湘钢3800mm板材厚度和板形控制的优化
论6~8mm薄板轧制集成化生产管理

论6~8mm薄板轧制集成化生产管理 作者:蒋凌枫 来源:《广东科技》 2014年第20期
蒋凌枫 (华菱集团湘钢宽厚板厂,湖南湘潭 411101) 摘 要:追溯了6~8mm薄板轧制环节、轧制过程,结合生产过程,深入分析了生产6~8mm薄板在厚板轧机上生产的主要影响因素,提出了解决制约因素的对策。通过实践和不断优化,形成了6~8mm薄板轧制集成化生产管理理念,以及生产组织模式,取得了良好的成效。
关键词:薄板轧制;影响因素;集成化;生产管理 0 引 言 在钢铁市场竞争日趋激烈的当下,钢企竞争趋向“高、精、尖”的产品。在板材生产线上,生产“极宽、极厚、极薄”的钢板已是角逐点。湘钢某厂在“极薄”的精品战略上卓有成效,其通过薄板(厚度在6~8mm)的试制、归纳、分析,逐步形成了集成化生产管理,开发出适应本生产线的极薄板材生产技术和设备保障措施,从而提高了该生产线在市场的竞争力水平。
1 薄板轧制过程 薄板试制三次,坯料料型均为180mm×1420mm×2230mm。首批试轧,粗轧采用5道次,精轧采用7道次,中间坯厚度70mm,由于精轧轧辊已轧制56km,板凸度难以控制,造成成品浪形比较严重,基本没有轧制成功。第二批试轧,中间坯厚度变为80mm,精轧轧至26km组织生产,由于中间坯偏厚,精轧7道次单道次压下率过大,尤其是末道次大于25%,轧制过程中板形波动较大,轧制过程不稳定,产品不能满足质量要求。第三批试轧,调整加热温度,加强生产前工艺、设备精度的确认工作,进一步优化中间坯和压下规程,轧制过程顺利,板形良好,完全能达到供货标准。随后又批量生产了约1000吨,无轧制废品,成材率达到92%以上,取得良好的成效。
2 影响薄板轧制的主要因素 2.1 精轧机轧制温度 轧钢关键是温度控制,在薄规格产品的轧制过程尤为重要。精轧机轧制过程中,受工作辊冷却水、轧辊凸度、传输辊道冷却水、钢板长度、中间坯厚度、环境温度等因素影响,钢板在轧制过程中降温很快。从现场数据统计、分析,钢板精轧机轧制7道次,开轧温度必须在1000℃以上,终轧温度在780℃左右,才能保证正常轧制。
热轧带钢生产中的板形控制范文
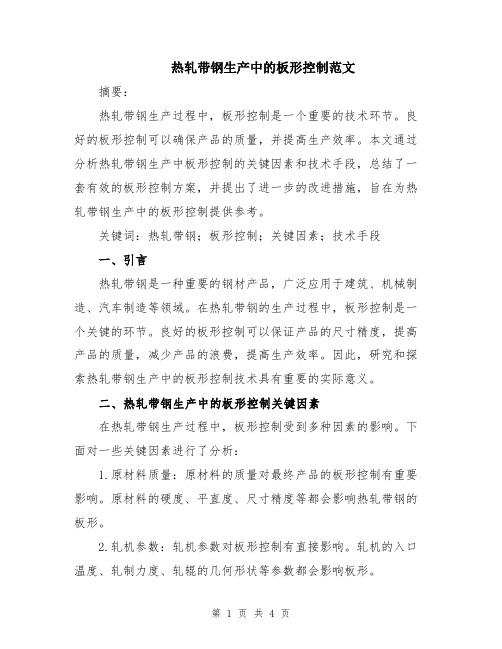
热轧带钢生产中的板形控制范文摘要:热轧带钢生产过程中,板形控制是一个重要的技术环节。
良好的板形控制可以确保产品的质量,并提高生产效率。
本文通过分析热轧带钢生产中板形控制的关键因素和技术手段,总结了一套有效的板形控制方案,并提出了进一步的改进措施,旨在为热轧带钢生产中的板形控制提供参考。
关键词:热轧带钢;板形控制;关键因素;技术手段一、引言热轧带钢是一种重要的钢材产品,广泛应用于建筑、机械制造、汽车制造等领域。
在热轧带钢的生产过程中,板形控制是一个关键的环节。
良好的板形控制可以保证产品的尺寸精度,提高产品的质量,减少产品的浪费,提高生产效率。
因此,研究和探索热轧带钢生产中的板形控制技术具有重要的实际意义。
二、热轧带钢生产中的板形控制关键因素在热轧带钢生产过程中,板形控制受到多种因素的影响。
下面对一些关键因素进行了分析:1.原材料质量:原材料的质量对最终产品的板形控制有重要影响。
原材料的硬度、平直度、尺寸精度等都会影响热轧带钢的板形。
2.轧机参数:轧机参数对板形控制有直接影响。
轧机的入口温度、轧制力度、轧辊的几何形状等参数都会影响板形。
3.辊道调整:辊道的调整能够直接改变板形。
通过调整辊道的水平度、垂直度、辊冠等参数,可以获得理想的板形。
4.冷却措施:冷却措施可以改变钢材的温度分布,进而影响板形。
冷却方式、冷却速度等参数都会对板形产生影响。
以上因素只是热轧带钢生产中的一部分,还有许多其他因素也会对板形控制产生影响。
了解这些关键因素,并采取相应的措施进行控制,是有效控制板形的基础。
三、热轧带钢生产中的板形控制技术手段在热轧带钢生产中,有多种技术手段可用于板形控制。
下面介绍几种常用的技术手段:1.辊道调整:通过调整辊道的水平度、垂直度、辊冠等参数,可以改变钢材的板形。
辊道调整是热轧带钢生产中最常用的板形控制手段之一。
2.冷却措施:通过改变冷却方式、冷却速度等参数,可以改变热轧带钢的板形。
冷却措施是一个非常有效的板形控制手段。
热轧宽带钢卷形控制系统的优化及改进

热轧宽带钢卷形控制系统的优化及改进伴随着科学技术的快速发展,各行各业都有了长足的进步。
热轧宽带钢的生产,其产品的质量受到多方面因素的影响,而为了提升热轧宽带钢卷形控制系统的可靠性,就应该对于相关的生产线进行优化,对卷取区侧导板大梁结构和其材质进行改进,使得卷筒的冷却、夹送辊辊缝设置以及助卷辊辊缝标定进行优化,使得热轧宽带钢卷形的质量大大改善,并且使得相关设施的使用寿命有所增加。
对于热轧宽带钢卷形控制系统的优化及改进,有着非常重要的作用。
标签:热轧宽带钢;卷形控制;系统优化;改进在我们国家的经济发展过程之中,对于经济的发展目标不再是快速发展,现阶段国家制定的经济发展战略是高质量发展经济,去产能成为了很多行业发展的主流,尤其的是对于一些传统的工业行业来说,怎样进行高质量的发展成为了行业关注的焦点。
在钢铁行业之中,存在着产能过剩的问题,要提升钢铁行业的产品生产质量,是目前钢铁企业的重要发展方向。
热轧宽带钢卷形控制系统对于带钢卷形的质量非常重要,如果热轧宽带钢卷形控制系统的稳定性高,那么带钢卷形质量必定也很高,但是目前的热轧宽带钢卷形控制系统有着较多的因素影响卷形控制的质量,进一步的还会对于下一道工序,或者是下游客户的成材率和有效作业率产生影响。
为了使得卷形控制系统的稳定性有所提升,现在对于相关的工艺设施进行优化改造[1]。
对于热轧宽带钢卷形控制系统的优化及改进,在钢铁行业中具有非常重大的意义。
一、对于侧导板进行改进在热轧宽带钢卷形控制系统之中,侧导板主要是使用H型钢作为主体焊接制造的,在相关设备进行卷取操作前,如果侧导板没有对于带钢进行有效的对中,那么在卷取之后钢卷就会成为塔形,严重的话还可能使得卷取堆钢事故出现。
对于侧导板的改进主要有两个方面,第一个方面是进行侧导板大梁的结构改进,因为在带钢卷取的时候,会有碰撞和冲击,尤其是带钢的头部跑偏或者是有镰刀弯,就更加容易使得侧导板大梁出现变形的情况,这样就会使得侧导板对于带钢的夹持对中效果受到影响。
板带材高精度轧制和板形控制
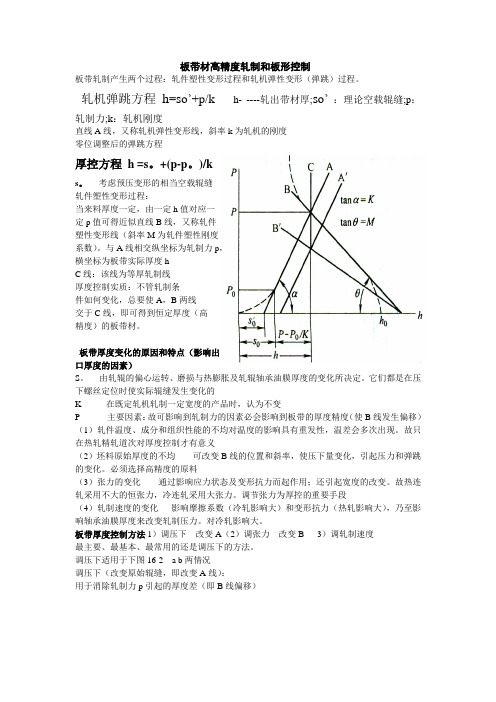
板带材高精度轧制和板形控制板带轧制产生两个过程:轧件塑性变形过程和轧机弹性变形(弹跳)过程。
轧机弹跳方程h=s o’+p/k h- ----轧出带材厚;s o’:理论空载辊缝;p:轧制力;k:轧机刚度直线A线,又称轧机弹性变形线,斜率k为轧机的刚度零位调整后的弹跳方程厚控方程h =s。
+(p-p。
)/ks。
----考虑预压变形的相当空载辊缝轧件塑性变形过程:当来料厚度一定,由一定h值对应一定p值可得近似直线B线,又称轧件塑性变形线(斜率M为轧件塑性刚度系数)。
与A线相交纵坐标为轧制力p,横坐标为板带实际厚度hC线:该线为等厚轧制线厚度控制实质:不管轧制条件如何变化,总要使A,B两线交于C线,即可得到恒定厚度(高精度)的板带材。
板带厚度变化的原因和特点(影响出口厚度的因素)S。
----由轧辊的偏心运转、磨损与热膨胀及轧辊轴承油膜厚度的变化所决定。
它们都是在压下螺丝定位时使实际辊缝发生变化的K ----在既定轧机轧制一定宽度的产品时,认为不变P -----主要因素:故可影响到轧制力的因素必会影响到板带的厚度精度(使B线发生偏移)(1)轧件温度、成分和组织性能的不均对温度的影响具有重发性,温差会多次出现。
故只在热轧精轧道次对厚度控制才有意义(2)坯料原始厚度的不均可改变B线的位置和斜率,使压下量变化,引起压力和弹跳的变化。
必须选择高精度的原料(3)张力的变化通过影响应力状态及变形抗力而起作用;还引起宽度的改变。
故热连轧采用不大的恒张力,冷连轧采用大张力。
调节张力为厚控的重要手段(4)轧制速度的变化影响摩擦系数(冷轧影响大)和变形抗力(热轧影响大),乃至影响轴承油膜厚度来改变轧制压力。
对冷轧影响大。
板带厚度控制方法1)调压下改变A(2)调张力改变B 3)调轧制速度最主要、最基本、最常用的还是调压下的方法。
调压下适用于下图16-2 a b两情况调压下(改变原始辊缝,即改变A线):用于消除轧制力p引起的厚度差(即B线偏移)调张力利用前后张力来改变轧件塑性变形线B的斜率以控制厚度。
淬火机配置优化与工艺改进对板形控制的影响
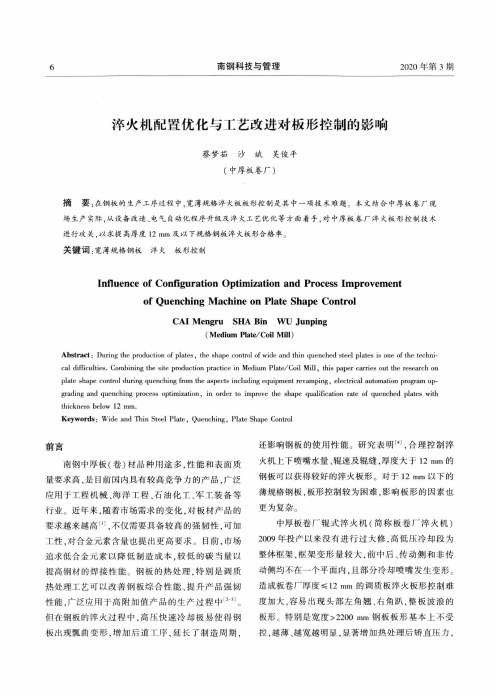
淬火机配置优化与工艺改进对板形控制的影响蔡梦茹沙斌吴俊平(中厚板卷厂)摘要:在钢板的生产工序过程中,宽薄规格泮火板板形控制是其中一项技术难题。
本文结合中厚板卷厂现场生产实际,从设备改造、电气自动化程序升级及泮火工艺优化等方面着手,对中厚板卷厂泮火板形控制技术进行攻关,以求提高厚度丨2 m m及以下规格钢板泮火板形合格率。
关键词:宽薄规格钢板泮火板形控制Influence of Configuration Optimization and Process Improvementof Quenching Machine on Plate Shape ControlCAI Mengru SHA Bin WU Junping(Medium Plate/Coil Mill)Abstract :During the production of plates, the shape control of wide and thin quenched steel plates is one of the technical difficulties. Combining the site production practice in Medium Plate/Coil Mill, this paper carries out the research on plate shape control during quenching from the aspects including equipment revamping, electrical automation program upgrading and quenching process optimization, in order to improve the shape qualification rate of quenched plates with thickness below 12 mm.Keywords:Wide and Thin Steel Plate, Quenching, Plate Shape Controlmm南钢中厚板(卷)材品种用途多,性能和表面质 量要求高,是目前国内具有较高竞争力的产品,广泛 应用于工程机械、海洋工程、石油化工、军工装备等 行业。
宽厚钢板板形控制理论及实践综述

宽厚钢板板形控制理论及实践综述Theory and Practice of Shape Control for Wide and Thick Steel Plates供稿|曹殿政 / CAO Dian-zhengDOI: 10.3969/j.issn.1000-6826.2020.03.004作者单位:河钢集团舞钢公司,河南 平顶山 462500自1949年以来中国钢铁工业走过了一条不平凡的发展之路,中国宽厚钢板作为钢铁工业的一个重要领域,也同样经历了从无到有,从弱到强的艰辛历程。
从40多年前中国第一家宽厚板生产科研基地——舞钢的诞生到数十家宽厚板生产线的成长,凝聚了无数宽厚板科研及生产工作者的共同努力。
当前,中国宽厚板生产面临的问题不再是产量的提高和低价的竞争,而是产品结构的优化调整和产品质量的不断提升。
内在性能质量和外在板形质量这两大方面,都需要向国内外市场的更高标准看齐和迈进。
板形质量在当前日益激烈的市场竞争中对于赢得客户特别是高端客户和高端市场尤为重要。
对于一般的钢板来说,国内外的质量控制差距不大,但对于高强度大厚度的宽厚板来说,板形控制我们还有差距,当然也就有了提升和进步的巨大技术和市场空间,因此,宽厚板的板形控制研究就显得具有现实和长远意义。
本文针对宽厚钢板的板形控制关键设备、工艺、理论和实践进行综述,旨在为生产实践提供借鉴和帮助。
宽厚板生产关键设备在宽厚板生产过程中设备是基础,其中关键设备在整个流程中发挥着关键的作用。
加热炉加热炉是通过将来料钢坯加热到一定温度来满足轧机压力加工工艺的需求。
宽厚板加热炉分为以下几个种类:一是加热钢锭的均热炉,采用加热宽厚钢板Metal World坑式的加热方式;二是连续式加热炉,分为推钢式加热炉和步进式加热炉两种。
从加热使用的能源介质来说,包括:天然气、高炉煤气、转炉煤气以及混合气体等。
从热风利用来说,有换热式和蓄热式两种。
由于目前国际国内大厚度连铸坯的应用越来越广泛,加上大厚度电渣钢坯的应用,钢锭的使用量在减少,因此加热坑式的加热炉将逐渐减少,连续式加热炉的应用将逐渐增多。
中板厂粗轧机板型控制的优化

立辊 侧 压法通 过展 宽 侧压 、 轧侧 压 及 精 轧 精
阶段液 压 A WC控 制 , 现 钢 板 平 面形 状 矩 形 化 实
控 制 。以钢 板平 面不 均匀 部 分 面 积最 小 为 目标 ,
其中 日 本居领先地位 , 许多板材厂的成材率已达
到 9% , 5 切头 尾 和切 边 量 已降 到 4 。 国外 还 广 % 泛采用 液 压 AG 横 向板 型 控 制 和 计 算 机 控 制 , C、
pa t f i n , a e oo g t y ntec r n s u t n d t mi s jr n u n i c r.Atr a ig印一 l g g m k sa h ru hs d ur t i a o , e r n o f e cn f t s f kn n oJa t u o h e t i e e ma il ga o et
saecn o ara ,dsr e epe n s tso p t saecnr nruhn i em du l emUn lp t l bod eci s h r e t t u f l e hp ot l g i ml i t eim p t l o r b t s a a oo o g lnh a i g
1 1 1 立辊侧 压 法 ..
控制也 是一项 重 要 内容 , 两 项 指 标 除 了用 于表 这
征板材 的外形 质量 外 , 直 接与 负偏 差轧制有 关 , 还
因而 与成材率 密切 相关 。
1 国 内外板 型控 制 的现状 及我 厂现 状分析 1 1 国 内外 板型 控制 的现 状 . 国外不 少厂 家 已普遍 采 用 板 型 控制 新 技 术 ,
p r t o v n mp ae s li gmft r s h mm h p ee t f eta se a r m o s igmi a e e i mv d, h ut g i .. e ,t e d Au '¥ s a e d fc t r frb rf oh n o ru hn l h sb n mp e t e c t n i ls fpa e e h s b e e u e d sg i c te o o c b n f s h v e n a h e e . o so lt d a e n rd c d a inf a c n mi e e t a e b e c iv d n in i Ke wo d P a es a e c n r l Op i z t n, r m s a y rs lt h p o t , t o miai D u h p o e
优化板型和剪切控制精度的研究分析

钢板 成材率 是影 响 济钢 中板 厂降本 增效 工作 的 关键 技术 指标 ,多年 来 济钢 中板 厂通过 提 高生产 过 程控 制水 平 , 化毛 宽和 厚度 负偏 差控 制 , 强 提高板 型 控制 稳定性 等 技术保 障措 施 ,钢板 成材 率指 标 已经 提升 到较 高 的水 平 。随着 市场 形 势 的不 断发 展 和产
沿轴向南北窜动, 辊系产生交叉 , 板型控制难度增加 ,
钢板 的头尾及 边部切损 增加 , 一定程 度上影 响 了成材 率 的提高 。我们主要从 提高设备 精度 , 辊系控制 保证
稳定性和推床对中性人手 , 提高板型控制稳定性。 11 辊 系稳 定性 研究 .1 . 经 过对 四辊 轧机辊 系进行 系统 检测 ,发 现 四辊 轧 机辊 系 出现受力 交叉 、辊系 与轧 机牌坊 滑 板之 间
高水 平上 继续稳 步提 升 , 造 了 良好 的经济 效益 。 创
1 提高成 材 率
1 —1 工 作 辊 对 中性 测 量 示 意 图
11 板 型控 制能 力 . 济 钢 四辊 轧机 经过 2 0多年来 的高 负荷 运作 , 辊 系精 度低 ,主要 表现在 薄规格钢板 板型控制 不稳定 , 靠两 侧压下调 整难 以实 现成 品的平 直 ; 轧辊在 轧机 内
摘
要 :主要 围绕提 高成材率开展 了板型控制及钢板剪切 精度 控制研 究。通过对辊 系及推床 系统进行测量分
析, 实施 了滑板 间隙补偿 和推床对 中测量 , 实现 了板型的良好控制 ; 通过对 A GC咬入速度 的控制和轧机 刚度的
标定 , 高了 A 提 GC 系统厚 度 控 制 的 稳 定性 和 精 确 度 ; 过 对 新 线 定 尺 剪测 长 系统 分析 和 改进 , 高 了钢 板 尺 寸 通 提
- 1、下载文档前请自行甄别文档内容的完整性,平台不提供额外的编辑、内容补充、找答案等附加服务。
- 2、"仅部分预览"的文档,不可在线预览部分如存在完整性等问题,可反馈申请退款(可完整预览的文档不适用该条件!)。
- 3、如文档侵犯您的权益,请联系客服反馈,我们会尽快为您处理(人工客服工作时间:9:00-18:30)。
湘钢3800mm板材厚度与板形控制的优化(五米宽厚板厂彭敦向)概要:本文主要介绍湘钢3800mm宽厚板轧机厚度与板形控制的功能、组成,研究和优化厚度与板形控制的各种数学模型与补偿,以及液压小辊缝控制的研发与使用,为湘钢3800mm宽厚板产品质量和成材率的提升奠定了坚实的基础。
1 前言本论文属于轧制科学技术领域,是为了保证板材的交货质量,提高成材率而做的探索和改进。
07年前,按照宽厚板产品大纲,外方调试完毕的轧机设备轧制的产品基本满足要求,但随着产量的不断提升及产品的不断升级,控制系统必须保证质量的稳定。
相对之前主要是探索在提高轧制节奏下板材厚度与板形控制的稳定性,因此对L2模型的再计算功能,精轧机AGC、PFC控制等进行深入了解及优化,同时对轧辊的配辊、辊形进行摸索调整。
本论文主要内容是通过自动化手段,实现对板材的厚度和板形的精确控制,以求达到优化产品质量,减少废次品;提高成材率,减少头尾和切边余量。
2、板材厚度和板形控制的探索2.1 厚度控制厚度控制的不准确不仅仅影响产品质量,同时由于中间坯厚度的不准确直接威胁到轧机的安全。
影响厚度的主要原因是辊缝的不准确,所以只有保证辊缝的准确性,才能保证板材厚度的准确和稳定,决定辊缝的因素有:道次表设定辊缝●轧机弹性变形补偿●轧辊热凸度补偿●轧辊磨损补偿●油膜补偿●零点修正补偿要解决厚度控制不准的问题,首先必须从这几个方面入手2.1.1道次表设定辊缝二级道次表计算模型(PSC),是采用的平均压下率进行道次计算的,计算模式有4种,一是预计算,即板坯入炉后通过原始的PDI对板坯进行计算,用以检测可轧性;二是设定计算,板坯入炉后,模型采集加热炉温度模型计算的板坯温度,进行道次表计算;三是再计算,板坯轧过第一道次后的计算称为再计算,模型采集轧制过程中的各种测量值,例如温度、宽度、厚度和轧制力等,利用测量值为下道次进行重新计算;四是事后计算,钢板轧制完后,通过轧后的数据进行重新计算,用于长期自适应。
通过观察和检查二级程序,我们发现板坯经过粗轧轧完后,进入中间辊道,在经过高温计时,模型没有采用该测量值进行重新计算,而是直接使用的是粗轧结束时的道次表,中间坯在中间辊道上的温度损失没有考虑在道次表计算,造成精轧的实际轧制力和期望轧制力偏差较大,使厚度控制发生偏差,更严重的有时可以造成卡钢或断辊事故,对轧辊和主电机造成较大损害。
通过修改二级程序(PlateBufferManager),在收到高温计检测到的温度后向模型服务器发送再计算请求事件,待计算完成后再向DataHandler程序发送道次表发送事件,DataHandler程序收到事件后,将计算完的新的道次表发送到TCS 系统中,用于实际轧制。
修改后的程序投入运行后,精轧的第一道次的实际轧制力和期望轧制力较为接近,厚度控制得到改善,卡钢事故的次数明显减少,从以前每月的2-3次,现在基本上杜绝了由于道次表引起的卡钢。
2.1.2轧机弹性变形轧制时,在轧制压力的作用下,轧机工作基座产生一定量的弹性变形。
弹性变形的结果将使实际压下量减小,轧件的出口厚度大于空载时的辊缝。
为了获得正确的轧件的厚度,即必须减小空载时的辊缝,用以补偿由于轧机弹性变形引起的辊缝变化。
轧件厚度等于轧机的空载辊缝值加上轧机的弹性变形量,轧机的变形量在一定范围内正比于轧制力F ,也就是:M FS h +=h 为轧件出口厚度,S 为空载辊缝,F 为轧制力。
M 为轧机弹性变形系数。
但在实际应用中,在轧制力小的情况下轧制力与轧机弹跳值并不是线性关系,辊缝真实零位很难确定,所以一般采用辊缝零调来标定人工零位,再以人工零位为基础进行辊缝控制,就是:M F F S h 0-+=S 为相对人工辊缝零位的辊缝值,0F 为确定人工辊缝零位时的轧制力。
如图1中的A 线。
另一方面,当作用在轧件上的轧制力变化F ∆时,轧件厚度上将被压下h ∆,其关系为:Q Fh ∆-=∆其中,Q 值称为轧件塑性系数。
表现为图1中的B 线。
图1 P-H 图利用P-H 图可以综合分析轧机与轧件之间相互作用力与变形关系,如图1,当来料厚度变化H∆(BB'→)时,分析轧制力与辊缝变化趋势,需要如何移动辊缝来消除来料厚度变化引起的轧件厚度变化(AA'→);又比如当辊缝变化时,对轧件厚度的影响是多少。
AGC也就是依照P-H图原理调节辊缝,保证轧件出口厚度稳定。
要获得正确的补偿量就必须摸清楚轧机的弹性变形曲线,这个曲线揭示了弹性变形对板材厚度的影响。
为了获得这样的曲线,一般的方法是采用压靠法获得,我们的轧机同样是采用压靠法用以获得这样的曲线,在轧机的长标定过程中,同过轧辊的在一定轧制力的压靠下,通过HGC的位置传感器获得弹性变形量,然后通过在不同轧制力下的不同变形量,通过一次或2次差分,拟合成轧机的弹性变形曲线。
下面是某次长标定后的轧机测量数据。
拟合成轧机弹性曲线(P-H)如下图但是上图只是显示了轧制力和轧机弹性之间的简单关系,实际上轧机弹性和轧件的宽度有重要的关系,为了获得准确的补偿值还需要找出弹性变形和宽度之间的关系。
在实际轧制中, 轧件宽度不同, 对应相同的轧制力, 轧机弹跳也不同。
当轧机中有宽度为B 的轧件时,关系式:f B ( P) = h - S式中:f B ( P) 为轧机弹跳; P 为轧制力; h 为轧件厚度; S 为辊缝。
我们的主要任务是找出在不同厚度下的轧机弹跳方程和曲线,以获得正确的轧机厚度补偿。
上图为轧机在各个轧制力情况下,宽度和厚度补偿之间的关系从上图可以看出轧制力的不同,随着轧件宽度的变化,轧机的弹跳补偿值是不同的,同时轧辊的辊系变化也影响着轧机的弹跳补偿。
2.1.3轧辊热凸度补偿和轧辊磨损补偿轧辊的磨损和热凸度是无法在实际生产中进行测量的,一般都是采用有限元分析方法,通过模型对轧辊的磨损和热凸度间接模拟计算用以获得磨损和热凸度的值,用以补偿辊缝变化。
在实际生产中,发现实际的磨损和热凸度和模型计算出来的存在一定的偏差,特别在轧辊的初期和轧辊末期,人工对厚度的修正往往很大。
针对这些现象,首先确认在线使用的所有轧辊材质和类型,以确保输入模型的数据准确。
其次检查模型的各种参数,在检查模型参数时发现在模型设定的大量参数中,有许多参数偏离了现场的实际值,例如轧辊的重量,冷却水的温度等,对于这一部分参数我们严格按照现场的实际值进行设定,对于另外一些需要调整的参数,通过摸索和试验,用以确定最优的参数。
经过优化后的模型计算输出值和实际接近,操作工无需再频繁的修正。
2.1.4油膜厚度补偿如下图,显示的是油膜厚度和速度之间的关系轧制过程中,当轧线升速,支撑辊中的油膜分布产生变化,其作用体现在辊缝变小,而在轧制力大的情况下,油膜变化程度相对较小。
所以,油膜补偿量是由轧机转速和轧制力共同决定的。
通过实验测得油膜量、轧制力以及转速的关系曲线如上图。
2.1.5零点修正虽然弹跳模型的计算精度较高,弥补了对辊系弹性变形考虑不足的缺点,但是轧辊磨损和热凸度的变化很难用数学模型精确地计算出来,而且还可能存在某些不确定的因素影响着轧机弹跳的计算。
常见的而且是有效的方法是在轧机弹跳方程上附加零点漂移的处理方法。
零点修正实际上是一个长期自适应的过程,它通过比较实测的轧件厚度(主要是通过测厚仪)和AGC的辊缝进行比较,通过自适应的算法,为下一道次或者是下一个轧件的出口辊缝进行修正,以达到厚度的精确控制的目的,一般算法如下:Δ0 ( n) = (1 - α)Δ0 ( n - 1) +α( h′n - 1 - hn - 1) ) (0 <α< 1)式中, h′n - 1 是上一块钢实测的出口厚度, hn - 1 是上一块钢的软测量的出口厚度,Δ0 ( n - 1) 是上一块钢的零点漂移修正量,Δ0 ( n) 是本块钢板的零点漂移修正量。
因此通过优化测厚仪的测量反馈值,使其测量值接近或者等于轧件实际厚度值,以保证测量值的准确,同时修正自适应系数,并对零点修正的值作限幅处理,使其在一个合理的范围内进行修正,目前限幅在-0.3mm和+0.3mm之间。
2.2 板形控制板形是钢板几何形状的描述,包括横截面形状(Profile)和平直度(Flatness)两项内容。
横截面形状主要由凸度,楔形度等参数表示,其中凸度(截面中点厚度与边部标志点处厚度之差)为最常见的表示参数;平直度用相对延伸差(长短纤维长度差/纤维长度)或翘曲度(浪高/浪长)表示,平常所说的板形从直观上来说就是指钢板的平直度,即是指钢板的浪形,瓢曲或镰刀弯的有无及程度而言平直度缺陷主要分为下面2类:●板面瓢曲,包括长度方向瓢曲和宽度方向瓢曲●形状不良,包括中间波浪,边部波浪,镰刀弯2.2.1 镰刀弯的控制镰刀弯形成的主要原因:●机械压下行程或HGC行程原因造成两边有辊缝差●轧辊附加水冷却不均造成轧辊热凸度形成不当●钢板沿横向温度不均,造成两侧轧制力差从而两侧轧辊的弹性压扁值不同●轧件未能完全对中,咬入时偏离中心线针对成因主要优化了机械压下和HGC的控制程序,减小两边辊缝差,以实现消除镰刀弯。
2.2.1.1 精轧机机械压下系统优化空载时辊缝的调整是通过压下丝杆(D)来实现的,压下丝杆(D)通过三相变频电机(A)和蜗轮蜗杆副(C)来传动。
在轧制过程中和急停时通过气动抱闸将机械压下系统锁紧在设定的位置。
在压下丝杆下部,是上支撑辊平衡系统,以确保在轧制过程中使压下丝杆和上支撑辊轴承座之间产生持续的压紧力,空载时使上支撑辊压靠在压头上,消除压头与上支撑辊轴承座之间的间隙,在压下丝杆动作时,支撑辊平衡压力必须降低,使得辊系跟随丝杆动作。
压下装置示意图机械压下系统由以下几个部分组成:A、交流电机B、气动抱闸C、涡轮蜗杆副D、压下丝杆E、压头F、紧急回松装置生产过程中轧制的镰刀弯,通过分析是由于辊缝动作后支撑辊平衡力没有消除压下蜗轮蜗杆的间隙,在位置传感器检测位置到达后,平衡压力调节到240bar,此压力充分消除了各间隙,由于两侧间隙不一致,造成1~3mm的偏差,由于此误差在PLC的允许范围内,但轧制时便出现镰刀弯。
为解决此问题,必须合理设定压下动作时的平衡力,综合以下因数考虑:●上支撑辊重129t,上工作辊重34t,上辊系总重约224t●压下系统调节速度0-32mm/s,●消除丝杆的间隙●避免平衡力过大造成压下不动作或蜗轮蜗杆过度磨损将压下下降时平衡力设为180bar,上升时设为185bar ,通过跟踪两侧偏差在0.01mm,满足生产要求,并过度无磨损。
2.2.1.2 HGC辊缝控制(薄板轧制时由液压压下进行小辊缝调节)以前宽厚板轧制时辊缝调节的两种形式:●辊缝大于30mm时机械压下与液压压下同时动作●辊缝小于30mm时机械压下先动作,液压压下后动作机械压下:电机速度600rpm,0-32mm/sec,减速比18.5,允许偏差2秒8mm液压压下:调节行程80mm,位置精度±10um,响应时间40um,速度15mm/s可见在小辊缝时用液压调节的响应时间和精确性要比机械调节效果好。