塑料制品的常见缺陷及改善方法
注塑常见缺陷的解决方法

注塑常见缺陷的解决方法注塑是一种常见的制造工艺,可以用于生产各种塑料制品。
然而,在注塑过程中常常会出现一些缺陷,如翘曲、气泡、短射等。
这些缺陷会降低产品的质量,影响使用效果。
因此,解决这些缺陷是注塑加工中重要的一环。
下面是一些常见缺陷的解决方法:1.翘曲:翘曲是指注塑制品的形状变形,不符合设计要求。
翘曲的原因可能是注塑温度过高、材料流动不均匀等。
解决方法包括:优化注塑工艺参数,例如调整注塑温度、压力、速度等;增加型腔冷却方式,以提高产品的冷却效果;使用合适的塑料料种,如改变注塑材料的配方,选择更具平衡性能的材料。
2.气泡:气泡是指注塑制品中出现的气体孔洞,影响了产品的外观和性能。
气泡的形成可能是由于注塑材料中的挥发性成分未完全排除、注塑机排气不良等原因。
解决方法包括:增加注塑所需的压力和温度,以促使挥发性成分完全排出;改善注塑机的排气系统,有效排除气泡。
3.短射:短射是指注塑过程中,塑料流动未能充满整个模具的情况。
短射的原因可能是注塑料温度过低、注塑机压力不足、型腔阻力过大等。
解决方法包括:提高注塑温度和压力,以增加塑料的流动性;改善模具的设计,减少型腔的阻力;检查注塑机的喷嘴和螺杆是否损坏,及时更换。
4.热流线:热流线是指注塑制品表面出现的不均匀纹路,影响产品的外观。
热流线的形成可能是由于塑料流动速度过快、模具温度不均匀等原因。
解决方法包括:调整注塑机的喷嘴和螺杆速度,控制塑料的流动速度;优化模具的冷却系统,使模具温度均匀分布。
5.尺寸偏差:尺寸偏差是指注塑制品的尺寸与设计要求不符,可能是由于模具磨损、注塑工艺参数不恰当等原因。
解决方法包括:定期检查和修复模具,以保证模具的精度;优化注塑工艺参数,例如调整注射时间、压力和温度,以控制产品的尺寸。
总的来说,解决注塑常见缺陷需要综合考虑材料、工艺和设备等方面的因素。
通过不断优化参数和改进工艺,可以改善产品的质量,提高注塑加工的效率。
此外,定期维护和保养注塑设备和模具也是预防和解决缺陷的重要措施。
注塑缺陷描述及解决方案

注塑缺陷描述及解决方案一、注塑缺陷描述注塑是一种常用的塑料加工方法,但在注塑过程中常会出现一些缺陷。
以下是常见的注塑缺陷描述:1. 气泡:注塑制品表面出现小气泡,影响外观质量。
2. 热缩:制品在注塑后出现尺寸变化,导致尺寸不准确。
3. 热分解:注塑过程中,塑料材料发生热分解,导致制品表面出现黑斑或发黄。
4. 热裂纹:注塑制品在冷却过程中出现裂纹。
5. 短射:注塑模具中未完全填充塑料材料,导致制品缺少部分或完全缺失。
6. 缩痕:注塑制品表面出现凹陷或凸起的痕迹。
7. 毛边:注塑制品边缘出现毛糙或不平整。
8. 色差:注塑制品颜色不均匀或与预期颜色不符。
二、解决方案针对以上注塑缺陷,可以采取以下解决方案:1. 气泡:增加注塑过程中的压力和温度,使用抗气泡添加剂,调整注塑工艺参数。
2. 热缩:优化注塑模具设计,增加冷却系统,控制注塑过程中的温度。
3. 热分解:选择合适的塑料材料,避免过高的注塑温度,加强模具通风。
4. 热裂纹:优化注塑模具设计,增加冷却时间,降低注塑温度。
5. 短射:调整注塑工艺参数,增加注塑压力和速度,优化模具结构。
6. 缩痕:增加注塑压力和温度,调整模具结构,增加冷却时间。
7. 毛边:优化模具设计,增加模具表面光洁度,调整注塑工艺参数。
8. 色差:选择合适的塑料材料,控制注塑温度和时间,使用色母粒。
除了以上解决方案,还可以通过对注塑设备进行维护保养,提高操作人员的技术水平,加强质量检验等措施来预防和解决注塑缺陷问题。
总结:注塑缺陷是在注塑加工过程中常见的问题,但通过合理的解决方案可以有效降低缺陷率,提高注塑制品的质量。
在实际生产中,需要根据具体情况选择合适的解决方案,并进行持续改进和优化,以确保注塑制品的质量和生产效率。
塑胶产品的常见缺陷及分析

塑胶产品的常见缺陷及分析塑料制品是现代生活中不可或缺的一部分。
然而,塑料制品仍然存在一些常见的缺陷,这些缺陷可能导致产品质量下降,甚至无法使用。
下面是一些常见的塑料制品缺陷及其分析。
1.气泡和气孔:塑料制品中的气泡和气孔是由于在制造过程中塑料内部的空气没有完全排除或者在冷却期间塑料表面形成的。
这些气泡和气孔会导致产品表面不光滑,并在应力作用下引起断裂。
减少气泡和气孔的方法包括将塑料完全熔化,并控制良好的冷却过程。
2.毛边和厚度不均:由于模具设计和制造不当,塑料制品的边缘可能会有毛边。
毛边的存在会影响产品的外观和使用寿命。
此外,塑料制品的厚度分布不均匀可能导致产品一些部分容易破裂。
为了解决这些问题,需要优化模具设计,并确保模具制造过程的准确性。
3.烧伤和变色:在注塑过程中,如果温度控制不当,塑料可能会被过热,导致烧伤和变色。
这些问题会影响产品的外观和性能。
要解决这些问题,需要正确控制注塑机的温度和压力,并使用合适的冷却设备。
4.变形和翘曲:塑料制品可能在使用过程中变形或翘曲,这主要是由于应力超过材料的强度限制引起的。
为了避免变形和翘曲,可以通过增加产品的结构设计,加固材料强度或者改变制造过程来提高产品的稳定性。
5.色差:塑料制品可能存在色差,这是由于原料、配方和加工条件的变化引起的。
色差会影响产品的外观一致性。
要解决这个问题,需要优化原料和配方的选择,严格控制加工过程的温度和压力,以确保产品色差的控制在可接受的范围内。
综上所述,塑料制品的常见缺陷包括气泡和气孔、毛边和厚度不均、烧伤和变色、变形和翘曲以及色差。
这些缺陷可能导致产品质量下降,影响外观和性能。
为了解决这些问题,需要优化模具设计、加强原料和配方的控制,严格控制加工过程中的温度和压力。
只有通过严格的质量控制,才能生产出高质量的塑料制品。
注塑件常见缺陷及原因分析【详解】
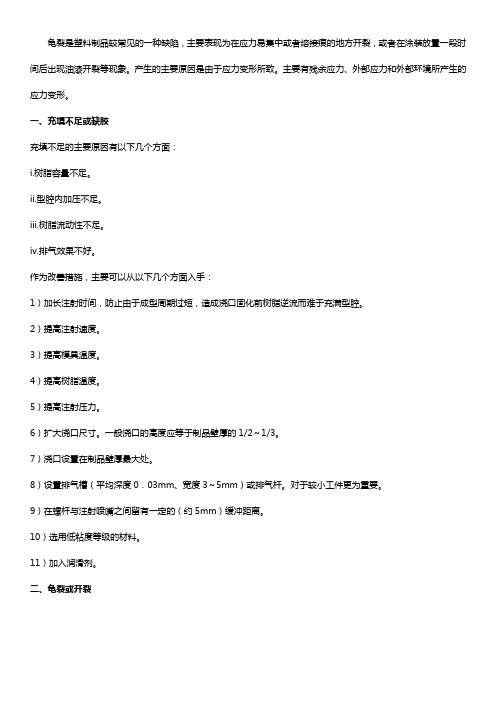
龟裂是塑料制品较常见的一种缺陷,主要表现为在应力易集中或者熔接痕的地方开裂,或者在涂装放置一段时间后出现油漆开裂等现象。
产生的主要原因是由于应力变形所致。
主要有残余应力、外部应力和外部环境所产生的应力变形。
一、充填不足或缺胶充填不足的主要原因有以下几个方面:i.树脂容量不足。
ii.型腔内加压不足。
iii.树脂流动性不足。
iv.排气效果不好。
作为改善措施,主要可以从以下几个方面入手:1)加长注射时间,防止由于成型周期过短,造成浇口固化前树脂逆流而难于充满型腔。
2)提高注射速度。
3)提高模具温度。
4)提高树脂温度。
5)提高注射压力。
6)扩大浇口尺寸。
一般浇口的高度应等于制品壁厚的1/2~1/3。
7)浇口设置在制品壁厚最大处。
8)设置排气槽(平均深度0.03mm、宽度3~5mm)或排气杆。
对于较小工件更为重要。
9)在螺杆与注射喷嘴之间留有一定的(约5mm)缓冲距离。
10)选用低粘度等级的材料。
11)加入润滑剂。
二、龟裂或开裂龟裂是塑料制品较常见的一种缺陷,主要表现为在应力易集中或者熔接痕的地方开裂,或者在涂装放置一段时间后出现油漆开裂等现象。
产生的主要原因是由于应力变形所致。
主要有残余应力、外部应力和外部环境所产生的应力变形。
(一)残余应力引起的龟裂残余应力主要由于以下三种情况,即充填过剩、脱模推出和金属镶嵌件造成的。
作为在充填过剩的情况下产生的龟裂,其解决方法主要可从以下几方面入手:1)由于直浇口压力损失最小,所以,如果龟裂最主要产生在直浇口附近,则可考虑改用多点分布点浇口、侧浇口及柄形浇口方式。
2)在保证树脂不分解、不劣化的前提下,适当提高树脂温度可以降低熔融粘度,提高流动性,同时也可以降低注射压力,以减小应力。
3)一般情况下,模温较低时容易产生应力,应适当提高温度。
但当注射速度较高时,即使模温低一些,也可减低应力的产生。
4)注射和保压时间过长也会产生应力,将其适当缩短或进行Th次保压切换效果较好。
塑料件缺陷范文范文

塑料件缺陷范文范文一、引言塑料制品作为一种重要的工业产品,在我们的日常生活中起着不可或缺的作用。
然而,由于生产过程中的一些问题,塑料件往往会出现一些不可避免的缺陷。
本文旨在探讨塑料件常见的缺陷及其产生的原因,并提出相应的解决方案,以期提高塑料件的质量。
二、塑料件的常见缺陷1.表面缺陷:塑料件表面可能出现划痕、气泡、色差等问题,影响其外观质量。
2.尺寸缺陷:塑料件的尺寸可能与设计要求不符,包括尺寸过大、过小、不均匀等问题。
3.结构缺陷:塑料件的结构可能存在开裂、变形等问题,影响其使用寿命和强度。
4.功能缺陷:塑料件可能存在功能性能不良的问题,如阻力过大、泄漏等。
三、塑料件缺陷产生的原因1.材料选择不当:塑料件的材料选择不恰当会导致其性能不稳定,易出现缺陷。
2.模具设计问题:塑料件的模具设计不合理会导致形状、尺寸等方面的缺陷。
3.生产工艺控制不严:生产过程中的温度、压力、速度等参数控制不严谨会导致塑料件出现缺陷。
4.人为操作错误:操作人员的技术水平、经验丰富程度等因素也会对塑料件的质量产生影响。
四、解决塑料件缺陷的方法1.加强材料选择:选择合适的塑料材料,进行材料测试和性能评估,确保材料质量稳定。
2.优化模具设计:通过精确的模具设计,确保塑料件的形状、尺寸等符合要求。
3.强化生产工艺控制:加强对生产过程中的温度、压力、速度等参数的控制,确保塑料件质量稳定。
4.培训操作人员:对操作人员进行培训,提高其技术水平和责任心,减少人为操作错误的发生。
五、案例分析以汽车塑料件为例,根据上述解决方法,对常见的缺陷进行分析和解决。
1.表面缺陷:选择适合汽车外观要求的塑料材料,完善表面处理工艺,如喷漆、研磨等,修复塑料件表面的划痕和色差。
2.尺寸缺陷:优化模具设计,通过模具参数控制塑料件的尺寸,采用自动化生产流程,减少人为因素对尺寸的影响。
3.结构缺陷:在原材料中添加增强剂,改善塑料件的强度和耐热性,通过模具设计和生产工艺控制,减少自然热应力对塑料件的影响。
热塑性塑料注射成型中常见缺陷改善对策

热塑性塑料注射成型中常见缺陷改善对策1.鼓包缺陷:鼓包是指塑料制品表面出现隆起、凹陷等现象。
造成鼓包的原因可能是注塑机压力过高、模具开发板不均匀、塑料熔融不均衡等。
改善对策是合理调节注塑机的压力和速度,仔细调整模具,增加剂量尺寸。
2.短斑缺陷:短斑是指塑料制品表面出现小孔洞或不完整的斑点。
这可能是由于模具中的残留气体造成的,或者是熔融塑料中含有杂质。
改善对策包括使用具有较好流动性的塑料材料、提高塑料熔点来减少气体生成、增加熔融进气口。
3.流痕缺陷:流痕是指塑料制品表面出现沟槽状痕迹的现象,它可能是由于塑料熔融不均匀、模具过热或注射速度过快造成的。
改善对策包括增加塑料的温度,调整模具温度,减少注射速度。
4.尺寸偏差:尺寸偏差是指塑料制品的实际尺寸与设计尺寸之间存在差异。
尺寸偏差可能是由于模具设计不合理、熔融塑料冷却不均匀等原因造成的。
改善对策包括重新设计模具、增加冷却系统、提高塑料的熔融温度。
5.热损失:热损失是指在塑料注射成型过程中,熔融塑料的温度下降过快,导致无法充分填充模具腔体。
改善对策包括增加塑料温度,提高注塑机的注射速度和压力,加热模具等。
6.气泡缺陷:气泡是指塑料制品内部或表面存在充气空洞的现象。
气泡可能是由于塑料材料中含有过多的水分或气体,模具温度不恰当,注射过程中太多的空气进入等原因导致的。
改善对策包括使用低含水量的塑料材料、调整模具和注射过程中的温度、加强模具和注射机的密封性。
7.翘曲缺陷:翘曲是指塑料制品的形状出现变形的现象,通常是由于注射过程中的过度冷凝和收缩造成的。
改善对策包括调整注射温度和注射速度,增加模具的支撑结构,选择具有较小收缩率的塑料材料。
总之,热塑性塑料注射成型中常见的缺陷有很多种,针对不同的缺陷,需要采取相应的改善对策。
通过调整注射机参数、优化模具设计和选择合适材料,可以有效降低注射成型过程中的缺陷发生,提高产品质量。
同时,定期检查和维护设备、监控质量指标的变化也是预防和改善缺陷的必要措施。
注塑制品常见缺陷分析及改善措施

注塑制品常见缺陷分析及改善措施注塑制品是一种常见的塑料制品,它被广泛应用于各个领域。
然而,由于注塑过程中存在很多因素的影响,注塑制品常常会出现一些缺陷。
本文将对常见的注塑制品缺陷进行分析,并提出相应的改善措施。
首先,短斑是指注塑制品表面上出现小块区域与周围区域颜色不一致的现象。
短斑的产生原因主要有以下几点:一是注塑过程中,塑料熔融不均匀,导致注塑制品的物理性能不一致;二是模具构造不合理,导致注射流道中存在死角或交叉断面,使得塑料无法均匀地填充模具。
改善措施包括调整注射温度和速度,提高熔融的均匀性;优化模具结构,避免死角和交叉断面的存在。
其次,气泡是指注塑制品中出现的气体囊泡。
气泡的产生原因主要有以下几点:一是塑料熔融时,吸附在塑料中的气体因温度升高而析出;二是模具内空气被困,形成气泡。
改善措施包括提高注料温度和压力,使气体充分溶解于塑料中;优化模具结构,改善气体的排除。
再次,翘曲是指注塑制品的形状不平整,出现弯曲或变形的现象。
翘曲的产生原因主要有以下几点:一是注塑过程中,注射压力不均匀,导致塑料流动不稳定;二是模具温度不均匀,导致塑料的冷却速度不一致。
改善措施包括提高注射速度和压力,增加注塑壁厚度的控制;优化模具温度控制系统,使模具温度均匀。
此外,色差是指注塑制品表面颜色不均匀的现象。
色差的产生原因主要有以下几点:一是注塑材料质量不均匀,导致色料分散不均匀;二是注塑过程中的温度和压力不稳定,使色料没有充分混合。
改善措施包括选用质量稳定的注塑材料;提高注塑温度和压力的稳定性;增加色料的溶解和混合时间。
最后,露胶是指注塑制品表面出现塑料外露的现象。
露胶的产生原因主要有以下几点:一是模具设计不合理,导致模具分离缺陷;二是注射流道中存在死角或结构不当,使得塑料无法完全填充模具。
改善措施包括优化模具设计,确保模具分离平整;优化注射流道结构,避免死角的存在。
综上所述,注塑制品的常见缺陷主要包括短斑、气泡、翘曲、色差和露胶等。
注塑成型缺陷及解决方法

注塑成型缺陷及解决方法注塑成型是一种常用的塑料制品生产工艺,但在实际操作过程中,难免会出现一些缺陷。
下面将介绍几种常见的注塑成型缺陷及其解决方法。
1.短射:短射指的是塑料在模腔中注入不完全,导致制品形状不完整或缺少一部分。
短射可能由于注射速度过快或进气不畅引起。
解决方法是调整注塑机的注射速度和压力,确保塑料充分进入模腔,并检查进气口是否畅通。
2.气泡:气泡是指制品表面或内部出现空洞。
气泡的形成可能由于塑料中含有水分、模具开放不当等原因。
解决方法是在注塑前将塑料干燥处理,确保塑料中不含水分,并检查模具密封性以防止气体进入模腔。
3.缩短:缩短是指制品尺寸比设计要小,可能由于塑料收缩不均匀或模具温度不稳定引起。
解决方法是通过调整模具温度和冷却系统,使塑料在注塑过程中均匀收缩,并确保模具温度稳定。
4.色差:色差是指制品表面颜色不均匀,可能由于塑料熔融不充分、颜料添加不均匀等原因。
解决方法是加长塑料的熔化时间,确保塑料充分熔融,并确保颜料充分混合均匀。
5.枝晶:枝晶是指制品表面出现树枝状的纹理,可能由于注塑温度过高或冷却时间不足引起。
解决方法是降低注塑温度,延长冷却时间,确保塑料在注塑过程中充分凝固。
6.毛刺:毛刺是指制品表面出现刺状的尖突物,可能由于模具间隙过大或模具磨损引起。
解决方法是调整模具间隙,确保模具紧密结合,并定期检查模具磨损情况。
7.烧焦:烧焦是指塑料在注塑过程中受热过度,产生发黑或炭化的现象。
烧焦可能由于注塑温度过高或注射速度过快引起。
解决方法是降低注塑温度,调整注射速度,确保塑料受热均匀。
总结起来,解决注塑成型缺陷的关键是调整注塑机参数、保证模具质量和稳定性,以及进行适当的后处理工艺。
此外,及时发现和修复模具的损坏也是避免缺陷的重要措施。
- 1、下载文档前请自行甄别文档内容的完整性,平台不提供额外的编辑、内容补充、找答案等附加服务。
- 2、"仅部分预览"的文档,不可在线预览部分如存在完整性等问题,可反馈申请退款(可完整预览的文档不适用该条件!)。
- 3、如文档侵犯您的权益,请联系客服反馈,我们会尽快为您处理(人工客服工作时间:9:00-18:30)。
塑料制品的常见缺陷及改善方法
1. 批锋:降低注塑压力;增加或调整进胶口位置以降低注塑压力.
2. 缩水:增加注塑压力;增加或调整进胶口位置;调整进胶口或流道大小;减薄缩水处壁厚; 缩
水处壁厚均匀过渡; 降低缩水处柱高或壁厚.
3.夹水纹:前模加热油,后模加冷水,将夹水纹留在后模;增加或调整进胶口位置;进胶口附近
挡料来调整夹水纹的位置;夹水纹处加冷料穴;减少脱模剂的使用;提高烘料温度及
射胶速度;增加排气位。
由于是材料最后会合的地方,故其强度较弱,应避开成品承
受负载的地方。
夹水纹在模具上的位置和大小基本不变,不同于划伤.
4.变形:降低注塑压力;增加或调整进胶口位置以降低注塑压力;调整进胶口或流道大小;局部
增加壁厚或加强筋;增加保压及冷却时间.
5.喷油夹模飞油:设计预留夹模位,尺寸大于: 0.5*0.3MM
6.丝印偏位: 增加丝印对位FILM
7.丝印断,缺: 改丝印FILM,保证最小线粗大于0.15MM,勤洗丝印网.。