渗碳淬火热处理工艺
正火对渗炭淬火质量的影响
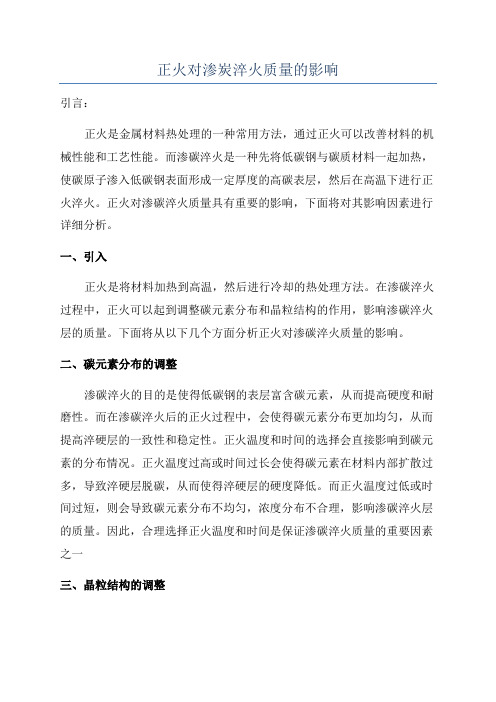
正火对渗炭淬火质量的影响引言:正火是金属材料热处理的一种常用方法,通过正火可以改善材料的机械性能和工艺性能。
而渗碳淬火是一种先将低碳钢与碳质材料一起加热,使碳原子渗入低碳钢表面形成一定厚度的高碳表层,然后在高温下进行正火淬火。
正火对渗碳淬火质量具有重要的影响,下面将对其影响因素进行详细分析。
一、引入正火是将材料加热到高温,然后进行冷却的热处理方法。
在渗碳淬火过程中,正火可以起到调整碳元素分布和晶粒结构的作用,影响渗碳淬火层的质量。
下面将从以下几个方面分析正火对渗碳淬火质量的影响。
二、碳元素分布的调整渗碳淬火的目的是使得低碳钢的表层富含碳元素,从而提高硬度和耐磨性。
而在渗碳淬火后的正火过程中,会使得碳元素分布更加均匀,从而提高淬硬层的一致性和稳定性。
正火温度和时间的选择会直接影响到碳元素的分布情况。
正火温度过高或时间过长会使得碳元素在材料内部扩散过多,导致淬硬层脱碳,从而使得淬硬层的硬度降低。
而正火温度过低或时间过短,则会导致碳元素分布不均匀,浓度分布不合理,影响渗碳淬火层的质量。
因此,合理选择正火温度和时间是保证渗碳淬火质量的重要因素之一三、晶粒结构的调整渗碳淬火后,材料的晶粒结构会出现两种情况,即晶粒细化和晶粒长大。
渗碳淬火后的正火过程中,晶粒结构会得到进一步调整。
正火可以通过晶界扩散、晶界迁移和晶界消解等机制,调整晶粒的大小和形状。
较小的晶粒可以提高材料的强度和硬度,同时也可以提高渗碳淬火层的一致性。
因此,正火温度和时间的选择对晶粒结构的调整具有重要影响。
四、残余应力的消除在渗碳淬火中,材料经历变形和温度梯度的变化,会导致残余应力的产生。
正火可以通过热处理过程中的加热和冷却来调整材料的残余应力,并最终消除它们。
残余应力的存在会影响渗碳淬火层的质量,引起裂纹和变形等问题。
因此,正火的加热温度和冷却速率的选择对残余应力的消除具有重要意义。
五、冷却介质的选择正火的冷却介质是决定渗碳淬火质量的关键因素之一、冷却介质的选择取决于渗碳淬火层的厚度和要求,以及材料的性能要求。
真空渗碳技术工艺控制原理

真空渗碳技术工艺控制原理与传统井式炉气体渗碳工艺不同,真空渗碳时“碳势”的概念失效,不存在气体渗碳时的气氛反应平衡,也就不能使用氧探头等设备测量真空渗碳时的“碳势”。
由于真空渗碳热处理设备的精密性、可控性好和工艺重现性好等优点,真空渗碳工艺主要采用强渗—扩散型工艺控制方法,即采用多个强渗—扩散周期,在每一个周期内通过短时间的强渗(通常强渗时间为30s ~ 180s),工件表层碳浓度达到该渗碳温度下的奥氏体饱和碳浓度,随后停止渗碳气氛供应,进入扩散阶段,当表面碳浓度达到设定的最低碳浓度时,扩散阶段结束,再次通入渗碳气氛,如此进行多个循环,直至达到工艺要求的最终表面碳浓度和渗层深度,最后执行相应的淬火工艺。
图1即为真空渗碳过程工件表面碳浓度分布图。
图1真空渗碳过程工件表面碳浓度随时间分布真空渗碳热处理工艺过程主要分为以下几步:(1)工件清洗、入炉,在真空条件(小于10Pa,基本达到无氧条件)下进行加热,根据工件材质可进行分段加热,可选择通入N2保持一定分压加快真空加热室内热传递速率;(2)达到设定的奥氏体化温度并保温,关闭和抽去N2,充入C2H2,保持一定分压开始进行强渗,进入第一个渗碳周期,强渗一定时间为使工件表面碳浓度达到该温度下奥氏体饱和碳浓度;(3)关闭和抽去C2H2,充入N2,进入扩散阶段,保持一定分压,使工件表面较高碳浓度向工件心部低碳浓度区扩散一定时间,使工件表面碳浓度下降,渗碳层厚度增加;(4)当工件表面碳浓度下降至预先设定的碳浓度,关闭和抽去N2,再充入C2H2,保持分压,进入第二个渗碳周期,然后重复步骤(2)和(3),并在最后一个渗碳周期时给一个较长时间的扩散,以满足工件最终表面碳浓度的要求。
在这样多个渗碳周期内完成碳的扩散并调整工件表面碳浓度,达到工艺要求的渗碳层深度;(5)真空渗碳过程结束后,工件降温至淬火温度并保温一定时间,然后将工件转移至冷室(淬火室),根据热处理工艺要求进行真空油淬。
高碳钢的热处理有哪些方法

高碳钢的热处理有哪些方法高碳钢是一种碳含量较高的钢材,具有优良的机械性能和磨耗性能。
为了进一步改善高碳钢的性能,常常需要进行热处理。
热处理是通过加热和冷却过程改变材料的结构和性能的方法。
下面将介绍几种常见的高碳钢热处理方法。
1. 碳化处理:碳化处理是高碳钢热处理中的一种常见方法。
碳化处理通过在高温下使钢材中的碳元素与铁元素相互作用,形成高硬度的碳化物,从而提高材料的硬度和耐磨性。
碳化处理一般分为两种:渗碳处理和固溶碳处理。
渗碳处理是将高碳钢材浸入含有碳元素的介质中,使碳元素渗透到钢材表面形成碳化层。
常用的渗碳处理方法有气体渗碳、液体渗碳和固体渗碳。
渗碳处理可以使高碳钢的表面硬度和耐磨性大幅提高。
固溶碳处理是在高温下将高碳钢加热至固溶温度,使碳元素溶解到铁晶格中,然后迅速冷却。
固溶碳处理可以提高高碳钢的强度和韧性,但不会改变材料的硬度。
2. 淬火处理:淬火是高碳钢热处理中的一种重要方法。
淬火是指将高碳钢加热至临界温度以上,然后迅速冷却,使钢材的结构发生相变,形成马氏体。
马氏体具有高硬度和脆性,可以提高高碳钢的硬度和强度。
淬火的冷却介质常用水、油和盐等。
淬火过程中需要控制冷却速度,以避免产生过多的残余应力和裂纹。
同时,淬火后的高碳钢通常需要进行回火处理,以降低材料的脆性,提高韧性。
3. 回火处理:回火是高碳钢热处理中的一种常见方法。
回火是指将已经淬火的高碳钢加热至适当温度,保持一段时间后冷却。
回火的目的是通过改变材料的组织结构,降低硬度和脆性,提高韧性和塑性。
回火温度和时间的选择是关键,不同的回火条件会产生不同的效果。
一般来说,高回火温度和长回火时间可以降低材料的硬度和强度,提高韧性和塑性;而低回火温度和短回火时间可以保持较高的硬度和强度,但会降低韧性和塑性。
4. 磁化处理:磁化处理是一种较新的高碳钢热处理方法。
磁化处理通过施加磁场改变高碳钢的磁性,从而改变材料的组织结构和性能。
磁化处理可以提高高碳钢的硬度、耐磨性和疲劳寿命。
渗碳——精选推荐

渗碳⽓体渗碳⽓体渗碳是⽐较完善和经济的渗碳⽅法,它的主要优点如下:①它不需要渗碳箱,零件直接加热,⽣产周期较短。
②易于控制渗碳⽓氛,产品质量较稳定。
③便于直接淬⽕,便于实现⾃动化。
④周围环境清洁,⼤⼤减轻劳动强度。
但是,⽓体渗碳⼀般需要专门的设备,因⽽影响了普遍推⼴使⽤。
⽓体渗碳所采⽤的炉⼦,⼀般有连续式⽆马弗炉和井式炉。
⼀般中,⼩批量⽣产的⼯⼚,⼤都采⽤井式渗碳炉进⾏⽓体渗碳。
渗薄时,把零件装于⽤耐热钢诸如此类料筐内。
放⼊炉膛中,密封加热,然后输⼊氢把有机液体(煤油、苯、酒精、丙酮等)滴⼊炉内。
滴⼊剂的种类很短⽽以煤油应⽤得最⼴泛,因价格便宜,来源充分,且有很强的渗碳能⼒,可满⾜渗碳要求。
(⼀) ⽓体渗碳的基本原理煤油滴⼊渗碳炉后,经过⾼温热裂分解⼀氧化碳(CO),⼆氧化碳(CO2),氧(O2),氢(H2)和饱和碳氢化合物(CnH2n+2)及不饱和碳氢合化物(CnH2n)等多种混合⽓体。
⽓体渗碳主要利⽤其中⼀氧化碳,饱和的碳氢化合物和不饱和的碳氢化合物,靠这些⽓体在渗碳温度分解得到原⼦状态的碳⽽产⽣渗碳作⽤。
2CO —→CO2 + [C]CnH2n+2 —→(n+1)H2 + n[C]⼀氧化碳在⾼温渗碳时,其分解速度较慢,分解与吸收基本平衡,因此,⼀般没有过剩碳沉积,⽽不饱和碳氢化合物,渗碳开始时会猛烈地析出碳,形成⼀层碳⿊,附于零件表⾯,阻⽌渗碳的进⾏。
所以,渗碳⽓体中不饱和碳氢化合物含量应控制低些。
(⼆) ⽓体渗碳⼯艺及操作⒈装炉:把零件与相同钢材的试样⼀起置于渗碳料筐中,零件之间应留5—10mm 间隙,空炉加热(封闭炉盖)⾄920—940℃时将渗碳料筐迅速吊⼊炉膛中,扳紧螺母以压紧炉盖,开⼤甲醇滴量,打开废⽓孔排⽓,并启动风扇马达。
⒉升温:⼯件装炉后⽴即开始升温,此时炉温下降较多,(约800—850℃),⽽⼯件的温度更低。
此时不宜滴⼊⼤量的渗碳剂(因炉温低,不能充分裂解,⽽且⼯件温度低不能吸碳,滴⼊的渗碳剂将会形成⼤量的碳⿊附于⼯件表⾯,影响随后渗碳正常进⾏)。
热处理工艺流程

热处理工艺流程热处理是通过加热和冷却金属材料,改变其内部结构和性能的一种工艺方法。
热处理可以提高材料的硬度、强度、耐磨性、耐蚀性等性能,同时也可以改善材料的加工性能和组织结构。
下面介绍一下常见的热处理工艺流程。
首先是退火工艺流程。
退火是将金属材料加热到一定温度,并在一定时间内保持在此温度下,然后缓慢冷却至室温的过程。
退火可以使材料中的晶粒长大,减少晶界的能量,消除或减少材料中的应力和缺陷,从而提高材料的塑性和韧性。
退火的条件包括加热温度、保温时间、冷却速度等。
第二是正火工艺流程。
正火是将材料加热到一定温度,保温一段时间后快速冷却的过程。
正火可以使材料中的母相转化为奥氏体结构,从而提高材料的硬度和强度。
正火时,加热温度的高低、保温时间的长短以及冷却速度的快慢都会影响材料的性能。
第三是淬火工艺流程。
淬火是将材料加热到一定温度,保温一段时间后,将材料迅速冷却到室温的过程。
淬火可以使材料中的母相快速转变为马氏体结构,从而提高材料的硬度和强度。
淬火时,加热温度、保温时间和冷却介质的选择都对材料的性能起着决定性的作用。
第四是回火工艺流程。
回火是将淬火后的材料加热到一定温度,保温一段时间后慢慢冷却的过程。
回火可以使淬火后的材料中的残余应力得到释放,减少脆性,提高韧性。
回火时,加热温度、保温时间以及冷却速度都会影响回火后材料的性能。
另外,还有一些特殊的热处理工艺,如表面强化工艺。
表面强化是通过改变材料表面的组织和性能,提高材料在特定环境下的耐磨、耐蚀性能。
表面强化工艺包括渗碳、氮化、渗硅等。
总之,热处理在金属材料的制造和加工过程中起着非常重要的作用。
通过合理选择和控制热处理工艺流程,可以使金属材料的性能得到优化和提升。
渗碳淬火的问题和对策
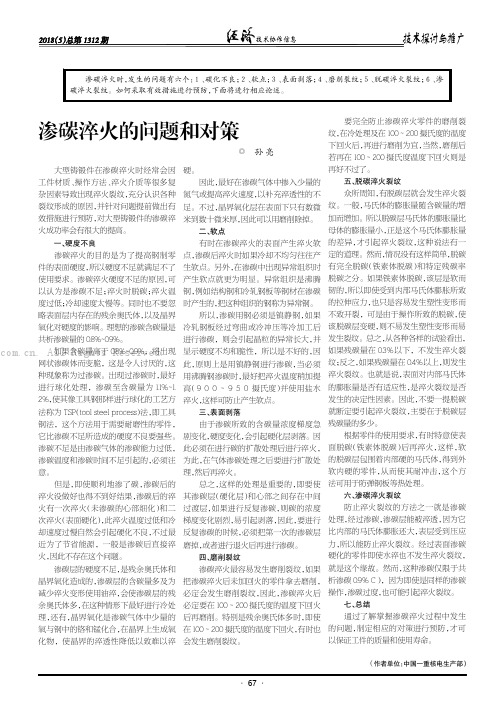
大型铸锻件在渗碳淬火时经常会因工件材质、操作方法、淬火介质等很多复杂因素导致出现淬火裂纹,充分认识各种裂纹形成的原因,并针对问题提前做出有效措施进行预防,对大型铸锻件的渗碳淬火成功率会有很大的提高。
一、硬度不良渗碳淬火的目的是为了提高钢制零件的表面硬度,所以硬度不足就满足不了使用要求。
渗碳淬火硬度不足的原因,可以认为是渗碳不足;淬火时脱碳;淬火温度过低;冷却速度太慢等。
同时也不要忽略表面层内存在的残余奥氏体,以及晶界氧化对硬度的影响。
理想的渗碳含碳量是共析渗碳量的0.8%~0.9%。
如果含碳量高于0.8%~0.9%,将出现网状渗碳体而变脆,这是令人讨厌的,这种现象称为过渗碳。
出现过渗碳时,最好进行球化处理,渗碳至含碳量为1.1%~1.2%,使其像工具钢那样进行球化的工艺方法称为TSP (tool steel process )法,即工具钢法,这个方法用于需要耐磨性的零件,它比渗碳不足所造成的硬度不良要强些。
渗碳不足是由渗碳气体的渗碳能力过低,渗碳温度和渗碳时间不足引起的,必须注意。
但是,即使顺利地渗了碳,渗碳后的淬火没做好也得不到好结果,渗碳后的淬火有一次淬火(未渗碳的心部细化)和二次淬火(表面硬化),此淬火温度过低和冷却速度过慢自然会引起硬化不良,不过最近为了节省能源,一般是渗碳后直接淬火,因此不存在这个问题。
渗碳层的硬度不足,是残余奥氏体和晶界氧化造成的,渗碳层的含碳量多及为减少淬火变形使用油淬,会使渗碳层的残余奥氏体多,在这种情形下最好进行冷处理,还有,晶界氧化是渗碳气体中少量的氧与钢中的铬和锰化合,在晶界上生成氧化物,使晶界的淬透性降低以致难以淬硬。
因此,最好在渗碳气体中掺入少量的氮气或提高淬火速度,以补充淬透性的不足。
不过,晶界氧化层在表面下只有数微米到数十微米厚,因此可以用磨削除掉。
二、软点有时在渗碳淬火的表面产生淬火软点,渗碳后淬火时如果冷却不均匀往往产生软点。
另外,在渗碳中出现异常组织时产生软点就更为明显。
20号钢渗碳淬火变形
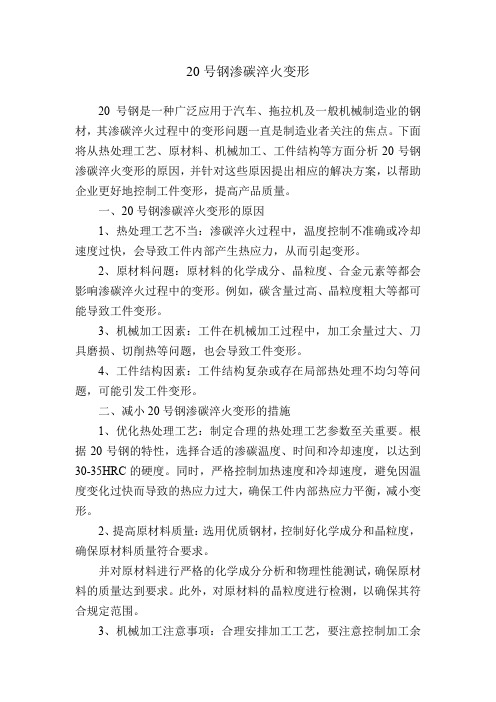
20号钢渗碳淬火变形20号钢是一种广泛应用于汽车、拖拉机及一般机械制造业的钢材,其渗碳淬火过程中的变形问题一直是制造业者关注的焦点。
下面将从热处理工艺、原材料、机械加工、工件结构等方面分析20号钢渗碳淬火变形的原因,并针对这些原因提出相应的解决方案,以帮助企业更好地控制工件变形,提高产品质量。
一、20号钢渗碳淬火变形的原因1、热处理工艺不当:渗碳淬火过程中,温度控制不准确或冷却速度过快,会导致工件内部产生热应力,从而引起变形。
2、原材料问题:原材料的化学成分、晶粒度、合金元素等都会影响渗碳淬火过程中的变形。
例如,碳含量过高、晶粒度粗大等都可能导致工件变形。
3、机械加工因素:工件在机械加工过程中,加工余量过大、刀具磨损、切削热等问题,也会导致工件变形。
4、工件结构因素:工件结构复杂或存在局部热处理不均匀等问题,可能引发工件变形。
二、减小20号钢渗碳淬火变形的措施1、优化热处理工艺:制定合理的热处理工艺参数至关重要。
根据20号钢的特性,选择合适的渗碳温度、时间和冷却速度,以达到30-35HRC的硬度。
同时,严格控制加热速度和冷却速度,避免因温度变化过快而导致的热应力过大,确保工件内部热应力平衡,减小变形。
2、提高原材料质量:选用优质钢材,控制好化学成分和晶粒度,确保原材料质量符合要求。
并对原材料进行严格的化学成分分析和物理性能测试,确保原材料的质量达到要求。
此外,对原材料的晶粒度进行检测,以确保其符合规定范围。
3、机械加工注意事项:合理安排加工工艺,要注意控制加工余量,避免因加工余量过大而导致工件变形。
合理选择刀具,注意刀具的磨损和切削热对工件的影响。
此外,合理安排加工顺序,避免因加工顺序不当导致的工件变形。
4、工件结构设计:工件的结构设计也是影响渗碳淬火变形的重要因素。
设计时应尽量使工件结构简单、对称,避免复杂结构带来的热处理不均匀问题。
对于存在局部热处理不均匀的工件,可以采用局部淬火或分区淬火的方法,以减小变形。
低温化学热处理方法——氮碳共渗
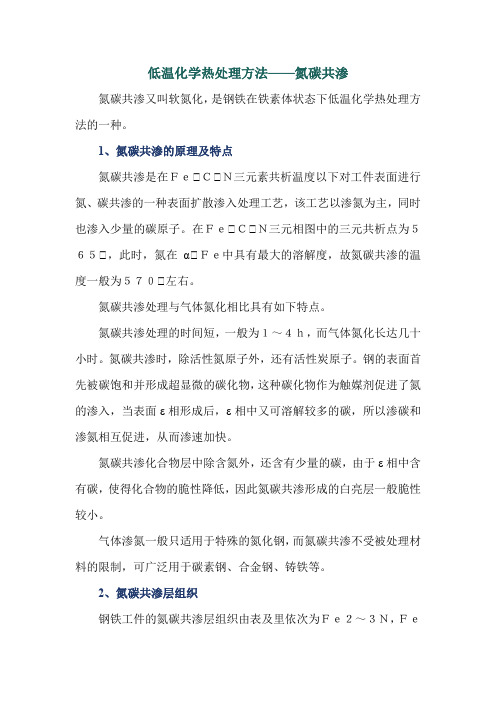
低温化学热处理方法——氮碳共渗氮碳共渗又叫软氮化,是钢铁在铁素体状态下低温化学热处理方法的一种。
1、氮碳共渗的原理及特点氮碳共渗是在Fe⁃C⁃N三元素共析温度以下对工件表面进行氮、碳共渗的一种表面扩散渗入处理工艺,该工艺以渗氮为主,同时也渗入少量的碳原子。
在Fe⁃C⁃N三元相图中的三元共析点为565⁃,此时,氮在α⁃Fe中具有最大的溶解度,故氮碳共渗的温度一般为570⁃左右。
氮碳共渗处理与气体氮化相比具有如下特点。
氮碳共渗处理的时间短,一般为1~4h,而气体氮化长达几十小时。
氮碳共渗时,除活性氮原子外,还有活性炭原子。
钢的表面首先被碳饱和并形成超显微的碳化物,这种碳化物作为触媒剂促进了氮的渗入,当表面ε相形成后,ε相中又可溶解较多的碳,所以渗碳和渗氮相互促进,从而渗速加快。
氮碳共渗化合物层中除含氮外,还含有少量的碳,由于ε相中含有碳,使得化合物的脆性降低,因此氮碳共渗形成的白亮层一般脆性较小。
气体渗氮一般只适用于特殊的氮化钢,而氮碳共渗不受被处理材料的限制,可广泛用于碳素钢、合金钢、铸铁等。
2、氮碳共渗层组织钢铁工件的氮碳共渗层组织由表及里依次为Fe2~3N,Fe3N和Fe4N构成的化合物层(如是合金钢,还有Cr、W、V、Al、Mo等合金氮化物)和扩散层(主要是氮在α⁃Fe中的固溶体)。
碳钢氮碳共渗后的组织由白亮的化合物层和暗黑色的扩散层组成。
化合物层主要为ε相和γ′相。
合金钢氮碳共渗后,表面也得到由ε相和γ′相组成的白亮化合物层。
3、氮碳共渗层性能(1)共渗层硬度氮碳共渗显著提高工件表面硬度及耐磨性,与调质、感应淬火相比较,磨损失重分别降低1~2个数量级。
(2)共渗层的抗疲劳性能氮碳共渗后的疲劳强度高于渗碳或碳氮共渗淬火以及感应淬火。
低、中碳钢可提高40%~80%;合金结构钢提高25%~35%;不锈钢提高30%~40%;灰铸铁提高20%左右,见下图。
▲氮碳共渗处理使疲劳强度提高的情况(球墨铸铁)最近采取在氮碳共渗后高频淬火的复合热处理工艺。
- 1、下载文档前请自行甄别文档内容的完整性,平台不提供额外的编辑、内容补充、找答案等附加服务。
- 2、"仅部分预览"的文档,不可在线预览部分如存在完整性等问题,可反馈申请退款(可完整预览的文档不适用该条件!)。
- 3、如文档侵犯您的权益,请联系客服反馈,我们会尽快为您处理(人工客服工作时间:9:00-18:30)。
渗碳淬火工艺1、钢的淬火钢的淬火与回火是热处理工艺中最重要,也是用途最广泛的工序。
淬火可以显著提高钢的强度和硬度。
为了消除淬火钢的残余应力,得到不同强度,硬度和韧性配合的性能,需要配以不同温度的回火。
所以淬火和回火又是不可分割的、紧密衔接在一起的两种热处理工艺。
淬火、回火作为各种机器零件及工、模具的最终热处理是赋予钢件最终性能的关键工序,也是钢件热处理强化的重要手段之一。
1.1 淬火的定义和目的把钢加热到奥氏体化温度,保温一定时间,然后以大于临界冷却速度进行冷却,这种热处理操作称为淬火。
钢件淬火后获得马氏体或下贝氏体组织。
图4为渗碳齿轮20CrNi2Mo材料淬火、回火工艺。
度200℃8 空冷时间h图4 渗碳齿轮20CrNi2Mo材料淬火、回火工艺淬火的目的一般有:1.1.1 提高工具、渗碳工件和其他高强度耐磨机器零件等的强度、硬度和耐磨性。
例如高速工具钢通过淬火回火后,硬度可达63HRC,且具有良好的红硬性。
渗碳工件通过淬火回火后,硬度可达58~63HRC。
1.1.2 结构钢通过淬火和高温回火(又称调质)之后获得良好综合力学性能。
例如汽车半轴经淬火和高温回火(280~320HB)及外圆中频淬火后,不仅提高了花键耐磨性,而且使汽车半轴承受扭转、弯曲和冲击载荷能力(尤其是疲劳强度和韧性)大为提高。
淬火时,最常用的冷却介质是水、盐水、碱水和油等。
通常碳素钢用水冷却,水价廉易得,合金钢用油来冷却,但对要求高硬度的轧辊采用盐水或碱水冷却,辊面经淬火后硬度高而均匀,但对操作要求非常严格,否则容易产生开裂。
1.2 钢的淬透性2.2.1 淬透性的基本概念所谓钢材的淬透性是指钢在淬火时获得淬硬层深度大小的能力(即钢材淬透能力),其大小用钢在一定条件下(顶端淬火法)淬火获得的有效淬硬层深度来表示,淬透性是每种钢材所固有的属性,淬硬层愈深,就表明钢的淬透性愈好,例如45、40Cr 、42CrMo钢三种试样,按相同条件淬火后(油冷却),经检测45钢能被淬透的最大直径(称临界直径)φ10mm;40Cr钢能被淬透的最大直径φ22mm;42CrMo钢能被淬透的最大直径φ40mm。
实际工件的有效淬硬深度与钢的淬透性、工件尺寸及淬火介质的冷却能力等许多因素有关,例如,同一钢种在相同介质中淬火,小件比大件的淬硬层深;同一钢种相同尺寸时,水淬比油淬的淬硬层深。
同一种钢,其成分和冶炼质量必然在一定范围内波动,因而有关手册上所提供的某钢号的淬透性曲线往往不是一条线,而是一个范围,称淬透性带。
图5为40Cr钢的淬透性带。
图5 40Cr钢的淬透性带钢的淬透性值可用J(HRC/ d )表示,其中J表示末端淬透性,d表示至水冷端的距离,HRC为该处测得的硬度值。
例如淬透性值J (42/5)表示距水冷端5mm处试样硬度值为42HRC;淬透性值J (30~35/10)表示距水冷端10mm处试样硬度值为30~35HRC。
对淬透性值有具体要求的钢应根据GB/T5216-2004《保证淬透性结构钢》标准的规定订货,其钢号最后用H表示,例如42CrMoH。
2、钢的回火2.1 回火的定义和目的钢淬火后必须经过回火,回火是指将淬火钢加热到Ac1(钢件加热时的临界点)以下的某一温度,经过保温,然后以一定的冷却方法冷至室温的热处理工艺,见图4。
回火的目的:2.1.1 降低脆性,减少或消除内应力,防止工件变形或开裂。
2.1.2 获得工艺所要求的力学性能。
淬火工件的硬度高且脆性大,通过适当回火可调整硬度,获得所需要的塑性、韧性。
,它们会自发地向稳定的平衡组织转变,从而引起工件尺寸和形状的改变,通过回火可使淬火马氏体和残余奥氏体转变为较稳定组织,以保证工件在使用过程中不发生尺寸和形状的变化。
2.1.4 对于某些高淬透性的合金钢,空冷便可淬成马氏体,如采用退火软化,则周期很长。
此时可采用高温回火,降低硬度,以利切削加工。
淬火钢不经回火一般不能直接使用,为了避免工件在放置过程中发生变形和开裂,淬火后应及时回火。
2.2、回火的种类淬火钢回火后组织性能决定于回火温度,根据回火温度范围,可将回火分为三类:2.2.1 低温回火低温回火的温度为150~250℃,回火后组织为回火马氏体,低温回火主要降低钢的淬火内应力和脆性,同时保持钢在淬火后的高硬度(一般为58~64HRC)和耐磨性,常用于处理各种工具、模具、轴承、渗碳件及经表面淬火工件。
中温回火的温度为350~500℃,回火后不仅保持较高硬度(一般为35~45HRC)和强度,而且具有高的弹性极限和足够的韧性。
中温回火主要用于各种弹簧的处理,还用于某些塑料模、热锻模以及要求较高强度的轴、轴套等。
2.2.3 高温回火高温回火的温度为500~650℃。
高温回火后的组织为回火索氏体,这种组织具有良好的综合力学性能。
二、化学热处理工件放在一定的化学介质中加热到一定温度,使其表面与介质相互作用,吸收其中某些化学元素的原子(或离子),并自表面向内部扩散的过程称为化学热处理。
化学热处理包括渗碳、渗氮、碳氮共渗等。
化学热处理的结果是改变了金属表面的化学成分和性能。
例如低碳钢经过表面渗碳淬火后,该钢种的工件表面就具有了普通高碳钢淬火后的高硬度、高耐磨的性能特征,而心部仍保留低碳钢淬火后良好的塑性、韧性的特征。
显然这是单一的低碳钢或高碳钢所不能达到的。
1、钢的渗碳1.1钢的渗碳基本原理和气体渗碳工艺在渗碳温度下(920℃)渗碳过程包括三个基本过程:一是由介质(甲醇、煤油、异丙醇)分解出活性原子。
如分解产生的一氧化碳和甲烷分解出活性碳原子:2CO ——CO2+[C]CH4——2H2+[C]二是活性碳原子被工件表面吸收。
三是被吸收碳原子向工件内部扩散。
渗碳过程由分解、吸收、扩散三过程组成,三个过程又是同时发生的,全部过程存在着复杂物理化学反应。
气体渗碳法是将工件放入密封的渗碳炉内,图8为气体渗碳法示意图,使工件在920℃高温的渗碳气氛中进行渗碳。
通入的有机物液体(甲醇、煤油、异丙醇)在高温下分解,产生活性碳原子,并被加热到奥氏体状态的工件表面吸收,而后向钢内部扩散。
渗碳时最主要的工艺参数是加热温度和保温时间。
加热温度愈高,渗碳速度就愈快,且扩散层的厚度也愈深。
图8 气体渗碳法示意图h)图9 气体渗碳典型工艺图9为气体渗碳典型工艺,从工艺中明显可见渗碳剂分解(含排气)、强渗(吸收)、扩散和炉冷到850℃直接油冷淬火的全过程。
1.2 渗碳件质量要求对渗碳件质量要求在国标GB/T8539-2000中已有明确规定,这里对几个主要方面再说明一下。
1.2.1 表面硬度和心部硬度指齿顶部表面硬度。
轮齿的心部硬度是指齿宽中部齿根30o切线的法向上,深度为5倍硬化层深,但不少于1倍模数。
这是一个推荐测量部位,为了便于可操作性,可按技术条件或供需双方协议的图10 齿心部硬度示意图检查方法进行检查。
一般检测齿宽中部法截面上,在轮齿的中心线与齿根圆相交处的硬度,见图10示意图。
表面硬度和心部硬度是工件耐磨性能的重要指标,也是材料抗接触疲劳和弯曲疲劳的一个特性。
经渗碳淬火后表面硬度应达到58~64HRC(大截面齿轮和齿轮轴一般56~62HRC),心部硬度根据不同质量要求按规定控制,一般在25~42HRC,MQ级齿轮要求25HRC 以上,ME级齿轮要求35HRC以上。
硬度一般采用里氏硬度计或洛氏硬度计作为检测工具。
1.2.2 渗碳层表面碳浓度和碳浓度梯度渗碳零件表面碳浓度要求控制在0.75~0.95%为宜,过低会使耐磨性下降,过高时脆性增大,强度不能满足要求。
碳浓度梯度反映了碳浓度沿渗层下降的指标,它间接地反映了渗层的硬度梯度。
碳浓度下降得越平稳越好,以保证渗层与基体牢固结合,避免在使用过程中产生剥落现象。
图11为相同渗碳层总深度(3 mm)三种碳浓度梯度状况。
图11 相同渗碳层总深度(3 mm)三种碳浓度梯度a)好 b)不好 c)不好1.2.3 有效硬化层深度(渗碳层深度)有效硬化层深度取决于零件的工作条件和心部强度,是确定零件承载能力的重要参数。
目前对有效硬化层深度我厂技术设计部推荐采用GC/SY01-10《渗碳淬火齿轮有效硬化层深度技术规范》的标准。
有效硬化层深度是指零件渗碳淬火后,从零件表面到维氏硬度值为550HV1处的垂直距离。
测定硬度所采用的试验力为9.807N(1 kgf)。
1.3、零件渗碳后的热处理工件渗碳的目的在于使表面获得高的硬度和耐磨性,因此渗碳后的工件,必须通过热处理使表面获得马氏体组织,渗碳后的热处理方法有三种:直接淬火法是将工件自渗碳温度炉冷到淬火温度后立即淬火,然后在160~190℃进行低温回火。
这种方法不需要重新加热淬火,因而减小了热处理变形,节省了时间和降低成本,但由于渗碳温度高,渗碳加热时间长,因而奥氏体晶粒粗大,淬火后残余奥氏体量较多,使工件性能下降,所以直接淬火法只适用于本质细晶粒钢或性能要求较低的工件。
这是一般工厂经常采用工艺。
1.3.2 一次淬火法一次淬火法是将工件自渗碳后以适当方式冷至室温,然后再重新加热淬火并低温回火。
对于要求心部有较高强度和较好韧性的零件,可以细化晶粒。
这是大型齿轮、齿轮轴等经常采用方法。
1.3.3 两次淬火法两次淬火法是将工件自渗碳后冷至室温后再进行两次淬火。
第一次淬火目的是细化心部晶粒,淬火温度较高,第二次淬火目的是细化表层晶粒,淬火温度较低,这种方法适宜用使用性能要求很高的工件,缺点是工艺复杂,生产周期长,工件容易变形,工厂应用较少。
对于零件有不允许渗碳硬化部位应在设计图样上标明,该部位可采用防渗涂料进行保护。
近几年来,我厂为适应宝钢进口设备齿轮箱的国产化要求,对热处理进行了相应技术改造,添置具有国内外先进水平的计算机过程控制的大型渗碳炉,由工业计算机、进口智能控温仪、进口智能碳控仪、氧探头等组成,炉温控制精度≤±3℃,炉温采用炉内主控,炉外辅控;碳浓度控制精度≤±0.05%;渗碳层深度偏差≤10%;渗碳硬化层深度范围1~6mm 。
从而对炉内碳浓度、炉温、渗碳硬化层深度等实现精确控制,保证了产品渗碳质量。
为减少盘形齿轮变形,从俄罗斯进口了淬火压床。
目前我厂有φ3000×2000mm、φ2000×2500mm、φ1700×2000mm、φ1200×2000mm、φ900×1200mm井式气体渗碳炉五台。
2、我国对齿轮用钢的冶金质量检验标准和要求齿轮钢材的冶金质量不仅影响到产品的机械性能,特别是疲劳性能,而且还影响到齿轮生产过程中的冷热加工性能及热处理工艺性能。
所以对齿轮钢材的冶金质量有各种规定和要求,现列出部份相关标准和要求,供有关人员查阅和使用。
必须指出,随着对齿轮产品质量要求不断提高和与国外厂商合作的不断加强,对钢材的冶金质量要求会越来越高。