不锈钢焊接发黑主要原因是(终审稿)
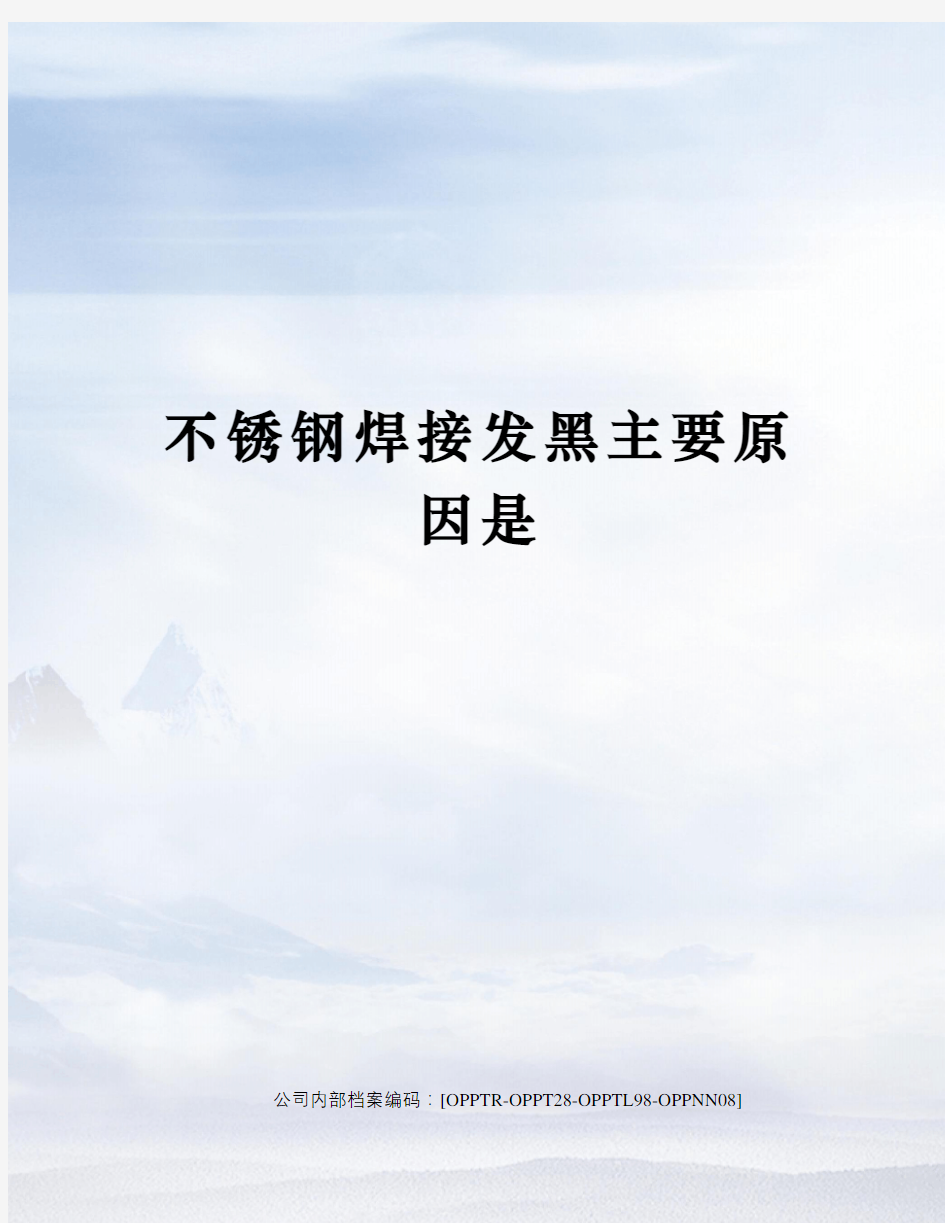

不锈钢焊接发黑主要原
因是
公司内部档案编码:[OPPTR-OPPT28-OPPTL98-OPPNN08]
不锈钢焊接发黑主要原因是:焊缝表面氧化及周边材料高温氧化。
造成不锈钢发黑的原因主要是:1、焊前板材等焊件未清理;2、氩气保护不足; 3、长时间焊接;4、电流过大;5、焊接钨针与焊件距离保持不当;6、钨针选择不当;7、熔池温高,焊接完成后没有继续保护;8、不锈钢焊件焊接背面保护不到位(背面发黑)。
具体分析:1、焊前未清理,不锈钢焊件上有油等杂质,造成焊接发黑。应对:焊件焊接部位焊前认真清理。
2、氩气保护不足,原因有:1、保护气体不纯,气体含氧及水分。应对:保证氩气质量。
3、保护气体输送管路有破损,有其他气体混入,造成焊接时氧化。应对:检查是否漏气,堵住焊枪瓷嘴,按下焊枪供气开关,(小心电击)。稍等,以检查有否压力。可从氩气瓶上加装的压力表及压力气柱上观察。
4、氩气供应不足。应对:观察压力表及压力气柱流量,气压不足时,更换氩气瓶。
5、对于焊接时氩气流量,送气、停气时机的把握,焊接开关时间上的把握,焊接电流大小调节,焊接时钨针与焊件的距离,钨针的选择,焊点熔池温度的高低,焊丝与焊件的匹配等焊接工艺参数的掌握及焊工手法与焊接工艺水平有直接关系。
对于氩弧焊焊接要求:1、提前送气:焊前,先送气然后对焊件进行焊接。以保证氩气对焊接部位的保护,防止氧化。
2、滞后送气:焊接收枪以后,枪口不要离开焊件焊接部位,继续送气,以保证焊件焊缝及周边部位不被高温氧化。
3、焊枪开关的控制:对于不锈钢,特别是薄板,在焊接时不可大电流长时间连续焊接,要多用点焊。电流过大,焊接速度过慢都会引起焊缝发黑。所以焊接时要根据板材厚度选电流,根据电流选钨针,根据钨针选瓷嘴,根据瓷嘴选气量。焊接速度要快,手法要准。
4、手法:钨针针尖与焊件的距离,钨针挨上焊件,焊缝发黑;钨针距离焊件太远,焊缝也发黑。其主要原因是保证焊接时焊接燃弧的稳定性及强度。
5、钨针的选择:①钨针尽量要选用带有黄色及白色标示的钨针,钨针质量要可靠;
②钨针在使用中要保持其尖锐,其原因是:钨针钝了,电流得不到集中,在焊接时电弧的稳定性不易保持,易发散。
6、焊点熔池温度的控制:与焊工手法及走枪速度有关。熔池温度满足焊件熔接与电流大小息息相关,而在保证冷却前不氧化则与走枪速度有关,边焊边冷却,走枪速度要保证氩气对前熔池的保护,不会被高温氧化。
7、要依据焊件材质选择焊丝材质,以保证材质上的统一性,避免材质差异而焊接发黑。
6、对于焊件焊点及周边部位背面的保护:可在焊件背面通氩气保护或涂保护剂。
7、焊工焊接技艺及其领悟和改进能力:理解电焊原理,明白其相互联系,在实践中总结、改善、提高及改进。比如:钨针出瓷嘴的长度;钨针离焊件的距离,不同厚度焊件所需的电流,不同电流所需的氩气流量等。
改进举例说明:焊枪内部钨针上饶铜丝,其作用是,在瓷嘴出气口使氩气形成紊流,加大气体的保护宽度,从而保证在走枪过快时对前焊点的保护及对焊点周边的不氧化保护。
在焊接工艺好的情况下,焊缝呈金黄色乃至白色。但若出现焊缝发黑,则需要处理。
对不锈钢焊件焊缝发黑的处理:最常用的有:一、羊毛刷+抛光蜡:对焊缝进行打磨。焊缝及其周边呈不锈钢光泽,最适合镜面箱体;
二、酸洗钝化膏:在焊缝及其周边涂抹酸洗钝化膏,数分钟后,以清水彻底清洗。焊缝及其周边恢复不锈钢色泽。
注:1、对不锈钢焊缝发黑处理必须在焊件冷却后进行。
2、若涂抹酸洗钝化膏除黑,在不锈钢材质标号不高的情况下必须认真彻底清洗,避免过腐蚀及形成色差。
3、焊缝除黑在焊缝焊渣清除之后进行。
现我厂可行的方案最好是进行除黑,并在同时进行氩弧焊焊接工艺的提高。这样可以减少箱体生产过多工艺步骤。立柱可以直接焊接在箱体上,免除立柱打孔,箱体螺丝焊接,螺丝固定立柱等工序,降低人工和材料成本,同时增强箱体强度。
对于箱体45度边框对角下料,有专用模具可以购买,这样可使生产快速方便,产品美观。
不锈钢焊接工艺作业指导书
不锈钢焊接工艺作业指导书-标准化文件发布号:(9456-EUATWK-MWUB-WUNN-INNUL-DDQTY-KII
不锈钢焊接工艺管道作业指导书 1.目的 为规范焊工操作,保证焊接质量,不断提高焊工的实际操作技术水平,特编制本指导书。 2. 编制依据 2.1. 设计图纸 2.2.《手工钨极氩弧焊技术及其应用》 2.3.《焊工技术考核规程》 3. 焊接准备 3.1. 焊接材料 焊丝:0Cr18Ni9Ti φ1、φ1.5、φ2.5、φ3 焊丝应有制造厂的质量合格证,领取和发放有焊材管理员统一管理。焊丝在使用前应清除油锈及其他污物,露出金属光泽。 3. 2. 氩气 氩气瓶上应贴有出厂合格标签,其纯度≥99.95%,所用流量6-9升/分钟,气瓶中的氩气不能用尽,瓶内余压不得低于0.5MPa ,以保证充氩纯度。 3.3. 焊接工具 3.3.1. 采用直流电焊机,本厂用WSE-315和TIG400两种型号焊机。 3.3.2. 选用的氩气减压流量计应开闭自如,没有漏气现象。切记不可先开流量计、后开气瓶,造成高压气流直冲低压,损坏流量计;关时先关流量计而后关氩气瓶。 3.3.3. 输送氩气的胶皮管,不得与输送其它气体的胶皮管互相串用,可用新的氧气胶皮管代用,长度不超过30米。 3.4. 其它工器具 焊工应备有:手锤、砂纸、扁铲、钢丝刷、电磨工具等,以备清渣和消缺。4.工艺参数 不锈钢焊接工艺参数选取表 5. 工序过程 5.1. 焊工必须按照规定经相应试件考试合格后,方可上岗位焊接。 5.2. 严禁在被焊件表面随意引燃电弧、试验电流或焊接临时支撑物等。
5.3. 焊工所用的氩弧焊把、氩气减压流量计,应经常检查,确保在氩弧焊封底时氩气为层流状态。 5.4. 接口前应将坡口表面及母材内、外壁的油、漆、垢锈等清理干净,直至发出金属光泽,清理范围为每侧各为10-15mm,对口间隙为2.5~3.5mm。 5.5. 接口间隙要匀直,禁止强力对口,错口值应小于壁厚的10%,且不大于 1mm。 5.6. 接口局部间隙过大时,应进行修整,严禁在间隙内添加塞物。 5.7. 接口合格后,应根据接口长度不同点4-5点,点焊的材料应与正式施焊相同,点焊长度10-15mm,厚度3-4mm。 5.8. 打底完成后,应认真检查打底焊缝质量,确认合格后再进行氩弧焊盖面焊接。 5.9. 引弧、收弧必须在接口内进行,收弧要填满熔池,将电弧引向坡口熄弧。 5.10. 点焊、氩弧焊、盖面焊,如产生缺陷,必须用电磨工具磨除后,再继续施焊,不得用重复熔化方法消除缺陷。 5.11. 应注意接头和收弧质量,注意接头熔合应良好,收弧时填满熔池。为保证焊缝严密性。 5.12. 盖面完毕应及时清理焊缝表面熔渣、飞溅。 6. 质量标准: 6.1. 质量按Q/ZB74-73 焊接通用技术条件和机械结构用不锈钢焊接管(GB/T12770—2002)标准检验。 6.2. 缺陷种类、原因分析及改进方法 氩弧焊焊接产生缺陷的原因及防止方法
不锈钢焊接工艺
不锈钢焊接工艺(第一部分:氩弧焊接) 焊接工艺指导书 一氩弧焊接 1.目的 为规范焊工操作,保证焊接质量,不断提高焊工的实际操作技术水平,特编制本指导书。 2.编制依据 . 设计图纸 .《手工钨极氩弧焊技术及其应用》 .《焊工技术考核规程》 3.焊接准备 . 焊接材料 焊丝:H1Cr18Ni9Tiφ、φ1、φ、φ、φ 焊丝应有制造厂的质量合格证,领取和发放有焊材管理员统一管理。焊丝在使用前应清除油锈及其他污物,露出金属光泽。 3. 2.氩气 氩气瓶上应贴有出厂合格标签,其纯度≥%,所用流量6-9升/分钟,气瓶中的氩气不能用尽,瓶内余压不得低于,以保证充氩纯度。 .焊接工具 3.3.1. 采用直流电焊机,本厂用WSE-315和TIG400两种型号焊机。 选用的氩气减压流量计应开闭自如,没有漏气现象。切记不可先开流量计、后开气瓶,造成高压气流直冲低压,损坏流量计;关时先关流量计而后关氩气瓶。输送氩气的胶皮管,不得与输送其它气体的胶皮管互相串用,可用新的氧气胶皮管代用,长度不超过30米。 .其它工器具 焊工应备有:手锤、砂纸、扁铲、钢丝刷、电磨工具等,以备清渣和消缺。4.工艺参数
不锈钢焊接工艺参数选取表 表一 5.工序过程 . 焊工必须按照“考规”规定经相应试件考试合格后,方可上岗位焊接。 . 严禁在被焊件表面随意引燃电弧、试验电流或焊接临时支撑物等。 . 焊工所用的氩弧焊把、氩气减压流量计,应经常检查,确保在氩弧焊封底时氩气为层流状态。 . 接口前应将坡口表面及母材内、外壁的油、漆、垢锈等清理干净,直至发出金属光泽,清理范围为每侧各为10-15mm,对口间隙为~。 .接口间隙要匀直,禁止强力对口,错口值应小于壁厚的10%,且不大于1mm。. 接口局部间隙过大时,应进行修整,严禁在间隙内添加塞物。 . 接口合格后,应根据接口长度不同点4-5点,点焊的材料应与正式施焊相同,点焊长度10-15mm,厚度3-4mm。 . 打底完成后,应认真检查打底焊缝质量,确认合格后再进行氩弧焊盖面焊接。. 引弧、收弧必须在接口内进行,收弧要填满熔池,将电弧引向坡口熄弧。 . 点焊、氩弧焊、盖面焊,如产生缺陷,必须用电磨工具磨除后,再继续施焊,不得用重复熔化方法消除缺陷。 . 应注意接头和收弧质量,注意接头熔合应良好,收弧时填满熔池。为保证焊缝严密性。 . 盖面完毕应及时清理焊缝表面熔渣、飞溅。 6.质量标准: . 质量按Q/ZB74-73 焊接通用技术条件和机械结构用不锈钢焊接管 (GB/T12770—2002)标准检验。
铸钢件通用焊接工艺
铸钢件通用焊接工艺 编制: 审核: 批准: 湖南湘船重工有限公司 2014年11月1日
铸钢件通用焊接工艺 1.编制目的及适用范围 编制目的 为规范船体结构工程现场铸钢件的焊接质量,特编制此通用焊接工艺。 适用范围 本工艺适用于公司建造所有船舶的铸钢件现场焊接施工。 2.焊接方法的选择 平焊、横焊、立焊采用焊条电弧焊打底,CO2焊填充; 仰焊采用焊条电弧焊打底、填充。 3.焊接材料的选择 焊条电弧焊采用E5015(J507)焊条,φ、φ4; CO2焊采用ER50-6实芯焊丝,φ。 4.焊前准备 焊条在使用前必须按规定烘焙,E5015焊条的烘焙温度为350℃。烘焙1小时后冷却到150℃保温,随用随取,领取的焊条应放入保温筒内。 不得使用药皮脱落或焊芯生锈的变质焊条、锈蚀或折弯的焊丝。 二氧化碳气体的纯度必须大于%,含水率小于等于%,瓶装气体必须留1Mpa气体压力,不得用尽。 焊前,焊缝坡口及附近50mm范围内清除净油、锈等污物。 施焊前,复查组装质量,定位焊质量和焊接部位的清理情况,如不符合要求,修正合格后方可施焊。 焊条电弧焊现场风速不大于8m/s、气体保护焊现场风速不大于2m/s,当超过规定风速时应设防风装置。 焊接前,检查各焊接设备是否出于正常运行状态。 检查坡口尺寸是否达到要求。 焊工必须持证上岗。
5.焊接工艺 焊接工艺参数的选择 (1)立焊:焊条电弧焊打底,CO2焊填充; (2)横焊:SMAW打底,GMAW填充; (3)仰焊:SMAW打底,SMAW填充 预热与后热 (1)预热铸钢件与异种钢施焊前应进行焊前预热,采用2~3把烘枪进行火焰预热。预热温度为170℃。待温度降至150℃时方可进行焊接。 (2)后热焊接结束后,用烘枪对焊缝进行后热处理。后热温度为200℃,之后采用50mm的保温棉对焊缝后热处理部分进行包裹,缓冷至室温。 焊接坡口:所有对接缝位置均按照设计图纸开全焊透坡口 焊接工艺措施 5.4.1焊接层间温度应控制在200~250℃; 5.4.2打底焊接时,采用手工电弧焊多层多道焊接,每层焊缝高度约为焊条直径,当焊道宽度大于20mm时方可以进行二氧化碳气体保护焊; 5.4.3焊接前应将每个铸钢件焊缝的真实坡口形式记录备案, 5.4.4铸钢件与异种钢接头的焊接,应按厚板焊接的有关工艺规定进行施焊
奥氏体不锈钢管道焊接工艺规程
奥氏体不锈钢管道焊接工艺规程 浙江华业电力工程股份有限公司企业标准 E n t er p ri s e S ta nd a rd f or zh e ji an g H u ay e Po w er En gi n ee r in g Co.,l t d HYDBP401-2004 奥氏体不锈钢管道焊接工艺规程 2004—04—01 发布 2004—04—01实施 浙江华业电力工程股份有限公司发布
前言 本标准主要起草人:仲春生 本标准审核人:朱文杰、周丰平、刘浩、王新宇 本标准批准人:沈银根 本标准自2004年04月01日发布,04月01日起在全公司范围内试行。本标准由公司工程部负责解释。
奥氏体不锈钢管道焊接工艺规程 1 范围 本标准适用于工业管道、公用管道和发电厂奥氏体不锈钢管道焊接施工。本标准也适用于手工氩弧焊和手工电弧焊作业。 2 规范性引用文件 下列文件中的条款通过本标准的引用而成为本标准的条款,凡是注日期的引用文件,其随后的修改单(不包括勘误的内容)或修订版均不适用于标准,然而,鼓励根据本部分达成协议的各方研究是否可使用这些文件的最新版本。凡是不注日期的引用文件,其最新版本适用于本标准。 GB50235—97 《工业金属管道工程施工及验收规范》 GB/T 983—95 《不锈钢焊条》 DL/T869-2004 《火力发电厂焊接技术规程》 劳人部[1988]1号《锅炉压力容器焊工考试规则》 HYDBP006-2004《压力管道安装工程焊接、热处理过程控制程序》 HYDBP018-2004《压力管道安装工程焊接材料管理程序》 HYDBP013-2004《压力管道安装工程材料设备储存管理程序》 HYDBP012-2004《压力管道安装工程材料设备搬运管理程序》 HYDBP008-2004《压力管道安装工程计量管理手册》 HYDBP007-2004《压力管道安装工程检验和试验控制程序》 HYDBP010-2004《压力管道安装工程不合格品控制程序》 劳动部发[1996]140号《压力管道安全管理与监察规定》 3 先决条件
2205双相不锈钢的焊接工艺规程(DOC)
1 绪论 随着工业技术的日益发展,一般奥氏体不锈钢难以满足应力腐蚀、点腐蚀和缝隙隧洞式腐蚀的要求。为此,冶金工作者进行了大量研究,研制出奥氏体—铁素体型不锈钢,即双相不锈钢。 传统的奥氏体不锈钢在晶间腐蚀、应力腐蚀、点腐蚀和缝隙腐蚀等局部腐蚀方面的抗力不足,尤其是应力腐蚀引起的断裂,其危害性极大。双相不锈钢是近二十年来开发的新钢种。通过正确控制各合金元素比例和热处理工艺使其固溶组织中铁素体相和奥氏体相各约占50%,从而将奥氏体不锈钢所具有的优良韧性和焊接性与铁素体不锈钢所具有的较高强度和耐氯化物应力腐蚀性能结合在一起,使双相不锈钢兼有铁素体不锈钢和奥氏体不锈钢的优点。 所谓双相不锈钢是在其固溶组织中铁素体相与奥氏体相约各占一半,一般量少相的含量也需要达到30%。在含C较低的情况下,Cr含量在18%-28%,Ni含量在3%-10%。有些钢还含有Mo、Cu、Nb、Ti,N等合金元素。该类钢兼有奥氏体和铁素体不锈钢的特点,与铁素体相比,塑性、韧性更高,无室温脆性,耐晶间腐蚀性能和焊接性能均显著提高,同时还保持有铁素体不锈钢的475℃脆性以及导热系数高,具有超塑性等特点。与奥氏体不锈钢相比,强度高且耐晶间副食和耐氯化物应力腐蚀有明显提高。双相不锈钢具有优良的耐孔蚀性能,也是一种节镍不锈钢。 由于两相组织的特点,通过正确控制化学成分和热处理工艺,使双相不锈钢兼有铁素体不锈钢和奥氏体不锈钢的优点,它将奥氏体不锈钢所具有的优良韧性和焊接性与铁素体不锈钢所具有的较高强度和耐氯化物应力腐蚀性能结合在一起,正是这些优越的性能使双相不锈钢作为可焊接的结构材料发展迅速,80年代以来已成为和马氏体型、奥氏体型和铁素体型不锈钢并列的一个钢类。 上世纪30年代就已在瑞典的试验室中研制出双相不锈钢(3RE60、Uranus50等),但是双相不锈钢真正产业化还是在上世纪60年代以后,其发展经历了3代历程。 1.1 我国双相不锈钢的应用 双相不锈钢是根据石油化工中强酸强碱造成的局部点蚀、应力腐蚀以及孔穴式腐蚀现象,一般不锈钢难以胜任的容器、管道以及零部件等而研制的,但由于
不锈钢焊接工艺
不锈钢焊接工艺 The Standardization Office was revised on the afternoon of December 13, 2020
焊接工艺指导书 一氩弧焊接 1.目的 为规范焊工操作,保证焊接质量,不断提高焊工的实际操作技术水平,特编制本指导书。 2. 编制依据 . 设计图纸 .《手工钨极氩弧焊技术及其应用》 .《焊工技术考核规程》 3. 焊接准备 . 焊接材料 焊丝:H1Cr18Ni9Ti φ1、φ、φ、φ3 焊丝应有制造厂的质量合格证,领取和发放有焊材管理员统一管理。焊丝在使用前应清除油锈及其他污物,露出金属光泽。 3. 2. 氩气 氩气瓶上应贴有出厂合格标签,其纯度≥%,所用流量6-9升/分钟,气瓶中的氩气不能用尽,瓶内余压不得低于,以保证充氩纯度。 . 焊接工具 3.3.1. 采用直流电焊机,本厂用WSE-315和TIG400两种型号焊机。 选用的氩气减压流量计应开闭自如,没有漏气现象。切记不可先开流量计、后开气瓶,造成高压气流直冲低压,损坏流量计;关时先关流量计而后关氩气瓶。 输送氩气的胶皮管,不得与输送其它气体的胶皮管互相串用,可用新的氧气胶皮管代用,长度不超过30米。 . 其它工器具 焊工应备有:手锤、砂纸、扁铲、钢丝刷、电磨工具等,以备清渣和消缺。4.工艺参数 不锈钢焊接工艺参数选取表
5. 工序过程 . 焊工必须按照“考规”规定经相应试件考试合格后,方可上岗位焊接。 . 严禁在被焊件表面随意引燃电弧、试验电流或焊接临时支撑物等。 . 焊工所用的氩弧焊把、氩气减压流量计,应经常检查,确保在氩弧焊封底时氩气为层流状态。 . 接口前应将坡口表面及母材内、外壁的油、漆、垢锈等清理干净,直至发出金属光泽,清理范围为每侧各为10-15mm,对口间隙为~3.5mm。 . 接口间隙要匀直,禁止强力对口,错口值应小于壁厚的10%,且不大于 1mm。 . 接口局部间隙过大时,应进行修整,严禁在间隙内添加塞物。 . 接口合格后,应根据接口长度不同点4-5点,点焊的材料应与正式施焊相同,点焊长度10-15mm,厚度3-4mm。 . 打底完成后,应认真检查打底焊缝质量,确认合格后再进行氩弧焊盖面焊接。 . 引弧、收弧必须在接口内进行,收弧要填满熔池,将电弧引向坡口熄弧。. 点焊、氩弧焊、盖面焊,如产生缺陷,必须用电磨工具磨除后,再继续施焊,不得用重复熔化方法消除缺陷。 . 应注意接头和收弧质量,注意接头熔合应良好,收弧时填满熔池。为保证焊缝严密性。 . 盖面完毕应及时清理焊缝表面熔渣、飞溅。 6. 质量标准: . 质量按Q/ZB74-73 焊接通用技术条件和机械结构用不锈钢焊接管 (GB/T12770—2002)标准检验。 . 缺陷种类、原因分析及改进方法 氩弧焊焊接产生缺陷的原因及防止方法
不锈钢焊接工艺标准
不锈钢焊接工艺标准 Document serial number【LGGKGB-LGG98YT-LGGT8CB-LGUT-
焊接工艺指导书 一氩弧焊接 1.目的 为规范焊工操作,保证焊接质量,不断提高焊工的实际操作技术水平,特编制本指导书。 2. 编制依据 . 设计图纸 .《手工钨极氩弧焊技术及其应用》 .《焊工技术考核规程》 3. 焊接准备 . 焊接材料 焊丝:H1Cr18Ni9Tiφ1、φ、φ、φ3 焊丝应有制造厂的质量合格证,领取和发放有焊材管理员统一管理。焊丝在使用前应清除油锈及其他污物,露出金属光泽。 3. 2. 氩气 氩气瓶上应贴有出厂合格标签,其纯度≥%,所用流量6-9升/分钟,气瓶中的氩气不能用尽,瓶内余压不得低于,以保证充氩纯度。 . 焊接工具输送氩气的胶皮管,不得与输送其它气体的胶皮管互相串用,可用新的氧气胶皮管代用,长度不超过30米。 . 其它工器具 焊工应备有:手锤、砂纸、扁铲、钢丝刷、电磨工具等,以备清渣和消缺。4.工艺参数 不锈钢焊接工艺参数选取表
. 焊工必须按照“考规”规定经相应试件考试合格后,方可上岗位焊接。 . 严禁在被焊件表面随意引燃电弧、试验电流或焊接临时支撑物等。 . 焊工所用的氩弧焊把、氩气减压流量计,应经常检查,确保在氩弧焊封底时氩气为层流状态。 . 接口前应将坡口表面及母材内、外壁的油、漆、垢锈等清理干净,直至发出金属光泽,清理范围为每侧各为10-15mm,对口间隙为~。 .接口间隙要匀直,禁止强力对口,错口值应小于壁厚的10%,且不大于 1mm。 . 接口局部间隙过大时,应进行修整,严禁在间隙内添加塞物。 . 接口合格后,应根据接口长度不同点4-5点,点焊的材料应与正式施焊相同,点焊长度10-15mm,厚度3-4mm。 . 打底完成后,应认真检查打底焊缝质量,确认合格后再进行氩弧焊盖面焊接。 . 引弧、收弧必须在接口内进行,收弧要填满熔池,将电弧引向坡口熄弧。. 点焊、氩弧焊、盖面焊,如产生缺陷,必须用电磨工具磨除后,再继续施焊,不得用重复熔化方法消除缺陷。 . 应注意接头和收弧质量,注意接头熔合应良好,收弧时填满熔池。为保证焊缝严密性。 . 盖面完毕应及时清理焊缝表面熔渣、飞溅。 6. 质量标准: . 质量按Q/ZB74-73 焊接通用技术条件和机械结构用不锈钢焊接管 (GB/T12770—2002)标准检验。 . 缺陷种类、原因分析及改进方法 氩弧焊焊接产生缺陷的原因及防止方法
不锈钢焊接工艺标准
焊接工艺指导书 一氩弧焊接 1.目的 为规范焊工操作,保证焊接质量,不断提高焊工的实际操作技术水平,特编制本指导书。 2. 编制依据 2.1. 设计图纸 2.2.《手工钨极氩弧焊技术及其应用》 2.3.《焊工技术考核规程》 3. 焊接准备 3.1. 焊接材料 焊丝:H1Cr18Ni9Ti 1、φ1 5、φ2 5、φ3 焊丝应有制造厂的质量合格证,领取和发放有焊材管理员统一管理。焊丝在使用前应清除油锈及其他污物,露出金属光泽。 3. 2. 氩气 氩气瓶上应贴有出厂合格标签,其纯度≥99.95%,所用流量6-9升/分钟,气瓶中的氩气不能用尽,瓶内余压不得低于0.5MPa ,以保证充氩纯度。 3.3. 焊接工具 3.3.1. 采用直流电焊机,本厂用WSE-315和TIG400两种型号焊机。
3.3.2. 选用的氩气减压流量计应开闭自如,没有漏气现象。切记不可先开流量计、后开气瓶,造成高压气流直冲低压,损坏流量计;关时先关流量计而后关氩气瓶。 3.3.3. 输送氩气的胶皮管,不得与输送其它气体的胶皮管互相串用,可用新的氧气胶皮管代用,xx不超过30米。 3.4. 其它工器具 焊工应备有:手锤、砂纸、扁铲、钢丝刷、电磨工具等,以备清渣和消缺。 4.工艺参数 不锈钢焊接工艺参数选取表 表一 5. 工序过程 5.1. 焊工必须按照“考规”规定经相应试件考试合格后,方可上岗位焊接。 5.2. 严禁在被焊件表面随意引燃电弧、试验电流或焊接临时支撑物等。 5.3. 焊工所用的氩弧焊把、氩气减压流量计,应经常检查,确保在氩弧焊封底时氩气为层流状态。 5.4. 接口前应将坡口表面及母材内、外壁的油、漆、垢锈等清理干净,直至发出金属光泽,清理范围为每侧各为10-15mm,对口间隙为2.5~3.5mm。 5.5. 接口间隙要匀直,禁止强力对口,错口值应小于壁厚的10%,且不大于1mm。 5.6. 接口局部间隙过大时,应进行修整,严禁在间隙内添加xx。 5.7. 接口合格后,应根据接口xx不同点4-5点,点焊的材料应与正式施焊相同,点焊xx10-15mm,厚度3-4mm。
通用焊接工艺规程
通用焊接工艺规程 2006-05-25发布2006-06-01日实施
1 碳素钢、合金钢及不锈钢的焊接 1.1 焊前准备 1.1.1焊缝的坡口形式和尺寸应符合设计文件的规定,当无规定时,符合本规附录A.0.1的规定. 1.1.2焊件的坡口加工宜采用机械方法,也可采用等离子弧、氧乙炔焰等热加工方法,在采用热加工方法加工坡口后,必须除去坡口表面的氧化皮、熔渣及影响接头质量的表面层,并应将凹凸不平处打磨平整。 1.1.3焊件组焊前应将坡口及其两侧表面不小于30 mm围的油、漆、垢、锈、毛刺及镀锌层等清除干净,不得有裂纹、夹层、加工损伤、毛刺及火焰切割熔渣等缺陷。油污清理方法如下,首先用丙酮或四氯化碳等有机溶剂擦洗,然后用不锈钢丝刷清理至露出金属光泽,使用的钢丝刷应定期进行脱脂处理。 1.1.4 管子或管件、筒体对接焊缝组对时,壁应齐平,壁错边量不宜超过管壁厚度的10%,且不应大于2mm; 1.1.5 焊缝的设置应避开应力集中区,便于焊接和热处理,并应符合下列规定: 1.1.5.1 钢板卷筒或设备、容器的筒节与筒节、筒节与封头组对时,相邻两纵向焊缝间的距离应大于壁厚的3倍,且不应小于100 mm,同一筒节上两相邻纵缝间的距离不应小于200 mm; 1.1.5.2除焊接及成型管件外的其他管子对接焊缝的中心到管子弯曲起点的距离不应小于管子外径,且不应小于l00 mm;管子对接焊缝与支、吊架边缘之间的距离不应小于50 mm。同一直管段上两对接焊缝中心面间的距离:当公称直径大于或等于150mm 时不应小于150mm;公称直径小于150mm时不应小于管子外径; 1.1.5.3 不宜在焊缝及其边缘上开孔。
不锈钢焊接工艺标准(完整资料).doc
此文档下载后即可编辑 焊接工艺指导书 一氩弧焊接 1.目的 为规范焊工操作,保证焊接质量,不断提高焊工的实际操作技术水平,特编制本指导书。 2. 编制依据 2.1. 设计图纸 2.2.《手工钨极氩弧焊技术及其应用》 2.3.《焊工技术考核规程》 3. 焊接准备 3.1. 焊接材料 焊丝:H1Cr18Ni9Ti φ1、φ1.5、φ2.5、φ3 焊丝应有制造厂的质量合格证,领取和发放有焊材管理员统一管理。焊丝在使用前应清除油锈及其他污物,露出金属光泽。 3. 2. 氩气 氩气瓶上应贴有出厂合格标签,其纯度≥99.95%,所用流量6-9升/分钟,气瓶中的氩气不能用尽,瓶内余压不得低于0.5MPa ,以保证充氩纯度。 3.3. 焊接工具 3.3.1. 采用直流电焊机,本厂用WSE-315和TIG400两种型号焊机。 3.3.2. 选用的氩气减压流量计应开闭自如,没有漏气现象。切记不可先开流量计、后开气瓶,造成高压气流直冲低压,损坏流量计;关时先关流量计而后关氩气瓶。 3.3.3. 输送氩气的胶皮管,不得与输送其它气体的胶皮管互相串用,可用新的氧气胶皮管代用,长度不超过30米。 3.4. 其它工器具 焊工应备有:手锤、砂纸、扁铲、钢丝刷、电磨工具等,以备清渣和消缺。 4.工艺参数 不锈钢焊接工艺参数选取表
5. 工序过程 5.1. 焊工必须按照“考规”规定经相应试件考试合格后,方可上岗位焊接。 5.2. 严禁在被焊件表面随意引燃电弧、试验电流或焊接临时支撑物等。 5.3. 焊工所用的氩弧焊把、氩气减压流量计,应经常检查,确保在氩弧焊封底时氩气为层流状态。 5.4. 接口前应将坡口表面及母材内、外壁的油、漆、垢锈等清理干净,直至发出金属光泽,清理范围为每侧各为10-15mm,对口间隙为2.5~3.5mm。 5.5. 接口间隙要匀直,禁止强力对口,错口值应小于壁厚的10%,且不大于1mm。 5.6. 接口局部间隙过大时,应进行修整,严禁在间隙内添加塞物。 5.7. 接口合格后,应根据接口长度不同点4-5点,点焊的材料应与正式施焊相同,点焊长度10-15mm,厚度3-4mm。 5.8. 打底完成后,应认真检查打底焊缝质量,确认合格后再进行氩弧焊盖面焊接。 5.9. 引弧、收弧必须在接口内进行,收弧要填满熔池,将电弧引向坡口熄弧。 5.10. 点焊、氩弧焊、盖面焊,如产生缺陷,必须用电磨工具磨除后,再继续施焊,不得用重复熔化方法消除缺陷。 5.11. 应注意接头和收弧质量,注意接头熔合应良好,收弧时填满熔池。为保证焊缝严密性。
铝合金通用焊接工艺规程
铝合金通用焊接工艺规程 1 使用范围及目的 范围:本规范是适用于地铁铝合金部件焊接全过程的通用工艺要求。目的:与焊接相关的作业人员按标准规范作业,同时也使焊接过程检查更具可操作性。 2 焊前准备的要求 2.1 在焊接作业前首先必须根据图纸检查来料或可见的重要尺寸、形位公差和焊接质量,来料不合格不能进行焊接作业。 2.2 在焊接作业前,必须将残留在产品表面和型腔内的灰尘、飞溅、毛刺、切削液、铝屑及其它杂物清理干净。 2.3 用棉布将来料或工件上的灰尘和脏物擦干净,如果工件上有油污,使用清洗液清理干净。 2.4 使用风动不锈钢丝轮将焊缝区域内的氧化膜打磨干净,以打磨处呈白亮色为标准,打磨区域为焊缝两侧至少25mm以上。 2.5 焊前确认待焊焊缝区域无打磨时断掉的钢丝等杂物。 2.6 钢焊和铝焊的打磨、清理工具禁止混用。 2.7 原则上工件打磨后在48小时内没有进行焊接,酸洗部件在72小时内没有进行焊接,则焊前必须重新打磨焊接区域。 2.8 为保证焊丝的质量,焊丝原则上用完后再到焊丝房领用,对于晚班需换焊丝的,可以在当天白班下班前领用,禁止现场长时间(24小时以上)存放焊丝。 2.9 在焊接作业前,必须检查焊接设备和工装处于正常工作状态。焊 前应检查焊机喷嘴的实际气流量(允差为+3L/min),自动焊焊丝在8圈以下,手工焊焊丝在5圈以上,否则需要更换气体或焊丝;检查导电嘴是否拧紧,喷嘴是否需要清理。导电嘴不能只简单的采用手动拧紧,必须采用尖嘴钳拧紧。检查工装状
态是否完好,若工装有损坏,应立即通知工装管理员进行核查,并组织维修,禁止在工装异常状态下进行焊接操作。 2.10 焊接前必须检查环境的温度和湿度。作业区要求温度在5?以上,MIG焊湿度小于65,,TIG焊湿度小于70,。环境不符合要求,不能进行焊接作业。 2.11 焊接过程中不允许有穿堂风。因此,在焊接作业前必须关闭台位附近的通道门。当焊接过程中,如果有人打开台位相近处的大门,则要立即停止施焊。如果台位附近的空调风影响到焊接作业,也必须将该处空调的排风口关闭,才能进行焊接作业。 2.12 对于厚度在8mm以上(包括8mm)的铝材,焊接要预热,预热温度 80?,120?,层间温度控制在60?,100?。预热时要使用接触式测温仪进行测温,工件板厚不超过50mm时,正对着焊工的工件表面,距坡口表面4倍板厚,最多不超过50mm的距离处测量,当工件厚度超过50mm时,要求的测温点应位于至少75mm距离的母材或坡口任何方向上同一的位置,条件允许时,温度应在加热面的背面上测定,严禁凭个人感觉及经验做事。 2.13 按图纸进行组装,点焊固定,点焊要满足与焊接相同的要求,不属于焊接组成部分的点焊要尽可能在焊接时完全熔化(图纸要求的点焊 除外,如焊接垫板的固定),组焊后不能出现图纸要求之外的焊点,部件固定后按图纸要求进行尺寸、平行度、垂直度等项点的自检,自检合格后,根据图纸进行焊接,操作工人必须及时、真实填写操作记录。 2.14 当图纸要求或工艺要求使用焊接垫板时,应将焊接垫板点焊在工件上,点焊应符合焊接质量要求,点焊要求为:焊接垫板小于100mm时,在焊接垫板两端点焊固定,焊接垫板大于100mm时,根据焊接垫板长度点焊均匀分布,间距100mm。 2.15 为了避免腐蚀,铝合金配件存放时不允许直接采用钢或者铜材质的容器存放,不允许将配件直接放置在钢制的工装或地板上。 2.16 对于焊缝质量等级为
不锈钢管道焊接施工作业指导书-内容
目录 1. 编制依据 (2) 2. 工程概述 (2) 3. 开工条件和施工准备 (3) 4. 人员及工器具配备 (3) 5. 主要施工工序和方法 (4) 6. 质量保证措施 (6) 7. 职业健康安全环境保护措施 (7) 8. 环境控制措施 (9) 9. 附图 (10)
1.编制依据 1.1 1.2 施工组织总设计和汽机专业施工组织设计; 1.3 《火电施工质量检验及评定标准》第五部分管道及系统DL/T5210-2009; 1.4 《电力建设安全工作规程》(火力发电厂部分DL/T5009.1-2002); 1.5 《锅炉压力容器管道焊工考试与管理细则》[2002]109号; 1.3 《钢制承压管道对接焊接接头射线技术规程》DL/T 821-2002; 1.4 《火力发电厂焊接技术规程》DL/T869-2004; 1.9 《焊接工艺评定规程》DL/T868-2004; 1.10 《电力建设施工质量验收及评价规程》第七部分焊接DL/T5210.7-2010; 1.11 《火力发电厂焊接热处理技术规程》DL/T819-2002; 1.12 《火力发电厂金属技术监督规程》DL/T438-2009; 1.13 《火力发电厂异种钢焊接技术规程》DL/T752-2001; 1.14 1.15 《工程建设标准强制性条文》电力工程部分—2006版; 1.16 《电力建设施工及验收技术规范》管道篇DL/T 5031-94。 2 工程概述 可实现集中供热,不仅能够满足石河子市区近、远期采暖热负荷增长的需要,提高能源综合利用率,而且有利于改善城区生态环境和地区环境空气质量,促进地方经济可持续发展,符合国家能源产业政策及环保政策。 2.2 施工内容 依据设计院设计图纸,不锈钢管道主要包括:仪用压缩空气系统、化学水系统、本体润滑油及抗燃油油等系统组成,为了在施工过程中提高焊接质量,特制订此作业指导书。 本机组不锈钢管道材质分别为:仪用压缩空气系统材质为0Cr18Ni9;本体套装油管道材质为0Cr18Ni9Ti;化学水系统材质均为1Cr18Ni9Ti。 仪用压缩空气系统:设计压力1.0MPa,常温,管道从汽机精处理接出至锅炉仪用压缩空气管道,管道主要规格为φ159×4.5。 本体润滑油管道为套装油管道,设计压力:0.3MPa,45℃,接口形式均为钢管对接,由主机油箱引出至前轴承箱,#1--#9各轴承箱进、排油管道,包括顶轴油管道规格有:φ219×6,φ610×10,φ57×4,φ108×4.5,φ325×8,φ89×4.5,φ20×2.5等。
不锈钢焊接实用工艺..
市瑞昌电力技术 不锈钢焊接工艺规 生产部/质检部
不锈钢焊接工艺标准 一氩弧焊接 1.目的 为规焊工操作,保证焊接质量,不断提高焊工的实际操作技术水平,特编制本指导书。 2. 编制依据 2.1. 设计图纸 2.2.《手工钨极氩弧焊技术及其应用》 2.3.《焊工技术考核规程》 3. 焊接准备 3.1. 焊接材料 焊丝:H1Cr18Ni9Ti φ1、φ1.5、φ2.5、φ3 焊丝应有制造厂的质量合格证,领取和发放有焊材管理员统一管理。焊丝在使用前应清除油锈及其他污物,露出金属光泽。 3. 2. 氩气 氩气瓶上应贴有出厂合格标签,其纯度≥99.95%,所用流量6-9升/分钟,气瓶中的氩气不能用尽,瓶余压不得低于0.5MPa ,以保证充氩纯度。 3.3. 焊接工具 3.3.1. 采用直流电焊机。 3.3.2. 选用的氩气减压流量计应开闭自如,没有漏气现象。切记不可先开流量计、后开气瓶,造成高压气流直冲低压,损坏流量计;关时先关流量计而后关氩气瓶。 3.3.3. 输送氩气的胶皮管,不得与输送其它气体的胶皮管互相串用,可用新的氧气胶皮管代用,长度不超过30米。 3.4. 其它工器具 焊工应备有:手锤、砂纸、扁铲、钢丝刷、电磨工具等,以备清渣和消缺。 4.工艺参数 不锈钢焊接工艺参数选取表 表一 壁厚mm 焊丝直 径mm 钨极 直径 mm 焊接电流 A 氩气流 量 L/min 焊接 层次 喷嘴 直径 mm 电源 极性 焊缝 余高 mm 焊缝 宽度 mm 1 1.0230-50616正接13 2 1.2240-60616正接14 3 1.6-2.4360-9081-28正接1-2.55 4 1.6-2.4380-10081-28正接1-2.06 5. 工序过程
不锈钢焊接工艺
1?目的 为规范焊工操作,保证焊接质量,不断提高焊工的实际操作技术水平,特编制本指导书。 2.编制依据 2丄设讣图纸 2.2.《手工钩极氮弧焊技术及实应用》 2.3.《焊工技术考核规程》 3?焊接准备 3.1.焊接材料 焊丝J HlCrl8Ni9Ti
5.工序过程 5.1.焊工必须按照“考规‘‘规泄经相应试件考试合格后,方可上岗位焊接。 52 严禁在被焊件表而随意引燃电弧、试验电流或焊接临时支撑物等。 5.3.焊工所用的氮弧焊把、氮气减压流应经常检査,确保在氮弧焊封底时氮气为层流状态。 54 接口前应将坡口表而及母材内、外壁的油、漆、垢锈等淸理干净,直至发出金属光泽,淸理范用为每侧齐为10-15mm,对口间隙为2.5?3?5mm. 5.5?接口间隙要匀直?禁止强力对口,错口值应小于壁厚的10%.且不大于1mm. 56 接口局部间隙过大时,应进行修整,严禁在间隙内添加塞物。 5.7.接口合格后,应根据接口长度不同点4-5点,点焊的材料应与正式施焊相同,点焊长度10-15mm> 厚度 3-4mm.z 5.8.打底完成后,应认貞?检査打底焊缝质量,确认合搭后再进行氮弧焊盖而焊接。 5.9.引弧、收弧必须在接口内进行,收弧要填满熔池,将电弧引向坡口熄弧。 5.10.点焊、氯弧焊、盖而焊,如产生缺陷,必须用电磨工具氏等除后,再继续施焊,不得用重复熔化方法消除缺陷. 5.ir 应注意接头和收弧质量,注意接头熔合应良好,收弧时填满熔池。为保证焊缝严密性。 5A2.孟面完毕应及时淸理焊缝表而熔渣、飞溅。 6?质量标准: 6.1.质量按Q/ZB74-73焊接通用技术条件和机械结构用不锈钢焊接管(GBZn2770—2002) 标准检验。 6.2.缺陷种类、原因分析及改进方法 氮弧焊焊接产生缺陷的原因及防止方法
通用轨道焊接工艺
轨道焊接通用工艺 1、适用范围: 本通用工艺适用于P38~P60 (GB183-63 GB2585-81)、A65、A75和A100起重机轨道的对接施焊。 2、轨道的采购要求和加工 2.1、轨道采购要求 市场上常见轨道为两端淬火及已钻鱼尾孔,为便于轨道焊接,今后此种轨道订货时要求轨道两端不淬火,且两头不钻鱼尾孔。 技术条件见GB183-63 GB2585-81 2.2、淬火轨道的处理方法: 2.2.1、用机械切割设备割去轨道两端150mm(见下图) 2.2.2、用氧乙炔割去轨道两端150mm,切割前需预热(详见5、预热、保温及层间温度的控制) 2.3、坡口加工 轨道焊接坡口可采用风割或机械切割两种加工方法,用氧乙炔切割轨道前应在切割处预热(详见5、预热、保温及层间温度的 控制),切割后必须用砂轮打磨平整;磁粉探伤检查轨道端部材料
质量,检查合格方可使用。 3、冷作装配要领(见轨道拼装示意图一、二) 3.1、利用反变形法来控制焊接变形,反变形量为6mm/6m,即按L/1000 放高度反变形量,轨道对接接头间隙为20+2mm。 3.2、约束:按图二所示对轨道上下左右充分约束,以防轨道接口产生错边现象。 3.2.1、用刚性梁放置在轨道下作平台之用。 3.2.2、左右方向的约束采用L型约束4件,位置距接头200mm处。
3.2.3、上下方向的约束采用门型约束,位置距接头500mm处设置一档,其余每隔2500mm设置一档。 3.2.4、所有约束在焊接接头焊妥,热处理完毕,接头缓冷后方可拆除。3.3、衬垫:衬垫采用Q235钢板,规格-6 ×60×(B+40),其中B为轨道底部宽度,衬垫与轨道的装配间隙越小越好。 4、焊前准备工作 4.1、焊前必须对轨道两端各150mm范围清除铁锈、油漆、水份等杂质。4.2、焊条轨道底部、腹部采用E6015(Φ4mm、Φ5mm)、头部JH-40B (Φ4mm)或HF-350(Φ4mm)手工焊电焊条,焊前须经350oC 恒温烘焙1小时,然后放在100--150?C恒温桶内随用随取;若焊条受潮只能重新烘干一次;从焊条保温筒内抽用每一根焊条后立即盖好保温筒盖子,以免焊条受潮。 4.3、焊接轨道时应做好防风防雨措施,轨道施焊时若有风,应用挡风板挡住风源,以免接缝产生气孔、裂缝。轨道接缝每只接头必须 一次焊毕。 5、预热、保温及层间温度的控制 焊接前用氧乙炔中性火焰对轨道接头两端各200mm范围内进行均匀加热,预热温度250~300°C,预热恒温时间15分钟,焊接层间250~300°C。预热处理温度和层间温度根据气温可浮动,如气温在10℃以上预热,温度取下限。 6、焊接要领 6.1、轨道接头焊前对约束、衬垫板、预热进行检查。
不锈钢焊接工艺标准
不锈钢焊接工艺标准 Revised by Chen Zhen in 2021
焊接工艺指导书 一氩弧焊接 1.目的为规范焊工操作,保证焊接质量,不断提高焊工的实际操作技术水平,特编制本指导书。 2. 编制依据 . 设计图纸 .《手工钨极氩弧焊技术及其应用》 .《焊工技术考核规程》 3. 焊接准备 . 焊接材料 焊丝:H1Cr18Ni9Tiφ1、φ、φ、φ3 焊丝应有制造厂的质量合格证,领取和发放有焊材管理员统一管理。焊丝在使用前应清除油锈及其他污物,露出金属光泽。 3. 2. 氩气 氩气瓶上应贴有出厂合格标签,其纯度≥%,所用流量6-9升/分钟,气瓶中的氩气不能用尽,瓶内余压不得低于,以保证充氩纯度。 . 焊接工具输送氩气的胶皮管,不得与输送其它气体的胶皮管互相串用,可用新的氧气胶皮管代用,长度不超过30米。 . 其它工器具焊工应备有:手锤、砂纸、扁铲、钢丝刷、电磨工具等,以备清渣和消缺。 4.工艺参数 不锈钢焊接工艺参数选取表 . 焊工必须按照“考规”规定经相应试件考试合格后,方可上岗位焊接。 . 严禁在被焊件表面随意引燃电弧、试验电流或焊接临时支撑物等。 . 焊工所用的氩弧焊把、氩气减压流量计,应经常检查,确保在氩弧焊封底时氩气为层流状态。
. 接口前应将坡口表面及母材内、外壁的油、漆、垢锈等清理干净,直至发出金属光泽,清理范围为每侧各为10-15mm,对口间隙为~。 .接口间隙要匀直,禁止强力对口,错口值应小于壁厚的10%,且不大于 1mm。 . 接口局部间隙过大时,应进行修整,严禁在间隙内添加塞物。 . 接口合格后,应根据接口长度不同点4-5点,点焊的材料应与正式施焊相同,点焊长度10-15mm,厚度3-4mm。 . 打底完成后,应认真检查打底焊缝质量,确认合格后再进行氩弧焊盖面焊接。 . 引弧、收弧必须在接口内进行,收弧要填满熔池,将电弧引向坡口熄弧。. 点焊、氩弧焊、盖面焊,如产生缺陷,必须用电磨工具磨除后,再继续施焊,不得用重复熔化方法消除缺陷。 . 应注意接头和收弧质量,注意接头熔合应良好,收弧时填满熔池。为保证焊缝严密性。 . 盖面完毕应及时清理焊缝表面熔渣、飞溅。 6. 质量标准: . 质量按Q/ZB74-73 焊接通用技术条件和机械结构用不锈钢焊接管 (GB/T12770—2002)标准检验。 . 缺陷种类、原因分析及改进方法 氩弧焊焊接产生缺陷的原因及防止方法
史上最全的不锈钢焊接工艺
史上最全的不锈钢焊接工艺 不锈钢焊接工艺技术要点不锈钢焊管是在焊 管成型机上,由不锈钢板经若干道模具碾压成型并经焊接而成。由于不锈钢的强度较高,且其结构为面心立方晶格,易形成加工硬化,使焊管成型时:一方面模具要承受较大的摩擦力,使模具容易磨损;另一方面,不锈钢板料易与模具表面形成粘结(咬合),使焊管及模具表面形成拉伤。因此,好的不锈钢成型模具必须具备极高的耐磨和抗粘结(咬合)性能。我们对进口焊管模具的分析表明,该类模具的表面处理都是采用超硬金属碳化物或氮化物覆层处理。激光焊接、高频焊接与传统的熔化焊接相比具有焊接速度快、能量密度高、热输入小的特点,因此热影响区窄、晶粒长大程度小、焊接变形小、冷加工成形性能好,容易实现自动化焊接、厚板单道一次焊透,其中最重要的特点是Ⅰ形坡口对接焊不需要填充材料。焊接技术主要应用在金属母材上,常用的有电弧焊,氩弧焊,CO2保护焊,氧气-乙炔焊,激光焊接,电渣压力焊等多种,塑料等非金属材料亦可进行焊接。金属焊接方法有40种以上,主要分为熔焊、压焊和钎焊三大类。熔焊是在焊接过程中将工件接口加热至熔化状态,不加压力完成焊接的方法。熔焊时,热源将待焊两工件接口处迅速加热熔化,形成熔池。熔池随热源向前移动,冷却后
形成连续焊缝而将两工件连接成为一体。在熔焊过程中,如果大气与高温的熔池直接接触,大气中的氧就会氧化金属和各种合金元素。大气中的氮、水蒸汽等进入熔池,还会在随后冷却过程中在焊缝中形成气孔、夹渣、裂纹等缺陷,恶化焊缝的质量和性能。压焊是在加压条件下,使两工件在固态下实现原子间结合,又称固态焊接。常用的压焊工艺是电阻对焊,当电流通过两工件的连接端时,该处因电阻很大而温度上升,当加热至塑性状态时,在轴向压力作用下连接成为一体。各种压焊方法的共同特点是在焊接过程中施加压力而不加填充材料。多数压焊方法如扩散焊、高频焊、冷压焊等都没有熔化过程,因而没有象熔焊那样的有益合金元素烧损,和有害元素侵入焊缝的问题,从而简化了焊接过程,也改善了焊接安全卫生条件。同时由于加热温度比熔焊低、加热时间短,因而热影响区小。许多难以用熔化焊焊接的材料,往往可以用压焊焊成与母材同等强度的优质接头。钎焊是使用比工件熔点低的金属材料作钎料,将工件和钎料加热到高于钎料熔点、低于工件熔点的温度,利用液态钎料润湿工件,填充接口间隙并与工件实现原子间的相互扩散,从而实现焊接的方法。焊接时形成的连接两个被连接体的接缝称为焊缝。焊缝的两侧在焊接时会受到焊接热作用,而发生组织和性能变化,这一区域被称为热影响区。焊接时因工件材料焊接材料、焊接电流等不同,焊后在焊缝和热影
氩弧焊通用焊接工艺
氩弧焊通用焊接工艺 Modified by JACK on the afternoon of December 26, 2020
手工钨极氩弧焊 通 用 焊 接 工 艺 目录 1、一般要求 2、应用范围 3、焊接准备 4、操作技术 5、焊接 6、氩气焊丝和焊条 7、焊接工艺
8、质量记录 9、焊接及注意事项 10、钨极氩弧焊安全规程 11、焊接危险点危险源辩识、评价及控制对策表 一、一般要求 1、焊接材料 焊丝:用于GB的焊丝应符合GB/T8110的有关规定,对于入库时间长而有锈斑,影响使用的应予报废。 保护气体的种类和质量:采用纯度大于%纯氩。 钨极的种类:采用钍钨极或铈钨电极,其端头的几何形状应根据电流的大小选择,采用小电流时,端头夹角为30度。 焊接设备:氩弧焊机。 焊接辅助装备:安全防护用品、手锤、角向砂轮等。 焊工资格:焊工必须经过南昌市技术质量监督局培训,并且取得相应的合格项目,方可从事相关焊接工作。 焊接工作必须按照技要、技术标准进行。 焊接环境:当风速大于2m/s、相对湿度大于90%、雨、雪环境、焊件温度低于0℃时,均应采取相应的措施来保证焊接质量。当焊件温度在-18~0℃之间时,应将始焊点周围100mm的母材预热到约15℃再开始焊接。否则禁止施焊。 焊接极性:直流正接既焊枪接负极,工件接正极。 在操作过程中若有个人无法解决的问题,应立即与班组长、检验员或焊接工程师联系。
根据焊接位置、持证项目、接头形式和作业情况等选择合适的焊接辅助装置。 去除坡口内、外20mm范围内的水、锈、油污等杂质。 根据图纸、工艺要求核对坡口形式及角度、材质、坡口尺寸及装配质量。 如需要标记移植,检查标记移植情况。 检查所用设备是否完好情况。 不锈钢管焊接的接头,应内部充氩保护,保护时,管子两头和管子四周的孔应该用美纹纸或铁板封住,以增强保护效果。 试焊,根据表1调节焊接参数。 表1焊接参数 二、应用范围 不同直径的钢管及耐热合金钢管子一般采用钨极氩弧焊打底,手工电弧焊填充及盖面层焊接,小直径管子可用手工钨极氩弧焊打底及盖面层焊接。 采用手工钨极氩弧焊打底的焊接工艺,具有很多优越性,它不仅能充分保证母材根部的良好熔透,焊缝具有良好的成型,同时可提高根部焊缝的塑性和韧性,减少焊接应力,从而可以避免产生根部裂纹,施焊中也不易出现未焊透、夹渣、气孔等缺陷。所以,已广泛用于一般重要设备,如承压管道、高压容器和高温高压锅炉中管子的焊接。 钨极氩弧焊焊接管子,主要有两种形式,一种是水平钨极自动氩弧焊(管子转动),主要用于可转动的直管子对接焊缝,另一种是全位置自动钨极氩弧焊(焊枪或机头围绕管子转动),主要用于焊接不可转动的弯管,这种焊接方法多采用程控脉冲电源。