湿法脱硫系统经济运行优化
烟气氨法脱硫运行中的主要问题及改进措施
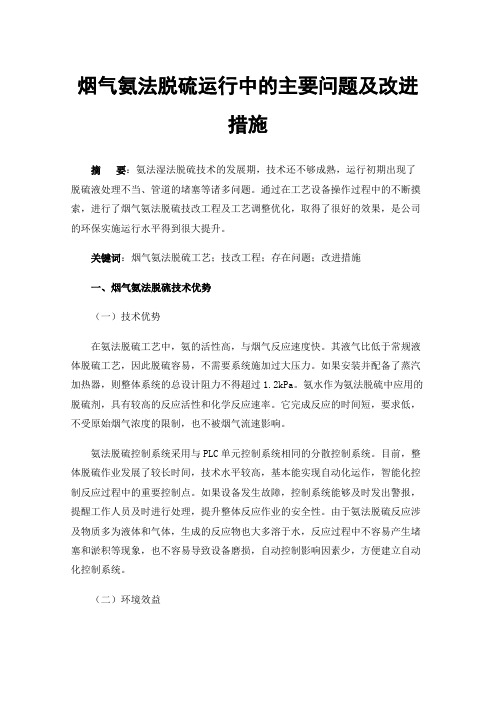
烟气氨法脱硫运行中的主要问题及改进措施摘要:氨法湿法脱硫技术的发展期,技术还不够成熟,运行初期出现了脱硫液处理不当、管道的堵塞等诸多问题。
通过在工艺设备操作过程中的不断摸索,进行了烟气氨法脱硫技改工程及工艺调整优化,取得了很好的效果,是公司的环保实施运行水平得到很大提升。
关键词:烟气氨法脱硫工艺;技改工程;存在问题;改进措施一、烟气氨法脱硫技术优势(一)技术优势在氨法脱硫工艺中,氨的活性高,与烟气反应速度快。
其液气比低于常规液体脱硫工艺,因此脱硫容易,不需要系统施加过大压力。
如果安装并配备了蒸汽加热器,则整体系统的总设计阻力不得超过1.2kPa。
氨水作为氨法脱硫中应用的脱硫剂,具有较高的反应活性和化学反应速率。
它完成反应的时间短,要求低,不受原始烟气浓度的限制,也不被烟气流速影响。
氨法脱硫控制系统采用与PLC单元控制系统相同的分散控制系统。
目前,整体脱硫作业发展了较长时间,技术水平较高,基本能实现自动化运作,智能化控制反应过程中的重要控制点。
如果设备发生故障,控制系统能够及时发出警报,提醒工作人员及时进行处理,提升整体反应作业的安全性。
由于氨法脱硫反应涉及物质多为液体和气体,生成的反应物也大多溶于水,反应过程中不容易产生堵塞和淤积等现象,也不容易导致设备磨损,自动控制影响因素少,方便建立自动化控制系统。
(二)环境效益目前我国全面强调环保工作的重要性,不论各个地区,环保部门已逐步提出按期完成锅炉烟气处理设备现代化改造的要求,能够确保极低的SO2排放。
氨法脱硫技术基本上不产生废气、废水和废渣,基本不会造成二次污染。
氨法脱硫最终废气排放量较低,也不生成二氧化碳气体。
如果二氧化硫质量浓度达到极低排放水平,即10~20mg/时,对大气污染较小,不存在二次污染现象。
氨法脱硫同时可以做到无废水排放,氨法脱硫产生的废水可返回脱硫塔作为工艺用水回收,基本不需要进行排放,减少对水资源浪费和污染二、烟气氨法脱硫技改工程建设存在的问题及改进措施(一)脱硫液的处理问题以及相应的改进措施当前各个工业企业所实际采用的锅炉烟气氨法脱硫技术主要是采用必要的脱硫液来在生产工作当中循环往复地实现针对烟气当中含有的二氧化硫气体进行吸收,一般情况下脱硫循环液当中含有的化学成分非常复杂,主要包括有灰尘、氯离子、硫酸铵以及亚硫酸铵等化学成分。
湿法脱硫存在的主要问题与技术探讨

湿法脱硫存在的主要问题与技术探讨摘要:经济的发展,城市化进程的加快,人们对电能的需求也逐渐增加。
在我国现代化建设阶段,燃煤电厂发挥着重要作用,也是国民经济的支柱性产业之一。
燃煤电厂的生产运作有效地满足了广大群体日常生活、生产中对电力的需求,对我国经济发展进步起到推动型作用。
燃煤发电阶段形成废水、废气等污染物,其中废水的类型较多,脱硫废水便是其中的典范。
化学沉淀是处理脱硫废水的常用方法,尽管其费用支出较少,但经该工艺处理后的污水,很难保证整体达标,污水内含盐量偏高,若未经处理直接排放很可能导致二次污染。
湿法脱硫废水零排放处理能解除如上问题,具有能耗低、环保等诸多优势。
本文就湿法脱硫存在的主要问题与技术展开探讨。
关键词:脱硫系统;问题;技术探讨;经验分享;经济运行;节能与减排引言随着环保形势的日益严格,以及《国务院关于印发水污染防治行动计划的通知》发布与执行,燃煤电厂脱硫废水零排放也成为关注重点。
脱硫废水零排放工艺是指将脱硫废水进行预处理后对废水进行采用蒸发、结晶等方法进行深度处理,达到废水零排放的目的。
1燃煤电厂脱硫废水的来源及特点在燃煤电厂,烟气污染物主要包括了二氧化硫、硫化物、氯化物、氟化物、重金属离子和烟尘等,为了防止硫化物的污染,要对含硫烟气进行脱硫处理。
按工艺特点目前主要可分湿法、半干法和干法3种烟气脱硫技术,中国烟气脱硫技术和其应用比例如图1所示,大部分燃煤电厂采用石灰石-石膏湿法脱硫工艺。
湿法脱硫工艺为避免系统内污染物富集,须排放一部分废水以维持系统内污染物浓度,这部分废水主要含有大量悬浮物、过饱和的亚硫酸盐、硫酸盐以及重金属等污染物。
脱硫废水水质特点及其可能危害影响见表1。
图1中国烟气脱硫技术与其应用占比表1脱硫废水水质特点及可能危害影响2湿法脱硫存在的主要问题某公司2×330MW机组采用石灰石-石膏湿法烟气脱硫装置,每台机组对应一座脱硫塔,烟气系统不设GGH和旁路烟道,增压风机与引风机合并设置,脱硫系统压降通过引风机克服,两台机组共用一座210m高内衬钛钢烟囱,每台机组脱硫设施原设计配置三台脱硫浆液循环泵,原脱硫设施设计脱硫出口二氧化硫排放浓度200mg/Nm3以下,为了进一步满足日益严格的污染物排放标准,2015年,通过对脱硫设施实施提效改造,目前,每座脱硫塔配置五台脱硫浆液循环泵,设计脱硫效率98.99%,在脱硫设施出口新增湿式除尘器,经过改造后,净烟气二氧化硫排放浓度达到35mg/Nm3以下,满足超低排放指标要求。
浅谈火电厂脱硫系统节能降耗的重要性及措施

浅谈火电厂脱硫系统节能降耗的重要性及措施随着环保意识的提升和能源结构的调整,火电厂脱硫系统的节能降耗已成为当前热门话题。
脱硫系统是火电厂环保设施的重要组成部分,其主要作用是将烟气中的二氧化硫去除,减少对大气环境的污染。
脱硫系统消耗大量能源,同时也会产生额外的成本,因此如何降低脱硫系统的能耗成为了当前火电厂重要的工作任务。
本文将从脱硫系统节能降耗的重要性和具体措施两个方面对此问题进行探讨。
1. 环保要求随着环保政策的日益严格,火电厂需要不断提升自身的环保设施,确保排放的废气达标。
而目前脱硫系统是火电厂实现大气污染物减排的重要手段之一。
脱硫系统的设备运转需要大量的电能和化学药剂,这就要求我们要不断寻求脱硫系统的节能降耗方案,以降低对环境的负面影响。
2. 能源效率火电厂是能源的生产和利用者,而脱硫系统的能耗直接影响着整个电厂的能源效率。
当前我国能源资源严重依赖进口,而且焚烧煤炭过程中排放的二氧化硫还会造成酸雨、大气污染等问题,因此提升火电厂脱硫系统的能源利用效率对于整个能源体系的平衡和可持续发展至关重要。
3. 经济效益脱硫系统的运行成本主要包括化学药剂和电能消耗,而如何合理降低这些成本对于电厂的经济效益至关重要。
若能有效地节约这些成本,既能降低企业的生产成本,还能提升企业的竞争力。
以上三个方面说明了火电厂脱硫系统节能降耗的重要性。
下面我们将从具体措施来解决这个问题。
二、火电厂脱硫系统节能降耗的具体措施1. 先进脱硫技术火电厂脱硫系统的技术更新对于节能降耗至关重要。
目前,一些国内外先进的脱硫设备已经应用在一些电厂,如石灰石湿法脱硫技术、燃料气脱硫技术等。
这些技术不仅可以提高脱硫效率,还可以降低化学药剂的使用量,从而减少了脱硫设备的运行成本。
2. 合理的脱硫系统工艺设计脱硫系统的工艺设计对于节能降耗也起着至关重要的作用。
特别是在设备的选型和运行参数的确定上,需要充分考虑到设备的能源消耗情况。
通过合理的工艺设计来提高设备的利用率,减少能源消耗。
湿法脱硫pH计安装方式的优化改进

粒度 较大 , 而且 极易 结 垢 , p 电极 冲刷 、 损 很 对 H 磨 严重 。部分脱 硫 项 目投 运 后 , H 计 在 测 量 方 面 出 p
燃煤电厂各种干法半干法湿法脱硫技术及优缺点汇总

燃煤电厂各种干法、半干法、湿法脱硫技术及优缺点汇总目前,湿法烟气脱硫技术最为成熟,已得到大规模工业化应用,但由于投资成本高还需对工艺和设备开展优化;干法烟气脱硫技术不存在腐蚀和结露等问题,但脱硫率远低于湿法脱硫技术,一般单想电厂都不会选用,须进一步开发基于新脱硫原理的干法脱硫工艺;半干法脱硫技术脱硫率高,但不适合大容量燃烧设备。
不同的工况选择最符合的脱硫方法才会得到最大的经济效益,接下来根据电厂脱硫技术的选择原则来分析各种工艺的优缺点、适用条件。
电厂脱硫技术的选择原则:1、脱硫技术相对成熟,脱硫效率高,能到达环保控制要求,已经得到推广与应用。
2、脱硫成本比较经济合理,包括前期投资和后期运营。
3、脱硫所产生的副产品是否好处理,最好不造成二次污染,或者具有可回收利用价值。
4、对发电燃煤煤质不受影响,及对硫含量适用范围广。
5、脱硫剂的能够长期的供给,且价格要低廉一、干法脱硫干法脱硫工艺工艺用于电厂烟气脱硫始于20世纪80年代初。
传统的干法脱硫工艺主要有干法喷钙脱硫工艺、荷电干法吸收剂喷射脱硫法、电子束照射法、吸附法等。
传统的干法脱硫技术有工艺简单投资少,设备简占地面积小且不存在腐蚀和结露,副产品是固态无二次污染等优点,在缺水地区优势明显。
但是脱硫效率很低,一般脱硫效率只能到达70%左右,难以满足排放要求。
干法喷钙脱硫工艺工艺介绍磨细的石灰石粉通过气力方式喷人锅炉炉膛中温度为900〜1250。
C的区域在炉内发生的化学反应包括石灰石的分解和煨烧,S02和SO3与生成的Cao之间的反应。
颗粒状的反应产物与飞灰的混合物被烟气流带人活化塔中;剩余的CaO与水反应,在活化塔内生成Ca(OH)2,而Ca(OH)2很快与S02反应生成CaSo3,其中部分CaSO3被氧化成CaSo4;脱硫产物呈干粉状,大部分与飞灰一起被电除尘器收集下来,其余的从活化塔底部分离出来从电除尘器和活化塔底部收集到的部分飞灰通过再循环返回活化塔中。
优化运行降低湿法烟气脱硫石膏水份

气 液 分 离 灌到 真空 泵 的 管 道 内衬 板 进行 更 换, 防止 管 道 内衬 板 脱 落 , 致 管 道 结垢 堵 导 塞 。4 采用 程 控 冲 洗法 , () 同时 对 冲洗 孔 加 强 检查 , 持 一 定 冲洗 水 量 , 止 滤 布 孔径 被 维 防
杂质堵塞 。 3. 优 化 真空 脱水 皮带 机运 行方 式 2 ( ) 节 石 膏 浆 液 泵 压 力 , 制 进 入 旋 1调 控
iI : 1 . 。 il i l . 。 。 。 I : 。 。 。 . 。 。。
工 业 技 术
优 化 运行 降低 湿 法 烟气 脱 硫 石 膏 水 份 ①
朱 文彬 (. 1 上海 理工大学 上海 2 0 9 ; 2 上海外 高桥 发 电有 限责任 公司 上 海 2 0 7 00 3 . 01 ) 3 摘 要 : 电厂如采 用石灰石一 石膏涅法烟 气脱硫 , 么谈脱硫 工艺产生 的副产品是石膏 。 火 那 评价石 膏品质的好坏主 要有三个 因素, 即石膏 纯度 . 石膏含水 率及 石膏含氯 卒 。 文兢如何 降低 脱硫 石 膏含 水率提 高石膏品 质进行 分析探讨 , 本 使脱硫 石 膏能够被 综合 利用 。 符合 国 既 家发展 循环 经济 的 原则 。 利于保 护 生态环 境 。 又 关 键词 : 脱硫 石膏 石膏品质 真空皮带机 中 图分 类号 : U T 7 文 献标 识码 : A 文章 编 号 : 6 4 0 8 ( 0 0 0 () 0 7 - 1 1 7 - 9 X 2 1 ) 7c- 0 4 0
真 空 箱 、 布 、 涤 装 置 、 动 滚 筒 和 自动 滤 洗 驱 纠偏 装 置 构 成 。 经过 初 级 脱 水 的 石 膏浆 液 ; 至 滤布 上 , 成 固定 厚度 的一 层 浆 液 , f 形 以 保 证 参 数 恒 定 和 脱 水 性 能稳 定 。 布 铺 敷 滤 橡胶皮带上, 由其 拖 动 同 步运 行 。 胶 皮 带 橡 下 面 即是 真 空 箱 , 空箱 与 真 空 泵 相 连 , 真 因 此 箱 内始 终 保 持 一 定 的真 空 度 , 胶 带 上 在 形 成 抽滤 区 。 真 空 的抽 吸作 用 下 , 在 滤液 穿 过滤 布 经橡 胶 带 上 的 沟 槽 和 小 孔进 入 真 空 室, 固体 颗 粒 则 被 截 留在 滤 布 上 , 成一 层 形 滤 饼 。 空 箱 内 的 滤 液 继 续 流 动进 入 汽 水 真 分 离 器 排 出 , 滤饼 继 续 随 滤 布 前 行 至 洗 而 涤区 , 到新 鲜 工 艺 水 冲 洗 , 使氯 离 子 含 受 以 量 达 到 要 求 的 水 平 。 经 吸 干 区抽 吸水 分 再 达 到 工 艺 要 求 后 , 滤 布 平 台 尽 头 处 自动 在 卸出 , 降落 至 下 方 的 石 膏 储 仓 , 然后 进 行 综 合利用 。 2. 通 过对 外高 桥 电厂 真空 脱水 皮 带机 现 2
【2024版】脱硫系统运行规程

可编辑修改精选全文完整版13、锅炉脱硫装置 (107)13.1第一章脱硫系统工艺介绍 (107)13.2第二章系统各单体设备维护及操作规程 (115)13.3、第三章 FGD系统启动、运行和停运操作程序 (125)附录一饱和压力(绝对压力)与饱和温度对照表 (137)14、锅炉系统图14.1、图一锅炉脱硫系统图14.3、图三:锅炉脱销系统图13、锅炉脱硫装置13.1 第一章脱硫系统工艺介绍13.1.1 系统简介脱硫采用石灰石-石膏湿法脱硫工艺,按照两炉一塔方式建设脱硫装置,两塔共用一套系统。
整套脱硫装置由七大系统组成:烟气系统、脱硫塔系统、石灰石粉储存和浆液制备系统、脱硫产物脱水系统、工艺水系统、电气系统和自动控制系统。
13.1.2主要工艺技术指标13.1.3工艺原理石灰石-石膏湿法脱硫工艺是碳酸钙与水反应生成氢氧化钙,再与二氧化硫溶于水生成的亚硫酸溶液进行酸碱中和反应,生成亚硫酸钙和硫酸钙,亚硫酸钙再氧化后生成硫酸钙。
脱硫过程中发生的主要化学反应有:CaCO3+H2O=Ca (OH)2+CO22Ca (OH)2+3SO2=CaSO3+ Ca (HSO3)2+H2OCa (HSO3)2+1/2O2= CaSO3+H2OCaSO3 +1/2O2=CaSO4由于石灰石-石膏湿法脱硫的反应产物是硫酸钙,结晶产物CaSO4·2 H2O,俗称石膏,经脱水系统进行处理后,产物为含水率相对较低的石膏进行外运处理。
13.1.4工艺流程锅炉产生的烟气,经过除尘器去除大部分烟尘后,从引风机出来经进口烟道进入脱硫塔。
烟气经喷淋、吸收SO2等酸性气体并脱水除雾后,通过与脱硫塔连接的出口烟道连接至烟囱排入大气。
脱硫塔底部的脱硫液经抽出泵打至板框压滤机进行脱水处理,经脱水后的脱硫渣进行外运处理,滤液进入厂区污水管网。
外购石灰石粉经罐车打入粉仓内储存,使用时经螺旋给料机卸出,进入浆液罐内与加入的工艺水混合成一定密度的石灰石浆液,使用时经石灰石浆液输送泵输送到脱硫塔内使用。
「半干式反应塔喷雾干燥脱硫法及优化设计」

「半干式反应塔喷雾干燥脱硫法及优化设计」半干式反应塔喷雾干燥脱硫法是一种联合利用湿法和干法的脱硫技术。
在半干式反应塔中,烟气与喷雾剂(通常是石灰石浆或石膏浆)接触,在反应塔内进行化学反应和质量传递,从而实现脱硫的目的。
该技术具有占地面积小、设备投资低、脱硫效率高等优点。
在半干式反应塔中,主要的工艺参数包括石灰石浆或石膏浆的浓度、烟气进口温度、喷雾剂喷雾速率、反应塔高度等。
对于不同的燃煤电厂和工业锅炉,这些参数可能会有所不同。
因此,针对具体的工艺条件和运行要求,进行优化设计是非常重要的。
首先,针对石灰石浆或石膏浆的浓度,应在一定范围内进行选择。
过低的浓度会导致脱硫效率低下,而过高的浓度则会增加喷雾剂的使用量和能耗。
因此,根据燃煤电厂或工业锅炉的实际情况,选择合适的浓度是必要的。
其次,烟气进口温度对脱硫效果会产生一定的影响。
在太低的烟气进口温度下,石灰石浆或石膏浆的蒸发速率会较慢,脱硫效率也会降低。
因此,适当提高烟气进口温度,可以提高脱硫效率。
然而,过高的烟气进口温度可能会导致脱硫剂的过量使用,增加运行成本。
因此,需要进行综合考虑和优化设计。
此外,喷雾剂的喷雾速率和反应塔的高度也是影响脱硫效果的重要参数。
适当增加喷雾剂的喷雾速率和反应塔的高度,可以增加烟气与喷雾剂的接触时间,提高脱硫效率。
然而,过高的喷雾速率和反应塔的高度可能会导致能耗增加。
因此,在设计中需要进行合理的优化,以实现最佳的经济效益和环保效果。
除了以上的工艺参数,还需要对反应塔的结构和内部组件进行优化设计。
例如,合理设计反应塔的内部分隔板和喷头,可以增加烟气与喷雾剂的接触面积,提高脱硫效率。
此外,还需要考虑喷雾剂的循环系统、脱硫废液的处理等方面的问题。
综上所述,半干式反应塔喷雾干燥脱硫法是一种有效的脱硫技术,可以广泛应用于燃煤电厂和工业锅炉。
通过合理选择和优化设计工艺参数,可以提高脱硫效率,降低运行成本,并达到环保要求。
因此,在实际应用中,需要综合考虑工艺条件、运行要求和经济环保效益,进行合理的优化设计。
- 1、下载文档前请自行甄别文档内容的完整性,平台不提供额外的编辑、内容补充、找答案等附加服务。
- 2、"仅部分预览"的文档,不可在线预览部分如存在完整性等问题,可反馈申请退款(可完整预览的文档不适用该条件!)。
- 3、如文档侵犯您的权益,请联系客服反馈,我们会尽快为您处理(人工客服工作时间:9:00-18:30)。
——?竺竺【!!!!!!m“!!!竺!!!!!型竖!!!!坚・!塑湿法脱硫系统经济运行优化孙正杰.邵炜国电浙江北仑第一发电有限岱司.浙江宁波310007
摘要“M№单nso相对成奉最十*m*目#,at目革《*#iAmR机、《&培pHⅡ等m"t”**m女.*到最*∞FGDtni式.井∞“女#.取群T"Ⅱ∞&##&关键月:FGD:∞*,E单镕质iSO,,相畸±P成^
1概进随着囤家对环保T1f1=的n益重视,环境标准也n益提高.对f火电J的俐气脱琉装置fH,D)I徘电提出r生商的要求。火电rFGI)的建设.不仪需要大址的投资赞用.而且装置投^使用后迁需霹大碹的4行维护费用姑估算.在湿法FGDi行维护费儿j中电费和石藏石柑费用r々到总4行费朋的50rd-左j】在妻际运行・h由于机组负荷燃烧煤种的变化.必然需要调整相应的mD运行方矗米确保脱硫嫂率选刮要求,因此如何在确保H保排放选标的情乱下,确定最优的运行t况.成为FGD运{』优化的盖键
2北仑电厂FGD系统简介北仑电厂5x
600MW机组的烟气脱疏上程拄单兀制
设1i.采崩一炉一塔、塔内强制氧化的石灰石一石膏湿法脱硫T艺其副产品为石膏,其系统}监由石灰右柑磨制辖遗系统、石灰石浆液制备系统、炯气系统吸收塔系统T岂水系统亓膏脱水系统浆液疏排系统废水处理系统驶压缩空气系坑等组成工岂流程如图1所Ⅲ,锅炉烟气从引风机后烟道引出通过增Ⅱ风机升压冉进^气一气换热器(I,(m)降温后进人吸收塔.在吸收塔内脱硫净化.净烟气经除雾器除去水雾后.再经气一气换热器(GGH)加热升盟,进人旁龉托板后的蝤道从原有烟囱巾排人大气:进^吸收塔的石灰石浆液与自下m】L的含有sn的圳气混台后反应生成再膏浆液.m石膏排出采
t’I瓤亭‘hi。’1F.魏。卜“≯
琶。。l垂。
3脱单位髓量SO:相对生产成本概念FGD装置的各项远行成本包括脱琉装置的运{r消耗性贽用(电费,柬赞脱硫剂费用)设备修理费用.折日赞其他综合费川等。其巾设备修理赞用折…赞综合管理费不受脱硫工况的影响水费受脱疏T况的影响很小.在计算中可不予考虑。此外,FGD的投运状况还会影响刊SO,的排污撤费.另由十石膏销售收^的不确定性(女II,V能销售m去,迁需璺增加处置成本).也不f-芎睡。为r堕好的展开FGD的优化研究.特提出脱单位质毋Sf),相对生产成本(K)慨念,此数据直接的反映除脱豫单位SO,所需要的相对生产啦本。、,^2“
1‘iI,1+I,.1,3
112009年全国电力行业脱硫脱硝技术协作网年会暨脱硫脱硝企业CEO论坛论文集式中:鼻,.一脱除单位质量sO:的相对生产成本,元/l【g胁一相对生产成本Q—SO:脱除量肘厂FGD系统电费尬一FGD脱硫剂费用肘厂FGD投运后减少的so:排污费用显然,对发电企业来说,K参数越小,则运行工况越经济。从整个电厂角度来考虑。在发电量一定的情况下,特定的煤炭燃烧产生的SO:总量是一定的,它不会随着锅炉运行工况的变化而变化。因此如果能够减小参数K,则对发电企业来说,就节省了成本。减小K的途径,主要是有二种:降低粉耗与电耗。FGD系统中功率最大的设备主要有增压风机、浆液循环泵、氧化风机等,其电耗占到整个FGD系统电耗的85%以上,因此减少电能的损耗应从以上设备入手研究;而系统的粉耗则需要从浆液pH值着手研究。因此优化方法从以下几点人手:浆液循环泵的优化;氧化风机的优化;pH值控制系统的优化;优化的方法主要是在理论基础上,通过试验比较并结合定量分析,得到最优的运行方式。4浆液循环泵的运行优化北仑电厂配置3台浆液循环泵,按设计要求FGD运行时三台泵运行,无备用。在实际运行中,当FGD的S02质量流量较低时,脱硫效率很高,此时可以考虑停运一台浆液循环泵来达到的减小K的目的。试验以参数K的大小为指导依据,通过比较试验,找到较优的浆液循环泵的运行方式;在此基础上,找到一个合适的Q舯值,确定当FGD的SO:负荷低于Q旆时,通过停运一台浆液循环泵来实现浆液循环泵的最经济运行。4.1试验方案本试验时锅炉燃煤含硫量均值为1.24%,SO:质量浓度平均值为2850mg/m3(标干态,75%机组负荷下);试验方案在3种不同机组负荷下(350WM、400MW,450MW),进行运行三台浆液循环泵与运行二台浆液循环泵的比较试验(停运的浆液循环泵均为lA)。在试验时,吸收塔控制pH值在5.3左右,吸收塔水位控制在8.2米,石灰石供浆浓度控制在1250咖,。氧化风机2台运行。
经济指标计算依据如下:电价按上网电价计算:0.39元/度;石灰石粉价格250元,吨;石灰石纯度95%;Ca/S比1.03;脱硫装置年运行6000小时;在燃烧该煤种时标准状态下SO:浓度在2770Nmg/m3—2973Nmg/m3之间波动;排污费用:0.63元/l【gS02。
4.2试验数据试验数据如下,表格1为试验时采集的数据值,表格2
表1浆液循环泵比较试验主要数据工况机组负荷MW质量流量k加脱硫效率%出口S02浓度mg/m3浆液循环泵A、B、C电流(A)备注l450470094.6156137.5、147.2、166循泵A、B、C运行2450469788.06356149.9、165.9循泵B、C运行3400413695.4126134、147、165
循泵A、B、C运行
4400413789.6296148.6、166.2循泵B、C运行5350355896.9964135、147.2、165.5循泵A、B、C运行
6350355793.37180151.2、165.6循泵B、C运行
表2浆液循环泵比较试验各工况主要经济指标工况电贡(刀兀)石灰石费用(刀兀)排污费用(力兀)相对成本【力兀)S0:脱除量(吨)K(元每千克)l1477.741129.81680.2926.5266770.34721338.881051.041563.47826.924817.10.33331367.71002.651491.15878.823674.50.37141232.75941.921401.15773.622240.50.34851337.12876.631304.07909.720699.6l0.43961193.44844.181255.76781.9
19932.630.392
122009年全国电力行业脱硫脱硝技术协作网年会暨脱硫脱硝企业CEO论坛论文集为在此工况下折合成的年经济指标。4.3试验结果分析分析试验结果。我们可以得到如下结论:1.从各项成本的构成看,电费占整个FGD的费用指出中约60%。石灰石消耗费用约占40%,减少的排污费用数量也很可观,减少的费用要比电费开支还要大;2.从表中可以看出,工况l与丁况2的差值为0.014,工况3与工况4的差值为0.023,工况5与工况6的差值为0.047.显然随着机组负荷的减小,的差值越来越大,这表明,负荷越低,通过停运一台浆液循环泵的经济效益越明显。3.从本次试验中,工况6时,停运一台浆液循环泵后效率还达到93.37%,因此值的选取可以考虑在3558k加左右,但是具体的值还要根据实际的运行情况来确定。4.4浆液循环泵优化运行方案的制定通过上述试验分析,并考虑到实际运行过程中检修、电动机启动频率的要求等各种因素,制定如下浆液循环泵的优化运行方案:原烟气So:浓度2100Ing/Nm3以下,机组负荷在450MW以下,并预计该负荷下连续运行8小时以上;原烟气S02浓度2100mg/Nm3~2400mg/Nm3之间,机组负荷在400MW以下,并预计该负荷下连续运行8小时以上;原烟气S02浓度2400mg/Nm3—2750mg/Nm3之间,机组负荷在350MW以下,并预计该负荷下连续运行8小时以上。当机组在以上三种工况下运行时,FGD撤出一台浆液循环泵运行。如果机组运行工况超出以上三个范围,且脱硫效率小于90%.启动停运的浆液循环泵。5氧化风机运行优化FGD装置配置了三台氧化风机(2运1备),提供氧化反应所需要的氧化空气。氧化风过多,浪费电能;反之,必然会引起氧化反应不够充分,脱硫效率下降等问题。因此氧化风的投运数量应与FGD的SO:质量流量的变化而来变化。下面采用理论计算与实际相结合的方式,找到最优的运行氧化风机方式,来保证FGD氧化风的合理供给。5.1氧化风量的设计要求FGD的脱硫氧化风机的容量为90.8Nm3/min(1atm、O℃)。一般情况下.为保证氧化反应的完全进行。脱硫系统氧化风的氧量与SO:中s的O/S要控制在2.0—2.5之间。在设计工况下(0.99%硫份:入口二氧化硫浓度G萨2135mgfNm3,烟气量G=2099139Nm3/h)二氧化硫负荷为:Qs。2=‰×C--4482(kg/h)--4482(kg/h)/64(mg/m01)=70(kmol/h)
当O/S=2时:需要0:=70×2/2=70(kmol/h)=70×22.4(1_/m01)/60=26.1(Nm3/min)需要空气=26.1/21%=124.3(Nm3/min)当O/S=2.5时:需要02=70×2.5/2=87.5(kmol/h)=87.5×22.4/60=32.7(Nm3/min)需要空气=32.7/21%=155.7(Nm3/min)显然在设计负荷下,不管是OIS=2还是O/S=2.5,都需要运行2台氧化风机。按照上述方法.我们可以算出运行一台氧化风机与运行二台氧化风机的SO:质量流量。如果运行一台氧化风机,S02负荷范围:2615kgha一3268.8k:rCh如果运行2台氧化风机.SO:负荷范围:5230.1kg/h一6537.6kg,ll。如果sO:负荷超出6537.6k:g/}l,则需要运行三台氧化风机。5.2氧化风机优化运行试验下面通过试验来验证理论是否符合实际情况,试验时FGD入ElSO:质量浓度平均值为2850mg/m3(标干态,75%机组负荷下);试验方案在2种不同机组负荷下(350WM、400MW)进行运行2台氧化风机与运行l台氧化风机的比较试验。在进行氧化风机试验时,对石膏进行化验,没有发现石膏品质异常,因此Ca/S也按照1.03计算。其余运行工况与经济指标计算依据与浆液循环泵一致。试验数据如下,表3为试验时采集的数据值,表4为在此工况下折合成的年经济指标(表3、表4见下页)。5.3试验结果分析根据试验结果,分析如下:1.按照理论计算,工况l、2需要运行2台氧化风机,工况3、4需要运行1台氧化风机,显然在实际运行中,与理论一致的运行方式的经济性要高。2.与浆液循环泵的试验相比较。通过调整氧化风机运行方式所取得的经济效益要小的多.这主要是因为氧化风
13