PDC钻头切削齿定位点测量研究
锚杆PDC钻头主要几何参数的研究

式中
j=1
nd— ——设计组数; φ(j)— ——与第 j 组设计相关的权重; f (j)— ——第 j 组设计对应的有限元计算值; f^ (j) — ——第 j 组设计对应的近似值。
Σ Σ Σ
ΣΣ ≤ Σ Σ
ΣΣ Σ
minf(X)=f(x1,x2,…,xn)
按最小二乘原理, 未知量应使得 E2 取极小值,
②侧转角的优化结果 侧转角对钻头的切削性能有较大的影响,调整 侧转角度,可加强钻头清洗效果,提高钻进效率,合
[1]唐胜利,王永强等. 煤矿井巷用 PDC 锚杆钻头的研究[J]. 探矿工 程 ,1999 (2 ):20-22.
LIU Xiang-dong, QU Jun-li (College of Science, Xi ’an University of Science & Technology, Xi ’an 710054, China)
Abstract: PDC cutter intensity has a higher demand because of the small diameter and unique way of placing cutting, and the working angles of the cutter have an important influence on the cutting efficiency and performance. And therefore the proper design of the cutter on the cutting angle and the side angle is very important in the design of PDC bits. Based on finite element soft ware ANSYS, the cutting angle and the side angle of the PDC cutter are optimized. Applications from different considerations, the main geometric parameters of the two separate single -parameter and two -parameter optimization analysis, obtained the optimal values under different the circumstances of its use, which provides a theoretical basis for rational design of the PDC bit. Key words: PDC bit; optimization; finite element; ANSYS
双级PDC钻头的理论及试验研究
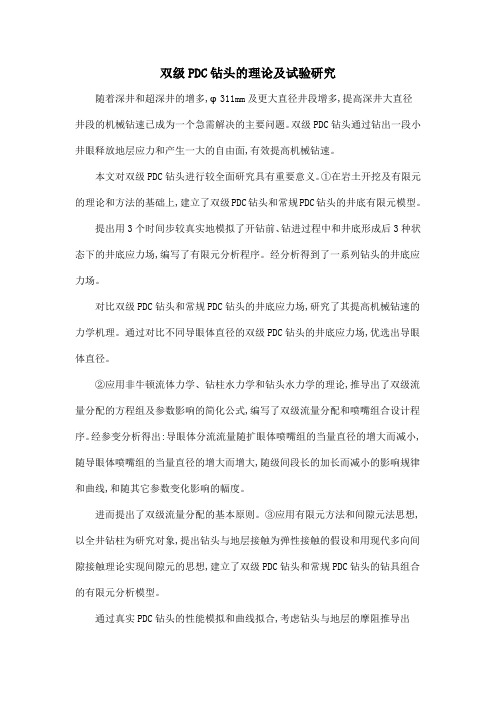
双级PDC钻头的理论及试验研究随着深井和超深井的增多,φ311mm及更大直径井段增多,提高深井大直径井段的机械钻速已成为一个急需解决的主要问题。
双级PDC钻头通过钻出一段小井眼释放地层应力和产生一大的自由面,有效提高机械钻速。
本文对双级PDC钻头进行较全面研究具有重要意义。
①在岩土开挖及有限元的理论和方法的基础上,建立了双级PDC钻头和常规PDC钻头的井底有限元模型。
提出用3个时间步较真实地模拟了开钻前、钻进过程中和井底形成后3种状态下的井底应力场,编写了有限元分析程序。
经分析得到了一系列钻头的井底应力场。
对比双级PDC钻头和常规PDC钻头的井底应力场,研究了其提高机械钻速的力学机理。
通过对比不同导眼体直径的双级PDC钻头的井底应力场,优选出导眼体直径。
②应用非牛顿流体力学、钻柱水力学和钻头水力学的理论,推导出了双级流量分配的方程组及参数影响的简化公式,编写了双级流量分配和喷嘴组合设计程序。
经参变分析得出:导眼体分流流量随扩眼体喷嘴组的当量直径的增大而减小,随导眼体喷嘴组的当量直径的增大而增大,随级间段长的加长而减小的影响规律和曲线,和随其它参数变化影响的幅度。
进而提出了双级流量分配的基本原则。
③应用有限元方法和间隙元法思想,以全井钻柱为研究对象,提出钻头与地层接触为弹性接触的假设和用现代多向间隙接触理论实现间隙元的思想,建立了双级PDC钻头和常规PDC钻头的钻具组合的有限元分析模型。
通过真实PDC钻头的性能模拟和曲线拟合,考虑钻头与地层的摩阻推导出PDC钻头扭矩预测公式;提出用迭代方法计算零钻压下的悬重和给定指重表钻压下的钻头钻压,较真实地模拟钻井的钻压-扭矩响应、稳定或振荡过程;考虑泥浆浮力、钻井液阻力偶、钻柱-井壁摩擦力及扭矩、钻头扭矩等边界条件,编写了有限元分析程序,研究了双级PDC钻头的井底钻具组合的井斜控制特性。
分析双级PDC钻头的塔式钻具组合和塔式钟摆钻具组合得出:在小井斜和较大井眼扩大系数下,双级PDC钻头与塔式(钟摆)钻具组合配合使用具有较好的防斜作用。
PDC钻头讲稿解析

2000 1500 1000
500 0
-500 0
胎体钻头
钢体钻头
PDC钻头的结构
PDC 钻 头 主 要由钻头体、切 削齿、喷嘴、保 径面和接头等组 成。
PDC钻头的保径结构
主动保径 (保径齿) 被动保径 (保径块)
PDC钻头的冠部剖面形状
PDC钻头冠部剖面的几何形状影响钻头的稳定性、 井底清洗、钻头磨损、钻头各部位载荷分布。钻头冠部 剖面形状一般包括内锥、鼻部、侧面、肩部及保径五个 基本部位。常见的形状如下图。
PDC复合片磨损机理
1.复合片磨损速度与岩石的岩性关系密切。 岩石抗压强度增加,岩石中石英含量及粒度 增大,复合片的磨损速度随之增大。 2.磨损速度与切削正压力的α次方成正比。 随正压力增加,破岩速度增大,同时磨损速度 也增大。正压力指数α值为0.93~1.62。 3.复合片磨损速度与切削线速度的β次方成 正比。切削线速线增加,磨损速度加快。切 削线速度指数β值为0.98~1.29。
PDC钻头轮廓结构
双锥轮廓钻头具有尖的鼻部和深 的内锥,适合于中到高密度布齿,适用于 钻进中到中硬地层。适合钻进多夹层 地层的钻头冠部轮廓形状,浅锥、双圆 弧冠部轮廓,外锥长度适中。这种双圆 弧形轮廓剖面具有的特点:一是使得 钻头表面尽可能有效地布置切削齿; 二是使钻头从鼻部切削齿到保径切削 齿能够圆滑地过渡。
人造聚晶金刚石复合片它由两层组成,一 层是聚晶金刚石切削层(一种人造超硬材料); 另一层是硬质合金(碳化钨)衬底层。PDC钻 头是用聚晶金刚石复合片镶嵌于钻头钢体(或 焊于钻头胎体)而制成的一种切削型钻头,它以 聚晶金刚石复合片作为切削刃,以负刃前角剪 切方式破碎岩石。
PDC钻头的发展
20世纪的后半个世纪,钻探工业的 发展与金刚石钻头的发展密切相关。60 年代初,人造金刚石的应用大大推动了 金刚石钻探技术的发展,使钻探成本大 幅度降低,70年代,PDC钻头的兴起大 大提高了钻进效率,并在软-中硬地层中 得到广泛应用,随后热稳定PDC钻头的 发展,使之硬地层中的应用成为可能,
pdc钻头分析
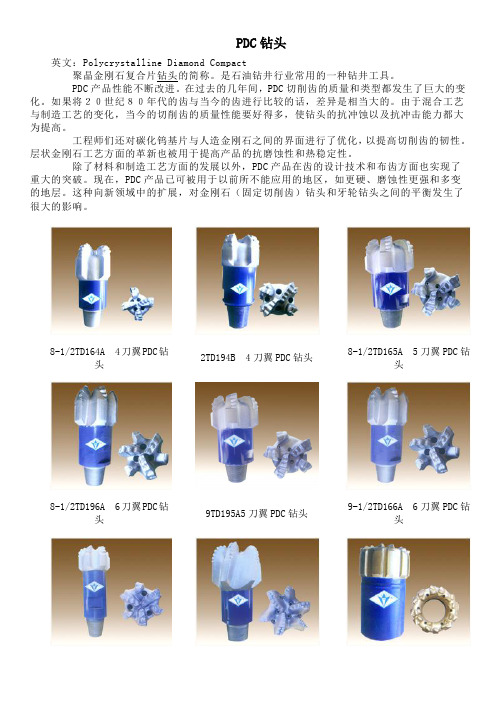
PDC钻头英文:Polycrystalline Diamond Compact聚晶金刚石复合片钻头的简称。
是石油钻井行业常用的一种钻井工具。
PDC产品性能不断改进。
在过去的几年间,PDC切削齿的质量和类型都发生了巨大的变化。
如果将20世纪80年代的齿与当今的齿进行比较的话,差异是相当大的。
由于混合工艺与制造工艺的变化,当今的切削齿的质量性能要好得多,使钻头的抗冲蚀以及抗冲击能力都大为提高。
工程师们还对碳化钨基片与人造金刚石之间的界面进行了优化,以提高切削齿的韧性。
层状金刚石工艺方面的革新也被用于提高产品的抗磨蚀性和热稳定性。
除了材料和制造工艺方面的发展以外,PDC产品在齿的设计技术和布齿方面也实现了重大的突破。
现在,PDC产品已可被用于以前所不能应用的地区,如更硬、磨蚀性更强和多变的地层。
这种向新领域中的扩展,对金刚石(固定切削齿)钻头和牙轮钻头之间的平衡发生了很大的影响。
8-1/2TD164A 4刀翼PDC钻头2TD194B 4刀翼PDC钻头8-1/2TD165A 5刀翼PDC钻头8-1/2TD196A 6刀翼PDC钻头9TD195A5刀翼PDC钻头9-1/2TD166A 6刀翼PDC钻头最初,PDC 钻头只能被用于软页岩地层中,原因是硬的夹层会损坏钻头。
但由于新技术的出现以及结构的变化,目前PDC 钻头已能够用于钻硬夹层和长段的硬岩地层了。
PDC 钻头正越来越多地为人们所选用,特别是随着PDC 齿质量的不断提高,这种情况越发凸显。
由于钻头设计和齿的改进,PDC 钻头的可定向性也随之提高,这进一步削弱了过去在马达钻井中牙轮钻头的优势。
目前,PDC 钻头每天都在许多地层的钻井应用中排挤掉牙轮钻头的市场。
PDC 钻头厚层砾岩钻进技术探索与实践:为了降低海上钻井作业成本、提高作业效率,开发了PDC 钻头厚层砾岩钻进技术.在保持普通PDC 钻头快速切削性能的基础上,通过优选新型高强度PDC 切削 齿、改进钻头切削结构提高钻头的整体强度,通过采用后倾角渐变、力平衡设计、加强切削齿保护等方法提高钻头的稳定性,并且在使用中通过优化钻具组合、采用 合理的钻井参数和"中低排量-中低转速-中高钻压"的平稳钻进模式预防PDC 钻头在砾岩段的先期破坏,有效延长了钻头在砾岩钻进中的寿命.应用该技术实现 了用PDC 钻头在辽东湾一次性钻穿馆陶组和东营组上部疏松地层中垂厚近80 m 的砾岩段,有的井钻穿砾岩段后又直接钻下部中硬地层至完钻井深.采用PDC 钻头厚层砾岩钻进技术,可以大量节省海上钻井作业时间,显著降低钻井费用.PDC 钻头工程技术措施石油钻井装备:1)、首先做好PDC 钻头的选型工作,钻头水眼、流道设计应利于排屑;2)、下入PDC 钻头之前,应充分循环泥浆,清洗井眼,防止起钻后滞留在井眼内的钻屑继续水化分散;3)、下钻时钻头不断刮削井壁,井壁上的泥饼或滞留于井内的钻屑会在钻头下堆积,到一定程度便会压实在钻头上,那么下钻中途进行循环,将钻头 冲洗干净也是有其必要的;4)、下钻过程中还应适当控制速度,防止钻头突然冲入砂桥,钻进一堆烂泥中;另外如果速度恰当,PDC 钻头会顺着上一只钻头所钻的螺旋形井眼轨道行 进,而不是在井壁上划拉下大量泥饼。
PDC钻头模具三维设计和数控加工技术研究与应用

PDC钻头模具三维设计和数控加工技术研究与应用摘要本文对PDC钻头模具三维设计和数控加工一体化技术的方法、步骤和相关工艺技术进行了研究。
解决了PDC钻头模具辅助设计二维数据的三维转化问题,提出了模具三维造型和参数化开发的方法,并应用CAD/CAM系统软件PRO/E建立了PDC钻头模具三维模型,应用PRO/PROGRAM(程序)开发模块进行PDC钻头模具造型的参数化开发,并编制了相应的参数化开发软件,提高了PDC钻头模具造型速度和准确性。
在建立PDC钻头模具三维造型的根底上,确定了模具数控加工工艺,摸索出一套利用PRO/E软件进行PDC钻头模具计算机辅助制造的方法和步骤,实现了PDC钻头模具一次装卡、一次成形的高精度自动化数控加工技术。
关键词 PDC钻头模具三维设计数控加工技术 CAD/CAM 聚晶金刚石复合片钻头(简称PDC钻头)由钻头体、接头组成,根据钻头体按材料的不同分为胎体PDC钻头和钢体PDC钻头。
胎体PDC钻头的钻头体是采用铸造碳化钨粉和浸渍料经无压浸渍烧结而成的。
钻头体形状是通过模具的形状而间接实现的。
模具由底模、中模和上模三局部组成。
模具的中模和上模的设计与加工都很容易实现。
但底模是具有复杂曲面特征的实体,PDC钻头的冠部形状参数、切削齿位置和方向参数、水力结构参数等都是通过底模的形状来实现的。
因此底模的设计和加工是模具设计和加工中最重要的一局部,其设计的好坏和加工的精度都直接关系到钻头的最终使用效果。
高质量的模具是保证PDC钻头质量的关键因素之一。
目前国内PDC钻头模具的形成主要有三种方法。
第一种(应用最多的,如以下列图)是利用普通车床车削形成钻头冠部形状,依靠分度头手工划线定位、普通万能铣床铣削完成切削齿和水眼的加工,再通过手工修模完成水力结构的造型等多道工序完成的。
这种加工方法的缺点是工人劳动强度大、加工精度低、人为误差大,难以控制和保证质量,很难到达设计的要求。
第二种是数控加工,利用数控机床加工形成钻头的冠部形状和切削齿的定位,然后再通过手工修模或者粘上相应形状成形的水力结构(粘上以后也要进行一定的手工修理)而最后形成模具的。
PDC钻头切削齿和岩石作用模型

SPE-98988PDC钻头–源于牙轮和岩石间的相互作用L.Gerbaud, S.Menand, SPE, H. Sellami, SPE, 来自巴黎的Ecole des Mines摘要在过去的几十年里,由于在PDC磨损、抗冲击性和对井斜进一步理解上的创新,在硬岩中PDC钻头性能已获得大幅度改善。
钻头设计通常要考虑钻头平衡、沿钻头剖面的平均磨损分布、达到最佳可钻性和导向性。
为了达到所需的钻井性能,钻头设计者调整剖面形状、保径和主要的切削齿特征(形状、类型和方向)等性能。
切削齿和岩石作用模型已经成为设计过程中一个非常重要的因素了。
但是以前用的模型只是基于切削齿和岩石相互接触面考虑了作用在切削齿上的3个力:正压力,切向力和侧向力。
但是随着带倒角或其他特殊形状的切削齿的发展,这种模型已经不适用了。
本文介绍一种新的切削齿和岩石作用模型,较之以前做了些改进。
它是基于文献中经常提到的在切削面上挤压岩屑的增斜边的存在。
同时,倒角也严重影响钻速,因此也被考虑了进去(形状和大小)。
由于岩石变形和被压碎的岩屑的排出对切削齿后部的力也被考虑了。
最终,得到的很多单齿试验结果(在常压和规定的压力下)并且和新的切削齿和岩石作用模型的预测相比较。
同时本文还分析了PDC钻头各种特征的影响作用(形状,大小,倒角,后倾角和侧倾角)。
这个模型被用来优化切削效率和钻头的导向能力,同时给出了一些设计的原则,使比能最小,使侵入岩石速率最高。
最终,全尺寸钻进实验和油田数据表明,应用精确地岩石和钻头相互作用模型能帮助钻头设计者针对特定区块找到最合适的钻头。
标准的实验室全尺寸钻进过程已经发展起来。
实验表明通过对切削齿的特征,切削齿的部齿,切边齿的特征和保径类型的调整,钻头的钻进能力,稳定性,导向能力和磨损可以改善和控制。
介绍从19世纪七十年代开始,PDC钻头性能不断改进,从改善PDC的工艺水平,切削齿结构,动力学稳定性,水力因素和导向性到平滑快速钻进。
PDC钻头综合受力模型的试验研究
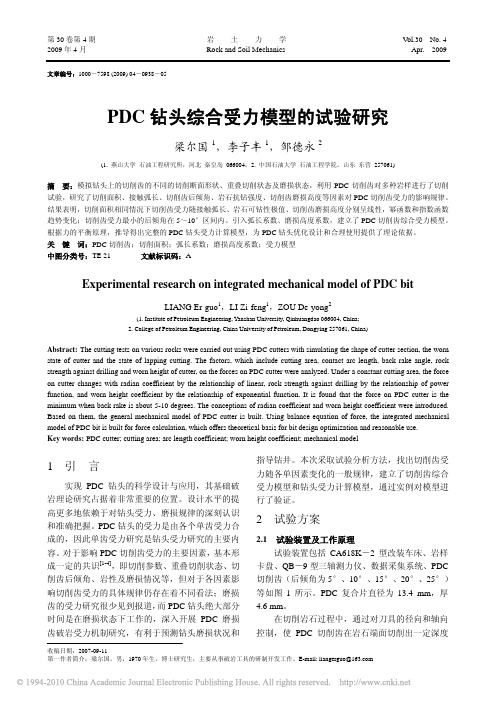
900
—切向力
750
—轴向力
600
450
300
150
0 0 5 10 15 20 25 30 A /mm2
图 6 磨损齿受力 F/μ f 与 切 削 面 积 A 关 系 Fig.6 The relationship between force of cutters worn
(F/μ f ) and cutting area (A)
摘 要:模拟钻头上的切削齿的不同的切削断面形状、重叠切削状态及磨损状态,利用 PDC 切削齿对多种岩样进行了切削
试验,研究了切削面积、接触弧长、切削齿后倾角、岩石抗钻强度、切削齿磨损高度等因素对 PDC 切削齿受力的影响规律。
结果表明,切削面积相同情况下切削齿受力随接触弧长、岩石可钻性极值、切削齿磨损高度分别呈线性,幂函数和指数函数
1引言
实现 PDC 钻头的科学设计与应用,其基础破 岩理论研究占据着非常重要的位置。设计水平的提 高更多地依赖于对钻头受力、磨损规律的深刻认识 和准确把握。PDC 钻头的受力是由各个单齿受力合 成的,因此单齿受力研究是钻头受力研究的主要内 容。对于影响 PDC 切削齿受力的主要因素,基本形 成一定的共识[1-4],即切削参数、重叠切削状态、切 削齿后倾角、岩性及磨损情况等,但对于各因素影 响切削齿受力的具体规律仍存在着不同看法;磨损 齿的受力研究很少见到报道,而 PDC 钻头绝大部分 时间是在磨损状态下工作的,深入开展 PDC 磨损 齿破岩受力机制研究,有利于预测钻头磨损状况和
area in general cutting
940
岩土力学
2009 年
3.1.2 接触弧长对切削齿受力的影响 重叠切削状态下切削齿切削岩样产生各种不规
PDC_切削齿直径对切削力的影响规律研究

◀钻井技术与装备▶PDC切削齿直径对切削力的影响规律研究∗未九森㊀邵方源㊀谭紫阳㊀刘维㊀高德利(中国石油大学(北京)石油工程教育部重点实验室)未九森ꎬ邵方源ꎬ谭紫阳ꎬ等.PDC切削齿直径对切削力的影响规律研究[J].石油机械ꎬ2023ꎬ51(4):8-15.WeiJiusenꎬShaoFangyuanꎬTanZiyangꎬetal.InfluenceofPDCcutterdiameteroncuttingforce[J].ChinaPetro ̄leumMachineryꎬ2023ꎬ51(4):8-15.摘要:针对不同地层岩性特点ꎬ需进行个性化PDC钻头设计ꎬ其中PDC切削齿的直径是重要的钻头优化设计参数之一ꎮ为了探究不同PDC切削齿直径对破岩切削力的影响ꎬ通过室内模拟试验方法进行研究ꎮ试验所用岩样为石灰岩ꎮ单齿破岩试验选取了ø13 44㊁ø15 88㊁ø19 05㊁ø21 95mm的常规圆柱状PDC切削齿和3个不同的切削深度作为试验变量ꎬ使用三轴力传感器记录了切削力数据并收集了岩屑ꎬ对比了不同试验条件下单齿破岩过程的机械比能和不同直径切削齿的攻击性ꎻ使用水平钻机进行了全尺寸钻头破岩试验ꎬ对比了3种不同PDC切削齿直径的钻头在3mm左右吃入深度下的破岩机械比能ꎮ试验结果显示:PDC切削齿的破岩切削力并不随着直径的增大而增大ꎻ在相同吃入深度下ꎬø19 05mm齿的破岩效果最好ꎻ随着吃入深度的增加ꎬ切削岩石所需要的力变大ꎮ全尺寸钻头破岩试验结果表明ꎬø19 05mm齿的全尺寸钻头机械比能最低ꎮ分析认为ꎬ在破岩过程中ꎬPDC切削齿直径会改变岩石内部产生的应力区域ꎬ影响PDC切削齿的破岩效果ꎮ选取与岩性匹配的PDC切削齿直径能够取得最优的破岩钻进效果ꎮ研究结果可为PDC钻头优化设计提供部分理论指导ꎮ关键词:PDC钻头ꎻ破岩效率ꎻ切削力ꎻ机械比能ꎻ单齿破岩ꎻ全尺寸钻头破岩中图分类号:TE921㊀文献标识码:A㊀DOI:10 16082/j cnki issn 1001-4578 2023 04 002InfluenceofPDCCutterDiameteronCuttingForceWeiJiusen㊀ShaoFangyuan㊀TanZiyang㊀LiuWei㊀GaoDeli(MOEKeyLaboratoryofPetroleumEngineeringꎬChinaUniversityofPetroleum(Beijing))Abstract:PDCbitdesignneedstobecustomizeddependingupontheformationlithologycharacteristicsꎬandespeciallythediameterofPDCcutterisanimportantparameterinbitdesignoptimization.AseriesoflaboratorysimulationtestswereconductedtoexploretheinfluenceofPDCcutterdiameteronrock ̄breakingcuttingforce.Therocksamplesusedinthetestswerelimestone.Intherock ̄breakingtestofsinglecutterꎬtheø13 44ꎬø15 88ꎬø19 05andø21 95mmconventionalcylindricalPDCcuttersweretestedatthreecuttingdepthsꎬthetriaxialforcesensorwasusedtorecordthecuttingforcedataꎬthecuttingswerecollectedꎬandthemechanicalspecificenergyofsinglecutterrock ̄breakingprocessunderdifferenttestconditionsandtheaggressivenessofdifferentdiametersofcutterswerecompared.Moreoverꎬfull ̄scalebitrock ̄breakingtestwasperformedusingthehorizontaldrillingrigꎬ8 ㊀㊀㊀石㊀油㊀机㊀械CHINAPETROLEUMMACHINERY㊀2023年㊀第51卷㊀第4期∗基金项目:国家自然科学基金创新研究群体项目 复杂油气井钻井与完井基础研究 (51821092)ꎻ国家自然科学基金重点项目 复杂结构 井工厂 立体设计建设基础研究 (52234002)ꎻ国家自然科学基金石油化工联合基金项目 页岩和致密油气田高效开发建井基础研究 (U1762214)ꎻ中国石油大学(北京)科研启动基金项目 高效钻头的研究 (ZX20190065)ꎻ中石油战略合作科技专项专题 陆相页岩油深部地层钻井提速技术研究 (ZLZX2020-01-07-01)ꎮandtherock ̄breakingmechanicalspecificenergiesofbitswiththreePDCcutterdiametersatabout3mmpenetra ̄tiondepthwerecompared.Thetestresultsshowthattherock ̄breakingcuttingforceofPDCcutterdoesnotincreasewiththeincreaseofdiameter.Atthesamepenetrationdepthꎬtherock ̄breakingeffectofø19 05mmcutteristhebest.Asthepenetrationdepthincreasesꎬtheforcerequiredtocuttherockbecomeslarger.Therock ̄breakingtestresultsoffull ̄scalebitshowthatthemechanicalspecificenergyofø19 05mmcutterfull ̄scalebitisthelowest.Itisbelievedthatintheprocessofrock ̄breakingꎬthePDCcutterdiameterchangesthestressareageneratedinsidetherockꎬtherebyaffectingtherock ̄breakingeffectofPDCcutter.UseofaPDCcutterdiametermatchingtheli ̄thologycanachievetheoptimalrock ̄breakingeffect.TheresearchresultsprovidesometheoreticalguidancefortheoptimizationdesignofPDCbit.Keywords:PDCbitꎻrock ̄breakingefficiencyꎻcuttingforceꎻmechanicalspecificenergyꎻrock ̄breakingofsinglecutterꎻrock ̄breakingoffull ̄scalebit0㊀引㊀言PDC钻头具有切削破岩效率高㊁使用寿命长的优势ꎬ在油气钻探行业广泛使用ꎮ随着当前油气勘探开发朝着深层㊁深水㊁非常规方向迈进ꎬ地下钻井条件越来越复杂ꎬ对聚晶金刚石复合片(PolycrystallineDiamondCompactꎬPDC)钻头性能提出了更高的要求ꎮ过去有很多研究人员针对PDC钻头的破岩问题进行了深入而广泛的研究ꎬ提出了多种PDC切削齿切削力计算模型[1-11]ꎮ部分学者使用无倒角圆柱状PDC切削齿ꎬ通过室内试验研究了单齿切削岩石过程ꎬ结果发现ꎬ影响单齿切削力的主要因素包括齿与岩石接触面积㊁齿刃部接触弧长㊁吃入深度以及接触面形状等[12-14]ꎮ尽管基于这些参数建立的切削力模型能够很好预测单齿切削力ꎬ但这些模型只针对相同直径的PDC切削齿ꎬ无法适用于不同直径之间的切削力对比ꎮ通常使用的PDC切削齿刃部存在倒角ꎬ一些研究人员[15-18]基于这一认识ꎬ将齿切削接触面分为2部分ꎬ给出了表面分离的切削力计算模型ꎬ在计算单齿切削力的时候将倒角和平面接触部分分别进行考虑ꎬ预测结果与试验结果能够相符ꎮ邹德永等[15-16]基于室内全尺寸钻头试验ꎬ研究了包括钻头齿直径㊁后倾角㊁布齿密度等不同设计参数对PDC钻头整体破岩效率的影响规律ꎬ研究过程中注意到切削齿直径对PDC钻头整体切削力及破岩效率的影响ꎮ尽管已有较多PDC钻头破岩效率和单齿切削力的相关研究ꎬ但其内容多着眼于PDC切削齿的空间位置参数对力的影响ꎬ如后倾角等[21-23]ꎬ很少有人研究PDC切削齿直径对单齿破岩过程切削力的影响ꎮ为此ꎬ笔者通过开展室内单齿切削试验ꎬ研究分析PDC切削齿直径对破岩的影响ꎬ以给出在脆性岩石条件下几种不同直径PDC切削齿的破岩效果ꎬ揭示直径对破岩过程的影响规律ꎬ并通过室内全尺寸钻头模拟钻进试验对单齿破岩试验结果进行验证ꎮ研究结果可为PDC钻头优化设计提供部分理论指导ꎮ1㊀单齿破岩试验图1㊀立式转塔车床测试系统Fig 1㊀Verticalturretlathetestsystem1 1㊀试验装置立式转塔车床(VTL)测试系统被广泛应用于PDC切削齿的切削磨损测试ꎬ由于其工作方式为旋转车削运动ꎬ所以本次研究将利用这一装置开展单齿破岩试验研究[17ꎬ24]ꎮ图1展示了VTL测试系统的主要构成部分ꎬ包括旋转工作台㊁数控系统㊁PDC切削齿夹具㊁三轴力传感器以及数据采集系统等ꎮ其中PDC切削齿夹具与试验变量设置相对应ꎬ包括ø13 44㊁ø15 88㊁ø19 05以及ø21 95mm共4种夹具尺寸ꎮ被切削的岩石样品为圆柱状石灰岩ꎬ直径1100mmꎬ密度2 51g/cm3ꎬ弹性模量14 94GPaꎬ泊松比0 28ꎬ单轴抗压强度92023年㊀第51卷㊀第4期未九森ꎬ等:PDC切削齿直径对切削力的影响规律研究㊀㊀㊀96 06MPaꎬ岩石内部黏聚力23 85MPaꎬ内摩擦角41 7ʎꎮ1 2㊀试验原理及方法单齿破岩试验装置的夹具夹持PDC切削齿在岩石上端面进行圆弧轨迹切削ꎮPDC切削齿静止ꎬ岩石在旋转工作台带动下ꎬ相对PDC切削齿做恒定线速度的旋转运动ꎬ相对线速度15m/minꎬ吃入深度恒定ꎮ在PDC切削齿切削岩石过程中ꎬ三轴力传感器以固定频率(400Hz)记录PDC切削齿所受的三轴正交切削力FX/FY/FZꎬ传感器测量力的方向如图2所示ꎮ为了分析不同PDC切削齿直径对切削力的影响规律ꎬ选择了4种常规圆柱带倒角PDC切削齿(ø13 44㊁ø15 88㊁ø19 05和ø21 95mm)和3个不同的吃入深度(1㊁2和3mm)进行试验ꎮ所有的切削后倾角均设置为20ʎꎬ无侧转角ꎮ前期试验表明ꎬ切削旋转半径和切削速度对切削力基本无影响ꎮ选取的4个PDC切削齿如图3所示ꎮ为了减少试验误差ꎬ将每组试验设置重复测试3次ꎬ具体试验方案如表1所示ꎮ图2㊀试验结果中的三轴力方向Fig 2㊀Triaxialforcedirectionintestresults图3㊀试验用的4种直径PDC切削齿Fig 3㊀PDCcutterswith4differentdiametersusedinthetest表1㊀单齿切削试验设置方案1 3㊀试验步骤(1)首先将岩石样品上端面磨平ꎮ在上端面相应位置使用工具预置沟槽ꎬ以能够下降PDC切削齿到预设的吃入深度为宜ꎮ(2)将试验用PDC切削齿夹持于VTL测试系统上ꎬ并将齿刃部最低点与岩石上端面对齐ꎬ手动调整到岩石端面预置沟槽中ꎬ降落到相应吃入深度ꎮ(3)打开三轴力传感器以接收切削力信号ꎬ设定VTL测试系统的切削速度为15m/minꎬ开始切削试验ꎮ(4)切削1道后主轴自动停止ꎬ关闭三轴力传感器ꎬ抬升PDC切削齿观察是否损坏ꎬ同时收集产生的岩屑ꎬ测量切削轨迹长度ꎮ(5)调整试验参数ꎬ重复进行试验直至结束ꎮ2㊀试验结果分析2 1㊀试验结果为了方便控制切削过程ꎬ在PDC切削齿的X轴方向设置了相对于轨迹长度微小的每转进给量(1~2mm/r)ꎬ因此X轴方向的力非0ꎬ但相比于Y轴和Z轴2方向的力很小ꎬ在试验结果分析过程中可忽略不计ꎮ最终试验结果仅考虑水平切向力和垂直法向力ꎬ如图4所示ꎮ图5给出了通过计算岩屑体积得到的不同试验条件下的机械比能值和攻击性值ꎮ计算机械比能和攻击性的公式为[25]:EMS=FsLρm(1)A=FsFN(2)式中:EMS为单齿切削的机械比能ꎬJ/cm3ꎻFs为01 ㊀㊀㊀石㊀油㊀机㊀械2023年㊀第51卷㊀第4期破岩过程中的平均水平切向力ꎬNꎻL为切削过的痕迹长度ꎬcmꎻρ为切削岩石的密度ꎬg/cm3ꎻm为切削产生的岩屑质量ꎬgꎻA为攻击性ꎬ1ꎻFN为破岩过程中的平均垂直力ꎬNꎮ图4㊀不同试验条件下的水平力FY和垂直力FZFig 4㊀HorizontalforceFYandverticalforceFZunderdifferenttestconditions图5㊀不同试验条件所得机械比能和攻击性Fig 5㊀Mechanicalspecificenergyandaggressivenessobtainedunderdifferenttestconditions2 2㊀分析与讨论笔者团队建立的带倒角的圆形齿切削力预测计算模型认为ꎬ单齿破岩过程中产生的切削力可分为2个部分ꎬ分别是位于齿前平面上的切削力和位于刃部倒角位置的切削力ꎬ合力计算方法为[17]:Fr=Fp+Fc(2)式中:Fr为PDC切削齿切削过程合力ꎬNꎻFp为分布在齿前平面上的切削力ꎬNꎻFc为分布在齿刃部倒角的切削力ꎬNꎮ齿前平面和倒角部分的切削力计算公式为:Fp=ResAp(3)Fc=ResAc(4)式中:Res为岩石切削过程中的破岩固有比能ꎬMPaꎻAp和Ac分别为齿前平面和倒角部分在切削过程的接触面积ꎬmm2ꎮAp=(R-l)2arccos1-hR-læèçöø÷-h2R-l()-h[](R-l-h)(5)Acʈ2㊀2{2R-l()arccos1-hR-læèçöø÷+Dcosα+1-sinα+㊀2sinπ4-αæèçöø÷cosαéëêêêùûúúúlüþýïïïl(6)h=Dcosα-㊀2sinπ4-αæèçöø÷cosαl(7)式中:R为齿的半径ꎬmmꎻl为齿倒角长度ꎬmmꎻD为吃入深度ꎬmmꎻα为切削过程齿的后倾角ꎬ(ʎ)ꎮ由于公式(6)的计算结果为近似值ꎬ所以倒角部分接触面积借助3D建模软件进行数值计算ꎬ最终结果见表2ꎮ表2㊀齿与岩石接触部分面积图6和图7展示了4种齿的切削合力与接触面积之间的关系ꎮ图6显示的结果与式(2)~式(4)给出的切削力模型相符ꎬ线性系数为单齿切削时岩石破碎固有比能ꎮ由图7可知ꎬ吃入深度相同ꎬ改变直径引起的接触面积变化与切削力为非线性关系ꎬ不同直径的PDC切削齿会大大影响切削过程中的固有比能ꎮ随着吃入深度逐渐增加ꎬ齿直11 2023年㊀第51卷㊀第4期未九森ꎬ等:PDC切削齿直径对切削力的影响规律研究㊀㊀㊀径对固有比能的影响变大ꎬ原因是不同直径的PDC切削齿对岩石内部的破碎应力分布状态影响较大ꎬ导致不同切削齿直径在相同吃入深度下ꎬ切削力与接触面积的比值不同ꎬ即破岩固有比能非定值ꎮ图6㊀不同齿直径条件的接触面积与合力关系Fig 6㊀Relationshipbetweencontactareaandresultantforceunderdifferentcutterdiameters图7㊀不同吃入深度条件的接触面积与合力关系Fig 7㊀Relationshipbetweencontactareaandresultantforceatdifferentpenetrationdepths㊀㊀从图7中可知ꎬ当直径由13 44mm变为15 88mm时ꎬ切削力结果相比于趋势线上的预测值更大ꎬ其中以吃入深度为3mm时差距最大ꎮPDC切削齿在破岩过程中ꎬ切削力大小由倒角接触面积和齿前平面接触面积两者共同影响ꎮ结合齿前平面面积和刃部倒角面积变化趋势可知ꎬ当吃入深度为3mm且直径由13 44mm变为15 88mm时ꎬ刃部倒角面积变小ꎬ齿前平面面积变大ꎬ所以此时切削力主要受齿前平面大小影响ꎮ图4中吃入深度为3mm时ꎬø13 44和ø19 05mm齿的水平和垂直切削力结果几乎相同ꎬ原因是当使用ø19 05mm齿切削时ꎬ在齿前方的岩石内产生了理想的断裂形状ꎬ齿前平面中心没有完全接触岩石ꎬ所以在切削过程中所需要的切削力较小ꎬ存在有规律且较为完整的岩石崩片过程ꎮ直径对2种PDC切削齿切削过程中产生的裂缝形态的影响如图8所示ꎮ图8中红色渐变部分为接触部位边界处的应力影响区域ꎮø19 05mm齿的左右应力区域互相影响ꎬ产生了左右一体的连通裂缝ꎬ此时ꎬ齿前平面正前方的岩石已在上次崩片后剥落ꎬ即齿前平面并没有完全接触岩石ꎬ齿整体受力较小ꎬ因此能保证与ø13 44mm直径钻头齿受力在同一水平ꎮ图8㊀直径对2种PDC切削齿切削过程中产生的裂缝形态的影响Fig 8㊀InfluenceofPDCcutterdiameteronthefracturemorphologycreatedinthecuttingprocess当直径增加到21 95mm时ꎬ由于齿直径太大ꎬ接触部位左右宽度较大ꎬ齿的左右应力区域无法相互影响ꎬ产生的裂缝左右各自独立向前发展ꎬ与岩石接触的左右边界产生的应力无法传递到接触面正中心的岩石ꎬ无法造成此处岩石的断裂失效ꎬ 21 ㊀㊀㊀石㊀油㊀机㊀械2023年㊀第51卷㊀第4期所以齿前平面前方的岩石还受到即将被切削到的岩石的支持ꎬ齿前平面需要对岩石施加力来破坏两道裂缝中间的岩石ꎬ导致ø21 95mm的齿需要更大的破岩切削力ꎮ图9展示了3种不同吃入深度情况下的切削痕迹ꎮ由图9可以发现:吃入深度为1mm时ꎬ切削过程均匀ꎬ痕迹两侧没有剥落或岩石崩片ꎻ当吃入深度为2或3mm时ꎬ崩片剥落痕迹大量分布ꎬ且吃入深度越大分布越多ꎮ一般在吃入深度较小时ꎬ破碎岩石产生的岩屑大多为粉碎状ꎬ在吃入深度较大时则为块状崩片ꎮ由图5中机械比能和攻击性值的对比可以发现ꎬ在使用相同直径的PDC切削齿进行单齿切削时ꎬ由于较大的吃入深度能够产生大量的岩石体积破碎ꎬ所以机械比能越小ꎮ图9㊀使用ø21 95mm齿切削后的岩石表面痕迹参考Fig 9㊀Rocksurfacetracesaftercuttingwithø21 95mmcutter在吃入深度为1mm时ꎬø15 88mm的齿的机械比能最小ꎬ破岩效率最高ꎮ通过比较4种齿的倒角尺寸可知ꎬ当吃入深度较小ꎬ破岩过程中倒角影响较大ꎻø15 88mm的PDC切削齿倒角尺寸最小ꎬ能产生比其他齿大的应力集中ꎬ更容易破岩ꎻ当吃入深度为2mm时ꎬ由于倒角尺寸和PDC切削齿直径效应2种因素的共同作用ꎬ导致ø15 88mm钻头齿和ø19 05mm钻头齿的机械比能相差不大ꎻ而在吃入深度为3mm时ꎬ由于PDC切削齿的直径影响变大ꎬ使用ø19 05mm的PDC切削齿能够取得最优的破岩效率ꎬ具有最佳的破岩效果ꎮ由于ø21 95mm的PDC切削齿直径最大ꎬ不同吃入深度的攻击性基本相同ꎮ3㊀全尺寸钻头破岩试验验证为了验证PDC切削齿大小对单齿破岩和全尺寸PDC钻头钻进效果的影响规律是否相同ꎬ使用水平钻机开展了全尺寸钻头钻进模拟试验ꎮ水平钻机结构如图10所示ꎬ主要的部件包括水平钻机主体以及随钻测量短节ꎬ其中随钻测量短节用于记录钻图10㊀全尺寸钻头钻进试验用水平钻机及随钻测量短节Fig 10㊀HorizontaldrillingrigandMWDsubforfull ̄scalebitdrillingtest进过程中钻头受力ꎮ试验用的岩石样品与单齿破岩试验相同ꎮ钻进用钻头分别为使用ø15 88㊁ø19 05㊁ø21 95mm圆齿设计的直径为215 9mm(8 5in)的4刀翼PDC钻头ꎬ每只钻头的冠部曲线等设计参数均相同ꎮ在试验过程中ꎬ设置水平钻机的转速为75r/minꎬ在每次钻进试验时ꎬ使用随钻测量短节记录钻头上的钻压和钻速数据ꎮ3只钻头的钻进试验结果如图11所示ꎮ为了比较在相同吃入深度情况下的钻进效率ꎬ需要保证钻头在钻进过程中的吃入深度相同ꎬ由于钻机的转速为75r/min保持不变ꎬ所以只要在保证机械钻速相同的条件下对3只钻头的钻压进行对比ꎬ即可得知3只钻头的钻进效率ꎮ机械钻速和吃入深度之间的换算关系为:VROP=60VRPMD(8)式中:VROP为机械钻速ꎬm/hꎻVRPM为钻头转速ꎬr/minꎻD为钻头每转吃入深度ꎬm/rꎮ通过式(8)可计算出机械钻速为13 5m/h时ꎬ符合单齿破岩试验的3mm吃入深度条件ꎮ由于PDC钻头直径相同ꎬ且吃入深度也相同ꎬ所以钻头破岩效果仅受PDC切削齿直径的影响ꎮ通过下式计算3只钻头各自的机械比能ꎬ详细数据见表3ꎮEMS=2MTOBDR2+FWOBπR2(9)式中:MTOB为测量得到的钻头扭矩ꎬN mꎻD为钻头每转吃入深度ꎬmꎻR为钻头半径ꎬmmꎻFWOB为测量得到的钻头钻压ꎬNꎮ表3 全尺寸钻头破岩试验结果31 2023年㊀第51卷㊀第4期未九森ꎬ等:PDC切削齿直径对切削力的影响规律研究㊀㊀㊀图11为全尺寸PDC钻头钻进试验结果对比ꎮ由图11可知ꎬ当试验钻头的每转吃入深度接近3mm时ꎬø19 05mm的钻头所需的钻进能量为最小ꎬ且所需钻压和产生的反扭矩最小ꎬ符合单齿破岩试验结果显示出的规律ꎮ图11㊀全尺寸PDC钻头钻进试验结果对比图Fig 11㊀Comparisonoffull ̄scalePDCbitdrillingtestresults4㊀结论及建议(1)不同PDC切削齿直径对岩石切削过程的受力影响较大ꎬ且齿直径和固有比能两者之间没有明显规律ꎬ前人的力-接触面积线性关系模型在PDC切削齿直径不变情况下比较适用ꎬ反之则不然ꎮ(2)在试验结果中吃入深度相同的情况下ꎬ当PDC切削齿直径不大于15 88mm时ꎬ随着直径变大ꎬ实际测得的切削力相比于切削力-接触面积线性关系模型的预测值要大ꎻ在齿直径为19 05mm时ꎬ实测值小于预测值ꎻ当齿直径为21 95mm时ꎬ实测值大于预测值ꎮ(3)单齿破岩试验结果显示ꎬ直径19 05mm的齿在3mm的吃入深度条件下切削岩石时ꎬ机械比能值为全局最低ꎬ可获得最理想的切削效果ꎮ在全尺寸钻头破岩试验中ꎬ直径19 05mm齿的PDC钻头在相同机械钻速下ꎬ所需的钻进能量最小ꎮ因此ꎬ当实钻地层岩性为类似于试验用岩石样品性质的硬脆性地层时ꎬ建议选用ø19 05mm作为主要的PDC钻头工作齿ꎬ以便在有限的钻压下取得较高机械钻速ꎮ若钻进其他岩性的地层ꎬ建议进行单齿破岩试验对PDC钻头切削齿直径进行优选ꎮ(4)在单齿切削岩石过程中ꎬ岩石中产生的切削应力会影响岩石破坏的形式ꎬ从而导致破碎岩石所需要的切削力呈现出无规律变化ꎮ可通过岩石应力分布状态加以解释ꎬ有待开展深入研究ꎮ参㊀考㊀文㊀献[1]㊀史怀忠ꎬ傅新康ꎬ陈振良ꎬ等.高温高压条件下PDC钻头破碎花岗岩试验研究[J].石油机械ꎬ2021ꎬ49(12):1-9.SHIHZꎬFUXKꎬCHENZLꎬetal.ExperimentalstudyongranitebrokenbyPDCbitunderhightempera ̄tureandhighpressure[J].ChinaPetroleumMachin ̄eryꎬ2021ꎬ49(12):1-9.[2]㊀孟昭ꎬ毛蕴才ꎬ张佳伟ꎬ等.超深层井底应力环境下PDC单齿破岩机理研究[J].石油机械ꎬ2020ꎬ48(5):1-7.MENGZꎬMAOYCꎬZHANGJWꎬetal.Researchonsingle ̄toothPDCrockbreakingmechanismatultra ̄deepbottomholestress[J].ChinaPetroleumMachin ̄eryꎬ2020ꎬ48(5):1-7.[3]㊀张佳伟ꎬ孟昭ꎬ纪国栋ꎬ等.PDC钻头破岩效率及稳定性室内试验研究[J].石油机械ꎬ2020ꎬ48(12):35-43ꎬ51.ZHANGJWꎬMENGZꎬJIGDꎬetal.Laboratoryex ̄perimentalstudyonrockbreakingefficiencyandstabili ̄tyofPDCbit[J].ChinaPetroleumMachineryꎬ2020ꎬ48(12):35-43ꎬ51.[4]㊀杨迎新.PDC钻头切削力学研究[D].成都:西南石油学院ꎬ2003.YANGYX.ResearchonmechanicsofPDCbitrockcuttingprocess[D].Chengdu:SouthwestPetroleumInstituteꎬ2003.[5]㊀李其州ꎬ张凯ꎬ周琴ꎬ等.切削深度对PDC齿超高速破岩机理的影响分析[J].石油机械ꎬ2022ꎬ50(6):1-8ꎬ15.LIQZꎬZHANGKꎬZHOUQꎬetal.Influenceofcut ̄tingdepthonrockbreakingmechanismofPDCcutteratultra ̄highspeed[J].ChinaPetroleumMachineryꎬ2022ꎬ50(6):1-8ꎬ15.[6]㊀邓敏凯ꎬ伍开松ꎬ胡伟.PDC钻头切削齿破岩仿真与试验分析[J].石油机械ꎬ2014ꎬ42(1):10-13.DENGMKꎬWUKSꎬHUW.Rock ̄breakingsimula ̄tionandexperimentalanalysisofPDCbitcutter[J].ChinaPetroleumMachineryꎬ2014ꎬ42(1):10-13.[7]㊀李田军.PDC钻头破碎岩石的力学分析与机理研究[D].武汉:中国地质大学(武汉)ꎬ2012.LITJ.Mechanicalanalysisandfragmentationmecha ̄nismofPDCbitsdrillingrock[D].Wuhan:ChinaU ̄niversityofGeosciences(Wuhan)ꎬ2012.[8]㊀CHENSLꎬGROSZGꎬANDERLESꎬetal.Theroleofrock ̄chipremovalsandcutting ̄areashapesinpoly ̄crystalline ̄diamond ̄compact ̄bitdesignoptimization[J].SPEDrilling&Completionꎬ2015ꎬ30(4):334-347.[9]㊀马清明ꎬ王瑞和.PDC切削齿破岩受力的试验研究[J].中国石油大学学报(自然科学版)ꎬ2006ꎬ30(2):45-47ꎬ58.41 ㊀㊀㊀石㊀油㊀机㊀械2023年㊀第51卷㊀第4期MAQMꎬWANGRH.ExperimentalstudyonforceofPDCcutterbreakingrock[J].JournalofChinaUni ̄versityofPetroleum(EditionofNaturalScience)ꎬ2006ꎬ30(2):45-47ꎬ58.[10]㊀GLOWKADA.Useofsingle ̄cutterdataintheanaly ̄sisofPDCbitdesigns:part1-developmentofaPDCcuttingforcemodel[J].JournalofPetroleumTech ̄nologyꎬ1989ꎬ41(8):797-849.[11]㊀CHENPJꎬMISKASZꎬRENRꎬetal.Poroelasticmodelingofcuttingrockinpressurizedcondition[J].JournalofPetroleumScienceandEngineeringꎬ2018ꎬ169:623-635.[12]㊀翟应虎ꎬ蔡镜ꎬ刘希圣.重叠和覆盖条件下PDC切削齿破岩规律[J].石油学报ꎬ1994ꎬ15(3):119-125.ZHAIYHꎬCAIJꎬLIUXS.StudyontherockbreakingofPDCchippingbitsunderoverlayandcover ̄ageconditions[J].ActaPetroleiSinicaꎬ1994ꎬ15(3):119-125.[13]㊀谭凯文.PDC钻头破岩机理实验研究[D].北京:中国石油大学(北京)ꎬ2017.TANKW.StudyOnTheRockFragmentationMecha ̄nismofPDCbit[D].Beijing:ChinaUniversityofPetroleum(Beijing)ꎬ2017.[14]㊀李劲ꎬ尹卓ꎬ刘忠ꎬ等.PDC齿破岩力预测模型研究[J].石油机械ꎬ2021ꎬ49(8):23-29ꎬ38.LIJꎬYINZꎬLIUZꎬetal.Researchonrockbreak ̄ingforcepredictionmodelofPDCcutter[J].ChinaPetroleumMachineryꎬ2021ꎬ49(8):23-29ꎬ38. [15]㊀邹德永ꎬ曹继飞ꎬ袁军ꎬ等.硬地层PDC钻头切削齿尺寸及后倾角优化设计[J].石油钻探技术ꎬ2011ꎬ39(6):91-94.ZOUDYꎬCAOJFꎬYUANJꎬetal.OptimizationdesignofthecuttersizeandbackrakeforPDCbitinhardformation[J].PetroleumDrillingTechniquesꎬ2011ꎬ39(6):91-94.[16]㊀陈多礼.PDC齿切削力数值分析与建模[D].成都:西南石油大学ꎬ2014.CHENDL.NumericalanalysisandmodelingofPDCcuttercuttingforce[D].Chengdu:SouthwestPetro ̄leumUniversityꎬ2014.[17]㊀SHAOFYꎬLIUWꎬGAODL.Effectsofthecham ̄ferandmaterialsonperformanceofPDCcutters[J].JournalofPetroleumScienceandEngineeringꎬ2021ꎬ205:108887.[18]㊀DETOURNAYEꎬDEFOURNYP.Aphenomenologicalmodelforthedrillingactionofdragbits[J].Interna ̄tionalJournalofRockMechanicsandMiningSciences&GeomechanicsAbstractsꎬ1992ꎬ29(1):13-23. [19]㊀王家骏ꎬ邹德永ꎬ杨光ꎬ等.PDC与岩石相作用模型[J].中国石油大学学报(自然科学版)ꎬ2014ꎬ38(4):104-109.WANGJJꎬZOUDYꎬYANGGꎬetal.InteractionmodelofPDCcutterandrock[J].JournalofChinaUniversityofPetroleum(EditionofNaturalScience)ꎬ2014ꎬ38(4):104-109.[20]㊀邹德永ꎬ蔡环.布齿参数对PDC钻头破岩效率影响的试验[J].中国石油大学学报(自然科学版)ꎬ2009ꎬ33(5):76-79.ZOUDYꎬCAIH.Experimentoneffectofcutterpa ̄rametersofPDCbitonrateofpenetration[J].Jour ̄nalofChinaUniversityofPetroleum(EditionofNatu ̄ralScience)ꎬ2009ꎬ33(5):76-79.[21]㊀王镇全ꎬ周悦辉.PDC钻头切削齿切削角度对破岩效果影响规律的研究[J].煤矿机械ꎬ2009ꎬ30(8):49-51.WANGZQꎬZHOUYH.Studyonrockbreakingreg ̄ulationinoptimizingcuttingangleofPDCbit[J].CoalMineMachineryꎬ2009ꎬ30(8):49-51. [22]㊀RAJABOVVꎬMISKASꎬMORTIMERLꎬetal.TheeffectsofbackrakeandsiderakeanglesonmechanicalspecificenergyofsinglePDCcutterswithselectedrocksatvaryingdepthofcutsandconfiningpressures[C]ʊIADC/SPEDrillingConferenceandExhibition.SanDiegoꎬCaliforniaꎬUSA:IADC/SPEꎬ2012:SPE151406-MS.[23]㊀GHOSHOUNIMꎬRICHARDT.Effectofthebackrakeangleandgroovegeometryinrockcutting[C]ʊISRMInternationalSymposium-5thAsianRockMe ̄chanicsSymposium.TehranꎬIran:ISRMꎬ2008:ISRM-ARMS5-2008-027.[24]㊀SHAOFYꎬLIUWꎬGAODLꎬetal.Studyonrock ̄breakingmechanismofaxe ̄shapedPDCcutter[J].JournalofPetroleumScienceandEngineeringꎬ2021ꎬ205:108922.[25]㊀LYONSNꎬIZBINSKIKꎬPAULIAꎬetal.FootageinSTACKlateralofOklahomaincreasedby185%throughnewnon ̄planarPDCcuttergeometrydevelop ̄mentandimplementation[C]ʊIADC/SPEDrillingConferenceandExhibition.FortWorthꎬTexasꎬUSA:IADC/SPEꎬ2018:SPE189638-MS.㊀㊀第一作者简介:未九森ꎬ生于1996年ꎬ现为在读博士研究生ꎬ研究方向为PDC钻头切削力学ꎮ地址:(102249)北京市昌平区ꎮE ̄mail:js_wil@qq comꎮ通信作者:高德利ꎬE ̄mail:gaodeli_team@126 comꎮ㊀收稿日期:2022-10-22(本文编辑㊀刘㊀锋)512023年㊀第51卷㊀第4期未九森ꎬ等:PDC切削齿直径对切削力的影响规律研究㊀㊀㊀。
- 1、下载文档前请自行甄别文档内容的完整性,平台不提供额外的编辑、内容补充、找答案等附加服务。
- 2、"仅部分预览"的文档,不可在线预览部分如存在完整性等问题,可反馈申请退款(可完整预览的文档不适用该条件!)。
- 3、如文档侵犯您的权益,请联系客服反馈,我们会尽快为您处理(人工客服工作时间:9:00-18:30)。
其工 作性 能 。从 文 献 [ ] 研 究 可 知 , D 1的 P C钻 头 切
削齿 的空 间几 何位 置参 数 如齿前 角 、 转 角 、 侧 装配 角 都是 通过切 削齿 ( 复合 片 ) 的定 位点 进 行 定 义 的 , 同 时定 位点 又构成 了钻头 冠 部 轮廓 线 , 因此 要对 P DC 钻头 进行立 体检 测 , 取其 加工精 度 的信 息 , 获 首先 必 须对 复合片在 钻 头胎 体 上 的定 位 点 进 行 测 量 ; 采 而 用普通 的机加 工计 量器 具无法 直接 对复 合 片定位 点
坐标值 进行测 量 , 者重 点 阐述 如何 建立 P C钻 头 笔 D 切削齿 ( 复合 片) 的空 间柱 面数 学 模 型 , 根 据 复 合 并
片的柱 面和切 削端 面 所 测 量 的点 的坐 标 , 立对 应 建 的超定方 程组 , 采用 矩 阵 左 除 法求 解 出复 合 片 的定
P:l一 锄 zlI B l一 Zl z3一 一 , I
P 一
O Z的坐标 为 P ( Y , ) 复合 片切 削 端 面 m XY z , , 上测 量的 3个不共 线 点在 H 的坐 标分 别 为 : P
H 的 坐标 分 别 (1 , 1 , 2 r ,2 h ) P ( ,3 h ) 在 复 合 片 r , h ) P (2 o ,2 , 3 o , 3 ; 柱 面上测 量 的 5个 不 共 面点 在 为 : 4 r , , 4 , 5 r , , 5 , 6 r ,6 h ) P P (4 h ) P (5 h ) P (e o , 6 , 7
1 5
第 2 卷 4
中 国石 油 大 学 胜 利 学 院 学 报
21 0 0年
第 2 期
2 2 柱面定 义 .
, { A PB P ) l P , , c. 一
动直线 L 平行 于定 方 向 且 与 定 曲线 C 相 交
而产 生的 曲面为 柱 面 , 每一 条 动 直 线 为柱 面 的直母
建立 两 个 坐 标 系 ( 1 , 个 是 钻 头 圆 柱 坐 标 系 图 )一
假设 P C钻 头 上复 合 片 的 柱 面是 一 个 标 准 圆 D
柱面, 复合 片 的切削 端面 为一标 准平 面 , 切削端 面与 柱 面 完全垂 直 。
[ 收稿 日期]2 1—32 0 00 —6
[ 者 简 介 ]黄 作 成 (9 4 ) 男 , 北襄 阳人 , 利 石 油 管 理 局 黄 河 钻 井 总 公 司工 程 师 。 17一 , 湖 胜
解析 几 何 原 理 , 导 出复合 片 的 空 间柱 面数 学模 型 ; 据 复 合 片 柱 面 和 切 削端 面 所 测 量 的 点 的 坐标 , 立 对 应 的 超 推 根 建
定线 性 方 程 组 , 用 矩 阵 左 除 法对 超 定 线性 方程 组进 行 求 解 。 编 制 出相 应 的 MAT AB程 序 , 采 并 L 有效 地 解 决 了 P C D
第2 4卷
第 2期
P C钻 头 切 削齿 定 位 点测 量 研 究 D
黄 成
( 利 石 油 管 理 局 黄 河钻 井 总公 司 , 胜 山东 东 营 2 7 0 ) 5 0 9
[ 摘 要 ] 通过分析 P C钻头的布齿情况, D 建立钻头的圆柱坐标 系O O 和直角坐标系O Y 利用空间 RH X Z.
21 0 0年 6月
中 国石 油 大 学 胜 利 学 院 学 报
J u n l fS e gi l g hn iest fP toe m o r a h n lCol eC iaUnv r i o er lu o e y
J n 2 1 u .0 0
Vo . 4 NO 2 12 .
位 点坐标 。
图 1 P C钻 头 的 坐 标 系统 D
1 建 立 坐 标 系
P C钻头 的切 削齿 布置 在 一个 旋 转 曲 面上 , D 切
2 复 合 片柱 面数 学模 型 的推 导
2 1 理 论 假 设 .
削齿 在胎 体上定 位点 即复 合片 的切削 端 面 圆心在钻 头胎 体 的冠部 曲面上 。根 椐 P C钻头 的结 构 特点 , D
由式 ( ) 求得 9可
PA —
线 , 曲线为 面 的准线 , 定 为柱 面 的直 母线 方 向 。
2 3 理论推 导 .
f 一 I一2 一 f, Y l Y 3一 1 I Xl Y3一 YlI . 23一 f
假设 P C 钻 头 上 的 某 一 个 复 合 片 定 位 点 在 D
用 坐标 ( , , ) z Y z 来表 示 。
P C钻头 是 2 D O世 纪 8 O年 代 钻 井 技 术 的重 大 创新 之一 , 已广泛应 用 于石油 勘探 开发 中 , 过几 现 经
十年 的发展 , 头 的设 计理 论 已成体 系 。但 P C钻 钻 D
头 的检测技 术一 直未得 到有 效 的发展 , 参数 直接 影响
O H, H 轴 与 钻 头轴 线 重 合 , 向 与钻 进 方 向 RO 其 方 相 同 , 半 径 R 指 向钻 头外 侧 , 角 以顺 时 针 为 极 极 正 , 量装 置基 于 此坐 标 系进行 测 量 。另 一 个 是 直 测 角 坐标 系 O Z, Z轴 同 H 轴 , y轴 方 向见 图 XY 其 X, 1 下 述计算 均相 对于本 坐标 系 。复合 片 的柱 面和 切 , 削端 面上 的任何 一点 既可用 坐标 ( ,, ) r ^ 表示 , 可 也
钻 头定 位 点 测 量 的 难 题 。
[ 关键 词] P C钻头; D 复合片定位点; 解析几何; 超定方程组; 矩阵左除法 [ 中图分类 号- 9 1 1 [ 2 . TE [ 献标 识码 ]A 文 [ 文章编 号] 6 35 3 ( 0 0 0 —0 50 1 7 —9 5 2 1 )20 1 —3