离心风机CFD模拟及改进
FLG40-200离心泵内流场数值模拟及性能改善的开题报告
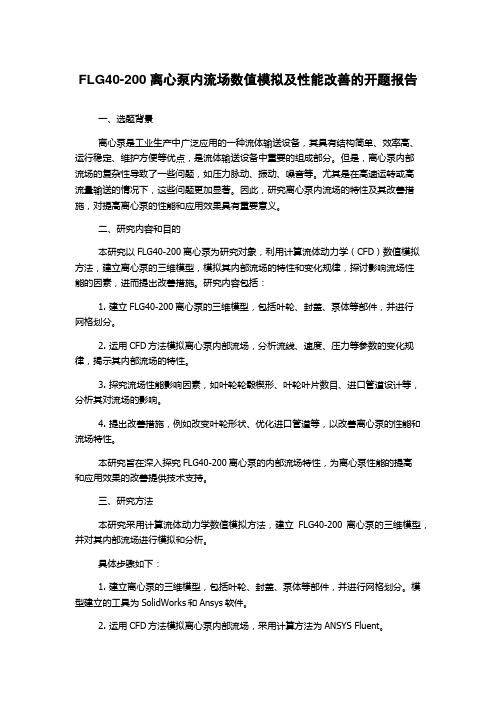
FLG40-200离心泵内流场数值模拟及性能改善的开题报告一、选题背景离心泵是工业生产中广泛应用的一种流体输送设备,其具有结构简单、效率高、运行稳定、维护方便等优点,是流体输送设备中重要的组成部分。
但是,离心泵内部流场的复杂性导致了一些问题,如压力脉动、振动、噪音等。
尤其是在高速运转或高流量输送的情况下,这些问题更加显著。
因此,研究离心泵内流场的特性及其改善措施,对提高离心泵的性能和应用效果具有重要意义。
二、研究内容和目的本研究以FLG40-200离心泵为研究对象,利用计算流体动力学(CFD)数值模拟方法,建立离心泵的三维模型,模拟其内部流场的特性和变化规律,探讨影响流场性能的因素,进而提出改善措施。
研究内容包括:1. 建立FLG40-200离心泵的三维模型,包括叶轮、封盖、泵体等部件,并进行网格划分。
2. 运用CFD方法模拟离心泵内部流场,分析流线、速度、压力等参数的变化规律,揭示其内部流场的特性。
3. 探究流场性能影响因素,如叶轮轮毂楔形、叶轮叶片数目、进口管道设计等,分析其对流场的影响。
4. 提出改善措施,例如改变叶轮形状、优化进口管道等,以改善离心泵的性能和流场特性。
本研究旨在深入探究FLG40-200离心泵的内部流场特性,为离心泵性能的提高和应用效果的改善提供技术支持。
三、研究方法本研究采用计算流体动力学数值模拟方法,建立FLG40-200离心泵的三维模型,并对其内部流场进行模拟和分析。
具体步骤如下:1. 建立离心泵的三维模型,包括叶轮、封盖、泵体等部件,并进行网格划分。
模型建立的工具为SolidWorks和Ansys软件。
2. 运用CFD方法模拟离心泵内部流场,采用计算方法为ANSYS Fluent。
3. 根据模拟结果,分析流线、速度、压力等参数的变化规律,揭示其内部流场的特性。
4. 分析流场性能影响因素,如叶轮轮毂楔形、叶轮叶片数目、进口管道设计等,分析其对流场的影响。
5. 提出改善措施,例如改变叶轮形状、优化进口管道等,以改善离心泵的性能和流场特性。
离心风机的参数化建模及设计分析

叶轮是离心风机的主要部件,由前盘、叶片、后盘和轴盘组成。叶轮的几何形 状、尺寸、叶片数目和制造精度对性能有很大影响。要保证离心风机平稳地转动,
1
华中科技大学硕士学位论文
叶轮需要经静平衡和动平衡的严格校正。按照叶片的形状,叶片可以分为平板形、 圆弧形和机翼形。按叶片出口安放角的大小区分,叶轮分为前向、径向和后向三种 型式。前向叶片的叶片出口安放角大于 90°,叶片顶部向叶轮旋转方向倾斜;径向叶 片的出口安放角等于 90°,叶片顶部是向径向的;后向叶片的叶片安放角小于 90°, 叶片顶部向叶轮旋转的反向倾斜。从气体获得的压力来看,前向叶片最大,径向次 之,后向叶片最小。从效率的角度看,后向叶片最高,径向次之,前向叶片最低。 在相同的流量和转速条件下,要达到相同压力,前向的叶轮尺寸最小,径向次之, 后向最大。叶片的型线以平板直叶片最简单,机翼型叶片最复杂。叶片与盖盘的联 接采用焊接或铆接。焊接叶轮的重量较轻,流道光滑。低、中压小型离心通风机的 叶轮也有采用铝合金铸造的[4]。
风机叶轮离心浇注模改进设计

心 , 而 减 少 了 叶 轮 整 体 的初 始 动 平 衡 量 , 到 减 小 风 机 自振 动 振 幅 。 从 达
关 键 词 :叶 轮 ;叶 片 ;跳 动 ;初 始 动 不 平 衡 量 ;动 平衡 ;振 动
中 图分 类 号 : TG2 3 3 3 .
文 献标识 码 : A
文 章 编 号 :1 7 — 4 7 2 1 ) 10 6 — 3 6 4 6 5 ( 0 2 0 —0 8 0
工 作时 , 叶轮 随 电机 高速 ( 0 / n 旋 转 而产 生 50 0rmi)
强 大风 力 。
1 钢 套 2 铝 体 31 0块 叶 片 均 布 . . .2
图 1 叶 轮
Fi 1 I p le g. m e lr
收 稿 日期 :2 1 - 71 0 10 — 1
作 者 简介 :彭名  ̄ ( 9 4 ) 男 , 1 6 - , 四川 遂 宁人 , 工程 师 , 主要 从 事 产品 工 艺设 计 、 具设 计 。 模
( . t n Own d F co y 5 1 ,Ch n qn 0 3 1 1 Nai o e atr 0 9 o g ig 4 1 3 ,Chn ;2 Ar lg t f e i h n q n ,Ch n qn 0 3 1 i a . my De a e Ofi n C o g ig e c o g ig 4 1 n n n mi a in me h d r m h l o i o i g a d l n t t o .A o a i g s e v n o i o i g r g s twe ea d d,t eo ii a l d i i a o l c tn le ea da p st n n i e r d e i n h rg n l a ed — b a h a m s r d c d S h t h ld s we ee e l it i u e .Th o c n r iyo mp l rse v t h mp l r wa n p r g wa e u e O t a e b a e r v n y ds rb t d t e c n e ti t fi el le e wih t ei el s e — c e e
基于CFD模拟的轴流风机扇叶设计优化研究

基于CFD模拟的轴流风机扇叶设计优化研究摘要:本研究采用计算流体动力学(CFD)模拟方法,旨在优化轴流风机扇叶的设计以提高性能和效率。
通过数值模拟,我们系统地研究了不同扇叶参数对风机性能的影响,并提出了一种优化设计方案,以实现更高的能效和性能。
研究结果表明,通过CFD模拟可以有效地改善轴流风机的性能,并为风机工程领域的进一步发展提供有力支持。
关键词: CFD模拟;轴流风机;扇叶设计;优化;性能一、引言轴流风机作为工业和商业领域中广泛应用的关键设备,对能源效率和性能提出了不断增长的需求。
其中,扇叶作为轴流风机的核心部件,其设计和优化对整个风机系统的性能至关重要。
随着计算流体动力学(CFD)模拟方法的不断发展,研究人员可以更深入地理解风机流场,并进行更精确的性能预测和优化设计。
二、文献综述2.1 轴流风机的发展历程轴流风机作为工业领域的核心设备,其发展历程从19世纪末至今经历了令人瞩目的进步。
早期,轴流风机的设计主要依赖于经验和试验,限制了其性能和效率。
然而,随着科学和工程技术的进步,数学模型、实验室测试和计算流体力学等新方法的应用使轴流风机的设计变得更精确和可预测。
这些技术创新促使了风机的能效提升、噪音降低和寿命延长,从而为各行业带来了更高水平的气流控制和空气处理能力。
2.2 扇叶设计的重要性扇叶作为轴流风机的核心组成部分,其设计对风机性能至关重要。
扇叶的几何形状、叶片数目、叶片角度等参数直接影响风机的效率、噪音产生、能耗和寿命。
一个优化的扇叶设计可以显著提高风机的能效,降低运行成本,减少环境影响。
所以,深入研究和优化扇叶设计是提高轴流风机性能的关键步骤。
近年来,计算流体动力学(CFD)模拟技术的不断发展已经引领了轴流风机研究的新时代。
这一技术的崭新应用为风机工程领域带来了深刻的影响。
通过CFD,研究人员能够以前所未有的准确性模拟轴流风机内部复杂流动现象,如湍流、涡流和分离现象。
这种全面的流场信息为风机性能的深入理解提供了强大工具,并且为设计和优化提供了坚实基础。
多翼离心风机数值计算及改进设计研究

从表 1 中可以看出,采用的 3 种 k-ε 湍流模型所 得到的结果极为接近,并且与试验结果也比较吻合, 这说明了数值计算的结果是合理的,计算方法是可靠 的,同时也说明了采用这 3 种 k-ε 模型计算风机内部 流场均是可行的。从表 1 可以看出,数值计算结果比 试验测量结果偏大,产生该误差的主要原因如下:
( 1) 建模阶段对风机的部分区域进行了简化处 理,从而使得数值计算中的摩擦损失、轮阻损失和泄 漏损失与试验测量结果相比偏小。
( 2) 建模时忽略的一些次要结构,会带来一定 的误差。
( 3) 由于模型的复杂性以及计算条件的限制, 选用的网格类型是非结构网格,精度有限,从而引起 一定的误差。 1. 4 流场分析
对以上 4 个流体区域的连接面,有两种处理方 法: 一种方法是将连接面定义为内边界 ( interior) , 此时就要在几何建模阶段使这个面相邻的两个区域 共用该面; 另一种方法是将连接面定义为交界面 ( interface) ,此时在几何建模阶段,对这个面相邻的 两个区域分别定义一个面,而这两个面的几何位置 和形状是相同的,但拥有不同的名称和标记,并可采 用不同的网格类型。采用第一种方法,在计算中不 需要进行任何处理; 若采用第二种方法,则在计算中 需要通过 Fluent 中的 Define / Grid interface 来实现这 两个面的数据交换[2]。
2 结构参数对风机性能的影响 影响多翼离心风机性能的结构参数很多,如叶片
进口安装角、叶片出口安装角、叶轮宽度比、叶轮内外 径比、叶轮外径、叶片型线、叶片数、蜗壳型线、蜗舌间 距等等。笔者只在转速、叶轮内外径、叶轮宽度不变 的情况下,对叶片进口安装角、叶片出口安装角、叶片 数、叶片型线、蜗壳型线和蜗舌间距这些影响多翼离 心风机性能的结构参数进行数值模拟计算。 2. 1 叶片进口安装角的影响
基于数值模拟的离心风机性能优化

Pe f r an e O ptm ia i n o n r ug lFan Ba e o u e ia m ul to ro m c i z to f Ce t i a f s d n N m r c lSi ain
p r r n e c a g f e t f g l a y me n fc a g n ld s n t lt n a ge a d u i gt e fi s a e b a e T en me - ef ma c h n e o n r u a n b a s o h n i gb a e ’i sa ai n l n s h l h p l d . o c i f l o n o- h u r i
K e wor s: c n rf a a n y d e tiug f n; ume c lsm u ain; ro a c ptmiain l i r a i lto pef r n e o i z to m
1 前 言
工 况及 其 附近运 行 时 , 具有 较 高的效 率 , 有 的风 但
W ANG o, U — o g, Ha W Ya d n OUYANG a Hu
( h nhi i tn nvri ,hnh i 0 20,hn ) Sa ga Ja ogU iesyS ag a 20 4 C ia o t
Ab t a t Ce t f g lfn frt xi o c r e y ma y e p lsb c u e o sc mp ia in o p l ai n st ain T i p 。 sr c : nr u a a o e tl i c n en d b n x e e a s fi o lc t n a p i t i t . h s a i es t o c o u o
离心泵流场的CFD模拟研究
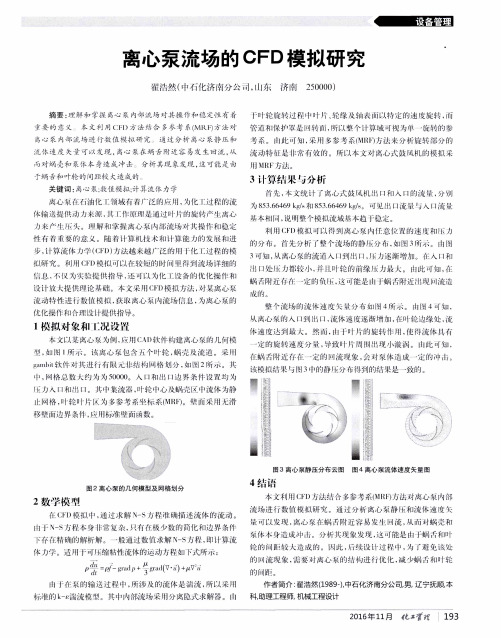
然( r f I 4 f f t 济南 分 公 j , l I I 尔
摘要 : 理 解和 掌握 离心 泵 内部流 场 对其操 作 和稳 定性 有 存
重要 的 意 义 本 文利 用 CF I ) 方法结 合 多参 : 予系( MI F ) 方法 对
离 心 泵 内 部 流 场 进 行 故 值 馍 拟 研 究 通 过 分 析 离心 泵 静 压 和
g a t n l I 软 件对 其进 行 仃 元非结 构 恪 划分 , l 冬 l 2 所求。j f 1 , 总 教 大约 为 乃5 0 0 0 0 。入¨ H j l i 边 界 条什 胃均 为 I f 集流 器 , 叶轮 I 及蜗 先【 i I l I 流体 为肺
济南
2 5 0 0 0 0 )
I 叶轮 旋转 过程 中叶 "、 轮 缘 及轴 = 良 以特 定的述 旋转 , 而
管道 l 羊 l J 护 是 同转 , 所以电 芝 个计弹域 可 } 见 为
・ 抛转的 参
考系。I l I 此可知, 采H J 影参 考系( MI { ¨ 法求 分析 旋转 部 分的 流 动特 址 常 有 效的 。所 以 小文 埘离心 式鼓 风 {  ̄ ] L l f 9 摸f f I 呆
J 1 1 MR F办法 。
流体速 , 乏矢量 可 以发现 , 离心 采荭蜗 舌 附近容 易发 生 回流 , 从 而对蜗 壳和 泵体本 身造 成 P 击 分析其现 象发现 , 这可能 是 由
于蜗 舌 和 叶 轮 的 间距 较 大 造 成 的
3计算
程 的流
分析
关键词 : 离心采: 故 值模拟: 计算流体 力学 离心 油化 I 领域 有荷 r 乏 的 应 , 7 o f t
基于CFD仿真的风力发电机组叶片优化设计

基于CFD仿真的风力发电机组叶片优化设计随着对可再生能源需求的增加,风力发电在现代能源产业中占据着重要地位。
而风力发电机组的叶片作为转动能量的主要组成部分,其设计对于风力发电效率的提高至关重要。
因此,基于CFD (Computational Fluid Dynamics,计算流体动力学)仿真的风力发电机组叶片优化设计成为了当前研究和工程实践的热点之一。
1.概述风力发电机组通过将风能转化为机械能,再经由发电机转化为电能的过程,实现了清洁、可再生能源的利用。
在风力发电机组中,叶片作为风能转化的关键组件,其设计直接影响到发电机组的发电效率和性能。
优化叶片设计可以有效提高风能的转化效率,增加风力发电机组的发电量。
2.风力发电机组叶片设计的挑战风力发电机组叶片设计面临诸多挑战。
首先,由于风能是不稳定的,叶片需要具备良好的自适应能力以适应不同条件下的风能变化。
其次,由于风力发电机组的结构复杂、工作环境恶劣,叶片需要具备较高的强度和耐久性。
同时,为了提高叶片的发电效率,叶片的气动特性也需要得到充分的考虑。
3.CFD在叶片设计中的应用CFD是一种基于数值方法的仿真技术,通过对流动领域中各项物理方程的求解,可以较为准确地预测流场的分布和特性。
在风力发电机组叶片优化设计中,CFD技术的应用可以快速、有效地评估不同叶片设计方案的性能,并指导优化设计过程。
首先,利用CFD技术可以对叶片在不同风速下的气动特性进行模拟和分析。
通过计算流场中的风速、压力等参数,可以获得叶片的气动力,并对叶片设计进行评估和调整。
其次,CFD技术还可以模拟叶片与周围环境的相互作用。
在风力发电机组叶片设计中,考虑叶片与塔筒、浆轮等部件的相互作用对于提高效率和减少振动非常重要。
通过CFD仿真,可以定量分析叶片与周围环境的相互影响,并针对性地进行叶片结构和布置的优化设计。
最后,CFD技术还可以辅助优化叶片的材料选择和制造工艺。
通过模拟和分析叶片在不同材料和工艺条件下的性能,可以选择最佳的材料和工艺参数,提高叶片的强度和耐久性。
- 1、下载文档前请自行甄别文档内容的完整性,平台不提供额外的编辑、内容补充、找答案等附加服务。
- 2、"仅部分预览"的文档,不可在线预览部分如存在完整性等问题,可反馈申请退款(可完整预览的文档不适用该条件!)。
- 3、如文档侵犯您的权益,请联系客服反馈,我们会尽快为您处理(人工客服工作时间:9:00-18:30)。
2005 Fluent 中国用户大会论文集由于CFD计算可以相对准确地给出流体流动的细节,如速度场、压力场、温度场等特性,因而不仅可以准确预测流体产品的整体性能,而且很容易从对流场的分析中发现产品和工程设计中的问题,所以在国外已经逐步得到广泛的应用。
另外,跨学科组合优化设计方法也已经成为复杂叶轮产品的设计平台。
如今,CFD技术运用于风机的实例在我国已不少见,但由于计算机计算能力的限制,模型过于简单。
如单独一个离心叶轮的流道或单独算一个蜗壳;或运用一个流道与蜗壳迭代计算的方法研究风机内部流动,上述模型均忽略了由于蜗壳型线的非对称而导致叶轮各叶道流动呈现的非对称流动特征,而且从离心风机通道内流场分析来看,各部件间的相互影响很严重,所以,必须充分考虑它们之间的相互影响,不能孤立地分别研究[2]。
本文应用Fluent流动分析软件,计算某型号离心通风机全流场,详细得到通风机内部流场流动情况,并根据气动流场,对叶轮前盘形状和蜗壳出口部位等进行优化设计,同时,运用多学科优化平台软件OPTIMUS集成流体计算软件FLUENT,优化计算通风机进口型线,比较集成优化型线与单独用Fluent反复计算的结果,两者基本接近,说明集成优化是可信的。
将流动区域分为三部分:通风机进口部分、叶轮和蜗壳。
进口部分和蜗壳是静止元件,叶轮转动,采用gambit进行参数化建模。
整个通风机的网格数为80 万,网格采用四面体和六面体混合的非结构网格技术。
气体在通风机内流动时,它的气动性能在很大程度上由它本身的造型决定。
由于流道形状、哥氏力和粘性力的影响,通风机内的气体流动十分复杂。
一般认为气流在叶轮内的相对运动和在静止元件内的绝对运动为定常流,而且通风机内的气体压强变化不大,可忽略气体的压缩性。
因此,通风机内的流动是三维、定常、不可压缩流动。
求解相对稳定的、三维不可压缩雷诺平均N-S方程,湍流模型采用标准的εκ−两方程模型,采用一阶迎风格式离散方程,用SIMPLE方法求解控制方程。
在OPTIMUS提供的优化算法中,采用序列二次规划算法。
3 数值计算结果与分析 3.1原通风机建模及数值模拟原有离心通风机存在风量不足、风压不均匀等问题,所以首先对原通风机模型进行数值模拟,分析其内部气流流动状况,找出问题所在。
图 1 原通风机子午面的速度分布表2 原通风机回转面的速度分布叶轮出口部位的速度分布很不均匀,在叶轮前半部分,叶轮不出风反而进风,所以此处有较多逆流存在。
观察叶轮子午面上速度分布如图1所示,可以看到叶轮出口明显的逆流现象。
风机出风口有较多逆流现象,如图2所示。
通过上述流场仿真计算,可以确定原通风机的气动性能很不好。
分析气动流场,认为性能差的原因主要基于三个方面:1叶片进口部位缺乏导流部分,气体流动的流线不能折转,所以造成叶片前半部分压强低,产生逆流。
由于叶轮出口有较多逆流,导致进入蜗壳的气流速度不均匀。
2原模型叶轮采用前向叶片,叶轮的前盘采用平前盘。
平前盘制造简单,但对气流的流动情况有不良影响[3]。
3通风机蜗壳出口的面积过大,所以在蜗壳出口处压力过低而产生较多的逆流。
3.2通风机改型优化计算优化是对通风机改型以得到较好气动性能的过程。
针对原通风机模型气动流场中存在的问题,在结构上作一些相应修改。
3.2.1 改进模型A 针对原通风机模型计算中存在的叶片前半部分逆流现象严重的问题,将叶轮前盘改为弧线型,使计算结果改善。
但由于将叶轮的前盘改为弧形,而使叶轮出口宽度减小,所以为了不降低流量,将叶轮的轴向尺寸增加。
叶轮出口宽度增加到252mm。
如此改动后,叶轮沿子午面速度分布如图3所示。
改为弧形前盘,对气流进行导流,则气动性能改善。
与原模型相比,通风机的出口风压增加24.9%,出口流量增加17%,轴功率增加9.4%,效率增加7.6%。
2005 Fluent 中国用户大会论文集90 气动性能有所改善,但轴功率增加。
通过观察通风机内部气流的流动情况,叶轮进口部位的流动得到好转,但蜗壳出口部位的流动仍然不好,蜗壳出口仍然存在着逆流现象。
3.2.2 改进模型B 在模型A的基础上,把蜗壳出口部位的尺寸减小,消除了蜗壳出口逆流的现象。
蜗壳出口截面的位置没有改变,但尺寸减小。
出口风量有所减小,但转矩减小,轴功率减小,出口总压增加,效率提高。
可见气动特性有很大的提高。
原蜗壳模型改进模型B 图3 蜗壳改动前后z=-0.2 压力分布蜗壳出口改动之后,出口截面尺寸减小,质量流量有所下降,但蜗壳出口逆流面减少,效率提高7.4%,轴功率减小12%。
说明改动使通风机内部的气动流场得到较大改善。
3.2.3 改进模型C 离心式通风机的空气动力特性除了取决于叶轮内部的结构之外,还与通风机的进口形状密切相关,进口又称为集风器,其形状对风机的性能有很大的影响。
在改进模型B的基础上,进一步改善叶轮进口的流动情况。
对进口管道处做成缩放型,从而与叶轮轮盖处的曲线对接,使流动平缓地从轴向转向径向使进口气流缓慢从轴向向径向过渡。
通风机网格数130万。
通过多次改变进气管形状计算,最终得到较好模型。
改进模型的气动性能大为改善,通风机出口总压增加14.1%,出口流量增加6.9%,效率提高8.21%,轴功率增加0.1%。
所以通风机进口部位型线对气流的导向作用非常关键。
若把物体制成流线型,可使边界层的分离点后移,甚至不发生分离,阻力系数大大减小。
在此,一方面减小阻力,另一方面对气流流动起导向作用,使叶轮进口速度分布均匀,流动状况好转。
2005 Fluent 中国用户大会论文集91 图 4 改进模型C沿叶轮子午面速度分布图5 改进模型C回转面速度分布图6 通风机内部气流运动轨迹在子午平面上,流动被很好的导向。
由于蜗壳的存在,使得每一个流道内的速度和压力分布是非对称的。
表一模型改进性能参数一览表出口总压(Pa) 出口流量(kg/s) 转矩(N·m) 轴功率(W) 效率原始模型2014 5.294 122.7 38033.4 22.9% 改进模型A 2515.9 6.193 134.3 41600 30.5% 改进模型B 2951.5 5.746 117.9 36539 37. 9% 改进模型C 3368.8 6.141 118.1 36607 46.1% 通过上述通风机结构的改变,多方案比较,改型后的叶轮气动性能改善。
叶轮出口和蜗壳出口没有逆流,出口流量均匀。
出风量和风压有所提高,效率提高,轴功率基本小于或等于原模型的轴功率。
与原模型相比,通风机的出口流量增加16%,出口总压增加67.3%,轴功率下降3.8%,效率增加23.2%。
4 基于OPTIMUS与FLUENT的离心通风机进口优化在数值化的今天,新产品的开发周期越来越短,产品的成本需要大幅降低,而产品的外延性以及拓展空间又需要极大的扩展,这就需要广泛地采用优化技术进行产品设计。
通过数值模拟通常能够得到一些比较满意的设计方案,但远远不是最佳方案。
CFD已完全具备求解用户设定的一个确定问题的能力,但是工业界对优化设计有越来越强的需求。
目前设计—分析—修改设计—分析的过程仍然是不连续的、孤立的、人工干预的,而非自动的。
虽然分析人2005 Fluent 中国用户大会论文集92 员可以不厌其烦地在屏幕前一次次修改设计参数以寻找最理想方案,但缩短开发周期的压力通常要求分秒必争,人们可能没有更多的时间对数据参数进行手工调整。
最优化技术引入使人们从繁重的凑试工作中解脱出来,同时使设计水平也达到一个新的高度。
多学科多目标优化软件Optimus,具有强大的集成优化能力,可以集成多种CAE/CAD软件。
它可以自动调度通用的流体分析、结构分析软件并由用户设置其它约束条件来完成一个特定优化问题的自动求解过程,使人工的干预降低到最低限度。
这样得到的优化结果是符合目标函数的最佳设计。
根据目标进行设计的理念,彻底颠覆了传统的工程设计过程,从所希望的目标开始,然后定义达到目标所需的设计参数。
本文运用多学科优化平台软件OPTIMUS集成流体计算软件FLUENT6.1和GAMBIT2.1对通风机进口进行优化计算,优化设计建立在仿真分析的基础上。
一个典型的优化过程通常需要经过以下的步骤来完成:(1)参数化建模,利用Fluent软件的参数化建模功能把将要参与优化的数据(设计变量)定义为模型参数,为以后软件修正模型提供可能。
(2) 求解,对参数化模型流场进行数值仿真,把状态参数(约束条件)和目标函数(优化目标)提取出来供优化处理器进行优化参数评价。
(3)优化参数评价,优化处理器根据本次循环提供的优化参数(设计变量、目标函数)与上次循环提供的优化参数作比较之后确定该次循环目标函数是否达到了最小,或者是否达到最优,如果最优,完成迭代,推出优化循环圈,否则,进行下步。
根据已完成的优化循环和当前优化变量的状态修正设计变量,重新投入循环。
通过设计实验方法(DOE)对响应空间作初步的探索,然后对其进行优化计算。
DOE是一种设计空间探索技术,用来对设计空间进行初步探索,可以减小优化问题的计算规模,本例通过对DOE 结果分析,可以看出,只有减小截面尺寸的分析是有效的,因此把变量的变化范围缩小,提高计算效率,减少计算时间。
OPTIMUS中提供了局部优化算法如梯度算法、序列二次规划算法,全局搜索算法如自适应遗传算法、模拟退火法等[4] 。
本例采用了序列二次规划算法,在设定的空间内进行了7次迭代,图7为离心风机的效率随迭代次数变化。
横坐标为迭代次数,纵坐标为风机效率。
图7 优化迭代效率曲线通过对通风机入口优化,在对原通风机模型改动很小的情况下,可以有效提高通风机的性能,出口总压、流量等指标都有很大的提高,效率提高11.41%图8中的左边圆锥形进口为原模型的进口,右边为优化计算得到的进口形状。
通过优化,可以有效改善入口流场的流动,减少不必要的能量损失,明显提高通风机的性能。
优化结果形状与本文3.2.3提供的数值仿真优化模型进口形状基本一致。
人工重复每一个中间态的设计分析工作最终求得一个优化解的过程是漫长和昂贵的,采用OPTIMUS可以提高效率,节省时间,尽快得到问题的最优解。
2005 Fluent 中国用户大会论文集93 图8 优化前后进口形状5总结根据上述对离心通风机内部三维粘性流场进行数值模拟及其改进设计,可以得出如下结论: 1 通过对原离心通风机内部三维粘性流场进行数值模拟,认为该风机气动流场性能比较差,效率只有22.2%.。
主要原因是:(1)叶轮叶片进口缺乏导流部分,所以造成叶片前半部分压强低,产生逆流。
由于叶轮出口有较多逆流,从而导致蜗壳入口流动有逆流,进入蜗壳的气流速度不均匀,恶化了气流在蜗壳内的流动。
(2)原模型叶轮采用前向叶片,叶轮的前盘采用平前盘。