第十二章 推镗加工
镗削加工

镗削加工1.什么叫悬伸镗削法?它有哪些特点?使用悬伸的单镗刀杆,对中等孔径和不穿通的同轴孔进行镗削加工,这种加工方法叫悬伸镗削法。
悬伸镗削法的主要特点有:(1)由于悬伸镗削所使用的镗刀杆一般均较短、粗,刚性较好,切削速度的选择可高于支承镗刀杆,故生产效率高。
(2)在悬伸镗刀杆上装夹、调整刀具方便,在加工中又便于观察和测量,能节省辅助时间。
(3)用悬伸镗削法采用主轴送进切削时,由于镗刀杆随主轴送进而不断悬伸,刀杆系统因自重变化产生的挠度也不同,在加工较长内孔时,孔的轴线易产生弯曲。
由于主轴不断伸出,整个刀杆系统刚性不断变差,镗削时在切削力作用下,系统弹性变形逐渐增大,影响孔的镗削精度,使被加工孔产生圆柱度误差。
2、试述采用工作台进给悬伸镗削的特点。
这种镗削方式对被加工孔的精度有何影响?用工作台进给悬伸镗削时;由于主轴悬伸长度在切削前已经调定,故切削过中由刀杆系统自重和受切削力引起的挠曲变形及弹性变形相对较为稳定。
因此被加工孔产生的轴线弯曲和圆柱度误差均比用主轴进给悬伸镗削时小。
这种镗削方式影响孔加工精度的主要原因是床身和工作台导轨的直线度误差,以及它们之间的配合精度。
若床身导轨在水平平面和垂直平面内有直线度误差,会使被加工孔的轴线产生直线度误差和对基准表面产生位置误差;若导轨配合精度差,将会使被加工孔产生圆度误差。
3、什么叫支承镗削法?它有哪些特点?支承镗削法是采用架于镗床尾座套筒内的支承镗杆进行镗削的一种切削加工方式。
支承镗削法的特点是:(1)与悬伸镗削法相比,大大增强了镗杆的刚性。
(2)适合同轴孔系的加工。
可配用多种精度较高的镗刀,加工精度高,能确保加工质量。
(3)装夹和调整镗刀较麻烦、费时,不易观察加工情况,试镗、测量等操作没有悬伸镗削法那样直观、方便。
4、试述采用镗杆进给支承镗削法的特点。
这种镗削方式对被加工孔的精度有何影响?采用镗杆进给支承镗削法镗孔,镗杆伸出长度随主轴进给而不断变化,但镗杆和主轴在两支承点之间的距离不变。
工程训练基础第十二章
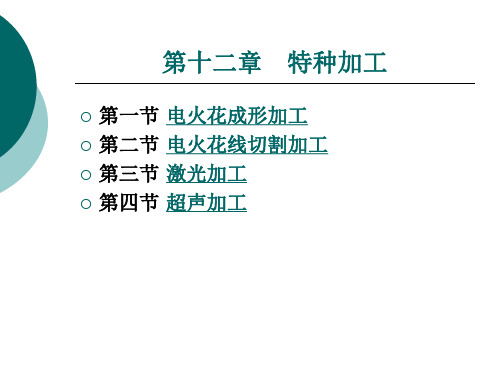
下一页 返回
第二节
电火花线切割加工
12.2.1
数控电火花线切割机床
数控快走丝电火花线切割机床主要由机床本体、控制系 统、脉冲电源、工作液循环系统和机床附件等部分组成。图 12-8为BKDC数控电火花线切割机床示意图。 1. 机床本体 机床本体又称切割台,是线切割机床的机械部分,由床 身、工作台、走丝机构、锥度切割装置、丝架和夹具等部分 组成。
上一页 下一页 返回
第二节
电火花线切割加工
12.2.2
线切割加工原理、特点及应用
1. 线切割加工原理 电火花线切割加工是利用移动的细金属导线(钼丝或铜 丝)作为电极,对工件进行脉冲火花放电,靠放电时局部瞬 间产生的高温来除去工件材料,以此进行切割加工的方法, 如图12-9所示。作为工具电极的钼丝或铜丝,在储丝筒带 动下作正反向交替移动,脉冲电源的负极连接电极丝,正极 连接工件,在电极丝和工件之间喷注工作液,工作台在水平 面的两个坐标方向上各自按预定的控制程序,由数控系统驱 动作伺服进给移动,完成工件的切割加工。
上一页 下一页 返回
第二节
电火花线切割加工
2. 线切割加工的特点及应用 (1) 加工特性:其加工性主要取决于材料的导电性和热学 特性,而几乎与材料的力学性能无关。 (2) 加工成形工具及复杂形状:由于靠放电加工,电极丝 很细(<0.3 mm),可以加工微细异形孔、窄缝和形状复 杂的工件,如带锥度型腔的电极、微细复杂形状的电极和各 种样板、成形刀具等,用于各种模具制造,如凸模、凹模及 各种形状的冲模等。采用移动的长电极丝进行加工,单位长 度上的损耗很少,从而提高了加工精度。尺寸精度可达 0.01~0.02 mm,表面粗糙度Ra可达1.6 μm。
第二节镗孔加工

第六章 孔系加工
二、镗孔刀具
镗刀由刀柄和刀具组成,具有一个或两个切削 部分,专门用于对已有的孔进行粗加工、半精加 工或精加工的刀具,如下图所示。镗刀可在镗床、 车床或铣床上使用。因装夹方式的不同,镗刀柄 部有方柄、莫氏锥柄和7:24锥柄等多种形式。在 数控铣床上一般采用7:24锥柄镗刀。
第六章 孔系加工
(3)刀具安装后进行动态跳动检查。动态跳动检 查是一个综合指标,它反映机床主轴精度、刀具精度 以及刀具与机床的连接精度。这个精度如果超过被加 工孔要求的精度的 1/2 或 2/3 就不能进行加工,需 找出原因并消除后才能进行。这一点操作者必须牢记, 并严格执行,否则加工出来的孔不能符合要求。
第六章 孔系加工
格式: G85 X__Y__Z__R__ F__; G86 X__Y__Z__R__ P__F__;
第六章 孔系加工
式中 G85─镗孔循环在孔底时主轴不停转,然后快速退
刀;如下图a所示。 G86─镗孔循环在孔底时主轴停止,然后快速退刀;
如下图b所示。
图6-13 粗镗孔动作图
a)G98 G85动作
b)G98 G86动作
第六章 孔系加工
(2)G76/G87程序段中Q代表刀具在轴反向位移增量。 (3)G87指令编程时,注意刀具进给切削方向是从工件的 下方到工件的上方。 (4)为了提高加工效率,在指令固定循环前,应先使主轴 旋转。 (5)由于固定循环是模态指令,因此,在固定循环有效期
机械加工镗削工艺
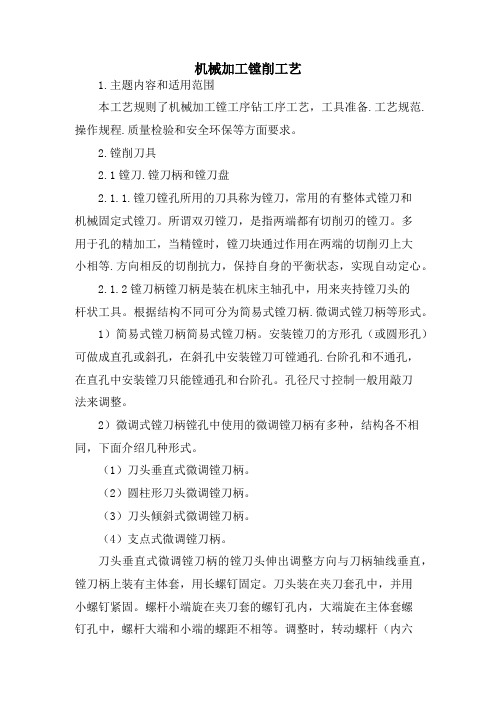
机械加工镗削工艺1.主题内容和适用范围本工艺规则了机械加工镗工序钻工序工艺,工具准备.工艺规范.操作规程.质量检验和安全环保等方面要求。
2.镗削刀具2.1镗刀.镗刀柄和镗刀盘2.1.1.镗刀镗孔所用的刀具称为镗刀,常用的有整体式镗刀和机械固定式镗刀。
所谓双刃镗刀,是指两端都有切削刃的镗刀。
多用于孔的精加工,当精镗时,镗刀块通过作用在两端的切削刃上大小相等.方向相反的切削抗力,保持自身的平衡状态,实现自动定心。
2.1.2镗刀柄镗刀柄是装在机床主轴孔中,用来夹持镗刀头的杆状工具。
根据结构不同可分为简易式镗刀柄.微调式镗刀柄等形式。
1)简易式镗刀柄简易式镗刀柄。
安装镗刀的方形孔(或圆形孔)可做成直孔或斜孔,在斜孔中安装镗刀可镗通孔.台阶孔和不通孔,在直孔中安装镗刀只能镗通孔和台阶孔。
孔径尺寸控制一般用敲刀法来调整。
2)微调式镗刀柄镗孔中使用的微调镗刀柄有多种,结构各不相同,下面介绍几种形式。
(1)刀头垂直式微调镗刀柄。
(2)圆柱形刀头微调镗刀柄。
(3)刀头倾斜式微调镗刀柄。
(4)支点式微调镗刀柄。
刀头垂直式微调镗刀柄的镗刀头伸出调整方向与刀柄轴线垂直,镗刀柄上装有主体套,用长螺钉固定。
刀头装在夹刀套孔中,并用小螺钉紧固。
螺杆小端旋在夹刀套的螺钉孔内,大端旋在主体套螺钉孔中,螺杆大端和小端的螺距不相等。
调整时,转动螺杆(内六角),使夹刀套和镗刀头前后移动,移动最大量等于大端螺距和小端螺距之差。
在螺杆头上刻有刻线,以准确地掌握镗刀头移动尺寸。
调整时,要松开固定刀头的小螺钉圆柱形刀头微调镗刀柄上的镗刀头呈圆柱形,转动微调螺钉,可带动镗刀头沿镗刀柄径向移动。
拧动内六角螺钉传动两个滑块,能夹紧或松开镗刀头。
镗刀柄的斜孔与刀柄轴线成一定角度,它是通过刻度和精密螺纹来进行微调的。
装有可转位镗刀片的镗刀头上有精密螺纹,镗刀头的外圆柱与镗刀柄上的孔相配,并在其后端采用内六角紧固螺钉及垫圈拉紧。
镗刀头的螺纹上旋有带刻度的调整螺母,调整螺母的背部是一个圆锥面,与镗刀柄孔口的内锥面紧贴。
第十二章 锻压
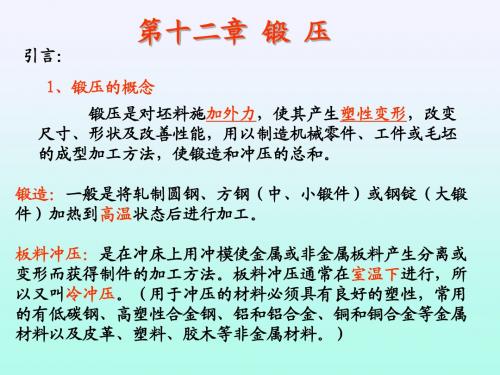
(4)锻压主要生产承受重载荷零件的毛坯,如机器中的 主轴、齿轮等,但不能获得形状复杂的毛坯或零件。
液压机
利用高压水为动力进 行工作。靠静压力工 作。常用吨位为 5~150吨,用于锻造 大型锻件,是大型锻 件的唯一设备。
空气锤
利用压缩空气推动锻锤进 行工作。以落下部分质量 来表示锻造能力;常用吨 位为65—750千克,用于 锻造小型锻件。
2)自由锻常用工具
3、自由锻工序
自由锻工序分为基本工序、辅助工序和精整工序。
三、锻造比
锻造比是锻造时金属变形程度的一种表示方法。
拔长时的锻造比为 Y拔=S0/S=L/L0
镦粗时的锻造比为
Y镦=H0/H=S/S0
一般情况下,增加锻造比,对改善金属的组织和性能是有 利的。但是锻造比太大是无益的。
第二节
自由锻
自由锻是只用简单的通用性工具,或在锻造设备的上、 下砧间直接使坯料变形而获得所需的几何形状及内部质 量锻件的方法。
4)切断模膛 其作用是切断金属。单件锻造时,用它从坯 料上切下锻件或从锻件上切下钳口,多件锻造时,用它来分 离成单个件。
(二)模锻工艺规程的制订 模锻生产的工艺规程包括制订锻件图、计算坯料尺寸、 确定模锻工步、选择设备及安排修整工序等。 1、制订模锻锻件图 模锻锻件图是制造和检验终锻模膛的依据。这是以零件图 为基础,考虑了分模面的选择、加工总余量、公差、余块、模 锻斜度和圆角半径等绘制的。 (1)分模面的选择 选择分模面位置最基本的原则是:应选在锻件具有最大水平投 影尺寸的位置上,最好为锻件中部的一个平面,并使锻件上所 加余块最少,上、下模膛深度最浅且尽可能基本一致。
第十二章 磨削
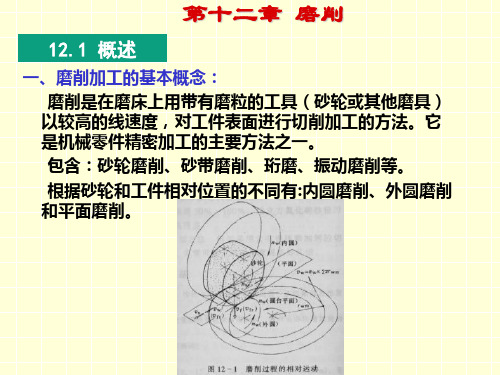
12.3 砂轮表面形貌图
有效磨粒切削刃,无效磨粒切削刃。 测量砂轮表面形貌目前主要用接触法: 1、静态法 2、动态法 3、工件复印法
12.4 磨削过程
一、磨削运动 磨削时,一般有四个运动。 1、主运动 砂轮的旋转运动,主运动的速度 就是砂轮外圆的线速度。 vs=πdsns/1000 2、径向进给运动:砂轮切入工件的运动,其 大小用径向进给量fr表示。又称磨削深度。
• • • •
天然金刚石 人造金刚石 CBN 普通磨料
二、粒度
粒度:磨粒颗粒的尺寸大小。
粗磨粒粒度(颗粒最大尺寸大于40μm ):用机械筛分法,
每平方英寸筛网上孔的数量,如60#,80#。粒度号数越大,
颗粒尺寸越细。
微粉磨粒粒度(颗粒尺寸小于40μm ):用显微镜分析法, 粒度号数即该颗粒最大尺寸的μm数。如W5,W3,W0.5
• 普通磨料固结磨具的标志按国标GB2484-84规定,其书写 顺序为:磨具形状、尺寸、磨料、粒度、组织、结合剂、 最高工作线速度。
国标GB2484-84
国际标准ISO
• 超硬磨料磨具的标志书写顺序为:形状、尺寸、 磨料、粒度、结合剂和浓度等。平行砂轮标志 示例如下:
超硬磨料磨具的结构
• 超硬磨料砂轮一般由磨料层、过渡层和基体组成。
四、磨削循环 一、磨削力的特征 磨削力的来源:一是各个磨粒的切削刃挤压切入工件后,工 件材料发生弹性、塑性变形时所产生的阻力;二是磨粒和结 合剂与工件表面之间的摩擦力。 以外圆纵磨为例,磨削力分解为切向力、法向力和轴向力。
由于磨粒上的切削刃为负前角,所以法向分力Fn远大于 切向分力Ft。轴向分力Fa最小。
以磨粒率表示的磨具组织及其应用范围
组织号 磨粒率 (%) 0 62 1 60 2 58 3 56 4 54 5 52 6 50 7 48 8 46
镗孔的加工工艺及夹具设计
镗孔的加工工艺及夹具设计1.镗孔加工工艺设计1.1镗孔的定位分析在镗床上加工孔时,需要对零件进行夹紧,因此需要对零件进行夹紧设计,镗孔应采用专用夹具,根据六点定位原则来确定工件的定位方式。
下面对图一中的镗孔进行定位分析:该道工序为镗三个平行的孔,但是由于工件自身尺寸较大,孔径也较大,其定位基准分布在同一平面上,所以根据六点定位原理选择A面为定位基准。
由一个角铁作为安装的底座,工件的定位和导向机构完全安装在角铁上,脚架和压紧丝杠限制了X、Z方向的转动及移动,定位销限制了Y方向的转动和移动,由此可见,实现了工件镗孔时的完全定位。
图1镗床夹具图1.2切削力与夹紧力的计算(1)镗Φ146孔查表给定镗刀B=30H=20L=200I=100d=20选择合金钢镗刀公称直径Φ146;在镗孔时候只考虑圆周切削力;查文献得;(1.1)Kmp=(HB/150)n取n=0.55所以Kmp=1.17;所以;;由于夹紧机构产生的实际夹紧力应满足下式:P=KFz(1.2)取安全系数K=K1K2K3K4K5式中K1——基本安全系数1.5;K2——夹紧状态系数1.2;K3——刀具钝化系数1.0;K4——考虑夹紧动力稳定性系数1.0;K5——尽在有力矩企图使用回转时开考虑支撑面接触情况的系数1.0;所以得到K=K1K2K3K4K5=1.9,得到P=KFz=1.9X365.18=693.88N (2)镗Φ48孔选择高速钢镗刀公称直径Φ48;查表给定镗刀B=25H=30L=170I=80d=15在镗孔时候只考虑圆周切削力;查文献得;Kmp=(HB/150)n取n=0.55所以Kmp=1.17;所以;;由于夹紧机构产生的实际夹紧力应满足下式:P=KFz取安全系数K=K1K2K3K4K5式中K1——基本安全系数1.5;K2——夹紧状态系数1.2;K3——刀具钝化系数1.0;K4——考虑夹紧动力稳定性系数1.0;K5——尽在有力矩企图使用回转时开考虑支撑面接触情况的系数1.0;所以得到K=K1K2K3K4K5=1.9,得到P=KFz=1.9X223.2=424.08N <ol> 镗Φ80孔</ol>镗Φ80孔的计算过程与上边量孔的方法是一样的,就是选择高速钢镗刀公称直径Φ80的镗刀,最后计算结果为P=KFz=569.23N 根据上边的计算夹紧力不是很大,且夹具选择的种类为组合夹具,所以动力选择手动夹紧。
机械制造基础第十二章 齿轮加工.
齿形加工比较复杂,按原理分为成形法和展成法
(也叫范成法和包络法)两种。
成形法是用与被切齿轮齿槽法向截面形状相符的
成形刀具切出齿形的方法。
展成法则是利用齿轮刀与被切齿轮的啮合运动,
在专用齿轮加工机床上切出齿形的方法。
二 齿形加工方法
1铣齿
铣齿属于成形法加工,是一种粗加工。
铣齿的主运动是铣刀的旋转,进给运动是齿轮坯
轴向进行的垂直移动。
(2)滚齿的特点与应用
加工精度高:插、滚齿IT8-7,铣齿IT12-9(插齿
和滚齿相当,且都比铣齿高)。
齿面粗糙度小:Ra3.2~0.6μm。
生产效率高:滚齿高于插齿,更高于铣齿。 滚齿主要用于加工各种批量的直齿或斜齿外圆柱
齿轮、蜗轮。不能加工内齿轮和相距很近的多联 齿轮。
3磨齿
磨齿是用砂轮在磨齿机上加工高精度齿形的方法。
磨齿具有加工精度高(可达IT6~4级)、齿面粗
糙度低(Ra值0.4~0.2μm)的特点。
磨齿有成形法磨齿和展成法磨齿两种,可以磨削
淬火或未淬火的齿轮。 成形法磨齿生产率较高,但精度较低(IT6~5)。 展成法磨齿生产率较低,但精度较高(IT6~4)。
机械制造基础
第十二章 齿轮加工
黄石理工学院
一 齿轮及加工概述
齿轮是重要的机械零件,为了保证其运转精确、
平稳可靠,必须采用合适的齿形曲线。最常用的 齿形曲线是渐开线,此外还有摆线和圆弧。
齿轮的加工包括两个部分:齿坯加工、齿形加工。 齿坯加工采用通用的方法:铸件或锻件,车削加
工(单件或小批量)或钻孔-拉孔-多刀车削(大 批量)。
(2)铣齿的特点与应用
铣齿的误差:齿形误差和分齿误差。 铣齿可以加工直齿、斜齿、人字齿圆柱齿轮,也
镗孔工艺
6.7 镗孔工艺、编程6.7.1 镗孔加工概述1.镗孔加工要求镗孔是加工中心的主要加工内容之一,它能精确地保证孔系的尺寸精度和形位精度,并纠正上道工序的误差。
通过镗削上加工的圆柱孔,大多数是机器零件中的主要配合孔或支承孔,所以有较高的尺寸精度要求。
一般配合孔的尺寸精度要求控制在IT7~IT8,机床主轴箱体孔的尺寸精度为IT6,精度要求较低的孔一般控制在IT11。
对于精度要求较高的支架类、套类零件的孔以及箱体类零件的重要孔,其形状精度应控制在孔径公差的1/2~1/3。
镗孔的孔距间误差一般控制在±0.025~0.06 mm,两孔轴心线平行度误差控制在0.03~0.10 mm。
镗削表面粗糙度,一般是Ra1.6~0.4 μm。
2.镗孔加工方法孔的镗削加工往往要经过粗镗、半精镗、精镗工序的过程。
粗镗、半精镗、精镗工序的选择,决定于所镗孔的精度要求、工件的材质及工件的具体结构等因素。
⑴粗镗粗镗是圆柱孔镗削加工的重要工艺过程,它主要是对工件的毛坯孔(铸、锻孔)或对钻、扩后的孔进行预加工,为下一步半精镗、精镗加工达到要求奠定基础,并能及时发现毛坯的缺陷(裂纹、夹砂、砂眼等)。
粗镗后一般留单边2~3 mm作为半精镗和精镗的余量。
对于精密的箱体类工件,一般粗镗后还应安排回火或时效处理,以消除粗镗时所产生的内应力,最后再进行精镗。
由于在粗镗中采用较大的切削用量,故在粗镗中产生的切削力大、切削温度高,刀具磨损严重。
为了保证粗镗的生产率及一定的镗削精度,因此要求粗镗刀应有足够的强度,能承受较大的切削力,并有良好的抗冲击性能;粗镗要求镗刀有合适的几何角度,以减小切削力,并有利于镗刀的散热。
⑵半精镗半精镗是精镗的预备工序,主要是解决粗镗时残留下来的余量不均部分。
对精度要求高的孔,半精镗一般分两次进行:第一次主要是去掉粗镗时留下的余量不均匀的部分;第二次是镗削余下的余量,以提高孔的尺寸精度、形状精度及减小表面粗糙度。
机械制造技术基础 第6章 镗削加工方法
6.2.4镗削加工工艺及案例分析
[ 案 例 2] 悬 伸 镗 削
但镗刀后刀面与工件内孔表面摩擦较大,镗杆悬 伸较长,故切削条件较差,容易引起振动。镗 削加工生产率不高,要求工人技术水平高;镗 削加工一般用于加工机座、箱体、支架及回转 体等复杂的大型零件上的大直径孔;有位置精 度要求的孔及孔系;亦可加工外圆、端面、平 面,配备附件、专用镗杆和相应装置,可加工 螺纹、孔内沟槽、内外球面等,可以镗削单孔 和多孔组成的孔系。镗孔时,其尺寸精度可达 IT7 ~ IT6 级,孔距精度可达 0.015mm ,表面粗 糙度可达Ra1.6~0.8μ m。如图6.2所示。
镗削加工是以镗刀的旋转运动为主运动,与工件 随工作台的移动(或镗刀的移动)为进给运动相 配合,切去工件上多余金属层的一种加工方法。 它与以工件旋转为主运动的加工方式相比,避 开了大型工件作旋转运动的弊端。如零件外形 大而孔径小,不能高速切削;孔在工件上处于 不对称位置,工件旋转时,就会产生失衡问题。 镗削加工适应能力较强。这是因为镗床的多种 部件都能作进给运动,使其具有加工上的多功 能性。
6.2镗削加工工艺系统组成要素
6.2.1镗床及技术参数 1.卧式镗床
2. 坐标镗床
6.2ห้องสมุดไป่ตู้2镗刀
• • • • • • 1. 镗刀种类 (1)整体式单刃镗刀 (2)精镗微调镗刀 (3)双刃镗刀 (4)镗刀头 (5)镗刀块
2 镗 刀 的 安 装
6.2.3镗床夹具
• (2)镗套
(3)镗床夹具上及与镗床夹具有关的其它结构
第6章 镗削加工方法
6.1镗削的工作内容 镗削加工是用各种镗床(图6.1)对孔进行 镗削加工的加工手段。镗床上对已有孔进行 扩大孔径并提高质量的加工方法。 与钻床比较,镗床可以加工直径较大的孔, 精度较高,且孔与孔的轴线的同轴度、垂直 度、平行度及孔距的精确度均较高。因此, 镗床特别适合加工箱体、机架等结构复杂, 尺寸较大的零件。
- 1、下载文档前请自行甄别文档内容的完整性,平台不提供额外的编辑、内容补充、找答案等附加服务。
- 2、"仅部分预览"的文档,不可在线预览部分如存在完整性等问题,可反馈申请退款(可完整预览的文档不适用该条件!)。
- 3、如文档侵犯您的权益,请联系客服反馈,我们会尽快为您处理(人工客服工作时间:9:00-18:30)。
2、在保证可靠断屑的条件下,采用一定压力的大流 量切削液进行冷却、润滑和排屑,可避免切屑对已加工 表面的划伤。
3、镗刀在切削中产生的径向切削分力由导向块的支 反力来平衡,可减弱镗削中的弯曲振动。
3、合理导向
由于深孔的长径比大,刀杆细而长,刚性较低,易产 生振动,并使加工的孔偏歪而影响加工精度和生产效率 ,因此深孔加工的导向问题需很好的解决。目前,在深 孔加工刀具中,都有2个以上导向块,使刀具在工件内 孔中以3点定圆,自行导向,解决了刀杆刚性不足的问 题。另外,在刀具切入时,还需要有导向装置和辅助支 承。
3.1 滚压加工的特点
滚压加工与切削加工相比,有以下特点:
(1)可降低零件表面的表面粗糙度,一般表面粗糙度R。可达0.2 ~0.05μm,特别是对软金属(如铜、铝及其合金等)可得到很 好的表面粗糙度,部分可代替精磨、研磨、珩磨和抛光等精加工 工序。
(2)强化金属表层,并保持金属纤维组织的完整。一般可使工件 表面层的显微硬度HV比原始硬度提高10%~60%,表面硬化层 可达0.2~5mm;可提高零件的疲劳强度5%~30%,使被加工零 件提高承受交变载荷的能力。
第十二章 深孔加工
第一节 深孔加工的基础知识
1.1 深孔的定义 孔加工分为浅孔加工和深孔加工两类,也包括介于
两者之间的中深孔加工。一般规定孔深L与孔径D之比 大于5~10,即L∕D>5~10的孔称为深孔;L∕D≤5的孔 称为浅孔。
孔深度与直径之比,决定了孔加工工艺系统的刚度 及刀具结构上特点。L∕D增大,工艺系统刚度降低,切 屑排出及冷却、润滑的难度加大。
主轴箱
支撑架
{}
床头花篮
输油器
尾座
2.5 输油器的结构
图3输油器 1—前导向套;2—护盖;3—隔套;4—轴承架;5—中间接;6—圆螺母;7—轴
承架;8—套筒;9—输油器座;10—后导向套;11—锥套;12—调节螺母
2.6 深孔镗刀的结构
深孔镗刀在结构上具有深孔刀具的共性,即有导向 块,有排屑孔或进切屑液孔。深孔镗刀有多种结构形 式,常见的有焊接式硬质合金深孔镗刀、机械夹固式 硬质合金深孔镗刀和机夹可转位式硬质合金深孔镗刀 等。由刀块的位置和刀体内孔的形式,确定镗刀的镗 削方式。
(5)滚压加工与其他精密加工工艺相比,具有较高的 生产率。滚压工具结构简单,制造容易,操作方便, 刀具耐用度高,在普通车床、钻床、镗床上均可使用 。
(6)滚压加工适用于各种被加工材料,如碳素钢、合 金钢、铸铁、有色金属等。但对于原始硬度很高的零 件(超过HB400),其强化效果并不显著。一般以被 滚压材料的表面硬度不超过HB350为宜。
削能校正已有孔上的缺陷,如圆度误差、直线度误差 ,从而获得良好的几何精度和表面粗糙度。一般情况 下,镗孔精度可达IT7~IT8,表面粗糙度Ra可达3.2 ~0.4μm。
深孔镗削兼有普通镗削和深孔钻削的特点 ,深孔镗 削通过以下方法解决振动和镗杆刚性问题以及断削和 排削问题:
深孔镗削正是针对这些问题吸取深孔钻的优点,其特 点是:
图--粗镗头 1—粗镗刀体;2(7—9)—导向键;3—调整螺钉;4—导向合金
5(8—10)—垫片;6—紧定螺钉;11—压紧螺钉;12—镗刀
图—带修光刃的双刃镗刀块 1、刀体12、刀体23、紧固螺钉4、调整螺钉
第三节 深孔滚压加工
滚压加工是在常温状态下用滚压工具对零件表面 施加压力,使金属表面层产生塑性变形,修正零件表 面微观不平度,降低表面粗糙度数值;改变零件表层 的金相组织,形成有利的残余应力分布,提高零件的 物理机械性能和使用寿命。多数情况下,它可代替零 件的表面处理(如表面淬火、镀铬等)及精加工序( 如研磨、珩磨、抛光等)。它是内孔精加工的一种精 密强化加工方法,在机械加工中具有独特的加工意义 。
4、观察镗削过程困难,往往只能根据切屑的颜色或形 状、切削的声音、镗杆的振动来判断镗削过程是否正常 。
2.2 深孔镗削的分类
送进力方向
排削方式
推镗
拉镗
内排削 外排削 前排削 后排削
工序特征
粗镗
精镗
按主运动
工件旋转
刀具旋转
2.3 切削液的注入方式
切削液从镗杆后端输入
切削液从授油器输
2.4 深孔钻镗床的结构
深孔加工在我国20世纪50年代研制了群钻,自1958年开始使用 BTA钻头;70年代,研制并推广喷吸钻法;到1978年,DF法已在我 国设计完成并正式用于生产;1989年成功研制外排屑枪钻系统; 1994年,又成功研制了多尖齿内排屑深孔钻。
深孔加工的设备现多采用常规机床,如深孔钻镗床、深孔磨床 、珩磨机及通用车床改造成的深孔钻镗床。近年来,已出现数控深 孔钻镗床。
图--滚柱滚压工具 1—滚压元件;2—支承体
(2)滚轮式(见图):滚压元件为滚轮,滚轮轴线偏斜一个 角度β,以减小滚轮与工件的实际接触面积,提高单位滚压力 。在滚压时,工件表面与滚轮表面之间产生一定的速度差, 既有相对滚动,也有相对滑动,两种运动形成滚压与挤压的 综合效果,加大了工件表层金属的塑性变形,可强化和改善 工件表面质量。 滚轮式与滚珠式相比其特点是:滚压效果显著,可采用 较大进给量;滚轮寿命长,可以进行修磨;滚轮的材料、几 何形状及偏斜角等的选择余地大,滚压力大,但要求工艺系 统刚性要好,机床的功率要大。
1.3 深孔加工的特点
深孔加工是处于封闭或半封闭状态下进行的,故具有 以下特点:
1不能直接观察到刀具的切削情况。目前只能凭经验或使 用简易的电流(电压)表来判断切削过程是否正常。
2切削热不易传散。一般切削过程中80%的切削热被切屑 带走,而深孔加工只有40%,刀具占切削热的比例较 大,扩散迟、易过热,刃口的切削温度可达600℃,必 须采用强制有效的冷却方式。
(2)加长的导向键(见图11)导向性能好,同时也起到了承 托刀具的作用,及 润滑效果更好。
(4)利用刀头后端的调整螺钉,使加工尺寸更易控制。
(5)可拆卸的导向键,易于更换,节约成本。同时,通过更 换底部垫片,可以随时调整,加工不同孔径。
※ 焊接式深孔镗刀如图5所示,它由硬质合金刀片2、 硬质合金导向块1和刀体3焊接而成。该刀结构简单, 刚性好,制造方便,使用灵活,应用比较广泛。但焊 接式深孔镗刀存在着焊接缺陷,如刀片产生微观裂纹 和硬度降低,刀体随刀片一起报废。并且随着直径增 大,该缺点愈加突出。
图5焊接工深孔镗刀 1—导向块;2—硬质合金刀片;3—刀体
1—调整斜铁;2—刀垫;3—可转位刀片;4—导向块; 5—刀体;6—调整螺钉;7—刀垫压紧螺钉;8—导向块压紧螺钉
※粗镗头 该粗镗头(见下图)是我公司自主研发的深孔加工刀具,适 用于Φ63-Φ320缸筒内孔的粗加工。具有以下特点:
(1)通过尾端的特殊方牙螺纹与镗杆联接,保证与镗杆中心 线等高,更加利于尺寸精度的控制。
切削热不易传散,切屑不易排出,因此必须采用强 制冷却和强制排屑措施。目前采用高压将切削液通过 钻杆或内部直接送入切削区,起到冷却、润滑作用后 ,将切屑由钻杆内部或外部排出,达到强制冷却和排 屑的目的。
2、切屑的处理
排屑问题从切削过程来看,与分屑、卷屑和断屑三方 面密切联系。采用分屑和断屑措施来降低切屑容屑系 数(切屑容积与所切除金属体积之比),并应使切削 过程稳定,避免出现切屑开头突然变化和无规律状态 。
图--工件表面金属层变形
3.3 滚压加工方式
(1)滚珠式(见图):滚压元件为钢球,滚压时它与工件加工 表面呈点状接触,因此所施加的压力虽小,但单位滚压力较大 ,足以使工件表面产生一定的塑性变形。在滚压过程中,滚动 摩擦阻力使钢球随阻力的方向转动,钢球与工件之间只有相对 滚动,而无相对滑动。工件表面不会产生擦伤现象,因而表面 粗糙度较小。同时,钢球磨损均匀,且磨损量较小,使用寿命 较长。这种滚压方式适宜压光刚性较差的工件。
以上三个问题,构成了深孔加工技术的核心,所用的 刀具、装置和设备,构成了深孔加工系统。所以深孔加 工技术可定义为:使用一定压力的冷却润滑液及排屑系 统,采用导向良好的深孔刀具、机床和附加装置,来达 到高效、高精度的加工深孔的目的。
第二节 深孔镗削系统
2.1 深孔镗削的特点 深孔镗削是提高深孔加工精度的一种方法。深孔镗
(3)扩大配合零件的有效接触面积(一般较磨削后大20%左右) ,从而提高了零件的耐磨性和稳定性,改善了与其相配零件的配 合特性,如加速其磨合性、改善相对运动的工作条件、或提高过 盈配合的可靠性等。
(4)滚压加工过程中,工作平稳,受力均匀,产生热量少,一般 不产生表面退火、烧伤和裂纹等缺陷。但若滚压量过大,塑性变 形严重,孔表面易起皮或撕裂。
1.2 深孔加工的发展
1、18世纪初发明了扁钻;
2、1860年美国人改进了扁钻,发明了麻花钻;
3、20世纪初,由于枪炮生产的发展,发明了枪钻;
4、1943年,德国海勒公司发明毕涅耳加工系统,也就是我们常 说的内排屑深孔钻削系统,改进后称BTA法;
5、1963年,山特维克公司发明了喷吸钻法;
6、20世纪70年代中期,日本结合BTA及喷吸钻法的优点发明了DF 法,即单管双进油。
3切屑不易排出。由于孔深,切屑经过的路线长,容易发 生阻塞,造成刀具崩刃。因此,切屑的长短和形状要 加以控制,并要进行强制性排屑。
4工艺系统刚性差。因受孔径尺寸限制,孔的长径比较大 ,钻杆细而长,刚性差,易产生振动,钻孔易走偏, 因而支承导向极为重要。
1.4 深孔加工过程中要解决的问题
1、冷却、润滑与排屑
(7)内孔滚压加工的尺寸范围较大,加工直径为Φ2~ Φ500mm,可加工浅孔和深孔。
由此可见,滚压加工主要功用是精整尺寸、压光表 面、强化表层。不同的滚压方式其功用也有所侧重。 根据工件的尺寸、结构、具体用途、尺寸精度及表面 粗糙度的不同要求,可采用不同滚压方式和不同结构 的内孔滚压工具。