误差预防和误差补偿
机械制造工艺学知识点汇总 全 (复习资料)

粗基准概念:以未加工的表面为定位基准的基准。
精基准概念:以加工过的表面为定位基准的基准。
精基准的选择:1基准重合原则2统一基准原则3互为基准原则4自为基准原则5便于装夹原则6 精基准的面积与被加工表面相比,应有较大的长度和宽度,以提高其位置精度。
粗基准的选用原则:1保证相互位置要求2保证加工表面加工余量合理分配3便于工件装夹4粗基准一般不得重复使用原则(1、若必须保证工件上加工表面与非加工表面间的位置要求,则应以不加工表面作为粗基准;2、若各表面均需加工,且没有重点要求保证加工余量均匀的表面时,则应以加工余量最小的表面作为粗基准,以避免有些表面加工不起来。
3、粗基准的表面应平整,无浇、冒口及飞边等缺陷。
4、粗基准一般只能使用一次,以免产生较大的位置误差。
)生产纲领:计划期内,应当生产的产品产量和进度计划。
备品率和废品率在内的产量六点定位原理:用来限制工件自由度的固定点称为定位支承点。
用适当分布的六个支承点限制工件六个自由度的法则称为六点定位原理(六点定则)组合表面定位时存在的问题:当采用两个或两个以上的组合表面作为定位基准定位时,由于工件的各定位基准面之间以及夹具的各定位元件之间均存在误差,由此将破坏一批工件位置的一致性,并在夹紧力作用下产生变形,甚至不能夹紧定位误差:由于定位不准确而造成某一工序在工序尺寸或位置要求方面的加工误差。
产生原因:1工件的定位基准面本身及它们之间在尺寸和位置上均存在着公差范围内的差异;2夹具的定位元件本身及各定位元件之间也存在着一定的尺寸和位置误差;3定位元件与定位基准面之间还可能存在着间隙。
夹紧装置的设计要求:1夹紧力应有助于定位,不应破坏定位;2夹紧力的大小应能保证加工过程中不发生位置变动和振动,并能够调节;3夹紧后的变形和受力面的损伤不超出允许的范围;4应有足够的夹紧行程;5手动时要有自锁功能;6结构简单紧凑、动作灵活、工艺性好、易于操作,并有足够的强度和刚度。
A/C轴双摆头几何精度误差的预防与补偿方案
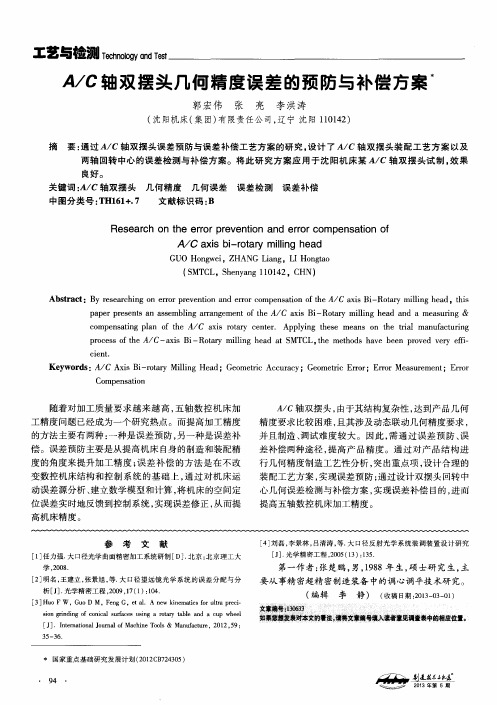
第一作 者 : 张楚鹏 , 男, 1 9 8 8年 生 , 硕 士研 究生 , 主
[ 2 ] 明名 , 王建立 , 张景旭 , 等. 大 口径望远 镜光学 系统 的误差分 配与分
析[ J ] . 光学精密工程 , 2 0 0 9, 1 7 ( 1 ) : 1 0 4 . [ 3 ] H u o F W, G u o D M, F e n g G,e t a 1 .A n e w k i n e ma t i c s f o r u l t r a p r e c i -
数控机床综合几何误差的建模及补偿研究
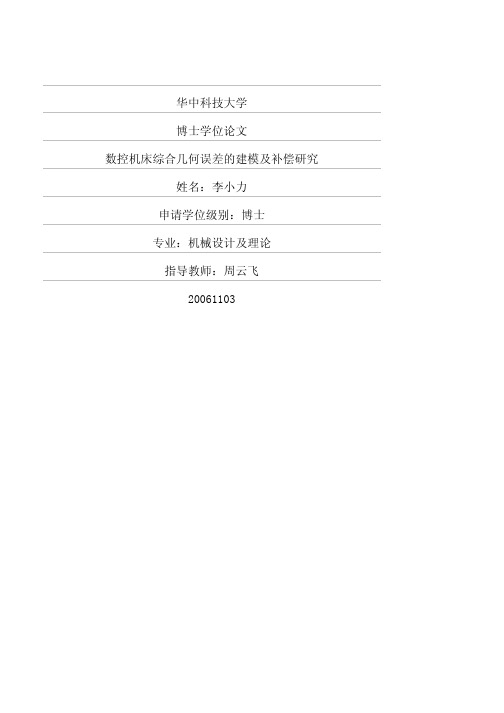
关键词:数控机床
综合几何误差模型
误差检测与识别
误差补偿
快速检测装置
III
华
中
科
技
大
学
博
机械制造技术基础简答题

1.何为刀具的工作角度?刀具角度变化的根本原因是什么?车刀安装位置和进给运动对刀具工作角度有何影响?以切削过程中实际的基面,切削平面和正交平面为参考系所确定的刀具角度称为刀具的工作角度,又称实际角度。
角度变化的根本原因是基面,切削平面和正交平面位置的改变.横向进给运动:进给量f增大,前角增大,后角减小。
轴向进给运动:进给量f增大,前角增大,后角减小。
刀具安装高低:车削外圆时,刀尖高于工件轴线,工作前角增大,工作后角减小;刀尖低于工作轴线,工作角度的变化则正好相反。
2.何为积屑瘤?影响因素有哪些?对切削过程的影响?避免产生和减小积屑瘤的措施?以中低切削速度切削一般钢料或其他塑性金属时,常常在刀具前刀面靠近刀尖处黏附着一块硬度很高的金属楔状物,称为积屑瘤。
切削温度,刀-屑接触面间的压力,前刀面粗糙度,粘结强度。
使刀具实际前角增大,切削力降低;影响刀具耐用度;使切入深度增大;使工件表面粗糙度值增大.避开产生积屑瘤的中速区,采用较低或较高的切削速度;采用润滑性能好的切削液,减小摩擦;增大刀具前角,减小刀—屑接触压力;采用适当的热处理方法提高工件硬度,减小加工硬件倾向。
3.切屑的类型?影响切屑变形的主要因素?带状切削,挤裂切削,单元切屑,崩碎切屑.工件材料:工件材料强度愈高,切屑变形愈小,工件材料塑形愈大,切屑变形就愈大。
前角:前角愈大,切屑变形愈小。
切削速度:在无积屑瘤的切削速度范围内,切削速度愈高,切屑变形就愈小;在积屑瘤增长阶段,实际前角增大,变形随切削速度增加而减小,在积屑瘤消退阶段,实际前角减小,变形随之增大.4.切削力的来源?切削层金属,切屑和工件表面层金属的弹性,塑性变形所产生的变形抗力。
(2)刀具与切屑,工件表面间的摩擦阻力.5.切削热的来源?影响切削温度的因素?切削热来源于:切削层金属发生弹性变形和塑性变形所产生的热和切屑与前刀面,工件与主后刀面间的摩擦热。
1)切削用量:Vc,f,ap增加,切削功率增大,切削热增多,温度升高,其中。
机械制造工艺学
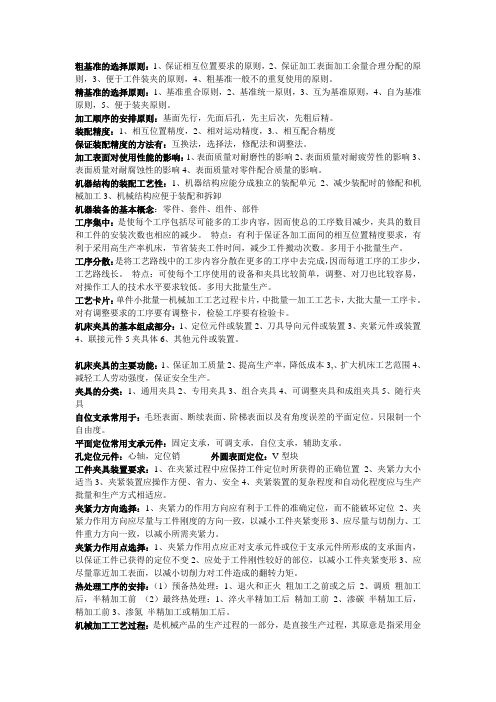
粗基准的选择原则:1、保证相互位置要求的原则,2、保证加工表面加工余量合理分配的原则,3、便于工件装夹的原则,4、粗基准一般不的重复使用的原则。
精基准的选择原则:1、基准重合原则,2、基准统一原则,3、互为基准原则,4、自为基准原则,5、便于装夹原则。
加工顺序的安排原则:基面先行,先面后孔,先主后次,先粗后精。
装配精度:1、相互位置精度,2、相对运动精度,3.、相互配合精度保证装配精度的方法有:互换法,选择法,修配法和调整法。
加工表面对使用性能的影响:1、表面质量对耐磨性的影响2、表面质量对耐疲劳性的影响3、表面质量对耐腐蚀性的影响4、表面质量对零件配合质量的影响。
机器结构的装配工艺性:1、机器结构应能分成独立的装配单元2、减少装配时的修配和机械加工3、机械结构应便于装配和拆卸机器装备的基本概念:零件、套件、组件、部件工序集中:是使每个工序包括尽可能多的工步内容,因而使总的工序数目减少,夹具的数目和工件的安装次数也相应的减少。
特点:有利于保证各加工面间的相互位置精度要求,有利于采用高生产率机床,节省装夹工件时间,减少工件搬动次数。
多用于小批量生产。
工序分散:是将工艺路线中的工步内容分散在更多的工序中去完成,因而每道工序的工步少,工艺路线长。
特点:可使每个工序使用的设备和夹具比较简单,调整、对刀也比较容易,对操作工人的技术水平要求较低。
多用大批量生产。
工艺卡片:单件小批量—机械加工工艺过程卡片,中批量—加工工艺卡,大批大量—工序卡。
对有调整要求的工序要有调整卡,检验工序要有检验卡。
机床夹具的基本组成部分:1、定位元件或装置2、刀具导向元件或装置3、夹紧元件或装置4、联接元件5夹具体6、其他元件或装置。
机床夹具的主要功能:1、保证加工质量2、提高生产率,降低成本3,、扩大机床工艺范围4、减轻工人劳动强度,保证安全生产。
夹具的分类:1、通用夹具2、专用夹具3、组合夹具4、可调整夹具和成组夹具5、随行夹具自位支承常用于:毛坯表面、断续表面、阶梯表面以及有角度误差的平面定位。
机械加工出现误差的原因与防范措施

机械加工出现误差的原因与防范措施摘要:机械加工误差导致的原因是各种各样的,要想减少加工误差产生的机率,就需要提高产品性能与使用寿命。
本文首先从相关概念着手,分析了机械加工误差导致的原因,然后提出了机械加工误差防范措施,以供相关工作人员研究和参考。
关键词:机械加工;误差;原因;防范措施基于机械加工零件类型不一样的情况,通常需要使用各种加工技艺,结合加工零件用途的差异性,灵活选择和运用。
精准的加工工艺可以提高机械零件质量,继而保证产品使用年限延长。
据此,技术工作者需要进一步认识到机械加工的重要性,持续改革与创新产品工艺,保证机械加工质量,从而有效预防机械加工过程中出现的误差。
一、概念分析所谓机械加工误差,指的就是零件加工以后的实际几何参数和理想中的几何参数相互之间的偏差。
在具体实践过程中,实际加工以后的零件和理想中的零件无法完全相同。
在机械加工过程中,加工误差对加工精度有很大的影响。
对于某些加工误差问题,需要采用科学方法进行综合分析,找出产生加工误差的原因并进行解决。
虽然不能完全避免误差产生,不过可以提升加工工艺,提高操作者操作能力,根据主观与客观方面,尽可能地降低加工误差产生的概率,从而增加机械加工精度[1]。
二、误差原因机械加工过程中,出现误差可以说是必然的,需要经过防范误差提高精度,从而满足精度要求。
在机械加工中,误差的出现通常是由多种因素导致的,为了确保机械加工质量,对机械加工误差原因进行分析有一定的现实作用与意义。
(一)定位误差通常而言,定位误差就是机械阿积功过程未能精准定位,继而造成定位原界河加工零件二者之间产生了误差。
该种误差会缩小机械零件于尺寸、规格上的精度,带来质量与使用年限等问题。
通常而言,该种因为定位导致的误差涵盖了基准不重合、定位基准错误两种,所谓基准不重合就是技术工作者加工过程尚未全部根据施工图纸进行,定位基准有所偏差,造成加工零件于规格、尺寸等精度受到了不良影响。
定位基准错误就是技术工作者的主观意愿符合图纸要求,可是加工过程中定位错误,造成不能精准固定加工零件具体位置。
电气测量中系统误差成因和预防对策
电气测量中系统误差成因和预防对策摘要:科学技术的进步,使得测量在各行各业中占据重要地位,测量结果成为人们恒定某一行业生产标准和效果的重要数据。
但是在测量过程中,测量的值和真实值之间易出现差值,造成这种差值的原因是多种多样的。
在电气测量中,系统误差一般分为恒定误差和变值系统误差,正常情况下的固定系统误差不会影响测量精准度,而且系统误差是可以通过多种测量方法予以修补和避免的。
关键词:电气测量;系统误差;成因;预防对策一、系统误差的种类 1、系统误差系统误差是来源于电力测量方法或者器械的固有误差,这个误差常常不是我们换用器械,提高操作技巧或者改良工具而可以消除的。
但是系统误差中来自测量方法的误差有时具有一定的规律性,可以根据相关的规律而消除誤差。
2、偶然误差偶然误差来自于操作过程中的各种因素的影响,可能呢由于实验环境导致的某些参数的不符合,比如环境中的各种变量、温度、信号干扰等,这种误差可以尽量避免,但是大部分时候是无法避免的。
这种误差的特点是,多次相同条件下的测量没有确定的规律,因为环境因素的变化是随机的。
值得注意的是,偶然误差中如果只改变某个微小的条件,不会产生可见的误差。
产生误差的情况,多是由于多个条件发生改变。
3、粗差粗差相比于前面的两种误差具有更多的可调控性。
粗差的测量结果与实际的结果误差颇大。
这样大的误差一般是由于操作人员的素质不高导致的,并且这种误差常常十分明显,一个明显的不正确操作就可以导致大的误差,这种类型的误差只要提高对工作人员的培训就可以改进。
同时购买高质量的精密仪器也可以大大降低这种粗差的产生。
而如果是由于实验方法的误差,则需要长期监测观察,用新的算法来弥补这个误差。
二、造成系统误差的主要原因1、设备因素测量设备虽然是按照生产标准,再经过严格测试后才出厂并投入使用的,但是仪器设备上的缺陷是很难避免的,即设备本身就存在误差。
设备本身自带的误差会使测量过程中测得的数据存在系统误差。
关于数控加工的误差分析及应对措施
关于数控加工的误差分析及应对措施xx年xx月xx日•数控加工误差概述•数控加工误差分析•数控加工误差应对措施目录•数控加工误差控制案例分析•总结与展望01数控加工误差概述数控加工误差是指工件在数控加工过程中产生的尺寸、形状、表面质量等参数与理想状态下的工件参数之间的偏差。
数控加工误差包括机床、刀具、夹具、工件、切削液等多个因素的影响,这些因素相互作用,导致加工误差的产生。
由于工件或刀具的位置不准确,导致加工出的工件与理想状态下的工件参数之间的偏差。
定位误差由于机床、刀具、夹具等设备的制造、安装、调整不当,导致加工出的工件与理想状态下的工件参数之间的偏差。
几何误差由于切削过程中切削力的大小、方向、作用点等因素发生变化,导致加工出的工件与理想状态下的工件参数之间的偏差。
切削力误差由于机床、工件、刀具等在切削过程中产生的热量变化,导致加工出的工件与理想状态下的工件参数之间的偏差。
热误差1 2 3数控加工误差会导致工件的尺寸、形状、表面质量等参数与理想状态下的工件参数存在偏差,从而影响加工精度。
加工精度下降由于数控加工误差的存在,可能导致工件在装配、使用过程中出现故障,影响产品的整体性能和寿命。
产品质量下降为了控制数控加工误差,需要进行反复的调试和修正,增加了生产周期和成本。
生产效率降低02数控加工误差分析编程误差数控编程过程中,由于计算方法或近似处理等原因,导致加工路径与实际路径存在偏差,从而产生误差。
工件误差工件本身存在形状、尺寸等方面的误差,也会对加工精度产生影响。
机床误差机床本身精度不高或长期使用导致磨损,也会对加工精度产生影响。
刀具误差刀具在加工过程中会受到磨损、变形等因素影响,导致加工精度降低。
误差产生的原因分析03尺寸误差加工过程中,由于刀具磨损、温度变化等因素影响,导致加工出的工件尺寸与设计要求存在偏差。
误差对加工精度的影响01位置误差加工过程中,刀具与工件之间的相对位置不准确,导致加工出的工件形状、尺寸与设计要求存在偏差。
提高机械加工精度的措施
4.就地加工法
就地加工法是指零部件先按经济精度加工, 待装配后通过就地加工来实现其最终的加工精度 要求。
5.误差平均法
误差平均法是指对有密切联系的工件表面进行相 互比较和修正,或使其互为基准进行加工,从而使工 件表面的误差较为均匀,以提高工件的加工精度。
二、误差补偿
误差补偿是指通过分析、测量现有误差,人为地 在系统中引入一个附加的误差源,使之与现有的误差 相抵消,以减少或消除工件的加工误差。
机械制造技术
提高机械加工精度的措施
一、误差预防
误差后,采用适当的技术减少原始误差或减少原始 误差的影响,即减少误差源或改变误差源至加工误差 之间的数量转换关系。
1.减少误差法
减少误差法是指在查明影响加工精度的主要原始 误差因素之后,有针对性地将其直接消除或减少,这 是生产中应用较广的一种基本方法。
这种方法是在加工过程中随时测量工件的实际尺 寸,及时给刀具附加补偿量,以控制刀具与工件之间 的相对位置,使工件尺寸的变动范围始终在控制中。 现代机械加工中的在线测量和在线补偿均属于这种形 式。
2.偶件自动配磨
这种方法是将互配件中的一个零件作为基准, 去控制另一个零件的加工精度。在加工过程中自动 测量工件的实际尺寸,并和基准件的尺寸进行比较, 达到规定的差值时机床就自动停止加工,从而保证 精密偶件间具有很高的配合精度。
2.转移误差法
转移误差法是指把影响加工精度的原始误差 转移到不影响或少影响加工精度的方向上。
3.均分误差法(误差分组法)
均分误差法的具体方法为:把毛坯或上道工序 的工件按误差大小分为n组,每组工件的误差就缩小 为原来的1/n,然后按各组分别调整刀具与工件的相 对位置或选用合适的定位元件,就可大大缩小整批工 件的尺寸分散范围。
自动控制原理误差分析知识点总结
自动控制原理误差分析知识点总结自动控制是现代科学技术的重要组成部分,广泛应用于各个领域。
误差分析是自动控制中的一个关键概念,用于评估实际输出与期望输出之间的差异,并通过相应的控制策略来减小该差异。
本文将对自动控制原理中的误差分析知识点进行总结。
一、误差定义与分类在自动控制中,误差是指实际输出值与期望输出值之间的差别。
根据误差的来源和性质,可以将误差分为系统误差和随机误差两类。
1. 系统误差:指由于系统本身结构、参数、非线性等因素引起的误差,具有一定的规律性和可预测性。
2. 随机误差:指由于外界干扰、测量误差等原因引起的误差,具有无规律性和不可预测性。
二、误差分析方法为了准确评估误差并找到相应的控制策略,可以采用以下常用的误差分析方法。
1. 均方根误差(Root Mean Square Error, RMSE):通过计算误差的平方和的均值再开方得到,用于评估系统的总体误差水平。
2. 最大偏差(Maximum Deviation):指实际输出值与期望输出值之间的最大差异,用于评估系统的极端误差情况。
3. 稳态误差(Steady-state Error):指系统在稳态下输出值与期望输出值之间的差别,用于评估系统的稳定性能。
4. 频域分析:通过对系统的频率响应进行分析,评估不同频率下的误差变化情况,用于优化系统的频率特性。
三、误差补偿控制方法误差分析的目的是找到相应的控制策略来减小误差,常用的误差补偿控制方法包括:1. 比例控制(Proportional Control):根据误差的大小进行比例调整,控制输出与期望输出之间的比例关系。
2. 积分控制(Integral Control):通过积分误差以消除稳态误差,使输出趋于期望输出。
3. 微分控制(Derivative Control):通过对误差的变化率进行调整,改善系统的动态响应特性。
4. 预测控制(Predictive Control):基于模型对未来误差进行预测,提前采取相应控制策略以减小误差。
- 1、下载文档前请自行甄别文档内容的完整性,平台不提供额外的编辑、内容补充、找答案等附加服务。
- 2、"仅部分预览"的文档,不可在线预览部分如存在完整性等问题,可反馈申请退款(可完整预览的文档不适用该条件!)。
- 3、如文档侵犯您的权益,请联系客服反馈,我们会尽快为您处理(人工客服工作时间:9:00-18:30)。
(三)转移原始误差
误差转移法是把影响加工精度的原始误差转移 到不影响(或少影响)加工精度的方向或其它 零部件上去 例 1:
图所示利用转移误差的方法转移转塔车床转塔刀架
转角误差
分析
转塔车床的转塔刀架在工作时需经常旋转,因 此要长期保持本息的转位精度是比较困难 假如转塔刀架上外圆车刀的切削基面也像卧式 车床那样在水平面内,那末转塔刀架的转位误 差处在误差敏感方向。将严重影响加工精度
(六)就地加工法
在机械加工和装配中,有些精度问题牵涉到很多
零部件的相互关系,如果单ห้องสมุดไป่ตู้依靠提高零部件的 精度来满足设计要求,有时不仅困难,甚至不可 能。而采用就地加工法可解决这种难题
例如:在转塔车床制造中,转塔上六个安装刀架的大
孔轴线必须保证与机床主轴回转轴线重合。各大孔的 端面又必须与主轴回转轴线垂直 如果把转塔作为单独零件加工出这些表面,那末在装 配后要达到上述两项要求是很困难的 采用就地加工方法,把转塔装配到转塔车床上后,在 车床主轴上装镗杆和径向进给小刀架来进行最终精加 工,就很容易保证上述两项精度要求
一、误差预防技术
(一)合理采用先进工艺与设备 (二)直接减少原始误差法 (三)转移原始误差 (四)均分原始误差 (五)均化原始误差 (六)就地加工法
(一)合理采用先进工艺与设备
1、这是保证加工精度的最基本方法 2、在制订零件加工工艺规程时,并尽可能 合理采用先进的工艺和设备,使每道工序都具备 足够的工序能力 3、随着产品质量要求的提高,产品生产数 量的增大和不合格率的降低,经过成本核算将会 证明采用先进的加工工艺和设备,其经济效益是 十分显著的
(二)直接减少原始误差法
这是在生产中应用较广的一种基本方法。它 是在查明影响加工精度的主要原始误差因素之后, 设法对其直接进行消除或减少。
例: 加工细长轴时,因工件刚度极差,容易产生 弯曲变形和振动,严重影响加工精度。为了减少 因吃刀抗力使工件弯曲变形所产生的加工误差, 可采取下列措施:
1)采用反向进给的切削方式,进给方向由卡盘一 端指向尾座,使Fx力对工件起拉伸作用、同时尾座 改用可伸缩的弹性顶尖,就不会因Fx和热应力而压 弯工件 2)采用大进给量和较大主偏角的车刀,增大Fx, 工件在强有力的拉伸作用下,具有抑制振动的作用 ,使切削平稳
(四)均分原始误差
生产中会遇到这样的情况:本工序的加工精度 是稳定的,但由于毛坯或上工序加工的半成品 精度起了变化,引起定位误差或复映误差太大, 因而造成本工序的加工超差
这类问题最好采用分组调整(均分误差)的方 法: 把毛坯按误差大小分为n组,每组毛坯的误差就 缩小为原来的1/n 按各组分别调整刀具与工件的相对位置或选用 合适的定位元件,就可大大缩小整批工件的尺 寸分散范围 比提高毛坯精度或上工序加工精度要简便易行
用误差补偿的方法来消除或减小常值系统误差一 般来说是比较容易的,因为用于抵消常值系统误 差的补偿量是固定不变的。对于变值系统误差的 补偿就不是用一种固定的补偿量所能解决的。于 是生产中就发展了所谓积极控制的误差补偿方法。 积极控制有三种形式: 1.在线检测,在线误差 补偿 2.偶件自动配磨 3.积极控制起决定 作用的误差因素
这种“自己加工自己”的加工方法,生产 中应用很多,如:
牛头刨床、龙门刨床为了使它们的工作
台面分别对滑枕和横梁保持平行的位置 关系,就都是在装配后在自身机床上进 行“自干自”的精加工 平面磨床的工作台面也是在装配后作"自 磨自"的最终加工
二、误差补偿技术
误差补偿的方法就是人为地造出一种新的原始误 差去抵消当前成为问题的原有的原始误差,并应 尽量使两者大小相等,方向相反,从而达到减少 加工误差,提高加工精度的目的
概述
为了保证和提高机械加工精度,必须找出造 成加工误差的主要因素(原始误差),然后采取 相应的工艺技术措施来控制或减少这些因素的影 响。 生产实际中尽管有许多减少误差的方法和措 施,但从误差减少的技术上看,可将它们分成两 大类: 1)误差预防 2)误差补偿
1)误差预防 指减少原始误差或减少原始误差的影响,亦即 减少误差源或改变误差源至加工误差之间的数 量转换关系。 2)误差补偿 在现存的表现误差条件下,通过分析、测量, 进而建立数学模型,并以这些信息为依据,人 为地在系统中引入一个附加的误差源,使之与 系统中现存的表现误差相抵消,以减少或消除 零件的加工误差。
生产中采用“立刀”安装法,把刀刃的切削基 面放在垂直平面内,把刀架的转位误差转移到 了误差的不敏感方向
例2
在成批生产中,用镗模加工箱体孔系的方 法,也就是把机床的主轴回转误差、导轨 误差等原始误差转移掉,工件的加工精度 完全靠镗模和镗杆的精度来保证。
由于镗模的结构远比整台机床简单,精度 容易达到,故实际生产中得到广泛的应用。
(五)均化原始误差
用易位法加工精密分度蜗轮是均化原始 误差法的一典型实例:
1. 影响被加工蜗轮精度中很关键的一个因素
就是机床母蜗轮的累积误差,它直接地反 映为工件的累积误差 2. 所谓易位法,就是在工件切削一次后,将 工件相对于机床母蜗轮转动一个角度,再 切削一次。使加工中所产生的累积误差重 新分布一次