齿轮磨削(完整资料).doc
15节的磨齿打法大全

15节的磨齿打法大全
【最新版】
目录
1.磨齿打法的概述
2.磨齿打法的种类
3.磨齿打法的技巧
4.磨齿打法的应用
5.总结
正文
【1.磨齿打法的概述】
磨齿打法,又称齿轮加工,是一种将齿轮的齿形通过磨削的方式加工出来的技术。
在机械制造业中,磨齿打法被广泛应用于各种齿轮的制造过程中,以保证齿轮的精度和耐用性。
【2.磨齿打法的种类】
磨齿打法主要分为以下几种:
(1)外圆磨齿:主要用于加工外齿轮,其原理是将外齿轮固定在磨床上,用砂轮进行磨削。
(2)内圆磨齿:主要用于加工内齿轮,其原理与外圆磨齿类似,只不过磨削的是齿轮的内部。
(3)圆锥磨齿:主要用于加工锥齿轮,其原理是将锥齿轮固定在磨床上,用圆锥形的砂轮进行磨削。
【3.磨齿打法的技巧】
(1)齿轮的安装:在磨削齿轮之前,需要将齿轮安装在磨床上,使其与砂轮的轴线平行。
(2)砂轮的选择:根据齿轮的材料和硬度,选择合适的砂轮,以保证磨削的效果和砂轮的耐用性。
(3)磨削的深度:磨削的深度应根据齿轮的齿高和齿厚来确定,以保证齿轮的精度。
(4)磨削的速度:磨削的速度应根据砂轮的硬度和齿轮的材料来确定,以保证磨削的效果和砂轮的耐用性。
【4.磨齿打法的应用】
磨齿打法在各种齿轮的制造中都有应用,如汽车、机床、船舶等机械设备的齿轮制造。
通过磨齿打法,可以提高齿轮的精度和耐用性,从而提高机械设备的运行效率和寿命。
【5.总结】
磨齿打法是齿轮加工的一种重要技术,其种类繁多,技巧丰富。
齿轮创成磨原理

齒輪創成磨原理
齿轮作为机械传动装置中重要的组成部分,其传动效率和精度直接影响到整个机械系统的性能。
而齿轮的制造过程中,磨削是一项非常重要的工艺,可以提高齿轮的表面质量和精度。
那么,齿轮磨削的原理是什么呢?
齿轮磨削的原理主要是利用磨料和加工表面之间的相对运动,将工件表面的毛刺、凸起等不平整部分去除,并在表面形成一定的几何形状和粗糙度。
具体来说,磨削过程中,磨料与工件表面之间的摩擦力和压力作用下,磨料颗粒逐渐磨损,磨料表面形成新的锋利刃口,从而不断切削工件表面,将其去除。
同时,磨削过程中,磨料与工件表面的接触面积较小,热量集中在很小的区域内,不会对工件产生较大的变形和热影响,保证了齿轮的精度和表面质量。
在齿轮磨削过程中,磨料的粒度和硬度、质量和形状等都会对磨削效果产生影响。
因此,在选择磨料时需要根据工件的材料、加工要求等条件进行合理的选择。
此外,磨削还需要考虑到切削液的使用、磨削力的控制、磨削工艺参数的优化等方面,才能保证齿轮的磨削质量和效率。
综上所述,齿轮磨削是一项非常重要的工艺,其原理是利用磨料与工件表面的相对运动,将工件表面的毛刺、凸起等不平整部分去除,从而提高齿轮的表面质量和精度。
在磨削过程中,还需要注意磨料选择、切削液使用、磨削力和工艺参数的控制等方面,才能保证齿轮的磨削效果和质量。
磨削加工25°压力角的斜齿轮

式中
—— 法向磨 削角( 由工艺给定 ) ;
卢 —— 节圆螺旋 角(i = s cs 0 ) s i oa/cs 。  ̄
磊 工冷 工 加
WWW. et wor i m al k ng1 50 c 9 . om
21年 2 0 第期 o
立 车 工 作 台 沉 孔 加 工
l进 入 钻 模 的 定 位孔 d 就 实现 了 沉 孔 的 定 位 ,这 时就 可 以开 动 进 给进 行 沉 孔 加 工
1 .定位柱
图
2
2 合 金部 分 3 锥 柄 . .
了。在 钻 模 的 实
际应 用 中要 合 理
设计 钻模 的长度 , 还可 以根 据 工 作
台 的规 格 将 钻 模
可综合为以下公式 : 展成交换齿轮
i=( lb ) C/ 1 f a/ 1 ×(1d )=182 1 / 7 . 9 d 8
由于该齿轮 采用 了 O l 5 的压 力角 ,在我 国属非 =2 。 标设计 ,滚齿我们订购 了非标磨前齿 轮滚刀加工并 留 出
分度交换齿轮 i=( 2 6)X( ): 4 z( o/2 c/ 2 / 6~1 齿 为 1/ ) 1 2 z 进给交换齿轮 i= / 0 0 19 s( a b: .0 1 粗磨 )
( 圆周长 ) 分 ,而成 为某一 磨 削节 圆的周 长 竹 ( 图 d 见 2 ,这时展成交换齿轮计算公式 中的 d 改为 d 。其数 ) 应
值按下式计算 直齿
斜齿
d =doa OO cs/CS I
d =m. ( / o 3 ) × (o /cs ) x z cq cs o
, \
将 以上 关 系代 入展 成交 换 齿轮 计 算公 式 中,得 到
齿轮标准大全资料.doc

齿轮标准大全(精度部分)1 、 GB/T 2821-92齿轮几何要素代号(已作废)(注:已有GB/T 2821-2003 在标准参考资料<十二> 中)2 、 GB1356-88 渐开线圆柱齿轮基本齿廓(已作废)(注:已有GB/T 1356-2001 在标准汇编中)3 、 GB1357-87 渐开线圆柱齿轮模数(已作废)(注:已有“GB/T 1357-2008 通用机械和重型机械用圆柱齿轮模数”在标准汇编第九部分中)4 、 GB1356-88 渐开线圆柱齿轮基本齿廓、GB1357-87 渐开线圆柱齿轮模数编制说明5 、 GB10095-88 渐开线圆柱齿轮精度(已作废)6 、 GB10095-88 渐开线圆柱齿轮精度编制说明(注:已有GB/T 10095.1.2-2001 在标准参考资料<九>中)7 、 GB10096-88 齿条精度8 、 GB10096-88 齿条精度编制说明9 、 GB6443-86 渐开线圆柱齿轮图样上应注明的尺寸数据10 、 GB6443-86 渐开线圆柱齿轮图样上应注明的尺寸数据编制说明11 、 GB/T13924-94 渐开线圆柱齿轮精度检验规范12 、 GB/T13924-94 渐开线圆柱齿轮精度检验规范编制说明(注:已有GB/T 13924-2008渐开线圆柱齿轮精度检验细则在标准参考资料<九>中)13 、 JB/T53441-94 渐开线圆柱齿轮产品质量分等通则(注:标准出版社出版标准汇编中没有)14 、 JB/T53441-94 渐开线圆柱齿轮产品质量分等通则编制说明(蜗轮蜗杆部分)1 、GB10085-88圆柱蜗杆传动基本参数2 、GB10085-88圆柱蜗杆传动基本参数编制说明3 、GB10086-88圆柱蜗杆传动、蜗轮术语及代号4 、GB10087-88圆柱蜗杆基本齿廓5 、GB10087-88圆柱蜗杆基准齿形编制说明6 、GB10088-88圆柱蜗杆模数和直径7 、GB10088-88圆柱蜗杆模数和直径编制说明8 、GB10089-88圆柱蜗杆、蜗轮精度9 、GB10089-88圆柱蜗杆、蜗轮精度编制说明10 、 GB/T12760-91圆柱蜗杆、蜗轮图样上应注明的尺寸数据(圆弧齿轮部分)1 、 GB 1840-89圆弧圆柱齿轮模数2 、 GB 1840-89圆弧圆柱齿轮模数修订说明3 、 GB12759=91双圆弧圆柱齿轮基本齿廓4 、 GB12759=91双圆弧圆柱齿轮基本齿廓编制说明5 、 GB/T13799-92双圆弧圆柱齿轮承载能力计算方法6 、、 GB/T13799-92双圆弧圆柱齿轮承载能力计算方法编制说明7 、 GB/T14348.1-93双圆弧齿轮滚刀型式和尺寸(注:标准出版社出版标准汇编中没有)8 、 GB/T14348.2-93双圆弧齿轮滚刀技术条件(注:标准出版社出版标准汇编中没有)9 、 GB/T14348.1-93双圆弧齿轮滚刀型式和尺寸、GB/T14348.2-93双圆弧齿轮滚刀技术条件编制说明10 、 GB/T 15752-1995圆弧圆柱齿轮基本术语11 、 GB/T 15752-1995圆弧圆柱齿轮基本术语编制说明12 、 GB/T 15753-1995圆弧圆柱齿轮精度13 、 GB/T 15753-1995圆弧圆柱齿轮精度编制说明(锥齿轮部分)1 、 GB10062-88锥齿轮承载能力计算方法(已作废)(注:已有GB/T 10062.1.2.3-2003在标准参考资料<十一 > 中)2 、 GB10062-88锥齿轮承载能力计算方法编制说明3 、 GB11365-89锥齿轮和准双曲面齿轮精度4 、 GB11365-89锥齿轮和准双曲面齿轮精度编制说明5 、 GB11367-89锥齿轮胶合承载能力计算方法(注:标准出版社出版标准汇编中没有)6 、 GB11367-89锥齿轮胶合承载能力计算方法编制说明7 、 GB12368-90锥齿轮模数8 、 GB12368-90锥齿轮模数编制说明9 、 GB12369-90直齿及斜齿锥齿轮基本齿廓10 、 GB12369-90直齿及斜齿锥齿轮基本齿廓编制说明11 、 GB12370-90锥齿轮和准双曲面齿轮术语12 、 GB12371-90锥齿轮图样上应注明的尺寸数据13 、 GB12371-90锥齿轮图样上应注明的尺寸数据编制说明(齿轮装置部分)1 、 GB6404-86齿轮装置噪声声功率级测定方法(已作废)(注:已有 GB/T 6404.1-2005/ISO8579-1:2002 (代替 GB/T 6404-1986 )齿轮装置的验收规范第1 部分:空气传播噪声的试验规范在最新标准中)2 、 GB6404-86 齿轮装置噪声声功率级测定方法编制说明3 、 GB8542-87 透平齿轮传动装置技术条件4 、 GB8542-87 透平齿轮传动装置技术条件编制说明5 、 GB8543-87 验收试验中齿轮装置机械振动的测定(已作废)(注:已有GB/T 6404.2-2005/ISO 8579-2:2002 (代替 GB/T 8543-1987 )齿轮装置的验收规范第2 部分:验收试验中齿轮装置机械振动的测定在最新标准中)6 、 GB8543-87 验收试验中齿轮装置机械振动的测定编制说明7 、 GB/T14231-93 齿轮装置效率测定方法8 、 GB/T14231-93 齿轮装置效率测定方法编制说明9 、 JB/T5076-91 齿轮装置噪声评价10 、 JB/T5076-91 齿轮装置噪声评价编制说明11 、 JB/T5077-91 通用齿轮装置型式试验方法12 、 JB/T5077-91 通用齿轮装置型式试验方法编制说明13 、 JB/T6078-92 齿轮装置质量检验总则14 、 JB/T6078-92 齿轮装置质量检验总则编制说明15 、 JB/T7929-95 齿轮传动装置清洁度16 、 JB/T7929-95 齿轮传动装置清洁度编制说明17 、 JB/T8831-1999 工业齿轮润滑油选用方法(已作废)(注:已有JB/T8831-2001在标准出版社出版标准汇编中)18 、 JB/T8831-1999工业齿轮润滑油选用方法编制说明(齿轮热处理部分)1 、 GB/T3480.5-2008直齿轮和斜齿轮承载能力计算第五部分;材料的强度和质量2 、 GB/T3480.5-2008直齿轮和斜齿轮承载能力计算第五部分;材料的强度和质量编制说明3 、 GB/T17879-1999齿轮磨削后表面回火的浸蚀检验(注:标准出版社出版标准汇编中没有)4 、 GB/T17879-1999齿轮磨削后表面回火的浸蚀检验编制说明5 、 JB/T5078-91高速齿轮材料选择及热处理质量控制的一般规定6 、 JB/T7516-94齿轮气体渗碳热处理工艺及其质量控制7 、 JB/T9171-1999齿轮火焰及感应淬火工艺及其质量控制8 、 JB/T9171-1999齿轮火焰及感应淬火工艺及其质量控制标准介绍9 、 JB/T9172-1999齿轮渗氮、氮碳共渗工艺及其质量控制10 、 JB/T9172-1999齿轮渗氮、氮碳共渗工艺及其质量控制标准介绍11 、 JB/T9173-1999齿轮碳氮共渗工艺及其质量控制12 、 JB/T9173-1999齿轮碳氮共渗工艺及其质量控制标准介绍(齿轮减速器部分)1 、 JB/T8853-2001圆柱齿轮减速器2 、 JB/T7935-1999圆弧圆柱蜗杆减速器3 、 JB/T7936-1999直廓环面蜗杆减速器4 、 JB/T9050.1-1999圆柱齿轮减速器通用技术条件5 、 JB/T9050.2-1999圆柱齿轮减速器接触斑点测定方法6 、 JB/T9050.3-1999圆柱齿轮减速器加载试验方法7 、 JB/T9051-1999平面包络环面蜗杆减速器(新齿轮精度部分)1 、 GB/T10095.1-2008圆柱齿轮精度制第1部分:轮齿同侧齿面偏差的定义和允许值2 、 GB/T10095.2-2008圆柱齿轮精度制第2部分:径向综合偏差与径向跳动的定义和允许值3 、 GB/Z18620.1-2008圆柱齿轮检验实施规范第1部分:轮齿同侧齿面的检验4 、 GB/Z18620.2-2008圆柱齿轮检验实施规范第2部分:径向综合偏差、径向跳动、齿厚和侧隙的检验3 、 GB/Z18620.3-2008圆柱齿轮检验实施规范第3部分:齿轮坯、轴中心距和轴线平行度4 、 GB/Z18620.4-2008圆柱齿轮检验实施规范第4部分:表面结构和轮齿接触斑点的检验5 、 GB/T 13924-2008渐开线圆柱齿轮精度检验细则6 、 GB/T 1357-2008通用机械和重型机械用圆柱齿轮模数(齿轮刀具国标部分)1 、 GB/T 6081-2001直齿插齿刀基本型式和尺寸2 、 GB/T 6082-2001直齿插齿刀通用技术条件3 、 GB/T 6083-2001齿轮滚刀基本型式和尺寸4 、 GB/T 6084-2001齿轮滚刀通用技术条件5 、 GB/T 14333-93盘形剃齿刀6 、 GB/T 14348.1-93双圆弧齿轮滚刀型式和尺寸7 、 GB/T 14348.2-93双圆弧齿轮滚刀技术条件8 、 GB 9205-88镶片齿轮滚刀(齿轮刀具行标部分)1 、 JB/T 2494.1-94小模数齿轮滚刀基本型式和尺寸2 、 JB/T 2494.2-94小模数齿轮滚刀技术条件3 、 JB/T 3095.1-94小模数直齿插齿刀基本型式和尺寸4 、 JB/T 3095.2-94小模数直齿插齿刀技术条件5 、 JB/T 3227-1999高精度齿轮滚刀通用技术条件6 、 JB/T 4103-94剃前齿轮滚刀基本型式和尺寸7 、 JB/T 4104-94剃前齿轮滚刀技术条件8 、 JB/T 7654.1-94整体硬质合金小模数齿轮滚刀基本型式和尺寸9 、 JB/T 7654.2-94整体硬质合金小模数齿轮滚刀技术条件10 、 JB/T 7967-1999渐开线内花键插齿刀基本型式和尺寸11 、 JB/T 7968.1-1999磨前齿轮滚刀基本型式和尺寸12 、 JB/T 7968.2-1999磨前齿轮滚刀技术条件13 、 JB/T 7970.1-1999盘形齿轮铣刀基本型式和尺寸14 、 JB/T 7970.2-1999盘形齿轮铣刀技术条件15 、 JB/T 8345-96弧齿锥齿轮铣刀 1 ︰ 24 圆锥孔尺寸及公差16 、 JB/T 9990.1-1999直齿锥齿轮精刨刀基本型式和尺寸17 、 JB/T 9990.2-1999直齿锥齿轮精刨刀技术条件(锥齿轮部分)1 、 GB/T10062.1-2003/ISO10300-1:2001锥齿轮承载能力计算方法第1部分:概述和通用影响系数2 、 GB/T10062.2-2003/ISO10300-1:2001锥齿轮承载能力计算方法第2部分:齿面接触疲劳(点蚀)强度计算3 、 GB/T10062.3-2003/ISO10300-1:2001锥齿轮承载能力计算方法第3部分:齿根弯曲强度计算4 、 GB/Z6413.1-2003/ISO/TR 13989-1:2000圆柱齿轮、锥齿轮和准双曲面齿轮胶合承载能力计算方法第 1 部分:闪温法5 、 GB/Z6413.2-2003/ISO/TR 13989-1:2000圆柱齿轮、锥齿轮和准双曲面齿轮胶合承载能力计算方法第 2 部分:积分温度法1 、 GB/Z 19414-2003/ISO/TR 13593:1999工业用闭式齿轮齿轮传动装置2 、 GB/T 19406-2003/ISO 9085:2002渐开线直齿和斜齿圆柱齿轮承载能力计算方法工业齿轮应用3 、 GB/T2821-2003/ISO 701:1998齿轮几何要素代号(齿轮量仪部分)1 、 GB/T 1217-2004公法线千分尺2 、 GB 5106-85圆柱直齿渐开线花键量规3 、GB 6060.2-85表面粗糙度比较样块磨、车、镗、铣、插及刨加工表面4 、 GB 6060.5-88表面粗糙度比较样块抛(喷)丸、喷砂加工表面5 、 GB/T 6316-1996齿厚游标卡尺6 、 GB/T 6320-1997杠杆齿轮比较仪7 、 GB/T 6467-2001齿轮渐开线样板8 、 GB/T 6468-2001齿轮螺旋线样板9 、 GB 10919-89矩形花键量规10 、 JB/T 10008-1999测量蜗杆11 、 JB/T 10012-1999万能测齿仪12 、 JB/T 10013-1999万能渐开线检查仪13 、 JB/T 10019-1999齿轮齿距测量仪14 、 JB/T 10020-1999万能齿轮测量机15 、 JB/T 10021-1999齿轮螺旋线测量仪16 、 JB/T 10022-1999便携式齿轮齿距测量仪17 、 JB/T 10023-1999便携式齿轮基节测量仪18 、 JB/T 10024-1999立式滚刀测量仪19 、 JB/T 10025-1999齿轮双面啮合综合测量仪20 、 JB/T 10026-1999齿轮单面啮合整体误差测量仪。
齿轮磨削工艺技术
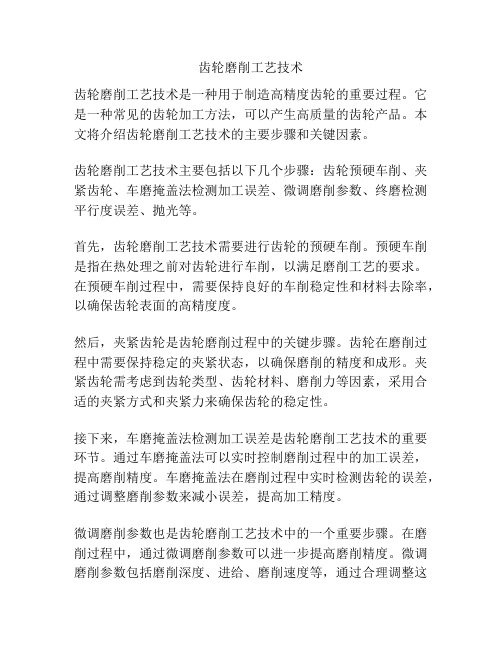
齿轮磨削工艺技术齿轮磨削工艺技术是一种用于制造高精度齿轮的重要过程。
它是一种常见的齿轮加工方法,可以产生高质量的齿轮产品。
本文将介绍齿轮磨削工艺技术的主要步骤和关键因素。
齿轮磨削工艺技术主要包括以下几个步骤:齿轮预硬车削、夹紧齿轮、车磨掩盖法检测加工误差、微调磨削参数、终磨检测平行度误差、抛光等。
首先,齿轮磨削工艺技术需要进行齿轮的预硬车削。
预硬车削是指在热处理之前对齿轮进行车削,以满足磨削工艺的要求。
在预硬车削过程中,需要保持良好的车削稳定性和材料去除率,以确保齿轮表面的高精度度。
然后,夹紧齿轮是齿轮磨削过程中的关键步骤。
齿轮在磨削过程中需要保持稳定的夹紧状态,以确保磨削的精度和成形。
夹紧齿轮需考虑到齿轮类型、齿轮材料、磨削力等因素,采用合适的夹紧方式和夹紧力来确保齿轮的稳定性。
接下来,车磨掩盖法检测加工误差是齿轮磨削工艺技术的重要环节。
通过车磨掩盖法可以实时控制磨削过程中的加工误差,提高磨削精度。
车磨掩盖法在磨削过程中实时检测齿轮的误差,通过调整磨削参数来减小误差,提高加工精度。
微调磨削参数也是齿轮磨削工艺技术中的一个重要步骤。
在磨削过程中,通过微调磨削参数可以进一步提高磨削精度。
微调磨削参数包括磨削深度、进给、磨削速度等,通过合理调整这些参数可以减小磨削误差,提高加工精度。
终磨检测平行度误差也是齿轮磨削工艺技术中的一个关键环节。
通过终磨检测可以准确测量齿轮的平行度误差,进一步改善加工精度。
终磨检测平行度误差需要使用高精度的测量仪器和设备,以确保测量结果的准确性。
最后,齿轮磨削工艺技术还需要进行抛光等后续处理。
抛光可以进一步提高精度和光洁度,使得齿轮的表面更加光滑和平整。
总的来说,齿轮磨削工艺技术是一种制造高精度齿轮的重要方法。
通过预硬车削、夹紧齿轮、车磨掩盖法检测加工误差、微调磨削参数、终磨检测平行度误差和抛光等步骤,可以获得高质量的齿轮产品。
这些步骤中的关键因素包括材料选用、磨削参数调整、夹紧方式等,需要进行合理的选择和调整,以实现高精度度的齿轮磨削。
齿轮磨削加工工艺
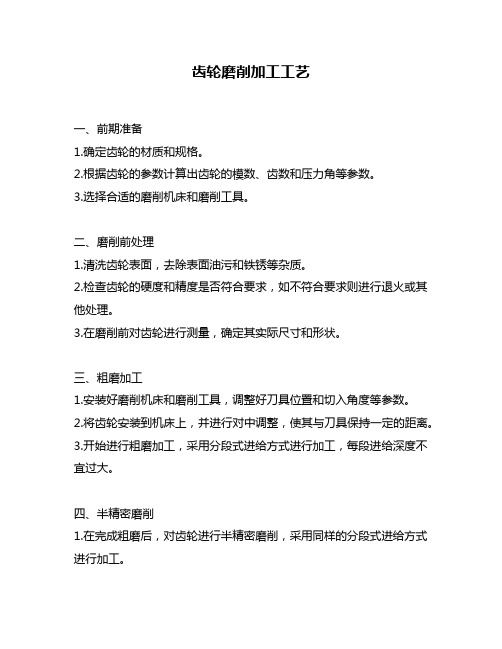
齿轮磨削加工工艺
一、前期准备
1.确定齿轮的材质和规格。
2.根据齿轮的参数计算出齿轮的模数、齿数和压力角等参数。
3.选择合适的磨削机床和磨削工具。
二、磨削前处理
1.清洗齿轮表面,去除表面油污和铁锈等杂质。
2.检查齿轮的硬度和精度是否符合要求,如不符合要求则进行退火或其他处理。
3.在磨削前对齿轮进行测量,确定其实际尺寸和形状。
三、粗磨加工
1.安装好磨削机床和磨削工具,调整好刀具位置和切入角度等参数。
2.将齿轮安装到机床上,并进行对中调整,使其与刀具保持一定的距离。
3.开始进行粗磨加工,采用分段式进给方式进行加工,每段进给深度不宜过大。
四、半精密磨削
1.在完成粗磨后,对齿轮进行半精密磨削,采用同样的分段式进给方式进行加工。
2.为了保证加工质量,需要对磨削机床和磨削工具进行定期检查和维护。
3.在半精密磨削过程中,需要注意控制切削速度、进给速度和切削深度等参数,以确保加工精度。
五、精密磨削
1.在完成半精密磨削后,进行最后的精密磨削。
此时需要采用更加细致的进给方式和切入角度等参数。
2.为了保证加工质量,需要对磨削机床和磨削工具进行更加细致的检查和维护。
3.在精密磨削过程中,需要采用更加严格的控制方法来控制切割参数,以确保齿轮的最终形态、尺寸和表面质量。
六、后处理
1.完成齿轮的精密磨削后,需要对其表面进行清洗,并去除可能存在的毛刺和其他杂质。
2.对齿轮进行测量,并与原始设计要求进行比较,以确保其符合要求。
3.最后将齿轮包装好,并妥善保存。
齿轮的磨齿方法
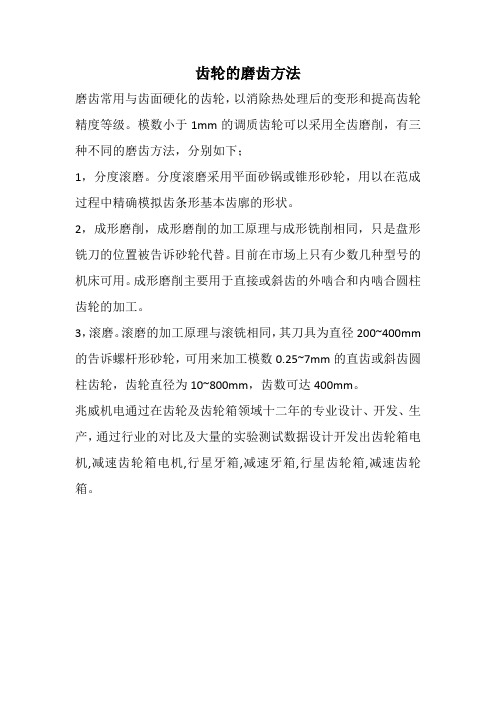
齿轮的磨齿方法
磨齿常用与齿面硬化的齿轮,以消除热处理后的变形和提高齿轮精度等级。
模数小于1mm的调质齿轮可以采用全齿磨削,有三种不同的磨齿方法,分别如下;
1,分度滚磨。
分度滚磨采用平面砂锅或锥形砂轮,用以在范成过程中精确模拟齿条形基本齿廓的形状。
2,成形磨削,成形磨削的加工原理与成形铣削相同,只是盘形铣刀的位置被告诉砂轮代替。
目前在市场上只有少数几种型号的机床可用。
成形磨削主要用于直接或斜齿的外啮合和内啮合圆柱齿轮的加工。
3,滚磨。
滚磨的加工原理与滚铣相同,其刀具为直径200~400mm 的告诉螺杆形砂轮,可用来加工模数0.25~7mm的直齿或斜齿圆柱齿轮,齿轮直径为10~800mm,齿数可达400mm。
兆威机电通过在齿轮及齿轮箱领域十二年的专业设计、开发、生产,通过行业的对比及大量的实验测试数据设计开发出齿轮箱电机,减速齿轮箱电机,行星牙箱,减速牙箱,行星齿轮箱,减速齿轮箱。
变速器齿轮磨削工艺研究
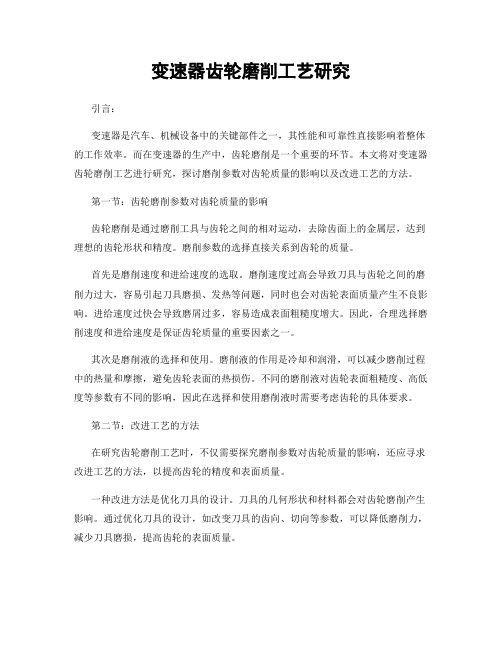
变速器齿轮磨削工艺研究引言:变速器是汽车、机械设备中的关键部件之一,其性能和可靠性直接影响着整体的工作效率。
而在变速器的生产中,齿轮磨削是一个重要的环节。
本文将对变速器齿轮磨削工艺进行研究,探讨磨削参数对齿轮质量的影响以及改进工艺的方法。
第一节:齿轮磨削参数对齿轮质量的影响齿轮磨削是通过磨削工具与齿轮之间的相对运动,去除齿面上的金属层,达到理想的齿轮形状和精度。
磨削参数的选择直接关系到齿轮的质量。
首先是磨削速度和进给速度的选取。
磨削速度过高会导致刀具与齿轮之间的磨削力过大,容易引起刀具磨损、发热等问题,同时也会对齿轮表面质量产生不良影响。
进给速度过快会导致磨屑过多,容易造成表面粗糙度增大。
因此,合理选择磨削速度和进给速度是保证齿轮质量的重要因素之一。
其次是磨削液的选择和使用。
磨削液的作用是冷却和润滑,可以减少磨削过程中的热量和摩擦,避免齿轮表面的热损伤。
不同的磨削液对齿轮表面粗糙度、高低度等参数有不同的影响,因此在选择和使用磨削液时需要考虑齿轮的具体要求。
第二节:改进工艺的方法在研究齿轮磨削工艺时,不仅需要探究磨削参数对齿轮质量的影响,还应寻求改进工艺的方法,以提高齿轮的精度和表面质量。
一种改进方法是优化刀具的设计。
刀具的几何形状和材料都会对齿轮磨削产生影响。
通过优化刀具的设计,如改变刀具的齿向、切向等参数,可以降低磨削力,减少刀具磨损,提高齿轮的表面质量。
另一种改进方法是引入超声波辅助磨削技术。
超声波振动可以改变切削区域的状况,进一步提高齿轮磨削的精度和效率。
超声波辅助磨削技术可以减小刀具与齿轮之间的接触力,降低刀具磨损,同时还可以改善材料的断裂行为,提高齿轮的表面质量。
结论:在变速器齿轮磨削工艺研究中,磨削参数的选取和改进工艺的方法都是关键因素。
合理选择磨削速度和进给速度,使用适当的磨削液,可以提高齿轮的质量。
优化刀具的设计和引入超声波辅助磨削技术,可以进一步提高齿轮的精度和表面质量。
通过不断的研究和改进,变速器齿轮磨削工艺将会更加完善,为汽车和机械设备的工作效率提供更好的保障。
- 1、下载文档前请自行甄别文档内容的完整性,平台不提供额外的编辑、内容补充、找答案等附加服务。
- 2、"仅部分预览"的文档,不可在线预览部分如存在完整性等问题,可反馈申请退款(可完整预览的文档不适用该条件!)。
- 3、如文档侵犯您的权益,请联系客服反馈,我们会尽快为您处理(人工客服工作时间:9:00-18:30)。
此文档下载后即可编辑
齿轮加工机床的效率、精度、性能等方面介绍
来源:机械专家网发布时间:2009-11-20 机械专家网
随着科学技术和经济的发展,齿轮加工业对于齿轮加工机床的性能要求不断提高,反之,齿轮加工机床制造业对于齿轮加工又具有导向作用,形成有机的联动发展。
为此,一批能适应社会科技和经济发展节拍的新产品应运而生;反之,则被淘汰。
这在齿轮磨床制造业中尤为突出。
像瑞士马格公司(Magg)七十余年来一直以其生产的碟形双砂轮磨齿机在国际市场独显风采,作为磨齿机中最高精度的代表产品,采用展成磨削原理,及其它技术措施,可磨削出三级以上精度的齿轮。
但是,马格磨齿机亦有不足之处,主要是:效率低展成磨削为点接触加上碟形砂轮自身强度、刚度限制,不能作深切或强力磨削;生产成本高所需的特殊附件多,如缺口分度板齿数须和工件齿数相匹配,工作基圆要与滚圆盘的直径一致等,工作种类愈多,所需附件愈多。
为此,这家世界闻名、历史悠久的公司,于八十年代末被瑞士奥立康公司(Oerllkon)兼并。
国内曾研制出Y7032A、Y7063A、Y7160等碟形双砂轮磨齿机,其中原秦川机床厂制造的Y7032A,其主要性能均达到马格公司同类产品SD-32-X碟形双砂轮磨齿机水平,荣获国家科技进步一等奖。
但是,由于高效蜗杆砂轮磨齿机制造技术的成熟应用,碟形双砂轮磨齿机的市场占有率逐年缩小。
从马格公司被兼并的现实,留给人们思考的是两个字:“效率”。
效率是物质能量的反映,是生命力的象征。
为此,自七十年代末至今,国内外磨齿机发展趋势,一直以高效率、高精度为追求目标。