不銹钢管内表面处理简介
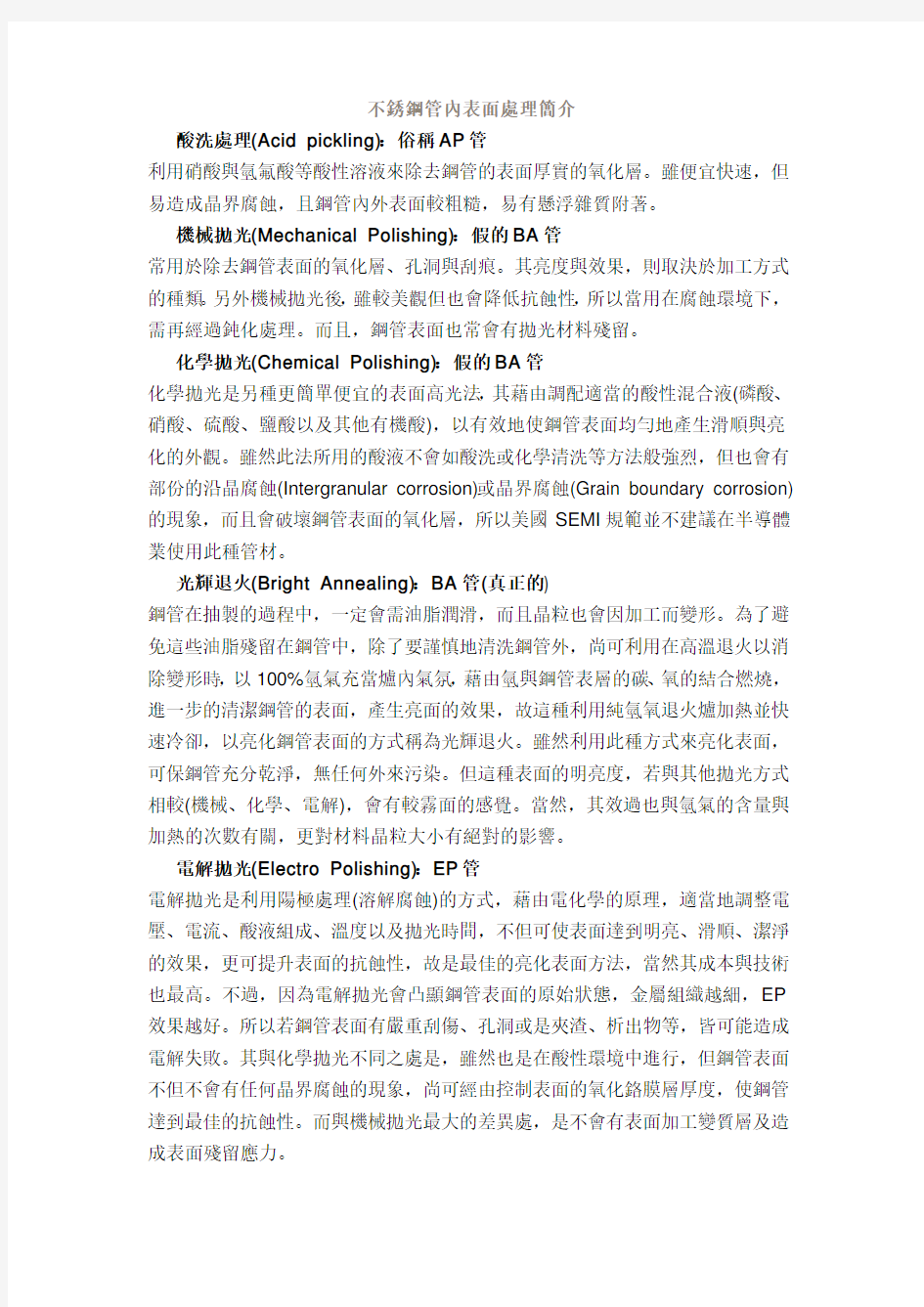

不銹鋼管內表面處理簡介
酸洗處理(Acid pickling):俗稱AP管
利用硝酸與氫氟酸等酸性溶液來除去鋼管的表面厚實的氧化層。雖便宜快速,但易造成晶界腐蝕,且鋼管內外表面較粗糙,易有懸浮雜質附著。
機械拋光(Mechanical Polishing):假的BA管
常用於除去鋼管表面的氧化層、孔洞與刮痕。其亮度與效果,則取決於加工方式的種類。另外機械拋光後,雖較美觀但也會降低抗蝕性,所以當用在腐蝕環境下,需再經過鈍化處理。而且,鋼管表面也常會有拋光材料殘留。
化學拋光(Chemical Polishing):假的BA管
化學拋光是另種更簡單便宜的表面高光法,其藉由調配適當的酸性混合液(磷酸、硝酸、硫酸、鹽酸以及其他有機酸),以有效地使鋼管表面均勻地產生滑順與亮化的外觀。雖然此法所用的酸液不會如酸洗或化學清洗等方法般強烈,但也會有部份的沿晶腐蝕(Intergranular corrosion)或晶界腐蝕(Grain boundary corrosion)的現象,而且會破壞鋼管表面的氧化層,所以美國SEMI規範並不建議在半導體業使用此種管材。
光輝退火(Bright Annealing):BA管(真正的)
鋼管在抽製的過程中,一定會需油脂潤滑,而且晶粒也會因加工而變形。為了避免這些油脂殘留在鋼管中,除了要謹慎地清洗鋼管外,尚可利用在高溫退火以消除變形時,以100%氫氣充當爐內氣氛,藉由氫與鋼管表層的碳、氧的結合燃燒,進一步的清潔鋼管的表面,產生亮面的效果,故這種利用純氫氧退火爐加熱並快速冷卻,以亮化鋼管表面的方式稱為光輝退火。雖然利用此種方式來亮化表面,可保鋼管充分乾淨,無任何外來污染。但這種表面的明亮度,若與其他拋光方式相較(機械、化學、電解),會有較霧面的感覺。當然,其效過也與氫氣的含量與加熱的次數有關,更對材料晶粒大小有絕對的影響。
電解拋光(Electro Polishing):EP管
電解拋光是利用陽極處理(溶解腐蝕)的方式,藉由電化學的原理,適當地調整電壓、電流、酸液組成、溫度以及拋光時間,不但可使表面達到明亮、滑順、潔淨的效果,更可提升表面的抗蝕性,故是最佳的亮化表面方法,當然其成本與技術也最高。不過,因為電解拋光會凸顯鋼管表面的原始狀態,金屬組織越細,EP 效果越好。所以若鋼管表面有嚴重刮傷、孔洞或是夾渣、析出物等,皆可能造成電解失敗。其與化學拋光不同之處是,雖然也是在酸性環境中進行,但鋼管表面不但不會有任何晶界腐蝕的現象,尚可經由控制表面的氧化鉻膜層厚度,使鋼管達到最佳的抗蝕性。而與機械拋光最大的差異處,是不會有表面加工變質層及造成表面殘留應力。
Subject:電解拋光技術
半導體氣體供應零組件要求高潔淨性、表面平滑性、抗蝕性、低洩漏率等,目前適用於半導體元
件的表面處理方法有:機械拋光法+化學鈍化法、化學抛光法(chemical polishing, CP)、光輝熱
處理(bright annealing, BA)與電解拋光法(electro-polishing, EP)等。由於電解拋光法具有以下
幾種特性,衍然已成為半導體製程中重要閥件與零組件處理流道表面的主要方法。
● 鈍化層:不銹鋼材料在進行EP處理後的表面,會在表面生成鈍化層,鈍化層生成原因是因為
EP在處理時,鐵鎳移去的速率比鉻快,造成表面富鉻化效應,同時在表面生成氧化鉻層,可有
效提昇表面抗腐蝕能力,此為其他種抛光無法達到的特色。
● 光澤化:抛光能力優越,較機械抛光更佳,可以達到鏡面級的光澤,商品化
的管件可以用EP
達到Ra=0.01μm的層次。
● 高潔淨度:EP製程將工程表面移去一層,因此表面之髒汙層、氧化層、雜質層、碳化層、應
力層等,都會被EP所移去,同時表面平坦化,無藏污納垢的凹陷,因此可使工件表面達到高潔
淨層度。
● 特殊形狀加工:EP過程中,接觸工件的僅有電解液,工件在處理過程中,不受任何應力,可
處理薄型工件,且可除去因機械加工產生的表面應力層。同時,EP可處理特殊形狀工件,對於特
殊形狀表面可均勻拋光,對於小型工件的外部EP處理,可大批量一次進行,可減少加工時間。
由於EP處理具有以上幾項優點,因此在半導體設備的氣體供應元件中被大量使用,也因為僅有EP
可以達到表面超高潔淨度之要求,且對於氣體流道的鈍化效果可提供優越的抗腐
蝕能力,能確保
管件不受多種特別強腐蝕性氣體腐蝕,在對於線幅越來越小的半導體製程中,潔淨度的要求越來
越高之條件下,未來對EP處理之產品的要求勢必越來越重要。
電解拋光技術在歐美早已成熟30年以上,直到近年來半導體工業的發展,才使得這項技術在國內
有發展之契機。EP技術可分為外表面與內孔表面兩種,數年前國內業者始引進外表面EP技術,然
而內孔表面EP技術因涉及電極夾治具的設計障礙,致使國內業者仍缺乏這方面之技能。本部門從
事半導體設與閥件之研發,深深瞭解EP關鍵技術在各項零組件流到表面處理的重要性,因此致力
於研究與開發內孔表面EP技術,以提昇本部門在關鍵零組件之研發與製造之能力。
電解拋光原理
電解拋光原理乃將工件接於陽極,以某種金屬接於陰極,置於電解液中通以直流電,以電解作用將
工件表面金屬移除,亦即反電鍍作用,如圖2-3所示(詳情請參考附件)。在適當的電解液和操作條
件下,使工件表面發生材料之消蝕,具有清除毛稜之作用,使工件表面光澤化與平坦化。以不銹鋼
而言,所含之元素如鐵、鉻、鎳都同時參與此反電鍍反應,在工件表面發生材料之消蝕,並發生表
面平順化作用,造成拋光效果。在此同時也會生成一些副產物,這些副產物必須小心地予以控制以
得到最高的拋光品質;例如不銹鋼所含之不同金屬成分有所差異,元素的溶解移除速率也就不盡相
同,鐵原子會先被移除掉,因此留下的表面鎳與鉻含量會變高,使得表面出現“富鉻化”的效果,
產生EP工件重要的鈍化層,此乃有助於提昇工件表面的抗蝕能力。
電解拋光之所以有抛光效果,主要有以下幾種效應:
(一) 電場集中效應:亦稱之為避雷針效應,此為最主要之拋光效應。將工件表面放大而視之,可
發現表面凹凸不平,尖突處如同避雷針,可吸附較大電場,造成局部的電流密度增加,因此
尖端處的金屬迅速的被侵蝕;而凹陷處之電流密度較低,金屬被侵蝕較少,因此有抛光平坦
化之效果。
(二) 陽極膜飽和效應(黏度效應):電解抛光過程中,將產生厚約0.1mm的陽極膜(anode film),
陽極膜呈黏膜狀,具高電阻,金屬帶正電離子不易擴散出與陰極離子結合,因此電流不易通過
。由於表面凹陷處電解液流動較慢,易形成飽和陽極膜,電流密度因而降低;而尖突處電解液
流動較快,不易生成飽和陽極膜,電流密度較高,因而具有拋效果。(三) 氣體擾動效應:電解拋光過程中,陽極會產生氧氣氣泡,而尖突處電流大,所以產生氣泡較多
,因此也較易打破陽極膜,形成抛光之效果。
電解拋光發展現況與趨勢
電解拋光技術在歐美早已成熟30年以上,目前主要專注於特殊金屬如鈮鉭等金屬的拋光技術,以及
特殊電解液的添加濟配方等方向發展。另方面,對於自動化設備及節省成本的新製程,如各種大小
管件、彎曲管件、細長無縫鋼管、大小筒槽、大量散裝件之製程及專用機自動化設備等,都是發展
之重點。以日本而言,早已完成30m無縫EP鋼管製程,並已於市場銷售,目前正研發300m無縫
鋼管EP鋼管製程。就整體EP技術而言,美國優於歐日;以無縫EP鋼管技術來說,日本技術最為領
先。早些年在台灣的民間業者已自行引入外表面EP技術,主要應用於欄杆、不銹鋼門窗光澤美化等
。幾年前,中科院為研製飛機零組件,也引進外表面EP技術;工研院化工所、清大機械所及雲林技
術學院機械系也曾就外表面EP技術進行研究。
至少內孔EP技術,主要關鍵在於夾治具的設計,其次才是電解液之配方。夾治具視待EP工件形狀與
數量而定,一般而言,夾治具必須包括電極連接端子與連接線與電源供應器相連接,外部EP夾治具
一般為掛架,懸掛工件置於電解槽內或是吊籃滾筒類以安置小型工件,內孔EP 夾治具則為提供電解
液流動通道並電解液流出入內孔。夾治具材料因需抗電解液腐蝕,需通電的通常用鎢或鈦,不通電
則選用PTFE或PP類材質。
以EP製程本身而言,夾治具設計受到工件不同而具有相當大的歧異性,由於國外廠商將夾治具的設計
列為機密,以致國內對此技術完全闕如。再則,夾治具設計需要多方面的分析模擬以及實驗的驗證,
再加以經驗之累積使成,因此在國內少有業者願意投資研發,致使此項技術延宕至今,另一項需要經
驗累積的則是EP參數的調整,此方面技術也需進行長時間的試驗及累積足夠的資料庫後,始可達到良
好的控制。同時,對於EP處理後的品質檢驗程序技術,國內的能力與經驗也略嫌不足,這方面仍有待
投入更多的時間與人力持續從事研發工作。有鑑於此,本部門於開發質流控制器的同時,也深切體會
到EP技術的重要性,因此積極開發此項關鍵技術,以期提升產品品質,並落實本土化技術。
半导体行业中不锈钢管道系统的表面处理方式
半导体行业中为了提高不锈钢管道系统的表面质量,即改善表面形态和形态结构,降低能量水平,减少介层数量,目前常见的表面处理方式有如下几种:1、机械拉拔(Plug draw)简称PD。
以塞栓精密冷拔来提高表面粗糙度,可以提高表面结构,但不会改善形态结构、能量水平和介层数量。作为最基本的表面处理工艺,机械拉拔的粗糙度为其他表面处理工艺奠定了基础。
2、机械研磨(Mechanically Polished)称MP。
以精密研磨方式来提高表面粗糙度,可以提高表面构,但不会改善形态结构、能量水平和介层数量。
3、羽布抛光(Buffed Polished)简称BP。
装饰不锈钢业常用的用来提高表面光亮度的方式,尽管Ra值可能很好,但在电子显微镜下可观察到许多裂缝,实际表面积扩大,局部有分离出来的铁素体及马氏体结构。表面夹杂许多杂质,如研磨颗粒。由于使用抛光膏,许多能量被储存在原先得到凹陷中,使得介质数量也会增加。这种管道一般不允许使用在微电子、光电子及生物制药的敏感、腐蚀介质中。
4、酸洗或钝化(Pickled & Passivated/Chemically Polished)简称AP和CP。管道经过酸洗或钝化,不会提高表面粗糙度,但可去除表面残存的颗粒,降低能量水平,但不会减少介层数量。
5、光亮烧钝(Bright Annealing)简称BA。
在加氢或真空状态高温热处理,一方面消除内部应力,另一方面在管道表面形成一层钝化膜,以改善形态结构,减少能量水平,但不会提高表面粗糙度。
6、亚电化学抛光(Anodical Cleaning)简称AC。
欧洲工厂在BA基础上再进行一道表面处理工艺,即轻度电解抛光工艺,以尽可能地减少表层面积,加厚钝化膜,从而增加耐腐蚀性能、改善表面的形态结构、减少能量水平。经过这种表面处理方式之后的产品虽然没有前面的光亮,但表面质量有了很大的提高,不会产生颗粒,减少表层铁和氧化铁的成分。
7、电化抛光(Electro-Polished)简称EP。
通过电化学抛光,可以极大地提高表面形态及结构,使表层实际面积得到最大程
度的减少。表面是一层封闭的、厚厚的氧化铬膜,能量接近合金的正常水平,同时介质数量也会降为最少。
微电子、光电子和生物制药等行业对传输敏感或腐蚀性介质的高纯、洁净管道系统一般都采用光亮烧钝(BA)、亚电化学抛光(AC)、电化抛光(EP)产品。
钢管除锈的工艺过程
钢管除锈的工艺过程 随着我国经济的快速发展,在输油管线防腐施工过程中,钢管表面处理是决定管线防腐使用寿命的关键因素之一,它是防腐层与钢管能否牢固结合的前提,也是降低管道经济损失的关键。 下面让我们来看一下钢管除锈的工艺过程: 钢管除锈的工艺过程: 工具除锈 主要使用钢丝刷等工具对钢材表面进行打磨,可以去除松动或翘起的氧化皮、铁锈、焊渣等。手动工具除锈能达到Sa2级,动力工具除锈可达到Sa3级,若钢材表面附着牢固的氧化铁皮,工具除锈效果不理想,达不到防腐施工要求的锚纹深度 清洗 利用溶剂、乳剂清洗钢材表面,以达到去除油、油脂、灰尘、润滑剂和类似的有机物,但它不能去除钢材表面的锈、氧化皮、焊药等,因此在防腐生产中只作为辅助手段。 酸洗 一般用化学和电解两种方法做酸洗处理,管道防腐只采用化学酸洗,可以去除氧化皮、铁锈、旧涂层,有时可用其作为喷砂除锈后的再处理。化学清洗虽然能使表面达到一定的清洁度和粗糙度,但其锚纹浅,而且易对环境造成污染。 喷(抛)射除锈 喷(抛)射除锈是通过大功率电机带动喷(抛)射叶片高速旋转,使钢砂、钢丸、铁丝段、矿物质等磨料在离心力作用下对钢管表面进行喷(抛)射处理,不仅可以彻底清除铁锈、氧化物和污物,而且钢管在磨料猛烈冲击和磨擦力的作用下,还能达到所需要的均匀粗糙度。 喷(抛)射除锈后,不仅可以扩大管子表面的物理吸附作用,而且可以增强防腐层与管子表面的机械黏附作用。因此,喷(抛)射除锈是管道防腐的理想除锈方式。一般而言,喷丸(砂)除锈主要用于管子内表面处理,抛丸(砂)除锈主要用于管子外表面处理。采用喷(抛)射除锈应注意几个问题。 磨料的粒径及配比
为获得较好的均匀清洁度和粗糙度分布,磨料的粒径及配比设计相当重要。粗糙度太大易造成防腐层在锚纹尖峰处变薄;同时由于锚纹太深,在防腐过程中防腐层易形成气泡,严重影响防腐层的性能。 粗糙度太小会造成防腐层附着力及耐冲击强度下降。对于严重的内部点蚀,不能仅靠大颗粒磨料高强度冲击,还必须靠小颗粒打磨掉腐蚀产物来达到清理效果,同时合理的配比设计不仅可减缓磨料对管道及喷嘴(叶片)的磨损,而且磨料的利用率也可大大提高。通常,钢丸的粒径为0.8~1.3mm,钢砂粒径为0.4~1.0mm,其中以0.5~1.0mm为主要成分。砂丸比一般为5~8。 应该注意的是在实际操作中,磨料中钢砂和钢丸的理想比例很难达到,原因是硬而易碎的钢砂比钢丸的破碎率高。为此,在操作中应不断抽样检测混合磨料,根据粒径分布情况,向除锈机中掺入新磨料,而且掺人的新磨料中,钢砂的数量要占主要的。 除锈速度 钢管的除锈速度取决于磨料的类型和磨料的排量,即单位时间内磨料施加到钢管的总动能E及单颗粒磨料的动能E1。 式中:m——磨料的喷(抛)量; V——磨料运行速度; m1——单颗粒磨料的质量。 m。的大小与磨料破碎率有关,破碎率大小直接影响表面处理作业的成本及除锈设备的费用。当设备固定不变后,m为常数,y为常数,所以E也是一个常数,但由于磨料破碎,m1发生变化,因此,一般应选择损耗率较低的磨料,这样有利于提高清理速度和长叶片的寿命。 除锈等级 对于钢管常用的环氧类、乙烯类、酚醛类等防腐涂料的施工工艺,一般要求钢管表面达到近白级(Sa2.5)。实践证明,采用这种除锈等级几乎可以除掉所有的氧化皮、锈和其他污物,锚纹深度达到40~100μm,充分满足防腐层与钢管的附着力要求,而喷(抛)射除锈工艺可用较低的运行费用和稳定可靠的质量达到近白级(Sa2.5)技术条件。
表面处理技术简介
手机常用工艺简介 作者:杨波发表人:中国手机研发网添加日期:2007-9-19手机常用工艺简介 一、金属装饰件的类型及工艺 随着消费者审美标准的提高,以及手机工艺的快速发展,为了丰富手机外观颜色搭配和提升质感 的表达效果,越来越多的各种类型的手机装饰件被应用于手机上。大致分为电铸件、铝装饰件、不锈 钢装饰件、粉末冶金件、水晶标牌、钻石及人造宝石等几类。 电铸件: (一)特点 金属感强,档次高,耐磨性好。能进行超精密加工、容易加工出形状复杂的零件;零件和模具一体。(二)工艺 刻模具(材料铜,钢,镍),也称为原始模具。模具与零件反型。采用立体雕刻机或者精密 CNC 加工。将原始模具放置到电解槽中镀镍,厚度由电解时间和电流大小决定,得到的模具和零件一样。 将电镀出的零件剥离,作为模具再镀 10~12 小时,得到的模型与零件反型,此为一级模一级模再电镀一次,称为二级模,进行微处理后,得到的模具和零件一样。二级模处理成为三级模,与零件反型。 三级模处理成为四级模,与零件一样,样件是 2~5 件。在四级模的基础上复制成凸模,再复制成凹模,循环复制,把所有的凹模连板焊接成为模具。电铸出的产品用切割机切割成产品。一张模具的使用寿 命不超过 10 次就需要报废。(在前面几级模具中,每一套都要进行微处理,处理成光面和麻面两种效果;光面用砂纸或抛光机抛光,麻面则可采用喷砂、腐蚀、电火花等工艺。) (三)表面处理及效果 镭射效果:镭射雕刻的图案一般是凹进去,其七彩效果是靠表面的细碎面进行光的反射达到的。 雕刻深度不超过 3mm,拔模在 10 度以上。夏新手机上的龙和蝴蝶是镭射雕刻,图案一般凹进去,镭 射的面很细微,容易磨损,一般做凹进去的效果,凸出来容易磨损掉。镭射加工,类似防伪标记, 但防伪标记达不到这种装饰件效果。 颜色效果:银色,为本色;黄色,镀金;黑珍珠色,镀黑珍珠镍。电铸件只能镀出三种颜色:银 色、金色、黑色。其它色只能通过后期喷涂达到 (四)设计要点 浮雕或隆起部分边缘处应留有拔模斜度,最小为10°,随产品高度增加,拔模斜度也相应增大。 字体的拔模斜度应在15°以上。铭牌的理想高度在3mm 以下,浮雕或凸起部分在0. 4~0.7mm 间。字 体的高度或深度不超过0.3mm。若采用镭射效果则高度或深度不超过0.2mm,最佳高度或深度为 0.1mm。板材的平均厚度为0.2±0.05,若产品超过此高度则应做成中空结构,并允许产品高度有 0.05mm 的误差;由于板材厚度是均匀结构,产品表面的凸起或凹陷部分背面也有相应变化。产品的 外型轮廓使用冲床加工,为防止冲偏伤到产品或产品冲切变形,其外缘切边宽度平均为0.07mm,尽 量保证冲切部分在同一平面或尽量小的弧度上,避免用力集中而造成产品变形。冲切是只能在垂直产 品的方向作业。铭牌表面效果,可采用磨砂面、拉丝面、光面、镭射面相结合的方式。光面多用于图 案或者产品的边缘,产品表面应该避免大面积的光面,否则易造成划伤;磨砂面和拉丝面多用于铭牌 底面,粗细可进行调整;在实际的生产中,磨砂面的产品要比拉丝面的产品不良率低,但是开发周期 长一些。镭射面多用于字体和图案,也可用于产品底面。若产品表面需要喷漆处理,应该提供金属漆 的色样。由于工艺的限制,应允许最终成品的颜色与色样有轻微的差异若铭牌装配时为嵌入的结构, 请提供机壳的正确尺寸及实样。若铭牌的尺寸过大过高,应在机壳上相应的部位加上支撑结构。 铝装饰件 (一)特点 效果及颜色多样化 (二)工艺 铝板拉丝
pcb表面处理方式一是osp二是hasl此两种表面处理之区别在那呢 (1)
PCB表面处理方式:一是OSP ,二是HASL,此两种表面处理之区别在那呢? 1热风整平(HAL) 热风整平(HAL)或热风焊料整平(HASL)是20世纪80年代发展起来的一种先进工艺,到了90年代中、后期,它占据着整个PCB 表面涂(镀)覆层的90%以上。只是到了90年代的末期,由于表面安装技术(SMT)的深入发展,才使HAL在PCB中的占有率逐步降低下来,但是,目前HAL在PCB表面涂(镀)覆中的占有率仍在50%左右。尽管SMT的高密度发展会使HAL在PCB中的应用机率不断下降,但是HAL技术在PCB生产中的应用仍有很长的生命力,即使禁用铅的焊料(无铅的绿色焊料),无铅的HAL技术和工艺也会开发和应用起来。 1.1热风整平工艺和应用 热风整平技术是指把PCB(一般为在制板 panel)浸入熔融的低共熔点(183℃,如图1所示)Sn/Pb(比例应等于或接近于63/37,操作温度为230∽250℃之间)合金中,然后拉出经热风(控制热风温度、风速和风刀角度,其中风刀结构与PCB板距离等已优化而固定下来)吹去多余的Sn/Pb合金,得到所要求组成和厚度的Sn/Pb合金层。在热风整平生产过程中要控制和维护好Sn/Pb合金组成的成份比例(一般要定期补充纯锡,因为才锡比铅更易于氧化,加上锡也易于与其它金属形成合金,所以锡消耗比铅要快)。同时,在高温热风整平的过程中,PCB上的铜也会熔入到Sn/Pb 合金中去,使Sn/Pb合金中含有铜的组分,由于铜和锡会形成高熔点的合金化合物,如Cu6/Sn5、Cu4/Sn3、Cu3/Sn等。当Sn/Pb合金中的铜含量≥0.3%(重量百分比)时,不仅会是使热风整平温度提高(如超过250℃以上)才能得到平整而光亮的涂覆Sn/Pb合金层,甚至会形成粗糙不平或沙石状的表面。因此应定期进行分析Sn和Pb含量与比例,以保证其比例处于62∽64/38∽36之间。同时,由于锡比铅更易于氧化,因此,熔融的锡/铅合金表面应具有耐高温的防氧化剂或耐热助焊剂等加以保护。另外,还要经常清除去在熔融的锡/铅合金表面上的氧化物和锡与铜的合金化合物(要采用比HAL更高的温度和一定保温时间,使铜与锡能充分反应,并漂浮在熔融的锡/铅合金表面上。然后降低温度到230℃左右清除去表面层或残渣),以保证熔融的锡/铅合金的组成比例和纯洁。 HAL的锡/铅合金厚度的控制是极其重要的。对于THT(通孔插装技术)来说,HAL的锡/铅合金厚度一般为5∽7um或更大些。但对于SMT(表面安装技术)来说,HAL的锡/铅合金厚度应控制在3∽5μm之间为宜,厚度太厚或太薄都会带来PCB焊接的可靠性问题。 1.2 热风整平问题和挑战 HAL的锡/铅合金的最大的优点是它具有与焊料相同的组成和成分比例,同时,它能够很好覆盖于新鲜的铜的表面上而保护了铜不被氧化和污染。因此,HAL的锡/铅合金具有极好的保护性、可焊性和可靠性。 但是,HAL的锡/铅合金层在SMT的应用中也遇到了问题和挑战,主要是来自熔融锡/铅合金的表面张力太大(约为水的表面张力的6∽8倍)和在高温下产生锡/铜金属间化合物(IMC,intermetallic compound)以及在HAL过程中PCB受到高温(230∽250℃)的热冲击等三大方面。 (1)熔融的锡/铅合金表面张力太大带来的问题和挑战。当表面安装用的PCB不断向高密度发展时,PCB的连接盘(焊盘)的密度越来越大,而其尺寸越来越小,在涂覆相同要求厚度的熔融锡/铅合金下,由于表面张力的作用,使尺寸小的连接盘上锡/铅合金层呈显“龟背”现象(如图2所示)。这种“龟背”现象将随着高密度化(或连接盘微小化)的发展而严重化起来,其结果会导致元器件(特别是SMD 表面安置器件)的引脚与连接盘之间形成“点”的接触,从而影响焊接的可靠性(特别是在高密度化焊接时,会引起位移和错等位)问题.
各种表面处理简介
各種表面處理簡介 1.Entek(有機保焊處理)—指裸銅板之OSP處理 原為美商公司Enthone所開發的護銅皮膜技術,商名簡稱為Entek。係利用Banzotriazo(BTA)有機化學品的槽液,對裸銅面(焊墊)進行一種透明膜之護銅處理,而達到護銅和可焊(易溶於微酸液中)的雙重目的。 早期曾在IBM之PCB流程中充作暫時性的護銅劑,品名稱為CU-56,其改良後的現役商品稱為”Entek Plus CU-106A”,可代替噴錫做為細線薄板的可焊處理層,對降低成本有很大好處。 但此種106A常會在金手指表面上形成薄膜,有礙接觸導電的品質。新型改良品106X已無此種缺點。 2.Electroless Nickel/ Immersion Gold (EN/IG)化鎳浸金 許多面積較小或不適於噴錫的板類,經常在裸銅焊墊或焊環上,加做化學鎳與浸鍍金的皮膜,可達到焊接零件的目的外,尚可執行”接觸”導通(Contact),散熱與打線的其他功能,是近年來筆記型電腦板類與手機板類的主要表面處理皮膜。 不過因其焊點強度與可靠度時常出問題,目前手機板許多焊點已改成了OSP有機保焊劑處理,而只在按鍵或圍牆基地上改採用選擇性的EN/IG了。 至於”浸鎳金”的生長,則是一種無須還原劑的典型”置換”(Replacement)反應,也就是說當”化學鎳表面”進入浸金槽液中時,在鎳層被溶解拋出兩個電子的同時,其”金層”也隨即自鎳表面取得電子而沉積在鎳金屬上。一旦鎳表面全被金層所蓋滿後,金層的沉積反應逐漸停止,很難增加到相當的厚度,至於另一系列”厚化金”,則還須強力的還原劑方可使金層逐漸加厚。 一般而言,化鎳層厚度幾乎可以無限增長,實用規格以150~200u”為宜,而浸鍍金層的厚度則以2~3u”而已,厚化金有時可達20~30u”,當然價格也就另當別論了。 3. Hot Air Solder Leveling (HASL)噴錫 是將印過綠漆半成品的板子浸在溶錫液體中,使其孔壁及裸銅焊墊上沾滿銲錫,接著立即自錫池中提出,再以高壓的熱風自兩側用力將孔中的填錫吹出,但仍使孔壁及板面都能沾上一層有助於焊接的銲錫層,此種製程稱為”噴
原产地证明种类
原产地证明种类 FORM A: GENERALIZED SYSTEM OF PREFERENCES CERTIFICATE OF ORIGIN(COMBINED DECLARATION AND CERTIFICATE)FORM A 它是受惠国(一般为发展中国家)的原产品出口到给惠国(一般为发达国家)时享受普惠制减免关税待遇时必备的官方凭证,所有的给惠国都接受。格式A证书由受惠国出品商填制申报,受惠国签证机构审核,证明及签发。在我国,国家出入境检验检疫局是签发普惠制产地证的官方机构。 发达国家对进口商品征税至少有三种税率标准:一般税率、最惠国待遇税率、普惠制税率GPS 目前给予我国普惠制待遇的国家共39个:欧盟27国(比利时、丹麦、英国、德国、法国、爱尔兰、意大利、卢森堡、荷兰、希腊、葡萄牙、西班牙、奥地利、芬兰、瑞典、波兰、捷克、斯洛伐克、拉脱维亚、爱沙尼亚、立陶宛、匈牙利、马耳他、塞浦路斯、斯洛文尼亚、罗马尼亚、保加利亚)、挪威、瑞士、土耳其、俄罗斯、白俄罗斯、乌克兰、哈萨克斯坦、日本、加拿大、澳大利亚、新西兰和列支敦士登公国。但有1个给惠国不对中国给惠,即美国 FORM B: 《亚太贸易协定》原产地证明书 2006年9月1日起签发《亚太贸易协定》原产地证书。可以签发《亚太贸易协定》原产地证书的国家有:韩国、斯里兰卡、印度、孟加拉等4个国家。降税幅度从5%到100%不等 FORM D: 是中国出入境检验检疫局针对我国出口到东盟十国的货物所签发的一种产地证,就跟FORM A一样,在当地的商检局可以办理。 FORM E: 中国- 优惠原产地证明书 可以签发《中国——东盟自由贸易区》优惠原产地证书的国家有:文莱、柬埔寨、印尼、老挝、马来西亚、缅甸、菲律宾、新加坡、泰国、越南等10个国家。中国和东盟六个老成员国(即文莱、印度尼西亚、马来西亚、菲律宾、新加坡和泰国)2010年1月1日将关税最终削减为零。 FORM F: 中华人民共和国政府和智利共和国政府自由贸易协定 FORM L: 《CERTIFICATE OF ORIGIN FORM FOR CHINA-COSTA RICA FREE TRADE AGREEMENT》凭贸促会出具的中国-哥斯达黎加原产地证书FORM L可享受10%至100%的关税减免 FORM M: 是尼日利亚买方要申请的一个表格,上面会有一个FORM M编号。是进口商向尼日利亚当地银行领取,然后依据出口商这边提供的P/I (PROFORMA INVOICE,就是形式发票)填写,填写FORM M表的内容应该和P/I中的内容是完全一致。然后将填写完毕的FORM M表连同P/I交银行,这样进货商在尼日利亚就完成了进口前的必要手续。申请下来的FORM M号码甚至申请公司名称要求显示在提单上,这主要是关系着尼日利亚当地清关及外汇管制. FORM P: Certificate of Origin China-Pa-kistan FTA (Combined Declaration and Certificate) 中巴产地证FORM P的签发,限于已公布的《中国—巴基斯坦自贸区协定》项下给予关税优惠的产品,这些产品必须符合《中国—巴基斯坦自由贸易区原产地规则》。
钢管的表面处理技术
钢管表面处理技术 涂塑钢管的主要生产工艺包括连接方式的焊接、钢管表面处理和钢管涂塑等过程,在此过程中表面处理担任着及其重要的角色。前期钢管表面的处理对后期涂塑产品质量产生较大的影响,这种影响主要包括涂层气孔、附着力低下和表面杂质等。目前国内较为常见的钢管表面处理技术主要包括酸洗磷化、抛丸、喷砂。 酸洗磷化:酸洗磷化是一种化学处理技术,酸洗是利用在配槽液中添加以盐酸为主要添加物辅以其他效果溶液达到钢管除锈目的一种方法。磷化是指在经酸洗、水洗、表面调节、水洗等环节后,利用磷化液配槽液在钢管表面形成一层致密的磷化膜以达到增强钢管表面附着力和产生一定防腐效果的技术。经酸洗磷化后的钢管除锈完全,钢管表面磷化膜较为粗糙,涂塑后能较好的达到涂层对附着力的要求。酸洗磷化对任何规格型号的管材均有较好的处理效果,但生产废液处理难度较高、处理周期较长,在防腐行业中是一种采用率较小的表面处理方式。 抛丸:抛丸是一种物理处理技术,通过大功率离心抛头高速旋转,使钢砂、钢丸、铁丝切段、矿物质等磨料在离心力作用下对钢管表面进行表面处理,不仅可以彻底清除铁锈、氧化物和污物,而且钢管在磨料猛烈冲击和磨擦力的作用下,还能达到所需要的平均粗拙度。抛丸除锈不仅可以扩大管子表面的物理吸附作用,而且可以增强防腐层与钢管表面的机械黏附作用。抛丸是一种较为理想的处理技术,且磨料在一定程度内可循环使用,但是在小口径管材内表面处理上存在较为大的弊端。 喷砂:喷砂同是一种物理处理技术,是采用压缩空气为动力,以形成高速喷射束将喷料(铜矿砂、石英砂、金刚砂、铁砂)高速喷射到需要处理的钢管表面,使钢管表面的外表面的外表或形状发生变化的一种处理技术。由于磨料对工件表面的冲击和切削作用,使钢管的表面获得一定的清洁度和不同的粗糙度,使钢管表面的机械性能得到改善,因此提高了工件的抗疲劳性,增加了它和涂层之间的附着力,延长了涂膜的耐久性。喷砂时的喷料可以根据钢管表面处理要求进行选择,和抛丸相同,喷料可回收(石英砂除外),但是喷砂在大口径管材表面处理上处理效果不明显。 在行业实际生产过程中,常采用外抛丸与内喷砂结合的方式进行小口径管材的表面处理,对于大口径的管材则采用内外抛丸的方式进行。 研发中心技术部 孔德彬
表面处理介绍
摘要:本文主要介绍不锈钢的几种表面处理工艺,介绍了其特性、优缺点以及如何应用这些工艺技术对不锈钢产品进行表面精饰,指出了不锈钢产品更广泛的用途及市场前景。关键词:不锈钢;表面处理技术;亚光处理;光亮处理;彩色处理 1、前言 不锈钢表面精饰处理技术分为亚光处理技术、镜面光亮处理技术、表面彩色处理技术。目前这些工艺技术应用于不同产品和不同领域都得到极好效果。 2、不锈钢亚光处理技术应用 不锈钢亚光处理技术是指加工成型的产品达到均匀的银白色,与不锈钢本身色泽一致,并具有金属光泽。这一般指制作大型不锈钢产品而言,因为大型不锈钢件经过卷板、冲压、折边和焊接加工过程,加工成型的工件表面有焊缝及油污、铁锈、黄斑等,既不美观,又易锈蚀,降低了其不锈钢产品的质量和价值。 要使不锈钢产品出厂达到美观,受到客户的欢迎,就必须对不锈钢产品进行表面精饰处理加工。 于大型不锈钢件产品一般采用成型后进行亚光处理,不过在处理前也可先作部件预处理,复合后再作最后处理。经过这个处理既能达到外表美观,又能提高其防腐性和防变色性能。也可先作喷砂处理然后再进行酸洗钝化处理来达到亚光目的。 经过上述方法处理后,不锈钢产品的防腐性可提高2~3倍。因为不锈钢之所以不会生锈主要由于有铬、镍成分存在,再经过亚光处理,不但能消除不锈钢基体夹杂的杂质和表面富铁层,而且能使铬、镍富集在表面,形成完整纯化膜,起到较好的防腐作用。 3、不锈钢镜面光亮处理技术应用 根据不锈钢产品的复杂程度和用户要求情况不同,可分别采用机械抛光、化学抛光、电化学抛光等方法来达到镜面光泽。 下面笔者分别介绍这三种工艺方法的优缺点,供大家参考选用,见表1。 表1 三种抛光工艺的优缺点 项目 方法优点缺点适用产品备注 机械抛光整平性好,光亮劳动强度大,污染严重,复杂无法加工,光泽下降,易生锈,投资
技术澄清模板
江苏民生 技术澄清 (2013.7.24,双方确认) 1、在本标技术文件中,甲方——指招标方、买方、业主;乙方——指投标方、卖方、供货方。请在技术文件中,统一用“甲方”、“乙方”表述。 答复:我公司标书已送出,纸质版和电子版的标书上已更改不了。 如预中标后,另行说明。 2、本标设备供货由乙方总包,即设备制造、设备外表面防腐、双管板管程内涂防腐、设备运输。设备制造和双管板内涂防腐分项报价。 答复:我公司报价没有包含内涂防腐的价格,双管板换热器每台内防腐价格为4万元。 3、对双管板设备内涂防腐项目,由乙方负责推荐2至3个具有该防腐业绩的厂家(含厂家资料介绍)给甲方,共同协商确定最终双管板管程内涂防腐厂家。其内涂防腐方案、报价、防腐质量等均由投标方负责。 答复:双管板设备内涂防腐厂家我公司没有合作,无法提供,可接受甲方指定内涂防腐厂家,本条对商务报价无影响。 4、设备外表面防腐采用“两底;两中”涂层,底层、中层防腐涂料的选择按成达设计院《涂漆规定》。 答复:满足要求。 5、在“一、综述 2. 规范标准及引用文件”中,漏掉部分主要材料、制造标准:请添加在技术标书中。 5.1 GB13296-2007锅炉、热交换器用不锈钢无缝钢管 5.2 GB8163-2008输送流体用无缝钢管 5.3 GB9948-2006石油裂化用无缝钢管 5.4 GB713-2008;锅炉和压力容器用钢板 5.5 GB 24511-2009 承压设备用不锈钢钢板及钢带. 5.6成达设计院防腐规定: 5.6.1 CDT0032-1806-2012防腐涂层及衬里钢壳设备表面处理施工工程技术规定; 5.6.2 外防腐设计规定:00-46-0000-01-015涂漆规定; 5.6.3 双管板内涂防腐01-00-0000-32-005漆酚酞螯合高聚防腐涂料防腐施工要求。
原产地证书类型和自助打印2020.04.20
我国的原产地证书主要分为三大类——非优惠原产地证书、优惠原产地证书和专用原产地证书。 1)非优惠原产地证书 俗称一般原产地证书或普通原产地证书,英文名称为Certificate of origin,简称C/O或CO。签发这种证书的,通常出口到是中东、非洲、东南亚、中南美洲等地的国家。 2)优惠原产地证书 优惠原产地证书包括绝大多数发达国家给予我国的普惠制待遇(FORM A证书),以及中国与一些国家或地区签订有双边或多变优惠贸易协定的(FORM B证书,FORM E证书,FORM F证书,FORM P证书,FORM N证书,FORM X证书等)。优惠原产地证书一般由各地出入境检验检疫机构签发。 (1)普惠制原产地证书(FORM A证书) 可签发FORM A 证书的国家为:英国、法国、德国、意大利、荷兰、卢森堡、比利时、爱尔兰、丹麦、希腊、西班牙、葡萄牙、奥地利、瑞典、芬兰、波兰、匈牙利、捷克、斯洛伐克、斯洛文尼亚、爱沙尼亚、拉脱维亚、立陶宛、塞浦路斯、马耳他、保加利亚、罗马尼亚、瑞士、列支敦士登、挪威、俄罗斯、白俄罗斯、乌克兰、哈萨克斯坦、日本、澳大利亚、新西兰、加拿大、土耳其共39个,不包括美国。 (2)《亚太贸易协定》原产地证书(FORM B 证书) 可签发FORM B 证书的国家为:中国、印度、斯里兰卡、孟加拉国、老挝和韩国(《亚太贸易协定》成员国)。 (3)中国-东盟自由贸易区原产地证书(FORM E 证书) 可签发FORM E 证书的国家为:中国、老挝、越南、泰国、缅甸、柬埔寨、菲律宾、文莱、印度尼西亚、马来西亚和新加坡(东盟成员国)。 (4)中国-巴基斯坦自由贸易区原产地证书(FORM P 证书) 中国产品出口到巴基斯坦,中国出口商向各地出入境检验检疫机构申请签发FORM P 证书,巴基斯坦给予FORM P证书项下货物关税优惠待遇;巴基斯坦产品出口到中国,巴基斯坦出口商向巴基斯坦有关部门申请签发FORM P 证书,中国给予FORM P证书项下货物关税优惠待遇。这是互惠的(跟FROM A的单边给惠有根本区别)。 以下FORM F、FORM N、FORM X、FORM S等证书同理,都是互惠的优惠原产地证书。 (5)中国-智利自由贸易区原产地证书(FORM F 证书) (6)中国-新西兰自由贸易区原产地证书(FORM N 证书) (7)中国-新加坡自由贸易区优惠原产地证书(FORM X 证书) (8)中国-瑞士自由贸易协定产地证明书(FORM S 证书) (9)中国-秘鲁自由贸易区优惠原产地证书(中国-秘鲁FTA证书) (10)中国-哥斯达黎加自由贸易区优惠原产地证书(FORM L证书)
钢管的表面处理方法
钢管的表面处理方法 随着我国经济的持续发展,国家大力发展能源行业,长输油气管线是能源保障的重要方式,在输油(气)管线防腐施工过程中,螺旋钢管表面处理是决定管线防腐使用寿命的关键因素之一,它是防腐层与钢管能否牢固结合的前提。经研究机构验证,防腐层的寿命除取决于涂层种类、涂覆质量和施工环境等因素外,钢管的表面处理对防腐层寿命的影响约占50%,因此,应严格按照防腐层规范对钢管表面的要求,不断探索和总结,不断改进钢管表面处理方法。 1、清洗 利用溶剂、乳剂清洗钢材表面,以达到去除油、油脂、灰尘、润滑剂和类似的有机物,但它不能去除钢材表面的锈、氧化皮、焊药等,因此在防腐生产中只作为辅助手段。 2、工具除锈 主要使用钢丝刷等工具对钢材表面进行打磨,可以去除松动或翘起的氧化皮、铁锈、焊渣等。手动工具除锈能达到Sa2级,动力工具除锈可达到Sa3级,若钢材表面附着牢固的氧化铁皮,工具除锈效果不理想,达不到防腐施工要求的锚纹深度 3、酸洗 一般用化学和电解两种方法做酸洗处理,管道防腐只采用化学酸洗,可以去除氧化皮、铁锈、旧涂层,有时可用其作为喷砂除锈后的再处理。化学清洗虽然能使表面达到一定的清洁度和粗糙度,但其锚纹浅,而且易对环境造成污染。 4、喷(抛)射除锈
喷(抛)射除锈是通过大功率电机带动喷(抛)射叶片高速旋转,使钢砂、钢丸、铁丝段、矿物质等磨料在离心力作用下对钢管表面进行喷(抛)射处理,不仅可以彻底清除铁锈、氧化物和污物,而且钢管在磨料猛烈冲击和磨擦力的作用下,还能达到所需要的均匀粗糙度。 喷(抛)射除锈后,不仅可以扩大管子表面的物理吸附作用,而且可以增强防腐层与管子表面的机械黏附作用。因此,喷(抛)射除锈是管道防腐的理想除锈方式。一般而言,喷丸(砂)除锈主要用于管子内表面处理,抛丸(砂)除锈主要用于管子外表面处理。采用喷(抛)射除锈应注意几个问题。 4.1除锈等级 对于钢管常用的环氧类、乙烯类、酚醛类等防腐涂料的施工工艺,一般要求钢管表面达到近白级(Sa2.5)。实践证明,采用这种除锈等级几乎可以除掉所有的氧化皮、锈和其他污物,锚纹深度达到40~100μm,充分满足防腐层与钢管的附着力要求,而喷(抛)射除锈工艺可用较低的运行费用和稳定可靠的质量达到近白级(Sa2.5)技术条件。 4.2喷(抛)射磨料 为了达到理想的除锈效果,应根据螺旋钢管表面的硬度、原始锈蚀程度、要求的表面粗糙度、涂层类型等来选择磨料,对于单层环氧、二层或三层聚乙烯涂层,采用钢砂和钢丸的混合磨料更易达到理想的除锈效果。钢丸有强化钢表面的作用,而钢砂则有刻蚀钢表面的作用。钢砂和钢丸的混合磨料(通常钢丸的硬度为40~50HRC,钢砂的硬度为50~60HRC可用于各种钢表面,即使是用在C级和D级锈蚀的钢表面上,除锈效果也很好。
常见表面处理技术介绍
常见表面处理技术介绍 电镀(电沉积) 化学镀阳极氧化(铝, 镁, 钛及它们的合金 化学氧化(铝及其合金,钢铁等等) 电化学及化学转化学铬酸监处理(钢铁上的锌,铬镀层,铝, 镁, 铜) 磷酸监处理(磷化) 热浸镀(常用的有热浸锌, 锡, 铝, 铅) 火焰喷涂 气喷涂 爆炸喷涂 热濆涂电弧喷涂 电濆涂等离子喷涂 高频感应喷涂 橡胶涂层 非金属涂覆塑料涂层 油漆涂层 渗镀 化学气象沉积 扩散涂镀真空镀膜 包镀 达克罗(Dacromet,浸入锌–铝,锌–铝等浆液中,形成涂层,然后烘烤干燥成膜) 1.磷酸监皮膜处理 大陆称为磷化处理 1.1磷酸监皮膜处理 2H3PO4+M→M(H2PO4)+H2 3M(H2PO4)2→4H3PO4+M3(PO4)2 M(H2PO4)2→MHPO4+H3PO4 生成的M3(H2PO4)2和MHPO4为磷酸监膜的主要成分 1.2磷酸监皮膜的性质和用途 (1)耐蚀性 在大气条件下很稳定,在有机油类,苯,苯及各种气种体燃料中有很好的耐蚀性.但磷酸监皮膜不耐酸,碱,
氨,海水及水蒸气等.磷酸监膜经过封闭处理后能大大提高其耐蚀性. (2)吸附性 磷酸监膜具有多孔构,有很好的吸附性,因此常用作油漆的底层和吸附润滑油后作为减摩层和润滑层. (3)电绝缘性 磷酸监膜是高电阻膜层,有很好的电绝缘性,击穿电压为240~250V,涂绝缘漆后可耐1000~1200V,又由于磷酸监膜不影响透磁性,因此常用作电磁装置的硅钢片. (4)不粘附熔融金属的特性 此特性用于在热浸锌,锡铅合金时保护不需要浸涂部分.在浇铸减摩合金和电机铸铝转子时,将钢膜作磷酸监处理,以防粘附. 1.3邻酸监膜成机理和构成 1.4分类 钢铁用化成处理剂 铝用化成处理剂 锌用化成处理剂 不锈钢用化成处理剂 铜用化成处理剂 镁用化成处理剂 其他化成处理剂 涂装打底用的化成处理剂 塑性加工用化成处理剂 防锈用化成处理剂 耐磨用化成处理剂 绝缘用化成处理剂 塑料迭片用化成处理剂 涂装打底用皮膜特点: 致密, 均匀, 薄得适当 结晶粗大会吸入涂料而减少光泽:不均匀会降低涂装后的耐蚀性;由于磷酸监膜很硬很脆,皮膜过厚的话,涂装后遭后到弯曲或冲击等外力时,即使别无缺陷,也可能脱落. 防锈用皮膜特点: 致密, 均匀, 厚度越厚越好,孔隙率越低越好. 表
pcb表面处理
常见的PCB表面处理工艺 这里的“表面”指的是PCB上为电子元器件或其他系统到PCB的电路之间提供电气连接的连接点,如焊盘或接触式连接的连接点。 裸铜本身的可焊性很好,但是暴露在空气中很容易氧化,而且容易受到污染。这也是PCB必须要进行表面处理的原因。 1、HASL 在穿孔器件占主导地位的场合,波峰焊是最好的焊接方法。采用热风整平(HASL,Hot-air solder leveling)表面处理技术足以满足波峰焊的工艺要求,当然对于结点强度(尤其是接触式连接)要求较高的场合,多采用电镀镍/金的方法。HASL是在世界范围内主要应用的表面处理技术,但是有三个主要动力推动着电子工业不得不考虑HASL的替代技术:成本、新的工艺需求和无铅化需要。 从成本的观点来看,许多电子元件诸如移动通信和个人计算机正变成平民化的消费品。以成本或更低的价格销售,才能在激烈的竞争环境中立于不败之地。 组装技术发展到SMT以后,PCB焊盘在组装过程中要求采用丝网印刷和回流焊接工艺。在SMA场合,PCB表面处理工艺最初依然沿用了HASL技术,但是随着SMT器件的不断缩小,焊盘和网板开孔也在随之变小,HASL技术的弊端逐渐暴露了出来。HASL技术处理过的焊盘不够平整,共面性不能满足细间距焊盘的工艺要求。 环境的关注通常集中在潜在的铅对环境的影响。 2、有机可焊性保护层(OSP)
OSP的保护机理 故名思意,有机可焊性保护层(OSP, Organic solderability preser vative)是一种有机涂层,用来防止铜在焊接以前氧化,也就是保护P CB焊盘的可焊性不受破坏。目前广泛使用的两种OSP都属于含氮有机化合物,即连三氮茚(Benzotriazoles)和咪唑有机结晶碱(Imida zoles)。它们都能够很好的附着在裸铜表面,而且都很专一―――只情有独钟于铜,而不会吸附在绝缘涂层上,比如阻焊膜。 连三氮茚会在铜表面形成一层分子薄膜,在组装过程中,当达到一定的温度时,这层薄膜将被熔掉,尤其是在回流焊过程中,OSP比较容易挥发掉。咪唑有机结晶碱在铜表面形成的保护薄膜比连三氮茚更厚,在组装过程中可以承受更多的热量周期的冲击。 OSP涂附工艺 清洗: 在OSP之前,首先要做的准备工作就是把铜表面清洗干净。其目的主要是去除铜表面的有机或无机残留物,确保蚀刻均匀。 微蚀刻(Microetch):通过腐蚀铜表面,新鲜明亮的铜便露出来了,这样有助于与OSP的结合。可以借助适当的腐蚀剂进行蚀刻,如过硫化钠(sodium persulphate),过氧化硫酸(peroxide/sulfuric aci d)等。 Conditioner:可选步骤,根据不同的情况或要求来决定要不要进行这些处理。 OSP:然后涂OSP溶液,具体温度和时间根据具体的设备、溶液的特性和要求而定。
材料表面处理工艺
材料表面处理工艺 一、表面处理分以下方式: 1、机械表面处理:喷砂、拉丝、机械抛光、压纹、喷涂、抛丸、磨光、刷光、刷漆、抹油化学表面处理:QPQ处理、光中氮化、铬化、镀铬、镀锌、化学镀镍、化学抛光、发黑/发蓝、酸洗 2、电化学表面处理:阳极氧化、磷化、电化学镀镍、电化学抛光、电泳。 现代化超硬化表面处理:TD覆层处理、物理气相沉积(PVD)、物料化学气相沉积(PCVD)、化学气相沉积(CVD) 3、其他类型表面处理:离子镀膜、离子注入、激光表面处理 二、机械表面处理说明: 1、喷砂:利用高速砂流的冲击作用清理和粗化零件表面,行成哑光珍珠银面。 特点:提高工件抗疲劳性,增加工件与涂层的附着力,延长涂层的耐久性,利于涂料的流平和装饰、表面易脏。 用途:可适用所有黑色金属及铝合金材料进行表处前进行或者不锈钢钣金表面。 2、拉丝:通过研磨产品在工件表面形成线纹,起到装饰效果的表面处理,形成缎面效果,体现金属材料的质感 3、机械抛光:利用抛光工具和磨料颗粒或其它抛光介质对工件表面进行修饰加工,降低表面粗糙度,获得光亮、平整表面的加工方式。 4、压纹:压制各种纹理 5、喷涂:覆盖其他非金属涂层。钢钣金常用喷涂颜色:大波纹米白色静电喷涂、表面粉末静电喷涂黑色亚光、黑色细砂纹静电喷涂 三、化学表面处理说明: 1、QPQ:将黑色金属放入两种性质不同的盐浴中,通过多种元素渗入金属表面形成复合渗层,使表面改性的目的。 特点:良好的耐磨性和耐疲劳性;良好的抗腐蚀性;变形小;时间周期短;无公害。误差可保持在0.005mm。 颜色:亮黑色 用途:可适用所有黑色金属材料。 2、光中氮化:QPQ升级工艺,将钢或不锈钢放入由多种元素混合的盐浴中进行渗透处理,
原产地证 附样本
原产地证 C/O为CERTIFICATE OF ORIGIN的简称,意思为“原产地证书”,以下为具体内容。 一、原产地证书的作用 原产地证明书(CERTIFICATE OF ORIGIN)是出口商应进口商要求而提供的、由公证机构或政府或出口商出具的证明货物原产地或制造地的一种证明文件。原产地证书是贸易关系人交接货物、结算货款、索赔理赔、进口国通关验收、征收关税在有效凭证,它还是出口国享受配额待遇、进口国对不同出口国实行不同贸易政策的凭证。 二、原产地证书的类型 根据签发者不同,原产地证书一般可分为以下三类: ①商检机构出具的原产地证书, 如:中华人民共和国检验检疫局(CIQ)出具的普惠制产地证格式A(GSP FORM A);一般原产地证书(CERTIFICATE OF ORIGIN)。 ②商会出具的产地证书, 如:中国国际贸易促进委员会(CCPIT)出具的一般原产地证书,简称贸促会产地证书(CCPIT CEERTIFICATE OF ORIGIN); ③制造商或出口商出具的产地证书; 在国际贸易实务中,应该提供哪种产地证明书,主要依据合同或信用证的要求。一般对于实行普惠制国家出口货物,都要求出具普惠制产地证明书。如果信用证并未明确规定产地证书的出具者,那么银行应该接受任何一种产地证明书。现在我国多数出口商习惯于使用贸促会出具的证书。 三、原产地证书的申请 根据我国的规定,企业最迟于货物报关出运前三天向签证机构申请办理原产地证书,并严格按照签证机构的要求,真实、完整、正确地填写以下材料: ①《中华人民共和国出口货物原产地证书/加工装配证明书申请书》; (见附页)此处显示一份《一般原产地证明书/加工装配证明书》图5-1(国际商务单证103) ②《中华人民共和国出口货物原产地证明书》一式四份; ③出口货物商业发票;
不锈钢管表面处理最有效的方法
随着我国经济的持续发展,国家大力发展能源行业,长输油气管线是能源保障的重要方式,在输油(气)管线防腐施工过程中,不锈钢管表面处理是决定管线防腐使用寿命的关键因素之一,它是防腐层与不锈钢管能否牢固结合的前提。经研究机构验证,防腐层的寿命除取决于涂层种类、涂覆质量和施工环境等因素外,不锈钢管的表面处理对防腐层寿命的影响约占50%,因此,应严格按照防腐层规范对钢管表面的要求,不断探索和总结,不断改进钢管表面处理方法。 1、清洗 利用溶剂、乳剂清洗不锈钢材表面,以达到去除油、油脂、灰尘、润滑剂和类似的有机物,但它不能去除钢材表面的锈、氧化皮、焊药等,因此在防腐生产中只作为辅助手段。 2、工具除锈 主要使用不锈钢钢丝刷等工具对钢材表面进行打磨,可以去除松动或翘起的氧化皮、铁锈、焊渣等。手动工具除锈能达到Sa2级,动力工具除锈可达到Sa3级,若钢材表面附着牢固的氧化铁皮,工具除锈效果不理想,达不到防腐施工要求的锚纹深度。 3、酸洗 一般用化学和电解两种方法做酸洗处理,管道防腐只采用化学酸洗,可以去除氧化皮、铁锈、旧涂层,有时可用其作为喷砂除锈后的再处理。化学清洗虽然能使表面达到一定的清洁度和粗糙度,但其锚纹浅,而且易对环境造成污染。 4、喷(抛)射除锈 喷(抛)射除锈是通过大功率电机带动喷(抛)射叶片高速旋转,使钢砂、钢丸、铁丝段、矿物质等磨料在离心力作用下对钢管表面进行喷(抛)射处理,不仅可以彻底清除铁锈、氧化物和污物,而且不锈钢管在磨料猛烈冲击和磨擦力的作用下,还能达到所需要的均匀粗糙度。 喷(抛)射除锈后,不仅可以扩大管子表面的物理吸附作用,而且可以增强防腐层与管子表面的机械黏附作用。因此,喷(抛)射除锈是管道防腐的理想除锈方式。一般而言,喷丸(砂)除锈主要用于管子内表面处理,抛丸(砂)除锈主要用于管子外表面处理。采用喷(抛)射除锈应注意几个问题。 4.1除锈等级 对于钢管常用的环氧类、乙烯类、酚醛类等防腐涂料的施工工艺,一般要求钢管表面达到近白级(Sa2.5)。实践证明,采用这种除锈等级几乎可以除掉所有的氧化皮、锈和其他污物,锚纹深度达到40~100μm,充分满足防腐层与不锈钢管的附着力要求,而喷(抛)射除锈工艺可用较低的运行费用和稳定可靠的质量达到
原产地证明种类
原产地证明种类编辑本段原产地证书的三大特性 真实性是原产地证明的核心 不能体现真实和反映事物本来面目的任何证明都是伪证。如果由于明同样如此。因此, 证明行为人, 不管是法人还是自然人, 公正是确保证明结论真实可靠的基矗 合法性是原产地证明有用的基本条件 货物原产地证明书在国际贸易中能否起到居间证明、举证作用以及通关入境和享受市场准入等相关作用, 主要取决于证书是否合法, 签证机构法律地位是否明确等。同时, 也取决于签证行为人的签证程序是否完整, 依据是否明确, 诸如与有关鉴定的标准、国际贸易惯例、公约、规则等是否相符, 都是导致证书是否合法的因素。因此, 就货物原产地证明的合法性而言, 应注意: ( 1 ) 签证机构的法律地位是确立的; ( 2 ) 签证行为是准确和规范的; ( 3 ) 证明事实的依据是确凿的。那种认为“原产地证明的认受性并不取决于签发方, 而是取决于要求方即进口方”说法, 显然有失偏颇。 准确性是原产地证明的灵魂 货物原产地证明和其他鉴定业务一样都应亲自实践,以确保证明结论的准确。为此签证行为人应: ( 1 ) 对货物原产地的鉴定程序是准确和规范的。按照签证程序的基本要求, 完成签证程序。诸如标识、标志、牌号、产品说明书、中性包装货物的流通动态以及原产地规则的掌握和运用等等, 都必须是规范、有序的。 ( 2 ) 用以检测货物质量和品味的仪器设备、器具、试剂和环境等必须符合检验、鉴定依据规定的技术条件和应达到的精度。 ( 3 ) 对证明货物原产地结论所依据的材料必须进行客观、周密的调查了解, 分析研究, 做到立论有据, 结论准确。 编辑本段原产地证书的类型 原产地明书根据签发对象不同,一般有三大类:第一类是普惠制原产地证明书;第二类是一般原产地证明书;第三类是某些专业性原产地证明书。 一般原产地证 一般原产地证的定义 一般原产地证,即我们常说的CO(CERTIFICATE OF ORIGIN),是原产地证的一种,其是用以证明有关出口货物生产地、制造地的一种证明文件,是在国际贸易行为中证明货物“原籍”的证书。在特定情况下进口国据此对进口货物给予不同的关税待遇,具有重要意义。 在我国,凡符合“中华人民共和国进出口货物原产地条例”规定的出口产品均可申请办理一般原产地证明书。 办理原产地证的注册登记须知 1.填写《申请一般原产地证明书注册登记表》; 2.提交:企业营业执照有效复印件及 中资企业:进出口经营权资格证书/登记证有效复印件 外资企业:批准证书有效复印件 3.进行资格审核合格后,予以编号、登记、发证:《中华人民共和国出口货物原产地证明书注册登记证》。 一般原产地证的作用 在国际贸易中,世界各国根据各自的对外贸易政策,普遍实行进口贸易管制,对进口商品实施差别关税和数量限制,并由海关执行统计。进口国要求出口国出具货物的原产地证明,已成为国际惯例,因此一般原产地是进行国际贸易的一项重要证明文件,归纳起来,具有以下几方面的作用:
钣金件表面处理主要工艺方法介绍
表面处理工艺 表面处理技术介绍 一、什么叫做表面处理 表面处理:以最经济和最有效的方法改变产品表面及近表面区的形态、化学成分和组织结构,有效地改善和提高产品的装饰性能、耐腐蚀性能和耐磨性能,延长产品的使用寿命。 常见的表面处理:电镀,化学镀,转化膜技术,物理气相沉积,化学气相沉积,热喷涂,热浸镀,喷砂,化学转化,阳极氧化,涂装等; 表面处理技术还能赋予材料表面各种光、电、磁、热、声、化学以及功能转换等特性。 1.各种光的表面技术:镜子;防反光; 2.各种电的表面技术:绝缘的镀银,金,铜;导电的用塑料保护 3.各种磁的表面技术:隐身技术(重点) 4.热的表面技术:红外,吸收红外,防热; 5.声的表面技术:防声纳 6.化学:钢材镀锌 表面处理的种类 表面处理根据产品的使用要求可以分为:防护型表面处理,如电镀、氧化(化学氧化、电化学氧化)、装饰型表面处理(如涂装、、功能型表面处理,总的来说,没有明显的划分界限,其主要目的是延长产品的使用寿命,最大程度的节省和利用资源。 二、钣金加工中为什么要进行表面处理? 1.钣金加工所用的材料多为冷轧板、热轧板、电解板、白口铁、不锈钢、铝合金板及型材、铜材等,这些材料暴露在大气中,与空气中的水分和氧充分接触后,会发生电化学反应,从而造成材料表面腐蚀,同时物理及化学性质不同的材料间相互接触也会由于彼此间的电位差而形成原电池,从而造成接触腐蚀。为避免钣金加工中材料在各加工工序间及成品在存放及使用中发生腐蚀,生产中通过对材料进行表面处理方式来控制腐蚀的产生或延缓腐蚀的产生,从而减少由于腐蚀的产生而造成产品返修或报废,尽可能地节约资源及生产成本。 2.各种材料经过钣金加工转化为商品时,为了满足顾客的需求及商品给予人视觉上的美感,就对产品外观作各种表面处理,如电镀、氧化着 三、在钣金加工业中铝合金材料通常需进行哪些表面处理? 在钣金加工业中,铝合金材料通常需进行以下表面处理:无色化学氧化、黑色化学氧化、金黄色化学氧化、拉丝无色化学氧化、喷砂无色化学氧化、光亮无色化学氧化、喷砂光亮阳极氧化、化学氧化着色、化学氧化后涂装(喷漆、喷粉),其中氧化层有导电与绝缘两种;硬质、耐磨等; 前处理 四、磷化工艺 A、磷化工艺流程:预脱脂----脱脂----流动水洗----流动水洗----表调----磷化----流动水洗 ----流动水洗----纯水洗----烘干 B、前处理生产线 喷淋线、浸泡线