化.熔分炉采用热装时同样需要采取防氧化的措施.2.4 炉子热工转底炉高温快速还原,关键炉温必须保持在1350℃左右,国外使用天然气为燃料,容易实现大于1350℃的炉温.我们采用发生炉煤气或者高炉煤气,实现办法主要采取高风温和煤气预热.另一方Vol.29 Suppl.1朱荣等:转底炉工艺的发展与实践• 173 •面,预热段、还原段应喷吹二次空气并形成强紊流,使得预热段产生的挥发分和还原产生的CO在炉内快速、充分地燃烧(后燃烧),以便弥补球团还原强烈吸热,节约外部燃料消耗.在炉子还原末段,为了避免球团层上表面再氧化,则应严格控制二次空气流的进入,且控制烧嘴燃烧在亚化学计量条件下进行,以保持该区域一定的还原性气氛.烧嘴设计应最大程度确保:在炉料上提供均匀的温度分布,防止局部过热;降低扰动和炉料附近的搅拌,以消除被CO2和H2O再氧化.根据还原过程的要求控制炉内各段的温度和气氛,从而优化各段烧嘴的布置.3转底炉炼铁从直接还原到熔融还原的过渡原来冶金界希望由转底炉生产出来的金属化球团能够直接作为炼钢原料,并为此努力了很多年.但是由于转底炉工艺以含碳球团为原料,所得到的产品中既包括了矿粉中的脉石,又增加了煤灰分,导致产品中的TFe含量低.因此,必然要求选用高品位精矿粉以及低灰分煤.转底炉直接还原工艺另一个难以克服的难点是原料中硫含量绝大部分保留在金属化球团产品中,过高的硫含量显然不适用于炼钢的要求.于是,国外研究者不得不将目光转向预还原金属化球团+熔分生产铁水的工艺路线,主要采用埋弧电炉与转底炉相匹配,结果每吨铁水耗电500~550 kWh,不符合我国国情.在这样的背景下,北京科技大学自主开发了转底炉预还原+热装终还原熔分炉的工艺,见图1.熔分炉,又名熔融造气炉,类似于COREX的终还原炉,不同的是它不用氧气,而用高温热风(1200℃).金属化球团从上部热装入炉(1000℃),可充分利用原料的物理热.熔融造气炉每生产 1 t 铁水,大约使用300 kg型煤,可以节约焦炭及焦煤资源.金属化球团在熔融造气炉内进一步还原、熔化,使渣铁分离,调节炉渣的碱度,可使大部分硫进入到炉渣中,有较强的脱硫作用,既保证了铁水质量又减少了SO2向大气的排放.熔融造气炉与转底炉相匹配,无论在技术上还是在经济上都实现了最佳配合和互补,转底炉为熔融造气炉提供了优质的原料,即金属化球团,实现了无焦炼铁.熔分的结果使原料的脉石和有害杂质去除,获得优质铁水.熔融造气炉还可分担一部分还原任务,从而提高了转底炉的生产率.熔融造气炉的副产品煤气除了可用于热风炉,还可作为转底炉的燃料.图1转底炉——熔分炉双联炼铁工艺流程图4转底炉熔融还原炼铁的应用转底炉熔融还原炼铁存在的主要问题仍在于转底炉薄层炉料操作导致整个工艺的生产率低.目前为止最大的转底炉单炉产量是动力钢公司的年产60万t金属化球团,这样的产量不足以进入钢铁生产主流程.目前转底炉熔融还原炼铁主要应用于:(a)为电炉短流程提供热装铁水;(b)钢铁厂粉尘回收利用;(c)特殊矿综合利用.如何解决厚料层的还原是实现提高生产规模的关键,我们正在致力于这方面的实验研究.5结论转底炉直接还原生产金属化球团直接供给电炉作炉料必须用高品位的铁矿和低灰分低硫煤,否则影响电炉产量和质量;而且转底炉要另供煤气作燃料.转底炉与熔分炉相匹配,使熔分炉获得金属化原料,从而大大提高生产效率;缓解了直接还原受原料品位的制约,使普通高炉用的矿源和普通煤种也可用于直接还原,这对我国发展直接还原具有现实意义.反过来,熔分炉又为转底炉提供煤气作为燃料,同时充分利用转底炉烟气余热,率先采用助燃风和煤气双预热的蓄热式烧咀,在热工上实现了• 174 • 北京科技大学学报2007年增刊1突破.转底炉熔分炉双联工艺,与传统的高炉工艺(含烧、焦)相比,投资省、成本低、环保好,具有良好的经济效益和社会效益.参考文献[1] Nagata K, Kojima R, Murakami T, et al. Mechanisms of pig-ironmaking from magnetite ore pellets containing coal at low tem-perature. ISIJ Int,2001,41(11):1316[2] Sawa Y, Yamamoto T, Takeda K, et al. New coal-based processto produce high quality DRI for the EAF. ISIJ Int,2001,41(Suppl):S17[3] 晓苏. Itmk3——第三代煤基直接还原炼铁技术. 钢铁,2002,37(6):40[4] Tsuge O, Kikuchi S, Tokuda K, et al. Successful iron nuggetsproduction at Itmk3 pilot plant. Ironmaking Con Proc,2002: 511 [5] 万天骥. 直接还原铁熔分造气炉.专利,200420005647.5.2004-03-02[6] 万天骥,任大宁,孔令坛,等. 煤基热风转底炉熔融还原炼铁法:中国专利,CN1443856A. 2003-9-24Development and practice on the rotary hearth furnace ironmaking processZHU Rong, REN Jiangtao, LIU Gang, WAN Tianji, XU MengMetallurgical and Ecological Engineering School, University of Science and Technology Beijing, Beijing 100083,ChinaABSTRACT The development of the rotary hearth furnace (RHF) ironmaking process at home and abroad was introduced. Emphasis was paid on elucidating the achievement and experience on the course of the research on RHF technology by University of Science and Technology Beijing. Based on chinese conditions and policies, the combined process of RHF pre-reduction and melting-gasifying furnace should be considered as the orienta-tion to develop RHF technology, which should be mainly applied to supplying hot metal to EAF, recovery of dust from these iron and steel plants, and comprehensive utilization of special ores etc.KEY WORDS rotary hearth furnace process; ore/coal composite pellets; direct reduction; melting reduction。