凸轮轴加工工艺
课程设计--设计凸轮轴的机械加工工艺规程

课程设计--设计凸轮轴的机械加工工艺规程1. 引言本文档旨在设计凸轮轴的机械加工工艺规程,确保凸轮轴的加工过程符合技术标准,提高产品质量和生产效率。
2. 加工工艺流程以下是凸轮轴的机械加工工艺流程:2.1 材料准备- 选择适合的材料,如某种合金钢。
- 确保材料质量符合要求,进行材料检验和试样制备。
2.2 设计凸轮轴图纸- 根据产品要求和设计要求,在计算机辅助设计软件中绘制凸轮轴图纸。
- 确保凸轮轴的尺寸、形状和孔位准确无误。
2.3 加工准备- 准备适当的机床和刀具。
- 制定加工方案,包括选择合适的切削参数和加工顺序。
2.4 粗加工- 将所选材料加工成初步形状,以便后续加工。
- 采用合适的工艺方法,如车削、钻孔等。
2.5 精加工- 根据凸轮轴的要求,采用适当的工艺方法进行精加工,如磨削、镗削等。
- 确保凸轮轴的尺寸、形状和表面光洁度达到要求。
2.6 检验- 对加工后的凸轮轴进行尺寸、形状和质量检验。
- 确保凸轮轴符合技术标准和产品要求。
2.7 产品调试和完善- 安装凸轮轴到相关的设备上,并进行调试。
- 根据实际使用情况,进一步完善凸轮轴的性能。
3. 安全注意事项在进行凸轮轴的机械加工过程中,请注意以下安全事项:- 穿戴适当的个人防护装备。
- 检查机床和刀具的安全性能,确保操作安全。
- 注意切削液的使用和储存,避免造成伤害和环境污染。
- 遵循操作规程,严禁违规操作。
4. 结束语本文档详细介绍了设计凸轮轴的机械加工工艺规程,包括加工工艺流程、安全注意事项等。
在实际操作中,请务必遵循技术标准和相关要求,确保凸轮轴的加工质量和生产效率。
凸轮轴工艺基础知识-图文

凸轮轴工艺基础知识-图文凸轮轴的种类在现代发动机中,凸轮轴的位置已经从下置式改成了上置式。
以往一般采用的下置凸轮轴,即凸轮轴在气缸侧面,由正时齿轮直接驱动。
为了把凸轮轴的转动变换为气门的往复运动,必须使用气门挺杆来传递动力。
这样,往复运动的零件较多,惯性质量大,不利于发动机高速运动。
而且,细长的挺杆具有一定的弹性,容易引起振动,加速零件磨损,甚至使气门失去控制。
上置凸轮轴分为上置单凸轮轴和上置双凸轮轴。
上置单凸轮轴在气缸盖上用一根凸根轴,直接驱动进、排气门,它具有结构简单,适用于高速发动机,但对凸轮轴的加工质量要求较高。
上置双凸轮轴是在缸盖上装有两根凸轮轴,一根用于驱动进气门,另一根用于驱动排气门。
采用顶置双凸轮轴对凸轮轴和气门弹簧的设计和加工要求不高,特别适用于气门V形配置的半球形燃烧室,也便于和四气门配气机构配合使用,在高速强化发动机上应用较多,如ZD30发动机的凸轮轴,每个发动机上有进气凸轮轴和排气凸轮轴各一根,都不需要抛光,而康明斯几种凸轮轴抛光后,凸轮表面粗糙度要求Ra0.2,主轴颈表面粗糙度要求Ra0.4。
康明斯作业部4B凸轮轴加工工艺:零件号:3929885材料:冷激铸铁硬度:HB230-320加工工艺流程:0J毛坯检查10铣端面钻中心孔20钻油孔去毛刺30打标记35粗磨第三主轴径40粗精车全部轴径,台肩,清根槽并倒角45手动校直47精磨第三主轴径50精磨其余主轴径60精磨小轴径,台肩及第一主轴径前端面70铣键槽100粗精磨全部凸轮105去毛刺110磁粉探伤130抛光140清洗150J最终检查160防锈包装康明斯作业部6B(欧Ⅱ)凸轮轴加工工艺:零件号:3283179材料:冷激铸铁硬度:HB230-320加工工艺流程:0J毛坯检查10铣端面钻中心孔20钻油孔,去毛刺30打标记35粗磨第四主轴径40粗精车全部轴径,台肩,清根槽并倒角45手动校直47精磨第四主轴径50精磨其余主轴径60精磨小轴径,台肩及第一主轴径前端面70铣键槽100粗精磨全部凸轮105去毛刺110磁粉探伤130抛光140清洗150J最终检查160防锈包装康明斯作业部6C凸轮轴加工工艺:零件号:3923478材料:冷激铸铁硬度:HB230-320加工工艺流程:0J毛坯检查10铣端面钻中心孔20钻油孔,去毛刺30打标记35粗磨第四主轴径40粗精车全部轴径,台肩,清根槽并倒角45手动校直47精磨第四主轴径50精磨其余主轴径60精磨小轴径,台肩及第一主轴径前端面70铣键槽100粗精磨全部凸轮105去毛刺110磁粉探伤130抛光140清洗150J最终检查160防锈包装10工序铣端面钻中心孔20工序钻油孔,去毛刺230工序打标记35工序粗磨中间主轴径340工序粗精车全部轴径,台肩,清根槽并倒角447工序精磨中间主轴径50工序精磨其余主轴径5。
汽车凸轮轴加工工艺分析

汽车凸轮轴加工工艺分析内容摘要凸轮轴作为汽车发动机配气机构中的关键部件,其性能直接影响着发动机整体性能。
因此凸轮轴的加工工艺有特殊要求,合理的加工工艺对于降低加工成本、减少生产环节以及合理布置凸轮轴生产线具有很大的现实意义。
本文针对凸轮轴的加工特点,结合工厂的实际,从前期规划开始,对凸轮轴的加工工艺进行了深入的分析、研究。
建立了用数控无靠模方法。
对凸轮廓形进行计算和推倒,对凸轮轮廓的加工进行了探讨并提出适用于发动机凸轮轴的加工方法。
关键词:发动机;凸轮轴;工艺分析目录一、引言 (3)(一)汽车发动机行业的发展状况 (3)(二)凸轮轴的性能要求 (3)(三)本文研究内容 (5)二、凸轮轴生产线前期规划 (5)(一)产品规格 (5)(二)工艺设计原则及凸轮轴加工工艺分析 (6)(三)小结 (7)三、凸轮轴生产线工艺分析 (7)(一)生产线布置............................................ 错误!未定义书签。
(二)工艺设计.. (7)(三)工艺分析 (9)(四)工艺特点 (10)(五)工艺难点 (13)四、凸轮廓形理论计算及加工控制参数 (14)(一)凸轮轴凸轮的廓形要求 (14)(二)包络线理论 (16)(三)凸轮廓形坐标 (17)五、总结.................................................................. 参考文献.................................................................. 致谢........................................................................汽车凸轮轴加工工艺设计学生姓名:孟德宏指导老师:郭小凯一、引言(一)汽车发动机行业的发展状况现代汽车发动机行业的发展十分迅速,这种趋势要求各发动机厂家不仅要具有大批量生产的能力,也同时要具有小批量、多品种的生产技术。
凸轮轴工艺基础知识

凸轮轴⼯艺基础知识凸轮轴⼯艺基础知识凸轮轴的种类在现代发动机中,凸轮轴的位置已经从下置式改成了上置式。
以往⼀般采⽤的下置凸轮轴,即凸轮轴在⽓缸侧⾯,由正时齿轮直接驱动。
为了把凸轮轴的转动变换为⽓门的往复运动,必须使⽤⽓门挺杆来传递动⼒。
这样,往复运动的零件较多,惯性质量⼤,不利于发动机⾼速运动。
⽽且,细长的挺杆具有⼀定的弹性,容易引起振动,加速零件磨损,甚⾄使⽓门失去控制。
上置凸轮轴分为上置单凸轮轴和上置双凸轮轴。
上置单凸轮轴在⽓缸盖上⽤⼀根凸根轴,直接驱动进、排⽓门,它具有结构简单,适⽤于⾼速发动机,但对凸轮轴的加⼯质量要求较⾼。
上置双凸轮轴是在缸盖上装有两根凸轮轴,⼀根⽤于驱动进⽓门,另⼀根⽤于驱动排⽓门。
采⽤顶置双凸轮轴对凸轮轴和⽓门弹簧的设计和加⼯要求不⾼,特别适⽤于⽓门V形配置的半球形燃烧室,也便于和四⽓门配⽓机构配合使⽤,在⾼速强化发动机上应⽤较多,如ZD30发动机的凸轮轴,每个发动机上有进⽓凸轮轴和排⽓凸轮轴各⼀根,都不需要抛光,⽽康明斯⼏种凸轮轴抛光后,凸轮表⾯粗糙度要求Ra 0.2,主轴颈表⾯粗糙度要求Ra0.4。
康明斯作业部4B凸轮轴加⼯⼯艺:零件号: 3929885 材料:冷激铸铁硬度:HB230-320加⼯⼯艺流程:0J⽑坯检查10铣端⾯钻中⼼孔20 钻油孔去⽑刺30打标记35粗磨第三主轴径40粗精车全部轴径,台肩,清根槽并倒⾓45⼿动校直47精磨第三主轴径50精磨其余主轴径60精磨⼩轴径,台肩及第⼀主轴径前端⾯70铣键槽100粗精磨全部凸轮105去⽑刺110磁粉探伤130抛光140清洗150J最终检查160防锈包装康明斯作业部6B(欧Ⅱ)凸轮轴加⼯⼯艺:零件号:3283179 材料:冷激铸铁硬度:HB230-320加⼯⼯艺流程:0J⽑坯检查 10铣端⾯钻中⼼孔 20 钻油孔,去⽑刺 30打标记 35粗磨第四主轴径 40粗精车全部轴径,台肩,清根槽并倒⾓45⼿动校直 47精磨第四主轴径 50精磨其余主轴径 60精磨⼩轴径,台肩及第⼀主轴径前端⾯70铣键槽 100粗精磨全部凸轮 105去⽑刺 110磁粉探伤 130抛光 140清洗150J最终检查 160防锈包装康明斯作业部6C凸轮轴加⼯⼯艺:零件号:3923478 材料:冷激铸铁硬度:HB230-320加⼯⼯艺流程:0J⽑坯检查 10铣端⾯钻中⼼孔 20 钻油孔,去⽑刺 30打标记35粗磨第四主轴径 40粗精车全部轴径,台肩,清根槽并倒⾓ 45⼿动校直 47精磨第四主轴径 50精磨其余主轴径 60精磨⼩轴径,台肩及第⼀主轴径前端⾯ 70铣键槽 100粗精磨全部凸轮 105去⽑刺 110磁粉探伤 130抛光 140清洗 150J最终检查160防锈包装10⼯序铣端⾯钻中⼼孔20⼯序钻油孔,去⽑刺30⼯序打标记35⼯序粗磨中间主轴径40⼯序粗精车全部轴径,台肩,清根槽并倒⾓47 ⼯序精磨中间主轴径50⼯序精磨其余主轴径60⼯序精磨⼩轴径,台肩及第⼀主轴径前端⾯70⼯序铣键槽100⼯序粗精磨全部凸轮105⼯序去⽑刺110⼯序磁粉探伤130⼯序抛光140⼯序清洗加⼯⼯艺简介:A.凸轮轴强化加⼯⼯艺1.凸轮轴⽑坯材料为冷激铸铁:a)⼯艺⽅法:铸造时,在凸轮轴模具内放冷铁,浇铸后凸轮急速冷却,促使其迅速的凝固,在表⾯形成莱⽒体硬化层。
凸轮轴的工艺分析及生产类型的确定

1 凸轮轴的工艺分析及生产类型的确定1.1 凸轮轴的用途任务书所指凸轮轴为内燃机配气机构的零件,其主要工作表面是两个凸轮面,推动顶杆移动,从而控制进、排气门的开合。
正火处理,硬度为170-241HBS 。
凸轮表面及0.0320.03915--∅表面应高频淬火,硬化层深1.5~3,凸轮顶部允许达6,淬硬层硬度为55-63HRC 。
淬火层金相组织应为细针状和中等针状回或马氏体及少量屈氏体;进、排气凸轮均为对称形,对于表中所列理论升程之偏差:103.5-118.5,范围内不大于0.04。
在118.5-180范围内不大于0.06;升程变化率公差在103.5-118.5范围内0.004/1,在118.5-180范围内0.006/1。
进、排气凸轮用平面测量头从凸轮对称中心为0处向两侧测量;凸轮轴精加工后,各支承轴颈和凸轮表面应光洁。
不允许有碰伤,凹痕,毛刺,裂缝等缺陷存在;凸轮轴精加工后应经磁力探伤,探伤后退磁;去锐边,尖角(包括凸轮两侧);按JB/T510482-92《柴油机凸轮轴检验方法》检验。
1.3 审查凸轮轴工艺性由零件图可知,凸轮轴进气排气凸轮表面、ø15外圆面、ø25外圆面、ø24外圆面,ø 18外圆面、两个槽、ø30及ø24端面为主要的工作表明,加工精度高,需要高精度机床或磨床进行加工,其余表面加工精度均较低,不需要高精度机床加工,通过车、铣粗加工即可达到加工要求;由此分析,该零件的工艺性较好。
1.4 确定凸轮轴的生产类型依设计题目指示可知该凸轮轴的生产类型为大批量生产,其对应夹具设计成专用夹具。
2 确定毛坯,绘制毛坯简图2.1 选择毛坯由于该凸轮轴在工作过程中要承受交变载荷,并且工作环境温度变化较大,为增强凸轮轴的强度和冲击韧性,获得纤维组织,毛坯选用锻件。
该凸轮轴的轮廓尺寸不大,生产类型属于大批生产,为提高生产率和锻件精度,宜采用模锻方法制造毛坯。
汽车发动机凸轮轴加工工艺设计及质量控制研究

汽车发动机凸轮轴加工工艺设计及质量控制研究作者:王林峰来源:《时代汽车》2023年第18期摘要:凸轮轴作为关键性零部件,关乎到汽车发动机的性能表现,因此对凸轮轴的质量与性能提出了较高要求。
本文对汽车发动机凸轮轴的加工工艺进行分析,了解其设计原则以及工艺特征,随后提出了完整的工艺设计流程。
从生产线布置、定位基准选择、加工划分、凸轮形面加工等,并提出定位键优化改善、控制键槽裂纹、主动测量与自然补偿等方式全面提高凸轮轴加工质量。
关键词:汽车发动机凸轮轴质量控制工艺设计1 引言近年来我国汽车行业迅速发展,发动机生产厂商获得了前所未有的生产动力。
而在汽车发动机中最为重要的关键性结构就是凸轮轴的存在。
由于凸轮轴特殊的材料以及工艺要求,在加工过程中需要对其质量进行控制,并尽可能的实现成本节约,避免不合理环节布置,从而对凸轮轴生产线进行合理规划,确保其形成良好的生产效果。
基于凸轮轴在发动机中的性能表现,则需要确保其在实际加工制造过程中表现出更加精良的工艺特征以及质量成果。
2 汽车发动机凸轮轴加工工艺分析2.1 工艺设计原则凸轮轴不仅是组成汽车发动机的重要零部件,其使用性能与产品质量对汽车发动机安全稳定运行也有着直接影响。
科学合理设计汽车发动机凸轮轴加工工艺,有利于更好地把控凸轮加工精度和加工成本,并保障汽车发动机凸轮轴加工效益。
汽车发动机凸轮轴加工工艺设计原则,应遵循以下几点要求:(1)工艺设计合理性,并在工艺设计优化的基础上融合其他现代先进技术手段,增强产品核心竞争优势。
(2)国内外可靠且具有影响力厂家的先进设备优先考虑,以此保障汽车发动机凸轮轴加工工艺水平。
(3)既要体现工艺设计先进性,也要兼具经济性,做到在不影响产品质量的基础上最大程度地节约工艺成本。
(4)各生产环节的安全性与操作便捷性是汽车发动机凸轮轴加工工艺设计中需要给予高度重视的问题。
(5)基于经济条件允许的前提下,坚持柔性生产原则,根据凸轮轴结构特点,合理设计其加工工艺,尽可能减少凸轮轴在加工过程中对其精度的干扰影响。
凸轮加工工艺流程
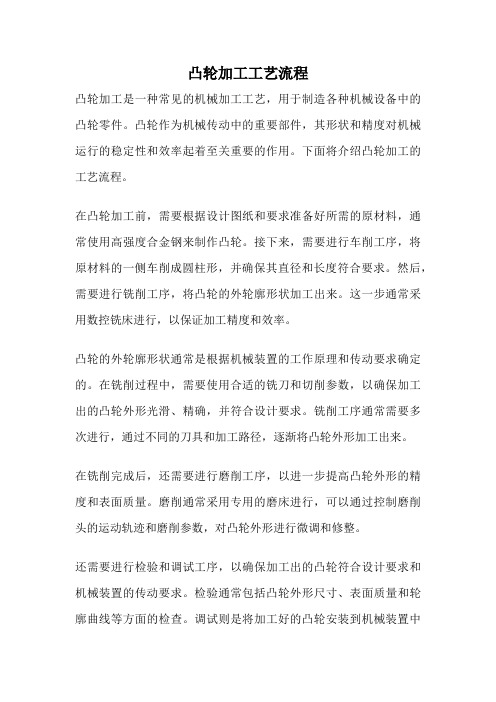
凸轮加工工艺流程凸轮加工是一种常见的机械加工工艺,用于制造各种机械设备中的凸轮零件。
凸轮作为机械传动中的重要部件,其形状和精度对机械运行的稳定性和效率起着至关重要的作用。
下面将介绍凸轮加工的工艺流程。
在凸轮加工前,需要根据设计图纸和要求准备好所需的原材料,通常使用高强度合金钢来制作凸轮。
接下来,需要进行车削工序,将原材料的一侧车削成圆柱形,并确保其直径和长度符合要求。
然后,需要进行铣削工序,将凸轮的外轮廓形状加工出来。
这一步通常采用数控铣床进行,以保证加工精度和效率。
凸轮的外轮廓形状通常是根据机械装置的工作原理和传动要求确定的。
在铣削过程中,需要使用合适的铣刀和切削参数,以确保加工出的凸轮外形光滑、精确,并符合设计要求。
铣削工序通常需要多次进行,通过不同的刀具和加工路径,逐渐将凸轮外形加工出来。
在铣削完成后,还需要进行磨削工序,以进一步提高凸轮外形的精度和表面质量。
磨削通常采用专用的磨床进行,可以通过控制磨削头的运动轨迹和磨削参数,对凸轮外形进行微调和修整。
还需要进行检验和调试工序,以确保加工出的凸轮符合设计要求和机械装置的传动要求。
检验通常包括凸轮外形尺寸、表面质量和轮廓曲线等方面的检查。
调试则是将加工好的凸轮安装到机械装置中进行试运行,检查其传动效果和稳定性,并根据实际情况进行调整和修正。
凸轮加工是一项复杂而精密的工艺,需要经过多个工序的加工和调试。
通过合理的工艺流程和精确的操作,可以加工出符合设计要求的凸轮零件,为机械装置的正常运行提供保障。
凸轮加工的工艺流程可以根据具体的需求和装备的不同,进行适当的调整和优化,以提高加工效率和质量。
凸轮轴的钨极氩弧重熔淬火工艺

凸轮轴的钨极氩弧重熔淬火工艺
凸轮轴是发动机的关键部件之一,用于控制气门的开关时间和顺序,对发动机的性能和燃油经济性起着重要作用。
为了提高凸轮轴的
强度和耐磨性,需要采用一些特殊的材料和加工工艺进行处理。
钨极氩弧重熔淬火技术是一种先进的表面改性工艺,可以显著提
高材料的抗磨性、耐蚀性和疲劳寿命,对凸轮轴的性能提升非常有帮助。
具体工艺流程如下:
1. 准备凸轮轴样品,并对其进行表面处理,去除表面的氧化物
和油污等杂质。
2. 在凸轮轴的表面上喷涂一层钨的粉末。
3. 采用钨极氩弧焊工艺,通过高温高压的钨极氩弧束,使钨粉
末与基材表面熔融成为一体。
4. 再经过淬火处理,使得材料的组织结构更加致密,硬度更高,抗磨性和耐蚀性得到显著提升。
钨极氩弧重熔淬火技术不仅可以用于凸轮轴的表面改性,还可以
用于其他材料的改性,例如钛合金、高速钢等。
这种工艺具有成本低、效率高、目标精度高等优点,被广泛应用于航空航天、汽车工业、机
械加工等领域。
- 1、下载文档前请自行甄别文档内容的完整性,平台不提供额外的编辑、内容补充、找答案等附加服务。
- 2、"仅部分预览"的文档,不可在线预览部分如存在完整性等问题,可反馈申请退款(可完整预览的文档不适用该条件!)。
- 3、如文档侵犯您的权益,请联系客服反馈,我们会尽快为您处理(人工客服工作时间:9:00-18:30)。
凸轮轴的加工工艺凸轮轴的加工工艺凸轮轴的材料:球墨铸铁、合金铸铁、冷激铸铁、中碳钢球墨铸铁:将接近灰铸铁成份的铁水经镁或镁的合金或其它球化剂球化处理后而获得具有球状石墨的铸铁。
石墨呈球状,大大减轻了石墨对基体的分割性和尖口作用,球墨铸铁具有较高的强度、耐磨性、抗氧化性、减震性及较小的缺口敏感性。
球墨铸铁的凸轮轴一般用在单缸内燃机上,如S195柴油机,做凸轮轴用的球墨铸铁用QT600-3或QT700-2,要求球化为2级(石墨球化率90-95%)石墨粒度大小大于6级。
凸轮轴整体硬度HB230-280合金铸铁:将接近灰铸铁成份的铁水加入Mn、Cr、Mo、Cu等元素。
从而与珠光体形成合金,减少铁素体的数量。
合金铸铁的凸轮轴一般用于高转速凸轮轴。
如CAC480凸轮轴,凸轮轴整体硬度HB263-311。
冷激铸铁:一般用于低合金铸铁表面冷激处理,使外层为白口或麻口组织,心部仍是灰口组织。
如:372凸轮轴。
使用冷激铸铁的凸轮轴处于干摩擦或半干摩擦工作状态,而具有承受较大的弯曲与接触应力,要求材料表面层抗磨且高的强度,心部仍有一定的韧性。
目前国内所用的冷激铸铁主要有两大类:铬、钼、铜冷激铸铁和铬、钼、镍冷激铸铁,冷硬层的金相组织:莱氏体+珠光体(索氏体)冷激铸铁硬度为HRC45—52,目前,国内冷激铸铁的硬度在HRC47左右。
中碳钢:一般用于大型发动机凸轮轴。
如:6102发动机采用模锻锻造成型,也有一部分用于摩托凸轮轴,成型较简单。
模锻后一般要进行退火处理以便于机械加工。
凸轮轴加工的典型工艺一.凸轮轴轴颈粗加工采用无心磨床磨削无心磨床的磨削方式有2种:贯穿式无心磨削和切入式无心磨削。
贯穿式无心磨削一般用于单砂轮,它的导轮是单叶双曲面,推动凸轮轴沿轴向移动,仅仅用于磨削光轴。
切入式无心磨削是由多砂轮磨削(若是单砂轮磨削,一般砂轮被修整成成型砂轮,如:磨削液压挺柱的球面),如现有480凸轮轴的磨削,可磨削阶梯轴,导轮为多片盘状组合而成,工件不能沿轴向移动,无论是哪一种磨削方式,工件的中心都高于砂轮和导轮的中心,一般切入式磨削都有上料工位、磨削工位、测量工位、卸料工位组成。
砂轮线速度60m/s,轴颈径向磨削余量可达3.5mm,单件磨削时间18s,单件工时25s。
用无心磨床加工凸轮轴是一种新颖、独特的新工艺,新方法,但又存在一定的局限性,特别是不易磨削轴肩和端面,一般不用于多品种凸轮轴的加工,只用于单一品种、大批量的生产,若要更换所加工的凸轮轴品种,就要更换导轮和砂轮,各砂轮间距需重新调整。
切入式无心磨床的修整一般采用单颗粒金刚石修整,修整器所走的路线是凸字形,修整器靠模各段差值与凸轮轴的各段轴颈差值相等。
粗磨凸轮轴轴颈所用的砂轮都属于碳化物系列,粒度为60,砂轮线速度为45m/。
二、铣端面,钻中心孔中心孔加工是以后加工工序的定位基准,在铣端面时,一般只限定5个自由度即可,用2个V型块限定4个自由度,轴向自由度是由凸轮轴3#轴颈前端面或后端面(在产品设计中,该面应提出具体要求)。
目前普遍采用的是自定心定位夹紧,密齿刀盘铣削。
轴向尺寸保证后端面到毛坯的粗定位基准尺寸和整个凸轮轴长度,鉴于凸轮轴皮带轮轴颈尺寸较小,钻中心孔时一般选用B5中心钻,钻后的孔深用φ10钢球辅助检查,保证球顶到后端面尺寸和2钢球顶部之间的距离,这样可保证以后定位的一致性。
三、凸轮轴的热处理热处理:将原材料或未成品置于空气或特定介质中,用适当方式进行加热、保温和冷却,使之获得人们所需要的力学或工艺性能的工艺方法。
热处理分类:一般热处理、化学热处理、表面热处理球墨铸铁凸轮轴一般都是等温淬火。
冷却介质为10号、20号锭子油盐浴或碱浴,淬火后经140°C-250°C低温回火,回火后的组织为黑色针叶状马氏体,硬度HRC50-54。
合金铸铁和钢件凸轮轴一般采用中频淬火:淬火频率1000-10000Hz,一般选用7000Hz。
也就是感应加热表面淬火,其原理是:将凸轮轴的凸轮放入加热线圈中,由于电流的集肤效应,使凸轮由外层向内加热、升温,使表层一定深度组织转变成奥氏体,而后迅速淬硬的工艺,目前480凸轮轴采用自然回火的方法,其凸轮表面组织为针状马氏体。
凸轮轴经表面热处理:可较大地提高零件的扭转和弯曲疲劳强度和表面的耐磨性。
感应加热淬火变形小、节能、成本低、劳动生产率高、淬火机可放在冷加工生产线上,便于生产管理。
480凸轮轴中频淬火机在感应加热时,要对电源、变压器、感应线圈进行冷却,要求冷却水的温度在25°C-30°C,淬火冷却液的温度为53°C-62°C,若机床本身达不到要求,必须在机床外提一套附加冷却装置,用来给冷却水制冷。
四、凸轮轴的深孔加工在机械加工中L/D>5时的孔加工可称为深孔加工,用普通麻花钻钻深孔时有以下困难。
1.钻头细长。
刚性差,加工时钻头易弯曲和振动,难以保证孔的直线度与加工精度。
2.切屑多,而排除切屑的通道长而狭窄,切屑不容易排出。
3.孔深切削液不易进入,切削温度过高,散热困难,钻头容易断。
深孔钻按工艺的不同可分为在实心物体上钻孔、扩孔、套料3种,而以在实心料上钻孔用得最多,如480凸轮所用的深孔都是由枪钻经2头加工而成的。
每次钻孔深为L/2+10mm。
枪钻钻削是单刃外排屑式的,一般适用于加工φ2-φ20mm孔, L/D>100、表面粗糙度Ra12.5-3.2mm、精度H8-H10级的深孔。
单刃外排屑深孔钻,最早用于加工枪管,故称枪钻,也是φ2-φ6mm深孔加工的唯一办法。
枪钻带有V形切削刃和一个切削液孔的钻头、钻杆、及适用于某专用设备的钻柄组成。
高压切削液(7MPa)通过钻头的小孔送到切削区域内,进行冷却、润滑并帮助排屑,然后再将切屑与切削液顺着V型刀杆排入集中冷却系统中。
钻头为硬质合金,采用焊接式结构。
切削用量一般为0.06-0.1mm/r,为了更好地控制刀具的破损程度,刀具采用径向负荷反馈,一旦刀具切削力达到一定的数值,在数控系统的作用下,刀具能自动退回,从而避免枪钻折断,提高刀具的使用寿命。
磨钝后的刀具换下,再重新进行刃磨后方可使用。
凸轮轴深孔加工冷却液一般用锭子油,虽然油的冷却效果比乳化液差,但油的润滑效果比冷却液要好得多。
五、主轴颈快速点磨加工与CBN砂轮编辑本段快速点磨是德国勇克公司开发出来的一种先进的外圆高效磨削新工艺,该机床加工凸轮轴只需两顶尖定位夹紧,无需任何夹紧工具,利用前顶尖的高速旋转,通过顶尖和凸轮轴中心孔的摩擦来驱动工件运动,可以实现轴类零件在一次装夹后,用一片砂轮完成7个轴颈、一个端面和一个磨削圆角的工艺。
快速点磨砂轮是横向磨损,在磨损过程中,被磨削的凸轮轴外形尺寸不会因此而发生变化,磨削端面时,砂轮可倾斜±0.5︒,使砂轮与工件的接触面只有传统磨削端面的1/2。
CBN具有良好的导热性,其导热率是硬质合金的13倍,铜的3倍,另外CBN具有远优于金刚石的热稳定性和化学稳定性(金刚石与铁簇元素易产生亲和作用),可耐1300—1500的高温,并且与铁簇元素有很大的化学惰性,CBN是制作切削黑色金属的理想刀具材料。
CBN属于立方晶系,它的硬度、强度和其它物理性能远远优于刚玉等系列磨料。
在进行磨削过程中CBN自身磨损非常少,在大批量生产过程中,单个零件所需要的成本较小。
砂轮的形状、尺寸变化极小,耐用度较高,修整频次约为刚玉系列的1/20,每次修整量约为刚玉系列的1/25,砂轮与工件的磨削区内磨削温度较低,可避免在磨削的弹性变形阶段工件所产生的裂纹和磨削烧伤等现象的出现。
CBN具有良好的化学稳定性与耐热性,与碳在2000︒C时才起反应,在高温下易与水产生反应。
砂轮的耐用度高,机床的使用率可达97%以上,与一般砂轮磨削相比,可提高功效600%--700%。
当砂轮在宽度方向的磨损量占砂轮宽度的80%时便对砂轮进行修整,砂轮每次修整量为0.006mm,共分3部进行修整,每一步修整量为0.002mm,每修整一次可磨削120根凸轮轴,砂轮线速度为120m/s,可获得较高的金属切除率,使用冷却油做为冷却液,不仅仅是给砂轮和工件提供冷却液,同时也给砂轮和工件提供更好的润滑,同时由于油膜的吸附作用,还可以防止凸轮轴的轴颈表面氧化,防止磨削完后的工件表面生锈。
磨削液的供给是采用喷射法提供的冷却液,冷却较充分,可使砂轮的寿命提高一倍,金属切除率提高一倍以上,同时采用冷却液反冲的方法,冲洗砂轮表面,防止砂轮堵塞,使CBN颗粒始终以锋利的状态对工件进行切削,再加上CBN粒度较小,凸轮轴轴颈单位面积上参加切削的磨粒比一般砂轮要多,轴颈在被切削时所产生的弹性摩擦和变形阶段均较小,因此产生的弹性变形和塑性变形均较小,提高了表面粗糙度,防止表面产生磨削烧伤和因磨粒因素而引起的裂纹。
在磨粒切削阶段,对产生的热应力和变形应力均较小。
由于磨削速度很高,磨削热量来不及传入工件的深处,瞬时聚集在凸轮轴很薄的表层,形成切屑被带走。
磨粒切削点的温度达1000︒C以上,而内部只有几十度选用CBN砂轮磨削,磨粒锋利,磨削力小,故磨削区发热量少CBN显微硬度7300—9000HV,抗弯强度300MPa、抗压强度800--1000MPa、热稳定性1250︒C--1350︒C。
应用声音传感器严格限制砂轮和金刚滚轮间的距离,主要是防止砂轮修整时砂轮和金刚滚轮发生撞击。
砂轮架纵向进给时,传感器测头与砂轮间形成一小的缝隙,砂轮高速旋转压缩砂轮周围的空气,根据空气流通的通道大小不同,所产生的气阻声音大小不一样,从而判断传感器和砂轮间的缝隙而做出反馈,一旦砂轮和金刚滚轮产生接触,修整器自动修整砂轮,而声音传感器能根据声音尖锐响声大小来判断砂轮修整的正确性。
与树脂类结合剂相比,陶瓷结合剂化学性能稳定,耐热、抗酸、碱,气孔率大,工作时不易发热,在磨削过程中易脱落,热膨胀系数小,强度较高,能保持好CBN的几何形状,且磨具易修整。
用于磨削凸轮轴轴颈和端面的CBN砂轮立方氮化硼厚度只有4.5—5MM,并且是粘附在刚性钢盘上,刚性较好。
工件转速与砂轮转速的比为:40/8000无进给磨削即光磨,可提高工件的几何精度和降低表面粗糙度参数值,表面粗糙度随光磨次数的增加而降低,细粒度砂轮比粗粒度好砂轮的修整:修整通常包括整形和修锐,整形是使砂轮达到要求的几何形状和精度,砂轮的几何形状采用数控插补法进行,修锐是除去磨粒间的结合剂,使磨粒露出结合剂一定高度,形成切削刃,磨粒间空隙以容纳切屑。
金刚石滚轮磨削修整的特点:生产率高:以切入法进行修整,修整时间仅需2-10秒,可在进行凸轮轴更换工件时进行修整,不耽误生产节拍,同时由于金刚滚轮的寿命长,修整时间短,大大缩短了辅助时间,单件工件的消耗较低,金刚滚轮的精度较高,修整后的砂轮表面质量也较好。