第1章 阀控非对称缸液压伺服系统 (2)
对称阀控制非对称缸电液伺服系统建模分析
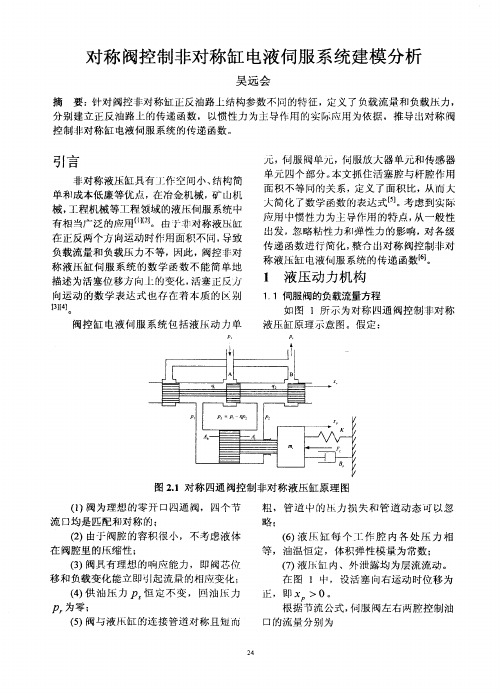
尸) 臼
— —
,
“
无 杆 腔活 塞有 效作 用 面 积 , 有杆 腔活 塞有 效 作用 面 积 ,
m
— —
式 ( . )所描 述 的伺 服 阀负 载流 量特 11 2 性 是 非线 性 的 。 系统 进行 动态 分析 时 , 对 必 须 将 这个 方程 线性 化 。 经过 线 性化 处理 后 的 负载 流量 特 性方 程为
出发 ,忽略 粘性力 和弹 性力 的影 响 , 各级 对 传 递 函数进 行简 化 , 整合 出对 称 阀控制 非对 称液 缸 电液伺服 系统 的传 递 函 。
l 液 压 动 力 机 构
1 1伺服 阀的负载流量方程 . 如 图 1所 示 为对 称 四通 阀控制 非对 称 液压 缸原 理示 意 图。假 定 :
( .) 19
( .0 11 )
,
, , 出的流量 q 为 从 液 缸 同汕 腔流 U V ,
记 伺 服 阀 的负载 流量 为 q ,则有 【 , 3
q£= q 1 ( .1 11 )
J C
4 ~ 一 - C p)C
. ‘ 4 ・
ห้องสมุดไป่ตู้p
式 中 : C — — 液 缸 内 泄 露 系 数 ,
q= dx/P 2 CW 1 2 三 V
(2 1) ・
式 L : q — — 汕缸 尢 杆腔 流量 , m s } j q — — 油缸 有 杆腔 流量 , S C —流 量 系 数 ,无量 纲 — 节流 阀 口面 积梯 度 , m x 电液 伺 服 阀 阀芯 位 移 , m p—— . 度 , k m 油密 g P — — 汕源 压 力 , 尸 P — — 油缸 尢 杆腔 力 . Pa P — — 油 缸有 杆腔 压 力 , Pa 根据 流 量 的连 续性 , 呵写 山每个 液 缸 l 作腔 的流 量方 程 , 即 流 入液 缸 进 油腔 的流 量 g 为 + :+ c( )c . (・ 3
液压伺服系统(DOC)

液压伺服系统液压伺服系统是以高压液体作为驱动源的伺服系统,是使系统的输出量,如位移、速度或力等,能自动地、快速而准确地跟随输入量的变化而变化,与此同时,输出功率被大幅度地放大。
液压伺服系统以其响应速度快、负载刚度大、控制功率大等独特的优点在工业控制中得到了广泛的应用。
一、液压伺服系统的基本组成液压伺服系统无论多么复杂,都是由一些基本元件组成的。
如图就是一个典型的伺服系统,该图表示了各元件在系统中的位置和相互间的关系。
(1)外界能源—为了能用作用力很小的输入信号获得作用力很大的输出信号,就需要外加能源,这样就可以得到力或功率的放大作用。
外界能源可以是机械的、电气的、液压的或它们的组合形式。
(2)液压伺服阀—用以接收输入信号,并控制执行元件的动作。
它具有放大、比较等几种功能,如滑阀等。
(3)执行元件—接收伺服阀传来的信号,产生与输入信号相适应的输出信号,并作用于控制对象上,如液压缸等。
(4)反馈装置—将执行元件的输出信号反过来输入给伺服阀,以便消除原来的误差信号,它构成闭环控制系统。
(5)控制对象—伺服系统所要操纵的对象,它的输出量即为系统的被调量(或被控制量),如机床的工作台、刀架等。
二、液压伺服系统的分类液压伺服系统是由液压动力机构和反馈机构组成的闭环控制系统,分为机械液压伺服系统和电气液压伺服系统(简称电液伺服系统)两类。
电液伺服系统电液伺服系统是一种由电信号处理装置和液压动力机构组成的反馈控制系统。
最常见的有电液位置伺服系统、电液速度控制系统和电液力(或力矩)控制系统。
如图是一个典型的电液位置伺服控制系统。
图中反馈电位器与指令电位器接成桥式电路。
反馈电位器滑臂与控制对象相连,其作用是把控制对象位置的变化转换成电压的变化。
反馈电位器与指令电位器滑臂间的电位差(反映控制对象位置与指令位置的偏差)经放大器放大后,加于电液伺服阀转换为液压信号,以推动液压缸活塞,驱动控制对象向消除偏差方向运动。
当偏差为零时,停止驱动,因而使控制对象的位置总是按指令电位器给定的规律变化。
液压伺服系统-研究生

第1章 绪论
1.1 液压伺服控制系统的工作原理及组成
1.1.1 液压伺服控制系统的工作原理 在这种系统中,输出量(位移、速度、力等)能够自动地、
快速而准确地复现输入量的变化规律。与此同时。还对输入信 号进行功率放大,因此也是一个功率放大装置。
液压泵是系统的能源,它以恒定的压力向系统供油.供 油压力由溢流阀调定。液压动力元件由四边滑阀和液压缸组成。 滑阀是转换放大元件,它将输入的机械信号(阀芯位移)转换成 液压信号(流量、压力)输出,并加以功率放大。液压缸是执行 元件,输入是压力油的流量,输出是运动速度(或伙移)。滑阀 阀体与液压缸体刚性连结在一起,构成反馈回路。因此,这是 个闭环控制系统。
液压伺服系统-研究生
二、滑阀的静态特性曲线
2. 压力特性曲线:是指负载流量等于常数时,负载压降与阀 的开度之间的关系,重要的是负载流量QL=0时的压力特 性, 通常所讲的压力特性即指此而言。
液压伺服系统-研究生
二、滑阀的静态特性曲线
3.压力一流量特性曲线:是指阀的开度一定时,负载流量与 负载压力间的关系, 压力一流量特性曲线族。
液压伺服系统-研究生
流量增益为
2、理想零开口四边滑阀的阀系数
Kq=Cd 1(ps pL)
流量-压力系
数增益为
理想零开口四边滑阀的零
Kc= 2
C1( dpxsV1pL)=Cdx( 2V ps1( ppLs)pL)
位流量增益决定于供油压 力P.和面积梯度,在Ps为常 数时,唯一的由面积梯度 所决定,因此是阀的最重 要的参数。Ps和面积梯度是
2、按输出物理量分:有位置伺服系统、速度 伺服系统、力(或压力)伺服系统等。
3、按控制元件分:有阀控系统和泵控系统两 类。
非对称缸电液伺服系统分析和设计

有杆腔:
哈工大电液所 IEST Lihr@
15
15
10 p 1'
10
p1
P1(MPa)
5
P2(MPa)
P2' 5 P2 0
0
-5 -2
-1
0
1 F2
-1
0
1 FL(N)
2
液压缸无杆腔的压力变化(m≠n)
3 4 x 10
液压缸有杆腔的压力变化(m≠n)
PS
防气蚀装置原理图
哈工大电液所 IEST Lihr@
9
2.4非对称阀控制非对称缸的压力特性 为了从根本上改善液压系统压力特性,建议采用非对称阀控制非对称缸 2.4.1阀与缸完全匹配的情况 阀的节流窗口面积梯度比与缸的面积比相等(m=n),这时两腔压力为
nps FL / A1 p1 p 1 n
p1气蚀条件 p1超压条件
n3 ( p1限制条件) 2 Ps A1 FL Ps A1 m m2 (1 n 2 ) Ps A1 FL Ps A1 (p2限制条件) n p 超压条件 p 气蚀条件
2 2
(活塞杆伸出)时, 当 xv 0 负载 FL 的变化范围限制在
p1' 气蚀条件 p1' 超压条件
C wx Q v 1 d 1 v A1 A1 C wx ( Ps P1 ) d 1 v A1 2 2m 2 ( Ps PL ) 3 2 (n m )
当活塞杆缩回(Xv <0),
Q1 C d w1 x v v A1 A1
C wx P1 d 1 v A1 2
哈工大电液所 IEST Lihr@
16
以对称阀控制非对称缸为例,其压力特性如图所示
浙江大学研究生液压伺服课件第一章
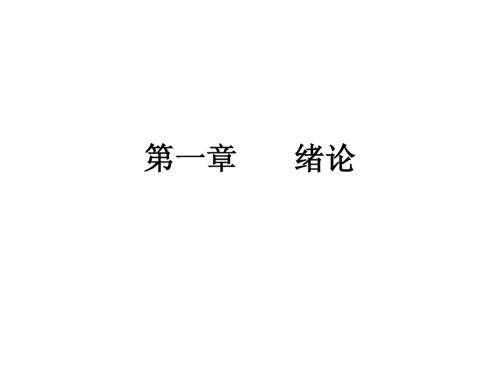
电液伺服阀发展方向
发展方向: • 大流量、高频响的电液伺服阀的研制 • 电液伺服系统(高精度、高响应) • 机电液一体化 • 低成本、可靠性高的电液伺服阀研制 • 特种伺服阀 • 低成本伺服阀如何提高系统性能 • 电液比例伺服阀 • 低功耗电液伺服阀的研制
液压控制系统
• 液压传动与液压控制系统
其输出量为位移, 故称位移伺服控制系 统。在该系统中,输 入信号和反馈信号均 由机械构件实现,所 以也称机械液压伺服 系统。液压控制元件 为滑阀,靠节流原理 工作,也称节流式或 阀控式液压伺服系统。
• 优点:响应速度快、控制精度高、结构简单 • 缺点:效率低
– 容积式控制(变量泵控制或变量马达控制两大 类)
• 优点:效率高 • 缺点:响应速度较慢、结构复杂
液压伺服控制系统分类
• 按信号传递介质的形式分类
– 机械液压伺服系统 – 电气液压伺服系统 – 气动液压伺服系统
第三节 液压伺服控制的优缺点
优点: • 液压元件的功率-重量比和力矩-惯量比大 • 液压动力元件快速性好,系统响应快 • 液压伺服系统负载的刚度大 缺点: • 抗污染能力差 • 油液的体积弹性模量随油温和混入油中的空气含 量而变化,对系统的性能有很大影响 • 容易引起外漏 • 液压元件制造精度高,成本高 • 液压能源的获得和远距离传输都不如电气系统方 便
第二节 液压伺服控制的分类
• 控制系统输入信号的变化规律分类
– 定值控制系统 – 程序控制系统 – 伺服控制系统
• 按被控物理量的名称分类
– 位置伺服控制系统 – 速度伺服控制系统 – 力控制系统 – 其它物理量控制系统
液压伺服控制系统分类
• 按液压动力元件的控制方式或液压控制元 件的形式分类
液压伺服系统工作原理

液压伺服系统工作原理之南宫帮珍创作1.1 液压伺服系统工作原理液压伺服系统以其响应速度快、负载刚度年夜、控制功率年夜等共同的优点在工业控制中获得了广泛的应用.电液伺服系统通过使用电液伺服阀, 将小功率的电信号转换为年夜功率的液压动力, 从而实现了一些重型机械设备的伺服控制.液压伺服系统是使系统的输出量, 如位移、速度或力等, 能自动地、快速而准确地跟随输入量的变动而变动, 与此同时, 输出功率被年夜幅度地放年夜.液压伺服系统的工作原理可由图1来说明.图1所示为一个对管道流量进行连续控制的电液伺服系统.在年夜口径流体管道1中, 阀板2的转角θ变动会发生节流作用而起到调节流量qT的作用.阀板转动由液压缸带动齿轮、齿条来实现.这个系统的输入量是电位器5的给定值x i.对应给定值x i, 有一定的电压输给放年夜器7, 放年夜器将电压信号转换为电流信号加到伺服阀的电磁线圈上, 使阀芯相应地发生一定的开口量x v.阀开口x v使液压油进入液压缸上腔, 推动液压缸向下移动.液压缸下腔的油液则经伺服阀流回油箱.液压缸的向下移动, 使齿轮、齿条带动阀板发生偏转.同时, 液压缸活塞杆也带动电位器6的触点下移x p.当x p所对应的电压与x i所对应的电压相等时, 两电压之差为零.这时, 放年夜器的输出电流亦为零, 伺服阀关闭,液压缸带动的阀板停在相应的qT位置.图1 管道流量(或静压力)的电液伺服系统1—流体管道;2—阀板;3—齿轮、齿条;4—液压缸;5—给定电位器;6—流量传感电位器;7—放年夜器;8—电液伺服阀在控制系统中, 将被控制对象的输出信号回输到系统的输入端, 并与给定值进行比力而形成偏差信号以发生对被控对象的控制作用, 这种控制形式称之为反馈控制.反馈信号与给定信号符号相反, 即总是形成差值, 这种反馈称之为负反馈.用负反馈发生的偏差信号进行调节, 是反馈控制的基本特征.而对图1所示的实例中, 电位器6就是反馈装置, 偏差信号就是给定信号电压与反馈信号电压在放年夜器输入端发生的△u.图2 给出对应图1实例的方框图.控制系统经常使用方框图暗示系统各元件之间的联系.上图方框中用文字暗示了各元件,后面将介绍方框图采纳数学公式的表达形式.图2 伺服系统实例的方框图液压伺服系统的组成液压伺服系统的组成由上面举例可见, 液压伺服系统是由以下一些基本元件组成;输入元件——将给定值加于系统的输入真个元件.该元件可以是机械的、电气的、液压的或者是其它的组合形式.反馈丈量元件——丈量系统的输出量并转换成反馈信号的元件.各种类形的传感器经常使用作反馈丈量元件.比力元件——将输入信号与反馈信号相比力, 得出误差信号的元件.放年夜、能量转换元件——将误差信号放年夜, 并将各种形式的信号转换成年夜功率的液压能量的元件.电气伺服放年夜器、电液伺服阀均属于此类元件;执行元件——将发生调节举措的液压能量加于控制对象上的元件, 如液压缸或液压马达.控制对象——各类生产设备, 如机器工作台、刀架等.液压伺服数学模型2.1 数学模型为了对伺服系统进行定量研究, 应找出系统中各变量(物理量)之间的关系.不单要搞清楚其静态关系, 还要知道其静态特性, 即各物理量随时间而变动的过程.描述这些变量之间关系的数学表达式称之为数学模型.2.1.1 微分方程伺服系统的静态行为可用各变量及其各阶导数所组成的微分方程来描述.当微分方程各阶导数为零时, 则酿成暗示各变量间静态关系的代数方程.有了系统运动的微分方程就可知道系统各变量的静态和静态行为.该微分方程就是系统的数学模型.2.1.2 拉氏变换与传递函数拉氏变换全称为拉普拉斯变换.它是将时间域的原函数f (t)变换成复变量s域的象函数F(s), 将时间域的微分方程变换成s域的代数方程.再通过代数运算求出变量为s的代数方程解.最后通过拉氏反变换获得变量为t的原函数的解.数学上将时域原函数f(t)的拉氏变换界说为如下积分:而拉氏逆变换则记为实际应用中其实不需要对原函数逐一作积分运算, 与核对数表相似, 查拉氏变换表(表1)即可求得.拉氏变换在解微分方程过程中有如下几个性质或定理:(1)线性性质设则有式中 B——任意常数.(2)迭加原理这一性质极为重要, 它使我们可以不作拉氏逆变换就能预料系统的稳态行为.(6)初值定理微分方程表征了系统的静态特性, 它在经过拉氏变换后生成了代数方程, 仍然表征了系统的静态特性.如果所有起始条件为零, 设系统(或元件)输出y(t)的拉氏变换为Y(s)和输入x(t)的拉氏变换为X(s), 则经过代数运算得(1)G(s)为一个以s为变量的函数, 我们称这个函数为系统(或元件)的传递函数.故系统(或元件)的静态特性也可用其传递函数来暗示.传递函数是经典控制理论中一个重要的概念.用常系数线性微分方程暗示的系统(或元件), 在初始条件为零的条件下, 经拉氏变换后, 微分方程中n阶的导数项相应地变换为s n项, 而系数不变.即拉氏变换后所得代数方程为一系数与原微分方程相同, 以s n取代n阶导数的多项式, 移项后就是其传递函数.故一个系统(或元件)的传递函数极易求得.表1 拉氏变换表(部份)原函数ƒ(t)拉氏变换函数F(s)原函数图形(t≥0)1 单元脉冲函数δ(t)= 1单元阶跃函数=1(t>0)2=0(t≤0)3 t4 t n56 (1-)7 sinωt8 cosωt9 sin(ωt+θ)10 cos(ωt+θ)11 cosbt1213141sinhωt51coshωt6例如图3所示为一个质量-弹性-油阻尼系统, 该系统的力平衡微分方程为(2)式中 M——质量;x——质量的位移;B C——阻尼系数;k——弹簧刚度.图3 质量-弹性-油阻尼系统经拉氏变换得(3)写成传递函数为(4)方框图及其等效变换图4 所示是一种文字形式的方框图, 它暗示系统结构中各元件的功用及它们之间的相互连结和信号传递线路.这种方框图又称作结构方框图.另一种方框图即“函数方块图”, 就是将元件或环节的传递函数写在相应的方框中, 用箭头线将这些方框连接起来, 如图4所示.指向方框图的箭头暗示对其输入信号;从方框图出来的箭头暗示输出.图中圆圈暗示比力点, 亦称加减点, 它对二个以上信号根据其正、负进行代数运算.同一信号线上的各引出信号, 数值与性质完全相同.方框图输出信号的因次, 即是输入信号的因次与方程中传递函数因次的乘积.图4 系统方框图1—输入信号;2—比力点;3—引出信号;4—输出信号方框图等效变换、简化法则见表2.表2 方块图变换法则序号原方块图等效方块图1234567891011121314电液伺服阀电液伺服阀电液伺服阀既是电液转换元件, 又是功率放年夜元件, 它能够把微小的电气信号转换成年夜功率的液压能(流量和压力)输出.它的性能的优劣对系统的影响很年夜.因此, 它是电液控制系统的核心和关键.为了能够正确设计和使用电液控制系统,必需掌握分歧类型和性能的电液伺服阀.伺服阀输入信号是由电气元件来完成的.电气元件在传输、运算和参量的转换等方面既快速又简便, 而且可以把各种物理量转换成为电量.所以在自动控制系统中广泛使用电气装置作为电信号的比力、放年夜、反馈检测等元件;而液压元件具有体积小, 结构紧凑、功率放年夜倍率高, 线性度好, 死区小, 灵敏度高, 静态性能好, 响应速度快等优点, 可作为电液转换功率放年夜的元件.因此, 在一控制系统中常以电气为“神经”, 以机械为“骨架”, 以液压控制为“肌肉”最年夜限度地发挥机电、液的长处.由于电液伺服阀的种类很多, 但各种伺服阀的工作原理又基秘闻似, 其分析研究的方法也年夜体相同, 故今以经常使用的力反馈两级电液伺服阀和位置反馈的双级滑阀式伺服阀为重点, 讨论它的基本方程、传递函数、方块图及其特性分析.其它伺服阀只介绍其工作原理, 同时也介绍伺服阀的性能参数及其测试方法电液伺服阀的组成电液伺服阀在电液控制系统中的位置如图27所示.电液伺服阀包括电力转换器、力位移转换器、前置级放年夜器和功率放年夜器等四部份.3.1.1 电力转换器包括力矩马达(转动)或力马达(直线运动), 可把电气信号转换为力信号.3.1.2 力位移转换器包括钮簧、弹簧管或弹簧, 可把力信号酿成位移信号而输出.3.1.3 前置级放年夜器包括滑阀放年夜器、喷嘴挡板放年夜器、射流管放年夜器.3.1.4 功率放年夜器——滑阀放年夜器由功率放年夜器输出的液体流量则具有一定的压力, 驱动执行元件进行工作.图27 电液控制系统方块图电液伺服阀的分类电液伺服阀的分类电液伺服阀的种类很多, 根据它的结构和机能可作如下分类:1)按液压放年夜级数, 可分为单级伺服阀、两级伺服阀和三级伺服阀, 其中两级伺服阀应用较广.2)按液压前置级的结构形式, 可分为单喷嘴挡板式、双喷嘴挡板式、滑阀式、射流管式和偏转板射流式.3)按反馈形式可分为位置反馈、流量反馈和压力反馈.4)按电-机械转换装置可分为动铁式和动圈式.5)按输出量形式可分为流量伺服阀和压力控制伺服阀.6)按输入信号形式可分为连续控制式和脉宽调制式.伺服阀的工作原理伺服阀的工作原理下面介绍两种主要的伺服阀工作原理.力反馈式电液伺服阀的结构和原理如图28所示, 无信号电流输入时, 衔铁和挡板处于中间位置.这时喷嘴4二腔的压力p a=p b, 滑阀7二端压力相等, 滑阀处于零位.输入电流后, 电磁力矩使衔铁2连同挡板偏转θ角.设θ为顺时针偏转, 则由于挡板的偏移使p a>p b, 滑阀向右移动.滑阀的移动, 通过反馈弹簧片又带动挡板和衔铁反方向旋转(逆时针), 二喷嘴压力差又减小.在衔铁的原始平衡位置(无信号时的位置)附近, 力矩马达的电磁力矩、滑阀二端压差通过弹簧片作用于衔铁的力矩以及喷嘴压力作用于挡板的力矩三者取得平衡, 衔铁就不再运动.同时作用于滑阀上的油压力与反馈弹簧变形力相互平衡, 滑阀在离开零位一段距离的位置上定位.这种依靠力矩平衡来决定滑阀位置的方式称为力反馈式.如果忽略喷嘴作用于挡板上的力, 则马达电磁力矩与滑阀二端不服衡压力所发生的力矩平衡, 弹簧片也只是受到电磁力矩的作用.因此其变形, 也就是滑阀离开零位的距离和电磁力矩成正比.同时由于力矩马达的电磁力矩和输入电流成正比, 所以滑阀的位移与输入的电流成正比, 也就是通过滑阀的流量与输入电流成正比, 而且电流的极性决定液流的方向, 这样便满足了对电液伺服阀的功能要求.图28 力反馈式伺服阀的工作原理1—永久磁铁;2—衔铁;3—扭轴;4—喷嘴;5—弹簧片;6—过滤器;7—滑阀;8—线圈;9—轭铁由于采纳了力反馈, 力矩马达基本上在零位附近工作,只要求其输出电磁力矩与输入电流成正比(不象位置反馈中要求力矩马达衔铁位移和输入电流成正比), 因此线性度易于达到.另外滑阀的位移量在电磁力矩一定的情况下, 决定于反馈弹簧的刚度, 滑阀位移量便于调节, 这给设计带来了方便.采纳了衔铁式力矩马达和喷嘴挡板使伺服阀结构极为紧凑, 而且动特性好.但这种伺服阀工艺要求高, 造价高, 对油的过滤精度的要求也较高.所以这种伺服阀适用于要求结构紧凑, 动特性好的场所.力反馈式电液伺服阀的方框图如图29.图29 力反馈式伺服阀方框图3.3.2 位置反馈式伺服阀图30为二级滑阀式位置反馈伺服阀结构.该类型电液伺服阀由电磁部份, 控制滑阀和主滑阀组成.电磁部份是一只力马达, 原理如前所述.动圈靠弹簧定位.前置放年夜器采纳滑阀式(一级滑阀).如图所示, 在平衡位置(零位)时, 压力油从P腔进入, 分别通过P腔槽, 阀套窗口, 固定节流孔3、5达到上、下控制窗口, 然后再通过主阀(二级阀芯)的回油口回油箱.输入正向信号电流时, 动圈向下移动, 一级阀芯随之下移.这时, 上控制窗口的过流面积减小, 下控制窗口的过流面积增年夜.所以上控制腔压力升高而下控制腔的压力降低, 使作用在主阀芯(二级阀芯)两真个液压力失去平衡.主阀芯在这一液压力作用下向下移动.主阀芯下移, 使上控制窗口的过流面积逐渐增年夜, 下控制窗口的过流面积逐渐缩小.当主阀芯移动到上、下控制窗口过流面积重新相等的位置时, 作用于主阀芯两真个液压力重新平衡.主阀芯就停留在新的平衡位置上, 形成一定的开口.这时, 压力油由P 腔通过主阀芯的工作边到A腔而供给负载.回油则通过B腔, 主阀芯的工作边到T腔回油箱.输入信号电流反向时, 阀的举措过程与此相反.油流反向为P→B, A→T.上述工作过程中, 动圈的位移量, 一级阀芯(先导阀芯)的位移量与主阀芯的位移量均相等.因动圈的位移量与输入信号电流成正比, 所以输出的流量和输入信号电流成正比.图30 位置反馈伺服阀结构1—阀体;2—阀套;3—固定节流口;4—二级阀芯;5—固定节流口;6—一级阀芯;7—线圈;8—下弹簧;9—上弹簧;10—磁钢二级滑阀型位置反馈式伺服阀的方框图如图31所示.该型电液伺服阀具有结构简单, 工作可靠, 容易维护, 可在现场进行调整, 对油液清洁度要求不太高.图31 位置反馈式电液伺服阀方框图电液伺服阀的基本特性空载时输出流量和输入信号电流之间的关系, 经常使用空载流量特性曲线来暗示(图32).由这一曲线可获得该阀的额定值、线性度、滞环、流量增益等特性.额定电流I R——在这一电流范围内, 阀的输出流量与输入信号电流成正比.额定空载流量——在额定压力与额定电流下阀的空载流量.线性度——q-I曲线直线性的怀抱.图32 空载流量特性曲线I R——额定电流;q0——最年夜空载流量;tanθ——流量增益滞环——主要用来标明信号电流改变方向时, 由摩擦力、磁滞等原因使I-q曲线不重合的水平.常以曲线上同一流量下电流最年夜差值△I max与阀的额定电流I R之比来暗示.流量增益——q L与I之比值, 即q-I曲线的平均斜率.3.4.2 压力增益特性在一定供油压力下, 在输入电流I和负载压力p L=p1-p2曲线上, 比值△p L/△I称为压力增益.当负载流量坚持为零时, 在零位(中间平衡位置)附近的压力增益称为零位压力增益.零位压力增益与主滑阀的开口形式有关, 以零开口形式最高.提高供油压力p s也可提高零位压力增益.但这一特性主要与阀的制造质量有关.提高零位压力增益, 对减小不灵敏区、提高精度有作用, 但对稳定性起相反的作用.图33是零开口伺服阀的零位压力增益特性曲线.图33 零位压力增益特性曲线3.4.3 负载压力、流量特性这一特性往往是选用伺服阀的主要依据.图34即为负载压力-流量特性曲线.3.4.4 对数频率特性它暗示电液伺服阀的静态特性.幅频曲线中一3dB时频率为该阀的频宽.其值越年夜则该阀的工作频率范围越年夜.对数频率特性也是分析伺服系统动特性以及设计、综合电液伺服系统的依据.图35即为阀的对数频率特性曲线.3.4.5 零飘与零偏伺服阀由于供油压力的变动和工作油温度的变动而引起的零位(Q L=p L=0的几何位置)变动称为零飘.零飘一般用使其恢复位所需加的电流值与额定电流值之比来衡量.这一比值越小越好.另外, 由于制造、调整、装配的分歧, 控制线圈中不加电流时,滑阀纷歧定位于中位.有时必需加一定的电流才华使其恢复中位(零位).这一现象称为零偏.零偏以使阀恢复零位所需加之电流值与额定电流值之比来衡量.图34 负载压力-流量特性曲线图35 对数频率特性曲线3.4.6 不灵敏度由于不灵敏区的存在, 伺服阀只有在输入信号电流达一定值时才会改变状态.使伺服阀发生状态变动的最小电流与额定电流之比称为不灵敏度.其值愈小愈好.液压伺服系统设计液压伺服系统设计在液压伺服系统中采纳液压伺服阀作为输入信号的转换与放年夜元件.液压伺服系统能以小功率的电信号输入, 控制年夜功率的液压能(流量与压力)输出, 并能获得很高的控制精度和很快的响应速度.位置控制、速度控制、力控制三类液压伺服系统一般的设计步伐如下:1)明确设计要求:充沛了解设计任务提出的工艺、结构及时系统各项性能的要求, 并应详细分析负载条件.2)拟定控制方案, 画出系统原理图.3)静态计算:确定动力元件参数, 选择反馈元件及其它电气元件.4)静态计算:确定系统的传递函数, 绘制开环波德图, 分析稳定性, 计算静态性能指标.5)校核精度和性能指标, 选择校正方式和设计校正元件.6)选择液压能源及相应的附属元件.7)完成执行元件及液压能源施工设计.本章的内容主要是依照上述设计步伐, 进一步说明液压伺服系统的设计原则和介绍具体设计计算方法.由于位置控制系统是最基本和应用最广的系统, 所以介绍将以阀控液压缸位置系统为主.4.1 全面理解设计要求4.1.1 全面了解被控对象液压伺服控制系统是被控对象—主机的一个组成部份, 它必需满足主机在工艺上和结构上对其提出的要求.例如轧钢机液压压下位置控制系统, 除应能够接受最年夜轧制负载, 满足轧钢机轧辊辊缝调节最年夜行程, 调节速度和控制精度等要求外, 执行机构—压下液压缸在外形尺寸上还受轧钢机牌坊窗口尺寸的约束, 结构上还必需保证满足更换轧辊方便等要求.要设计一个好的控制系统, 必需充沛重视这些问题的解决.所以设计师应全面了解被控对象的工况, 并综合运用电气、机械、液压、工艺等方面的理论知识, 使设计的控制系统满足被控对象的各项要求.4.1.2 明角设计系统的性能要求1)被控对象的物理量:位置、速度或是力.2)静态极限:最年夜行程、最年夜速度、最年夜力或力矩、最年夜功率.3)要求的控制精度:由给定信号、负载力、干扰信号、伺服阀及电控系统零飘、非线性环节(如摩擦力、死区等)以及传感器引起的系统误差, 定位精度, 分辨率以及允许的飘移量等.4)静态特性:相对稳定性可用相位裕量和增益裕量、谐振峰值和超调量等来规定, 响应的快速性可用载止频率或阶跃响应的上升时间和调整时间来规定;5)工作环境:主机的工作温度、工作介质的冷却、振动与冲击、电气的噪声干扰以及相应的耐高温、防水防腐蚀、防振等要求;6)特殊要求;设备重量、平安呵护、工作的可靠性以及其它工艺要求.4.1.3 负载特性分析正确确定系统的外负载是设计控制系统的一个基本问题.它直接影响系统的组成和动力元件参数的选择, 所以分析负载特性应尽量反映客观实际.液压伺服系统的负载类型有惯性负载、弹性负载、粘性负载、各种摩擦负载(如静摩擦、动摩擦等)以及重力和其它不随时间、位置等参数变动的恒值负载等.4.2 拟定控制方案、绘制系统原理图在全面了解设计要求之后, 可根据分歧的控制对象, 按表6所列的基本类型选定控制方案并拟定控制系统的方块图.如对直线位置控制系统一般采纳阀控液压缸的方案, 方块图如图36所示.图36 阀控液压缸位置控制系统方块图表6 液压伺服系统控制方式的基本类型伺服系统控制信号控制参数运动类型元件组成机液电液气液电气液模拟量数字量位移量位置、速度、加速度、力、力矩、压力直线运动摆动运动旋转运动1.阀控制:阀-液压缸, 阀-液压马达2.容积控制:变量泵-液压缸;变量泵-液压马达;阀-液压缸-变量泵-液压马达3.其它:步近式力矩马达4.3 动力元件参数选择动力元件是伺服系统的关键元件.它的一个主要作用是在整个工作循环中使负载按要求的速度运动.其次, 它的主要性能参数能满足整个系统所要求的静态特性.另外, 动力元件参数的选择还必需考虑与负载参数的最佳匹配, 以保证系统的功耗最小, 效率高.动力元件的主要参数包括系统的供油压力、液压缸的有效面积(或液压马达排量)、伺服阀的流量.被选定液压马达作执行元件时, 还应包括齿轮的传动比.4.3.1 供油压力的选择选用较高的供油压力, 在相同输出功率条件下, 可减小执行元件——液压缸的活塞面积(或液压马达的排量), 因而泵和动力元件尺寸小重量轻, 设备结构紧凑, 同时油腔的容积减小,容积弹性模数增年夜, 有利于提高系统的响应速度.可是随供油压力增加, 由于受资料强度的限制, 液压元件的尺寸和重量也有增加的趋势, 元件的加工精度也要求提高, 系统的造价也随之提高.同时, 高压时, 泄漏年夜, 发热高, 系统功率损失增加, 噪声加年夜, 元件寿命降低, 维护也较困难.所以条件允许时, 通常还是选用较低的供油压力.经常使用的供油压力品级为7MPa到28MPa, 可根据系统的要求和结构限制条件选择适当的供油压力.4.3.2 伺服阀流量与执行元件尺寸简直定如上所述, 动力元件参数选择除应满足拖动负载和系统性能两方面的要求外, 还应考虑与负载的最佳匹配.下面着重介绍与负载最佳匹配问题.(1)动力元件的输出特性将伺服阀的流量——压力曲线经坐标变换绘于υ-F L平面上, 所得的抛物线即为动力元件稳态时的输出特性, 见图37.图37 参数变动对动力机构输出特性的影响a)供油压力变动;b)伺服阀容量变动;c)液压缸面积变动图中 F L——负载力, F L=p L A;p L——伺服阀工作压力;A——液压缸有效面积;υ—;—液压缸活塞速度,q L——伺服阀的流量;。
阀控非对称缸电液伺服系统线性自抗扰控制
问题,本文提出了一种电液伺服系统线性自抗扰控制方法,利用线性扩张状态观测器实现综合扰动的实
时估计,并采用状态误差反馈控制律给予主动补偿,同时消除跟踪误差。证明了设计的线性扩张状态观
测器状态观测误差的收敛性。根据工程实际中的参数进行仿真研究,其结果表明这种控制方法能有效
抑制电液伺服系统中不确定性扰动,与PIT控制器相比具有较强的鲁棒性,并提高了位置跟踪精度。
181
匹配线性未知参数与非线性未知参数之间的耦合
问题,仿真 了该方法的有。方
[14]针
对电液位 服 存在的非线性、参数
问题,给出了 [15]为
自适应动态面控 设计方法O
电液控
中非线性不
数
的 ,提出了 滑模自适应控制方
,通过构建 的Lyapncov函数,设计了
自
适应控,给出了参数自适应律, 控 能oGDOURAEK等〔心 电液
收稿日期:201852-55 基金项目:山西省煤机重点科技攻关项目(MJ2014-02) 作者简介:金坤善(1778 -),男,博士研究生,主要研究方向为锻压设备及其先进控制技术;通信作者:宋建丽教授,E-maU:
sovgjianC@ bistu. edn. cn.
第44卷第3期
金坤善,等:阀控非对称缸电液伺服系统线性自抗扰控制
液压伺服系统工作原理及实例
(3)电液速度伺服控制系统
? 测速发电机:将输出转换为反馈电压信号 Uf,它是反馈装置。
速度指令 +
ug u-f
伺服放大器
电液伺服阀
ω 滚筒
位移 传感器
测速发电机 电液速度伺服控制原理图
3、电液伺服阀
QDY系列伺服阀属于干式力矩马达喷嘴挡板滑阀式 力反馈伺服阀。该系列电液伺服阀性能质量都非常过关, 应用较多。
DY系列伺服阀是动圈双级滑阀式伺服阀,冶金矿山行 业用的较多。
图示为QDY电液伺服阀原理图
3、电液伺服阀
QDY的基本组成如下图: 液 压 放 大 器
输入信号 (电流)
电气-机械
液压伺服系统的原理及实例
伺服系统(又叫随动系统或跟踪系统)是一中自动控制系统, 在这种系统中执行机构能以一定的精度自动地按照输入信号 的变化规律动作。
液压伺服系统:凡是采用液压控制元件和液压执行元件, 根据液压传动原理建立起来的伺服系统,都称为液压伺服系 统。
电液伺服控制系统
? 电液伺服控制系统是由电气的信号处理部分与液 压的功率输出部分组成的闭环控制系统。具有控 制精度高、响应速度快、信号处理灵活、输出功 率大、结构紧凑、重量轻等特点。应用广泛。
电液伺服阀
工作台
xf
放大器
uf Δu
反馈电位器 xo +E
ug
指令电位器
xg
双电位器位置控制电液伺服系统
4、液压伺服控制系统举例
? 电液伺服阀处于零位,没有 流量进出系统,工作台不动. 当指令电位器向右移动一个 位移△U=K △Xg, 经放大 去控制电液伺服阀,输出压 力油推动工作台右移,同时 使工作台位移增加,当增加 量为△U=Xf+△Xf-Xg- △Xg=0,工作台重新停止.
非对称伺服阀在阀控缸电液伺服系统中的应用
非对称伺服阀在阀控缸电液伺服系统中的应用摘要:非对称液压缸具有占用空间小、制造简单、成本低等优点,在液压系统中得到广泛应用。
但是,在液压伺服系统中,特别是在零开度伺服阀控制的阀控缸系统中,由于非对称液压缸活塞两侧的承载面积不同,当伺服阀芯在零开度附近摆动时,液压缸的两个腔室交替供油,活塞的运动方向交替变化。
此时液压缸的两个腔室会产生突然的压力跳变,导致系统振荡、爆炸,不仅影响系统的稳定性,还会导致系统无法正常工作,甚至导致液压。
在使用计算机仿真设计液压系统时,这个问题很容易被忽略,导致设计失败。
关键词:伺服阀;不对称液压缸;三通阀;分析一个实际零开口对称伺服阀控不对称液压缸的液压系统设计案例,对对称阀控制不对称液压缸进行了不相容性分析,明确系统产生“爆振”的原因,以及提出该设计失败后的改进方案。
一、对称四通伺服阀控制不对称液压缸可行性1.对称四通伺服阀控制不对称液压缸方程推导。
对称四通伺服阀控制不对称液压缸如图1所示。
图1对称四通伺服阀控制不对称液压缸图1中,L1、A1为液压缸无杆腔行程和有效工作面积;L2、A2为液压缸有杆腔行程和有效工作面积;V1、V2分别为液压缸无杆腔和有杆腔容积;p1、p2分别为液压缸无杆腔和有杆腔压力;vp1、vp2分别为活塞杆伸出与退回速度;∑F1、∑F2分别为活塞杆伸出时负载和退回时负载;q1、q2分别为液压缸无杆腔流量和有杆腔流量;q3为活塞杆外伸时伺服阀的回油流量;q4为活塞杆退回时伺服阀的回油流量;a1、a2、a3、a4为四通伺服阀各节流口的通流截面积;xp为液压缸活塞的位移;mt为活塞及其刚性联接件、油液及负载等效到活塞上的总质量;BP为活塞和负载的黏性阻尼系数;ps为四通伺服阀进油压力;xv为四通伺服阀阀芯位移。
当四通伺服阀为对称零开口阀时,为简化分析,不考虑油液的可压缩性和液压缸的泄漏,假设∑F为液压缸活塞上的总负载,FL为外负载,FC为摩擦力。
2.仿真设计的误区。
液压伺服控制系统课件
收稿日期:2004-08-29作者简介:王野牧(1965-),男,副教授,辽宁本溪人,硕士.文章编号:1000-1646(2005)01-0005-04液压伺服控制系统课件王野牧,李天阳,韦 茵(沈阳工业大学机械工程学院,沈阳110023)摘 要:在液压伺服控制系统及控制工程中经常会遇到一些重要概念、定义及术语,可以通过实验教学加以理解,但所使用的设备、仪器数量、时间及复杂程度都将是惊人的,在教学时间内几乎不可能完成.为此,介绍了由伺服阀控制对称液压缸和位移传感器构成的液压位置闭环控制系统及其工作原理,给出了该系统的频率特性及动态响应数学表达式.以V ISU AL BASIC为开发工具,开发出了适用于液压伺服控制系统及控制工程基础课程的教学课件.关 键 词:伺服阀;对称液压缸;控制工程;频率特性;动态响应中图分类号:T P271 31 文献标识码:ACAI for hydraulic servo control systemWANG Ye-mu,LI Tian-yang,WEI Yin(School of M echanical Engineer ing,Shenyang U niversity of T echnology,Sheny ang110023,China)Abstract:For hydraulic servo control system and control engineering,many im portant concepts,definitions and items met from time to time can be understood through ex periment teaching.How ever,the quantity of instrument,time spent and the complexity w ould be astonishing,w hich can not be completed in predeter-m ined teaching hours.In this paper,the domination principle of the hydraulic position closed-loop system consisted of the position sensor and symmetrical hydraulic cylinder controlled by the servo valve is intro-duced.The m athematical models of frequency characteristics and dynamic response of the system are dis-cussed.With V isual Basic Language,the CAI suitable for the hydraulic servo control system and the control eng ineering foundation is developed.Key words:servo valve;symmetrical hydraulic cylinder;control engineering;frequency characteristics;dynamic response在液压伺服控制系统及控制工程基础课程的教学过程中由始至终都会遇到一些重要的概念、定义及术语,如开环系统、闭环系统、反馈、偏差、稳定性、频率特性、频宽、动态响应、误差等,这些都是一些比较抽象的概念,学生不容易理解和掌握.可以通过实验教学来加深理解,但受实验条件所限,有些项目无法完成.而且,由于实验教学的集中性,课堂教学中无法及时地、有针对性地、形象地进行讲解,使得教学效果不理想.利用MAT-LAB中动态仿真工具SIMU LINK软件包,也可以帮助学生理解上述概念,但对于一点基础没有的学生来讲,仍嫌不够直观、难于理解.液压伺服位置闭环控制系统是一种非常典型的闭环控制系统,在生产实际中得到了广泛的应用,利用V I-SUAL BASIC通过软件来直观的显示它的组成、工作原理,并在数学模型的基础上,通过可视化的动画方式来直观、灵活、随意地在教学中演示一些重要的过程及参数[1],可有效地提高教学质量.1 课件所用控制系统的物理模型及工作原理图1是一个由伺服阀或比例阀所构成的闭环位置控制系统.U i为输入的电压信号;U f为由位移传感器构成的反馈信号.当U i增加时U i与U f 的偏差信号就会增加,使得3的输出力增加,这样第27卷第1期2005年2月沈 阳 工 业 大 学 学 报Journal of Shenyang University of TechnologyVol 27No 1Feb.2005就会推动4向左侧移动,高压油P s 就会经过阀输出到油缸的左腔,推动油缸向右侧运动,油缸向右侧的运动使得位移传感器1的输出电压U f 增加,U i 与U f 的偏差值就会随之减小直到零为止(无负载时),这样油缸就会在右侧新的位置上停止.如果U i 减小,响应过程与上述过程相反.当输入信号为等幅变频的周期性正弦时,油缸位移的稳态输出值随角频率的变化情况即为频率特性.当输入信号为单位阶跃信号时,油缸位移的瞬态输出随时间的变化情况即为动态响应特性.可通过可视化的油缸运动表现来描述上述两种特性.图1 液压系统模型图F ig.1 M odel of the hydraulic control system 1位移传感器 2双作用对称液压缸的活塞杆 3力马达或比例电磁铁 4伺服阀或比例阀 5电液伺服阀或电液比例阀控制器2 课件所用控制系统的数学模型将图1所示控制系统线性化,可得控制系统传递函数框图,如图2.图2 控制系统传递函数框图Fig.2 T ransfer function of the hydraulic contro l system其中:K a 伺服阀放大器放大倍数;K sv 伺服阀的电流-位移增益;K q 伺服阀流量增益;A p 油缸有效作用面积;W n 无阻尼固有频率;S n 阻尼比;K f 位移传感器放大倍数.根据上边的闭环传递函数框图可得闭环传递函数为[2]G (S )=K vS 3W 2n+2S n W n S 2+S +K v K f(1)其中:K v =K a K sv K qA p这样就可根据频率特性的定义求出闭环幅频特性和闭环相频特性.对应不同的角频率求出不同的幅值衰减量和相位滞后值.将这些数据保存到数组中,作为可视化显示频率特性的数据.将式(1)化成状态方程,利用四阶龙格-库塔法解微分方程组,可得出系统在单位阶跃信号输入下的动态响应数据,将这些数据保存到数组中,作为可视化显示动态响应特性的数据[3].3 课件主要功能简介1)演示说明开环、闭环系统图3为控制系统具有闭环检测回路时(闭环生效时)的一个稳态工作点[4].图3所示的状态为输入电压3V 时的油缸位置,当输入电压不同时可以很明确地看出油缸的位置不同.通过这个界面可以很好地理解位置控制系统的实质及其在生产实际中的具体表现.另外,通过观察阀口开度的变化情况,可以说明偏差控制系统的实质,以及控制系统的主反馈为什么一定是负反馈.图3 闭环状态演示界面Fig.3 Demonstration interface of the closed -loop hy -draulic system图4为反馈回路失效时的控制系统表现状态.当反馈不存在时,油缸只能停留在其两端,系统将不再是位置控制系统,将变成一个无反馈的开环控制系统,无法控制油缸的位置.这种现象也6 沈 阳 工 业 大 学 学 报第27卷正是生产实际中检测回路失效时的一种表现[5].图4 反馈回路失效时状态演示界面Fig.4 Demonstration interface of the hydraulic systemfor the failure mode of feedback loop2)演示说明频率特性图5为频率特性演示界面.讲明频率特性的实质和含义一直是教学过程中的一个难点,通过这个界面可以充分地演示说明频率特性的实质.当输入信号为等幅变频的周期性正弦时,油缸位移的稳态输出值可以通过动画及曲线同时显示在该界面中.选择输入不同的角频率值可以明显地看出油缸输出位移变化的幅值衰减情况及相位滞后情况[6],将输入电压信号与输出的位移信号同时在右侧的PICTURE 框中显示将更有利于观察这一点.另外,软件具有选择显示速度及步长的功能[7],可以通过 慢镜头 进一步进行演示及讲解.界面中右下脚PICTURE 框中显示的是真实坐标下的频率特性曲线[8],而没有采用控制工程中常用的对数坐标,这样将更加有利于理解两种坐标的区别,容易说明对数坐标的实质、含义及优点.图5 频率特性演示界面Fig.5 Demonstration interface of frequency char acteristics3)演示说明动态响应特性图6为动态响应特性演示界面.当输入信号为单位阶跃信号时,油缸位移的瞬态输出通过动画及曲线同时显示在该界面中.当改变控制系统的开环放大倍数时,控制系统的输出将会有所不同,可以明显、直观地看出输出量振荡次数的增多及调整时间的加长,开环放大倍数增加到一定程度,控制系统将不稳定[8].另外,将闭环系统中其它几个重要参数的变化情况(如阀口开度、油缸前腔压力、油缸后腔压力、反馈电压等),也都同时显示在界面中,有利于理解闭环系统中信号的转换、传递、放大等过程.该界面同样具有选择显示速度及步长的功能,以利于演示及观察.该课件中所涉及到的不同的曲线均采用不同的颜色绘制,油缸前、后腔的颜色也随着压力的不同而动态变化,以便更生动的感受信号及参数的变化情况.图6 动态响应特性演示界面F ig.6 Demonstration inter face o f dynamic respo nse4 结 论该课件可以很直观、方便地演示几乎所有在控制工程中所涉及到的重要过程,进而通过它更容易、方便地理解和掌握控制理论中的重要思想.它的演示过程与做实验比较具有明显的优势,它更加灵活、方便、重复使用性强,如果将课件中的功能完全由真实实验来完成,所使用的设备、仪器数量、时间、消耗、复杂程度将都是非常惊人的,在教学时间内几乎不可能完成.控制理论中所涉及到的重要概念和思想几乎分布在课程的各处,可以随时利用该课件进行演示和讲解,这必将给教学质量的提高带来很大的益处.7第1期王野牧等:液压伺服控制系统课件参考文献:[1]吴昌平.Visual Basic6.0程序设计[M].北京:人民邮电出版社,2002.(Wu C P.V isual Basic6.0progr amming[M].Beijing: Posts&T elecom Press,2002.)[2]王春行.液压控制系统[M].北京:机械工业出版社,2004.(Wang C X.Hydraulic control system[M].Beijing: China M achine Press,2004.)[3]何光渝.V ISUA L BASIC常用数值算法[M].北京:科学出版社,2002.(He G Y.G eneral numerical v alue algor ithm on V isual Basic languag e[M].Beijing:Science Press,2002.) [4]成大先.机械设计手册 液压控制[M].北京:化学工业出版社,2004.(Cheng D X.T he handbook of machine design-hydraulic contro l[M].Beijing:Chemical Industry Pr ess,2004.)[5]江小霞,卢长耿,钟荣龙.液压控制系统的动态测试系统[J].液压与气动,2002(11):29-31.(Jiang X X,Lu C G,Zhong R L.Dynamic test system of hydraulic control system[J].Chinese Hy draulics& P neumatics,2002(11):29-31.)[6]Guo H B,L i H R.Study on the characterist ics of thesing le rod hydr aulic cylinder controlled by asymmetric valv e[A].Pr oc.of ISFP[C].W uhan,China,IA PW-PC,2003:477-482.[7]黄晓东,聂继方.电液伺服阀特性计算机辅助测试系统[J].机床与液压,2003,5:187-189.(Huang X D,N ie J F.T he CAT system for t he feature of electro hy draulic servo valve[J].M achine T ool and Hydraulic,2003(5):187-189.)[8]王栋梁,李洪人.阀控液压缸伺服系统的键图分析[J].济南大学学报,2002(12):355-358.(Wang D L,L I H R.Bond g raph analysis on the valve contr olling servo system[J].Jour nal of Jinan U nivers-i ty,2002(12):355-358.)(责任编辑:邓美艳 英文审校:王世杰)待发表文章摘要预报移动机器人数学模型的近似线性化及状态反馈镇定研究姜 勇1,孙茂相1,董再励2(1 沈阳工业大学信息科学与工程学院,沈阳110023;2 中国科学院沈阳自动化研究所机器人学重点实验室,沈阳110016)摘 要:针对机器人控制领域中一类多输入多输出(MIM O)仿射非线性系统,提出了一种基于平衡流形的近似线性化状态反馈镇定算法,并用此算法解决了一类完整约束轮式移动机器人(WMR)的镇定问题.仿真分析表明,此方法不仅能够实现系统的镇定,而且降低了因平衡工作点变动给系统稳定性带来的影响,同时也大大地简化了对非线性系统的综合设计过程,具有良好的控制效果和实用性.8 沈 阳 工 业 大 学 学 报第27卷。
- 1、下载文档前请自行甄别文档内容的完整性,平台不提供额外的编辑、内容补充、找答案等附加服务。
- 2、"仅部分预览"的文档,不可在线预览部分如存在完整性等问题,可反馈申请退款(可完整预览的文档不适用该条件!)。
- 3、如文档侵犯您的权益,请联系客服反馈,我们会尽快为您处理(人工客服工作时间:9:00-18:30)。
C d wxv A1
2 (nPs + PL1 ) ρ (1 + n 3 )
c、非对称阀控非对称缸输出特性
xv > 0
C wx Q v = 1 = d 1 v A1 A1 C wx ( Ps − P1 ) = d 1 v A1 ρ 2 2m 2 ( Ps − PL ) 3 2 ρ (n + m )
xv < 0
P 1 P2
A2 A1
特点:两侧的有效作用面积不同,相同流 量情况下,伸出和缩回的速度不同
xv
A1 ≠ A2
P 1
P2
A1
A2
特点:活塞两端杆径相同,运动特性 相同
xv
A1Hale Waihona Puke = A2P2P 1
A1
P2
A2
xv
A1 = A2
特点:单出杆,作用面积相同,运动 速度相同
§1-1研究的目的意义 2、非对称缸的应用 1、六自由度运动模拟系统
Ps − n 2 FL / A1 P = 1 + n3
' 2
nPs (1 − n ) ∆P = P − P = 1 1 1 + n3
2 ' 1
nP + FL / A1 P' = s 1 1 + n3
Ps (1 − n 2 ) ∆P2 = P2' − P2 = 1 + n3
mL
防气蚀阀组
安全阀组 A B
FL A1 P20 = 1+ n
P2' =
Ps − FL / A1 1+ n
∆P = 0 1
∆P2 = 0
阀与缸不完全匹配( m≠n )
15
15
10 P1(M Pa)
P2(M Pa)
10
p 1' 5 p1
P 2' 5 P2
0
0
-5 -2
-5 -2
-1
0
-1
0
1 FL(N)
2
3 x 10
4
1 FL(N)
QL = Q1 + nQ2 1 + n2
−Q2 = − A2 y +
.
V0
.
βe
P2
5)
QL = A1 y +
.
. V0 PL β e (1 + n 2 )
6)
(3)滑阀的流量方程 Q2 A2 Q1 Q2 = =n 稳态时: = =v Q1 A2 A1 A2 Q1 + nQ2 Q1 (1 + n 2 ) = = Q1 这是有 QL = 2 2 1+ n 1+ n Q1 代表流量连续性方程中的 Q(很牵强的一种近似) L 对表达式 Q1 = Cd ω xv
Q′ C w x v′ = 1 = d 1 v A1 A1
阀的空载最大流量
C wx P1′ = d 1 v A1 ρ 2
Q0 = Cd w1 xv max
2m 2 (nPs + PL ) 3 2 ρ (n + m )
2m 2 P ρ (n3 + m 2 ) s
Q0 Cd w1 xv max = 活塞杆的空载最大速度 v0 = A1 A1 x F 无因次处理 FL = L xv = v PS A1 xv max
FL
-0.25 -0.5 -0.75 -1.0
超压区
xv > 0
v = Q1 C d wx v = A1 A1 2
nV0max+
ρ
( Ps − P1 ) =
C d wx v A1
2 ( Ps − PL1 ) ρ (1 + n 3 )
xv < 0
v′ =
Q1′ C d wx v = A1 A1
2
ρ
P1′ =
2m 2 Ps 3 2 ρ (n + m )
xv >0
xv < 0
x v = v 1 − FL / Ps A1 v0 xv max x v′ = v n + FL / Ps A1 v0 xv max
讨论:
m = 1, m = n, m > n, m < n
1.25
1 2
/ 1 0.75 0.5 0.25 0 -0.25
V QL/A (QL/Q0) V0 + (Q0(Qmax+))
QL = Cd wxv
1
ρ
( Ps −
xv PL ) xv
FL0=0
-1 (-PSA)
1.0 0.75 0.5 05 0.25
Q0 = Cd wxv max
FL=APL (PL/PS)
1 (PSA)
1
ρ
Ps
0
-0.25 -0.5 -0.75 -1.0
P1 (MPa)
×
×
有杆腔( PS = 10MPa )
Ps − n 2 FL / A1 P = 1 + n3
' 2
无杆腔( PS = 10MPa )
xv > 0 xv = 0 xv < 0
压差
n3 Ps + FL / A1 P= 1 1 + n3
nPS + P = 10 FL A1 1+ n
FL A1 P20 = 1+ n PS −
∆P = 0 1
∆P2 = 0
5 0
-2
-1
0
1 FL (N )
2
× 104
3
-2
-1
0 1 FL (N )
2
× 10 4
3
阀与缸不完全匹配( m≠n )
15
15
10 P1(M Pa)
P2(M Pa)
10
p 1' 5 p1
P 2' 5 P2
n(m 2 − n 2 ) Ps ∆P = P − P = 1 1 n3 + m 2
nPs (1 − n 2 ) 1 + n3
5 0 气蚀区
Ps (1 − n 2 ) ∆P2 = P − P2 = 1 + n3
' 2
-2
-1
0
1 FL(N)
2
× 104
3
×
阀与缸完全匹配(m=n)
15 P1 (MPa )
15 P2 (MPa )
10 P1 ,P ' ,P10 1 5 0
10
P2 , 2', 20 P P
§1-2 阀控非对称缸的静态特性
假设条件: 1、理想零开口四通滑阀, 四个节流窗口匹配且对称 2、节流窗口处的流动为紊 流。液体压缩量的影响在 阀中可以忽略; 3、阀具有理想的响应能力, 即对于阀芯位移和阀压降 的变化响应的流量变化能 瞬间发生; 4、供油压力恒定,回油压 力为零; 5、连接管路短而粗、流体 质量影响和管路动态影响 忽略不计; 6、液压缸每个工作腔内压 力相同,油液温度和容积 弹性模型恒定; 7、液压缸内外泄漏为层流 流动; 8、液压缸为理想单出杆液 压缸
2
3 x 10
4
无杆腔的压力变化(m≠n)
有杆腔的压力变化(m≠n)
xv > 0 xv < 0
无杆腔:
n3 Ps + m 2 FL / A1 P= 1 m 2 + n3
nm2 Ps + m 2 FL / A1 P1 = m 2 + n3
'
n 2 ( Ps − FL / A1 ) P2 = m 2 + n3 m 2 Ps − n 2 FL / A1 ' P2 = m 2 + n3
-0.4
/
1.0 0.8 0.6 0.4 0.2 0 -0.2
-0.5
-0.6
-0.75 -1
-0.8 -1.0
n
-1.25 -n
-0.25
0
0.25 /
0.5
0.75
1
对称阀控非对称缸系统输出特性曲线(m=1)
-n3/ 2 /m 1 0.8 0.6 0.4 0.2 0 -0.2 -0.4 -0.6 -0.8 -1 -n 0 -0.2 -0.4 -0.6 -0.8 -1.0 0.5 1-n+n3/m2 1 超压区 (无杆 腔) 气蚀区 (无杆腔) FL0/ 1.0 0.8 0.6 0.4 0.2
A1 P − A2 P2 = m y + Bc y + FL 1
.. .
1) 2)
令 PL = P1 − nP2
A1 PL = m y + Bc y + FL
.. .
3)
2) 2)液压缸流量连续性方程 ①忽略外泄漏 ②两腔容积相同 . V0 . Q1 = A1 y + P 无杆腔: 4) βe 1 有杆腔: 令
2
2
p1
p2
p1'
xv < 0
p1'
p1'
' p2
n3 −nPs A1 ≤ FL ≤ (1 − n + 2 ) Ps A1 m m2 −nPs A1 ≤ FL ≤ 2 Ps A1 n ' '
p2 p2
§1-2 阀控非对称缸静态特性 5. 阀控非对称缸的输出特性(P-Q、F-V特性) a、对称阀控对称缸输出特性
3、道路模拟系统 2、振动模拟系统
§1-1研究的目的意义 3、阀控非对称缸的特点 问题1、阀控非对称缸的控制与阀控对称缸的控制是否一样? ①换向压力突跳问题,易出现气蚀和超压现象; ②两个方向上系统动特性不对称; ③本质的非线性,尤其在分析系统大扰动稳定性和大给定下的动态 品质时,就不易近似的作为线性系统处理,传统的传递函数方式不 适用,需要采用状态空间进行描述 结论1: 非对称缸电液伺服系统远比对称缸系统复杂,控制起来存在许 多问题。 问题2、阀控非对称缸的设计和分析与阀控对称缸的设计分析是否一样? 设计过程一样: 负载特性 动力机构设计 负载匹配 优化设计结果 分析方法不一样: 1)是否存在液压固有频率,如何确定? 2)仿真分析如何做?传统的分析方法是否可行等? 结论2: 分析与设计方法与对称缸电液伺服系统不同