国内外铜精矿先进铜冶炼工艺专业技术综述
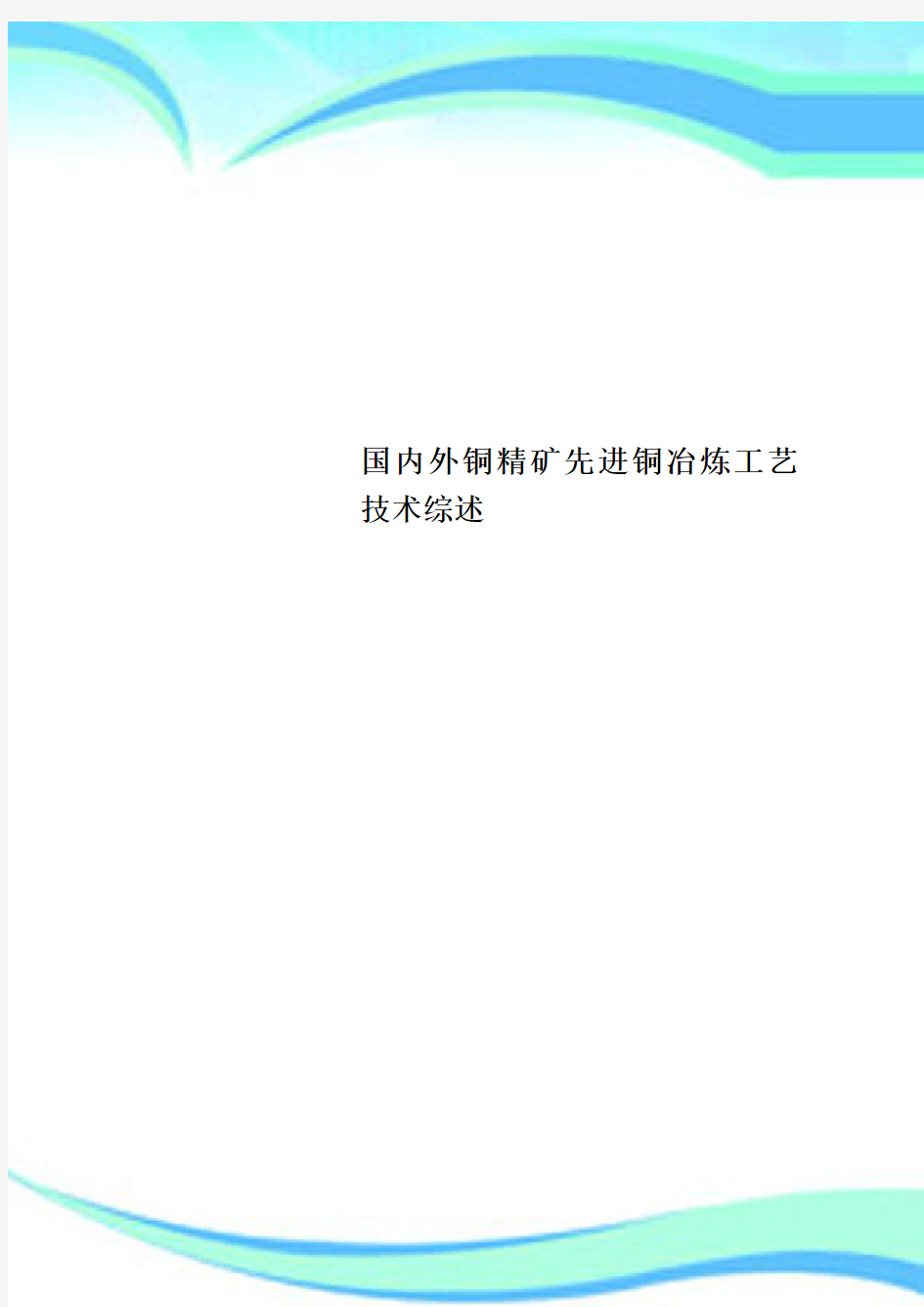

国内外铜精矿先进铜冶炼工艺技术综述
————————————————————————————————作者:————————————————————————————————日期:
铜冶炼三种方法
目前,中国已引进世界上最先进的炼铜新工艺有:闪速炉熔炼、艾萨熔炼、奥斯麦特熔炼、诺兰达熔炼等。国内自主创新的有白银法熔炼、金川合成炉熔炼、东营方圆的氧气底吹熔炼。后3种都是中国人自己研制的,都具有自主知识产权。这7种也算世界上较先进的炼铜法。通过多年的实践,国外的先进技术尚存不足之处,分述如下: 1、双闪速炉熔炼法: 投资大,专利费昂贵,熔剂和原料先进行磨细再进行深度干燥,需额外消耗能源这不尽合理。熔炉产出的铜硫需要水碎再干燥再细磨,工序繁杂。每道工序均难以保证100%回收率,会产生部分机械损失;热态高温铜锍水碎物理热几乎全部损失,水碎后再干燥,再加上炉内大量水套由冷却水带走热量,热能利用也不尽合理。铜锍水碎需要大量的水冲,增加动力消耗。破碎、干燥要增加人力和动力的消耗。这些都是多年来该工艺没有得到大量推广的重要原因。 2、艾萨法和澳斯麦特法均属于顶吹冶炼系列: 顶吹都要建立高层厂房,噪音大、高氧浓度低烟气量大、顶吹的氧枪12米长,3天至一周要更换一次,不锈钢消耗量大、投资大、操作不方便。都用电炉做贫化炉,渣含铜一般大于%不合国情。 3、三菱法的不足 4个炉子(熔炼炉、贫化电炉、吹炼炉、阳极炉)自流配置,第一道工序的熔炼炉需要配置在较高的楼层位置,建筑成本相对较高,炉渣采用电炉贫化,弃渣含铜量达%~%,远远高于我国多数大型铜矿开采的矿石平均品位,资源没有得到充分的利用。 4、诺兰达和特尼恩特连续吹炼法,尚在工业试验阶段。 诺兰达是侧吹、要人工打风眼、劳动强度很大、风眼漏风率达10%~15%。有很大噪音、操作条件不好、冶炼环境不理想。如果掌握不好容易引起泡沫渣喷炉事故。 综上所述,让我们来寻求新的冶炼工艺,在不断的探索中发现新途径。 氧气底吹炉炼铅、炼铜最早是湖南水口山和中国有色工程设计研究总院共同研发在水口
铜冶炼的现状及其发展状况
铜冶炼的现状及其发展状况 林程星 (江西理工大学冶金学院江西赣州 341000) 摘要:目前铜冶金工业仍然是以火法为主。而近年来铜的湿法冶金技术受到了人们的极大关注,越来越广泛的应用于低品位氧化矿的处理、废铜资源的回收等方面。本文主要介绍了铜冶金的火法以及湿法冶炼的工艺和发展状况。 关键字:铜冶金湿法冶金火法冶金 Present situation and development of copper metallurg y Chengxing Lin (School of Nonferrous Metallurgy,Jiangxi University of Science and Technology,Ganzhou Jiangxi,341000) Abstract: At present,the copper thermometallurgy is still the main method used in copper metallurgy industry. But in recent years, the copper hydrometallurgy technology , which is more and more widely applied in low grade oxidized ore processing, waste resources recovery etc, has attracted people’s great interest.This paper mainly introduces the process and development of thermometallurgy and hydrometallurgy of copper. Keywords: Copper metallurgy , thermometallurgy, hydrometallurgy 铜是国民经济发展的重要原材料,特别是在电气工业方面应用更是广泛。对于中国铜工业来说,大力发展中国铜工业是全球经济一体化下的迫切需求。目前,我国是全球铜消费量位居首位的国家,同时也是铜加工工业大国,受到了社会各界的高度关注,因此从科学发展观的高度,探索我国铜冶金技术行业发展的路子非常重要。目前国内外的铜冶炼技术的发展主要还是以火法冶炼为主,湿法为辅。铜的火法生产量占总产量的80%左右。目前,全世界约有110座大型火法炼铜厂。其中,传统工艺(包括反射炉、鼓风炉、电炉)约占1/3;闪速熔炼(以奥托昆普炉为主)约占1/3;熔池熔炼(包括特尼恩特炉、诺兰达炉、三菱炉、艾萨炉、中国的白银炉、水口山炉等)约占1/3。下面主要介绍火法和湿法炼铜的现状和发展状况。 1、火法冶炼铜的现状及发展 目前火法熔炼技术发展迅速并得到广泛的应用, 在铜工业生产中已明确提出清洁生产的目标。环境意识要求清洁的生产工艺, 即工艺过程中极少排放废物, 对火法炼铜技术的进一步完善提出了更高的要求。下面叙述了目前世界火法炼铜的主要工艺、工业生产实例及进展情况, 对现代铜冶金新方法:闪速熔炼、熔池熔炼以及其它熔炼技术作了较为详细的介绍, 并指出了铜火法冶炼存在的问题及今后的主要技术发展方向。 1.1火法炼铜主要工艺 火法炼铜主要包括: 铜精矿的造锍熔炼,铜锍吹炼成粗铜,粗铜火法精炼,阳极铜电解精炼。经冶炼产出最终产品-电解铜(阴极铜)。目前世界铜冶炼厂使用的主要熔炼工艺为闪速熔炼和熔池熔炼。在熔池熔炼工艺中,精矿被抛到熔体的表面或者被喷入熔体内,通常向熔池中喷入氧气和氮气使熔池发生剧烈搅拌,精矿颗粒被液体包围迅速融化,因此 ,使含有氧气的气泡和包裹硫化铜/铁的溶液发生质量传递。而闪速熔炼中的干精矿是散布在氧气和氮气的气流中的,精矿中所含的硫和铁发生燃烧,在熔融颗粒进入反应空间时即产生熔炼和吹炼。当这些颗粒与
镁的冶炼方法主要分为两种
镁的冶炼方法主要分为两种:一是硅热还原法;二是电解法。目前国内的原镁厂家大都采用硅热还原法中的皮江法,以下就比较成熟的皮江法作简单的介绍。 皮江法生产金属镁是以煅烧白云石或菱镁矿石为原料、硅铁为还原剂、萤石为催化剂,进行计量配料。粉磨后压制成球,称为球团。将球团装入还原罐中,加热到1200℃,内部抽真空至13.3Pa或更高,则产生镁蒸气。镁蒸气在还原罐前端的冷凝器中形成结晶镁,亦称粗镁。再经加熔剂精炼,产出商品镁锭,即精镁。 皮江法炼镁生产工序: (1)白云石煅烧:将白云石在回转窑或竖窑中加热至1100~1200℃,烧成煅白(MgOCaO)。 (2)配料制球:将煅白、硅铁粉和萤石粉计量配料、粉磨,然后压制成球。 (3)还原:将料球在还原罐中加热至(1200+10)℃,在13.3Pa或更高真空条件下,保持8~10小时,氧化镁还原成镁蒸气,冷凝后成为粗镁。 (4)精炼铸锭:将粗镁加热熔化,在约710℃高温下,用熔剂精炼后,铸成镁锭,亦称精镁。 (5)酸洗:将镁锭用硫酸或硝酸清洗表面,除去表面夹杂,使表面美观。 镁合金的冶炼技术 镁合金熔炼工艺的关键是阻燃保护,其次是必须进行精炼处理以去除镁合金熔体中的金属杂质和非金属杂质夹渣及有害气体。 (1)准备工作 备齐工具,检查坩埚,清理炉膛内渣子等杂物,检修电阻丝,保证测温热电偶处在正常位置,使电气控制和自动控温正常,灵敏准确; (2)坩埚、炉料预热 炉料预热去除水分,防止爆炸等安全事故,同时减少炉料中水分带入合金液中的气体含量增加。 (3)装料熔化 在已预热的坩埚中加入预热的炉料,升温熔化。 (4)合金化和精炼 待温度升到熔化温度以上镁锭熔化后加入中间合金,并充分搅 拌使之均匀,再升温至适当的温度,向熔液中撒入精炼剂精炼。此过程关键是要控制好合金加入量和精炼的温度,这是由不同种类的合金决定的。 5)静置
先进制造技术论文
先进制造技术论文 学院:xxx 班级:xxx 姓名:xxx 学号:xxx 目录 ? ? ? ? ? ? ? 概述 摘要:随着我国制造业的的不断发展,先进制造技术得到越来越广泛的应用。介绍了先进制造技术和先进制造模式的内容和发展情况,从两种角度解释其结构特征和关系,并从各种不同角度展望先进制造技术和先进生产模式的发展前景及其趋势特征。 先进制造技术AMT(AdvancedManufacturingTecnology)是在传统制造的基础上,不断吸收机械、电子、信息、材料、能源和现代管理技术等方面的成果,将其综合应用于产品设计、制造、检测、管理、销售、使用、服务的制造全过程,以实现优质、高效、低耗、清洁、灵活生产,提高对动态多变的市场的适应能力和竞争能力的制造技术的总称,也是取得理想技术经济效益的制造技术的总称。 当前的金融危机也许还会催生新的先进制造制造技术,特别在生产管理技术方面。先进制造技术不是一般单指加工过程的工艺方法,而是横跨多个学科、包含了从产品设计、加工制造、到产品销售、用户服务等整个产品生命周期全过程的所有相关技术,涉及到设计、工艺、加工自动化、管理以及特种加工等多个领域,并逐步融合与集成。 可基本归纳为以下五个方面:
一、先进的工程设计技术 二、先进制造工艺技术 三、制造自动化技术 四、先进生产管理技术、制造哲理与生产模式 五、发展。 一、先进的工程设计技术 先进的工程设计技术包括众多的现代设计理论与方法。包括CAD、CAE、CAPP、CAT、PDM、模块化设计、DFX、优化设计、三次设计与健壮设计、创新设计、反向工程、协同产品商务、虚拟现实技术、虚拟样机技术、并行工程等。 (1)产品(投放市场的产品和制造产品的工艺装备(夹具、刀具、量检具等))设计现代化。以CAD为基础(造型,工程分析计算、自动绘图并提供产品数字化信息等),全面应用先进的设计方法和理念。如虚拟设计、优化设计、模块化设计、有限元分析,动态设计、人机工程设计、美学设计、绿色设计等等; (2)先进的工艺规程设计技术与生产技术准备手段。在信息集成环境下,采用计算机辅助工艺规程设计、即CAPP,数控机床、工业机器人、三坐标测量机等各种计算机自动控制设备设备的计算机辅助工作程序设计即CAM等。 二、先进制造工艺技术 (1)高效精密、超精密加工技术,包括精密、超精密磨削、车削,细微加工技术,纳米加工技术。超高速切削。精密加工一般指加工精度在10~μm(相当于IT5级精度和IT5级以上精度),表面粗糙度Ra值在μm以下的加工方法,如金刚车、金刚镗、研磨、珩磨、超精研、砂带磨、镜面磨削和冷压加工等。用于精密机床、精密测量仪器等制造业中的关键零件加工,如精密丝杠、精密齿轮、精密蜗轮、精密导轨、精密滚动轴承等,在当前制造工业中占有极重要的地位。 超精密加工是指被加工零件的尺寸公差为~μm数量级,表面粗糙度Ra值为μm 数量级的加工方法。此外,精密加工与特种加工一般都是计算机控制的自动化加工。 (2)精密成型制造技术,包括高效、精密、洁净铸造、锻造、冲压、焊接及热处理与表面处理技术。 (3)现代特种加工技术,包括高能束流(主要是激光束、以及电子束、离子束等)加工,电解加工与电火花(成型与线切割)加工、超声波加工、高压水加工等。电火花加工(Electricaldischargemachining(EDM)电火花加工electricsparkmachining)是指在一定介质中,通过工具电极和工件电极之间脉冲放电的电蚀作用对工件进行的加工。能对任何导电材料加工而不受被加工材料强度和硬度的限制。可分为电火花成型加工(EDM)和电火花线切割加工(电火花线切割加工electricaldischargewire–cutting--EDW) 两大类。一般都采用CNC控制。 (4)快速成型制造(RPM).快速成形技术是在计算机控制下,基于离散堆积原理采用不同方法堆积材料最终完成零件的成型与制造的技术。从成型角度看,零件可视为“点”或“面”的叠加而成。从CAD电子模型中离散得到点、面的几何信息,再与成型工艺参数信息结合,控制材料有规律、精确地由点到面,由面到体地堆积零件。 (5)先进制造工艺发展趋势 1)采用模拟技术,优化工艺设计; 2)成形精度向近无余量方向发展; 3)成形质量向近无“缺陷”方向发展; 4)机械加工向超精密、超高速方向发展; 5)采用新型能源及复合加工,解决新型材料的加工和表面改性难题; 6)采用自动化技术,实现工艺过程的优化控制;
金属镁冶炼工艺比较
金属镁冶炼工艺比较 李晓波 (山西阳煤丰喜股份责任有限公司闻喜复肥分公司闻喜礼元镇PC043802) 摘要:阐述了皮江法炼镁的存在的问题,提出了解决措施,指明了冶炼金属镁的最佳工艺是渣炼镁。 关键词:电解镁皮江法炼镁回转窑无渣炼镁硅铁Magnesium metal smelting process is compared Li Xiao-bo (Shanxi YangMei FengXi wenxi compound branch shares responsibility co., LTD Wenxi li yuan town pc043802) Abstract: expounds the existing problems of smelting magnesium was numerically simulated, and the solution measures are put forward, pointed out the best technology of smelting magnesium metal magnesium smelting slag. Key words: Electrolytic magnesium Pidgeon magnesium smelting Rotary kiln No slag smelting magnesiumFerrosilicon 2000年到今天, 中国金属镁企业均向万吨级转向,其总生产能力已超过80万吨/年,而全世界金属镁的使用量在60万吨/年以上,也就是说供大于求已是不争之实事,如何解决此矛盾,使企业走出困境,重点分析硅热法(皮江法)炼镁及碳热法炼镁。
铜冶炼基础知识
冶金概论讲义 1 冶金基本知识 1.1 冶金的概念及冶金方法分类 冶金就是从矿石或二次金属资源中提取金属或金属化合物,用各种加工方法制成具有一定性能的金属材料的过程和工艺。 冶金的技术主要包括火法冶金、湿法冶金以及电冶金, 根据冶炼金属的不同,冶金工业又了可以分黑色冶金工业和有色冶金工业,黑色冶金主要指包括生铁、钢和铁合金(如铬铁、锰铁等)的生产,有色冶金指后者包括其余所有各种金属的生产。 1.2 火法冶金 火法冶金是在高温条件下进行的冶金过程。矿石或精矿中的部分或全部矿物在高温下经过一系列物理化学变化,生成另一种形态的化合物或单质,分别富集在气体、液体或固体产物中,达到所要捉取的金属与脉石及其它杂质分离的目的。实现火法冶金过程所需热能,通常是依靠燃料燃烧来供给,也有依靠过程中的化学反应来供给的,比如,硫化矿的氧化焙烧和熔炼就无需由燃料供热;金属热还原过程也是自热进行的。火法治金过程没有水溶液参加,所以又称为干法冶金。火法冶金是提取金属的主要方法之一,其生产成本一般低于湿法治金。 火法冶金包括:干燥、焙解、焙烧、熔炼,精炼,蒸馏等过程。 1.3 湿法冶金 湿法冶金是在溶液中进行的冶金过程。湿法冶金温度不高,一般低于100℃,现代湿法冶金中的高温高压过程,温度也不过473K左右,极个别情况温度可达573K。 湿法冶金包括:浸出、净化、制备金属等过程。 (1)浸出用适当的溶剂处理矿石或精矿,使要提取的金属成某种离子(阳离子或络阴离子)形态进入溶液,而脉石及其它杂质则不溶解,这样的过程叫浸出。浸出后经沉清和过滤,得到含金属(离子)的浸出液和由脉石矿物绢成的不溶残渣(浸出渣)。对某些难浸出的矿石或精矿,在浸出前常常需要进行预备处理,使被提取的金属转变为易于浸出的某种化合物或盐类。例如,转变为可溶性的硫酸盐而进行的硫酸化焙烧等,都是常用的预备处理方法。 (2)净化在浸出过程中,常常有部分金属或非金属杂质与被提取金属一道进入溶液,从溶液中除去这些杂质的过程叫做净化。
镁合金文献综述
金属镁及其镁合金的制备与应用 摘要:本文评述了金属镁的制备,镁合金的种类,以及镁及其镁合金的应用。 关键词镁镁合金制备应用 镁是最轻的金属元素,其比重只有1.74,仅相当于铝的2/3,铁的1/4。而且镁资源特别丰富,占地壳总重量的2.1%,海水中的o.13%,可谓取之不尽,用之不竭。金属镁及其合金具有密度小、比强度和比刚度高、导电导热性能较好、阻尼减震和电磁屏蔽性能良好、易于加工成型、废料容易回收等优点[1],广泛应用于航天航空、交通运输、电子技术、光学器材、精密机械、日用商品等领域。由此镁及镁合金获得“21世纪的绿色工程材料”的美誉[2]。 1.金属镁的制备 金属镁的制备方法可分为两大类:电解法和热还原法。 1.1电解法炼镁[3-5] 电解法的原理是电解熔融的无水氯化镁,使之分解成金属镁和氯气。依据所用原料及处理原料的方法不同,可细分为以下具体的方法:道乌法、氧化镁氯化法、诺斯克法和光卤石法等[6]。以下主要介绍氧化镁氯化法和光卤石法。 1.1.1 氧化镁氯化法利用天然菱镁矿,在700~800℃下煅烧,80%得到活性较好的轻烧氧化镁。氧化镁的粒度要小于0.144mm,然后与碳素混合制团,团块炉料在竖式电炉中氯化,制得无水氯化镁,直接投入电解槽,最后电解得金属镁。 制备MgCL 2的程式为:2MgO+2CL 2 +C=2Mgcl 2 +CO 2 。 1.1.2 光卤石法将光卤石(Mgcl 2·kcl·6H 2 O)脱水后,直接电解制取金属镁。 光卤石脱水时水解反应不像Mgcl 2 那样严重,但也有一定的水解,因而在无水化 的处理过程中,也需要氯化过程,由于加入了,需要经常清理电解槽。 1.1.3 电解法制镁存在的问题 制备无水Mgcl 2 困难:在氯化镁的脱水过程中,由一水氯化镁脱水制取结 晶氯化镁的过程极易水解,产生碱式氯化镁[Mg(OH)CL]和氧化镁,生产工 艺较难控制;在HCL气氛下,水氯镁石脱水需要较高的温度(一般约为450℃), 能耗大,设备腐蚀严重。在金属镁的生产成本中,大约50%的费用用于Mgcl 2 脱水。金属镁的纯度较低:电解法制取的粗镁中主要含有电解质中的氯化物及Fe、Si、Ni、Cr、Mn和K、Na等金属杂质,其存在会降低镁及其合金的耐腐蚀性能,因此需要采取措施,提高镁的纯度。 1.2 热还原法炼镁 热还原法的典型代表是皮江法,皮江法是1940年左右发展起来的一 种炼镁方法[7],我国目前约98%以上的原镁是由皮江法生产的。皮江法将煅烧白 云岩和硅铁按一定配比磨粉,压成团块,在高温和真空条件下,使煅烧白云岩 中的氧化镁还原为镁蒸气,然后冷凝结晶为粗镁,再经精炼制得镁锭。
先进制造技术结课论文
先进制造技术课程论文 学院:机电学院 专业:机械设计制造及其自动化 姓名: 学号: 2014年4月20
自动化立体仓库的基本设施与特点 摘要:自动化立体仓库又称自动化高架仓库和自动存储系统。它是一种基于高层货架、采用电子计算机进行控制管理、采用自动化存储输送设备自动进行存取作业的仓储系统。自动化立体仓库是实现高效率物流和大容量的关键系统,在自动化生产和商品流通中具有举足轻重的作用。 自动化立体仓库系统最早在美国诞生。20世纪50年代初美国开发了世界上第一个自动化立体仓库,并在60年代即采用计算机进行自动化立体仓库的控制和管理。日本在1967年制造出第一座自动化立体仓库,并在此后的20年间使这一技术得到广泛应用。进入20世纪80年代,自动化立体仓库在世界各国发展迅速,使用的范围涉及几乎所有行业。 关键字:自动化;立体仓储;发展;高效率; 正文: 一、自动化立体仓库的概述 (一)、自动化立体仓库的发展 随着现代工业发展的发展,柔性制造系统、计算机集成制造系统和工厂自动化对自动化仓库提出更高的要求,搬运存储技术要具有更可靠更实时的信息,工厂和仓库中的物流必须伴随着并行的信息流。无线数据通信、条形码技术和数据采集越来越多的应用于自动化立体仓库系统。 在自动化立体仓库发展过程中,经历了自动化、集约化、集成化和智能化几个发展过程。自动化时期主要在20世纪60到70年代,随着计算机技术的发展,自动化立体仓库得到了迅猛发展。在1967到1977年 10年中,日本建设超过了8000套自动化立体仓库系统。集约化发展是伴随大规模生产需求而发展的。其 规模曾经发展到超过100个巷道,货位数超过20万个。但事实表明,大型自动化立体仓库系统已不再是发展方向。美国Hallmark公司安装的多达120个巷道的系统已经达到巅峰。为了适应工厂发展的新趋势,出现了规模更小,反应速度更快,用途更广的自动化仓库系统。它结合先进的控制技术,应用到分段输送和按预定线路输送方面保持了高度的柔性和高生产率,满足了工业库存搬运的需要。儿大规模的立体仓库系统一般应用于大型配送中性。集成化的标志是随着信息系
镁的冶炼及应用
书山有路勤为径,学海无涯苦作舟 镁的冶炼及应用 一、镁的冶炼A.融盐电解法炼镁 1.工艺方法可分为以菱镁矿为原料的无水氯化镁电解法和以海水为原料制取无水氯化镁的电解法。其中后者最大的难点是如何去MgCl2-6H2O 中的结晶水。电解法生产镁的工艺很多,但基本原理相同,其中最有代表性的有DOW 工艺、I.G.Farben 工艺、Magnola 工艺等。 2.生产过程镁电解采用多组分氯盐作电解质。向氯化镁电解质中加入其他组分的目的是要降低熔点和粘度,提高熔体的电导率以及降低MgCl2 的挥发度和水解作用等。阴极产生的液态镁因比电解质的密度小而上浮于表面;阳极产生的氯气则通过氯气罩排出。B.皮江法炼镁 1.工艺原理皮江法生产金属镁是以煅烧白云石为原料、硅铁为还原剂、萤石为催化剂,进行计量配料。粉磨后压制成球,称为球团。将球团装入还原罐中,加热到1200℃,内部抽真空至13.3Pa 或更高,则产生镁蒸气。镁蒸气在还原罐前端的冷凝器中形成结晶镁,亦称粗镁。再经熔剂精炼,产出商品镁锭,即精镁。 2.生产工序(1)白云石煅烧:将白云石在回转窑或竖窑中加热至1100~1200℃,烧成煅白(MgOCaO)。(2)配料制球:将煅白、硅铁粉和萤石粉计量配料、粉磨,然后压制成球。(3)还原:将料球在还原罐中加热至1200+10℃,在13.3Pa 或更高真空条件下,保持8~10 小时,氧化镁还原成镁蒸气,冷凝后成为粗镁。(4)精炼铸锭:将粗镁加热熔化,在约710℃高温下,用溶剂精炼后,铸成镁锭,亦称精镁。(5)酸洗:将镁锭用硫酸或硝酸清洗表面,除去表面夹杂,使表面美观。(6)造气车间:将原煤转换成煤气,作为燃料使用。直接使用原煤的镁厂没有造气车间。二、镁的应用A.铝合金生产由于镁的密度小,比强度高,并能与铝、铜、锌等金属构成高强度合金,因此,镁是重要的合金元素。世界上镁的最大消费领域是作铝合金添加元素。2002 年世界主要地
全球铜冶炼新技术简述pdf
全球铜冶炼新技术简述 冶炼是萃取冶金的一种形式,其主要用途是从矿石中生产一种金属。这包括从铁矿石中萃取铁,从铜矿石中萃取铜,以及从其他矿石中萃取其他基本金属。 冶炼不仅仅是从矿石中熔炼出来金属,大多数矿石提炼出来的是金属的化合物,含有多种元素,例如氧(一种氧化物),硫(一种硫化物),或者碳和氧在一起(一种碳酸盐)。为了生产金属,这些化合物必须经过一个化学反应,所以冶炼是利用适合的还原物质和那些氧化的元素结合来分离金属。 从历史上讲,第一次冶炼工艺采用碳(木碳形式)还原锡(SnO2)、铜(CuO)、铅(PbO)以及铁(Fe2O3)。在所有这些反应中还原剂实际上是一氧化碳(CO),当木碳和氧化物仍是固态时,它们互相之间不能发生反应。对于铜和铅来讲,主要的矿石是硫化物,即:CuS2和PbS。这些硫化物必须先在空气中焙烧转化成氧化物。 锡和铅 很久以前,第一批冶炼的金属是锡和铅。公元前6500年,土耳其安纳托利亚的Catal H?yük发现铸铅珠,这比发明文字还早几千年,却没有记载铸铅球是如何冶炼出来的。然而,在偶然的机遇中将矿石放入木材火里,于是就冶炼出来锡和铅。 铜和青铜 在锡和铅之后,下一个要冶炼的金属似乎就是铜,如何发现铜仍存在很大争议。人们猜测铜的第一次冶炼是在陶器窑里进行的。在欧洲和近东最早发现铜冶炼是在伊朗,距今约公元前6000年,第一个冶炼铜的人工制品是在Can Hasan发现的一个权杖头。而铜冶炼最早的依据要追溯到公元前5500年到公元前5000年之间,在塞尔维亚的普罗科尼克(Plocnik)和拜罗沃德(Belovode)发现的,而现代铜的冶炼工艺经历了技术的更新。 无碳冶炼技术 最近,完全拥有自主技术产权的铜冶炼技术通过了中国有色金属协会在山东东营组织的专家审查,实现了在铜冶炼工艺的第一个碳零排放,并且开启了中国有色工业低碳发展的新途径。 专家们相信,无碳铜冶炼技术在主要技术参数上比以前的铜冶炼技术都好,经济和技术方面具有方便,低成本,环保和灵活度上都具有优势。已经证明无碳铜冶炼技术非常适合有色金属冶炼企业的技术更新。 Xstrata铜冶炼技术 Xstrata的ISA SMELT铜冶炼技术的提供了一种创新,高强度,低成本浸没式喷枪冶炼技术工艺,操作简单,可以用于铜和铅冶炼,ISA SMELT主要用于铅和铜冶炼和吹炼生产,在全球应用,包括澳大利亚、美国、比利时、
铜冶炼
铜冶炼方法综述 摘要:目前世界上从硫化矿中提取铜, 85% ~90%是采用火法冶炼,因为该法与湿法冶炼相比,无论是原料的适应性,还是在生产规模、贵、稀金属富集回收方面都有明显的优势。因此为了降低能耗,减少火法炼铜的环境污染,闪速熔炼、熔池熔炼以及其它熔炼技术都在不断改进和发展。 关键词:铜冶炼火法炼铜熔池熔炼闪烁熔炼 1.前言 随着环境保护的日益严格,铜冶金工业面临着严峻挑战。当今世界铜冶金方法主要有火法和湿法两种,其中火法占主导地位。火法冶金种类较多,目前国际上存在的主要火法炼铜工艺有闪速炉、反射炉、鼓风炉、诺兰达炉、艾萨炉(奥斯麦特炉)、瓦纽可夫炉、三菱炉、特尼恩特炉、电炉、白银炉等十几种冶炼工艺。大部分工艺存在能力低、成本高、能耗大、污染严重等问题,严重制约着铜冶金工业的发展。 2.火法炼铜 火法炼铜主要包括[1]: (1)铜精矿的造锍熔炼;(2)铜锍吹炼成粗铜; (3)粗铜火法精炼; (4)阳极铜电解精炼。经冶炼产出最终产品-电解铜(阴极铜)。 2.1熔炼 2.1.1熔池熔炼 在熔池熔炼工艺中,精矿被抛到熔体的表面或者被喷入熔体内,通常向熔池中喷入氧气和氮气使熔池发生剧烈搅拌,精矿颗粒被液体包围迅速融化,因此,吹炼反应能够产生维持熔炼作业所需的大部分热量,使含有氧气的气泡和包裹硫化铜/铁的溶液发生质量传递。 澳斯麦特熔炼法/艾萨熔炼法是20世纪70年代由澳大利亚联邦科学工业研究组织矿业工业部J.M.Floyd博士领导的研究小组发明的。随后芒特#艾萨矿物控股有限公司(简称MIM)和澳大利亚国家科学院(简称CSIRO)在20世纪80年代联合开发了艾萨熔炼法,MIM于1987年在铜冶炼厂建起了一座示范工厂, 1996年MIM开发了Enterprise和ErnentHenry矿,铜精矿产量增加,于是决定扩建铜
皮江法冶炼镁的工艺过程与优缺点
皮江法冶炼镁的工艺过程与优缺点 镁的冶炼方法总体上可分成三种:一种是电解法;一种是硅热法(皮江法);另一种是碳热法。 皮江法是一种应用广泛的镁的冶炼方法,以发明者皮江(L_M.Pidgeon)命名的这种方法应用时间较长,可称是硅热法炼镁的经典方法。与其他方法相比,此法具有建厂快、投资省、可利用多种热源、产品质量好等优点,但由于间歇作业、单台生产能力低、能耗较高等问题,而影响它的发展。加拿大蒂尼柯(Timminco)公司的哈雷(taley)镁厂于1941年最先采用皮江法炼镁生产金属镁。随后,日本古河镁厂和字部兴产镁厂也先后采用这种炼镁方法。70年代以后,这些炼镁厂对皮江法炼镁的工艺和设备进行了改进,并逐步实现机械化、自动化操作后,进一步改善了作业条件和提高了劳动生产率。 皮江法炼镁的主要工艺流程是:
白云石在回转窑或立窑中煅烧成煅白,经破碎后与硅铁粉(含硅75%)和萤石粉(含GaF2)=95%)混合均匀制团,装入耐热不锈钢还原罐内,置于还原炉中,在1200-1250℃及真空的1.33Pa 真空度下还原制取粗镁,经过熔剂精制、铸锭、表面处理得到成品镁锭。 具体工艺过程: (1)白云石煅烧:将白云石在回转窑或竖窑中加热至1100~1200℃,烧成煅白(MgOCaO)。 白云石煅烧天然白云石是一种分布很广的矿物,其分子式为MgCO3?CaCO3。用于皮江法炼镁的白云石一般含MgO19%~21%、CaO30%~33%、(SiO2+A12O3+Fe2O3)<0.5%、(Na2O+K2O)<0.05%,粒度10~30mm。白云石要先进行煅烧。国际上主要的皮江法炼镁厂均采用回转窑煅烧法,使用的燃料有天然气、重油、重油焦粉(或煤粉)、半水煤气、焦炉煤气、发生炉煤气等。白云石在1423~1473K温度下煅烧,分解成Mg()?CaO。经煅烧的白云石称煅烧白云石,含MgO37%~39%,灼减1%以下(最好0.5%以下),活度超过30%。 (2)配料制球:将煅白、硅铁粉和萤石粉计量配料、粉磨,然后压制成球。 粉磨与压球煅烧白云石与破碎过的硅铁(Si>75%、Al<1.5%。Mn<0.05%)按摩尔比Si:MgO=1.2~1.3配料,并加入总料质量3%的萤石粉((2aF2>95%)。将配好的物料磨细至O.1mm粒级以下的煅烧白云石占60%,0.075mm粒级以下的硅铁占70%~80%。磨细的物料经混合后,用对辊式压球机在大于150MPa的压力下压制成球团。压制好的球团装入防潮的纸袋中备用。 (3)还原:将料球在还原罐中加热至1200+10℃,在13.3Pa或更高真空条件下,保持8~10小时,氧化镁还原成镁蒸气,冷凝后成为粗镁。 真空热还原球团料装入还原炉的还原罐中于真空下被硅铁中的硅还原成金属镁的过程。
镁产业发展历程
一、引言 镁属轻金属元素,其比重只有1.74g/cm3,仅为铁的1/5、铝的2/3,与塑料相近。镁的储藏量极为丰富,占地壳含量的2.8%,海水含量的0.13%,在工程金属中仅次于铝、铁而居第三位。镁合金是在纯镁中加入铝、锌、锰和稀土等元素形成的,具有许多优良性能,在交通、计算机、通讯、消费类电子、国防军工等诸多领域具有极为广泛的应用前景。由于受技术和价格等因素的限制,长期以来镁合金只少量应用于航空、航天等军事工业。二十世纪七、八十年代以来,随着全球节能和环保法规的日趋严格,对汽车减重节能降耗的要求不断高涨,轻量化已成为汽车选材的主要发展方向。镁合金作为工业应用最轻的金属工程材料,具备阻尼减震等优良性能,成为汽车轻量化的首选材料。此外,镁合金由于具有比强度高,导热导电性、电磁屏蔽性以及环境相容性好等优良性能,可代替塑料壳体满足3C(计算机、通讯、消费类电子)产品轻、薄、小型化、高集成化以及严格的环保要求,在信息产业中得到了广泛的应用。但镁及镁合金作为一种轻金属材料,其应用潜力尚未充分挖掘出来,生产加工及应用技术还远不如钢铁、铜、铝等金属材料成熟。因此,在许多传统金属矿产资源趋于枯竭、环境污染日益严重的今天,加速镁及其合金的应用开发和产业化,已成为当今世界各国和地区所普遍关注的战略问题。基于上述原因,上个世纪九十年代以来,全球掀起了镁合金开发应用热潮,世界各工业发达国家从战略高度纷纷出台大型研究计划推动镁合金在交通、计算机、通讯、消费类电子、国防军工等诸多领域的应用。随着技术和价格两大瓶颈的突破,全球镁合金用量急剧增长,应用范围不断
扩大,正在成为继钢铁、铝之后的第三大金属工程材料,被誉为“21世纪绿色工程材料”。 我国镁资源储量、生产量和出口量世界第一。上世纪九十年代以来,随着我国镁冶炼技术的不断完善和在劳动力方面的优势逐渐显现,中国造原镁在国际市场上的竞争力越来越强。1990年~2001年我国原镁产量增长了40倍,从镁进口国一跃成为全球最大的镁生产国和出口国。目前我国原镁已占全球产能的3/4,产量的1/2。但与国外相比,我国镁合金应用开发严重滞后,80%以上的原镁作为初级原料低价出口,属典型的以牺牲资源和环境为代价的原料出口型工业,已连续几次被欧盟和北镁反倾销,原镁生产企业面临严重压力,与我国作为镁生产和出口大国的地位极不相称。为改变这种局面,“十五”计划期间,国家科技部启动了“十五”国家科技攻关计划重大项目“镁合金应用开发与产业化”,其最终目标是建立镁合金技术创新体系,加强应用开发,培育具有国际竞争力的镁合金及相关高新技术产业群,将我国的镁资源优势转化为经济优势。同时,国家“863”高技术研究计划新材料领域、国家中小企业创新基金等计划也启动了对镁合金研发及产业化的支持工作,国家发改委也将镁合金产业化列为高技术产业化示范项目。此外,有关地方政府配合国家项目也对镁合金的技术研发与产业化工作给予了支持。 在国家政策引导和市场驱动下,通过产学研联合攻关,目前在北到长春、沈阳,南到珠江三角洲,西到宁夏、青海,东到胶东半岛、长江三角洲以及西南的重庆、四川等辽阔的中国土地上,已经形成从高品质镁及镁合金、镁合金关键装备与工艺、镁合金应用产品开发生产到产业化示范基地建设的一条完整的镁合金技术创新
铜冶炼工艺
铜冶炼工艺 粗铜的火法精炼 火法精炼原理:粗铜中多数杂质对O的亲和力大于Cu对O的亲和力,而且,杂质氧化物在Cu中的溶解度非常小,因此,杂质以氧化物炉渣的形式出去。同时氧化过程的进行使铜中产生过量的氧化铜,最终需要还原得到粗铜。即粗铜的火法精炼分为氧化过程和还原过程。 1.氧化过程(氧化除渣阶段) 空气进入铜熔体,首先与铜反应生成Cu2O,再与其它金属杂质 作用使杂质氧化,化学反应如下: 4Cu+O2→2Cu2O Cu2O+Me→MeO+Cu 反应式中的Me代表金属杂质。 2.还原过程(还原得到阳极铜) 氧化除渣后铜液中的Cu2O,用还原剂进行还原: Cu2O+H2→2Cu+H2O Cu2O+CO→2Cu+CO2 Cu2O+C→2Cu+CO 还原剂有:重油、天然气、液化石油气、木炭等。得到的阳极铜送电解车间进行电解精炼。
铜的电解精炼 铜的电解精炼,是将火法精炼的铜浇铸成阳极板,用纯铜薄片作为阳极片,相间地装入电解槽中,用硫酸铜和硫酸的水溶液作电解液,在直流电的作用下,阳极上的铜和电位较负的金属溶解进入溶液,而贵金属和某些金属(硒、碲)不溶,成为阳极泥沉淀于电解槽底,溶液中的铜在阳极上优先析出,而其他电位较负的金属不能在阳极上析出。这样,阳极上析出的金属铜纯度很高,成为阴极铜或电解铜。 电解精炼过程: 阳极:火法精炼铜; 阴极:电解铜(阴极铜); 电解液:硫酸铜和硫酸的水溶液。 引入直流电,阳极铜溶解,在阴极析出纯铜,杂质进入阳极泥或电解液,从而实现铜和杂质的分离。 1.阳极反应 电解液中含有H+、Cu2+、SO42-和水分子,当通入直流电时,在阳极上可能的氧化反应为: Cu-2e→Cu2+ Me-2e→Me2+ SO42--2e→SO3+1/2O2 H2O-2e→2H++1/2O2 Me指Fe、Pb、Ni、As、Sb等,电极电位比铜负,与铜一起溶解进入电解液;SO42-和H2O电极电位比铜正得多,在阳极上不可能进行
炼铁工艺流程图描述
熔炼工艺流程及简介 1 熔炼炉生产概况 熔炼炉是制铁工艺流程的主体,它是由耐火砖砌筑的竖立圆筒炉体,外壳钢枝制作,外壳与耐火砖之间有冷却设备,我公司450m3熔炼炉冷却壁共有348块,共分12层冷却壁;一层冷却板;1-3层为光板冷却壁、材质耐热铸铁冷却壁;4-12层为镶砖冷却壁材质是铁素体球墨铸铁冷却壁;6-7层冷却壁之间有一层冷却板,炉喉有18块水冷炉喉钢砖,炉缸有一个铁口、2个渣口、14个风口;从其上部装入矿石,熔剂和燃料向下运动,下部鼓入被加热的空气。熔炼炉生产的主要产品是生铁,副产品有炉渣和煤气,炉渣可用来制作水泥,保温材料、建筑材料和肥料,煤气可以做为燃料供给各用户。 1.1熔炼炉生产的主要工艺过程: 1.1.1供料 熔炼炉冶炼用的主要原燃料:块矿、烧结矿、石灰石、焦炭,有K1、J1皮带机把原燃料送到1#转运站,经K2、J2皮带机、分料车运到指定的矿槽。 1.1.2上料 由料仓输出的原料,燃料和熔剂,经仓下给料机、振动筛、经筛分、称量后,用料车按一定比例一批一批有序地送到熔炼炉炉顶,并卸入炉顶受料斗。 1.1.3装料 炉顶装料设备的任务就是把提升到炉顶的炉料,按一定的工作制度装入熔炼炉炉喉。 1.1.4冶炼 熔炼炉冶炼主要是还原过程,把铁氧化物还原成含有碳、硅、锰、硫、磷、镍、铬等杂质的铁合金。由鼓风机连续不断地把冷风送到热风炉加热到1100~1250℃,再通过炉缸周围的风口进入熔炼炉,由炉顶加入的焦炭和风口鼓入的热空气燃烧燃料,产生大量的煤气和热量,使矿石源源不断地熔化还原,产生的铁水和熔渣贮存在熔炼炉炉缸内,定期地由铁口和渣口排出。 1.1.5产品处理 在渣铁处理中,出铁前先从渣口放出溶渣,流入冲渣沟进行粒化后,以脱水器脱水,有皮带运到渣仓。设有一个应急用干渣坑,出铁时,用液压开口机打开铁口,使铁水流入铁水罐车运到铸铁机铸成铁块,出完铁后用液压泥炮把铁口堵上。 经熔炼炉顶部导出的煤气通过重力除尘器、布袋除尘过滤后,经调压阀组调压后输往各煤气用户使用,从重力除尘器、布袋除尘器排出的炉尘,经过处理回收运往焙烧厂作为烧结原料。
铜冶炼的工艺流程及原理
铜冶炼的工艺流程及原理-标准化文件发布号:(9456-EUATWK-MWUB-WUNN-INNUL-DDQTY-KII
铜冶炼技术的发展经历了漫长的过程,但至今铜的冶炼仍以火法冶炼为主,其产量约占世界铜总产量的85%。 1)火法冶炼一般是先将含铜百分之几或千分之几的原矿石,通过选矿提高到20-30%,作 为铜精矿,在密闭鼓风炉、反射炉、电炉或闪速炉进行造锍熔炼,产出的熔锍(冰铜)接着送入转炉进行吹炼成粗铜,再在另一种反射炉内经过氧化精炼脱杂,或铸成阳极板进行电解,获得品位高达99.9%的电解铜。该流程简短、适应性强,铜的回收率可达95%,但因矿石中的硫在造锍和吹炼两阶段作为二氧化硫废气排出,不易回收,易造成污染。 近年来出现如白银法、诺兰达法等熔池熔炼以及日本的三菱法等、火法冶炼逐渐向连续化、自动化发展。 2)现代湿法冶炼有硫酸化焙烧-浸出-电积,浸出-萃取-电积,细菌浸出等法,适于低 品位复杂矿、氧化铜矿、含铜废矿石的堆浸、槽浸选用或就地浸出。湿法冶炼技术正在逐步推广,预计本世纪末可达总产量的20%,湿法冶炼的推出使铜的冶炼成本大大降 低。 向左转|向右转 电解铝的基本原理和工艺过程:电解铝就是通过电解得到金属铝。现代电解铝工业生产采用冰晶石-氧化铝熔融电解法。熔融冰晶石是溶剂,氧化铝是溶质,以碳素体作为阳极,铝液作为阴极,通入强大的直流电后,在950℃~970℃下,在电解槽内进行电化学反应。阳极主要产物是二氧化碳和一氧化碳气体,其中含有一定量的氟化氢等有害气体和固体粉尘,该气体需经过净化处理后排空。阴极产物是铝液,铝液通过真空抬包从电解槽内抽出,送至铸造车间,在保温炉内经净化澄清后,浇铸成铝锭或直接加工成线坯、型材等 生产工艺流程其生产工艺流程如下图: 氧化铝氟化盐碳阳极直流电↓ ↓ ↓ ↓ ↓ 排出阳极气体------ 电解槽↑ ↓ ↓ 废气← 气体净化铝液↓ ↓ 回收氟化物净化澄清----------------------- ↓ ↓ ↓ 返回电解槽浇注轧制或铸造↓ ↓ 铝锭线坯或型材方程电解铝就是通过电解得到的铝. 重要通过这个方程进行:2Al2O3==4Al+3O2。阳极:2O2ˉ- 4eˉ=O2↑ 阴极:Al3+ +3eˉ=Al 粗铜的火法精炼:火法精炼原理:粗铜中多数杂质对O的亲和力大于Cu对O的亲和力,而且,杂质氧化物在Cu中的溶解度非常小,因此,杂质以氧化物炉渣的形式出去。同时氧化过程的进行使铜中产生过量的氧化铜,最终需要还原得到粗铜。即粗铜的火法精炼分为氧化过程和还原过程。 1. 氧化过程(氧化除渣阶段)空气进入铜熔体,首先与铜反应生成Cu2O,再与其它金属杂质作用使杂质氧化,化学反应如下:4Cu+O2→2Cu2O Cu2O+Me→MeO+Cu 反应式中的Me代表金属杂质。 2. 还原过程(还原得到阳极铜)氧化除渣后铜液中的Cu2O,用还原剂进行还原:Cu2O+H2→2Cu+H2O Cu2O+CO→2Cu+CO2 Cu2O+C→2Cu+CO 还原剂有:重油、天然气、液化石油气、木炭等。得到的阳极铜送电解车间进行电解精炼。铜的电解精炼:铜的电解精炼,是将火法精炼的铜浇铸成阳极板,用纯铜薄片作为阳极片,相间地装入电解槽中,用硫酸铜和硫酸的水溶液作电解液,在直流电的作用下,阳极上的铜和电位较负的金属溶解进入溶液,而贵金属和某些金属(硒、碲)不溶,成为阳极泥沉淀于电解槽底,溶液中的铜在阳极上优先析出, 2
烧结技术综述
1文献综述 1.1烧结生产概况 1.1.1烧结及其发展 烧结法是迄今为止除北美以外使用最为广泛的铁矿石造块方法。自20世纪80年代起烧结技术得到了快速发展,主要体现在烧结工艺和新技术的研究开发和应用上。烧结工艺方面如自动化配料、混合料强化制粒、偏析布料、冷却筛分、整粒技术及铺底料技术等;新技术主要表现为球团烧结技术、小球烧结技术、低温烧结技术等。上述工艺和技术目前已经在大部分钢铁企业推广应用,并取得了显著的经济效益。 1897年,T.Huntington和F,Heberlein申请并注册了第一个有关烧结方面的专利。1905年,E.J.Savelsberg首先把T.Huntington-F.Heberlein烧结杯用于铁矿石烧结,从而开辟了烧结法进行铁矿粉造块的新纪元。在当今的冶金生产中,烧结已成为一道重要的单元工序并占有相当重要地位。据统计,全世界约有一半的生铁是用烧结矿生产的。过去十年中,世界上烧结矿年产量维持在538×106t~586×106t范围内。从1989年起,由于独联体和其他部分东欧国家发生巨变,因此,它们的钢铁工业进行了重新调整,导致烧结矿产量有所下降。欧洲和日本的经济衰退也影响了产量,但是不久烧结矿的产量又慢慢恢复。东欧和独联体的产量将下降,而中国、朝鲜和台湾的产量将继续上升。尽管出现新的炼铁工艺,但是在下一个十年中或更长的时间内,它们仍不可能对高炉产量有巨大影响。因此,烧结矿产量在未来相当长的时间内仍将维持在目前水平。 1.1.2烧结生产目的 铁矿粉烧结是一种铁矿粉造块的方法,是将细粒含铁物料与燃料、熔剂按一定比例混合,再加水润湿、混匀和制粒成为烧结料,加于烧结设备上,点火、抽风,借助燃料燃烧产生高温和一系列物理化学变化,生成部分低熔点物质,并软化熔融产生一定数量的液相,将铁矿物颗粒润湿粘结起来,冷却后,即成为具有一定强度的多孔块状产品一侥结矿。 烧结生产的目的主要是: 1.将粉状物料制成具有高温强度的块状料以适应高炉冶炼、直接还原等在流体力学方面的要求; 2.通过烧结改善铁矿石的冶金性能,使高炉冶炼指标得到改善; 3.通过烧结去除某些有害杂质,回收有益元素以达到综合利用资源和扩大炼铁矿石原料资源的目的。 1.1.3烧结反应过程 烧结反应过程是分层依次向下进行的。抽入的空气通过已烧结好的热烧结矿
先进制造技术文献综述详解
摘要:介绍了电火花加工控制涉及的主要问题及放电状态检测方法。详细论述了近20年来自适应控制、模糊控制、神经网络控制、遗传算法、专家系统、混合智能控制等在电火花加工中的研究状况。对电火花加工过程中控制变量的优化及过程监测与控制等进行了讨论,就控制技术在电火花加工中的发展趋势进行了展望。 关键词: 电火花加工;自适应控制;模糊控制;人工神经网络控制;混合智能控制 一、前言 经过半个多世纪的研究和开发,电火花加工已成为制造业中一种重要的加工手段,在机械、宇航、电子、仪器、轻工、汽车等领域获得了广泛的应用。然而,电火花加工过程是一个典型的非线性过程[1],影响加工过程的因素很多,其中主要是电源参数和伺服运动参数。电源参数主要包括开路电压、电流、脉冲宽度、脉冲间隔、间隙平均电压、电极放电时间周期等;伺服运动参数包括电极抬刀周期、电极抬刀高度和抬刀速度等;还有其他因素如:工件材料、放电点分布情况、加工深度、电介质浓度、有无冲油等。这些因素相互影响、相互制约,造成了电火花加工过程控制的复杂性。 二、正文 本文将介绍电火花加工涉及的主要控制问题和目前的状态检测技术,然后分别叙述6种控制方式(自适应控制、模糊控制、神经网络控制、遗传算法、专家系统、混合智能控制)在电火花加工过程中的应用情况。 1 电火花加工控制技术 1.1 电火花加工中的主要控制问题 控制对电火花加工质量的优劣一直起着举足轻重的作用,电火花加工过程需解决的主要控制问题有[2]: (1)为了形成有效的放电脉冲,工具电极和工件被加工表面之间必须保持一定的放电间隙,故需控制极间间隙的伺服运动。 (2)要形成稳定、高效的电火花加工,火花放电必须为瞬时的脉冲性放电,故电火花加工必须采用脉冲电源。而脉冲电源的各参数(如:极性、脉宽、脉间、电流幅度)与加工状态及加工