大型齿轮磨削装备的关键技术
高速超高速磨削技术发展与关键技术

* 国家自然科学基金资助项目(编号:50475052) 教育部科学技术研究重点项目(编号:104190)高校博士学科点专项科研基金资助项目(编号:20040145001)高速超高速磨削技术发展与关键技术*青岛理工大学 机械工程学院 ( 266033) 李长河东北大学 机械工程与自动化学院 (110004) 修世超 蔡光起摘 要 论述了高速超高速磨削加工技术的发展、特点以及关键技术。
关键词 高速超高速 磨粒加工 关键技术1 高速/超高速磨削技术发展超高速磨削技术是现代新材料技术、制造技术、控制技术、测试技术和实验技术的高度集成,是优质与高效的完美结合,是磨削加工工艺的革命性变革。
德国著名磨削专家T.Tawakoli 博士将超高速磨削誉为“现代磨削技术的最高峰”。
日本先端技术研究学会把超高速加工列为五大现代制造技术之一。
在1996年国际生产工程学会(CIRP )年会上超高速磨削技术被正式确定为面向21世纪的中心研究方向之一,是当今在磨削领域最为引人注目的技术。
高速加工(High-speed Machining)和超高速加工(Ultra-High Speed Machining )的概念是由德国切削物理学家Carl.J.Salomon 博士于1931年首先提出,他发表了著名的Salomon 曲线,创造性地预言了超越Talor 切削方程式的非切削工作区域的存在,提出如能够大幅度提高切削速度,就可以越过切削过程产生的高温死谷而使刀具在超高速区进行高速切削,从而大幅度减少切削工时,成倍地提高机床生产率。
他的预言对后来的高速甚至超高速磨削的发展指明了方向,为高速超高速磨削技术研究开辟了广阔的空间,对于高速超高速磨削技术的实用化也起到了直接的推动作用。
通常将砂轮线速度大于45 m/s 的磨削称为高速磨削,而将砂轮线速度大于150 m/s 的磨削称为超高速磨削。
超高速磨削在欧洲、日本和美国等发达国家发展较快。
欧洲高速超高速磨削技术的发展起步比较早, 最初在20世纪60年代末期就开始进行高速超高速 磨削的基础研究,当时实验室的磨削速度就已经达到210~230 m/s 。
大模数粉末冶金齿轮磨齿工艺

1序言粉末冶金是制取金属粉末或用金属粉末(或金属粉末与非金属粉末的混合物)作为原料,经过成形和烧结,制造金属材料、复合材料以及各种类型制品的工艺技术。
粉末冶金材料是用粉末冶金工艺制得的多孔、半致密或全致密材料(包括制品)。
随着对新材料应用的不断探究,航空发动机齿轮类零件越来越多地采用粉末冶金材料。
但是,由于粉末冶金材料特殊的成形方法及材料本身所具有的特殊性能,因此使得在磨齿时会出现尺寸不稳定、烧伤等现象。
高精度齿轮精度要求在国标4~5级时,只能用磨齿、玷齿的方法来保证其加工精度。
大模数齿轮(模数m≥5)磨齿时,齿根转接处和根径烧伤十分严重。
2零件及材料性能分析图1所示齿轮零件加工要求:模数=6、齿数=11、压力角=28。
、齿圈径向圆跳动公差二0.028mm、公法线长度变动量公差=0.02mm、齿距极限偏差=±0.011mm、齿形总偏差=0.01mm、齿向偏差=0.0Imm以及单个齿距偏差二0.008mm,达到了5级精度,属于高精度大模数齿轮,在加工中必须依靠磨齿来保证最终精度。
图1齿轮零件示意该零件模数虽较大,但只有11个齿,属于根切齿轮。
零件的变位系数为O,没有变位,这就意味着在零件的齿根转接处会形成很大的转接半径R及内凹,在成形磨齿加工中,齿根转接处的散热性较差,容易产生烧伤。
另外,在磨齿过程中由于模数较大,因而砂轮与齿面的接触面积也较大,散热受阻,严重影响了齿轮加工精度。
零件材料为AHPIOV粉末冶金高钢工具钢材料中碳化物多,在渗氮处理后,其硬度高达65~70HRC材料耐磨性高,其多孔性及高硬度直接影响了磨齿精度。
3磨齿时齿根转接处烧伤分析经多次实际加工发现,此种大模数少齿数粉末冶金齿轮磨齿时,烧伤大多发生在齿根转接处,分析其原因,主要有以下几个方面。
1)粉末冶金材料本身具有难磨削性,渗氮处理后,其硬度高达65~70HRC,高硬度使得材料磨削困难。
2)由于模数大、齿数少以及没有变位,因而齿轮本身就会有严重的根切,在齿根转接处会产生内凹,这样一来,磨齿时就会在转接处积累大量的磨削热,导致散热性不好。
磨机大齿轮的加工工艺

(11)钳 :按 已 经 钻 好 孔 的 一 件 半 齿 轮 号 划 另 一 件 半 齿 轮结合面上 4 个锥销孔的加工线;
(12)镗 :a. 方 箱 上 活 ,在 另 一 件 半 齿 轮 两 端 结 合 面 上 分别用百分表在水平和垂直方箱找正,扩镗一件半齿轮 结合面上把合孔及锥销孔均按小于孔径 1mm 镗出并背面 锪平;b. 精 铣 半 齿 轮 的 结 合 面 ,铣 平 为 止(检 查 变 形 量 ,如 超过 1mm,经技术员同意后再精铣,铣平为止)。
参考文献
[1] 王选逵主编.ISBN:机械制造工艺学 .机械工业出版社出版 . [2] 孟少农主编.机械加工工艺手册.机械工业出版社出版. [3] 江旭昌主编.管磨机大齿轮.中国建材工业出版社.
Pr ocessing Technic of Mill Gear wheel GAO Jin,CHEN Qiaoyun (Jinan Heavy Machinery Joint- Stock Co., LTD, jinan, 250109) Abstract :This article introduced the main processing technic of mill gearwheel and the application of this processing technic in practical production. It played a key role in guiding the actual production and controlling the quality of products. Keyword :gearwheel, processing technic, three turning and two hobbing
大型齿轮磨削装备的关键技术

大型齿轮磨削装备的关键技术
郭召
【期刊名称】《工具技术》
【年(卷),期】2016(50)7
【摘要】目前,我国正在大力发展海洋资源勘探装备、大型舰艇、风电、核电、高速机车、航空航天、军工、大型工程机械等新兴产业。
这些行业要求齿轮传动在高速、重载、冲击多变及恶劣工况下具有高可靠性、长寿命、高传动效率和低噪音的工作性能。
大型、高精度硬齿面齿轮是重型机械传动行业中关键的动力传动元件,这些行业的快速发展造成对大型齿轮磨削装备的需求扩大。
【总页数】2页(P80-81)
【关键词】大型齿轮;齿轮传动;硬齿面齿轮;磨齿机;恶劣工况;精密磨削;传动元件;大型工程机械;传动效率;齿面
【作者】郭召
【作者单位】秦川机床工具集团股份公司
【正文语种】中文
【中图分类】TG616
【相关文献】
1.大型齿轮加工新技术提升大型齿轮加工装备水平,加速推进中国由齿轮大国走向齿轮强国访中国齿轮行业专家、北京工业大学教授石照耀 [J], 杜春玲;索菲娅
2.大型行星齿轮磨削烧伤分析及预防措施 [J], 翟阳;谭小明;陈亮;石磊
3.大型齿轮磨削余量快速识别方法研究 [J], 郭召
4.大型渗碳人字齿轮磨削烧伤控制技术 [J], 黄啸;张阳;王作鹏
5.泵齿轮端面砂带磨削及倒棱关键技术研究 [J], Yin Jiachao;Huang Yun;Zou Lai 因版权原因,仅展示原文概要,查看原文内容请购买。
重庆大学科技成果——复杂修形齿轮精密数控加工关键技术与装备

重庆大学科技成果——复杂修形齿轮精密数控加工关键技术与装备(2018年国家科技进步二等奖)成果简介:复杂修形齿轮是克服高速重载工况下力热耦合形变影响的高端齿轮,直接决定装备传动系统的振动、噪声、寿命等服役性能及其核心竞争力,广泛应用于航母、潜艇、汽车等。
针对复杂修形齿面精密制造面临全齿面修形加工存在原理误差、传统试错修调法提升加工精度困难、齿面淬硬层均匀性及纹理难以调控等问题,在国家科技重大专项、863计划等支持下,开展复杂修形齿轮精密数控加工关键技术与装备研究,成果获2018年国家科技进步二等奖。
主要取得突破和创新如下:1、提出复杂修形齿轮加工的点矢量族包络计算新理论,不用建立和求解啮合方程,以数字法替代解析法,突破啮合原理解析法无法求解奇异点、计算复杂的瓶颈;发明齿面扭曲消减方法,解决刀具廓形精确设计及原理误差消减难题,齿面扭曲减少70%以上,达国际领先。
2、发明复杂修形齿轮加工工艺系统误差调控技术,开辟齿轮修形精度提升新途径。
提出制齿机床热态精度提升技术,发明热致误差补偿方法,保证机床精度稳定;提出基于等效虚拟轴的齿面误差补偿方法,解决修形精度提升难题,提高传动精度1-2级,获中国专利优秀奖。
3、研制大规格精密数控滚齿机、精密多功能数控磨齿机、高速干切滚齿机等具有齿面扭曲消减及加工误差补偿的高端制齿机床,填补国内空白;开发集齿轮修形设计、工艺规划于一体的制齿软件,打破了国外高端机床垄断。
滚齿精度达5-6级,磨齿达3级,干切滚齿提高效率2-3倍,与同类国际先进水平相当,打破高端制齿机床垄断,迫使国外同类机床降价30%以上,并出口英、法、日等。
4、发明复杂修形齿轮滚磨一体化工艺技术,确保修形精度及表面一致性。
研制复杂修形齿轮刀具,实现齿轮刀具的数字化设计制造;研发滚磨余量协同分配、齿面柔性修形、磨削纹理优化等工艺,实现磨后齿面淬硬层均匀分布、齿面纹理可控、修形工艺快速固化,提高齿面疲劳寿命。
满足了军方供货要求,支撑我国主要舰艇齿轮加工,汽车变速箱的批量国产化提供了保障。
大型齿轮加工机床回转工作台关键技术

大型齿轮加工机床回转工作台关键技术目前,我国正在大力发展海洋资源勘探装备、大型舰艇、风电、核电、高速机车、航空航天、军工和大型工程机械等新兴产业。
这些行业的快速发展对大型精密齿轮加工机床提出了迫切的市场需求。
图1所示为一款大型齿轮传动装置,大型齿轮位于动力传动关键环节,其加工需要大型数控齿轮加工机床。
而数控转台作为大型精密数控齿轮加工机床核心功能部件,起到承载工件、分度及传递精度的作用,要求转速范围宽、响应速度快、承载大及刚性高。
工作台参与联动加工,要求定位精度及重复定位精度高、响应快且运行平稳,其性能直接影响整机性能。
数控转台的研制是开发大型齿轮加工机床的关键。
图1 大型齿轮传动装置1.转台驱动技术大型齿轮加工机床回转工作台主要功能是承载工件并带动工件实现与刀具的相对运动。
根据加工方式的不同,转台的运动不同。
例如大型内齿轮铣齿机利用成形铣刀加工大型内齿,转台主要用于承载工件及分度。
大型数控滚齿机则要求转台与刀具在电子齿轮箱的匹配下构成内联系传动链,实现连续运转。
大型数控成形磨齿机则要求转台在加工斜齿轮时能够跟随砂轮在一定角度范围内往复运动。
通过对大型齿轮加工工艺分析,大型齿轮加工机床转台需要实现任意角度分度,为避免传动链加工误差对工件精度的影响,需要对转台进行全闭环控制。
大型齿轮自身质量大、惯量高,加工过程中需要的驱动转矩大,转台的驱动需要兼顾动力传递及精度传递。
(1)蜗轮蜗杆传动,蜗杆齿廓为连续螺旋面,啮合过程连续平稳、重合度高、冲击小及噪声低,是一种广泛应用的精密传动机构。
回转工作台要进行正向和反向的传动和定位,传动系统元件之间的间隙影响其精度,对转台的定位精度、双向重复定位精度、响应时间和运行平稳性等性能指标造成影响。
当采用机械传动链时,采用各种不同的结构,消除传动链间隙非常关键。
采用蜗轮蜗杆传动关键是合理的消隙技术。
为防止制造误差,尤其是齿距误差或者使用过程中的磨损造成过大的间隙,影响运动及精度的准确传递,因此分度蜗杆传动副的传动啮合间隙应尽可能调整到允许的最小值,且能够在使用过程中进行调整补偿。
齿轮磨削工艺技术
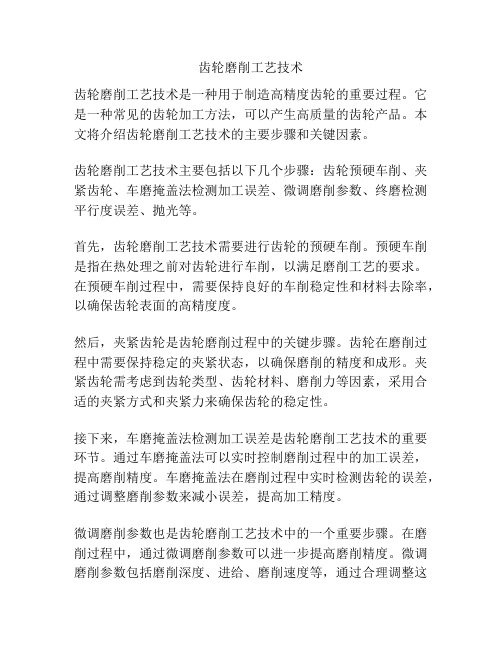
齿轮磨削工艺技术齿轮磨削工艺技术是一种用于制造高精度齿轮的重要过程。
它是一种常见的齿轮加工方法,可以产生高质量的齿轮产品。
本文将介绍齿轮磨削工艺技术的主要步骤和关键因素。
齿轮磨削工艺技术主要包括以下几个步骤:齿轮预硬车削、夹紧齿轮、车磨掩盖法检测加工误差、微调磨削参数、终磨检测平行度误差、抛光等。
首先,齿轮磨削工艺技术需要进行齿轮的预硬车削。
预硬车削是指在热处理之前对齿轮进行车削,以满足磨削工艺的要求。
在预硬车削过程中,需要保持良好的车削稳定性和材料去除率,以确保齿轮表面的高精度度。
然后,夹紧齿轮是齿轮磨削过程中的关键步骤。
齿轮在磨削过程中需要保持稳定的夹紧状态,以确保磨削的精度和成形。
夹紧齿轮需考虑到齿轮类型、齿轮材料、磨削力等因素,采用合适的夹紧方式和夹紧力来确保齿轮的稳定性。
接下来,车磨掩盖法检测加工误差是齿轮磨削工艺技术的重要环节。
通过车磨掩盖法可以实时控制磨削过程中的加工误差,提高磨削精度。
车磨掩盖法在磨削过程中实时检测齿轮的误差,通过调整磨削参数来减小误差,提高加工精度。
微调磨削参数也是齿轮磨削工艺技术中的一个重要步骤。
在磨削过程中,通过微调磨削参数可以进一步提高磨削精度。
微调磨削参数包括磨削深度、进给、磨削速度等,通过合理调整这些参数可以减小磨削误差,提高加工精度。
终磨检测平行度误差也是齿轮磨削工艺技术中的一个关键环节。
通过终磨检测可以准确测量齿轮的平行度误差,进一步改善加工精度。
终磨检测平行度误差需要使用高精度的测量仪器和设备,以确保测量结果的准确性。
最后,齿轮磨削工艺技术还需要进行抛光等后续处理。
抛光可以进一步提高精度和光洁度,使得齿轮的表面更加光滑和平整。
总的来说,齿轮磨削工艺技术是一种制造高精度齿轮的重要方法。
通过预硬车削、夹紧齿轮、车磨掩盖法检测加工误差、微调磨削参数、终磨检测平行度误差和抛光等步骤,可以获得高质量的齿轮产品。
这些步骤中的关键因素包括材料选用、磨削参数调整、夹紧方式等,需要进行合理的选择和调整,以实现高精度度的齿轮磨削。
齿轮磨削加工工艺
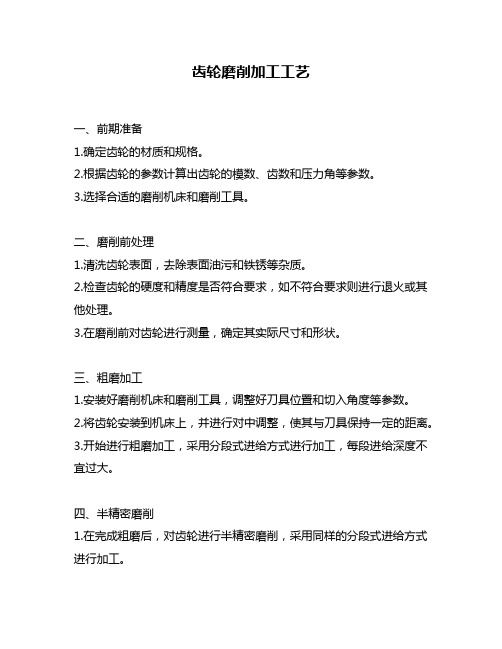
齿轮磨削加工工艺
一、前期准备
1.确定齿轮的材质和规格。
2.根据齿轮的参数计算出齿轮的模数、齿数和压力角等参数。
3.选择合适的磨削机床和磨削工具。
二、磨削前处理
1.清洗齿轮表面,去除表面油污和铁锈等杂质。
2.检查齿轮的硬度和精度是否符合要求,如不符合要求则进行退火或其他处理。
3.在磨削前对齿轮进行测量,确定其实际尺寸和形状。
三、粗磨加工
1.安装好磨削机床和磨削工具,调整好刀具位置和切入角度等参数。
2.将齿轮安装到机床上,并进行对中调整,使其与刀具保持一定的距离。
3.开始进行粗磨加工,采用分段式进给方式进行加工,每段进给深度不宜过大。
四、半精密磨削
1.在完成粗磨后,对齿轮进行半精密磨削,采用同样的分段式进给方式进行加工。
2.为了保证加工质量,需要对磨削机床和磨削工具进行定期检查和维护。
3.在半精密磨削过程中,需要注意控制切削速度、进给速度和切削深度等参数,以确保加工精度。
五、精密磨削
1.在完成半精密磨削后,进行最后的精密磨削。
此时需要采用更加细致的进给方式和切入角度等参数。
2.为了保证加工质量,需要对磨削机床和磨削工具进行更加细致的检查和维护。
3.在精密磨削过程中,需要采用更加严格的控制方法来控制切割参数,以确保齿轮的最终形态、尺寸和表面质量。
六、后处理
1.完成齿轮的精密磨削后,需要对其表面进行清洗,并去除可能存在的毛刺和其他杂质。
2.对齿轮进行测量,并与原始设计要求进行比较,以确保其符合要求。
3.最后将齿轮包装好,并妥善保存。
- 1、下载文档前请自行甄别文档内容的完整性,平台不提供额外的编辑、内容补充、找答案等附加服务。
- 2、"仅部分预览"的文档,不可在线预览部分如存在完整性等问题,可反馈申请退款(可完整预览的文档不适用该条件!)。
- 3、如文档侵犯您的权益,请联系客服反馈,我们会尽快为您处理(人工客服工作时间:9:00-18:30)。
基金项目:国家科技重大专项(2014ZX04001-191);秦川机床工具集团股份公司科研项目(科研工作令2014G-科研-035号)收稿日期:2016年1月
大型齿轮磨削装备的关键技术
郭召
秦川机床工具集团股份公司
引言
目前,我国正在大力发展海洋资源勘探装备、大型舰艇、风电、核电、高速机车、航空航天、军工、大型工程机械等新兴产业。
这些行业要求齿轮传动在高速、重载、冲击多变及恶劣工况下具有高可靠性、长寿命、高传动效率和低噪音的工作性能。
大型、高精度硬齿面齿轮是重型机械传动行业中关键的动力传动元件,这些行业的快速发展造成对大型齿轮磨削装备的需求扩大。
大型磨齿装备概况
传统的大型齿轮精密磨削加工多采用锥面砂轮磨齿机展成磨削,砂轮和工件齿面为点接触,工件分度运动采用蜗轮副单齿分度,加工效率低,上世纪90年代逐渐被淘汰。
德国KAPP公司在20世纪80年代初,开发了应用CBN砂轮的成形磨齿机,由于CBN砂轮万能性差,制造价格昂贵,没有得到普及推广。
到2
0世纪90年代末期,随着计算机技术及数控技术发展成熟,德国NILES及Pfauter、意大利Sampustensili等多家公司相继推出应用可修整普通砂轮的数控成形砂轮磨齿机。
机床操作界面实现人机对话,用户仅需输入磨削齿轮参数,即可完成成形砂轮截形计算及修整,实现工件自动循环磨削。
近年来,大型数控成形磨齿机发展呈现出以下特点:机床集成了在机测量、磨削自动对刀、磨削余量自动分配、磨削状态实时监测、砂轮在机动平衡等先进技术,机床加工精度达到GB/T10095.1-20083级精度,更符合大型、精密齿轮的加工需求。
主要的齿轮机床制造商均针对大型齿轮的加工提出各自的解决方案。
(1)德国KAPP-NILES
德国卡帕集团拥有ZE系列、ZP系列、ZPI系列、ZPB系列多款大型磨齿机,为用户提供大型齿轮加工方案。
齿轮最大加工直径8m,最大模数
40mm。
NILES磨齿机的特点是采用模块化设计,加工直径1
m齿轮的机床与加工直径8m齿轮的机床采用同一磨削功能模块,仅在机床转台和床身长度上有区分。
机床基础大件采用球墨铸铁浇铸,相比传统灰铸铁,大幅提升刚性。
(2)德国霍夫勒
霍夫勒公司是德国第二家大型磨齿机制造商,开发了R
APID系列、RAPID—MFM系列和RAPID—AI系列大型磨齿机,最大加工直径6m,最大模数50mm。
特点在于机床床身、立柱等基础大件采用矿物铸件制造,吸振性、热稳定性性能优越。
机床采用直线电机驱动,响应快,无磨损,精度保持性好。
机床回转轴采用力矩电机直接驱动,尤其是在机床磨削角控制轴率先采用了力矩电机直驱技术。
(3)美国Gleason-Pfauter
格里森公司以生产螺旋伞齿轮加工设备著称,和德国Pfauter公司联合后,充分吸收Pfauter公司在大型精密滚齿机方面的丰富经验,结合自身在齿轮磨削技术方面的积累,开发了P系列大型磨齿机。
双齿面无扭曲磨削工艺可减少50%的精加工时间,独特的新优化磨削(OPTIGRIND)技术可同时使用三个或更多的砂轮,以替代单片砂轮,效率、精度、表面质量兼顾。
(4)意大利桑普
意大利桑普坦斯利公司推出了HG系列大型磨齿机,将滚齿及磨齿进行复合。
在一台机床上,可以实现粗、精加工。
机床配备自动换刀装置,实现滚刀与砂轮的自动切换。
(5)中国秦川
国内大型磨齿装备研发起步较晚,秦川机床厂在2000年开始研制数控成形磨齿机,2004年推出第一款大型数控磨齿机YK73125,十多年来开发了YK7363、YK7380/A、YK73100、YK73125/A、YK73200、YK73400、YK75200系列大规格数控成形磨齿机,形成了系列化产品,产品销售100多台,解决了我国重型机械传动的关键动力元件加工问题,
提高了大型、高速、重载硬齿面齿轮磨削精度,实现了高速、重载、平稳、高寿命传动。
0
8工具技术
大型磨齿机关键技术
大型磨齿机属于集机、电、液、仪一体化的高端精密装备,面临重型机床高精度化难题,关键技术主要包括以下几方面:
(1)大型磨齿机高刚性设计技术
大型磨齿机伺服轴采用全闭环控制,影响精度的关键点是系统的稳定性,而机床刚性对系统稳定性至关重要。
大型磨齿机的设计需要对静刚度、动刚度、热刚度综合考虑,提高静刚度,保证机床在运动过程中具有相同的综合位移;提高动刚度,保证机床在加工状态下的高稳定性;提高热刚度,使机床的热变形均匀。
三者要兼顾考虑,实现在耦合状态下的机床高刚性设计。
(2)大型精密力矩电机回转工作台设计制造及控制技术
数控转台是大型磨齿机的关键功能部件,承载数十吨工件完成微米级控制,不但要精确定位,还要配合其他直线伺服轴完成插补运动,要求响应灵敏。
目前大型磨齿机转台普遍采用力矩电机直接驱动,力矩电机转台的设计制造、力矩电机的惯量匹配、力矩波动抑制等技术成为制约转台性能的关键技术。
(3)大型精密机床的静压导轨及静压轴承技术
大型磨齿机工件重达数十吨,移动部件重达十几吨,需要实现微米级控制,运动单元的支撑普遍采用静压技术。
静压供油方式、油膜刚度控制、油品清洁度控制及轴承温升控制等成为研究热点。
(4)砂轮主轴的大功率直接驱动、内置动平衡及AE技术
大模数、大齿深齿轮的磨削需要配置大功率磨削主轴,大功率磨削主轴的核心技术在于精确控制和发热抑制。
砂轮经修整后,其气孔、粘接剂及磨粒分布发生改变,造成主轴系统不平衡,影响磨削精度,需要配置机动平衡装置,及时自动检测不平衡量并自动补偿。
磨削过程中砂轮的磨损检测及防碰撞保护需要借助声发射(AE)技术实现。
(5)在机测量技术
大型齿轮起吊、安装、调整不便,采用在机测量技术可以对已磨削工件进行精度检测,根据误差调整磨削工艺,在一次装夹过程中即可磨削出合格工件。
在机测量成为机床认知加工对象的重要手段,是大型磨削装备实现智能磨削的关键因素。
(6)砂轮截形专用计算软件及砂轮修整装置及技术
大型磨齿机采用成形法磨削,取决于截形计算精度及砂轮修整精度。
通过算法优化不断提高计算精度,通过修整装置可实现精确的轮廓计算。
不同制造商研制了多种成形砂轮修整装置,应用最多的是两轴联动的直角坐标系修整装置。
在此基础上,砂轮的修整工艺成为关键。
结语
大型磨齿机未来的技术发展方向主要有:
(1)大型精密齿轮复合磨削技术
大型齿轮价格昂贵,需求量有限,但对精度的要求极高,采用复合加工是大型齿轮精密加工的发展趋势。
大型齿轮机床融合吸收各种先进技术,完善功能,提高自动化程度,向着齿轮磨削中心的方向发展,为用户提供一种大型齿轮全面加工的解决方案。
(2)成形磨削专家系统
提高机床对加工对象的自识别能力。
工件安装就位后,通过机床在机测量装置对齿轮形貌进行识别,分配余量,自动优化磨削工艺。
完成磨削后,精度自动检测,识别加工误差后,调整磨削工艺参数,进行纠正磨削。
(3)大型磨齿机电磁兼容性研究
大型磨齿机数控化程度高,采用了大功率磨削主轴和大扭矩力矩电机,配置了在机测量装置和动平衡装置以及大量的电气化功能部件及技术的应用,需要推进机床电磁兼容性研究,提高机床电气系统运行稳定性。
(4)齿廓精确修形及齿面纹路控制技术
大型重载齿轮及高速齿轮要求进行精确的齿廓修形才能稳定安全地工作,为了优化工作状态,减小振动噪音,设计出来的廓形越来越复杂,对齿面纹路和磨削装备都提出了更高的要求。
参考文献
[1]郭召,樊利军,谢斌.高速、精密、大型数控成形砂轮磨齿机研制[R].科技报告[71007221X-2009ZX04001091/01].2013,11.
[2]遇立基.磨齿工艺与磨齿机的技术发展概况[J].现代制造工程,2008(2):1-4.
[3]马云.从CIMT2005看磨齿机的发展趋势[J].世界制造技术与装备市场,2005(3):66-69.
[4]张四弟.磨齿技术与装备及其发展趋势[J].制造技术与机床,2011(5):46-48.
作者:郭召,工程师,秦川机床工具集团股份公司研究院,721009陕西省宝鸡市
1
8
2016年第50卷No.7。