PDC钻头布齿设计技术
一种pdc钻头布齿算法
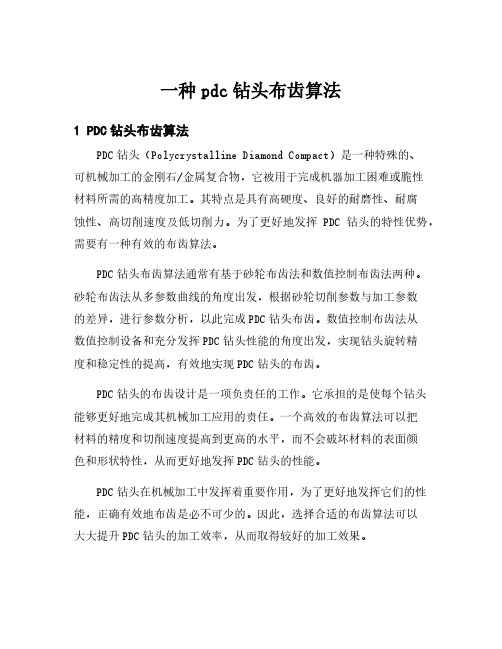
一种pdc钻头布齿算法
1 PDC钻头布齿算法
PDC钻头(Polycrystalline Diamond Compact)是一种特殊的、
可机械加工的金刚石/金属复合物,它被用于完成机器加工困难或脆性
材料所需的高精度加工。
其特点是具有高硬度、良好的耐磨性、耐腐
蚀性、高切削速度及低切削力。
为了更好地发挥PDC钻头的特性优势,需要有一种有效的布齿算法。
PDC钻头布齿算法通常有基于砂轮布齿法和数值控制布齿法两种。
砂轮布齿法从多参数曲线的角度出发,根据砂轮切削参数与加工参数
的差异,进行参数分析,以此完成PDC钻头布齿。
数值控制布齿法从
数值控制设备和充分发挥PDC钻头性能的角度出发,实现钻头旋转精
度和稳定性的提高,有效地实现PDC钻头的布齿。
PDC钻头的布齿设计是一项负责任的工作。
它承担的是使每个钻头能够更好地完成其机械加工应用的责任。
一个高效的布齿算法可以把
材料的精度和切削速度提高到更高的水平,而不会破坏材料的表面颜
色和形状特性,从而更好地发挥PDC钻头的性能。
PDC钻头在机械加工中发挥着重要作用,为了更好地发挥它们的性能,正确有效地布齿是必不可少的。
因此,选择合适的布齿算法可以
大大提升PDC钻头的加工效率,从而取得较好的加工效果。
PDC钻头布齿设计技术

第26卷第3期2003年6月 勘探地球物理进展Progress in Exploration G eophysicsV ol.26,N o.3Jun.,2003文章编号:167128585(2003)0320225203PDC钻头布齿设计技术刘建风(成都理工大学环境与土木工程学院,四川成都610059)摘要:合理的布齿是保证PD C钻头具有优良工作性能的关键。
目前常用的PD C钻头布齿设计方法是图解调整法,该方法速度慢,设计工作烦琐,工作量大,效率低,欠灵活,而且有时会出现不必要的误差。
讨论了PD C钻头布齿设计的特点,按切削原则设计了钻头冠部形状,并选择了合理的切削结构,为PD C钻头布齿计算机辅助设计软件提供了理论支撑。
关键词:PD C钻头;布齿;结构设计中图分类号:P63414 文献标识码:AComputer2aided placement of tooth for PDC bitLiu Jianfeng(C ollege of Environment and Civil Engineering,Chengdu University of T echnology,Chengdu610059,China)Abstract:Proper placement of tooth is the key to ensure the performance of PDC bit.The comm only used method for placement of tooth for PDC bit is to draw and adjust the scheme.It is boring and inefficient,s ometimes even leads to errors.This paper discusses the principle and the way to place teeth for PDC bit,which provide a theoretical ground for placement of tooth for PDC bit by the C omputer2aided design.K ey w ords:PDC bit;tooth placement;structural design PDC钻头(P olycrystalline Diam ond C om pact Bit)用人造聚晶金刚石复合片作为切削元件以切削方式破碎岩石。
煤矿复杂硬地层用胎体式PDC钻头的研制
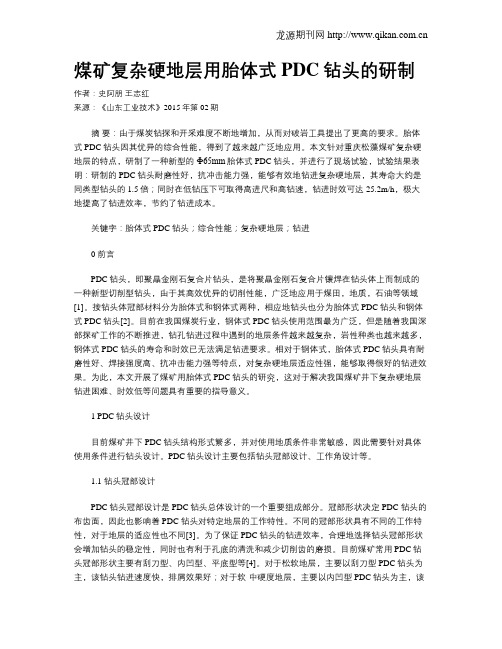
煤矿复杂硬地层用胎体式PDC钻头的研制作者:史阿朋王志红来源:《山东工业技术》2015年第02期摘要:由于煤炭钻探和开采难度不断地增加,从而对破岩工具提出了更高的要求。
胎体式PDC钻头因其优异的综合性能,得到了越来越广泛地应用。
本文针对重庆松藻煤矿复杂硬地层的特点,研制了一种新型的Ф65mm胎体式PDC钻头,并进行了现场试验,试验结果表明:研制的PDC钻头耐磨性好,抗冲击能力强,能够有效地钻进复杂硬地层,其寿命大约是同类型钻头的1.5倍;同时在低钻压下可取得高进尺和高钻速,钻进时效可达25.2m/h,极大地提高了钻进效率,节约了钻进成本。
关键字:胎体式PDC钻头;综合性能;复杂硬地层;钻进0 前言PDC钻头,即聚晶金刚石复合片钻头,是将聚晶金刚石复合片镶焊在钻头体上而制成的一种新型切削型钻头,由于其高效优异的切削性能,广泛地应用于煤田,地质,石油等领域[1]。
按钻头体冠部材料分为胎体式和钢体式两种,相应地钻头也分为胎体式PDC钻头和钢体式PDC钻头[2]。
目前在我国煤炭行业,钢体式PDC钻头使用范围最为广泛,但是随着我国深部探矿工作的不断推进,钻孔钻进过程中遇到的地层条件越来越复杂,岩性种类也越来越多,钢体式PDC钻头的寿命和时效已无法满足钻进要求。
相对于钢体式,胎体式PDC钻头具有耐磨性好、焊接强度高、抗冲击能力强等特点,对复杂硬地层适应性强,能够取得很好的钻进效果。
为此,本文开展了煤矿用胎体式PDC钻头的研究,这对于解决我国煤矿井下复杂硬地层钻进困难、时效低等问题具有重要的指导意义。
1 PDC钻头设计目前煤矿井下PDC钻头结构形式繁多,并对使用地质条件非常敏感,因此需要针对具体使用条件进行钻头设计。
PDC钻头设计主要包括钻头冠部设计、工作角设计等。
1.1 钻头冠部设计PDC钻头冠部设计是 PDC钻头总体设计的一个重要组成部分。
冠部形状决定PDC 钻头的布齿面,因此也影响着 PDC 钻头对特定地层的工作特性。
分析PDC钻头内镶式二级齿新技术

分析PDC钻头内镶式二级齿新技术摘要:常规PDC钻头主要适用于钻进软到中硬程度的均质地层,而对于某些地区地层硬夹层多、软硬悬殊或者可钻性差的地层,常规PDC钻头难以发挥有效的作用,且容易加剧PDC齿的磨损速度,甚至造成冲击损坏,严重影响到PDC钻头的正常使用寿命。
本文提出了一种基于PDC钻头的内镶式二级齿新技术,通过该技术的有效应用,能显著提升PDC钻头的适用范围以及在难钻地层中工作时的使用寿命。
关键词:PDC钻头内镶式二级齿新技术应用PDC钻头是聚晶金刚石复合片钻头的简称,也是当前石油钻井行业中所经常使用到的一种钻井工具。
内镶式二级齿新技术,即是在常规PDC钻头的切削结构的基础上,再另行添加后备的切削结构,并使二级齿能处于主切削齿的上方。
通过二级齿与主切削齿的配合使用,以构建出能够连续工作的复合切削结构。
经过工程实践证明,PDC钻头内镶式二级齿新技术的应用,钻头工作平稳,可钻范围和使用寿命增加,能显著提升钻井的整体经济效益。
一、PDC钻头的损坏机理PDC钻头在实际工作过程中的损坏,主要表现为切削齿的损坏。
根据现场实际统计资料显示,切削齿损坏主要表现为磨损破坏和冲击破坏这两种主要形式。
1.切削齿磨损破坏机理PDC切削齿的磨损机理主要受到PDC片以及合金基体磨损机理的影响。
其中,PDC切削齿的使用材料和内部结构是决定了切削齿磨损方式的内部因素;而切削齿的工作环境、切削面所产生的摩擦热效果以及冲击性荷载的大小,是决定切削齿磨损机理的外部因素。
2.切削齿冲击破坏机理大量现场统计资料表明,由冲击荷载所引发的切削齿碎裂是引发PDC钻头过早失效的主要因素。
由于抗冲性能差是金刚石材料固有的缺点,虽然PDC复合片在耐冲性能上有所改善,但是在受到冲击荷载时,仍然较容易碎裂。
根据冲击荷载的作用方式,还可将PDC切削齿的损坏形式主要划分为,因钻头轴向冲击荷载所引发的剥落以及因水平方向冲击荷载所引发的崩刃(如下图1和下图2所示)。
pdc钻头设计方法及软件编制
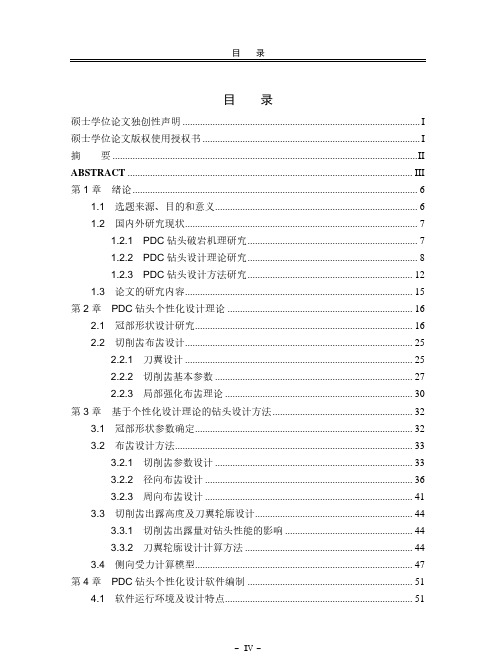
目录硕士学位论文独创性声明 (I)硕士学位论文版权使用授权书 (I)摘要 .......................................................................................................................... I I ABSTRACT (III)第1章绪论 (6)1.1选题来源、目的和意义 (6)1.2国内外研究现状 (7)1.2.1PDC钻头破岩机理研究 (7)1.2.2PDC钻头设计理论研究 (8)1.2.3PDC钻头设计方法研究 (12)1.3论文的研究内容 (15)第2章PDC钻头个性化设计理论 (16)2.1冠部形状设计研究 (16)2.2切削齿布齿设计 (25)2.2.1刀翼设计 (25)2.2.2切削齿基本参数 (27)2.2.3局部强化布齿理论 (30)第3章基于个性化设计理论的钻头设计方法 (32)3.1冠部形状参数确定 (32)3.2布齿设计方法 (33)3.2.1切削齿参数设计 (33)3.2.2径向布齿设计 (36)3.2.3周向布齿设计 (41)3.3切削齿出露高度及刀翼轮廓设计 (44)3.3.1切削齿出露量对钻头性能的影响 (44)3.3.2刀翼轮廓设计计算方法 (44)3.4侧向受力计算模型 (47)第4章PDC钻头个性化设计软件编制 (51)4.1软件运行环境及设计特点 (51)4.2软件介绍 (52)4.3软件设计实例 (59)第5章结论及展望 (64)参考文献 (65)致谢 (67)第1章绪论1.1选题来源、目的和意义随着金刚石复合材料的发展,PDC钻头问世并兴起,直到今天设计理论和技术仍在不断完善。
1978年L.E.HIBBS指出,无论新钻头采用何种形式,其设计都需要从一些基本的准则入手,并指出钻头布齿设计在理论上应当遵循等切削、等磨损和等功率三个原则[1]。
PDC 钻头自动优化布齿设计软件平台建立

PDC 钻头自动优化布齿设计软件平台建立田红平;杨春雷【摘要】在 PDC 钻头产品结构中,布齿结构设计至关重要,直接影响 PDC 钻头的使用性能和寿命。
利用 PDC 钻头切削力学分析程序计算钻头不平衡力和径向力/周向力比值,调整 PDC 钻头布齿结构,直到钻头力平衡与功力满足要求为止。
采用人工探索的方式进行布齿结构设计,存在设计效率低、设计质量不稳定等缺点。
利用 MDO 方法建立 PDC 钻头自动优化布齿设计平台,实现布齿结构自动优化设计,布齿结构设计时间仅为原来的1/16~1/8,其中人工干预时间仅为原来的1/96~1/48,布齿结构设计质量提高3~5倍,大幅降低了产品开发成本,提高了产品设计可靠性。
%Among the structure of PDC bits,design of cutter arrangement is vital,which will di-rectly affect the application performance and service life of PDC bits.Mechanical analysis proce-dure for cutting structure of PDC bits is utilized to calculate the unbalanced force and radial force/circumferential force ratio of bits,cutter arrangement of PDC bits is adjusted,until force balance and power as well as cutting force ofbits can meet the requirements.Disadvantages like low de-sign efficiency and unstable design quality normally exist when design cutter arrangement with ar-tificial research e MDO method to set up automatic optimization design platform for cutter arrangement of PDC bits,and realize automatic optimization design for cutter arrangement, the cutter arrangement design time is only 1/16 ~1/8 ofprevious,wherein,artificial intervention time is only 1/96~1/48 of previous,but cutter arrangement design quality is 3~5 times of previ-ous,which dramatically decrease product development cost and enhance product design reliability.【期刊名称】《石油矿场机械》【年(卷),期】2015(000)011【总页数】5页(P22-26)【关键词】MDO;优化设计;PDC 钻头;布齿结构【作者】田红平;杨春雷【作者单位】江汉石油钻头股份有限公司,武汉 430223;江汉石油钻头股份有限公司,武汉 430223【正文语种】中文【中图分类】TE921.102在PDC钻头设计过程中,布齿设计至关重要,直接影响PDC钻头的使用性能和寿命。
基于Pro_E的PDC钻头三维参数化布齿设计
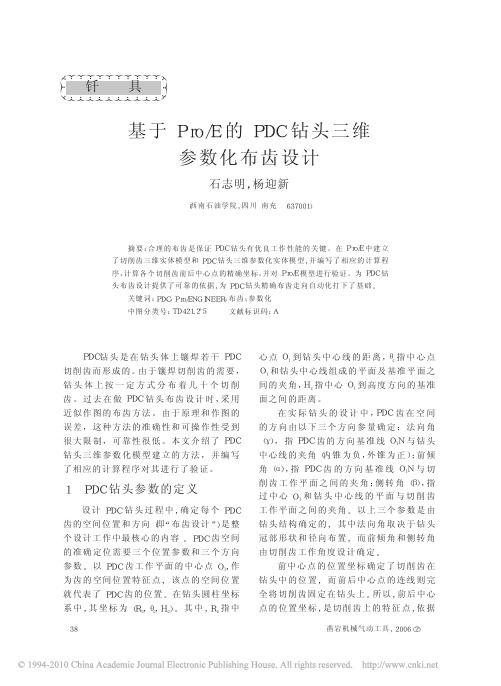
!!!!!!!!!!"!"!!!!!!!!!!"!"钎具PDC钻头是在钻头体上镶焊若干PDC切削齿而形成的。
由于镶焊切削齿的需要,钻头体上按一定方式分布着几十个切削齿。
过去在做PDC钻头布齿设计时,采用近似作图的布齿方法。
由于原理和作图的误差,这种方法的准确性和可操作性受到很大限制,可靠性很低。
本文介绍了PDC钻头三维参数化模型建立的方法,并编写了相应的计算程序对其进行了验证。
1PDC钻头参数的定义设计PDC钻头过程中,确定每个PDC齿的空间位置和方向(即“布齿设计”)是整个设计工作中最核心的内容。
PDC齿空间的准确定位需要三个位置参数和三个方向参数。
以PDC齿工作平面的中心点O1,作为齿的空间位置特征点,该点的空间位置就代表了PDC齿的位置。
在钻头圆柱坐标系中,其坐标为(Rc,θc,Hc)。
其中,Rc指中心点O1到钻头中心线的距离,θc指中心点O1和钻头中心线组成的平面及基准平面之间的夹角,Hc指中心O1到高度方向的基准面之间的距离。
在实际钻头的设计中,PDC齿在空间的方向由以下三个方向参量确定:法向角(γ),指PDC齿的方向基准线O1N与钻头中心线的夹角(内锥为负,外锥为正);前倾角(α),指PDC齿的方向基准线O1N与切削齿工作平面之间的夹角;侧转角(β),指过中心O1和钻头中心线的平面与切削齿工作平面之间的夹角。
以上三个参数是由钻头结构确定的,其中法向角取决于钻头冠部形状和径向布置,而前倾角和侧转角由切削齿工作角度设计确定。
前中心点的位置坐标确定了切削齿在钻头中的位置,而前后中心点的连线则完全将切削齿固定在钻头上。
所以,前后中心点的位置坐标,是切削齿上的特征点,依据基于Pro/E的PDC钻头三维参数化布齿设计石志明,杨迎新(西南石油学院,四川南充637001)摘要:合理的布齿是保证PDC钻头有优良工作性能的关键。
在Pro/E中建立了切削齿三维实体模型和PDC钻头三维参数化实体模型,并编写了相应的计算程序,计算各个切削齿前后中心点的精确坐标,并对Pro/E模型进行验证。
PDC钻头模具三维设计和数控加工技术研究与应用

PDC钻头模具三维设计和数控加工技术研究与应用摘要本文对PDC钻头模具三维设计和数控加工一体化技术的方法、步骤和相关工艺技术进行了研究。
解决了PDC钻头模具辅助设计二维数据的三维转化问题,提出了模具三维造型和参数化开发的方法,并应用CAD/CAM系统软件PRO/E建立了PDC钻头模具三维模型,应用PRO/PROGRAM(程序)开发模块进行PDC钻头模具造型的参数化开发,并编制了相应的参数化开发软件,提高了PDC钻头模具造型速度和准确性。
在建立PDC钻头模具三维造型的根底上,确定了模具数控加工工艺,摸索出一套利用PRO/E软件进行PDC钻头模具计算机辅助制造的方法和步骤,实现了PDC钻头模具一次装卡、一次成形的高精度自动化数控加工技术。
关键词 PDC钻头模具三维设计数控加工技术 CAD/CAM 聚晶金刚石复合片钻头(简称PDC钻头)由钻头体、接头组成,根据钻头体按材料的不同分为胎体PDC钻头和钢体PDC钻头。
胎体PDC钻头的钻头体是采用铸造碳化钨粉和浸渍料经无压浸渍烧结而成的。
钻头体形状是通过模具的形状而间接实现的。
模具由底模、中模和上模三局部组成。
模具的中模和上模的设计与加工都很容易实现。
但底模是具有复杂曲面特征的实体,PDC钻头的冠部形状参数、切削齿位置和方向参数、水力结构参数等都是通过底模的形状来实现的。
因此底模的设计和加工是模具设计和加工中最重要的一局部,其设计的好坏和加工的精度都直接关系到钻头的最终使用效果。
高质量的模具是保证PDC钻头质量的关键因素之一。
目前国内PDC钻头模具的形成主要有三种方法。
第一种(应用最多的,如以下列图)是利用普通车床车削形成钻头冠部形状,依靠分度头手工划线定位、普通万能铣床铣削完成切削齿和水眼的加工,再通过手工修模完成水力结构的造型等多道工序完成的。
这种加工方法的缺点是工人劳动强度大、加工精度低、人为误差大,难以控制和保证质量,很难到达设计的要求。
第二种是数控加工,利用数控机床加工形成钻头的冠部形状和切削齿的定位,然后再通过手工修模或者粘上相应形状成形的水力结构(粘上以后也要进行一定的手工修理)而最后形成模具的。
- 1、下载文档前请自行甄别文档内容的完整性,平台不提供额外的编辑、内容补充、找答案等附加服务。
- 2、"仅部分预览"的文档,不可在线预览部分如存在完整性等问题,可反馈申请退款(可完整预览的文档不适用该条件!)。
- 3、如文档侵犯您的权益,请联系客服反馈,我们会尽快为您处理(人工客服工作时间:9:00-18:30)。
第26卷第3期2003年6月 勘探地球物理进展Progress in Exploration G eophysicsV ol.26,N o.3Jun.,2003文章编号:167128585(2003)0320225203PDC钻头布齿设计技术刘建风(成都理工大学环境与土木工程学院,四川成都610059)摘要:合理的布齿是保证PD C钻头具有优良工作性能的关键。
目前常用的PD C钻头布齿设计方法是图解调整法,该方法速度慢,设计工作烦琐,工作量大,效率低,欠灵活,而且有时会出现不必要的误差。
讨论了PD C钻头布齿设计的特点,按切削原则设计了钻头冠部形状,并选择了合理的切削结构,为PD C钻头布齿计算机辅助设计软件提供了理论支撑。
关键词:PD C钻头;布齿;结构设计中图分类号:P63414 文献标识码:AComputer2aided placement of tooth for PDC bitLiu Jianfeng(C ollege of Environment and Civil Engineering,Chengdu University of T echnology,Chengdu610059,China)Abstract:Proper placement of tooth is the key to ensure the performance of PDC bit.The comm only used method for placement of tooth for PDC bit is to draw and adjust the scheme.It is boring and inefficient,s ometimes even leads to errors.This paper discusses the principle and the way to place teeth for PDC bit,which provide a theoretical ground for placement of tooth for PDC bit by the C omputer2aided design.K ey w ords:PDC bit;tooth placement;structural design PDC钻头(P olycrystalline Diam ond C om pact Bit)用人造聚晶金刚石复合片作为切削元件以切削方式破碎岩石。
它结构简单,无运动部件,整个钻头是一个整体,在软到中等硬度均质地层中破岩能力强、钻速高(为牙轮钻头的2倍以上)、进尺快(为牙轮钻头的4~6倍)、工作寿命长、钻进成本低、事故少,因此倍受业内人士的关注。
我国的PDC钻头生产技术与国外先进水平相比有很大差距,尤其是在设计方面。
所以开展PDC 钻头设计技术方面的研究是一项极有意义的工作[1~3]。
PDC钻头设计分为前期准备、布齿设计、工作性能分析和其他部分设计等阶段[4]。
其中最重要的是布齿设计。
在进行PDC钻头布齿设计时,应先根据资料和经验确定钻头总体结构、布齿方式、喷嘴大小和数目等,然后对钻头冠部形状和切削结构进行设计。
1 钻头冠部形状设计PDC钻头的冠部形状从长抛物线型到平底型共分成9个等级。
冠部形状决定了PDC的布齿面,不同的冠部形状其切削齿相对高差和切削齿轴线与钻头轴线间的夹角也不相同,从而影响各切削齿的切削体积,导致各齿破岩能力不一样;另外,不同冠部形状还会使切削齿受力情况不同。
因而,一个合理的冠部形状会增加钻头的稳定性,利于井底的清洗及减小切削齿的磨损[5]。
从设计上讲,无论何种冠部形状,最终都以“易于布齿、便于加工、保证质量、提高效率”为原则。
为了提高效率,理论上可按以下几种原则设计:①按等切削原则;②按等磨损原则;③按等功率原则。
本文按“等切削原则”设计冠部形状。
设钻头半径为R,切削齿半径为r,钻头每转进尺为δ,切削齿总数为N,一般地,δ<r,则钻头每转的破岩体积V为V=πR2δ 按等切削原则,各齿每转破碎岩石体积V为V=V/N=πR2δ/N设第i个齿的旋转半径(切削齿工作面中心到钻头轴线的距离)为x i,切削面积为S i,则有V=2πx i S i,即S i=R2δ2Nx i(1)收稿日期:20021225。
作者简介:刘建风(1977),男,成都理工大学硕士在读,研究方向为岩土钻掘设计与工程施工。
这说明要实现等切削,就要求切削齿尽量靠近钻头中心,离钻头中心越近,其切削面积越大。
但钻头中心部分的切削齿无法达到这一要求,存在一个最小旋转半径,只有旋转半径大于这个最小旋转半径的切削齿才能实现等切削。
这主要取决单个切削齿最大切削面积,即无其他齿干扰时单齿最大切削面积S max (图1中的阴影部分),其计算式为 S max =(π-2arccos δ2r )r 2+δ24r 2-δ2 (2)将式(2)代入式(1)获得对应的最小旋转半径为x min =R 2·δ2N ·(π-2arccos δ2r )r 2+δ24r 2-δ2(3) 一般情况下,PDC 钻头冠部形状轮廓线主要由内锥面、顶部圆弧面和保径面三部分组成(如图2),内锥面和顶部圆弧面以x =x min 为分界线,当x i >x min 时,切削齿等切削。
应用文献1中按等切削原则设计冠部形状轮廓线得到理论冠部曲线的一般方程式为Z =x min2ln (x +x 2-x 2min )-x 2x minx 2-x 2min +c(4)式中,c 是保径环长度,为常数,这时钻头冠部形状轮廓线由多段近似圆弧的曲线组成;当x i ≤x min 时,切削齿不能等切削,钻头冠部形状轮廓线是过(x min ,x min2ln xmin +c )点的直线,其方程式为Z =tg φ(x -x min )+x min2ln x min +c (5)式中,φ为直线倾角,采用类比法确定。
图1 单切削齿最大切削面积图2 钻头冠部形状轮廓线2 切削结构设计切削结构设计主要是确定切削齿空间的位置,包括切削齿的选择、布齿密度、切削齿的结构角以及切削齿中心的周向、径向布置。
2.1 切削齿的选择包括齿的大小和大概数目,主要由所钻地层岩性的特点来决定。
2.2 布齿密度主要由所钻地层的硬度和研磨性来决定。
2.3 切削齿的结构角切削齿最重要的两个结构角是齿前角(见图3)和侧转角(见图5)。
和其他切削刀具一样,PDC 切削齿结构角对切削齿的切削效率和工作性能有重要影响。
齿前角决定切削齿作用于地层力的方向,合理的齿前角能提高切削效率、保护切削齿、延长钻头的寿命,有助于提高钻速。
侧转角决定齿前切屑的排屑力的方向,反映工作面方向与切削齿对齿前切削侧向作用力的大小及方向之间的关系。
合理的侧转角有利于钻头清洗和岩屑搬移,减少钻头泥包发生几率。
PDC 钻头切削结构由若干个分布在钻头表面不同部位的切削齿组成,每个切削齿的空间方位和工作部位都不同,所以各切削齿的齿前角和侧转角也不同。
由于要保持切削齿良好的工作性能,须控制切削齿在工作过程中的磨损,使切削齿磨损降为最小。
因此,以切削齿磨损最小为目标对切削齿齿前角和侧转角进行优化,确定各齿结构角大小。
如图4中,a ,b ,c 为切削齿齿刃在井底半径平面内留下的切痕轮廓线;d ,e ,f 为切削齿磨损一段时间后齿刃在井底半径平面内留下的切痕轮廓线。
a ,c ,d ,f 分别是切削齿与井底接触区的内、外端点;b ,e 分别为切痕轮廓线的中点;ad 和cf 分别为接触区的内、外端点处两轮廓线的间隙;be 为切削齿齿刃的磨损量。
设h w 1=|ad |,h w 2=|df |,h w 3=|b e |,进行优化的数学模型为设计变量X =[α,β]T(6)目标函数min F (X )=|hw1-h w2|(7)约束条件α1≤α≤α2;β1≤β≤β2;|h w 3-h w |<ε(8)622勘探地球物理进展 第26卷式中,α,β,ε,h w 分别为齿前角、侧转角、一假定为很小的数值、切削齿允许磨损高度。
通过上述优化计算,即可求得钻头上各齿的齿前角和侧转角。
2.4 切削齿的周向布置切削齿的周向布置是在垂直于钻头轴线平面内按一定方式确定切削齿的周向位置角(见图5),得到周向布置图。
切削齿在钻头表面有螺旋形、翼片形和随意等三种布置方式[6],随意布齿在齿的清洗和冷却方面容易出问题,一般用得较少;翼片形布齿实际上是螺旋形布齿的一种特例,故本文只讨论最常用的螺旋形。
图5 切削齿的周向布置示意图螺旋形布置是使每个切削齿工作面的圆心位于数条螺旋线上,而这些空间螺旋线在垂直于钻头轴线平面内的投影是数条平面螺旋线,因此,可结合钻头冠部形状,在垂直于钻头轴线平面内对钻头切削齿进行周向布置设计。
螺旋形的布齿基线有等距螺旋线和变距螺旋线之分,这两种布齿方式都与相应的水力结构相配合,其基线在垂直于钻头平面内的极坐标形式分别是r =a θ+θ0 (9)r =a (θ+θ0)n(0<n <1)(10) 在进行周向布齿时,先用螺旋线方程确定切削齿工作面圆心位置,再根据切削齿侧转角的大小确定齿的方向。
由于切削齿周向布置的特点是:越往钻头外侧,切削齿径向密度越大。
因此,利用等距螺旋线方式布齿时,越向外侧同一螺旋线上相邻切削齿之间切向坐标θ的差越小;利用变距螺旋线布齿时,因为0<n <1,随着r 增大螺旋线的径向间距越小。
所以,即使螺旋线上相临切削齿之间分布角θ间距相同,但越靠近钻头外侧,切削齿的径向密度也越高。
变距螺旋线控制每个切削齿的径向坐标各不相同,使得钻头外侧切削齿排列密度高于钻头内侧,利用等分布角θ分布的等螺旋线控制同一变距螺旋线上相临两切削齿θ的间距相等。
2.5 切削齿的径向布置切削齿径向布置是在钻头半径平面内沿冠部外形轮廓布置切削齿,确定中心齿、保径齿和其他各齿的径向位置,得到径向布齿图(图6),它反映切削齿的分布密度和在井底的覆盖情况。
设计重点是使切削齿能完全覆盖井底。
确定中心齿位置的原则是使中心齿处于切掉中心岩石的最有利位置;确定保径齿位置的原则是保证保径齿工作面超出规径线部分与加工要求磨削量相等。
在确定中心齿和保径齿的位置时,把切削齿与井底半径平面相交的图形视为圆。
确定了冠部形状、中心齿和保径齿的位置后,所有切削齿中心的连线就确定了,它是冠部曲线的等距线,两曲线间距为齿中心出露高度(见图3),它等于切削齿半径乘以齿出露系数,出露系数通常采用类比法确定。
最后,根据由周向布置得到的各齿旋转半径x i ,确定各齿工作面圆心在径向布置图上的具体位置。
图6 径向布置示意图3 结束语通过探讨PDC 钻头布齿设计的特点,得到确定钻头冠部形状和切削结构的方法,以及PDC 钻头布齿设计所需的基本参数和各参数的计算方法,为我们利用Visual C ++和Visual Lisp (AutoC AD 2000中)语言编制PDC 钻头的布齿计算机辅助设计软件提供理论支撑。