2009-基于仿真的汽车发动机再制造生产线配置优化
X汽车公司发动机装配生产线的分析与优化设计开题报告
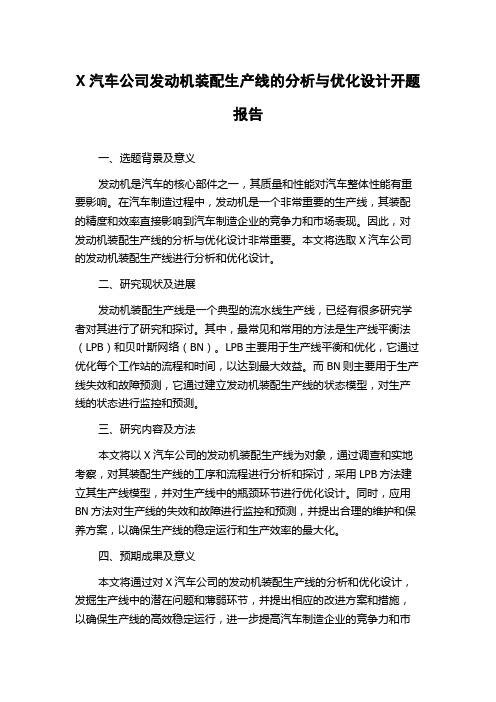
X汽车公司发动机装配生产线的分析与优化设计开题
报告
一、选题背景及意义
发动机是汽车的核心部件之一,其质量和性能对汽车整体性能有重要影响。
在汽车制造过程中,发动机是一个非常重要的生产线,其装配的精度和效率直接影响到汽车制造企业的竞争力和市场表现。
因此,对发动机装配生产线的分析与优化设计非常重要。
本文将选取X汽车公司的发动机装配生产线进行分析和优化设计。
二、研究现状及进展
发动机装配生产线是一个典型的流水线生产线,已经有很多研究学者对其进行了研究和探讨。
其中,最常见和常用的方法是生产线平衡法(LPB)和贝叶斯网络(BN)。
LPB主要用于生产线平衡和优化,它通过优化每个工作站的流程和时间,以达到最大效益。
而BN则主要用于生产线失效和故障预测,它通过建立发动机装配生产线的状态模型,对生产线的状态进行监控和预测。
三、研究内容及方法
本文将以X汽车公司的发动机装配生产线为对象,通过调查和实地考察,对其装配生产线的工序和流程进行分析和探讨,采用LPB方法建立其生产线模型,并对生产线中的瓶颈环节进行优化设计。
同时,应用BN方法对生产线的失效和故障进行监控和预测,并提出合理的维护和保养方案,以确保生产线的稳定运行和生产效率的最大化。
四、预期成果及意义
本文将通过对X汽车公司的发动机装配生产线的分析和优化设计,发掘生产线中的潜在问题和薄弱环节,并提出相应的改进方案和措施,以确保生产线的高效稳定运行,进一步提高汽车制造企业的竞争力和市
场表现。
同时,本文的方法和技术也可为其他类似生产线的优化设计提供参考和借鉴。
制造业生产流水线仿真与优化
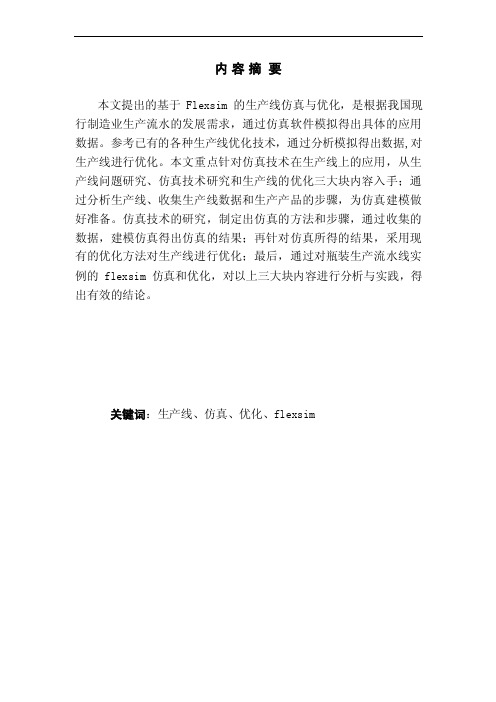
内容摘要本文提出的基于Flexsim的生产线仿真与优化,是根据我国现行制造业生产流水的发展需求,通过仿真软件模拟得出具体的应用数据。
参考已有的各种生产线优化技术,通过分析模拟得出数据,对生产线进行优化。
本文重点针对仿真技术在生产线上的应用,从生产线问题研究、仿真技术研究和生产线的优化三大块内容入手;通过分析生产线、收集生产线数据和生产产品的步骤,为仿真建模做好准备。
仿真技术的研究,制定出仿真的方法和步骤,通过收集的数据,建模仿真得出仿真的结果;再针对仿真所得的结果,采用现有的优化方法对生产线进行优化;最后,通过对瓶装生产流水线实例的flexsim仿真和优化,对以上三大块内容进行分析与实践,得出有效的结论。
关键词:生产线、仿真、优化、flexsimABSTRACTThis paper put forward by Flexsim based on simulation and optimization of the production line, according to existing manufacturing production lines in China's development needs, through the simulation of the simulation software that specific application data. And refer to a variety of existing technologies to optimize production line, through the analysis of simulated data to optimize production lines. This chapter focusing on technology in the production line, from the production line of study, simulation technology research and production lines to optimize,start with these three big parts. Analysis production lines to prepare for simulation modeling, data collection and production of production line products step. According to existing simulation technology, work out the steps of the simulation, through the modeling and simulation data simulation results obtained. Based on the simulation results obtained ,using the existing optimization methods to optimize production lines. Finally,through the case about simulation and optimization of production bottle line, the above analysis of three large pieces of content and practice, to draw valid conclusions.KEYWORDS:Production Line,Simulation, Optimization, FlexsimII目录第一章引言 (1)第一节研究的背景与现状 (1)第二节选题的意义 (1)第二章生产线问题研究 (2)第一节生产线的概念 (2)第二节生产线的生产能力指标 (2)第三节生产线的生产能力的计算与确定 (3)一、单台设备及流水线生产能力的计算和确定 (3)二、设备组生产能力的计算 (3)三、工段(车间)生产能力的计算和确定 (3)第三章离散事件仿真研究 (4)第一节离散事件的概念及要素 (4)第二节离散事件的仿真步骤 (5)第三节 F LEXSIM仿真软件介绍 (7)一、flexsim简介 (7)二、flexsim的功能特点 (8)第四章生产线平衡优化研究 (9)第一节生产线平衡优化的相关概念 (9)第二节生产线平义衡优化的意义 (10)第三节生产线平衡优化的方法 (11)第五章基于FLEXSIM的瓶装生产流水线仿真与优化 (13)第一节基于FLEXSIM对生产线仿真优化的步骤 (13)第二节瓶装生产流水线仿真优化 (14)一、瓶装生产线仿真问题描述 (14)二、瓶装生产线资料的收集与分析 (14)三、瓶装生产线仿真模型的建立 (15)四、装生产线仿真模型的运行与数据分析 (16)五、瓶装生产线仿真模型的优化与再运行 (18)六、瓶装生产线优化后仿真结果分析 (20)第六章结论 (22)中国最大的论文知识平台参考文献 (23)致谢............................... 错误!未定义书签。
基于eM-Plant的汽车后桥装配线仿真与优化

基于eM-Plant的汽车后桥装配线仿真与优化
楚云军;阚树林;许洁;董巧英;任漪舟;尉玉峰
【期刊名称】《机械制造》
【年(卷),期】2008(046)010
【摘要】借助面向对象的仿真软件eM-Plant,对某汽车后桥装配线进行仿真优化研究,提出改进方案.改进后的生产线,增加一个适当容量的缓冲区和少量工人轮班.仿真结果及工厂实践表明,产量和作业率有大幅提高.
【总页数】4页(P26-29)
【作者】楚云军;阚树林;许洁;董巧英;任漪舟;尉玉峰
【作者单位】上海大学,机电工程与自动化学院,上海,200072;上海大学,机电工程与自动化学院,上海,200072;上海大学,机电工程与自动化学院,上海,200072;上海大学,机电工程与自动化学院,上海,200072;上海大学,机电工程与自动化学院,上
海,200072;上海大学,机电工程与自动化学院,上海,200072
【正文语种】中文
【中图分类】TP391.9
【相关文献】
1.基于eM-Plant的路径优化问题仿真研究 [J], 周敏;余昭江
2.基于Em-Plant汽车后桥装配线系统建模与仿真技术研究 [J], 王治军
3.基于eM-Plant的活塞混流生产线仿真与优化 [J], 张伟;曾思通
4.一种基于Em-Plant的AGV物料配送路径优化仿真方案 [J], 徐曼菲;谢竺妍;刘
治红
5.基于eM-Plant的装配线物料配送仿真与优化 [J], 周金波;樊留群
因版权原因,仅展示原文概要,查看原文内容请购买。
基于Witness发动机测试线布局优化和仿真分析

的应 用价值 。
关键 词 : Wi t n e s s ; 发 动机 ; 空间布局 优化 ; 节拍 中 图分类 号 : T H1 2 2; T G 5 0 6 文献 标 识码 : A
第 9期 2 0 1 6年 9月
组 合 机 床 与 自 动 化 加 工 技 术
Mo du l a r Ma c h i n e To o l& A u t o ma t i c Ma nu f a c t u r i ng Te c h n i q u e
NO. 9 S e p.2 01 6
( 1 . S c h o o l o f M e c h a n i c a l E n g i n e e r i n g , D a l i a n U n i v e r s i t y o f T e c h n o l o g y , D a l i a n L i a o n i n g 1 1 6 0 2 4 , C h i n a ; 2 .
廖 忠情 , 郑华栋 , 丛
连 1 1 6 0 3 6 )
明 , 刘 冬 , 刘云ቤተ መጻሕፍቲ ባይዱ
( 1 . 大连 理 工大 学 机 械 工程 学 院 , 辽 宁 大连 1 1 6 0 2 4 ; 2 . 大连 豪 森 瑞德 设 备 制 造 有 限公 司, 辽 宁 大
摘要 : 根 据 某发 动机 测 试 线的 实际运 行情 况 , 运 用 Wi t n e s s 仿 真 软件 对 生产 线进 行 建模 和 优化 分 析 。 利 用软 件 的分析模 块 对仿 真结 果进行 图像 化 处理 , 发现 了原检 测线 中存 在 的 限制 整体 生 产 节拍 的设 计 缺 陷 。通过 对测试 线 的空 间布局 进行 局部 调 整 , 减 少 了测 试 线 的 生产 节拍 和 占地 面 积 、 提 高 了年
基于eM-Plant的汽车焊装生产线仿真与优化技术研究的开题报告
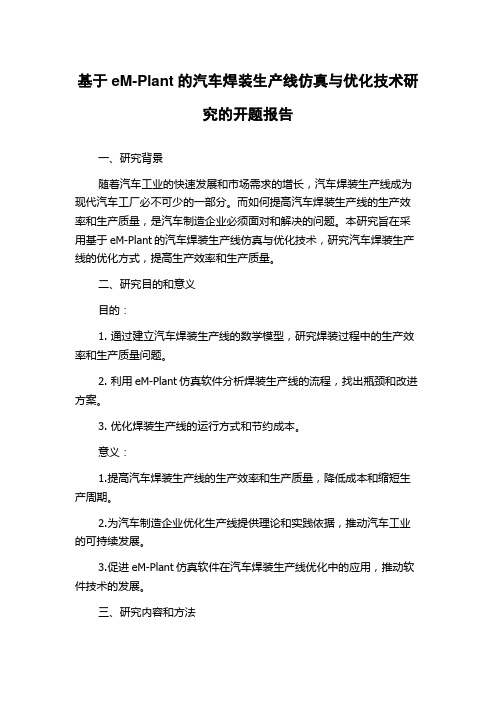
基于eM-Plant的汽车焊装生产线仿真与优化技术研究的开题报告一、研究背景随着汽车工业的快速发展和市场需求的增长,汽车焊装生产线成为现代汽车工厂必不可少的一部分。
而如何提高汽车焊装生产线的生产效率和生产质量,是汽车制造企业必须面对和解决的问题。
本研究旨在采用基于eM-Plant的汽车焊装生产线仿真与优化技术,研究汽车焊装生产线的优化方式,提高生产效率和生产质量。
二、研究目的和意义目的:1. 通过建立汽车焊装生产线的数学模型,研究焊装过程中的生产效率和生产质量问题。
2. 利用eM-Plant仿真软件分析焊装生产线的流程,找出瓶颈和改进方案。
3. 优化焊装生产线的运行方式和节约成本。
意义:1.提高汽车焊装生产线的生产效率和生产质量,降低成本和缩短生产周期。
2.为汽车制造企业优化生产线提供理论和实践依据,推动汽车工业的可持续发展。
3.促进eM-Plant仿真软件在汽车焊装生产线优化中的应用,推动软件技术的发展。
三、研究内容和方法内容:1. 建立汽车焊装生产线的数学模型,分析生产过程和产能瓶颈。
2. 利用eM-Plant仿真软件分析焊装生产线的流程,找出瓶颈和改进方案。
3. 优化焊装生产线的运行方式和节约成本。
方法:1. 搜集汽车焊装生产线的相关知识和资料,建立数学模型。
2. 利用eM-Plant仿真软件对焊装生产线进行仿真模拟。
3. 分析仿真结果,找出瓶颈和改进方案。
4. 通过优化焊装生产线的运行方式和节约成本,提高生产效率和生产质量。
四、预期结果和局限性预期结果:1. 通过建立数学模型和仿真模拟,找到汽车焊装生产线的瓶颈和改进方案。
2. 优化焊装生产线的运行方式和节约成本,提高生产效率和生产质量。
3. 推动eM-Plant仿真软件在汽车焊装生产线优化中的应用,促进软件技术的发展。
局限性:1.研究范围的局限性,只能研究某一特定焊装生产线的优化方法。
2.数据采集的局限性,影响研究的可靠性和准确性。
3.研究过程中的局限性,可能遇到技术和数据难以解决的问题。
制造系统建模与仿真的案例研究.
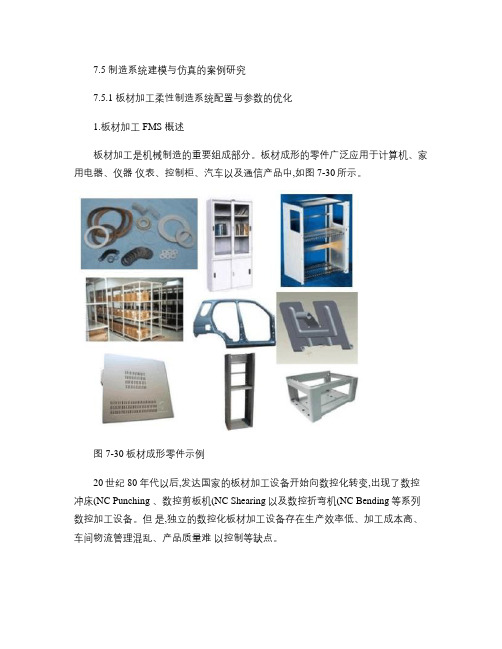
7.5 制造系统建模与仿真的案例研究7.5.1 板材加工柔性制造系统配置与参数的优化1.板材加工 FMS 概述板材加工是机械制造的重要组成部分。
板材成形的零件广泛应用于计算机、家用电器、仪器仪表、控制柜、汽车以及通信产品中,如图 7-30所示。
图 7-30 板材成形零件示例20世纪 80 年代以后,发达国家的板材加工设备开始向数控化转变,出现了数控冲床(NC Punching 、数控剪板机(NC Shearing以及数控折弯机(NC Bending等系列数控加工设备。
但是,独立的数控化板材加工设备存在生产效率低、加工成本高、车间物流管理混乱、产品质量难以控制等缺点。
1967年,英国人研制成功世界上第一条柔性制造系统(FMS 。
1979年,世界上第一条板材加工 FMS 在日本三菱电机公司研制成功。
柔性加工方式具有高效率、高柔性、高质量以及高度自动化等优点,填补了流水线的大批量生产方式与数控加工小批量生产方式之间的空白。
FMS 的出现给机械制造业带来了深远影响。
在欧洲、美国和日本等地区已出现多家专业生产板材数控及柔性加工设备的公司,如意大利 Salvagnini 、芬兰 Finn-Power 、日本 Marata 以及德国 Trumpf 等。
板材加工FMS 可以为企业带来显著的经济效益。
例如:日本 Yaskawa 公司投产一条板材加工FMS 后,操作人员由 23人减少为 9.5人,材料利用率由 76.9%提高到 91.4%,占地面积由 725m 2减少为 377m 2,外包加工费由 37800美元 /月减少为 3000美元 /月,零件库存费用由 41640美元 /月减少为 7500美元 /月,材料种类由 10种减少为 7种。
20世纪 80年代末, 板材柔性加工设备开始进入我国市场。
广西柳州开关厂、上海第二纺织机械厂、江苏扬中长江集团以及南京电力自动化设备厂等多家企业先后从国外引进生产线。
1991年, 我国第一条自主开发的板材加工 FMS 研制成功, 在长城开关厂投入使用。
基于FactoryPrograms的发动机装配线规划仿真

e gn se l ie i ic se n her a ia in t c n lg a e n t e F co y o r mss f r s n i e a s mb y l sd s u s d a d t e l t e h o o y b s d o h a tr Pr g a o t e i n z o wa
20 0 7年 3月
文 章 编 号 :0 8—1 5 ( 07 0 — 0 3— 5 10 6 8 2 0 ) 1 0 3 0
基 于 F c r P o rms的发 动机 装 配 线 规划 仿真 at y rg a o
柴树 峰 , 红 军 王
( 北京机械1 、学院 : 机械工程系 , 京 10 8 ) 北 0 0 5
关
键
词 : 动机 装 配线 ; 发 生产 线规划 ; 仿真模 型 ;atyrga s Fc rPorm ; o
文献标识 码 : A
中图 分类号 :P3 19;H 1 5 T 9 . T 6
Pl n i nd sm ul to f e g n s e b y ln y t m s a n ng a i a i n o n i e a s m l i e s s e b s d o co y o r m s a e n Fa t r Pr g a
生 产过程 、 高生产效 率。发 动机 装 配线 的规 划设 计 需要 计 算机 仿 真技 术 予 以 支撑 和验 证 , 先 提 首 论述 发动机 装配 线的 系统 仿 真技 术 , 介 绍在 软 件 环境 F c rPorm 并 at y rga s下 的具 体 实现 技 术 , o 最后 在 生产线仿 真优化 工具 F c rPorm 环境 下进行 发 动机装 配线建模 仿 真示例 。 at y rga s o
基于模糊机会约束规划的再制造装配车间调度优化方法

基于模糊机会约束规划的再制造装配车间调度优化方法张铭鑫 葛茂根 张 玺 刘从虎 凌 琳 扈 静合肥工业大学,合肥,230009摘要:针对再制造零部件质量的不确定性导致工位装配时间波动范围大和调度模型难以准确描述的问题,采用基于可信性测度的模糊变量表示再制造零部件的装配时间,建立基于置信水平下的模糊机会约束规划调度模型,并提出求解该模型的混合智能优化算法:应用模糊模拟技术产生样本数据;利用反向传播算法训练多层前向神经网络逼近不确定函数;将训练后的神经网络与遗传算法相结合,以优化再制造装配车间调度问题㊂实例验证了该模型和算法的可行性㊂关键词:再制造;装配车间调度;模糊机会约束规划;混合智能算法中图分类号:T H 186 D O I :10.3969/j.i s s n .1004132X.2015.11.011O p t i m i z a t i o n M e t h o do fR e m a n u f a c t u r i n g A s s e m b l y S h o p S c h e d u l i n g B a s e do nF u z z y C h a n c e ‐c o n s t r a i n e dP r o g r a m m i n gZ h a n g M i n g x i n G eM a o g e n Z h a n g X i L i uC h o n g h u L i n g L i n H u J i n gH e f e iU n i v e r s i t y o fT e c h n o l o g y,H e f e i ,230009A b s t r a c t :T h e q u a l i t y u n c e r t a i n t y d u r i n g t h e p r o c e s s o f p a r t s r e a s s e m b l i n g c a u s e d t h e b i g r a n ge of t h e f l u c t u a t i o n o f t h e a s s e m b l y t i m e a n d d i f f i c u l t d e s c r i p t i o n o f s c h e d u l i ng m o d e .A i m i n g a t thi s p r o b -l e m ,t h e a s s e m b l y t i m e o f t h e r e a s s e m b l e d p a r t sw a s r e p r e s e n t e db y t h e f u z z y v a r i a b l e b a s e d o n c r e d i -b i l i t y m e a s u r e t o e s t a b l i s h t h e sc h ed u l i n g m o de lw i t h t h ef u z z y c h a n c e ‐c o n s t r a i n t s b a s e do n t h e c o n f i -d e n c e l e v e l .T h e n ,ah y b r i d i n t e l l i g e n to p t i m i z a t i o na l g o r i t h m w a s p r o p o s e dc o m b i n e dw i t han e u r a l n e t w o r ka n d g e n e t i c a l g o r i t h m ,w h e r e t h en e u r a l n e t w o r kb a s e do nb a c k p r o p a g a t i o na l g o r i t h m sw a s t o a p p r o x i m a t e t h eu n d e t e r m i n e dr e l a t i o nf u n c t i o nb e t w e e nt h e i n p u ta n do u t p u td a t a g e n e r a t e db yu s i n g t h e f u z z y s i m u l a t i o n t e c h n i q u ea n d t h e g e n e t i ca l go r i t h me m b e d d e d t h e t r a i n e dn e u r a l n e t w o r k w a s t o s o l v e t h e s c h e d u l i n g m o d e l .F i n a l l y ,a s t u d y c a s ew a s g i v e n t o p r o v e t h e f e a s i b i l i t y o f t h e p r o -p o s e dm o d e l a n da l go r i t h m.K e y wo r d s :r e m a n u f a c t u r i n g ;a s s e m b l y s h o p s c h e d u l i n g ;f u z z y c h a n c e ‐c o n s t r a i n e d p r o g r a mm i n g ;h y b r i d i n t e l l i g e n t a l go r i t h m 收稿日期:20140822基金项目:国家重点基础研究发展计划(973计划)资助项目(2011C B 013406)0 引言再制造是指通过回收㊁拆卸㊁分拣㊁清洗㊁喷涂㊁翻修及再装配等环节,修复或改造废旧产品,恢复零部件或产品性能的技术和活动[1]㊂与传统制造过程相比,再制造过程对象是报废的成形零件,存在着尺寸超差㊁残余应力㊁内部裂纹和表面变形等一系列缺陷㊂因此,再制造车间具有多重不确定性,集中表现为[2]:①再制造产生的原因及发生时间㊁地点㊁数量等难以准确预测;②再制造产品的性能㊁质量及制造需求不确定;③产品的再制造工艺路线㊁再制造周期及再制造成本不确定;④再制造的目标具有多样性,如减少资源消耗㊁保护环境㊁降低生产成本和提高服务质量等;⑤再制造后产品的市场需求㊁价格等难以准确预计㊂如何在不确定环境下对再制造车间生产调度进行优化设计,保证再制造生产过程顺利运行,已成为再制造企业提高生产管理水平的关键环节之一㊂再制造调度主要包括拆卸调度㊁再加工调度和再装配调度[2]㊂目前,已有学者对再制造生产调度进行了研究㊂L i 等[3]提出了一种混合遗传算法对再制造生产计划进行优化,且运用优先随机批量机制对其进行仿真㊂J a c 等[4]研究了分组作业调度问题,建立了混合整数规划模型,使用智能算法进行求解㊂目前再制造调度研究文献主要集中于再制造加工调度,而对再制造拆卸和装配㊃8841㊃中国机械工程第26卷第11期2015年6月上半月Copyright ©博看网. All Rights Reserved.调度研究较少㊂再制造装配过程中,零部件是由再利用件㊁再制造件和新品件组成,文献[5‐6]描述了再制造装配质量的复杂性,得出零部件的装配质量的不确定性导致工位装配时间波动很大,精确的装配时间难以获得的结论㊂由于再制造产业的特殊性,对于这些不确定性信息,很难估计它的概率分布规律,只能凭借经验或历史数据给出大致的区间估计,故采用模糊理论来描述不确定信息㊂模糊集合理论[7]自从提出以来,在自动控制㊁模式识别等许多领域获得了广泛的应用㊂研究者就模糊调度问题开展了许多研究㊂孙燕等[8]提出一种基于微粒群算法的求解模糊机会约束规划的混合智能算法,通过仿真实验验证了其可行性㊂胡恒等[9]针对加工时间和交货期都不确定的模糊调度问题,提出一种基于多群体并行的遗传算法㊂本文在借鉴现有研究成果的基础上,采用模糊变量来描述再制造车间装配时间的不确定性,构建了基于模糊机会约束规划的再制造装配车间的不确定性模型,提出了一种求解该模型的混合智能算法,并给出了求解方法及相应流程,最后,通过仿真实例验证了该混合智能算法对解决再制造装配车间调度问题的可行性㊂1 再制造装配车间调度问题模型1.1 模糊变量及其数学描述不确定环境下的工位装配时间一般采用随机变量或模糊变量来描述,其中描述随机变量的概率密度函数是以大量稳定的统计数据为基础的㊂对于再制造装配车间而言,零部件质量受回收数量㊁拆卸数量和库存数量等因素的影响,其不确定性往往导致工位装配时间范围波动很大,因此本文采用基于可信性测度的模糊变量来描述再制造车间工位装配时间㊂定义1[10] 设θ是非空集合,P(θ)是θ的幂集㊂如果P o s是可能性测度,则三元组(θ,P(θ), P o s)称为可能性空间㊂定义2[10] 设ξ为一从可能性空间(θ,P(θ), P o s)到实直线R上的函数,则称ξ是一个模糊变量㊂定义3[11] 假设(θ,P(θ),P o s)是可能性空间,A是幂集P(θ)中的一个元素,则称C r{A}= 12(P o s{A}+N e c{A})为事件A的可信性测度㊂在模糊理论中,文献[12‐13]定义了可能性测度P o s{},文献[11]定义了必要性测度N e c{}㊂定义4[14] 设ξ为模糊变量,且α∈(0,1],则称ξi n f(α)=i n f(r|C r{ξ≤r}≥α)为模糊变量ξ的α悲观值㊂1.2 问题描述再制造装配车间调度问题类似于流水车间调度问题㊂描述如下:假定一个再制造装配车间有n个产品要在m台机器上进行装配,由于要组装n 个产品的零部件质量等级不同,导致工位装配时间和装配成本随零部件质量等级波动范围大,是变化的不确定量;每个产品的装配工序都相同,并且以相同的次序在各机器上装配;同时忽略装配工位的流转时间㊁准备时间㊁装配时间和卸载时间,统称为装配时间;在满足工序顺序约束㊁机器约束和交货期约束等前提下以最小化预定置信水平下最大装配时间的悲观值为调度目标㊂该模型满足如下假设:①所有产品在每台机器上装配次序相同;②不同产品之间具有相同的优先级;③同一台机器在某一时刻只能装配一个产品,同一产品的同一道工序在同一时刻只能被一台机器装配;④产品的每道工序一旦开始,装配便不能中断;⑤所有产品在零时刻都可以被装配㊂再制造装配作业调度问题变量描述如下:J= {J1,J2, ,J n}表示n个产品的集,M={M1,M2, ,M m}表示m台机器的集,~S i j㊁~E i j㊁~T i j分别表示产品J i的第j道工序的开始时间㊁完成时间和装配时间,~S i㊁~E i㊁~T i分别表示工件J i的最后一道工序的开始时间㊁完成时间和装配时间,工件J i的交货期为D i㊂1.3 调度建模由于再制造装配时间为模糊变量,因此开始时间㊁完工时间也都是模糊变量㊂在这样的模糊环境下,再制造装配车间调度模型无法像经典约束条件那样,给出一个精确的数学模型和确定的可行集㊂模糊机会约束规划是由L i u等[15]提出的一类模糊规划,其显著特点是模糊约束条件至少以一定的置信水平成立,允许所做决策在一定程度上不满足约束条件,只要求该决策使约束条件成立的可信性不小于决策者预先给定的置信水平㊂它为不确定性决策问题提供了解决思路㊂对于求极小化问题,模糊机会约束规划模型通常表示为m i n fs.t.C r{f(x,ξ)≤f}≥βC r{g i(x,ξ)≤0}≥α i=1,2, ,p式中,x为决策向量;ξ为模糊向量;f(x,ξ)为目标函数;㊃9841㊃基于模糊机会约束规划的再制造装配车间调度优化方法 张铭鑫 葛茂根 张 玺等Copyright©博看网. All Rights Reserved.g i(x,ξ)为约束函数;α㊁β分别为决策者预先给定的置信水平㊂在装配时间为模糊变量的再制造装配车间中,交货期约束可以描述为模糊机会约束,即C r{~E i-D i≤0}≥α i=1,2, ,p现取预定置信水平下最小化最大装配时间悲观值作为优化目标,其模糊机会约束模型描述为m i n Cs.t.C r{m a x(~S i+~T i}≤C}≥β式中,m i n C为目标函数m a x{~S i+~T i}在置信水平β下的最小化最大装配时间的悲观值㊂同时,还要受到产品装配顺序约束和机器资源的约束,即~S i(j-1)+~T i(j-1)≤~S i j~S(i-1)j+~T(i-1)j≤~S i}j综上所述,装配时间为模糊变量的模糊机会约束规划模型可表示为m i n Cs.t.C r{m a x(~S i+~T i}≤C}≥βC r{~E i-D i≤0}≥α i=1,2, ,p~S i(j-1)+~T i(j-1)≤~S i j~S(i-1)j+~T(i-1)j≤~S i j2 模型求解2.1 混合智能算法介绍求解模糊机会约束规划主要有两种方法㊂第一种方法是转化为确定性的等价规划,但这种方法要求目标函数和约束条件的参数符合某种特征分布㊂由于再制造车间的不确定性,导致相关参数呈现模糊性特性,故无法转化为清晰等价形式㊂第二种方法是逼近法,通过模拟仿真生成大量样本数据集来逼近机会约束函数,结合智能算法来优化求解模型㊂第二种方法更符合再制造生产实际,本文在参考文献[10,16]基础上设计一种将模糊模拟技术㊁神经元网络和遗传算法相结合而成混合智能算法,用来对模糊机会约束规划进行求解㊂在仿真平台上,运用模糊模拟技术,产生大量的输入输出样本数据;利用样本数据结合反向传播算法训练多层前向神经网络,逼近不确定函数;将不确定函数嵌入到遗传算法中,检验染色体的可行性和计算染色体的目标值,优化再制造装配调度问题㊂2.2 模糊模拟模糊模拟是对模糊系统进行抽样试验的一项技术,当模拟次数达到一定程度时,模拟值就可以无限接近精确值㊂下面给出本文需要的模糊模拟计算方法㊂利用模糊模拟计算事情的可信性:L=C r{g(x,ξ)≤0}≥α算法步骤[8]如下:(1)设L=C r{g(x,ξ)≤0}㊂(2)分别从θ中均匀产生θk,使得P o s{g(x,ξ(θk))}≥ε,并定义v k=P o s{g(x,ξ(θk))},k= 1,2, ,N,其中ε是个充分小的数㊂(3)计算L=12(m a x1≤k≤N{v k|g(x,ξ(θk))≤0}+m i n1≤k≤N{1-v k|g(x,ξ(θk))>0})(4)若L≥α则将L作为样本数据㊂当采用可信性测度时,利用模糊模拟确定最小的f,使得C r{f(x,ξ)≤f}≥β成立的算法步骤[11]如下:(1)设L(r)=C r{f(x,ξ)≤f}㊂(2)分别从θ中均匀产生θk,使得P o s{f(x,ξ(θk))}≥ε,并定义v k=P o s{f(x,ξ(θk))},k= 1,2, ,N,其中ε是个充分小的数㊂(3)计算L(r)=12(m i n1≤k≤N{v k|f(x,ξ(θk))≤r}+m a x1≤k≤N{1-v k|f(x,ξ(θk))>r})找到满足L(r)≥β的最小值r㊂(4)由L(r)的单调性知,可以采用二分法找到最小的r,返回r㊂这个最小的r可以作为f的估计值㊂本文利用仿真软件E x t e n d建立上述模糊模拟模型,进行多次仿真试验,检验模糊机会约束规划模型的约束条件,并计算优化目标值,为训练神经网络提供近似样本数据㊂2.3 神经网络的函数逼近2.3.1 多层前向神经元网络人工神经网络是由许多神经元连接而成,用以抽象简化和模拟人脑行为的一类适应系统㊂M i n s k y等[17]提出的多层前向神经元网络是目前使用较多的网络结构,已经被广泛用于函数逼近㊁模式识别和网络优化等领域,已经证明对于任何在闭区间的一个连续函数都可以用一个三层前向神经元网络来逼近㊂因此,我们通过模糊模拟产生的大量样本数据,训练神经网络来逼近p+1个不确定函数,即U1(X)=m i n(C r{m a x{~S i+~T i}≤C}≥β) U2(X)=C r{~E i-D i≤0}≥a i=1,2, ,}p 2.3.2 反向传播算法训练神经网络反向传播算法是训练多层前向神经网络的基本方法,它实际上是一种梯度下降的最小化方㊃0941㊃中国机械工程第26卷第11期2015年6月上半月Copyright©博看网. All Rights Reserved.法㊂该过程是通过选择权重来极小化网络输出和实际输出之间的误差,是一种无约束化的计算方法㊂一般以网络输出的误差平方和E(ω)=1N∑N i=1‖F(x i,ω)-y i‖最小作为网络训练的理想结果㊂其中ω为权重向量㊁F(x i,ω)为神经网络的输出映射函数,(x i, y i)为训练数据㊂主要步骤[10]如下㊂(1)初始化权重向量ω,并令μ=1,β=4/3,α=0.05,学习速率η=0.01,预先确定的精确度E0=0.05,适应参数λ=1,k=0㊂(2)k←k+1㊂(3)根据下列两式调整权值ω:Δω1i j←-α∂E k∂ω1i j+ηω1i j=αC1i x1k,j+ηΔω1i jΔω0i j←-α∂E k∂ω0i j+ηω0i j=αC0i x1k,j+ηΔω0i jC1i=λ(d k,i-y k,i)+(1-λ)t a n h(β(d k,i-y k,i))(4)根据下式计算误差E k:E k=12∑m i=1[λ(d k,i-y k,i)2+(1-λ)Φ(d k,i-y k,i)]式中,d k,i为期望输出;y k,i为实际输出;Φ(x)=l n(c o s(βx))/β㊂(5)如果k<N,返回步骤(2),其中,N是学习样本数,k是学习样本的序号㊂(6)计算E=∑N k=1E k㊂(7)如果E>E0,那么k=0,λ=e x p(-μ/E2)并返回步骤(2)㊂(8)结束㊂2.4 利用遗传算法优化再制造装配调度问题(1)编码和解码㊂由于再制造产品装配顺序相同,染色体采用自然数来表示工件的加工顺序㊂例如[42153],表示该批产品的加工顺序为J4㊁J2㊁J1㊁J5㊁J3,一条染色体对应一个可行的调度方案㊂(2)初始化㊂初始化染色体种群,设置种群大小㊁交叉概率㊁变异概率和算法迭代次数等,用训练好的神经网络检测染色体的可行性,判断是否满足交货期机会约束㊂(3)适应度函数㊂将训练后的神经网络嵌入到遗传算法中,根据输出最大装配时间悲观值将染色体由好到坏排序,采用基于序的评价函数e v a l(C h r o m o i)=a(1-a)i-1进行评价,其中,a为评价参数,e v a l表示评价函数,C h r o m o i表示第i 个染色体㊂ (4)选择㊂从父代染色体种群中选择适应值最高的个体遗传到下一代种群中㊂本文采用最常用的轮盘赌选择法进行选择㊂(5)交叉㊂采用随机两点交叉,其操作规则是,首先随机选取两个基因作为交叉基因,交叉后,判断染色体中[1,n]区间内缺失的自然数,然后将未参与交叉基因中重复的自然数替换成缺失的自然数㊂(6)变异㊂随机选取染色体中的部分基因进行互换,以维护种群的多样性㊂(7)算法终止条件为预先设定的最大迭代次数或出现可接受解终止㊂综上所述,混合智能算法主要步骤如图1所示㊂图1 混合智能算法主要步骤3 算例分析以某再制造装配车间为例,现准备装配7个产品,装配工序由5台机器完成㊂根据对历史数据的统计分析,总结出组装产品的再制造件在不同失效等级的概率及对应情况下的模糊加工时间(用三角模糊数表示)和交货期机会约束,如表1所示㊂如组装产品J1的零部件失效等级为二级的概率约为0.56,在机器M1上的工序装配时间为(16,17,19)m i n,即最乐观加工时间为16m i n,最可能加工时间为17m i n,最悲观加工时间为19m i n㊂产品J1在置信水平0.7下,交货期为485m i n;在置信水平0.8下,交货期为500m i n;在置信水平0.9下,交货期为515m i n㊂㊃1941㊃基于模糊机会约束规划的再制造装配车间调度优化方法 张铭鑫 葛茂根 张 玺等Copyright©博看网. All Rights Reserved.表1 废旧件模糊装配时间及交货期机会约束工件失效等级失效等级的概率装配时间(m i n )M 1M 2M 3M 4M 5交货期(m i n )置信水平J 1一级0.31(141823)(353946)(182127)(293540)(5710)4850.7二级0.56(161719)(384144)(202223)(313639)(689)5000.8三级0.13(151922)(364047)(152025)(303742)(5912)5150.9J 2一级0.48(364145)(365563)(293336)(152133)(436073)4800.7二级0.23(344044)(345462)(283235)(132028)(415363)4950.8三级0.29(354145)(365563)(293336)(152133)(436073)5100.9J 3一级0.18(606879)(182327)(172230)(324048)(657078)4500.7二级0.45(687481)(202224)(192427)(434852)(717883)4750.8三级0.37(637077)(223035)(152132)(354350)(506070)5000.9J 4一级0.21(101520)(202837)(586875)(435058)(576065)4500.7二级0.26(71318)(253243)(607080)(505660)(556270)4700.8三级0.53(479)(303541)(667278)(475255)(596367)5000.9J 5一级0.47(91520)(101417)(586269)(283237)(496275)4850.7二级0.24(71015)(81520)(506070)(253035)(455464)5000.8三级0.29(101522)(121422)(556275)(263340)(475867)5200.9J 6一级0.34(51015)(71015)(172530)(202529)(263038)4500.7二级0.51(71116)(5710)(213136)(222630)(283237)4750.8三级0.15(81320)(61215)(192732)(182332)(253340)5150.9J 7一级0.23(182532)(121925)(162430)(546574)(405060)4850.7二级0.63(222730)(141823)(182124)(627076)(455260)5000.8三级0.14(202431)(162027)(202732)(566777)(435665)5150.9本次试验通过仿真软件E x t e n d 建立模糊模拟仿真模型,样本容量为1000,模糊模拟次数为1000,以获得样本数据;基于这些样本数据,利用反向传播算法(初始化权重0.9)训练神经元网络(7个输入神经元,15个隐层神经元,8个输出神经元)来逼近不确定函数;把训练好的神经元网络嵌入到遗传算法中,种群规模50,最大迭代次数1000,交叉概率0.8,变异概率0.1,基于序的评价常数a =0.05,优化目标为满足工序顺序约束㊁机器约束和交货期约束等前提下最小化预定置信水平下最大装配时间的悲观值㊂在C P U 为C O R E ‐2T 5600,主频为1.83G H z ,内存为2G B 的硬件环境上应用MA T L A B R 2009编写仿真实验程序㊂依次改变置信水平,通过运行混合智能算法得到的调度结果如表2所示㊂由表2可以看出,不同的置信水平下,调度方案是不完全相同的,表中的调度结果不一定是最优解,但是能够保证在满足相关约束和在一定置信水平前提下,最大的装配时间悲观值最小㊂随着置信水平的增大,系统的稳定性增强,装配周期也随着增大,表明再制造企业决策者要根据管理目标,选择相应的置信水平,折中选择相应的调度方案㊂由于篇幅所限,只给出置信水平为0.8时,算法最优结果的迭代过程图(图2)㊂从图2可以看出,由于混合智能算法计算量较大,仿真运行时间也较长,在一定置信水平下,该解是一种较理想的妥协解㊂表2 不同置信水平下的调度结果置信水平调度结果最小化最大装配时间悲观值(m i n)0.767534214790.867435214860.96127534503图2 调度结果收敛曲线4 结论(1)针对不确定环境下的再制造装配车间调㊃2941㊃中国机械工程第26卷第11期2015年6月上半月Copyright ©博看网. All Rights Reserved.度问题,采用基于可信性测度的模糊变量描述装配时间,建立了约束条件以一定置信水平成立的模糊机会约束规划调度模型,并研究了模型的求解方法㊂(2)提出了一种集模糊模拟㊁神经网络和遗传算法相结合的混合智能算法㊂应用模糊模拟技术在仿真软件平台上产生样本数据,通过反向传播算法训练神经网络以逼近不确定函数,并将训练好的神经网络和遗传算法相结合,求解再制造装配调度问题㊂(3)通过实例对模型和算法的可行性进行了验证㊂该模型和算法为不确定性环境下再制造装配车间调度理论提供了新的思路和方法㊂参考文献:[1] 徐滨士,刘世参,史佩京,等.汽车发动机再制造效益分析及对循环经济的贡献[J].中国表面工程, 2005(1):1‐7.X uB i n s h i,L i uS h i c a n,S h iP e i j i n g e ta l.S t u d y o n t h eC o n t r i b u t i o no fE n g i n eR e m a n u f a c t u r i n g t ot h eR e c y c l eE c o n o m y[J]C h i n a S u r f a c e E n g i n e e r i n g, 2005(1):1‐7.[2] G u i d eJ rV D R.P r o d u c t i o nP l a n n i n g a n dC o n t r o lf o r R e m a n u f a c t u r i n g:I n d u s t r y P r a c t i c e a n d R e-s e a r c hN e e d s[J].J o u r n a lo f O p e r a t i o n s M a n a g e-m e n t,2000,18(4):467‐483.[3] L i J i a n z h i,M i g u e lG,Z h uY u n.A H y b r i dS i m u l a-t i o n o p t i m i z a t i o nM e t h o d f o r P r o d u c t i o nP l a n n i n g o fD e d i c a t e dR e m a n u f a c t u r i n g[J].I n t e r n a t i o n a l J o u r-n a l o fP r o d u c t i o nE c o n o m i c s,2009,117(2):286‐301.[4] M i nJ,K i mJS,L e eD H.S c h e d u l i n g A l g o r i t h m st o M i n i m i z et h e T o t a lF a m i l y F l o w T i m ef o rJ o bS h o p sw i t hJ o bF a m i l i e s[J].I n t e r n a t i o n a l J o u r n a lo f P r o d u c t i o nR e s e a r c h,2011,49(22):6885‐6903.[5] G eM a o g e n,L i uC o n g h u,L i u M i n g z h o u.T h eO n-l i n eQ u a l i t y C o n t r o lM e t h o d s f o r t h eA s s e m b l i n g o fR e m a n u f a c t u r e dE n g i n e s’C y l i n d e r B l o c k a n dC o v e ru n d e rU n c e r t a i n t y[J].T h e I n t e r n a t i o n a l J o u r n a l o fA d v a n c e d M a n u f a c t u r i n g T e c h n o l o g y,2014,74(1/4):225‐233.[6] L i u M i n g z h o u,L i u C o n g h u,X i n g L i n g l i n g,e ta l.Q u a l i t y O r i e n t e dA s s e m b l y G r o u p i n g O p t i m a l A l l o-c a t i o n M e t h o df o r R e m a n u f a c t u r ed C o m p le x M e-c h a n i c a l P r od u c t s[J].C h i ne s e J o u r n a l o fM e c h a n i-c a l E n g i n e e r i n g,2014,50(8):150‐155.[7] Z a d e h lA.F u z z y S e t s[J].I n f o r m a t i o na n dC o n t r o l,1965,8:383‐353.[8] 孙燕,谭英,曾建潮.求解模糊机会约束规划模型的微粒群算法[J].系统工程与电子技术,2009,31(2): 376‐379.S u n Y a n,T a n Y i n g,Z e n g J i a n c h a o.P a r t i c l eS w a r m O p t i m i z a t i o nf o rF u z z y C h a n c eC o n s t r a i n e dP r o g r a mm i n g M o d e l[J].S y s t e m sE n g i n e e r i n g a n dE l e c t r o n i c s,2009,31(2):376‐379.[9] 胡恒,鲁建厦,李英德.基于多群体并行遗传算法的混流混合车间模糊调度研究[J].浙江工业大学学报,2012,40(5):554‐558.H uH e n g,L uJ i a n s h a,L iY i n g d e.S t u d y o f M i x e d‐M o d e lH y b r i dS h o p F u z z y S c h e d u l i n g P r o b l e mB a s e o n M u l t i‐P o p u l a t i o n s P a r a l l e l G e n e t i c A l g o r i t h m[J].J o u r n a l o fZ h e J i a n g U n i v e r s i t y o fT e c h n o l o g y, 2012,40(5):554‐558.[10] 刘宝碇,赵瑞清,王纲.不确定规划及应用[M].北京:清华大学出版社,2003.[11] L i uB,L i uY K.E x p e c t e dV a l u e o f F u z z y V a r i a b l ea n d F u z z y E x p e c t e d V a l u e M o d e l s[J].I E E ET r a n s a c t i o n s o nF u z z y S y s t e m s,2002,10(4):445‐450.[12] L i uB.T o w a r dF u z z y O p t i m i z a t i o nw i t h o u tM a t h e-m a t i c a lA m b i g u i t y[J].F u z z y O p t i m i z a t i o n a n dD e-c i s i o n M a k i n g,2002,1(1):13‐28.[13] N a h m i a sS.F u z z y V a r i a b l e s[J].F u z z y S e t sa n dS y s t e m s,1978,1(2):97‐110.[14] L i uB.T h e o r y a n dP r a c t i c eo fU n c e r t a i nP r o g r a m-m i n g[M].H e i d e l b e r g:P h y s i c a V e r l a g,2002. [15] L i uB,I w a n m u r aK.C h a n c e‐c o n s t r a i n e dP r o g r a m-m i n g w i t hF u z z y P a r a m e r e r s[J].F u z z y S e t sa n dS y s t e m s,1998,94(2):227‐237.[16] 张国军,李婵娟,朱海平,等.不确定信息条件下J o b‐S h o p调度的混合智能算法[J].中国机械工程,2007,18(16):1939‐1942.Z h a n g G u o j u n,L i C h a n j u a n,Z h u H a i p i n g,e t a l.AH y b r i d I n t e l l i g e n tA l g o r i t h mf o r J o b‐s h o p S c h e d u-l i n g u n d e rU n c e r t a i n I n f o r m a t i o nE n v i r o n m e n t[J].C h i n a M e c h a n i c a l E n g i n e e r i n g,2007,18(16):1939‐1942.[17] M i n s k y M,P a p e r tS.P e r c e p t r o n s[M].C a m b r i d g e,M A:M I TP r e s s,1969.(编辑 袁兴玲)作者简介:张铭鑫,男,1980年生㊂合肥工业大学机械与汽车工程学院讲师㊁博士研究生㊂主要研究方向为生产系统建模与仿真等㊂葛茂根,男,1979年生㊂合肥工业大学机械与汽车工程学院副教授㊂张 玺,男,1985年生㊂合肥工业大学机械与汽车工程学院博士研究生㊂刘从虎,男,1981年生㊂合肥工业大学机械与汽车工程学院博士研究生㊂凌 琳,女,1987年生㊂合肥工业大学机械与汽车工程学院助教㊁博士㊂扈 静,女,1976年生㊂合肥工业大学机械与汽车工程学院副教授㊂㊃3941㊃基于模糊机会约束规划的再制造装配车间调度优化方法 张铭鑫 葛茂根 张 玺等Copyright©博看网. All Rights Reserved.。