三宝2号高炉炉体系统的设计
邯宝2×3 200 m3高炉系统工程设计及采用的新技术

阀、泄压阀、流化装置、煤粉仓底部流化床及锥部流化嘴、喷煤阀、分配器以及关键的检测元件采用国外产品,其余设备均由国内供货。
(10)鱼雷罐修理库。
320t鱼雷罐修理库由冷却场、解体场、砌筑间及干燥场等作业区组成。
主要设备有:内衬解体机、装载机、切砖机、磨砖机、喷补机、给料、干燥设备等。
(11)铸铁机。
为解决高炉开炉初期生产的不适宜炼钢的铁水及炼钢车间定期检修时生产的一部分铁水,在作适当产能调整的同时,考虑设置铸铁机。
铸铁机主要技术参数:链轮中心距(斜长)74.48m;生产能力260t/h;铸铁机生产率70%;链带运行速度12~19m/min;铸铁块重量6×8kg。
2高炉系统工程公辅设施配置2.1公辅设施组成公辅设施主要有:机械化贮运(原、燃料供应设施、原煤贮运、水渣贮运)、热力设施(鼓风机站、冷风、蒸汽、压缩空气输配)、燃气设施(高炉煤气净化系统、TRT、高炉煤气、转炉煤气、焦炉煤气、氧气和氮气输配)、给排水设施(软水、净化水、工业水、消防水、生活水、雨水等)、通风除尘设施、空调采暖设施、电力输配、电气传动、仪表、计算机、自动化控制、电讯、总图运输、铁路信号、消防、安全、卫生、环保设施、地上、地下综合管网等系统。
2.2主要的公辅设施配置(1)机械化贮运。
由原燃料供应及返矿、粉焦运输、原煤贮运、水渣贮运组成。
烧结矿从烧结厂,球团矿、块矿、杂矿从原料场,通过3条皮带(B=1 200mm,Q=1 200t/h)运至高炉矿槽内;焦炭从焦化厂,通过l条皮带(B=1 400mm,Q=400t /h)运至焦槽内。
返矿和粉焦用皮带或汽车运输。
2座高炉喷吹用的原煤在一个面积为156 m×35 131的干煤棚内贮存,通过配煤后经皮带送入原煤仓。
水渣通过皮带送贮存量约2.2万t的水渣堆场,可用火车或汽车运出。
(2)热力设施。
2座高炉配鼓风机组3台,2台进口,1台国产,型号全部为AV90—15电动全静叶可调轴流压缩机组。
2000m3高炉本体设计
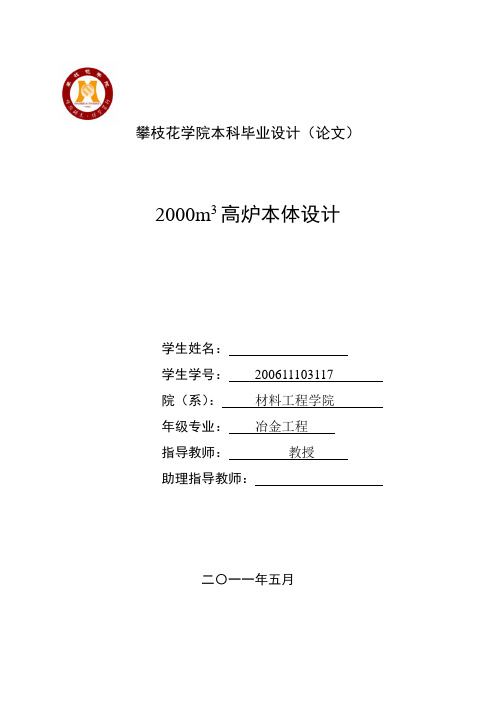
攀枝花学院本科毕业设计(论文)2000m3高炉本体设计学生姓名:学生学号:200611103117院(系):材料工程学院年级专业:冶金工程指导教师:教授助理指导教师:二〇一一年五月摘要高炉炼铁的历史悠久,炼铁技术日臻成熟,是当今主要的炼铁方式。
高炉作为炼铁工艺的主体设备,其结构的合理性对炼铁的工艺操作、生产技术指标以及自身的寿命都有十分重要的影响。
根据攀枝花钒钛磁铁矿的高炉冶炼特点,通过进行配料计算和物料平衡计算,设计了2000m3高炉本体。
设计过程除考虑通常的高炉设计方案外,还考虑了攀枝花钒钛磁铁矿多年高炉冶炼的一些生产实践经验。
所设计完成的高炉本体炉缸直径为9.88m、炉腰直径为10.97m、高径比为2.55、有效高度为27.97m;高炉基础的基墩高1.9m、直径13.53m、基座高2m;采用碳砖加高铝砖综合炉底、全碳砖炉缸;冷却设备的设计为水冷炉底、炉缸和炉底采用三段光面冷却壁、炉身采用镶砖冷却壁;高炉钢结构采用炉体框架式结构,最后采用CAD绘制出高炉本体图。
关键词高炉,高炉本体,炉型,钒钛磁铁矿ABSTRACTThe blast furnace iron-making has a long history which has become the main way of iron manufacture. As the main equipment of ironmaking, the blast furnace plays the most important role. The rationality of the blast furnace’s structural design has great influence on the process operations and technique level of ironmaking and it will decide the useful life of the blast furnace itself. According to the characteristics of the vanadic titanomagnetite smelted in BF in Panzhihua, the 2000m3blast furnace body was designed in this subject based on the calculations of the burden control and the material balance. Besides common design plans of the blast furnace, some practical experiences of the vanadic titanomagnetite smelted in BF was considered in this subject. The basic information of the blast furnace which has been designed is as following: the diameter hearth is 9.88m, the belly diameter is 10.97m, the aspect ratio of the furnace is 2.55, the effective height is 27.97m. As to the blast furnace foundation, the height of under hearth is 1.9m, the diameter of the under hearth is 13.53m, the furnace pad or foundation is 2 m. The hearth bottom adopts carbon bricks and high alumina bricks synthesize technic, the hearth just builds up with carbon bricks. The cooling device is designed to water-cooled hearth bottom, three segments mill finish stave is used for the hearth and hearth bottom, the stack uses inlaid brick stave to make it cool down. The steel structure of the BF adopts frame-type for the furnace body. Finally, the diagram of BF body was gained by using the CAD drawing tools.Key words blast furnace,BF body,furnace type,V-Ti magnetite目录摘要 (I)ABSTRACT (II)1 绪论 (1)1.1 课题背景 (1)1.2 攀枝花钒钛磁铁矿特点 (2)1.3 课题设计的内容及意义 (2)2 高炉设计原始数据 (4)2.1 矿石原料成分 (4)2.2 配矿比 (4)2.3 焦炭成分 (4)2.4 喷吹煤粉成分 (4)2.5 生铁成分 (4)2.6 元素分配比 (5)2.7 炉渣碱度 (5)2.8 工艺技术指标 (5)3 高炉设计工艺计算 (6)3.1 配料计算 (6)3.1.1 根据铁平衡求铁矿石需求量 (6)3.1.2 根据碱度平衡计算石灰石用量 (6)3.1.3 终渣成分 (6)3.1.4 生铁成分校核 (7)3.2 物料平衡计算 (8)3.2.1 需要补充的原始条件 (8)3.2.2 根据碳平衡计算风量 (8)3.2.3 计算煤气成分及数量 (9)3.2.4 编制物料平衡表 (11)4 高炉内型设计计算 (12)4.1 高炉炉型 (12)4.2 高炉炉型设计原则 (13)4.3 高炉内型尺寸确定 (13)4.3.1 炉缸直径 (14)4.3.2 炉腰直径 (14)4.3.3 炉喉直径 (15)4.3.4 铁口中心线到炉底砌砖之间的距离 (15)4.3.5 炉缸高度 (15)4.3.6 炉腹角与炉腹高度 (15)4.3.7 炉身角与炉身高度 (16)4.3.8 有效高度、炉喉高度、炉腰高度 (16)4.3.9 风口、渣口、铁口数 (17)4.3.10 炉容校核 (17)5 高炉本体及主要设备选择 (19)5.1 高炉基础 (19)5.1.1 高炉基础设计条件 (20)5.1.2 基墩设计计算 (20)5.1.3 基座设计 (20)5.2 高炉内衬结构 (21)5.2.1 炉底 (21)5.2.2 炉缸 (22)5.2.3 炉腹 (22)5.2.4 炉腰 (23)5.2.5 炉身 (23)5.2.6 炉喉 (23)5.3 高炉冷却设备设计 (24)5.3.1 冷却设备的作用 (24)5.3.2 冷却介质 (24)5.3.3 高炉各部位冷却设备设计 (24)6 高炉钢结构设计 (26)6.1 炉壳 (26)6.1.1 炉壳厚度的计算 (26)6.1.2 炉壳折点的确定 (27)6.2 炉体平台及走梯 (27)6.3 高炉本体钢结构类型 (28)6.4 高炉主要热工检测仪表 (29)结论 (30)参考文献 (32)致谢 (34)1 绪论1.1课题背景尽管21世纪是一个信息的时代。
高炉结构工程施工设计方案

目录1 编制说明21.1工程名称:21.2工程性质:21.3编制依据22 工程概况32.1工程简介32.2工程容32.3建设单位:32.4设计单位:32.5施工单位:43. 施工组织43.1施工组织模式43.2施工组织机构44施工准备44.1组织准备44.2技术准备54.3资源准备54.4施工条件与场地64.5施工用电、用水74.6测量控制网74.7施工现场临设安排74.8主要施工机械设备与材料见附表74.9施工劳动力安排计划见附表75 钢结构施工方案75.1构件来源与运输85.2基础复测85.3材料检验与构件制作85.4现场拼装105.5主体结构安装155.6钢结构现场焊接205.7钢结构吊装方法245.8高炉除尘和矿槽除尘管道制安256 质量技术保证措施307 现场文明施工管理348 安全方针与安全保护措施358.1安全方针与目标358.2安全保护措施368.3雨期施工安全409 环境保护管理4010 施工进度计划41西钢炼铁工艺优化升级系统改造工程1260m³高炉钢结构制作安装施工组织设计1 编制说明1.1 工程名称:西钢炼铁工艺优化升级系统改造工程1.2 工程性质:工艺优化升级系统改造工程1.3编制依据1.3.1 本施工组织设计依据国家建设施工有关法律法规;1.3.2 本施工组织设计依据国家建设施工的专业技术标准和规;1.3.3 三冶公司与西林钢铁签订的施工合同;1.3.4 三冶公司的施工组织总设计;1.3.5 中冶工程技术的施工图;1.3.6 国家与行业相关标准《钢结构工程施工质量验收规》GB50205-2001《炼铁机械设备工程安装验收规》GB50372-2006《工业金属管道工程施工与验收规》GB50235-97《现场设备工业管道焊接工程施工与验收规》GB50236-98《建筑防腐工程施工与验收规》GB50212-2002《工业金属管道工程质量检验评定标准》GB50184-93《冶金机械设备安装工程施工与验收通用规定》YBJ201-882 工程概况2.1 工程简介西林钢铁集团拟新建2座1260m³高炉,分二期建设,本设计为一期建设,年产铁水94.8万吨,能源介质为1座1260m³高炉的能耗指标。
第3章 高炉本体设计(4).ppt
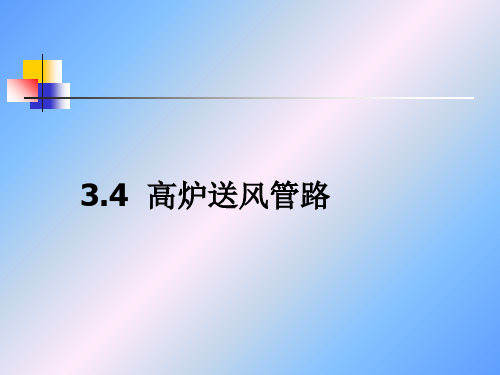
(5)弯管的作用是转变送风支管方向和 连接直吹管,设有观察孔和下部拉杆。
2. 张紧装置:
(1)作用: 稳定和紧固送风支管,并使直吹管
紧压在风口小套上。 (2)组成: 包括吊杆、拉杆、松紧法兰螺栓等。
3.送风支管附件:
包括托座、起吊链钩、观察孔等。 (1)托座固定在炉壳上,用来固定中部 拉杆。 (2)起吊链钩用于更换风口时使弯管和 直吹管成振摆状运动,便于更换风口。 (3)观察孔用来观察风口区燃烧情况。
(2)必须按设计要求进行水压和气密性试验。 (3)要求喷吹管中心线与直吹管管体中心线的 夹角符合设计要求,一般夹角为12°~14°左 右。
3.4.4风口装置
风口(小套)与风口中套、风口大 套装配在一起,加上冷却水管等其它部件, 形成高炉的风口装置。
风口装置结构示意图
1-风口中套冷水管;2-风口大套密封罩;3-炉壳;4-抽气孔;5-风口大套; 6-灌泥浆孔;7-风口小套冷水管;8-风口小套;9-风口小套压紧装置 10-
21, 2021
谢谢观赏
You made my day!
我们,还在路上……
3.4 高炉送风管路
3.4.1热风总管与围管
1. 作用: (1)热风总管:输送热风
(2)热风围管ቤተ መጻሕፍቲ ባይዱ将热风总管送来的热 风均匀地分配到各送风支管中。
2. 材质:
均由钢板焊成,管中有耐火材料 筑成的内衬。
3. 直径的确定:
热风总管与热风围管的直径相同, 由下式计算:
式中:
d 4Q
v
d ——热风总管或热风围管内径,m;
3.4.3 直吹管
直吹管是高炉送风支管的一部分, 尾部与弯管相连,端头与风口紧密相连。 1. 组成:
酒钢1~#、2~#高炉喷煤系统扩能改造设计
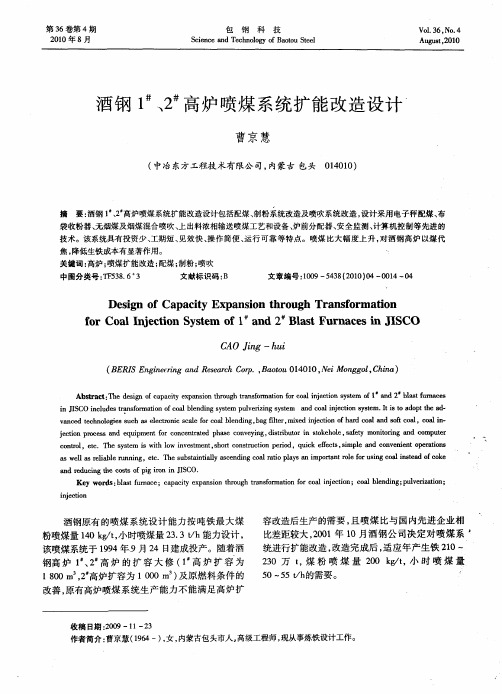
a l a l b er n i g t .T es b ti t l c n n o t ly o tn oe fru i gc a se d o o e s we r i l u nn ,ec h u san i ya e d gc a r i pa sa i ra t l sn o li t a f k ls e a l a s i la o n mp r o n c
c nto ,ec Th y tm s wih lw n e t n , h r o sr ci n peid,quc fe t , i pe a n n e to e ain o rl t. e s se i t o iv sme t s otc n tu to ro i k e c s sm l nd co ve i n p r t s o
焦, 降低生铁成本有显著作用。 关键词 : 高炉 ; 喷煤扩 能改造 ; 配煤 ; 制粉 ; 喷吹
中 图分 类 号 :F 3. T586 3 文 献标 识码 : B 文 章 编 号 :0 9— 4 8 2 1 )4—0 1 0 10 5 3 (00 o 04— 4
t
De in fCa ct p nso h o g a so m a i n sg o pa iy Ex a in t r u h Tr n f r to
曹 京 慧
( 中冶 东方工程技 术有 限公 司, 内蒙 古 包头 04 1 ) 100
摘
要: 酒钢 1、 高炉喷煤系统扩能改造设计包括 配煤 、 系统改造及喷吹系统改造 , 采用 电子秤配煤 、 2 制粉 设计 布
袋 收粉器 、 无烟煤及烟煤混合喷吹 、 上出料浓相输送喷煤工艺和设备 、 炉前 分配器 、 安全监 测、 计算机控制等先进 的 技术 。该系统具有投资少 、 工期短 、 见效 快 、 操作简便 、 运行 可靠等 特点。喷煤 比大幅度上 升 , 酒钢 高炉 以煤代 对
安钢炼铁厂高炉工艺简介

2、工艺流程
4800m3高炉工艺布置图
3、主要工艺参数
序号 1 2 3 4 5 6 7 8 9 10 12 13 14 15 16 17 18 项目 有效容积 利用系数 焦比 煤比 富氧率 熟料率 烧结矿配比 球团矿配比 块矿配比 入炉矿品位 入炉风量 热风温度 炉顶温度 炉顶压力 渣铁比 日产生铁 年产生铁 单位 m3 t/(m3·d) kg/t铁 kg/t铁 1# 2200 2.36 350 169 5.10% 95% 80% 15% 4.50% 55.91% 4200 1185 150~260 0.21 368 5200 187 3# 4800 2.3 305 200 4% 86% 91% 75% 73.30% 16% 13% 9% 13.60% 59.20% 55.47% 7000 5800 1250 1250 150~260 150~250 0.25 0.22 310 365 10918 6500 382 237
1#、2#高炉,矿、焦槽单独设置,各用一条运 输胶带机(供矿皮带和供焦皮带),共用一条上 料主皮带,构成两个独立、并列的系统。
4.1矿焦槽系统
3#高炉,矿、焦槽呈双排布置,不设中间斗, 矿石、焦炭在槽下筛分称量后共用一条胶带机运 入上料主胶带输送机,然后运至高炉炉顶设备。
4#、5#高炉,矿、焦槽单独设置,矿石筛分 后经皮带机运输到两个矿石集中斗,焦炭由焦槽 直接进入焦炭集中斗,称量后装入料车,然后运 至高炉炉顶设备。
4.5炉体系统
4.5炉体系统
4.5.4炉底、炉缸内衬
2200m3 和2800m3 高炉采用陶瓷杯炭砖水冷炉底炉缸结构。 炉底中心下部立砌两层国产炭砖,其中下层为半石墨炭 砖,上层为微孔炭砖;上部砌两层低导热刚玉莫来石砖,炉 缸内侧砌低导热刚玉莫来石砖,外侧炉缸采用进口微孔炭 砖,在进口微孔炭砖与风口组合砖之间砌筑3层国产微孔炭 砖;在炉缸,炉底交接处采用加厚陶瓷质耐火材料和进口 微孔炭砖砌筑结构。 在风口区采用大块组合砖砌筑,以加强结构的稳定性; 铁口通道采用大块和小块相结合特殊组合砖结构。
梅钢二号高炉全外购焦生产实践
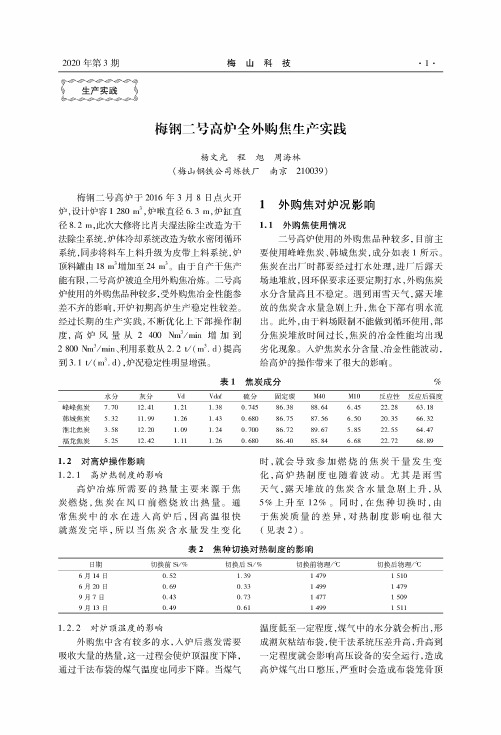
2020年第3期梅山科技-1-梅钢二号高炉全外购焦生产实践杨文光程旭周海林(梅山钢铁公司炼铁厂南京210039)梅钢二号高炉于2016年3月8日点火开炉,设计炉容1280m3,炉喉直径6.3m,炉缸直径&2m,此次大修将比肖夫湿法除尘改造为干法除尘系统,炉体冷却系统改造为软水密闭循环系统,同步将料车上料升级为皮带上料系统,炉顶料罐由18m3增加至24m3。
由于自产干焦产能有限,二号高炉被迫全用外购焦冶炼。
二号高 炉使用的外购焦品种较多,受外购焦冶金性能参差不齐的影响,开炉初期高炉生产稳定性较差。
经过长期的生产实践,不断优化上下部操作制度,高炉风量从2400Nm3/min增加到2800Nm3/min、利用系数从2.2t/(m3.d)提高到3.10(m3.d),炉况稳定性明显增强。
1外购焦对炉况影响1.1外购焦使用情况二号高炉使用的外购焦品种较多,要使用峰峰焦炭、韩城焦炭,成分如表1所示。
焦炭在出厂时都要经过打水处理,进厂后露天,环期水,外购焦水分含量高且不稳定。
遇到雨雪天气,露天堆的焦水量上升,焦有水出。
此外,由于料场限制不能做到循环使用,部焦,焦的冶金性能劣化现象。
入炉焦炭水分含量、冶金性能波动,给高炉的操作带来了很大的影响。
表1焦炭成分%水分灰分Vd Vdaf硫分固定碳M40M10反应性反应后强度峰峰焦炭7.7012.41 1.21 1.380.74586.3888.64 6.4522.2863.18韩城焦炭 5.3211.99 1.26 1.430.68086.7587.56 6.5020.3566.32焦 3.5812.20 1.09 1.240.70086.7289.67 5.8522.5564.47焦 5.2512.42 1.11 1.260.68086.4085.84 6.6822.7268.891.2对高炉操作影响1.2.1高炉热制度的影响高炉冶炼的量于焦炭燃烧,焦炭在风口前燃烧放出热量。
3200m3高炉本体及渣铁处理系统设计

中文摘要目前我国钢铁企业蓬勃发展,许多钢铁厂都在新建或扩建高炉,高炉逐渐向大型化发展,因此在原有高炉的基础上引进新技术对高炉适当的改造设计是必要的。
由于设计的需要,某些数据采自施工现场工长、炉长和工人的经验数据,许多参数的设计以理论数据为参照、以实际地区实际原料条件下的情况进行选定、以实际应用参数为基准。
本说明书采用包头地区原料条件下,对3200m³高炉本体进行设计,其设计内容主要包括:高炉炉型设计计算、高炉炉衬选择计算、高炉冷却系统设计、高炉钢结构及基础设计、出铁场设计、炉前设备的选择确定、铁水处理系统设计、炉渣处理系统设计、绘制高炉本体立剖图和高炉出铁场平面布置图。
高炉设计主要参数如下:利用系数-2.3;焦比-370㎏;煤比-170㎏;炉渣碱度-1.03;高炉高颈比-2.19;高炉有效高度-m;日产铁-7360吨。
本高炉本体以五段炉型为标准,以适应原料条件为前提,冶炼过程能够顺行为保障,日产量最大,质量最优,能耗最低,寿命最长为目标进行设计。
为达到以上目标,与传统高炉相比,本高炉炉型驱于矮胖型。
为进一步提高高炉寿命,炉底炉缸采用全碳砖结构,这是因为包头矿含有高氟,对炉缸炉底的侵蚀严重。
炉底采用了5段低络铸铁光面冷却壁,炉腹、炉腰及炉身下部采用铜冷却壁冷却,它的冷却强度大、对砖衬支撑作用强、损坏后可更换。
高炉钢结构采用炉体框架式结构, 它的优点在于取消了炉缸支柱,风口平台宽敞,炉前操作方便。
出铁场为环形出铁场,设置四个铁口连续出铁,它的优点在于布置紧凑,占地面积少,场地有效利用率高,自然通风条件好。
渣的处理采用目前我国大高炉都使用的热法INBA渣处理系统,其工作效率高,对环境污染少。
关键字:高炉本体渣铁处理系统设计内容AbstractAt present, China's iron and steel industry is flourish, and many iron and steel plant is building or expansion of blast furnace, blast furnace is gradualateing developed to large-scale, and therefore the basis of the original blast furnace to introduce new technology on the blast transformation and the appropriate design is necessary. As the design needs of some of the datas collected from the plant and the works , a long furnace empirical data, many of the design parameters to the theoretical data for the reference to the actual areas of raw materials under the conditions of the actual situation in selected parameters in the practical application of basement.Baotou region of the specification of raw materials used under the conditions of the blast furnace of 3200m ³ to design, its design includes:Design and calculation of blast furnac e、Calculation and option of blast furnace linin g、Design of blast furnace cooling syste m、Blast furnace and basic steel structure desig n、Design of cast hous e、Determine the choice of steel equipmen t、Iron water treatment system desig n、Slag handling system desig n、Draw essence of blast furnace autopsy charts and blast furnace Layout field. The main blast furnace design parameters are as follows: use of coefficient of-2.3; coke ratio-370㎏; coal than-170㎏; slag basicity-; blast high neck than-2.19; highly effective-29.98; Day total of iron production-7360t.The blast furnace ia design as five as the standard to meet the prerequisite conditions for raw materials, smelting process to shun acts of protection, the largest output, the quality of the optimal energy consumption and the lowest life expectancy of up to design goals. To achieve these objectives, as compared with the traditional blast furnace, the blast furnace to reduce the ratio of height to diameter, or blast furnace in the squat-type flooding. To further enhance the life of a blast furnace, hearth to adopt advanced technology ceramic cup with hot bricks small carbon composite structure, which is refractory hearth with an important progress. Bottom using a 5-walled gray cast iron cooling smooth, belly stove, stove and furnace are lower lumbar copper cooling stave, and its cooling intensity, supporting the role of thebrick lining, and damage can be replaced. Market for the iron ring of iron field, set up four consecutive iron taphole, it is the layout of the advantages of compact, small area, high space utilization, natural ventilation conditions. The use of slag handling large blast furnace in China are used Hing Hong - INBA slag thermal processing system, its high efficiency and less environmental pollutionKey word: blast furnace body slag handling system design contents目录中文摘要 (1)Abstract (2)目录 (4)第一章文献综述 (7)1.1 我国钢铁行业发展现状 (7)1.2 高炉炉型发展史 (7)1.3 国外高炉发展现状 (8)1.4 我国高炉发展现状 (9)1.5 高炉炉体系统 (11)1.5.1 炉喉 (12)1.5.2 炉身 (12)1.5.3 炉腰 (13)1.5.4 炉腹 (13)1.5.5 炉底、炉缸 (13)1.6 高炉内衬 (14)1.6.1 我国高炉内衬发展过程 (14)1.6.2 高炉炉体内衬结构基本形式和发展现状 (15)1.6.3 高炉各部位内衬发展趋势 (18)1.6.4 高炉用各种耐材的介绍 (19)1.7 高炉的冷却 (21)冷却设备 (21)1.7.2 冷却介质 (24)1.7.3 冷却方式介绍 (26)1.8 高炉钢结构及基础 (27)1.8.1 高炉本体钢结构类型 (27)1.8.2 炉壳 (28)高炉基础 (29)1.9 渣铁处理系统 (30)1.9.1 风口平台类型的介绍 (30)1.9.2 出铁场类型及发展趋势 (30)1.9.3 渣铁处理方法的介绍 (31)1.9.4 几种常用炉渣粒化工艺的比较 (32)1.10 本高炉本体设计思想 (33)第二章工艺计算 (33)2.1 原料条件 (34)2.1.1 矿石成分 (34)2.1.2 燃料成分 (35)2.1.3 其它条件 (36)2.2 配料计算 (36)2.2.1 吨铁矿石用量计算 (36)2.2.2 石灰石的用量计算 (37)2.3 物料平衡计算 (38)2.3.1 鼓风量的计算 (39)2.3.2 煤气组成及煤气量计算 (40)2.3.3 考虑炉料的机械损失,实际入炉量 (42)2.3.4 物料平衡表 (42)2.4 全炉热平衡计算 (42)2.4.1 热收入 (42)2.4.2 热支出 (43)2.4.3 列热平衡表 (45)2.5 理论焦比的计算 (46)第三章高炉炉型设计计算 (48)3.1 炉型的计算 (48)3.1.1 铁口 (48)3.1.2 渣口 (49)3.1.3 风口 (49)3.1.4 日产铁量的计算 (50)3.1.5 死铁层厚度 (50)3.1.6 炉缸尺寸计算 (50)3.1.7 炉腰直径炉腹角炉腹高度 (50)3.1.8 炉喉直径炉喉高度炉身高度炉腰高度 (51)3.2 炉容的校核 (51)第四章高炉各部位耐火材料的选择及计算 (53)4.1. 各部位砖衬的选择 (53)4.1.1 炉底、炉缸部位的选择 (53)4.1.2 炉腹部位的选择 (53)4.1.3 炉腰部位的选择 (53)4.1.4 炉身及炉喉部位的选择 (54)4.2 各部位砖量计算 (54)4.2.1 炉腹的计算 (55)4.2.2 炉腰的计算 (56)4.2.3 炉身的计算 (56)4.3 砖衬的砌筑 (57)4.4 高炉炉体用耐火材料性质及参数表 (58)第五章冷却介质及冷却设备的选择 (66)5.1 各部位冷却器的配置 (66)5.2 软水密闭循环系统 (66)5.2.1 高炉软水闭路冷却系统工作原理 (67)5.2.2 软水闭路冷却的特点 (67)5.2.3 硬水的软化过程 (68)第六章高炉钢结构及高炉基础 (69)第七章渣铁处理系统 (70)7.1 风口平台及出铁厂 (70)7.1.2 出铁场的选择 (70)7.1.3 圆形出铁厂与矩形出铁厂的比较 (70)7.1.4 环形出铁场的优点 (71)7.2 炉前设备 (72)7.2.1 开铁口机 (72)7.2.2 液压泥炮 (72)7.2.3 摆动流嘴 (72)7.2.4 炉前运输工具 (72)7.2.5 铁水罐对位 (73)7.3 铁水的处理 (73)7.4 炉渣的处理 (74)7.4.1 炉渣处理方法的选择 (74)7.4.2 冷热INBA法比较 (74)7.4.3 因巴(NIBA)法炉渣粒化装置工艺流程 (75)参考文献 (76)专题论述—高炉长寿的探讨 (78)致谢 (84)第一章文献综述1.1 我国钢铁行业发展现状对任何国家而言,钢铁行业都是一个非常重要的基础行业,一个国家的经济要腾飞,社会的进步都直接地依赖钢铁行业的发展。
- 1、下载文档前请自行甄别文档内容的完整性,平台不提供额外的编辑、内容补充、找答案等附加服务。
- 2、"仅部分预览"的文档,不可在线预览部分如存在完整性等问题,可反馈申请退款(可完整预览的文档不适用该条件!)。
- 3、如文档侵犯您的权益,请联系客服反馈,我们会尽快为您处理(人工客服工作时间:9:00-18:30)。
文档从互联网中收集,已重新修正排版,word格式支持编辑,如有帮助欢迎下载支持。 1如有帮助欢迎下载支持 三宝2号高炉炉体系统的设计 董训祥 (中冶南方工程技术有限公司,武汉430223) 摘 要 三宝钢铁2#高炉充分采用了国内外一系列先进、成熟、实用的技术,设计了合理的炉型和内衬结构;采用了砖壁合一、薄壁内衬新技术、全冷却壁形式;采用了投资省、成本低、效率高的联合软水密闭循环冷却系统;根据原料条件在炉底设置了功能可靠的排铅槽;建立功能齐全的炉体检测自动控制系统。 关键词 高炉炉体;长寿;联合软水;设计 福建三宝钢铁股份有限公司200万吨钢铁项目一次规划2座1080m3高炉,每座1080m3高炉年产铁水105万吨,分期设计,分期建设。本次一期2#高炉的设计以“先进、实用、可靠、成熟、环保”为原则,结合国内外先进、可靠的成熟技术,做到高产、稳产、低耗、长寿四个方面的统一。 1主要技术特点 三宝钢铁2#高炉炉体系统的设计充分利用了国内外同行的先进技术和成熟工艺,并结合三宝钢铁的实际情况进行设计,确保高炉稳定向炼钢输送铁水、提供产品市场竞争力的同时,延长高炉寿命。三宝钢铁2#高炉设计寿命≥12年,主要技术特点如下: (1)采用适当矮胖、适宜强化冶炼的操作炉型,有利于实现稳定、顺行和高产; (2)砖壁合一、薄内衬全冷却壁结构,大型高炉的主流技术方案; (3)铸铁冷却壁、铸钢冷却壁、铜冷却壁分区使用,确保高炉配置合理、可靠、经济; (4)高炉冷却系统采用联合全软水密闭循环系统,该系统配置合理优化、冷却强度高、冷却系数大、补充水量少、投资省、运行成本低、各种功能完善,布置简单、检修维护方便。 (5)根据三宝钢铁的原料条件设置了排铅槽,对于提高高炉一代炉龄、改善炉前工作环境、强化高炉冶炼、增创经济效益等具有重大意义。 (6)完善的内衬、冷却壁、软水系统的检测、监测、控制系统; 2 高炉内型 合理的高炉内型既能保证炉料顺行,又能使煤气的热能和化学能充分利用,可使高炉获得高产、稳产、低耗、长寿的效果。现代高炉内型的设计特点主要表现在大炉缸、多风口、适当矮胖、减小炉身及炉腹角、加深死铁层等方面,其目的是为了改善料柱透气性、改善煤气分布、提高喷煤比、适当抑制边缘、吹透中心,以实现高产、长寿、低耗、顺行的目的。 本高炉采用砖壁合一、薄壁内衬结构的高炉炉型,在设计上就考虑了实际生产中出现的问题,设计炉型基本上就是操作炉型,一代炉役其操作炉型基本维持不变。 根据以上前提,同时总结国内外同类容积优秀高炉的内型尺寸,并结合三宝钢铁实际的原燃料条件,确定了本高炉内型尺寸,列于表2中。 3 冷却系统 =高炉寿命在很大程度上取决于炉体冷却系统的冷却效率,而高炉冷却效率的高低主要看炉墙的热面温度能否稳定的降低到化学侵蚀及机械破损临界温度以下,形成稳定的渣壁[1]。 从我国高炉生产实践来看。影响高炉寿命的主要问题是炉底、炉缸以及炉身下部的寿命问题,例如:炉缸因蘑茹状侵蚀,产生炉缸烧穿。炉身下部、炉腰等部位的冷却壁过早大量损坏,失去砖衬,造成炉壳开裂,影响高炉寿命,因此,为了达到高炉高产、长寿的目的,除了合理的高炉炉型、优质的耐火材料、正常的高炉操作制度外,高效、稳定的高炉冷却系统将成为关键。 3.1 冷却设备 在现代高炉普遍采用诸如优质的陶瓷杯、微孔炭砖、超微孔炭砖等技术而使得炉底、炉文档从互联网中收集,已重新修正排版,word格式支持编辑,如有帮助欢迎下载支持。 2如有帮助欢迎下载支持 缸寿命得以基本解决的情况下,冷却设备的寿命直接决定了一代高炉的寿命。高炉炉体冷却设备主要有冷却板、冷却壁和板、壁复合结构。全冷却壁形式由于具有冷却面积大、冷却均匀、维持炉型好、投资省、安装方便等诸多优点而得到了广泛应用。 本设计选择全冷却壁结构型式,采用最新的砖壁合一技术。由于炉内纵向各区域不同的工作条件和热负荷大小,炉内不同区域采用了不同材质和不同结构形式的冷却壁。炉腹、炉腰及炉身下部等高热负荷区域分别采用铜冷却壁和双层水冷铸钢冷却壁,其主要特征见表3。 (1)炉底、炉缸区:风口以下采用共3段冷却壁,均为光面低铬铸铁冷却壁,每块冷却壁水管为4进4出,竖直排列,水管直径均为φ76×6mm。在两个铁口区域冷却壁水管为7进7出。 (2)风口带:采用光面球墨铸铁冷却壁,本段冷却壁水管为6进6出或7进7出,水管直径均为φ76×6mm。 (3)炉腹、炉腰:炉腹1段(第5段)、炉腰1段(第6段)采用单层水冷4通道铜冷却壁,冷却壁热面设有燕尾槽。冷却水通道采用长圆形通道(80 mm×35 mm),适当增加通道面积,提高了冷却水管比表面积;同时降低冷却水流速,减小阻损[2]。 (4)炉身下部:炉身下部3段(第7~9段),采用双层水冷镶砖铸钢冷却壁,冷却壁热面设有燕尾槽,冷却壁内竖直管直径为φ76×6mm,蛇形管直径为φ76×6mm。 (5)炉身中上部:炉身中上部共5段冷却壁,材质均为球墨铸铁。第10~12段为单层水冷镶砖铸铁冷却壁;第13~14段为倒扣式镶砖铸铁冷却壁,壁体内侧面为高炉内型。 冷却壁的固定方式:采用中冶南方专有技术固定型式,第1~4段冷却壁由于炉底炉缸温度波动范围小,采用4点螺栓固定型式,但冷却壁水管与炉壳间设置变形补偿套管;第5~6段铜冷却壁采用固定销固定,配有4个螺栓进行安装定位,并在冷却壁中部设有固定套筒以防止铜冷却壁高温下受重力作用而发生变形;第7~14段冷却壁采用特殊的固定点和滑动点、浮动点相结合的固定方式,冷却壁水管与炉壳间加膨胀器,少量水管根据需要设置变形补偿套管,从而避免因炉壳与冷却壁问的温差不同导致水管剪断而出现破漏的情况[3]。 由于铸铁冷却壁不能很好地满足高炉长寿的需要,而铜冷却壁性能虽好,但造价太高,不可能被大量应用。而铸钢冷却壁作为一种新型冷却设备近年来被频繁应用于高炉,并以其高性价比的优势受到用户的青睐。且从马钢、济钢、南钢高炉中铸钢冷却壁实际应用情况来看[4-8],铸钢冷却壁应用的优势非常明显,因此本高炉在热负荷较大的炉身下部区域采用了3段铸钢冷却壁,以保证冷却壁热面温度足够低,便于结渣挂渣,渣皮脱落后也能快速恢复,而达到可靠、经济、长寿的目的。 3.2冷却水系统 除设备制造质量外,高炉冷却设备的寿命的长短与高炉冷却系统的好坏直接相干,一定程度上决定了整座高炉的寿命。随着冷却水技术的发展和国家产业政策的要求,高炉冷却水技术由工业水直流冷却、汽化冷却、净化水冷却、软水和净化水联合冷却,向独立软水闭路循环冷却和联合软水密闭循环水冷却系统演变。软水密闭循环冷却系统具有不结垢、无污染、冷却强度高、冷却效果好、余压完全得到利用、能耗低、泄漏少、补充水很少、自动化程度高、运行安全可靠等诸多优点,符合现代大型高炉发展的要求,所以在国外大中型高炉上已得到了日益广泛的应用。 本设计采用联合软水密闭循环系统,采用并联加串联的方法将原有三个独立的系统合成一个系统,充分发挥软水不结垢,可适当提高水温差的优点,从而达到节省投资、减少水量、节约能源的目的。 冷却壁、炉底、风口小套、中套、热风阀、倒流休风阀通过串联和并联的方式组合在一个系统中,系统总循环水量2880m3/h,具体方案是:从软水泵站出来的软水在炉前一分为文档从互联网中收集,已重新修正排版,word格式支持编辑,如有帮助欢迎下载支持。 3如有帮助欢迎下载支持 二,其中冷却炉底512m3/h,冷却壁直冷管2368m3/h,两者回水进入冷却壁回水总管。从冷却壁回水总管出来的软水一分为二,其中1830m3/h水回到总回水管,另外有1050m3/h的水进入第一组增压泵增压,增压后的水一部分直接供热风阀使用(350m3/h),另一部分(700m3/h)直接进入下一组增压泵进行二次加压,供风口小套使用。风口小套的回水部分再供给风口中套使用(500m3/h);热风阀及风口系统的回水与上述1830m3/h水量一起回到总回水管,经过脱气罐脱气和膨胀罐稳压,最后回到软水泵房,经过二次冷却,再循环使用。 另外,本高炉还设置了一路中压工业净化水循环系统和一路中压工业净化水直排系统,同时还配备了炉体冷却安全措施。中压工业净化水循环系统供炉顶齿轮箱、炉顶液压站、红外摄像仪等冷却用。中压工业净化水直排系统供风口事故水、炉顶洒水、螺旋清灰机、各平台洒水、炉役后期炉壳喷水、风口平台冲洗等用水。炉体冷却安全措施为: (1)设置风口事故水处理系统:当个别风口产生微漏时,微漏风口可通过专门设置的相应管路切换成工业水冷却,水压0.8MPa,当风口破损到一定数量或定期休风时,集中一次更换,更换后的风口再转换回软水冷却。 (2)配备柴油机泵组临时启用系统:软水密闭循环系统及工业净循环水系统除备用电动泵组外,还分别设置有柴油机泵组,当停电及电动泵事故时,柴油机组能在10秒钟内自动启动,维持水系统运行。 (3)自动转汽化冷却功能:当因停电及其它事故引起电动泵不能正常运行时,整个软水系统可自动转化成汽化冷却状态,可维持时间~30分钟,当柴油泵组启动运行后,软水系统自动转换成正常密闭循环冷却状态。 4 高炉内衬 三宝钢铁2#高炉在内衬设计上充分考虑高炉各部位不同的工作条件和侵蚀机理,有针对性的选用耐火材料,并在结构上加强耐火砖衬的稳定性。 炉底、炉缸是高炉长寿的关键区域,炉底、炉缸耐材的损坏,意味着一代炉龄的结束,特别是铁口及铁口以下的异常侵蚀区,越来越成为制约高炉长寿的最重要因素。碱金属和锌对高炉内衬有严重的侵蚀破坏作用。锌甚至是炉缸炭砖侵蚀破坏的主要因素[9]。针对这一现状,本设计对炉底炉缸进行了优化,适当加大了炉缸的容积、加深死铁层厚度、优化冷却系统的设置,同时合理选择耐材的配置。采用高热导率的微孔、超微孔炭砖配以高热导率炭捣料。 炉底炉缸耐火材料的选择,依照“内堵外疏”的原则,即高炉内侧采用导热性低的陶瓷材料,外侧采用导热性高的炭质材料。炉底满铺砖第1层采用国产石墨砖,高度400mm;炉底满铺砖第2、3层采用国产微孔炭砖,第2层高度400。mm,第3层高度500;炉底满铺砖第4层采用国产超微孔炭砖,高度500mm;炉底炭砖总高度~1800mm。炉缸侧壁外侧第5~7层采用国产超微孔炭砖,总高度~1300mm;炉缸侧壁外侧第8~14层采用国产微孔炭砖,总高度~3300mm,其中铁口区域采用国产超微孔炭砖。其中铁口区域采用国产超微孔炭砖。炉缸侧壁内侧采用国产小块陶瓷杯结构。三宝钢铁2#高炉炉底、炉缸的设计,在保证炉底、炉缸长寿的基础上,实现了工程投资的优化。三宝钢铁2#i高炉炉底、炉缸结构如图1所示。 整个风口区全部采用大块组合砖砌筑,以加强结构的稳定性;同时采取措施,增加风口冷却壁与炉腹铜冷却壁交接处组合砖厚度。风口及铁口均采用刚玉组合砖,以提高其抗渣铁侵蚀及冲刷能力。 在炉腹及其以上的部位采用砖壁合一、薄壁内衬型式。本高炉在炉腹第5段、炉腰第6段共2段铜冷却壁的热面,采用150mm厚的特种喷涂料。炉身中下部第7~9段共3段铸钢冷却壁的热面,冷却壁镶砖采用烧成微孔铝碳砖。炉身上部第10~14段单层水冷铸铁冷却壁区域,冷却壁镶砖采用浸磷粘土砖。镶砖冷却壁均为砖壁合一、薄壁内衬的结构形式,