金属材料短流程、近终形的生产工艺
金属成型工艺
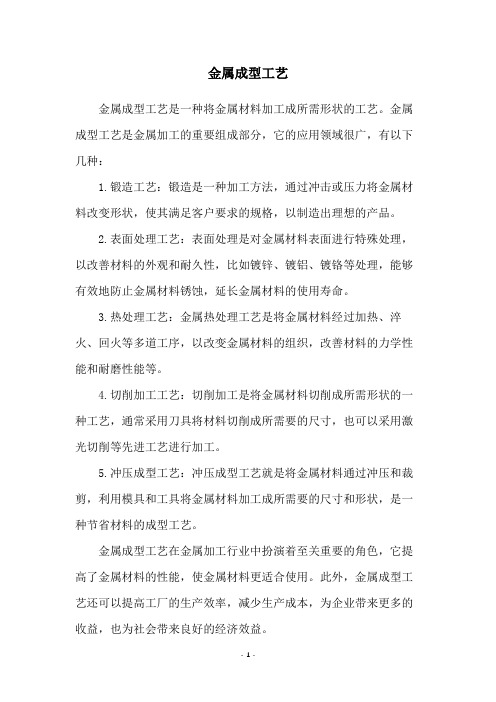
金属成型工艺金属成型工艺是一种将金属材料加工成所需形状的工艺。
金属成型工艺是金属加工的重要组成部分,它的应用领域很广,有以下几种:1.锻造工艺:锻造是一种加工方法,通过冲击或压力将金属材料改变形状,使其满足客户要求的规格,以制造出理想的产品。
2.表面处理工艺:表面处理是对金属材料表面进行特殊处理,以改善材料的外观和耐久性,比如镀锌、镀铝、镀铬等处理,能够有效地防止金属材料锈蚀,延长金属材料的使用寿命。
3.热处理工艺:金属热处理工艺是将金属材料经过加热、淬火、回火等多道工序,以改变金属材料的组织,改善材料的力学性能和耐磨性能等。
4.切削加工工艺:切削加工是将金属材料切削成所需形状的一种工艺,通常采用刀具将材料切削成所需要的尺寸,也可以采用激光切削等先进工艺进行加工。
5.冲压成型工艺:冲压成型工艺就是将金属材料通过冲压和裁剪,利用模具和工具将金属材料加工成所需要的尺寸和形状,是一种节省材料的成型工艺。
金属成型工艺在金属加工行业中扮演着至关重要的角色,它提高了金属材料的性能,使金属材料更适合使用。
此外,金属成型工艺还可以提高工厂的生产效率,减少生产成本,为企业带来更多的收益,也为社会带来良好的经济效益。
金属成型工艺发挥着越来越重要的作用,为实现现代化发展做出了重要贡献,但它也面临着许多挑战,比如针对不同金属材料的加工,需要不同的工艺条件,这就需要不断改进加工方法和技术,以满足不同金属材料的加工需求;此外,还需要加强金属成型工艺的环境保护,以满足现代社会对资源节约和环境保护的要求。
未来,随着科学技术和材料科学的发展,金属成型工艺会出现新的发展方向和前景,更加精致的成型工艺和先进的加工方法将被广泛应用于金属加工行业,有效扩大金属加工行业的应用领域,更好地满足社会的需求。
总之,金属成型工艺是金属加工行业不可或缺的工艺,它带来了巨大的经济效益,促进了社会的发展,为我们的生活带来了更加舒适的环境。
未来,金属成型工艺将继续提高性能,发挥着更大的作用,使我们的生活更加便利。
金属材料的成型工艺

金属材料的成型工艺金属材料的成型工艺是指通过物理或化学方法将金属材料加工成所需形状的工艺过程。
成型工艺广泛应用于各个领域,如汽车、航空、船舶、建筑、制造业等。
它可以改变金属材料的形状、尺寸、性能和组织结构,使其适应不同的使用需求。
锻造是将金属材料加热至一定温度后,施加力并改变形状的工艺。
锻造可分为自由锻造、模锻和精锻。
自由锻造是直接对金属进行锻造,适用于简单形状的零部件。
模锻是使用模具对金属进行锤击或压制,适用于复杂形状和高精度要求的零部件。
精锻是在高温下对金属进行精密锻造,适用于高精度要求的零部件。
冲压是通过金属板材的拉伸、弯曲、切割和成形等工艺来制作零部件。
冲压工艺具有高效、节约材料、适用于大批量生产等优点,广泛应用于汽车制造、家电制造等领域。
铸造是通过将金属材料熔化后倒入模具中,使其凝固成型的工艺。
铸造可分为压力铸造和重力铸造。
压力铸造包括压铸、低压铸造和真空压力铸造。
压铸是将熔融金属注入压铸机模腔中,通过高压填充,并快速凝固成型。
低压铸造是将熔融金属通过压力填充式注射系统注入模具中,然后通过压力使其充满整个模腔,并凝固成型。
真空压力铸造是在真空环境中进行压铸,以提高铸件的质量和密度。
重力铸造是靠铸造机中的重力将熔融金属倒入模具中,凝固成型。
焊接是通过加热材料至熔化状态,通过外界压力和/或其他形式的能量传递,使金属材料连接起来的工艺。
常用的焊接方法包括电弧焊、气体保护焊、激光焊接等。
焊接工艺广泛应用于电子、汽车、船舶、航空航天等领域。
拉伸成型是将金属材料通过拉伸、挤压或者弯曲等方法成型的工艺。
拉伸成型可以提高材料的强度、硬度和耐磨性。
常见的拉伸成型工艺包括拉伸成型、锻造成型和爆炸成型等。
热成型是通过加热金属材料至塑性状态,然后在模具中进行变形的工艺。
热成型可以提高材料的塑性,使其更容易成形,并改变金属材料的结构和性能。
常用的热成型方法包括热压成型、热挤压、热拉伸等。
挤压成型是通过将金属材料放置在模具中,然后施加压力,使其通过模孔挤压成型的工艺。
金属加工全部流程(工序)
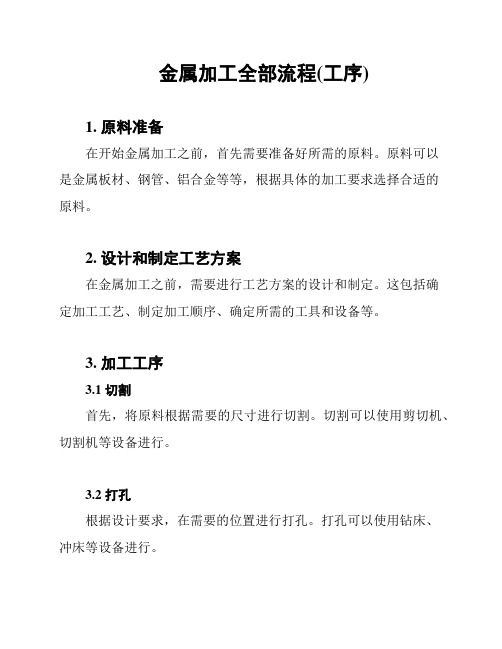
金属加工全部流程(工序)1. 原料准备在开始金属加工之前,首先需要准备好所需的原料。
原料可以是金属板材、钢管、铝合金等等,根据具体的加工要求选择合适的原料。
2. 设计和制定工艺方案在金属加工之前,需要进行工艺方案的设计和制定。
这包括确定加工工艺、制定加工顺序、确定所需的工具和设备等。
3. 加工工序3.1 切割首先,将原料根据需要的尺寸进行切割。
切割可以使用剪切机、切割机等设备进行。
3.2 打孔根据设计要求,在需要的位置进行打孔。
打孔可以使用钻床、冲床等设备进行。
3.3 弯曲和成形根据设计要求,将金属材料进行弯曲和成形。
这可以使用弯曲机、成形机等设备进行。
3.4 焊接如果需要将多个金属部件连接在一起,可以进行焊接。
焊接可以使用电弧焊、氩弧焊等方法进行。
3.5 铆接铆接是将两个或多个金属部件通过铆钉连接在一起。
铆接可以使用铆接枪、铆钉等工具进行。
3.6 研磨和抛光在加工完成后,可以对金属部件进行研磨和抛光,以提高外观和质量。
研磨和抛光可以使用砂纸、抛光机等进行。
3.7 清洗和除锈最后,对金属部件进行清洗和除锈处理,以去除表面的污垢和氧化物。
清洗和除锈可以使用清洗剂、除锈剂等进行。
4. 质检和包装完成金属加工后,需要进行质检以确保加工质量符合要求。
通过使用检测仪器和设备进行质量检测。
通过包装,保护金属部件免受损坏和污染。
以上是金属加工的全部流程(工序),其中涵盖了原料准备、工艺方案设计、加工工序、质检和包装等环节。
根据具体的加工要求和产品设计,可以调整和优化该流程。
金属制品生产工艺流程

金属制品生产工艺流程金属制品生产工艺流程金属制品生产工艺流程是指将原材料经过一系列加工工艺和技术处理,最终转变成满足特定使用要求的金属制品的过程。
本文将以一般性的金属制品生产工艺流程为例,按照先后顺序进行详细描述。
首先,金属制品生产的第一步是原材料准备。
原材料可以是不同种类的金属,例如铁、铝、铜等。
原材料应经过检验、清理和分类,以确保其质量符合要求,并且便于后续加工。
接下来,是金属材料的加工。
这个步骤包括多个子流程,如材料切割、冲压、折弯和锻造等。
在切割过程中,通常会使用剪切机、火焰切割机、激光切割机等设备,将原材料切割成所需的形状和尺寸。
冲压是指利用冲压机将金属材料在模具中进行一次或多次冲击,使其形成所需的凹凸表面。
折弯则是通过机械或手工操作,将金属材料弯曲成所需的形状,以增加强度和刚度。
锻造是将金属材料加热至一定温度后,在冲压或压力下使其塑性变形,以改变形状或提高性能。
然后,进行金属材料的修磨和焊接。
修磨是为了去除加工过程中产生的表面粗糙度和不规则性,从而使金属材料表面更加平滑。
常用的修磨方法包括打磨、研磨和抛光等。
焊接是将两个或多个金属材料通过热源加热至可熔化状态,在相互接触和施加压力的条件下使其连接在一起。
焊接可以采用电弧焊、气体保护焊、激光焊等不同方法,具体选择根据金属材料和所需焊接质量来决定。
接下来是表面处理。
表面处理是为了改善金属制品的外观和性能,包括表面涂装、镀层、防腐和氧化等处理。
涂装包括喷涂、涂刷、浸涂等方法,目的是增加金属制品的美观度和抗腐蚀性。
镀层是将金属制品浸泡在含有金属离子的溶液中,通过电化学反应使金属离子还原到金属表面,形成一层金属薄膜。
防腐是通过在金属表面形成一层防护膜,防止氧化和腐蚀的发生。
氧化是指将金属材料暴露在氧气或氧气加热的条件下,使其表面发生氧化反应,形成一层氧化膜,以改善外观和保护金属材料。
最后,是金属制品的组装和包装。
组装是将各个零件按照设计要求和顺序进行组合,形成最终的金属制品。
金属工艺学金属加工的工艺流程

金属工艺学金属加工的工艺流程金属工艺学:金属加工的工艺流程引言金属工艺学是一门研究金属材料加工工艺的学科,通过对金属材料的性质、加工方法和工艺流程的研究,实现对金属制品的加工和生产。
金属工艺学的发展对于推动工业制造和经济发展具有重要意义。
本文将介绍金属加工的一般工艺流程,包括原材料准备、铸造、锻造、压力加工、切割、焊接和表面处理等环节。
一、原材料准备金属加工的起点是原材料的准备。
原材料通常是金属矿石,经过冶炼和精炼等过程得到金属原料。
这些原料需要经过配料、熔炼和铸锭等步骤,最终得到符合要求的金属材料。
二、铸造铸造是将熔化的金属倒入预先设计的铸型中,通过冷却凝固而形成特定形状的过程。
铸造工艺可以分为砂型铸造、金属型铸造、压力铸造等多种方法。
通过铸造,可以制造出金属铸件,如铸造零件和铸件原型等。
三、锻造锻造是通过对金属进行加热处理和塑性变形,改变其形状和性能的过程。
锻造通常包括两个步骤,即预热和锻造成形。
预热可以提高金属材料的塑性和可锻性,锻造成形则可以得到所需的金属件形状。
四、压力加工压力加工是指通过机械力或液压力对金属进行加工和成形的过程。
常见的压力加工方法包括冲压、拉伸、挤压等。
压力加工可以加工出薄壁件、复杂形状和高精度的金属制品。
五、切割切割是将金属材料分离成所需形状和尺寸的过程。
常见的切割方法有机械切割、火焰切割、激光切割等。
切割可以实现对金属材料的分割、切断和开孔。
六、焊接焊接是将金属材料通过热或者压力连接在一起的过程。
常见的焊接方法有电弧焊、氩弧焊、气焊等。
焊接可以实现金属构件的连接和修复。
七、表面处理表面处理是对金属制品的表面进行改性或者修饰的过程。
常见的表面处理方法有电镀、喷涂、抛光等。
表面处理可以提高金属制品的耐腐蚀性、耐磨性和美观度。
结论金属加工是一项精细而复杂的制造工艺,涉及多个环节和方法。
金属工艺学的研究和应用,不仅可以提高金属制品的质量和性能,还能推动整个工业制造的发展。
通用的金属材料生产工艺
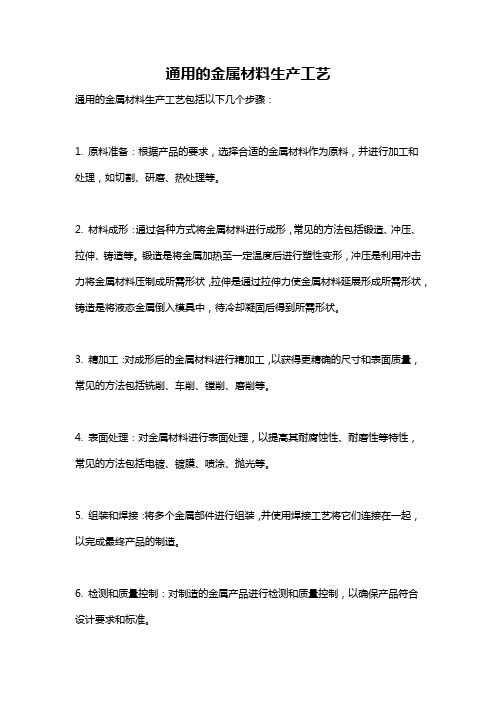
通用的金属材料生产工艺
通用的金属材料生产工艺包括以下几个步骤:
1. 原料准备:根据产品的要求,选择合适的金属材料作为原料,并进行加工和处理,如切割、研磨、热处理等。
2. 材料成形:通过各种方式将金属材料进行成形,常见的方法包括锻造、冲压、拉伸、铸造等。
锻造是将金属加热至一定温度后进行塑性变形,冲压是利用冲击力将金属材料压制成所需形状,拉伸是通过拉伸力使金属材料延展形成所需形状,铸造是将液态金属倒入模具中,待冷却凝固后得到所需形状。
3. 精加工:对成形后的金属材料进行精加工,以获得更精确的尺寸和表面质量,常见的方法包括铣削、车削、镗削、磨削等。
4. 表面处理:对金属材料进行表面处理,以提高其耐腐蚀性、耐磨性等特性,常见的方法包括电镀、镀膜、喷涂、抛光等。
5. 组装和焊接:将多个金属部件进行组装,并使用焊接工艺将它们连接在一起,以完成最终产品的制造。
6. 检测和质量控制:对制造的金属产品进行检测和质量控制,以确保产品符合设计要求和标准。
这些是金属材料生产的一般工艺步骤,具体的工艺可能会根据不同的材料和产品类型而有所不同。
金属生产工艺

金属生产工艺金属生产工艺是指将金属原料经过一系列加工和处理的过程,转化为各种金属制品的方法和技术。
金属生产工艺涵盖了金属的提取、熔炼、铸造、锻造、焊接、冲压、表面处理等多个环节。
以下将简要介绍金属生产工艺的主要环节和工艺流程。
金属的提取是金属生产的第一步。
金属常见的提取方法有开采法和冶炼法。
开采法是通过采矿、选矿和预处理等步骤,将含有金属矿石中的金属元素提取出来。
冶炼法则是将金属矿石经过高温熔炼,分离金属和非金属成分。
熔炼是将金属矿石加热至高温,使其熔融,并分离出金属和非金属的过程。
熔炼方法主要有火法和湿法两种。
火法熔炼是利用高温燃烧将矿石中的金属分离出来,常见的火法熔炼方法有焙烧、电炉炼铁、高炉冶炼等。
湿法熔炼则是通过化学反应将金属溶解在液体中,并通过萃取、电解等方法将金属分离出来。
铸造是将金属熔融后,倒入预先准备好的铸型中,冷却凝固,得到所需形状的金属制品的过程。
铸造方法根据铸型材料的不同可分为砂型铸造、金属型铸造和陶瓷型铸造等。
砂型铸造是最常见的铸造方法,通过将金属熔液倒入砂型中,凝固后取出并清理,得到所需的铸件。
锻造是将金属加热到一定温度后,放入压力机或锤击机中,通过机械力使金属发生塑性变形,得到所需形状的金属制品的过程。
锻造方法根据金属的变形方式可以分为冷锻、热锻和温锻等。
锻造可以使金属的内部结构得到改善,增加金属的强度和韧性。
焊接是将金属零件通过加热使其部分或全部熔化,然后冷却凝固,使其连接为整体的工艺。
焊接方法根据焊接材料的不同可分为电弧焊接、气焊、激光焊接、等离子焊接等。
焊接可以在不改变金属物理性质的情况下,将两个或多个金属零件连接在一起,起到加强连接和密封的作用。
冲压是利用冲压设备将金属板材经过模具的压力变形,以实现所需形状和尺寸的工艺。
冲压方法包括剪切、冲孔、弯曲、拉伸等。
冲压工艺可以高效地生产大量形状复杂的金属零件,具有工艺稳定性高、生产效率高的特点。
表面处理是对金属制品进行涂镀或喷涂,以增加金属的耐腐蚀性、装饰性和使用寿命的方法。
金属材料生产工艺

金属材料生产工艺一、引言金属材料生产工艺是指通过一系列加工和处理过程将金属原料转化为具有特定形状、结构和性能的金属制品的过程。
金属材料广泛应用于各个领域,如建筑、汽车、机械、电子等。
本文将介绍金属材料生产工艺的一些常见方法和技术。
二、铸造铸造是最常见的金属材料生产工艺之一。
它是将金属原料加热至熔化状态,然后借助模具将熔融金属注入,并在冷却固化后得到所需形状的工艺。
铸造方法包括砂型铸造、金属型铸造、压力铸造等。
其中,砂型铸造是最为传统和常用的方法,它适用于各种复杂形状的制品。
三、锻造锻造是通过加热金属原料至一定温度后,将其放置于模具之间,然后施加压力使金属发生塑性变形,最终得到所需形状制品的工艺。
锻造方法包括自由锻造、冷锻造、热锻造等。
锻造可以提高金属的内部结构和力学性能,广泛应用于航空航天、造船、军工等领域。
四、焊接焊接是将两个或多个金属部件通过热源加热至熔化状态,然后使其相互结合的工艺。
焊接方法包括电弧焊、气体焊、激光焊等。
焊接可以实现金属部件的连接,广泛应用于制造业、建筑业等领域。
五、切削加工切削加工是通过切削工具对金属进行削减,从而得到所需形状的工艺。
常见的切削加工方法包括车削、铣削、钻削等。
切削加工可以实现高精度加工,广泛应用于制造业、机械加工等领域。
六、表面处理金属制品在生产过程中常需要进行表面处理,以提高其耐腐蚀性、耐磨性和美观性。
常见的表面处理方法包括镀层、喷涂、阳极氧化等。
表面处理可以改善金属制品的性能和外观,广泛应用于建筑、家具、电子等领域。
七、热处理热处理是通过加热和冷却的方式改变金属的组织结构和性能的工艺。
常见的热处理方法包括退火、淬火、回火等。
热处理可以提高金属的硬度、强度和耐磨性,广泛应用于机械、工具等领域。
八、总结金属材料生产工艺是将金属原料转化为具有特定形状、结构和性能的金属制品的过程。
铸造、锻造、焊接、切削加工、表面处理和热处理是常见的金属材料生产工艺方法。
通过合理选择和应用这些工艺方法,可以满足不同领域对金属制品的需求,推动工业发展和技术进步。
- 1、下载文档前请自行甄别文档内容的完整性,平台不提供额外的编辑、内容补充、找答案等附加服务。
- 2、"仅部分预览"的文档,不可在线预览部分如存在完整性等问题,可反馈申请退款(可完整预览的文档不适用该条件!)。
- 3、如文档侵犯您的权益,请联系客服反馈,我们会尽快为您处理(人工客服工作时间:9:00-18:30)。
金属材料短流程、近终形的生产工艺多个进程(如凝固与成形)的综合化,称短流程化,如喷射成形技术、半固态加工技术和持续铸轧技术等。
打破传统的材料成形与加工模式,缩短生产工艺流程,简化工艺环节,实现近终形、短流程的持续化生产,提高生产效率。
近终型、短流程的成形加工技术具有高效、节能等特点,在技术上突出的特点是缩短加工周期,尽可能减少变形量或后续加工环节,由金属熔体直接取得所需的制品或近似的制品,同时,这些制品还具有现有加工方式所生产制品的性能和组织,这可大大减少后续挤压、轧制和压铸等耗能大、投资大、用工多的加工进程。
例如,半固态成形、持续铸轧和持续铸挤等是将凝固与成形两个进程合而为一,实行精准控制,形成以节能、降耗、高效和优质为主要特征的新技术和新工艺。
1半固态成型金属材料的半固态成型是在半液半固的两相状态下进行的,所以与全液体成型或全固体成型相较,具有许多长处。
首先,在凝固进程中有固液两相,同时存在的合金系都可进行半固态成型。
半固态材料浆的粘度比熔融金属的粘度高得多,因此成型时可形成层流,也能更均匀地填充模型。
金属浆的成型温度较低,与常规铸造工艺相较:可节约35%左右的能源;可以延长模型寿命;凝固时间较短;可缩短生产周期;由于有固体存在和温度较低,零件在模内的收缩较小。
用金属浆生产的零件内的宏观气孔与显微疏松比常规铸件中的少得多。
半固态材料填充模型时,材料前端呈层流充满型腔,比熔融金属的流动平稳得多,不会卷入气体。
半固态成型零件的尺寸可与成品零件的相等或几乎相等,极大地减少了机械加工量与切削量,既节约了材料,又可以生产形状复杂的零件或难于加工的薄壁零件。
半固态模锻件与压铸件表面平整滑腻,内部组织致密,晶粒细小,力学性能高。
2近终形轧制技术(1)热连轧技术热连轧技术是将均热后的坯锭同时在几个机架中产生塑形变形的持续轧制进程。
与单机架轧制相较较,热连轧技术具有工艺流程短,生产率高,产品质量高和生产本钱低等长处。
热连轧工艺虽然取得了较为普遍的应用,可是该工艺将熔体的熔铸和成形加工分为两个独立的环节,金属熔体往往先制备成大的坯锭,然后再进行均热后进行热轧成形,能耗增加。
而且需要锯头、铣面、预热或均匀化,工艺流程较长,原始投资本钱也较高。
在热连轧技术中,热轧坯锭的质量对产品的工艺性能和最终质量影响很大。
而目前的轧制供坯中,铸锭内部的质量仍然较差,成份、组织不均匀,仍然存在偏析、晶粒粗大、缩孔、裂纹和夹渣等铸造缺点,这些缺点的存在对加工进程和产品的质量影响极大,造成了大量废品。
造成铝材成品率不高。
因此,提高热轧铸坯的质量是轧制控制的关键环节之一,这客观上对坯锭的熔铸进程提出了更高的要求,如采用新型的熔处置技术、处置工艺和铸造技术等。
(2)双辊式持续铸轧工艺双辊式持续铸轧工艺是指液态金属直接在两旋转辊间结晶,并经受必然的热变形而取得板带坯料的生产方式。
与热连轧不同,该方式在铸轧的同时直接完成铸造和热轧进程,将坯锭的制备和成形进程合而为一,不需要铸锭锯切、铣面、加热等工序,缩短了工艺流程,几何损失和工艺废品少、成品率高,设备减少,占地面积少,投资本钱低,且易实现生产进程的自动化和科学管理,因此在轧制生产中占有很重要的地位。
铸轧生产线具有建设周期短、投资少、能源低、材料利用率高、保护费用低、技术门坎低、成品率高达97%、环境友好等长处。
可是产品的合金品种和规格较为局限,铸轧后产品为铸造结构,须经冷轧才能达到l~2mm厚度。
可是双辊式持续铸轧生产的合金品种少,往往只适合于纯铝加工,应用范围受到很大限制。
为了克服之一不足,国内外也开展了必然的研究。
如发展了半固态铸轧技术,该技术将高效、节能、短流程的持续铸轧技术与半同态加工技术相结合,取得半同态持续铸轧成形技术,可以兼具这两种先进技术的长处,将是一种全方位高效、节能、短流程、近终形的加工方式,而且这种技术可生产的合金品种显著扩大,成份偏析小,是一种很有发展前途的新型轧制技术。
(3)带式连铸连轧法连铸连轧法是指金属在一条作业线上持续通过熔化、铸造、轧制、剪切、卷取等工序而取得板带坯料的生产方式。
与热连轧技术和双辊式持续铸轧工艺相较,带式连铸连轧法直接将金属的熔化到成品加工于一路,其生产流程更短,在节能降耗、生产近终形板带材方面具有独特的优势。
按照连铸机的机构类型,连铸连轧法有多种类型,可是目前国内外应用最多的是双带式连铸连轧法,如哈兹利特法和亨特一道格拉斯法和3C法。
带式连铸连轧法直接将金属的熔化到成品加工于一路,在节能降耗方面具有独特的优势,将是实现轧制技术短流程、近终形的主要方向之一。
3近终型压铸技术传统压铸铝合金件不宜进行热处置,这制约了压铸铝合金力学性能的提高。
压铸新工艺(真空压铸、充氧压铸、挤压铸造、半同态压铸和超低速压铸等)的开发应用,改善了压铸进程的成形条件,显著提高压铸件内在质量,大大提高了压铸件力学性能、物理性能和耐蚀性能,尤其是气密性、可热处置性和可焊性。
目前,制备高性能零件的压铸新艺受到愈来愈普遍的重视,尤其是流变压铸其基础性研究和应用工作也不断深切。
另外,将不同压铸技术的结合应用,也成为此刻压铸技术研究的重点。
超低速压铸与一般压铸方式有所不同,它是以极低的压射速度,使金属液以极低的速度(>0.15m/s)顺序充填型腔'减小卷气偏向,降低铸件气体含量,以取得表面光洁、轮廓清楚、内部组织致密的压铸件(气体量控制在~/lOOg,一般压铸气体量在25ml/100g)。
可是该方式生产效率较低,且在生产中由于压射速度太低,往往会造成压铸件产生冷隔、浇不足、压铸件轮廓不完整清楚等铸造缺点,而且压射速度的控制较为复杂,操作也不方便。
真空压铸法是将型腔中的气体抽暇或部份抽暇,降低型腔中的气压,以利于充型和合金熔体中气体的排除,使合金熔体在压力的作用下充填型腔,并在压力下凝同而取得致密的压铸件。
真空压铸法与普通压铸法相较具有以下特点:(1)气孔率大大降低;(2)真空压铸的铸件的硬度高,微观组织细小;(3)真空压铸件的力学性能较高。
该技术操作方便,不降低生产效率,所以真空压铸法自出现以来取得了必然规模的发展应用,可是该方式中涉及到复杂的真空处置系统,系统结构复杂庞大,购买本钱高,致使压铸件的本钱较高,因此限制了该技术应用范围的进一步扩大。
充氧压铸是在压铸前将氧气充人型腔,取代其中的空气。
当金属液进入型腔时,一部份氧气从排气槽排出,残留的氧与金属液发生反映,生成弥散状的氧化物微粒,在铸型内形成瞬间真空,从而取得无气孔的压铸件的方式,由于充氧压铸需要附加充氧控制装置,且消耗大量氧气,增大床铸循环时间,这致使了充氧压铸件铸造本钱的提高,因此只用于生产需热处置或组焊、要求气密性高和在较高温度下利用的压铸件。
半固态压铸是在液态金属凝同时进行搅拌,在必然的冷却速度下取得约30%乃至更高固相分数的浆料,然后采用半固态浆料进行压铸的技术。
半固态压铸具有以下特点:(1)因含有30%或更高的固相成份,合金的收缩量小,同时又具有较好的流动性,便于补缩;(2)半固态合金进入型腔不流淌,紊流程度小,大体上达到全壁厚充填,卷气少,易取得无气孔铸件;(3)浇注温度低,且在搅拌时已有30%的结晶潜热散失,减少了对压室、压铸型腔和压铸机部件的热冲击,从而提高压铸型的利用寿命;(4)半固态压铸所要求的拔模斜度小,乃至零拔模斜度,减少铸件的脱型阻力,提高铸件的精度;(5)半固态合金在剪切力的作用下使固态枝晶破碎,有利于细化晶粒,改善合金组织;(6)半固态压铸件含气量少,可进行热处置和组焊,提高了力学性能,扩大了应用范围。
因此是很有发展前途的一门新型压铸技术,具有良好的应用前景。
4持续铸挤技术持续铸挤技术是持续挤压技术的进一步发展,它将液态金属持续铸造与加工合为一体,实现液态金属直接加工成形,属短流程,高效节能的先进工艺。
在Conform 持续挤压的基础上,通过大量的实验研究。
英国霍尔顿(Holton)公司对持续挤压机进行了改良,采用液态金属作坯料直接进入主机。
铸挤轮与固定靴块形成挤压型腔,液态金属在型腔内进行结晶与变形,然后被挤出模孔成材,形成铸造与挤压为一体的新型的挤压技术。
持续铸挤技术同常规生产同类产品的塑性加工方式相较较,具有如下长处:(1)可持续生产很长的产品;(2)节约能源约40%,成品率高达90%,降低本钱30%以上;(3)产品精度高,表面光洁平整;(4)可以实现液一固复合材料的生产;(5)膜具容易改换,安装维修方便;(6)设备结构紧凑,占地面积小,投资小。
可是缺点是工艺控制精度要求很高。
可是目前该技术只应用于冶金行业和电缆电线行业中的一些小型管、棒。
线、型材的生产,较大规模和大型加工材的应用未见报导。
5近终形连铸的工艺技术是指在保证最终产品质量所需压下量的前提下,更接近于产品最终形状的连铸技术。
主要包括:薄板坯连铸技术、薄带连铸技术、喷雾沉积技术等。
传统的薄型钢材生产工艺包括多道次热轧和反复冷轧等工序,工序复杂、生产周期长、能耗大、产品本钱高、劳动强度大。
采用薄带连铸技术,能将持续辟造、轧制,乃至热处置融为一体,设备投资减少、生产工序简化、生产周期缩短、产品本钱显著降低,且产品质量不亚于传统工艺。
另外,利用薄带连铸技术的快速凝固效应,还能生产出轧制工艺难以生产的材料和具有特殊性能的新材料。
(1)CSP技术CSP的工艺进程为:采用立弯式连铸机生产厚50~60mm的铸坯,经分段剪切后,送入辊底式均热炉(120~185m)进行加热、均热。
薄板坯经加热炉入口段、加热段和均热段加速到20~30m/min进入轧制工序。
六机架精轧机组将厚50~60mm 的铸坯轧制成丨.2~12.7mm的带材,经层流水帘冷却后卷取。
生产线全长约270m。
长处:流程短,峰产稳定,产品质量好等。
缺点:对钢水质量要求高、难以生产很宽或较厚的钢板、均热炉设备尚未定型化等。
(2)ISP技术ISP的工艺进程为:采用带轻压下扇形段的弧形连铸机生产厚40mm左右的连铸坯通过初轧机轧至20mm左右,经感应加热、克雷莫纳炉加热、均热送至精轧机组轧制成成品。
生产线全长约175m。
长处:生产线布置紧凑、生产能耗少等。
缺点:感应加热炉设备较复杂且维修困难、薄片形水口寿命较短等。
(3)C0NR0LL技术CONROLL的工艺进程为:CONROLL连铸机与热轧机平行布置,铸坯按Dynacs冷却模型玲却,铸机尾部装有一台火焰切割装置,将铸坯切成所需长度后进入加热炉,薄板坯离开加热炉后,通过粗轧机架5个道次的可逆式轧制,轧成厚25mm后进入带巷箱,再次除鳞,最后在6机架精轧机上轧成厚1.7~12.7mm的热轧带钢,出轧机再经层流冷却后,卷曲成卷。
长处:生产效率高、产品本钱较低等。
缺点:生产线的缓冲能力未必足够、铸坯尺寸范尉较窄等。