催化裂化吸收稳定系统 ppt课件
催化裂化工艺流程
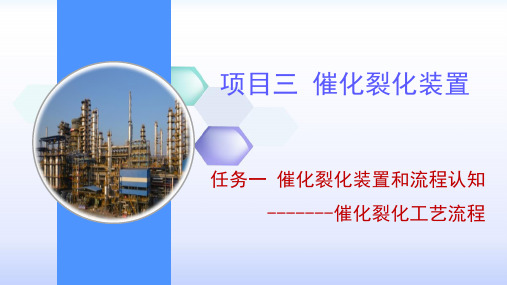
任务布置
1.绘制重油催化裂化工艺原则流程图。 2.口头复述工艺流程。
注意事项: 1.催化裂化设备的简要画法。 2.催化裂化装置一般几部分构成?
知识拓展
催化裂化的发展历程 催化裂化自1936年实现工业化至今经历了四个阶段: 固定床、移动床、流化床和提升管。
Fixed Bed
Moving Bed
Fluid Bed
同学们上节课已经学习了催化裂化原料、产品、化学反应及 催化剂。 检查同学们掌握的情况: 1、催化裂化的主要化学反应有哪些? 2、催化裂化催化剂的组成是什么?
提出问题
催化裂化反应及产品分离是通过什么工艺实现的?催 化剂是如何参与反应并再生的?
催化裂化
催化裂化工艺流程框图
图2-1 催化裂化生产工艺方框流程图
此流程是如何实现?
催化裂化工艺原则流程图
图2-2 重油催化裂化工艺原则流程图 1 原料加热炉 2 提升管反应器 3 沉降器 4 再生器 5 辅助燃烧室 6 外取热器 7 分馏塔 9 油气分离器 10 柴油汽提塔 11 气压机 12 吸收塔 13 气压机出口油气分离器 14 解吸塔 15 再吸收塔 16 稳定塔 17 稳定塔回流罐 18 液化气碱洗罐
任务布置
1.绘制重油催化裂化工艺原则流程图。 2.口头复述工艺流程。
注意事项: 1.催化裂化设备的简要画法。 2.催化裂化装置一般几部分构成?
知识拓展
催化裂化的发展历程 催化裂化自1936年实现工业化至今经历了四个阶段: 固定床、移动床、流化床和提升管。
Fixed Bed
Moving Bed
Fluid Bed
图22重油催化裂化工艺原则流程图油气分离器10柴油汽提塔11气压机12吸收塔13气压机出口油气分离器14解吸塔15再吸收塔16稳定塔17稳定塔回流罐18液化气碱洗罐催化裂化工艺原则流程图任务布置任务布置1
催化裂化
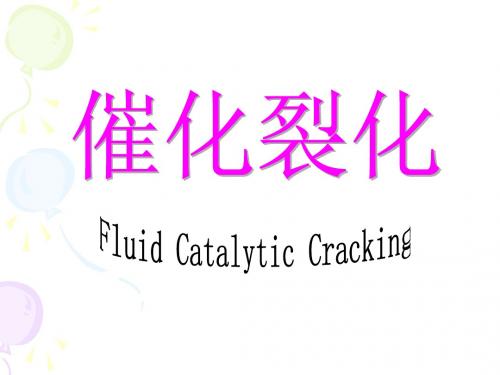
胜利
0.23 0.29 <0.02 0.2~0.4 4.7 8.5 4.8 39.2
2.以重油为裂化原料时会遇到以下技术困难: ①焦炭产率高 原因是:
重油的H/C比较低,含稠环芳烃多,胶质沥青质含量高;
重金属污染催化剂 引起一系列的问题,主要有: 再生器烧焦负荷大 焦炭产率过高,会大大破坏装置的热平衡 装置能耗增大
5~10
6~8
二:催化裂化的发展过程
分解等反应生成气体、汽油等小分子产物
催化裂化反应
缩合反应生成焦炭
反应:吸热过程
催化裂化 再生:放热过程
催化裂化的发展可以分成以下几个阶段:
1.天然白土和固定床催化裂化 2.合成硅铝催化剂和移动床催化裂化
①移动床催化裂化
②流化床催化裂化
3.分子筛催化剂和提升管催化裂化
次反应
二次反应并非对我 们的生产都有利,应 适当加以控制
为了获得较高轻质油收率,不追求反应深度过大,而是在
适当反应深度的基础上对未反应原料进行回炼 “未反应原料”是指反应产物中沸点范围与原料相当的那 一部分,称回炼油或循环油 目前我国的催化裂化装置采用的反应温度一般比国外低
三:渣油催化裂化
芳香基原料油、催化裂化循环油或油浆(其中含有较多的稠
环芳烃)较难裂化,要选择合适的反应条件或者先通过预处理
来减少其中的稠环芳烃而使其成为优质的裂化原料,如循环 油可作如下处理: 加氢→含环烷烃较多→优质裂化原料 溶剂抽提分理出芳烃(化工原料)→裂化
2.复杂的平行—顺序反应
重质石油馏分
中间馏分
烷烃
烯烃
①反应速度比烷烃快得多; ②氢转移显著,产物中烯烃、尤其 是二烯烃较少。
①反应速度与异构烷烃相似; ②氢转移显著,同时生成芳烃。 ①反应速度比烷烃快得多; ②在烷基侧链与苯环连接的键上断 裂。
催化裂化装置课件
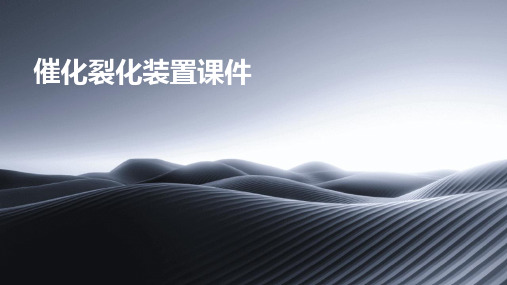
阐述液体产物精制的原理及方法,包括蒸馏、萃取、 吸附和离子交换等。
04
催化裂化装置的维护与保养
日常维护
01
02
03
每日检查
检查装置的外观、紧固件 、连接部位等是否正常, 确保无泄漏、无特殊声响 和振动。
温度和压力监控
定期检查装置的温度和压 力是否在正常范围内,并 记录数据,以便及时发现 特殊情况。
02
03
04
严格遵守操作规程
操作人员必须经过专业培训, 熟悉装置的操作流程和安全规
范。
定期检查和维护
对装置进行定期检查,及时发 现和处理潜伏的安全隐患。
危险品管理
对装置涉及的危险品进行严格 管理,确保储存和使用安全。
应急预案
制定完善的事故应急预案,提 高应对突发事件的快速响应能
力。
事故应急处理
火灾应急处理
THANKS
感谢观看
原料的干燥与脱硫脱氮
介绍原料的种类、性质和来源,说明 原料对催化裂化过程的影响。
阐述原料在进入反应器前进行干燥和 脱硫脱氮的原理及方法。
原料的预热与混合
说明原料在进入反应器前的预热和混 合的必要性,以及预热和混合的方法 。
反应过程
01
反应原理
详细介绍催化裂化反应的原理, 包括反应机理、反应条件和影响 因素。
催化裂化装置的应用
催化裂化装置广泛应用于石油化工行业,是炼油厂的重要加工装置之一 。
它主要用于处理重质石油原料,如减压馏分油、脱油沥青等,将其转化 为高价值的轻质产品。
通过催化裂化装置的处理,可以提高石油产品的质量和产量,满足市场 需求。同时,催化裂化技术也在不断发展和改进,以提高生产效率和环 保性能。
催化裂化

再生器的主要作用是烧去催化剂上因反应而生成的积炭, 使催化剂的活性得以恢复。再生用空气由主风机供给,空气通 过再生器下面的辅助燃烧室及分布管进人流化床层。 催化剂(称再生催化剂)落人淹流管,经再生斜管送回反应器 循环使用。再生烟气经旋风分离器分离出夹带的催化剂后,经双 动滑阀排人大气。 再生烟气的温度很高,不少催化裂化装置设有烟气能量回收 系统,利用烟气的热能和压力能(当设能量回收系统时,再生器的 操作压力应较高些)做功,驱动主风机以节约电能,甚至可对外输 出剩余电力。对一些不完全再生的装置,再生烟气中含有5%-10% (体积分数)的CO,可以设CO锅炉使CO完全燃烧以回收能量。
工艺流程概述
包括:反应-再生系统、分馏系统、吸收-稳定系 统、再生烟气的能量回收系统和液化气、汽油的 脱硫精制等 1.反应—再生系统
高低并列式提升管催化裂化装置的工艺流程
470~510 ℃
3 ~4s
650~700 ℃
300~380 ℃
新鲜原料油经换热后与回炼油浆混合,经加热 炉加热后至催化裂化提升管反应器下部的喷嘴,原 料油由蒸气雾化并喷入提升管内,在其中与来自再 生器的高温催化剂接触,随即汽化并进行反应。
进入分馏塔的油气含有相当大量的不凝气和惰性气
体,它们会影响塔顶冷凝冷却器的效果 提高富气压缩机的入口压力以降低气压机的功率损
耗
3.吸收—稳定系统
主要由吸收塔、解吸塔、再吸收塔及稳定塔组成。
催化裂化

旋风分离器
粗旋 单旋 三旋
目录
催化裂化的工艺流程
催化裂化的重要设备 催化裂化的重要控制点
催化裂化的关键控制
反应温度控制: 催化裂化工艺中,反应器温度一般是通过调节再生滑 阀(塞阀)开度来改变再生催化剂循环量,达到控制 温度的目的。需要关注的问题主要有: 反应温度取样点的选择 再生滑阀的低压差限保护
正常生产中再生压力由烟机入口蝶阀的开度来控 制,在保证再生压力的前提下,烟气尽可能全部通过 烟机回收能量,双动滑阀旁路配合烟机入口蝶阀共同 完成再生压力的控制。需关注的事项有: 烟机的保护与再生压力的控制紧密相连,避免烟机的 超速或工作在临界状态。 两器差压的控制选择。
催化裂化的关键控制
其他重要控制回路: 分馏塔底液位与温度的控制
催化裂化的关键控制
反应压力的控制 : 反应压力是通过控制催化分馏塔顶压力来实现, 即调节富气压缩机入口压力,通过改变压缩机蒸汽透 平流量,改变压缩机转速。同时配合入口反飞动阀、 入口放火炬阀、分馏塔顶油气蝶阀等,形成了完整的 机组-反应压力的正常生产、开停工控制系统。控制 方案做到: 在较高的机组入口压力下平稳操作,达到降低能耗目 的。 机组的安全运行,避免喘振现象的出现以及事故状态 下的机组保护。
分馏塔顶温度控制
分馏塔顶油气分离器液位 吸收稳定装置富气凝缩油罐液位和界位的控制
机组控制
主风机 气压机 烟机
机组控制 机组的防喘振控制 喘振线 压 缩 比 喘振 区 操作线 Qg 入口流量
在反应过程中与催化剂接触,生成焦炭沉积在催化剂上, 催化剂因而失活,催化剂可在再生器内用空气烧掉焦炭,
回复活性。这样催化剂就形成了反应-失活-再生-反应
第九章_催化裂化

R
R + CH2=C-CHCH2CH2CH3
R + CH2=C-CH2CH2CH2CH3+ R'
C-H键的断裂则会逐步脱氢形成芳烃
R + R R + R R + R R
环己烷在催化裂化时约有25%转化成苯,气
体中氢气的含量比烷烃裂化时要多。
六员环还会异构化成为五员环烷,其反应很 可能是通过质子化环丙烷中间物进行的。
化在反应历程上是有相当的差别的。
2、烯烃
由于催化裂化原料基本不含有烯烃,所以烯烃
的反应基本上属于二次反应。烯烃的催化裂化反应
与其热裂化反应差别很大,烯烃很容易形成正碳离
子,因此它的催化裂化反应比同碳数的正构烷烃要
快2~3个数量级。
(1)裂化反应
烯烃的催化裂化反应速率比同碳数的烷烃快2-3 个数量级,而产物分布与烷烃相似。
产品的加工过程。
催化裂化的原料:
最初是减压馏分油(VGO)。
近年来以常压渣油和减压渣油脱沥青油为 原料的重油催化裂化工艺(简称RFCC)发 展较快。
催化裂化的产物: 气体:产率10~20%,主要是C3和C4,
其中烯烃含量可达50%以上。
汽油:产率30~60%,其RON约为80~ 90,安定性较好。 柴油:产率0~40%,由于含较多的芳 烃,十六烷值较低,安定性较差。 焦炭:产率5~10%,沉积在催化剂表面。
子而形成环烷烃,也可以失去质子而形成环烯烃,
环烯烃进一步脱氢可形成芳烃。
3、环烷烃
环烷烃的催化裂化反应速度与异构烷烃相似,
基本是上环断裂生成烯烃和二烯烃,脱氢生成
催化裂化讲义

第一节 催化裂化化学反应原理
▪ 一、单体烃催化裂化的化学反应 ▪ (一)烷烃
▪ 烷烃主要发生分解反应,分解成较小分子的烷烃和烯烃, 烷烃分解时多从中间的C—C键处断裂,分子越大越容易 断裂
▪ (二)烯烃
▪ 烯烃的主要反应也是分解反应,但还有一些其它重要反应, 主要反应有:
(二)三阀
▪ 1.单动滑阀
单动滑阀用于床层反应器催化裂化和高低并列式提升管催化裂化装置。 其作用是:正常操作时用来调节催化剂在两器间的循环量,出现重大事 故时用以切断再生器与反应沉降器之间的联系,以防造成更大事故。
▪ 2.双动滑阀
双动滑阀是一种两块阀板双向动作的超灵敏调节阀,安装 在再生器出口管线上(烟囱),其作用是调节再生器的压 力,使之与反应沉降器保持一定的压差。
径或筛分组成。工业用微球催化剂颗粒直径一般在20~80之间。 ▪ 我国用磨损指数来评价微球催化剂的机械强度 ▪ (六)密度 ▪ 1.真实密度:颗粒的质量与骨架实体所占体积之比 ▪ 2.颗粒密度:把微孔体积计算在内的单个颗粒的密度 ▪ 3.堆积密度 :催化剂堆积时包括微孔体积和颗粒间的孔隙体积的密
度
三、裂化催化剂的失活与再生
▪ 综合上述两个排列顺序可知,芳烃虽然吸附能力强,但反应能力弱,使 整个石油馏分的反应速度变慢 ;对于烷烃,虽然反应速度快,但吸附 能力弱,从而对原料反应的总效应不利。富含环烷烃的石油馏分应是催 化裂化的理想原料
(二)石油馏分的催化裂化反应是复杂的平 行—顺序反应
▪ 石油馏分进行催化裂化反应时,原料向几个方向进行反应, 中间产物又可继续反应,从反应工程观点来看,这种反应 属于平行—顺序反应。原料油可直接裂化为汽油或气体, 属于一次反应,汽油又可进一步裂化生成气体,这就是二 次反应。平行—顺序反应的一个重要特点是反应深度对产 品产率分布有重大影响。
第三章催化裂化全

第三章催化裂化全第三章催化裂化第一节概述一. 催化裂化目的少图图3-5(a原油经过常减压蒸馏可以获得到汽油、煤油及柴油等轻质油品,但收率只有10~40%。
而且某些轻质油品的质量也不高,例如直馏汽油的马达法辛烷值一般只有40~60。
随着工业的发展,内燃机不断改进,对轻质油品的数量和质量提出了更高的要求。
这种供需矛盾促使炼油工业向原油二次加工方向发展,进一步提高原油的加工深度,获得更多的轻质油品并提高其质量。
而催化裂化是炼油工业中最重要的一种二次加工过程,在炼油工业中占有重要的地位。
催化裂化过程是原料在催化剂存在时,在470~530℃和0.1~0.3MPa的条件下,发生以裂解反应为主的一系列化学反应,转化成气体、汽油、柴油、重质油(可循环作原料或出澄清油)及焦炭的工艺过程。
其主要目的是将重质油品转化成高质量的汽油和柴油等产品。
由于产品的收率和质量取决于原料性质和相应采用的工艺条件,因此生产过程中就需要对原料油的物化性质有一个全面的了解。
二. 催化裂化原料、产品及特点1. 原料油来源催化裂化原料范围很广。
有350~500℃直馏馏分油、常压渣油及减压渣油。
也有二次加工馏分如焦化蜡油、润滑油脱蜡的蜡膏、蜡下油、脱沥青油等。
1)直馏馏分油一般为常压重馏分和减压馏分。
不同原油的直馏馏分的性质不同,但直馏馏分含烷烃高,芳烃较少,易裂化。
我国几种原油减压馏分油性质及组成见表3.1.1。
表3.1.1 国内几种减压馏出油性质及组成根据我国原油的情况,由表3.1.1可知,直馏馏分催化原料油有以下几个特点:①原油中轻组分少,大都在30%以下,因此催化裂化原料充足;②含硫低,含重金属少,大部分催化裂化原料硫含量在0.1%~0.5%,镍含量一般为0.1~1.0μg/g,只有孤岛原油馏分油硫含量及重金属含量高;③主要原油的催化裂化原料,如大庆、任丘等,含蜡量高,因此特性因数K也高,一般为12.3~12.6。
以上说明,我国催化裂化原料量大、质优,轻质油收率和总转化率也较高。