毕业设计-齿轮环焊缝超声自动检测装置设计
超声波探伤论文-超声波探伤毕业论文

超声波探伤论文-超声波探伤毕业论文摘要本毕业设计的课题是板材焊缝超声波探伤测试。
主要任务是在掌握过程设备制造流程和焊接缺陷及其产生原因的基础上,研究超声波探伤技术在钢制压力容器对接焊接接头探伤检测中的应用,并给出焊缝返修的具体方案。
本文详述了国内外超声检测技术的发展和现状,并在简述过程设备制造、焊接及无损探伤的基础上详细介绍了超声波探伤技术及其在焊缝无损探伤中的应用及评定等级和注意事项。
针对给定的板材焊缝,通过实验检测该焊缝的缺陷,本文详细介绍了试块选用,设备调试,现场探伤中的常见问题及解决方法。
同时给出了现场探伤、缺陷定位和长度测量的具体方法,并通过GB11345-89标准对试验中检测到的缺陷进行了等级评定并得出了检测工艺卡。
关键词:焊缝;超声波探伤。
AbstractThe task of the graduation design is the plate weld ultrasonic testing. The main task is to master the process equipment manufacturing and welding defects and its causes, study of ultrasonic flaw detection technology in steel pressure vessel butt welded joint flaw detection, and gives the concrete plan of the weld repairing. This paper describes the domestic and foreign development and present situation of ultrasonic detection technology, and in the process equipment manufacturing, welding and nondestructive testing based on detailed introduces the ultrasonic detection technology and its application in weld NDE and rating and matters needing attention. For a given plate welding, the weld defects detection by experiment, this paper introduces the test block selection, equipment commissioning, on-site inspection of the common problems and solutions. At the same time provides on-site testing, defect location and length measurement methods, and through the GB11345-89 standard to test the detected defects were rating and the detection process card.Key words: Weld; ultrasonic testing目录1.1选题的背景及意义过程设备是各个工业部门不可缺少的重要生产设备,用于供热、供电和储存各种工业原料及产品,完成工业生产过程必需的各种物理过程和化学反应。
全自动超声波检测技术在管道对接环焊缝检测中的应用

试验研究N DT 无损检测全自动超声波检测技术在管道对接环焊缝检测中的应用田国良(葫芦岛市特种设备监督检验所,辽宁葫芦岛 125001)摘 要:介绍了全自动超声波检测技术在管道对接环焊缝检测中的应用。
采用全自动超声波检测、手动超声波检测以及射线检测方法对预制缺陷进行了检测。
通过金相解剖对比三种检测方法的优劣,发现全自动超声波检测技术的优势和发展潜力,得出超声波衍射时差法结合超声脉冲反射法可有效检测管道对接环焊缝缺陷。
关键词:全自动超声波检测;手动超声波检测;射线检测;超声波衍射时差法;预制缺陷 中图分类号:T G115.28 文献标识码:A 文章编号:100026656(2007)0820472205Application of Automatic U ltrasonic T esting T echnology in the Inspectionof Butt G irth Welds of PipelineTIAN G uo2liang(Huludao Special Equipment Supervision and Inspection Institute,Huludao Liaoning125001,China)Abstract:The application of automatic ultrasonic testing for the inspection of butt girth welds of pipeline was introduced.Automatic ultrasonic testing,manual ultrasonic testing and radiographic testing techniques were used on the inspection of embedded parisons between existing testing results showed that automatic ultrasonic testing had great advantages and bright application f uture.Final conclusion was drawn that the combination of both time of flight diffraction technique and pulse echo technique was effective for the butt girth welds testing of pipeline.K eyw ords:Automatic ultrasonic testing;Manual ultrasonic testing;Radiographic testing;Time of flight diffraction technique;Embedded defect 2006年伊朗IO EC公司在中国石油天然气管道局考察全自动超声波检测(以下简称AU T)应用于伊朗海上管道工程项目的效果时,提出在X70钢、<1016mm×21mm管件上用手工焊接预制11个缺陷(裂纹、未熔合、根部未焊透、夹渣及气孔等),分别采用AU T、手动超声波检测(以下简称MU T)以及射线检测(以下简称R T)进行对比试验,以验证AU T方法的可靠性[1,2]。
开题报告圆桶焊缝超声检测机械装置

(3)探测装置
探测移动平台驱动系统:采用丝杠螺母,可以由步进电机进行驱动。
四、准备工作情况和主要工作措施:
(一)准备工作情况:
根据设计题目可知,需设计一台可以对一定长度和直径的金属管管体进行焊缝超声检测的机械装置。其中,金属管件长度、直径以及壁厚存在一定范围的变量。机械装置流程如下:送料装置 夹紧装置 探测装置 夹紧装置 送料装置 初始步骤(送料装置)
六、文献综述:
1 无损检测技术简介
(1)超声波检测
超声波是一种机械波,具有传播能量损失小、穿透能力强、传播距离大等特点。超声波从一种介质进入到另一种介质时,若两种介质的声阻抗相差较大时,就会在两种介质的分界面产生反射,这就是变压器绕组变形的检测原理。
超声检测是工业上无损检测的方法之一,超声检测管体遇到缺陷时,一部分声波会产生反射,检测仪器可对反射波进行分析,就能精准无误地测出缺陷来,并且能够显示出内部缺陷的位置与大小,测定材料的厚度等。超声检测应用在脉冲反射探伤法中,通常用于锻件、焊缝等的检测,可发现工件内部较小的裂纹、夹杂、缩孔、未焊透等缺陷。优点是穿透力大,探伤灵敏度高,并可测定缺陷的深度和相对大小等。缺点在于不能检查复杂的工件,被检查的表面具有一定的光洁度和要求具有一定经验的检验人员来进行检测等。
毕业设计开题报告
毕业设计题目
圆桶焊缝超声检测机械装置
设计类型
理论研究
应用研究
调查研究
用于生产
其它
√
一、完成本题的目的和意义:
本课题主要研究设计一种适用于管体超声检测机械装置,以实现工件从工作台取出并放置到指定工位的功能,将送料过来的工件进行夹紧的功能,调整组件以及完成探头测量的功能。
焊接药筒环焊缝缺陷超声自动检测系统设计

焊接药筒环焊缝缺陷超声自动检测系统设计结合多年科研工作,提出了焊接药筒环焊缝超声自动检测方法和系统设计方案,并设计了多输入-单输出电路,特征提取电路。
1 焊接药筒环焊缝超声检测方法1.1 焊接药筒介绍焊接钢质药筒是国营753厂研制定型的火炮药筒。
其筒底和筒体是由环焊机焊接而成的。
在焊接处,筒底厚度为2.6 mm,筒体厚度1.6 mm,焊接后形成4~6 mm宽的环形焊缝,且内表面有起伏,不规则。
在炮弹发射时,药筒内压力很大,焊缝中的疵病可能导致严重的后果。
军方要求对焊缝百分之百的检验。
焊缝中主要会出现气孔、横裂纹、焊偏等缺陷。
为了适应生产线批量生产自动检测的要求,结合成本等因素,采用水浸超声自动检测方法。
1.2 环焊缝超声正交扫描检测方案疵病有点状和线状两种。
通过对药筒及环焊缝的具体分析,采取如图1所示方案,从两个方向对焊缝进行正交检测,这样不易漏检,也可根据两个方向获得的信息对缺陷进行定性分析。
图1中三个探头装在一个探头架上,全部采用水浸聚焦探头。
整个探头和药筒被测部分浸在水中(图中未画出水)。
图1(a)中,探头1是发射探头,发射的纵波在水中传播斜入射到药筒筒体,在钢板中产生A1模式的板波。
板波沿垂直于焊缝的方向传播,在传播的同时部分能量以纵波的形式向水中辐射,穿过焊缝的板波到达某一点时,其辐射的纵波能量被探头2接收。
当板波声束穿过的焊缝处有气孔或焊偏缺陷时,探头2接收到的信号变小。
图1(b)中,探头3发射的纵波斜入射到焊缝上,在焊缝中产生表面波,沿焊缝方向传播,当在焊道上距入射点一定距离内有横裂纹、气孔等缺陷时,表面波沿焊缝方向反射,反射回波的部分能量以纵波的形式向水中辐射,被探头3接收形成缺陷反射回波信号(无疵病时,信号幅度为零)。
通过对两组探头信号的处理与综合分析,可得出焊道上被测点的焊接情况。
这就是检测的基本原理和方法。
图1 环焊缝超声正交检测示意图2 自动检测系统总体设计根据检测方案,检测系统应具有以下功能:①两组探头对同一点先后检测,并把各自的回波信号进行处理;②提取回波信号的主要特征以便分析判断;③为了获得整个焊道的信息,药筒和探头必须有相对运动,使系统对整个圆周的焊缝都能检测到;④整个系统由微机进行控制和数据处理。
汽车后桥环焊缝自动超声波探伤系统
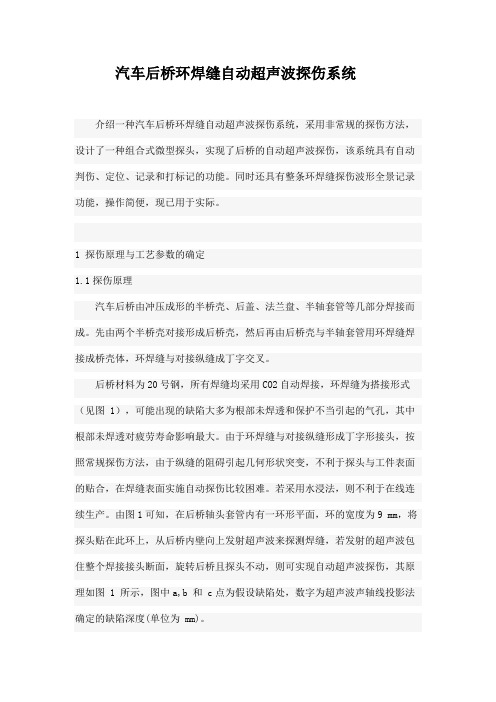
汽车后桥环焊缝自动超声波探伤系统介绍一种汽车后桥环焊缝自动超声波探伤系统,采用非常规的探伤方法,设计了一种组合式微型探头,实现了后桥的自动超声波探伤,该系统具有自动判伤、定位、记录和打标记的功能。
同时还具有整条环焊缝探伤波形全景记录功能,操作简便,现已用于实际。
1 探伤原理与工艺参数的确定1.1探伤原理汽车后桥由冲压成形的半桥壳、后盖、法兰盘、半轴套管等几部分焊接而成。
先由两个半桥壳对接形成后桥壳,然后再由后桥壳与半轴套管用环焊缝焊接成桥壳体,环焊缝与对接纵缝成丁字交叉。
后桥材料为20号钢,所有焊缝均采用CO2自动焊接,环焊缝为搭接形式(见图 1),可能出现的缺陷大多为根部未焊透和保护不当引起的气孔,其中根部未焊透对疲劳寿命影响最大。
由于环焊缝与对接纵缝形成丁字形接头,按照常规探伤方法,由于纵缝的阻碍引起几何形状突变,不利于探头与工件表面的贴合,在焊缝表面实施自动探伤比较困难。
若采用水浸法,则不利于在线连续生产。
由图1可知,在后桥轴头套管内有一环形平面,环的宽度为9 mm,将探头贴在此环上,从后桥内壁向上发射超声波来探测焊缝,若发射的超声波包住整个焊接接头断面,旋转后桥且探头不动,则可实现自动超声波探伤,其原理如图 1 所示,图中a,b 和c点为假设缺陷处,数字为超声波声轴线投影法确定的缺陷深度(单位为 mm)。
图 1探伤原理及缺陷回波定位法示意图1.2探头参数的选择1.2.1K值由于后桥环缝位置的几何形状和尺寸的限制,满足自动探伤要求的位置狭小,为了保证探伤的可靠性,采用多探头多方位扫查方式。
探头设计成组合探头形式,后桥头每边采用4只探头,两边共8只探头同时检测,每个组合探头中的探头以圆心为对称点,相隔90°均布。
探头扫查方向如图 2 所示,1号探头向斜下方扫查焊缝,另外3只探头从斜上方扫查环焊缝。
两端的组合探头呈对称布置。
斜探头入射角β由后桥环缝位置的几何尺寸确定,其原则是超声波束要包络整个焊缝断面,如图1所示。
管道环焊缝相控超声检测系统设计

摘要:在管道环焊缝过程中,其超声检测技术是一项非常重要的技术。随着我国工业产业规模的不断扩大,长输管道的使用服务功能正在逐渐完善,为相关行业生产效率的提高带来了重要的保障作用。结合现阶段长输管道监督检查的实际发展状况,可知其中依然存在着一定的问题,影响了长输管道的焊接质量,需要采取必要的措施及时地处理这些问题,避免长输管道使用中出现焊缝缺陷现象。基于此,本文将对长输管道焊缝无损检测监督要点进行必要地探讨,本文针对超声检测的相关技术和设计进行了分析。
关键词:管道环焊缝;超声检测;系统设计
1前言
全自动超声波检测技术(AUT)是一项在超声波检测技术(UT)的基础上研发的焊缝质量无损检测技术,具有检测灵敏度高、速度快、对焊缝缺欠定位和定量准确等优点,在工业管道的焊缝质量检测中得到了应用和推广,提高了检测质量和工效,降低检测作业强度。
2检测工艺原理
根据超声波相控阵声聚焦和焊缝分区扫查原理进行管道焊缝的检测设置,检测前测量管道的超声波声速、对管道表面进行处理、画检测参考线和标识,通过校准试块校验系统稳定性和校准检测灵敏度,在管道焊缝的2-3点位安装扫查器道接头,在管道焊缝的正上方安装扫查器,进行管道表面耦合,通过焊缝分区扫查形成AUT扫查图,再根据A扫描、B扫描和TOFD扫描图谱综合评价焊缝质量。
4.2 AUT可靠性研究及成果试用
4.2.1 AUT可靠性研究
国内无损检测技术可靠性研究在理论和实际应用方面仍处于起步阶段,尚未形成具有自主知识产权的无损检测可靠性技术体系,缺少相应的认证和评定程序。要推行管道全自动焊技术,应该针对管道自动焊的AUT技术可靠性开展研究工作,建立质量体系并制定程序文件。通过对陆地长输管道AUT技术可靠性、工艺评定及其质量体系建立的研究获得以下成果:(1)AUT的缺欠检出率高于RT。试验设计人工缺点263处,AUT检出255处,缺欠检出率为96.96%;RT检出187处,缺欠检出率为71.1%。(2)AUT的检测灵敏度略高于RT。AUT发现的最小缺欠(高度)尺寸小于RT发现的最小缺欠,RT对热焊和根部的未熔合类型(或高度小于0.5mm)缺欠检出率较低。(3)AUT能够对缺欠深度进行较为精确的定位,RT则不能,只能依靠经验判断,误判的可能性较大。(4)AUT(A扫描通道)对气孔(条孔、密集气孔)不敏感,检出率低,但通过体积通道和TOFD通道的补充检测,也可以检测到气孔等体积型缺欠。综合可靠性指标、切片对比结果,针对陆地长输管道全自动焊焊缝,AUT检测结果的检出率和可靠性要远高于RT。AUT技术对于全自动焊焊口,不存在缺欠漏检,可检出的最小缺欠尺寸也小于RT,且AUT比RT多了一个缺欠高度的验收指标,在质量保证方面更加全面、科学。因此,AUT能够代替RT对陆地长输管道全自动焊焊缝进行检测。
齿轮缺陷超声自动检测系统的设计
由数据采集子系统、 机械扫描及控制子系统、 超声检 测信号处理及自动判读子系统、 检测操作子系统和系 统校准试件等五部分组成。
图 ; 超声检测系统结构框图
< 系统的结构设计
该齿轮超声自动检测系统的结构见图 !。系统
收稿日期: &’’+ 年 % 月
(!) 数据采集子系统 数据采集子系统用于实现对齿轮缺陷检测的数 据采集, 它主要由超声波探伤仪、 探测器、 单片机触发 卡、 9 N O 数据采集卡和工业控制机组成。 超声波探伤仪激励探测器发射超声波, 并将从被 检工件反射或透射的超声波经探测器接收后转换为
采用线聚集探头, 探头 . 采用焦柱比较长的线聚集 (或点聚集) 探头 (见图 3) 。
图 $ 探头示意图
采用超声脉冲液浸回波法, 沿多个方向分别对齿 (齿顶面、 内孔面和齿侧面) 进行扫 轮的 3 个轮廓面 描, 检测齿轮内部存在的缺陷 (见图 <) 。
图 ! 轮齿齿顶面检测示意图
采用 947=4> 软件的处理工具, 对中小模数斜齿 轮内部不同类型、 不同形状及大小的缺陷检测实验结 果进行分析, 结果表明: 齿轮超声自动检测系统的缺 陷检测分辨率可达到 /?0@@。
#*
工具技术
齿轮缺陷超声自动检测系统的设计
姜 辉!
!
张吉堂!
&
顾立强&
中北大学
哈尔滨工业大学摘源自要: 针对齿轮制造过程中可能出现的各种内部缺陷, 设计了一种基于单片机、 工业控制机和数控机床的齿轮
超声自动检测系统, 重点介绍了系统的结构特点、 工作原理及软件设计。 关键词: 齿轮, 缺陷检测, 超声波
$)); 年第 4+ 卷 <+
齿轮综合误差测量器设计和实现论文设计
目录摘要 (Ⅰ)Abstract.............................................................................................................. I I 1 绪论 (1)1.1 齿轮测量技术的发展 (1)1.2 齿轮双面啮合综合测量仪前景分析 (1)1.3 课题主要工作任务 (1)1.4 课题预期目标 (1)1.5 小结 (2)2 齿轮综合误差试验机总体方案 (2)2.1 总体方案设计 (2)2.2 方案确定 (3)2.3 工作原理 (4)2.4 齿轮双面啮合综合测量仪的使用 (4)3 动力驱动部分设计 (4)3.1 步进电动机的介绍 (4)3.2 步进电动机的分类及特点 (4)3.3 步进电动机的三要素 (5)4 机械结构部分设计计算 (7)4.1 轴的设计 (7)4.2 丝杠螺母副的计算 (9)4.3 滚动轴承的选用和计算 (14)4.4 联轴器的选用和计算 (14)4.5 螺纹联接的选用计算 (16)4.6 键的选用 (17)4.7 销的选用 (19)4.8 导轨的设计 (20)5 传感测试及控制电路部分设计 (21)5.1 传感器的定义及分类 (21)5.2 电感式位移传感器 (22)5.3 光电编码器 (22)5.4 控制系统 (22)6 圆柱齿轮参数 (22)6.1 标准齿轮参数 (23)6.2 被测齿轮参数 (23)结论 (25)致谢 (26)参考文献 (27)摘要齿轮是轮式机械部件,其通过齿的啮合传递扭矩。
齿轮由其余齿形机械部件(如另一个齿蜗,齿条,杆轮)驱动,改动目的并改变运动形式。
因为齿轮的普遍应用在我们生活中,不同情况差别很大,不同的形态和更多的几何参数,这将直接引出制作和装置中的某些谬误,这将影响使用质量。
对于符合齿轮的各种数据,必需测试各种数据。
齿轮的误差对于齿轮的整体精度有重要的影响,也是整个齿轮箱检测的重要一环。
毕业设计(论文)-超声波定位系统设计
提供全套毕业论文图纸,欢迎咨询论文题目超声波定位系统设计系别工程学院专业机械自动化年级2010级学号学生姓名指导教师完成时间2014 年 5 月XX学院教务处制XX学院本科生毕业设计(论文)声明本人郑重声明:所呈交的本科毕业设计(论文)是本人在XX学院学习期间,在指导教师指导下独立完成,内容真实可靠,无抄袭、剽窃等学术道德不端行为,除文中已经注明引用的内容外,本文不包含任何其他个人或集体已经发表或撰写过的作品成果。
对本文的研究做出重要贡献的个人和集体,均已在文中以明确方式标明。
同时,本人完全了解并愿意遵守XX学院有关保存、使用毕业论文(设计)的规定,其中包括:1.学院有权保管并向有关部门递交毕业设计(论文)的原件、复印件和电子文件。
2.学院可以采用影印、缩印、电子文件或其他复制方式保存毕业设计(论文)。
3.学院可以以学术交流为目的,赠送和交换毕业设计(论文)。
4.学院可以允许毕业设计(论文)被查阅或借阅。
5.学院可以按著作权法的规定公布毕业设计(论文)的部分内容或全部内容[保密毕业设计(论文)在解密后遵守此规定]。
6.除另有科研合同或其他法律文书制约,本文的科研成果属于XX学院。
本声明的法律结果将完全由本人承担。
作者签名:日期:年月日超声波定位系统设计作者:XXX中文摘要我们根据超声波的特性来研发制成超声波传感器,机械振动频率比声波高的波,我们称之为超声波。
超声波的频率比较高,其次波长短和绕射现象不明显,而且具有方向性好,能量消耗缓慢,能长距离传播等优点。
当今社会,在传感器以及自动控制测距离的方案中,超声波测距是被最广泛应用的一个方案,它被使用于以下的实际操作中,例如,水位的测量,建筑工地测距这些场合。
本论文讨论了超声波的定位系统以及相应的算法,还比较全面地描述了超声波传感器的原理以及特性。
基于超声波测距原理的分析,提出了超声波测距系统的设计过程和需要注意的问题。
以STC12C5A60S2单片机为核心,我们设计好的超声波测距仪以及硬件电路有很多优势,它的精度高、低成本以及数字显示的使用微型。
焊缝超声自动检查设备
1.LSI - 大型结构机器人自动爬行超声C扫描探伤系统——美国物理声学公司LSI为一套由便携式笔记本电脑或手动遥控器控制的机器人自动爬行超声C-扫描探伤系统。
该系统可爬行于压力容器、锅炉、储罐、管道与船体等大型结构之上进行超声测厚、腐蚀、探伤及焊缝检测等作业,实现百分之百覆盖的自动超声A/B/C扫描并自动给出满足API653标准的扫查报告。
该系统既可现场检测大型结构的壁厚、腐蚀与缺陷的状况,又可配以使用TOFD装置对大型结构的焊缝进行现场检测。
所有检测结果均可存入硬盘永久保留,并可对多处分别检测的结果进行整合以提供大型结构整体的检测报告。
LSI主要下列部件组成:由防水电机(满足IP-65标准)驱动的机器人爬行器(可爬高至数十米)及超声扫查架(250-600mm宽)。
由高性能、高质量的超声脉冲发射/接收卡(30MHZ带宽,12位精度)及运动控制卡构成的超声控制系统手动遥控装置室内、外用加固型笔记本电脑及集扫描、探伤、分析成像、评估于一体的窗式软件ULTRAWIN。
远距离辅助视频成像系统。
图1 LSI - 大型结构机器人自动爬行超声C-扫描探伤系统图2 图3网址:/ut-lsi.htm2. 自动超声相控阵管道环焊缝检测系统(奥林巴斯)图4 自动超声相控阵管道环焊缝检测系统近年来,自动超声检测(AUT)技术已开始取代了传统的射线成像术,成为世界上首选的管线焊缝检测方法。
射线成像技术具有明显的局限性:面缺陷检测的效果不好、无垂直定量缺陷的性能、具有安全方面及环境污染方面的隐患。
自动超声检测的优势:•无辐射危害、无化学污染、无需得到许可。
•检测周期极短,提高了生产率。
•检测及定量精确性更高,降低了次品率。
•使用工程临界评估(ECA)验收标准对缺陷指示的垂直高度和深度进行测量,降低了次品率。
•通过智能输出显示进行实时分析。
•提供与电子支持相关的数据和检测报告。
•更好地控制焊接过程,降低了次品率。
PipeWIZARD设备计算机与软件坚固耐用的笔记本电脑内装有Microsoft Windows和PipeWIZARD数据采集和分析软件。