稼动率与设备总合效率(OEE)分析
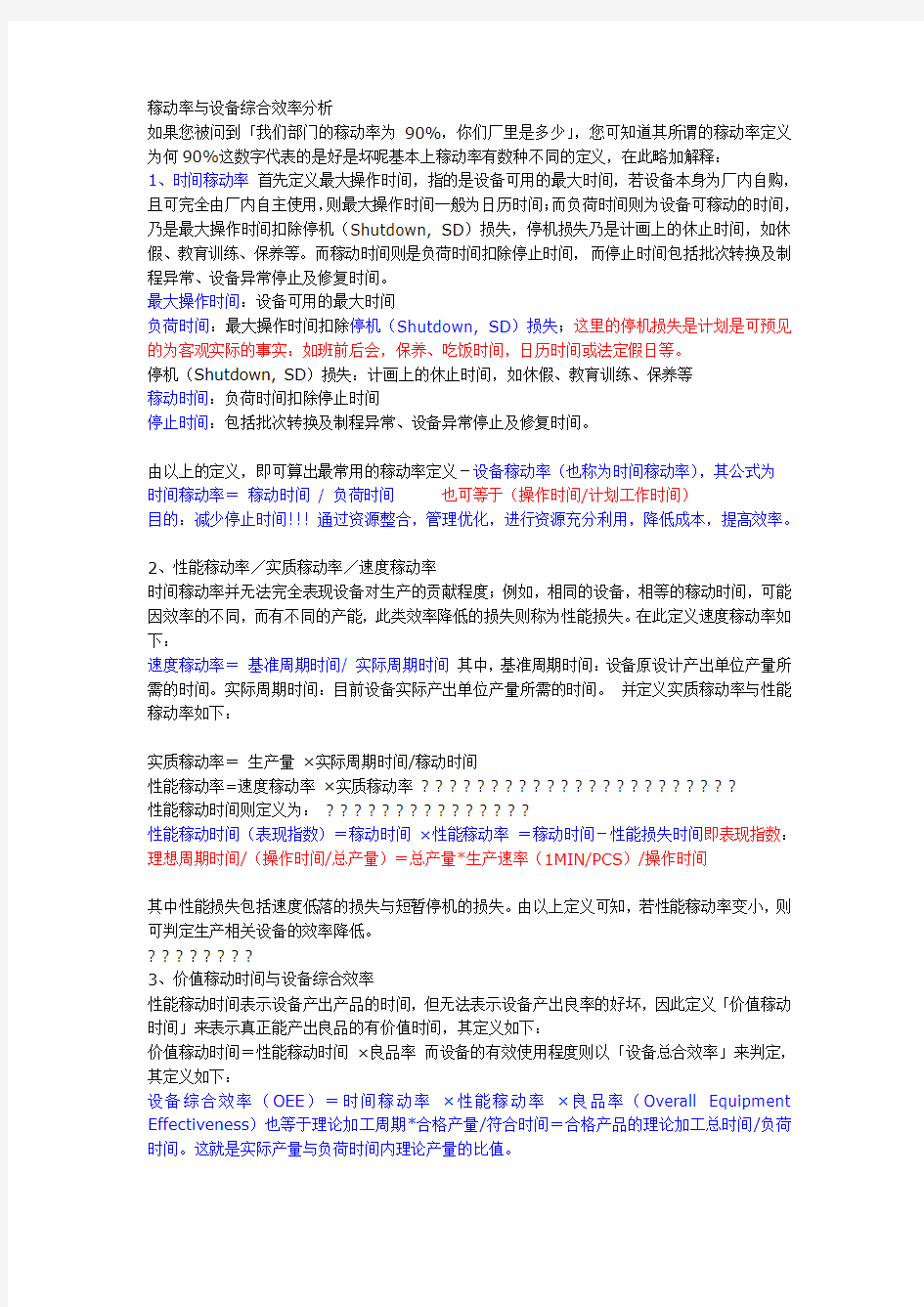

稼动率与设备综合效率分析
如果您被问到「我们部门的稼动率为90%,你们厂里是多少」,您可知道其所谓的稼动率定义为何90%这数字代表的是好是坏呢基本上稼动率有数种不同的定义,在此略加解释:
1、时间稼动率首先定义最大操作时间,指的是设备可用的最大时间,若设备本身为厂内自购,且可完全由厂内自主使用,则最大操作时间一般为日历时间;而负荷时间则为设备可稼动的时间,乃是最大操作时间扣除停机(Shutdown, SD)损失,停机损失乃是计画上的休止时间,如休假、教育训练、保养等。而稼动时间则是负荷时间扣除停止时间,而停止时间包括批次转换及制程异常、设备异常停止及修复时间。
最大操作时间:设备可用的最大时间
负荷时间:最大操作时间扣除停机(Shutdown, SD)损失;这里的停机损失是计划是可预见的为客观实际的事实:如班前后会,保养、吃饭时间,日历时间或法定假日等。
停机(Shutdown, SD)损失:计画上的休止时间,如休假、教育训练、保养等
稼动时间:负荷时间扣除停止时间
停止时间:包括批次转换及制程异常、设备异常停止及修复时间。
由以上的定义,即可算出最常用的稼动率定义-设备稼动率(也称为时间稼动率),其公式为
时间稼动率=稼动时间/ 负荷时间也可等于(操作时间/计划工作时间)
目的:减少停止时间!!!通过资源整合,管理优化,进行资源充分利用,降低成本,提高效率。
2、性能稼动率/实质稼动率/速度稼动率
时间稼动率并无法完全表现设备对生产的贡献程度;例如,相同的设备,相等的稼动时间,可能因效率的不同,而有不同的产能,此类效率降低的损失则称为性能损失。在此定义速度稼动率如下:
速度稼动率=基准周期时间/ 实际周期时间其中,基准周期时间:设备原设计产出单位产量所需的时间。实际周期时间:目前设备实际产出单位产量所需的时间。并定义实质稼动率与性能稼动率如下:
实质稼动率=生产量×实际周期时间/稼动时间
性能稼动率=速度稼动率×实质稼动率? ? ? ? ? ? ? ? ? ? ? ? ? ? ? ? ? ? ? ? ? ? ?
性能稼动时间则定义为:? ? ? ? ? ? ? ? ? ? ? ? ? ? ?
性能稼动时间(表现指数)=稼动时间×性能稼动率=稼动时间-性能损失时间即表现指数:理想周期时间/(操作时间/总产量)=总产量*生产速率(1MIN/PCS)/操作时间
其中性能损失包括速度低落的损失与短暂停机的损失。由以上定义可知,若性能稼动率变小,则可判定生产相关设备的效率降低。
? ? ? ? ? ? ? ?
3、价值稼动时间与设备综合效率
性能稼动时间表示设备产出产品的时间,但无法表示设备产出良率的好坏,因此定义「价值稼动时间」来表示真正能产出良品的有价值时间,其定义如下:
价值稼动时间=性能稼动时间×良品率而设备的有效使用程度则以「设备总合效率」来判定,其定义如下:
设备综合效率(OEE)=时间稼动率×性能稼动率×良品率(Overall Equipment Effectiveness)也等于理论加工周期*合格产量/符合时间=合格产品的理论加工总时间/负荷时间。这就是实际产量与负荷时间内理论产量的比值。
例题:
设某设备每天工作8小时,计划班前停机10Min,故障停机30 Min,设备调整35 Min,产品理论加工周期(标准工时)1Nin/件,1天共加工400件,有20件废品求设备综合效率(OEE):时间稼动率(可用率)=8*60-10-30-35/(8*60-10)*100%=405/470=86.17% 性能稼动率(表现指数)=400/405=98.76%
量品率(质量指数)=(400-20)/400*100%=380/400=95%
OEE=86.17%*98.76%*95%=80.85%
按OEE=合格产品的理论加工总时间/负荷时间=(400-20)*1/(8*60-10)*100%=80.85%也可更方便得出OEE的结果,只是不能很清晰地分析出时间稼动率,性能稼动率和良率因素影响,做出最终的改善方案。
设备综合效率OEE的理解
设备综合效率OEE的理解 设备综合效率OEE考虑了三个方面,设备的工作时间、性能和质量水平。用公式表示为:设备综合效率=时间开动率*性能开动率*合格率 时间开动率反映了设备的时间利用情况,性能开动率反映了设备性能的发挥情况,合格率反映了设备的有效工作情况。 a.时间开动率=实际工作时间/计划工作时间 计划工作时间=每班可用时间-计划停机时间计划停机时间主要包括计划 维护、晨会等所需时间; 实际工作时间=计划工作时间-非计划停机时间非计划停机时间主要包括设 备故障、产品换型、设备调整等消耗的时间; b.性能开动率,是指理论产出与实际产出的比值,他考虑两个方面:净开动率和速度 运转率 性能开动率=净开动率*速度运转率 净开动率用以测量设备稳定性、小停顿造成的损失、小问题及及试制造成的损失。 净开动率=(产量*实际节拍)/实际工作时间 速度运转率反映了设备由于老化或维护不良,达不到设计的或理论的节拍所造成的 损失。 速度运转率=理论节拍/实际节拍 由净开动率和速度运转率的公式可以简化性能开动率公式: 性能开动率=(产量*理论节拍)/实际工作时间 综合以上各公式,整理设备综合效率公式: 设备综合效率=【(产量*理论节拍)/计划工作时间】*合格率 来个例题:若每班单班生产,每班工作8小时,每班可用时间为480分钟,其中有15分钟的换型时间,10分钟班前例会,30分钟非计划设备故障。问计划工作时间和时间开动率多少? 计划工作时间=480-10=470;实际工作时间=470-15-30=425;时间开动率=425/470=90.4% 若一个班加工了300件,实际节拍时间是每件1分钟,理论节拍时间是每件40秒,问净开动率、速度运转率和性能开动率是多少? 净开动率=300*1/425=70.59% 速度运转率=40s/60s=67.7% 性能开动 率=70.59%*67.7%=47.08% 若质量合格率为95%,则设备的综合效率OEE=90.4%*47.08%*95%=40.4%
设备综合效率计算
设备综合效率计算 影响设备综合效率的主要原因是停机损失、速度损失和废品损失。它们分别由时间开动率、性能开动率和合格品率反映出来,故得到下面设备综合效率公式:设备综合效率=时间开动率×性能开动率×合格品率 时间开动率=(工作时间/负荷时间)×100% 这里,负荷时间为规定的作业时间除去每天的停机时间,即 负荷时间=总工作时间-计划停机时间 工作时间则是负荷时间除去那些非计划停机时间,如故障停机、设备调整和更换刀具、工夹具停机等。 【例1】若总工作时间为8h,班前计划停机时间是20min,而故障停机为20min,安装工夹具时间为20min,调整设备时间为20min。于是负荷时间=480-20=460min 开动时间=460-20-20=400min 时间开动率=速度开动率×净开动率 速度开动率=(理论加工周期/实际加工周期)×100% 净开动率=(加工数量×实际加工周期/开动时间)×100% 这里,理论加工周期是按照标准的加工进给速度计算得到的,而实际的加工周期一般要比理论加工周期长。开动时间即是设备实际用于加工的时间,也就是工作时间减去计划停机和非计划停机所得时间,或是负荷时间减去非计划停机所得时间。 实际上 性能开动率=速度开动率×净开动率= 从计算上看,用简化了的公式也可以得到同样的结果。之所以用速度开动率和净开动率共同表示性能开动率,是因为从计算过程更容易看出性能开动率的损失原因。 【例2】有400件零件加工,理论加工周期为0.5min,实际加工周期为0.8min。则 净开动率=0.8×400/400=80% 速度开动率=0.5/0.8=62.5% 性能开动率=80%×62.5%=50% 合格品率=((加工数量-不合格品数量)/加工数量)×100% 【例3】如果仍延用上面的例子,假如设备合格品率为98%,则 设备综合效率(全效率)=87%×50%×98%=42. 6% 我们把上面的公式和例子总结成以下的序列,得到 (A)每天工作时间=60×8=480min。 (B)每天计划停机时间(生产、维修计划、早晨会议等)=20min。 (C)每天负荷时间=A-B=460min。 (D)每天停机损失=60min(其中故障停机=20min,安装准备=20min,调整=20min)。 (E)每天开动时间=C-D=400min。 (F)每天生产数量=400件。
设备综合效率OEE的计算方法
OEE的计算方法 OEE(Overall Equipment Effectiveness), 即设备综合效率,其本质就是设备负荷时间内实际产量与理论产量的比值。企业在进行OEE计算时常常遇到很多迷惑的问题,如工厂停水、停电、停气、停汽使设备不能工作,等待定单、等待排产计划、等待检查、等待上一道工序造成的停机,不知如何计算。本文引入非设备因素停机的概念,修改了OEE的算法,使计算得到的OEE更能够真实反映设备维护的实际状况,让设备完全利用的情况由完全有效生产率这个指标来反映。本文同时介绍了在不同情况下如何分析设备损失的PM分析流程。 1、 OEE表述和计算实例 OEE= 时间开动率×性能开动率×合格品率 其中,时间开动率 = 开动时间/负荷时间 而,负荷时间 = 日历工作时间-计划停机时间 开动时间 = 负荷时间–故障停机时间–设备调整初始化时间 性能开动率 = 净开动率×速度开动率 而,净开动率 = 加工数量×实际加工周期/开动时间 速度开动率 = 理论加工周期/实际加工周期 合格品率 = 合格品数量/ 加工数量 在OEE公式里,时间开动率反映了设备的时间利用情况;性能开动率反映了设备的性能发挥情况;而合格品率则反映了设备的有效工作情况。反过来,时间开动率度量了设备的故障、调整等项停机损失,性能开动率度量了设备短暂停机、空转、速度降低等项性能损失;合格品率度量了设备加工废品损失。 OEE还有另一种表述方法,更适用于流动生产线的评估, 即 OEE= 时间开动率×性能开动率×合格品率 而,时间开动率 = 开动时间/计划利用时间 而,计划利用时间 = 日历工作时间-计划停机时间 开动时间 = 计划利用时间–非计划停机时间 性能开动率 = 完成的节拍数/计划节拍数 其中,计划节拍数 = 开动时间/标准节拍时间
设备稼动率
一)设备稼动率: 二) 1.(最大操作时间):指的是设备可用的最大时间,若设备本身为?S内自?,且可完 全由?S内自主使用,则最大操作时间一般为日历时间。EW C 5?plb 2.(负荷时间):则为设备可稼动的时间,乃是(最大操作时间)扣除停机(Shutdown, SD)损失,停机损失乃是计划上的休止时间,如休假、教育训练、保养等。X A ^7M 3.(稼动时间):则是(负荷时间) - (停线时间),而停线时间包括批次转换及制程?常、 设备?常停止及修?蜁r间。D,VPfN6\*O 由以上的定义,即可算出最常用的稼动率定义—设备稼动率(也称为时间稼动率), 其公式为-!.\|-4` 设备稼动率= 稼动时间∕负荷时间n] ?I- R (二)性能稼动率∕?质稼动率∕速度稼动率}O jS:a1 时间稼动率?K无法完全表现设备对生产的贡献程度:例如,相同的设备,相等的 稼动时间,可能因效率的不同,而有不同的产能,此?效率降低的损失则称为性能 损失。在此定义速度稼动率如下:K $ L+ K: 速度稼动率=基准周期时间∕?际周期时间V9Qed |[gd 其中,[MBBgsapC! 基准周期时间:设备原设计产出单位产量所需的时间。z -Q G 02 ?际周期时间:目前设备?际产出单位产量所需的时间。?K定义?质稼动率与性能 稼动率如下:,] $ Z _T' ?质嫁动率= 生产量* ?际周期时间∕稼动时间G7p V> 性能稼动率= 速度稼动率* ?质稼动率R5?G# 0 性能稼动时间= 稼动时间* 性能稼动率= 稼动时间- 性能损失时间&yA n 稼动率是一个重要的指标, 如果您被问到“我们部门的稼动率为90%,你们厂里是多少?”,您可知道其所谓的稼动率定义为何?90%这数字代表的是好?是坏呢?基本上稼动率有数种不同的定义,在此略加解释: 1、时间稼动率首先定义最大操作时间,指的是设备可用的最大时间,若设备本身为厂内自购,且可完全由厂内自主使用,则最大操作时间一般为日历时间;而负荷时间则为设备可稼动的时间,乃是最大操作时间扣除停机(Shutdown, SD)损失,停机损失乃是计画上的休止时间,如休假、教育训练、保养等。而稼动时间则是负荷时间扣除停止时间,而停止时间包括批次转换及制程异常、设备异常停止及修复时间。 最大操作时间:设备可用的最大时间 负荷时间:最大操作时间扣除停机(Shutdown, SD)损失; 停机(Shutdown, SD)损失:计画上的休止时间,如休假、教育训练、保养等 稼动时间:负荷时间扣除停止时间 停止时间:包括批次转换及制程异常、设备异常停止及修复时间。 由以上的定义,即可算出最常用的稼动率定义-设备稼动率(也称为时间稼动率),其公式为 时间稼动率=稼动时间/ 负荷时间 目的:减少停止时间!!!通过资源整合,管理优化,进行资源充分利用,降低成本,提高效率。 2、性能稼动率/实质稼动率/速度稼动率 时间稼动率并无法完全表现设备对生产的贡献程度;例如,相同的设备,相等的稼动时间,可能因效率的不同,而有不同的产能,此类效率降低的损失则称为性能损失。在此定义速度稼动率如下: 速度稼动率=基准周期时间/ 实际周期时间 其中,基准周期时间:设备原设计产出单位产量所需的时间。实际周期时间:目前设备实际产出单位产量所需的时间。并定义实质稼动率与性能稼动率如下: 实质稼动率=生产量×实际周期时间/稼动时间 性能稼动率=速度稼动率×实质稼动率 性能稼动时间则定义为: 性能稼动时间=稼动时间×性能稼动率=稼动时间-性能损失时间 其中性能损失包括速度低落的损失与短暂停机的损失。由以上定义可知,若性能稼动率变小,则可判定生产相关设备的效率降低。 3、价值稼动时间与设备总合效率 性能稼动时间表示设备产出产品的时间,但无法表示设备产出良率的好坏,因此定义「价值稼动时间」来表示真正能产出良品的有价值时间,其定义如下: 价值稼动时间=性能稼动时间×良品率而设备的有效使用程度则以「设备总合效率」来判定,其定义如下: 设备总合效率=时间稼动率×性能稼动率×良品率 设备管理好帮手 -----OEE(设备综合效率)计算方式 纸箱厂进行整体生产时规划时,目标之一就是提高设备的使用效率,让每台设备对 的每个零件都能最大限度地发挥其潜力即生产能力,并且能够始终保持稳定状态。 为了使生产速度最大化,必须首先了解导致生产速度下降的原因,并采取相应的措施。在这些解决措施中,设备综合效率分析(OEE)是一种非常实用的、有效的设备管理方式,可以帮我们了解设备的潜在的生产能力。 (OEE)是世界级稳定性组织(WCR)中一个非常重要的测量手段.借助OEE,可以与六大损失相关联(故障/停机损失、换装和调试损失、空闲和暂停损失、减速损失、质量缺陷和返工损失、启动损失)。有三大测量指标:设备利用率、生产速度和合格产品率。 六大损失包括 故障/停机损失(Equipment Failure/Breakdown) 设备故障/停机损失是指故障停机造成时间损失,这将减少合格产品数量。如果出现设备故障或停机,就需要对设备进行维修处理。在平时,应该采取正确预防性保养措施、改进操作程序、改进生产设计以防止故障发生。要减少设备故障,生产部门与维修商之间良好的合作与沟通也非常重要。 预防性保养技术包括震动检测、定期上油和温度记录分析,用以防止设备故障的发生。如果出现机器故障,可以采取根本原因分析(RCFA)法来确定导致故障的根源。RCFA可以使企业解决故障问题从事后处理转变为事前处理。RCFA切实有效的“寻根溯源”解决方案能够消除或转移故障发生以及造成的影响。 换装和调试损失(Setup and Adjustment) 换装和调试损失是指在生产不同产品时定单切换时间损失。定单切换时间损失不归入计划停机时间范畴。 空闲和暂停损失(Ldling and Minorsyoppage Losses) 空闲和暂停损失是指由于错误操作而停顿或设备本身发生的短暂停机时间损失。通常在5-10分钟之间,还包括一些小调整或类似清洗之类的活动造成的时间损失。不包括运送原料造成的时间损失。 减速损失(Reduced Speed Losses) OEE-稼动率相关报表填表说明 OEE-稼动率总报表自4月1日试用以来,经逐步规范和完善,基本运行正常,为保证各项数据的现场记录、报表录入、检查、分析的准确、真实、及时,现将报表填报规范说明如下: 一、总说明 1、为准确、真实、及时反映、了解、掌握生产现场的产品、生产、设备等信息,拟制本表。 2、本报表系统由SMT生产日报表、生产报表登入区、标准工时登入区、PM 分析表、各条线稼动率可视化、综合生产指标&OEE指标可视化组成。 3、SMT生产日报表由当班作业人员填写。生产报表登入区、标准工时登入区的白色区域由班长登入。其他灰色区或其他工作表为工时自动计算,不允许改动。 二、报表栏目说明 (一)SMT生产日报表 1、订单号:该产品销售合同订单内部编号。 2、产品名称:指产品的名称,如高清、标清、光猫、前控、卡板等。 3、面别。指印制板的的A/B面,直接在下拉条进行选择。 4、开始时间。产品开始导入时间。 4、结束时间。产品最后一块下线时间。 5、产量。该产品生产数量。 6、节假日。指因计划安排放假引起的停机时间。 7、会议、培训、教育。指上班后进行的例行的计划性的早会、晚会、培训、教育会等停机时间。 8、计划维保、点检。指列入计划的对设备进行的维护、保养、点检等活动引起的停机时间。 9、停水、电、气。指外部因素引起的生产要素水电气等无供应引起的停机时间。 10、无生产排单。指因无市场订单造成的机器停止时间。 11、交接班。指每班人员上下班对设备、产品等进行的交接引起的停机时间。 12、转产。指上单产品最后一块进入回流炉到下单产品第一块进入回流炉的时间。 13、首检。指第1-3块板的质量检验、确认时间。 14、设备故障、事故。指设备运行中出现偶发故障或人为因素引发的事故导致的机器停止时间。 15、调试设备。指生产中进行的设备参数、零件、程序、物料等调整引起的机器停止时间。 16、质量问题。是指生产过程中因处理产品质量问题引发的停机时间。 17、待料。指生产过程中因物料不足引发的停机待料时间。 18、结单。指上单产品正常产品生产完时打叉板等问题产品的时间。 (Overall Equipment Effectiveness), 即设备综合效率,其本质就是设备负荷时间 内实际产量与理论产量的比值。企业在进行OEE计算时常常遇到很多迷惑的问题,如工厂停水、停电、停气、停汽使设备不能工作,等待定单、等待排产计划、等待检查、等待上一道工序造成的停机,不知如何计算。本文引入非设备因素停机的概念,修改了OEE的算法,使计算得到的OEE更能够真实反映设备维护的实际状况,让设备完全利用的情况由完全有效生产率这个指标来反映。本文同时介绍了在不同情况下如何分析设备损失的PM分析流程。 1、 OEE表述和计算实例 OEE= 时间开动率×性能开动率×合格品率 其中,时间开动率 = 开动时间/负荷时间 而,负荷时间 = 日历工作时间-计划停机时间 开动时间 = 负荷时间–故障停机时间–设备调整初始化时间 性能开动率 = 净开动率×速度开动率 而,净开动率 = 加工数量×实际加工周期/开动时间 速度开动率 = 理论加工周期/实际加工周期 合格品率 = 合格品数量/ 加工数量 在OEE公式里,时间开动率反映了设备的时间利用情况;性能开动率反映了设备的性能发挥情况;而合格品率则反映了设备的有效工作情况。反过来,时间开动率度量了设备的故障、调整等项停机损失,性能开动率度量了设备短暂停机、空转、速度降低等项性能损失;合格品率度量了设备加工废品损失。 OEE还有另一种表述方法,更适用于流动生产线的评估, 即 OEE= 时间开动率×性能开动率×合格品率 而,时间开动率 = 开动时间/计划利用时间 而,计划利用时间 = 日历工作时间-计划停机时间 开动时间 = 计划利用时间–非计划停机时间 稼动率与设备综合效率分析 如果您被问到「我们部门的稼动率为90%,你们厂里是多少?」,您可知道其所谓的稼动率定义为何?90%这数字代表的是好?是坏呢?基本上稼动率有数种不同的定义,在此略加解释:1、时间稼动率首先定义最大操作时间,指的是设备可用的最大时间,若设备本身为厂内自购,且可完全由厂内自主使用,则最大操作时间一般为日历时间;而负荷时间则为设备可稼动的时间,乃是最大操作时间扣除停机(Shutdown, SD)损失,停机损失乃是计画上的休止时间,如休假、教育训练、保养等。而稼动时间则是负荷时间扣除停止时间,而停止时间包括批次转换及制程异常、设备异常停止及修复时间。 最大操作时间:设备可用的最大时间 负荷时间:最大操作时间扣除停机(Shutdown, SD)损失;这里的停机损失是计划是可预见的为客观实际的事实:如班前后会,保养、吃饭时间,日历时间或法定假日等。 停机(Shutdown, SD)损失:计画上的休止时间,如休假、教育训练、保养等 稼动时间:负荷时间扣除停止时间 停止时间:包括批次转换及制程异常、设备异常停止及修复时间。 由以上的定义,即可算出最常用的稼动率定义-设备稼动率(也称为时间稼动率),其公式为 时间稼动率=稼动时间/ 负荷时间也可等于(操作时间/计划工作时间) 目的:减少停止时间!!!通过资源整合,管理优化,进行资源充分利用,降低成本,提高效率。 2、性能稼动率/实质稼动率/速度稼动率 时间稼动率并无法完全表现设备对生产的贡献程度;例如,相同的设备,相等的稼动时间,可能因效率的不同,而有不同的产能,此类效率降低的损失则称为性能损失。在此定义速度稼动率如下: 速度稼动率=基准周期时间/ 实际周期时间其中,基准周期时间:设备原设计产出单位产量所需的时间。实际周期时间:目前设备实际产出单位产量所需的时间。并定义实质稼动率与性能稼动率如下: 实质稼动率=生产量×实际周期时间/稼动时间 性能稼动率=速度稼动率×实质稼动率 性能稼动时间则定义为: 性能稼动时间(表现指数)=稼动时间×性能稼动率=稼动时间-性能损失时间即表现指数:理想周期时间/(操作时间/总产量)=总产量*生产速率(1MIN/PCS)/操作时间 其中性能损失包括速度低落的损失与短暂停机的损失。由以上定义可知,若性能稼动率变小,则可判定生产相关设备的效率降低。 3、价值稼动时间与设备综合效率 性能稼动时间表示设备产出产品的时间,但无法表示设备产出良率的好坏,因此定义「价值稼动时间」来表示真正能产出良品的有价值时间,其定义如下: 价值稼动时间=性能稼动时间×良品率而设备的有效使用程度则以「设备总合效率」来判定,其定义如下: 设备综合效率(OEE)=时间稼动率×性能稼动率×良品率(Overall Equipment Effectiveness)也等于理论加工周期*合格产量/符合时间=合格产品的理论加工总时间/负荷时间。这就是实际产量与负荷时间内理论产量的比值。 设备综合效率OEE详解 OEE的定义 一般,每一个生产设备都有自己的最大理论产能,要实现这一产能必须保证没有任何干扰和质量损耗。当然,实际生产中是不可能达到这一要求,由于许许多多的因素,车间设备存在着大量的失效: 例如除过设备的故障,调整以及设备的完全更换之外,当设备的表现非常低时,可能会影响生产率,产生次品,返工等。 OEE是一个独立的测量工具,它用来表现实际的生产能力相对于理论产能的比率。国际上对OEE的定义为:OEE是Overall Equipment Effectiveness(设备综合效率)的缩写,它由可用率,表现性以及质量指数三个关键要素组成,即: OEE=可用率X 表现性X质量指数。 其中: 可用率=操作时间/ 计划工作时间 它是用来考虑停工所带来的损失,包括引起计划生产发生停工的任何事件,例如设备故障,原料短缺以及生产方法的改变等。 表现性=理想周期时间/ (操作时间/ 总产量)=(总产量/ 操作时间)/ 生产速率 表现性考虑生产速度上的损失。包括任何导致生产不能以最大速度运行的因素,例如设备的磨损,材料的不合格以及操作人员的失误等。 质量指数=良品/总产量 质量指数考虑质量的损失,它用来反映没有满足质量要求的产品(包括返工的产品)。 利用OEE的一个最重要目的就是减少一般制造业所存在的六大损失:停机损失、换装调试损失、暂停机损失、减速损失、启动过程次品损失和生产正常运行时产生的次品损失。下面表格是六大损失的说明及其与OEE的关系: 表一六大损失与OEE的关系 OEE计算实例 我们举一个例子来说明OEE的计算方法: 设某设备某天工作时间为8h, 班前计划停机15min, 故障停机30min,设备调整25min, 产品的理论加工周期为0.6 min/件, 一天共加工产品450件, 有20件废品, 求这台设备的OEE。 根据上面可知: 设备综合效率 影响设备综合效率的主要原因是停机损失、速度损失和废品损失。它们分别由时间开动率、性能开动率和合格品率反映出来,故得到下面设备综合效率公式: 设备综合效率=时间开动率×性能开动率×合格品率 这里,负荷时间为规定的作业时间除去每天的停机时间,即 负荷时间=总工作时间-计划停机时间 工作时间则是负荷时间除去那些非计划停机时间,如故障停机、设备调整和更换刀具、工夹具停机等。 【例1】若总工作时间为8h,班前计划停机时间是20min,而故障停机为20min,安装工夹具时间为20min,调整设备时间为20min。于是 负荷时间=480-20=460min 开动时间=460-20-20=400min 时间开动率=速度开动率×净开动率 这里,理论加工周期是按照标准的加工进给速度计算得到的,而实际的加工周期一般要比理论加工周期长。开动时间即是设备实际用于加工的时间,也就是工作时间减去计划停机和非计划停机所得时间,或是负荷时间减去非计划停机所得时间。 实际上 从计算上看,用简化了的公式也可以得到同样的结果。之所以用速度开动率和净开动率共同表示性能开动率,是因为从计算过程更容易看出性能开动率的损失原因。 【例2】有400件零件加工,理论加工周期为0.5min,实际加工周期为0.8min。则 净开动率=0.8×400/400=80% 速度开动率=0.5/0.8=62.5% 性能开动率=80%×62.5%=50% 【例3】如果仍延用上面的例子,假如设备合格品率为98%,则 设备综合效率(全效率)=87%×50%×98%=42. 6% 我们把上面的公式和例子总结成以下的序列,得到 竭诚为您提供优质文档/双击可除oee设备综合效率表格 篇一:oee设备综合效率三种叫法和计算公式并举例子oee(设备综合效率)是衡量设备综合性时间损失大小的指标,反应设备在负荷时间内有 多少时间是有价值的开动时间。 叫法之一: oee=时间开动率×性能开动率×良品率 即: (1)〔时间开动率〕:是衡量测定因故障、准备、调整等导致停止损失大小的指标。 时间开动率=(负荷时间—停止时间)/负荷时间*100% (2)〔性能开动率〕:是衡量因空转、小停工及速度降低等导致时间损失大小的指标。 性能开动率=(基准节拍*产量)/开动时间*100% (3)〔良品率〕:是衡量保证充分满足消费者质量要求的指标。 良品率=合格品件数/生产总件数*100% 叫法之二: oee=时间利用率*设备性能率*产品合格率=(合格的产 品*设计速度)/负荷时间 1.时间利用率=(负荷时间-停机损失)/负荷时间 *100%=(有效)利用时间/负荷时间 2.设备性能率=(生产产品数*设计速度)/利用时间*100% 3.质量合格率=(生产产品数-不合格品)/生产产品数 *100% 其实:设计速度即基本节拍 工厂/车间的设备综合效率 =(1#设备综合效率*产量+2#设备综合效率*产量+…+n#设备综合效率*产量)÷总产量 叫法之三: oee=可使用率x工作表现率x品质率 1.可使用率:指实际运转时间与可用时间(负荷时间)之比。 (1)可用时间:指从一天(或一个月)的工作时间中, 减去生产计划、计划保养,以及日 常管理上必要的的停顿时间后所剩下的时间。 (2)停机时间(停止时间):指因故障、setup、调整、更换模具等所停止的时间。 (3)公式:可使用率=(可用时间-停机时间)/可用时 稼动率的计算方法 时间稼动率:首先定义最大操作时间,指的是设备可用的最大时间,若设备本身为厂内自购,且可完全由厂内自主使用,则最大操作时间一般为日历时间;而负荷时间则为设备可稼动的时间,乃是最大操作时间扣除停机(Shutdown,SD)损失,停机损失乃是计划上的休止时间,如休假、教育训练、保养等。而稼动时间则是负荷时间扣除停止时间,而停止时间包括批次转换及制程异常、设备异常停止及修复时间。 最大操作时间:设备可用的最大时间负荷时间:最大操作时间扣除停机(Shutdown,SD)损失; 停机(Shutdown,SD)损失:计画上的休止时间,如休假、教育训练、保养等 稼动时间:负荷时间扣除停止时间 停止时间:包括批次转换及制程异常、设备异常停止及修复时间。 由以上的定义,即可算出最常用的稼动率定义-设备稼动率(也称为时间稼动率),其公式为时间稼动率=稼动时间/负荷时间 目的:减少停止时间!!!通过资源整合,管理优化,进行资源充分利用,降低成本,提高效率。 性能稼动率/实质稼动率/速度稼动率 时间稼动率并无法完全表现设备对生产的贡献程度; 例如,相同的设备,相等的稼动时间,可能因效率的不同,而有不同的产能,此类效率降低的损失则称为性能损失。在此定义速度稼动率如下:速度稼动率=基准周期时间/实际周期时间 其中,基准周期时间:设备原设计产出单位产量所需的时间。实际周期时间:目前设备实际产出单位产量所需的时间。并定义实质稼动率与性能稼动率如下: 实质稼动率=生产量×实际周期时间/稼动时间 性能稼动率=速度稼动率×实质稼动率 性能稼动时间则定义为:性能稼动时间=稼动时间×性能稼动率=稼动时间-性能损失时间 其中性能损失包括速度低落的损失与短暂停机的损失。由以上定义可知,若性能稼动率变小,则可判定生产相关设备的效率降低。 价值稼动时间与设备综合效率(OverallEquipmentEffectiveness)性能稼动时间表示设备产出产品的时间,但无法表示设备产出良率的好坏,因此定义「价值稼动时间」来表示真正能产出良品的有价值时间,其定义如下: 价值稼动时间=性能稼动时间×良品率 设备稼动率如何计算? 悬赏分:0|解决时间:2010-10-28 16:02 |提问者:cyq1119|检举 假如我公司有十台设备,但因产订单不足每天只开动6台设备。每台每天工作8小时。其中一台因故障停机1小时,1台因工装停机0.5小时。我们今天的设备稼动率如何计算,敬请告知。最好能列出计算过程。 首先,你的设备利用率是6台/10台*100%=60%(这个跟设备综合效率无关) 第二,设备综合效率(即是综合稼动率)=可动率(已计划的)*表现效率(实际运作时间)*品质合格率。 你提供的条件里;已计划的可动率=?,假设:6台机器不需要停机(比如工人吃饭无需停机、中间无需停机休息、计划内的换模时间为0.5小时);那么可动率=(8小时*6台-0.5小时)/8小时*6台*100%=98.96% 表现效率=(已计划的可动时间)47.5小时-(计划外的损失时间)故障停机1 小时/47.5小时*100%=97.89% 品质合格率=?,假设为100%。 那么,按你提供的条件,你的设备利用率是60%;设备综合稼动率 =98.96%*97.89%*100%=96.87%。 但是,我认为是你提供的数据条件不充分,有很多机器的损失时间你还没有列出来,比如:轻微的停顿、开机的损失、返工的损失等。还有良品率的问题等。 希望这样表达能让你弄明设备白综合稼动率(即综合效率OEE)的概念。如有需要帮助,可以给我留言。 设备综合效率是Overall Equipment Effectiveness,简称OEE。一般,每一个生产设备都有自己的理论产能,要实现这一理论产能必须保证没有任何干扰和质量损耗。OEE就是用来表现实际的生产能力相对于理论产能的比率,它是一个独立的测量工具。 OEE是由可用率,表现性以及质量指数三个关键要素组成: OEE=可用率*表现指数*质量指数 其中: 可用率=操作时间/计划工作时间 它是用来评价停工所带来的损失,包括引起计划生产发生停工的任何事件,例如设备故障,原材料短缺以及生产方法的改变等。 表现指数=理想周期时间/(操作时间/总产量)=(总产量/操作时间)/生产速率 OEE设备综合效率提升训练 授课对象: 生产副总经理、生产总监、精益/IE部经理、生产制造经理、设备/工程部经理、TPM推进领导小组成员、IE主管、生产计划统计、设备维修主管及工程师、其他中层管理人员和设备相关工程技术人员。 课程背景: 世界经济复苏进行时,中国经济发展进入新常态,工业、移动互联网、互联网+,一个个新名词扑面而来,德国工业和中国制造2025,将从观念、技术手段上极大地提升制造业的效率,未来企业的竞争一定是效率之争,这已经毋庸置疑。 目前国内很多制造企业还有很多在使用设备故障停机时间、故障停机率来考核设备部门及其绩效。这些指标不能完整地体现设备的工作成绩,也不能体现与生产有关各部门对生产的影响。自上个世纪70年代英国的维修杂志主编丹尼斯巴克斯发表了设备综合工程学的理论,提出要用设备综合效率来衡量设备的绩效。引起了维修行业的广泛的关注和进行了深入的研究,经过实践取得了良好效果。 OEE目前已经成为企业公认的考核设备运行效率的重要指标! OEE的评价可使设备的运转状态与企业的经济效率结合起来,有利于“设备服务于生产”,从而形成全员参与的设备维护的综合管理体制。 OEE的统计和分析能全面暴露出企业效率管理各个方面的问题。有利于改善设备的使用、维护保养、资材保证、质量检查及后勤服务的工作,消除浪费,挖掘生产潜力、提高生产效率;提高企业利润和投资回报率。 世界经济500强企业、无论是在欧美还是日韩,都在使用设备综合效率OEE来评价和管理设备的绩效,因此引入OEE管理是现代管理的大势所趋,是实施精益生产的基础。 OEE是构建工厂数字化管理的基础,适应未来制造大数据的采集和分析应用。 本课程通过讲授有成功经验的做法,给学员以训练和借鉴。帮助学员掌握企业可以持久运行的改善设备综合效率OEE的方法,进行适合自己公司的推进,从而解决推进过程中的一系列生产运营的实战问题,为企业长久高效运营提供可靠的保障。 设备综合效率OEE计算公式和应用实例影响设备综合效率的主要原因是停机损失、速度损失和废品损失。它们分别由时间开动率、性开动率和合格品率反映出来,故得到下面设备综合效率公式: 设备综合效率=时间开动率×性能开动率×合格品率 这里,负荷时间为规定的作业时间除去每天的停机时间,即 负荷时间=总工作时间-计划停机时间 工作时间则是负荷时间除去那些非计划停机时间,如故障停机、设备调整和更换刀具、工夹具停机等。 【例1】若总工作时间为8h,班前计划停机时间是20min,而故障停机为20min,安装工夹具时间为20min,调整设备时间为20min。于是 负荷时间=480-20=460min 开动时间=460-20-20=400min 时间开动率=速度开动率×净开动率 这里,理论加工周期是按照标准的加工进给速度计算得到的,而实际的加工周期一般要比理论加工周期长。开动时间即是设备实际用于加工的时间,也就是工作时间减去计划停机和非计划停机所得时间,或是负荷时间减去非计划停机所得时间。 从计算上看,用简化了的公式也可以得到同样的结果。之所以用速度开动率和净开动率共同表示性能开动率,是因为从计算过程更容易看出性能开动率的损失原因。 【例2】有400件零件加工,理论加工周期为0.5min,实际加工周期为0.8min。则净开动率=0.8×400/400=80% 速度开动率=0.5/0.8=62.5% 性能开动率=80%×62.5%=50% 【例3】如果仍延用上面的例子,假如设备合格品率为98%,则 设备综合效率(全效率)=87%×50%×98%=42. 6% 我们把上面的公式和例子总结成以下的序列,得到 (A)每天工作时间=60×8=480min。 (B)每天计划停机时间(生产、维修计划、早晨会议等)=20min。 (C)每天负荷时间=A-B=460min。 (D)每天停机损失=60min(其中故障停机=20min,安装准备=20min,调整=20min)。 (E)每天开动时间=C-D=400min。 (F)每天生产数量=400件。 (G)合格品率=98%。 (H)理论加工周期=0. 5min/件。 (I)实际加工周期= 0. 8min/件。 (J)实际加工时间=I×F=0. 8×400=320min。 (K)时间开动率=(E/C) ×100%=(400/460)×100%=87%。 (L)速度开动率=(H/I)×100%= (0. 5/0.8)×100%=62.5%。 (M)净开动率=(J/E)× 100%=(320/400)×100%=80%。 (N)性能开动率=L×M×100%=0. 625×0. 80 ×100%=50%。 最后得 设备综合效率(全效率)=K×N×G×100%=0.87×0.50×0.98×100%=42.6% 日本全员生产维修体制中,要求企业的设备时间开动率不低于90%,性能开动率不低于95%,合格品率不低于99%,这样设备综合效率才不低于85%。这也是TPM所要求达到的目。 稼动率的计算方法[编辑本段][回目录] 时间稼动率:首先定义最大操作时间,指的是设备可用的最大时间,若设备本身为厂内自购,且可完全由厂内自主使用,则最大操作时间一般为日历时间;而负荷时间则为设备可稼动的时间,乃是最大操作时间扣除停机(Shutdown,SD)损失,停机损失乃是计划上的休止时间,如休假、教育训练、保养等。而稼动时间则是负荷时间扣除停止时间,而停止时间包括批次转换及制程异常、设备异常停止及修复时间。 最大操作时间:设备可用的最大时间负荷时间:最大操作时间扣除停机(Shutdown,SD)损失; 停机(Shutdown,SD)损失:计画上的休止时间,如休假、教育训练、保养等稼动时间:负荷时间扣除停止时间 停止时间:包括批次转换及制程异常、设备异常停止及修复时间。 由以上的定义,即可算出最常用的稼动率定义-设备稼动率(也称为时间稼动率),其公式为时间稼动率=稼动时间/负荷时间 目的:减少停止时间!!!通过资源整合,管理优化,进行资源充分利用,降低成本,提高效率。 性能稼动率/实质稼动率/速度稼动率[编辑本段][回目录] 时间稼动率并无法完全表现设备对生产的贡献程度; 例如,相同的设备,相等的稼动时间,可能因效率的不同,而有不同的产能,此类效率降低的损失则称为性能损失。在此定义速度稼动率如下: 速度稼动率=基准周期时间/实际周期时间 其中,基准周期时间:设备原设计产出单位产量所需的时间。实际周期时间:目前设备实际产出单位产量所需的时间。并定义实质稼动率与性能稼动率如下:实质稼动率=生产量×实际周期时间/稼动时间 性能稼动率=速度稼动率×实质稼动率 性能稼动时间则定义为:性能稼动时间=稼动时间×性能稼动率=稼动时间-性能损失时间 其中性能损失包括速度低落的损失与短暂停机的损失。由以上定义可知,若性能稼动率变小,则可判定生产相关设备的效率降低。 价值稼动时间与设备综合效率(OverallEquipmentEffectiveness) 性能稼动时间表示设备产出产品的时间,但无法表示设备产出良率的好坏,因此定义「价值稼动时间」来表示真正能产出良品的有价值时间,其定义如下:价值稼动时间=性能稼动时间×良品率 而设备的有效使用程度则以「设备总合效率」来判定,其定义如下: 设备综合效率(OEE)=时间稼动率×性能稼动率×良品率 稼动率与开动率[编辑本段][回目录] 因翻译的不同,有的地方也将稼动率翻译为开动率,于是也有相对应的性能开动率/时间开动率等词汇,其实质上为相同内容。什么是稼动率
OEE 设备综合效率 计算方式
OEE-稼动率相关报表填表说明
设备OEE计算方法
稼动率与设备总合效率(OEE)分析
设备综合效率OEE详解
(设备管理)设备综合效率
oee设备综合效率表格
稼动率的计算方法
设备稼动率如何计算
OEE设备综合效率提升训练
设备综合效率OEE计算公式和应用实例
稼动率的计算方法