铁合金冶炼工艺学期末复习资料
钢铁冶金期末复习
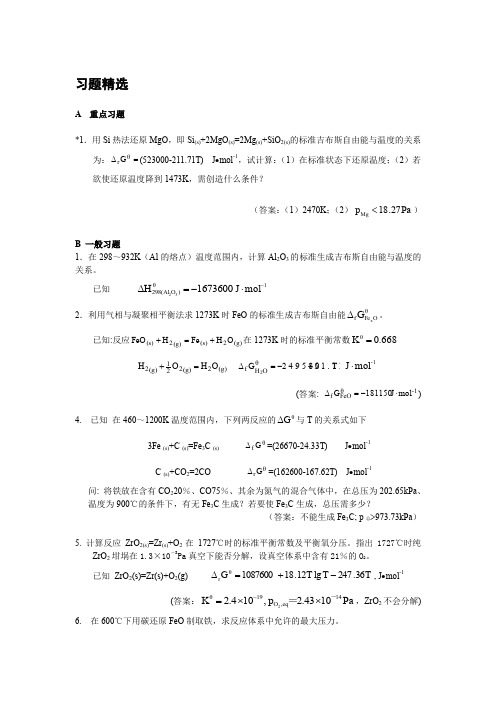
习题精选A 重点习题*1.用Si 热法还原MgO ,即Si (s)+2MgO (s)=2Mg (s)+SiO 2(s)的标准吉布斯自由能与温度的关系为:=∆θr G (523000-211.71T ) J ∙mol -1,试计算:(1)在标准状态下还原温度;(2)若欲使还原温度降到1473K ,需创造什么条件?(答案:(1)2470K ;(2)Pa 27.18Mg <p )B 一般习题1.在298~932K (Al 的熔点)温度范围内,计算Al 2O 3的标准生成吉布斯自由能与温度的关系。
已知 1673600θ)O 298(Al 32-=∆H 1mol J -⋅2.利用气相与凝聚相平衡法求1273K 时FeO 的标准生成吉布斯自由能θO Fe f x G ∆。
已知:反应(g)2(s)(g)2(s)O H Fe H FeO +=+在1273K 时的标准平衡常数668.0θ=K(g)2(g)221(g)2O H O H =+ T G 51.11249580θOH f 2+-=∆ -1mol J ⋅ (答案: -1θFeOf mol J 181150⋅-=∆G ) 4. 已知 在460~1200K 温度范围内,下列两反应的θG ∆与T 的关系式如下3Fe (s)+C (s)=Fe 3C (s) θf G ∆=(26670-24.33T ) J ∙mol -1 C (s)+CO 2=2CO θr G ∆=(162600-167.62T ) J ∙mol -1问: 将铁放在含有CO 220%、CO75%、其余为氮气的混合气体中,在总压为202.65kPa 、温度为900℃的条件下,有无Fe 3C 生成?若要使Fe 3C 生成,总压需多少?(答案:不能生成Fe 3C; p 总>973.73kPa )5. 计算反应ZrO 2(s)=Zr (s)+O 2在1727℃时的标准平衡常数及平衡氧分压。
指出1727℃时纯ZrO 2坩埚在1.3×10-3Pa 真空下能否分解,设真空体系中含有21%的O 2。
钢铁冶金概论复习资料

钢铁冶金概论期末复习(炼铁部分)1比较说明不同钢铁生产工艺流程铁矿石→去脉石、杂质和氧→铁铁→精炼(脱S、P、Si等)→钢还原熔化过程氧化精炼过程(炼铁)(炼钢)1.绘制高炉本体内型结构说明各部分名称(画白色部分即可:炉喉、炉身、炉腰、炉腹、炉缸、风口、渣口、铁口)高炉五大附属系统名称及作用(1)原料供应系统:保证及时、准确、稳定地将合格原料从贮矿槽送上高炉的炉顶;(2)送风系统:保证连续可靠地供给高炉冶炼所需数量和保证足够温度的热风;(3)渣铁处理系统:及时处理高炉排放出的渣铁,保证高炉生产正常运行,获得合格的生铁和炉渣产品;(4)煤气清洗系统:保证回收高炉煤气,使其含尘量降到15mg/m3左右,以便利用;(5)燃料喷吹系统:保证喷入高炉所需燃料,以代替部分焦炭消耗。
高炉内按物料变化五个区域的划分,并简单了解各部分的变化过程(1)块状区主要特征:焦与炭呈交替分布层状,皆为固体状态主要反应:矿石间接还原,碳酸盐分解(2)软熔区主要特征:矿石呈软熔状,对煤气阻力大主要反应:矿石的直接还原,渗碳和焦炭的气化反应(3)滴落区主要特征:焦炭下降,其间夹杂渣铁液滴主要反应:非铁元素还原,脱碳、渗碳、焦炭的气化反应(4)焦炭回旋区主要特征:焦炭作回旋运动主要反应:鼓风中的氧和蒸汽与焦炭及喷入的辅助燃料发生燃烧反应(5)炉缸区主要特征:渣铁相对静止,并暂存于此主要反应:最终的渣铁反应熟练掌握高炉冶炼主要技术经济指标的表达方式1有效容积利用系数ημ定义:每立方米高炉有效容积每昼夜生产的合格铁量(t/m3·d)我国ημ=1.6~2.4(t/m3·d)日本ημ=1.8~2.8(t/m3·d)2焦比定义:冶炼每吨生铁所消耗的焦炭的千克数(kg/t)我国焦比为250~650(kg/t)3煤比定义:冶炼每吨生铁所消耗的煤粉的千克数(kg/t)我国煤比为50~220(kg/t)4燃料比(焦比+煤比)定义:冶炼每吨生铁所消耗的固体燃料的总和(kg/t)我国燃料比为450~700(kg/t)5综合焦比(焦比+煤比×煤焦置换比)6煤焦置换比定义:喷吹1kg煤粉所能替代的焦炭的千克数,一般为0.8左右7焦炭冶炼强度定义:每立方米高炉有效容积每昼夜燃烧的焦炭吨数(t/m3·d)8综合冶炼强度定义:每立方米高炉有效容积每昼夜燃烧的综合焦炭的吨数(t/m3·d),一般为0.9~1.15t/m3·d利用系数、焦比及冶炼强度三者关系纯焦冶炼时:利用系数=焦炭冶炼强度/焦比喷吹燃料时:利用系数=综合冶炼强度/综合焦比(5)休风率定义:指高炉休风时间占规定作业时间的百分比(6)焦炭负荷指每批炉料中铁矿石的重量与焦炭重量之比,用以评估燃料利用水平和调节配料四种天然铁矿石的名称和分子式及特点(1)磁铁矿:主要含铁矿物为Fe3O4 特点:理论含铁量72.4%,红条痕,较软,易还原。
炼铁学复习资料

ೖᄤኧআᇴᓾ೯!
ဉීǖጲሆᒑ۞ࠤஊျਜ਼ݝॊৈཱཽྀᆐᒮገࡼ൙ၤᄌLjఠ၂ดྏᏐࡍ᎖ᑚৈपᆍLjด
ྏᑵཀྵቶݙতۣᑺLjࡊښஞݬఠ!
名词解释:
假象及半假象赤铁矿:由于地表的氧化作用,自然界中纯磁铁矿很少见,在化学成分上Fe3O4被氧化成Fe2O3,但仍保留了原磁铁矿结晶结构特征。
有效容积利用系数:每立方米高炉有效容积每昼夜生产的合格铁量。
焦比:冶炼每吨生铁所消耗的焦炭的千克数。
煤比:冶炼每吨生铁所消耗的煤粉的千克数。
燃料比:冶炼每吨生铁所消耗的固体燃料的总和。
(燃料比=焦比+煤比)
综合焦比:焦比+煤比X煤焦置换比
煤焦置换比:喷吹1kg煤粉所能代替的焦炭数。
焦炭冶炼强度:每立方米高炉有效容积每昼夜燃烧的焦炭吨数。
综合冶炼强度:每立方米高炉有效容积每昼夜燃烧的综合焦炭的吨数。
燃烧强度:每平方米炉缸截面积每昼夜燃烧的焦炭吨数。
工序能耗:Ci=(燃料消耗+动力消耗-回收二次能源)/产品产量
固相反应:在一定温度下,某些离子克服晶格结合力,进行位置交换,并扩散到与其相邻的其他晶格内的过程,叫固相反应。
铁酸钙理论(低温烧结理论):生产高碱度烧结矿,粘结相主要由铁酸钙组成。
该系的特点是无需高温,燃料消耗少;矿物的强度高还原性好。
自蓄热作用:随着烧结层的下移,料层温度的最高值逐渐提高。
自蓄热来源于被上层热烧结矿预热了的空气以及上层带入的热废气的加热作用。
HPS:指小球烧结法,即将烧结混合料用圆盘造球机预先制成一定粒度(上限为6·~8mm),然后使小球外裹部分燃料,最后铺在烧结台车上进行烧结的造块新工艺。
SFCA:即复合铁酸钙理论,实际烧结矿中的铁酸钙,无论是针状还是片状,都不是单纯的CaO和Fe2O3组成的,铁酸钙中含有一定量的Al2O3和SiO2等,称为复合铁酸钙。
铁氧化物的直接还原:还原剂为固体C,还原产物为CO。
铁氧化物的间接还原:还原剂是H2或CO,还原产物为H2O或CO2。
直接还原度:通过直接还原方式还原出来的铁量与还原出来的总铁量之比。
耦合反应:风口以下炉缸区域,渣铁间的氧化还原反应,即耦合反应。
熔化温度:炉渣受热升温过程中,固相完全消失的最低温度,即相图上的液相线温度(相当于软熔带下沿温度)。
熔化性温度:炉渣可以自由流动时的最低温度。
长渣和短渣:温度降到一定值后,粘度急剧上的称为短渣;随温度下降粘度上升缓慢称为长渣。
表面张力:生成单位面积的液相与气相的新交界面所消耗的能量。
界面张力:渣铁之间形成单位面积界面所消耗的能量。
燃烧带:风口前碳被氧化而气化的区域,又叫风口回旋区,它是高炉内唯一的氧化区域,故又称氧化带。
管道行程:煤气总是沿着透气性好的路线上升,高炉炉料的特性及在炉内的分布时不同的,在炉内局部出现气流超过临界速度的转态,局部区域煤气流过分发展的现象。
液泛现象:当渣量多,渣粘度大,煤气流速快时,出现煤气把渣铁拖住而不能降落的现象。
空区(热储备区):高炉中下部,炉料与煤气的温差很小,大约只有5~50℃左右,发生微弱
金属工艺学复习资料

金属工艺学复习资料第一章1.使用性能:材料在使用过程中所表现的性能(力学性能,物理性能,化学性能)2.工艺性能:材料在加工过程中表现的性能(铸造,锻压,焊接,热处理,材料性能)3.拉伸过程的4个阶段:I.弹性形变II.屈服III.均匀塑性变形阶段IV.颈缩4.δs:屈服强度δ0.2:条件屈服强度δb:抗拉强度A k:冲击韧性HB:布氏硬度HR:洛氏硬度HV:维式硬度Ψ:收缩率δ:伸长率5.韧脆转变温度:在某一温度范围内冲击韧性值急剧下降的现象。
6.疲劳极限:材料经过无数次应力循环而不发生疲劳断裂的最高应力。
用δ-1表示。
第二章1.常见纯金属的晶格类型:体心立方晶格:晶格常数a,原子数2,常见金属α-Fe,δ-Fe。
面心立方晶格:晶格常数a,原子数4,常见金属γ-Fe,Cu,Ag。
密排六方晶格:晶格常数:底面边长a和高c存在c/a=1.633,常见金属Mg,Zn,Be。
2.结晶:物质由液态转化为晶态的过程。
3.过冷度:理论结晶温度和实际结晶温度之差,过冷度大小与冷速有关。
冷速越大,过冷度越大,过冷是结晶的必要条件。
4.结晶的过程:晶核的形成----晶核长大,长成树枝晶。
5.晶粒大小对金属机械性能的影响:常温下,晶粒越细小,晶界面积越大,金属机械性能越好。
强度,硬度高,塑性韧性高。
6.细化晶粒的过程:控制过冷度----变质处理----振动搅拌----热处理7.同素异形体的转变:金属在固态下,随着温度的改变其晶体结构发生变化的现象。
912℃1394℃例:α-Fe------------γ-Fe-------------δ-Fe(体心)(面心)(体心)7.重结晶(二次结晶):同素异构的转变。
8.合金:由两种或两种材料以上(其中一种是金属)组成的具有金属特性的材料。
9.相:金属或结晶中凡是化学成分和晶体结构相同,并与其他部分有界面分开的均匀组成部分。
10.固溶强化:由于溶质原子融入溶剂晶格产生晶格畸变而造成材料硬度和强度升高,塑性和韧性没有明显降低。
炼钢学复习资料
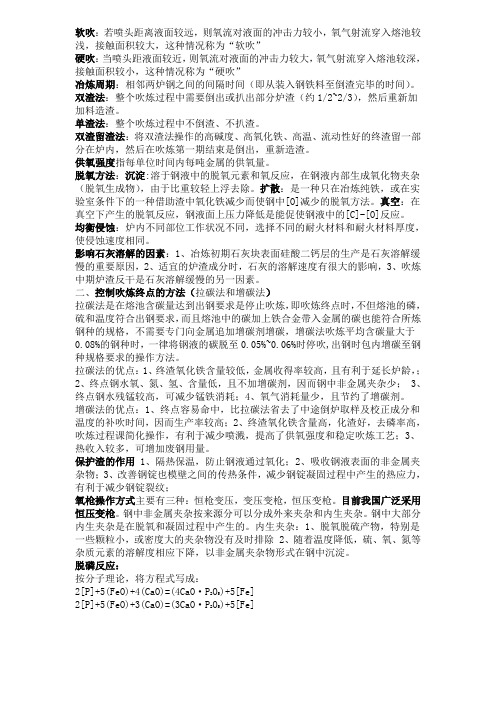
软吹:若喷头距离液面较远,则氧流对液面的冲击力较小,氧气射流穿入熔池较浅,接触面积较大,这种情况称为“软吹”硬吹:当喷头距液面较近,则氧流对液面的冲击力较大,氧气射流穿入熔池较深,接触面积较小,这种情况称为“硬吹”冶炼周期:相邻两炉钢之间的间隔时间(即从装入钢铁料至倒渣完毕的时间)。
双渣法:整个吹炼过程中需要倒出或扒出部分炉渣(约1/2~2/3),然后重新加加料造渣。
单渣法:整个吹炼过程中不倒渣、不扒渣。
双渣留渣法:将双渣法操作的高碱度、高氧化铁、高温、流动性好的终渣留一部分在炉内,然后在吹炼第一期结束是倒出,重新造渣。
供氧强度指每单位时间内每吨金属的供氧量。
脱氧方法:沉淀:溶于钢液中的脱氧元素和氧反应,在钢液内部生成氧化物夹杂(脱氧生成物),由于比重较轻上浮去除。
扩散:是一种只在冶炼纯铁,或在实验室条件下的一种借助渣中氧化铁减少而使钢中[O]减少的脱氧方法。
真空:在真空下产生的脱氧反应,钢液面上压力降低是能促使钢液中的[C]-[O]反应。
均衡侵蚀:炉内不同部位工作状况不同,选择不同的耐火材料和耐火材料厚度,使侵蚀速度相同。
影响石灰溶解的因素:1、冶炼初期石灰块表面硅酸二钙层的生产是石灰溶解缓慢的重要原因,2、适宜的炉渣成分时,石灰的溶解速度有很大的影响,3、吹炼中期炉渣反干是石灰溶解缓慢的另一因素。
二、控制吹炼终点的方法(拉碳法和增碳法)拉碳法是在熔池含碳量达到出钢要求是停止吹炼,即吹炼终点时,不但熔池的磷,硫和温度符合出钢要求,而且熔池中的碳加上铁合金带入金属的碳也能符合所炼钢种的规格,不需要专门向金属追加增碳剂增碳,增碳法吹炼平均含碳量大于0.08%的钢种时,一律将钢液的碳脱至0.05%~0.06%时停吹,出钢时包内增碳至钢种规格要求的操作方法。
拉碳法的优点:1、终渣氧化铁含量较低,金属收得率较高,且有利于延长炉龄,;2、终点钢水氧、氮、氢、含量低,且不加增碳剂,因而钢中非金属夹杂少;3、终点钢水残锰较高,可减少锰铁消耗;4、氧气消耗量少,且节约了增碳剂。
钢铁冶金复习资料
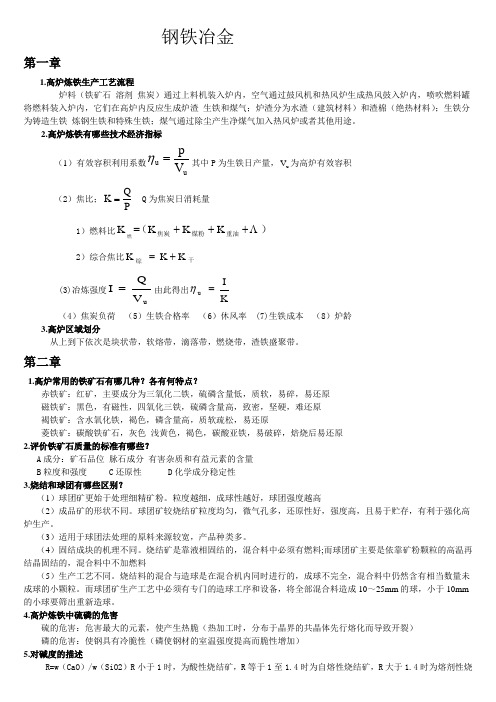
钢铁冶金第一章1.高炉炼铁生产工艺流程炉料(铁矿石 溶剂 焦炭)通过上料机装入炉内,空气通过鼓风机和热风炉生成热风鼓入炉内,喷吹燃料罐将燃料装入炉内,它们在高炉内反应生成炉渣 生铁和煤气;炉渣分为水渣(建筑材料)和渣棉(绝热材料);生铁分为铸造生铁 炼钢生铁和特殊生铁;煤气通过除尘产生净煤气加入热风炉或者其他用途。
2.高炉炼铁有哪些技术经济指标(1)有效容积利用系数uu V p=η其中P 为生铁日产量,u V 为高炉有效容积 (2)焦比;PQ K = Q 为焦炭日消耗量 1)燃料比)(重油煤粉焦炭燃 +++=K K K K2)综合焦比干综K K K +=(3)冶炼强度u V QI =由此得出K I u =η(4)焦炭负荷 (5)生铁合格率 (6)休风率 (7)生铁成本 (8)炉龄3.高炉区域划分从上到下依次是块状带,软熔带,滴落带,燃烧带,渣铁盛聚带。
第二章1.高炉常用的铁矿石有哪几种?各有何特点?赤铁矿:红矿,主要成分为三氧化二铁,硫磷含量低,质软,易碎,易还原磁铁矿:黑色,有磁性,四氧化三铁,硫磷含量高,致密,坚硬,难还原褐铁矿:含水氧化铁,褐色,磷含量高,质软疏松,易还原菱铁矿:碳酸铁矿石,灰色 浅黄色,褐色,碳酸亚铁,易破碎,焙烧后易还原2.评价铁矿石质量的标准有哪些?A 成分:矿石品位 脉石成分 有害杂质和有益元素的含量B 粒度和强度C 还原性D 化学成分稳定性3.烧结和球团有哪些区别?(1)球团矿更始于处理细精矿粉。
粒度越细,成球性越好,球团强度越高(2)成品矿的形状不同。
球团矿较烧结矿粒度均匀,微气孔多,还原性好,强度高,且易于贮存,有利于强化高炉生产。
(3)适用于球团法处理的原料来源较宽,产品种类多。
(4)固结成块的机理不同。
烧结矿是靠液相固结的,混合料中必须有燃料;而球团矿主要是依靠矿粉颗粒的高温再结晶固结的,混合料中不加燃料(5)生产工艺不同。
烧结料的混合与造球是在混合机内同时进行的,成球不完全,混合料中仍然含有相当数量未成球的小颗粒。
完整版北京科技大学钢铁冶金学炼铁部分知识点复习
完整版北京科技大学钢铁冶金学炼铁部分知识点复习第一章概论1、试述3种钢铁生产工艺的特点。
答:钢铁冶金的任务:把铁矿石炼成合格的钢。
工艺流程:①还原熔化过程(炼铁):铁矿石去脉石、杂质和氧铁;②氧化精炼过程(炼钢):铁精炼(脱C、Si、P 等)钢。
高炉炼铁工艺流程:对原料要求高,面临能源和环保等挑战,但产量高,目前来说仍占有优势,在钢铁联合企业中发挥这重大作用。
直接还原和熔融还原炼铁工艺流程:适应性大,但生产规模小、产量低,而且很多技术冋题还有待解决和完善。
2、简述高炉冶炼过程的特点及三大主要过程。
答:特点:①在逆流(炉料下降及煤气上升)过程中,完成复杂的物理化学反应;②在投入(装料)及产出(铁、渣、煤气)之外,无法直接观察炉内反应过程,只能凭借仪器仪表简介观察;③维持高炉顺行(保证煤气流合理分布及炉料均匀下降)是冶炼过程的关键。
三大过程:①还原过程:实现矿石中金属元素(主要是铁)和氧元素的化学分离;②造渣过程:实现已还原的金属与脉石的熔融态机械分离;③传热及渣铁反应过程:实现成分与温度均合格的液态铁水。
3、画出高炉本体图,并在其图上标明四大系统。
答:煤气系统、上料系统、渣铁系统、送风系统。
4、归纳高炉炼铁对铁矿石的质量要求。
答:①高的含铁品位。
矿石品位基本上决定了矿石的价格,即冶炼的经济性。
② 矿石中脉石的成分和分布合适。
脉石中SiO2和A12O3要少,CaO多,MgO含量合适。
③有害元素的含量要少。
S、P、As、Cu对钢铁产品性能有害,K、Na、Zn、Pb、F对炉衬和高炉顺行有害。
④有益元素要适当。
Mn、Cr、Ni、V、Ti等和稀土元素对提高钢产品性能有利。
上述元素多时,高炉冶炼会出现一定的问题,要考虑冶炼的特殊性。
⑤矿石的还原性要好。
矿石在炉内被煤气还原的难易程度称为还原性。
褐铁矿大于赤铁矿大于磁铁矿,人造富矿大于天然铁矿,疏松结构、微气孔多的矿石还原性好。
⑥冶金性能优良。
冷态、热态强度好,软化熔融温度高、区间窄。
钢铁冶复习资料
钢冶金一、炼钢的基本任务?答:炼钢的基本任务是脱碳、脱硫、脱磷、脱氧,去除有害气体和非金属夹杂物,提高温度和调整成分。
(“四脱”、“二去”、“二调整”。
)二、铁水预脱硫的优势(意义)?答:①铁水中含有大量的硅、碳和锰等还原性好的元素,能够大大提高硫在铁水中的活度系数,在使用不同类型的脱硫剂,特别是强脱硫剂,不会发生大量的烧损以致影响脱硫反应的进行,与炼铁、炼钢相结合可以实现深度脱硫。
②对炼铁来说,能减轻高炉负担,降低焦比,减少渣量,提高生产率。
③对炼钢来说,能减轻负担,简化操作,减少渣量,提高炼钢生产率和金属回收率,提高钢的品种质量。
④可以在出铁水沟,鱼雷罐车或者铁水罐中进行,设备简单,操作方便。
三、铁水预脱硅的目的及方法?答:目的:由于铁水中硅的氧势比磷的氧势低得多,当脱磷过程加入氧化剂后,硅与氧的结合能力远远大于磷与氧的结合能力,所以硅比磷优先氧化。
为了减少脱磷剂用量,提高脱磷效率,开发了铁水预脱硅技术。
脱硅剂:固体氧化剂有氧化铁皮、铁矿石等(即FeO,Fe2O3,Fe3O4)气体氧化剂有空气或O2方法:A.高炉出铁沟脱硅法B.鱼雷罐车或铁水罐中喷射脱硅剂脱硅法C.“两段式”脱硅法(前两种的综合先A后B)四、有利于脱磷反应进行的工艺条件。
答:高碱度、高(FeO)含量(氧化性)、流动性良好的熔渣、充分的熔池搅拌、适当的温度和大渣量。
五、转炉炼钢的工艺流程。
答:装料:废钢、铁水;吹炼:供氧,造渣;取样测温;出钢;脱氧合金化;溅渣护炉;出渣。
六、转炉炼钢脱硫的基本途径、原理及有利条件。
答:转炉炼钢有两个基本途径:炉渣脱硫和气化脱硫。
1)炉渣脱硫:①原理:[S]+(CaO)=(CaO)+[O][S]+(MnO)=(MnS)+[O][S]+(MgO)=(MgS)+[O]②有利条件:高温,高碱度,低(FeO)含量,良好的流动性。
2)气化脱硫:①原理:[S]+2[O]={SO2}(FeS)+2[O]=Fe+{SO2}②有利条件:具有一定的氧势,即氧的浓度。
钢铁冶金工艺学考试重点
第1章1.高炉内型从下往上分别是 炉缸、炉腹、炉腰、炉身、炉喉。
2.高炉附属系统: 供料系统、送风系统、除尘系统、渣铁处理系统、燃料喷吹系统。
3.根据物料存在形态不同可将高炉划分五个不同区域:块状带、软熔带、滴落带、燃烧带、渣铁盛聚带。
特征:块状带: 炉料中水分蒸发及受热分解,铁矿石还原,炉料与煤气热交换焦炭与矿石以层状分布,呈固体状态,以气—固相反应为主。
软熔带: 炉料在该区域软化,在下部边界开始熔融滴落,主要进行直接还原反应,初渣形成。
滴落带: 滴落的液态渣、铁与煤气及固体炭之间进行多种复杂的反应。
燃烧带: 喷入的燃料与热风发生燃烧反应,产生高热煤气是炉内温度最高的区域。
渣铁盛聚带:在渣铁层间的交界面及铁滴穿过渣层时发生渣金反应。
4.高炉生铁: ][Fe w 在%5.4~%5.2范围,铸铁中不超过%5。
生铁分为铸造生铁、炼钢生铁、特殊生铁。
5.高炉煤气: CO 占%25%20- 2CO 占%20%15- 2N 占%55左右 2H 和4CH 含量很少。
高炉煤气是钢铁联合企业的重要二次能源,主要用作热风炉燃料,还可供动力炼焦烧结炼钢轧钢等部门使用。
6.有效容积利用系数 指高炉单位有效容积的日产铁量。
7.焦比)(K 指 生产每吨生铁消耗的焦炭量8.冶炼强度 )(I 指单位体积高炉有效容积内的焦炭日消耗量第2章1.高炉冶炼的三种原料: 焦炭、溶剂、铁矿石 焦炭作为燃料和还原剂,是主要能源;溶剂主要用来助熔造渣;铁矿石是主要的冶炼对象。
2.矿石 :能从中经济合理的提炼金属矿物 脉石:没有提炼价值的矿物或岩石 高炉冶炼的铁矿石分为两类:天然富矿和人造富矿。
3.天然铁矿石按其主要矿物分为 :赤铁矿、磁铁矿、褐铁矿、菱铁矿4.铁矿石质量评价: A.成分a.矿石品位:即铁矿石的铁含量。
入炉品位越高,越有利于提高产量、降低焦比。
矿石的贫富一般以其理论铁含量的%70来评价 b.脉石成分 c.有害杂质和有益元素的含量。
合金熔炼期末复习题精简版
第一章1.概念题1)铸铁:含碳量大于2.14%或者组织中具有共晶组织的铁碳合金。
2)铁碳双重相图:Fe-Fe3C介稳定系相图和Fe-C(石墨)稳定系相图相结合的双重相图。
3)分配系数:4)偏析系数:5)珠光体领域:每个珠光体团由多个结构单元组成,每个结构单元中片层基本平行。
每个结构单元称作一个珠光体领域。
2.简答题1)普通灰铸铁,除铁外还还有哪些元素?C、Si、Mn、S、P。
2)介稳定和稳定相图的共晶共析点差异。
共晶点: Fe-Fe3C 1147℃ 4.3%(介稳定)Fe-C 1153℃ 4.26%(稳定)共析点:Fe-Fe3C 727℃ 0.77%Fe-C 736℃ 0.69%3)含Si量对稳定系相图的影响。
Si增加,共晶点和共析点含碳量减少,温度增加。
硅的加入使相图上出现了共晶和共析转变的三相共存区。
Si越多,奥氏体加石墨的共晶温度高出奥氏体加渗碳体的温度也越多。
硅量的增加,缩小了相图上的奥氏体区。
4)说明碳当量、共晶度的定义、意义,如何使用碳当量、共晶度确定铸铁的组织。
元素对共晶点实际碳量的影响,将这些元素的量折算成碳量的增减,叫做碳当量CE。
CE>4.26%为过共晶成分 CE=4.26%为共晶成分; CE<4.26%亚共晶成分。
铸铁的实际含碳量和共晶点的实际含碳量的比值,叫做共晶度S C。
S C >1为过共晶;S C =1为共晶;S C <1为亚共晶成分。
5)按石墨形态铸铁分为哪几种,做出各种石墨形态的示意图?灰铸铁(片状) 球墨铸铁蠕墨铸铁团絮状石墨铸铁(可锻铸铁)6)形成球状石墨的两个必要条件。
铁液凝固时必须有较大的过冷度和较大的铁液和石墨的界面张力。
第二章一、概念题1.灰口铸铁:通常是指断面呈灰色,其中的碳的主要以片状石墨形式存在的铸铁。
2.孕育处理:铁液浇注以前,在一定的条件下,向铁液中加入一定量的孕育剂以改变铁液的凝固过程,改善铸态组织,从而达到提高性能为目的的处理方法。
- 1、下载文档前请自行甄别文档内容的完整性,平台不提供额外的编辑、内容补充、找答案等附加服务。
- 2、"仅部分预览"的文档,不可在线预览部分如存在完整性等问题,可反馈申请退款(可完整预览的文档不适用该条件!)。
- 3、如文档侵犯您的权益,请联系客服反馈,我们会尽快为您处理(人工客服工作时间:9:00-18:30)。
绪论一铁合金定义:铁合金是一种或者两种以上金属或非金属元素融合在一起的合金分类单元合金二元合金多元合金,块状合金线状合金粉状合金二铁合金主要用途:1做脱氧剂,消除钢业中的过量的氧2做合金元素添加剂,改善钢的质量与性能3用作铸造晶核孕育剂(不锈钢、工具钢、轴承钢)4用作还原剂三铁合金分类:1按铁合金中主元素分类:主要有Si、Mn、Cr、V、Ti、W、Mo等系列铁合金。
2按产品中含碳量分类:高碳、中碳、低碳、微碳、超微碳等。
3按生产方法分类:高炉铁合金、电炉铁合金、炉外法铁合金、真空固态还原法铁合金、转炉铁合金、电解法铁合金。
1.2铁合金生产的主要方法1按使用设备分类:高炉法电炉法、炉外法、转炉法及真空电阻炉法2方法的特点:高炉法 1.生产率高,连续生产,量大,成本低2.品种高炉Fe-Mn、富锰渣、低硅铁、低硅锰、镍铁;矿热炉1.连续生产2.品种 Fe-Si、硅钙合金、工业硅、高碳锰铁、硅锰合金、高碳铬铁、硅铬合金等。
电弧炉1生产是间歇进行的。
2品种中、低碳锰铁,中、低、微碳铬铁及钒铁等。
转炉1.容量小小于等于12t,6t为主;吹氧气底吹、顶吹为主2.必须先建高炉或矿热炉与之匹配。
真空电阻炉法1真空状态下冶炼,间歇式2品种超微C Fe-Cr C≤0.03%,Fe-Mn-N,Fe-Cr-n3根据渣量多少:有渣法、无渣法4根据连续与否5冶炼过程热量来源分类1.碳热2.电热3.电硅热4.碳硅热5.金属热第四节铁合金冶炼的技术经济指标一产量指标:1基准量(t):在一段时间内(年月日)生产的(合格铁合金产品其准成分折算后的铁合金产品产量)核算公式:基准量(t)=实物量(t)*实际成分%/基准成分%2实物量(t):实际的合格铁合金产品弃量(没有可比性)二质量指标:1合格率:一段时间内,生产的合格铁合金产品占生产总生产量的百分比。
2.品级率:一段时间内生产某一品级的合格铁合金占总生产量的百分比。
三消耗指标:1电耗:一段时间内,生产一吨的某铁合金所消耗的电量,KWh/t(不含冶炼过程中的动力学消耗电和照明耗电量)2原料消耗:一段时间内生产一吨的某铁合金所消耗的原材料量,kg/t。
指标要求:优质、高产、低耗。
第二章铁合金冶炼的基本原理第一节铁合金冶炼的任务任务的含义用恰当的还原剂或者氧化剂从开采的矿石中将我们所需的元素还原或者氧化出来,得到我们所需的合金。
(恰当的含义:1.还原或者氧化的能力 2.价格低廉 3.来源广泛,容易获得)第二节还原剂的选择碳质还原剂1种类:石油焦、沥青、气煤焦、冶金焦、煤炭2成分:固定碳+灰分+挥发分=100%3特点:(1)碳的还原能力强(2)生成产物CO自动逸出,同时再参与还原(3)改善了透气性(4)还原后合金渗碳产品普遍碳含量高4品种Fe-Si、工业硅、Ca-Si、Ba-Si、Ba-Al-Si、Mn-Si、Cr-Si、Ba-Ca-Si、Fe-Al-Si用Al做还原剂1.只能还原部分氧化物2. 产物用Si做还原剂1.通常只能去还原MoO、TiO2、Fe-W2部分还原时炉里需要加石灰3.品种:Fe-Mo、Fe-W、Fe-Ti第三节氧化精炼生产铁合金转炉法生产中低碳Fe-Cr、中低碳Fe-Mn1原料:液态高碳铬铁、高碳锰铁2吹氧[C]+{O2}——{CO}↑[Cr]+{O2}——(Cr2O3)[Mn]+{O2}——(Mno}真空电阻炉生产微碳Fe-Cr1.原料: 高碳Fe-Cr、铬精矿粉2.反应机理Cr2O3+Cr7O3——9[Cr]+3{CO}↑抽真空将CO带走,反应不断向右进行,从高碳Fe-Cr变成微碳Fe-Cr第四节选择氧化与选择还原选择还原(氧化)用同一种还原剂(氧化剂)去还原(氧化)多种氧化物的时候,必然有的元素先还原(氧化)有的后还原(氧化),希望的元素多还原(不氧化或少氧化),不希望的元素少还原或不还原(多氧化)。
第三章电极一作用电极是电炉的重要部件,是短网的一部分。
依靠电极把经过电炉用变压器输送来的低电压和大电流送到炉内,通过电极端部的电弧,炉料电阻以及炉内熔体,把电能转换成热能而进行高温冶炼。
第三节自焙电极的事故及处理一悬料事故:1电极的悬料:电极糊块大,:使糊柱内出现较大空间2漏糊事故:液态电极糊从电极壳损坏处流出3过早烧结事故:电极在铜瓦上半部呈塑性状态,这是正常的烧结过程,但有时由于在铜瓦以上的部分已过早的烧结好。
4硬断:已烧结好的正常工作的电极发生折断5软断:未焙烧好的电极发生折断6糊柱高度:电极糊在电极壳内的填充高度。
第四章硅铁的冶炼:硅铁生产简况:产量最大厂家最多耗电最多第三节硅铁牌号、用途1.根据Si Al来划分五档<=0.5%,1%1.5%2%>2%2.根据Si含量不同分为ABC:A含74~80%C含72~80%3基准量含Si 75%折算4.Al含量生产硅钢用Fe—Si做合金剂第四节硅铁冶炼的原料一硅石二焦炭小炉子3~15mm 大炉子5~25mm 小于3mm焦粉40~100mm 下限~上限减少上下限使力度均匀转鼓?的制定焦炭的强度第五节硅铁冶炼的原理一SiO2被C还原的总反应式SiO2+2C==Si+2CO Si+Fe==FeSi SiO2+Fe+2C==FeSi+2CO Si 33.33%二.SiO2的还原机理熔炼的硅铁含硅量越低,二氧化硅被还原的理论开始温度也就越低。
三.其他元素的还原1.Al的还原Al2O3 局部 2.Fe的还原F2O3 全部3.Ca的还原CaO 少量4.P的还原P2O5全部5.Mg的还原MgO少量四.硅的挥发:由于二氧化硅还原生成一氧化硅中间产物,必然有SiO挥发,还有极少量SiO没有被还原而进入炉渣。
第六节硅铁合金冶炼的操作一几个基本概念:1坩埚区炉内进行显著熔化反应的区域2锥体以电极为中心,为充分吸收电极周围的盐量二形成的一个锥形炉料3扎眼为了改善炉料的透气性,用圆钢或木棒在炉料上扎若干个孔洞4捣炉为了改善炉料的透气性,用捣炉机火锅铁铲改变炉料在炉内的分布的操作。
(1.上面翻到下面2.中心料到边缘去)5刺火在冶炼过程中由于炉料透气性差,导致炉内还原的气体不能正常逸出,随温度升高,气体体积膨胀,造成炉内大量的气体积聚在炉料某薄弱处冲击形成的大火叫刺火。
(危害1.热量损失2.Si挥发)二正常炉况的标志1负荷稳定,电极插入炉料深而稳定2炉料透气性好,全炉均匀冒淡黄色火焰3刺火塌料,现象少4出铁出渣正常5产品质量合格,产量高而稳观察1.看料面2.看配电表3.看结果三不正常炉况的标志1.还原剂过量:特征是:炉料导电性增加,电流上涨,电极上抬;炉料松散,火焰长,刺火塌料严重,塌料后电极表面很光;捣炉时料面松散像生料,多碳后期,电极下插很浅,能清楚地听到电弧声,炉料难以压住弧光,锥体边缘结成硬块;炉眼难开,出铁量少,铁水温度低,排渣困难。
处理:应在料批中减少焦炭用量,同时加强炉口操作管理。
还原剂过剩严重时,可在电极周围增加适量硅石。
炉内形成碳化硅时,可加些铁屑予以破坏。
2.还原剂不足;特征:前期电极能深插,但负荷送不足;后期电流急剧波动,电极反而上抬,炉子吃料慢,炉料发粘,透气性不好,捣炉时粘料多,刺火严重并不难以解除,炉口温度高,料面冒火少,火苗暗软无力,炉内死气沉沉,有的地方发黑不冒火,未还原的融融石英积聚于炉缸,炉眼堵塞,出铁口难开,炉渣黏不易排出,炉内气体压力大,出铁口有喷火现象,出铁口难堵,合金含硅低,出铁量少;炉口表面干锅界限明显,电极消耗快,电极上粘附有粘稠的石英玻璃丝,且较难铲除。
处理应稳住电极,放宽锥体,勤扎眼,彻底捣炉,在捣炉时根据实际情况添加定量焦炭,并在料批中增加焦炭的用量。
四出铁出渣1出铁次数2出渣3浇注:分层浇第六节钢铁分化与成分偏析1、什么叫硅铁粉化指硅铁在储存或运输过程中,自动的由块状变为粉状的现象。
2、硅铁粉化产生的原因:内因:硅铁中存在的杂质含量Al、Ca、P偏高。
外因:硅铁遇雨或受潮加速硅铁的粉化。
3硅铁粉化预防措施:1、精料,降低原料中带入的三氧化二铝、氧化钙、五氧化二磷2、在储运过程中严防淋雨或避免受潮4什么叫成分偏析硅铁锭中Si化学成分分布不均匀的现象。
5产生偏析的原因:内因:Fe的密度远大于Si的密度造成在凝固过程中Si上浮Fe下沉,造成同一断层上Si上下不均匀。
外因:与凝固铁水温度,浇铸厚度相关。
6避免偏西措施:①降低铁水浇注温度,太高的铁水镇静后浇铸②减薄浇铸厚度75%Fe-Si厚度≦100mm③改善通风条件,加速冷却六Fe-Si冶炼技术经济指标(加)七配料计算第八节硅铁精炼一什么叫硅铁精炼从矿热炉冶炼出的硅铁铁水含有较高的Al及其他杂质含量对其采取精炼的方法降低硅铁中的Al等杂质,成这个过程为硅铁精炼。
二含铝高的硅铁在炼钢浇铸过程结瘤。
三原理:通过吹氧气或吹入氯气去与液态硅铁铁水中Al、Ca、P、C、Ti发生氧化或氯化反应,生成氧化物或氯化物。
去除尽量少与Si、Fe发生氧化或氯化反应,不是杂质Si、Fe尽量不损失。
四、方法1、氧化精炼法:吹氧气(成本高效果好)吹空气(效果不好一般不用)加合成渣(成本低,可以用)2、氯化:吹入氯气(危险剧毒)化学性质1、四种氧化物氧化锰最稳定。
2.锰与碳由于部分碳和锰以化合物形式存在于锰铁中,所以用碳还原锰矿时得到的是高碳锰铁。
3、锰与铁锰与铁在固态和液态均可以完全互溶,锰矿中锰的含量一般为52%-90%,液相线逐渐下降。
锰铁熔点为1020-1350℃,在同样含碳量的情况下,随着锰含量的增加,熔点逐渐下降。
4、锰与硅锰与硅生成的硅化物中Mn5Si3和MnSi最稳定,它们比锰的碳化物稳定得多,猛鬼合金含量范围范围为锰60%-63%,硅12%-23%,且随着含硅量的增加熔点升高:锰硅合金熔点为1040-1285℃5、锰与磷能形成稳定的磷化物,Mn3P2最稳定,所以在锰铁中,特别是高炉锰铁一般含磷较高6、锰与硫7固溶体含氮量为2.13%-9.22%,这是氮在氮化锰铁中存在的形式和范围。
第二节、锰系合金牌号一、牌号1、分类按产品的碳含量分为高碳、中碳、低碳、微碳锰铁。
按冶炼方法分高炉锰铁和电炉锰铁,电炉锰铁又分为高、中、低、微碳。
按。
分为氧化矿和碳酸矿。
按用途分冶金用锰矿和化工用锰矿。
按铁锰比分。
二、锰矿的资源有国内资源和国外资源三、对锰矿质量的评价标准1.化学成分1)含锰量≥30%2)铁不是有害元素,不是越高越好,锰铁比=3-10 3)磷是有害元素,越低越好锰磷比≥200-500 4)三氧化二铝不是有用的≤7% 5)氧化钙氧化镁是有用的,不限制6)二氧化硅除冶炼硅锰合金不受限制外其他越低越好7)Cu Pb Zn As有色金属越低越好2、物理性能1)粒度均匀,与炉子大小有关2)水分要低≤7%3)强度≥5.0MPa四、锰矿造块1、锰矿造块的目的①改善锰系合金冶炼技术经济指标②扩大对贫锰矿粉矿资源的利用2、造块的方法烧结成球团。