有色冶炼中铁矾渣的资源化利用
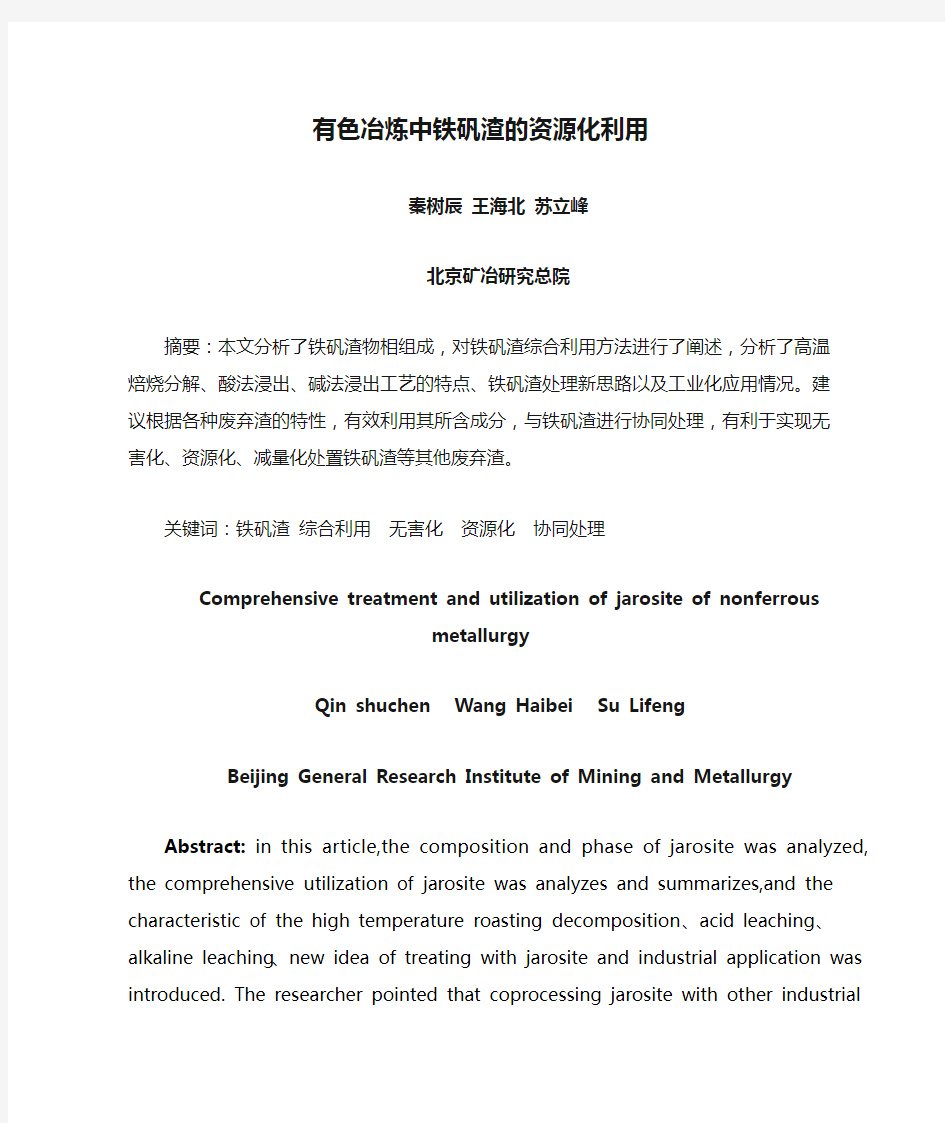

有色冶炼中铁矾渣的资源化利用
秦树辰王海北苏立峰
北京矿冶研究总院
摘要:本文分析了铁矾渣物相组成,对铁矾渣综合利用方法进行了阐述,分析了高温焙烧分解、酸法浸出、碱法浸出工艺的特点、铁矾渣处理新思路以及工业化应用情况。建议根据各种废弃渣的特性,有效利用其所含成分,与铁矾渣进行协同处理,有利于实现无害化、资源化、减量化处置铁矾渣等其他废弃渣。
关键词:铁矾渣综合利用无害化资源化协同处理
Comprehensive treatment and utilization of jarosite of nonferrous metallurgy
Qin shuchen Wang Haibei Su Lifeng
Beijing General Research Institute of Mining and Metallurgy
Abstract: in this article,the composition and phase of jarosite was analyzed, the comprehensive utilization of jarosite was analyzes and summarizes,and the characteristic of the high temperature roasting decomposition、acid leaching、alkaline leaching、new idea of treating with jarosite and industrial application was introduced. The researcher pointed that coprocessing jarosite with other industrial waste slag is conducive to process jarosite and other slag in harmless、reclamation and reducing quantity method.
Key words: Jarosite Comprehensive utilization Harmless Reclamation Coprocessing
1.前言
铁矾渣是湿法炼锌厂除铁过程中产出的固体废弃渣,通常含有铁、铅、锌和铜等有价金属,也会夹杂有铟、银等高附加值金属,具有一定经济回收价值。铁矾渣在一定的酸性条件下能够稳定存在,但当环境PH升高或受热时,会发生分解或者水解,溶出重金属离子,造成土壤和水体污染。因此,铁矾渣不易长期堆放,应及时进行处理合理利用,否则会造成资源浪费,而且也会给周边环境带来污染隐患。
铁矾渣一般含有铁25-30%,铜0.2-0.8%,铅0.5-10%,锌5-12%,有些含有镓、锗、铟和银等稀散贵金属,其物相主要是六方晶系的铵铁矾、黄钾铁矾或铅锌铁矾等混合铁矾、Fe3O4、铁酸锌(ZnFe2O4)和ZnSO4。经分析可知[1],铟主要存在于铁矾中,是铁矾法沉铁过程中以类质同象的形式替代铁离子,占据铁矾晶格形成铟铁矾。银元素也会以类质同象赋存于铁帆中,绝大多数为铁矾所包裹[2-3]。铁矾类物质受热晶格会被破坏,在不同温度段会有发生失重,逐步脱水,脱氨分解,分解形成不同的晶体物质,利用此性质,通常采用热分解或者还原热分解处理铁矾渣[4-5]。
2.铁矾渣综合利用现状
综合处理铁矾渣是提取其有价金属,无害固化处理无价物质,有火法和湿法两大类工艺方法,火法主要是高温焙烧分解处理;湿法主要有:酸浸分解、碱浸分解。
2.1火法工艺
火法处理主要是高温焙烧分解法,是指先在高温下焙烧破坏铁钒晶体结构,使其分解,再利用碳热还原成金属,挥发后再氧化成氧化物进行收集。温度一般为1100~1300℃,配入焦粉或碎煤形成还原性气氛。铁、硅进入渣中进行选矿分离送炼铁系统,铅、锌和铜等金属富集与烟尘中回收利用。
2.1焙烧-磁选法
曹晓恩等人提出直接还原-磁选-反浮选工艺,指出在碱度为2.5,配碳比为1.4,温度为1300℃还原30min金属化率达到98.47%,铅、锌挥发率分别达到86.25%和98.54%,渣在
磁场强度为159.2 KA/m磁选后,铁精矿Ⅰ品位为46.66%,铁回收率达到79.79% ,经反浮选后得到品位60.30%的铁精矿Ⅱ,此工艺体现出工艺简单,生产效率高,分离效果好的优点[6]。
路殿坤等人[7]进行了焙烧-磁选工艺研究,研究指出在900℃还原焙烧后进行磁选,磁选精矿铁品位为58.99-58.72%,含硫2.5-3%,但磁选精矿中锌含量均比尾矿高约1%,不能作为原料返回高炉冶炼。
2.2氯化焙烧法
也有学者提出氯化挥发处理铁矾渣,氯化焙烧是指在一定条件下,借助氯化剂的作用,使物料中的某些组分转变为气相或凝聚相的氯化物,利用金属氯化物低沸点、高挥发性特点,以使有价金属和其它组分分离富集。
1998年F.泰勒卡和D.J.弗雷利用氯气和聚乙烯氯化物残渣对黄钾铁矾进行氯化回收金属,将黄钾铁矾或者将其与锌的铁酸盐混合之后在450-600℃下预热,然后热水浸出,滤渣在空气中用纯氯气进行直接氯化处理或者用聚乙烯氯化物残渣燃烧产生的HCl进行间接氯化处理,直接氯化处理能够使得锌挥发率达到90%以上,50%以上的铁转化成赤铁矿[8]。2.2湿法工艺
2.2.1碱浸分解法
由于碱溶液在常温常压下能够有效分解铁矾,陈永明等人提出NaOH分解含铟铁矾渣新工艺,指出铁矾渣经NaOH溶液浸出分解后形成Na2SO4浸出液和含In和Zn的浸出渣,含In和Zn的浸出渣经盐酸选择浸出后用TBP萃取In和Zn,所得渣经磁选富集后可以作为炼铁原料。研究表明:在m(NaOH):m(铁矾渣)=0.3814:1、温度60℃、液固比2:1、反应时间2h的最优条件下,铁矾渣分解率达到98.03%,其他杂质金属大部分留在渣中,铁主要以Fe3O4形式沉淀入渣,渣中铁能够富集至38.81%,实现有效利用铁资源,但仍有含铅弃渣产生[9]。
北京矿冶研究总院研究了氨水分解铁矾渣的研究,指出在一定条件下氨水能够使得95%铁矾渣分解,约有60%的锌和铜进入溶液中,75%的银留在渣中,经渣样物相分析查明,分解渣样中基本不存在铁矾,同时含硫量很低。
2.2.2酸浸分解法
酸浸分解一是利用浓硫酸直接溶解,再分步结晶使得大部分铁分离,然后生产聚合硫酸铁或者加热分解生产氧化铁或还原制备铁粉;二是酸浸过程中加入金属铁,将一定量的硫酸铁还原为硫酸亚铁,镍、钴和铜等进入硫酸亚铁溶液,采用沉淀法回收,溶液净化后用于制备铁的化工产品,但这些工艺除杂过程较为复杂[10]。
王玉棉等人进行了热酸浸出黄钠铁矾渣工艺研究,研究指出浸出黄钠铁矾渣的最佳工艺条件为:硫酸质量浓度为225 g/ L, 反应温度为95℃, 反应时间为2.5h, Fe、Zn 浸出率均大于96%,黄钾铁矾渣中有价金属反应比较彻底[11]。
程柳等人用浓硫酸在160℃下浸出黄钾铁矾,浸出时间6h,锌浸出率达到98%[12]。
刘鹏飞等人对比研究了硫酸和盐酸浸出黄钾铁矾渣,硫酸浸出黄钾铁矾渣的最佳工艺条件是温度95℃、时间 2 h、搅拌速率300 r/min、硫酸浓度1.2 mol/L、液固质量比100:5,Fe,Zn的浸出率达80%。盐酸浸出黄钾铁矾渣的最佳工艺条件是温度95℃、盐酸浓度2.8 mol/L、搅拌速率400 r/min、时间1.5 h、液固质量比100:5,Fe, Zn, Pb 的浸出率分别达83%, 89%和99%,从渣样中分析可知,盐酸浸出渣中主要是SiO2以及少量Fe2O3,基本上不含Pb元素,盐酸可将渣中Pb全部回收[13]。
北京矿冶研究总院将热酸浸出液与锌精矿、铁矾渣一起加入压力釜内进行,利用热酸浸出液中铁和铁矾渣中铁水解生成赤铁矿产出的酸,以及热酸浸出液残酸浸出锌精矿,实现综合利用,锌浸出率达到96%(按锌精矿含锌计),并且回收铁矾渣中57%以上的锌,提高了
浸出渣中铁含量,减少了铁矾渣堆存。
北京矿冶研究总院开展了氨浸/酸浸-氨性分解-锌液萃取的试验,指出酸性体系浸出效果最好,浸出率达到81%,酸性浸出渣进行氨性分解浸出,锌的分解率达到37%,锌总回收率达到88%,用P204三级萃取锌,总萃取率达到84%。
东北大学符岩等人提出一种综合利用黄钠铁矾渣的方法,利用1%~5%的硫酸溶液按液固比3:1-10:1将黄钠铁矾有价金属选择性浸出,浸出液回收镍、铜、钴和锌等,将浸出渣与硫酸混合,在微波辐射下加热6-15min,加入水和含金属铁的物料,常温下熟化2~8h,调节溶液中的全铁浓度为160~180g/L,并且使得二价铁离子含量占全铁含量的20~40%;加热至40~80℃,加入双氧水反应1~3h,三价铁水解、聚合制备成聚合硫酸铁[14]。
2.3火法-湿法联合工艺
根据铁矾渣特性,适当选择组合火法焙烧和湿法浸出工序,实现有效浸出有价金属,焙烧主要是改变铁矾渣物相,分解难浸物相。
蓝碧波等人提出铁矾渣酸浸-焙烧-酸浸工艺,该工艺首先利用硫酸在室温下浸出铁矾渣中硫酸锌,然后在620℃焙烧1.5h使得铁矾转变成氧化铁,再通过酸浸焙砂中的锌和其他元素。锌回收率能够达到99.11%,酸浸渣中铁含量达到66%以上,可以作为铁精矿产品销售,本方法不仅用于处理铁矾渣也可以用于处理铅银渣,综合回收有价金属[15]。
薛佩毅等人研究了中低温焙烧-NH4Cl浸出-碱浸工艺,铁矾渣在650℃下焙烧1h后,渣中KFe3(SO4)2(OH)6分解为Fe2O3,ZnSO4和PbSO4,在105℃下用6mol/LNH4Cl浸出2h,Zn,Pb和Cd的浸出率均在95%以上,Fe含量由焙烧后的23.21%提高到40%。再用23.08%的NaOH溶液于160℃下浸出1h,Fe含量可提高到54%左右,且As含量可降低到0.1%,最终的浸出渣可作为铁精矿使用。此工艺采用了NH4 Cl体系,能够使得许多有价金属如锌、铅、铜、镍、钴、银等与氯或氨配位进入溶液;而铁、硅、钙等由于溶液呈中性或碱性而不被浸出;可很方便地进行萃取净化[10]。
高丽霞等人研究了中低温活化焙烧-低酸浸出铁矾渣,指出在680-720℃焙烧1.5h后用0.5mol/L的硫酸常温浸出1h,锌浸出率大于95%,铟浸出率达到82%,铁浸出率小于10%,可以有效回收锌和铟,铁没有大量浸出[16]。
2.4铁矾渣处理新思路
魏继业针对富含赤铁矿和铁酸锌的黄钾铁矾渣,利用热酸浸出铁矾渣中铁和锌,经过铁粉还原、硫化沉淀、氟化沉淀等工序制备软磁锰锌铁氧化体用前驱粉体,可以为制备电器元件提供原料,实现铁矾渣的有效利用[17]。
阳征会等人研究了采用还原焙烧-酸浸工艺制备复合镍锌铁氧体,指出黄钠铁矾渣与无烟煤在800℃下还原焙烧0.5h, 铁矾渣中铁被还原为二价铁,焙烧渣用0.5 mol/L 硫酸溶液在70 ℃浸出40 min, 渣中93%的铁和镍进入浸出液中。浸出液经过净化除杂后加入硫酸镍和硫酸锌,以NH4HCO3为沉淀剂制备镍锌铁碳酸盐。该工艺过程简单, 工艺条件易于控制, 为黄钠铁矾渣的有效利用提供了新的途径[18]。
侯小强等人用硅酸盐水泥固化铁矾渣,通过添加外加剂如沸石、硫化钠能够提高重金属离子的稳定性,形成固化体的浸出毒性符合国家标准要求,实现铁矾渣无害化处置[19-21]。
马红周等人采用真空还原蒸馏的方法回收铁矾渣中的铅、锌,在还原蒸馏铅锌的过程中,使渣中铁转变为磁铁矿或者铁单质,经过真空蒸馏,既回收铅锌,又使铁转变为较易回收的形式,从而充分利用铁矾渣中的有价金属,并使铁矾渣减量[22]。
巨少华等人利用微波能具有选择性加热物料、对冶金反应有促进作用、可降低冶金反应的温度等特点,开发了微波硫酸化焙烧-水浸处理铁矾渣的一种清洁的综合利用铁矾渣的方法,将铁矾渣与浓硫酸混合后进行微波焙烧,焙烧渣进行水浸和固液分离后,得到富含有价金属Fe、Zn、In、Cu、Ag和Cd等的浸出液和富含Pb的浸出渣[23]。
姚金环等人也将超声波引入到处理铁矾渣中,利用超声波能够加快铁矾渣溶解,能够提高铟和锌的浸出率。这些都为铁矾渣处理提取有价金属提供了新方法。
2.5铁矾渣处理工业应用现状
目前,铁矾渣综合利用工艺研发较多,也有已经工业化应用的。韩国锌业有限公司(KZC)于1995年8月采用奥斯麦特技术处理锌冶炼产出的黄钾铁矾渣,能够形成一种惰性的利于环保的炉渣。
北京矿冶研究总院针对铁矾渣进行了低酸浸出-中和-萃取回收锌的小型和扩大试验,巴彦淖尔紫金有色金属公司于2012年开工建设年处理20万吨铁矾渣的示范工程,可溶锌总回收率81.15%,年回收锌量4545t/a,减少了渣排放量和渣中有色金属含量,具有显著经济效益和社会效益。
3结束语
铁矾渣是湿法炼锌排放出的一种废弃渣,既是一种污染物也是一种资源,处理铁矾渣要回收其中铅、锌、铜、银和铟等有色金属及伴生稀散贵金属,而且更为重要的是需要一种环境友好的处理方法,实现无害化处置无价物质,不能造成二次污染。
根据其成分及物相状态,选择合适的处理工艺,结合其他废弃渣成分特性,有效利用不同废弃渣,降低有价物料消耗,实现铁矾渣与其他废弃物料资源再生利用与协同处理,或者利用铁矾渣制备具有高附加值产品,有利于实现真正意义上的无害化、资源化、减量化处置铁矾渣等废弃渣。
参考文献
[1]姚金环,丘雪萍,陈钦,张会,李延伟.超声波辅助浸出铁矾渣中铟、锌试验研究[J].湿法冶金,2017,36(04):262-266.
[2]曹晓恩,徐洪军,洪陆阔,武兵强,石鑫越,周和敏,齐渊洪.铁矾渣直接还原-浮选回收银工艺研究[J].矿冶工程,2017,37(02):71-73+78.
[3]黄汝杰,谢建宏,刘振辉.从锌冶炼渣中回收银的试验研究[J].矿冶工程,2013,33(02):52-55.
[4]吴文伟,李姝姝,廖森,吴学航,侯生益,蒙鲜谊,王凡.黄钾铵铁矾的热分解过程及其产物[J].有色金属,2009,61(03):71-75.
[5]曹晓恩,洪陆阔,周和敏,唐小芳,齐渊洪.铁矾渣热分解过程研究[J].矿冶工程,2016,36(02):67-70.
[6]曹晓恩,徐洪军,郭玉华,周和敏,齐渊洪.铁矾渣直接还原—磁选—反浮选工艺探索[J].有色金属(冶炼部分),2016,(06):13-15.
[7]路殿坤,金哲男,谢峰,王萌.铁矾渣还原焙烧制备磁铁矿的研究[J].铜业工程,2013, (01):6-11.
[8]F.泰勒卡, D.J.弗雷, 张明义. 用氯气和聚乙烯氯化物残渣对黄钾铁矾进行氯化以从中回收锌[J]. 现代矿业, 1999,(9):17-19.
[9]陈永明,唐谟堂,杨声海,何静,唐朝波,杨建广,鲁君乐.NaOH分解含铟铁矾渣新工艺[J].中国有色金属学报,2009,19(07):1322-1331.
[10]薛佩毅,巨少华,张亦飞,王新文.焙烧-浸出黄钾铁矾渣中多种有价金属[J].过程工程学报,2011,11(01):56-60.
[11]王玉棉,罗咏梅,侯新刚,王学武.热酸浸出黄钠铁矾渣工艺[J].兰州理工大学学报,2009,35(06):17-21.
[12]程柳,谢涛,卢安军,龙智翔.黄钾铁矾法炼锌矿渣中锌的提取条件试验[J].广西师范学院学报(自然科学版),2011,28(01):50-53.
[13]刘鹏飞,张亦飞,游韶玮,薄婧,江小舵.热酸浸出回收黄钾铁矾渣中有价元素[J].过程工程学报,2016,16(04):584-589.
[14]岩符, 翟秀静, 范川林. 一种综合利用黄钠铁矾渣的方法:, CN 101407355 A[P]. 2009-04-15.
[15]蓝碧波,刘晓英,刘丽华.铁矾渣综合利用技术研究[J].矿产综合利用,2013,(06):54-58.
[16]高丽霞,戴子林,张魁芳,刘志强,董颖超.黄铵铁矾渣的焙烧酸浸行为研究[J].有色金属(冶炼部分),2016,(10):9-11+57.
[17]侯新刚,魏继业,苏瑞娟.利用黄钾铁矾渣制备软磁锰锌铁氧体工艺研究[J].中国有色冶金,2012,B(04):72-76.
[18]阳征会,龚竹青,李宏煦,陈文汨,龚胜.用黄钠铁矾渣制备复合镍锌铁氧体[J].中南大学学报(自然科学版),2006,37(04):685-691.
[19]侯小强,郑旭涛,郭从盛,谭宏斌.极端环境对铁矾渣水泥固化体的影响[J].有色金属科学与工程,2014,5(03):56-59.
[20]谭宏斌,侯小强,郑旭涛,郭从盛. 硅酸盐水泥与铁矾渣反应产物及固化[J]. 有色金属工程,2015,5(06):74-77
[21]侯小强,郑旭涛,郭从盛,谭宏斌.外加剂对水泥固化铁矾渣性能的影响[J].上海有色金属,2014,35(03):123-127.
[22]马红周,桂海平,樊鹏斌,王耀宁,燕超,王曦.湿法炼锌黄钾铁矾渣资源化的新探索[J].工业加热,2016,45(02):8-11.
[23]巨少华, 彭金辉, 刘超, et al.一种微波化硫酸化焙烧-水浸处理铁矾渣的方法:, CN103589861A[P]. 2015-4-22.
作者信息:秦树辰(1990年),助理工程师,从事有色金属冶金科研、设计、咨询等工作。E-mail:qshuchen@https://www.360docs.net/doc/c29135100.html,
基金项目:国际合作项目(KY201502004),科技部科技伙伴计划资助,国家自然科学基金-硫化矿加压湿法冶金的机理研究(51434001)资助
镍电解液净化除铁的生产实践
书山有路勤为径,学海无涯苦作舟 镍电解液净化除铁的生产实践 镍电解液净化除铁的生产实践镍电解厂通常都采用空气中的氧伯化剂,使 阳极电解液中的Fe2+氧化成Fe3+,然后水解沉淀。除铁反应过程受Fe2+氧化 反应速度控制,溶液中存在有少量铜离子时,对Fe2+的氧化有催化作用。因 此,通常都将除铁过程安排在除铜之前。镍电解阳极液水解沉淀所得的含镍 铁渣经酸溶和用氯酸钠氧化后,用黄钠铁矾法除铁。一、阳极电解液净化除 铁除铁作业有连续和间断两种作业方式。大型镍电解厂采用连续作业;小型 工厂则多采用间断作业。连续净化方式质量稳定,设备生产能力大,是这一工 艺发展的方向。除铁过程包括亚铁离子氧化和三价铁水解沉淀反应:除铁 过程有H+生成,须在鼓风同时加入中和剂。为了避免过多的钠离子进入生产 体系常以NiCO3 作除铁中和剂:4H++2NiCO3=2Ni2++2CO2↑+2H2O提高反应 P 可以加速除铁反应,但PH 值过高会引起渣含镍升高。溶液中铜离子的存 在,可以加速Fe2+的氧化反应。这是因为铜离子在Fe2+的氧化过程中起传递 电子作用:Cu+-e=Cu2+Cu2++Fe2+=Cu++Fe3+ 净化水解铁渣还呆带走溶液中 1/3~2/5 的铜,减轻了除铜负担。在除铁过程中,由于使用空气作氧化剂所形 成的溶液电位不足以使Ni2+、Co2+氧化成高价态,但部分Ni2+会以碱式盐的 形式水解沉淀:3NiSO4+4NiCO3+4H2O=3NiSO4.4Ni(OH)2↓+4CO2↑Fe(OH)3 具有很强的吸附性,在除铁过程中,一定量的锌能与Fe(OH)3 产生共沉淀而被 除去,同时部分铜也会水解沉淀: 3CuSO4+2NiCO3+2H2O=CuSo4.2Cu(OH)2↓+2NiSO4+2CO2↑某工厂的除铁过程,是将阳极电解液经钛管换热器加热至65~75℃后,再连续经过5 个75m3 帕 秋卡式空气搅拌槽。往槽内鼓入空气,既作氧化剂,又为搅拌用。在第一个搅拌 槽入口处,加入碳酸镍,中和除铁反应所析出的酸,使除铁反应控制PH 为3.5~4
浅析铜冶炼渣缓冷场设计应注意的几个问题
浅析铜冶炼渣缓冷场设计应注意的几个问题 摘要:本文针对国内已建成的渣缓冷场生产实践中存在的通病,在新建项目设 计中做了部分改进,总结出渣缓冷场设计时需要关注的几个问题,以期为铜冶炼 厂渣缓冷场的工程设计提供有益借鉴。 关键词:渣缓冷场;防渗膜;地面腐蚀和开裂;铸钢板铺设;排水;喷淋系 统 铜冶炼炉渣是铜精矿经冶炼加工后剩余的残渣,其中蕴含丰富的铜、金、银 等有价金属【1】,采用缓冷-磨浮工艺对冶炼渣进行综合回收,选矿后弃渣含铜 品位通常可降至0.25-0.3%之间【2】,具有铜、金、银的回收率高,能耗低【3】、效益好的优势。因此,缓冷-磨浮工艺在国内大型铜冶炼企业得到广泛运用,近年 来相继建成若干座大型铜冶炼渣缓冷场。 渣缓冷场作用在于将熔融态炉渣冷却为固态炉渣,然后将固态炉渣经过翻包 摔渣、破碎、堆存,最终运输至粗破碎车间进入渣选矿生产流程。渣缓冷场处于 熔炼车间和渣选车间承上启下的位置【2】。 鉴于渣缓冷场对铜冶炼生产的重要性,在我公司负责HL铜冶炼厂设计过程中,对国内部分已建成的渣缓冷场生产实践中存在的问题进行了调研,并在本次 工程设计时有针对性的加以改进,特总结出如下几点体会,以期为今后类似工程 设计时提供些许参考: 1.新建缓冷场应特别注意铺设HDPE防渗膜 渣包喷淋冷却水及炉渣淋溶水呈弱酸性并含有少量重金属,会沿着缓冷场混 凝土面层局部开裂缝隙渗至地下,造成一定污染。根据环保需要,渣缓冷场设计 时十分必要在混凝土结构层下铺设HDPE防渗膜。调研发现,受早期公众环保认 识不足的局限,国内已建成的部分渣缓冷场没有铺设防渗膜,如后期增加防渗膜 花费代价太高,很少有企业再进行补救的,致使土壤和地下水的污染无法终止。 随着公众环保意识的提高,在新建渣缓冷场设计阶段,设计人员有责任说服业主 做好渣缓冷场的防渗工程。 在HL铜冶炼厂设计时,渣缓冷场全范围均铺设了HDPE防渗膜。HDPE膜铺 设顺序自下而上为:粘土地基夯实、400g/m2无纺土工布、2.0mm厚光面HDPE 膜、6.0mm复合土工排水网、400g/m2无纺土工布、300mm厚粗砂保护层。缓 冷场混凝土结构层在粗砂保护层上铺砌。 铺膜设计应注意:1)铺膜前地基处理时,应尽量选用透水性差的粘土适当 换填,膜下800mm深度范围的地基压实系数不应小于0.90,与膜接触的地基表 面应设置0.5-0.8%汇水坡度。2)缓冷场应分区域设置一定数量的渗流收集沟或收 集池,收集池内埋设D650mmHDPE管道,用于渗漏观测和抽取残液,见图1。3)HDPE膜上铺设6.0mm复合土工排水网、粗砂保护层,利用粗砂渗透性强和土工 排水网的导流作用,将渗流液能顺利导流排向收集池。 图1 渗漏液收集池 2.混凝土地面应注意采取防止腐蚀和开裂的措施 由于循环喷淋水带有弱酸性,并且缓冷场内行驶的抱罐车满载时荷载大多 120t以上,致使缓冷场混凝土地面出现腐蚀和开裂现象严重,这是国内铜冶炼企
从氰化尾渣中回收金、银的研究进展
氰化尾渣综合利用研究进展 作者:求真 一、氰化尾渣的性质 由于金矿石性质和企业生产工艺的差异,导致氰化尾渣中各元素含量存在着一定的差异,通常氰化尾渣含 Au 1~8 g/t、Ag 25~90 g/t、Fe 20% ~35% 、 S 20% ~ 45% 、SiO225% ~ 40% 、Cu0.5% ~5% 、Pb 1%~5% 、Zn 1% ~ 5% 。 各元素在尾渣中的赋存状态也因原料工艺不同而不尽相同。我国大部分黄金冶炼企业以硫化矿为原料,多采用浮选——焙烧——氰化的工艺从矿石中提金,此种工艺产生的氰化尾渣中铁主要以赤铁矿形式存在,脉石成分主要是石英和硅酸盐类物质,其它金属元素也主要以氧化物形式存在,而金、银被赤铁矿和脉石成分包裹其中。对于少硫化物金矿石,黄金冶炼企业多在浮选得到金精矿后,直接对精矿进行氰化浸出,此工艺产生的氰化尾渣中,铁主要以黄铁矿形式存在,脉石同样是石英和硅酸盐类,其它金属也主要以硫化物形式存在,金、银被包裹在黄铁矿和脉石中。尽管元素含量不同且元素赋存状态有所区别,但氰化尾渣在性质上仍具有一些共同特点如: 氰化尾渣多为粉末,粒度较细,且泥化现象严重,氰化尾渣中铁含量和脉石含量较高等。而从氰化尾渣中回收金、银,难点在于: (1) 氰化尾渣中的金、银多以微细粒嵌存在铁矿物和脉石矿物中,常规手段难以使金银有效单体解离,导致氰化尾渣中的金、银回收困难。 (2) 氰化尾渣粒度较细,泥化现象严重,矿石经长时间氰化后,矿物表面性质发生变化且渣中含有残留氰化物,导致浮选处理较为困难。 近年来,国内外科技工作者在氰化尾渣的综合回收利用上做了大量试验研究,并取得了一定的进展。但是各种方法均存在着一定的局限性,如成本较高,回收金银的成本远高于氰化尾渣的附加值,适应性较差,不宜推广应用等缺点。目前,研究重点在于,如何建立一套低成本、且适应性较高的工艺对氰化尾渣进行回收利用。 目前处理氰化尾渣有几种不同的方法,包括湿法、火法、浮选法等。采用湿法处理氰化尾渣,一般通过浸出破坏金、银的包裹态,使金、银裸露并富集。采用火法处理氰化尾渣,一般通过焙烧破坏黄铁矿或者赤铁矿对金、银的包裹,使金、银充分裸露。采用浮选法回收氰化尾渣中的金、银,一般使金、银富集在精矿中,再进行回收利用。 二、从氰化尾渣中回收金、银的方法 1、湿法回收金、银 根据氰化尾渣中大部分金、银被铁矿物包裹的特点,科技工作者提出湿法处理氰化尾渣的思路,即利用湿法冶金手段使金、银解离成单体。由于各地氰化尾渣在性质上存在差异,所以处理方法也不尽相同。按预处理方法的不同,具体又可分为酸浸-浸出法、氧化-浸出法、细磨—浸出法等方法。 (1)酸浸—浸出法 采用酸浸—浸出法处理氰化尾渣,主要适用于处理金被赤铁矿包裹的氰化尾渣。
铜冶炼水淬渣中铜的资源化利用研究
铜冶炼水淬渣中铜的资源化利用研究 本文采用湿法冶金技术对我国铜冶炼过程中产生的大量水淬渣进行铜的资 源化利用研究,研究采用氧化氨浸法对铜冶炼水淬渣中铜进行浸取,并考察浸取 时间、浸出温度、过硫酸铵用量、氨水浓度、渣样粒度大小、搅拌转速、液固比对铜浸出率的影响,得出铜浸出的最佳条件。浸出后的溶液与硫化铵反应,制取硫化铜,并研究硫化铵用量、反应温度、机械搅拌速度、反应时间对浸出液中铜回收率及硫化铜纯度的影响,得出影响浸出液中铜回收率及硫化铜纯度的最佳条件。 具体实验结果如下:(1)取10g渣样,当控制温度为50℃,浸取时间为120min,粒径大小为100目,转速为400r/min,(NH4)2S2O8用量为渣样的0.7倍,NH3·H2O 浓度为10mol/L时考察液固比(m/m)对铜冶炼水淬渣中铜、锌浸出率的影响。实验结果表明:最佳液固比为4:1(m/m),此时,Cu浸出率为49.1%,Zn浸出率为 0.32%。 (2)取10g渣样,当控制液固比(m/m)为4:1,浸取时间为120min,粒径大小为100目,转速为400r/min,用量为渣样的0.7倍,NH3·H2O浓度为10mol/L时考察温度对铜冶炼水淬渣中铜、锌浸出率的影响。实验结果表明:最佳温度为35℃,此时,Cu的浸出率为53.5%,Zn的浸出率为0.15%。 (3)取10g渣样,当控制液固比(m/m)为4:1,温度为35℃,粒径大小为100目,转速为400r/min,用量为渣样的0.7倍,NH3·H2O浓度为10mol/L时考察浸取时间对铜冶炼水淬渣中铜、锌浸出率的影响。实验结果表明:最佳浸取时间为180min,此时,Cu的浸出率为58.3%,Zn的浸出率为0.23%。 (4)取10g渣样,当控制液固比(m/m)为4:1,温度为35℃,浸取时间为180min,转速为400r/min,用量为渣样的0.7倍,NH3·H2O浓度为10mol/L时考察粒径大
铜冶炼炉渣混合浮选工艺研究及生产实践
铜冶炼炉渣混合浮选工艺研究及生产实践 张鑫,惠兴欢,朱江,杞学峰,王礼珊 (楚雄滇中有色金属有限责任公司,楚雄) 摘要:本文针对楚雄滇中有色金属公司铜冶炼过程产生的电炉渣、转炉渣进行了混合浮选研究。混合渣含铜,磨至细度为后进入浮选作业,通过二次粗选、二次扫选、粗精矿不磨三次精选的工艺流程,可获得铜精矿品位为,尾矿品位以下,回收率以上的工艺指标。在实际生产中,通过对工艺流程的改造,又进一步优化了浮选指标。 关键词:电炉渣;转炉渣;浮选 , , , , ( . ,,) :( ) . . ( ) . , ( ) . . : , , 引言 我国铜炉渣数量大,其中大量铜及相当数量的贵金属和稀有金属长期堆存,占用大量用地,严重污染环境。随着冶炼技术的发展,髙效率熔炼炉的应用,炉渣含金属量还有上升趋势。因此,开发利用铜炉渣资源具有重要意义和十分可观的经济效益。 近年来,国内外很多单位对铜渣的利用进行了不同规模的研究,主要集中在以下两方面:()提取有价金属[];()生产化工产品和制备建筑材料等[].尽管取得一定成绩,但是铜渣综合利用水平低,循环力度弱的状况仍未改变。铜渣的贫化方法有熔炼法和缓冷选矿法,选择何种方法,要根据渣中金属存在形态和经济效果的对比来决定。魏明安[]研究了转炉渣的特性和铜转炉渣选矿的一般特点。并在此基础上,针对国内某铜转炉渣中铜赋存状态复杂、嵌布粒度细及难磨等的特点,提出处理该转炉渣的适宜技术条件为阶段磨矿阶段选别,在浮选机充气量3.3L和高浓度浮选的条件下,取得了铜精矿铜品位、回收率为的实验室闭路试验指标。云南耿马铜渣由于其含铜品位低,回收利用难,研究结果表明,浮选可以很好地对其进行回收利用,浮选条件为:磨矿细度-0.074mm占、捕收剂用量为162g、活化剂硫化钠用量为3.4kg的条件下得到了品位、回收率的较好试验结果[]。宋温等[]针对某转炉冶炼厂的炉渣硬度大、难磨且氧化程度较高的情况,采用一粗一精二扫中矿循序返回的浮选流程。药剂采用丁黄药、松醇油。原矿品位为,得到了铜精矿品位,铜回收率的浮选指标。 采用选矿方法从炉渣中可以回收大部分铜,不但可获得一定的经济效益,而且还可实现铜资源最大限度的合理利用,这符合当前发展循环经济,建设节约型社会的基本国策。 铜渣的工艺矿物学研究 楚雄滇中有色金属有限责任公司冶炼厂采用的铜冶炼工艺为:富氧顶吹熔炼电炉沉降转炉吹炼,沉降电炉排出的渣含铜品位约~左右,转炉渣不返入电炉(品位约),转炉渣分解破碎后大部分进入艾萨熔炼系统,使得生产成本急剧增加,同时也会造成电炉渣含铜增加,每年损失大量铜金属,为此,需要对炉渣贫化进行专门研究。 铜渣的物理特性 楚雄滇中有色金属有限责任公司冶炼铜渣经缓冷后,外观呈黑色,松散容重2.4g,密度。性质比较稳定,嵌布粒度较细。铜渣含铁量很高,故它的质地致密、坚硬,莫氏硬度达到度,
黄钾铁钒法沉铁
A 黄铁矾法除铁原理 a 黄铁矾沉淀组成及热力学稳定性 黄铁矾的分子式通常可以写成A 20·3Fe 2 3 ·4S0 3 ·6H 2 0或AFe 3 (S0 4 ) 2 (OH) 6,或A 2 [ Fe 6 ( SO 4 ) 4 (OH) 12 ,式中A代表一价阳离子,即可以是K+、Na+、 NH 4+、Rb+、Ag+、—Pb2+或H 3 +O等,例如: 黄钾铁矾:KFe 3 (S0 4 ) 2 (OH) 6 ,其化学组成:K 2 0 9.41%,Fe 2 3 47.83%, S0 331.97%,H 2 0 10.79%。黄钠铁矾:NaFe 3 (S0 4 ) 2 (OH) 6 ,其化学组成:Na 2 0 6.4%; Fe 20 3 49.42%;S0 3 33.04%,H 2 0 11.14%。黄铵铁矾:NH 4 Fe 3 (S0 4 ) 2 (OH) 6 ,其 化学组成:(NH 4) 2 O 5.43%,Fe 2 3 49.93%,S0 3 33.37%,H 2 0 11.27%。 这些化合物通常称黄钾铁矾或黄铁矾。在自然界里,有些矿物具有类似的组成,相同的结构和结晶形态,即所谓类质同晶。所谓矾,是一系列类质同晶矿物的总称,而黄钾铁矾是矾中的一种。 波北兹涅克和麦尔文研究了Fe 20 3 -S0 3 -H 2 0三元系在某些温度下的平衡情 况,如下图所示。所有碱式盐、酸式盐及正盐都位于三元系相图内部,这是由于 它们都含有结晶水的缘故。无水硫酸高铁位于Fe 20 3 -S0 3 二元系线上,但它在50℃ 和75℃的条件下不是平衡相,即不会从溶液中以这种成分析出,因而没有在图上出现。按照平衡固相来分类,图大致可分成以下三类区域:
中和渣资源化利用研究进展
Sustainable Development 可持续发展, 2020, 10(4), 501-506 Published Online September 2020 in Hans. https://www.360docs.net/doc/c29135100.html,/journal/sd https://https://www.360docs.net/doc/c29135100.html,/10.12677/sd.2020.104063 中和渣资源化利用研究进展 张艺婷1,2,尹少华1,2*,李浩宇1,2,朱镕1,2,张利波1,2* 1昆明理工大学冶金与能源工程学院,云南昆明 2昆明理工大学省部共建复杂有色金属资源清洁利用国家重点实验室,云南昆明 收稿日期:2020年5月31日;录用日期:2020年8月17日;发布日期:2020年8月24日 摘要 中和渣通常含有锌、铜、镍、钴、锗等有价元素,是综合回收重要的二次资源。目前国内中和渣处理方法大致有三类:1) 通过火法处理回收有价元素;2) 通过湿法处理回收有价元素;3) 替代水泥在建筑领域或作为辅剂进行直接利用。本文总结归纳了以中和渣为研究对象,针对不同有价金属综合回收的工艺流程及过程参数等,为冶金企业的工艺选择提供参考依据。 关键词 中和渣,二次资源,有价元素,资源化利用 Research Progress on Resource Utilization of Neutralization Slag Yiting Zhang1,2, Shaohua Yin1,2*, Haoyu Li1,2, Rong Zhu1,2, Libo Zhang1,2* 1Faculty of Metallurgical and Energy Engineering, Kunming University of Science and Technology, Kunming Yunnan 2State Key Laboratory of Complex Nonferrous Metal Resources Clean Utilization, Kunming University of Science and Technology, Kunming Yunnan Received: May 31st, 2020; accepted: Aug. 17th, 2020; published: Aug. 24th, 2020 Abstract Neutralization slag usually contains some valuable elements, such as zinc, copper, nickel, cobalt and germanium, and it is an important secondary resource for comprehensive recovery. At present, *通讯作者。
氰化尾渣处理安全操作规程
编号:SM-ZD-12499 氰化尾渣处理安全操作规 程 Through the process agreement to achieve a unified action policy for different people, so as to coordinate action, reduce blindness, and make the work orderly. 编制:____________________ 审核:____________________ 批准:____________________ 本文档下载后可任意修改
氰化尾渣处理安全操作规程 简介:该规程资料适用于公司或组织通过合理化地制定计划,达成上下级或不同的人员之间形成统一的行动方针,明确执行目标,工作内容,执行方式,执行进度,从而使整体计划目标统一,行动协调,过程有条不紊。文档可直接下载或修改,使用时请详细阅读内容。 1.上班时,必须穿戴好必备的劳动保护用品。 2. 正常开车时,要尽量保持连续均匀给矿,减少波动。 3. 控制好上矿浓度在要求范围内。 4. 检查真空度是否在-0.09~0.098MPa,滤液池液位是否正常。 5.检查刮刀运行情况,松紧度是否合适,有无积矿。 检查主电机、减速机有无异声、震动、发热现象。 水过滤器前后压力差不大于0.1MPa,后压力不小于0.15MPa,若发现问题,应及时更换或冲洗滤芯. 反冲洗水压力为0.08~0.12MPa,不得超过0.12MPa. 缓冲器压力与反冲洗压力相同. 10.气压在0.4~0.7MPa. 11.清洗前必须穿戴好劳保用品防护服装和面具,酸泵必须用50%至68%浓硝酸供液,温度应保持常温,槽体必须
湿法炼锌酸浸液除铁-黄钾铁矾法沉淀除铁
湿法炼锌酸浸液除铁-黄钾铁矾法沉淀除铁 A 黄铁矾法除铁原理 a 黄铁矾沉淀组成及热力学稳定性 黄铁矾的分子式通常可以写成A 20·3Fe 203·4S03·6H 20或AFe 3(S04)2(OH)6, 或A 2[ Fe 6( SO 4)4(OH )12,式中A 代表一价阳离子,即可以是K +、Na +、NH 4+、Rb +、Ag +、—Pb 2+或H 3+ O 等,例如: 黄钾铁矾:KFe 3(S04)2(OH )6,其化学组成:K 20 9.41%,Fe 203 47.83%,S03 31.97%,H 20 10.79%。黄钠铁矾:NaFe 3(S04)2(OH )6,其化学组成:Na 20 6.4%;Fe 203 49.42%;S03 33.04%,H 20 11.14%。黄铵铁矾:NH 4 Fe 3(S04)2(OH )6,其化学组成:(NH 4)2O 5.43%,Fe 203 49.93%,S03 33.37%,H 20 11.27%。 这些化合物通常称黄钾铁矾或黄铁矾。在自然界里,有些矿物具有类似的组成,相同的结构和结晶形态,即所谓类质同晶。所谓矾,是一系列类质同晶矿物的总称,而黄钾铁矾是矾中的一种。 波北兹涅克和麦尔文研究了Fe 203-S03-H 20三元系在某些温度下的平衡情况,如下图所示。所有碱式盐、酸式盐及正盐都位于三元系相图内部,这是由于它们都含有结晶水的缘故。无水硫酸高铁位于Fe 203-S03二元系线上,但它在50℃和75℃的条件下不是平衡相,即不会从溶液中以这种成分析出,因而没有在图上出现。按照平衡固相来分类,图大致可分成以下三类区域:
铜冶炼行业现行政策条件 2020版
铜的冶炼仍以火法冶炼为主,我国铜产量约占世界铜总产量的85%。为进一步加快铜产业转型升级,促进铜冶炼行业技术进步,提升资源综合利用率和节能环保水平,推动铜冶炼行业高质量发展,根据国家有关法律法规和产业政策,经商有关部门,工业和信息化部制定了《铜冶炼行业规范条件》,下面我们一起来看一下2019年铜冶炼行业规范条件主要有哪些内容。 2019年铜冶炼行业规范条件 为推进铜冶炼行业供给侧结构性改革,促进行业技术进步,推动铜冶炼行业高质量发展,制定本规范条件。 本规范条件适用于已建成投产利用铜精矿和含铜二次资源的铜冶炼企业(不包含单独含铜危险废物处置企业),是促进行业技术进步和规范发展的引导性文件,不具有行政审批的前置性和强制性。 一、企业布局 (一)铜冶炼项目须符合国家及地方产业政策、土地利用总体规划、主体功能区规划、环保及节能法律法规和政策、安全生产法律法规和政策、行业发展规划等要求。 二、质量、工艺和装备 (二)铜冶炼企业应建立、实施并保持满足GB/T19001要求的质量管理体系,并鼓励通过质量管理体系第三方认证。阳极铜符合行业标准(YS/T1083),阴极铜符合国家标准(GB/T467),其他产品质量符合国家或行业相应标准。
(三)利用铜精矿的铜冶炼企业,应采用生产效率高、工艺先进、能耗低、环保达标、资源综合利用效果好、安全可靠的闪速熔炼和富氧强化熔池熔炼等先进工艺(如旋浮铜熔炼、合成炉熔炼、富氧底吹、富氧侧吹、富氧顶吹、白银炉熔炼等工艺),不得采用国家明令禁止或淘汰的设备、工艺。鼓励有条件的企业对现有传统转炉吹炼工艺进行升级改造,提升无组织烟气排放管控水平。须配置烟气制酸、资源综合利用、节能等设施。烟气制酸须采用稀酸洗涤净化、双转双吸等先进工艺,烟气净化严禁采用水洗或热浓酸洗涤工艺,硫酸尾气需设治理设施。配备的冶炼尾气余热回收、收尘工艺及设备须满足国家《节约能源法》《清洁生产促进法》《环境保护法》等要求。 (四)利用含铜二次资源的铜冶炼企业,须采用先进的节能环保、清洁生产工艺和设备。企业应强化含铜二次资源的预处理,最大限度进行除杂、分类。禁止采用化学法以及无烟气治理设施的焚烧工艺和装备。冶炼工艺须采用NGL炉、旋转顶吹炉、倾动式精炼炉、富氧顶吹炉、富氧底吹炉、100吨以上改进型阳极炉(反射炉)等生产效率高、能耗低、资源综合利用效果好、环保达标、安全可靠的先进生产工艺及装备。同时,应根据原料状况配套二噁英排放控制设施或净化设施,须使用预热空气和余热锅炉等设备。禁止使用直接燃煤的反射炉熔炼含铜二次资源。禁止使用无烟气治理措施的冶炼工艺及设备。 (五)鼓励有条件的企业开展智能工厂建设。建立铜冶炼大数据平台,广泛应用自动化智能装备,逐步建立企业资源计划系统(ERP)、数据采集与监视控制系统(SCADA)、制造执行系统(MES)、产品数据管理系统
氰化尾渣处理安全操作规程(2021)
The prerequisite for vigorously developing our productivity is that we must be responsible for the safety of our company and our own lives. (安全管理) 单位:___________________ 姓名:___________________ 日期:___________________ 氰化尾渣处理安全操作规程 (2021)
氰化尾渣处理安全操作规程(2021)导语:建立和健全我们的现代企业制度,是指引我们生产劳动的方向。而大力发展我们生产力的前提,是我们必须对我们企业和我们自己的生命安全负责。可用于实体印刷或电子存档(使用前请详细阅读条款)。 1.上班时,必须穿戴好必备的劳动保护用品。 2.正常开车时,要尽量保持连续均匀给矿,减少波动。 3.控制好上矿浓度在要求范围内。 4.检查真空度是否在-0.09~0.098MPa,滤液池液位是否正常。 5.检查刮刀运行情况,松紧度是否合适,有无积矿。 检查主电机、减速机有无异声、震动、发热现象。 水过滤器前后压力差不大于0.1MPa,后压力不小于0.15MPa,若发现问题,应及时更换或冲洗滤芯. 反冲洗水压力为0.08~0.12MPa,不得超过0.12MPa. 缓冲器压力与反冲洗压力相同. 10.气压在0.4~0.7MPa. 11.清洗前必须穿戴好劳保用品防护服装和面具,酸泵必须用50%至68%浓硝酸供液,温度应保持常温,槽体必须干净、清洗并放水至超声装置之上(超声装置浸入水面).
《铜冶炼炉渣回收铜》国家标准
《铜冶炼炉渣回收铜》国家标准 编制说明 铜陵有色金属集团控股有限公司 2010年8月
《铜冶炼炉渣回收铜》国家标准编制说明 1、任务来源 根据中色协综字[2010]015号文件,关于下达2009年第二批有色金属国家、行业标准制(修)订项目计划通知,《铜冶炼炉渣回收铜》由铜陵有色金属集团控股有限公司负责起草,参加起草单位大冶有色金属集团控股有限公司。负责起草单位接到通知后立即成立标准编制小组。经过半年的相关准备,制定出本讨论稿。 2、铜冶炼炉渣回收铜产品简介 目前国内铜冶炼所采用的主要是熔炼和吹炼二道炼铜工艺,以往第一道工艺所产生的熔炼渣由于含铜量较低基本上作为废料丢弃,也有部分作为建筑行业添加剂销售。第二道工艺所产生的吹炼渣由于含铜量相对较高,有的厂家返回上道工序使用,有的采用选矿富集再利用。 由于近年来铜价较高,不少厂家对含铜量较低熔炼渣在投入和产出比进行了测算;同时,随着选矿回收技术的提高,各冶炼厂纷纷上马选矿厂回收熔炼渣中铜金属。 无论是熔炼渣还是吹炼渣所回收的铜,与井下和地表开采的铜矿物所选的铜精矿相比除含硫品位较低和粒度较细外,其性质基本相同,各冶炼厂都是把该产品与铜精矿配料使用。 3、标准编制前期工作 在编制标准期间,首先,进行了相关信息和资料的搜集。标准编制小组于今年6月至7月,先后前往云南铜业公司、大冶有色金属控
股公司、江西铜业公司、金川有色金属公司、中条山有色金属集团公司、祥光铜业公司、铜陵有色稀贵金属公司、铜陵有色金口岭矿业公司、铜陵有色天马山矿业公司进行实地考察调研,收集了大量的相关数据和资料,并取样进行了分析。 通过调研,基本掌握国内铜冶炼炉渣回收铜的生产和需求厂家的情况,覆盖面达到90%以上,应当说具有广泛的代表性。具体收集和分析的相关数据见附表。 4、标准编制原则 4.1本标准格式按照GB/T1.1-2009最新版本要求编写。 4.2本标准参考YS/T 318-2007《铜精矿》标准进行编写。 4.3本标准编制遵循“先进性、实用性、统一性、规范性”的原则,使标准制定具有可操作性。 4.4本标准充分考虑了使用单位的意见和建议。 5、标准中主要内容确定 5.1关于标准名称 标准的名称有三个可采用:“铜冶炼炉渣回收铜”、“铜冶炼炉渣回收铜精矿”、“铜冶炼炉渣渣精矿”,我们建议采用“铜冶炼炉渣回收铜”作为该产品的标准名称。该产品名称确定是为了区别于井下或地表开采铜矿物所选的铜精矿,来源于铜冶炼中。 5.2关于产品分类 根据调研所收集和取样分析的资料,按照精矿含铜品位高低不同确定为三个品级,三级品含铜品位不小于15%,一级品含铜品位不小
黄金冶炼氰化尾渣提金及综合利用
书山有路勤为径,学海无涯苦作舟 黄金冶炼氰化尾渣提金及综合利用 成果名称:黄金冶炼氰化尾渣提金及综合利用申请单位:清华大学鉴定编号:鉴字[教SW2003]第008号鉴定日期:2003年09月07日学科:土建水成果简介:该技术在国内外未见报道,由金涌院士主持的项目评估认为,该技术达到国际先进水平。由教育部主持的项目鉴定认为,该项目工艺先进可行,创新明显,规模经济效益高。随着金矿开采程度的加深,难选金矿的产量越来越大,利用传统的氰化法提金,会产生大量金含量高的黄金冶炼尾渣。在现有的已经公开的技术或发表的专利文献中,对难选金精矿或黄金冶炼尾渣,特别是含硫化物或砷化物较多的难选金精矿,能够工业化的技术一般采用焙烧法,此法能使金的回收率有所提高,也能够回收其中硫,但金的回收率提高的幅度有限,而且产生大量的污染废渣,砷也难处理。含硫铁矿较高的尾渣大多外卖到水泥厂,作水泥辅料,产生硫、砷和铅的污染。如果堆放在冶炼厂附近,会产生自燃,也会产生煤烟污染,氰化物随着天然雨水等进入地下水,引起环境恶化。为此研究催化氧化法处理难选金精矿和尾渣:该方法选用催化剂,在常压下利用空气中的氧气氧化黄金冶炼氰化尾渣,以提取金属银、金属铜、铅的化合物、锌的化合物,制备铁系颜料等,同时提取黄金。处理后尾渣中包裹金的硫化物、砷化物被催化氧化,增加金与催化剂接触的几率,提高金的回收率。同时,还可综合回收银、铜、铅、砷等,利用其中的铁生产透明超细铁红,各种污染物质也同时变为无污染物质。催化氧化后的尾渣残有量20%左右,有的低于5%,并可以综合利用,金、银、同铁盒铁的回收率达到99%。因此,该方法不但解决了含硫化物或砷化物较高的金精矿金回收率低的难题,还最大限度提高有价金属的回收率,解决了黄金冶炼尾渣堆放活处理难的问题。另外该技术的成功开发,有利于改进企业落后的氰化提金工
氰化尾渣处理安全操作规程(新编版)
氰化尾渣处理安全操作规程 (新编版) The safety operation procedure is a very detailed operation description of the work content in the form of work flow, and each action is described in words. ( 安全管理 ) 单位:______________________ 姓名:______________________ 日期:______________________ 编号:AQ-SN-0391
氰化尾渣处理安全操作规程(新编版) 1.上班时,必须穿戴好必备的劳动保护用品。 2.正常开车时,要尽量保持连续均匀给矿,减少波动。 3.控制好上矿浓度在要求范围内。 4.检查真空度是否在-0.09~0.098MPa,滤液池液位是否正常。 5.检查刮刀运行情况,松紧度是否合适,有无积矿。 检查主电机、减速机有无异声、震动、发热现象。 水过滤器前后压力差不大于0.1MPa,后压力不小于0.15MPa,若发现问题,应及时更换或冲洗滤芯. 反冲洗水压力为0.08~0.12MPa,不得超过0.12MPa. 缓冲器压力与反冲洗压力相同. 10.气压在0.4~0.7MPa. 11.清洗前必须穿戴好劳保用品防护服装和面具,酸泵必须用
50%至68%浓硝酸供液,温度应保持常温,槽体必须干净、清洗并放水至超声装置之上(超声装置浸入水面). 12.维修时轻拿轻放,不得敲打过滤板刮刀及仪表等设备. 13.硝酸罐内有无配好的硝酸,以备下班清洗用。 14.出现过滤板损坏或其它紧急情况时,应将“手操排水阀、急停旋”钮摆放在急停位置,当故障处理完毕后,应将“手操排水阀、急停”摆放在垂直位置. 15.掌握入料时间及压力,控制滤饼水份,精矿水份≤25%。 XXX图文设计 本文档文字均可以自由修改
铜冶炼渣中单质铜对浮选指标的影响及控制方案研究
铜冶炼渣中单质铜对浮选指标的影响及控制方案研究 我国铜冶炼企业在每年都会产生大量的铜冶炼渣,其中单质铜对于浮选指标是有一定程度影响的。本文主要分析了铜冶炼渣当中的单质铜对于浮选指标的影响以及提出了相应的控制方法,对铜渣的浮选提出工艺上的意见,予以相关企业参考与借鉴。 标签:铜冶炼;单质铜;浮选指标;影响;控制方案 1 铜渣的性质 铜冶炼渣是一种人工矿石,其理化性质,物理组成,矿物之间的共生关系与矿物之间的嵌布粒度粗细与冶炼的技术,设备以及冷却方式等因素相关,所以炉渣性质一般都是不太稳定的。铜渣一般呈现黑色,块状,易碎难磨,性脆是铜渣的主要性质。其矿物组成成分中绝大多数是铁橄榄石,其次是磁铁矿,还有少量脉石组成的玻璃体。其中的铜矿物多呈硫化物形态存在。由于冶炼技术的不同,硫化铜矿、氧化铜矿、金属铜及化合铜矿等以不同含量分布于炉渣之中,部分渣料因处理的铜矿石原料特殊,產生的炉渣中含有金、银等贵重金属以及铅、锌、钴、镍等有价成分。铜渣当中还含有铝,钙,镁等重要元素,其主要是以氧化镁,氧化钙,三氧化二铝的形式所存在。铜矿物或被硅铁氧化物所包裹,或与铜铁矿物共同形成斑状结构及多矿物共生嵌于铁橄榄石基体中。炉渣的冷却方式有三种:自然冷却、水淬、保温冷却+水淬,其中保温冷却+水淬有利于铜的浮选回收,根据其不同的冷却方式,铜渣可以分为自然冷却渣、水淬渣与缓冷渣。铜渣中铜矿物的结晶粒度大小和炉渣的冷却速度密切相关,炉渣缓冷有利于铜相粒子迁移聚集长大,即在炉渣的缓冷过程中,炉渣溶体的初析微晶可通过溶解-沉淀形成成长,形成结晶良好的自形晶或半自形晶,同时有用矿物因此扩散迁移、聚集并长大成相对集中的独立相,使其易于单体解离和选别回收。铜渣的冷却方式对于炉渣的结晶过程与铜渣组分颗粒的凝聚长大都有着一定程度的影响,而且还会影响铜渣的结晶颗粒大小与每种矿物之间的共生关系。渣中铜如果在自然缓慢的冷却那么其结晶的速度是很快的,若采用水淬冷却的方式,在高温的铜渣冷却速度则会更快,有可能会出现非结晶质的结构,与此同时还会阻碍铜矿物质的颗粒聚集长大,铜颗粒分布呈现树状又或者是针状的其他矿物当中。目前自然冷却铜渣与缓冷渣铜渣浮选回收铜成功的案例较多,但水淬铜渣由于其矿物成分多,物相复杂,且相互连生包裹,使得铜矿物与脉石难以分离,从而加大了回收难度。因此,我们要采用水淬冷却的铜渣让其细磨将大部分的铜颗粒与同脉石进行解离,这样就会使得铜渣很难磨矿之后使用浮选的方式进行回收。这样也有利于析出铜细颗粒在缓慢的冷却过程中借助扩散与凝结的作用慢慢的聚集在一起。若冷却速度足够缓慢,那么缓慢成长的结果是形成结晶良好的自形晶和半自形晶,借扩散和迁移作用,铜渣熔体的初析微晶就能通过溶解一沉淀形式缓慢成长;此两类铜晶体微粒将成长为独立的晶像,易于磨矿工序的单体解离和浮选过程的药剂作用。 2 水淬浮选工艺
高炉熔渣处理及资源化利用技术概述
第11卷 第5期 中 国 水 运 Vol.11 No.5 2011年 5月 China Water Transport May 2011 收稿日期:2011-03-11 作者简介:朱文渊(1981-),男,武汉都市环保工程技术股份有限公司工程师。 高炉熔渣处理及资源化利用技术概述 朱文渊 (武汉都市环保工程技术股份有限公司,湖北 武汉 430071) 摘 要:文中针对钢铁企业高炉渣的处理及资源化利用技术进行了概述。首先介绍了高炉熔渣的物性,然后概述了目前高炉渣处理及资源化利用的现状,并分析了其存在的问题,接着介绍了目前国外高炉渣处理及资源化利用的新技术,最后提出了高炉渣处理及资源化利用的工艺技术路线及发展趋势。 关键词:高炉渣;粒化;热能回收 中图分类号:X705 文献标识码:A 文章编号:1006-7973(2011)05-0107-03 一、引言 高炉渣是冶炼生铁时从高炉中排出的一种熔融状态的废渣,其从高炉中排出的温度在1450~1650℃。2010年我国生铁产量5.9亿吨,按平均每吨生铁产生0.35t 渣来计算[1],高炉渣产量为2.065亿吨。由于高炉熔渣温度高,产量很大,如果得不到合理的处理和利用,不但是对二次能源及资源的极大浪费,而且还会对环境造成很大的污染,国内外都在对高炉渣的处理及资源化利用进行研究。 二、高炉熔渣的物性 1.成分 高炉渣主要成分为CaO、SiO 2和Al 2O 3,另外含有少量的MgO、FeO 和一些硫化物如CaS、MnS 和FeS [2]。碱度(CaO/SiO 2)大于1的高炉渣具有基本的水泥质特性(潜在的水硬活性),同时也可能具有一些火山灰质特性(与生石灰反应)。 2.温度及热焓 高炉出口熔渣温度约为1450~1650℃。1500℃时,高炉渣理论焓为1606.21kJ/kg,约合54.8kg 的标准煤。 3.粘度 普通高温熔渣粘度为0.2~0.6Pa·S,熔化性温度为1250~1400℃[3]。熔渣粘度随温度的降低缓慢增加,大约1320℃时开始出现凝固相后,熔渣粘度急剧增加。成分对熔渣粘度的影响较大。实验研究表明,刚粒化的热渣粒具有依赖于温度的粘附力,非晶质渣粒间的不粘附温度小于950℃,高温渣粒对被撞击表面的不粘附温度为1050~1070℃。 4.表面张力 高炉熔渣的表面张力随温度的变化显示出明显的阶段性,不论成分怎样,T>1390-1400℃表面张力处于一稳定的较低水平(0.54-0.59N/m);T<1390℃,表面张力随温度下降急剧升高。 5.比热 高炉渣的比热与温度有关,实验研究表明,温度在900K 以上时,比热与温度近似呈线性关系。 6.导热特性 高炉渣的导热特性与其状态(温度)紧密相关,在液渣状态(T>1400℃),导热系数很小,仅0.1~0.3W/(m.K),在凝固过程中,导热系数迅速增大到2~3W/(m.K),在固化过 程中,导热系数随着温度的降低而增加,约为1~2W/m.K) [4] 。 三、国内高炉渣处理及资源化利用现状及存在的问题 1.现状 目前,高炉渣主要通过水淬处理,产品作为水泥生产原料。而对于高炉渣的显热回收,国内对此仍然处在工业试验性阶段,还没有完整的设备。 水淬处理工艺主要有INBA 法、图拉法、沉渣池法和底滤法、RASA 法、螺旋法等,这些水淬工艺按其形式可以分为两大类: 1)高炉熔渣直接水淬工艺,其处理过程是首先将高炉熔渣渣流用高压水进行水淬,然后进行渣水输送和渣水分离; 2)高炉熔渣先机械破碎,后水淬工艺,其处理过程是将高炉熔渣渣流首先采用机械破碎,形成运动的液滴后进行水淬粒化,然后进行渣水分离和输送。 在实际应用中,INBA 法、图拉法、沉渣池法和底滤法,RASA 法、螺旋法等水淬工艺方法采用较多。 2.存在的问题 高炉渣水淬处理过程中存在的主要问题是: (1)水耗高。水淬渣过程中水压大于0.2MPa,水渣之比为(8~15):1,吨渣新水消耗约0.8t~1.2t。 (2)在水淬渣的过程中产生的硫化物会随蒸汽排入大气造成大气污染,渣中的碱性元素会进入冲渣水中造成水污染。 (3)未回收显热。1t 液态渣水淬时散失的热量约为1600~1800MJ,相当于标准煤55~61kg 完全燃烧后所产生的热量。液态高炉渣的温度为1450~1500℃,从火用分析的角度看,其余热品质非常高,极具利用价值。 (4)需干燥处理。高炉水渣含水率高达10%以上,作为水泥原料生产时须干燥处理,仍要消耗一定的能源。 (5)对于水渣系统而言,电耗和系统维护的工作量非常大。水冲渣系统循环水中所含大量为细颗粒对水泵和阀门等部件的磨损和堵塞非常严重,故使用一段时间后会导致水压下降、电耗增加、冲渣效果变差,清除水中的微粒还需大量资金。
氰化尾渣处理安全操作规程通用版
操作规程编号:YTO-FS-PD322 氰化尾渣处理安全操作规程通用版 In Order T o Standardize The Management Of Daily Behavior, The Activities And T asks Are Controlled By The Determined Terms, So As T o Achieve The Effect Of Safe Production And Reduce Hidden Dangers. 标准/ 权威/ 规范/ 实用 Authoritative And Practical Standards
氰化尾渣处理安全操作规程通用版 使用提示:本操作规程文件可用于工作中为规范日常行为与作业运行过程的管理,通过对确定的条款对活动和任务实施控制,使活动和任务在受控状态,从而达到安全生产和减少隐患的效果。文件下载后可定制修改,请根据实际需要进行调整和使用。 1.上班时,必须穿戴好必备的劳动保护用品。 2. 正常开车时,要尽量保持连续均匀给矿,减少波动。 3. 控制好上矿浓度在要求范围内。 4. 检查真空度是否在-0.09~0.098MPa,滤液池液位是否正常。 5.检查刮刀运行情况,松紧度是否合适,有无积矿。 检查主电机、减速机有无异声、震动、发热现象。 水过滤器前后压力差不大于0.1MPa,后压力不小于0.15MPa,若发现问题,应及时更换或冲洗滤芯. 反冲洗水压力为0.08~0.12MPa,不得超过0.12MPa. 缓冲器压力与反冲洗压力相同. 10.气压在0.4~0.7MPa. 11.清洗前必须穿戴好劳保用品防护服装和面具,酸泵必须用50%至68%浓硝酸供液,温度应保持常温,槽体必须干净、清洗并放水至超声装置之上(超声装置浸入水面). 12.维修时轻拿轻放,不得敲打过滤板刮刀及仪表等设
铜冶炼渣包使用与管理技术标准
铜冶炼渣包使用与管理技术标准 1. 适用范围 本标准规定了渣包的使用、维修与管理技术标准,适用于铜冶炼行业的渣包管理工作。 2. 渣包的使用与维修 2.1 渣包的正确使用 2.1.1新渣包在使用前必须有半年以上的自然失效时间,使用前对渣包进行认真的检查,确认渣包是否符合制作订货技术要求之检验要求。确认旧渣包焊缝是否达到渣包修理的焊接技术要求。 2.1.2 将渣包预热至250至300℃,条件允许应在包底垫0.5——1立方米的铜渣。 2.1.3 渣包在接渣时,要确保渣液的落点在渣包的底部中点,以避免渣液冲刷包壁。 2.1.4 装渣量要适中,在确保渣包车安全运行的前提下,力争多装。渣线应控制在包口下250——300mm处。 2.1.5 渣包满载状态下,不容许长时间让耳轴受力。如包体外表面温度达到300℃没能及时运往渣场,则只能让渣包就近缓冷至倾渣温度后再运往渣场,否则将会引起渣包变形。 2.1.6 满载后的渣包要及时运往渣场,坐包时,渣包底部应悬空,更不得将包底浸泡在积水中。 2.1.7 在满足渣选工艺的前提下,满载的渣包应自然缓冷四小时后再进行水淬处理。倾渣时,铜渣的温度应在200℃以上,即倾渣后渣包的余温应在150℃以上(至少应高于气温50℃以上并及时运往下渣口接渣)。 2.1.8 除在线所需的渣包数量外,至少还需要30%以上的备用包,用于在线轮换修整,即定期将一定数量的渣包退出生产线进行长达2——3个月的自然失效以
消除应力。 2.1.9 应有专职人员在每次使用前(即倾渣后)检查渣包是否有裂纹、变形、耳轴磨损、局部超温等现象存在。在点检中一旦发现微裂纹,及时退出生产线,进行修理。不得强行带伤使用。否则随着使用次数的增加,裂纹会不断扩展,最终导致修复困难,以致报废。 2.2 渣包的维修 2.2.1 渣包维修资质要求 2.2.1.1从事渣包修理的单位不仅要取得相应的焊接资质、具有一定的焊接技术、施工和管理实力,由于渣包的材料是通过特殊处理,不同于一般的铸钢件,所以应以对此材料有一定的了解、有过此类渣包修理经验的单位为优先单位。 2.2.1.2参与修理渣包的技术人员要求:技术人员需具备专业知识,焊工需具备焊接高级工以上资质。 2.2.2清除缺陷处理 2.2.2.1 清除缺陷前的加热处理:如果是开放性裂纹,最好是在倾渣后,渣包有一定的余温(温度150℃以上)及时对缺陷进行处理,否则需采用陶瓷电加热的方法将缺陷部位加热到150——200℃,然后对缺陷进行处理。 2.2.2.2 缺陷的清除:除较大的开放性裂纹采取碳弧气刨清除缺陷外,一般采用电动铣刀进行清除(清除时可以在常温状态下进行),以避免裂纹扩展。清除完成后采用着色探伤的方式确认缺陷是否彻底清除。 2.2.3 焊接 2.2. 3.1 焊前准备 (1)焊条(焊材)准备:根据缺陷所在位置的母材材质选用与之相匹配的焊条(焊材),按焊条的使用要求进行烘烤后转入焊条保温箱,随用随取。 (2)破口准备:对用电弧气刨处理的缺陷部位,打磨至金属光泽并修磨成“U”或破口角度大于45°小于60°以利于焊接。