白车身焊装生产线如何提升效率
浅谈白车身焊装夹具设计要点分析

浅谈白车身焊装夹具设计要点分析一、引言白车身焊装夹具设计是汽车生产中的关键环节之一,夹具设计的质量直接影响到整个生产线的效率和产品质量。
白车身焊装夹具设计的要点分析对于提高生产效率、降低生产成本、保证产品质量具有重要意义。
本文将从夹具设计的要点入手,分析影响夹具设计的关键因素,为相关从业人员提供参考。
二、白车身焊装夹具设计的要点分析1. 结构设计白车身焊装夹具的结构设计是决定其功能和稳定性的关键。
优秀的结构设计应该具有简单、坚固、稳定的特点。
夹具应该能够固定车身零部件,确保其在焊接过程中不会发生位移或变形。
夹具的结构应该简单,易于安装和拆卸,便于操作人员进行维护和保养。
夹具的结构应该坚固耐用,能够承受汽车生产线高频率的使用,确保生产过程的稳定性和安全性。
2. 材料选择夹具设计中的材料选择直接关系到夹具的耐用性和使用寿命。
应该选择具有良好的机械性能和抗腐蚀性能的材料,以确保夹具在高频使用的情况下不易损坏和生锈。
对于一些特殊工艺需求的夹具设计,应根据具体情况选择合适的特种材料,以保证夹具的稳定性和可靠性。
3. 工艺要求夹具设计应该考虑到生产工艺的需求,确保夹具能够适应不同产品的焊接要求。
对于多品种、小批量生产的汽车生产线,夹具设计需要具有一定的灵活性,能够适应不同车型的生产需求。
夹具的设计也应考虑到组装和拆卸的便捷性,以减少生产线上的换线时间,提高生产效率。
4. 精度控制夹具设计中的精度控制是保证产品质量的关键。
夹具应该具有良好的定位和固定能力,确保焊接工艺中的高精度要求得以满足。
对于一些需要提高精度的工序,如车身焊接中的角度、尺寸等要求,夹具的设计应该考虑到这些因素,保证产品焊接后的精度和稳定性。
5. 成本控制夹具设计中的成本控制是企业经营的重要因素。
夹具的设计应该充分考虑生产成本、工时成本等因素,选择合适的设计方案来降低生产成本。
夹具的使用寿命也是成本控制的重要因素,应尽量选择耐用、易维护的设计方案,以减少后期的维护和更换成本。
如何高效提升车间的生产效率
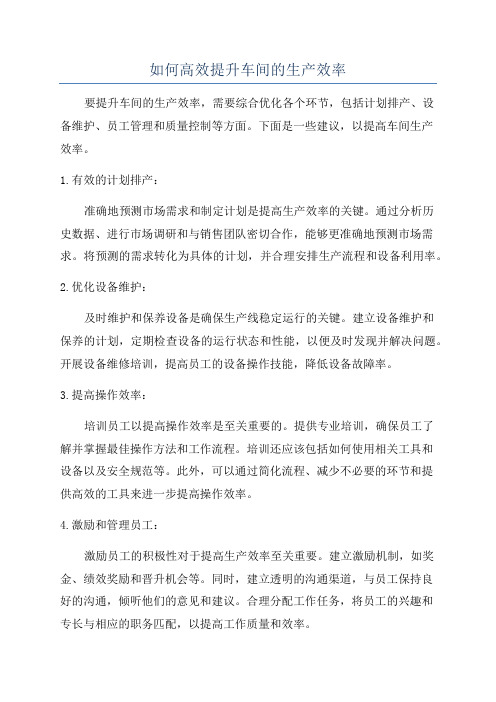
如何高效提升车间的生产效率要提升车间的生产效率,需要综合优化各个环节,包括计划排产、设备维护、员工管理和质量控制等方面。
下面是一些建议,以提高车间生产效率。
1.有效的计划排产:准确地预测市场需求和制定计划是提高生产效率的关键。
通过分析历史数据、进行市场调研和与销售团队密切合作,能够更准确地预测市场需求。
将预测的需求转化为具体的计划,并合理安排生产流程和设备利用率。
2.优化设备维护:及时维护和保养设备是确保生产线稳定运行的关键。
建立设备维护和保养的计划,定期检查设备的运行状态和性能,以便及时发现并解决问题。
开展设备维修培训,提高员工的设备操作技能,降低设备故障率。
3.提高操作效率:培训员工以提高操作效率是至关重要的。
提供专业培训,确保员工了解并掌握最佳操作方法和工作流程。
培训还应该包括如何使用相关工具和设备以及安全规范等。
此外,可以通过简化流程、减少不必要的环节和提供高效的工具来进一步提高操作效率。
4.激励和管理员工:激励员工的积极性对于提高生产效率至关重要。
建立激励机制,如奖金、绩效奖励和晋升机会等。
同时,建立透明的沟通渠道,与员工保持良好的沟通,倾听他们的意见和建议。
合理分配工作任务,将员工的兴趣和专长与相应的职务匹配,以提高工作质量和效率。
5.质量控制:高质量的产品是提高生产效率的前提。
建立严格的质量控制体系,包括原材料检测、工艺控制、生产过程监控和成品检验。
为员工提供质量意识培训,加强质量意识,提高工作的准确性和一次通过率。
定期对质量控制体系进行评估和改进,以确保其有效性。
6.引进新技术和自动化:引进新技术和自动化设备是提高生产效率的有效手段。
通过自动化生产线和机器人的应用,可以提高生产速度和质量,并减少人为因素带来的错误和故障。
同时还可以提高设备的利用率和产能。
7.持续改进:持续改进是提高生产效率的关键。
建立改进机制,鼓励员工提出改进建议,并通过操作过程的监控和数据分析,发现问题和瓶颈,并制定相应的改进措施。
车身装配生产线平衡改善案例
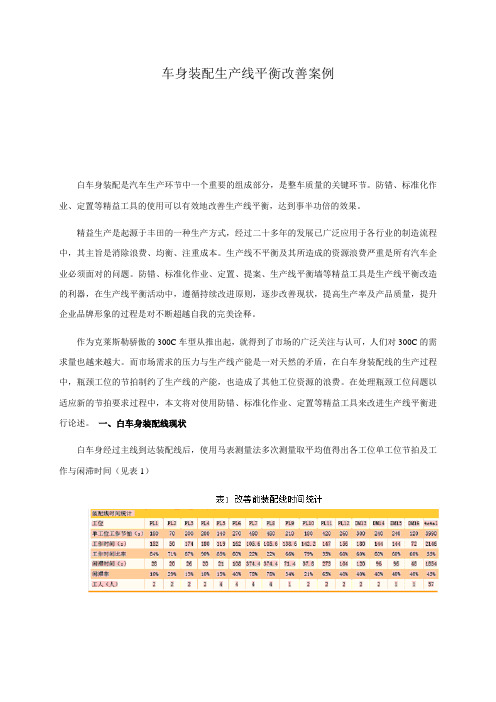
车身装配生产线平衡改善案例白车身装配是汽车生产环节中一个重要的组成部分,是整车质量的关键环节。
防错、标准化作业、定置等精益工具的使用可以有效地改善生产线平衡,达到事半功倍的效果。
精益生产是起源于丰田的一种生产方式,经过二十多年的发展已广泛应用于各行业的制造流程中,其主旨是消除浪费、均衡、注重成本。
生产线不平衡及其所造成的资源浪费严重是所有汽车企业必须面对的问题。
防错、标准化作业、定置、提案、生产线平衡墙等精益工具是生产线平衡改造的利器,在生产线平衡活动中,遵循持续改进原则,逐步改善现状,提高生产率及产品质量,提升企业品牌形象的过程是对不断超越自我的完美诠释。
作为克莱斯勒骄傲的300C车型从推出起,就得到了市场的广泛关注与认可,人们对300C的需求量也越来越大。
而市场需求的压力与生产线产能是一对天然的矛盾,在白车身装配线的生产过程中,瓶颈工位的节拍制约了生产线的产能,也造成了其他工位资源的浪费。
在处理瓶颈工位问题以适应新的节拍要求过程中,本文将对使用防错、标准化作业、定置等精益工具来改进生产线平衡进行论述。
一、白车身装配线现状白车身经过主线到达装配线后,使用马表测量法多次测量取平均值得出各工位单工位节拍及工作与闲滞时间(见表1)图1中,最长工序时间(480s)决定装配线节拍,装配线整体节拍为7.5件/h,8h单班日产量为60件。
图1 工作与闲滞时间二、瓶颈分析1、工序分析:BPT1(Basic Pitch Time):工序平均所持加工净值(不含浮余率)。
BPT2:人均所持加工净值(不含浮余率)。
BPT1=总加工时间净值/工序数=(PL1+PL3+PL4+PL4+PL5+PL6+PL7+PL8+PL9+PL10+PL11+ PL12+ DM13+DM14+DM15+DM16)/16=3990/16=249.375s。
BPT2=总加工时间净值/作业人员人数=3990/37=107.9s。
2、制成作业平均时间表□按照工序顺序,记入必要事项:工序号码、工序名称、PT线、加工时间净值。
浅谈白车身焊装夹具设计要点分析
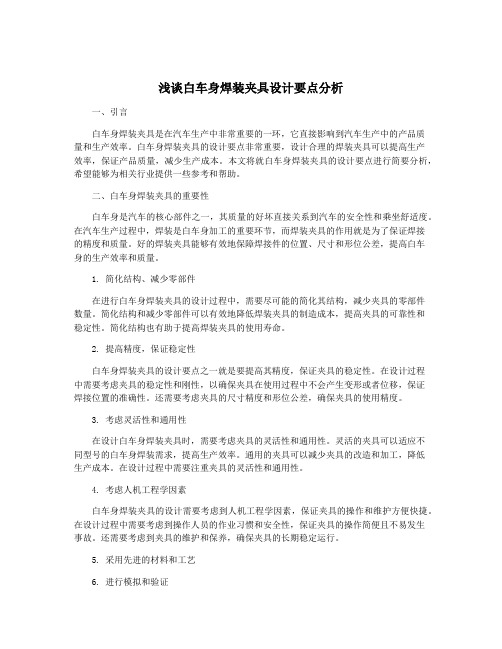
浅谈白车身焊装夹具设计要点分析一、引言白车身焊装夹具是在汽车生产中非常重要的一环,它直接影响到汽车生产中的产品质量和生产效率。
白车身焊装夹具的设计要点非常重要,设计合理的焊装夹具可以提高生产效率,保证产品质量,减少生产成本。
本文将就白车身焊装夹具的设计要点进行简要分析,希望能够为相关行业提供一些参考和帮助。
二、白车身焊装夹具的重要性白车身是汽车的核心部件之一,其质量的好坏直接关系到汽车的安全性和乘坐舒适度。
在汽车生产过程中,焊装是白车身加工的重要环节,而焊装夹具的作用就是为了保证焊接的精度和质量。
好的焊装夹具能够有效地保障焊接件的位置、尺寸和形位公差,提高白车身的生产效率和质量。
1. 简化结构、减少零部件在进行白车身焊装夹具的设计过程中,需要尽可能的简化其结构,减少夹具的零部件数量。
简化结构和减少零部件可以有效地降低焊装夹具的制造成本,提高夹具的可靠性和稳定性。
简化结构也有助于提高焊装夹具的使用寿命。
2. 提高精度,保证稳定性白车身焊装夹具的设计要点之一就是要提高其精度,保证夹具的稳定性。
在设计过程中需要考虑夹具的稳定性和刚性,以确保夹具在使用过程中不会产生变形或者位移,保证焊接位置的准确性。
还需要考虑夹具的尺寸精度和形位公差,确保夹具的使用精度。
3. 考虑灵活性和通用性在设计白车身焊装夹具时,需要考虑夹具的灵活性和通用性。
灵活的夹具可以适应不同型号的白车身焊装需求,提高生产效率。
通用的夹具可以减少夹具的改造和加工,降低生产成本。
在设计过程中需要注重夹具的灵活性和通用性。
4. 考虑人机工程学因素白车身焊装夹具的设计需要考虑到人机工程学因素,保证夹具的操作和维护方便快捷。
在设计过程中需要考虑到操作人员的作业习惯和安全性,保证夹具的操作简便且不易发生事故。
还需要考虑到夹具的维护和保养,确保夹具的长期稳定运行。
5. 采用先进的材料和工艺6. 进行模拟和验证在完成白车身焊装夹具的设计后,需要进行模拟和验证,确保夹具的性能和稳定性。
生产车间效率提升计划

生产车间效率提升计划在当今竞争激烈的市场环境中,企业需要不断提高生产效率以保持竞争力。
生产车间作为企业生产的核心,其效率的提升对于企业的整体运营至关重要。
本文将探讨如何制定一个有效的生产车间效率提升计划,以提高生产效率、降低成本并提升企业盈利能力。
一、分析现状与问题在制定生产车间效率提升计划之前,需要对现有的生产情况进行全面的分析,找出存在的问题和瓶颈。
这包括对生产流程、设备状况、人员配置、物料管理等方面的检查。
通过深入分析,可以确定影响生产效率的关键因素,为后续的改进提供方向。
二、优化生产流程针对分析结果,对生产流程进行优化是提高效率的关键。
可以考虑以下几个方面:1.简化操作流程:通过合并、减少或重新排序生产步骤,降低复杂度,提高生产速度。
2.标准化操作:制定标准操作程序,确保员工遵循统一的流程,减少差错率。
3.引入自动化设备:用自动化设备替代人工操作,提高生产线的自动化水平,减少人工误差。
4.优化物料管理:建立科学的物料管理制度,确保物料供应及时、准确,降低停工待料时间。
三、培训与激励员工员工的技能和积极性对生产效率有直接影响。
因此,培训和激励员工是提升计划的重要环节。
具体措施包括:1.定期培训:为员工提供技能培训和安全教育,提高其操作水平和安全意识。
2.激励制度:建立绩效考核和奖励制度,激励员工主动提高工作效率。
3.团队建设:加强团队沟通与协作,提高整体执行力。
四、强化设备维护与管理设备是生产车间的核心要素,其运行状况直接关系到生产效率。
因此,必须重视设备的维护与管理:1.定期检查:制定设备检查制度,定期对设备进行全面检查,确保设备处于良好状态。
2.预防性维护:推行预防性维护体系,定期对设备进行保养和维修,降低故障率。
3.设备更新:及时淘汰老旧设备,引进新设备和技术,提高生产能力。
五、监控与持续改进制定生产车间效率提升计划后,需要建立监控机制以确保实施效果并持续改进。
具体措施包括:1.设定关键绩效指标(KPI):根据企业战略目标和生产实际情况,设定合理的关键绩效指标,如产量、质量、成本等。
车身装配焊接生产线

车身装配焊接生产线引言车身装配焊接生产线是汽车制造过程中的关键环节之一。
它涉及到车身的组装和焊接工序,直接影响到汽车的质量和效率。
本文将介绍车身装配焊接生产线的工作流程、设备和关键技术。
基本工作流程车身装配焊接生产线的基本工作流程包括以下几个步骤:1.车身零部件供应:车身零部件是车身装配焊接的基本组成部分,供应商将零部件送至生产线。
2.车身装配:在装配区域,工人将车身零部件按照装配顺序进行组装。
这包括安装车身框架、车身面板、车身底盘等。
装配过程中需要使用各种设备和工具,如螺丝刀、气动压机等。
3.焊接工序:在焊接区域,车身的各个零部件会通过焊接技术进行连接。
常用的焊接方法包括气体焊接、电弧焊接等。
焊接工序需要使用焊接设备和辅助设备,如焊接机器人、焊接工作台等。
4.质检和修正:焊接完成后,车身会通过质检线进行检查。
检查包括焊接缺陷、尺寸偏差、外观等方面。
如果发现问题,需要对车身进行修正,确保其质量达到标准要求。
5.上涂料和烤漆:车身经过质检合格后,会进入涂料区域。
在这里,工人会给车身上涂底漆、面漆、清漆等。
然后将车身送至烤漆室,进行加热和固化,以确保漆面质量和耐久性。
6.装配附件:在装配线上,还需要安装一些附件,如车灯、门把手、车身贴纸等。
这些附件的安装需要工人进行手工操作,确保符合设计要求。
7.最终装配和检验:车身装配完毕后,会进行最终的检验,包括车身外观、内饰、灯光等方面。
通过检验后,车身会被送至下一工序或最终组装线。
设备和技术车身装配焊接生产线涉及到一系列设备和关键技术,以下是常用的设备和技术:•焊接机器人:焊接机器人是车身焊接生产线的核心设备之一。
它可以实现自动化焊接,提高焊接质量和效率。
通过使用焊接机器人,可以减少人为因素的影响,提高生产线的稳定性和一致性。
•自动测量系统:为了确保车身装配的精度和一致性,常常使用自动测量系统。
这些系统可以对车身的尺寸、位移、角度等进行测量和分析,及时发现装配差异,并进行修正。
生产车间生产效率提升方案
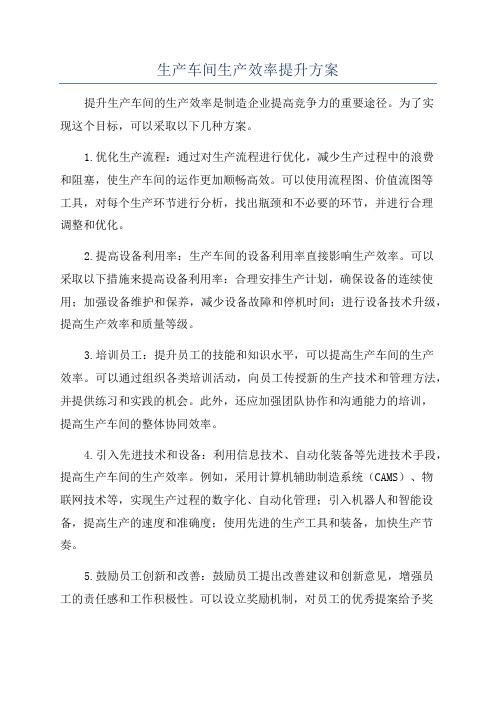
生产车间生产效率提升方案提升生产车间的生产效率是制造企业提高竞争力的重要途径。
为了实现这个目标,可以采取以下几种方案。
1.优化生产流程:通过对生产流程进行优化,减少生产过程中的浪费和阻塞,使生产车间的运作更加顺畅高效。
可以使用流程图、价值流图等工具,对每个生产环节进行分析,找出瓶颈和不必要的环节,并进行合理调整和优化。
2.提高设备利用率:生产车间的设备利用率直接影响生产效率。
可以采取以下措施来提高设备利用率:合理安排生产计划,确保设备的连续使用;加强设备维护和保养,减少设备故障和停机时间;进行设备技术升级,提高生产效率和质量等级。
3.培训员工:提升员工的技能和知识水平,可以提高生产车间的生产效率。
可以通过组织各类培训活动,向员工传授新的生产技术和管理方法,并提供练习和实践的机会。
此外,还应加强团队协作和沟通能力的培训,提高生产车间的整体协同效率。
4.引入先进技术和设备:利用信息技术、自动化装备等先进技术手段,提高生产车间的生产效率。
例如,采用计算机辅助制造系统(CAMS)、物联网技术等,实现生产过程的数字化、自动化管理;引入机器人和智能设备,提高生产的速度和准确度;使用先进的生产工具和装备,加快生产节奏。
5.鼓励员工创新和改善:鼓励员工提出改善建议和创新意见,增强员工的责任感和工作积极性。
可以设立奖励机制,对员工的优秀提案给予奖励;组织员工参与改善项目,鼓励他们在生产过程中发现问题并提出解决方案。
6.精益生产管理:采用精益生产管理方法,精确分析生产过程中的浪费和低效因素,并采取相应措施进行改进。
可以运用价值流图、作业标准化等工具,优化流程、减少库存、降低生产成本。
7.加强质量管理:优先保证产品质量,提高生产效率。
通过建立健全的质量管理体系,严格控制产品生产过程中的质量标准和环节,减少生产中的次品率和质量问题,降低返工率,提高生产效率。
8.优化供应链管理:加强与供应商和客户的合作,优化供应链,提高物料和信息流的流动效率。
提高装配效率的措施
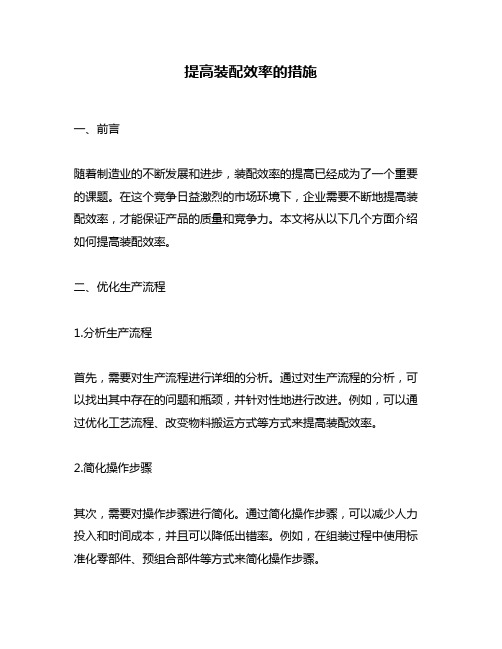
提高装配效率的措施一、前言随着制造业的不断发展和进步,装配效率的提高已经成为了一个重要的课题。
在这个竞争日益激烈的市场环境下,企业需要不断地提高装配效率,才能保证产品的质量和竞争力。
本文将从以下几个方面介绍如何提高装配效率。
二、优化生产流程1.分析生产流程首先,需要对生产流程进行详细的分析。
通过对生产流程的分析,可以找出其中存在的问题和瓶颈,并针对性地进行改进。
例如,可以通过优化工艺流程、改变物料搬运方式等方式来提高装配效率。
2.简化操作步骤其次,需要对操作步骤进行简化。
通过简化操作步骤,可以减少人力投入和时间成本,并且可以降低出错率。
例如,在组装过程中使用标准化零部件、预组合部件等方式来简化操作步骤。
3.优化物料供应链此外,还需要优化物料供应链。
通过优化物料供应链,可以确保物料及时到位,并且减少因为缺失物料而导致的停工现象。
例如,在与供应商对接时要求其按时交货,建立物料库存管理系统等方式来优化物料供应链。
三、提高员工技能1.培训员工员工是企业的重要资源,他们的技能水平直接影响到企业的生产效率和质量。
因此,需要通过培训来提高员工的技能水平。
例如,可以开展专业技术培训、安全生产培训、岗位职责培训等方式来提高员工技能。
2.激励员工除了培训之外,还需要通过激励机制来激发员工的积极性和创造力。
例如,可以通过设立奖金、晋升机制等方式来激励员工。
四、采用先进设备1.引进先进设备在现代化制造业中,先进设备是提高装配效率的关键因素之一。
因此,需要引进先进设备,并根据实际情况进行定制化改造。
例如,在自动化装配线上使用机器人等智能化设备。
2.维护保养设备除了引进先进设备之外,还需要及时维护保养现有设备。
通过定期检查和维护保养,可以确保设备始终处于最佳状态,并且延长其使用寿命。
五、优化管理模式1.建立科学的管理体系建立科学的管理体系是提高装配效率的关键。
通过建立科学的管理体系,可以实现生产过程的标准化和流程化,从而提高生产效率。
- 1、下载文档前请自行甄别文档内容的完整性,平台不提供额外的编辑、内容补充、找答案等附加服务。
- 2、"仅部分预览"的文档,不可在线预览部分如存在完整性等问题,可反馈申请退款(可完整预览的文档不适用该条件!)。
- 3、如文档侵犯您的权益,请联系客服反馈,我们会尽快为您处理(人工客服工作时间:9:00-18:30)。
白车身焊装生产线如何提升效率
2016-05-26 16:54
1. 焊装生产线概述
车身是构成汽车的主要组成部分,车身制造技术也是现代汽车工业的重要组成部
分,车身制造水平的优劣直接体现了一个国家汽车工业的水平。自1913年福特
汽车公司采用“流水线”生产方式以来,汽车生产线在汽车工业中占据了极其重要
的地位,它对提高生产效率,降低汽车成本起到了至关重要的作用,在大规模生
产方式下居于核心地位。
汽车白车身焊装生产线是把各车身冲压零件装配焊接成白车身的全部成形工位
的总称,它通常包含发动机舱、侧围、地板及车顶顶盖等焊接分总成线及最后合
装主焊生产线。根据生产节拍、自动化程度及生产方式等不同,主焊线及分总成
线又划分为若干工位,各工位通过各种类型输送装置连接为一体,每一工位负责
完成一部分工作。单工位一般由连接设备、焊装夹具、传输装置等几部分组成(见
图1)。
图1 焊装总拼工位
1.传输装置 2.焊接设备 3.车身焊装夹具
2 .焊装生产线问题
(1)工位故障率问题
每条白车身焊装流水线由若干工位组成,而每个工位完成车身的一道或几道工艺,
因此每个工位由若干设备组成,如图1所示。此工位为主焊接线的一个重要工艺
工位,其工艺流程为:车身由升降传输辊床运输到工位内部,到位之后,由车身
焊接定位夹具将车身侧围、顶盖横梁和车体主结构定位夹紧,然后机器人抓取点
焊焊枪对于车身进行点焊焊接。焊接结束之后,夹具打开,车身再由升降辊床运
输到下一个工位。整个工位的设备组成:机器人+点焊焊枪7台;左右侧围定位
车身焊接夹具两台;升降辊床传输装置1台。
单台设备对应的平均故障间隔时间,平均修复间隔时间,以及可利用率参数如表
1所示。
以上这些设备构成了一个可修复系统。虽然这些设备都是独立不相关,发生故障
的概率也没有联系,但是当其中任何一个设备发生故障时,整个系统将要停机用
于修复,所以为了保障整条生产线效率,不仅在设计过程中就要为此工位留出修
复的时间,同时在生产过程中,还要安排维修人员进行维护和及时修复。
(2)暂存区域问题
白车身焊装车间最主要的问题在于每条生产线中,设备随机的故障而导致的停产,
比如焊接设备中的机器人故障、车身焊装夹具中气缸的故障,传输装置中升降传
输辊床故障,这些设备造成整条生产线停产而导致线效率的下降。为了避免整个
生产系统全部停产瘫痪,在关键工位之间、每条线体之间增加暂存区域,这样可
以有效地降低部分系统产生问题对于整个系统的影响。因此,每个生产系统之间,
例如地板总线和主焊接线之间就要设置暂存区域,但地板总线因故障而导致停产
时,主焊接线还是利用暂存区域里的储备物料进行生产。
但是暂存区域的数目以及每个暂存区域的容量也不是越大越好,它会造成以下几
点问题:①暂存区域会造成投资成本、生产运营成本、维修成本上升。②暂存区
域会占用生产工位的操作空间。③暂存区域没有生产活动,会产生空闲时间,并
且在生产预热过程中,需要填满所有的这些暂存区域才能使得生产系统工作,从
而导致整体的生产效率下降。
所以,焊装车间的设计以及布置的目标之一就是最小化暂存区域。
(3)生产时间变动影响
在高度自动化的白车身焊装车间,每个工位,每条生产线的期望的生产节拍是恒
定的,但是这是无法满足的。假定生产安排JPH=60,设计要求的生产线效率为
85%,那么生产节拍为:
因此每个工位、每条生产线的节拍要求都不能超过Tmax=51s,否则就会产生瓶
颈工位。另外,在不超过指定节拍前提下,要求生产活动尽量用足指定节拍,从
而减少生产设备、工位以及操作工人。另外一个与节拍相关的目标是尽量均衡每
个工位之间的生产时间。当每个工位之间生产时间都均衡的条件下,也可以降低
暂存区的数目。
(4)焊装生产线目标函数
综上所述,白车身焊装生产线是一个多目标优化问题,需要考虑的目标包含:①
最小化暂存区容量。②最大化每个工位生产时间。③最小化每个工位生产时间之
间的差异。④生产必须满足JPH要求,从而满足每天N辆车的目标。
但是上述设定目标和现实之间还有冲突,例如,由于每个设备存在着不同的可利
用率,上述第3项就和生产时间最大满足节拍要求冲突。因为可利用率是一个随
机的波动值,如果不留余量的话很容易造成瓶颈工位。
3. 车身总拼线建模分析
(1)仿真平台
Tecnomatix公司的数字化工厂软件Plant Simulation是一款完全采用面向对象方
法的仿真软件,它构建了一个完整的工厂,从生产线、加工单元到工序操作的所
有层次进行设计、物流仿真和优化的集成计算机环境。面向白车身的解决方案主
要解决白车身焊装生产线的工艺规划、焊装生产线的布局等问题,同时应用物流
仿真模块对整个生产线进行物流分析和优化。
(2)实例车身仿真模拟
某工厂建立的焊装车间,规划设计的产能是JPH=60,进行车间生产线的平面布
置和设备的选取。每条生产线根据工艺需求分为若干工位,如图2所示,其焊装
主线由13个工位串联组成,焊接车身地板总成和侧围内板以及顶盖横梁。
图2 车身主线
注:①为Afo4100 Lifter,②为Afo4110 Manual sealling,③为Afo4120 Manual
Loading & Tab,④为Afo4130 Manual Loading & Tab,⑤为Afo4135,⑥为Afo4140
Framing inner Geo,⑦为Afo4150 Auto Re-spot,⑧为Afo4160 Auto Re-spot,⑨
Afo4170 Auto Re-spot,⑩为Afo4175 Auto Re-spot,⑪为Afo4180 Man Repair,
⑫为Afo4185 Inline Measuring,⑬为Afo4190 Lifter。
焊装主线上每个工位的可利用率、失效间隔平均时间、维修间隔平均时间,具体
参数如表2所示。
从数据上分析,4140工位的可利用率相对较低,并且MTBF间隔时间最短,因
此4140为瓶颈工位,那么从Plant Simulation环境下对其进行建模仿真研究,并
且验证解决方案对于提升生产线效率的有效性。
将4140工位和4130、4150工位串联起来组成一个分系统,建立仿真模型,根据
表3输入参数(见图3)。
图3
经过系统的仿真,输出这个分系统的效率为96.08%。从理论上而言,如果是独
立系统的效率达到96.08%的话,这个系统的生产率还是很高的,也不用产生额
外的成本去优化处理。但这个分系统只是串联系统中的一部分,所以对于这个分
系统的优化还是必要的。
优化方法一:改变部分工艺顺序,缩短4140工位实际的加工活动时间,将原本
51s的加工时间缩短至49s,仿真结果如图4所示。
图4 4140瓶颈工位优化仿真一
通过优化仿真,分系统的生产效率提升至96.28%,相对原来系统生产率提升了
0.2%。
优化方法二:在瓶颈工位4140前后增加暂存工位,各增加两个串联的暂存工位,
仿真结果如图5所示。
图5 4140瓶颈工位优化仿真二
通过优化仿真,分系统的生产效率提升至96.34%,相对原来系统生产率提升了
0.26%。
优化方法三:在生产线上增加一个并联的4140工位,由于生产线的节拍保持51s
不变,理论上单个4140工位生产节拍可以做到102s,但为了防止可利用率的波
动造成效率影响,将单个4140工位生产节拍提升到90s,仿真结果如图6所示。
图6 4140瓶颈工位优化仿真三
通过优化仿真,分系统的生产效率提升至96.72%,相对原来系统生产率提升了
0.64%。
综合上述三种优化方法,生产线效率的提升随着方法是递增的,但是同时加工成
本也是随着方法递增的。在实际的生产活动中,必须综合考虑各方面的因素而选
择布置操作工位,解决瓶颈工位的问题。
(3)生产线仿真模拟
根据表3建立主线1的模型,如图7所示,通过仿真模拟,整条生产线的效率为
91.96%,满足规划设计85%的设计要求。
从仿真结果来看,工位4100,4135(暂存工位)产生空闲时间,可以安排工作
内容,以均衡整条生产线之间每个工位生产节拍;另外,工位4140、4150为瓶
颈工位,规划设计以及实际生产活动中,都应该着重提高这两个工位的效率,避
免瓶颈的出现。
图7 主线1仿真模型
4. 结语
白车身焊装生产线系统是一种典型的离散系统,受随机因素影响较大,离散系统
仿真算法较多,其中面向对象的仿真方法更符合生产线的实际情况。Plant
Simulation具有丰富的建模单元,能够模拟生产系统中的各种加工单元,再加上
软件本身强大的实验分析、遗传算法等功能,可清楚地看出系统的瓶颈所在,并
且结合生产经验仿真解决措施,从而提升生产线效率。
该研究对于汽车生产企业的生产线效率提升具有较强的参考价值。
本文刊登于《金属加工(热加工)》2012年22期