塑料模具制品常见缺陷及解决办法
注塑缺陷描述及解决方案

注塑缺陷描述及解决方案一、注塑缺陷描述注塑是一种常用的塑料加工方法,但在注塑过程中常会出现一些缺陷。
以下是常见的注塑缺陷描述:1. 气泡:注塑制品表面出现小气泡,影响外观质量。
2. 热缩:制品在注塑后出现尺寸变化,导致尺寸不准确。
3. 热分解:注塑过程中,塑料材料发生热分解,导致制品表面出现黑斑或发黄。
4. 热裂纹:注塑制品在冷却过程中出现裂纹。
5. 短射:注塑模具中未完全填充塑料材料,导致制品缺少部分或完全缺失。
6. 缩痕:注塑制品表面出现凹陷或凸起的痕迹。
7. 毛边:注塑制品边缘出现毛糙或不平整。
8. 色差:注塑制品颜色不均匀或与预期颜色不符。
二、解决方案针对以上注塑缺陷,可以采取以下解决方案:1. 气泡:增加注塑过程中的压力和温度,使用抗气泡添加剂,调整注塑工艺参数。
2. 热缩:优化注塑模具设计,增加冷却系统,控制注塑过程中的温度。
3. 热分解:选择合适的塑料材料,避免过高的注塑温度,加强模具通风。
4. 热裂纹:优化注塑模具设计,增加冷却时间,降低注塑温度。
5. 短射:调整注塑工艺参数,增加注塑压力和速度,优化模具结构。
6. 缩痕:增加注塑压力和温度,调整模具结构,增加冷却时间。
7. 毛边:优化模具设计,增加模具表面光洁度,调整注塑工艺参数。
8. 色差:选择合适的塑料材料,控制注塑温度和时间,使用色母粒。
除了以上解决方案,还可以通过对注塑设备进行维护保养,提高操作人员的技术水平,加强质量检验等措施来预防和解决注塑缺陷问题。
总结:注塑缺陷是在注塑加工过程中常见的问题,但通过合理的解决方案可以有效降低缺陷率,提高注塑制品的质量。
在实际生产中,需要根据具体情况选择合适的解决方案,并进行持续改进和优化,以确保注塑制品的质量和生产效率。
塑料件缺陷及改进措施

塑料件缺陷及改进措施塑料件在实际应用中存在一些常见的缺陷,这些缺陷可能会对产品的质量和性能产生负面的影响。
下面将介绍一些常见的塑料件缺陷,并提出相应的改进措施。
1.熔接线痕:在注塑过程中,由于熔融塑料的流动不均匀,容易形成熔接线痕。
这些痕迹可能会导致产品强度降低、疲劳性能差等问题。
改进措施:调整注塑工艺参数,如制定适当的注射速度、保持压力等,以促进塑料的均匀流动,减少熔接线痕的产生。
2.气泡:注塑过程中,由于塑料内含有的气体随着高温熔融逸出,易形成气泡。
气泡会导致产品的密封性能下降、外观质量差等问题。
改进措施:提高注塑设备的真空度,减少气体残留。
此外,在塑料原料中加入消泡剂,能够降低气泡的产生。
3.龟裂:塑料零件在冷却过程中,由于不均匀的收缩率和内应力,易出现龟裂缺陷。
这种缺陷会导致产品的强度下降、易开裂等问题。
改进措施:采用合适的冷却方法,如适当提高冷却介质的温度、均匀冷却等,以减少塑料件的收缩和内应力的产生。
4.比色差:一些塑料件在生产过程中,由于塑料原料的不均匀混合或加工温度控制不当,易形成色差。
这会导致产品的外观质量差,影响产品的整体美观度。
改进措施:严格控制塑料原料的配比,确保原料的均匀混合。
同时,加强对注塑设备的温度控制,保持适当的加工温度,有助于减少温度对产品颜色的影响。
5.纹理不良:在塑料件表面会产生一些不良的纹理,如模具印痕、晶化痕迹等。
这些缺陷会降低产品的表面质量、减少产品的美观度。
改进措施:优化模具的设计和制造工艺,减少模具表面的磨损和粗糙度。
同时,在注塑过程中控制好注塑温度和注塑压力,以减小纹理缺陷的产生。
总而言之,塑料件的缺陷主要体现在熔接线痕、气泡、龟裂、比色差和纹理不良等方面。
为了改善塑料件的质量和性能,应从加工工艺、原料控制、模具改进等方面入手,提高生产工艺的稳定性和可控性。
同时,加强质量检测和监控,及时发现和解决问题,以确保塑料件的质量满足产品要求。
塑胶件常见成型缺陷及改善策略
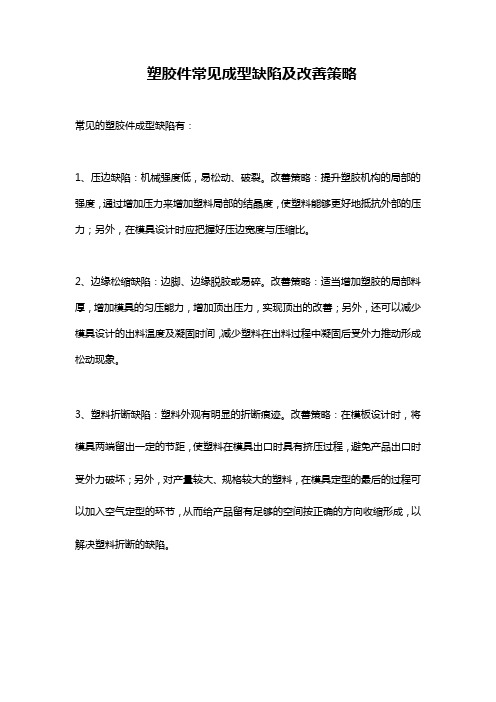
塑胶件常见成型缺陷及改善策略
常见的塑胶件成型缺陷有:
1、压边缺陷:机械强度低,易松动、破裂。
改善策略:提升塑胶机构的局部的强度,通过增加压力来增加塑料局部的结晶度,使塑料能够更好地抵抗外部的压力;另外,在模具设计时应把握好压边宽度与压缩比。
2、边缘松缩缺陷:边脚、边缘脱胶或易碎。
改善策略:适当增加塑胶的局部料厚,增加模具的匀压能力,增加顶出压力,实现顶出的改善;另外,还可以减少模具设计的出料温度及凝固时间,减少塑料在出料过程中凝固后受外力推动形成松动现象。
3、塑料折断缺陷:塑料外观有明显的折断痕迹。
改善策略:在模板设计时,将模具两端留出一定的节距,使塑料在模具出口时具有挤压过程,避免产品出口时受外力破坏;另外,对产量较大、规格较大的塑料,在模具定型的最后的过程可以加入空气定型的环节,从而给产品留有足够的空间按正确的方向收缩形成,以解决塑料折断的缺陷。
塑料模具设计常见问题及改进方法

塑料模具设计常见问题及改进方法塑料模具是塑料制品生产的关键工具,其设计质量直接影响着产品的成型质量和生产效率。
在塑料模具设计过程中,常会遇到一些常见问题,例如设计不合理、成型不良等。
本文将介绍塑料模具设计常见问题及改进方法。
一、常见问题1.设计不合理在塑料模具设计过程中,设计不合理是最常见的问题之一。
设计不合理会导致模具结构复杂、易损件过多、成本增加等问题。
这些问题都会影响模具的使用寿命和生产效率。
2.成型不良成型不良也是常见的问题之一。
成型不良可能是由于模具设计不合理、材料选择不当、成型参数设置不正确等原因导致的。
成型不良会影响产品的质量,甚至导致生产事故。
3.模具寿命短模具寿命短是塑料模具常见问题之一。
模具寿命短可能是由于材料选择不当、表面处理不到位、使用条件不合理等原因导致的。
模具寿命短会增加生产成本,降低生产效率。
4.技术水平低一些塑料模具设计人员技术水平低也是常见问题。
技术水平低会导致设计不合理、制造精度低、模具寿命短等问题。
5.应力集中在塑料模具设计中,应力集中也是一个常见问题。
应力集中可能导致模具开裂、损坏等问题,从而影响模具的使用寿命和生产效率。
二、改进方法为了解决设计不合理的问题,可以通过优化设计来改进。
优化设计可以减少模具结构复杂度、减少易损件、降低成本等。
优化设计可以采用CAD软件进行模拟分析,找出设计不合理的地方并进行改进。
2.增加冷却系统成型不良的问题可以通过增加冷却系统来改进。
增加冷却系统可以有效降低成型温度、缩短成型周期、提高产品质量。
合理的冷却系统设计可以通过有限元分析和实验验证。
3.优化材料选择模具寿命短的问题可以通过优化材料选择来改进。
优化材料选择可以选择抗磨损、抗腐蚀、高强度的材料,从而提高模具的使用寿命。
还可以采用表面处理技术来提高模具的使用寿命。
为了解决技术水平低的问题,可以通过提高技术水平来改进。
提高技术水平可以通过培训、学习、实践等方式来进行。
提高技术水平可以提高设计水平、精度水平、制造工艺水平等。
塑件缺陷原因及改善方法

塑件缺陷原因及改善方法塑件是一种常见的工程材料,广泛应用于汽车、家电、电子、医疗设备等领域。
然而,在塑件生产过程中,常常会出现一些缺陷,如气泡、毛刺、热缩、变形等问题,这些缺陷会影响塑件的质量和性能。
因此,了解塑件缺陷的原因,并采取相应的改善方法,对于提高塑件质量和性能具有重要意义。
首先,塑件缺陷的原因有多种,下面是一些常见的原因及相应的改善方法:1.气泡:气泡是塑件生产过程中常见的缺陷,通常是由于原料中含有挥发性成分,或者模具中有气体积聚引起的。
改善方法包括:使用质量稳定的原料,避免使用含有挥发性成分的原料;在塑件生产过程中提高注塑压力,减少气泡的生成;对模具进行定期维护,清除模具中的积聚气体。
2.毛刺:毛刺是塑件表面出现的细小突起,通常是由于模具不平整或模具开合不良引起的。
改善方法包括:对模具进行定期检修和研磨,保持模具的平整度;调整模具开合速度和压力,使开合动作更加平稳;在设计模具时考虑减少毛刺的生成。
3.热缩:塑件在冷却后会发生热缩现象,导致尺寸变小。
这是由于塑料在冷却过程中会收缩引起的。
改善方法包括:在设计模具时考虑塑件的热缩率,合理设置模具尺寸,使得塑件在冷却后能得到正确的尺寸;控制注塑过程中的冷却时间和温度,避免过快或过慢的冷却导致过大的热缩。
4.变形:塑件在注塑过程中可能会发生变形,导致尺寸不准确或形状失真。
这是由于塑料在注塑过程中由于内应力不平衡引起的。
改善方法包括:优化模具设计,使模具在注塑过程中能够充分填充塑料,并保持良好的冷却效果;控制注塑过程的温度、压力和速度,减少内应力的释放。
此外,还有一些其他常见的塑件缺陷,如熔流线、白斑、开裂等。
这些缺陷的原因和改善方法也各不相同,需要具体问题具体分析。
总的来说,塑件缺陷的原因多种多样,通过针对不同的原因采取相应的改善方法,能够有效地提高塑件的质量和性能。
对于塑件生产企业来说,建立完善的质量控制体系,加强原材料的筛选和控制,定期维护和检修模具,改进注塑工艺,都是改善塑件质量和性能的重要措施。
注塑缺陷原因分析与解决方案
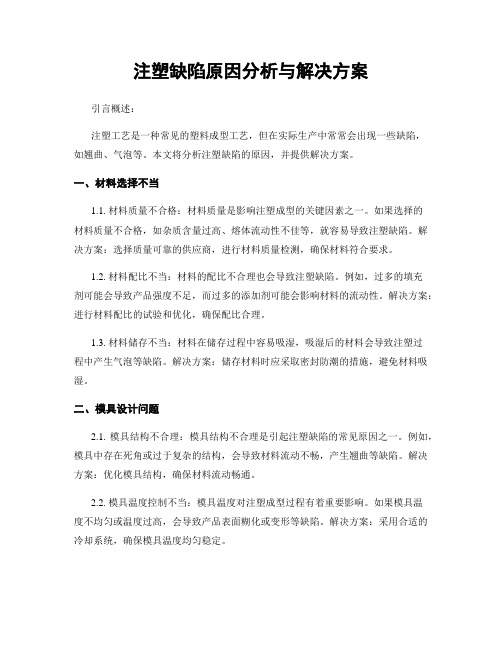
注塑缺陷原因分析与解决方案引言概述:注塑工艺是一种常见的塑料成型工艺,但在实际生产中常常会出现一些缺陷,如翘曲、气泡等。
本文将分析注塑缺陷的原因,并提供解决方案。
一、材料选择不当1.1. 材料质量不合格:材料质量是影响注塑成型的关键因素之一。
如果选择的材料质量不合格,如杂质含量过高、熔体流动性不佳等,就容易导致注塑缺陷。
解决方案:选择质量可靠的供应商,进行材料质量检测,确保材料符合要求。
1.2. 材料配比不当:材料的配比不合理也会导致注塑缺陷。
例如,过多的填充剂可能会导致产品强度不足,而过多的添加剂可能会影响材料的流动性。
解决方案:进行材料配比的试验和优化,确保配比合理。
1.3. 材料储存不当:材料在储存过程中容易吸湿,吸湿后的材料会导致注塑过程中产生气泡等缺陷。
解决方案:储存材料时应采取密封防潮的措施,避免材料吸湿。
二、模具设计问题2.1. 模具结构不合理:模具结构不合理是引起注塑缺陷的常见原因之一。
例如,模具中存在死角或过于复杂的结构,会导致材料流动不畅,产生翘曲等缺陷。
解决方案:优化模具结构,确保材料流动畅通。
2.2. 模具温度控制不当:模具温度对注塑成型过程有着重要影响。
如果模具温度不均匀或温度过高,会导致产品表面糊化或变形等缺陷。
解决方案:采用合适的冷却系统,确保模具温度均匀稳定。
2.3. 模具磨损严重:模具长时间使用后会出现磨损,磨损严重的模具会导致产品尺寸不准确或表面粗糙等缺陷。
解决方案:定期检查和维护模具,及时更换磨损严重的模具部件。
三、注塑工艺参数设置不当3.1. 注射压力过高或过低:注射压力是影响注塑成型的关键参数之一。
如果注射压力过高,会导致产品变形或开裂,而注射压力过低则会导致产品表面光洁度不高。
解决方案:根据产品要求和材料特性,合理设置注射压力。
3.2. 注射速度不合理:注射速度对产品的充填和冷却过程有着重要影响。
如果注射速度过快,会导致产品内部产生气泡或短射,而注射速度过慢则会导致产品表面瑕疵。
塑料模具设计常见问题及改进方法
塑料模具设计常见问题及改进方法塑料模具设计在实际应用中,常常会遇到一些问题,影响生产效率和产品质量。
下面将介绍一些常见的问题,并提出改进的方法。
1. 精度不够:在塑料模具的设计和制造过程中,如果精度不够,会导致产品尺寸和形状的不一致,影响产品的质量。
改进方法可以通过使用高精度加工设备和工艺,并进行严格的质量控制来提高精度。
2. 成型件表面质量不良:塑料模具中常常会出现成型件表面出现纹痕、气泡、疤痕等问题,影响产品的外观和质量。
改进方法可以选择适合的模具材料,提高模具表面光洁度,调整模具温度和冷却系统等。
3. 模具寿命短:塑料模具在长时间使用过程中容易出现磨损、疲劳断裂等问题,导致模具寿命较短。
改进方法可以选择耐磨性好的材料制作模具,增加模具的强度和硬度,正确使用和维护模具等。
4. 模具结构复杂:一些塑料模具的结构比较复杂,设计和制造难度大,容易出现问题。
改进方法可以使用先进的设计软件和CAD/CAM技术,优化模具结构,简化模具制造过程,提高生产效率和产品质量。
5. 生产周期长:一些塑料模具的设计和制造周期较长,影响生产进度和交货时间。
改进方法可以使用模具快速制造技术,如快速加工和快速制造等,缩短模具的设计和制造周期。
6. 模具排气不畅:在塑料模具制造过程中,如果模具的排气不畅,容易产生气泡等缺陷,影响产品质量。
改进方法可以优化模具的设计和加工过程,设置合适的排气口和排气系统,并通过模具试验和调整来改善排气效果。
7. 模具变形:一些大尺寸或复杂结构的塑料模具在使用中容易发生变形,影响产品的尺寸精度和外观。
改进方法可以通过增加模具的刚性和稳定性,使用优质的模具材料,控制模具温度和冷却系统等来减少模具变形。
塑料模具设计常见问题的改进方法主要包括提高精度、改善表面质量、增加模具寿命、简化结构、缩短生产周期、优化排气系统和控制模具变形等。
通过不断改进和优化,可以提高塑料模具的生产效率和产品质量。
注塑成型缺陷及解决方法
注塑成型缺陷及解决方法注塑成型是一种常用的塑料制品生产工艺,但在实际操作过程中,难免会出现一些缺陷。
下面将介绍几种常见的注塑成型缺陷及其解决方法。
1.短射:短射指的是塑料在模腔中注入不完全,导致制品形状不完整或缺少一部分。
短射可能由于注射速度过快或进气不畅引起。
解决方法是调整注塑机的注射速度和压力,确保塑料充分进入模腔,并检查进气口是否畅通。
2.气泡:气泡是指制品表面或内部出现空洞。
气泡的形成可能由于塑料中含有水分、模具开放不当等原因。
解决方法是在注塑前将塑料干燥处理,确保塑料中不含水分,并检查模具密封性以防止气体进入模腔。
3.缩短:缩短是指制品尺寸比设计要小,可能由于塑料收缩不均匀或模具温度不稳定引起。
解决方法是通过调整模具温度和冷却系统,使塑料在注塑过程中均匀收缩,并确保模具温度稳定。
4.色差:色差是指制品表面颜色不均匀,可能由于塑料熔融不充分、颜料添加不均匀等原因。
解决方法是加长塑料的熔化时间,确保塑料充分熔融,并确保颜料充分混合均匀。
5.枝晶:枝晶是指制品表面出现树枝状的纹理,可能由于注塑温度过高或冷却时间不足引起。
解决方法是降低注塑温度,延长冷却时间,确保塑料在注塑过程中充分凝固。
6.毛刺:毛刺是指制品表面出现刺状的尖突物,可能由于模具间隙过大或模具磨损引起。
解决方法是调整模具间隙,确保模具紧密结合,并定期检查模具磨损情况。
7.烧焦:烧焦是指塑料在注塑过程中受热过度,产生发黑或炭化的现象。
烧焦可能由于注塑温度过高或注射速度过快引起。
解决方法是降低注塑温度,调整注射速度,确保塑料受热均匀。
总结起来,解决注塑成型缺陷的关键是调整注塑机参数、保证模具质量和稳定性,以及进行适当的后处理工艺。
此外,及时发现和修复模具的损坏也是避免缺陷的重要措施。
注塑模成型过程中的常见缺陷及解决方法
注塑模成型过程中的常见缺陷及解决方法
1 注塑模成型过程中的缺陷
注塑模是指将塑料以液体状态注入模具内,并承受模具内设计好的形状而成型的加工工艺。
这种加工工艺的缺陷主要体现在:(1)内应力
由于冷凝和冻结等原因,塑料在冷却期内会形成一定的内应力,这些内应力会折断或变形塑料制品,影响其成型的精度和尺寸的准确性;
(2)开裂
由于注塑模具的温度失去平衡,容易引起塑料表面开裂,影响塑料制品的外观质量;
(3)射脂
由于过大的模具压力,塑料在冷却过程中产生弹性变形,导致部分塑料夹在模具内,出现射脂现象,从而影响塑料制品的精度;
(4)易燃体
一些易燃物质在注塑模具成型过程中,受到热源的热量,容易引发火灾。
2 注塑模成型过程中的解决方法
(1)改善冷凝条件
合理设计模具内的冷凝段,增加冷却水的循环流量,加快冷却速度,降低内应力,减少变形现象;
(2)模具润滑
模具润滑能有效减少注塑模具生产过程中开裂的几率;
(3)改变模具温度
根据注塑塑料特性,采取合理的模具温度,确保合理的射出压力,有效减少射脂;
(4)加强安全防护
增强环境湿度,禁止一切产生火花的设备进入生产现场,防止火灾。
总之,正确处理注塑模具成型过程中的缺陷和解决方法,能有效
改善塑料制品的成型精度,改善它们的外观、可靠性和使用寿命,能
为有效利用注塑技术提供有效援力。
注塑缺陷及其解决方法
注塑缺陷及其解决方法注塑是一种常用的塑料加工方法,通过将加热熔融的塑料材料注入到模具中,冷却后形成所需的产品。
然而,在注塑过程中,往往会出现一些缺陷,影响产品的质量。
以下是一些常见的注塑缺陷及其解决方法。
1.气泡:气泡是注塑中最常见的缺陷之一、它们可能是由于塑料材料中的挥发性成分排放不完全,或者是熔融塑料中的气体在注射过程中迅速扩散而形成的。
解决气泡问题的方法包括:合理选择塑料材料、充分预干燥材料、提高注射速度和压力、优化模具结构等。
2.沉痕:沉痕是表面上的凹陷,通常是由于塑料材料的收缩不均匀或冷却不充分造成的。
解决沉痕问题的方法包括:调整注射温度和压力、改善模具冷却系统、增加冷却时间等。
3.翘曲:翘曲是注塑过程中产品变形的一种形式。
它可能是由于模具设计不合理、注射温度过高或产品冷却不充分引起的。
解决翘曲问题的方法包括:优化模具结构、调整注射温度和压力、增加冷却时间等。
4.热断裂:热断裂指的是在注塑加工过程中,产品的一些部位出现开裂或裂纹。
它可能是由于注射过程中产生的应力超过了材料的承受能力引起的。
解决热断裂问题的方法包括:调整注射速度和压力、改变注射顺序、增加降温时间等。
5.色差:注塑产品在颜色上出现不均匀或异色现象。
这可能是由于原料配比不准确或注射过程中的温度变化等原因造成的。
解决色差问题的方法包括:准确控制原料比例、稳定注射温度、使用色差控制剂等。
6.熔接线:熔接线是由于注塑模具的设计和操作问题导致两个或多个熔融塑料部分相互连接而形成的。
解决熔接线问题的方法包括:调整模具结构,避免部件交汇点过多,调整注射速度和压力等。
总之,注塑缺陷的解决方法主要包括调整材料配比、优化模具结构、控制注射温度和压力、增加冷却时间等。
同时,及时调整机器参数、进行模具维护和清洁,以保证注塑过程的稳定性和可靠性。
通过以上的措施,可以有效减少注塑缺陷,提高产品质量。
- 1、下载文档前请自行甄别文档内容的完整性,平台不提供额外的编辑、内容补充、找答案等附加服务。
- 2、"仅部分预览"的文档,不可在线预览部分如存在完整性等问题,可反馈申请退款(可完整预览的文档不适用该条件!)。
- 3、如文档侵犯您的权益,请联系客服反馈,我们会尽快为您处理(人工客服工作时间:9:00-18:30)。
熔合纹成因及改善措施 -- 注塑工艺
注射压力过低
适当提高注射压力
熔体温度过低
适当提高熔体温度
.
熔合纹成因及改善措施 -- 注塑设备
注塑机塑化能力不够,塑料 不能充分塑化
检查注塑机的塑化能力
喷嘴孔直径过小,使得注射 速度较慢
换用较大直径喷嘴
.
熔合纹成因及改善措施 -- 原料
润滑剂太少,熔体的流动性差 适当增加润滑剂的添加量
.
凹陷成因及改善措施 -- 注塑模具
模具的浇口及流道截面积过小 扩大相应位置的截面积
排气不良
改善排气系统
浇口位置不对称,熔体进入各 型腔的速度不同,各型腔中的 浇口尽量设置在对称处 制品冷却不均衡
冷却系统设计不合理,冷却不 均衡或冷却不足
改善冷却系统
.
凹陷成因及改善措施 -- 注塑工艺
熔体温度太高
降低熔体温度
模具温度太高
适当加大冷却水量或降低冷却 水温度
注射时间和保压时间太短 适当延长注射时间和保压时间
保压压力太低
适当提高保压压力
.
凹陷成因及改善措施 -- 注塑设备
加料系统工作不稳定,使供 料不稳定
保证供料系统充分供料
注塑机的喷嘴孔太小或局部 更换大直径的喷嘴或对喷嘴
堵塞
进行清理疏通
.
凹陷成因及改善措施 -- 原料
.
短射成因及改善措施 -- 注塑设备
设备选型不当,最大注射量小于 更换注射量符合要求的注
制品重量
塑机
喷嘴孔太小,熔体的注射速度降 低
更换直径较大的喷嘴
止逆阀出现故障,使熔体倒流 检修止逆阀
喷嘴为异物所阻塞,造成熔体流 动不畅
疏通喷嘴
.
短射成因及改善措施 -- 原料
原料的流动性太差
选用流动性好的原料
薄壁处的厚度不够
增加截面厚度
没有冷料井或冷料井设计不 合理,熔体进入型腔并快速 合理设计冷料井 冷凝,使得熔体流动不畅
.
短射成因及改善措施 -- 注塑工艺
模具温度太低
注射压力太低 保压时间太短 熔体温度过低 注射速度太慢
调整模具温度使之处于正常 范围
适当加大注射压力 合理控制保压时间 提高熔体温度 适当提高注射速度
.
喷射流成因及改善措施 -- 注塑模具
浇口设计不当
重新布置或改变浇口设计, 引导熔体与侧壁金属模面接 触
浇口或流道截面积较小 冷料井设置不合理
加大浇口与流道尺寸 加大冷料井
.
喷射流成因及改善措施 -- 注塑工艺
注射速度设置不合理
调整注射速度曲线,使熔体 流前以低速通过浇口,等到 熔体流出浇口外再提高速度
完整,如图所示 ❖ 短射的主要产生原因是注射压力或注射速度太低,熔体在
流向最末端的过程中冷却,通常在低熔料温度和模温的条 件下注射高粘度原料时会碰到这种情况,它也会发生在保 压设置过低的时候
.
短射成因及改善措施 -- 注塑模具
模具排气结构欠佳
修正或改善排气结构
浇口或流道的截面积较小且 长,熔体压力在流动过程中 修正或改善浇注系统 损失太大
迹,不仅有碍制品的美观,而且影响制品的力学性能 ❖ 熔合纹的主要产生原因是由若干熔体在型腔中汇合在一起
时,在其交汇处彼此不能熔合为一体而形成线状痕迹
.
熔合纹的分类
❖ 分为两种类型,熔接线(Meld Line)和熔接痕(Weld Line)
❖ 差别在于两熔体前沿的夹角θ的大小,如果 135,则
形成熔接线,否则形成熔接痕
冷料井不够大或位置不正确, 使冷料进入型腔
浇注系统的主流道进口部位或 分流道的截面积太小,导致流 料阻力太大
冷却系统设计欠佳,熔体在型 腔中冷却太快且不均匀
采用分流少的浇口形式,合理 选择浇口位置,在可能的条件 下选用单一点浇口 尽量减少嵌件数量
重新考虑冷料井的位置和大小
扩大主流道及分流道截面积
重新审视冷却系统的设计
原料中水分或可挥发成份含 对原料进行充分干燥,或少
量过多
用含挥发成份过多的原料
加入的润滑剂太少,熔体的 流动性不好
适当增加润滑剂用量
塑料制品常见缺陷与解决办法
.
内容简介
❖ 塑料注射成形缺陷的别名与描述 ❖ 塑料注射成形缺陷的主要产生原因 ❖ 塑料注射成形缺陷的修正办法
.
引入 •请大家说出制件存在什么问题?
.
塑料制品的常见缺陷
❖ 短射
❖ 飞边
❖ 熔合纹
❖ 烧焦
❖ 喷射流
❖ 流痕
❖ 凹陷
❖ 银线痕
❖ 翘曲
❖ 裂纹
❖ 气泡
❖ 表面剥离
含湿量大或易挥发物含量高
干燥原材料或清除易挥发物 质
.
喷射流(Jetting)
❖ 喷射流是指当熔体以高速流过喷嘴、流道、或浇口等狭窄 的区域后,进入开放或较宽厚的区域,并且没有与模壁接 触,发生喷射。蛇状的喷射流使熔体折叠而互相接触,造 成小规模的缝合线,如图所示
❖ 产生的主要原因是由于熔体进模时注射速度过快,粘在模 壁上的很快冷却,而后来的熔体再与冷料熔合而在制品表 面上形成蚯蚓状纹路
熔体温度过低
提高注射温度
.
凹陷(Shrinkage)
❖ 凹陷又称缩痕、收缩等,是指制品表面不平整,向内产生 浅坑或陷窝,如图所示
❖ 制品在冷却过程中,由于外层紧靠型腔的地方先行冷却固 化,而其内部后冷却固化,制品在固化过程中,内外的收 缩不一致,导致制品外层发生变形,产生外层内陷形成凹 陷。就宏观讲,凹陷多发生在制品壁厚最厚的地方或壁厚 急剧改变的地方
.
操练
•请分别分析产生这些缺陷的原因?
.
塑料注射成形缺陷的影响因素
❖ 注射成形过程是一个多因素、多变量交叉影响的复杂过程
模具质量
工艺参数
成形缺陷影响因素
注射机
物料质量
.
短射(Short shot)
❖ 短射又称欠注、充填不足、制件不满、走胶不齐等 ❖ 是指型腔未完全充满,使得制件不饱满,塑件外形残缺不
.
熔合纹的形成机理
❖ 熔接线位置上的分子取向变化强烈,该位置的力学结构强 度明显减弱
❖ 熔接痕以一定角度混合,相比熔接线分子取向更加一致, 形成位置的结构强度比熔接线大,视觉上也不明显
.
熔合纹成因及改善措施 -- 注塑模具
浇注系统设计不合理导致熔料 的分流会合
嵌件太多,熔体流经嵌件时, 其流速、流线和温度都会发生 变化
原料含水量过多,加重了排 气系统的负担
预先干燥原料
原料中添加的再生料过多, 影响了熔体的流动性
严格控制再生料的加入量
原料中所含杂质过多,易堵 尽量清除原料中的难熔固体
塞流道或喷嘴
杂质
.
熔合纹(Weld lines)
❖ 熔合纹又称熔接痕、熔接不良、熔合缝、缝合线等 ❖ 是指各塑料流体前端相遇时在制品表面形成的一条线状痕