催化裂化吸收稳定流程说明
催化裂化装置吸收稳定单元停工操作法

催化裂化装置吸收稳定单元停工操作法一、吸收稳定单元退油当反应切断进料后,分馏岗位将V22203A、B中轻燃油抽空后,停T22304至T22301的补充吸收油,退油原则尽量将油赶至T22304,各抽出泵抽空后停泵,退油结束。
分馏一中扫线开始前T22304油退完。
轻油由T22301V22302T22302T22304精制单元出装置贫吸收油走付线不经T22303,直接返T22201A,T22303中油压回T22201A,现场注意T22303液位不要压空,严禁干气窜入T22201A。
稳定塔在再沸器出口温度变化不大的情况下,加大稳定轻燃油出装量,在保证塔顶温度不变的情况下尽量加大液化气外送量,V22303无液面时,停P22306AB。
二、吸收稳定单元水顶油1. 分馏未吹扫干净E22310管程,T22304严禁进水,防止突沸。
2. 不合格轻燃油出装置线:新鲜水P22202FV22218管线P22218/2管线P22222不合格轻罐油3. 新鲜水走正常流程进T22301:P22202给水FV22218T22301P22203给水FV222184. T22301一中、二中回流线:一中:二中:P22303LV22302E22303T22301 P22304LV22303E22304T223015. 凝缩油线:T22301P22302FV22302V22302P22301FV22306E22305T22302FV22305V22301注水P22309LV229016. 脱乙烷轻燃油线:T22302P22305FV22307E22307T223047. 稳定塔回流线:P22306给水FV22308T223048. T22301补充吸收剂线:P22307FV22301T22301T223049. 吸收稳定单元撇油。
吸收稳定单元改为三塔循环流程,2小时后,将T22301、V22302抽空,水全部集中在T22302、T22304中,两塔内水位要高,以撇油线在P22307入口见水为准。
催化吸收稳定工艺流程及原理

催化吸收稳定工艺流程及原理
催化吸收稳定工艺是一种在石油化工领域广泛采用的气体处理技术,主要用于炼油厂的气体回收和净化。
该工艺流程主要包括以下几个步骤:
1. 吸收过程:首先,从裂解装置或其他来源产生的富含烃类组分的工艺气(如催化裂化装置的干气),通过与富油吸收剂逆流接触,在吸收塔内将C3及以上烃类有效地溶解到吸收剂中。
2. 解吸过程:随后,含有被吸收烃类的富油进入解吸塔,在一定温度条件下,通过降低压力或加热,促使烃类从吸收剂中解析出来,得到富含C3、C4等轻烃的气体产品。
3. 稳定过程:对于含C5及更重组分的汽油组分,送入稳定塔进行进一步分离,通过精馏原理去除其中的C5+组分,以降低汽油蒸汽压,提高其储存和运输安全性。
整体而言,催化吸收稳定工艺通过连续的物理化学过程,实现了对裂解气和其他烃类混合气的有效分离和资源优化利用。
ASPEN-0-9-ASPEN_吸收稳定

催化吸收稳定系统流程模拟计算一、工艺流程简述催化裂化是我国最重要的重质石油馏份轻质化的装置之一。
它由反再、主分馏及吸收稳定系统三部分所组成。
分馏系统的任务是把反再系统来的反应产物油汽混合物进行冷却,分成各种产品,并使产品的主要性质合乎规定的质量指标。
分馏系统主要由分馏塔、产品汽提塔、各中段回流热回收系统,并为吸收稳定系统提供足够的热量,不少催化装置分馏系统取热分配不合理,造成产品质量不稳定、吸收稳定系统热源不足。
吸收稳定系统对主分馏塔来的压缩富气和粗气油进行加工分离,得到干气、液化气及稳定汽油等产品。
一般包括四个塔第一塔为吸收塔,用初汽油和补充稳定汽油吸收富气中的液化气组份,吸收后的干气再进入到再吸收塔,用催化分馏塔来的柴油吸收其中的较轻组份,再吸收塔顶得到含基本不含C3组份的合格干气,再吸收塔底富柴油回到分馏系统。
吸收塔底富吸收液进到解吸塔,通过加热富吸收液中的比C2轻的组份基本脱除从解吸塔顶出来再回到平衡罐,再进到吸收塔内;解吸塔底脱除C2组份的液化气和汽油组份再进到稳定塔,通过分离稳定塔顶得到C5合格的液化气组份,塔底得到蒸汽压合格的汽油,合格汽油一部分作为补充吸收剂到吸收塔,一部分作为产品出装置。
吸收稳定系统分离其工流流程如图4-1所示,所涉及主要模块有吸收塔(C10301)、解吸塔(C10302)、再解吸塔(C10303)、稳定塔(C10304)。
解吸塔进料预热器(E302)、稳定塔进料换热器(E303),补充吸收剂冷却器(C39),平衡罐(D301)。
图4-1 催化吸收稳定系统模拟计算流程图GGGAS干气; LLPG液化气; GGOIL稳定汽油;PCOIL贫柴油;PGAS干气;FCOIL富柴油;二汽油;LPG液化气;WDGOIL5稳定汽油产品;D301平衡罐;C10301吸收塔,C10302解吸塔,C10303再吸收塔,C10304稳定塔二、需要输入的主要参数1、装置进料数据2、单元操作参数3、设计规定4、灵敏度分析的应用应用方案研究功能研究,考察贫汽油流量、贫柴油流量对贫气中C3含量、液化气中C2含量的影响。
催化裂化分馏吸收稳定部分流程口诀
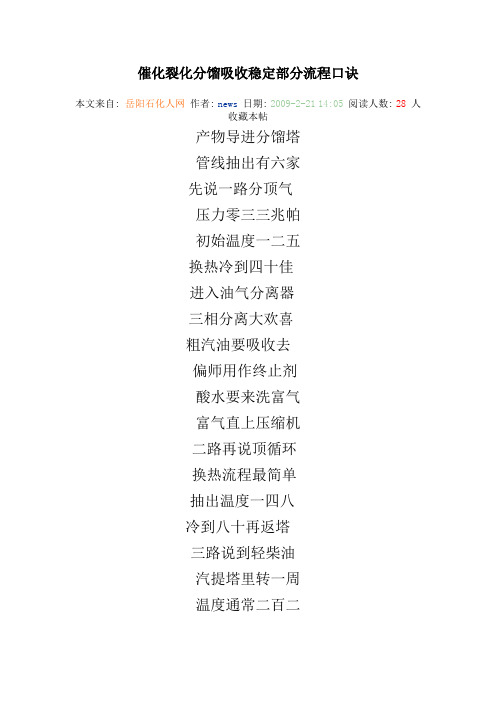
催化裂化分馏吸收稳定部分流程口诀本文来自: 岳阳石化人网作者: news日期: 2009-2-21 14:05阅读人数: 28人收藏本帖产物导进分馏塔管线抽出有六家先说一路分顶气压力零三三兆帕初始温度一二五换热冷到四十佳进入油气分离器三相分离大欢喜粗汽油要吸收去偏师用作终止剂酸水要来洗富气富气直上压缩机二路再说顶循环换热流程最简单抽出温度一四八冷到八十再返塔三路说到轻柴油汽提塔里转一周温度通常二百二冷到六十卖柴油一部深冷三十五正好用作再吸收四路说说一中段抽出温度二九三换热稳塔重沸器再至二百是限关五路说说二中油通常回炼要合流大部要走发生器小部直去反应区抽出温度三四四返塔温度二百七六路说说油浆线两相分离泪涟涟二百八十返回塔产品九十说再见说完分馏说吸收吸收稳定费琢磨富气直上压缩机压缩气用酸水洗其先抽出一分支补充分顶防喘息解顶气混空冷前吸底油混冷却器分离器前四十度液相解吸进料油酸水要到缓冲罐气相要去被吸收粗汽油作吸收剂稳定汽油来补足吸收塔顶再吸收温度只有四十度吸收一中四十始返塔温度三五低吸收二中同此理吸收塔底四十一解吸进料自分离塔顶气体混富气中段重沸是九七返回增加十度矣塔顶重沸一四八返塔更是一六七解吸塔底作进料稳定塔前一五七塔顶液化石油气初始温度五十七回流罐前四十一大部返塔要稳定小部产品出装置稳定塔底作二路一八零是初温度一路要去补吸收二路重沸再回流热源常是分一油温度上扬超十度说完稳定还得说不可或缺再吸收吸收剂才三十五其实就是轻柴油被吸则是吸顶气富油换热上分馏出来初温四十五终温一百正所求催化裂化一大家十二兄弟遍天涯MGG要吃蜡胃口好时也掺渣生产汽油最大量还有石油气液化ARGG裂常渣目的产品同上家DCC工艺二取一都要生产轻质烯一型原料是蜡油最大产出是丙烯二型原料重质油多产丙烯异构烯MIO掺渣油主体重质馏分油生产异丁异戊烯还有高辛值汽油MGD也不差原料蜡油和常渣汽油降烯效果好轻柴石油气液化异构烷烃MIP 同时汽油也降烯热裂解工艺CPP 制取乙烯和丙烯DNCC工艺牛吸附转化焦化油碱氮吸附催化剂烧焦再生也解毒DOCR石蜡基DOCP是兄弟高效复合分子筛提高汽油辛烷值FDFCC双提升灵活多效多轻烯调节产品升温度汽油大幅度降烯HCC接触剂重油接触制乙烯两段提升管工艺TSRFCC大幅提高转化率干气焦炭产率低辅助提升管工艺汽油改质靠降烯。
催化裂化吸收稳定系统流程模拟及优化
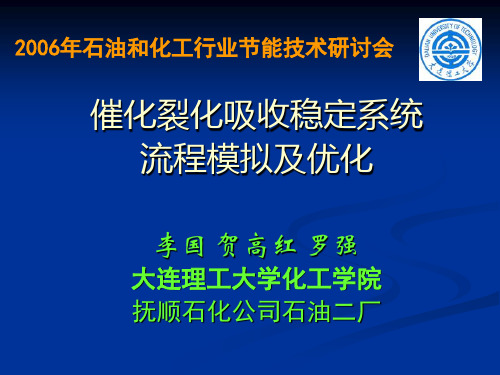
2.0 1.5 1.0 0.5 0.0 30 40 50 60 解析塔进料温度/℃Gj
30 28 26 24 22
30
40
50
60
解析塔进料温度/℃
70
80
90
吸收塔塔板数的影响
2.5
干气中丙烯浓度/%
2.0 1.5 1.0 0.5 5 10 15 20 吸收塔塔板数 25 30 35
总热负荷 总冷负荷
30
35
稳定塔塔板数的影响
1.10
干气中丙烯浓度/%
1.08
1.06 1.04 1.02 10 15 20 25 稳定塔塔板数
36
30
35
40
总热负荷
32
负荷/Gj
总冷负荷
28 24 20 10
15
20
25 稳定塔塔板数
30
35
40
优化工况与基本工况比较
参数比较 产品质量
经济效益
大连理工大学 热烈欢迎尊贵客人的 光临和指导
6.0 22 1.3 8.0 2.3 2.3 1.9 1.3 1.3
粗汽油和轻柴油组成
项目 初馏点 10%
52.0
30%
78.0
50%
93.0
70%
90%
干点
密度(20℃) /kg· m-1
711.6 kg/m
粗汽油
35.0
122.0 158.0 176.0
轻柴油
180.0
204.0 225.0 254.0 289.0 331.0 354.0 870.5Kg/m3
0.55
1.33 0.26 27.38 13.23 16.57
重油催化裂化装置主要工艺流程说明
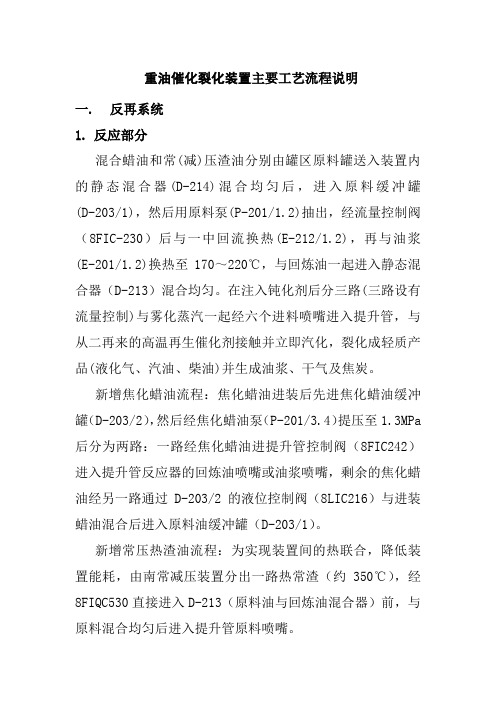
重油催化裂化装置主要工艺流程说明一. 反再系统1.反应部分混合蜡油和常(减)压渣油分别由罐区原料罐送入装置内的静态混合器(D-214)混合均匀后,进入原料缓冲罐(D-203/1),然后用原料泵(P-201/1.2)抽出,经流量控制阀(8FIC-230)后与一中回流换热(E-212/1.2),再与油浆(E-201/1.2)换热至170~220℃,与回炼油一起进入静态混合器(D-213)混合均匀。
在注入钝化剂后分三路(三路设有流量控制)与雾化蒸汽一起经六个进料喷嘴进入提升管,与从二再来的高温再生催化剂接触并立即汽化,裂化成轻质产品(液化气、汽油、柴油)并生成油浆、干气及焦炭。
新增焦化蜡油流程:焦化蜡油进装后先进焦化蜡油缓冲罐(D-203/2),然后经焦化蜡油泵(P-201/3.4)提压至1.3MPa 后分为两路:一路经焦化蜡油进提升管控制阀(8FIC242)进入提升管反应器的回炼油喷嘴或油浆喷嘴,剩余的焦化蜡油经另一路通过D-203/2的液位控制阀(8LIC216)与进装蜡油混合后进入原料油缓冲罐(D-203/1)。
新增常压热渣油流程:为实现装置间的热联合,降低装置能耗,由南常减压装置分出一路热常渣(约350℃),经8FIQC530直接进入D-213(原料油与回炼油混合器)前,与原料混合均匀后进入提升管原料喷嘴。
反应油气、水蒸汽、催化剂经提升管出口快分器分离出大部分催化剂,反应油气经过沉降器稀相沉降,再经沉降器(C-101)内四组单级旋风分离器分离出绝大部分催化剂,反应油气、蒸汽、连同微量的催化剂细粉经大油气管线至分馏塔人档下部。
分馏塔底油浆固体含量控制<6g/L。
旋分器分出的催化剂通过料腿返回到汽提段,料腿装有翼阀并浸没在汽提段床层中,保证具有正压密封,防止气体短路,汽提蒸汽经环形分布器进入汽提段的上中下三个部位使催化剂不仅处于流化状态,并汽提掉催化剂夹带的烃油气,汽提后的催化剂通过待生滑阀进入一再催化剂分布器。
催化裂化工艺流程及主要设备
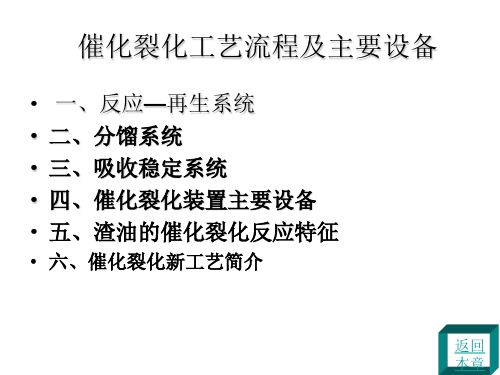
➢分布器可分为板式(蝶形)和管式(平面树枝或环形)两种
重催再生器需设取热设备: a.内取热式 b.外取热式
主要要求有:
①再生剂的含炭量较低,一般要求低于0.2%,甚
至低于0.05%;
②有较高的烧碳强度,当以再生器内的有效藏量
为基准时,烧碳强度一般为100~250kg/(t.h);
③催化剂减活及磨损较少; ④易于操作,能耗及投资少; ⑤能满足环保要求
①对于全混床反应器,第一段出口的半再生剂的含碳量 高于再生剂的含碳量,从而提高了烧碳速率;
②在第二段再生时可以用新鲜空气和更高的温度,提高 了烧碳速率;
③第二段内的水气分压可以很低,减轻了催化剂的水热 老化;且第二段的催化剂藏量比单段再生器的催化剂藏量低, 停留时间较短。因此,第二段可采用较高的再生温度。
从流化域来看,单段再生和两
段再生都属于鼓泡床和湍流床 的范畴,传递阻力和返混对烧 碳速率都有重要的影响。
你知道吗?
如果把气速提高到1. 2m/s
以上,而且气体和催化剂向 上同向流动,就会过渡到快 速床区域。
烧焦罐再生(亦称高效再生)就是 循环流化床的一种方式
二密床高度4~6m. 烟气流速 0.1~0.25m/s
稀相管高度8~15m.
烧焦罐再生 烟气流速7~10m/s
循环管是烧焦罐再生器的独有设备, 它的作用是把热催化剂从二密相返回 烧焦罐,提高烧焦罐底部温度和烧焦 罐密度,以提高烧焦速度并增加烧焦 能力。早期的烧焦罐装置循环比为 I~I.5,循环管直径与再生剂管直径相 当;近年设计的烧焦罐装置循环比为 1.5~2,循环管直径明显大于再生管 直径。
100~125mm厚的隔热耐磨衬里。 ➢ 伸到汽提段、沉降器内的部分只设耐磨衬里。 ➢ 提升管的上端出口处设有气-固快速分离机构,用于使催化剂与油气
催化裂化操作指南(分馏与稳定)解读
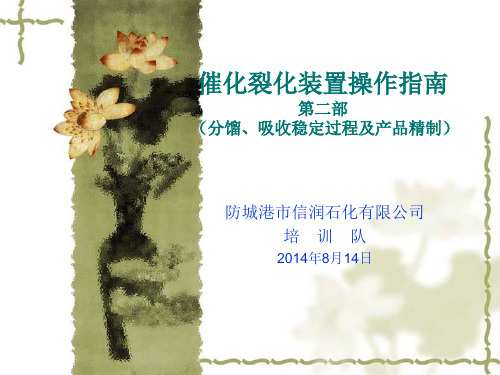
分馏过程
一、设备检查 1、塔器 (1)分馏塔 首次运行的分馏塔,必须逐层检查所有塔盘,确认按图纸正确安装; 如溢流口尺寸、堰高和塔盘水平度等。 对所有浮阀进行检查,确认清洁,活动自如;所有塔盘紧固件安装正 确、紧固;所有分布器安装定位正确,分布孔畅通。 每层塔盘和降液管清洁,顶循、中段、柴油等抽出槽和抽出口清洁无 杂物,集油箱焊缝完好,不泄漏。 底部脱过热段折流板(人字档板)等均坚固,焊缝完好,所有固定螺 栓均已经锤击或被点焊。 塔底搅拌蒸汽分布器、支撑等完好;油浆过滤器及其附件清洁,固定 或焊接牢固。 塔内设备检查完成后,应马上安装人孔,安排专人现场负责该项工作。
分馏过程
档板或园盘型档板,进入油气与260-360℃循环油浆逆流接触、换热、 冼涤,油气被冷却,将油气中夹带的催化剂细枌冼涤下来,防止其污染 上部的测线产品,堵塞上部塔盘。 (2)全塔过剩热量大 分馏塔进料是过热度很高的反应油气(480-510 ℃ ),塔顶是低温 (100-130 ℃ )气体,其他产品均以液态形式离开分馏塔。在整个分 馏过程中有大量的过剩热量需要移出。所以系统有大量的冷换设备和热 水器。 (3)产品分馏要求较容易满足 油品分馏难易程度可用相邻馏分50%馏出温度差值来衡量。差值越大, 馏分间相对挥发度越大,就越容易分离。催化分馏塔除塔顶为粗汽油外 还有轻柴油、重柴油、回炼油三个侧线组分。催化裂化各侧线组分50% 馏出温度值较大,馏分容易分离,所以产品分馏要求容易满足。
分馏过程
(5)轻污油系统 分馏、吸收稳定部分轻油设备(换热器、泵、过滤器、采样器等) 在停工或检修时存有少量的轻油,通过污油系统自流至地下轻污油罐, 用污油泵送出装置。 (6)重污油系统 装置内重油设备在停工或检修时存有少量的重油,通过重污油系统 送出装置。 5、事故处理流程 (1)富气放火炬流程 开工时提升管反应器已经进油,但富气压缩机还没有启动,在此期 间产生的富气从分馏塔顶油气分离器引出经富气放空管道排放至火炬系 统。正常生产中富气压缩机因故障紧急停机,则启用富气放火炬系统。 (2)汽油紧急排放流程 当分馏塔顶油气分离罐粗汽油液位突然升高,用正常方法处理不及 时,有汽油进入富气压缩机的危险时,可启用汽油紧急放空(粗汽油泵 入口管排放到轻污油罐)。
- 1、下载文档前请自行甄别文档内容的完整性,平台不提供额外的编辑、内容补充、找答案等附加服务。
- 2、"仅部分预览"的文档,不可在线预览部分如存在完整性等问题,可反馈申请退款(可完整预览的文档不适用该条件!)。
- 3、如文档侵犯您的权益,请联系客服反馈,我们会尽快为您处理(人工客服工作时间:9:00-18:30)。
催化裂化吸收稳定流程说明
一、工艺流程叙述
催化装置吸收稳定系统流程模拟流程图如图1 所示。
由分馏塔顶油气分离器来的富气经富气压缩机压缩到 1.6MPa(绝)。
压缩富气与解吸塔顶解吸气混合经气压机出口冷却器冷至55℃,再与吸收塔底油混合,经气压机出口后冷器冷至40℃,进入平衡罐(D-301)分离出气相(富气)及液相(凝缩油)。
吸收塔(C-301)位于脱吸塔(C-302)上部,压力1.4MPa(绝)。
由平衡罐来的富气进入吸收塔的下部,自稳定塔返回的补充吸收剂和分馏塔来的粗汽油均进入吸收塔的顶部,与气体逆流接触。
吸收塔设有两个中段回流,用以取走吸收过程所释放的热量,避免塔内温度上升过高。
中段回流自第14 层及第21 层用泵P3 及P4 抽出,分别经水冷器(E-306,E-307)冷至40℃,返塔第15 层及第22 层上方,吸收塔底釜液饱和吸收油返回到上游与压缩富气混合。
吸收塔顶采出的贫气,进入再吸收塔(C-304)底部,与轻柴油吸收剂逆流接触,吸收贫气中的汽油组分。
塔顶压力为1.3~1.4MPa(绝),塔顶干气为装置的副产品。
塔底富吸收油返回分馏塔。
D-301 底凝缩油经泵P1 加压,与稳定汽油换热(E-304)至70℃进入解吸塔C-302 上部,塔顶压力1.6MPa(绝)。
解吸塔底重沸器E-301 由分馏塔一中回流供热。
解吸塔顶气返回至E-305 前与压缩富气混合。
C-302 塔底脱乙烷汽油经稳定塔进料泵与稳定汽油换热(E-302)至165℃入稳定塔(C-303)。
C-303 塔顶压力1.17MPa(绝),塔底重沸器E-303由分馏二中回流供热。
液化气组分由C-303 顶馏出,经水冷器(E-308)冷却至40℃,入回流罐(D-302)。
液化气经回流泵加压(P-304)后,一部分作为顶回流,另一部分出装置。
稳定塔釜液稳定汽油先与脱乙烷汽油换热(E-302)至161.4℃,再与凝缩油换热(E-304)至130℃,再经除盐水冷却器(E-309)冷至40℃,一部分出装置,一部分用泵P6 打入塔C-301 顶作补充吸收剂。
二、流程计算初始数据
1、初始数据要求
(1)装置工艺流程图
(2)进料数据
吸收稳定系统的进料有压缩富气,粗汽油和贫吸收油三股。
对于压缩富气要求压力、温度、流量和组成数据;对于粗汽油和贫吸收油要求有该油品的恩氏蒸馏数据或实沸点蒸馏数据及密度、压力、温度和流量数据。
(3)塔工艺数据
要求提供吸收塔、解吸塔、再吸收塔和稳定塔的塔板数,进料位置、回流比,操作压力等数据。
吸收塔存在中段回流,需提供中段回流的采出位置,返回位置,采出量,返回温度等数据。
需提供各塔的分离要求作为塔计算的依据。
如解吸塔可提供塔釜C2 组分的浓度要求,稳定塔可提供液化气中C2 的浓度要求,釜液的C4 浓度或雷氏蒸气压要求等。
如需进行塔水力学核算,还需提供塔的结构参数,如塔径,塔板类型,板间距,浮伐数(或泡罩数、或筛孔数等),降液管尺寸和类型等参数;如是填料塔,需提供填料参数。