冲压模具制作技术要求

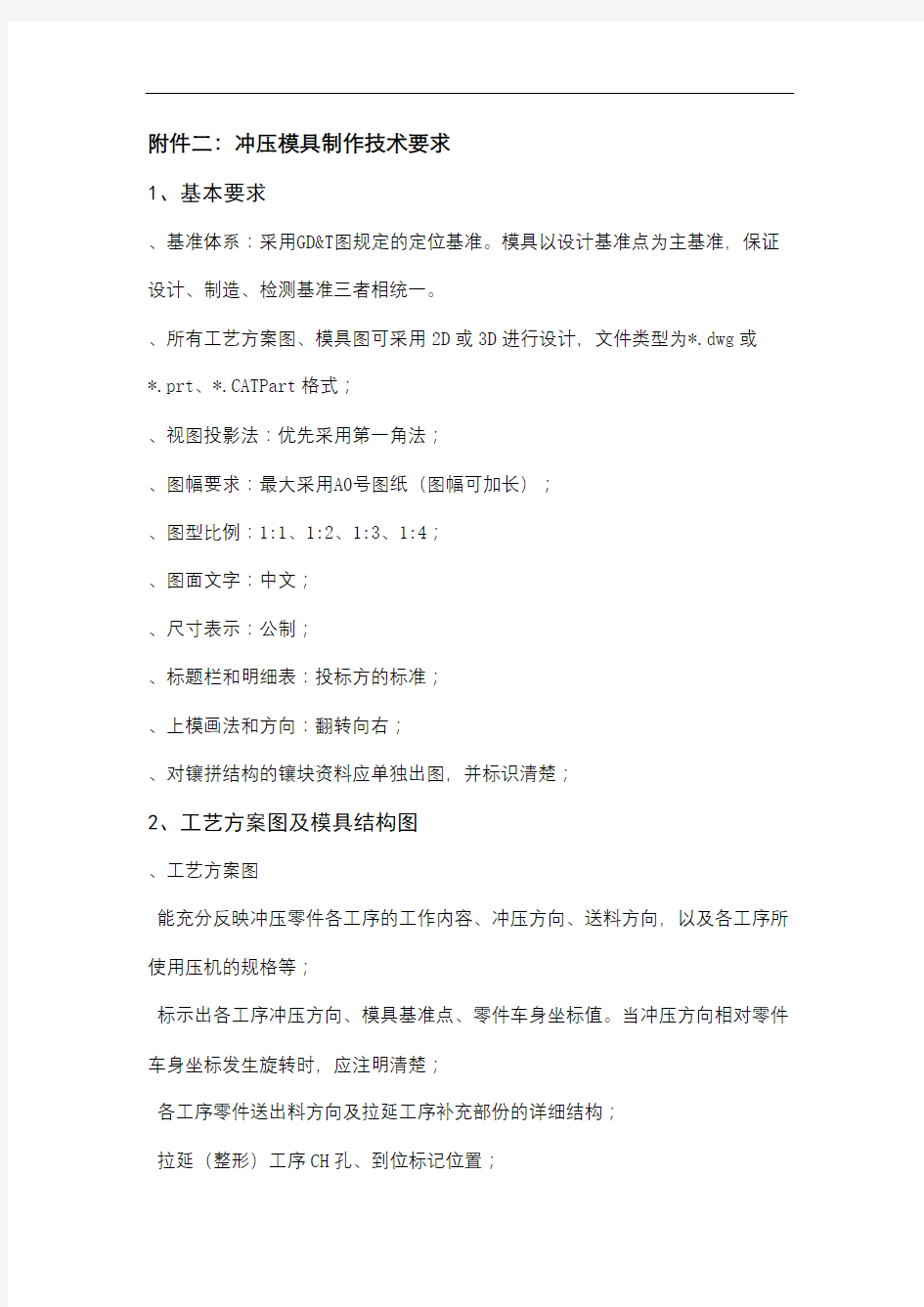
冲压模具制作技术要求 Company Document number:WTUT-WT88Y-W8BBGB-BWYTT-19998
附件二:冲压模具制作技术要求
1、基本要求
、基准体系:采用GD&T图规定的定位基准。模具以设计基准点为主基准,保证设计、制造、检测基准三者相统一。
、所有工艺方案图、模具图可采用2D或3D进行设计,文件类型为*.dwg或*.prt、*.CATPart格式;
、视图投影法:优先采用第一角法;
、图幅要求:最大采用A0号图纸(图幅可加长);
、图型比例:1:1、1:2、1:3、1:4;
、图面文字:中文;
、尺寸表示:公制;
、标题栏和明细表:投标方的标准;
、上模画法和方向:翻转向右;
、对镶拼结构的镶块资料应单独出图,并标识清楚;
2、工艺方案图及模具结构图
、工艺方案图
能充分反映冲压零件各工序的工作内容、冲压方向、送料方向,以及各工序所使用压机的规格等;
标示出各工序冲压方向、模具基准点、零件车身坐标值。当冲压方向相对零件车身坐标发生旋转时,应注明清楚;
各工序零件送出料方向及拉延工序补充部份的详细结构;
拉延(整形)工序CH孔、到位标记位置;
零件板材毛坯尺寸标注,中间工序的切边线;
废料切刀的布置位置及切边、冲孔废料的排除方式;
斜楔加工方向、加工范围;
顶杆布置图、废料流向示意及方案图中各种符号说明。
标明零件材料利用率。
、模具结构图
模具图应充分表达模具的工作状态,反映零件的送出料方向、所用的压机型号、顶杆位置与顶杆行程等。
模具图应准确注明模具中心、机床中心。模具中心应加注车身坐标系坐标值。每工序模具图应有工序内容简图。
模具结构中含弹簧/氮气缸的应有弹力工作示意图。
模具使用斜楔机构的应做出斜楔行程图及斜楔断面图。
模具如果配备气缸顶出机构,模具图中应附加气路图。
工艺方案图、模具图及数模文件的命名规则如下:
×××(项目代号) -×××(零件代号) -×××(零件版本) – OPx/y(x表示10、20…;y表示总工序数,如共五序则为50)。
3、工艺数模
、依据冲压零件3D数模,按冲压工艺方案图建立各工序的工艺数模,工艺数模中须完整表示出各工序线(如分模线、切边线、翻边线等),产品面与工艺补充面要用颜色或图层加以区分。
、产品3D数据以CATIA V5 R18版本格式提供。投标方工艺数模提供的3D数据格式为*.CATPart、*.prt或IGES。
、所有零件在建模中的坐标要与工艺方案一致。
、拉延成形零件须用Autoform或Dynaform分析软件对其进行CAE成形分析。复杂零件应对后工序进行回弹方面的仿真分析。对于外板零件要有合适的变形量(大于3%),CAE成形分析的最终结果由招标方确认。
4、模具结构通用要求
、冲压模具必须按照招标方冲压生产线设备参数进行设计和制造。对于自动化生产线能实现自动夹紧、板料及零件的自动传输、零件连动生产等全自动生产过程;手工生产线,要保证取送件容易,操作安全方便。
、在正常使用状态下,按5000件冲次为期限定期维护为前提。模具按30万件进行设计、制造。
、模具高度
模具闭高尽量相同。
、自动化生产用的传感器和气缸式顶升装置的气源接头规格要与压机相匹配。、模具的压力中心应与压机中心一致。
、模具上应有模具代号文字标识符,送料方向及模具前后方向标识符,拉延模须有顶杆布置标牌。
、铸造模具表面不允许有铸造缺陷,如无砂眼、疏松、缩孔、气泡、夹渣等。交验的模具表面应清洁,无切削、焊渣、尘砂、油污、锈蚀、杂物等。
、模具须合理设计排水孔,在选择电器元件及设计排水孔时要满足模具清洗的需要。
、拉延模型面贴合率要求:外板≥90%、内板≥80%。
、模具需要考虑噪音问题,对于厚板料需采用阶梯式凸模及波浪形刃口等方式。
、零件、废料退出凸、凹模无任何滞阻和粘附现象。手工生产线模具要求设计安装上下料架。
、起重装置
铸造模具采用铸入式起重臂或插销式吊耳,插销式超重吊耳应配有自锁功能起重棒。
凡冲模零件超过15Kg或取放不方便的冲模零件,均设置起重螺孔或起重孔。模具重心和多副模具组合在模板上的组合重心与模具的几何中心应尽量重合。、安全装置
冲压模具需加装自由状态下的存放限位装置,要设有安全平台,安全平台尺寸150mm×150mm,考虑防反措施。
上模压料器应有安全侧销或安全螺钉,上模销钉应有防落措施。
上下模相对活动部份及外露的活动部件须设有防护装置。
模具须加装运输时用的连接板。
不易区分的左右零件上应有“L”、“R”标记区分。
、导向装置
模具导向型式:
带冲裁的拉延模:采用导板+导柱复合导向方式;
冲裁类模具须有导柱导向,如有侧向力应采用导板+导柱复合导向方式;
整形类模具采用导板导向形式。有侧向力的需设计反侧机构;
退料(压料)板采用导板或导柱导向。
模具的导柱、导套要求采用植入式带锁紧结构,导套选用自润滑式。
模具存放时,上下导向部分接触面不小于导向面的1/3。
、模具的定位及U型槽结构、位置尺寸应与压机相匹配。
、拉延模工作部分采用MoCr铸铁或球铁,硬度HRC50以上。厚板(t≥)零件,高强度板(σs≥210)零件工作部分(压边圈压料面和上模压料面) 采用
Cr12MoV材料拼镶结构。拉延深度超过180mm零件,零件工作部分须进行TD处理。基座用HT300。
、切边模、翻边模料厚t<的零件,镶块材料为ICD5或7CrSiMnMoV,硬度HRC 50-55;厚板(t≥)零件,高强度板(σs≥210)零件,镶块材料为
SKDⅡ或Cr12MoV,硬度HRC 58-62。上下模座采用FC300或HT300。
、模具标准件须得到招标方的确认。
、模具外观及标志
模具本体及部件涂色标准由招标方提供。
使用气垫的模具,按招标方要求安装顶杆布置铭牌。
对于拆卸件、镶块,须刻印出安装位置的对应标记(字母或数字),模具各部分(包括镶块)均要用标准字头刻、铸出材质牌号。
铸造模具的铸字内容包括项目代号、零件名称、零件代号、工序号、工序内容、模具重量(上下模重量及总重量)等,具体由招标方确认。
5、拉延模
平衡垫块:保证所有平衡垫块均能与上模接触。
排气管采用铜弯管,排气孔位置应合理设置,不得影响制件表面质量,外板件上模应考虑防尘措施。
压边圈应使用标准安全螺栓。
为便于人工取件,可在压边圈上四角加弹顶销,但不得影响制件的成形。
顶杆行程:要小于机床气垫最大行程50mm。
采用到位标识,标记深度为以内,尽可能设置在废料上。
限位装置:采用限位安全档块或带套管式标准限位螺钉。
定位装置:制件在模具上采用可调式边定位块定位。
6、切边冲孔模
冲裁部分结构:
上、下模刃口为镶块结构,具有防侧向力功能,并便于更换与维修。
冲孔采用镶块时应考虑维修更换方便,原则上刃口处为镶块结构,易磨损部位及立切部位采用易换的小镶块结构。
废料刀应具有防侧向力功能,依托本体作靠背。
废料排出
废料刀的布置,根据工序安排适当处理,废料的最大对角线长度不允许超过600mm,要求手工线废料滑出模具区,自动化线废料要滑出机床。
废料滑板超出冲模底板以外时采用可叠式。废料滑板采用厚度为以上的钢板制作,两侧要求有翻边。废料滑槽一级滑槽的角度不小于25度。
直径小于20mm或最大对角线小于20mm的废料不能滑出工作台前后时,可采用废料盒盛装,且废料盒容量不少于1000冲次,1000次冲压后废料的重量(带废料盒)应在15kg以下,保证操作的方便。
自动化生产线上生产的模具尽量少使用废料盒。废料盒要求抽取方便,且能够自锁。
废料滑出工作台时,滑槽应有收口,让开操作空间,应满足废料滑出安全可靠,不飞溅,不妨碍冲压操作。
废料滑道终端宽度会签图纸时确认。
可以利用的冲压边料,在模具结构上采用从侧面取出的方式。
凸模:
有形状的凸模或镶块应有防转的锁紧装置。
薄板件侧冲孔应选用顶料型凸模。
尽量采用长度为80mm的凸模。
对特殊结构会签时确定。
凹模:
凹模套须选用带止转销形式。
凹模选用可换式的标准件(工作边距、孔距较小者除外)。
废料刀:
废料刀与凹模刃口随形。
废料刀要有足够的刃口长度和强度,材质与上下切刀相同。废料刀的布置要便于废料流出。
镶块:
切边凹模刃口采用镶块结构,凸模刃口采用镶块式或整体结构,直线段的镶块长度不大于500mm,形状复杂部位的拼块长度图纸会签时确定。
在镶块受侧向力的方向设置挡墙或挡键。
对于侧围门框、行李箱边框装胶条的部位,尽量采取整形后修边的方式,确保修边线的精度。
7、翻边整形模
凸模及压料板原则上采用整体结构,形状复杂受力较大易磨损处,应采用镶块结构。
整形处受力较大易磨损部位的压料板,应采用镶块结构。
要保证冲压零件脱模顺畅,脱模困难处应设置刮料或顶出装置。
所有的翻边镶块均应设有挡块或背托,不能仅用销钉。
易损部件要拆卸方便。
整形模具必须设置到位标记。
8、斜楔模
非标斜楔应设计强制回位机构。
非标斜楔回位,弹簧力应充分,设计时根据实际情况决定是否采用氮气弹簧。斜楔导向部位应采用自润滑结构。
斜楔驱动器的位置不得影响制件的进出。
斜楔机构优先采用标准件。
斜楔尽可能设置在模具两侧非操作区,确因冲压工艺和模具结构需要设置在操作区时,采用吊楔结构。
斜楔机构的驱动块和滑块的初始接触面积不小于整个斜面的1/3。
斜楔必须设置有防脱落的安全装置。
冲压模具制作技术要求
附件二:冲压模具制作技术要求 1、基本要求 1.1、基准体系:采用GD&T图规定的定位基准。模具以设计基准点为主基准,保证设计、制造、检测基准三者相统一。 1.2、所有工艺方案图、模具图可采用2D或3D进行设计,文件类型为*.dwg或*.prt、*.CATPart格式; 1.3、视图投影法:优先采用第一角法; 1.4、图幅要求:最大采用A0号图纸(图幅可加长); 1.5、图型比例:1:1、1:2、1:3、1:4; 1.6、图面文字:中文; 1.7、尺寸表示:公制; 1.8、标题栏和明细表:投标方的标准; 1.9、上模画法和方向:翻转向右; 1.10、对镶拼结构的镶块资料应单独出图,并标识清楚; 2、工艺方案图及模具结构图 2.1、工艺方案图 2.1.1 能充分反映冲压零件各工序的工作内容、冲压方向、送料方向,以及各工序所使用压机的规格等; 2.1.2 标示出各工序冲压方向、模具基准点、零件车身坐标值。当冲压方向相对零件车身坐标发生旋转时,应注明清楚; 2.1.3 各工序零件送出料方向及拉延工序补充部份的详细结构; 2.1.4 拉延(整形)工序CH孔、到位标记位置; 2.1.5 零件板材毛坯尺寸标注,中间工序的切边线; 2.1.6 废料切刀的布置位置及切边、冲孔废料的排除方式; 2.1.7 斜楔加工方向、加工范围; 2.1.8 顶杆布置图、废料流向示意及方案图中各种符号说明。 2.1.9 标明零件材料利用率。 2.2、模具结构图
2.2.1 模具图应充分表达模具的工作状态,反映零件的送出料方向、所用的压机型号、顶杆位置与顶杆行程等。 2.2.2 模具图应准确注明模具中心、机床中心。模具中心应加注车身坐标系坐标值。 2.2.3 每工序模具图应有工序内容简图。 2.2.4 模具结构中含弹簧/氮气缸的应有弹力工作示意图。 2.2.5 模具使用斜楔机构的应做出斜楔行程图及斜楔断面图。 2.2.6 模具如果配备气缸顶出机构,模具图中应附加气路图。 2.2.7 工艺方案图、模具图及数模文件的命名规则如下: ×××(项目代号) -×××(零件代号) -×××(零件版本) –OPx/y(x表示10、20…;y表示总工序数,如共五序则为50)。 3、工艺数模 3.1、依据冲压零件3D数模,按冲压工艺方案图建立各工序的工艺数模,工艺数模中须完整表示出各工序线(如分模线、切边线、翻边线等),产品面与工艺补充面要用颜色或图层加以区分。 3.2、产品3D数据以CATIA V5 R18版本格式提供。投标方工艺数模提供的3D 数据格式为*.CATPart、*.prt或IGES。 3.3、所有零件在建模中的坐标要与工艺方案一致。 3.4、拉延成形零件须用Autoform或Dynaform分析软件对其进行CAE成形分析。复杂零件应对后工序进行回弹方面的仿真分析。对于外板零件要有合适的变形量(大于3%),CAE成形分析的最终结果由招标方确认。 4、模具结构通用要求 4.1、冲压模具必须按照招标方冲压生产线设备参数进行设计和制造。对于自动化生产线能实现自动夹紧、板料及零件的自动传输、零件连动生产等全自动生产过程;手工生产线,要保证取送件容易,操作安全方便。 4.2、在正常使用状态下,按5000件冲次为期限定期维护为前提。模具按30万件进行设计、制造。 4.3、模具高度 模具闭高尽量相同。
五金模具技术规范
冷冲压模具设计制造技术规范 1.目的 提高五金件冷冲压模具质量;建立模具标准化;统一模具的设计标准及制造技术规范。 2.适用范围 本标准适用于本公司模具车间设计、制造的冷冲压模具,也适用于委外设计、制造的冷冲压模具。 3.引用标准 GB1298 《碳素工具钢技术条件》 GB1299 《合金工具钢技术条件》 GB699 《优质碳素结构钢号和一般技术条件》 GBT2854 《冲模模架技术条件》 GB2870 《冷冲模零件技术条件》 GB2867.5 《冷冲模卸料装置,圆柱头卸料螺钉》 GB2867.6 《冷冲模卸料装置,圆柱头内角卸料螺钉》 4.技术要求 4.1 模具设计要点: 4.1.1模具工艺编排应保证: ①模具加工之产品所有尺寸及技术要求符合 图纸且品质有保障: ②模具结构合理且强度足够; ③模具制造及维 修难度中等; ④模具设计寿命与预计生产订单相适应; ⑤产品及模 具加工费用均最经济合理. 4.1.2整体结构设计应保证: ①操作简便、安全; ②适应批量生产且效率 高; ③定位可靠; ④工作精度的稳定与持久性; ⑤维护及维修方便;
⑥封闭高度与所安装机床匹配; ⑦模具结构标准化. 4.1.3 零件设计基本规范: 4.1.3.1模架选用原则: ①原则上必须设置导向结构,对于成形类模具若 在结构上可以保证质量和使用寿命及效率时可以不设置,但此必须征得模具部工艺工程师同意,冲裁模架的导向件结构设置应方便工作刃口的刃磨;②在工作中导柱导套尽可能不脱离导向,导柱长度以合模后短于闭合高度10mm为宜;③外导柱、导套的结构采用独立导柱,普通导向精度要求的模架采用滑动独立导柱(TUB),高导向精度要求的模架采用滚动独立导柱(TUR)加内导柱, 内导柱、导套的结构采用压入结构;④模架有效面积大于400X300mm的模具不得使用铸件模架,对于选用的铸件模架应符合GB2854《冷冲模模架技术条件》规定,导柱直径和数量的设置应考虑导柱的刚度和模架面积大小,模架面积大于400X300mm应选取导柱直径大于φ25mm。 4.1.3.2 模板设计规范: ①凹模: ⑴厚度(B):零件尺寸300*300以下,材料厚度(T)小于1.6MM 时, 凹模板厚不小于24MM;材料厚度大于1.6MM小于5MM时, 凹模板厚不小于34MM; 材料厚度大于5MM,凹模板厚不小于45MM;零件尺寸大于300*300,材料厚度小于1.6MM时, 凹模板厚不小于34MM;材料厚度大于1.6MM小于5MM时, 凹模板厚不小于44MM; 材料厚度大于5MM,凹模板厚不小于55MM. ⑵凹模工作刃口至边距(A):最小边距(A min)为凹模厚度(B)的1.5倍以上,但应大于30MM; 材料厚度大于1.6MM时, 边距(A)为凹模厚度(B)的2倍以上. ②上下模座:⑴外形尺寸应稍大于凹模外形尺寸;⑵模座厚(H):尽可能
冲压模具制造工艺.
概述 模具是工业生产中使用极为广泛的工艺装备之一,也是发展工业的基础。模具是成形金属、塑料、橡胶、玻璃、陶瓷等制件的基础工艺装备,是工业生产中发展和实现少无切屑加工技术不可缺少的工具。模具是一种高效率的工艺设备,用模具进行各种材料的成型,可实现高速度的大批量生产,并能在大量生产条件下稳定的保证制件的质量、节约原材料。因此,在现代工业生产中,模具的应用日益广泛,是当代工业生产的重要手段和工艺发展方向。许多现代工业的发展和技术水平的提高,在很大程度上取决于模具工业的发展水平。 为了实现工业现代化今后的模具发展趋势大致包括以下几方面: 1、发展高效模具。对于大批量生产用模具,应向高效率发展。如为了适应当前高速压力机的使用,应发5冲模的工作部分零件必须具备的性能展多工位级进模以提高生产效率。 2、发展简易模具。对于小批量生产用模具,为了降低成本、缩短模具制造周期应尽量发展薄板冲模、聚氨酯模具、锌合金、低熔点合金,环氧树脂等简易模具。 3、发展多功能模具。为了提高效率和保证制品的质量,要发展多工位级进模及具有组合功能的双色、多色塑料注射模等。 4、发展高寿命模具。高效率的模具必然需要高寿命,否则将必然造成频繁的模具拆卸和整修或需要更多的备模。为了达到高寿命的要求,除模具本身结构优化外,还要对材料的选用和热处理、表面强化技术予以开发和创新。 5、发展高精度模具。计算机硬件,软件以及模具加工,检测技术的快速发展使得精锻模具CAD/CAM/CAE一体化技术成为锻造企业切实可行的技术。精密,高效是现代锻造业的发展趋势;应用该技术的实践表明,只有基于效率的模具CAD/CAM/CAE…CAX平台才能实现精锻件及其模具的高效率开发。
冲压模具技术经验要求
冲压模具技术经验要求集团企业公司编码:(LL3698-KKI1269-TM2483-LUI12689-ITT289-
技术要求 1.冲裁凸凹模刃口间隙不均匀度≤0.03mm; 2.成形凸凹模刃口间隙不均匀度≤0.06mm; 3.模具闭合时,长宽高尺寸为405×343×231.5;模具开启时,卸料板行程为21.5mm; 4.本模具采用开式压力机J23—63; 5.检查各个活动机构是否适当,保证没有松动和卡死现象,导柱和导套之间的相对运动既能保持精度又无阻滞现象,模具的开合过程流畅; 6.装配后进行试模验收,推出机构与其他零部件不得有干涉现象,制件质量要达到设计要求,不能有变形,如有不妥,修模再试; 7.模具制造按GB2854—81“冷冲模架技术条件”和GB2870—81“冷冲模零件技术条件”的有关规定执行,模架按Ⅰ级精度验收; 8.制件表面不平度≤0.15mm。 技术要求 1.冲裁凸凹模刃口间隙不均匀度≤0.03mm; 2.成形凸凹模刃口间隙不均匀度≤0.06mm; 3.模具闭合时,长宽高尺寸为405×343×231.5;模具开启时,卸料板行程为21.5mm; 4.本模具采用开式压力机J23—63; 5.检查各个活动机构是否适当,保证没有松动和卡死现象,导柱和导套之间的相对运动既能保持精度又无阻滞现象,模具的开合过程流畅; 6.装配后进行试模验收,推出机构与其他零部件不得有干涉现象,制件质量要达到设计要求,不能有变形,如有不妥,修模再试;
7.模具制造按GB2854—81“冷冲模架技术条件”和GB2870—81“冷冲模零件技术条件”的有关规定执行,模架按Ⅰ级精度验收; 8.制件表面不平度≤0.15mm。 技术要求 1.本模具为倒装落料拉深冲孔复合模,由于要求在凸缘上冲孔,故要在拉深完全完成的前提下进行冲孔. 2.该模具闭合高度为233mm. 3.本模具使用J21-25开式压力机. 4.模具制造按照GB2854-81"冷冲模架技术条件"和GB2870-81"冷冲模零件技术要求"的有关规定执行. 5.冲裁与拉深间隙都要均匀.冲裁双边间隙Zmin=0.1mmZmax=0.14mm,拉深双边间隙Z=1.1mm 6.导柱导套的轴线与模座上下面垂直公差为4级.
模具设计技术要求
级进模设计要求 1、用该模具所冲出的零件应该满足产品质量要求; 2、优化排样设计,使材料材料的利用率尽可能高; 3、强度和刚性较差的小冲裁凸模必须有护套加导向; 4、镶块、凸模安装方便,正确可靠,冲裁凸模修模后,高度调节要方便; 5、单边冲裁凸模,尽可能加导向部分;单侧弯曲时,模具上要有防止材料流动的对策; 6、间隙的均匀程度要到达70%以上; 7、模具安装平稳性好,调整方便,工作安全;模具结构应便于制造与维修; 8、压力中心偏移量不能超过凹模1/6; 9、各工作系统坚固可靠,活动部分灵活平稳,动作互相协调。定位起止正确,卸料板、顶块不倾斜,有足够的卸料、顶出件力,卸料安全可靠。进料、定料、出件、清理废料畅通、方便,没有废料上浮、漏料孔堵塞、叠件现象。保证稳定正常工作; 10、上模座沿导柱上、下移动平稳、无滞住现象。 11、级进模用四角滚珠导柱导套钢模,弹性卸料,小凸模用护套,卸料板用小导柱导套导向,凹模做成分段拼合或组合式,冲裁凸模修模后,高度要能调节,前后工位排废料、出工件方案合理,毛坯定位准确可靠,送料方便无阻碍,废料切断后回收。 工作量:图纸(1:1),装配图1张0号图纸;零件图,凸模、凹模、护套,其他工作零件必须画,其次按卸料板、凸模固定板、凹模固定板等顺序,画够2张以上0号图纸。说明书:要求30页以上。图纸和说明书质量按学校要求做。 冲压件要求(大批量生产) 一、零件附加说明 零件的形状和要求见附图,尺寸从图纸上量取 二、合格的制件应满足的要求 1.尺寸、形状符合图纸要求; 2.冲裁断面不允许有夹层,毛刺最好在一面、毛刺高度小于10%t; 3. 冲压件平整、形状无明显翘曲、畸形、扭曲、歪斜等形状缺陷; 4. 光面的均匀程度要求大于70%; 5. 搭接口不能出现错位、不平直、毛刺现象; 6. 成形部分平整、光滑,无起皱、裂纹、显著变薄、明显的刮痕现象; 7. 制件必须不能被模具的伤痕、划痕、表面块陷所影响; 8.保证制件质量稳定。
冲压模具技术要求
冲压模具技术要求 Company Document number:WTUT-WT88Y-W8BBGB-BWYTT-19998
技术要求 1.冲裁凸凹模刃口间隙不均匀度≤0.03mm; 2.成形凸凹模刃口间隙不均匀度≤0.06mm; 3.模具闭合时,长宽高尺寸为405×343×;模具开启时,卸料板行程为21.5mm; 4.本模具采用开式压力机J23—63; 5.检查各个活动机构是否适当,保证没有松动和卡死现象,导柱和导套之间的相对运动既能保持精度又无阻滞现象,模具的开合过程流畅; 6.装配后进行试模验收,推出机构与其他零部件不得有干涉现象,制件质量要达到设计要求,不能有变形,如有不妥,修模再试; 7.模具制造按GB2854—81“冷冲模架技术条件”和GB2870—81“冷冲模零件技术条件”的有关规定执行,模架按Ⅰ级精度验收; 8.制件表面不平度≤0.15mm。 技术要求 1.冲裁凸凹模刃口间隙不均匀度≤0.03mm; 2.成形凸凹模刃口间隙不均匀度≤0.06mm; 3.模具闭合时,长宽高尺寸为405×343×;模具开启时,卸料板行程为21.5mm; 4.本模具采用开式压力机J23—63; 5.检查各个活动机构是否适当,保证没有松动和卡死现象,导柱和导套之间的相对运动既能保持精度又无阻滞现象,模具的开合过程流畅;
6.装配后进行试模验收,推出机构与其他零部件不得有干涉现象,制件质量要达到设计要求,不能有变形,如有不妥,修模再试; 7.模具制造按GB2854—81“冷冲模架技术条件”和GB2870—81“冷冲模零件技术条件”的有关规定执行,模架按Ⅰ级精度验收; 8.制件表面不平度≤0.15mm。 技术要求 1.本模具为倒装落料拉深冲孔复合模,由于要求在凸缘上冲孔,故要在拉深完全完成的前提下进行冲孔. 2.该模具闭合高度为233mm. 3.本模具使用J21-25开式压力机. 4.模具制造按照GB2854-81"冷冲模架技术条件"和GB2870-81"冷冲模零件技术要求"的有关规定执行. 5.冲裁与拉深间隙都要均匀.冲裁双边间隙Zmin=0.1mm Zmax=0.14mm,拉深双边间隙Z=1.1mm 6.导柱导套的轴线与模座上下面垂直公差为4级.
冲压模具技术要求
冲压模具技术要求-标准化文件发布号:(9456-EUATWK-MWUB-WUNN-INNUL-DDQTY-KII
技术要求 1.冲裁凸凹模刃口间隙不均匀度≤0.03mm; 2.成形凸凹模刃口间隙不均匀度≤0.06mm; 3.模具闭合时,长宽高尺寸为405×343×231.5;模具开启时,卸料板行程为21.5mm; 4.本模具采用开式压力机J23—63; 5.检查各个活动机构是否适当,保证没有松动和卡死现象,导柱和导套之间的相对运动既能保持精度又无阻滞现象,模具的开合过程流畅; 6.装配后进行试模验收,推出机构与其他零部件不得有干涉现象,制件质量要达到设计要求,不能有变形,如有不妥,修模再试; 7.模具制造按GB2854—81“冷冲模架技术条件”和GB2870—81“冷冲模零件技术条件”的有关规定执行,模架按Ⅰ级精度验收; 8.制件表面不平度≤0.15mm。 技术要求 1.冲裁凸凹模刃口间隙不均匀度≤0.03mm; 2.成形凸凹模刃口间隙不均匀度≤0.06mm; 3.模具闭合时,长宽高尺寸为405×343×231.5;模具开启时,卸料板行程为21.5mm; 4.本模具采用开式压力机J23—63; 5.检查各个活动机构是否适当,保证没有松动和卡死现象,导柱和导套之间的相对运动既能保持精度又无阻滞现象,模具的开合过程流畅; 6.装配后进行试模验收,推出机构与其他零部件不得有干涉现象,制件质量要达到设计要求,不能有变形,如有不妥,修模再试; 7.模具制造按GB2854—81“冷冲模架技术条件”和GB2870—81“冷冲模零件技术条件”的有关规定执行,模架按Ⅰ级精度验收; 8.制件表面不平度≤0.15mm。 技术要求 1.本模具为倒装落料拉深冲孔复合模,由于要求在凸缘上冲孔,故要在拉深完全完成的前提下进行冲孔. 2.该模具闭合高度为233mm. 3.本模具使用J21-25开式压力机. 4.模具制造按照GB2854-81"冷冲模架技术条件"和GB2870-81"冷冲模零件技术要求"的有关规定执行. 5.冲裁与拉深间隙都要均匀.冲裁双边间隙Zmin=0.1mm Zmax=0.14mm,拉深双边间隙Z=1.1mm 6.导柱导套的轴线与模座上下面垂直公差为4级. 2
冲压模具制作技术要求
冲压模具制作技术要求 This manuscript was revised by the office on December 10, 2020.
附件二:冲压模具制作技术要求1、基本要求 1.1、基准体系:采用GD&T图规定的定位基准。模具以设计基准点为主基准,保证设计、制造、检测基准三者相统一。 1.2、所有工艺方案图、模具图可采用2D或3D进行设计,文件类型为*.dwg或*.prt、*.CATPart格式; 1.3、视图投影法:优先采用第一角法; 1.4、图幅要求:最大采用A0号图纸(图幅可加长); 1.5、图型比例:1:1、1:2、1:3、1:4; 1.6、图面文字:中文; 1.7、尺寸表示:公制; 1.8、标题栏和明细表:投标方的标准; 1.9、上模画法和方向:翻转向右; 1.10、对镶拼结构的镶块资料应单独出图,并标识清楚; 2、工艺方案图及模具结构图 2.1、工艺方案图 2.1.1 能充分反映冲压零件各工序的工作内容、冲压方向、送料方向,以及各工序所使用压机的规格等; 2.1.2 标示出各工序冲压方向、模具基准点、零件车身坐标值。当冲压方向相对零件车身坐标发生旋转时,应注明清楚; 2.1.3 各工序零件送出料方向及拉延工序补充部份的详细结构; 2.1.4 拉延(整形)工序CH孔、到位标记位置; 2.1.5 零件板材毛坯尺寸标注,中间工序的切边线; 2.1.6 废料切刀的布置位置及切边、冲孔废料的排除方式; 2.1.7 斜楔加工方向、加工范围; 2.1.8 顶杆布置图、废料流向示意及方案图中各种符号说明。 2.1.9 标明零件材料利用率。 2.2、模具结构图
冲压模具技术国内外发展现状
冲压模具技术国内外发展现状 ——计算机技术与冲压模具 摘要:文章首先简述了国内外模具工业的发展现状及趋势;然后具体结合计算机技术在冲压模具上的应用一点简述了国内外冲压模具技术的发展现状以及将来的发展趋势。关键词:冲压模具计算机技术应用 引言 冲压技术是一种具有悠久历史的加工方法和生产制造技术。根据文献记载和考古文物证明,我国古代的冲压加工技术走在世界之前,对人类早期文明社会的进步发挥了重要的作用,作出重要贡献[1]。 利用冲压机械和冲压模具进行的现代冲压加工技术,已有近二百年的发展历史。1839年英国成立了Schubler公司,这是早期颇具规模的、现今也是世界上最先进的冲压公司之一[2] 从学科角度上看,到本世纪10年代,冲压加工技术已经从一种从属于机械加工或压力加工艺的地位,发展成为了一门具有自己理论基础的应用技术科学[3]。俄罗斯(从前苏联时期开始)就有各类冲压技术学校。日本也有冲压工学之说。中国也有冲工艺学、薄板成形理论方面的教材及专著。可以认为这一学科现已形成了比较完整的知识结构系统。 冲压技术中冲压模具是制造业的重要基础工艺装备。用模具生产制件所达到的高精度、高复杂程度、高一致性、高生产率和低耗能、低耗材,使模具工业在制造业中的地位越来越重要。国外将模具比喻为“金钥匙”、“金属加工帝王”、“进入富裕社会的原动力”[4]等等。国内也将模具工业称为“永不衰亡的工业”、“点铁成金的行业”、“无与伦比的效益放大器”[5] 等等。现在,模具技术已成为衡量一个国家产品制造水平的重要标志之一。没有高水平的模具就没有高水平的产品已成为共识。就工程制造而言,进入80、90年代,由于世界各国经济的高速发展和国民生活水准的大大提高,人们对汽车、家用电器、住宅等的需求与日俱增,促进了冲压技术的快速发展,同时也就对模具技术提出了更高的要求。且由于电子计算机技术的广泛而有效的应用,不仅促进了冲压技术的理论深入发展,而且使冲压机械、模具及操作的自动化程度等,都达到了一个更高的阶段。由此我们不难看出,计算机技术在当今模具设计制造中起着尤为关键的作用。现今,冲压加工技术已发展成为了一种先进制造技术。当然,冲压技术(分为分离加工和成形加工两大类)无论从理论上或实践上仍会不断向前发展。 1、国内外模具工业的发展与现状 国外,特别是欧美和日韩等发达地区的模具工业起步较早,拥有比较先进的生产管理技术及经验,值得我们国内模具行业学习和借鉴。在欧美,许多模具企业将高新技术应用于模具的设计和制造,主要体现在[6]:(1)充分发挥了信息技术带动和提升模具工业的优越性;(2)高速切削、五轴高速加工技术基本普及,大大缩减制模周期,提高企业的市场竞争力;(3)快速成形技术和快速制模技术得到普遍应用;(4)从事模具行业的人员精简,一专多能,一人多职,精益生产;(5)模具产品专业化,市场定位准确;(6)采用先进的管理信息系统,实现集成化管理;(7)工艺管理先进、标准化程度高。日本模具加工的未来发展方向主要表现为无人手修模、无放电加工、加工时间缩短、五轴加工等方面。 中国虽然在很早以前就制造模具和使用模具,但一直未形成产业。由于长期以来模具制造一直作为保证企业产品生产的手段被视为生产后方。因此一直发展缓慢[7] 。1984年成立了中国模具工业协会,1987年模具首次被列入机电产品目录,当时全国共有生产模具的厂点约6 000家。总产值约30亿元。随着中国改革开放的日益深入,市场经济进程的加快,模具及其标准件、配套件作为产品,制造生产的企业大量出现,模具产业得到快速发展。在市场竞争中,企业的模具生产技术提高很快,规模不断发展,提高很快。20世纪90年代以来,中国在汽车行业的模具设计制造中开始采用CAD/CAM技术。国家科
冲压模装配技术要求
复合冲裁模具的装配 板书 一、教学目的: 1.能正确阅读零件图和装配图. 2.熟悉复合冲裁模的工作原理和结构特点. 3.能按技术要求进行装配、调试复合冲裁模. 二、相关工艺知识 2.1概念:模具的装配—; 复合冲裁模—; 倒装式复合模— 识读装配图:(使用带有立体图的挂图) (1)、阅读明细表 (2)、在图上找相应零件号码位置 (3)、找出零件图看形状、尺寸 2.3冲裁模工作原理: 2.4冲裁模结构特点: 三、装配过程:(用实物讲解和示范)1)组件装配(清洗、检验、加润滑油) ①组装模架。 辅助构件 工艺构件 工作零件 定位零件 压料,卸 导向零件 固定零件 紧固及其冲模零部 顶板 顶料器 退料板 凸凹模 挡料销 模柄 凹模 导柱 底板 螺钉
②组装凸模21 ③组装顶板5。 ④组装模柄8。 2)总装配 ①装上模(凹模4) ②配下模(凸凹模2) ③调整凸凹模间隙。 ④辅助零件的安装 ⑤检验、调试 四、装配及调试技术要点: 五、总结指导 实习课教案
δ复合冲裁模具的装配 二、相关工艺知识 2.1概念 1.模具的装配—就是根据模具的结构特点和技术条件,以一定的装配顺序和方法,将符合图纸技术要求的零件,经协调加工,组装成满足使用要求的模具。在装配过程中,既要保证配合零件的配合精度,又要保证零件之间的位置精度,对于具有相对运动的零(部)件,还必须保证它们之间的运动精度。因此,模具装配是最后实现冲模设计和冲压工艺意图的过程,是模具制造过程中的关键工序。模具装配的质量直接影响制件的冲压质量、模具的使用和模具寿命。 2.复合冲裁模—在压力机的一次行程中(如下图2),在模具的同一位置上,完成两个或两个以上的冲压工序的模具,叫复合模。 3.倒装式复合模—凹模在上模;倒装式复合模工作中不必清除废料,操作方便,所以被广泛采用。(如下图3) 图3 图2 2.2工作原理、结构特点 1.冲裁模工作原理如下图:
冲压模具 盖帽冲压工艺及模具设计 文献综述
一、冲压的概念及其优点 ……………………………………………………………………………… 二、课题国内外现状 ……………………………………………………………………………………… 三、课题研究主要成果 ……………………………………………………………………………… 四、未来冲压模具制造技术发展趋势 ……………………………………………………………………………… 五、中国汽车冲压技术发展存在的问题 ……………………………………………………………………………… 六、主要参考文献 ……………………………………………………………………………… 七、指导教师意见 ……………………………………………………………………………
一、冲压的概念及其优点 (1)冲压的概念 冷冲压是在常温下利用冲模在压力机上对材料施加压力,使其产生分离或变形,从而获得一定形状、尺寸和性能的零件加工方法。它是一种压力加工方法,是机械制造中的先进加工方法之一。 冲压模具是一个特殊的,一次性的一类精密工具,通过切割与塑形的方式使金属成为一个理想的形状或外形。大多数模具构造有几个基本组成部分,包括模板,防磨装置,模套,导向销,轴衬,垫块,垫板,螺钉,销钉,和螺栓。模具还需要冲孔模板,压力和冲压成型板,以及可用来保护它们---转子,肩螺栓,衔铁,保持架;和气体,线圈,或聚氨酯弹簧的工具。 (2)冲压的优点 冷冲压和线切割相比较,具有生产效率高、加工成本低、材料利用率高、产品尺寸精度稳定、操作简单容易实现机械化和自动化等一系列有点,特别适合于大批量生产。 冲压模具成形作为现代工业中一种十分重要的加工方法,用以生产各种板料零件,具有很多独特的优势,其成形件具有自重轻、刚度大、强度高、互换性好、成本低、生产过程便于实现机械自动化及生产效率高等优点,是一种其它加工方法所不能相比和不可替代的先进制造技术,在制造业中具有很强的竞争力,被广泛应用于汽车、能源、机械、信息、航空航天、国防工业和日常生活的生产之中。 在吸收了力学、数学、金属材料学、机械科学以及控制、计算机技术等方面的知识后,已经形成了冲压学科的成形基本理论。以冲压产品为龙头,以模具为中心,结合现代先进技术的应用,在产品的巨大市场需求刺激和推动下,冲压成形技术在国民经济发展、实现现代化和提高人民生活水平方面发挥着越来越重要的作用。 现代冲压模具生产是一种大规模继续作业的制造方式,由于高新技术的参与和介入,冲压生产方式由初期的手工操作逐步进化为集成制造。生产过程逐步实现机械化、自动化、并且正在向智能化、集成化的方向发展。实现自动化冲压作业,体现安全、高效、节材等优点,已经是冲压模具生产的发展方向。 日常生活中人们使用的很多用具是用冲压方法制造的,例如不锈钢饭缸,它就是用一块圆形金属板料在压床上利用模具对圆形板料加压而冲出来的。可以看出,冷冲压是一种在常温(冷态)下利用冲模在压床上对各种金
冲压工艺通用技术要求
1 范围 本标准规定了金属冷冲压件在原材料、形状和尺寸、表面质量、热处理、检验规则、包装等方面的通用技术要求。 本标准适用于冷冲压方法生产的板料厚度大于0.1mm的金属冷冲压件。 2 引用标准 GB/T 710-1991 优质碳素结构钢热轧薄钢板和钢带 GB/T 716-1991 碳素结构钢冷轧钢带 GB/T 2517-1981 一般结构用热连轧钢板和钢带 GB/T 2521-1996 冷轧晶粒取向、无取向磁性钢带(片) 3 定义 本标准采用下列定义。 3.1 平冲压件 指经平面冲裁工序加工而成平面形状的冲压件。 3.2 成形冲压件 经弯曲,拉深和其他成形工序加工而成的冲压件。 3.3 孔组间距 同一零件上一组孔的中心线和另一组孔的中心线间的距离。 3.4 毛刺 冲裁时存留在冲压件断面上突起的锋利的材料。 3.5 冲裁断面粗糙度 指冲裁断面上剪裂带的粗糙度。 3.6 表面质量
冲压件在成形过程中,由非冲裁断面形成的零件表面产生的各种物理现象。 4 技术要求 冲压件应按经规定程序批准的产品图样和技术文件制造,产品图样和技术文件中未规定的要求,应符合本标准的规定。 4.1 原材料 4.1.1 冲压件使用的原材料,需符合GB/T 710、GB/T 716、GB/T 2517、GB/T 2521等有关金属材料的标准规定,并符合对材料的供货状态或其他方面的要求。 4.1.2 冲压件的原材料应有关质量证明书,它保证材料符合规定的技术要求。当无质量证明书或其他原因,冲压件生产厂可按需要选择原材料进行复检。复检的主要项目和内容: 4.1.2.1 外观检验:检验材料表面缺陷、污痕、外廓尺寸、形状和厚度以及表面粗糙度。 4.1.2.2 化学分析、金相检验:分析材料总化学元素的含量;判定材料晶粒度级别和均匀程度;评定材料中游离渗碳体、带状组织和非金属夹杂物的级别;检查材料缩孔、疏松等缺陷。 4.1.2.3 力学性能检验:检验材料的抗拉强度δb、屈服强度δs、屈强比δs/δb、伸长率δ、断面收缩率ψ及洛氏硬度HRB等。 4.1.2.4 成形性能试验:对材料进行弯曲试验、北图试验、测定材料的加工硬化指数n值和塑性应变比γ值等。关于钢板成形性能试验方法,可按薄钢板成形性能和试验方法的规定进行。 4.1.2.5 其他性能要求测定:对材料的电磁性能和对镀层、涂层的附着能力等的
冲压模设计开题报告
1.课题研究的意义 本课题要求对给定零件防尘盖进行落料、冲孔、翻边、成形复合冲压模设计,通过对零件进行详细的工艺分析确定零件的冲压工艺方案并制定部分零件的制造工艺,如:凸模、凹模、凸凹模、凸模固定板、垫板、凹模固定板、卸料板、导尺、挡料销、导正销等。通过该课题能够让学生掌握中等复杂程度零件冲压模具设计与制造的一般方法,对零件冲压工艺方案的制定、工艺计算及模具设计有了更深层次的认识,并学会对模具设计资料的检索与整合以及对已有资料的充分合理的使用,该实践性课题是对学生理论学习水平的实践和检验,可对以后从事类似的工作有一定的指导性与实践性意义。 2、研究现状和发展趋势(文献综述) 2.1冲压技术的发展现状 随着科学技术的不断进步,工业产品生产日益复杂与多样化,产品性能和质量也在不断提高,因而对冷冲压技术提出了更高的要求。冲压技术自身也在不断地创新和发展。冲压技术的发展现状主要可以归纳为以下几个方面: (1)冲压加工自动化与柔性化 为了适应大批量高、高效率生产的需要,在冲压模具和设备上广泛应用了各种自动化的进、出料机构。对于大型冲压件,例如汽车覆盖件,专门配置了机械手或机器人。这不仅仅大大提高了冲压件的生产品质和生产率,而且也增加了冲压工作的安全性。在中、小件的大
批量生产方面,现已广泛应用多工位级模、多工位压力机或高速压力机。在中、小批量多品种生产方面,正在发展柔性制造系统。为了适应多品种生产时不断更换模具的需要,已成功地开发出快速换模系统。 (2)塑性成形的基础理论已基本形成 冲压成形工艺近年来有很多新的发展,在精密冲裁、精密成形、精密剪切、复合材料成形、超塑性成形、软模成形以及电磁成形等方面取得很大的进展。冲压件的成形精度、生产率越来越高。精密冲压的范围越来广,由平板零件精密冲裁拓宽到精密弯曲、精密拉深及立方体精密成形等。可加工的工件的厚度也不断提高,并可对高强度合金材料进行精密冲裁。 计算机辅助工程在冲压领域得到较好的应用,可进行应力、应变等的分析,排样、毛坯的优化设计及工艺过程的模拟与分析等,实现冲压过程的优化设计。 此外,冲压成形性能和成形极限的研究,冲压件成形难度的判定以及成形预报等技术的发展,均标志着冲压成形已从原来的经验、实验分析开始走上由冲压理论指导的科学联系使冲压成形趱计算机辅 助工程化和智能化的发展道路。 (3)以有限元为核心的塑性成形数值仿真技术日趋成熟,为人们 认识成形过程的本质规律提供了新途径。 以有限元为核心的塑性成形数值仿真技术可以用于冲压成形过 程的分析、优化和模具设计,能显著减少模具和调试周期,降低生产
冲压模具设计毕业论文
你如果认识从前的我,也许会原谅现在的我。 1 绪论 1.1 概述 冲压成形作为现代工业中一种十分重要的加工方法 用以生产各种板料零件 具有很多独特的优势 其成形件具有自重轻、刚度大、强度高、互换性好、成本低、生产过程便于实现机械自动化及生产效率高等优点 是一种其它加工方法所不能相比和不可替代的先进制造技术 在制造业中具有很强的竞争力 被广泛应用于汽车、能源、机械、信息、航空航天、国防工业和日常生活的生产之中 在吸收了力学、数学、金属材料学、机械科学以及控制、计算机技术等方面的知识后 已经形成了冲压学科的成形基本理论 以冲压产品为龙头 以模具为中心 结合现代先进技术的应用 在产品的巨大市场需求刺激和推动下 冲压成形技术在国民经济发展、实现现代化和提高人民生活水平方面发挥着越来越重要的作用1.2 冲压技术的进步 进几十年来 冲压技术有了飞速的发展 它不仅表现在许多新工艺与新技术在生产的广泛应用上 如:旋压成形、软模具成形、高能率成形等 更重要的是人们对冲压技术的认识与掌握的程度有了质的飞跃[1] 现代冲压生产是一种大规模继续作业的制造方式 由于高新技术的参与和介入 冲压生产方式由初期的手工操作逐步进化为集成制造(图1-1) 生产过程逐步实现机械化、自动化、并且正在向智能化、集成化的方向发展 实现自动化冲压作业 体现安全、高效、节材等优点 已经是冲压生产的发展方向 图1-1 冲压作业方式的进化冲压自动化生产的实现使冲压制造的概念有了本质的飞跃 结合现代技术信息系统和现代化管理信息系统的成果 由这三方面组合又形成现代冲压新的生产模式-计算机集成制造系统CIMS(Computer Integrated Manufacturing System) 把产品概念形成、设计、开发、生产、销售、售后服务全过程通过计算机等技术融为一体 将会给冲压制造业带来更好的经济效益 使现代冲压技术水平提高到一个新的高度 1.3 模具的发展与现状 模具是工业生产中的基础工艺装备 是一种高附加值的高技术密集型产品 也是高新技术产业的重要领域 其技术水平的高低已成为衡量一个国家制造水平的重要标志
毕业论文外文翻译-冲压模具技术
前言 在目前激烈的市场竞争中,产品投入市场的迟早往往是成败的关键。模具是高质量、高效率的产品生产工具,模具开发周期占整个产品开发周期的主要部分。因此客户对模具开发周期要求越来越短,不少客户把模具的交货期放在第一位置,然后才是质量和价格。因此,如何在保证质量、控制成本的前提下加工模具是值得认真考虑的问题。模具加工工艺是一项先进的制造工艺,已成为重要发展方向,在航空航天、汽车、机械等各行业得到越来越广泛的应用。模具加工技术,可以提高制造业的综合效益和竞争力。研究和建立模具工艺数据库,为生产企业提供迫切需要的高速切削加工数据,对推广高速切削加工技术具有非常重要的意义。本文的主要目标就是构建一个冲压模具工艺过程,将模具制造企业在实际生产中结合刀具、工件、机床与企业自身的实际情况积累得高速切削加工实例、工艺参数和经验等数据有选择地存储到高速切削数据库中,不但可以节省大量的人力、物力、财力,而且可以指导高速加工生产实践,达到提高加工效率,降低刀具费用,获得更高的经济效益。 1.冲压的概念、特点及应用 冲压是利用安装在冲压设备(主要是压力机)上的模具对材料施加压力,使其产生分离或塑性变形,从而获得所需零件(俗称冲压或冲压件)的一种压力加工方法。冲压通常是在常温下对材料进行冷变形加工,且主要采用板料来加工成所需零件,所以也叫冷冲压或板料冲压。冲压是材料压力加工或塑性加工的主要方法之一,隶属于材料成型工程术。 冲压所使用的模具称为冲压模具,简称冲模。冲模是将材料(金属或非金属)批量加工成所需冲件的专用工具。冲模在冲压中至关重要,没有符合要求的冲模,批量冲压生产就难以进行;没有先进的冲模,先进的冲压工艺就无法实现。冲压工艺与模具、冲压设备和冲压材料构成冲压加工的三要素,只有它们相互结合才能得出冲压件。 与机械加工及塑性加工的其它方法相比,冲压加工无论在技术方面还是经济方面都具有许多独特的优点,主要表现如下; (1) 冲压加工的生产效率高,且操作方便,易于实现机械化与自动化。这是
冲压模具设计技术要求
模具设计技术要求 江淮福臻车体装备有限公司 2005年3月16日
甲方:安徽江淮福臻车体装备有限公司 乙方: 安徽江淮福臻车体装备有限公司(以下简称甲方)委托(以下简称乙方)设计项目中个冲压件套模具,为保证设计质量,经双方认真协商达成以下协议。 一、所设计冲压件的资料 注:1 各工序模具使用生产线及设备在工艺方案会签时确定 2 模具详细资料见工程图(DL) 二、双方承担的工作和责任 1、甲方
1)提供完整、清晰的产品图纸和数模,产品更改时提供书面通知,明确更改内容; 2)提供设备规格(附后); 3)负责确定设计所选用标准件的厂家; 4)负责工程图、模具图纸的会签及泡沫模型实物状态的确认; 5)负责确定工程图及模具图纸的会签日期。 2、乙方 1)审查工艺合理性,对无法完成的工序提交双方讨论,经甲方、乙方双方审查完成甲方签字后方可进行更改; 2)自双方签订订货合同日起,乙方按甲方确定的会签日期进行设计及会签; 3)乙方必须向甲方提供完整的电子版工程(DL)图(工序内容完整,图形表示清晰)和其他相关图纸、资料; 4)乙方必须对所设计的图纸进行认真校对和审核,电子版图纸上必须有设计人员、校对人员、审核人员的签名; 5)所有结论前的产品及工艺更改,涉及到设计内容的则需要修改相应工程图、模具图及检具图。对于工作量较大的,增加费用问题与甲方协商解决; 6)按甲方清单注明的零件需做成型模拟分析的,提供模拟结果并对结果负责; 7)乙方所设计模具必须符合甲方自动化生产要求:机械手上下件、气动挺件、废料自动滑出等; 8)如甲方在生产制造过程中对乙方所设计的图纸存在疑问,乙方有责任在24小时内派技术人员对现场进行解疑及指导。 三、模具寿命及冲压线分布 1、开发模具生产纲领要求:总寿命万辆,(双、单)班万辆/年。 2、冲压设备流水分布图示: 1) A线: 2) B1线:
中国冲压模具发展现状和方向
中国冲压模具的发展现状和发展方向 一、中国冲压模具的发展现状 中国冲压模具的发展现状改革开放带了我国的经济进入高速发展的时期,模具的市场的需求量也进一步的增加。模具行业也一直以15%左右的增速再发展。因此带来的模具工业企业的所有制成分的巨大变化,一些国有专业模具厂也如雨后春笋般的建立起来,同时也带来了以集体、独资、私营和合资等形式的快速发展。 赋有“模具之乡”的浙江宁波和黄岩地区是现今我国规模最大的两个地方;广东地区也渐渐掀起了开建模具厂的浪潮;其中科龙、康佳等集团纷纷建立了自己的模具制造中心;中外合资或是外商独资形式的模具企业现也有几千家。 近年许多模具企业加大了用于技术进步的投资力度,将技术进步视为企业发展的重要动力。一些国内模具企业已普及了二维CAD,并陆续开始使用UG、Pro/Engineer、I-DEAS、Euclid-IS 等国际通用软件,个别厂家还引进了Moldflow、C-Flow、DYNAFORM、Optris和MAGMASOFT 等CAE软件,并成功应用于冲压模的设计中。以汽车覆盖件模具为代表的大型冲压模具的制造技术已取得很大进步,东风汽车公司模具厂、一汽模具中心等模具厂家已能生产部分轿车覆盖件模具。此外,许多研究机构和大专院校开展模具技术的研究和开发。经过多年的努力,在模具CAD/CAE/CAM技术方面取得了显著进步;在提高模具质量和缩短模具设计制造周期等方面做出了贡献。 例如,吉林大学汽车覆盖件成型技术所独立研制的汽车覆盖件冲压成型分析KMAS软件,华中理工大学模具技术国家重点实验室开发的注塑模、汽车覆盖件模具和级进模CAD/CAE/CAM软件,上海交通大学模具CAD国家工程研究中心开发的冷冲模和精冲研究中心开发的冷冲模和精冲模CAD软件等在国内模具行业拥有不少的用户。 虽然中国模具工业在过去十多年中取得了令人瞩目的发展,但许多方面与工业发达国家相比仍有较大的差距。例如,精密加工设备在模具加工设备中的比重比较低;CAD/CAE/CAM 技术的普及率不高;许多先进的模具技术应用不够广泛等等,致使相当一部分大型、精密、复杂和长寿命模具依赖进口。 二、中国冲压模具的发展方向 模具技术的发展应该为适应模具产品“交货期短”、“精度高”、“质量好”、“价格低”的要求服务。达到这一要求急需发展如下几项: (1)全面推广CAD/CAM/CAE技术模具CAD/CAM/CAE技术是模具设计制造的发展方向。随着微机软件的发展和进步,普及CAD/CAM/CAE技术的条件已基本成熟,各企业将加大CAD/CAM技术培训和技术服务的力度;进一步扩大CAE技术的应用范围。计算机和网络的发展正使CAD/CAM/CAE技术跨地区、跨企业、跨院所地在整个行业中推广成为可能,实现技术资源的重新整合,使虚拟制造成为可能。 (2)高速铣削加工国外近年来发展的高速铣削加工,大幅度提高了加工效率,并可获得极高的表面光洁度。另外,还可加工高硬度模块,还具有温升低、热变形小等优点。高速铣削加工技术的发展,对汽车、家电行业中大型型腔模具制造注入了新的活力。目前它已向更高的敏捷化、智能化、集成化方向发展。
冲压模具技术外文翻译(含外文文献)
冲压模具技术外文翻译(含外文文献)
前言 在目前激烈的市场竞争中,产品投入市场的迟早往往是成败的关键。模具是高质量、高效率的产品生产工具,模具开发周期占整个产品开发周期的主要部分。因此客户对模具开发周期要求越来越短,不少客户把模具的交货期放在第一位置,然后才是质量和价格。因此,如何在保证质量、控制成本的前提下加工模具是值得认真考虑的问题。模具加工工艺是一项先进的制造工艺,已成为重要发展方向,在航空航天、汽车、机械等各行业得到越来越广泛的应用。模具加工技术,可以提高制造业的综合效益和竞争力。研究和建立模具工艺数据库,为生产企业提供迫切需要的高速切削加工数据,对推广高速切削加工技术具有非常重要的意义。本文的主要目标就是构建一个冲压模具工艺过程,将模具制造企业在实际生产中结合刀具、工件、机床与企业自身的实际情况积累得高速切削加工实例、工艺参数和经验等数据有选择地存储到高速切削数据库中,不但可以节省大量的人力、物力、财力,而且可以指导高速加工生产实践,达到提高加工效率,降低刀具费用,获得更高的经济效益。 1.冲压的概念、特点及应用 冲压是利用安装在冲压设备(主要是压力机)上的模具对材料施加压力,使其产生分离或塑性变形,从而获得所需零件(俗称冲压或冲压件)的一种压力加工方法。冲压通常是在常温下对材料进行冷变形加工,且主要采用板料来加工成所需零件,所以也叫冷冲压或板料冲压。冲压是材料压力加工或塑性加工的主要方法之一,隶属于材料成型工程术。 冲压所使用的模具称为冲压模具,简称冲模。冲模是将材料(金属或非金属)批量加工成所需冲件的专用工具。冲模在冲压中至关重要,没有符合要求的冲模,批量冲压生产就难以进行;没有先进的冲模,先进的冲压工艺就无法实现。冲压工艺与模具、冲压设备和冲压材料构成冲压加工的三要素,只有它们相互结合才能得出冲压件。 与机械加工及塑性加工的其它方法相比,冲压加工无论在技术方面还是经济方面都具有许多独特的优点,主要表现如下; (1) 冲压加工的生产效率高,且操作方便,易于实现机械化与自动化。这