复合电镀镍-金刚石工艺及其故障处理
PCB电镀镍工艺及故障原因与排除
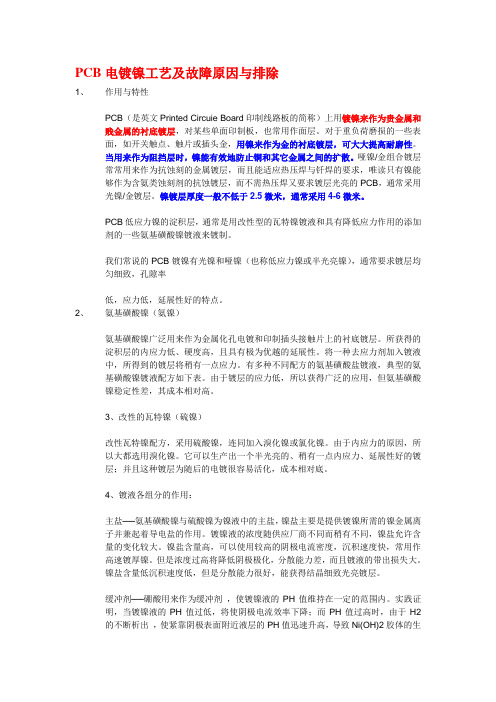
PCB电镀镍工艺及故障原因与排除1、作用与特性PCB(是英文Printed Circuie Board印制线路板的简称)上用镀镍来作为贵金属和贱金属的衬底镀层,对某些单面印制板,也常用作面层。
对于重负荷磨损的一些表面,如开关触点、触片或插头金,用镍来作为金的衬底镀层,可大大提高耐磨性。
当用来作为阻挡层时,镍能有效地防止铜和其它金属之间的扩散。
哑镍/金组合镀层常常用来作为抗蚀刻的金属镀层,而且能适应热压焊与钎焊的要求,唯读只有镍能够作为含氨类蚀刻剂的抗蚀镀层,而不需热压焊又要求镀层光亮的PCB,通常采用光镍/金镀层。
镍镀层厚度一般不低于2.5微米,通常采用4-6微米。
PCB低应力镍的淀积层,通常是用改性型的瓦特镍镀液和具有降低应力作用的添加剂的一些氨基磺酸镍镀液来镀制。
我们常说的PCB镀镍有光镍和哑镍(也称低应力镍或半光亮镍),通常要求镀层均匀细致,孔隙率低,应力低,延展性好的特点。
2、氨基磺酸镍(氨镍)氨基磺酸镍广泛用来作为金属化孔电镀和印制插头接触片上的衬底镀层。
所获得的淀积层的内应力低、硬度高,且具有极为优越的延展性。
将一种去应力剂加入镀液中,所得到的镀层将稍有一点应力。
有多种不同配方的氨基磺酸盐镀液,典型的氨基磺酸镍镀液配方如下表。
由于镀层的应力低,所以获得广泛的应用,但氨基磺酸镍稳定性差,其成本相对高。
3、改性的瓦特镍(硫镍)改性瓦特镍配方,采用硫酸镍,连同加入溴化镍或氯化镍。
由于内应力的原因,所以大都选用溴化镍。
它可以生产出一个半光亮的、稍有一点内应力、延展性好的镀层;并且这种镀层为随后的电镀很容易活化,成本相对底。
4、镀液各组分的作用:主盐──氨基磺酸镍与硫酸镍为镍液中的主盐,镍盐主要是提供镀镍所需的镍金属离子并兼起着导电盐的作用。
镀镍液的浓度随供应厂商不同而稍有不同,镍盐允许含量的变化较大。
镍盐含量高,可以使用较高的阴极电流密度,沉积速度快,常用作高速镀厚镍。
但是浓度过高将降低阴极极化,分散能力差,而且镀液的带出损失大。
金刚石线锯的复合电镀法制备及其性能研究

金刚石线锯的复合电镀法制备及其性能研究在大尺寸半导体基片和功能晶体的切割中。
固结磨料线锯以无可比拟的优点被认为是最好的切割方法之一。
与现有的几种固结超硬磨粒的方法相比,电镀方式具有制造周期短和生产成本低等优势,且电镀线锯具有耐热性和耐磨性良好等特点.固结金刚石线锯的电镀工艺是金刚石线锯生产和应用的关键技术。
本文根据硬脆晶体材料切片加工的要求和电化学共沉积工艺的特点,对固结金刚石线锯的复合电镀工艺进行了试验研究。
根据线锯性能要求,选用316L不锈钢丝作为电镀线锯芯线,金刚石作为第二相颗粒,并设计了相关的前处理工艺。
选择以氨磺酸型高速镀镍液作为基础镀液,通过正交试验研究了双脉冲电镀参数对镀层显微硬度的影响关系,试验结果表明:双脉冲供电模式下的镀层质量优于直流和单脉冲模式;双脉冲的频率和反向脉冲占空比是影响镀层显微硬度的显著因素。
在试验基础上,确定了获得高显微硬度镍镀层的双脉冲电镀参数。
设计并制造了一种连续电镀长线锯的试验设备,并且设计了连续制备长线锯的试验方案,实现了连续电镀。
通过试验研究了不同的上砂工艺,以及实现连续电镀过程中阳极排布方式对复合镀层质量的影响。
试验结果表明:与间歇搅拌的悬浮法相比,埋砂法能在锯丝基体表面上获得分布均匀一致、磨料密度较高的复合镀层;采用双阳极对称分布的方式能够改善锯丝表面电流分布,获得的复合镀层质量较好。
对电镀线锯表面镍—金刚石复合镀层的质量进行了检测,评价了固结金刚石线锯复合镀层质量,进行了切割试验,研究了制备的金刚石线锯的切割性能。
结果表明:固结金刚石线锯线径一致性好,镀层中金刚石颗粒分布均匀,表面积百分数50%以上,镀层对金刚石磨粒的把持力较高;切割加工试验表明,自制的电镀固结金刚石线锯在切割效率和加工精度方面均满足使用要求,并且切缝较窄,明显优于商品线锯。
镀镍问题与解决方案

镀镍问题与解决方案引言概述:镀镍是一种常见的金属表面处理方法,它可以提高金属的耐腐蚀性、硬度和外观。
然而,在镀镍过程中,我们常常会遇到一些问题,如镀层不均匀、气泡、缺陷等。
为了解决这些问题,我们需要采取一些有效的解决方案。
正文内容:1. 镀层不均匀问题:1.1 控制电流密度:调整电流密度可以使镀层均匀。
在镀层不均匀的区域增加电流密度,而在均匀的区域减少电流密度。
1.2 改善搅拌条件:通过改善搅拌条件,如增加搅拌桨的数量或改变搅拌桨的位置,可以使电解液均匀分布,从而获得均匀的镀层。
2. 气泡问题:2.1 降低电流密度:气泡往往是由于过高的电流密度造成的。
降低电流密度可以减少气泡的产生。
2.2 提高搅拌效果:通过增加搅拌桨的转速或改变搅拌桨的形状,可以提高搅拌效果,将气泡从电解液中排出。
3. 缺陷问题:3.1 清洗金属表面:在镀镍之前,彻底清洗金属表面是非常重要的。
通过去除污垢、油脂和氧化物,可以减少缺陷的产生。
3.2 控制镀液温度:镀液温度对镀层质量有很大影响。
在适宜的温度范围内进行镀镍,可以减少缺陷的发生。
3.3 选择合适的镀液配方:不同的金属需要不同的镀液配方。
选择合适的镀液配方可以提高镀层的质量,减少缺陷的产生。
4. 防止镀层剥落问题:4.1 提高镀层附着力:通过在金属表面进行预处理,如机械打磨、化学处理等,可以增加镀层的附着力,防止镀层剥落。
4.2 控制镀液pH值:镀液的pH值对镀层的附着力有重要影响。
在适宜的pH 范围内进行镀镍,可以提高镀层的附着力。
5. 提高镀层质量问题:5.1 优化镀液配方:通过调整镀液配方中的各种成分的比例,可以提高镀层的质量。
5.2 控制镀液温度和时间:镀液的温度和镀液时间对镀层质量有很大影响。
在适宜的温度和时间范围内进行镀镍,可以获得高质量的镀层。
总结:通过控制电流密度、改善搅拌条件、降低电流密度、提高搅拌效果、清洗金属表面、控制镀液温度、选择合适的镀液配方、提高镀层附着力、控制镀液pH值、优化镀液配方、控制镀液温度和时间等方法,可以解决镀镍过程中的一些常见问题,提高镀层的质量和均匀性,从而满足不同应用领域的需求。
电镀镍故障处理

电镀镍故障处理1,镀镍层发暗镀镍层表面发暗也是常见的电镀故障之一,这种故障多数出现在低电流密度区电镀获得的镀镍层,偶尔也出现在中电流密度区或高电流密度区,低电流密度区镀镍层发暗可能是镀镍液的温度太高,阴极电流密度太小,硫酸镍浓度太低;I,4一丁炔二醇或其他次级光亮剂过多或镀液中有铜、锌杂质污染引起;中电流密度区镀镍层发暗可能是由于镀液中次级光亮剂太少,有机杂质过多或有一定量的铁杂质污染造成的;高电流密度区镀层发暗可能是镀液pH值太高,初级光亮剂太少或镀液中有少量的铬酸盐、磷酸盐及铅杂质污染引起。
此外,镀前处理不良,镀件表面有碱膜或有机物吸附膜,或底镀层(氰化镀铜等)不好也会导致光亮镍镀层出现发暗现象。
可以取镀镍液做霍耳槽试验来分析这类电镀故障,对于低电流密度区出现的发暗现象,目前有的镀镍出现了比较好的走位剂,专门使得在低电流密度范围内获得光亮镀镍层。
另外还可以观察霍耳槽试片的外观进行逐步分析,如果镀液成分所做的霍耳槽样板上镀镍层状况良好,没有出现发暗的现象,那么电镀时出现的故障,就有可能是镀前处理不良或底镀层不好造成的,应该认真检查电镀镍前的情况。
若霍耳槽试验所得的阴极样板上出现低电流密度区镀层发暗,则可以根据前面提到的可能原因进行试验确定,或者加入合适的走位剂成分最后排除这种电镀故障。
中、高电流密度区的镀镍层发暗,也可用类似的方法进行试验分析。
2,镀镍层脆性镀层发脆,往往影响镀层的加工和质量,而且镀层的脆性与镀层应力有关。
镀镍液中次级光亮剂过多或初级光亮剂太少,铜、锌、铁或有机杂质过多,pH值过高或温度过低等都会使镀镍层发脆。
检查镀镍层脆性的方法,一是将镀好镍的小零件放在手中搓摩,或将镀镍薄片零件弯曲至18009若有碎镍层脱落,说明该镍层脆性大;另外就是将镍层镀在不锈钢试片上,控制镀层厚度在10ym左右,然后把镍层剥离下来,弯曲1800,用力挤压弯曲处,若不断裂,表示镀镍层不脆,弯曲折断,该镀镍层脆性就大。
金刚石表面真空镀镍的工艺分析
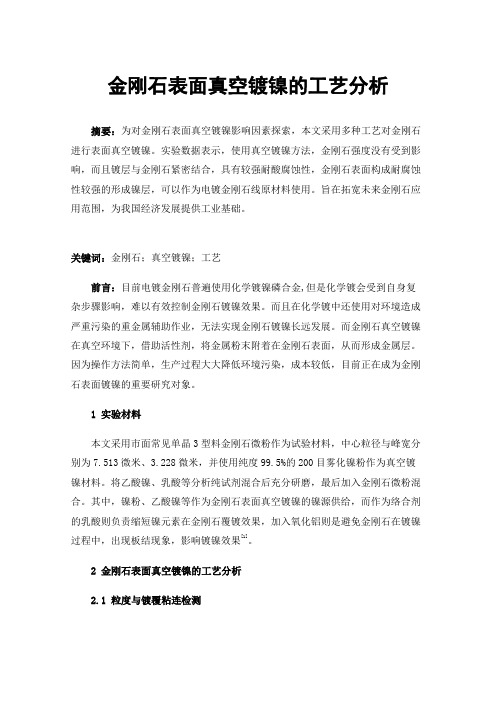
金刚石表面真空镀镍的工艺分析摘要:为对金刚石表面真空镀镍影响因素探索,本文采用多种工艺对金刚石进行表面真空镀镍。
实验数据表示,使用真空镀镍方法,金刚石强度没有受到影响,而且镀层与金刚石紧密结合,具有较强耐酸腐蚀性,金刚石表面构成耐腐蚀性较强的形成镍层,可以作为电镀金刚石线原材料使用。
旨在拓宽未来金刚石应用范围,为我国经济发展提供工业基础。
关键词:金刚石;真空镀镍;工艺前言:目前电镀金刚石普遍使用化学镀镍磷合金,但是化学镀会受到自身复杂步骤影响,难以有效控制金刚石镀镍效果。
而且在化学镀中还使用对环境造成严重污染的重金属辅助作业,无法实现金刚石镀镍长远发展。
而金刚石真空镀镍在真空环境下,借助活性剂,将金属粉末附着在金刚石表面,从而形成金属层。
因为操作方法简单,生产过程大大降低环境污染,成本较低,目前正在成为金刚石表面镀镍的重要研究对象。
1实验材料本文采用市面常见单晶3型料金刚石微粉作为试验材料,中心粒径与峰宽分别为7.513微米、3.228微米,并使用纯度99.5%的200目雾化镍粉作为真空镀镍材料。
将乙酸镍、乳酸等分析纯试剂混合后充分研磨,最后加入金刚石微粉混合。
其中,镍粉、乙酸镍等作为金刚石表面真空镀镍的镍源供给,而作为络合剂的乳酸则负责缩短镍元素在金刚石覆镀效果,加入氧化铝则是避免金刚石在镀镍过程中,出现板结现象,影响镀镍效果[1]。
2金刚石表面真空镀镍的工艺分析2.1粒度与镀覆粘连检测化学与真空镀覆都会出现连晶现象,但是连晶会影响电镀金刚石线使用质量,所以要对金刚石表面镀覆厚度进行检验,确保薄厚均匀,连晶情况少。
本文使用电阻测试法,借助位度分析仪完成粒度分析,对比金刚石镀覆前后峰型、峰宽,判断在镀覆作业后存在多少连晶金刚石[2]。
经过实验后,可以发现在镍源含量增加,在进行镍元素镀覆后,金刚石粒度明显增加,出现明显粘连情况。
而在镍源含量固定的情况下,络合剂含量增加,镀覆后的金刚石粒度有效降低。
电镀镍故障处理
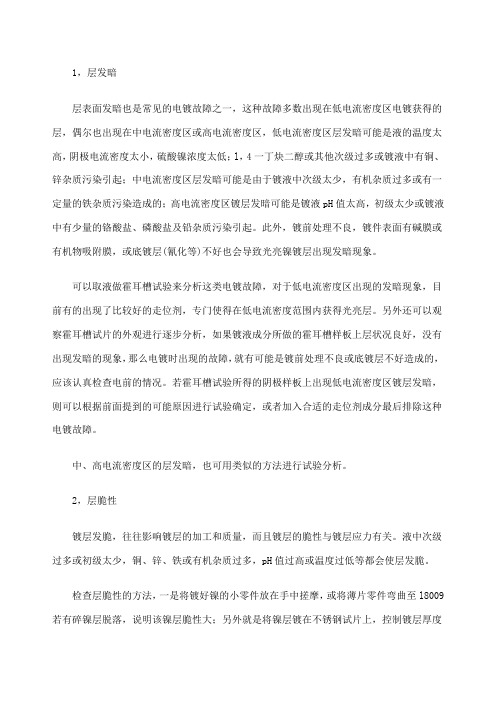
1,层发暗层表面发暗也是常见的电镀故障之一,这种故障多数出现在低电流密度区电镀获得的层,偶尔也出现在中电流密度区或高电流密度区,低电流密度区层发暗可能是液的温度太高,阴极电流密度太小,硫酸镍浓度太低;l,4一丁炔二醇或其他次级过多或镀液中有铜、锌杂质污染引起;中电流密度区层发暗可能是由于镀液中次级太少,有机杂质过多或有一定量的铁杂质污染造成的;高电流密度区镀层发暗可能是镀液pH值太高,初级太少或镀液中有少量的铬酸盐、磷酸盐及铅杂质污染引起。
此外,镀前处理不良,镀件表面有碱膜或有机物吸附膜,或底镀层(氰化等)不好也会导致光亮镍镀层出现发暗现象。
可以取液做霍耳槽试验来分析这类电镀故障,对于低电流密度区出现的发暗现象,目前有的出现了比较好的走位剂,专门使得在低电流密度范围内获得光亮层。
另外还可以观察霍耳槽试片的外观进行逐步分析,如果镀液成分所做的霍耳槽样板上层状况良好,没有出现发暗的现象,那么电镀时出现的故障,就有可能是镀前处理不良或底镀层不好造成的,应该认真检查电前的情况。
若霍耳槽试验所得的阴极样板上出现低电流密度区镀层发暗,则可以根据前面提到的可能原因进行试验确定,或者加入合适的走位剂成分最后排除这种电镀故障。
中、高电流密度区的层发暗,也可用类似的方法进行试验分析。
2,层脆性镀层发脆,往往影响镀层的加工和质量,而且镀层的脆性与镀层应力有关。
液中次级过多或初级太少,铜、锌、铁或有机杂质过多,pH值过高或温度过低等都会使层发脆。
检查层脆性的方法,一是将镀好镍的小零件放在手中搓摩,或将薄片零件弯曲至l8009若有碎镍层脱落,说明该镍层脆性大;另外就是将镍层镀在不锈钢试片上,控制镀层厚度在10μm左右,然后把镍层剥离下来,弯曲1800,用力挤压弯曲处,若不断裂,表示层不脆,弯曲折断,该层脆性就大。
产生镍层脆性的原因,若镀液pH值和温度没有问题,那么可能是镀液中光亮添加剂比例失调或镀液中杂质的造成的,由于光亮添加剂比例失调造成的脆性可以通过提高糖精添加剂(或其他应力消除成分)的含量来改善,通过补充糖槔等成分,观察层脆性是否改善来判断。
镀镍问题与解决方案
镀镍问题与解决方案一、问题描述镀镍是一种常见的表面处理工艺,用于提高金属制品的耐腐蚀性和外观质量。
然而,在镀镍过程中,可能会浮现一些问题,如镀层不均匀、气泡、氧化等,影响产品的质量和性能。
本文将针对镀镍过程中的问题进行分析,并提出相应的解决方案。
二、镀镍问题与解决方案1. 镀层不均匀问题描述:镀层在表面浮现不均匀的现象,有的地方厚度过薄,有的地方厚度过厚。
解决方案:首先,检查镀液的温度和浓度是否稳定,调整镀液的参数以确保均匀性。
其次,检查镀液搅拌设备是否正常工作,确保液体循环均匀。
此外,适当调整镀液的流速和镀液与工件的接触面积,以提高镀层的均匀性。
2. 气泡问题问题描述:镀层表面浮现大量气泡,影响了镀层的质量和外观。
解决方案:首先,检查镀液中是否存在杂质,如有必要,进行滤液处理。
其次,调整镀液的温度温和泡排出设备的工作状态,确保气泡能够顺利排出。
此外,适当调整镀液的流速和镀液与工件的接触方式,以减少气泡的产生。
3. 氧化问题问题描述:镀层表面浮现氧化现象,影响了镀层的质量和光泽度。
解决方案:首先,检查镀液中是否存在氧化剂过多的情况,如有必要,调整镀液的配方。
其次,加强镀液的循环和搅拌,以促进氧化物的排除。
此外,适当调整镀液的温度和镀液与工件的接触方式,以减少氧化的发生。
4. 色差问题问题描述:镀层表面浮现颜色不一致的现象,影响了产品的外观质量。
解决方案:首先,检查镀液中是否存在杂质或者其他污染物,如有必要,进行滤液处理。
其次,调整镀液的温度和浓度,以确保镀层颜色的一致性。
此外,加强镀液的循环和搅拌,以促进颜色的均匀分布。
5. 粘附力问题问题描述:镀层与基材之间的粘附力不够强,容易剥离或者脱落。
解决方案:首先,检查基材的表面处理是否充分,如有必要,进行打磨或者清洗。
其次,调整镀液的温度和浓度,以提高镀层与基材的结合力。
此外,加强镀液的循环和搅拌,以确保涂层能够均匀分布并与基材密切结合。
三、总结镀镍过程中可能浮现的问题包括镀层不均匀、气泡、氧化、色差和粘附力不足等。
电镀镍溶液的维护与故障处理措施
2019年7月| 65pH 对镀层、镀液性能影响的控制措施为,将镀镍电镀液pH 值控制在 4.2左右,在析氢现象的不断消耗H +过程中,会使镀镍电镀液pH 值缓慢上升。
需要对电镀液pH 值进行检测并调节。
工件经过稀酸活化后经过清洗步骤直接转入镀槽内进行镀层沉积,并且在保证活化效果的同时,开展酸洗液清洁工作,以免将前处理液中的杂质带入镀液并以此促使电镀镍溶液 pH 值趋于稳定。
2.3 镀镍电镀液处理措施若镀镍电镀液内存在污染物,可借助活性炭进行清洁处理,并将镀镍电镀液内的添加剂去除。
镀镍电镀液处理工艺主要包括:(1)取出镀镍电镀液阳极,接着加入5mL/L 的杂质去除水,加热镀镍电镀液,促使温度保持在60~70℃,连续搅拌2~2.5h 。
(2)若镀镍电镀液内的杂质物较多,需要先加入1g/L 高锰酸钾,连续搅拌2h ,接着加入3~5mL/L 、浓度为30%双氧水进行去杂处理,连续搅拌4h 。
(3)在不断搅拌下,加入3~5g/L 活性炭粉,持续搅拌2h ,静置4h ,在加助滤粉的过滤机进行过滤处理。
(4)清洗阳极并保养,更新阳袋后,将其挂回到镀槽,并将溶液倒回镀槽内,镀液成分检测后调节调节至配方含量。
(5)铜瓦楞板作阴极,连续电解8~12h,试验结束之后补充添加剂即可进行样片试镀。
镀镍电镀液处理措施,需要定期分析镀液成分,借助赫尔槽试验,完善产品质量报表,结合实际参数,科学调节镀镍电镀液,实时记录数据。
2.4 镀层粗糙和毛刺解决措施镀镍镀层表面粗糙,考虑可能是受到空气灰尘、微粒等外部影响,也可能是阳极袋破裂使阳极泥渣进入溶液。
电镀液内氯化物过多,将会加速阳极溶解速度,使得一些小颗粒镍从阳极进入到溶液中,或者镀液中镍含量太高等内部溶液因素导致,也会导致镀镍镀层表面粗糙度增加。
镀层粗糙和毛刺解决措施,若发现镀镍镀层表面粗糙是由固体微粒造成,则需要借助过滤镀液去除杂质,及时消除固体微粒、明确固体微粒来源,制定针对性的预防措施,避免微粒再次进入到镀镍电解液中。
电镀工艺常见故障和处理方法
Trouble Shooting Indexz电金工艺z碳膜工艺z电铜工艺z图像转移工艺z蚀板工艺z喷锡(热风整平)工艺z线路油墨工艺z电镍工艺z有机保焊膜工艺z压板工艺z沉铜(PTH)工艺z银浆贯孔工艺z电锡工艺z湿绿油工艺一、版权说明关於这个【Trouble Shooting】软件 的版权我想一定是属於 中国PCB技术网 所有,其中如果有同行要直接引用本软件则要与我联系,一般情况下我也希望此软件 在我们同行中广泛传播!但如果要用於商业用途则我们就要认真商量一个方案了!当然这其中的文章版权就是文章和作者和来自 的不同网站!如果我转录的这些文章,相关网站或作者不允许录入到这个软件中,请与我们联系,我们会立即删除并表示道歉!二、注册说明这是一个完全免费的软件,当然我们是想知道这个软件到哪里去了!如果你想要告诉我们,请用这三种方法:1、用EMAIL与我联系。
2、在就是技术网站上留言,并留下EMAIL地址。
3、寄一封书信给我们。
无论何种方法都请写明你的姓名、职业、使用此软件的用途等等。
如果你能对此软件进行一些有建设性的 评价,那我们首先感谢!如果你使用了此软件,觉得对你有一定的帮助,想寄一点钱给我们,那我们非常感激!!三、如何联系我们EMAIL:94TECH@OICQ:9371469网址:三、特别感谢本制程TROUBLE SHOOTING的内容基本上来自己《印制电路工艺》教课书。
此教程为国家信息产业部岗位培训的指定教材。
内容丰富,适用於行业培训。
在此特别感谢!◎ Copyright©2001-2002 ◎ 版权所有©2001-2002 中国PCB技术网◎电镀金工艺◎镀金层常见故障和纠正方法故障可能原因纠正方法低电流区发雾①温度太低②补充剂不足①调整温度到正常值②添加补充剂③有机污染④PH太高③活性炭处理④用酸性调整盐调低PH中电流区发雾,高电流区呈暗褐色①温度太高②阴极电流密度太高③PH太高④补充剂不够⑤搅拌不够⑥有机污染①降低操作温度②降低电流密度③用酸性调整盐调低PH④添加补充剂⑤加强搅拌⑥活性炭过滤高电流区烧焦①金含量不足②PH太高③电流密度太高④镀液比重太低⑤搅拌不够①补充金盐②用酸性调整盐调低PH③调低电流密度④用导电盐提高比重⑤加强搅拌镀层颜色不均匀①金含量不足②比重太低③搅拌不够④镀液被Ni,Cu等污染①补充金盐②用导电盐调高比重③加强搅拌④清除金属离子污染,必要时更换溶液板面金变色(特别是在潮热季节)①镀金层清洗不彻底②镀镍层厚度不够③镀金液被金属或有机物污染④镀镍层纯度不够⑤镀金板存放在有腐蚀性的环境中①加强镀后清洗②镍层厚度不小于2.5微米③加强金镀液净化④加强清除镍镀液的杂质⑤镀金层应远离腐蚀气氛环境保存,其变色层可浸5-15%H2SO4除去镀金板可焊性不好①低应力镍镀层太薄②金层纯度不够③表面被污染,如手印④包装不适当①低应力镍层厚度不小于2.5微米②加强镀金液监控,减少杂质污染③加强清洗和板面清洁④需较长时间存放的印制板,应采用真空包装镀层结合力不好①铜镍间结合力不好②镍金层结合力不好①注意镀镍前铜表面清洁和活化②注意镀金前的镍表面活化③ 镀前清洗处理不良④ 镀镍层应力大③ 加强镀前处理④ 净化镀镍液,通小电流或炭处理◎ Copyright ©2001-2002 ◎ 版权所有©2001-2002 中国PCB技术网 ◎碳膜电路制造技术◎碳膜印制板常见故障及纠正方法序号 故障 产生原因排除方法1碳膜方阻偏高1.网版膜厚太薄2.网目数太大3.碳浆粘度太低4.固化时间太短5.固化抽风不完全6.固化温度低7.网印速度太快1.增大网膜厚度2.降低选择的网目数3.调整碳浆粘度4.延长固化时间5.增大抽风量6.提高固化温度7.降低网印速度 2碳膜图形渗展1.网印碳浆粘度低2.网印时网距太低3.刮板压力太大4.刮板硬度不够1.调整碳浆粘度2.提高网印的网距3.降低刮板压力4.调换刮板硬度3碳膜附着力差1.印碳膜之间板面未处理清洁2.固化不完全3.碳浆过期4.电检时受到冲击5.冲切时受到冲击1.加强板面的清洁处理2.调整固化时间和温度3.更换碳浆4.调整电检时压力5.模具是否在上模开槽4碳膜层针孔1.刮板钝2.网印的网距高3.网版膜厚不均匀4.网印速度快5.碳浆粘度高1.磨刮板的刀口2.调整网距3.调整网版厚度4.降低网印速度5.调整碳浆粘度6.刮板硬度不够 6.更换刮板硬度◎ Copyright©2001-2002 ◎ 版权所有©2001-2002 中国PCB技术网◎酸性电镀铜工艺◎酸性镀铜常见故障及处理故障可能原因纠正方法镀层与基体结合力差镀前处理不良加强和改进镀前处理镀层烧焦①铜浓度太低②阳极电流密度过大③液温太低④阳极过长⑤图形局部导致密度过稀⑥添加剂不足①分析并补充硫酸铜②适当降低电流密度③适当提高液温④阳极就砒阴极知5-7CM⑤加辅助假阴极或降低电流⑥赫尔槽试验并调整镀层粗糙有铜粉①镀液过滤不良②硫酸浓度不够③电流过大④添加剂失调①加强过滤②分析并补充硫酸③适当降低④通过赫尔槽试验调整台阶状镀层氯离子严重不足适当补充局部无镀层①前处理未清洗干净②局部有残膜或有机物①加强镀前处理②加强镀前检查镀层表面发雾有机污染活性炭处理低电流区镀层发暗①硫酸含量低②铜浓度高③金属杂质污染④光亮剂浓度不当或选择不当①分析补充硫酸②分析调整铜浓度③小电流处理④调整光亮剂量或另选品种镀层在麻点、针孔①前处理不干净②镀液有油污③搅拌不够④添加剂不足或润湿剂不足⑤加强镀前处理⑥活性炭处理⑦加强搅拌⑧调正或补充镀层脆性大①光亮剂过多①活性炭处理或通电消耗② 液温过低③ 金属杂质或有机杂质污染② 适当提高液温③ 小电流处理和活性炭处理金属化孔内有空白点① 化学沉铜不完整② 镀液内有悬浮物③ 镀前处理时间太长,蚀掉孔内镀层① 检查化学沉铜工艺操作② 加强过滤③ 改善前处理孔周围发暗(所谓鱼眼状镀层)① 光亮剂过量② 杂质污染引起周围镀层厚度不足③ 搅拌不当① 调整光亮剂② 净化镀液③ 调整搅拌阳极表面呈灰白色 氯离子太多 除去多余氯离子阳极钝化① 阳极面积太小② 阳极黑膜太厚① 增大阳极面积至阴极的2倍② 检查阳极含P是否太多◎ Copyright ©2001-2002 ◎ 版权所有©2001-2002 中国PCB技术网 ◎光化学图像转移(D/F)工艺◎D/F常见故障及处理(1)干膜与覆铜箔板粘贴不牢(2)干膜与基体铜表面之间出现气泡原因解决方法1)干膜储存时间过久,抗蚀剂中溶剂挥发。
电镀镍故障处理宝典
镀镍液活性炭处理操作步骤1)将镀液加热至60-65℃。
2)泵至另一贮备缸。
3)加入3-5g/L活性碳粉,如用颗粒活性炭,则需加大用量。
4)搅拌三小时,然后澄清四至八小时(可安置整夜)。
5)过滤回电镀缸(如有需要,可多次在电镀缸及贮备缸间过滤,直至确认活性炭粉过滤干净。
)6)调整pH及温度至所需。
7)依Hull槽试验,补充镍充剂和润湿剂。
注:1、活性炭处理槽液,会使镀液损失5%左右,应在处理前补充相应的硫酸镍、氯化镍、硼酸一起处理,或将硫酸镍、氯化镍、硼酸单独处理,待镀液处理完经分析,补入。
2、据我们过去之经验所知,当做炭化处理时,间中会有未能达到的理想之效果,大部份乃由于镀液未得适当之搅拌所至,故于做炭化处理时,希望阁下用强烈搅拌器,免至浪费金钱与时间,用搅拌器会增加炭粉及镀液接触之机会,从而加强对吸收有机杂质之能力。
经数小时之搅拌后,更要等候沉绩4-8小时,待炭粉沉入缸底方可滤入电镀缸中(切勿将炭粉带入电镀缸中)。
镀镍液双氧水氧化及电解处理法操作步骤8)用硫酸降低pH至3左右。
9)泵溶液到另一贮备缸,其温度应为60-65℃。
10)加入3-5 mL/L H2O2,搅拌30min。
11)用碳酸镍或氢氧化镍调pH到5以上,同时升温到70℃以上。
12)加入3-5 g/L活性碳。
13)搅拌三小时,然后澄清八小时(可安放整夜)。
14)过滤回电镀缸。
15)用硫酸降低pH至3左右。
16)挂一清洁过之瓦楞形电解板,用4.5 A/dm2电镀3-5min。
17)在电解过程中,镀液需激烈机械或空气搅拌,并不停过滤。
18)用阴极电流密度0.2-0.5 A/dm2电解,直至镀层无暗黑色。
19)电解时,每两小时,加高电流至4.5 A/dm2一次,为时三分钟。
20)调整pH及温度至所需。
21)依Hull槽试验,补充镍光剂和润湿剂。
注:1、电解板必须经除油、活化处理,使其表面得到新鲜的金属层,才可放于镀液中。
2、据过去之经验所知,当做炭化处理时,间中会有未能达到的理想之效果,大部份乃由于镀液未得适当之搅拌所至,故于做炭化处理时,希望用强烈搅拌器,免至浪费金钱与时间,用搅拌器会增加炭粉及镀液接触之机会,从而加强对吸收有机杂质之能力。
- 1、下载文档前请自行甄别文档内容的完整性,平台不提供额外的编辑、内容补充、找答案等附加服务。
- 2、"仅部分预览"的文档,不可在线预览部分如存在完整性等问题,可反馈申请退款(可完整预览的文档不适用该条件!)。
- 3、如文档侵犯您的权益,请联系客服反馈,我们会尽快为您处理(人工客服工作时间:9:00-18:30)。
Electroplating&Pollution Control VoI.30 N0.3
复合电镀镍一金刚石工艺及其故障处理
Process and Fault Handling of Nickel—Diamond Composite Coating
霍苗,杨建桥
(陕西科技大学,陕西西安710021)
HUo Miao。 YANG Jian-qiao
(Department of Pulp and Paper Making.Shanxi University of Science&
Technology,Xi’an 710021,China)
摘要: 介绍了复合电镀镍一金刚石的工艺过程,详细分析了影响复合电镀工艺的诸多因素。介绍了电镀过程中经常遇到的一
些故障,并就这些故障提出了处理办法。
关键词: 复合电镀;工艺;常见故障;故障处理
Abstract:The process of composite nickel—diamond electroplating is presented,and the factors affecting the composite plating
are analyzed in detail.Some common faults in the plating process are described and solutions are suggested.
Key words: composite plating;process;common fault;fault handling
中图分类号:TQ 153 文献标识码:A 文章编号:1000—4742(2010)03—0010—02
0前言
复合电镀技术是指在电解质溶液中加入一种或
几种不溶性固体微粒,在金属离子被还原的同时,将
不溶性的固体微粒均匀地夹杂到金属镀层中。复合
镀层是一类以基质金属为均匀连续相和以不溶性微
粒为分散相的金属基复合材料的镀层。其在材料的
表面防护、表面改性以及表面强化等方面越来越显
示出不可替代的重要地位。由于其具有优良的机
械、物理、化学性能,已受到材料界的关注l1 ]。利用
复合镀技术可以制备出一系列性能优异的复合镀
层,目前研究较多的是高硬度、耐磨性镀层。此类复
合镀层是在基质金属中加入硬度较高的微粒,如:
SiC,A1。O。,金刚石等硬质微粒。这些微粒弥散分
布在镀层中能显著提高镀层的耐磨性能 ]。本文制
备了镍一金刚石复合镀层,并分析了复合电镀中常见
的故障,提出了相应的解决办法。
1复合电镀镍一金刚石
1.1 工艺流程
镀液配制一镀前预处理一电镀一镀后处
理——+热处理—一性能测试
1.2工艺规范及镀前预处理
(1)工艺规范
NiSO ・6H2 O
NiCl2・6H2O
200,~300 g/L
0,~50 g/L
金刚石粉(10 ̄20址m) 30 ̄45 g/L
H3BO3 10 ̄40 g/L
NaC1 16 g/L
表面活性剂0.05~O.15 g/L
pH值 3~5
Jk 1.O~2.5 A/dm。
40~55℃
t 1 h
(2)镀前预处理
基体镀前处理:
机械打磨一抛光一化学除油一弱酸活化
电镀
金刚石粉的预处理:
丙酮浸泡一去离子水洗一稀硝酸浸泡一
去离子水洗一稀氢氧化钠浸泡一去离子水冲洗
至pH值约为7一浸泡在镀液中待用
1.3常见故障及处理
1.3.1镀层结合力差
镀层结合力差,通常表现为起泡、开裂、脱皮等。
主要原因:镀前处理不良、零件表面有油及氧化物
等;电镀过程中产生双性电极或断电时间过长;镀液
中硼酸少、杂质多、pH值高、有油及有机杂质或光
亮剂过多等。
(1)前处理不良
镀层结合力差主要是镀前处理不良所造成的。
基体金属表面黏附油污不可避免,这些油污除不
2010年5月 电镀与环保 第30卷第3期(总第173期) ・11・
净,轻则影响镀层结合力,重则影响镀层结构。除油
不净因素:除油液成分、温度、时间不当等。因此,需
加强镀前处理(包括:除油、除锈),以保证零件表面
没有油污、锈斑和氧化皮,同时加强电镀前的活化处 理,保证零件表面在电镀前没有氧化膜产生。 (2)杂质多 铜、铬等杂质过多,除引起镀层毛刺外,还能影 响镀层结合力;有机添加剂分解产物过多也会影响 结合力。只要严格执行操作规程,减少杂质带入量, 就能将杂质的质量浓度降到最低值,不致产生危害。 1.3.2镀层表面出现针孔 针孔大多是气体在镀件表面停留而造成的,可 以使用润湿剂和强搅拌来减小它的影响。除此之 外,造成针孔的原因还有:表面润湿剂少、阴极电流 密度过大等。 (1)表面润湿剂少 电镀过程中阴极有氢气析出,如果镀液pH值 过低、阴极移动过缓、润湿剂的质量浓度不足都会使 氢气吸附在镀件表面,阻碍镀层金属的沉积,而在镀 层表面形成针孔、麻点。由于润湿剂在电镀过程中 被不断消耗,故应经常补充。 (2)阴极电流密度过大 针孔、麻点如出现在镀件的凸出部分(面向阳 极),则表明阴极电流密度过大,调低阴极电流密度 即可避免。 1.3.3镀层表面粗糙 粗糙是由于溶液中的微粒在电镀过程中留置在 镀层中而形成的。镀层粗糙的主要原因:主盐的质 量浓度过高。它也是镀液不稳定因素之一。当阳极 面积过大,阴极面积过小,阳极溶解的金属离子除少 量供阴极沉积外,还有大量剩余,必然导致主盐的质 量浓度上升。大量镍金属微粒从阳极分离,沉积槽 底,有的被带电吸附到阴极上,使高电流密度区产生 堆积镀层或粗糙无光,影响了镀层质量。所以,在配 制电镀液时,切忌主盐取上限值。另外,为了控制主 盐的质量浓度,也可挂人适量的不溶性阳极。 另外,本文采用的磨料微粒是金刚石微粉,当其 质量浓度过大时,表面质量会有所下降。由于金刚 石微粒属非导电性粒子,有空间位阻效应,减少了实 际沉积面积,相当于电流密度增加,引起小尺寸微粒 团聚,导致镀层表面粗糙,降低了表面质量。 1.3.4镀层发花 (1)氯化物和硼酸偏离规范 镍一金刚石镀液的阳极活化剂为NiC1。・6H。0。
其中c1一能促进阳极溶解,保证主盐的正常补充,并
能提高镀液的导电性和改善镀液分散能力。C1一的
质量浓度过低时,阳极局部易钝化,并大量析出氧
气,易生成黑色沉淀附着于阴极,造成镀层花斑。镀
液中硼酸的质量浓度偏低或偏高,都会影响pH值
的稳定。当pH值太低时,不仅降低阴极效率,而且
使工件表面产生大量氢气,部分氢气泡附在工件表
面,影响金属沉积,容易造成镀层花斑。所以,应该
严格控制氯化物和硼酸的质量浓度,将其控制在所
需范围内。
(2)前处理不良
前处理不良会引起花斑,除油不净是主要因素。
另外还有其它的一些因素,如:待镀工件有变色氧化
现象;工件经酸洗、化学除油后放置时间长而氧化变
色;用手接触工件容易有人体的油脂分泌物;经前处
理后的工件在空气中放置一段时间再镀也要发花
等。因此,一定要严格控制前处理的每一个环节,工
件除油后不得接触其它污染源,前处理完毕后应尽
快实施电镀,以减少镀层发花的可能性。
2 结语
根据上述各种常见故障的分析,可以先确定故
障原因,然后采取相应措施,即可排除。其实,只要
认真执行电镀的规范和规程,很多故障是可以避免
的,这也是减少或避免故障的最根本措施。
参考文献:
[1]李卫东,胡进,左正忠,等.有关复合电沉积机理研究[J].武汉
大学学报,2000,6(12):695—700.
EZ]徐龙堂,徐滨士,周美玲,等.电刷镀镍/镍包纳米Alz03颗粒
复合镀层微动磨损性能研究[J].摩擦学学报,2001,21(1):
24—27.
E3] 严祥成,刘磊,唐谊平,等.电沉积耐磨复合镀层的研究与进展
_J].电镀与环保,2004,24(3):5-9.
[4]毕晓勤,陈金身,胡余沛,等.铸铁基Ni—SiC复合电镀工艺的
研究[J].金刚石与磨料磨具工程,2008,28(4):66—69.
收稿日期:2009-09 7