转底炉工艺设备简介PPT演示文稿
转底炉 (2)
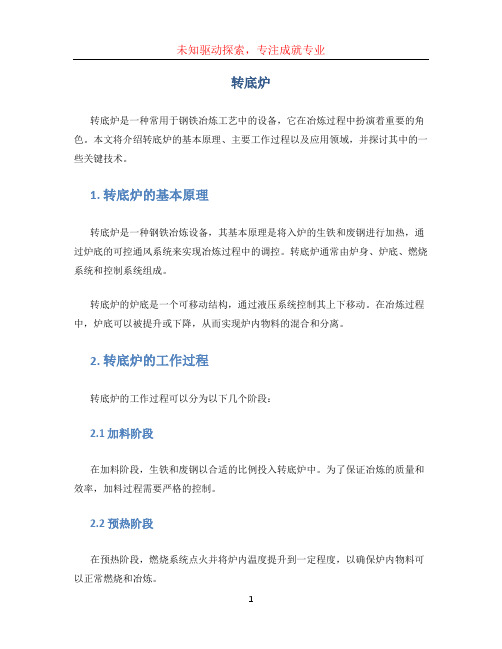
转底炉转底炉是一种常用于钢铁冶炼工艺中的设备,它在冶炼过程中扮演着重要的角色。
本文将介绍转底炉的基本原理、主要工作过程以及应用领域,并探讨其中的一些关键技术。
1. 转底炉的基本原理转底炉是一种钢铁冶炼设备,其基本原理是将入炉的生铁和废钢进行加热,通过炉底的可控通风系统来实现冶炼过程中的调控。
转底炉通常由炉身、炉底、燃烧系统和控制系统组成。
转底炉的炉底是一个可移动结构,通过液压系统控制其上下移动。
在冶炼过程中,炉底可以被提升或下降,从而实现炉内物料的混合和分离。
2. 转底炉的工作过程转底炉的工作过程可以分为以下几个阶段:2.1 加料阶段在加料阶段,生铁和废钢以合适的比例投入转底炉中。
为了保证冶炼的质量和效率,加料过程需要严格的控制。
2.2 预热阶段在预热阶段,燃烧系统点火并将炉内温度提升到一定程度,以确保炉内物料可以正常燃烧和冶炼。
2.3 冶炼阶段在冶炼阶段,炉底开始下降,炉内的物料在高温和高压的环境下进行冶炼反应。
冶炼过程中,炉内的废气通过翻转炉顶部的排气系统排出,同时新鲜空气通过炉底通风系统进入炉内维持燃烧所需的氧气供应。
2.4 炉底升起和排渣阶段在冶炼结束后,炉底开始升起,炉内产生的废渣通过炉底排渣装置排出。
同时,炉内残余渣和铁水经过冷却后也会从炉底排出。
3. 转底炉的应用领域转底炉主要应用于钢铁冶炼和废钢回收工艺中。
由于其灵活性和可控性,转底炉在这些工艺中被广泛使用。
转底炉可以适应不同种类和比例的原料,包括生铁、废钢、废铁等。
同时,转底炉还可以通过控制炉底的升降速度和炉内通风系统的调节来调整冶炼过程中的溶解度和升降速度。
4. 转底炉的关键技术转底炉作为一种复杂的冶炼设备,涉及到多种关键技术。
以下是其中的一些关键技术:4.1 燃烧系统转底炉的燃烧系统需要能够提供足够的热量来加热炉内物料,并确保燃烧的充分和稳定。
常用的燃料包括焦炭、天然气和重油等。
4.2 炉底控制系统转底炉的炉底控制系统需要能够准确地控制炉底的升降速度,以及炉内通风系统的调节。
转炉炼钢工艺课件
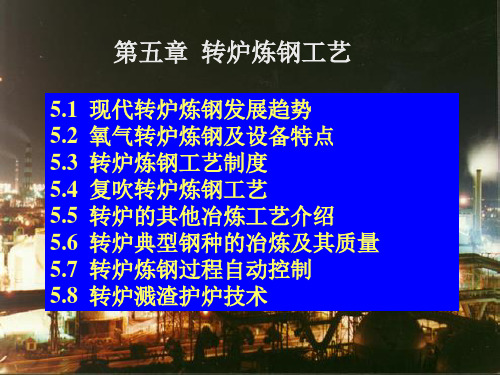
5.3.1 原料装入制度
不同的转炉,以及同一转炉在不同的生产条件 下,都有其不同的合理的金属装入量。
装入量过大,喷溅增加,熔池搅拌不好,造渣 困难,炉衬特别是炉帽寿命缩短,供氧强度也 因喷溅大而被迫降低。
装入量过小,炉产量减少。因熔池过浅,炉底 容易受来自氧气射流区的高温和高氧化铁的循 环流冲击,甚至损坏炉底。
回收→三通阀→水封逆止阀→V形水封→煤气柜 风机
放散→旁通阀→放散烟囱
LT法净化、回收系统工艺流程
LT法净化、回收系统工艺流程
未燃烟气(800~1000 ℃ )→活动罩裙→冷却烟道(或余热锅炉)→蒸发冷却器
(蒸发冷却塔)→煤气冷却(150~200℃) 、干燥(水雾蒸发)、除粗尘→
干粗尘
回收→三通阀→冷却塔→煤气柜
补炉长瓢 (与炉前共用);
补炉短瓢 (与炉前共用); 撬捧(与炉前共用); 长撬捧;泥塞棒;
氧气皮管, 氧气管
(与炉前共用); 铁锹;鎯头
(与炉前共用); 出钢口塞; 挡渣球。
炉后用具示意图
炉后操作用具
•转炉简介 •转炉解剖 •现场转炉炉内演示 •补炉操作程序
请单击画面
转炉是炼钢 的反应容器, 它由炉帽、 炉身和炉底 组成。在炉 帽和炉身的 连接处安置 一个出钢口
现 场 转 炉
兑铁水 加废钢
操 作
请单击画面
5.3.1 原料装入制度
装料工艺对转炉炼钢的技术经济指标有明显的 影响。
对使用废钢的转炉,如先装废钢后兑铁水,为 了保护炉衬不被废钢击伤,应先加洁净的轻废 钢,再加中型和重型废钢。过重的废钢,最好 在兑铁水后加入。
为了防止炉衬过分急冷,装完废钢后应立即兑 入铁水。
转炉双渣工艺课件PPT
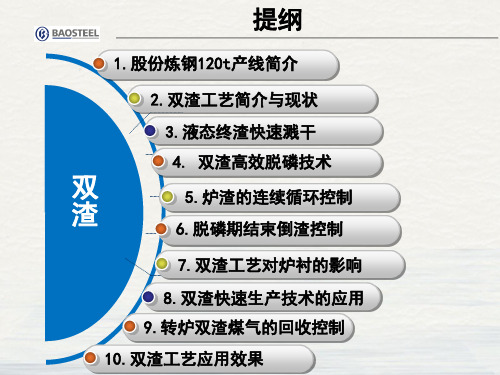
双渣工艺简介
转炉双渣法优点
1、利用前一炉高碱度的脱碳炉渣,自由CaO含量多,保留在下一炉脱硅 脱磷期继续使用,经过前期脱磷后,前期渣倒出部分后,第二次吹炼 可少渣冶炼,从而减少辅料和钢铁料消耗。
脱磷反应式:2[P]+5(FeO)+4(CaO)=(4CaO•P2O5)+5[Fe] 常规冶炼转炉终点渣(T.Fe)含量15-25%,碱度3.0~4.0,转炉双渣 法冶炼前期倒渣时渣中(T.Fe)含量7~13%,碱度一般1.3~1.6,因此, 既能减少石灰等造渣辅料消耗,又能降低钢铁料消耗。理论计算,前 期渣倒出10~15吨,渣量减少10~15%,可降低钢铁料消耗4~7kg/t.s。 2、常规转炉炼钢工艺,出钢后留在炉内的部分钢水随炉渣一起倒出,采 用留渣双渣法以后,出钢后不倒渣,可以提高钢水收得率。如出钢后 留在转炉内的钢水0.5~1.5吨,吨钢降低钢铁料消耗1.7~5.0kg/t.s。
25%
5% 10%
本科学历
技校
专科
铁水包搅拌脱硫设备组成
主要设备
(1)铁水包倾翻台车 (2)铁水包 (3)倾翻台车 (4)渣罐 (5)除尘烟罩 (6)扒渣机 (7)测温取样枪 (8)搅拌桨及其升降装置 (9)混合料储料仓 (10)受料仓
喷吹脱硫设备包括2套独立的 脱硫装置,KR脱硫是由1套双 工位装置组成。
270
0.01
7.74 91.53 8.48
275
八钢炼钢石灰进料及质量等级分布
八钢使用石灰为外购石灰,质量较国内先进炼钢厂差。
双渣工艺开发初期面临主要问题
脱磷期脱磷不充分,达不到50% 半钢倒渣量不足,仅为30%,造成连续循 环不起来 半钢渣中带金属铁明显
八钢双渣工艺开发目标
转体炉工艺
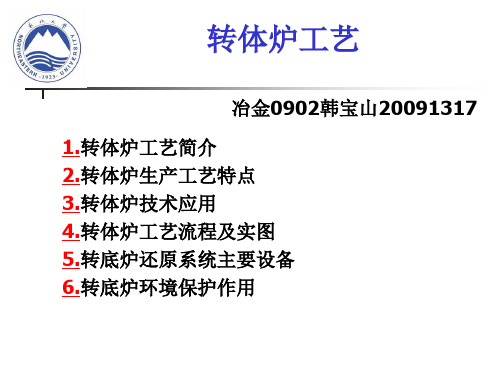
1250下℃加热25分钟,金属化率88%
转底炉应用之三
将V、Ti磁铁矿中的铁精矿、钛精矿制成含炭球团,经转底炉预 还原,再用电炉或矿热炉进行终还原和熔分。
2.转体炉生产工艺特点
1)以煤粉作为还原剂, 仅用少量煤气, 对煤的质量要 求也没有回转窑法那么严格, 故有利于广泛应用。 2)主要设备为环形转底炉,与回转窑相比,该工艺设备 较简单、投资省、能耗较低。 3) 对炉料的强度要求不高。因为料层很薄炉料既不 受压且随炉底一起转动,炉料与炉底之间没有相对运动,可 用含碳生球团.(10~20min) ,操作容易。 4)转底炉工艺可直接使用含铁废粉料(或粉矿)和 粉煤, 在矿石和能源上具有很好的适应性和经济性。金属 化率可达80%以上。
6.转底炉环境保护作用
1、转底炉使用净化的煤气作燃料,并且炉料在炉膛内无相对运动,排出的废 烟气中含尘为20_50 mg/m3,大大低于国家规定的标准:一类100 mg/m3; 二类150 mg/m3。 2、生产过程无污水和固体废弃物排放,工艺工程产生的粉尘可以全部重新利 用。 3、转底炉工艺是含碳球团的直接还原,其中煤中的硫只有极少量的通过烟气 排出,大部分固结在金属化球团内。 4、如果转底炉生产金属化球团加入高炉,代替烧结矿和球团矿,可以大大降 SO2的排放,并以普通煤代替资源紧缺的焦炭,大大降低了传统高炉冶炼对 环境的危害。 5、转底炉直接还原、熔融还原工艺是国家明确鼓励支持的冶金新技术,并且 对于处理钢铁厂尘泥具有较大的优势,是发展循环经济的可行的手段。 6、转底炉工艺需要考虑的环保措施主要是控制粉尘排放,如原料处理、转运、 转底炉出料过程产生的灰尘。
顶底复吹转炉培训PPT课件

图4吹炼终点[C]和[O]之间的关系
第16页/共71页
图5渣中铁含量与终点碳的关系
第17页/共71页
图6 终点[c]和吹炼终点[Mn]的关系
第18页/共71页
残锰的变化大
后期温度
终碳 过程返干
0.14%
铁水锰 2007.2 取样分析 铁水锰0.20% 残锰 ?
铁水锰0.32% 残锰 ?
第54页/共71页
第55页/共71页
济钢三炼钢副枪系统 副枪
第56页/共71页
探头
第57页/共71页
副枪夹持器
第58页/共71页
副枪与探头连接
第59页/共71页
副枪准备测量旋转过程中
第60页/共71页
副枪测量过程中
第61页/共71页
测量完毕从副枪孔拔出
第62页/共71页
测量完毕旋转至取枪位
第23页/共71页
第24页/共71页
第25页/共71页
(二) 底吹供气模式 • 1.底部供气采用N2、Ar2切换方式,根 据吹炼期的不同循环供气;底部供气总 管压力应≥1.2MPa。 • 2. 供气强度调节范围从0.005m3/ min.t到0.10m3/min.t。 • 3.冶炼的绝大多数钢种,供气强度最大 值在0.07~ 0.10m3/min.t。
缺点: 底吹转炉成渣困难,但可以通过底部供气喷
嘴向熔池喷入石灰粉,从而改善了脱P、S的 条件。由于从转炉底部供入氧气,喷嘴需要 冷却,一般是用碳氢化合物为冷却介质,所 以冶炼终点钢中氢含量较高。
第5页/共71页
氧气顶吹转炉 氧气底吹转炉 氧气侧吹转炉
顶底复吹转炉
第6页/共71页
3、顶底复合吹炼的种类 • 迄今为止用来作为搅拌钢水的气体: • 氧气
转底炉
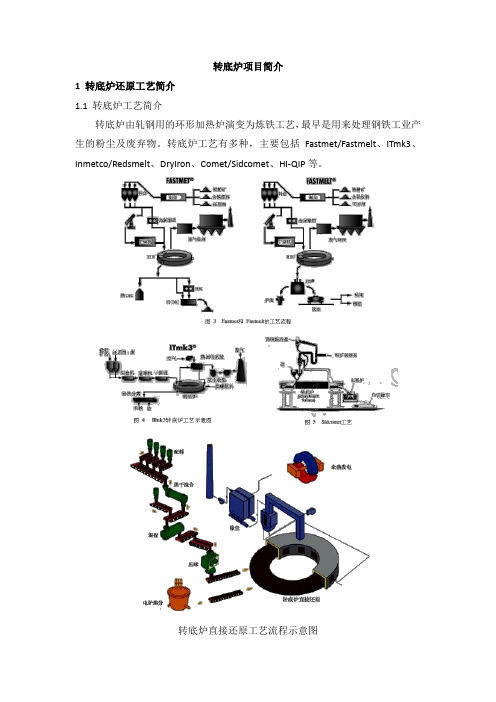
转底炉项目简介1 转底炉还原工艺简介1.1 转底炉工艺简介转底炉由轧钢用的环形加热炉演变为炼铁工艺,最早是用来处理钢铁工业产生的粉尘及废弃物。
转底炉工艺有多种,主要包括Fastmet/Fastmelt、ITmk3、Inmetco/Redsmelt、DryIron、Comet/Sidcomet、HI-QIP等。
转底炉直接还原工艺流程示意图1.2 转底炉工艺与其它相似工艺比较转底炉是煤基直接还原工艺中的核心设备之一,煤基直接还原工艺主要包括回转窑法(如SL-RN法)和转底炉法(如COMET法)。
而煤基直接还原工艺和气基直接还原工艺都是直接还原工艺,以铁产品为例直接还原工艺的产品为海绵铁(又称直接还原铁—DRI即Direct Reduced Iron)。
直接还原和熔融还原是两种主要的非高炉炼铁思路。
当转底炉的原料加入含碳球团时,其产品为金属化球团,可供电炉使用,也作为高炉的原料。
而链篦机—回转窑—环冷机(链回环)生产出来的产品是氧化球团,是为高炉炼铁提供的原料之一,称之为球团矿,而高炉炼铁的含铁原料还包括天然块矿、烧结矿。
转底炉直接还原技术采用含碳球团作原料,反应速度快,同时符合中国以煤为主要能源的特点。
以直接还原技术用于钒钛磁铁矿为例,转底炉技术相比隧道窑、回转窑工艺,以ITmk3为代表的转底炉工艺的优点主要是:○1还原原料在预热和还原过程中始终处于静止状态下随炉底一起进行,所以对生球强度要求不高;○2较高的还原温度(1350℃或更高)、反应快、效率高。
反应时间可在10-50min范围,可与矿热电炉熔炼容易实现同步热装;○3可调整喷入炉内燃料(可以是煤粉、煤气或油)和风量,能准确控制炉膛温度和炉内气氛;○4过程能耗低,回转窑法折算成每吨海绵铁的煤耗通常大于800kg,而转底炉法为600kg;○5从工艺角度来看,ITmk3技术流程简单,投资成本低,产品价格低,铁矿石原料及还原剂选择灵活。
另外,据马鞍山钢铁设计研究总院秦廷许的研究:转底炉-电炉炼铁流程与高炉传统炼铁流程比较,虽在铁精矿消耗量、还原剂和燃料的能源消耗量上相差不大,但吨铁成本低约10%;基建投资省22%左右;全流程电耗低48.6%。
转炉炼钢设备与工艺235页-BD

转炉炉型
C 截锥型 截锥型熔池为上大下小的圆锥台。其特点是构造简单且平底熔池便
于修砌这种炉型基本上能满足炼钢反应的要求适用于小型转炉。我国 30t 以下的转炉多用这种炉型。国外转炉容量普遍较大故极少采用此 种形式。
此外,有些国家(如法国、比利时、卢森堡等)的转炉,为了吹炼高 磷铁水,在吹炼过程中用氧气向炉内喷入石灰粉。为此他们采用了所 谓大炉膛炉型,这种炉型的特点是:炉膛内壁倾斜,上大下小,炉帽 的倾角较小(约50 °)。因为炉膛上部的反应空间增大,故适应吹炼 高磷铁水时渣量大和泡沫化严重的特点。这种炉型的砌砖工艺比较复 杂,炉衬寿命也比其他炉型低,故一般很少采用。
计算方法:
推荐经验公式:
DK
G t
D:熔池直径,m
G:新炉金属装入量,t
t: 吹氧时间,min
K:比例系数,可参考下表:
50t以下: 1.85~2.10
50~120t: 1.75~1.85
200t: 1.55~1.60
250t以上:1.50~1.55
炉型主要尺寸的确定
转炉冶炼周期和吹氧时间推荐值
转炉公称容量/t 吹炼周期/min 吹氧时间/min
炼钢技术—设备与工艺
提纲
1.炼钢原理 2.炼钢方法 3.炼钢方法的发展演变 4.转炉炼钢车间设备组成 5.转炉炼钢工艺 6.钢水炉外精炼技术
炼钢原理
❖ 根据所炼钢种的要求把生铁中的含碳量去除到规定范围,并使其 它元素的含量减少或增加到规定范围的过程。
❖ 简单地说,是对生铁降碳、去硫、磷、调硅、锰含量的过程。这 一过程基本上是一个氧化过程,是用不同来源的氧(如空气中的氧、 纯氧气、铁矿石中的氧)来氧化铁水中的碳、硅、 锰等元素。
转炉的公称容量
《顶底复吹转炉培训》课件
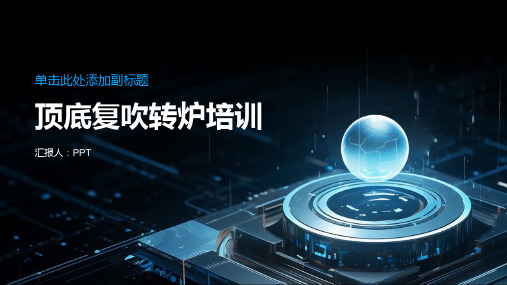
未来发展趋势与展望
顶底复吹转炉技术不断创新和完善 智能化、自动化水平不断提高 环保要求日益严格,绿色生产成为趋势 培训内容更加丰富和全面,提高员工素质
感谢观看
汇报人:PPT
维护记录:对每次检查和维修的情况进行记录,包括维修时间、维修内容、更换部件等 信息,方便后续管理和参考。
培训与指导:对操作人员进行培训和指导,提高其对顶底复吹转炉的维护保养意识和技 能水平,确保设备的正常运行和延长使用寿命。
故障排除与预防措施
常见故障及原因分析
故障排除方法与步骤
预防措施建议
维护保养注意事项
添加标题
添加标题
添加标题
添加标题
热量传递过程:炉顶和炉底的热 量通过辐射、对流和传导传递到 炉内熔池
热量传递影响因素:炉顶和炉底 的材质、结构以及操作参数等都 会影响热量传递效率
04
顶底复吹转炉操作规程
操作前准备
检查设备:确认转炉及其附属设备完好,无故障隐患 准备工具:准备好所需的工具和材料,如吹氧管、氮气等 确认安全:确认现场安全,无人员或其他障碍物影响操作 了解操作流程:熟悉顶底复吹转炉的操作流程和注意事项
添加项标题
顶底复吹转炉气体流动原理:炉内气体通过顶底复吹的方式进行 流动,实现金属的熔炼和氧化反应。
添加项标题
气体流动方向:炉内气体从炉顶进入,通过炉底排出,形成循环 流动。
添加项标题
气体成分:炉内气体主要由氧气、氮气、二氧化碳等组成,根据 不同的冶炼阶段,气体成分会有所变化。
添加项标题
气体流动速度:炉内气体流动速度与冶炼工艺、炉内温度等因素 有关,合理的控制气体流动速度可以提高冶炼效率。