轮胎、轮辋及气门嘴标准精选(最新)
轮毂与轮胎的匹配标准
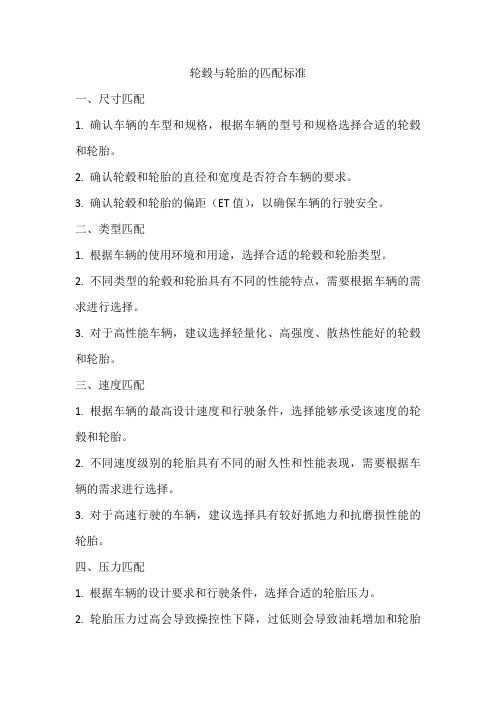
轮毂与轮胎的匹配标准
一、尺寸匹配
1. 确认车辆的车型和规格,根据车辆的型号和规格选择合适的轮毂和轮胎。
2. 确认轮毂和轮胎的直径和宽度是否符合车辆的要求。
3. 确认轮毂和轮胎的偏距(ET值),以确保车辆的行驶安全。
二、类型匹配
1. 根据车辆的使用环境和用途,选择合适的轮毂和轮胎类型。
2. 不同类型的轮毂和轮胎具有不同的性能特点,需要根据车辆的需求进行选择。
3. 对于高性能车辆,建议选择轻量化、高强度、散热性能好的轮毂和轮胎。
三、速度匹配
1. 根据车辆的最高设计速度和行驶条件,选择能够承受该速度的轮毂和轮胎。
2. 不同速度级别的轮胎具有不同的耐久性和性能表现,需要根据车辆的需求进行选择。
3. 对于高速行驶的车辆,建议选择具有较好抓地力和抗磨损性能的轮胎。
四、压力匹配
1. 根据车辆的设计要求和行驶条件,选择合适的轮胎压力。
2. 轮胎压力过高会导致操控性下降,过低则会导致油耗增加和轮胎
磨损。
3. 建议定期检查轮胎压力,以确保其处于正常范围内。
五、品牌匹配
1. 选择知名品牌的轮毂和轮胎,以确保质量和安全性。
2. 不同品牌的轮毂和轮胎具有不同的性能和质量特点,需要根据车辆的需求进行选择。
3. 对于高端车型,建议选择与原车配套的品牌和型号,以确保与车辆的整体性能相匹配。
轮辋规格

轮胎知识轮辋俗称轮圈,是车轮周边安装轮胎的部件。
我国轮辋规格代号,基本上与国际接轨。
其名义宽度和名义直径用英寸表示。
中间的联结符号(*或-)表示是否整体轮辋。
例如:4.50E*16表示名义宽度为4.5英寸,轮缘代号为E的整体轮辋。
6.5-20表示名义宽度为6.5英寸,名义直径为20英寸的多件式平底宽轮辋。
在使用时,汽车的轮辋规格是很重要的。
它决定汽车可以装用哪些轮胎。
1,国产轮辋轮廓类型及其代号目前轮辋轮廓类型有7种,深槽轮辋:代号DC,—深槽宽轮辋:代号WDC,半深槽轮辋:代号SDC,平底轮辋:代号FB,平底宽轮辋:代号WFB,全斜底轮辋:代号TB,对开式轮辋2代号DT。
轮辋的结构形式,根据其主要由几个零件组成分为:一件式轮辋\二件式轮辋、三件式轮辋\四件式轮辋和五件式轮辋。
一件式轮辋具有深槽的整体式结构。
二件式轮辋可以拆卸为轮辋体和弹性挡圈二个主要零件。
三件式轮辋可以拆卸为轮辋体、挡圈和锁圈三个主要零件。
四件式轮辋可以拆为轮辋体、挡圈、锁圈和座圈四个主要零件;也可以拆为轮辋体、锁圈和两个挡圈。
五件式轮辋可以拆卸为轮辋体\挡圈、锁圈、座圈和密封环五个主要零件示。
2,国产轮辋的规格代号轮辋规格用轮辋名义宽度代号\轮缘高度代号\轮辋结构形式代号\轮辋名义直径代号和轮辋轮廓类型代号来共同表示。
轮辋名义宽度和名义直径代号的数值是以in(英寸)表示(当新设计轮胎以mm表示直径时,轮辋直径用mm表示)。
直径数字前面的符号表示轮辋结构形式代号—,符号“X”表示该轮辋为一件式轮辋,符号“一”表示该轮辋为两件或两件以上的多件式轮辋。
在轮辋名义宽度代号之后的拉丁字母表示轮缘的轮廓(E、F、J、JJ、KB、L、V等)。
有些类型的轮辋(如平底宽轮辋),其名义宽度代号也代表了轮缘轮廓,不再用字母表示。
最后面的代号表示了轮辋轮廓类型代号。
例如:北京BJ2020型汽车轮辋为4.50Ex16,表示该轮辋名义宽度4.5in,名义直径16in,轮缘轮廓代号为E的一件式深槽轮辋。
新轮胎的检验标准

新轮胎的检验标准因国家和地区而异。
在中国,根据《中华人民共和国国家标准:机动车安全技术检验项目及方法》规定,注册登记和在用机动车的安全检验时,乘用车、挂车轮胎胎冠上花纹深度应大于或等于1.6毫米。
此外,轮胎花纹检查也是重要的一环,新轮胎的凹槽约为8毫米,当磨损至3-4毫米时,轮胎性能将开始下降,制动、抓地力等能力将开始下降。
使用限制为1.6毫米,如果接近这个标准,一定要更换轮胎。
新轮胎的检验标准是确保车辆行驶安全的重要环节。
在购买新轮胎时,消费者需要了解相关的检验标准,以便选择符合要求的优质产品。
以下是关于新轮胎检验标准的详细介绍:1. 外观检查首先,消费者需要对新轮胎进行外观检查。
这包括观察轮胎表面是否有明显的损伤、磨损或裂缝。
同时,还要检查轮胎上的生产日期和批次号,以确保购买到的产品是新鲜的。
此外,还需要检查轮胎的花纹深度,因为花纹深度直接影响到轮胎的抓地力和排水性能。
2. 尺寸检查新轮胎的尺寸必须与车辆原装轮胎相匹配。
消费者可以通过查看车辆说明书或者咨询专业人士来了解所需轮胎的尺寸。
在购买时,务必核对轮胎上的尺寸标识,确保所购产品与车辆要求相符。
3. 负荷指数和速度等级新轮胎的负荷指数和速度等级是衡量轮胎性能的重要指标。
负荷指数表示轮胎所能承受的最大载重,速度等级则表示轮胎所能承受的最高速度。
消费者在购买新轮胎时,需要根据车辆的实际使用情况选择合适的负荷指数和速度等级。
一般来说,负荷指数和速度等级越高,轮胎的性能越好,但价格也相对较高。
4. 耐磨性能新轮胎的耐磨性能直接影响到使用寿命。
消费者可以通过查看轮胎上的耐磨指数来判断其耐磨性能。
耐磨指数越高,轮胎的使用寿命越长。
此外,还可以通过查看轮胎的生产厂家和品牌来了解其产品质量和口碑。
5. 舒适性能新轮胎的舒适性能对于提高驾驶体验至关重要。
消费者可以通过试驾或者查阅相关评测来了解不同品牌和型号轮胎的舒适性能。
一般来说,高品质轮胎在行驶过程中能够有效降低噪音、减少震动,提高驾驶舒适度。
轮胎相关的团体标准

轮胎相关的团体标准
随着汽车行业的发展,轮胎作为汽车的重要零部件之一,其相关标
准也越来越重要。
下面将对轮胎相关的团体标准进行介绍。
一、ISO标准
1. ISO 4000:针对轮胎轮辋连接的尺寸、类型和配件进行了规定。
2. ISO 18164:2019:规定了轮胎标准的术语和定义,以及轮胎的性能要
求和试验方法。
二、中国GB标准
1. GB 9744:重型汽车用轮胎的通用技术条件。
2. GB/T 521-2012:轮胎标志、花纹和尺寸等规定。
三、美国TRAC标准
1. TRAC号码:根据轮胎的尺寸、载荷和速度等信息分配的标准号码。
2. TRAC报告:根据轮胎试验数据发布的性能评定报告。
四、欧洲ECE标准
1. ECE R30:针对汽车使用的轮胎进行了技术要求和试验方法的规定。
2. ECE R54:2017:规定了用于卡车和公共汽车等商用车辆的轮胎性能
要求、试验方法和标志规定。
五、日本JIS标准
1. JIS D4230:轮胎的尺寸、载荷能力和速度能力等进行了规定。
2. JIS D4215:规定了轮胎颜色、标志和标识等。
以上是一些轮胎相关的团体标准,这些标准的制定和遵守有助于确保轮胎的品质和安全性,同时也方便了消费者的选择和购买。
在购买轮胎时,应当注意选择符合相关标准的产品,以保障安全和车辆性能的稳定。
轮胎标准规格参数和胎压

轮胎标准规格参数和胎压一、导言轮胎是汽车的重要组成部分,它直接影响到汽车的性能、操控性和安全性。
了解轮胎的标准规格参数和正确的胎压是非常重要的,本文将详细介绍轮胎的标准规格参数和胎压相关知识。
二、轮胎标准规格参数1. 轮胎尺寸轮胎尺寸是指轮胎的直径、宽度、断面高度等参数。
通常以三个数字表示,例如185/65 R15,其中185代表轮胎的宽度(单位:毫米),65代表轮胎的断面高度与宽度之比(单位:百分比),R代表轮胎的结构形式(往往是放射式),15代表轮胎安装的轮毂直径(单位:英寸)。
2. 载重指数载重指数是指轮胎能承受的最大负荷。
它由一个数字表示,例如91,每个数字对应着一定的负荷范围。
具体的对照表可以在轮胎的侧壁上找到。
3. 速度级别速度级别是指轮胎的最高使用速度。
它由一个字母表示,例如H,每个字母代表一定的速度范围。
具体的对照表可以在轮胎的侧壁上找到。
4. 轮胎结构轮胎的结构形式主要有斜交式(B)和放射式(R)两种。
斜交式轮胎通常用于卡车等载重大的车辆,而放射式轮胎则用于轿车等普通车辆。
三、胎压相关知识1. 胎压的重要性正确的胎压是保证车辆行驶安全和轮胎寿命的关键因素。
过低或过高的胎压都会影响到车辆的操控性能和轮胎的使用寿命。
2. 胎压的检查与调整a. 检查胎压:应该定期检查轮胎的胎压,特别是在行驶前或长时间停车后。
可以使用胎压计来测量轮胎的胎压,胎压应该与汽车制造商提供的标准胎压相符合。
b. 调整胎压:如果发现轮胎的胎压过低或过高,应该及时调整胎压。
调整胎压时,应该参考汽车制造商提供的标准胎压,并使用胎压计逐渐调整到合适的数值。
3. 胎压对行驶性能的影响a. 胎压过低:当轮胎的胎压过低时,轮胎的侧壁会受到较大的挤压,导致轮胎发热、胎纹磨损加剧,并且增加了爆胎的风险。
此外,胎压过低还会导致车辆操控性能下降,制动距离增加。
b. 胎压过高:当轮胎的胎压过高时,轮胎的接地面积减小,导致轮胎与地面的摩擦力减小,影响了车辆的抓地力和操控性能。
轮胎标准规格参数和胎压
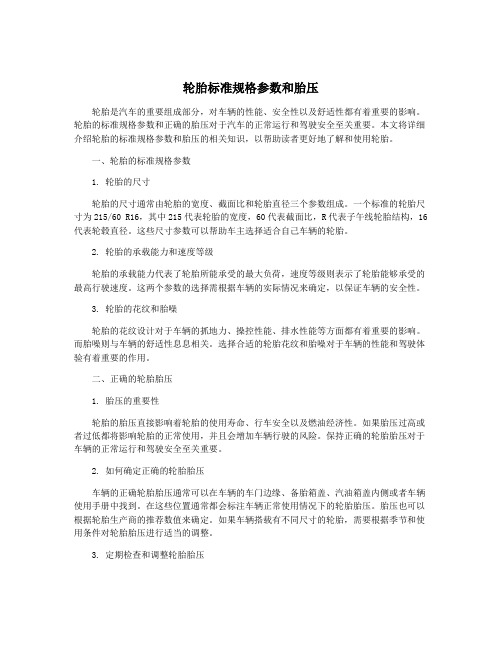
轮胎标准规格参数和胎压轮胎是汽车的重要组成部分,对车辆的性能、安全性以及舒适性都有着重要的影响。
轮胎的标准规格参数和正确的胎压对于汽车的正常运行和驾驶安全至关重要。
本文将详细介绍轮胎的标准规格参数和胎压的相关知识,以帮助读者更好地了解和使用轮胎。
一、轮胎的标准规格参数1. 轮胎的尺寸轮胎的尺寸通常由轮胎的宽度、截面比和轮胎直径三个参数组成。
一个标准的轮胎尺寸为215/60 R16,其中215代表轮胎的宽度,60代表截面比,R代表子午线轮胎结构,16代表轮毂直径。
这些尺寸参数可以帮助车主选择适合自己车辆的轮胎。
2. 轮胎的承载能力和速度等级轮胎的承载能力代表了轮胎所能承受的最大负荷,速度等级则表示了轮胎能够承受的最高行驶速度。
这两个参数的选择需根据车辆的实际情况来确定,以保证车辆的安全性。
3. 轮胎的花纹和胎噪轮胎的花纹设计对于车辆的抓地力、操控性能、排水性能等方面都有着重要的影响。
而胎噪则与车辆的舒适性息息相关。
选择合适的轮胎花纹和胎噪对于车辆的性能和驾驶体验有着重要的作用。
二、正确的轮胎胎压1. 胎压的重要性轮胎的胎压直接影响着轮胎的使用寿命、行车安全以及燃油经济性。
如果胎压过高或者过低都将影响轮胎的正常使用,并且会增加车辆行驶的风险。
保持正确的轮胎胎压对于车辆的正常运行和驾驶安全至关重要。
2. 如何确定正确的轮胎胎压车辆的正确轮胎胎压通常可以在车辆的车门边缘、备胎箱盖、汽油箱盖内侧或者车辆使用手册中找到。
在这些位置通常都会标注车辆正常使用情况下的轮胎胎压。
胎压也可以根据轮胎生产商的推荐数值来确定。
如果车辆搭载有不同尺寸的轮胎,需要根据季节和使用条件对轮胎胎压进行适当的调整。
3. 定期检查和调整轮胎胎压由于轮胎在使用过程中可能会出现漏气或者自然泄压的情况,因此车主需要定期检查轮胎的胎压,并根据需要进行调整。
通常建议每隔一个月或者每5000公里对轮胎胎压进行一次检查和调整。
在气温变化较大的季节,如春秋季节,胎压的变化可能更为明显,车主应及时对轮胎胎压进行调整。
国家汽车轮胎标准
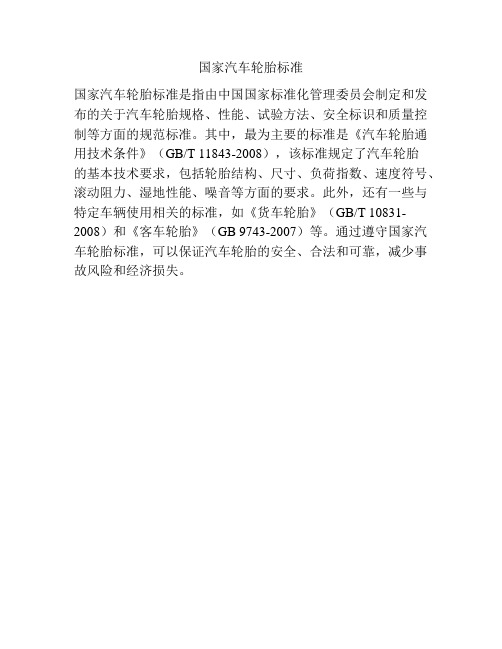
国家汽车轮胎标准
国家汽车轮胎标准是指由中国国家标准化管理委员会制定和发布的关于汽车轮胎规格、性能、试验方法、安全标识和质量控制等方面的规范标准。
其中,最为主要的标准是《汽车轮胎通用技术条件》(GB/T 11843-2008),该标准规定了汽车轮胎
的基本技术要求,包括轮胎结构、尺寸、负荷指数、速度符号、滚动阻力、湿地性能、噪音等方面的要求。
此外,还有一些与特定车辆使用相关的标准,如《货车轮胎》(GB/T 10831-2008)和《客车轮胎》(GB 9743-2007)等。
通过遵守国家汽车轮胎标准,可以保证汽车轮胎的安全、合法和可靠,减少事故风险和经济损失。
- 1、下载文档前请自行甄别文档内容的完整性,平台不提供额外的编辑、内容补充、找答案等附加服务。
- 2、"仅部分预览"的文档,不可在线预览部分如存在完整性等问题,可反馈申请退款(可完整预览的文档不适用该条件!)。
- 3、如文档侵犯您的权益,请联系客服反馈,我们会尽快为您处理(人工客服工作时间:9:00-18:30)。
轮胎、轮辋及气门嘴标准精选(最新)
轮胎、轮辋及气门嘴标准精选(最新)
G518《GB518-2007摩托车轮胎》
G519《GB/T519-2003充气轮胎物理性能试验方法》
G521《GB/T521-2012轮胎外缘尺寸测量方法》
G1190《GB/T1190-2009工程机械轮胎技术要求》
G1192《GB/T1192-2008农业轮胎技术条件》
G1702《GB/T1702-2008力车轮胎》
G1703《GB/T1703-2008力车内胎》
G1796.1《GB1796.1-2008轮胎气门嘴第1部分:压紧式内胎气门嘴》
G1796.2《GB1796.2-2008轮胎气门嘴第2部分:胶座气门嘴》
G1796.3《GB1796.3-2008轮胎气门嘴第3部分:卡扣式气门嘴》G1796.6《GB1796.6-2008轮胎气门嘴第6部分:气门芯》
G2933《GB/T2933-2009充气轮胎用车轮和轮辋的术语、规格代号和标志》
G2977《GB/T2977-2008载重汽车轮胎规格、尺寸、气压与负荷》G2978《GB/T2978-2014轿车轮胎规格、尺寸、气压与负荷》
G2979《GB/T2979-2008农业轮胎规格、尺寸、气压与负荷》
G2980《GB/T2980-2009工程机械轮胎规格、尺寸、气压与负荷》G2981《GB/T2981-2014工业车辆充气轮胎技术条件》
G2982《GB/T2982-2014工业车辆充气轮胎规格、尺寸、气压与负荷》
G2983《GB/T2983-2008摩托车轮胎系列》
G3487《GB/T3487-2005汽车轮辋规格系列》
G3900《GB/T3900-2012轮胎气门嘴系列》
G4501《GB/T4501-2008载重汽车轮胎性能室内试验方法》
G4502《GB/T4502-2009轿车轮胎性能室内试验方法》
G6326《GB/T6326-2005轮胎术语及其定义》
G6327《GB/T6327-1996载重汽车轮胎强度试验方法》
G7036.1《GB7036.1-2009充气轮胎内胎:汽车轮胎内胎》
G7036.2《GB7036.2-2007充气轮胎内胎:摩托车轮胎内胎》
G7037《GB7037-2007载重汽车翻新轮胎》
G7377《GB/T7377-2008力车轮胎系列》
G9102《GB/T9102-2003锦纶6轮胎浸胶帘子布》
G9743《GB9743-2015轿车轮胎》
G9744《GB9744-2015载重汽车轮胎》
G9745《GB9745-2009航空轮胎》
G9746《GB/T9746-2013航空轮胎系列》
G9747《GB/T9747-2008航空轮胎试验方法》
G9749《GB/T9749-2008力车轮胎性能试验方法》
G9764《GB9764-2009轮胎气门嘴芯腔》
G9765《GB9765-2009轮胎气门嘴螺纹》
G9766.1《GB/T9766.1-2008轮胎气门嘴试验方法第1部分:压紧式内胎气门嘴试验方法》
G9766.2《GB/T9766.2-2008轮胎气门嘴试验方法第2部分:胶座气门嘴试验方法》
G9766.3《GB/T9766.3-2008轮胎气门嘴试验方法第3部分:卡扣式气门嘴试验
方法》
G9766.4《GB/T9766.4-2009轮胎气门嘴试验方法第4部分:压紧式无内胎气门嘴试验方法》
G9766.5《GB/T9766.5-2009轮胎气门嘴试验方法第5部分:大芯腔气门嘴试验方法》
G9766.6《GB/T9766.6-2008轮胎气门嘴试验方法第6部分:气门芯试验方法》G9766.7《GB/T9766.7-2009轮胎气门嘴试验方法第7部分:零部件试验方法》G9767《GB/T9767-2002轮胎气门芯试验方法》
G9768《GB/T9768-2008轮胎使用与保养规程》
G9769《GB/T9769-2005轮辋轮廓检测》
G10823《GB/T10823-2009充气轮胎轮辋实心轮胎规格、尺寸与负荷》
G10824《GB/T10824-2008充气轮胎轮辋实心轮胎技术规范》
G11181《GB/T11181-2003子午线轮胎用钢帘线》
G12836.2《GB12836.2-2003无内胎气门嘴第2部分:压紧式气门嘴》
G12837《GB12837-1999大芯腔轮胎气门嘴》
G12839《GB/T12839-2012轮胎气门嘴术语及其定义》
G12939《GB/T12939-2002工业车辆轮辋规格系列》
G13202《GB/T13202-2007摩托车轮辋系列》
G13203《GB/T13203-2014摩托车轮胎性能试验方法》
G13204《GB/T13204-2002摩托车轮胎高速性能试验方法转鼓法》
G13652《GB/T13652-2004航空轮胎表面质量》
G14450《GB/T14450-2004胎圈用钢丝》
G14646《GB14646-2007轿车翻新轮胎》
G14687《GB/T14687-1993工业车轮》
G14688《GB/T14688-1993工业脚轮》
G14828《GB/T14828-2003农业轮胎牵引性能试验方法》
G15323《GB15323-2009航空轮胎内胎》
G15324《GB/T15324-2004航空轮胎内胎物理性能试验方法》
G16622《GB/T16622-2009压配式实心轮胎规格、尺寸与负荷》G16623《GB/T16623-2008压配式实心轮胎技术规范》
G18505《GB/T18505-2013汽车轮胎动平衡试验方法》
G18506《GB/T18506-2013汽车轮胎均匀性试验方法》
G18861《GB/T18861-2012汽车轮胎和摩托车轮胎滚动阻力试验方法多点试验》G19047《GB19047-2003增强型载重汽车轮胎》G19388《GB/T19388-2003轿车轮胎滚动周长试验方法》
G19389《GB/T19389-2003载重汽车轮胎滚动周长试验方法》
G19390《GB/T19390-2003轮胎用聚酯浸胶帘子布》
G21285《GB/T21285-2007轮胎气门嘴及其零部件的标识方法》G21286《GB/T21286-2007充气轮胎修补》
G22036《GB/T22036-2008轮胎惯性滑行通过噪声测试方法》
G22037《GB/T22037-2008航空有内胎轮胎胎圈密合压力试验方法电测法》
G22038《GB/T22038-2008汽车轮胎静态接地压力分布试验方法》
G22039《GB/T22039-2008航空轮胎激光数字无损检测方法》
G22391《GB/T22391-2008实心轮胎耐久性试验方法转鼓法》
G23657《GB/T23657-2009力车轮辋系列》
G23663《GB/T23663-2009汽车轮胎纵向和横向刚性试验方法》G23664《GB/T23664-2009汽车轮胎无损检验方法X射线法》
G24799《GB/T24799-2009轮胎用特种内胎》
G26276《GB/T26276-2010工程机械子午线轮胎无损检验方法X 射线法》
G26277《GB/T26277-2010轮胎电阻测量方法》
G26278《GB/T26278-2010轮胎规格替换指南》
G26732《GB/T26732-2011轮胎翻新工艺》
G29040《GB/T29040-2012汽车轮胎滚动阻力试验方法单点试验和测量结果的相关性》
G29042《GB/T29042-2012汽车轮胎滚动阻力限值》
G30193《GB/T30193-2013工程机械轮胎耐久性试验方法》
G30195《GB/T30195-2013汽车轮胎耐撞击性能试验方法》
G30196《GB/T30196-2013自体支撑型缺气保用轮胎》
G30197《GB/T30197-2013工程机械轮胎作业能力测试方法转鼓法》
G30198《GB/T30198-2013汽车轮胎不圆度试验方法》
JT752《JT/T752-2009横向力摩擦系数系统专用测试轮胎》
GJ107A《GJB107A-1995航空轮胎设计要求》
GJ108A《GJB108A-1998航空轮胎试验方法静负荷、动态模拟和导静电性能试验》GJ1261A《GJB1261A-2004军用越野汽车轮胎通用规范》
HG2177《HG/T2177-1998轮胎外观质量》
HG2195《HG/T2195-2001航空轮胎使用与保养》
HG3979《HG/T3979-2007工程机械翻新轮胎》
JJF1194《JJF1194-2008轮胎强度及脱圈试验机校准规范》
JJF1195《JJF1195-2008轮胎耐久性及轮胎高速性能转鼓试验机校准规范》
JJF1413《JJF1413-2013轮胎压力表型式评价大纲》。